Installation Mechanical — EVP . Trane RAUJ-C25, RAUJ-C50, RAUJ-C80, RAUJ-C60, RAUJ-C20, RAUJ-D10, RAUJ-D12, RAUJ-C40, RAUJ-C30
Add to My manuals132 Pages
advertisement
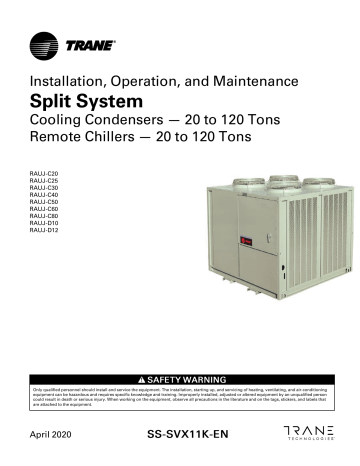
Installation Mechanical — EVP
EVP Chilled Water Piping
Requirements
• Install properly sized chilled water pipe between the
EVP chiller and the supporting equipment. See
Chilled Water Piping section for recommended system components and guidelines.
• Install supply and return water side pressure gauges (with isolation valves.)
• Install thermometers in water supply and return piping.
• Install isolation (shutoff) valves in water supply and return piping.
• Install a properly sized strainer in the supply piping.
• Install blowdown (recommended) valve or plug in strainer cleanout.
• Install a balancing valve in the return piping.
• Install a water flow switch in the return piping.
• Install chilled solution sensor well and sensor in the water outlet piping.
• Install freezestat well and freezestat bulb in the water outlet piping.
• Install chiller piping drain with shutoff valve.
• Install 1/2” x 14 NPT stainless steel or PVC plug in braze plate chiller body.
• Flush the chilled solution piping system, if applicable.
• Connect the chilled solution piping to the chiller.
• The braze plate chiller is intended for indoor application. If a subfreezing location is required, contact Trane for installation precautions required to prevent damage.
• If using an acidic, commercial flushing solution to prevent damage to the internal evaporator components, flush all chilled solution piping before making the final connection to the EVP chiller.
Typical Field-Installed EVP
Chiller Evaporator Piping
BA g--7 pllu gg
BA g--2 he att e prre ve assssa ess..
1. Install the TXV(s) directly to the unit liquid connection. See TXV recommendations in the Tube
Size and Component Selection Application Guide, publication number SS-APG012-EN.
ap orra ap orra ed ucce
2. Locate TXV bulb on top of the suction line 12” from the heat exchanger outlet.
3. Secure the bulb to the suction line with two clamps provided by the manufacturer and insulate the bulb.
4. Locate liquid line solenoid valve(s) near TXV.
5. Install the Frostat™ according to instructions enclosed in the kit as close to the evaporator as possible.
TXV for Remote Chiller
Piping between TXV and Chiller, a braze plate heat exchanger (BPHE), must be 8-12” long and same size as BPHE inlet ID. Field supplied reducer(s) may be required at TXV. A bleed port valve is not required with brazed plate heat exchanger applications.
• Install reducers at the TXV outlet only.
• See Dimensions and Weights chapter for
BPHE inlet dimensions.
• See Expansion Valve Selection tables in the
Installation Mechanical chapter for valve selections.
SS-SVX11K-EN 55
Figure 39.
EVP chiller, typical refrigerant piping
(2 circuit system)
Gauge Ports &
Superheat
Adjustment Port
#1 Suction Line
#2 Suction Line
The minimum and maximum water flow rates are given in the General Data section. Water flow rates below the tabulated values will result in laminar flow causing freeze-up problems, scaling, stratification and poor system control. Flow rates exceeding the maximum listed could result in very high pressure drop, erosion of the heat exchanger and damage to the water flow switch.
