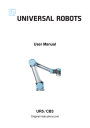
advertisement
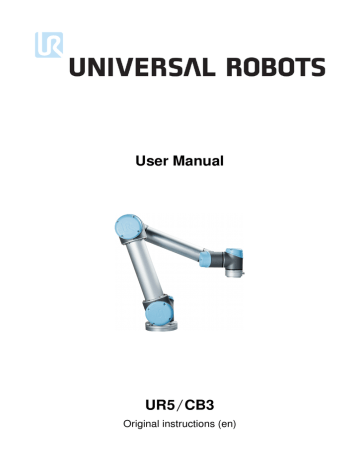
1 Safety
1.1
Introduction
This chapter contains important safety information, which must be read and understood by the integrator of UR robots.
The first subsections in this chapter are more general and the later subsections contain more specific engineering data relevant for setting up and programming the robot.
It is essential that all assembly instructions and guidance provided in other chapters and parts of this manual are observed and followed.
Special attention shall be paid to text associated with warning symbols. See Chap-
ter 5 for detailed descriptions of the safety-related functions and interfaces.
1.2
Validity and Responsibility
The information does not cover how to design, install and operate a complete robot application, nor does it cover all peripheral equipment that can influence the safety of the complete system. The complete system must be designed and installed in accordance with the safety requirements set forth in the standards and regulations of the country where the robot is installed.
The integrators of UR robots are responsible for ensuring that the applicable safety laws and regulations in the country concerned are observed and that any significant hazards in the complete robot application are eliminated.
This includes, but is not limited to:
• Making a risk assessment for the complete system;
• Interfacing other machines and additional safety devices if defined by the risk assessment;
• Setting up the appropriate safety settings in the software;
• Ensuring that the user will not modify any safety measures;
• Validating that the total system is designed and installed correctly;
• Specifying instructions for use;
• Marking the robot installation with relevant signs and contact information of the integrator;
• Collecting all documentation in a technical file.
Guidance on how to find and read applicable standards and laws is provided on http://support.universal-robots.com/
Version 3.1
(rev. 17782) I-3 UR5 /CB3
1.4 Warning Symbols in this Manual
1.3
Limitation of Liability
Any information given in this manual regarding safety must not be construed as a warranty by UR that the industrial manipulator will not cause injury or damage even if all safety instructions are complied with.
1.4
Warning Symbols in this Manual
The table below defines the captions specifying the danger levels used throughout this manual. The same warning signs are used on the product.
DANGER:
This indicates an imminently hazardous electrical situation which, if not avoided, could result in death or serious injury.
DANGER:
This indicates an imminently hazardous situation which, if not avoided, could result in death or serious injury.
WARNING:
This indicates a potentially hazardous electrical situation which, if not avoided, could result in injury or major damage to the equipment.
WARNING:
This indicates a potentially hazardous situation which, if not avoided, could result in injury or major damage to the equipment.
WARNING:
This indicates a potentially hazardous hot surface which, if touched, could result in injury.
CAUTION:
This indicates a situation which, if not avoided, could result in damage to the equipment.
UR5 /CB3 I-4 Version 3.1
(rev. 17782)
1.5 General Warnings and Cautions
1.5
General Warnings and Cautions
This section contains some general warnings and cautions. Some of which are repeated or explained in different parts of the manual. Other warnings and cautions are present throughout the manual.
DANGER:
Make sure to install the robot and all electrical equipment accord-
ing to the specifications and warnings found in the Chapters 3 and
Version 3.1
(rev. 17782)
WARNING:
1. Make sure the robot arm and tool are properly and securely bolted in place.
2. Make sure the robot arm has ample space to operate freely.
3. Make sure that safety measures and/or robot safety configuration parameters have been set up to protect both programmers, operators and bystanders, as defined in the risk assessment.
4. Do not wear loose clothing or jewellery when working with the robot. Make sure long hair is tied back when working with the robot.
5. Never use the robot if it is damaged.
6. If the software prompts a fatal error, immediately activate emergency stop, write down the conditions that led to the error, find the corresponding error codes on the log screen, and contact your supplier.
