- No category
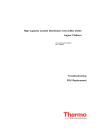
advertisement
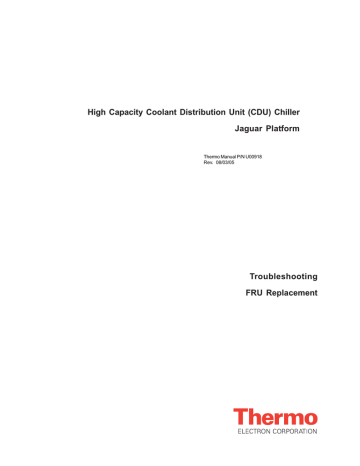
High Capacity Coolant Distribution Unit (CDU) Chiller
Jaguar Platform
Thermo Manual P/N U00918
Rev. 08/03/05
Troubleshooting
FRU Replacement
Table of Contents
Preface
After-sale Support .....................................................................................3
Warranty ..................................................................................................3
Section I Safety
Warnings ..................................................................................................5
EMO Circuit..............................................................................................6
Lockout/Tagout (LOTO) .............................................................................6
Section II Troubleshooting
Error Code Troubleshooting.......................................................................7
VFD Faults ............................................................................................. 21
Monitoring Fluid Loss ............................................................................. 23
Section III FRU List
FRU List ................................................................................................. 25
Section IV FRU Replacement
Electrical Components ........................................................................... 42
Electrical Box Assembly......................................................................... 44
Keypad ................................................................................................... 45
Drier Tube ............................................................................................... 46
Fill Port Screen ...................................................................................... 47
HFE Filter Bag Kit .................................................................................. 48
Pump Inline Drier .................................................................................... 53
Tank Level Switch ................................................................................... 54
Pump ..................................................................................................... 55
Temperature Control Valve Assembly ...................................................... 58
Temperature Control Valve Actuator ........................................................ 60
Water Flow Transducer ........................................................................... 61
HFE Side Temperature Sensor (rtd1) ...................................................... 62
Pressure Transducers ........................................................................... 63
Drip Pan Level Switch Kit ....................................................................... 64
Pressure Regulator ................................................................................. 65
Plumbing, Pressure Regulator to Temperature Control Valve .................. 67
Plumbing, Facility Inlet Pipe ................................................................... 68
H2O Side Temperature Sensor (rtd2) ...................................................... 69
Return Pipe Assembly, Process Flow ..................................................... 70
Supply Pipe Assembly, Process Flow .................................................... 72
PRV Cartridge ........................................................................................ 74
VFD Filter, Contactor, Transformer .......................................................... 75
EMO Thermostat .................................................................................... 76
VFD ........................................................................................................ 77
VFD Settings .......................................................................................... 78
Pump Motor Overloads ........................................................................... 79
Circuit Breaker........................................................................................ 80
Temp Option Board ................................................................................. 81
Chip Replacement .................................................................................. 82
- 1 -
TC-400 Controller .................................................................................... 83
LON Adapter Board ................................................................................. 85
Torque Specification Sheet ...................................................................... 86
Swagelok Tube Fitting Instructions ......................................................... 87
Section V Controller Loops
Main Loop .............................................................................................. 89
Engineering Loop .................................................................................... 90
Factory Reset ......................................................................................... 91
Section VI Drawings
FRU Exploded Views .............................................................................. 92
Flow Diagram ......................................................................................... 95
Electrical Diagram .................................................................................. 96
WARRANTY
- 2 -
Preface
After-sale Support
Thermo Electron Corporation is committed to customer service both during and after the sale. If you have questions concerning the CDU operation, contact our
Sales Department. If your CDU fails to operate properly, or if you have questions concerning spare parts contact our Service Department.
(800) 258-0830
(603) 436-9444
Fax: (603) 436-8411
Before calling, please obtain the following information:
- CDU BOM number
- CDU serial number
- CDU software version
- voltage of power source
The CDUs BOM and serial number label are located on the label on the fronttop of the CDU. See Service Manual for instructions on how to display the software version.
Warranty
CDUs have a warranty against defective parts and workmanship for 24 months from date of shipment. See back pages for more details.
- 3 -
This page intentionally left blank.
- 4 -
Section I Safety
Warnings
DANGER
WARNING
CAUTION
Make sure you read and understand all instructions and safety precautions listed in this manual before installing or operating your CDU. If you have any questions concerning the operation of your CDU or the information in this manual, contact our Sales Department for assistance.
DANGER indicates an imminently hazardous situation which, if not avoided, will result in serious injury or death. This signal word is limited to the most extreme situations.
WARNING indicates a potentially hazardous situation which, if not avoided, could result in serious injury or death.
CAUTION indicates a potentially hazardous situation which, if not avoided, may result in minor or moderate injury. It may also be used to alert against unsafe practices.
Performance of installation, operation, or maintenance procedures other than those described in this manual may result in a hazardous
situation and may void the manufacturers warranty.
Transport the CDU with care. Sudden jolts or drops can damage the
CDU.
Do not attempt to defeat any of the interlock switches or safety features built into the CDU.
Observe, and never remove, all warning labels.
Never operate damaged or leaking equipment.
Never operate the CDU without cooling fluid in the fluid reservoir.
Process fluid are subject to environmental regulatory restrictions. Do not dispose into the environment. In the United States use proper OSHA approved location for disposal.
Use remote lockout tag-out procedures prior to servicing the CDU. Make sure the CDU is off before connecting or disconnecting the power cord or other cables.
Always turn off the CDU and disconnect the power cord from the power source before performing any service or maintenance procedures, or before moving the CDU.
Always empty the fluid reservoir before moving the CDU.
Never operate equipment with damaged power cords.
Refer service and repairs to a qualified technician.
- 5 -
EMO Circuit
Each of the following safeties is part of the test system Emergency Off (EMO) circuit. The tripping of either of these safeties will cause power to be dropped to the CDU by the test system. The EMO circuit should not exceed 10A @
24VDC.
High Air Temperature (TSH-101)
This safety opens the EMO circuit when the air temperature safety switch detects a temperature inside the CDU greater than 70°C. The temperature switch is self-resetting at a temperature of 54°C or below.
Lockout/Tagout (LOTO)
Before performing Chiller maintenance, the energy sources associated with the
Chiller system must be lockout and tagged out (LOTO).
Since the CDU itself has no electrical LOTO, lock out power remotely.
Electrical LOTO can be provided by:
Disconnecting main power at the facility power source prior to the system controller cabinet.
The unit does not provide LOTO for the facility water flow. An external usersupplied device is required.
