advertisement
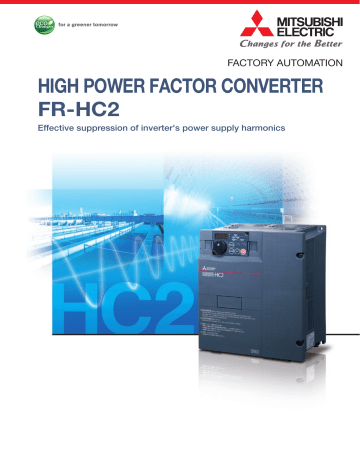
Standard specifications
Standard specification rating
200V
Model name FR-HC2 K
Applicable inverter capacity (kW)
Rated output capacity (kW)
Rated input voltage (V)
Rated input current (A)
Overload current rating
Permissible power supply voltage fluctuation
Permissible power supply frequency fluctuation
Input power factor
Power supply capacity (kVA)
Protective structure of the converter
Cooling system
7.5
15 30 55 75
7.5
15 30 55 75
10.7
33
19.8
38 71 92
Three-phase 200V to 220V 50Hz/200V to 230V 60Hz
61 115 215
150% 60s
170V to 242V 50Hz
278
170V to 230V
170V to 253V 60Hz 50Hz/60Hz
14
0.99 or more (when load ratio is 100%)
25
Enclosed type (IP20)
47 88
Open type (IP00)
7 12
5%
Forced air cooling
24 39
110
53
400V
Model name FR-HC2-H
7.5
15 30 55 75 110 160 220 280
Applicable inverter capacity (kW)
Rated output capacity (kW)
Rated input voltage (V)
Rated input current (A)
Overload current rating
Permissible power supply voltage fluctuation
Permissible power supply frequency fluctuation
Input power factor
Power supply capacity (kVA)
Protective structure of the converter
Cooling system
7.5
11.0
17
14 26
Enclosed type
(IP20)
9
15
20.2
31
30
37
57
323V to 506V 50/60Hz
55 75 110 160 220
73 92 135 192 264
Three-phase 380V to 460V 50Hz/60Hz
110 139 203 290 397
150% 60s
280
336
506
323V to 460V 50/60Hz
9
47
26
0.99 or more (when load ratio is 100%)
90 113 165 235 322
43
5%
Open type (IP00)
Forced air cooling
37 56 120 120
410
160
400
400
476
716
580
560
560
660
993
804
250 250
Model name of the 400V class ends with H.
The permissible voltage imbalance ratio is 3% or less. (Imbalance ratio = (highest voltage between lines - average voltage between three lines) / average voltage between three lines 100).
DC output capacity when the input voltage is 200VAC (400V for the 400V class).
Change the MC power supply stepdown transformer tap according to the input voltage. (Refer to the Instruction Manual)
The % value of the overload current rating indicates the ratio of the overload current to the converter's rated input current. For repeated duty, allow time for the converter and the inverter to return to or below the temperatures under 100% load.
The protective structure is IP40 for FR-DU07-CNV (except the PU connector) and IP00 for the outside box (220K or lower) and the reactor regardless of their capacities.
When the hook of the converter front cover is cut off for installation of the plug-in option, the protective structure changes to the open type (IP00).
Mass of FR-HC2 alone.
7
8
Common specifications
Control method PWM control
Power supply frequency range 50Hz to 60Hz
Current limit level Current limit value selectable (0 to 220% variable)
Input signal (Five terminal)
Output signal
Open collector output
(Five terminals)
Relay output (One terminal)
Operating status
The following signals can be assigned to Pr. 3 to Pr. 7 (input terminal function selection) : converter stop, monitor switching, converter reset, external thermal relay, and inrush resistance overheat detection.
The following signals can be assigned to Pr. 11 to Pr. 16 (output terminal function selection) : inverter run enable signal, converter reset, converter running, overload alarm, power supply phase detection, output voltage match, instantaneous power failure detection, regenerative drive recognition, electronic thermal relay pre-alarm, fan alarm, heatsink overheat pre-alarm, during retry, input current detection, zero current detection,life alarm, maintenance timer, instantaneous power failure detection hold, alarm, and fault output.
For meter
Pulse train output
(Max. 2.4kHz: one terminal)
Analog output
(Max. 10VDC: one terminal)
The following signals can be assigned to output.
