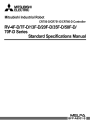
advertisement
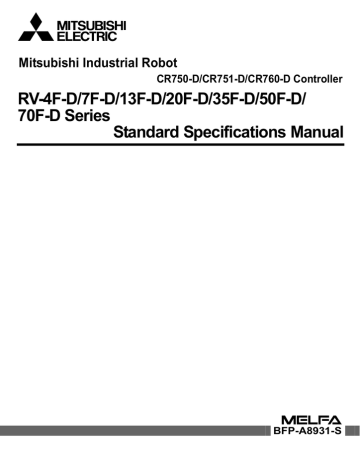
3 Controller
3.6.3 Door switch function
This function retrieves the status of the switch installed on the door of the safety fence, etc., and stops the robot when the door is opened. This differs from an emergency stop in that the servo turns OFF when the door is opened and an error does not occur. Follow the wiring example shown in
Page 134 "Fig. 3-18: External emergency stop connection (CR750)" ,
Page 138 "Fig. 3-22: External emergency stop connection (CR751)" , or Page 141 "Fig.
3-25: External emergency stop connection (CR760)" , and
Page 211, "6.1.7 Examples of safety measures"
. Those figure explains the wire is contact closes when the door is closed. Details of this function according to the robot status are shown below.
*During automatic operation .............. When the door is opened, the servo turns OFF and the robot stops. An error occurs. The process of the restoration: Close the door, reset the alarm, turn on the servo, and restart
*During teaching........................................ Even when the door is opened, the servo can be turned ON and the robot moved using the teaching pendant.
① Auto executing
Safeguard
STOP!!
(Op.) (Ext.)
Open
Robot arm
(Example)
Turns OFF the servo
② Teaching
Safeguard
AUTO
MANUAL
AUTO
AUTOMATIC
Open
Robot arm
(Example)
Teaching
pendant
The servo can be turned ON/Off by turning the enable switch ON/OFF.
Fig.3-29 : Door switch function
3.6.4 Enabling device function
When the abnormalities occur in teaching operations etc., the robot's servo power can be immediately cut only by switch operation of the enabling device
*1)
(servo-off), and the safety increases. To use the robot safely, please be sure to connect the enabling device.
(1) When door is opening
Please do teaching by two-person operations. One person has T/B, the other has enabling device. Turn on the servo power, in the condition that both of switches are pushed. (Enable switch of T/B and enabling device) Then the jog operation will be available. You can off the servo power only by releasing the switch of the enabling device.
And, care that the servo-on and releasing the brake cannot be done in the condition that the switch of the enabling device is released.
(2) When door is closing
You can turn on the servo power by operation of only T/B. In this case perform jog operation outside the safeguard sure.
*1) Recommendation products: HE1G-L20MB (IDEC)
Emergency stop input and output etc. 3-144
3 Controller
(3) Automatic Operation/Jog Operation/Brake Release and Necessary Switch Settings
The following is a description of various operations performed on the robot and switch settings that are required.
Table 3-6 : Various operations and necessary switch settings
Related switch settings
Note1)
No
2
3
4
Operation
1 Jog operation
Jog operation
Note2)
Brake release
Note3)
Automatic operation
Mode of controller
Manual
Manual
Manual
Automatic
T/B enable/ disable
Enable
Enable
Enable
Disable
T/B enable switch
ON
ON
ON
-
Enabling device input terminal
Door switch input terminal
Close(ON)
Open(OFF)
Close(ON)
-
Description
-
Close
(Door Close)
-
Close
(Door Close)
If the enabling device input is set to
Close (On), the state of door switch input does not matter.
If the enabling device input is set to
Open (Off), door switch input must be in a state of Close
Irrespective of the state of door switch input, enabling device input must be in a state of Close (On).
Door switch input must always be in a state of Close (Door Close).
Note1) "-" in the table indicates that the state of switch concerned does not matter.
Refer to the following for operation of each switch.
・ Mode of CR750 controller:
Mode of CR751 controller:
Mode of CR760 controller:
・ T/B enable/disable:
・ T/B enable switch:
・ Enabling device input terminal:
.................................................Page 211, "6.1.7 Examples of safety measures"
・ Door switch input terminal:
Note2) Jog operation, if door switch input is set for Close (Door Close), must be performed outside the safety bar
rier.
Note3) It is imperative that brake release operation be carried out by two persons. One person turns on the enabling device ("Close" on the enabling device input terminal) while the other manipulates the T/B. Brake release can be effected only when both of the enabling switch device and the T/B enable switch are placed in intermediate position (lightly gripped position). At this point, the state of door switch input does not mat
ter.
T/B being manipulated
CAUTION
Door in
Open state
Upon the release of brake, the robot arm may fall under its own weight depending on the axis which has been released. For added safety, provide support or take other precaution to prevent the falling of the arm.
Enabling device being manipulated
Fig.3-30 : Brake release operation
3-145
Emergency stop input and output etc.
3 Controller
3.7 Mode changeover switch input
Connect the key switch of customer prepared and change the right of robot’s operation by switch operation.
The key switch can be installed in the operation panel of customer preparation.
<Right of operation (mode)>
AUTOMATIC ......................The operation from external equipment becomes available. Operation which needs the right of operation from T/B cannot be performed. It is necessary to set the parameter for the rights of operation to connection with external equipment. Refer to the separate volume, "Instruction Manual/Detailed Explanation of Functions and
Operations" for detail.
MANUAL ..............................When T/B is available, only the operation from T/B becomes available. Operation which needs the right of operation from external equipment cannot be performed.
MANUAL
MODE
AUTOMATIC
* The controller is an example.
Mode changeover switch
(Customer-prepared)
Fig.3-31 : Mode changeover switch image figure (CR751)
CNUSR1
(1) Specification of the key switch interface
The function and specification of the key switch interface are shown below.
Table 3-7 : Function of the key switch interface
Pin number and Function (Connector: CNUSR1)
Change mode
Note1)
Pin number
49
24
50
25
Function
1st line KEY input
Power supply +24V of pin num
ber 49
2nd line KEY input
Power supply +24V of pin num
ber 50
MANUAL
Open
Open
AUTOMATIC
Close
Close
Note1) The mode changes by both opening or both closing between 49-24 pin and between 50-25 pin.
When input states differ between two lines, error H0044 (OP Mode key line is faulty) will occur.
[Note] In the customer's system, do not ground the + side of 24V power supply prepared by customer for connect to the controller. (related with emergency stop and parallel input/output) If it connects with the controller under the condi
tion that the + side is grounded, it will lead to failure of controller.
Table 3-8 : Specification of the mode changeover switch input
Rated voltage
Current rating
Input resistance
Response time (OFF->ON)
Common method
Connection method
Conformity electric wire size
Maker/Type
Item Specification
DC24V
Approx. 10mA
Approx. 2.2kΩ
Approx. 15ms
1 point per common
Connector
AWG#24 to #18
-
Remarks
Supply from the controller.
Select the switch or button which operates normally in 24V/10mA.
Example: The response time the program starts, after pushing the run button.
0.2 to 0.75mm
2
Maker: PHOENIX CONTACT/ Type: FKC2.5/4-STF-5.0B
Mode changeover switch input 3-146
3 Controller
(2) Connection of the mode changeover switch input
* The controller is an example.
Cover fixing screw (Two places)
Connector cover
Plug
CNUSR1
25
View A
Pin number of plug
1
Remove the connector cover
Connector for user wiring
50
Soldering
26
A
3mm
Connecting cable
(AWG #30 ~ #24(0.05mm
2
to 0.2mm
2
))
Connection procedure
Solder the user wiring connector that accompanies the product to the corresponding pin, and connect it to the
CNUSR1 connector at the back of the controller. For the connection cable, please use AWG #30 to 24 (0.05 to
0.2mm
2
).
1) Loosen the 2 fixing screws on the user wiring connector that accompanies the product, and remove the con
nector cover.
2) Peel the insulation of the connecting cable to 3mm, and solder it the appropriate connector pin number.
3) After the necessary cable has been soldered, re-fix the connector cover sing the same fixing screws and make sure it is fastened securely.
4) Connect the connector to the corresponding connector (CNUSR1) on the controller. With pin number 1 facing to the upper right, insert firmly until you hear the connector’s latch click in to place.
This concludes the connection procedure.
Fig.3-32 : Connection of the mode changeover switch input (CR751)
3-147
Mode changeover switch input
3 Controller
3.8 Additional Axis Function
This controller is equipped with an additional axis interface for controlling an additional axis when a traveling axis or rotary table is added to the robot. A maximum of eight axes of servo motors can be controlled at the same time by connecting a general-purpose servo amplifier (MR-J3-B, MR-J4-B series) that supports Mitsubishi's SSCNET III.
Refer to the separate "Additional axis interface Instruction Manual" for details on the additional axis function.
3.8.1 Wiring of the Additional Axis Interface
shows the connectors for additional axes inside the controller.
and
Fig. 3-34 (CR760) shows a connection example (configuration example).
Table 3-9 : Dedicated connectors inside the controller
Name Connector name
Connector for additional axes CR750/CR751: ExtOpt
CR760: OPT2
Details
The connector for connecting the general-purpose servo amplifier.
(1) CR750 controller
ExtOPT
Emergency stop output
(Refer to "3.6Emergency stop input and output etc." )
* Connect with a forced stop input of a servo ampli
fier.
Magnet contactor control connector output (AXMC) for addition axes
(Refer to "3.9Magnet contactor control connector output (AXMC) for addition axes" )
To CN1A
To CN1B
To CN1A
To CN1B
Fig.3-33 : Example of addition axis connection (CR750)
Additional Axis Function 3-148
3 Controller
(2) CR751 controller
* The controller is an example.
ExtOPT
Emergency stop output
(Refer to "3.6Emergency stop input and output etc."
)
* Connect with a forced stop input of a servo amplifier.
Magnet contactor control connector output (AXMC) for addition axes
(Refer to "3.9Magnet contactor control connector output
)
To CN1A con
-
To CN1B
To CN1A
To CN1B connector
Fig.3-34 : Example of addition axis connection (CR751)
3-149
Additional Axis Function
(3) CR760 controller
3 Controller
Emergency stop output
(Refer to "3.6Emergency stop input and output etc."
)
* Connect with a forced stop input of a servo amplifier.
EMG1
EMG2
Magnet contactor control connector output
(AXMC) for addition axes
(Refer to "3.9Magnet contactor control connector output (AXMC) for addition axes"
)
R760CPU unit
R700CPUユニット
OPT2 connector
OPT2コネクタ
SSCNETⅢケーブル
To CN1A connector
CN1Aコネクタへ
サーボアンプ
OPTコネクタへ
To CN1B
CN1Bコネクタへ connector
CN1Aコネクタへ
サーボアンプ
To CN1B
CN1Bコネクタへ
Cap
キャップ
Fig.3-35 : Example of addition axis connection (CR760)
Additional Axis Function 3-150
3 Controller
(4) Example of the installation of the noise filter
1) EMC filter (recommended)
Please install the recommendation filter shown below according to the example of connection.
1)
2)
Note1) For 1-phase 200V to 230VAC power supply, connect the power supply to L1, L2 and leave L3 open.
There is no L3 for 1-phase 100 to 120 VAC power supply.
Note2) The example is when a surge protector is connected.
Fig.3-36 : Example of EMC noise filter installation
3-151
Additional Axis Function
3 Controller
2) Line noise filter
This filter is effective in suppressing noises radiated from the power supply side and output side of the servo amplifier and also in suppressing high-frequency leakage current (zero-phase current) especially within 0.5MHz to 5MHz band.
Fig.3-37 : Example of noise filter installation
Additional Axis Function 3-152
3 Controller
3.9 Magnet contactor control connector output (AXMC) for addition axes
When an additional axis is used, the servo ON/OFF status of the additional axis can be synchronized with the servo ON/OFF status of the robot itself by using the output contact (AXMC) provided on the rear or inside of the controller and configuring a circuit so that the power to the servo amplifier for the additional axis can be turned off when this output is open.
"(2)Image of how to connect the controller connector" .