In addition, follow all local facility LOTO directives.
- 6 -
Error Code
Troubleshooting
Section II Troubleshooting
Also see Monitoring
83
- 7 -
- 8 -
NOTE: I If a pump shut down due to an overload condition than the corresponding MOL error message will also be on. Otherwise, measure the amperage of each pump to determine if it is running.
21
63
- 9 -
- 10 -
- 11 -
Also see Monitoring
- 12 -
- 13 -
- 14 -
- 15 -
- 16 -
- 17 -
- 18 -
82
82
83
- 19 -
- 20 -
- 21 -
- 22 -
Monitoring for Fluid
Loss
Each line on the Reservoir Gauge represents approximately 1/10 of a gallon.
On a routine basis check and record the fluid level. If the fluid level is dropping at a rate faster than indicated by the specification then perform the following:
1. Ensure the Tank Fill Port and the Tank Auxiliary Port Cap are properly installed and on hand tight.
2. Check all sanitary gaskets to insure that they are properly installed and
are on according to the Torque Specification Sheet on page 86.
3. Look for signs of a leak at all connections and solder joints.
4. If none of the above yield any results, use a Halogen Leak detector on each connection and joint.
5. Check for leaks at the Test Equipment per your procedures.
Reservoir Gauge
- 23 -
This page intentionally left blank.
- 24 -
Description
SYS HFE -30CDU
FRU CDU RETURN PIPE ASSY
FRU CDU FILTER BAG
FRU CDU FILTER O-RING
FRU CDU PUMP W/ GASKETS
FRU CDU PUMP SUCT LINE
FRU CDU INLINE DRIER
FRU CDU SUPPLY PIPE ASSY
FRU CDU FILL PORT SCREEN
FRU CDU PRESS REGULATOR
FRU CDU FLOW XDUCER
FRU CDU TEFLON PASTE
FRU CDU FACIL INLET PIPE
FRU CDU VALVE W/ACTUATOR
FRU CDU VLV ACTUATOR ONLY
FRU CDU INSUL TAPE
FRU CDU TANK LVL SWITCH
FRU CDU PRESS XDUCER
FRU CDU DRIP PAN SWITCH
FRU CDU RTD H2O SIDE
FRU CDU DRIER TUBE
FRU CDU RTD HFE SIDE
FRU CDU FILL PORT CAP
FRU CDU FILL PORT O-RING
FRU CDU PETES PLUG
FRU CDU CIRCUIT BREAKER
FRU CDU CONTACTOR
FRU CDU TRANSFORMER
FRU CDU VAR FREQ DRIVE
FRU CDU LON ADAPT BOARD
FRU CDU TEMP OPTION BRD
FRU CDU VFD FILTER
FRU CDU EMO THERMOSTAT
FRU CDU 1.5" SANIT GASKT
FRU CDU 2" SANIT GASKET
FRU CDU 1.5" SANIT CLMP
FRU CDU 2" SANIT CLMP
FRU CDU TC400 CNTRL BRD
FRU CDU EPROM SOFTWARE
FRU CDU PIPING TO MOD VLV
FRU PRV CARTRIDGE
FRU KEYPAD
FRU CDU DRIP PAN PLUG
FRU CDU ELECT BOX ASSY
FRU VFD BOX ASSY
FRU MOTOR OVERLOAD
093497
087774
093388
087775
087782
087820
087777
093362
087821
093397
093363
093384
087835
087836
087779
087837
Thermo
603099991707
093354
093355
093385
093356
093542
093449
093543
093386
093359
093544
093387
093496
087786
087787
087838
087788
093380
093381
093382
093383
087790
087791
093499
015779
015781
093498
087839
087840
087841
Section III FRU List
360-900-53
360-900-13
360-900-14
360-900-15
360-900-16
360-900-54
360-900-18
360-900-19
360-900-55
360-900-21
360-900-22
360-900-23
360-900-74
360-900-75
360-900-26
360-900-76
Teradyne
873-612-00.
360-900-00
360-900-01
360-900-02
360-900-03
360-900-70
360-900-05
360-900-71
360-900-07
360-900-08
360-900-72
360-900-10
360-900-52
360-900-28
360-900-29
360-900-77
360-900-31
360-900-32
360-900-33
360-900-34
360-900-35
360-900-38
360-900-39
360-900-59
360-900-41
360-900-42
360-900-57
360-900-79
360-900-80
360-900-81
- 25 -
360-900-72 Transducer,Water Flow
360-900-13 Valve Actuator Only
360-900-15 Tank Level Switch
- 26 -
360-900-54 Sensor Kit, Drip Pan Level
360-900-18 RTD H2O Side
360-900-55 RTD HFE Side
- 27 -
360-900-26 Transformer
360-900-77 VFD Filter
360-900-16 Pressure Transducer
- 28 -
360-900-74 Circuit Breaker
360-900-75 Contactor
360-900-76 Var Freq Drive
360-900-80 VFD Box Assembly
360-900-81 Motor Overload
NOTE: The VFD box,
360-900-80, consists of a VFD, two motor overloads, and the associated wiring.
- 29 -
360-900-28 LON Adapter Board
360-900-29 Temp Option Board
360-900-31 EMO Thermostat
- 30 -
360-900-79 Electrical Box Assembly
360-900-38 TC400 Control Board
360-900-00 Return Pipe Assembly, Process Flow
- 31 -
360-900-01 Filter Bag Kit
360-900-03 Pump with Gaskets
360-900-70 Pump Suction Line, with Gaskets
360-900-71, Supply Pipe Assembly
- 32 -
360-900-08 Pressure Regulator
360-900-52 Facility Inlet Pipe
360-900-53 Valve Assembly, Temperature Control
- 33 -
360-900-19 Drier Tube
360-900-32 Gasket 1½" / 360-900-33 Gasket 2"
360-900-34 Clamp, Sanitary Fitting 1½" / 360-900-35 Clamp, Sanitary Fitting 2"
- 34 -
360-900-23 Petes Plug
360-900-41 Pressure Relief Valve Cartridge
360-900-22 Service Kit, Fill Port Cap
- 35 -
360-900-02 O-ring, Filter Housing
360-900-07 Fill Port Screen
360-900-10 Teflon
®
Paste
- 36 -
360-900-14 Tape, Insulating
360-900-57 Fitting, Drip Pan Plug
360-900-21 Fill Port Cap
- 37 -
360-900-59 Piping to Mod Valve
360-900-05 Pump Inline Dryer
360-420-00 Programmable Chip Extractor
- 38 -
360-900-42 Keypad
- 39 -
This page intentionally left blank.
