- Home
- Domestic appliances
- Large home appliances
- Water heaters & boilers
- Lennox
- ML196DFE Series Units
- Installation instructions
advertisement
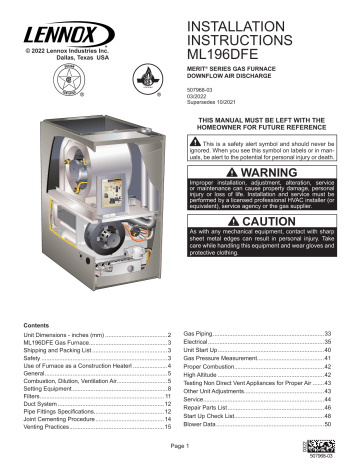
Gas Piping
Gas supply piping should not allow more than 0.5”W.C. drop in pressure between gas meter and unit. Supply gas pipe must not be smaller than unit gas connection.
CAUTION
If a flexible gas connector is required or allowed by the authority that has jurisdiction, black iron pipe shall be installed at the gas valve and extend outside the furnace cabinet. The flexible connector can then be added between the black iron pipe and the gas supply line.
WARNING
Do not over torque (800 in-lbs) or under torque (350 inlbs) when attaching the gas piping to the gas valve.
1 - Gas piping may be routed into the unit through either the left- or right-hand side. Supply piping enters into the gas valve from the side of the valve as shown
in Figure 51. Connect the gas supply piping into the
gas valve. The maximum torque is 800 in lbs and minimum torque is 350 in lbs when when attaching the gas piping to the gas valve.
2 - When connecting gas supply, factors such as length of run, number of fittings and furnace rating must be considered to avoid excessive pressure drop.
TABLE 11 lists recommended pipe sizes for typical
applications.
NOTE - Use two wrenches when connecting gas piping to avoid transferring torque to the manifold.
3 - Gas piping must not run in or through air ducts, clothes chutes, chimneys or gas vents, dumb waiters or elevator shafts. Center gas line through piping hole. Gas line should not touch side of unit. See
4 - Piping should be sloped 1/4 inch per 15 feet (6mm per 5.6m) upward toward the gas meter from the furnace. The piping must be supported at proper intervals, every 8 to 10 feet (2.44 to 3.05m), using suitable hangers or straps. Install a drip leg in vertical pipe runs to serve as a trap for sediment or condensate.
5 - A 1/8” N.P.T. plugged tap or pressure post is located on the gas valve to facilitate test gauge connection.
6 - In some localities, codes may require installation of a manual main shut-off valve and union (furnished by installer) external to the unit. Union must be of the ground joint type.
IMPORTANT
Compounds used on threaded joints of gas piping must be resistant to the actions of liquified petroleum gases.
Leak Check
After gas piping is completed, carefully check all field-in stalled piping connections for gas leaks. Use a commercially available leak detecting solution specifically manu factured for leak detection. Never use an open flame to test for gas leaks.
The furnace must be isolated from the gas supply sys tem by closing the individual manual shut-off valve during any gas supply system at pressures greater than or equal to ½ psig. (3.48 kPa, 14 inches w.c.). This furnace and its components are designed, manufactured and inde pendently certified to comply with all applicable ANSI/CSA standards. A leak check of the furnace and its components is not required.
1/8” N.P.T. PLUGGED TAP
CAP
Figure 50
FURNACE
IMPORTANT
When testing pressure of gas lines, gas valve must be
disconnected and isolated. See Figure 50. Gas valves
can be damaged if subjected to pressures greater than
1/2 psig (3.48 kPa).
WARNING
FIRE OR EXPLOSION HAZARD
Failure to follow the safety warnings exactly could result in serious injury, death, or property damage. Never use an open flame to test for gas leaks. Check all connections using a commercially available soap solution made specifically for leak detection. Some soaps used for leak detection are corrosive to certain metals. Carefully rinse piping thoroughly after leak test has been completed.