When you are using an additional axis, please perform appropriate circuit connections by referring to these draw
ings.
Refer to the separate "Additional axis interface Instruction Manual" for details on the additional axis function.
Note1) you use the addition axis function as a user mechanism who became independent of the robot arm, please do not connect this output signal. Servo-on of the user mechanism may be unable.
(1) Example circuit
■ CR750/CR751 controller
1) Get the power supply for the controller from the secondary terminal of short circuit breaker (NV) built in the addition axis amplifier box.
2) Get the power supply for the MC synchronization from the sec
ondary terminal of short circuit breaker (NV) built in the control
ler.
2)コントローラ内蔵漏電遮断器(NV)の2次側より、
MC同期用電源を取り出す。
NV
MC MC1 MC2
88
DC24V
NV
To the internal circuit
AXMC11
AXMC12
AXMC21
AXMC22
<走行軸(付加軸)アンプボックス>
AXMC11
AXMC12
AXMC21
AXMC22
コネクタ ピン番号
CNUSR2
CNUSR2
20
45
19
44
注2)ロボットがアラームの発生などでサーボOFFしたとき、本出力(接点)が開放します。
<接点容量>
DC24V/10mA~100mA
[Note] In the customer's system, do not ground the + side of 24V power supply prepared by customer for connect to the con
troller. (related with emergency stop and parallel input/output) If it connects with the controller under the condition that the + side is grounded, it will lead to failure of controller.
Fig.3-38 : Example of circuit for addition axes of Magnet contactor control output (CR750/CR751 controller)
3-153
Magnet contactor control connector output (AXMC) for addition axes
3 Controller
■ CR760 controller
1) Get the power supply for the controller from the secondary terminal of short circuit breaker (NV) built in the addition axis amplifier box.
2) Get the power supply for the MC synchronization from the sec
ondary terminal of short circuit breaker (NV) built in the controller.
2)コントローラ内蔵漏電遮断器(NV)の2次側より、
MC同期用電源を取り出す。
NV
MC MC1 MC2
88
DC24V
NV
To the internal circuit
AXMC11
AXMC12
AXMC21
AXMC22
AXMC11
AXMC12
AXMC21
AXMC22
コネクタ ピン番号
EMG1
EMG1
11
23
12
24
注2)ロボットがアラームの発生などでサーボOFFしたとき、本出力(接点)が開放します。
<接点容量>
DC24V/10mA~100mA
[Note] In the customer's system, do not ground the + side of 24V power supply prepared by customer for connect to the con
troller. (related with emergency stop and parallel input/output) If it connects with the controller under the condition that the + side is grounded, it will lead to failure of controller.
Fig.3-39 : Example of circuit for addition axes of Magnet contactor control output (CR760 controller)
(2) Image of how to connect the controller connector
■ CR750 controller
*Connects with CNUSR2 connector
3-20: Method of wiring for external emergency stop connection (CR750
.
Fig.3-40 : AXMC terminal connector (CR750)
フェライトコア
Pass twice
Magnet contactor control connector output (AXMC) for addition axes 3-154
3 Controller
■ CR751 controller
* The controller is an example.
フェライトコア
2回通し
Fig.3-41 : AXMC terminal connector (CR751)
■ CR760 controller
Inside of CR760 controller
* The CNUSR2 connector is connected by
soldering. Refer to Page 139 "Fig. 3-23:
Method of wiring for external emergency stop connection (CR751 (CNUSR1/2))"
.
Safety unit
(R760SFT)
EMG1
Within 30cm
Ferrite core
Pass twice
* Connection method is the same as the connection of emergency stop.
Refer to
Page 141 "Fig. 3-25: External emergency stop connection (CR760)"
.
Fig.3-42 : AXMC terminal connector (CR760)
3-155
Magnet contactor control connector output (AXMC) for addition axes
3 Controller
3.10 Options
■ What are options?
There are a variety of options for the robot designed to make the setting up process easier for user needs.
User installation is required for the options.
Options come in two types: "set options" and "single options".
1. Set options......................................A combination of single options and parts that together, form a set for serving some purpose.
2. Single options.................................That are configured from the fewest number of required units of a part.
Please choose user's purpose additionally.
3-156
3 Controller
(1) Teaching pendant (T/B)
■ Order type: CR750/CR760 controller ......... ● R32TB: Cable length 7m
● R32TB-15: Cable length 15m
CR751 controller ......................... ● R33TB: Cable length 7m
● R33TB-15: Cable length 15m
■ Outline
This is used to create, edit and control the program, teach the operation position and for jog feed, etc.
For safety proposes, a 3-position enable switch is mounted.
*1)
■ Configuration
Table 3-10 : Configuration device
Part name Type
CR750/CR760 controller
Teaching pendant R32TB
R32TB-15
CR751 controller
Teaching pendant R33TB
R33TB-15
Note1) Mass indicates one set.
Qty.
Either one pc.
Either one pc.
Mass (kg)
Note1)
1.7
2.8
1.7
2.8
Cable length is 7m. Hand strap is attached.
Cable length is 15m. Hand strap is attached.
Cable length is 7m. Hand strap is attached.
Cable length is 15m. Hand strap is attached.
■ Specifications
Table 3-11 : Specifications
Items
Outline dimensions
Body color
Mass
Connection method
Interface
Display method
Operation section
Specifications
195(W) x 292(H) x 106(D) (refer to outline drawing)
Dark gray
Approx. 0.9kg (only arm, excluding cable)
Connection with controller and connector.
RS-422
LCD method: 24 characters x 8 lines, LCD illumination: with backlight
36 keys
Remarks
Remarks
At 8x8 font
*1) <3-position enable switch>
In ISO/10218 (1992) and JIS-B8433 (1993), this is defined as an "enable device". These standards specify that the robot operation using the teaching pendant is enabled only when the "enable device" is at a specified position.
With the Mitsubishi Electric industrial robot, the above "enable device" is configured of an "Enable/Disable switch" and "Enable switch".
The 3-position enable switch has three statuses. The following modes are entered according to the switch state.
a) "Not pressed".......................... The robot does not operate.
*) b) "Pressed lightly" .................... The robot can be operated and teaching is possible.
c) "Pressed with force"............ The robot does not operate.
*)
*) Operations, such as program editing and status display, other than robot operation are possible.
Safety is secured as the servo power is turned OFF simultaneously with the input of the emergency stop.
3-157
Teaching pendant (T/B)
195.2
133
LCD
Emergency stop
Operetion key
105.5
Enable/Disable switch
3 Controller
<Front>
Body
Cable (with connector)
<side>
Enable switch
<Back>
<Bottom>
Fig.3-43 : Outside dimensions of teaching pendant
■ Installation method
The teaching pendant is connected to the T/B connector on the front of the controller.
Teaching pendant (T/B) 3-158
3 Controller
■ Key layout and main functions
②
④
⑤
⑥
⑦
⑨
⑪
⑫
⑬
⑭
⑮
⑯
⑳
①
⑤
⑥
⑧
⑩
⑰
⑱
⑲
③
① [Emergency stop] switch ................ The robot servo turns OFF and the operation stops immediately.
② [Enable/Disable] switch .................. This switch changes the T/B key operation between enable and dis
able.
③ [Enable] switch.................................... When the [Enable/Disable] switch " ② " is enabled, and this key is released or pressed with force, the servo will turn OFF, and the oper
ating robot will stop immediately.
④ LCD display panel .............................. The robot status and various menus are displayed.
⑤ Status display lamp ........................... Display the state of the robot or T/B.
⑥ [F1], [F2], [F3], [F4].......................... Execute the function corresponding to each function currently dis
played on LCD.
⑦ [FUNCTION] key ................................ Change the function display of LCD.
⑧ [STOP] key........................................... This stops the program and decelerates the robot to a stop.
⑨ [OVRD ↑ ][OVRD ↓ ] key ........... Change moving speed. Speed goes up by [OVRD ↑ ] key. Speed goes down by [OVRD ↓ ] key
⑩ [JOG] operation key......................... Move the robot according to jog mode. And, input the numerical value.
⑪ [SERVO] key........................................ Press this key with holding AA key lightly, then servo power will turn on.
⑫ [MONITOR] key .................................. It becomes monitor mode and display the monitor menu.
⑬ [JOG] key.............................................. It becomes jog mode and display the jog operation.
⑭ [HAND] key........................................... It becomes hand mode and display the hand operation.
⑮ [CHARCTER] key............................... This changes the edit screen, and changes between numbers and alphabetic characters.
⑯ [RESET] key......................................... This resets the error. The program reset will execute, if this key and the EXE key are pressed.
⑰ [ ↑ ][ ↓ ][ ← ][ → ] key................ Moves the cursor each direction .
⑱ [CLEAR] key ........................................ Erase the one character on the cursor position.
⑲ [EXE] key............................................... Input operation is fixed. And, while pressing this key, the robot moves when direct mode.
⑳ Number/Character key.................... Erase the one character on the cursor position. And, inputs the num
ber or character
Fig.3-44 : Teaching pendant key layout and main functions
3-159
Teaching pendant (T/B)
3 Controller
(2) Parallel I/O interface
■ Order type : ● 2D-TZ368 (Sink type)/2D-TZ378 (Source type)
■ Outline
This is used to expand the external inputs and outputs
・ The connecting cable with external equipment is not attached. Since we are preparing the external input-and-output cable (2D-CBL05 or 2D-CBL15) as the option, please use.
Notes)Although the combined use with the parallel input-and-output unit (2A-RZ361/2A-
RZ371) of another option is also possible, please use the setup of the station number by the different number separately. The station number is automatically determined by the position of the option slot which installed this interface. (CR750/
CR751 controller: station number 0 to 1, CR760 controller: station number 0 to 2)
■ Configuration
Table 3-12 : Configuration device
Part name Type
Qty.
Mass (kg)
Note1)
Remarks
Parallel I/O interface 2D-TZ368
2D-TZ378
Either one pc.
0.4
Input/output 32 points/32 points
2D-TZ368 is sink type. 2D-TZ378 is source type.
Note1) Mass indicates one set.
■ Specifications
Table 3-13 : Electrical specifications of input circuits
Item
Specification
Type
Number of input points
Insulation method
DC input
32
Photo coupler insulation
Rated input voltage
Rated input current
Working voltage range
ON voltage/ON current
OFF voltage/ OFF current
Input resistance
Response time
DC12V
Approx. 3mA
DC24V
Approx.9mA
DC10.2 ~ 26.4V
(Ripple factor should be less than 5%)
DC8V or more/2mA or more
DC4V or less/1mA or less
Approx. 2.7kΩ
OFF-ON 10ms or less(DC24V)
ON-OFF 10ms or less(DC24V)
Common method
External cable connection method
32 points per common
Connector
<Sink type>
Internal circuit
+24V/+12V
(COM)
820
2.7K
<Source type>
2.7K
820
Input
Input
24G/12G
Parallel I/O interface 3-160
3 Controller
Table 3-14 : Electrical specifications for the output circuits
Item
Specification
Type
No. of output points
Insulation method
Rated load voltage
Transistor output
32
Photo-coupler insulation
DC12V/DC24V
Rated load voltage range DC10.2 ~ 30V (peak voltage DC30V)
Max. load current 0.1A/point (100%)
Leakage current at OFF Within 0.1mA
Max. voltage drop at ON DC0.9V(TYP.)
Note1)
Respons e time
OFF-ON
ON-OFF
10ms or less(Resistance load) (hardware response time)
Fuse rating
10ms or less(Resistance load) (hardware response time)
Fuse 1.6A(one per common)
Replacement possible (max. 3)
Common method
External wire connection method
External power supply
Voltage
Current
16 points per common (common terminal: 2points)
Connector
DC12/24V(DC10.2 ~ 30V)
60mA(TYP.DC24V per common)(base drive current)
Note1) The maximum voltage drop value at signal ON.
Refer to it for the equipment connected to the output circuit.
<Sink type>
Internal circuit
<Source type>
Fuse
+24V/+12V
Output
24G/12G
Fuse
+24V/+12V
Output
24G/12G
Caution
The protection fuse of the output circuit prevents the failure at the time of the load short circuit and incorrect connection. The load connected of the customer should be careful not to exceed maximum rating current. The internal transistor may be damaged if maximum rating current is exceeded.
