Connect Refrigerant Lines. Whirlpool W4GH6, GOLD W4GH6
Add to My manuals20 Pages
Whirlpool GOLD W4GH6 heat pump is an energy-efficient and versatile HVAC system designed for outdoor use. It features a variable speed blower for precise temperature control and efficient airflow. With its 16 SEER rating, this heat pump delivers exceptional cooling and heating performance, resulting in significant energy savings. The thermal expansion valve ensures optimal refrigerant flow for enhanced cooling and heating capacity.
advertisement
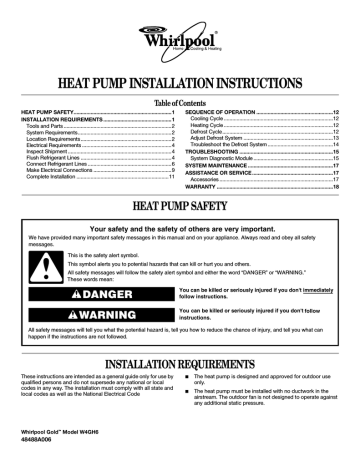
17. Install the valve cores.
A
B
18. Install the R-410A thermal expansion valve specified for this system in the indoor coil.
NOTE: R-410A systems use only thermal expansion valves.
19. Pressurize the lines and indoor coil with a pressure not to exceed 20 psig.
20. Leak test the lines with a pressure not to exceed 20 psig.
21. Open the suction and liquid service valves fully.
22. Insulate the suction line with refrigerant line insulation material of ¹⁄₄" or more wall thickness.
23. Pack insulating material around refrigerant lines where they penetrate the structure to protect the lines and to minimize vibration transmission.
A. Suction pressure tap
B. Liquid pressure tap
Connect Refrigerant Lines
Refrigerant lines must be connected by a licensed, EPA certified refrigerant technician in accordance with established procedures.
Thermal Expansion Valve Installation
A
IMPORTANT:
■ Connecting refrigerant lines must be clean, dehydrated, refrigerant-grade copper lines. Heat pumps should be installed only with specified line sizes for approved system combinations with elevation differences up to 15 ft and total length of up to 50 ft. See the Suction Line Sizes and Liquid
Line Sizes charts later in this section.
F
■
■
Avoid sharp bends or possible kinking in the refrigerant lines during installation as this may cause a reduction in performance.
Use care with the refrigerant lines during the installation process. Sharp bends or possible kinking in the lines will cause a reduction in performance.
A. Distributor
B. Teflon ® seal
C. Thermal expansion valve
E
■ To avoid contamination of the refrigerant system, do not remove the caps from the lines or system connection points until connections are ready to be completed.
To install the thermal expansion valve:
1. Separate the distributor assembly.
D
B
D. Liquid line stub
E. Strainer
F. Teflon ® seal
Install Thermal Expansion Valve
C
2. If a piston orifice is installed, remove the piston orifice and old
Teflon ® seal and discard.
W4GH6 heat pumps are designed for use with thermal expansion valve systems only. An R-410A system will not operate properly with an R-22 thermal expansion valve.
Thermal expansion valves equipped with Chatleff-type fittings are available from the manufacturer. See Thermal Expansion Valve
Kits chart in “System Requirements.”
3. Insert nozzle end of the thermal expansion valve along with a new Teflon ® seal into the distributor.
4. Tighten to 20 to 30 ft lbs. Use backup wrench on all wrench flats.
NOTE: Overtightening may crush the Teflon ® seal and cause a leak.
5. Attach liquid line portion of distributor assembly along with new Teflon ® seal to the inlet of the thermal expansion valve.
®Teflon is a registered trademark of E.I. Dupont de Nemours and
Company.
6
6. Tighten to 20 to 30 ft lbs. Use backup wrench on all wrench flats.
NOTE: Overtightening may crush the Teflon ® seal and cause a leak.
7. Connect the external equalizer line to the equalizer port on the suction line.
8. Tighten to 8 ft lbs.
9. Attach the superheat sensing bulb to the suction header with the strap provided with the thermal expansion valve.
A B
F
E
D
C
A. Equalizer port
B. Superheat sensing bulb
C. Thermal expansion valve
D. Liquid line
E. Suction line
F. Equalizer line
NOTE: If installing a thermal expansion valve on an indoor coil that previously used a fixed orifice, be sure to remove the existing fixed orifice. Failure to remove a fixed orifice when installing a thermal expansion valve to the indoor coil may result in improper operation and damage to the system.
Connect Liquid and Suction Lines
1. Route the suction and liquid lines from the fittings on the indoor coil to the fittings on the heat pump. Run the lines in as direct a path as possible, avoiding unnecessary turns and bends.
