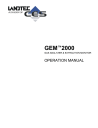
advertisement
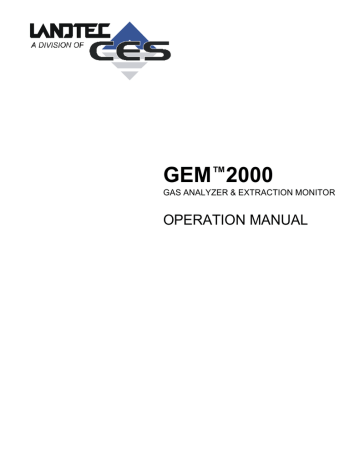
GEM™2000 Operation Manual
7.3 Techniques for Controlling Landfill Gas
There are many techniques for controlling landfill gas extraction. These techniques represent tools, which are used together to control landfill gas. The Accu-Flo wellhead is designed to work with all of these techniques. Below is a discussion of the individual techniques, how to use them, and their limitations.
Reliance on only a few of the techniques discussed can lead to misinterpretation of field data and improper operation of the well field. Later the best use of these techniques to optimize landfill gas control will be discussed.
7.3.1 Controlling by Wellhead Valve Position
Unless the valve handle is calibrated for a given flow rate, this method is unreliable. The position of the valve handle alone does not provide sufficient information about the well to control it. It is useful to note the relative position of the valve, and essential to know which valves are fully open or fully closed.
7.3.2 Controlling by Wellhead Vacuum
This technique relies on the relationship of well pressure/vacuum to flow for a given well. Reliance upon this method, however, can be misleading. This is because the square root relationship between flow and pressure is difficult to affect while performing day-to-day well field adjustments. As decomposition, moisture, and other conditions change, this method shows itself to be inadequate and imprecise.
7.3.3 Controlling by Gas Composition
This method determines methane, nitrogen (balance gas) and other gas composition parameters at wellheads and at recovery facilities using portable field instruments and, sometimes, analytical laboratory equipment. Complete knowledge of gas composition (i.e., major fixed gases: Methane, Carbon Dioxide,
Oxygen and Nitrogen) is desirable. It is also necessary to check other gas parameters, such as Carbon
Monoxide, to fully evaluate the condition of the well field. Reliance on this information can lead to improper operation of the well field. Indications of excessive extraction often do not show up right away. This method often leads to a cycle of damage to the methane producing bacteria population and then to over-correction.
This cycling of the well and producing area of the landfill is not a good practice. It leads to further misinterpretation of the condition of the well field and has a disruptive effect on the operation of the well field.
The use of analytical laboratory instrumentation such as a gas chromatograph is a valuable supplementary tool to verify gas composition. This normally requires collection of samples at the wellhead and analysis at some fixed location where the equipment is located. The drawbacks of this method as a primary means of obtaining information for well field adjustment are the time expended, cost, and probably most important, responsiveness to the needs of the well field for timely adjustment. The laboratory equipment required is also very costly. Some analysis is recommended for verification of field readings from time to time. It is recommended a monthly sample of the composite gas be taken at the inlet to the flare or gas recovery facility.
7.3.4 Controlling by Flow Rate
This is a more exacting technique for determining and adjusting gas flow at individual wells. It requires using a fixed or portable flow measurement device at each wellhead to obtain the data needed to calculate volumetric (or mass) flow rates. It is normally convenient to use cubic feet per minute or per day, as a standard unit of measure for volumetric flow. It is important to distinguish between the volumetric quantity of
Page 46
GEM™2000 Operation Manual landfill gas and the volumetric quantity of methane extracted from each well and the landfill in total. The two variables are somewhat independent of each other and it is the total quantity of methane extracted we are interested in. It is possible for the total quantity of landfill gas extracted to increase while the total quantity of methane extracted decreases. To monitor this, the quantity of methane extracted (LFG flow x percent methane) or the quantity of BTUs recovered per hour (LFG flow x percent methane x BTUs per cubic foot of methane x 60 minutes per hour) can be calculated. It is conventional to measure BTUs per hour as a unit of time. There are approximately 1012 BTUs of heat per cubic foot of pure methane (like natural gas), although this figure varies a little among reference texts.
Measuring flow is an essential part of monitoring and adjusting a well field. The well should be adjusted until the amount of methane recovered is maximized for the long term. A greater amount of methane or energy can usually be recovered over the short term; however, this ultimately leads to diminishing returns. This is seen in stages as increased CO
2
and gas temperature and later as increased oxygen from well over-pull. In time, the methane will also decline. This is the result of a portion of the landfill, usually at the surface, being driven aerobic. In this portion of the landfill, the methane-producing bacteria will have been destroyed (due to the presence of oxygen). With the methane-producing capacity of the landfill reduced, the pore space in the area no longer producing may become filled with landfill gas equilibrating (moving in) from an unaffected producing area. This leaves the impression that more gas can be recovered from this area, and may lead to the operator opening the well or increasing flow.