■ Installation method
The expansion parallel input/output interface is installed in the controller. Refer to separate "Instruction Manual/
Controller setup, basic operation, and maintenance" for details on the installing method.
If it installs in the option SLOT of the controller, the station number will be assigned automatically.
SLOT1: station number 0 (0 to 31)
SLOT2: station number 1 (32 to 63)
SLOT3: station number 2 (64 to 95)
Caution
If it uses together with parallel input-and-output unit 2A-RZ361/2A-RZ371, please do not overlap with the station number of the parallel input-and-output interface.
<CR750 controller>
SLOT1
SLOT2
Fig.3-45 : Parallel I/O interface installation position (CR750)
3-161
Parallel I/O interface
3 Controller
<CR751 controller>
* The controller is an example.
SLOT1
SLOT2
Fig.3-46 : Parallel I/O interface installation position (CR751)
<CR760 controller>
R760CPUユニット
SLOT1
SLOT2
SLOT3
Fig.3-47 : Parallel I/O interface installation position (CR760)
■ Pin layout of connector
1B 20B
1A
1D
1C
20A
20D
20C
Connector<2>
Output 16 to 31
Input 16 to 31
(when station number 0)
Connector<1>
Output 0 to 15
Input 0 to 15
(when station number 0)
Fig.3-48 : Pin layout of connector
Parallel I/O interface 3-162
3 Controller
■ Connector pin No. and signal assignment
The station number is fixed by the slot to install and the allocation range of the general-purpose input-andoutput signal is fixed.
Table 3-15 : The slot number and the station number
Slot number
Station number
Range of the general-purpose input-and-output signal
Connector <1> Connector <2>
SLOT1 0
SLOT2
SLOT3
1
2
Input : 0 to 15
Output : 0 to 15
Input : 32 to 47
Output : 32 to 47
Input : 64 to 79
Output : 64 to 79
Input : 16 to 31
Output : 16 to 31
Input : 48 to 63
Output : 48 to 63
Input : 80 to 95
Output : 80 to 95
The connector pin number of the parallel input-and-output interface installed in SLOT1 and signal number allocation are shown in
and
. If it installs in other slots, please interpret and utilize.
3-163
Parallel I/O interface
3 Controller
Table 3-16 : Connector<1> pin assignment list and external I/O cable (2D-CBL**) color(SLOT1)
Function name Function name
Pin
No.
Line color
General-purpose
Dedicated/power supply, common
Pin
No.
Line color
General-purpose
Dedicated/power supply, common
1C
2C
Orange/Red
Gray/Red
a
a
24G/12G: For pins 5D-
20D
COM : For pins
5C-20C
Note1)
Reserved 3C
White/Red a
4C
Yellow/Red
a
5C
Pink/Red
a
General-purpose input
15
6C
Orange/Red
b
General-purpose input
14
7C
Gray/Red
b
General-purpose input
13
8C
White/Red b
General-purpose input
12
9C
Yellow/Red
b
General-purpose input
11
10C
Pink/Red
b
General-purpose input
10
Reserved
11C
Orange/Red c
General-purpose input
9
12C
Gray/Red
c
General-purpose input
8
13C
White/Red
c
General-purpose input
7
14C
Yellow/Red
c
General-purpose input
6
15C
Pink/Red
c
General-purpose input
5 Operation rights input signal
Note2)
16C
Orange/Red
d
General-purpose input
4 Servo ON input signal
17C
Gray/Red
d
General-purpose input
3
18C
White/Red
d
General-purpose input
2 Error reset input signal
19C
Yellow/Red
d
General-purpose input
1 Servo OFF input signal
20C
Pink/Red
d
General-purpose input
0
Stop input
Note3)
1D
Orange/
Black a
2D
Gray/
Black a
+24V/+12V(COM): For pins 5D-20D
Reserved
3D
White/
Black a
4D
Yellow/
Black a
5D
Pink/
Black a
General-purpose output
15
6D
Orange/
Black b
General-purpose output
14
7D
Gray/
Black b
General-purpose output
13
8D
White/
Black b
General-purpose output
12
9D
Yellow/
Black b
General-purpose output
11
10D
Pink/
Black b
General-purpose output
10
11D
Orange/
Black c
General-purpose output
9
12D
Gray/
Black c
General-purpose output
8
13D
White/
Black c
General-purpose output
7
14D
Yellow/
Black c
General-purpose output
6
15D
Pink/
Black c
General-purpose output
5
Reserved
Reserved
16D
Orange/
Black d
General-purpose output
4
17D
Gray/
Black d
General-purpose output
3 Operation rights output
18D
White/
Black d
General-purpose output
2 Error occurring output
19D
Yellow/
Black d
General-purpose output
1 In servo ON output
20D
Pink/
Black d
General-purpose output
0
Note1) Sink type: +24V/+12V(COM), Source type: 24G/12G
Note2) The dedicated signal is assigned at shipping. It can change with the parameter.
Note3) The dedicated input signal (STOP) is assigned at shipping. The signal number is fixing.
Table 3-17 : Connector<2> pin assignment list and external I/O cable (2D-CBL**) color(SLOT1)
Function name Function name
Pin
No.
Line color
General-purpose
Dedicated/power supply, common
Pin
No.
Line color
General-purpose
Dedicated/power supply, common
1A
Orange/Red
a
2A
Gray/Red
a
24G/12G: For pins 5B-
20B
COM : For pins 5A-
20A
Note1)
Reserved
Reserved
1B
Orange/
Black a
2B
Gray/
Black a
+24V/+12V(COM): For pins 5B-20B
Reserved
3A
White/Red a
4A
Yellow/Red
a
5A
Pink/Red
a
General-purpose input
31
6A
Orange/Red
b
General-purpose input
30
7A
Gray/Red
b
General-purpose input
29
8A
White/Red b
General-purpose input
28
9A
Yellow/Red
b
General-purpose input
27
10A
Pink/Red
b
General-purpose input
26
11A
Orange/Red c
General-purpose input
25
12A
Gray/Red
c
General-purpose input
24
13A
White/Red
c
General-purpose input
23
14A
Yellow/Red
c
General-purpose input
22
15A
Pink/Red
c
General-purpose input
21
16A
Orange/Red
d
General-purpose input
20
17A
Gray/Red
d
General-purpose input
29
18A
White/Red
d
General-purpose input
18
19A
Yellow/Red
d
General-purpose input
17
20A
Pink/Red
d
General-purpose input
16
3B
White/
Black a
4B
Yellow/
Black a
5B
Pink/
Black a
General-purpose output
31
6B
Orange/
Black b
General-purpose output
30
7B
Gray/
Black b
General-purpose output
29
8B
White/
Black b
General-purpose output
28
9B
Yellow/
Black b
General-purpose output
27
10B
Pink/
Black b
General-purpose output
26
11B
Orange/
Black c
General-purpose output
25
12B
Gray/
Black c
General-purpose output
24
13B
White/
Black c
General-purpose output
23
14B
Yellow/
Black c
General-purpose output
22
15B
Pink/
Black c
General-purpose output
21
16B
Orange/
Black d
General-purpose output
20
17B
Gray/
Black d
General-purpose output
19
18B
White/
Black d
General-purpose output
18
19B
Yellow/
Black d
General-purpose output
17
20B
Pink/
Black d
General-purpose output
16
Reserved
Reserved
Note1) Sink type: +24V/+12V(COM), Source type: 24G/12G
Parallel I/O interface 3-164
3 Controller
<Reference> The example of connection with our PLC
<Sink>
Parallel I/O interface
(Output)
60mA
(+24/+12V)
Output
QX41
(Mitsubishi programmable controller)
COM
X
Output
24V
Fuse (24G/12G)
External power supply
(Input)
QY41P
(Mitsubishi programmable controller)
*The input/output circuit external power supply (24 VDC) must be prepared by the customer.
(COM)
+24V
3.3K
Input
Input
External power supply
24V
Y
COM
24G
Note) In the customer's system, do not ground the + side of 24V power supply prepared by customer for connect to the controller.
(related with emergency stop and parallel input/output) If it connects with the controller under the condition that the + side is grounded, it will lead to failure of controller.
Table 3-18 : Connection with a Mitsubishi PLC (Example of sink type)
<Source>
Parallel I/O interface
(Output)
Fuse
60mA
(+24/+12V)
Output
QX41
(Mitsubishi programmable controller)
(Input)
3.3K
Input
Input
(COM)
External
24V power supply
X
Output
24V
COM
(24G/12G)
External power supply
QY81P
+24V
(Mitsubishi programmable controller)
*The input/output circuit external power supply (24 VDC) must be prepared by the customer.
Y
24G
Note) In the customer's system, do not ground the + side of 24V power supply prepared by customer for connect to the controller. (related with emergency stop and parallel input/output) If it connects with the controller under the condition that the + side is grounded, it will lead to failure of controller.
Table 3-19 : Connection with a Mitsubishi PLC (Example of source type)
3-165
Parallel I/O interface
3 Controller
(3) External I/O cable
■ Order type : ● 2D-CBL □□ Note) The numbers in the boxes □□ refer to the length. (05: 5m, 15: 15m)
■ Outline
This is the dedicated cable used to connect an external peripheral device to the con
nector on the parallel I/O interface. For parallel I/O unit is another option 2A-CBL.**.
One end matches the connector on the parallel input/output unit, and the other end is free. Connect the peripheral device's input/output signal using the free end.
One cable correspond to the input 16 points and output 16 points.
Two cables are needed to connection of (input 32 points and output 32 points) with built-in standard.
■ Configuration
Table 3-20 : Configuration device
Part name Type
External I/O cable 2D-CBL □□
Qty.
1 pc.
Mass (kg)
Note1)
0.7(5m)
1.84(15m)
5m or 15m
Remarks
Note1) Mass indicates one set.
■ Specifications
Table 3-21 : Specifications
Items
Number of cables x cable size
Total length
AWG #28 x 20P (40 pairs)
5m, 15m
Specifications
■ Connector pin numbers and cable colors
Table 3-22 : Connector pin numbers and cable colors
Pin no. Cable colors Pin no. Cable colors Pin no. Cable colors Pin no. Cable colors
1A/C
2A/C
3A/C
4A/C
5A/C
6A/C
7A/C
8A/C
9A/C
Orange/Red a
Gray/Red a
White/Red a
Yellow/Red a
Pink/Red a
Orange/Red b
Gray/Red b
White/Red b
Yellow/Red b
11A/C
12A/C
13A/C
14A/C
15A/C
16A/C
17A/C
18A/C
19A/C
Orange/Red c
Gray/Red c
White/Red c
Yellow/Red c
Pink/Red c
Orange/Red d
Gray/Red d
White/Red d
Yellow/Red d
1B/D
2B/D
3B/D
4B/D
5B/D
6B/D
7B/D
8B/D
9B/D
Orange/Black a
Gray/Black a
White/Black a
Yellow/Black a
Pink/Black a
Orange/Black b
Gray/Black b
White/Black b
Yellow/Black b
11B/D
12B/D
13B/D
14B/D
15B/D
16B/D
17B/D
18B/D
19B/D
Orange/Black c
Gray/Black c
White/Black c
Yellow/Black c
Pink/Black c
Orange/Black d
Gray/Black d
White/Black d
Yellow/Black d
10A/C Pink/Red b 20A/C Pink/Red d 10B/D Pink/Black b 20B/D Pink/Black d
Notes) Pin number of connector<1> are 1C, 2C, ....20C, 1D, 2D, ....20D, connector<2> are 1A, 2A, ....20A, 1B,
2B, ....20B.
External I/O cable 3-166
3 Controller
■ Connections and outside dimensions
The sheath of each signal cable (40 lines) is color indicated and marked with dots. Refer to the cable color speci
-
fications in "Table 3-33: Connector pin numbers and cable colors" when making the connections.
