- No category
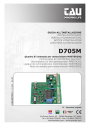
advertisement
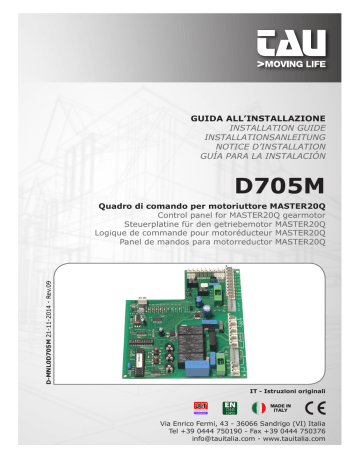
MANUFACTURER’S DECLARATION OF INCORPORATION
(in accordance with European Directive 2006/42/EC App. II.B)
Manufacturer:
Address:
TAU S.r.l.
Via E. Fermi, 43
36066 Sandrigo (Vi)
ITALY
Declares under its sole responsibility, that the product: designed for automatic movement of: for use in a: complete with:
Model:
Type:
Serial number:
Commercial name:
Electronic control unit
Sliding Gates
Communities / Industrial
Radioreceiver
D705M
D705M see silver label
Control panel for MASTER20Q gearmotor
Has been produced for incorporation on an access point (sliding gate) of for assembly with other devices used to move such an access point, to constitute a machine in accordance with the Machinery Directive 2006/42/EC.
Also declares that this product complies with the essential safety requirements of the following EEC directives:
- 2006/95/EC Low Voltage Directive
- 2004/108/EC Electromagnetic Compatibility Directive
and, where required, with the Directive:
- 1999/5/CE Radio equipment and telecommunications terminal equipment
Also declares that it is not permitted to start up the machine until the machine in which it is incorporated or of which it will be a component has been identified with the relative declaration of conformity with the provisions of
Directive 2006/42/EC.
The manufacturer undertakes to provide, on sufficiently motivated request by national authorities, all information pertinent to the quasi-machinery.
Sandrigo, 21/11/2014
Legal Representative
_________________________________________
Loris Virgilio Danieli
Name and address of person authorised to draw up all pertinent technical documentation:
Loris Virgilio Danieli - via E. Fermi, 43 - 36066 Sandrigo (Vi) Italy
12
D705M
WARNINGS
This manual has been especially written for use by qualified fitters. No information given in this manual can be considered as being of interest to end users. This manual is attached to the D705M control unit mounted on the MASTER20Q gearmotor, therefore it may not be used for different products!
Important information:
Disconnect the panel from the power supply before opening it.
The D705M control unit has been designed to control an electromechanical gear motor for automating gates and doors of all kinds.
Any other use is considered improper and is consequently forbidden by current laws.
Please note that the automation system you are going to install is classifi ed as “machine construction” and therefore is included in the application of European directive 2006/42/EC (Machinery Directive).
This directive includes the following prescriptions:
- Only trained and qualified personnel should install the equipment;
- the installer must first make a “risk analysis” of the machine;
- the equipment must be installed in a correct and workmanlike manner in compliance with all the standards concerned;
- after installation, the machine owner must be given the “declaration of conformity”.
This product may only be installed and serviced by qualified personnel in compliance with current, laws, regulations and directives.
When designing its products, TAU observes all applicable standards (please see the attached declaration of conformity) but it is of paramount importance that installers strictly observe the same standards when installing the system.
Unqualified personnel or those who are unaware of the standards applicable to the “automatic gates and doors” category may not install systems under any circumstances.
Whoever ignores such standards shall be held responsible for any damage caused by the system!
Do not install the unit before you have read all the instructions.
Installation
This product must be correctly installed by a qualified fitter. The maker declines all liability for damage caused by incapacity or neglect.
In particular:
1. make sure the cross-section of the power cables (power input, motors, earth and flashing light) is at least 1.5 mm² and, in any case, sufficient for the absorption and length of the wires. The above also applies to the other cables used by control and auxiliary devices except that the minimum cross-section is reduced to 0.5 mm²;
2. make connections to the terminal board so as not to alter the level of protection offered by the container which must be installed in a dry and protected place;
3. keep the power circuits separate from the control and auxiliary circuits, especially if the cables are long;
4. short any unused Normally Closed contacts.