- 40 -
CAUTION
Section IV FRU Replacement
For personal safety and equipment reliability, the following procedures should only be performed by a qualified technician. The following steps assume the technician is knowledgable of all Swagelok initial tightening and retightening procedures. Contact our Service Department for assistance.
WARNING
Contact with hazardous voltage inside the chiller can cause severe injury of death. Turn off and Lockout/Tagout (LOTO) power before servicing. Have a qualified technician verify that line voltage is no longer present within the unit after performing a LOTO procedure and before working on system.
CAUTION
Performance maintenance and service procedures other than those described in this manual may result in a hazardous situation.
- 41 -
Electrical Components
To access any of these electrical components you must remove the control box assembly and the side panel.
Temp Option Board
TC-400 Controller Board
Programmable Chip
LON Adapter
Board see
VFD Filter see
EMO Thermostat
Transformer see
Bottom View (See Next Page)
- 42 -
Device
Coolant RTD
Facility RTD
Connector Action
J102 Check resistance pins 1 and 7
P103
Level Switches J1
Check resistance pins 1 and 7
Values
100 Ohms @ 0°C
~110 Ohms @ room temp
100 Ohms @ 0°C
~110 Ohms @ room temp
Check resistance
Pins 1 and 2 warning
Pins 3 and 4 shut down
0 Ohms = closed
Ohms = open
Drip Pan
Switch
Facility Flow
Transducer
Motor Valve
J2
J4
J5
Pressure
Transducers
J6
Check resistance
Pins 1 and 2
0 Ohms = closed
Ohms = open
See chart below Check Voltage
Pins 1 and 2
Measure Voltage
Pins 1 and 2
100% open => 9.5 VDC
0% open = < 6.0 VDC
Measure voltage 37.5 psi per volt plus 0.5 volts
Pins 2 and 3 supply(example - 150 psi = 4.5 volts)
Pins 5 and 6 return
200.00
150.00
100.00
50.00
5 10 15 20
Flow Rate (gpm)
25 30 35
- 43 -
ElectricalBox Assembly
(360-900-79)
WARNING
Turn off and Lockout/Tagout (LOTO) power before servicing.
Tools Required:
#2 Philips Head Screwdriver
11/32" wrench
Wiring Diagram
Procedure:
1. Using #2 Philips Head, remove the 4 screws securing the electrical box assembly to the front of the unit.
2. Remove the single screw securing the base of the control box to the unit's midframe.
3. Remove the 8 connectors at the bottom of the control box.
4. At the pump motor, remove the wiring running from the base of the control box.
5. Remove the 11/32 nut securing the ground wire at the rear of the unit.
6. Slide the control box assembly out from the unit.
7. Swap out the LON Adapter board from the replaced assembly into the new
8. To reinstall, reverse the procedure.
Torque Control Box to Mid Pan, Bottom 14 - 16"-lbs
Torque Control Box to Mid Pan, Top 24 - 28"-lbs
Torque Control Box Assembly to Sides 24 - 28"-lbs
9. Rewire according to the wiring diagram.
10. Return the replaced assembly to Thermo Electron.
- 44 -
360-900-42 Keypad
Tools Required:
Screwdriver
11/32" wrench
Procedure:
1. Remove the 4 screws securing the keypad panel to the front of the unit.
2. Disconect ribbon cable from control board.
3. Remove the 11/32 grounding nut.
4. Peal the keypad off the panel.
5. When reinstalling, tighten gounding nut 14-16"-lbs.
- 45 -
Drier Tube
(360-900-19)
When the cartridge color-change feature (blue to pink) reaches the bottom of the top cap, the dryer tube needs changing.
WARNING
Turn off and Lockout/Tagout (LOTO) power before servicing.
Tools Required:
Tywrap cutter/scissors
Procedure:
1. Remove the top and bottom tubes from the dryer tube nipples.
2. Cut the ty-wrap.
3. Reverse the procedure to install a new dryer tube.
4. Once the unit is restarted check for leaks.
- 46 -
Fill Port Screen
(360-900-07)
WARNING
Turn off and Lockout/Tagout (LOTO) power before servicing.
Tools Required:
None
Procedure:
1. Remove the fill port cap by turning counterclockwise.
2. Remove the screen.
3. Replace the screen.
4. Reinstall the fill cap.
5. Once the unit is restarted check for leaks.
- 47 -
HFE Filter Bag Kit
(360-900-01)
WARNING
Turn off and Lockout/Tagout (LOTO) power before servicing.
Tools Required:
None
Procedure:
1. Crack open the reservoir fill to allow air into the tank.
2. Locate and then loosen the black knob on the clamp at the top of the filter housing.
3. Remove the clamp. Note how the "T" is locked into position on the clamp.
T
- 48 -
4. Remove the lid and gasket.
5. Remove the spacer, handle up.
- 49 -
6. Pull out the old bag to remove it.
7. Install a new bag. Ensure that the paper tag is removed from the bag.
- 50 -
8. Reinstall the spacer, handle up.
9. Replace the lid gasket and reinsall the lid.
- 51 -
10. To reinstall a new bag push down on the lid and gasket when tightening the black knob. Hand tighten until the gap matches the other two gaps.
11. Once the unit is restarted check for leaks.
12. Ensure the LED and error message on the controller are both extinguished.
- 52 -
Pump Inline Drier
(360-900-05)
WARNING
Turn off and Lockout/Tagout (LOTO) power before servicing.
Tools Required:
9/16" wrench
Procedure:
For easier access to the assembly remove the unit from the cabinet.
1. Note orientation of dryer assembly.
2. Crack open the reservoir fill to allow air into the tank.
3. Use the 9/16" wrench to remove the Swageloks securing the dryer assembly to the unit. To make removing the outer Swagelok easier, bend the inner dryer line down to get it out of the way.
Inner Swagelok
Outer Swagelok
Top View
4. Undo the two Velcro straps and remove the dryer assembly.
Dryer
5. Install a new dryer assembly. Secure the Velcro straps first to prevent bending the lines.
6. Connect the two ¼" lines and tighten the Swageloks per the tightening procedure on page 87.
7. Once the unit is restarted check for leaks.
- 53 -
Tank Level Switch
(360-900-15)
WARNING
Turn off and Lockout/Tagout (LOTO) power before servicing.
Tools Required:
Adjustable wrench
Tywrap cutter/scissors
Procedure:
1. For easier access to the switch, remove the electrical box assembly, see
2. Undo the electrical "D" connector on the rear of the unit.
3. Remove the ty wraps.
4. Undo the green plastic fitting and remove the switch assembly from the reservoir.
5. To reinstall a new assembly reverse the procedure. NOTE: To prevent cross threading, install the new assembly into the reservoir only hand tight.