(Eg.) Pin number: color indication
1 : Orange / Red / a
Type of dot mark (see figure below)
Color of dot mark
Color of sheath
Line color type a type
Pattern of the print mark
One dot b type
Two dots c type
Three dots d type
Four dots or
20A/C
20B/D
1A/C 1B/D
Fig.3-49 : Connections and outside dimensions
Plug (Fujitsu Ltd) Connector : FCN-361J040-AU
Cover : FCN-360C040-B
3-167
External I/O cable
3 Controller
(4) Parallel I/O unit
■ Order type: 2A-RZ361(Sink type)
2A-RZ371(Source type)
■ Outline
This is used to expand the external inputs and outputs. One one equal with this unit is built into the control unit among controllers the standard.
・ The connection cable is not included. .Prepare the optional external input/output cable (2A-CBL05 or 2A-CBL15).
・ Use 2A-RZ361 if the external input/output signal logic is of the sink type and 2A-
RZ371 for source type signal logic.
Notes) Although the combined use with the parallel I/O interface (2D-TZ368) of another option is also possible, please use the setup of the station number by the different number separately. The station number is auto
matically fixed by the position of the option slot which installed the parallel I/O interface in 0-1 (CR750/
CR751 controller) or 0-2 (CR760 controller).
■ Configuration
Table 3-23 : Configuration device
Part name Type
Parallel I/O unit
2A-RZ361
2A-RZ371
Robot I/O link connec
tion connector
Power connection con
nector
Terminator
NETcable-1
DCcable-2
R-TM
Note1) Mass indicates one set.
Qty.
Either one pc.
2 sets
1 set
1 pc.
Mass (kg)
Note1)
0.7
0.7
-
-
-
Remarks
Input/output 32 points/32 points
2A-RZ361 is the sink type.
2A-RZ371 is the source type.
Connector with pins.
The cable must be prepared and wired by the customer.
Connector with pins.
The cable must be prepared and wired by the customer.
100Ω(1/4W)
■ Specifications
1) The parallel I/O interface (2D-TZ368) of another option, and the a maximum of eight pieces in all. (One station occupies one unit.)
2) The power supply (24V) must be prepared by the customer and connected with the power connection cable
(DCcable-2)
A separate 24V power supply is required for the input/output circuit wiring.
Table 3-24 : Electrical specifications of input circuits
Item Specification
Type
Number of input points
Insulation method
Rated input voltage
Rated input current
Working voltage range
ON voltage/ON current
DC input
32
Photo coupler insulation
12VDC
Approx 3mA
24VDC
Approx 7mA
10.2 to 26.4VDC(Ripple factor should be less than 5%.)
8VDC or more/ 2mA or more
OFF voltage/ OFF current
Input resistance
Response time OFF-ON
ON-OFF
4VDC or less/ 1mA or less
Approx. 3.3kΩ
10ms or less (24VDC)
10ms or less (24VDC)
Common method 8 points per common
External cable connection method Connector
Internal circuit
<Sink type>
820
3.3K
<Source type>
3.3K
820
+24V/+12V
(COM)
24G/12G
Parallel I/O unit 3-168
3 Controller
Table 3-25 : Electrical specifications for the output circuits
Item
Type
No. of output points
Insulation method
Rated load voltage
Rated load voltage range
Max. load current
Leakage current at OFF
Max. voltage drop at ON
Response time
OFF-ON
ON-OFF
Fuse rating
Common method
External wire connection method
Specification
Transistor output
32
Photo-coupler insulation
12VDC/24VDC
10.2 to 30VDC(peak voltage 30VDC)
0.1A/point (100%)
0.1mA or less
0.9VDC(TYP.)
Note1)
2ms or less
(hardware response time)
2ms or less
(Resistance load) (hardware response time)
Fuse 3.2A (one per common) Replacement not possible
8 points per common (common terminal: 4 points)
Connector
External power supply
Voltage 12VDC/24VDC(10.2 to 30VDC)
Current 60mA (TYP. 24VDC per common) (base drive current)
Note1) The maximum voltage drop value at signal ON.
Refer to it for the equipment connected to the output circuit.
Internal circuit
<Sink type>
<Source type>
+24V/+12V
24G/12G
+24V/+12V
24G/12G
CAUTION
The output circuit protective fuses prevent failure in case of load short-circuit and improper connections. Please do not connect loads that cause the current to exceed the maximum rated current. If the maximum rated current is exceeded, the internal transistors may be damaged.
CAUTION
Inputs the power supply for control (DCcable-2) then inputs the controller’s power supply.
3-169
Parallel I/O unit
3 Controller
NETcable-1 (Network cable)
Pin No.
RIO1/2
1
2
3
TXRXH
TXRXL
SG(GND)
Note 2)
FG
RIO1/2
TXRXH
Pin No.
1
TXRXL 2
SG(GND) 3
Connector for CR750/CR751: 51103-0300
Connector for CR760: 1-178288-3
DCcable-2 (Power cable)
Pin No.
DCIN
1 24V
2
3
24G
FG(PE)
+
-
24V Power
Note 1)
Connected the frame ground or protect ground
R-TM (Terminator)
Pin No.
RIO1/2
1 TXRXH
2
3
TXRXL
SG(GND)
100Ω
List of parts and manufacturer
Type
NETcable-1
DCcable-2
R-TM
Connector type
1-178288-3 (2)
51103-0300 (1)
2-178288-3 (1)
1-178288-3 (1)
Contact type
1-175218-3 (6)
50351-8100 (3)
175218-3 (3)
175218-3 (2)
Resistant
-
-
-
100Ω(1/4W) (1)
Manufacturer
Tyco Electronics (Black connector)
MOLEX (White connector)
Tyco Electronics (Black connector)
Equivalent to KOA.
Note 1) The 24V power supply is prepared by customer (The power consumption is approx. 0.3A.)
In the customer's system, do not ground the + side of 24V power supply prepared by customer for con
nect to the controller. (related with emergency stop and parallel input/output) If it connects with the controller under the condition that the + side is grounded, it will lead to failure of controller.
Note 2) The cable for general purpose can be used to the network cable. However, use the twisted shield cable of
AWG#22(0.3mm
2
) or more.
Fig.3-50 : Specifications for the connection cable
Parallel I/O unit 3-170
3 Controller
■ Installation method
The expansion parallel input/output unit is installed outside of the controller. Connect with the network connection cable (NETcable-1) from the RIO connector in the rear/into of the controller.(Terminator is connected at the time of shipment)
<CR750 controller>
(4 0 ) (1 7 5 )
1 2 8
6
< 2 A - R Z 3 6 1 >
< 2 A - R Z 3 7 1 >
Fig.3-51 : Installing the parallel I/O unit (CR750)
5 4
6 0
6
3-171
Parallel I/O unit
<CR751 controller>
* The controller is an example.
(4 0 ) ( 1 7 5 )
1 2 8
6
< 2 A - R Z 3 6 1 >
< 2 A - R Z 3 7 1 >
Fig.3-52 : Installing the parallel I/O unit (CR751)
5 4
6 0
6
3 Controller
Parallel I/O unit 3-172
3 Controller
<CR760 controller>
( 4 0 ) (1 7 5 )
1 2 8
6
RIO
< 2 A - R Z 3 6 1 >
< 2 A - R Z 3 7 1 >
Fig.3-53 : Installing the parallel I/O unit (CR760)
5 4
6 0
6
3-173
Parallel I/O unit
3 Controller
<CR750 controller>
*1)
Station No. setting
1 . . . 6
20~30mm
Metal braid section
Peel the sheath in the position about 200-300mm from the connector end of the cable, so you can install and remove the cover.
* Don't damage the shield line.
Station No. setting
7
Ferrite core
(Only for the CE marking/
KC mark specification)
Pass twice
FG
*2)
<CN100>
注)
NETcable-1 cable
FG
DCIN connector
DCcable-2 cable
<CN300>
<CN100>
<CN300>
RIO2コネクタ
注)
Note)
NETcable-1 cable
DCIN connector
FG
DCcable-2 cable
R-TM terminator
*1) Install the ferrite core in within
100mm from each connector.
I/O unit the bottom connector layout
Connect the NET cable-1 to the RIO connector on the back of the controller. Each unit is connected to from a daisy chain.
Always install a terminator (R-TM) to the last unit.
Note) Use a shield cable for NET cable-1 as a measure against noise.
Always connect the shield to FG. Install the attached ferrite core in both ends.
The unit could malfunction because of noise if the shield cable is not used.
Fig.3-54 : Connection method of expansion parallel I/O unit (CR750)
Parallel I/O unit 3-174
3 Controller
<CR751 controller>
* The controller is an example.
*1)
Station No. setting
1 . . . 6
20~30mm
シースはケーブルのコネクタ端から200~300mmの箇所を目安に
カバーの着脱ができる程度の位置で剥いてください。
※シールド線に傷をつけないようにご注意願います。
Station No. setting
7
Ferrite core
(Only for the CE marking/
KC mark specification)
Pass twice
FG
*2)
<CN100>
NETcable-1 cable
<CN300>
<CN100>
<CN300>
FG
DCIN connector
DCcable-2 cable
RIO2コネクタ
注)
Note)
NETcable-1 cable
DCIN connector
FG
DCcable-2
ケーブル
R-TM terminator
*1) Install the ferrite core in within
100mm from each connector.
I/O unit the bottom connecter layout
Connect the NET cable-1 to the RIO connector on the back of the controller. Each unit is connected to from a daisy chain.
Always install a terminator (R-TM) to the last unit.
Note) Use a shield cable for NET cable-1 as a measure against noise.
Always connect the shield to FG. Install the attached ferrite core in both ends.
The unit could malfunction because of noise if the shield cable is not used.
Fig.3-55 : Connection method of expansion parallel I/O unit (CR751)
3-175
Parallel I/O unit
3 Controller
<CR760 controller>
RIO1 con
-
Station No. setting
1 . . . 6
0 . . . 6
Ferrite core
注)
Note)
NETcable-1 cable
<CN100>
FG
*2)
*1)
Station No. setting
7
7
<CN300>
<CN100>
<CN300>
FG
DCIN connector
NETcable-1 cable
ケーブル
DCcable-2
ケーブル
FG
DCIN connector
DCcable-2
ケーブル
RIO2 connector
R-TM
ターミネータ
*1) Install the ferrite core in within 100mm from each connector.
20~30mm
シースはケーブルのコネクタ端から200~300mmの箇所を目安に
カバーの着脱ができる程度の位置で剥いてください。
入出力ユニット底面
コネクタ配置図
Connect the NET cable-1 to the RIO connector on the back of the controller. Each unit is connected to from a daisy chain.
Always install a terminator (R-TM) to the last unit.
Note) Use a shield cable for NET cable-1 as a measure against noise.
Always connect the shield to FG. Install the attached ferrite core in both ends.
The unit could malfunction because of noise if the shield cable is not used.
Fig.3-56 : Connection method of expansion parallel I/O unit (CR760)
Parallel I/O unit 3-176
3 Controller
■ Pin arrangement of the connector
Channel No. setting
TXD
LED display
50
25
<CN100>
Input 0 to 15
Output 0 to 15
<CN300>
Input 16 to 31
Output 16 to 31
26
1
*2A-RZ361/2 A-RZ371 are 32/32 input-and-output units. (One-station occupancy)
Fig.3-57 : Pin arrangement of the parallel I/O unit
■ Assignment of pin number and signal
The assignment range of the general-purpose input-and-output signal is fixed by the setup of the station number.
Table 3-26 : Assignment of pin number and signal
Unit Number
Station number
CN100
1st set 0
2nd set
3rd set
4th set
5th set
6th set
7th set
8th set
1
2
3
4
5
6
7
Input : 0 to 15
Output : 0 to 15
Input : 32 to 47
Output : 32 to 47
Input : 64 to 79
Output : 64 to 79
Input : 96 to 111
Output : 96 to 111
Input : 128 to 143
Output : 128 to 143
Input : 160 to 175
Output : 160 to 175
Input : 192 to 207
Output : 192 to 207
Input : 224 to 239
Output : 224 to 239
CN300
Input : 16 to 31
Output : 16 to 31
Input : 48 to 63
Output : 48 to 63
Input : 80 to 95
Output : 80 to 95
Input : 112 to 127
Output : 112 to 127
Input : 144 to 159
Output : 144 to 159
Input : 176 to 191
Output : 176 to 191
Input : 208 to 223
Output : 208 to 223
Input : 240 to 255
Output : 240 to 255
The connector pin number of the parallel I/O unit of the station number 0 and signal number assignment are
and Table 3-28 . If it is set as other station number, please interpret and utilize.