Water Temperature Limits
#1 Liquid Line
Charging Ports
Expansion Valve
Moisture Indicator
Solenoid Valve
(Migration only)
Refrigerant “Shut Off” Valve
#2 Liquid Line
Remote EVP Chiller
Water Treatment
he att e an ellss..
ezziin g iin ag e ffrro d rru pttu d w atte an y,, iiss rre eq uiip
The use of untreated or improperly treated water could result in scaling, erosion, corrosion, and algae or slime buildup in the heat exchanger. This will adversely affect system capacity. Proper water treatment must be determined locally and depends on the type of system and local water characteristics. Neither salt nor brackish water is recommend, use of either will lead to a shortened heat exchanger life. Trane encourages employment of a qualified water treatment specialist, familiar with local water conditions, to assist in the establishment of a proper water treatment program.
Water Flow Limits
56 an d//o yo nd ess a bo da ma
Catalog chiller performance data is based on a water temperature drop of 10°F . Full load chilled water temperature drops from 8 to 14°F may be used as long as minimum and maximum water temperature and minimum and maximum flow rates are not violated.
Leaving water temperatures below 42°F require freeze protection down to 15°F. The maximum water temperature that can be circulated through the chiller when the unit is not operating is 125°F. Evaporator damage could result above this temperature.
Short Water Loops
Adequate chilled water system water volume is an important system design parameter because it provides for stable chilled water temperature control and helps limit unacceptable short cycling of chiller compressors. Typically, a five-minute water loop circulation time is sufficient to prevent short water loop issues. Therefore, as a guideline, ensure the volume of water in the chilled water loop equals or exceeds five times the evaporator flow rate. For systems with a rapidly changing load profile the amount of volume should be increased.
SS-SVX11K-EN
possible to maintain constant water flow through the water loop.
Chilled Water Piping
Typical Water Piping
Figure below illustrates typical water piping components for remote chiller applications. (Remote
Figure 40.
EVP chiller — typical water piping
Pipe Connections
Water Strainer
Air Vents
Chiller accessory kit includes strainer, water flow switch, pipe stubs, couplings, evaporator insulation and mounting legs, and a ship separate braze plate heat exchanger.)
Supply Line Outlet
Flow Switch
Air Vents
Shutoff Valves
Unions
Vibration Eliminators
Balancing Valve
Gate Valves
Pressure Gauge
Unions
Vibration Eliminators
Thermometers
Gate Valves
Return Line (Inlet)
(See Note 1)
Supply Line Outlet
• Shutoff valves are required for evaporator servicing.
• Evaporator is shown for illustration purposes only.
• Water inlet, outlet diameter dimensional locations depend on unit size.
• Water connections at the evaporator are grooved.
• Field supplied 1/2” x 14 NPTE stainless steel or PVC plug required.
• Locate freezestat and discharge temperature sensors close to the water outlet.
• Install drain with shutoff valve at low point in leaving piping before system valve.
Foreign matter in the chilled water system will increase pressure drop and reduce water flow. Installation of a properly selected strainer is also necessary to prevent debris larger than 0.039” from entering the heat exchanger. All building piping must be thoroughly flushed before making the final piping connections to the heat exchanger. The strainer must also be cleaned prior to initial start-up.
risks plugging chiller with debris and reducing capacity.
To reduce heat loss and prevent condensation, insulation should be applied to piping. Expansion tanks are also usually required to accommodate chilled water volume changes.
SS-SVX11K-EN 57
Braze Plate (BPHE) Chiller
Evaporator water inlet and outlet types, sizes and locations are shown in drawings in Dimensions and
Weights chapter. Installation of a field provided 1/2” x
14 NPTE stainless steel or PVC plug is required.
Strainer
Install a strainer in the water supply line to protect the chiller from plugging with system piping debris.
Table 17.
Chiller water pressure drop, Ft H2O
Flow
(GPM)
120
140
160
180
200
240
70
80
90
100
280
320
360
400
25
30
35
40
45
50
60
20
3.7
5.2
6.9
8.8
10.9
13.3
18.5
24.6
25
3.2
4.2
5.4
6.7
8.2
11.4
15.2
19.4
24.1
Chilled Water Flow Switch
30
8.9
11.4
14.2
17.3
3.1
3.9
4.8
6.7
40
5.3
7.5
10.1
13.0
16.3
19.9
28.3
10.9
15.4
20.7
26.7
4.1
5.5
7.1
8.9
Strainers should be installed as close as practical to the heat exchanger water inlet (the remote chiller accessory kit includes strainer and piping to connect with BPHE). A field provided blow down valve
(recommended) or plug must be installed in strainer cleanout if not present.