7.4 Well field Monitoring
The frequency of LFG well field monitoring varies depending upon field requirements and conditions. Normal monitoring frequency for a complete field monitoring session with full field readings (suggested normal and abbreviated field readings list follows) will vary from typically once a month to once a week. Well field monitoring should not normally be extended beyond one month. The importance of regular, timely monitoring cannot be overemphasized.
7.5 Typical Field Readings
•
Name of person taking readings
•
Date/time of each reading
•
Methane (CH
4
)
•
•
•
Oxygen (O
2
)
Carbon Dioxide (CO
2
)
Balance Gas (primarily nitrogen N
2
)
•
Wellhead gas temperature (flowing)
•
Ambient air temperature
•
Static pressure (PS) (from GEM™2000 or magnehelic) or other device(anemometer/velometer)
•
Velocity head (P or PT) (from GEM™2000 or pitot tube and magnehelic)
•
Wellhead gas flow (from GEM™2000, or pitot tube & magnehelic, or anemometer/velometer)
•
Wellhead adjustment valve position (initial and adjusted)
•
New wellhead vacuum and flow information after adjustment
•
Calculation of each well’s LFG and methane flow and sum total
•
Observations/comments
Additionally, Carbon Monoxide (CO) or Hydrogen Sulphide (H
2
S) readings may be taken if problems are suspected. Supplementary monitoring once to several times a week may be performed using an abbreviated form of field readings.
Page 47
GEM™2000 Operation Manual
7.6 Abbreviated Field Readings
•
Name of person taking readings
•
Date/time of each reading
•
Methane (CH
4
)
•
Oxygen (O
2
)
•
Wellhead gas temperature (flowing)
•
Ambient air temperature
•
Static pressure (PS) (from GEM™2000 or magnehelic)
•
Velocity head (P or Pt) (from GEM™2000 or pitot tube and magnehelic)
•
Wellhead gas flow (from GEM™2000, or pitot tube and magnehelic, or anemometer/velometer)
•
Wellhead adjustment valve position (initial and adjusted)
•
New wellhead vacuum and flow information after adjustment
•
Observations/comments
Line vacuums and gas quality may be taken at key points along the main gas collection header and at subordinate branches. This helps to identify locations of poor performance, excessive pressure drop, or leakage. Perform systematic monitoring of the well field, taking and logging measurements at each wellhead and major branch junction in the collection system.
During monitoring, examine landfill and gas collection system for maintenance issues. Record needed maintenance or unusual conditions. Examples of unusual occurrences or conditions are unusual settlement, signs of subsurface fires, cracks and fissures, liquid ponding, condensate/leachate weeping from side slopes, surface emissions and hot spots, and liquid surging and blockage in the gas collection system. Field readings should be kept in a chronological log and submitted to management on a timely basis.
7.7 Well field Adjustment Criteria
There are several criteria used in well field adjustment. The primary criterion is methane quality. Methane quality is an indicator of the healthy anaerobic state of the landfill and thus proper operation of the LFG collection system. However, a decline in the healthy productive state of the landfill is usually not immediately apparent from methane quality. Due to this, several criteria must be considered at once.
Conditions within the landfill favor methane production. Following are well field adjustment criteria and typical conditions for consideration:
•
Methane quality (ranging from 26 percent upwards)
• pH
•
Temperature
•
General overall quality
•
Moisture conditions
•
Waste stream characteristics
•
Placement chronology
•
Insulation characteristics
•
Oxygen quality (ranging below 1 percent, preferably less then ½ percent)
•
Landfill cover porosity and depth in the proximity of the well
•
Landfill construction factors including:
•
Type of fill
•
Size and shape of refuse mass
•
Depth of fill
Page 48
GEM™2000 Operation Manual
•
Compaction
•
Leachate control methods
•
Seasonal, climatic, geographical, and recent weather, or other considerations, including seasonally arid or wet conditions, precipitation, drainage, groundwater
•
Surrounding topography and geologic conditions
•
Proximity of the well to side slopes (within 150 to 200 feet and less may require conservative operation of the well)
•
Nitrogen (typically 8 to 12 percent and less)
•
Temperature (between ambient and about 130 °F)
•
LFG and methane flow from the wellhead
•
Design of the gas collection system
•
Landfill perimeter gas migration and surface emission control, or energy recovery objectives
•
Diurnal fluctuation (day to night) of atmospheric pressure
7.8 Establishing Target Flows
For a given individual well, a target flow is established which will likely support maintenance of methane and oxygen quality objectives while maximizing the recovery of landfill gas. Typically, small adjustments are made in flow to achieve and maintain quality objectives. The well must not be allowed to over pull. High well temperatures, (130
°
to 140
°
F and greater), are an indication of aerobic activity and, thus, well over-pull.