3-177
Parallel I/O unit
3 Controller
■ Parallel I/O interface (First expansion unit)
Table 3-27 : Connector CN100pin No. and signal assignment list (2A-CBL
□□
)
Function name
Pin
No.
Line color
General-purpose
Dedicated/power supply, common
Pin
No.
Line color
Function name
General-purpose
Dedicated/power supply, common
3
4
1 Orange/Red A
2 Gray/Red A
5
White/Red A
Yellow/Red A General-purpose output 0
FG
0V:For pins 4-7, 10-13
12V/24V:For pins 4-7
Operating output
Note1)
Pink/Red A General-purpose output 1 In servo ON output signal
26 Orange/Blue A
27 Gray/Blue A
28 White/Blue A
29 Yellow/Blue A General-purpose output 4
30 Pink/Blue A General-purpose output 5
FG
0V:For pins 29-32, 35-38
12V/24V:For pins 29-32
6 Orange/Red B General-purpose output 2 Error occurring output signal
31 Orange/Blue B General-purpose output 6
7
8
9
Gray/Red B General-purpose output 3 Operation rights output signal
White/Red B
Yellow/Red B
10 Pink/Red B General-purpose output 8
11 Orange/Red C General-purpose output 9
0V:For pins 4-7, 10-13
12V/24V:For pins 10-13
12 Gray/Red C General-purpose output 10
13 White/Red C General-purpose output 11
14 Yellow/Red C
15 Pink/Red C General-purpose input 0
16 Orange/Red D General-purpose input 1
COM0:For pins 15-22
Stop input
Note3)
Note2)
Servo OFF input signal
17 Gray/Red D General-purpose input 2
18
19
20
White/Red D
Yellow/Red D General-purpose input 4
Pink/Red D
General-purpose input 3
General-purpose input 5
Error reset input signal
Start input
Servo ON input signal
Operation rights input signal
21 Orange/Red E General-purpose input 6
22 Gray/Red E General-purpose input 7
23 White/Red E
24 Yellow/Red E
25 Pink/Red E
Reserved
Reserved
Reserved
32 General-purpose output 7
33 White/Blue B
34 Yellow/Blue B
35 Pink/Blue B General-purpose output 12
36 Orange/Blue C General-purpose output 13
37 Gray/Blue C General-purpose output 14
38 White/Blue C General-purpose output 15
39 Yellow/Blue C
40 Pink/Blue C General-purpose input 8
41 Orange/Blue D General-purpose input 9
0V:For pins 29-32, 35-38
12V/24V:For pins 35-38
COM1:For pins 40-47
42
Gray/Blue B
Gray/Blue D General-purpose input 10
43 White/Blue D General-purpose input 11
44 Yellow/Blue D General-purpose input 12
45 Pink/Blue D General-purpose input 13
46 Orange/Blue E General-purpose input 14
47 Gray/Blue E General-purpose input 15
48 White/Blue E
49 Yellow/Blue E
50 Pink/Blue E
Reserved
Reserved
Reserved
Note1) The dedicated signal is assigned at shipping. It can change with the parameter.
Note2) Sink type:12V/24V(COM),Source type:0V(COM)
Note3) The dedicated input signal (STOP) is assigned at shipping. The signal number is fixing.
Parallel I/O unit 3-178
3 Controller
Table 3-28 : Connector CN300pin No. and signal assignment list (2A-CBL
□□
)
Function name
Pin
No.
Line color
General-purpose
Dedicated/power supply, common
Pin
No.
Line color
Function name
General-purpose
Dedicated/power supply, common
3
4
1 Orange/Red A
2 Gray/Red A
White/Red A
Yellow/Red A General-purpose output 16
7
8
5 Pink/Red A General-purpose output 17
6 Orange/Red B General-purpose output 18
Gray/Red B
White/Red B
General-purpose output 19
9
10
Yellow/Red B
Pink/Red B General-purpose output 24
11 Orange/Red C General-purpose output 25
12
13
Gray/Red C
White/Red C
14 Yellow/Red C
General-purpose output 26
General-purpose output 27
15 Pink/Red C General-purpose input 16
16 Orange/Red D General-purpose input 17
17
18
Gray/Red D
White/Red D
General-purpose input 18
General-purpose input 19
19 Yellow/Red D General-purpose input 20
20 Pink/Red D General-purpose input 21
21 Orange/Red E General-purpose input 22
22 Gray/Red E General-purpose input 23
23 White/Red E
24 Yellow/Red E
25 Pink/Red E
FG
0V:For pins 4-7, 10-13
12V/24V:For pins 4-7
0V:For pins 4-7, 10-13
12V/24V:For pins 10-13
COM0:For pins 15-22
Note1)
Reserved
Reserved
Reserved
26 Orange/Blue A
27 Gray/Blue A
28 White/Blue A
29 Yellow/Blue A General-purpose output 20
30 Pink/Blue A General-purpose output 21
31 Orange/Blue B General-purpose output 22
32 Gray/Blue B General-purpose output 23
33 White/Blue B
34 Yellow/Blue B
35 Pink/Blue B General-purpose output 28
36 Orange/Blue C General-purpose output 29
37 Gray/Blue C General-purpose output 30
38 White/Blue C General-purpose output 31
39 Yellow/Blue C
40 Pink/Blue C General-purpose input 24
41 Orange/Blue D General-purpose input 25
42 Gray/Blue D General-purpose input 26
43 White/Blue D General-purpose input 27
44 Yellow/Blue D General-purpose input 28
45 Pink/Blue D General-purpose input 29
46 Orange/Blue E General-purpose input 30
47 Gray/Blue E General-purpose input 31
48 White/Blue E
49 Yellow/Blue E
50 Pink/Blue E
FG
0V:For pins 29-32, 35-38
12V/24V:For pins 29-32
0V:For pins 29-32, 35-38
12V/24V:For pins 35-38
COM1:For pins 40-47
Reserved
Reserved
Reserved
Note1) Sink type:12V/24V(COM),Source type:0V(COM)
3-179
Parallel I/O unit
3 Controller
<Reference> The example of connection with our PLC
<Sink>
Parallel I/O interface
(Output)
60mA
(+24/+12V)
Output
QX41
(Mitsubishi programmable controller)
COM
X
Output
24V
Fuse (24G/12G)
External power supply
(Input)
QY41P
(Mitsubishi programmable controller)
*The input/output circuit external power supply (24 VDC) must be prepared by the customer.
(COM)
+24V
3.3K
Input
Input
External power supply
24V
Y
COM
24G
Note) In the customer's system, do not ground the + side of 24V power supply prepared by customer for connect to the controller.
(related with emergency stop and parallel input/output) If it connects with the controller under the condition that the + side is grounded, it will lead to failure of controller.
Table 3-29 : Connection with a Mitsubishi PLC (Example of sink type)
<Source>
Parallel I/O interface
(Output)
Fuse
60mA
(+24/+12V)
Output
QX41
(Mitsubishi programmable controller)
X
(Input)
Output
24V
COM
(24G/12G)
External power supply
QY81P
+24V
(Mitsubishi programmable controller)
3.3K
Input
Y
Input
(COM)
24V
24G
External power supply
*The input/output circuit external power supply (24 VDC) must be prepared by the customer.
Note) In the customer's system, do not ground the + side of 24V power supply prepared by customer for connect to the controller.
(related with emergency stop and parallel input/output) If it connects with the controller under the condition that the + side is grounded, it will lead to failure of controller.
Table 3-30 : Connection with a Mitsubishi PLC (Example of source type)
Parallel I/O unit 3-180
3 Controller
(5) External I/O cable
■ Order type: 2A-CBL □□ Note) The numbers in the boxes □□ refer to the length. (05: 5m、 15: 15m)
■ Outline
This is the dedicated cable used to connect an external peripheral device to the con
nector on the parallel input/output unit.
One end matches the connector on the parallel input/output unit, and the other end is free. Connect the peripheral device's input/output signal using the free end.
One cable correspond to the input 16 points and output 16 points.
Two cables are needed to connection of (input 32 points and output 32 points) with built-in standard.
■ Configuration
Table 3-31 : Configuration device
Part name Type
External I/O cable 2A-CBL □□
Qty.
1pc.
Mass(kg)
Note1)
0.7(5m)
1.84(15m)
5m or 15m
Remarks
Note1) Mass indicates one set.
■ Specifications
Table 3-32 : Specifications
Items
Number of cables x cable size
Total length
50 pairs x AWG #28
5m or 15m
Specifications
■ Connector pin numbers and cable colors
Table 3-33 : Connector pin numbers and cable colors
Pin no.
Cable colors
Pin no.
Cable colors
Pin no.
Cable colors
1 Orange/Red A 11 Orange/Red C 21 Orange/Red E
8
9
6
7
10
4
5
2
3
Gray/Red A
White/Red A
Yellow/Red A
Pink/Red A
Orange/Red B
Gray/Red B
White/Red B
Yellow/Red B
Pink/Red B
16
17
18
19
20
12
13
14
15
Gray/Red C
White/Red C
Yellow/Red C
Pink/Red C
Orange/Red D
Gray/Red D
White/Red D
Yellow/Red D
Pink/Red D
26
27
28
29
30
22
23
24
25
Gray/Red E
White/Red E
Yellow/Red E
Pink/Red E
Orange/Blue A
Gray/Blue A
White/Blue A
Yellow/Blue A
Pink/Blue A
Pin no.
31
36
37
38
39
40
32
33
34
35
Cable colors
Orange/Blue B
Gray/Blue B
White/Blue B
Yellow/Blue B
Pink/Blue B
Orange/Blue C
Gray/Blue C
White/Blue C
Yellow/Blue C
Pink/Blue C
Pin no.
41
46
47
48
49
50
42
43
44
45
Cable colors
Orange/Blue D
Gray/Blue D
White/Blue D
Yellow/Blue D
Pink/Blue D
Orange/Blue E
Gray/Blue E
White/Blue E
Yellow/Blue E
Pink/Blue E
3-181
External I/O cable
3 Controller
■ Connections and outside dimensions
The sheath of each signal cable (50 lines) is color indicated and marked with dots. Refer to the cable color speci
fications in
"Table 3-33: Connector pin numbers and cable colors" when making the connections.
(Eg.) Pin number: color indication
1 : Orange / Red / A
Type of dot mark (see figure below)
Color of dot mark
Color of sheath
Type of dot mark
A type
B type
C type
D type
E type
1
1.5
1.5
1.5
1.5
Dot pattern
18.5
18.5
18.5
18.5
Continuous
Type of dot mark
F type
G type
H type
I type
J type
Dot pattern
3
18.5
3
18.5
3
7.5
18.5
18.5
7.5
Continuous
5000
26
1
50
25
13.54
16.2 9.27 35.7
Receptacle type (PCB side):57AE-40500-21D(D8)
Plug type (cable side):57YE-30500-2(D8)
Note1)
Maker
……DDK
……DDK
Note1) The type of the plug shows the specification of this cable.
The following connector is recommended when user make the cable.
・Plug type (cable side) : 57E series (Soldering type).....................................................DDK
57FE series (Flat cable pressure connection type)......DDK
Fig.3-58 : Connections and outside dimensions
External I/O cable 3-182
3 Controller
(6) Personal computer cable
■ Order type: CR760 controller ........................● 2D-232CBL03M (for PC/AT)
■ Outline
This is the RS-232 interface cable used for connecting the controller with a personal com
puter. The personal computer on hand may be usable with the above interface cable. Con
firm the connection specifications when placing an order.
Personal computer cables for the PC/AT compatible model is available.
■ Configuration
Table 3-34 : Configuration device
Part name
Personal computer cable (for PC/AT)
Note1) Mass indicates one set.
