- No category
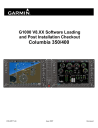
advertisement
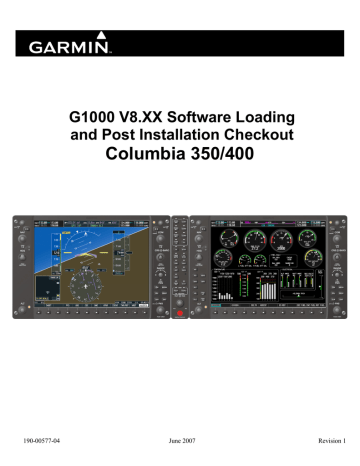
3.5 GMA 1347 Testing
Except for marker beacon operation, an in-aircraft checkout may be performed in the aircraft on the ramp with known good microphone, headset, and speaker.
3.5.1 Intercom System (ICS) Check
1. Plug in headsets at each ICS position.
2. Ensure that the MAN SQ key is off (no light).
3. Adjust volume for each position and verify that the ICS is working properly.
4. Check Pilot and Copilot ICS positions for isolation and proper operation of volume and squelch controls.
5. Press the PA key. Verify that microphone audio is heard over the speaker when the Push-To-
Talk (PTT) key is pressed.
3.5.2 Transceiver Operational Check
Perform a ramp test radio check by exercising the installed transceivers, microphone, microphone key and audio over the headphones and speaker. Verify that communications are clear and PTT operation is correct for each pilot position.
1. Select the audio source corresponding to each installed avionics unit (i.e. NAV1, NAV2, COM1,
COM2) and check for audio over the headsets.
2. Press the SPKR key and verify that the selected audio is heard over the speaker.
3. Verify communications with the ground tower using Comm. 1 and Comm 2.
4. Verify that the mic is being keyed using the pilot’s PTT switch, the copilot’s PTT switch (if installed) and a hand mic at the pilot and copilot positions.
3.5.3 Failsafe Operation Check
1. Turn the GMA 1347 off by pulling the AUDIO circuit breaker. This directs all COM 1 phone audio, MIC audio and MIC key to the pilot’s position.
2. Check the failsafe operation by exercising the COM 1 microphone, microphone key and audio over the headphones. All volume control for the COM audio should be through the PFD/MFD volume control. Verify proper operation of COM 1 using the failsafe operation.
3. Close the AUDIO circuit breaker to continue testing.
3.5.4 Marker Beacon Test
Figure 3-5. Marker Beacon Symbology
1. Using a ramp tester, simulate the outer marker, middle marker and inner marker signals by following the test equipment manufacturer’s instructions. Verify that each marker audio signal is present over the headphones and speaker.
Page 3-24
Revision 1
G1000 V8.XX S/W Load and Post Install Checkout – Columbia 350/400
190-00577-04
2. Verify that the outer, middle, and inner annunciations appear on the PFD when the corresponding signal is applied. Marker beacon annunciations appear at the upper left corner of the altitude indicator on the PFD (Figure 3-5). Operate the MKR MUTE key on the GMA 1347 and ensure that the audio signal is muted.
3.6 GIA 63 Testing
The following section applies to both GIA 63 units. Any differences in testing will be noted.
3.6.1 VHF COM Interference Test
This test must be conducted outside. Use of a GPS repeater inside a hangar may result in a failed test.
This procedure assumes that the system is currently set to 25 kHz COM channel spacing. Once the signal acquisition test from Section 3.3.1 has been completed successfully, perform the following steps:
1. On the MFD, monitor GPS signal strength bars on the 3 rd AUX page.
2. On the PFD, ensure that the CDI is set to GPS. If it is not, press the ‘CDI’ softkey until GPS
ENR is displayed.
3. Verify that the GPS “INTEG” flag is out of view.
4. Select 121.150 MHz on the No. 1 COM transceiver.
5. Transmit for a period of 35 seconds while monitoring GPS 1 signal strength levels.
6. During the transmit period, verify that the GPS “INTEG” flag does not come into view on the
PFD and verify that GPS 1 does not lose a 3-D navigation solution on the MFD.
7. Repeat steps 5 and 6 and re-transmit while monitoring GPS 2 signal levels on the MFD.
8. Repeat steps 5 through 7 for each of the following frequencies:
•
•
•
•
•
121.175 MHz
121.200 MHz
131.250 MHz
131.275 MHz
131.300 MHz
9. Repeat steps 4 through 8 for the No. 2 COM transceiver (GIA2).
10. On the MFD, select the AUX SYSTEM SETUP page (4 th page in AUX group).
11. Under the COM CONFIG field, change the COM channel spacing from 25 kHz to 8.33 kHz.
12. Go back to the 3 rd AUX page.
13. Select 121.185 MHz on the No. 1 COM transceiver.
14. Transmit for a period of 35 seconds while monitoring GPS 1 signal strength levels.
15. During the transmit period, verify that the GPS “INTEG” flag does not come into view on the
PFD and verify that GPS 1 does not lose a 3-D navigation solution on the MFD.
16. Repeat steps 14 and 15 and re-transmit while monitoring GPS 2 signal levels on the MFD.
17. Repeat steps 14 through 16 for each of the following frequencies:
• 121.190 MHz
•
•
130.285 MHz
131.290 Mhz
18. Repeat steps 13 through 17 for the No. 2 COM transceiver (GIA2).
G1000 V8.XX S/W Load and Post Install Checkout – Columbia 350/400
190-00577-04
Page 3-25
19. On the MFD, select the 4 th AUX page and change the COM channel spacing back to 25 kHz.
3.6.2 VOR/LOC/GS Test
Check the VOR, ILS, and Glideslope functions with ramp test equipment. Operate the equipment according to the test equipment manufacturer’s instructions. Adjust the RF signal to a level adequate to perform the test. Select the appropriate HSI source by using the CDI softkey.
NOTE
The PFD HSI does not show a course deviation bar unless a valid VHF nav frequency is tuned.
Simulate a VOR signal on radial 000° with a course-width of 20°. Verify full scale deflection of the CDI while applying a 10° deviation signal. Exercise the CDI with both right and left deviations for both NAV
1 and 2. Exercise the Glideslope deviation indicator with up and down deviation indications.
3.6.3 COM Antenna VSWR Checks
Check for insertion loss and VSWR (Voltage Standing Wave Ratio). VSWR should be checked with an in-line type VSWR/wattmeter inserted in the coaxial transmission line between the transceiver and the antenna. The VSWR should be inserted as close to the transceiver as possible. Any problem with the antenna installation is most likely seen as high reflected power. A VSWR of 3:1 may result in up to a
50% loss in transmit power. Ideally, the VSWR should be 2.5:1 or less.