7. Do not connect any safety equipment to normal I/O. Use safety-related interfaces only.
8. Make sure to use the correct installation settings (e.g. Robot mounting angle, weight in TCP, TCP offset, safety configuration). Save and load the installations file along with the program.
9. The freedrive function (Impedance/back-drive) shall only be used in installations where the risk assessment allows it. Tools and obstacles shall not have sharp edges or pinch points. Make sure that all people keep their heads and faces outside the reach of the robot.
10. Be aware of robot movement when using the teach pendant.
11. Do not enter the safety range of the robot or touch the robot when the system is in operation.
I-5 UR5 /CB3
UR5 /CB3
1.5 General Warnings and Cautions
11. Collisions can release high portions of kinetic energy, which are significantly higher at high speeds and with high payloads. (Kinetic Energy =
1
2
Mass
·
Speed
2
)
12. Combining different machines might increase hazards or create new hazards. Always make an overall risk assessment for the complete installation. When different safety and emergency stop performance levels are needed, always choose the highest performance level. Always read and understand the manuals for all equipment used in the installation.
13. Never modify the robot. A modification might create hazards that are unforeseen by the integrator. All authorized reassembling shall be done according to the newest version of all relevant service manuals. UNIVERSAL ROBOTS DIS-
CLAIMS ANY LIABILITY IF THE PRODUCT IS CHANGED
OR MODIFIED IN ANY WAY.
14. If the robot is purchased with an extra module (e.g. euromap67 interface) then look up that module in the respective manual.
WARNING:
1. The robot and controller box generate heat during operation.
Do not handle or touch the robot while in operation or immediately after operation. To cool the robot down, power off the robot and wait one hour.
2. Never stick fingers behind the internal cover of the controller box.
CAUTION:
1. When the robot is combined with or working with machines capable of damaging the robot, then it is highly recommended to test all functions and the robot program separately. It is recommended to test the robot program using temporary waypoints outside the workspace of other machines.
Universal Robots cannot be held responsible for any damages caused to the robot or to other equipment due to programming errors or malfunctioning of the robot.
2. Do not expose the robot to permanent magnetic fields. Very strong magnetic fields can damage the robot.
I-6 Version 3.1
(rev. 17782)
1.6 Intended Use
1.6
Intended Use
UR robots are industrial and intended for handling tools and fixtures, or for processing or transferring components or products. For details about the environmen-
tal conditions under which the robot should operate, see appendices B and D.
UR robots are equipped with special safety-related features, which are purposely designed for collaborative operation, where the robot operates without fences and/or together with a human.
Collaborative operation is only intended for non-hazardous applications, where the complete application, including tool, work piece, obstacles and other machines, is without any significant hazards according to the risk assessment of the specific application.
Any use or application deviating from the intended use is deemed to be impermissible misuse. This includes, but is not limited to:
• Use in potentially explosive environments;
• Use in medical and life critical applications;
• Use before performing a risk assessment;
• Use where the rated performance levels are insufficient;
• Use where the reaction times of the safety functions are insufficient;
• Use as a climbing aid;
• Operation outside the permissible operating parameters.
1.7
Risk Assessment
One of the most important things that an integrator needs to do is to make a risk assessment. The robot itself is partly completed machinery, as the safety of the robot installation depends on how the robot is integrated (E.g. tool, obstacles and other machines).
It is recommended that the integrator uses guidelines in ISO 12100 and ISO 10218-2 to conduct the risk assessment.
The risk assessment shall consider two scenarios:
• Teaching the robot while developing the robot installation;
• Normal operation of the robot installation.
If the robot is installed in a non-collaborative installation (E.g. when using a hazardous tool) the risk assessment might conclude that the integrator needs to connect additional safety devices (E.g. an enable device) to protect him while programming.
Universal Robots has identified the potential significant hazards listed below as hazards which must be considered by the integrator. Note that other significant hazards might be present in a specific robot installation.