The product must be properly earthed and the safety regulations in force in the country of installation must be observed.
D705M
13
CONTROL PANEL FOR 230 Vac SINGLE-PHASE MOTOR
• MICROPROCESSOR-CONTROLLED LOGIC
• INPUT STATUS LED’S
• LINE INPUT FUSE
• BUILT-IN FLASHING LIGHT CIRCUIT
• “MAN PRESENT” FUNCTION
• ELECTRIC BRAKING
• WEEKLY TIMER INPUT
• MOTOR TORQUE CONTROL AND OBSTACLE DETECTION BY MEANS OF ENCODER
• 433.92 MHz 2 CHANNEL BUILT-IN RADIO RECEIVER (CH)
• CONTROL OF THE SENSITIVE EDGE
ATTENTION:
-
- do not use single cables (with one single wire), ex. telephone cables, in order to avoid breakdowns of the line and false contacts.
do not re-use old pre-existing cables.
TESTING
When all connections have been made:
• All the green LED’s must be on (each corresponds to a Normally Closed input).
• They only turn off when the commands they are associated with are active.
• All the red LED’s must be off (each corresponds to a Normally Open input) they only turn on when the commands they are associated with are active.
TECHNICAL CHARACTERISTICS
Power input to board
Nominal power
Primary input line rapid fuse (F1 - 5x20)
Input voltage of motor circuits
Input voltage of auxiliary circuits
24Vac line rapid fuse (F2 - 5x20)
Logic circuit input voltage
Working temperature
Box protected to
230V AC - 50÷60Hz
600 W ca.
F3,15A - 250V AC
230V AC
24V AC
F1,6A - 250V AC
5V DC
-20°C ÷ + 55 °C
IP43
TERMINAL BOARD CONNECTIONS
Terminals
1 - 2
M1
M2
4 - 5 - 6
7 - 8
9 - 10
9 - 11
Function Description
POWER SUPPLY POWER input 230Vac, 50Hz, single-phase;
TRANSFORMER
transformer primary connector [ 2 white wires (230V) + 2 red wires (80V) ] ;
TRANSFORMER
MOTOR
transformer secondary connector [ (2 black wires (24V) + 2 blue wires (15V)] ;
MOTOR output single-phase 230Vac, 600 W, common=4, opening phase=5, closing phase=6, connect the capacitor between terminals 5 and 6;
FLASHING LIGHT
STOP
PEDESTRIAN
FLASHING LIGHT output 230 Vac 50 W max. The signal is already modulated for direct use. Flashing frequency during closing is doubl e. 7= 230 Vac, 8= 0 V
STOP button input (normally closed contact); this stops the automatic system. At the next command, the opposite operation to the previous one is performed (common=9);
PEDESTRIAN button input (normally open contact); partially opens the automatic system (by about 1 m) to allow pedestrians to pass by (common=9);
14
D705M
9 - 12
13 - 14
13 - 15
13 - 16
17 - 18
19 - 20
21 - 22
23 - 24
25 - 26
25 - 27
28 - 29
M3
M4
OPEN/CLOSE
OPEN
CLOSE
PHOTOCELL
FIXED SAFETY
EDGE
OPEN/CLOSE button input (contact normally open); for operating information see dip switch 2 - 4 and 10 functions (common=9);
OPEN button input (contact normally open); for operating information see dip switch 2 and 10 functions (common=13);
CLOSE button input (contact normally open); for operating information see dip switch 2 and 10 functions (common=13); input for PHOTOCELLS OR SAFETY DEVICES active during closure (Normally Closed contact); They stop the gate during closing and totally reopen it; they temporarily stop the gate during opening in order to allow the obstacle to be removed (if dip switch n° 3 set to ON), (13= Common). If there is more than one safety device, connect all the NC contacts IN SERIES.