These effects may not be immediately apparent.
Well adjustment should be made in as small an increment as possible, preferably an increment of ten percent of the existing flow or less. There may be obvious conditions when this is not appropriate, such as when first opening up a well or when serious over-pull is recognized. Every effort should be made to make adjustments and operations as smooth as possible. Dramatic adjustments, or operating while switching between a high flow mode and a well shutoff mode, should be avoided.
7.9 Well field Optimization
Every effort should be made to continuously locate and correct or eliminate conditions (e.g., gas condensate, surging and blockage, settlement, etc.), which inhibit efficient operation of the gas collection system. This allows well monitoring and adjustment to be significantly more effective.
7.10 Migration Control—Dealing with Poor Methane Quality
If methane and oxygen quality objectives cannot be maintained at a given well, such as a perimeter migration control well, then an attempt should be made to stabilize the well as closely as is practical, avoiding significant or rapid down trending of methane or up trending of oxygen.
It is not uncommon for perimeter migration control wells to be operated at less than 40 percent methane or greater than one-percent oxygen. It should be recognized that these wells are likely in a zone where some aerobic action is being induced, and that there is some risk of introducing or enhancing the spread of a subsurface fire. Sometimes a judicious compromise is necessary to achieve critical migration control objectives or because existing conditions do not allow otherwise. Such situations should be monitored closely.
Page 49
GEM™2000 Operation Manual
7.11 Well field Adjustment—Purpose and Objectives
The objective of well field adjustment is to achieve a steady state of operation of the gas collection system by stabilizing the rate and quality of extracted LFG in order to achieve one or several goals. Typical reasons for recovery of LFG and close control of the well field are:
•
Achieve and maintain effective subsurface gas migration control.
•
Achieve and maintain effective surface gas emissions control.
•
Assist with proper operation of control and recovery equipment.
•
Avoid well “over-pull” and maintain of a healthy anaerobic state within the landfill.
•
Optimize LFG recovery for energy recovery purposes.
•
Control nuisance landfill gas odors.
•
Prevent or control subsurface LFG fires.
•
Protect structures on and near the landfill.
•
Meet environmental and regulatory compliance requirements.
Well field adjustment is partly subjective and can be confusing because it involves judgment calls based on simultaneous evaluation of several variables, as well a general knowledge of site specific field conditions and historical trends. Well field evaluation and adjustment consist of a collection of techniques, which may be used, in combination, to achieve a steady state of well field operation.
Page 50
GEM™2000 Operation Manual
8 Troubleshooting
Problem
Unit does not turn on or operation is erratic
“Flow Fail” is displayed and an audible alarm is heard
Readings taken are not what was expected
Unit displays***** or >>>>>
Oxygen reading is high on all wells
Unit will not download readings or an error occurs while downloading.
Methane and Carbon Dioxide readings drift
Oxygen readings drift
Corrective Action/Reason
Battery charge is too low-recharge batteries.
Unit is too hot - cool down unit and try again.
Contact Factory Service.
The inlet is blocked.
Remove blockage and retry.
The particulate filter or water trap filter needs replacing.
Unit may be out of calibration. Calibrate unit with known gas concentration.
Water trap or particulate filters are clogged. Replace filter(s).
These symbols are substituted when the measured reading is out of range of the instruments capabilities in some fields or when a value needs to be entered manually such as temperature.
Check that the water trap housing is screwed on tight.
Check or replace O-rings on the water trap and instrument inlet.
Check the wellhead inset for cracks, replace O-ring on insert.
Field calibrate oxygen channel.
Verify that the communications software is the right version for the instrument being used.
Check that the proper serial port is selected in the software.
Contact Factory Service.
Perform a field calibration and check well again. Verify cal gas is flowing when regulator is turned on.
Verify all connections are tight and filters are not clogged.
Contact Factory Service.
Perform a field calibration - zero and span.
Contact Factory Service.
Black screen displayed when unit turned On Charge unit over night and try again.
Unit too hot - cool down and try again.
Try adjusting contrast level.
Contact Factory Service.
Nothing happens when the Gas Pod is installed Remove and re-seat the Gas Pod.