3.7 GDL 69 Testing
NOTE
This section verifies correct installation in the aircraft. It does not activate the GDL 69
XM data link radio. If the XM Radio is activated, the channel list will contain more channels than the three that are shown for a radio that has not been activated. Complete instructions for activating the XM data link can be found in document 190-00355-04.
Page 3-26
Revision 1
G1000 V8.XX S/W Load and Post Install Checkout – Columbia 350/400
190-00577-04
1. Select the AUX – XM RADIO page on the MFD.
2. Using the channel control located in the cabin, verify that you can increment and decrement the channels (the white arrow to the left of the channel list indicates the currently selected channel).
Select channel 1 when complete.
3. Using the volume control located in the cabin, verify that you can increase and decrease the XM radio volume (the volume bar at the bottom of the screen will show changes to the volume level).
Set the volume to the mid position when done.
4. Plug a set of headphones into one of the passenger stations and verify that you can hear the XM radio playing in both left and right channels. The volume level may be adjusted to a comfortable level at this point.
5. Plug a set of headphones into one of the pilot station and verify that you can hear the XM radio playing in both left and right channels.
6. Gently lift the stall vane on the left wing to set off the stall horn. Verify that the GDL 69 audio is muted as long as the stall vane is lifted and the stall horn is heard.
3.8 GTX 33 Testing
Operation of the GTX 33 Mode-S transponder is accomplished using the G1000 PFD. Refer to Garmin part number 190-00567-00, G1000 Cockpit Reference Guide for the Columbia 350/400, for basic operation. Perform a basic operational check on the transponder. Any discrepancies or anomalies should be corrected before proceeding. The integrated transponder/altitude reporting system must be verified in accordance with Title 14 of the Code of Federal Regulations (CFR) §§ 91.411 and 91.413.
3.9 GDC 74A TESTING
Verification of the altimeter and airspeed must be performed using a pitot/static ramp tester. The static port and altimeter must be verified in accordance with Title 14 of the Code of Federal Regulations (CFR)
§ 91.411 and Part 43 Appendix E.
NOTE
The following tests are above and beyond the requirements set forth in Part 43 Appendix E.
3.9.1 Pitot/Static Airspeed Test
1. Command air data test set (ADTS) to simulate air speeds shown in the table below.
2. Wait for ADTS to report that target values have been achieved.
3. Verify that computed air speeds shown on the PFD are within the tolerances specified in the table below:
Calibrated air speed, knots
Allowed tolerance, ±knots
50 5.0
80 3.5
100 2.0
120 2.0
150 2.0
180 2.0
205 2.0
3.9.2 Static Port Vertical Speed (Rate of Climb) Test
1. Command ADTS to change the altitude at the rates shown in the table below.
2. Wait for ADTS to report that target rates have been achieved.
G1000 V8.XX S/W Load and Post Install Checkout – Columbia 350/400
190-00577-04
Page 3-27
3. Verify that the Rate of Climb reported by the Vertical Speed field on the PFD is within the tolerances specified in the table below:
Vertical Speed, feet/minute Allowed tolerance, ±feet/minute
2000 100
1000 50
500 45
200 45
0 45
-200 45
-500 45
-1000 50
-2000 100
3.9.3 OAT Probe Check
Check the outside air temperature (OAT) measurement shown on the PFD to ensure it reads ambient temperature.
3.10 GRS 77/GMU 44 Initial Alignment
The GRS 77 AHRS unit and the GMU 44 magnetometer unit require calibration before first flight. There are three procedures to be carried out. The aircraft engine must be started after the first procedure is complete. When ready to perform the procedures, shut the PFD and MFD off by pulling the PFD and
MFD circuit breakers. Restart both displays in configuration mode.
3.10.1 GRS 77 Pitch/Roll Offset Calibration
Figure 3-6. Pitch/Roll Offset
This procedure must be carried out with the engine off. Rotate the large FMS knob to select the GRS page group on the PFD. Rotate the small FMS knob clockwise to access the GRS/GMU calibration page on the PFD.
Page 3-28
Revision 1
G1000 V8.XX S/W Load and Post Install Checkout – Columbia 350/400
190-00577-04
To perform the following procedures press the following softkeys: a) 9 b) 10 c) 11 d) 12 (Far Right softkey)
1. Level the aircraft to within ±0.25° of zero pitch and zero roll using Columbia maintenance procedures in the Columbia 350/400 Airplane Maintenance Manual.
2. Initiate the AHRS Ground Pitch/Roll Aircraft Level compensation mode by performing the following steps: a) Ensure that the No. 1 GRS 77 is selected. b) Select PITCH/ROLL OFFSET, then press the ENT key. c) Follow the checklist items displayed on the PFD and press the ENT key as each one is completed or confirmed. When the CALIBRATE field is blinking, press the ENT key to begin the procedure. d) After several seconds, a new checklist appears in the lower half of the PFD. Press the ENT key as each item is confirmed. When the CONFIRM AIRCRAFT IS
LEVEL field is blinking, press the ENT key to continue.
3. The result of the pitch/roll offset compensation is displayed on the PFD. If successful, the AHRS records the required pitch and roll offsets, informs the operator of a successful conclusion and returns to normal operation.
4. Press the ENT key on the PFD to conclude this procedure.
5. Restart both displays in normal mode and proceed to Section 3.11.
3.11 Engine Start
To carry out the two remaining GRS/GMU procedures, the aircraft engine must be started. In order to start the engine, all engine/airframe transducers must have been checked to ensure proper operation.
G1000 V8.XX S/W Load and Post Install Checkout – Columbia 350/400
190-00577-04
Page 3-29
Columbia 400 (with Oxygen System Option)
Columbia 350 (without Oxygen System Option)
Figure 3-7. Engine/Airframe Indicators (Full EIS page)
On the MFD, check the indication for each of the sensor or monitor inputs with the aircraft engine off.
Observe the full EIS page by pressing the SYSTEM soft key on the MFD. While on the full EIS page, verify the following sensor indications (see Figure 3-7):
Engine/Airframe
Indicator
Desired Reading Airframe Check
Oil Temperature
Oil Pressure
Ambient
Approximately 0
Manifold Air Pressure Atmosphere Pressure
Tachometer 0
Fuel Flow
L & R Fuel Tanks
EGT (qty 6)
TIT (qty 2)
0
FULL (F) w/ full tanks
Ambient
Ambient
CHT (qty 6)
L Alternator Amps
R Alternator Amps
L Battery Amps
R Battery Amps
L Bus Volts
Ambient
0 ± 3 if on external power
0 ± 3 if on external power
Negative if battery is discharging *
Negative if battery is discharging *
GPU voltage with cross-tie closed (L
Battery volts when GPU disconnected)
Both
Both
Both
Both
Both
Both
Both
Columbia 400 only
Both
Both
Both
Both
Both
Both
Page 3-30
Revision 1
G1000 V8.XX S/W Load and Post Install Checkout – Columbia 350/400
190-00577-04
Engine/Airframe
Indicator
Desired Reading Airframe Check
R Bus Volts
GPU voltage (R Battery volts when
GPU disconnected)
Both
* NOTE: Accuracy of indication is ±3A, so value may be positive for small discharge currents.