SENSITIVE EDGE input (resistive sensitive edge or fixed safety edge);
Works only when the gate is opening; temporarily stops the gate and partially closes it by about 20 cm in order to allow the obstacle to be removed. (17=Common);
Note: if a resistive sensitive edge is connected, short jumper
J1;
If a fixed edge with NC contact is connected, leave jumper
J1 open;
not connected ;
2 nd
RADIO CH
PHOTOCELL TX
PHOTOCELL
GATE OPEN
WARNING LIGHT
ANTENNA
FCC - FCA
ENCODER
2 nd
RADIO CHANNEL output (its operation depends on dipswitches nos. 7 - 8) to be used for opening/closing another gate, for controlling garden lights or for the “ZONE LIGHTING” function;
Warning: to connect other devices to the 2nd Radio Channel
(area lighting, pumps, etc.), use an additional auxiliary relay.
24 Vac 10 W POWER output for PHOTOCELL TX (only the one that performs the Phototest) max. no. 1 photocell transmitter. 23=
24 Vac, 15= 24 Vac;
Note: the photocell transmitter must always be supplied by terminals no. 23 - 24, since the safety system test (phototest) is carried out on it. To override the testing of the safety system, or when the photocells are not used, set dip-switch no.
6 to OFF. If the phototest is not successful, the control unit will not operate;
24 Vac 10 W output to POWER THE RXs AND ANY OTHER TXs
OF PHOTOCELLS THAT ARE PRESENT, EXTERNAL RECEIV-
ERS, etc.; connect a max. of 3 pair of photoce lls. 25= 0 V, 26=
24 Vac;
GATE OPEN WARNING LIGHT output 24 Vac - max. 3 W; during opening of the gate the warning light flashes slowly, when the gate is open it remains steadily illuminated and during closure it flashes twice as fast.
Turns off when the CLOSING LIMIT
SWITCH (CLS) is reached.
25= 0 V, 27= 24 Vac;
ANTENNA input (earth=28, signal=29);
(FCC) CLOSE LIMIT SWITCH input (normally closed contact);
(FCA) OPEN LIMIT SWITCH input (normally closed contact);
SAFETY MICROSWITCH input (normally closed contact), the motor stops when the guard is removed.
WARNING: the control unit is still live!
quick coupling for ENCODER connection.
Blue= 0 Vdc (GND), brown= 5 Vdc (+5V), white= ENCODER
SIGNAL (ENC);
D705M
15
LOGIC ADJUSTMENTS
TRIMMER
T.L.
T.C.A.
FR.
decrease.
Work Time adjustment: from approx. 5 to 240 seconds;
Automatic Closing Time adjustment: from approx. 5 to 120 seconds (see dip switch 1); obstacle detection sensitivity adjustment.
Note: turn the TRIMMER clockwise to increase adjustments; turn it anticlockwise to
Dip switch
1
2
AUTOMATIC
CLOSING
2 / 4 STROKE
T.C.A. trimmer expires;
Off a command is required to close the gate;
On
with automatic closing enabled, a sequence of open/close commands causes the gate to OPENCLOSE-OPEN-CLOSE etc (see also dip switch 4).
3
4
OPENING
PHOTOCELLS
OPERATION
NO REVERSE
Off during opening, the photocell does not cut in.
NO-REVERSE function activated; the gate ignores the closure com-
On
mands during opening and reversal of movement occurs only during closure;
5
ENCODER
Off ENCODER disabled;
On pre-flashing and “photocell test” function enabled;
6
PREFLASH. &
FOTOTEST
when the photocells are not used.
7 - 8 2nd RADIO CHANNEL operation (terminals no. 18 - 19)
Dip 7 Dip 8 Function
Gate contact open: The contact activates on opening the gate and remains ac-
Off Off
tive during the open time, during the TCA and during reclosure. It deactivates once the gate has completed its closure movement.
Off
On
On
9
BRAKING
On braking enabled;
Off braking disabled;
Note: the braking system activates whenever the motor must stop (CLS - OLS - STOP – change of direction) and reduces the inertia accumulated by the gear motor during movement.