6. Once the unit is restarted check for leaks.
7. Ensure the LED and error message on the controller are both extinguished.
- 54 -
Pump (360-900-03)
WARNING
Turn off and Lockout/Tagout (LOTO) power before servicing.
CAUTION Crack the fill cap to relieve any tank/system pressure.
Tools Required:
11/16" wrench
7/16" wrench
1/2" wrenchet.
Procedure:
For easier access to the pump remove the unit from the cabin
1. Drain the water. Refer to Teradyne Service Documentation for proper procedure.
2. Remove the electrical box assembly, see page 44.
3. Remove sanitary clamps from both suction and discharge lines to the plate exchanger.
- 55 -
4. Using a 11/16" wrench, remove the fitting from the pump's drain line.
5. Using a 7/16" wrench, remove the 6 bolts securing the pump plate to the unit.
CAUTION
6. Remove the pump and plate from the unit.
The pump weighs at least 80 pounds.
7. Using a 1/2" wrench, remove the nuts and washers securing the pump to the pump plate.
8. When reinstalling a new pump do not tighten any of the nuts, bolts, or clamps until all plumbing lines are properly aligned. Also, use new gaskets when reinstalling the sanitary clamps.
9. Reorrect pump discharge line to pump. Recheck the alignment.
- 56 -
10. Using a 11/16" wrench, install the fitting from the pump's drain line.
11. Install the sanitary clamps on the pump suction and discharge line.
12. Tighten all connections.
Torque Pump to Pump Plate
Torque Pump Plate to Case
Torque Sanitary Fittings
13. Reconnect all the wiring.
100-110"-lbs
75"-lbs
25"-lbs
Torque Pump Motor Ground Wires (3) 24 - 28"-lbs
14. Reinstall the electrical box assembly, see page 44.
15. Once the unit is restarted check for leaks.
16. Return the replaced pump to Thermo Electron.
- 57 -
Temperature Control
Valve Assembly
(360-900-53)
WARNING
Turn off and Lockout/Tagout (LOTO) power before servicing.
Tools Required:
1 3/4" wrench
Two 1 1/4" wrenches
Copper tubing cutting tool
Tywrap cutter/scissors
Tape, Insulating
Procedure:
For easier access to the valve remove the unit from the cabinet.
1. Drain the water. Refer to Teradyne Service Documentation for proper procedure.
2. Remove the insulation around the valve.
3. Use a 1 3/4" wrench to disconnect the Swageloks.
4. Unplug the 6-pin connector and disconnect the ground wire.
5. Open the clamp securing the valve to the unit.
- 58 -
6. To reinstall a new valve first connect the 1 3/4" Swageloks - finger tight.
7. Install the clamp.
8. Tighten the two Swageloiks. Refer to the Swagelok Installation on page 87.
Torque clamp 50"-lbs.
9. Reinstall the 6-pin connector and the ground wire.
Torque ground wire 24 - 28"-lbs.
10. Once the unit is restarted check for leaks.
11. Ensure the LED and error message on the controller are both extinguished.
12. Install insulation.
- 59 -
Temperature Control
Valve Actuator
(360-900-13)
WARNING
Turn off and Lockout/Tagout (LOTO) power before servicing.
Tools Required:
1 5/8" wrench
Tape, Insulating
Procedure:
For easier access to the actuator remove the unit from the cabinet.
1. Drain the water. Refer to Teradyne Service Documentation for proper procedure.
2. Use the 1 5/8" wrench to disconnect the actuator from the valve.
3. Unplug the 6-pin connector and disconnect the ground wire.
4. Reverse the procedure to install the actuator. Torque actuator to 20-25"-lbs.
5. Once the unit is restarted check for leaks.
6. Install insulation.
- 60 -
Water Flow Transducer
(360-900-72)
WARNING
Turn off and Lockout/Tagout (LOTO) power before servicing.
Tools Required:
Adjustable wrenches
Teflon Sealant (FasSeal-ATS
TM
)
Insulating Tape
Procedure:
For easier access to the assembly remove the unit from the cabinet.
1. Drain the water. Refer to Teradyne Service Documentation for proper procedure.
2. Remove the insulation.
3. Use a wrench to hold the bottom fitting in place and a second wrench to undo the top hose.
4. Remove the bottom Swagelok.
5. Unplug the wiring from under the electrical box.
6 The new flow transducer can be installed in either direction.
7. Connect both fittings, hand tight. NOTE: Use supplied thread sealant on upper connection.
8. Tighten the fittings, refer to the Swagelok Installation Sheet on page 87.
9. Connect the wiring to the control box.
10. Once the unit is restarted check for leaks.
11. Ensure the LED and error message on the controller are both extinguished.
12. Install insulation.
- 61 -
HFE Temp Sensor (rtd1)
(360-900-55)
Tools Required:
WARNING
Turn off and Lockout/Tagout (LOTO) power before servicing.
1/2" wrench
Tywrap cutters/Scissors
Procedure:
1. Use the 1/2" wrench to disconnect the sensor.
2. Slide the sensor down and through the unit's midpan.
3. Unplug the sensor from below the control box.
4. Reverse procedure to install new sensor. Refer to the Swagelok Installation
5. Once the unit is restarted check for leaks.
- 62 -
Pressure Transducers
(360-900-16)
WARNING
Turn off and Lockout/Tagout (LOTO) power before servicing.
Tools Required:
5/8" wrench
Tywrap cutters/Scissors
Procedure:
1. Unsnap the black plastic cap(s) on the transducer(s).
2. Use the 5/8" wrench to disconnect the transducer(s).
3. Unplug the wiring.
4. Reverse the procedure to install a new transducer. To tighten the fittings,
refer to the Swagelok Installation Sheet on pages 87.
5. Once the unit is restarted check for leaks.
- 63 -
Drip Pan Level
Switch Kit
(360-900-54)
WARNING
Turn off and Lockout/Tagout (LOTO) power before servicing.
Tools Required:
3/8" wrench
Tywrap cutters/Scissors
Procedure:
1. Remove the 3/8" nut securing the kit to its bracket.
2. Undo wiring from below the electrical box.
3. To reinstall, reverse the procedure.
- 64 -
Pressure Regulator
(360-900-08)
WARNING
Turn off and Lockout/Tagout (LOTO) power before servicing.