Pr. 54 FM terminal function selection (pulse train output)
Pr. 50 AM terminal function selection (analog output) and
: power supply frequency, input current, input voltage, converter output voltage, electronic thermal relay load factor, input power, reference voltage
Operation panel
(FR-DU07-CNV)
Operating status
Power supply frequency, input current, input voltage, fault or alarm indication, converter output voltage, electronic thermal relay load factor, cumulative energization time, cumulative power, input power, input power (with regenerative display), I/O terminal status
, power/regenerative drive indi-
cation, option fitting states
Fault definition is displayed when a fault occurs. Past eight fault records and the data right before the fault (input voltage/current/bus voltage/cumulative energization) are stored.
Parameter unit
(FR-PU07)
Fault record
Interactive guidance
Function (help) for operation guide
Protective/warning function t Surrounding air temperature
Ambient humidity
Storage temperature
Atmosphere
Altitude/ vibration
Protective function
Warning functions
Overcurrent, overvoltage, converter protection thermal, fin overheat, instantaneous power failure, undervoltage, input phase loss, HC2 dedicated board disconnection, input power supply fault, external thermal relay operation
, parameter error, PU disconnection
, retry count excess , converter
CPU fault, operation panel power supply short circuit, 24VDC power output short circuit, input current detection value exceeded
, inrush current limit circuit fault, internal circuit fault, option fault ,
communication option fault
.
Fan alarm, overload signal detection, electronic thermal relay pre-alarm, PU stop, maintenance
, parameter write error, copy operation error, operation panel lock, parameter copy
alarm, no-phase detection
-10 C to +50 C (non-freezing)
90%RH or less (non-condensing)
-20 C to +65 C
Indoors (without corrosive gas, flammable gas, oil mist, dust and dirt etc.)
Maximum 1,000m, 5.9 m/s
2
or less
at 10 to 55Hz (directions of X, Y, Z axes)
Can be displayed only on the operation panel (FR-DU07-CNV).
Can be displayed only on the option parameter unit (FR-PU07).
Temperature applicable for a short time, e.g. in transit.
This protective function is not available in the initial status.
This protective function is enabled when FR-A7NC is mounted.
2.9m/s 2 or less for the 160K or higher.
Checking peripheral devices
Peripheral devices
Always install the included peripheral devices. Check the model name of the each peripheral device.
For the 400V class peripheral devices, H is indicated in front of the model name.
FR-HC2-7.5K to 75K, FR-HC2-H7.5K to H220K
Peripheral Device
Model Name
FR-HC2-(H)
FR-HCL21-(H)
FR-HCL22-(H)
FR-HCB2-(H)
K
K
K
K
Description
High power factor converter
Filter reactor 1
Filter reactor 2
Outside box
Quantity
1
1
1
1
Terminal screws are enclosed for FR-HCB2-7.5K, 15K, FR-HCB2-H7.5K to H30K. (M5 6)
FR-HC2-H280K to H560K
Peripheral Device
Model Name
FR-HC2-H K
FR-HCL21-H K
FR-HCL22-H K
FR-HCC2-H K
Model Name of Consisting Parts
FR-HC2-H K
FR-HCL21-H K
FR-HCL22-H K
FR-HCC2-H K
MDA-1
FR-HCR2-H K
FR-HCM2-H K
0.96OHM BKO-CA1996H21
0.96OHM BKO-CA1996H31
1PH 630VA BKO-CA2001H06
S-N400FXYS AC200V 2A2B
S-N600FXYS AC210V 2A2B
SR-N4FX AC210V 4A
TS-807BXC-5P
C152C481H21
C152C423H21
MYQ4Z AC200/220
PYF14T
PYC-A1
M12 50 ZENNEJI
M12
MIGAKI 12
BANE 12
SW-PW-P-NA M5 12
Description
High power factor converter
Filter reactor 1
Filter reactor 2
Filter capacitor
Filter capacitor alarm detector
Inrush current limit resistor (without thermostat)
Inrush current limit resistor (with thermostat)
MC power supply stepdown transformer
(400V-200V)
Inrush current limit MC
Inrush current limit MC
Buffer relay
Terminal block
Terminal block shorting conductor
MC shorting conductor
Mini relay for filter capacitor alarm detector
Mini relay terminal block
Mini relay clip
MC shorting conductor bolt (M12 50)
MC shorting conductor nut (M12)
MC shorting conductor washer (flat washer)
MC shorting conductor washer (spring washer)
Inrush current limit resistor screw (M5 12)
—
—
—
—
—
—
6
—
—
—
1
6
—
1
Quantity
280K 400K 560K
1
1
1
1
—
1
2
1
1
2
1
3
1
1
3
8
1
1
15
3
1
15
3
1
2
24
24
48
24
54
—
6
1
1
3
—
2
—
2
24
24
48
24
54
—
6
1
1
3
—
2
—
9
10
Selection of the high power factor converter and the inverter
The required converter capacity differs by the multiple rating selection setting of the inverter.