Size, Tons
50 60
5.0
6.3
7.7
10.9
14.6
18.9
23.6
80
4.3
6.1
8.2
10.6
13.2
16.2
22.9
100
3.2
4.4
5.6
7.1
8.7
12.3
16.5
21.3
26.7
120
4.8
6.1
7.4
10.6
14.2
18.3
23.0
28.2
ap orra an d//o yo nd he att e de ow
58 SS-SVX11K-EN
Figure 41.
Optional flow switch
3-1/4”
1-5/8”
1/2” NPT
4-7/8”
1-15/16”
Hex
1” NPT
3-1/2”
1-1/8”
Install a flow switch or other flow sensing device to prevent or stop the compressor operation if the water flow drops below minimum limits. Locate the device in the chilled water return line as shown
.
Install per switch manufacturer’s instructions and refer to the field wiring and unit schematics for the flow switch electrical interlock connections. Adjust switch trip point to prevent operation below minimum limits.
The water flow switch included in the EVP chiller accessory kit must be adjusted to prevent flow below the minimum limit. To set the flow limit:
1. Establish minimum water flow.
2. Rotate the flow switch adjustment screw until the switch opens. This gets close to the correct setting but final adjustment must be done without water flow.
3. Beginning from water off, start flow and adjust
GPM until the switch trips. If flow rate is below minimum, stop water flow and rotate adjusting screw accordingly.
4. Repeat until the switch trips at or above minimum flow.
table to determine water flow rate. See General
Data for minimum flow limits.
Air Vents
Vents must be installed at high points in the piping system to facilitate air purging during the filling process. Air vents between the system shut off valve and heat exchanger are also useful for EVP chiller service and shutdown.
Water Pressure Gauges
Install pressure gauge(s) to monitor the entering and leaving chilled water pressure, and strainer condition.
Water Shutoff Valves
Provide shutoff valves in the "Supply" and "Return" pipe near the chiller so the gauge(s), thermostats, sensors, strainer, etc., can be isolated during service.
Pipe Unions
Use pipe unions to simplify disassembly for system service. Use vibration eliminators to prevent transmitting vibrations through the water lines.
Thermometers
Install thermometers in the lines to monitor the evaporator entering and leaving water temperatures.
Balancing Valves
Install a balancing cock (valve) in the leaving water line.
It will be used to establish a balanced flow.
have shutoff valves installed to isolate the evaporator for service.
Chiller Drain
Drain piping, with shut off valve, must be installed at the lowest point between the chiller and system piping valves to allow water removal for service and shut down procedures. The drain must be piped to a suitable facility.
system with water.
Water Temperature Sensor
The temperature sensor and sensor well must be installed in the leaving water piping as close to the chiller as possible. Both devices are located inside the remote panel. Thermal paste is also provided inside the remote panel and must be used when installing the sensor into the sensor-well.
da ag
Figure below illustrates the sensor well dimensions.
SS-SVX11K-EN 59
Figure 42.
Freezestat bulbwell, temperature sensor and well
Bushing
Freezestat (6S12) Bulbwell
Set Screw
1/2” NPT Adapter
3/8”
1/4” 1-13/16” 2-13/16”
Temperature Sensor Bulbwell
1/2” NPT chiller as possible. It should be located upstream of the temperature sensor location. The freezestat, located within the remote panel, is equipped with a remote sensing bulb and 20 feet of capillary tube. The remote sensing bulb must be installed by the installing personnel. Thermal paste is also provided inside the remote panel and must be used when installing the bulb into the bulb-well. Figure above illustrates the bulbwell dimensions.
piping to avoid vibration transmission.
Insulate all water piping. Use appropriate pipe sealant on all threaded connections.