16
D705M
10
MAN
PRESENT
On
Off
Man Present; the automation system will continue to open or close as long as the OPEN or CLOSE buttons are held down. The gear motor will stop when the button is released; normal (or pulse); when the OPEN, CLOSE or the PP button is pushed, the automatic system performs a complete opening or closing manoeuvre;
Note: in the Man Present mode, the PP input (n° 12) is disabled, as is the radio receiver.
J1 jumper inserted: resistive sensitive edge;
jumper not inserted: fixed edge with NC contact.
ADVANCED FUNCTIONS
Clock function: a timer can be connected to the open-close pushbutton in order to keep the gate open at certain times during the day, after which it reverts to automatic closing.
The gate remains open as long as the Op/Cl input continues to be activated.
“Gate open contact” function: when dipswitch 7 and dipswitch 8 are set to OFF, the second radio channel (terminals no. 18 - 19) will act as a voltage-free contact to indicate when the gate is open. This function can be used to connect “ZONE LIGHTING” or as a gate open indicator.
“Pedestrian with 2nd radio ch.” function: when drop contacts G1 and G2 are closed and when dipswitch 7 is ON and 8 is OFF, the second radio channel can be used to make the pedestrian opening.
433.92 MHz BUILT-IN RADIO RECEIVER
The radio receiver can learn up to a maximum of 30 dip-switches (TXD2, TXD4, BUG2, BUG4, K-SLIM,
K-SLIM-C, T-4, T-4C) or rolling codes (BUG2R, BUG4R, K-SLIM-RP, T-4RP) which can be set on the two channels as required.
The first channel directly commands the control board for opening the automatic device; the second channel commands a relay for a N.O. no-voltage output contact (terminals 18 and 19, max. 24 Vac, 1 A).
The learning mode (dip-switch or rolling code) is determined by the first radio control device and remains unchanged until all the codes have been cancelled.
LEARNING SYSTEM FOR RADIO CONTROL DEVICES
P1 = OPEN/CLOSE
P2 = 2nd channel
1_ press button P1 briefly to associate a radio control device with the OPEN/CLOSE function;
2_ LED DL8 turns off to indicate that the code learning mode has been activated (if no code is entered within 10 seconds, the board exits the programming mode);
3_ press the button of the relative radio control device;
4_ LED DL8 turns on again to indicate that the code has been memorised (if this does not happen, wait 10 seconds and start again from point 1);
5_ to memorise codes to other radio control devices, repeat the procedure from point 1 up to a maximum of 30 transmitters;
6_ to memorise codes on the 2nd channel, repeat the procedure from point 1 using button P2 instead of P1;
7_ to exit the learning mode without memorising a code, press button P1 or P2 briefly.
If the maximum number of radio controls is reached (30), the LED DL8 will begin to flash rapidly for about 3 seconds but without performing memorisation.
REMOTE PROGRAMMING BY MEANS OF T-4RP and K-SLIM-RP (V 4.X)
With the new version of software V 4.X it is possible to carry out the remote self-learning of the new version of transmitters T-4RP and K-SLIM-RP (V 4.X), that is without pressing the receiver’s programming buttons.
D705M
17
It will be sufficient to have an already programmed transmitter in the receiver in order to start the procedure of remote programming of the new transmitters. Follow the procedure written on the instructions of the transmitter T-4RP and K-SLIM-RP (V 4.X).
CANCELLING CODES FROM RADIO CONTROL DEVICES
1_ keep button P1 pressed for 3 seconds in order to cancel all the associated radio control devices;
2_ LED DL8 flashes slowly to indicate that the cancellation mode has been activated;
3_ press button P1 again for 3 seconds;
4_ LED DL8 turns off for approx. 3 seconds and then remains steady to indicate that the code has been cancelled;
5_ repeat the procedure from point 1 using button P2 to cancel all the associated radio control devices;
6_ to exit the learning mode without memorising a code, press button P1 or P2 briefly.
ATTENTION: TO memorise a code on a new type of remote control unit (e.g.: from dipswitch to rolling code or vice-versa) both channels must be cancelled.