The aircraft engine can now be started as needed to carry out the remaining GRS/GMU calibrations listed in Section 3.12. Follow the procedures in the applicable Pilot’s Operating Handbook, and start the engine. While the starter is engaged verify that the STARTER ENGD annunciation is displayed on the
PFD. Monitor engine instruments during startup for proper operation. When the engine is running, verify the following sensor indications at the appropriate EIS section (see Figure 3-7):
Engine/Airframe
Indicator
Desired Reading Airframe Check
L Alternator Amps
R Alternator Amps
L Bus Volts
R Bus Volts
Greater than 0 and L ALT OUT annunciation not displayed.
Greater than 0 and R ALT OUT annunciation not displayed.
Approximately 28 volts and L BUS
OFF annunciation not displayed.
Approximately 28 volts and R BUS
OFF annunciation not displayed.
Both
Both
Both
Both
With the engine at 1100 RPM or higher, verify that the OIL PRES LOW and FUEL PUMP annunciations are not displayed on the PFD.
3.12 Final GRS 77/GMU 44 Calibration Procedures
The Magnetometer Calibration Procedure (Calibration Procedure B) must be carried out at a site that is determined to be free of magnetic disturbances. If it is unsure whether the site is ‘clean’ the technician should verify that the site is ‘clean’ by following the guidance provided in Section 3.12.1. The technician may skip Section 3.12.1 if the site condition is acceptable.
3.12.1 Site Evaluation of Magnetic Disturbances for Magnetometer Calibration
Procedure (Optional)
NOTE
Typically, a compass rose is an acceptable location to perform the magnetometer calibration procedure. However, because not all compass roses are well maintained, even an existing compass rose should be regularly evaluated using the method described here to determine if it is free of magnetic disturbances. If evaluation of an existing compass rose indicates that magnetic disturbances are present, then an alternative location must be found to perform the Magnetometer Calibration
Procedure.
A G1000-equipped Columbia 350/400 airplane can be used to evaluate a candidate site for magnetic disturbances and determine whether it is a suitable location to perform the magnetometer calibration procedure. The magnetometer calibration procedure itself contains the logic to simultaneously survey the location for magnetic cleanliness while it is computing the magnetometer calibration parameters.
G1000 V8.XX S/W Load and Post Install Checkout – Columbia 350/400
190-00577-04
Page 3-31
The G1000-equipped Columbia 350/400 used to evaluate the site must have already completed the pitch/roll offset compensation procedure (Procedure A). However, prior completion of the Magnetometer
Calibration Procedure (Procedure B) is not required.
In order to evaluate a candidate site, the Magnetometer Calibration Procedure must be performed twice: once turning clockwise around the site, and once turning counter-clockwise. Both times, the procedure should be conducted as described in Section 3.12.2 of this document, with the exception of the direction of turns around the site.
NOTE
Although Section 3.12.2 indicates that the Magnetometer Calibration
Procedure should be performed by making a series of clockwise turns around the site, the procedure can also be performed by making counterclockwise turns for the purpose of evaluating the site for magnetic disturbances.
If, upon completion of the Magnetometer Calibration Procedure in each clockwise and counter-clockwise direction, the PFD displays the “CALIBRATION SUCCESSFUL / SITE IS CLEAN” message, then the candidate site is sufficiently free of magnetic disturbances and is acceptable for performing the
Magnetometer Calibration Procedure. It is important to obtain successful results in both the clockwise and counter-clockwise directions to ensure that the magnetometer sweeps over a large enough area at the candidate site.
If, upon completion of the Magnetometer Calibration Procedure in either of the two directions, the PFD displays either the “MAG FIELD AT SITE NOT UNIFORM”, or “MAG FIELD AT SITE DIFFERS
FROM IGRF MODEL” message, then the site contains magnetic disturbances that are too large.
3.12.2 GRS 77/GMU 44 Magnetic Calibration
CAUTION
CALIBRATION PROCEDURE B MUST BE CARRIED OUT ON A COMPASS ROSE IN ORDER TO
GUARANTEE MEASUREMENTS FREE OF ENVIRONMENTAL MAGNETIC DISTURBANCES.
ATTEMPTING TO CARRY OUT THIS MANEUVER ON A TYPICAL RAMP AREA MAY NOT
YIELD A SUCCESSFUL CALIBRATION. THE ACCURACY OF THE AHRS CANNOT BE
GUARANTEED IF THIS CALIBRATION IS NOT PERFORMED ON A MAGNETICALLY CLEAN
COMPASS ROSE OR EQUIVALENT. IF THE COMPASS ROSE CONDITION IS NOT KNOWN, IT
IS RECOMMENDED THAT THE TECHNICIAN FOLLOW THE GUIDANCE IN SECTION 3.12.1
1. Follow instructions in Section 3.11 and check the GEA 71. Start the aircraft engine following the procedures referenced in the G1000/Columbia 350/400 Airplane Flight Manual Supplement.
2. After aircraft engine startup, taxi the aircraft to a properly calibrated compass rose.
3. At the compass rose, align the aircraft to a heading of magnetic north ( ±5°).
4. Restart the PFD and MFD in configuration mode.
NOTE
The engine performance can be monitored on the GRS/GMU calibration pages during the procedure.
5. Go to the GRS Page Group on the PFD.
Page 3-32
Revision 1
G1000 V8.XX S/W Load and Post Install Checkout – Columbia 350/400
190-00577-04
6. Select the GRS/GMU Calibration page and enter the following softkey password: a) 9 b) 10 c) 11 d) 12 (Far Right softkey)
7. Activate the cursor and highlight the SELECT PROCEDURE window and select
MAGNETOMETER.
8. Press the ENT button.
9. Use the cursor to highlight the BEFORE CALIBRATION window.
10. Follow the checklist items displayed on the PFD and press the ENT key as each one is completed or confirmed. When the CALIBRATE field is blinking, press the ENT key to begin the procedure.
11. The PFD display advises the operator when to turn the aircraft, when to stop, and when to turn again.
12. Upon instruction to turn, taxi the aircraft in a right turn. After approximately 25° to 30° of turn from the last heading, the PFD display advises the operator to stop the aircraft.