Refer to the following table for the connectable inverter capacities when connecting one inverter to a high power factor converter. (Other combinations are not applicable.)
: Compatible
— : The converter can be used as a common converter or a regenerative converter, but its harmonic suppression effect reduces.
: Not compatible (Not applicable)
When the inverter capacity and the applicable motor capacity are equal (FR-A800 (ND rating), FR-F800
(LD rating), and 700 series inverters)
Inverter capacity
FR-HC2-7.5K
FR-HC2-15K
FR-HC2-30K
FR-HC2-55K
FR-HC2-75K
FR-HC2-H7.5K
FR-HC2-H15K
FR-HC2-H30K
FR-HC2-H55K
FR-HC2-H75K
Inverter capacity
FR-HC2-H110K
FR-HC2-H160K
FR-HC2-H220K
FR-HC2-H280K
FR-HC2-H400K
FR-HC2-H560K
Inverter capacity
FR-HC2-H280K
FR-HC2-H400K
FR-HC2-H560K
2.2K
or lower
—
—
—
—
—
—
—
—
—
—
45K or lower
—
—
—
—
—
—
3.7K
5.5K
7.5K
—
—
—
—
—
—
—
—
55K
—
—
—
—
—
—
—
—
—
—
—
—
—
75K
—
—
—
—
—
—
—
—
—
—
—
90K
—
—
—
—
11K
—
—
—
—
—
—
110K
—
—
—
15K
—
—
—
—
132K
—
—
—
18.5K
—
—
—
—
—
—
160K
22K
—
—
—
—
185K
—
—
30K
—
—
200K
—
37K
220K
—
45K
250K
—
280K 315K 355K 375K 400K 450K 500K 530K 560K
55K
75K
When the applicable motor capacity is higher than the inverter capacity (FR-A800 (LD rating), FR-A800
(SLD rating), and FR-F800 (SLD rating))
Compare the high power factor converter capacity chosen based on the table above and the applicable motor capacity. Then, choose the high power factor converter according to the capacity whichever is higher.
When the applicable motor capacity is lower than the inverter capacity (FR-A800 (HD rating)).
Inverter capacity
FR-HC2-7.5K
FR-HC2-15K
FR-HC2-30K
FR-HC2-55K
FR-HC2-75K
FR-HC2-H7.5K
FR-HC2-H15K
FR-HC2-H30K
FR-HC2-H55K
FR-HC2-H75K
2.2K
or lower
—
—
—
—
—
—
—
—
—
—
3.7K
5.5K
7.5K
—
—
—
—
—
—
—
—
—
—
—
—
—
—
—
—
—
—
—
—
—
—
11K
—
—
—
—
—
—
15K 18.5K
22K
—
—
—
—
—
—
—
—
—
—
—
—
30K
—
—
37K
45K
55K
Inverter capacity
FR-HC2-H110K
FR-HC2-H160K
FR-HC2-H220K
FR-HC2-H280K
FR-HC2-H400K
FR-HC2-H560K
Inverter capacity
FR-HC2-H400K
FR-HC2-H560K
45K or lower
—
—
—
—
—
—
55K
—
—
—
—
—
75K
—
—
—
—
—
90K
—
—
—
—
110K
—
—
—
250K 280K 315K 355K 400K
—
132K
—
—
—
160K
—
—
185K
—
—
220K
—
Inverter parameter settings
When using the high power factor converter with the inverter, the following inverter parameters must be set. The parameter setting differ by the inverter series.
For the parameters and the inverters not listed in the table, refer to the Instruction Manual of the inverter.
Inverter series
Pr.30 Regenerative function selection
V/F control
Pr.19 Base frequency voltage
Other than V/F control
Pr.83 Rated motor voltage
FR-A800, FR-F800 2
FR-E700, FR-F700PJ,
FR-D700
0 (initial value),
2 (automatic restart after instantaneous power failure is enabled)
Rated motor voltage
11
12
Wiring of several inverters to one converter
Up to ten inverters can be connected to one converter. Be sure to use a high power factor converter with the capacity equal to or higher than the total capacity of inverters/motors. Additionally, the total capacity of the inverters or motors needs to be equal to or higher than half the capacity of the high power factor converter. (High power factor converter capacity × 1/2
≤
total capacity of connected inverters or motors
≤
high power factor converter capacity)
If the total inverter capacity is less than half the capacity of the high power factor converter, the converter can be used as a common converter or a regenerative converter. However, its harmonic suppression effect is reduced.