2. For product efficiency, be sure that the suction line is insulated over the entire exposed length and that both suction and liquid lines are not in direct contact with floors, walls, ductwork, floor joists, or other piping.
3. Remove valve cores.
4. Wrap the service valves with a wet rag.
5. Connect the suction and liquid lines, using a brazing compound. Braze with an alloy of silver or copper and phosphorus with a melting point above 1,100°F.
NOTE: Do not use soft solder.
6. Make sure indoor coil has been put in place according to the
Installation Instructions and is connected to the refrigerant lines.
7. Replace valve cores.
8. Pressurize the lines and indoor coil with a pressure not to exceed 20 psig.
9. Leak test the lines with a pressure not to exceed 20 psig.
10. Evacuate the indoor coil and lines to a minimum of
500 microns to remove contamination and moisture, then disconnect the vacuum pump.
11. Open the suction and liquid service valves fully.
12. Insulate the suction line with refrigerant line insulation material of ¹⁄₄" or more wall thickness.
13. Pack insulating material around refrigerant lines where they penetrate the structure to protect the lines and to minimize vibration transmission.
Refrigerant Charge
Refrigerant lines must be connected by a licensed, EPA certified refrigerant technician in accordance with established procedures.
IMPORTANT:
■
■
Refrigerant charge adjustment will be required for line set lengths greater than 15 ft and for evaporator coils not matched to the systems.
The heat pump is factory charged with the proper refrigerant charge amount for a matching evaporator and 15 ft of refrigerant line. Refer to the heat pump rating plate for the exact amount of this factory charge.
■
■
■
Adjustment of the refrigerant charge will be necessary based on the system combination and line length. To adjust the refrigerant size for increased line lengths, add the following amount of refrigerant.
For line set lengths greater than 15 ft, add refrigerant by weighing in 0.60 oz per ft of ³⁄₈" O.D. liquid line.
If necessary, adjust the refrigerant charge for compatibility with the evaporator coil.
In heat pump systems, horizontal suction lines should be slightly sloped toward the heat pump. Piping must avoid dips or low spots, which can collect oil.
Check Charge Using Normal Operating Pressures
Use Normal Operating Pressures chart to perform maintenance checks.
NOTES:
■ The Normal Operating Pressures chart is not a procedure for charging the system.
■
■
Minor variations in these pressures may be due to differences in installations.
Significant deviations could mean that the system is not properly charged or that a problem exists with some component in the system.
7
Normal Operating Pressures
NOTE: Values provided in chart are typical pressures. Indoor unit matchup, indoor air quality and indoor load will cause pressures to vary.
Model
Temperature of the Air
Entering the Outdoor Coil
-24
Liquid
Cooling—1st Stage (Low Capacity)
Suction
-36
Liquid Suction
-48
Liquid Suction
-60
Liquid Suction
65ºF
75ºF
85ºF
95ºF
105ºF
232
264
307
353
403
115ºF 460
Cooling—2nd Stage (High Capacity)
146
148
149
151
153
155
225
261
302
349
397
461
144
147
149
151
153
157
235
268
310
356
407
466
144
145
147
148
150
152
225
264
305
352
405
459
138
141
142
146
148
150
65ºF
75ºF
85ºF
95ºF
105ºF
240
279
322
371
423
115ºF 485
Heating—1st Stage (Low Capacity)
40ºF 337
143
145
147
149
151
154
239
278
322
367
426
489
139
141
143
146
148
151
244
283
326
374
427
491
140
141
144
147
148
151
241
280
324
373
425
486
134
136
137
138
142
146
93
117
328
333
98
118
369
366
75
114
351
335
63
92 50ºF 322
Heating—2nd Stage (High Capacity)
20º
30ºF
40ºF
50ºF
279
288
302
306
62
76
93
112
296
309
322
336
62
75
92
113
311
334
354
381
58
72
89
108
308
323
318
329
59
70
69
82
8
advertisement
Related manuals
advertisement
Table of contents
- 1 HEAT PUMP SAFETY
- 1 INSTALLATION REQUIREMENTS
- 2 Tools and Parts
- 2 System Requirements
- 2 Location Requirements
- 4 Electrical Requirements
- 4 Inspect Shipment
- 4 Flush Refrigerant Lines
- 6 Connect Refrigerant Lines
- 9 Make Electrical Connections
- 11 Complete Installation
- 12 SEQUENCE OF OPERATION
- 12 Cooling Cycle
- 12 Heating Cycle
- 12 Defrost Cycle
- 13 Adjust Defrost System
- 14 Troubleshoot the Defrost System
- 15 TROUBLESHOOTING
- 15 System Diagnostic Module
- 17 SYSTEM MAINTENANCE
- 17 ASSISTANCE OR SERVICE
- 17 Accessories
- 18 WARRANTY