Tools Required:
Two 2 1/16" wrenches or adjustable wrenches
1/8" diameter test probe (Peterson Equip. Co. Inc. #500 Gauge Adapter or equivalent).
Insulating Tape
Procedure:
For easier access to the assembly remove the unit from the cabinet.
1. Drain the water. Refer to Teradyne Service Documentation for proper procedure.
2. Remove insulation around the regulator.
3. Loosen top union fitting.
4. Undo bottom union fitting.
5. Undo top union fitting.
6. When installing new regulator and washers ensure the arrow on the side of the regulator points down.
7. Install both unions, hand tight.
8. Tighten both unions, one full turn past hand tight.
9. Install new insulation.
10. Once the unit is restarted check for leaks.
11. Ensure the LED and error message on the controller are both extinguished.
12. Adjust the pressure differential, see next page.
- 65 -
Using the test probe, verify the differential pressure across the temperature control valve using the two pressure test ports (Petes Plugs) PP-102 and
PP-103.
With the unit off and facility water on, measure the pressure at PP-102. The pressure should match the facility water pressure. NOTE: If the pressure is 0 ensure that the facility water is on and that the facility supply valve is open.
Next measure the pressure at PP-103. The difference between the two readings should be 30 - 33 PSI.
PP-102
PP-103
If adjustment is necessary loosen the locknut on the pressure regulator and then turn the adjustment bolt clockwise to increase the pressure, counterclockwise to decrease the pressure. Tighten the locknut.
Pressure Regulator
13. Install insulation.
- 66 -
Plumbing, Pressure Regulator to Temperature
Control Valve (360-900-59)
WARNING
Turn off and Lockout/Tagout (LOTO) power before servicing.
Tools Required:
Two 2 1/16" wrenches or adjustable wrenches
One 1 3/4" wrench or adjustable wrench
Insulating Tape
Procedure:
For easier access to the assembly remove the unit from the cabinet.
1. Drain the water. Refer to Teradyne Service Documentation for proper procedure.
2. Remove insulation around the connections.
3. Undo the bottom union fitting on pressure regulator.
4. Use a 1 3/4" wrench to disconnect the Swagelok.
5. To reinstall tighten union, one full turn past hand tight.
6. Tighten the fitting, refer to the Swagelok Installation Sheet on page 87.
7. Once the unit is restarted check for leaks then install insulation.
- 67 -
Facility Inlet Pipe
(360-900-52)
WARNING
Turn off and Lockout/Tagout (LOTO) power before servicing.
Tools Required:
Two 2 1/16" wrenches or adjustable wrenches
One 1 3/4" wrench or adjustable wrench
Insulating Tape
Procedure:
For easier access to the assembly remove the unit from the cabinet.
1. Drain the water. Refer to Teradyne Service Documentation for proper procedure.
2. Remove insulation.
3. Undo top union fitting on pressure regulator.
4. Undo the u-bolts securing the plumbing to the bottom of the unit's midpan.
5. To reinstall, reverse the procedure.
6. Tighten u-bolts until split washers on both sides are flat.
7. Once the unit is restarted check for leaks then install insulation.
- 68 -
H2O Side
Temperature Sensor
(rtd2) (360-900-18)
WARNING
Turn off and Lockout/Tagout (LOTO) power before servicing.
Tools Required:
Tywrap cutters/Scissors
Insulating Tape
Procedure:
1. Remove the electrical box assembly, see page 44.
2. Remove the insulation covering the sensor.
3. Cut the aluminum tape securing the sensor to the facility line.
4. Undo the wiring from below the electrical box.
5. Attach new sensor with hose clamp.
6. Install new tape and insulation.
7. Connect wiring.
8. Ensure the LED and error message on the controller are both extinguished.
9. Install insulation.
- 69 -
Return Pipe Assembly, Process Flow
(360-900-00)
WARNING
Turn off and Lockout/Tagout (LOTO) power before servicing.
Tools Required:
One 1/2" wrench or adjustable wrench
One 9/16" wrench or adjustable wrench
One 5/8" wrench or adjustable wrench
Procedure:
1. Drain the HFE. Refer to Teradyne Service Documentation for proper procedure.
2. Unsnap the black plastic cap on the transducer
3. Use the 5/8" wrench to disconnect the transducer.
4. Use the 1/2" and 9/16" wrenchs to disconnect the two process flow lines.
- 70 -
5. Use the 1/2" wrench to disconnect the process lines from the dryer.
6. Undo the u-bolts securing the line to the unit.
7. Undo the sanitary fitting at the tank.
8. Reverse the procedure to install a new line. Tighten all connection. Refer to the Swagelok Installation on page 87.
Sanitary Fitting
U-bolts
25"-lbs.
Hand tighten and 3 turns
9. Once the unit is restarted check for leaks.
- 71 -
Supply Pipe Assembly, Process Flow
(360-900-71)
WARNING
Turn off and Lockout/Tagout (LOTO) power before servicing.
Tools Required:
One 1/2" wrench or adjustable wrench
One 9/16" wrench or adjustable wrench
One 5/8" wrench or adjustable wrench
Procedure:
1. Drain the HFE. Refer to Teradyne Service Documentation for proper procedure.
2.Unsnap the black plastic cap on the transducer
3. Use the 5/8" wrench to disconnect the transducer.
4. Use the 1/2" wrench to disconnect the temperature sensor.
5. Use the 1/2" and 9/16" wrenchs to disconnect the two process flow lines.
- 72 -
6. Undo the u-bolts securing the line to the unit.
7. Undo the sanitary fitting at the heat exchanger.
8. Reverse the procedure to install a new line. Tighten all connection. Refer to the Swagelok Installation on page 87.
Sanitary Fitting 25"lbs.
U-bolts
9. Once the unit is restarted check for leaks.
Hand tighten and 3 turns
- 73 -
PRV Cartridge (360-900-41)
Tools Required:
Adjustable wrench
Two screwdrivers
Procedure:
1. Loosen locknut and turn adjusting screw counterclockwise to remove the spring tension.
2. Remove the bonnet using the adjustable wrench.
3. Remove the cartridge using two screwdrivers as levers.
4. When installing new cartridge ensure the o-rings and washers are properly installed.
Washer
O-rings
- 74 -
VFD Filter (360-900-77)
Contactor (360-900-75)
Transformer(360-900-26)
WARNING
Turn off and Lockout/Tagout (LOTO) power before servicing.