NOTE
Due to the difficulties in executing smooth, accurate turns the PFD may incorrectly interpret a station and instruct to “HOLD POSITION” prior to full completion of a
30 ° turn. If this scenario is encountered, it is best for the operator to ignore the
“HOLD POSITION” command and instead use outside references to complete the approximate 30 ° turn. Instead of using the PFD instruction to turn as a real-time indication of when to turn, simply judge the 30° (±5°) turn increments of the aircraft by using the compass rose radials. Dwelling at these 30 ° increments for the time recommended by the PFD should result in successful calibration.
13. The PFD guides the operator to dwell at multiple headings around a complete circle.
G1000 V8.XX S/W Load and Post Install Checkout – Columbia 350/400
190-00577-04
Page 3-33
NOTE
Due to high winds or excessive airframe vibration, the operator may encounter a condition where the PFD restarts the 18-second countdown without full completion of the previous countdown. If this is encountered more than once for a given station, the operator should begin turning to the next station (approximately 30 °). A minimum of 2 successful stations per quadrant is required, where a successful station is a full 18-second countdown followed by instruction to move. Ensure that at least 2 stations per quadrant are completed. Thus, it may sometimes be required to dwell at a station after a countdown restart. A maximum of 20 stations is allowed for the entire calibration procedure. If too many countdown restarts are encountered, the calibration will fail with the message, “TOO MANY STATIONS.”
14. Repeat the turn-and-stop process until the PFD advises that a successful calibration is complete.
The GRS 77 AHRS then enters its normal operational mode. Press the ENT button on the PFD to conclude this procedure.
3.12.3 Engine Run-Up Vibration Test
Figure 3-8. Engine Run-Up Test
Initiate the AHRS engine run-up vibration test procedure by performing the following steps:
1. Select the ENGINE RUN-UP TEST procedure and press the ENT key.
2. Follow the checklist items displayed on the PFD, and press the ENT key as each one is completed or confirmed. When the CALIBRATE field is blinking, press the ENT key to begin the procedure.
3. The PFD display instructs the operator to gradually increase power from idle to full throttle and back to idle over a period of 1-2 minutes.
Page 3-34
Revision 1
G1000 V8.XX S/W Load and Post Install Checkout – Columbia 350/400
190-00577-04
4. When the operator has completed the engine run-up and the engine is back to an idle setting, press the ENT key to indicate that the process is complete. When this is done, the TEST
COMPLETE field stops blinking.
5. The PFD informs the operator if the installation has passed or failed the vibration test. If the test fails, the specific measurements causing the failure are identified and numeric values are displayed on the PFD.
6. Press the ENT key on the PFD to conclude this procedure.
NOTE
If failures are indicated, the engine run-up test may be repeated at most twice. If the test does not pass after three attempts, then the installation should not be considered reliable until the source of the vibration problem is identified and remedied. In the event of repeated failure of the engine run-up test, record the values that are reported to be out of range for future reference.
The following are potential causes for failure of the engine run-up test: a) Vibration motion of GRS 77 and/or GMU 44 caused by neighboring equipment and/or supports. b) Mounting screws and other hardware for GRS 77 and/or GMU 44 not firmly attached. c) GRS 77 connector not firmly attached to unit. d) Cabling leading to GRS 77 or GMU 44 not firmly secured to supporting structure. e) An engine / propeller that is significantly out of balance.
The aircraft can now be taxied back and the engine can be shut down for final testing. Restart both displays in normal mode to conduct autopilot, optional system and final system checks. Following a successful AHRS calibration, when the PFD powers up in normal mode, the AHRS attitude and heading information displayed should become valid within 1 minute of power-up.
G1000 V8.XX S/W Load and Post Install Checkout – Columbia 350/400
190-00577-04
Page 3-35
3.12.4 Magnetometer Interference Test
Figure 3-9. Magnetometer Interference Test
1. Initiate the AHRS magnetometer interference test procedure by performing the following steps: a) Select the MAG INTERFERENCE TEST procedure and press the ENT key. b) Follow the checklist items displayed on the PFD, and press the ENT key as each one is completed or confirmed. When the CALIBRATE field is blinking, press the ENT key to begin the procedure (as soon as the ENT key is pressed this time, a CALIBRATION
PROCEDURE window will appear).
Page 3-36
Revision 1
G1000 V8.XX S/W Load and Post Install Checkout – Columbia 350/400
190-00577-04
Figure 3-10. Magnetometer Interference Test Complete
2. After the “Begin test sequence” white text appears, wait approximately five seconds and then turn the Navigation lights on.
3. Leave the Navigation lights on for approximately 10 seconds, and then turn them off.
4. Wait approximately five seconds and then press the ENT key to complete the test.
5. The PFD informs the operator if the installation has passed or failed the magnetometer interference test. If the test passes, no further action is required.
6. Press the ENT key on the PFD to conclude this procedure.
NOTE
The magnetometer test will indicate a failure if any of the deviations exceed 2.5 mGauss.
However, the test can be considered passed even though MAG INTERFERENCE TEST
FAILED is displayed provided the deviations are less than the thresholds specified below.
7. If the MAG INTERFERENCE TEST indicates FAILED but ALL of the deviations are less than the following thresholds (X ≤ 5 mGauss, Y ≤ 5 mGauss, and Z ≤ 8 mGauss), the test can be considered to have passed and the installation is acceptable as-is.
NOTE
If the test does not pass the step above the magnetometer interference test may be repeated at most twice. If the test shows an X or Y deviation greater than 5 mGauss, or a
Z deviation greater than 8 mGauss after three attempts, then the installation should not be considered reliable until the source of the interference problem is identified and remedied. In the event of repeated failure of the magnetometer interference test, record
G1000 V8.XX S/W Load and Post Install Checkout – Columbia 350/400
190-00577-04
Page 3-37
the values that are reported to be greater than 5 mGauss for future reference and contact
Garmin for assistance.
3.13 Alternator Checks
With the aircraft engines still running, verify the operation of the alternator indications as follows:
1. Select the full screen EIS page on the MFD.
2. Verify that the left and right ALT AMPS are each indicating greater than 3A.
3. Turn off the LEFT ALT master switch. Verify that the left ALT AMPS drops to approximately zero on the MFD and the L ALT out annunciation appears on the PFD.
4. Turn on the LEFT ALT master switch and turn off the RIGHT ALT master switch. Verify that the right ALT AMPS drops to approximately zero on the MFD and the R ALT out annunciation appears on the PFD.
5. Turn on the RIGHT ALT master switch.
3.14 TAWS
1. Ensure that matching terrain data base cards are installed in the bottom card slots in the PFD and
MFD and the aircraft has a GPS position.