■ Specifications
Type
2D-232CBL03M
Qty.
Mass(kg)
Note1)
1pc.
4
Remarks
3m, D-SUB 9 pin
2D-232CBL03M
Robot controller side
(signal, pin number)
(Not use) DCD 1
R×D 2
T×D 3
DTR 4
DSR 6
RTS 7
CTS 8
GND 5
(Not use) RI 9
6
1 1
Personal computer side
(signal, pin number)
1 DCD
2 R×D
3 T×D
4 DTR
6 DSR
7 RTS
8 CTS
5 GND
9 RI (Not use)
6
9
5
Robot controller side
Table 3-35 : Connectors used with cable
Connection
Controller side
Personal computer side
Name
Connector
Case cover
Connector
Case cover
Part name
17JE-23090-02(D1)
17JE-09H-1A4-CF
HDEB-9S(05)
HDE-CTH1(4-40)(10)
5
9
Personal computer side
Maker
DDK
DDK
HIROSEDENKI
HIROSEDENKI
Fig.3-59 : Personal computer cable connection
3-183
Personal computer cable
3 Controller
(7) CC-Link interface
■ Order type: ● 2D-TZ576
■ Outline
The CC-Link interface is the optioninterface to not only add bit data to the robot controller. but also to add CC-Link field network function that allows cyclic transmission of word data.
■ Configuration
Table 3-36 : Configuration device
Part name Type
CC-Link interface
Manual
Ferrite core
Cable clamp
TZ576
BFP-A8701
E04SR301334
AL4
AL5
Note1) Mass indicates one set.
Qty.
2
2
1
1
2
Table 3-37 : Procured by the customer
Part name Type
Master station
QJ61BT11(Q series)
QJ61BT11N(Q series)
AJ61QBT11(QnA series)
A1SJ61QBT11(QnAS series)
AJ61BT11(A series)
A1SJ61BT11(AnS series)
A80BD-J61BT11(personal computer board)
Communication cable -
Terminal resistor -
Mass(kg)
Note1)
0.6
-
-
-
-
Qty.
1
1
1
Remarks
Be sure to install this for noise countermeasure.
Remarks
FX series products are not supported.
Shielded 3-core twisted cable
This cable may be manufactured by the customer.
110Ω or 130Ω is recommended.
Robot arm
CC-Link interface card
(This option)
Controller
(* The controller is an example.)
Fig.3-60 : Example of CC-Link Product Configuration
パ ー ト ナ ー メ ー カ ー の 機 器 device computer
CC-Link interface 3-184
3 Controller
■ Specifications
Table 3-38 : Specifications
Item
Communication function
Station type
Support station
The version corresponding to CC-Link
Mountable option slot
Number of mountable CC-Link interface cards
Number of stations
Specifications Remarks
Bit data and word data can be transmitted.
Word data are used by the registers.
Intelligent device station
Note1)
Local station
Ver.2
No master station function
The extended cyclic setup is possible.
CR750/CR751 controller: Slot 1, 2
CR760 controller: Slot 1 to 3
1
1 to 64 stations
10M/5M/2.5M/625K/156K bps
1 to 64
1/2/3/4
1/2/4/8
Each 896 points
Multiple CC-Link interface cards cannot be inserted.
When four stations are occupied, continuous station numbers are used. The station numbers are set by a DIP switch.
This is set by the rotary SW.
When two or more stations are occupied, continuous station numbers are used.
The two last cannot be used.
Transmission speed
Station number
Number of occupied stations
Extended cyclic setup
Maximum link point
Extended cyclic setup
Remote I/O
(RX, RY).
Remote register
(RWr, RWw)
-
Each 128 register 16 bits/register
1 fold setup
2 fold setup
3 fold setup
4 fold setup
32 point 32 point 64 point 128 point Link point per set
When one station is occupied
Remote I/O
(RX, RY).
Remote register
( RWw)
Remote register
(RWr)
Remote I/O
(RX, RY).
When two stations is occupied
When three stations is occupied
Remote register
( RWw)
Remote register
(RWr)
Remote I/O
(RX, RY).
Remote register
( RWw)
When four stations is occupied
Remote register
(RWr)
Remote I/O
(RX, RY).
Remote register
( RWw)
Remote register
(RWr)
Number of the maximum occupancy station
The I/O first number of the robot controller.
4 word
4 word
8 word
8 word
16 word
16 word
32 word
32 word
64 point 96 point 192 point 384 point
8 word 16 word 32 word
8 word 16 word 32 word
64 word
64 word
96 point 160 point 320 point 640 point
12 word 24 word 48 word
12 word 24 word 48 word
96 word
96 word
128 point 224 point 448 point 896 point
16 word 32 word 64 word 128 word
16 word 32 word 64 word 128 word
4 stations
No. 6000 -.
The number corresponding to the station number by the setup of the parameter
"CCFIX."
Note1) The CC-Link interface supports neither the transient transmission function nor the FX series.
3-185
CC-Link interface
3 Controller
■ Functions
(1) Communication function
・ The number of usable points is 896 points maximum for bit control and 128 points maximum for word control.
(2) Easy setup
・ The CC-Link interface card can be set by a rotary switch or DIP switch.
・No separate space is required to mount the CC-Link interface card as it is embedded in the robot controller (can only be mounted into slot 2).
・ Easy wiring since only four terminals need to be connected.
・ Dedicated commands have been added to MELFA-BASIC V (robot programming language); thus, no complex interface programming is required.
(3) High-speed response
・The link scan time when connecting 64 stations is approximately 7.2 ms, achieving superior high-speed response performance.
・ A transmission speed can be selected from 10M, 5M, 2.5M, 625K and 156K bps according to the transmission distance.
CC-Link interface 3-186
3 Controller
(8) Extension memory cassette
■ Order type: CR760 controller ........................● 2D-TZ454
■ Outline
Used to increase the total number of teaching points in the robot program.
■ Configuration
Table 3-39 : Configuration device
Part name
Extension memory cassette
Note1) Mass indicates one set.
Type
2D-TZ454
Qty.
1
Mass(kg)
Note1)
0.1
Remarks
■ Specifications
Table 3-40 : Specifications
Items
External dimensions
Mass
Connection method
Memory size
Note1)
Specifications
Approx. 94(W)X65(D)X15(H) mm
Approx. 0.2 kg
Connection using a special connector
Teaching point number: 37,800
Steps number: 75,600
Program number: 256
Remarks
Excluding the connection connector
The sum total value combined with the standard are
Teaching point number: 50,800
Steps number: 101,600
Program number: 512
Backup Backup using the controller's internal battery
Note1) As for the standard points, after adding an expansion memory cassette, the information in all backup memory areas in the controller is copied into the expansion memory cassette. Therefore, please note that if the expansion memory cassette is removed after it has been added, there will be no program left in the controller.
[CAUTION]
1) Inserting and removing the memory cassette
A memory cassette cannot be inserted or removed while the control power is on. Please turn off the con
trol power before handling the memory cassette to avoid destroying the memory information in the cas
sette.
The memory cassette alone does not have a memory backup function. Data security in the memory cas
sette removed from the controller is not guaranteed.
2) Backup using the RT ToolBox 2
The table below shows the time to back up the program using RT ToolBox2.
Interface
Ethernet interface (100Mbps)
USB (12Mbps)
RS-232 (9600bps)
Backup time
Approx. 100 seconds
Approx. 260 seconds
Approx. 200 minutes
Remarks
Each time in the table applies to the program consuming all of the available memory.
3-187
Extension memory cassette
3 Controller
(9) Controller protection box
■ Order type: CR750 controller ........................CR750-MB
CR751 controller ........................CR751-MB
■ Outline
<CR750-MB>
<CR751-MB>
By putting the controller in this box, the controller can be protected from oil mist environment.
Use this option, when the controller is installed where environment is oil mist such as machine shop etc.
■ Configuration
Table 3-41 : Configuration equipment and types
Part name Type Qty.
CR750 controller
Controller protection box
Internal power cable
CR750-MB 1
3
Internal earth cable
Label for serial number
Transparent seal
Cable tie
Screw for fixing of the controller mounting plate
Instruction Manual
CR751 controller
Controller protection box
Internal power cable
T50L
M4x8
BFP-A8896
CR751-MB
Internal earth cable
1
4
4
1
1
1
Label for serial number
Transparent seal
Cable tie
Screw for fixing of the controller mounting plate
Instruction Manual
Note1) Mass indicates one set.
T50L
M4x8
BFP-A8997
4
4
1
1
1
1
2
1
Mass (Kg)
Note1)
22
-
21
-
Remarks
For connection between the power supply relay terminal and controller inside this box
For connection between the grounding terminal and controller inside this box
For connection between the power supply relay terminal and controller inside this box
For connection between the grounding terminal and controller inside this box
Controller protection box 3-188
3 Controller
■ Specifications
Table 3-42 : Specifications
Item Unit
CR750 controller
Outside dimension
Mass
Construction
Grounding
Paint color
CR751 controller
Outside dimension
Mass
Construction
Grounding
Paint color mm
Kg
Ω mm
Kg
Ω
Specifications
500(W)×725(D)×250(H)
22
Self-contained floor type
100 or less (class D grounding)
Dark gray
500(W)×725(D)×250(H)
21
Self-contained floor type
100 or less (class D grounding)
Dark gray
IP54
Remarks
Excluding protrusions
IP54
Equivalent to Munsell: 3.5PB3.2/0.8
Excluding protrusions
Equivalent to Munsell: 3.5PB3.2/0.8
(1) The robot must be grounded by the customer.
(2) The cable for primary power supply connection and the grounding cable are customer preparations.
3-189
Controller protection box
3 Controller
■ Outside dimension
<CR750-MB>
Cable cover
Controller setting position
Drain hole
Rubber foot fixa
tion screw for placing vertically
(Four places)
Fig.3-61 : Outside dimension of CR750-MB
Controller protection box 3-190
3 Controller
<CR751-MB>
Controller setting position
Rubber foot fixation screw for placing ver
tically (Four places)
Cable cover
Fig.3-62 : Outside dimension of CR751-MB
3-191
Controller protection box
■ Names of each part
<CR750-MB>
Mode key switch
Window
Label for serial number
Transparent seal
T/B connector
Front view
Mode change SW extension cable
Controller
T/B junction cable
Front side of the controller
Controller mounting plate
Fixing lever
Power supply relay terminal
(M4 screw)
Grounding terminal (M4 screw)
Cable cover
Cable tie
External emergency stop wiring (customer preparation)
Machine cable CN2
Power supply cable,
Grounding cable
(customer preparation)
Machine cable CN1
Internal earth cable Internal power cable
Upper view
Fig.3-63 : Names of each part (CR750-MB)
3 Controller
Controller protection box 3-192
3 Controller
<CR751-MB>
Label for serial number
Transparent seal
Front view
Grounding terminal (M4 screw)
Power supply relay terminal
(M4 screw)
Controller mounting plate
Controller
Power supply cable,
Grounding cable
(customer preparation)
Machine cable CN1
Front side of the controller
Machine cable CN2
External emergency stop wiring (customer preparation)
Cable cover
Cable tie
Fixing lever
Internal power cable
Upper view
Internal earth cable
Fig.3-64 : Names of each part (CR751-MB)
3-193
Controller protection box
3 Controller
■ Wiring system diagram
<CR750-MB>
Single phase: RV-4F series
Controller protection box
Power supply cable
Grounding cable
(L1)
(L2)
Terminal
Internal power cable
(L1)
(L2)
FG
ACIN
CN1
CN2
CNUSR
11/12
Controller
AC fan
Internal earth cable
FG FG FG
Grounding terminal
Single phase/Three phase: RV-7F/13F series
Controller protection box
Terminal
Note1)
Internal power cable
Power supply cable
Grounding cable
(L1)
(L2)
(L3)
(L1)
(L2)
(L3)
FG
ACIN
CN1
CN2
CNUSR
11/12
Controller
AC fan
Internal earth cable
FG FG FG
Grounding terminal
Note1) When using the controller for the three phases with the single-phase power supply, connect the primary power supply to L1 and L2 electric terminal of the protection box so that the power supply may be supplied to the heat-exchanger AC fan of the protection box.