Tools Required:
McMaster Carr 8554A26, or equivalent torque screw driver
Wiring Diagram
Procedure:
1. Remove the electrical box assembly, see page 44.
2. Remove wiring and screws from transformer and contactor to access the RFI.
3. Remove wiring and screws securing RFI to the unit.
4 To reinstall components, reverse the procedure.
Torque Transformer Mounting Screws 14 - 16"-lbs
Torque Contactor/RFI Mounting Screws 24 - 28"-lbs
5. Reconnect wiring, refer to wiring diagram.
Torque RFI Wiring
Torque RFI Ground Wire
15½"-lbs
22 - 26"-lbs
Torque RFI Filter Wires to Contactor 25"-lbs
6. Ensure the LED and error message on the controller are both extinguished.
- 75 -
EMO Thermostat
(360-900-31)
WARNING
Turn off and Lockout/Tagout (LOTO) power before servicing.
Tools Required:
#6 Wrench or adjustable wrench
Loctite
®
threadlocker or equivalent
Procedure:
1. Remove the electrical box assembly, see page 44.
2. Remove the control box assembly side panel.
3. Locate the thermostat and remove the wiring and #6 nut.
4. To reinstall reverse the procedure. Hand-tight nut and secure with Loctite
®
.
- 76 -
Var Freq Drive VFD
(360-900-76)
WARNING
Turn off and Lockout/Tagout (LOTO) power before servicing.
Tools Required:
McMaster Carr 8554A26, or equivalent torque screw driver
Wiring Diagram
Procedure:
1. Remove all wiring to the VFD.
2. Remove the four screws securing the VFD to the box assembly.
3. When installing, torque all four screws to 24 - 28"-lbs.
4. Reconnect all wiring. Refer to wiring diagram.
Torque VFD Wire Connection Screws
Torque VFD Ground Nut
16 - 19"-lbs
14 - 16"-lbs
Torque VFD Signal Wires
Torque VFD Jumper Wires
Torque VFD Power Wires
Torque VFD Controller Panel
4.4 - 7"-lbs
4.4 - 7"-lbs
16 - 19"-lbs
10 - 12"-lbs
5. Calibrate the VFD and install default settings, see next page.
6. Check for error codes on the VFD and controller.
- 77 -
VFD Settings
Viewing and Editing Parameter Steps.
1. When Power is applied, the last user-selected Display Group parameter number is briefly displayed with flashing characters. The display then defaults to that parameters current value.
2. Press Esc once to display the Display Group parameter number shown on powerup. The parameter number will flash.
3. Press Esc again to enter the group menu. The group menu letter will flash.
4. Press the Up Arrow or Down Arrow to scroll through the group menu (d, P and A).
5. Press Enter or Sel to enter a group. The right digit of the last viewed parameter in that group will flash.
6. Press the Up Arrow or Down Arrow to scroll through the parameters that are in the group.
7. Press Enter or Sel to view the value of a parameter. If you do not want to edit the value, press Esc to return to the parameter number.
8. Press Enter or Sel to enter program mode to edit the parameter value. The right digit will flash and the Program LED will illuminate if the parameter can be edited.
9. Press the Up Arrow or Down Arrow to change the parameter value. If desired, press Sel to move digit to digit or bit to bit. The digit or bit that you can change will flash.
10. Press Esc to cancel a change. The digit will stop flashing, the previous value is restored and the Program LED will turn off.
Or
Press Enter to save a change. The digit will stop flashing and the Program LED will turn off.
11. Press Esc to return to the parameter list. Continue to press Esc to back out of the programming menu. If pressing Esc does not change the display, then d001
[Output Frequency] is displayed. Press Enter or Sel to enter the group menu.
Settings
Display Group and Number Setting
P031
P033
208
29.4
P036
P038
A051
A052
2
2
7
5
- 78 -
Pump Motor Overloads
(360-900-81)
WARNING
Turn off and Lockout/Tagout (LOTO) power before servicing.
Tools Required:
McMaster Carr 8554A26, or equivalent torque screw driver
Wiring Diagram
Procedure:
1. Remove all wiring to the overload.
2. Remove the two screws securing the overload to the box assembly.
3. When installing, torque all screws to 24 - 28"-lbs.
4. Reconnect all wiring. Refer to wiring diagram.
5. Check for error codes on the controller.
- 79 -
Circuit Breaker
(360-900-74)
WARNING
Turn off and Lockout/Tagout (LOTO) power before servicing.
Tools Required:
McMaster Carr 8554A26, or equivalent torque screw driver
Wiring Diagram
Procedure:
1. Remove the electrical box assembly, see page 44.
2. Remove the four nuts securing the circuit breaker to the unit.
3. Remove all wiring to the circuit breaker.
Spring
4. Press the spring on the circuit breaker to separate it from the bracket.
5. To reinstall, reverse the procedure.
Torque Circuit Breaker 11/32 Mounting Nuts
6. Reinstall wiring, refer to wiring diagram.
14 - 16"-lbs
Torque Circuit Breaker Wire Connections 20"-lbs
- 80 -
Temp Option Board
(TC-400 to LON Adapter)
(360-900-29)
WARNING
Turn off and Lockout/Tagout (LOTO) power before servicing.
WARNING
Use proper ESD (Electro Static Discharge) procedures when handling
the chip and controller. Typically a grounded wrist strap is used to ground the individual so static discharge is released prior to and during handling.
Tools Required:
Small pair of needle nose pliers
Wiring Diagram
Procedure:
1. Remove the electrical box assembly, see page 44.
2. Remove wiring
3. Using the pliers, press the "ears" on the four corners of the board and pull it out.
4. Snap new board back into position.
5. Install wiring, refer to wiring diagram.
6. Ensure the LED and error message on the controller are both extinguished.
- 81 -
Chip Replacement
(390-900-39)
WARNING
Turn off and Lockout/Tagout (LOTO) power before servicing.
WARNING
Use proper ESD (Electro Static Discharge) procedures when handling
the chip and controller. Typically a grounded wrist strap is used to ground the individual so static discharge is released prior to and during handling.
Tools Required
Plastic Leaded Chip Carrier (PLCC) extraction tool (not supplied) or equivalent.
Procedure
1. Remove electrical box assembly, see page 44.
2. The chip is located on the TC-400 Control Board, beneath the Communications Board. Remove the Communications Board.
3. Remove old programmed chip with the
PLCC extraction tool. If one is not available a suitable tool is available from
Thermo under part number 082166.
Additional instructions are provided with the tool.
4. Insert new programmed chip by placing the chip over the socket with the orientation dot on the chip aligned with the orientation arrow on the board. Note that sometimes dot may be covered by a label, see below. Do not rely on the chip label since its orientation can be random. You may also notice that a corner of the chip and socket are slightly flattened. Press chip onto the socket by applying equal pressure to the chip until the chip completely snaps into the socket.
