advertisement
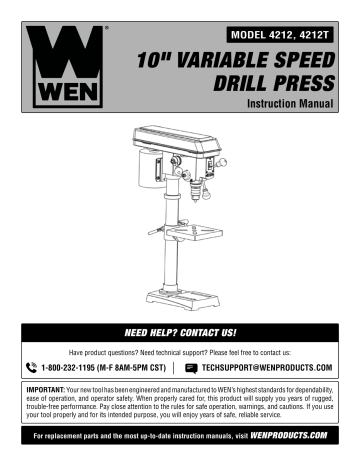
ASSEMBLY & ADJUSTMENTS
UNPACKING
With the help of a friend or trustworthy foe, carefully remove the drill press from the packaging. Make sure to take out all contents and accessories. Do not discard the packaging until the drill press is completely assembled.
Before using the drill press, you must assemble the unit using the instructions in this section. Check your packing list against the diagram below. If any part is damaged or missing, please contact our customer service at (800) 232-1195, M-F 8-5 CST or email us at [email protected].
CLEANING THE WORK TABLE SURFACE
Your drill press comes protected with a layer of anti-rust coating on its exposed (non-painted) metal surfaces, Clean the rust-protected surfaces using a soft cloth, moistened with kerosene. Do not use gasoline, or cellulose-based solvents such as paint thinner or lacquer thinner, as these will damage the painted surfaces. After cleaning, apply a light coat of good-quality paste wax to the table and column to prevent rust. Wipe all parts thoroughly with a clean, dry cloth.
PACKING LIST
Check your packing list against the diagram below. If any part is damaged or missing, please contact our customer service at (800) 232-1195, M-F 8-5 CST or email us at [email protected] and DO NOT plug the drill press in or turn ON.
Tools needed for assembly (not included):
• Adjustable wrench • Hammer and block of wood, or rubber mallet, or dead-blow hammer
14
3
13
1 2 4 5
10
6 7 8 9 10
1.
2.
3.
4.
5.
Head / Motor Assembly
Base
Table Locking Handle
Table Assembly
Table Adjustment
Handle
6.
7.
8.
9.
10.
AA Batteries (2)
Chuck
Chuck Key
Speed Adjustment
Handle
Feed Handles (3)
11 12
11.
12.
13.
14.
Hex Wrenches (3)
Socket Head Cap Screws (4)
Column Assembly
8mm Washers (4)
ASSEMBLY & ADJUSTMENTS
WARNING: Do not plug in or turn on the tool until it is fully assembled according on the instructions. Failure to follow the safety instructions may result in serious personal injury.
ATTACHING COLUMN TO BASE (FIG. 3)
1. Place the column tube (Fig. 3 - 1) on the base (Fig. 3 - 2), aligning the column support holes to the base holes.
2. Install a hex head bolt (Fig. 3 - 3) in each column support hole and tighten bolts using an adjustable wrench (not included).
ATTACHING TABLE TO COLUMN (FIG. 4)
1. Loosen the set screw (Fig. 4 - 4) in the rack collar (Fig. 4 - 5) and remove the collar from the column.
2. Remove the rack (Fig. 4 - 6) from the column (Fig. 4 - 7).
3. Insert the worm shaft (Fig. 4 - 8) into the hole of the table support crank handle (Fig. 4 - 9) from inside the table support.
The worm shaft should extend outside the housing about 1"
(25 mm).
4. Insert the rack (Fig. 4 - 6) into the geared groove of the table support (Fig. 4 - 9). Make sure the worm shaft (Fig. 4 - 8) on the inside of the table support is engaged with the teeth of the rack. The table support should sit at the center of the rack.
5. Slide the table support and rack assembly (Fig. 5 - 6, 5 - 8, and 5 - 9) down together onto the column. Insert the bottom edge of the rack into the lip (Fig. 5 - 10) of the column support.
Hold in this position until step 6 is complete.
6. Place the collar (Fig. 4 - 5) bevel side down over the rack.
Tighten the set screw (Fig. 4 - 4) with the 3 mm hex wrench to hold the rack in position.
NOTE: Make sure there is enough clearance to allow the table to rotate around the column. To avoid column or collar damage, only tighten the set screw enough to keep collar in place.
7. Insert the table support crank handle (Fig. 6 - 12) into the worm gear shaft on the side of the table support (Fig. 6 - 11).
Make sure the set screw (Fig. 6 - 13) is aligned on the flat of the shaft and as close to the table support as possible. Tighten the set screw.
8. Position the table in the same direction as the base, and tighten the column lock handle (Fig. 6 - 14).
14
1
3
4
5
6
7
6
8
9
10
2
Fig. 3
8
9
Fig. 4
Fig. 5
12
13
11
Fig. 6
11
12
ASSEMBLY & ADJUSTMENTS
DRILL PRESS HEAD TO COLUMN (FIG. 7)
CAUTION: The drill press head is heavy. To avoid injury, two people should lift it into position.
