INSTALLATION, PIPING, AND WIRING. IWAKI AMERICA MXM Series, MXM-545, MXM-543
Add to My manuals34 Pages
IWAKI AMERICA MXM-545 is a magnetic drive pump designed for industrial and commercial applications. It features a high-performance motor that delivers up to 5 HP, enabling it to handle a wide range of liquids, including corrosive and hazardous materials. The pump's non-metallic construction provides excellent resistance to chemical attack, making it suitable for use in harsh environments. The MXM-545 is also self-priming, allowing it to operate even when there is no liquid in the suction line.
advertisement
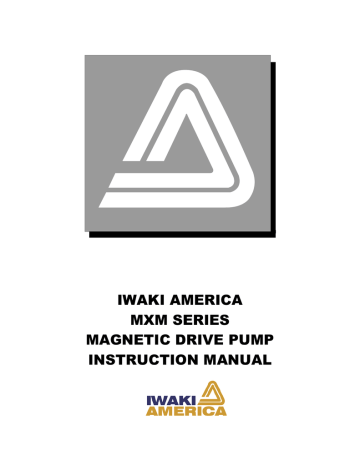
8 Installation, Piping, and Wiring
Installation Position
1. Install the pump as close to the suction tank as possible (flooded suction). If the suction port of the pump is positioned higher than the suction tank (suction lift), be sure to arrange a foot valve in the suction pipe. The lifting capability depends upon the liquid properties, temperature, and length of suction piping. For details, consult Iwaki America or your distributor.
2. The pump can be installed indoors or outdoors. However, there should be sufficient space around the pump to enable efficient and easy maintenance.
Installation
1. The pump anchoring area must be greater than the area of the pump baseplate. If the anchoring area is not large enough, the baseplate may be damaged due to the concentration of loads placed on it.
2. Set the pump baseplate on a concrete foundation and fasten the anchor bolts tightly to prevent the pump from vibrating during operation. A sturdy metal (or reinforced) skid or platform is also an acceptable mounting surface.
3.
Insert a spacer between the concrete suface and the bottom of the base to level the pump horizontally. Next put a level on the discharge flange surface to adjust the pump horizontally in the direction of the pump shaft. Also adjust the direction vertical to the pump shaft at the same time by placing a level on the suction flange surface. Pour cement mortar into the anchor bolt holes after leveling has been completed. When the cement mortar is hardened, fasten the anchor bolt nuts firmly. [Fig. 2]
4. In case there is influence of motor vibration during operation (e.g. sympathetic vibration with piping), an expansion joint should be provided between the pump and the piping before installation.
Otherwise, pipes and gauges may be damaged.
Anchor bolt
Base
Spacer
10
1.
Piping
Discharge pipe (use a support
To keep the pump free from the load of the pipe)
5. Motor
6. Pump
18
7
8
1
2
12
3
4
12
22
6 5 8 12 11 10
11. Suction pipe (shortest horizontal section with an ascending gradient toward the pump)
15
21
22
14
20
18
15. Suction pipe stabilizer brace
(used if suction pipe is particularly long)
16
17
19
17. 1.5D* or more
18. 18 inches or more
19. 1-1.5D* or more (if sediment
Figure 3
accumulates easily)
13
21. Screen
Suction Piping
1. The suction pipe should employ the flooded suction method if possible. The shortest pipe possible, with the minimum number of bends, should be designed. Arrange a proper support on the suction pipe so that the load and the thermal stress of the pipe itself are not applied to the pump.
2. Attach the coupling on the suction pipe carefully, so that no air enters the line. The presence of air in the suction pipe may prevent priming of the pump.
3. Avoid installations with poor suction conditions (e.g. vacuum in suction tank, large suction head or long suction piping). NPSHa should always be at least 2 feet greater than NPSHr. For NPSHr values, refer to the standard performance curve for your pump model or contact Iwaki America or your distributor.
9
11
4. When using a bend on the suction side, install a straight pipe which is more than 20 inches long or 10 times as long as the suction port diameter before the suction port of the pump. Use the largest possible radius of curvature for the bend.
5. Do not allow any projection where air may be trapped along the suction pipe. The suction pipe should have an ascending gradient toward the pump.