5. Replace the Communications Board and the control box assembly.
6. Start the unit and skip through any error messages using the controllers
NEXT key. (Error 3 may appear when the new chip is powered up for the first time.)
7. Unit must be recalibrated for proper operation. Refer to Teradyne Service
Documentation for proper procedure.
- 82 -
TC-400 Control Board
(360-900-38)
WARNING
Turn off and Lockout/Tagout (LOTO) power before servicing.
WARNING
Use proper ESD (Electro Static Discharge) procedures when handling
the chip and controller. Typically a grounded wrist strap is used to ground the individual so static discharge is released prior to and during handling.
Tools Required:
Small pair of needle nose pliers
Screwdriver
Phillips Screwdriver
¼" Nut driver
Plastic Leaded Chip Carrier (PLCC) extraction tool (not supplied) or equivalent.
Wiring Diagram
Procedure:
1. To allow the panel to fold down, remove the 4 screws securing the keypad panel to the front of the unit.
- 83 -
2. Remove all wiring to the board.
3. Remove the Temp Option Board and Programmable Chip, see previous two pages.
4. Undo the four corner mounting nuts securing the board to the unit.
TB2
TB1
TB4
5. To reinstall, reverse the procedure. Refer to wiring diagram. NOTE: Ensure jumper settings on new board match the settings on the wiring diagram.
Torque mounting nuts
Torque 1TB/2TB Wires
Torque 4TB Wires
6 - 8"-lbs
8 -10"-lbs
4.4 - 7"-lbs
6. Ensure the error message on the controller is extinguished.
- 84 -
LON Adapter Board
(360-900-28)
WARNING
Turn off and Lockout/Tagout (LOTO) power before servicing.
WARNING
Use proper ESD (Electro Static Discharge) procedures when handling
the chip and controller. Typically a grounded wrist strap is used to ground the individual so static discharge is released prior to and during handling.
Tools Required:
Small pair of needle nose pliers
Wiring Diagram
Procedure:
1. Remove the SMC Rider Board.
2. Remove the wiring to the LON.
3. Press the "ears" on all four corners of the board and pull it out.
4. To reinstall, reverse the procedure. Refer to wiring diagram.
5. Install the SMC Rider Board.
6. Calibrate the new board. Refer to Teradyne Service Documentation for proper procedure.
7. Ensure the LED and error message on the controller are both extinguished.
- 85 -
Torque Specification Sheet
Mechanical Assemblies
Pump Plate to Case
Pump to Pump Plate
Hose Clamps
Unions (Pressure Regulator)
CAM Lock Fittings
Sanitary Fittings
Facility Water Outlet Assembly
75"-lbs
100-110"-lbs
50"-lbs
One full turn past hand tight
70'-lbs
25"-lbs
75"-lbs
Process side U-bolts ¼-20 (084302)
Facility side U-bolts 3/8-16 (084292)
Temperature control valve actuator
Electrical Assemblies
Hand tighten and then 3 turns
Hand tighten until split washers are flat on both sides
20-25"-lbs
For phillips head screws we recommend using a McMaster Carr 8554A26, or equivalent
Float Switch
Motor Valve Ground Wire
Pump Motor Ground Wires (3)
Control Box Assembly to Mid Pan, Bottom
Control Box Assembly to Mid Pan, Top
Control Box Assembly to Sides
Contactor Connecting Screws
VFD Mounting Screws
Hand tight
24 - 28"-lbs
24 - 28"-lbs
14 - 16"-lbs
24 - 28"-lbs
24 - 28"-lbs
25"-lbs
24 - 28"-lbs
VFD Wire Connection Screws
VFD Ground Nut
VFD Signal Wires
VFD Jumper Wires
VFD Power Wires
VFD Controller Panel
Control Board Mounting #4 Nuts
16 - 19"-lbs
14 - 16"-lbs
4.4 - 7"-lbs
4.4 - 7"-lbs
16 - 19"-lbs
10 - 12"-lbs
6- 8"-lbs
1TB Wires
2TB Wires
4TB Wires
Key Pad Ground 11/32 Nut
8 -10"-lbs
8 -10"-lbs
4.4 - 7"-lbs
14 - 16"-lbs
RFI Filter Wires to Contactor
RFI Filter Mounting Screws
RFI Wiring
RFI Ground Wire
25"-lbs
24 - 28"-lbs
15½"-lbs
22 - 26"-lbs
Transformer Mounting Screws (8 - 32 x
1
/
4
") 14 - 16"-lbs
Contactor Mounting Screws (10 - 32 x
3
/
8
")
Circuit Breaker 11/32 Mounting Nuts
Circuit Breaker Wire Connections
24 - 28"-lbs
14 - 16"-lbs
20"-lbs
- 86 -
Swagelok Tube Fitting
Instructions
1
Installation
1. Insert tubing into the Swagelok tube fitting.
2. Make sure that the tubing rests firmly on the shoulder of the tube fitting body and that the nut is finger-tight.
3. Scribe the nut at the 6 oclock position.
4. While holding fitting body steady, tighten the nut 11/4 turns to the 9 oclock position. Note: For 1/16, 1/8, and 3/16 in; 2, 3, and 4 mm tube fittings, tighten the nut 3/4 turn to the 3 oclock position.
Installation in High-Pressure Applications and High Safety-Factor
Systems
1. Follow steps 1 and 2 of the Swagelok Tube Fitting Instructions.
2. Tighten the nut until the tubing will not rotate freely by hand.
3. Follow steps 3 and 4 of the Swagelok Tube Fitting Instructions.
Gageability On initial installation, the Swagelok gap inspection gauge assures the installer or inspector that a fitting has been sufficiently tightened.
Position the Swagelok gap inspection gauge next to the gap between the nut and body.
If the gauge will not enter the gap, the fitting is sufficiently tightened.
If the gauge will enter the gap, additional tightening is required.
- 87 -
Reassembly Instructions You may disassemble and reassemble a
Swagelok tube fitting, port connector, cap, and plug many times.
1. Insert tubing with pre-swaged ferrules into the fitting body until the front ferrule seats.
2. Rotate the nut with a wrench to the previously pulled-up position. At this point, a significant increase in resistance will be encountered.
3. Tighten slightly with a wrench. Note: Do not use the gap inspection gauge with reassembled fittings.
Do not mix or interchange parts with those of other manufacturers.
1. Swagelok Pocket Catalog of Tube Fittings MS-13-58
- 88 -
Section V Controller Loops
Main Loop
An alphanumeric display presents numeric readings of various operating conditions within the chiller. Display function is selected by pressing the appropriate keys to move through a menu of available information.