Connects with L1 and L3 electric terminal to the ACIN terminal block of the controller. Refer to the separate manual "Controller setup, basic operation, and maintenance" for detail of connecting the power cable and the grounding cable.
Fig.3-65 : Wiring system diagram (CR750-MB)
Controller protection box 3-194
3 Controller
<CR751-MB>
Single phase: RV-4F series
Controller protection box
Terminal
Internal power cable
Controller
Power supply cable
Grounding cable
AC fan
Internal earth cable
Grounding terminal
Single phase/Three phase: RV-7F/13F series
Controller protection box
Terminal
Note1)
Internal power cable
Controller
Power supply cable
Grounding cable
AC fan
Internal earth cable
Grounding terminal
Note1) When using the controller for the three phases with the single-phase power supply, connect the primary power supply to L1 and L2 electric terminal of the protection box so that the power supply may be supplied to the heat-exchanger AC fan of the protection box.
Connects with L1 and L3 electric terminal to the ACIN terminal block of the controller. Refer to the separate manual "Controller setup, basic operation, and maintenance" for detail of connecting the power cable and the grounding cable.
Fig.3-66 : Wiring system diagram (CR751-MB)
3-195
Controller protection box
3 Controller
■ Installation dimensions
<CR750-MB>
Placed horizontally
150mm or more
30mm or more
150mm or more
Placed vertically
150mm or more
30mm or more
150mm or more
150mm or more
150mm or more
Fig.3-67 : Installation dimensions (CR750-MB)
Controller protection box 3-196
3 Controller
<CR751-MB>
Placed horizontally
150mm or more
30mm or more
150mm or more
Placed vertically
150mm or more
30mm or more
150mm or more
150mm or more
150mm or more
Fig.3-68 : Installation dimensions (CR751-MB)
3-197
Controller protection box
3 Controller
(10) MELSOFT RT ToolBox2/RT ToolBox2 mini
■ Order type : ● MELSOFT
RT ToolBox2
*For windows CD-ROM
● MELSOFT
RT ToolBox2 mini
: 3D-11C-WINE
*For windows CD-ROM : 3D-12C-WINE
■ Outline
This is handy software that fully uses the personal computer functions. It can be used in various stages from the robot specifications study (tact study, etc.) to the design support
(creation and editing of programs), start up support (execution, control and debugging of program), and maintenance.
The "personal computer support software" which supports these function fully, and the
"personal computer support software mini" which does not have the simulation function are available.
■ Configuration
Table 3-43 : Product configuration
Part name Type
RT ToolBox2
RT ToolBox2 mini
3D-11C-WINE
3D-12C-WINE
Note1) Mass indicates one set.
Medium
CD-ROM
CD-ROM
Mass (kg)
Note1)
0.2
0.2
Remarks
■ Features
(1) Simple operation with guidance method and menu method
The Windows standard is used for windows operation, so the controller initialization and startup operations can be carried out easily by following the instructions given on the screen. Even a beginner can easily carry out the series of operations from program creation to execution.
(2) Increased work efficiency with ample support functions
The work efficiency is greatly improved with the multi-window method that carries out multiple steps and dis
plays in parallel. The renumbering function, and copy, search, syntax check and step execution are especially sufficient, and are extremely useful when editing or debugging the program.
With the simulation function support, the program can be debugged and the tact checked before starting the machine at the site. This allows the on-site startup work efficiently to be greatly improved.
(3) The maintenance forecast function increases the efficiency of maintenance work. Analyze the load condition while the robot is actually operating. Based on this analysis, calculate the time for maintenance, such as lubri
cation and belt replacement. By utilizing this information, the line stop time as well as the maintenance costs can be reduced.
(4) The position recovery support function increases the recovery efficiency in the event of origin position dis
placement. This function compensates the origin settings and position data by just reproducing several previ
ous teaching points when hand and/or arm displacement occurs, when replacing the motor and the belts, or when reloading the robot. This function can reduce the time required for recovery.
MELSOFT RT ToolBox2/RT ToolBox2 mini 3-198
3 Controller
■ Functions
Table 3-44 : Functions
Function
Compatible model
Program editing functions
Editing functions
Simulation func
tion
Monitor func
tions
Maintenance function
Control func
tions
Debugging func
tions
Functional existence
Note1)
○
○
○
○
○
○
○
○
○
○
○
×
○
○
Details
Personal computer running Windows XP, Windows Vista, Windows 7,
Windows 8, or Windows 8.1.
Note2)
・ MELFA BASIC V language compatible
・ Multiple editing screen simultaneously display
・ Command input, comment writing
・ Position data editing
・ File operation (writing to controller, floppy disk, personal computer)
・ Search and replace function (using characters, line Nos., labels)
・ Copy, cut, paste, insert (per character, line), undo (per command statement, position conversion)
・ Line No. automatic generation, renumbering
・ Batch syntax check
・ Command template
・ Position conversion batch editing
・ Position variable template
・ Print, print preview
・ Program file control (list, copy, movement, delete, content compari
son, name change, protect)
・ Direct editing of program in controller
・ Confirmation of robot program operation (step execution, direct exe
cution)
・ Off-line simulation of robot program operation using CG (computer graphics)
・ Tact time calculation
・ Robot operation monitor (robot operation state, stop signal, error monitor, program monitor (execution program, variables), general-pur
pose input/output signals (forced output possible), dedicated input/ output signals, operation confirmation (operation range, current posi
tion, hand, etc.)
・ Operation monitor (working time statistics, production information, robot version)
・ Servo monitor (load)
・ Parameter setting
・ Batch, divided backup
RT ToolBox2 mini
(3D-12C-WINE)
RT ToolBox2
(3D-11C-WINE)
Note1) The functions included with the RT ToolBox2 and the RT ToolBox2 mini are shown below.
○ : Function provided ×: Function not provided
Note2) Recommend corresponding to CE Marking, an FCC standard, and a VCCI standard.
3-199
MELSOFT RT ToolBox2/RT ToolBox2 mini
3 Controller
(11) Instruction Manual (bookbinding)
■ Order type: ● 5F-FF01-PE01...............RV-4F-D/7F-D/13F-D/20F-D/35F-D/50F-D/70F-D series
■ Outline
This is a printed version of the CD-ROM (instruction manual) supplied with this product.
■ Configuration
Table 3-45 : Product configuration
Name
Instruction Manual
Safety Manual
Standard Specifications
Robot Arm Setup & Maintenance
Controller Setup, Basic Operation and Maintenance
Detailed Explanation of Functions and Operations
Troubleshooting
Additional axis function
Tracking Function Manual
GOT Direct Connection Extended Function
Note1)
Mass indicates one set.
Type
5F-FF01-PE01
BFP-A8006
BFP-A8931
BFP-A8935
BFP-A8867
BFP-A8869
BFP-A8871
BFP-A8663
BFP-A8664
BFP-A8849
Mass (Kg)
Note1)
2.6
-
-
-
-
-
-
-
-
-
Specifications
The instructions manual set of RV-4F-D series, RV-
7F-D series, RV-13F-D series, and RV-50F-D series.
Items relating to safety in handling the robot
Specification of the robot arm and controller
Installation method of the robot arm, jog operation, and maintenance and inspection procedures
Installation method of the controller, basic operation, and maintenance and inspection procedures
Functions of the controller and T/B, operation method, and explanation of MELFA-BASIC V
Causes of errors occurred and their countermeasures
Function of the additional axis, operation method.
Function of the Tracking, operation method.
Explains of data configuration of shared memory, monitoring, and operating procedures, between the
GOT and controller.
Instruction Manual (bookbinding) 3-200
3 Controller
3.11 Maintenance parts
when required. Some Mitsubishi-designated parts differ from the maker's standard parts. Thus, confirm the part name, robot arm and controller serial No. and purchase the parts from your dealer.
Table 3-46 : Controller consumable parts list
No. Name Type
Note1)
1 Lithium battery Q6BAT
Qty.
1
Usage place Supplier
CR750/CR760 controller:
Inside of the interface cover
CR751 controller:
Inside of the filter cover
Inside the filter cover
Mitsubishi Electric
2 Filter CR750 controller:
BKOFA0773H42
CR751 controller:
BKOFA0773H41
1
Note1) Confirm the robot arm serial No., and contact the dealer or service branch of Mitsubishi Electric Co., for the type.
3-201
Maintenance parts
4Software
4 Software
4.1 List of commands
The available new functions in MELFA-BASIC V are given in
Table 4-1 : List of MELFA-BASIC V commands
Type Class Function Input format (example)
Joint interpolation Moves to the designated position with joint interpolation.
Linear interpolation Moves to the designated position with linear interpolation.
Circular interpolation Moves along a designated arc (start point → passing point → start point
(end point)) with 3-dimensional circular interpolation (360 degrees).
Speed designation
Moves along a designated arc (start point → passing point → end point) with 3-dimensional circular interpolation.
Moves along the arc on the opposite side of a designated arc (start point
→ reference point → end point) with 3-dimensional circular interpola
tion.
Moves along a set arc (start point → end point) with 3-dimensional cir
cular interpolation.
Designates the speed for various interpolation operations with a per
centage (0.1% unit).
Designate the speed for joint interpolation operation with a percentage
(0.1% unit).
Designates the speed for linear and circular interpolation with a numeri
cal value (mm/s unit).
Designates the acceleration/deceleration time as a percentage in respect to the predetermined maximum acceleration/deceleration. (1% unit)
Automatically adjusts the acceleration/deceleration according to the parameter setting value.
Operation
Position control
Float control
Pallet
Singular point pas sage
-
Mov P1
Mvs P1
Mvc P1,P2,P1
Mvr P1,P2,P3
Mvr2 P1,P9,P3
Mvr3 P1,P9,P3
Ovrd 100
JOvrd 100
Spd 123.5
Accel 50,80
Oadl ON
Sets the hand and work conditions for automatic adjustment of the acceleration/deceleration.
Adds a process unconditionally to the operation.
Loadset 1,1
Adds a process conditionally to the operation.
Designates smooth operation.
Wth
WthIf
Cnt 1,100,200
Performance of movement is upgraded corresponding to the application. MvTune 4
Designates the positioning completion conditions with a No. of pulses.
Fine 200
Designates the positioning completion conditions with a distance in a straight line
Designates the positioning completion conditions with a joint interpola
tion.
Fine 1, P
Fine 0.5, J, 2
Turns the servo power ON/OFF for all axes.
Limits the operation of each axis so that the designated torque is not exceeded.
Designates the base conversion data.
Designates the tool conversion data.
The robot arm rigidity is lowered and softened. (XYZ coordinate system) Cmp Pos ,&B00000011
The robot arm rigidity is lowered and softened. (JOINT coordinate sys
tem)
Cmp Jnt ,&B00000011
The robot arm rigidity is lowered and softened. (TOOL coordinate sys
tem)
The robot arm rigidity is returned to the normal state.
Cmp Tool ,&B00000011
Cmp Off
The robot arm rigidity is designated.
Defines the pallet.
Operates the pallet grid point position.
Move to a specified position using linear interpolation passing through a singular point.
Servo OFF
Torq 4,10
Base P1
Tool P1
CmpG
1.0,1.0,1.0,1.0,1.0,1.0,1.0,1.0
Def Plt 1,P1,P2,P3,P4,5,3,1
Plt 1,M1
Mvs P1 Type 0,2
List of commands 4-202
4Software
Type Class
Branching
Function
Branches unconditionally to the designated place.
Branches according to the designated conditions.
Input format (example)
GoTo 120
If M1=1 Then GoTo *L100
Else GoTo 20
End If
For M1=1 TO 10 Repeats until the designated end conditions are satisfied.
Repeats while the designated conditions are satisfied.
Branches corresponding to the designated expression value.
Executes program block corresponding to the designated expression value..
Next M1
While M1<10
WEnd
On M1 GoTo *La1, *Lb2, *Lc3
Select
Case 1
Break
Case 2
Collision detection
Subroutine
Interrupt
Wait
Stop
End
Hand open
Hand close
Assignment
Input
Output
Moves the program process to the next line.