Version 3.1
(rev. 17782) I-7 UR5 /CB3
1.9 Movement Without Drive Power
1. Entrapment of fingers between robot foot and base (joint 0).
2. Entrapment of fingers between wrist 1 and wrist 2 (joint 3 and joint 4).
3. Penetration of skin by sharp edges and sharp points on tool or tool connector.
4. Penetration of skin by sharp edges and sharp points on obstacles near the robot track.
5. Bruising due to stroke from the robot.
6. Sprain or bone fracture due to strokes between a heavy payload and a hard surface.
7. Consequences due to loose bolts that hold the robot arm or tool.
8. Items falling out of tool, e.g. due to a poor grip or power interruption.
9. Mistakes due to different emergency stop buttons for different machines.
Information on stopping times and stopping distances are found in appendix A.
1.8
Emergency Stop
Activate the emergency stop button to immediately stop all robot motion.
Emergency stop shall not be used as a risk reduction measure, but as a secondary protective device.
The risk assessment of the robot application shall conclude if more emergency stop buttons must be connected. Emergency stop buttons should comply with IEC
60947-5-5, see more in section 4.3.2.
1.9
Movement Without Drive Power
In the unlikely event of an emergency situation where one or more robot joints need to be moved and robot power is either not possible or unwanted, there are two different ways to force movements of the robot joints:
1. Forced back-driving: Force a joint to move by pushing or pulling the robot arm hard (500 N). Each joint brake has a friction clutch which enables movement during high forced torque.
2. Manual brake release: Remove the joint cover by removing the few M3 screws that fix it. Release the brake by pushing the plunger on the small electromagnet as shown in the picture below.
WARNING:
1. Moving the robot arm manually is intended for urgent emergencies only and might damage the joints.
2. If the brake is released manually, gravitational pull can cause the robot arm to fall. Always support the robot arm, tool and work item when releasing the brake.
UR5 /CB3 I-8 Version 3.1
(rev. 17782)
1.9 Movement Without Drive Power
Version 3.1
(rev. 17782) I-9 UR5 /CB3
1.9 Movement Without Drive Power
UR5 /CB3 I-10 Version 3.1
(rev. 17782)
advertisement
* Your assessment is very important for improving the workof artificial intelligence, which forms the content of this project
Related manuals
advertisement
Table of contents
- 11 Preface
- 11 What do the Boxes Contain
- 11 Important Safety Notice
- 11 How to Read This Manual
- 11 Where to Find More Information
- 13 I Hardware Installation Manual
- 15 Safety
- 15 Introduction
- 15 Validity and Responsibility
- 15 Limitation of Liability
- 16 Warning Symbols in this Manual
- 16 General Warnings and Cautions
- 18 Intended Use
- 19 Risk Assessment
- 20 Emergency Stop
- 20 Movement Without Drive Power
- 23 Transportation
- 25 Mechanical Interface
- 25 Workspace of the Robot
- 25 Mounting
- 29 Electrical Interface
- 29 Introduction
- 29 Electrical warnings and cautions
- 30 Controller I/O
- 31 Common specifications for all digital I/O
- 32 Safety I/O
- 33 Default safety configuration
- 34 Connecting emergency stop buttons
- 34 Sharing emergency stop with other machines
- 35 Safeguard stop with automatic resume
- 35 Safeguard stop with reset button
- 36 General purpose digital I/O
- 36 Load controlled by a digital output
- 36 Digital input from a button
- 36 Communication with other machines or PLCs
- 37 General purpose analog I/O
- 38 Using an analog output
- 38 Using an Analog Input
- 39 Remote ON/OFF control
- 39 Remote ON button
- 40 Remote OFF button
- 40 Tool I/O
- 41 Tool Digital Outputs