2. Select the TAWS page (5th page in the MAP group)
3. Verify that the title at the top of the page reads “MAP – TAWS”. If TAWS has not been enabled, the title will read “MAP – TERRAIN PROXIMITY” or “MAP – TERRAIN”.
4. Press the MENU button and select “Test TAWS” from the pop-up menu and press ENT.
5. After the TAWS test has completed, verify that “TAWS System Test Okay” is heard over the cockpit speaker.
Page 3-38
Revision 1
G1000 V8.XX S/W Load and Post Install Checkout – Columbia 350/400
190-00577-04
3.15 Optional System Checkouts
This section describes the checks that must be completed in order to verify that optional systems are correctly configured and connected to the G1000. The checks must be completed only for those systems that are part of a particular installation. Optional systems are considered previously installed; consequently, prior to (or concurrent with) the G1000 interface verification, additional system checks may be required – refer to the appropriate system installation manual for additional details.
3.15.1 WX500 Stormscope (if installed)
1. Verify that you can select the STORMSCOPE map page on the MFD.
2. Verify that LIGHTNING FAILED is not displayed in yellow in the center of the display (in place of the ownship symbol)
3. Using a Stormscope tester or equivalent, simulate lightning strikes on the map.
4. Open the STORM SCOPE circuit breaker on the avionics circuit breaker panel and verify that
LIGHTNING FAILED is displayed after several seconds.
5. Close the STORM SCOPE circuit breaker on the avionics circuit breaker panel and verify that
LIGHTNING FAILED is removed after several seconds.
G1000 V8.XX S/W Load and Post Install Checkout – Columbia 350/400
190-00577-04
Page 3-39
3.15.2 9900 BX TCAD (if installed)
NOTE
If the G1000 has not received any ARINC 429 data from TCAD, the
MUTE softkey will not be displayed. Instead, STBY, OPER and TEST softkeys will be displayed.
1. Select the TRAFFIC MAP map page on the MFD.
NOTE
If TIS is displayed instead of TAS, the G1000 has not been properly configured for TCAD.
2. Verify that the MUTE and ALT MODE soft keys are available on the bottom of the display.
Verify that a TAS mode (and not TAS FAIL ) is displayed in the upper left corner of the traffic map. Verify that NO DATA is not displayed in yellow in the center of the display (in place of the ownship symbol)
NOTE
The TCAD may take several minutes to warm up and become valid.
3. Press the MUTE soft key twice in half a second and verify that “Ground Mode, No Advisories” is heard over the cockpit speaker and “TCAD Altitude Data Invalid” is not heard.
4. Open the TRAFFIC circuit breaker on the avionics circuit breaker panel. On the MFD, verify that NO DATA is displayed in yellow after several seconds.
5. Close the TRAFFIC circuit breaker on the avionics circuit breaker panel and verify that NO
DATA is removed after several seconds.
Page 3-40
Revision 1
G1000 V8.XX S/W Load and Post Install Checkout – Columbia 350/400
190-00577-04
3.15.3 Oxygen System (if installed)
1. Select the full screen EIS page on the MFD.
2. Verify that the OXY QTY and OXY OUTLET gauges are displayed and do not have a red X through them (if the gauges are not displayed or have a red X through them, the oxygen system has not been properly configured).
3. Verify that the OXY QTY indicates the pressure in the oxygen bottle.
NOTE
For the remainder of the test, the oxygen bottle must be filled to at least
300 psi.
4. Plug an oxygen mask or cannula into the overhead distribution manifold. Ensure that the manual valve is open and that the breathing device is set to allow oxygen flow.
5. Press the OXYGEN softkey on the MFD to turn on the oxygen flow.
6. Verify that the OXY OUTLET indicates between 16 and 33 psi.
7. Press the OXYGEN softkey on the MFD to turn off the oxygen flow.
G1000 V8.XX S/W Load and Post Install Checkout – Columbia 350/400
190-00577-04
Page 3-41
3.16 Final System Checkout
The final checkout tests various secondary communications paths to ensure that the desired backup paths are in place. Perform the following steps and verify the results of each test.
3.16.1 GPS Failure Test
Not used.
3.16.2 GIA Failure Test
Single GIA Failure Conditions:
1. Remove power from GIA 1 by pulling
INTEG AVION 1 and COM 1 breakers.
2. Restore power to GIA 1. Allow to reacquire satellites.
3. Remove power from GIA 2 by pulling
INTEG AVION 2 and COM 2 breakers.
4. Restore power to GIA 2.
Dual GIA Failure Conditions:
1. Remove power from both GIA units.
2. Restore power to both GIA units.
GIA 1 Failure - For a GIA 1 failure, only the following shall flag invalid:
9 COM/NAV 1 field.
9 NAV 1 CDI loses deviation bar.
9 TAWS
9 AFCS
GIA 2 Power Failure - For a GIA 2 failure, only the following shall flag invalid:
9 COM/NAV 2 field.
9 NAV 2 CDI loses deviation bar.
9 TAWS
9 AFCS
9 CO Detector Fail
9 Stormscope Fail (if installed)
9 TCAD Altitude Invalid (if installed)
Dual GIA Failure - For a dual GIA failure, only the following shall occur:
9 COM/NAV 1 & COM/NAV 2 fields flag invalid.
9 GPS CDI flags INTEG on PFD.
9 NAV 1, 2 CDI loses deviation bar.
9 XPDR field flags invalid on PFD.
9 Engine Instrument field flags invalid on MFD.
9 TAWS
9 AFCS
9 CO Detector Fail
9 Stormscope Fail (if installed)
9 TCAD Altitude Invalid (if installed)
9 GMA 1 Fail (annunciation only)
9 AHRS 1 Not Receiving GPS Info alert
Page 3-42
Revision 1
G1000 V8.XX S/W Load and Post Install Checkout – Columbia 350/400
190-00577-04
3.16.3 Display Failure Test
MFD Display Failure Conditions:
1. Remove power from MFD.
2. Restore power to MFD.
PFD Display Failure Conditions:
1. Remove power from PFD.
2. Replace power to PFD.
The following shall occur when power is removed from the MFD:
9 PFD switches to reversion mode.
9 Attitude and Heading remain valid from AHRS.
9 Airspeed, Altitude, Vertical Speed, and OAT remain valid from Air Data Computer.
9 Engine Instrumentation appears on PFD.
9 COM/NAV 2 fields flag invalid.
9 TAWS
The following shall occur when power is removed from the PFD:
9 MFD switches to reversion mode.
9 Attitude and Heading remain valid from AHRS.
9 Airspeed, Altitude, Vertical Speed, and OAT remain valid from Air Data Computer.
9 MFD retains engine instrumentation.
9 COM/NAV 1 fields flag invalid.
9 TAWS
3.16.4 AHRS/ADC Backup Path Test
Secondary AHRS/ADC path check:
1. Remove power from PFD.
2. Remove power from GIA2.
3. Check for desired results.
4. Restore power to the PFD and GIA2.
The following shall occur on the MFD when power is removed from the PFD and GIA2:
9 MFD switches to reversion mode.
9 Attitude and Heading remain valid from AHRS.
9 Airspeed, Altitude, Vertical Speed, and OAT remain valid from Air Data Computer.
9 Engine Instrumentation flags invalid.
9 All COM & NAV fields flag invalid.
G1000 V8.XX S/W Load and Post Install Checkout – Columbia 350/400
190-00577-04
Page 3-43
3.17 Lighting Setup
NOTE
This section is for information only. Lighting data is loaded as part of the configuration upload.