1. Carefully lift the drill press head assembly (Fig. 7 - 1) and position it over the column (Fig. 7 - 2).
2. Place the mounting opening on the drill press head over the top of the column. Make sure the drill press head is seated properly on the column.
3. Align the direction of the drill press head with the direction of the base and the table.
4. Tighten the set screws (Fig. 7 - 3) using a hex wrench.
FEED HANDLES (FIG. 8)
1. Insert the three speed handles (Fig. 8 - 4) into the threaded openings on the feed hub (Fig. 8 - 5).
2. Manually tighten the handles into the openings.
NOTE: When using the drill press, one or two of the feed handles may be removed if an unusually-shaped workpiece interferes with the handle rotation.
SPEED HANDLE (FIG. 9)
1. Insert the speed handle (Fig. 9 - 6) into the threaded opening on the speed hub (Fig. 9 - 7).
2. Manually tighten the handle into the opening.
MOUNTING THE DRILL PRESS (FIG. 10)
The drill press must be securely fastened through the mounting holes (Fig. 10 - 8) to a stand or workbench with heavy-duty fasteners (not included). This will prevent the drill press from tipping over, sliding, or walking during operation.
IMPORTANT: If the stand or workbench has a tendency to move during operation, fasten the workbench securely to the floor.
4
5
2
Fig. 8
7
6
Fig. 9
8
8
Fig. 10
1
3
3
Fig. 7
ASSEMBLY & ADJUSTMENTS
INSTALL THE CHUCK (FIG. 11)
1. Inspect and clean the taper hole in the chuck and the spindle. Remove all grease, coatings, and particles from the chuck and chuck arbor surfaces with a clean cloth.
2. Open the chuck jaws by manually turning the chuck barrel clockwise. Make sure the jaws are completely recessed inside the chuck.
3. Seat the chuck on the chuck arbor by placing a block of wood (not included) under the chuck and tapping the wood with a hammer (not included). Alternatively, tap the chuck with a rubber mallet (not included). Pull firmly down on the chuck to ensure it is properly seated on the spindle. If it comes loose, clean the tapers and repeat steps 1-3 until the chuck is properly seated.
CAUTION: To avoid damaging the chuck, make sure the jaws are completely recessed into the chuck. Do not use a metal hammer to drive the chuck into the spindle.
REMOVE THE CHUCK
1. Turn the feed handles to lower the chuck to the lowest position.
1
Spindle
Chuck
Fig. 11
2
Fig. 12
2. Place a ball joint separator above the chuck and tap it lightly with a hammer to cause the chuck to drop from the spindle. Alternately, you may use a set of #6 Jacobs wedges (sold serperately).
NOTE: Be prepared to catch chuck as it falls, or place a cloth on the table to avoid damage to the table or chuck.
RAISE AND LOWER THE TABLE (FIG. 12)
1. Loosen the support lock handle (Fig. 12 - 1) and turn the crank handle (Fig. 12 - 2) until the table is at the desired height.
2. Tighten the support lock handle before drilling.
ROTATE THE TABLE (FIG. 12)
1. Loosen the support lock handle (Fig. 12 - 1) and turn the table around the column to the desired position.
NOTE: The rack should rotate around the column with the table support bracket. If the rack binds and does not rotate, slightly loosen the set screw in the rack collar.
2. Tighten the support lock before drilling.
13
14
ASSEMBLY & ADJUSTMENTS
TILT THE TABLE (FIG. 13)
1. Loosen the bevel lock bolt (under table) with a suitable socket or wrench (not included).
2. Tilt the table to the desired angle, using the bevel scale (1) as a basic guide.
1
3. Re-tighten the bevel lock bolt.
4. To return the table to its original horizontal position, loosen the bevel lock bolt.
Fig. 13
5. Realign the table to the 0° setting on the bevel scale.
6. Tighten the bevel lock bolt with the wrench.
WARNING: Make sure the chuck key is removed from the chuck before starting any drilling operation.
INSTALLING A DRILL BIT
1. Place the chuck key into the side keyhole of the chuck, meshing the key with the gear teeth.
2. Turn the chuck key counterclockwise to open the chuck jaws on the bit shank.
3. Insert a drill bit into the chuck far enough to obtain the maximum grip of the chuck jaws.
4. Center the drill bit in the chuck jaws before the final tightening of the chuck.
5. Tighten the chuck jaws using the chuck key to ensure that the drill bit will not slip while drilling. Tighten all three holes on the chuck to ensure maximum grip on the bit.