Page 33
MANUAL
MAIN SHUT-OFF
VALVE
(1/8 in. NPT plugged tap shown)
Left Side Piping
(Standard)
AUTOMATIC
GAS VALVE
(with manual shut-off valve)
AUTOMATIC
GAS VALVE
(with manual shut-off valve)
MANUAL
MAIN SHUT-OFF
VALVE
(1/8 in. NPT plugged tap shown)
GROUND
JOINT
UNION
GROUND
JOINT
UNION
DRIP LEG
FIELD
PROVIDED
AND INSTALLED
NOTE - BLACK IRON PIPE
ONLY
TO BE ROUTED INSIDE OF CABINET
DRIP LEG
Right Side Piping
(Alternate)
Figure 51
Nominal
Iron Pipe
Size Inches
(mm)
1/2
(12.7)
3/4
(19.05)
1
(25.4)
1-1/4
(31.75)
1-1/2
(38.1)
2
(50.8)
2-1/2
(63.5)
3
(76.2)
Internal
Diameter inches
(mm)
.622
(17.799)
.824
(20.930)
1.049
(26.645)
1.380
(35.052)
1.610
(40.894)
2.067
(52.502)
2.469
(67.713)
3.068
(77.927)
10
(3.048)
172
(4.87)
360
(10.19)
678
(19.19)
1350
(38.22)
2090
(59.18)
4020
(113.83)
6400
(181.22)
11300
(319.98)
20
(6.096)
118
(3.34)
247
(7.000)
466
(13.19)
957
(27.09)
1430
(40.49)
2760
(78.15)
4400
(124.59)
7780
(220.30)
TABLE 11
Gas Pipe Capacity - ft3/hr (m3/hr)
Length of Pipe - feet (m)
30
(9,144)
95
(2.69)
199
(5.63)
374
(10.59)
768
(22.25)
1150
(32.56)
2220
(62.86)
3530
(99.95)
6250
(176.98)
40
(12,192)
81
(2.29)
170
(4.81)
320
(9.06)
657
(18.60)
985
(27.89)
1900
(53.80)
3020
(85.51)
5350
(151.49)
50
(15.240)
72
(2.03)
151
(4.23)
284
(8.04)
583
(16.50)
873
(24.72)
1680
(47.57)
2680
(75.88)
4740
(134.22)
60
(18.288)
65
(1.84)
137
(3.87)
257
(7.27)
528
(14.95)
791
(22.39)
1520
(43.04)
2480
(70.22)
4290
(121.47)
70
(21.336)
60
(1.69)
126
(3.56)
237
(6.71)
486
(13.76)
728
(20.61)
1400
(39.64)
2230
(63.14)
3950
(111.85)
80
(24.384)
NOTE Capacity given in cubic feet (m3 ) of gas per hour and based on 0.60 specific gravity gas.
56
(1.58)
117
(3.31)
220
(6.23)
452
(12.79)
677
(19.17)
1300
(36.81)
2080
(58.89)
3670
(103.92)
90
(27.432)
635
(17.98)
1220
(34.55)
1950
(55.22)
3450
(97.69)
52
(1.47)
110
(3.11)
207
(5.86)
424
(12.00)
100
(30,480)
50
(1.42)
104
(2.94)
195
(5.52)
400
(11.33)
600
(17.00)
1160
(32.844)
1840
(52.10)
3260
(92.31)
Page 34
advertisement
Related manuals
advertisement
Table of contents
- 2 Unit Dimensions - inches (mm)
- 3 ML196DFE Gas Furnace
- 3 Shipping and Packing List
- 3 Safety
- 4 Use of Furnace as a Construction Heaterl
- 5 General
- 5 Combustion, Dilution, Ventilation Air
- 8 Setting Equipment
- 11 Filters
- 12 Duct System
- 14 Joint Cementing Procedure
- 15 Venting Practices
- 33 Gas Piping
- 35 Electrical
- 40 Unit Start Up
- 41 Gas Pressure Measurement
- 42 Proper Combustion
- 42 High Altitude
- 43 Testing Non Direct Vent Appliances for Proper Air
- 43 Other Unit Adjustments
- 44 Service
- 46 Repair Parts List
- 48 Start Up Check List
- 50 Blower Data