The lighting control system offers excellent configuration capability. During G1000 configuration, default lighting values are loaded. The following is only provided to allow for further refinement of the lighting system as determined by the technician.
3.17.1 Main Lighting Page
PFD, MFD and Audio Panel Lighting Adjustment
Page 3-44
Revision 1
G1000 V8.XX S/W Load and Post Install Checkout – Columbia 350/400
190-00577-04
Keypad Lighting Adjustment
Figure 3-11. Main Lighting Page
Through configuration settings on this main lighting page, G1000 lighting can be setup and adjusted to suit each installation/cockpit environment. Each GDU must be configured for individual performance.
The GMA 1347 audio panel and GCU 475/476 keypad lighting is also controlled from this page. Audio panel lighting is directly tied to display configuration, normally to the PFD (if the PFD fails, the MFD supplies lighting information to the GMA).
DISPLAY/KEY PARAMETERS
A particular unit is selected for setup using the FMS knob. The following parameters apply to both display lighting and key/bezel lighting. The two are divided into separate windows on screen as shown in
Figure 3-3.
INPUT (not active on GCU page): Input level is provided from two photocells on the display (ambient light) or an external avionics dimmer bus voltage. Range is between 0 and 99.99. The higher number indicates a corresponding demand for a brighter display. Input level is shown on the graph as the ‘x’
(horizontal) axis, with a vertical magenta line showing the current input value. The input value is only adjustable by varying the amount of light reaching the photocell or by manipulating the appropriate aircraft dimmer bus, if equipped.
BRIGHTNESS (not active on GCU page): Depicts actual brightness level of the display, shown on the graph as the ‘y’ (vertical) axis with a horizontal yellow line. For any given condition, the brightness is determined by the intersection of the input level and the lighting curve. Range is between 0.0 and 99.99.
SOURCE:
Selection Description
PHOTO
14V DC
28V DC
5V DC
5V AC
Allows the input level to be controlled by ambient lighting sensed from the display’s photocells.
Input level is controlled by 14 Vdc dimmer bus.
Input level is controlled by 28 Vdc dimmer bus.
Input level is controlled by 5 Vdc dimmer bus.
Input level is controlled by 5 V AC dimmer bus.
G1000 V8.XX S/W Load and Post Install Checkout – Columbia 350/400
190-00577-04
Page 3-45
RESPONSE TIME: Adjusts the speed, in seconds, that the brightness level responds to input level (bus voltage or ambient light) changes. Adjustable range is between 0 to 9 seconds. A higher number yields a greater delay in response. For testing purposes it might prove beneficial to set the response time to 0, or a low value, to see immediate reaction to an input stimulus.
MINIMUM: Sets the minimum display brightness. Adjustable range is between 0.14 to 99.99. The higher the number, the greater the minimum brightness. Display brightness will not decrease below the set minimum, regardless of input value or slope. The minimum needs to be set to avoid the input from going too low and experiencing display flicker caused by difficulties of lighting bulbs at low inputs.
EDIT CURVE VERTEX: Selects which point (vertex) on the lighting curve to adjust. See Figure 3-12.
By adjusting the vertices, the lighting curve slope(s) can be adjusted as functions of a single curve. This sets the brightness level for any given input level. When a point is selected for adjustment, the map-panning joystick on the PFD/MFD is used to manipulate the point.
Selection Description
NONE
1
2
3
4
ALL
No vertex point is selected.
The #1 vertex (bottom endpoint of curve) is selected for adjustment. This point cannot be moved in the vertical (y) direction. It is only adjustable in the horizontal (right/left) direction.
The #2 vertex is selected for adjustment.
The #3 vertex is selected for adjustment.
The #4 vertex (top endpoint of curve) is selected for adjustment.
All vertex points are selected for adjustment. Movement is only allowed within each respective bound of a vertex (vertex #1, the curve starting point, can not move vertically).
The most pronounced resultant movements would be a step or trough shaped curve.
Brightness Level Follows
Lighting Curve/Input Level Intersection
#3 Vertex
#4 Vertex (Maximum)
Selected Vertex Points Are
Adjusted Using the Map-Panning
Joystick
Intersection of Input Level,
Lighting Curve, and Brightness Level
#2 Vertex
Input Level Line
(Photocell or
Dimmer Bus Input)
#1 Vertex (Minimum)
Minimum Brightness
(Red Line)
Figure 3-12. Lighting Curve Vertices
3.17.1.1 GMA ANNUNCIATOR PARAMETERS (arrow lights above keys)
BRIGHTNESS: Depicts actual brightness level of the arrow lights beneath the keys on the GMA. Range is between 0.0 and 99.99.
GAIN: Controls the brightness level of the arrow lights beneath the keys on the GMA. Range is between
0 and 2. Gain is a brightness multiplier and is best suited for small adjustments.
Page 3-46
Revision 1
G1000 V8.XX S/W Load and Post Install Checkout – Columbia 350/400
190-00577-04
OFFSET: Allows an offset control of the brightness level for the arrow lights beneath the keys on the
GMA. Range is between -100 and 100. Offset allows for the largest change in brightness in efforts to match other cockpit lighting.
3.17.1.2 GMA KEY PARAMETERS
BRIGHTNESS: Depicts actual brightness level of the keys on the GMA. Range is between 0.0 and
99.99.
GAIN: Controls the brightness level of the keys on the GMA. Range is between 0 and 2. The gain is a multiplier that lends itself best to small adjustments, mainly used for tweaking the brightness.
OFFSET: Allows an offset control of the brightness level for the keys on the GMA. Range is between
-100 and 100. Offset allows for the largest change in brightness in efforts to match other cockpit lighting.