- 41 Using the Tool Digital Outputs
- 42 Tool Digital Inputs
- 42 Using the Tool Digital Inputs
- 42 Tool Analog Inputs
- 42 Using the Tool Analog Inputs, Non-differential
- 43 Using the Tool Analog Inputs, Differential
- 43 Ethernet
- 43 Mains connection
- 45 Robot connection
- 47 Safety-related Functions and Interfaces
- 47 Limiting Safety-related Functions
- 49 Safety Modes
- 49 Safety-related Electrical Interfaces
- 49 Safety-related Electrical Inputs
- 51 Safety-related Electrical Outputs
- 53 Maintenance and Repair
- 53 Safety Instructions
- 55 Disposal and Environment
- 57 Certifications
- 57 Third Party Certifications
- 57 Declarations According to EU directives
- 59 Warranties
- 59 Product Warranty
- 59 Disclaimer
- 61 Stopping Time and Stopping Distance
- 61 CATEGORY 0 stopping distances and times
- 63 Declarations and Certificates
- 63 CE Declaration of Incorporation (original)
- 63 Safety System Certificate
- 64 Environmental Test Certificate
- 66 EMC Test Certificate
- 67 Applied Standards
- 73 Technical Specifications
- 75 II PolyScope Manual
- 77 Introduction
- 77 Getting Started
- 77 Installing the Robot Arm and Control Box
- 78 Turning the Control Box On and Off
- 78 Turning the Robot Arm On and Off
- 78 Quick Start
- 79 The First Program
- 80 PolyScope Programming Interface
- 81 Welcome Screen
- 82 Initialization Screen
- 85 On-screen Editors
- 85 On-screen Keypad
- 85 On-screen Keyboard
- 86 On-screen Expression Editor
- 87 Pose Editor Screen
- 91 Robot Control
- 91 Move Tab
- 91 Robot
- 92 Feature and Tool Position
- 92 Move Tool
- 92 Move Joints
- 92 Freedrive
- 93 I/O Tab
- 94 MODBUS client I/O
- 94 AutoMove Tab
- 95 Installation Load/Save
- 96 Installation TCP Configuration
- 97 Adding, modifying and removing TCPs
- 97 The default and the active TCP
- 98 Teaching TCP position
- 98 Teaching TCP orientation
- 99 Payload
- 99 Center of gravity
- 99 Installation Mounting
- 101 Installation I/O Setup
- 102 Installation Safety
- 102 Installation Variables
- 103 Installation MODBUS client I/O Setup
- 105 Installation Features
- 109 Conveyor Tracking Setup
- 110 Installation Default Program
- 110 Loading a Default Program
- 111 Starting a Default Program
- 111 Auto Initialization
- 111 Log Tab
- 112 Load Screen
- 114 Run Tab
- 117 Programming
- 117 New Program
- 117 Program Tab
- 118 Program Tree
- 118 Program Execution Indication
- 119 Undo/Redo Buttons
- 119 Program Dashboard
- 120 Variables
- 121 Command: Empty
- 121 Command: Move
- 124 Command: Fixed Waypoint
- 126 Command: Relative Waypoint
- 127 Command: Variable Waypoint
- 128 Command: Wait
- 129 Command: Set
- 130 Command: Popup
- 130 Command: Halt
- 131 Command: Comment
- 131 Command: Folder
- 132 Command: Loop
- 133 Command: SubProgram
- 134 Command: Assignment
- 135 Command: If
- 135 Command: Script
- 136 Command: Event
- 137 Command: Thread
- 138 Command: Pattern
- 140 Command: Force
- 142 Command: Pallet
- 144 Command: Seek
- 147 Command: Start/Stop Conveyor Tracking
- 148 Command: Suppress
- 148 Graphics Tab
- 149 Structure Tab
- 150 Variables Tab
- 150 Command: Variables Initialization
- 153 Setup Screen
- 153 Language and Units
- 154 Update Robot
- 155 Set Password
- 156 Calibrate Screen
- 157 Setup Network
- 158 Set Time
- 159 Safety Configuration
- 160 Changing the Safety Configuration
- 160 Safety Synchronization and Errors
- 161 Tolerances
- 162 Safety Checksum
- 162 Safety Modes
- 163 Freedrive Mode
- 163 Password Lock
- 163 Apply
- 164 General Limits
- 166 Joint Limits
- 168 Boundaries
- 169 Selecting a boundary to configure
- 169 3D visualization
- 170 Safety plane configuration
- 173 Tool Boundary configuration
- 174 Safety I/O
- 177 Glossary
- 179 Index