Contact Factory Service.
Temperature does not update when temperature probe is installed
Check the probe fitting is fully seated.
Check the probe plug is screwed together tightly.
Contact Factory Service.
Page 51
GEM™2000 Operation Manual
9 Technical Specifications
9.1 Physical
Weight
Size
Case material
Keys
Display
Filters
4.4 lbs.
L 2.48” x W 7.48’’ x D 9.92”.
Anti-static ABS.
Membrane panel.
Liquid Crystal Display 40 x 16 characters. Fibre optic woven backlight for low light conditions.
User replaceable integral fibre filter at inlet port and an external
PTFE water trap filter.
9.2 General
Temperature measurement
Temperature accuracy
Visual and audible alarm
Communications
Relative pressure
9.3 Power supply
Battery type
Battery life
Battery charger
Charge time
Alternative power
Battery lifetime
9.4 Gas Ranges
Detection principle
With optional probe 14°F to 167
°
F.
±0.4ºF (± probe accuracy).
User selectable CO
2
, CH
4
and O
2
alarm levels via DataField 3.0.
RS232 protocol via download lead with variable baud rate.
±250 mbar from calibration pressure
Rechargeable Nickel Metal Hydride battery pack containing six
4AH cells. Not user replaceable.
Lithium Manganese battery for data retention.
Typical use 10 hours from fully charged condition.
Separate intelligent 2A battery charger powered from AC voltage supply (110-230V).
Approximately 2 hours from complete discharge.
Can be powered externally for fixed-in-place applications only.
Contact CES-LANDTEC for further information.
Up to 1,000 charge/discharge cycles.
Oxygen cell lifetime
Typical Accuracy
0 - Full Scale
CO
2
and CH
4
by dual wavelength infrared cell with reference channel.
O
2
by internal electrochemical cell.
Approximately 3 years in air.
Gas 0-5% volume
CH
4
±0.5%
CO
O
2
2
±0.5%
±1%
5-15% volume
±1%
±1%
±1%
15%-FS
±3%
±3%
±1%
(100%)
(60%)
(21%)
Response time, T90
Range
CH
4
CO
2
O
2
CH
4
CO
2
O
2
≤
20 seconds
≤
20 seconds
≤
20 seconds
0-70% to specification, 0-100% reading.
0-40% to specification, 0-100% reading.
0-25%
Page 52
GEM™2000 Operation Manual
9.5 Pump
Typical flow
Flow fail point
Flow with 200 mbar vacuum
Vacuum
300 cc/min.
50 cc/min approximately.
250 cc/min approximately.
70 inches H
2
0.
9.6 Operating Conditions
Operating temp range
Relative humidity
32°F to 104
°
F.
0-95% non-condensing.
Atmospheric pressure range 700-1200 mbar.
Displayed in Inches of Mercury (5.9 – 35.4“Hg).
Not corrected for sea level.
Atmospheric pressure accuracy ±5 mbar approximately.
Case seal IP65.
9.7 Optional Gas Pods
Typical Accuracy
(Subject to User calibration).
Response time, T90
Range
Gas
CO
H
2
S
SO
2
NO
2
CL
2
H
2
HCN
CO
H
2
S
SO
2
NO
2
CL
2
H
2
H
2
S
SO
2
NO
2
CL
2
H
2
HCN
0-Full Scale
±10% FS
±10% FS
±10% FS
±10% FS
±10% FS
±10% FS
±10% FS
60 seconds
≤
60 seconds
≤
60 seconds
≤
60 seconds
≤
60 seconds
≤
60 seconds
0-500ppm
0-50 or 0-200ppm
0-20 or 0-100ppm
0-20ppm
0-20ppm
0-1000ppm
0-100ppm
Page 53
advertisement
* Your assessment is very important for improving the workof artificial intelligence, which forms the content of this project
Related manuals
advertisement
Table of contents
- 8 WARNING Displayed
- 8 ERROR Displayed
- 13 Zero Channels
- 13 Span Channels
- 13 Factory Settings
- 13 Last Field Cal
- 16 Methane, Carbon Dioxide and Oxygen
- 17 S, CO and other Optional Gas Pods
- 20 3.0CS
- 24 Comments
- 26 Entering ID’s
- 29 Editing ID’s
- 31 Delete ID’s
- 32 Re-sequencing
- 34 Readings
- 37 Site Questions
- 42 Instrument Settings
- 48 Resource Links
- 50 Controlling by Wellhead Valve Position
- 50 Controlling by Wellhead Vacuum
- 50 Controlling by Gas Composition
- 50 Controlling by Flow Rate