Figure 3-13. Dimmer Bus Lighting
When the lighting input source is set to use dimmer bus voltage (14 Vdc, 28 Vdc, 5 Vdc, 5 V AC), installers can set a transition point where the display switches from using dimmer bus voltage to using the photocell (see Figure 3-13). The light green curve represents the selected input. If something other than photo input is used, the light-green curve will represent that input, while the dark-green input will represent the photo input.
PHOTO TRANSITION %: Sets the input level point at which the display transitions from using the photocell to dimmer bus. At input levels greater than the transition point, the display uses the dimmer bus. At input levels less than the transition point, the display uses the photocell. Should the installer desire to completely operate the display entirely on dimmer bus voltage, the transition point should be set to 0.0. This allows the brightness to track the full range of the dimmer bus voltage from the maximum input value to the minimum value.
EDIT PHOTO CURVE VERTEX: Controls the slopes of the lighting curve used by the photocell when the dimmer bus input level falls below the set transition point. Operation is identical to that of the normal vertex adjustment described above.
3.18 Cockpit Lighting Setup
The following guidance is recommended to help the installer determine a suitable setup. A test flight is recommended upon completion of the setup.
NOTE
To accurately configure the lighting, the ability to adjust ambient light conditions is required. The installer should be prepared to simulating complete darkness in the
G1000 V8.XX S/W Load and Post Install Checkout – Columbia 350/400
190-00577-04
Page 3-47
cockpit. Simply covering the photocells may not allow the installer’s eye to properly judge whether the display brightness is too bright, or too dim, for night use.
Photocell Configuration:
1. It is recommended to start configuration with a linear lighting curve slope (45° Straight Line).
2. Minimize photocell input levels by simulating night conditions in the cockpit. Any other instrument panel or cockpit lighting should be turned on for this adjustment. Seek uniform consistency between display lighting, bezel/key lighting, and any other illuminated objects. a) If a display/keypad is too bright, lower the minimum setting and/or adjust the lighting curve to achieve the desired brightness. b) If the display is not bright enough, raise the minimum setting to the desired brightness. c) In the case of the GMA, adjust gain and offset settings to achieve the desired brightness relative to other lighting.
3. Simulate direct maximum sunlight in the cockpit (best if done outside). a) Verify that the display produces maximum brightness on the graph.
4. Simulate average sunlight conditions in the cockpit (between ~50-75% input level). a) If the display is too bright or too dim, use a combination of lighting curve changes to achieve desired brightness at mid-range lighting input levels. b) Ensure that the lighting curve and minimum setting still maintain the low-light configuration achieved in Step 2. Repeat Step 2 if necessary to re-adjust night lighting settings. c) Adjust the response time to smooth changes to brightness as required.
Dimmer Bus Configuration:
1. Select the appropriate source voltage for the dimmer bus. Set the Photo Transition point to
0.0 for initial dimmer knob calibration.
2. Simulate night conditions in the cockpit. Turn the dimmer bus knob to its minimum setting and observe the graph for corresponding change to the input level. Attempt to seek uniform consistency between display lighting, bezel key lighting, and any other cockpit illuminated information. a) If a display/keypad is too bright, lower the minimum setting and/or adjust the lighting curve to achieve the desired brightness. b) If the display is too dim, increase the minimum setting to achieve desired levels. c) In the case of the GMA, adjust gain and offset settings to achieve the desired brightness relative to other lighting.
3. Simulate direct sunlight conditions in the cockpit. Turn the dimmer bus knob to its maximum setting and observe the graph for a corresponding change to the input level. a) If the brightness is below maximum on the graph, adjust the lighting curve settings to achieve maximum brightness. b) Check for smoothness in the transition from dark to light and adjust the lighting curve and response time settings to achieve desired results.
If desired, set the photocell transition point and associated photo lighting curve to achieve desired display performance over a variety of lighting conditions.
Page 3-48
Revision 1
G1000 V8.XX S/W Load and Post Install Checkout – Columbia 350/400
190-00577-04
3.19 COM Setup Page
The com transceivers in the GIA’s are preset at the factory. The following is only provided to allow for further refinement of the com parameters as determined by the technician.
Figure 3-14. COM Setup Page
SELECT GIA UNIT
This window shows the currently selected GIA 63, which can be selected using the FMS knob.
CALIBRATION
FREQUENCY: Selects a VHF communication frequency. For purposes of setting squelch and sidetone levels, only the frequencies 118.00, 127.00, 136.975 can be used.
NOTE
If a frequency other than 118.00, 127.00 or 136.975 is selected, the values cannot be stored and the STORE softkey is grayed out, indicating that it is unavailable. If one of these three frequencies is selected, and one of the items below is changed, the STORE softkey will no longer be grayed out.
SPACING:
Selection Description
25.0 kHz
8.33 kHz
Selects the traditional 25 kilohertz spacing (760 channel)
Selects 8.33 kilohertz channel spacing, required in certain areas of the world.
SQ 250: Sets the squelch threshold for 25 kHz channel spacing operation. May be set to any value between 0 (zero) and 63. The higher the number, the less signal is required to break squelch.
G1000 V8.XX S/W Load and Post Install Checkout – Columbia 350/400
190-00577-04
Page 3-49
SQ 833: Sets the squelch threshold for 8.33 kHz channel spacing operation. May be set to any value between 0 (zero) and 63. The higher the number, the more signal required to break squelch.
SIDETONE: Sets the sidetone audio output level. May be set to any value between 0 (zero) and 63.
MIC GAIN: Sets the headset microphone gain level. May set to any value between 0 (zero) and 63.
3.20 GMA Configuration Page
The GMA audio panel is configured as part of the G1000 system setup. The following is only provided to allow for further refinement of the marker beacon parameters as determined by the technician. No other settings should be adjusted.
Figure 3-15. GMA Configuration Page
SELECT GMA UNIT
This window shows the currently selected GMA 1347 audio panel.
MARKER BEACON
HI/LO SENSE THRESHOLD: Sets Hi/Lo marker sensitivity thresholds, value is adjustable between –31 and 31. Increasing the value increases the sensitivity of the receiver.
VOLUME: Adjusts marker beacon volume, value is adjustable between –31 and 31. Increasing the value increases the volume level output by the receiver.
Page 3-50
Revision 1
G1000 V8.XX S/W Load and Post Install Checkout – Columbia 350/400
190-00577-04
4 GFC 700 AUTOPILOT GROUND CHECKS
The following procedure will verify the proper operation of the GFC 700 AFCS. This procedure is designed to test the installation of the AFCS only after the G1000 testing in Section 3 has been conducted.
The technician performing these checks must be thoroughly familiar with the GFC 700 by studying the following:
•
•
•
Columbia 400 (G1000) Pilot’s Operating Handbook and FAA Approved AFMS, Columbia P/N
RC050005.