6. If the diameters of the pump suction port and the suction pipe are different, use an eccentric reducer pipe. Connect the eccentric reducer pipe such that the upper part of it is level. Never use a suction
pipe with a diameter smaller than that of the pump's suction port.
7. When using the flooded suction method, the suction pipe should be given a slight ascending gradient toward the pump so that no air pocket is created on the suction side.
8. The end of the suction pipe should be located 18 inches or more below the surface of the liquid.
9. A screen should be provided at the inlet of the suction tank to prevent the entrance of foreign matter into the suction pipe. Foreign matter may cause malfunctioning of and/or damage to the pump. The end of the suction pipe should be a least 1- 1.5D from the bottom of the suction tank. (D=Diameter of suction pipe).
10. When employing the suction lift method, install a foot valve on the suction pipe.
11. When using the flooded suction method, it is recommended that a gate valve be installed on the suction pipe for easier overhaul inspection of the pump. Since this valve is used only in the overhaul inspection of the pump, keep it fully opened during normal pump operation.
12. Pay close attention to the lowest level of the liquid in the suction tank to avoid vortexing, air entrapment and associated suction piping concerns.
The inflow pipe into the suction tank should be distanced from the suction pipe and positioned below the liquid surface as a means of preventing air entrainment to the suction pipe. If air bubbles are generated in the suction tank, install a baffle.
13. It is recommended that a vacuum/pressure gauge be installed on the suction piping approximately 6 pipe diameters from the pump suction port.
12
Figure 4
Discharge Piping
1. Use proper pipe supports so that the weight of the piping does not load the pump nozzle.
2. If a method other than flooded suction is used, install a special pipe for priming.
3. If the piping is very long, its diameter should be determined by calculating the piping resistance.
Otherwise, the specified performance may not be obtained due to increased piping resistance.
4. A check valve should be installed if any of the following conditions exists in the piping:
• The discharge piping is very long.
• The discharge head is 50 feet or more.
• The end of the discharge pipe is located 30 feet higher than the surface of the suction tank.
• Several pumps are connected in parallel with the same piping.
5. The installation of a gate valve on the discharge pipe is recommended for the adjustment of discharge quantity and for the prevention of motor overload. When installing both a check valve and a gate valve, the check valve should be positioned between the pump and the gate valve.
6. A pressure gauge must be installed on the discharge piping, prior to the gate valve.
13
7. An air bleeding valve should be installed if the discharge pipe is very long in the horizontal direction.
8. A drain valve should be installed for the drainage of liquid if there is a chance that the liquid in the discharge pipe will freeze.
Wiring
POWER
For ½ - 7½ HP motor:
R S T
OLR
M
MC
ON
OFF
OLR
M
MC
MOTOR
ELECTROMAGNETIC SWITCH
PUSH BUTTON
OVERLOAD RELAY
Figure 5
MC
OFF
ON
PUSHBUTTON
Use appropriate wiring materials, follow the instruction manual for the motor and abide by the local and national electrical codes. In addition, follow the instructions given below:
1. Use a motor contactor that conforms to the specifications (voltage, current, etc.) of the pump motor.
2. If the pump is installed outdoors, use waterproof wiring to protect the switches from rainwater and moisture.
3. The motor contactor and push button should be installed a reasonable distance from the pump.
Refer to the wiring examples shown above. (These examples do not include the installation of a dry run prevention device. Follow the instruction manual of the dry run prevention device when installing it.)
14
advertisement
Related manuals
advertisement
Table of contents
- 3 SAFETY INSTRUCTION
- 4 CAUTION
- 5 UNPACKING AND INSPECTION
- 6 MODEL IDENTIFICATION
- 7 SPECIFICATIONS
- 8 MATERIALS OF CONSTRUCTION
- 9 HANDLING INSTRUCTIONS
- 12 INSTALLATION, PIPING, AND WIRING
- 17 OPERATION
- 19 MAINTENANCE AND INSPECTION
- 23 TROUBLESHOOTING
- 25 PARTS DESCRIPTION AND EXPLODED VIEW
- 26 DISASSEMBLY AND ASSEMBLY OF PUMP
- 32 SPARE PARTS
- 33 DIMENSIONS AND WEIGHTS