Set to enable/disable the collision detection.
Set the detection level of the collision detection.
Executes the designated subroutine. (Within program)
Returns from the subroutine.
Executes the designated program.
Defines the program argument executed with the CALLP command.
Executes the subroutine corresponding to the designated expression value.
Defines the interrupt conditions and process.
Enables/disables the interrupt.
Defines the start line of the program to be executed when an interrupt is generated from the communication line.
Enables the interrupt from the communication line.
Disables the interrupt from the communication line.
Stops the interrupt from the communication line.
Designates the wait time, and the output signal pulse output time. (0.01s unit)
Waits until the variable becomes the designated value.
Stops the program execution.
Generates an error. During program execution, continue, stop or servo
OFF can be designated.
Ends the program execution.
Opens the designated hand.
Closes the designated hand.
Defines the input/output variables.
Retrieves the general-purpose input signal.
Calls out the general-purpose output signal.
Break
End Select
Skip
ColChk ON/OFF
ColLvl 100,80,,,,,,
GoSub *L200
Return
CallP "P10",M1,P1
FPrm M10,P10
On M1 GoSub *La1, *Lb2, *Lc3
Def Act 1, M1=1 GoTo *L100
Act 1=1
On Com(1) GoSub *L100
Com(1) On
Com(1) Off
Com(1) Stop
Dly 0.5
Wait M_In(1)=1
Hlt
Error 9000
End
HOpen 1
HClose 1
Def IO PORT1=BIT,0
M1=M_In(1)
M_Out(1) =0
Mechanism designa
tion
Selection
Start/stop
Acquires the mechanism with the designated mechanism No.
Releases the mechanism with the designated mechanism No.
Selects the designated program for the designated slot.
Carries out parallel execution of the designated program.
Stops parallel execution of the designated program.
Returns the designated program's execution line to the head and enters the program selection enabled state.
GetM 1
RelM 1
XLoad 2,"P102"
XRun 3,"100",0
XStp 3
XRst 3
4-203
List of commands
4Software
Type Class
Definition
Clear
File
Comment
Label
Function
Defines the integer type or real number type variable.
Defines the character string variable.
efines the layout variable. (Up to 3-dimensional possible)
Defines the joint variable.
Defines the position variable.
Defines the function.
Clears the general-purpose output signal, variables in program, variables between programs, etc.
Opens a file.
Closes a file.
Inputs data from a file.
Outputs data to a file.
Describes a comment.
Indicates the branching destination.
Input format (example)
Def Inte KAISUU
Def Char MESSAGE
Dim PDATA(2,3)
Def Jnt TAIHI
Def Pos TORU
Def FN TASU(A,B)=A+B
Clr 1
Open "COM1:" AS #1
Close #1
Input# 1,M1
Print# 1,M1
Rem "ABC"
*SUB1
List of commands 4-204
advertisement
Related manuals
advertisement
Table of contents
- 14 1 General configuration
- 14 1.1 Structural equipment
- 14 1.1.1 Standard structural equipment
- 14 1.1.2 Special specifications
- 14 1.1.3 Options
- 14 1.1.4 Maintenance parts
- 14 1.2 Model type name of robot
- 14 1.2.1 How to identify the robot model
- 14 (1) RV-4F/7F/13F series
- 14 (2) RV-50F series
- 14 1.2.2 Combination of the robot arm and the controller
- 14 (1) CR750 controller
- 14 (2) CR751 controller
- 14 (3) CR760 controller
- 14 1.2.3 Internal wiring and piping specification types
- 14 1.3 CE marking specifications
- 14 (1) CR750 controller
- 14 (2) CR751 controller
- 14 1.4 Indirect export
- 14 1.5 Instruction manuals
- 14 1.6 Contents of the structural equipment
- 14 1.6.1 Robot arm
- 14 (1) RV-4F/7F/13F series
- 14 (2) RV-50F series
- 14 1.6.2 Controller
- 14 (1) CR750controller
- 14 (2) CR751 controller
- 14 (3) CR760 controller
- 14 1.7 Contents of the Option equipment and special specification
- 14 (1) RV-4F/7F/13F series
- 14 (2) RV-50F series
- 15 2 Robot arm
- 15 2.1 Standard specifications
- 15 2.1.1 Basic specifications
- 15 (1) RV-4F/7F series
- 15 (2) RV-13F series
- 15 (3) RV-50F series
- 15 2.1.2 The counter-force applied to the installation surface
- 15 2.2 Definition of specifications
- 15 2.2.1 Pose repeatability
- 15 2.2.2 Rated load (mass capacity)
- 15 2.2.3 Relationships Among Mass Capacity, Speed, and Acceleration/Deceleration Speed
- 15 (1) Setting Load Capacity and Size (Hand Conditions)
- 15 2.2.4 Vibrations at the Tip of the Arm during Low-Speed Operation of the Robot
- 15 2.2.5 Collision detection
- 15 2.2.6 Protection specifications
- 15 (1) Types of protection specifications
- 15 (2) About the use with the bad environment
- 15 2.2.7 Clean specifications
- 15 (1) Types of clean specifications
- 15 2.3 Names of each part of the robot
- 15 2.4 Outside dimensions ・ Operating range diagram
- 15 (1) RV-4F
- 15 (2) RV-4FL/4FJL
- 15 (3) RV-7F
- 74 (4) RV-7FL
- 74 (5) RV-7FLL
- 74 (6) RV-13F/20F
- 74 (7) RV-13FL
- 74 (8) RV-50F series
- 74 2.4.1 Outside dimensions of machine cables
- 74 (1) Connection with the CR750 controller
- 74 (2) Connection with the CR751 controller
- 74 (3) Connection with CR760 controller
- 74 2.5 Tooling
- 74 2.5.1 Wiring and piping for hand
- 74 (1) RV-4F/7F/13F series standard specification (with no internal wiring and piping)
- 74 (2) RV-4F/7F/13F series internal wiring and piping specification (SH01)
- 74 (3) RV-4F/7F/13F series internal wiring and piping specification (SH02)
- 74 (4) RV-4F/7F/13F series internal wiring and piping specification (SH03)
- 74 (5) RV-4F/7F/13F series internal wiring and piping specification (SH04)
- 74 (6) RV-4F/7F/13F series internal wiring and piping specification (SH05)
- 74 (7) RV-50F series
- 74 2.5.2 Internal air piping
- 74 (1) RV-4F/7F/13F series
- 74 (2) RV-50F series
- 74 2.5.3 Internal wiring for the hand output cable
- 74 (1) RV-4F/7F/13F series
- 74 (2) RV-50F series
- 74 2.5.4 Internal wiring for the hand input cable
- 74 (1) RV-4F/7F/13F series
- 74 (2) RV-50F series
- 74 2.5.5 Ethernet cable, option wiring cable
- 74 (1) RV-4F/7F/13F series
- 74 (2) RV-50F series
- 74 2.5.6 Wiring and piping system diagram for hand
- 74 (1) RV-4F/7F/13F series standard specification (with no internal wiring and piping)
- 74 (2) RV-4F/7F/13F series internal wiring and piping specification (SH01)
- 74 (3) RV-4F/7F/13F series internal wiring and piping specification (SH02)
- 74 (4) RV-4F/7F/13F series internal wiring and piping specification (SH03)
- 74 (5) RV-4F/7F/13F series internal wiring and piping specification (SH04)
- 74 (6) RV-4F/7F/13F series internal wiring and piping specification (SH05)
- 74 (7) RV-50F series
- 74 2.5.7 Electrical specifications of hand input/output: For RV-4F/7F/13F series
- 74 2.6 Hand I/O card (RZ398 card): For RV-50F series
- 74 2.6.1 Specifications
- 74 2.6.2 I/O connector for hand
- 74 (1) Outline of RZ398 card
- 74 2.6.3 Air supply circuit example for the hand
- 74 2.6.4 About the Installation of Tooling Wiring and Piping
- 74 2.7 Shipping special specifications, options, and maintenance parts
- 74 2.7.1 Shipping special specifications
- 74 (1) Machine cable
- 74 2.8 Options
- 74 (1) Machine cable extension
- 74 (2) J1 axis operating range change
- 74 (3) Solenoid valve set
- 74 (4) Hand input cable
- 74 (5) Hand output cable
- 74 (6) Hand curl tube
- 74 (7) Forearm external wiring set/ Base external wiring set
- 74 2.9 About Overhaul
- 156 2.10 Maintenance parts
- 157 3 Controller
- 157 3.1 Standard specifications
- 157 3.1.1 Basic specifications
- 157 3.1.2 Protection specifications and operating supply
- 157 3.2 Names of each part
- 157 3.2.1 Controller
- 157 (1) CR750 controller
- 157 (2) CR751 controller
- 157 (3) CR760 controller
- 157 3.3 Outside dimensions/Installation dimensions
- 157 3.3.1 Outside dimensions
- 157 (1) CR750 controller
- 157 (2) CR751 controller
- 157 (3) CR760 controller
- 157 3.3.2 Installation dimensions
- 157 (1) CR750 controller
- 157 (2) CR751 controller: RV-4F/7F series
- 157 (3) CR751 controller: RV-13F series
- 157 (4) CR760 controller
- 157 3.4 External input/output
- 157 3.4.1 Types
- 157 3.5 Dedicated input/output
- 157 3.6 Emergency stop input and output etc
- 157 3.6.1 Connection of the external emergency stop
- 157 (1) CR750 controller
- 157 (2) CR751 controller
- 157 (3) CR760 controller
- 157 3.6.2 Special stop input (SKIP)
- 157 (1) CR750 controller
- 157 (2) CR751 controller
- 157 (3) CR760 controller
- 157 3.6.3 Door switch function
- 157 3.6.4 Enabling device function
- 157 (1) When door is opening
- 157 (2) When door is closing
- 157 (3) Automatic Operation/Jog Operation/Brake Release and Necessary Switch Settings
- 157 3.7 Mode changeover switch input
- 157 (1) Specification of the key switch interface
- 157 (2) Connection of the mode changeover switch input
- 157 3.8 Additional Axis Function
- 157 3.8.1 Wiring of the Additional Axis Interface
- 157 (1) CR750 controller
- 157 (2) CR751 controller
- 157 (3) CR760 controller
- 157 3.9 Magnet contactor control connector output (AXMC) for addition axes
- 157 (1) Example circuit
- 157 (2) Image of how to connect the controller connector
- 157 3.10 Options
- 157 (1) Teaching pendant (T/B)
- 157 (2) Parallel I/O interface
- 157 (3) External I/O cable
- 157 (4) Parallel I/O unit
- 157 (5) External I/O cable
- 157 (6) Personal computer cable
- 218 (7) CC-Link interface
- 218 (8) Extension memory cassette
- 218 (9) Controller protection box
- 218 (10) MELSOFT RT ToolBox2/RT ToolBox2 mini
- 218 (11) Instruction Manual (bookbinding)
- 218 3.11 Maintenance parts
- 219 4 Software
- 219 4.1 List of commands
- 219 4.2 List of parameters
- 220 5 Instruction Manual
- 220 5.1 The details of each instruction manuals
- 221 6 Safety
- 221 6.1 Safety
- 221 6.1.1 Self-diagnosis stop functions
- 221 6.1.2 External input/output signals that can be used for safety protection measures
- 221 6.1.3 Precautions for using robot
- 221 6.1.4 Safety measures for automatic operation
- 221 6.1.5 Safety measures for teaching
- 221 6.1.6 Safety measures for maintenance and inspections, etc
- 221 6.1.7 Examples of safety measures
- 221 (1) CR750 controller
- 221 (2) CR751 controller
- 221 (3) CR760 controller
- 221 (4) External emergency stop connection [supplementary explanation]
- 221 6.2 Working environment
- 221 6.3 Precautions for handling
- 221 6.4 EMC installation guideline
- 221 6.4.1 Outlines
- 221 6.4.2 EMC directive
- 221 6.4.3 EMC measures
- 221 6.4.4 Component parts for EMC measures
- 221 (1) Ferrite core
- 221 (2) Line noise filter