Columbia 350 (G1000) Pilot’s Operating Handbook and FAA Approved AFMS, Columbia P/N
RB050005.
G1000 Cockpit Reference Guide for the Columbia 350/400, Garmin P/N 190-00567-00
CAUTION
When the autopilot is engaged, flight control surface movement can occur.
4.1 Autopilot Pre-Flight Test
NOTE
The autopilot pre-flight test will run on every full airplane power-on.
1. Ensure that the A/P TRIM master switch in the overhead is ON.
2. Open the AUTOPILOT circuit breaker and reset. The AFCS will re-initiate the pre-flight test.
NOTE
A red AFCS ( ) annunciation will be displayed until both GIAs, the
AHRS, and the autopilot servos are online.
3. Verify that a white ‘PFT’ annunciation is displayed on the PFD, as shown in Figure 4-1.
G1000 V8.XX S/W Load and Post Install Checkout – Columbia 350/400
190-00577-04
Page 4-1
Figure 4-1. GFC 700 Pre-Flight Test
4. Upon successful completion of the pre-flight test, an aural alert will sound and the ‘PFT’ annunciation will clear. Continue to Section 4.2.
NOTE
If the ‘PFT’ annunciation turns red, the test has failed and additional troubleshooting will have to be performed prior to continuing with the test.
5. If the aural alert is not heard, but pre-flight testing passed, engage the Autopilot by pressing the
AP key on the MFD and disengage the Autopilot by pressing the AP key again. Visual and aural disconnect alerting should occur. If no alert is heard, the audio interface between GIA No. 1 and the audio panel should be checked. If an alert is heard, the audio interface between GIA No. 2 and the audio panel should be checked.
4.2 AFCS Switch Checks
To verify that the AFCS system buttons and switches are operating correctly, perform the following checks:
1. Actuate the manual electric trim (MET) hat switch forward/aft on the pilot’s control stick. The pitch trim should engage and the run in the selected direction. Check operation in both directions.
2. While actuating the pilot’s MET switch in the pitch axis, press the A/P DISC button on the pilot’s control stick and hold. The pitch trim should stop running and the pitch trim indication should stop moving. The pitch trim will not run for as long as the A/P DISC button is pressed.
3. Release the pilot’s A/P DISC button. The trim should resume running. Release the MET switch.
4. Actuate the MET switch forward/aft on the copilot’s control stick. The pitch trim should engage and the run in the selected direction. Check operation in both directions.
Page 4-2
Revision 1
G1000 V8.XX S/W Load and Post Install Checkout – Columbia 350/400
190-00577-04
advertisement
* Your assessment is very important for improving the workof artificial intelligence, which forms the content of this project
Related manuals
advertisement
Table of contents
- 18 General Information
- 18 Reference Documents
- 18 Post-Installation Procedures Summary
- 18 New Installation Checkout
- 18 Software Reload
- 18 Post Installation Process
- 18 System Description
- 18 G1000 System Communication
- 18 G1000 Control Interface
- 18 FMS Cursor
- 18 Softkeys
- 18 AFCS Controls
- 18 GMA 1347 Control
- 18 Starting Configuration Mode
- 19 Required Test Equipment
- 19 Wiring Harness Checkout
- 19 G1000 Hardware/Software Compatibility Check
- 19 System Installation
- 19 G1000 Software/Configuration Procedure
- 19 System Power Up
- 19 MFD & PFD Software Load
- 19 G1000 System Software Upload
- 19 GIA 63 Boot Block Update
- 19 Software Load Confirmation
- 19 Final Configuration and Setup Items
- 19 Optional System Activation
- 19 Aircraft Registration Number Entry
- 19 TAWS Activation (if installed)
- 19 ChartView (if installed)
- 19 Terrain/Obstacle/SafeTaxi Database Cards
- 19 Aviation Database Loading
- 19 Software/Configuration Troubleshooting
- 19 System Communication Hierarchy
- 66 Aircraft Interface Testing – Configuration Mode
- 66 Discrete Inputs
- 66 Carbon Monoxide Warning System
- 66 WX-500 Stormscope (if installed)
- 66 Ryan TCAD 9900BX (if installed)
- 66 Calibration and Activation
- 66 Aileron and Elevator Trim Calibration
- 66 Fuel Quantity Transducer Calibration
- 66 Initial Display Testing
- 66 GPS Signal Acquisition
- 66 Aircraft Interface Testing – Normal Mode
- 66 CHT Probes
- 66 EGT Probes
- 66 TIT Probes (C400 only)
- 66 Door Open
- 66 Rudder Hold (C400 Only)
- 66 Rudder Limiter (C350 Only)
- 66 Electrical Bus Voltages, Battery Currents and Alert Audio
- 66 Cooling Fans
- 66 Fuel System Discretes
- 66 Lighting
- 66 GMA 1347 Testing
- 66 Intercom System (ICS) Check
- 66 Transceiver Operational Check
- 66 Failsafe Operation Check
- 66 Marker Beacon Test
- 66 GIA 63 Testing
- 66 VHF COM Interference Test
- 66 VOR/LOC/GS Test
- 66 COM Antenna VSWR Checks
- 66 GDL 69 Testing
- 66 GTX 33 Testing
- 66 GDC 74A TESTING
- 66 Pitot/Static Airspeed Test
- 66 Static Port Vertical Speed (Rate of Climb) Test
- 66 OAT Probe Check
- 66 GRS 77/GMU 44 Initial Alignment
- 66 GRS 77 Pitch/Roll Offset Calibration
- 66 Engine Start
- 66 Final GRS 77/GMU 44 Calibration Procedures
- 66 Site Evaluation of Magnetic Disturbances for Magnetometer Calibration Procedure (Optional)
- 66 GRS 77/GMU 44 Magnetic Calibration
- 66 Engine Run-Up Vibration Test
- 66 Magnetometer Interference Test
- 95 Alternator Checks
- 95 Optional System Checkouts
- 95 WX500 Stormscope (if installed)
- 95 9900 BX TCAD (if installed)
- 95 Oxygen System (if installed)
- 95 Final System Checkout
- 95 GPS Failure Test
- 95 GIA Failure Test
- 95 Display Failure Test
- 95 AHRS/ADC Backup Path Test
- 95 Lighting Setup
- 95 Main Lighting Page
- 95 Cockpit Lighting Setup
- 95 COM Setup Page
- 95 GMA Configuration Page
- 96 Autopilot Pre-Flight Test
- 96 AFCS Switch Checks
- 96 Autopilot Clutch Overpower Check
- 96 Autopilot Disengagement Check
- 96 Manual Electric Trim Check
- 96 Autopilot Operation Checks