6. Remove the chuck key.
ASSEMBLY & ADJUSTMENTS
SQUARING THE TABLE TO THE DRILL BIT (FIG. 14)
1. Insert a 3" drill bit (Fig. 14-1) into the chuck (Fig. 14-2) and tighten.
2. Raise and lock the table (Fig. 14 - 3) about 1" from the end of the drill bit.
3. Place a combination square (Fig. 14 - 4) on the table as shown.
The drill bit should be parallel to the straight edge of the square.
4. If an adjustment is needed, loosen the bevel lock (Fig. 14 - 5) with a wrench.
5. Square the table to the bit by tilting the table.
6. Tighten the bevel lock bolt (Fig. 14 - 5) when square.
2
3
1
5
4
Fig. 14
WARNING: Do not stare directly at the laser beam. Observe all safety rules.
• Never aim the beam at a person or an object other than the workpiece.
• Always make sure the laser beam is aimed at a workpiece that does not have reflective surfaces, as the laser beam could reflect into your eyes or the eyes of others.
ADJUSTING THE LASER (FIG. 15)
1. Place a workpiece on the table.
1
2. Turn the laser switch to the ON position. 2
3. Lower the drill bit to meet the workpiece. The two laser lines should cross where the drill meets the workpiece.
Fig. 15
4. If the laser needs to be adjusted: a) Using a 3 mm hex key, turn the laser adjustment screws (Fig. 15 - 1) counterclockwise. b) Rotate the laser light housing (Fig. 15 - 2) until the two laser lines intersect where the drill meets
the workpiece. DO NOT stare directly at the laser lines.
5. Re-tighten the adjustment set screws (Fig. 15 - 1).
15
16
ASSEMBLY & ADJUSTMENTS
SPINDLE RETURN SPRING (FIG. 16A)
The spindle is equipped with an auto-return mechanism. The main components are a spring and a notched housing. The spring was properly adjusted at the factory and should not be readjusted unless absolutely necessary.
1. Unplug the drill press.
2. Place a screwdriver into the loop (Fig. 16A - 1) to hold the spring in place.
4
2
3
1
Fig. 16A
3. Loosen the two housing nuts (Fig. 16A - 3) approximately 1/4" (6 mm). Do not remove the nuts from the threaded shaft. Do not allow the spring or spring housing to slip out of control.
4. While firmly holding the spring housing (Fig. 16A - 4), carefully pull the spring housing out until it clears the raised notch (Fig. 16A - 2).
5. Turn the housing so that the next notch is engaged with the raised notch (Fig. 16A - 2).
• To increase the spindle return tension, turn the spring housing counter-clockwise.
• To decrease the tension, turn the spring housing clockwise.
6. Tighten the two housing nuts. Do not overtighten the two nuts. If the nuts are tightened too much, the movement of the spindle and feed handles will become sluggish.
ANGULAR “PLAY” OF THE SPINDLE (FIG. 16B)
Move the spindle to the lowest downward position and hold in place. Try to make the spindle revolve around its axis while also moving it with a side motion. If there is too much “play”, proceed as follows:
1. Loosen the lock nut (Fig. 16B - 5).
2. Without obstructing the upward and downward motion of the spindle, turn the screw (Fig. 16B - 6) clockwise to eliminate the “play.” NOTE: A little bit of “play” is normal.
3. Tighten the lock nut (Fig. 16B - 5).
6
5
Fig. 16B
ASSEMBLY & ADJUSTMENTS
DRILL PRESS ON/OFF SWITCH (FIG. 17)
1. To turn the drill press ON, insert the yellow safety key
(Fig. 17-1) into the switch housing (Fig. 17 - 2). As a safety feature, the switch cannot be turned ON without the safety key.
2. Turn the switch to the ON position.
3. To turn the drill press OFF, flip the switch downward.
4. To lock the switch in the OFF position, remove the safety key
(Fig. 17 - 1) from the switch. Store the safety key in a safe place.
CHANGING THE BELT
WARNING: Disconnect the drill press from the power source before replacing the belt.
1
2
Fig. 17
Belt tension and drill press speed is controlled by automatic adjustments made to the diameter of the front spindle when the speed handle is moved.
NOTE: See page 19 for information on the variable speed function of this drill press.
1. Plug in the drill press and turn it ON. Adjust the speed to the highest setting, then turn the drill press
OFF and unplug it.
2. Open the belt cover (remove the Phillips-head screw from the right side, then open the lid.
3. Press down on the bottom side of the motor pulley. This will loosen the belt tension. Work the belt off the pulleys.
4. Place the new belt on the motor pulley, then press down on the bottom side of the pulley as before and get the belt as close to the motor shaft as possible. Make sure the bottom side of the pulley is pushed fully downward.
5. Work the belt around the spindle pulley. The belt will not be taut, but will self-seat later.
6. Close and secure the belt cover.
7. Plug in and turn ON the drill press. The belt will self-seat and achieve proper tension on its own.
WARNING: Do not change the drive speed when the drill press is turned off.
17
advertisement