Main Loop
When the controller is first powered up it goes through a short self-test, and then enters the Main Loop and displays the unit configuration.
Unit Configuration
NEXT
Process Fluid Supply
Temperature
NEXT
Facility Fluid Supply
Temperature
NEXT
Facility Water Flow Rate
NEXT
Process Fluid Differential
Pressure
NEXT
Main Loop
- 89 -
Engineering Loop
The Engineering Loop allows you to open or close the temperature control valve. Use the YES button to enter the valve condition. The display will then flash between the position of the valve and the facility flow value. Use the YES or the NO buttons to open or close it in 10% increments. When the desired value is displayed press ENTER and then NEXT to sequence through the displays.
Press NEXT to sequence the display through the cool duty cycle, the coolant return pressure, the coolant supply pressure, the facility water temperature, and the ambient air temperature. Press NEXT again to return to the Main Loop.
HICAPACITY
ENTER
NEXT
NO
ENTER
NEXT
NO
YES or
YES
NO
NEXT
NEXT ENTER
NEXT
NEXT
NEXT
NEXT
NEXT
- 90 -
Engineering Loop
Factory Reset
A Factory Reset returns all the controller settings to its factory preset values.
HICAPACITY
ENTER
NO YES
NO
+
ENTER SILENCE
After the Reset a controlller calibration is required. Refer to Teradyne Service
Documentation for proper procedure.
- 91 -
WARRANTY
Thermo Electron Corporation warrants for 24 months from date of shipment any Thermo Electron unit according to the following terms.
Any part of the CDU manufactured or supplied by Thermo Electron and found in the reasonable judgment of
Thermo Electron to be defective in material or workmanship will be repaired at an authorized Thermo Electron
Repair Depot without charge for parts or labor. The CDU, including any defective part must be returned to an authorized Thermo Electron Repair Depot within the warranty period. The expense of returning the CDU to the authorized Thermo Electron Repair Depot for warranty service will be paid for by the buyer. Thermo Electrons responsibility in respect to warranty claims is limited to performing the required repairs or replacements, and no claim of breach of warranty shall be cause for cancellation or recision of the contract of sales of any CDU. With respect to CDUs that qualify for field service repairs, Thermo Electrons responsibility is limited to the component parts necessary for the repair and the labor that is required on site to perform the repair. Any travel labor or mileage charges are the financial responsibility of the buyer.
The buyer shall be responsible for any evaluation or warranty service call (including labor charges) if no defects are found with the Thermo Electron product.
This warranty does not cover any CDU that has been subject to misuse, neglect, or accident. This warranty does not apply to any damage to the CDU that is the result of improper installation or maintenance, or to any
CDU that has been operated or maintained in any way contrary to the operating or maintenance instructions specified in Thermo Electrons Instruction and Operation Manual. This warranty does not cover any CDU that has been altered or modified so as to change its intended use.
In addition, this warranty does not extend to repairs made by the use of parts, accessories, or fluids which are either incompatible with the CDU or adversely affect its operation, performance, or durability.
Thermo Electron reserves the right to change or improve the design of any CDU without assuming any obligation to modify any CDU previously manufactured.
THE FOREGOING EXPRESS WARRANTY IS IN LIEU OF ALL OTHER WARRANTIES, EXPRESSED OR
IMPLIED, INCLUDING BUT NOT LIMITED TO WARRANTIES OR MERCHANTABILITY AND FITNESS FOR A
PARTICULAR PURPOSE.
Thermo Electrons OBLIGATION UNDER THIS WARRANTY IS STRICTLY AND EXCLUSIVELY LIMITED TO THE
REPAIR OR REPLACEMENT OF DEFECTIVE COMPONENT PARTS AND Thermo Electron DOES NOT
ASSUME OR AUTHORIZE ANYONE TO ASSUME FOR IT ANY OTHER OBLIGATION.
Thermo Electron ASSUMES NO RESPONSIBILITY FOR INCIDENTAL, CONSEQUENTIAL, OR OTHER DAM-
AGES INCLUDING, BUT NOT LIMITED TO LOSS OR DAMAGE TO PROPERTY, LOSS OF PROFITS OR
REVENUE, LOSS OF THE UNIT, LOSS OF TIME, OR INCONVENIENCE.
This warranty applies to CDUs sold in the United States. Any CDUs sold elsewhere are warranted by the affiliated marketing company of Thermo Electron. This warranty and all matters arising pursuant to it shall be governed by the law of the State of New Hampshire, United States. All legal actions brought in relation hereto shall be filed in the appropriate state or federal courts in New Hampshire, unless waived by Thermo Electron.
advertisement
* Your assessment is very important for improving the workof artificial intelligence, which forms the content of this project
Related manuals
advertisement
Table of contents
- 4 After-sale Support
- 4 Warranty
- 6 Warnings
- 7 EMO Circuit
- 7 Lockout/Tagout (LOTO)
- 8 Error Code Troubleshooting
- 22 VFD Faults
- 24 Monitoring Fluid Loss
- 26 FRU List
- 43 Electrical Components
- 45 Electrical Box Assembly
- 46 Keypad
- 47 Drier Tube
- 48 Fill Port Screen
- 49 HFE Filter Bag Kit
- 54 Pump Inline Drier
- 55 Tank Level Switch
- 59 Temperature Control Valve Assembly
- 61 Temperature Control Valve Actuator
- 62 Water Flow Transducer
- 63 HFE Side Temperature Sensor (rtd1)
- 64 Pressure Transducers
- 65 Drip Pan Level Switch Kit
- 66 Pressure Regulator
- 68 Plumbing, Pressure Regulator to Temperature Control Valve
- 69 Plumbing, Facility Inlet Pipe
- 70 H2O Side Temperature Sensor (rtd2)
- 71 Return Pipe Assembly, Process Flow
- 73 Supply Pipe Assembly, Process Flow
- 75 PRV Cartridge
- 76 VFD Filter, Contactor, Transformer
- 77 EMO Thermostat
- 79 VFD Settings
- 80 Pump Motor Overloads
- 81 Circuit Breaker
- 82 Temp Option Board
- 83 Chip Replacement
- 84 TC-400 Controller
- 86 LON Adapter Board
- 87 Torque Specification Sheet
- 88 Swagelok Tube Fitting Instructions
- 90 Main Loop
- 91 Engineering Loop
- 92 Factory Reset
- 93 FRU Exploded Views
- 96 Flow Diagram
- 97 Electrical Diagram