DIAGNOSTICS LED
DL1 (STOP)
DL2 (PEDESTRIAN)
DL3 (STEP BY STEP)
DL4 (OPEN)
DL5 (CLOSE)
DL6 (SENSITIVE EDGE)
DL7 (PHOTOCELL)
DL8 (CLOSE LIMIT SWITCH)
DL9 (OPEN LIMIT SWITCH)
DL10 (RADIO CONTROLS)
STOP button green LED signal
PEDESTRIAN button red LED signal
STEP BY STEP button red LED signal
OPEN button red LED signal
CLOSE button red LED signal
SENSITIVE EDGE green LED signal
PHOTOCELL green LED signal
CLOSE LIMIT SWITCH green LED signal
OPEN LIMIT SWITCH green LED signal
RECEIVER PROGRAMMING INFORMATION and ERRORS red LED signal
LED - DL10
Led DL10, as well as the normal radio control programming signals, also indicates any errors with a series of pre-set flashes:
2 flashes: phototest error;
Disable phototest (dip-switch 6 OFF), check operation and connection of photocells;
5 flashes: absence of encoder signal;
Check wiring, check encoder through TEST-ENCODER (optional);
6 flashes: presence of obstacle after 5 failed attempts to close;
Make sure there are no obstacles across the path of the gate and that it slides smoothly;
The display of multiple errors is shown with a pause of 2 seconds between one message and the next. The error remains on display until a new complete manoeuvre (open and close) is performed by the automation.
In the event of 5 consecutive activations (during the same closing manoeuvre) of the encoder (obstacle detection), the control unit opens completely on the next manoeuvre. To reset, the automation must complete a manoeuvre (opening and then closing); otherwise the end stop search process will be repeated after each activation of the encoder.
18
D705M
MALFUNCTIONS: POSSIBLE CAUSES AND SOLUTION
The automation does not start
a_ Check there is 230Vac power supply with the multimeter; b_ Check that the NC contacts of the card are actually normally closed (5 green LEDs on); c_ Check that the red LED DL10 is steadily illuminated; d_ Set the dip 3 (man present function) to OFF, dip 5 (encoder) to ON, dip 6 (phototest) to OFF; e_ Check that the fuses are intact with the multimeter.
The radio control has very little range
a_ Check that the ground and the aerial signal connections have not been inverted; b_ Do not make joints to increase the length of the aerial wire; c_ Do not install the aerial in a low position or behind walls or pillars; d_ Check the state of the radio control batteries.
The gate opens the wrong way
a_ Invert the motor phase wires (terminals 5 - 6) and also those of the limit switches (red and orange wires).
GUARANTEE: GENERAL CONDITIONS
TAU guarantees this product for a period of 24 months from the date of purchase (as proved by the sales document, receipt or invoice).
This guarantee covers the repair or replacement at TAU’s expense (ex-works TAU: packing and transport at the customer’s expense) of parts that TAU recognises as being faulty as regards workmanship or materials.
For visits to the customer’s facilities, also during the guarantee period, a “Call-out fee” will be charged for travelling expenses and labour costs.
The guarantee does not cover the following cases:
• If the fault was caused by an installation that was not performed according to the instructions provided by the company inside the product pack.
• If original TAU spare parts were not used to install the product.
• If the damage was caused by an Act of God, tampering, overvoltage, incorrect power supply, improper repairs, incorrect installation, or other reasons that do not depend on TAU.
• If a specialised maintenance man does not carry out routine maintenance operations according to the instructions provided by the company inside the product pack.
• Wear of components.
The repair or replacement of pieces under guarantee does not extend the guarantee period.
In case of industrial, professional or similar use, this warranty is valid for 12 months.
D705M
19
advertisement
* Your assessment is very important for improving the workof artificial intelligence, which forms the content of this project
Related manuals
advertisement
Table of contents
- 2 Wiring Diagram
- 4 Italiano
- 4 Dichiarazione di incorporazione
- 12 English
- 12 Manufacturer's declaration of incorporation
- 20 Deutsch
- 20 Integrierungserklärung des Herstellers
- 29 Français
- 29 Déclaration d'incorporation du fabricant
- 38 Español
- 38 Declaración de incorporación del fabricante
- 48 Estensione Garanzia