Final Water Piping Connections
1. Flush all water piping in the system thoroughly before making the final connections.
3/8”
1”
Insulation
Length
3-1/4”
Insertion Length
Temperature Sensor
2-5/8”
Freezestat
A bulbwell (located inside the remote panel) must be installed in the leaving water piping as close to the he att e by assss tth
2. Clean strainer.
3. Connect the water pipe to the EVP chiller.
4. Make sure the 1/2” x 14 NPTE plug is installed.
5. Close the drain shutoff valve.
6. While filling the chiller system with solution, vent the air from the system at the highest points.
60 SS-SVX11K-EN
advertisement
Related manuals
advertisement
Table of contents
- 7 Model Number Description
- 7 20 to 60 Ton Units
- 8 80 to 120 Ton Units
- 9 General Information
- 9 Unit Inspection
- 9 Exterior Inspection
- 9 Inspection for Concealed Damage
- 9 Repair
- 9 Nameplates
- 9 Unit Nameplate
- 9 Compressor Nameplate
- 9 EVP Chiller — Applications Only
- 9 Unit Protection
- 9 Phase Monitor (1U3)
- 10 Manual Motor Protectors (380V through 575V Only)
- 10 Discharge Line Thermostat
- 10 Unit Description
- 12 General Data
- 14 Dimensions and Weights
- 14 Unit Clearances
- 16 Unit Dimensions
- 39 Unit Weights
- 40 Installation Mechanical
- 40 Location Requirements
- 40 Isolation
- 40 Foundation
- 40 Ground Level Installation
- 40 Rooftop Applications
- 40 Leveling the Unit
- 40 Rigging and Lifting
- 43 Unit Mounting
- 44 Unit Isolation
- 44 Neoprene Isolators (20 to 60 Ton units)
- 45 Spring Isolators (20 to 120 Ton units)
- 46 Installation
- 46 General Unit Requirements
- 46 Refrigerant Piping Requirements
- 46 Refrigerant Piping Components
- 47 Suction Line Components
- 47 Liquid Line Components
- 49 Refrigerant Piping
- 50 Suction Line Piping
- 50 Liquid Line Piping
- 51 Typical Field-Installed Evaporator Piping: Dual-Circuit Examples
- 52 Hot Gas Bypass for Commercial Comfort-Cooling Applications
- 52 Optional Pressure Gauges
- 53 Final Refrigerant Pipe Connections
- 53 Brazing Procedures
- 54 Leak Testing Procedure
- 55 Installation Mechanical — EVP
- 55 EVP Chilled Water Piping Requirements
- 55 TXV for Remote Chiller
- 55 Typical Field-Installed EVP Chiller Evaporator Piping
- 56 Remote EVP Chiller
- 56 Water Treatment
- 56 Water Flow Limits
- 56 Water Temperature Limits
- 56 Short Water Loops
- 57 Chilled Water Piping
- 57 Typical Water Piping
- 58 Braze Plate (BPHE) Chiller
- 58 Strainer
- 58 Chilled Water Flow Switch
- 59 Air Vents
- 59 Water Pressure Gauges
- 59 Water Shutoff Valves
- 59 Pipe Unions
- 59 Thermometers
- 59 Balancing Valves
- 59 Chiller Drain
- 59 Water Temperature Sensor
- 60 Freezestat
- 60 Final Water Piping Connections
- 61 Installation Electrical
- 61 Electrical
- 63 Wiring Requirements
- 63 Main Electrical Power Requirements
- 63 Field Installed Control Wiring Requirements
- 63 115 Volt Control Wiring (All Units)
- 63 “No Controls” Units
- 63 EVP Chiller Units
- 64 Low Voltage Wiring (AC & DC)
- 64 Variable Air Volume (VAV) Units
- 64 Constant Volume Units
- 64 EVP Chillers
- 64 Field Installed Power Wiring
- 65 Disconnect Switch External Handle (Factory Mounted Option)
- 65 Main Unit Power Wiring
- 66 Power Wire Sizing and Protection Devices
- 66 Field Installed Control Wiring
- 67 Controls Wiring — 115 VAC