(1) Junction terminals or cross wiring are used to connect several inverters, so carefully select the wire gauge. Start adding the inverter capacities from the furthest inverter.
(2) When connecting several inverters, connect starting with the inverter with the highest capacity.
(3) Installation of a fuse, which corresponds with each motor capacity, is recommended for each inverter when connecting several inverters to one converter. Select a fuse according to the motor capacity.
When using a motor, of which capacity is smaller than the inverter capacity by two ranks or more, select the converter capacity according to the inverter capacity.
(4) Keep the total wiring length within 50m.
Main circuit wiring example
The following diagram shows a connection example of the FR-HCL-55K to six inverters: the FR-A820-01540(30K),
00770(15K), 00340(5.5K), 00167(2.2K), 00105(1.5K), and 00070(0.75K) (54.95 kW capacity in total).
FR-HC2
-55K
P/+
1)
N/-
3)
Junction terminal 1
Fuse
P/+
2)
N/-
Junction terminal 2
P /+
INV1
A820
30K
INV2
30kW
Motor
1st inverter 1) Wire gauge between FR-HC2 and the junction terminal 1 is 100mm 2 according to the FR-HC2 capacity.
2) Wire gauge between the junction terminal 1 and the inverter is 60mm 2 because the inverter capacity is 30K.
15kW
4)
N /-
A820
15K
5)
Junction terminal 3
6)
P/+
N/-
INV3
A820
5.5K
2nd inverter 3) Wire gauge between the junction terminal 1 and junction terminal 2 can be calculated as follows: 15+5.5+2.2+1.5+0.75=24.95K, and 24.95K rounds up to 30K, so the wire gauge is 60mm 2 .
4) The Wire gauge between the junction terminal 2 and the inverter is 22mm 2 because the inverter capacity is 15K.
5.5kW
Motor
7)
Junction terminal 4
8)
P/+
N/-
INV4
A820
2.2K
3rd inverter 5) Wire gauge between the junction terminal 2 and junction terminal 3 can be calculated as follows: 5.5+2.2+1.5+0.75=9.95K, and 9.95K rounds up to
11K, so the wire gauge is 14mm 2 .
6) Wire gauge between the junction terminal 3 and the inverter is 14mm 2 because the inverter capacity is 5.5K.
2.2kW
Motor
9)
Junction terminal 5
10)
P/+
INV5
A820
1.5K
4th inverter 7) Wire gauge between the junction terminal 3 and junction terminal 4 can be calculated as follows: 2.2+1.5+0.75=4.45K, and 4.45 K rounds up to 5.5K, so the wire gauge is 5.5mm
2 .
8) Wire gauge between the junction terminal 4 and the inverter is 2mm 2 because the inverter capacity is 2.2K.
1.5kW
Motor
N/-
11)
Junction terminal 6
INV6
P/+
12)
N/-
A820
0.75K
5th inverter 9) Wire gauge between the junction terminal 4 and junction terminal 5 can be calculated as follows: 1.5+0.75=2.25K, and 2.25K rounds down to
2.2K, so the wire gauge is 2mm 2 .
10) Wire gauge between the junction terminal 5 and the inverter is 2mm 2 because the inverter capacity is 1.5K.
0.75kW
Motor
6th inverter 11) Wire gauge between the junction terminal 5 and junction terminal 6 is
2mm 2 because the inverter capacity is 0.75K.
12) Wire gauge between the junction terminal 6 and the inverter is 2mm 2 because the inverter capacity is 0.75K.
advertisement
Related manuals
advertisement
Table of contents
- 1 FR-HC2 catalog
- 4 Features
- 6 Connection example
- 7 Standard specifications
- 7 Standard specification rating
- 8 Common specifications
- 9 Checking peripheral devices
- 10 Selection of the high power factor converter and the inverter
- 11 Inverter parameter settings
- 12 Wiring of several inverters to one converter
- 13 Outline dimension drawings
- 17 Protruding the heatsink
- 19 Terminal connection diagram (when using with the FR-A800 series)
- 21 Terminal specification explanation
- 23 Parameter list
- 25 Protective functions
- 26 Option and peripheral devices
- 26 Option List
- 26 Peripheral devices/cable size list
- 30 Precaution on selection and operation
- 30 Installation Precautions
- 30 Wiring distance
- 30 Reactor installation at power supply side
- 30 Operating Precautions
- 30 Selection Precautions
- 30 Connectable inverter
- 30 Sine wave filter selection precautions
- 31 Peripheral Device Selection Precautions
- 31 Selection and installation of the moulded case circuit breaker
- 31 Electromagnetic interference
- 33 Warranty