- 67 Controls Wiring — 24 VAC
- 68 Controls — DC Analog Input/Outputs
- 68 Economizer Actuator Circuit
- 70 No System Control
- 74 Variable Air Volume Control(Honeywell W7100A)
- 77 Discharge Air Sensor (Honeywell 6RT3 or Honeywell 8RT3)
- 77 Suction Line Thermostat
- 78 Night Setback
- 78 W7100G Discharge Chilled Water Controller
- 78 Outside Air Thermostat(5S57 Field Provided)
- 78 Constant Volume Control(Honeywell W973) — 20 - 60 Ton Units Only
- 79 Electronic Zone Thermostat (Honeywell T7067)
- 81 Thermostat Checkout
- 81 Discharge Air Sensor (Honeywell 6RT1)
- 82 EVP Chiller Control
- 86 Operating Principles
- 86 Component Locations
- 86 Condenser Fans
- 87 Compressors
- 88 Compressor Junction Box
- 89 Unit Operation
- 89 VAV W7100A Discharge Air Controller (7U11)
- 90 Economizer Cycle
- 90 Chilled Water Temperature Controller (6U11)
- 91 Thermostatic Expansion Valve
- 91 Condenser Fans
- 91 20 to 60 Ton Specs
- 92 80 to 120 Ton Specs
- 92 Low Ambient Dampers
- 92 Compressor Crankcase Heaters
- 93 Low Ambient Thermostats
- 93 20 to 60 Ton Units
- 93 Hot Gas Bypass Operation
- 94 Pre-Start
- 94 EVP Chiller Applications
- 94 System Evacuation Procedures
- 95 Standing Vacuum Test
- 96 Discharge Air Controller Checkout (Honeywell W7100A)
- 98 Discharge Air Sensor Checkout (Honeywell Sensor)
- 98 Economizer Actuator Checkout
- 99 EVP Chiller Control Checkout (Honeywell W7100G)
- 100 Chilled Water Sensor Checkout (Honeywell Sensor)
- 101 Master Energy Control Checkout
- 102 Zone Thermostat Checkout (Honeywell T7067)
- 102 Discharge Air Sensor Checkout (Honeywell 6RT1)
- 104 Voltage Imbalance
- 104 Electrical Phasing
- 105 Start-Up
- 105 Low Ambient Damper Adjustment (Factory or Field Installed)
- 105 EVP Chiller Applications
- 105 Freezestat Setting
- 105 “Air Over” Evaporator Application
- 105 Verifying Proper Supply Fan Rotation
- 106 System Airflow Measurement
- 106 Measuring Airflow
- 106 Alternate Method
- 107 Preliminary Expansion Valve Adjustment
- 108 Adding Preliminary Charge
- 109 Compressor Start-Up(All Systems)
- 112 Motors Rotating Backward
- 112 All Motors are Rotating Backward
- 113 Some Motors are Rotating Backward
- 113 Subcooling
- 113 Measuring Subcooling
- 113 Measuring Superheat
- 113 Compressor Oil
- 113 Compressor Crankcase Heaters
- 114 Compressor Sequencing
- 114 Pressure Curves
- 116 Final System Setup
- 119 Maintenance
- 119 Monthly Maintenance
- 119 Air Handling Equipment
- 119 Condensing Unit
- 120 Coil Cleaning
- 120 Microchannel Condenser Coil Repair and Replacement
- 120 EVP Remote Evaporator Chiller
- 120 Water Strainer Maintenance
- 121 EVP Evaporator Replacement
- 121 Water Loop
- 121 Scroll Compressor
- 121 Operational Sounds
- 121 Shutdown
- 121 Low Ambient Start-Up
- 121 Failure Diagnosis and Replacement
- 121 Refrigerant Evacuation and Charging
- 122 Compressor Replacement
- 122 CSHD Compressors (20 to 60 Ton)
- 122 CSHN Compressors (80 to 120T)
- 123 Electrical Phasing
- 123 Precision Suction Restrictor
- 123 Compressor Circuit Breakers
- 125 Suction Line Filter
- 125 Fuse Replacement Data
- 126 Fall Restraint — Condenser Roof
- 127 Warranty and Liability Clause
- 127 Commercial Equipment Rated 20 Tons and Larger and Related Accessories
- 127 Products Covered
- 128 Wiring Diagrams