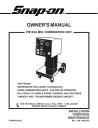
advertisement
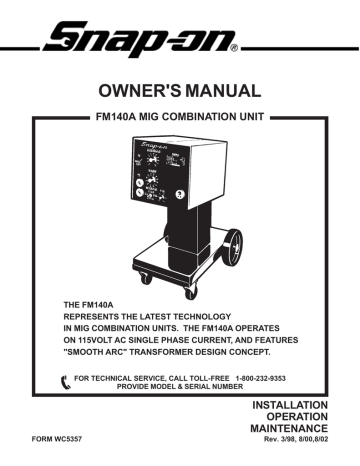
TROUBLE SHOOTING
(SYMBOL*)
FOR TECH. SERVICE, CALL TOLL-FREE 1-800-232-9353
The Trouble Shooting Chart is a guide in identifying and correcting possible troubles which may occur when operating this equipment.
FAULT POSSIBLE CAUSE REMEDY
Main power on, torch trigger activated, no response.
EQUIPMENT MALFUNCTION
No main power, fan does not operate,
"on" indicator
FM140A switch is "OFF".
Wall breaker is "tripped".
"Open" circuit breaker on FM140A.
(CB1)
(CB1) light is off.
Loose or broken connection in power input circuit.
Turn switch "on".
Reset wall breaker.
Reset or replace breaker.
Tighten or repair connection.
MIG torch unplugged.
Faulty trigger switch.
Fault in torch cable.
(S1)
Loose or broken connection on wiring harness.
Wire feed motor unplugged.
(RC1)
Faulty control transformer.
Check for 28VAC output.
(T2)
Loose spot timer circuit board.
(PC2)
Defective spot timer circuit board.
(CR2)(PC2)
Plug in MIG torch.
Replace micro switch.
Check torch cable for continuity.
Check or repair connections.
Plug in motor.
Install properly.
Replace board.
Main power on, torch trigger activated,
Pressure roll arm unlatched.
Latch arm & add tension.
"Slippage" at drive rolls.
Increase drive roll
Wire path restricted.
tension. See page 7.
Clean path or replace no wire feed but contactor 5 amp mini breaker is operates & gas flows.
tripped.
(CB2)
Wire feed circuit board needs calibrated.
torch liner.
Reset or replace breaker.
Calibrate wire feed circuit board. See page 18.
Replace circuit board.
Defective wire feed circuit board.
(PC1)
Faulty wire feed motor or connection.
(M)
Repair or replace faulty item.
Check motor on a
12VDC battery.
Faulty motor relay.
(CR1)
Sand points or replace relay.
Loose or broken connection.
Tighten or repair connection.
(SYMBOL*)
- USE THIS IDENTIFIER, ALONG WITH THE SCHEMATIC DIAGRAM FOUND IN THE SERVICE
MANUAL, FOR TROUBLE-SHOOTING PURPOSES.
14 Snap-on Tools Corporation Kenosha, WI 53141-1410
TROUBLE SHOOTING (Cont.)
(SYMBOL*)
FOR TECH. SERVICE, CALL 1-800-232-9353
FAULT POSSIBLE CAUSE
EQUIPMENT MALFUNCTION (Cont.)
REMEDY
Main power on, torch trigger activated, no welding current, but gas flows & wire feeds.
Loose torch thumb screw.
Tighten thumb screw.
Broken or loose connection.
Check cables for continuity.
Repair or tighten
Unplugged or faulty power contactor switch.
(W)
#1 Transformer wire off.
"Opened" thermal switch.
(W) connections.
Plug in or replace switch.
Reattach wire.
(TP1)
Faulty diodes.
(D1-D2)
Allow unit to cool, then retry.
Check diodes. See page
17.
Replace tank.
Torch trigger activated, no gas flow,
No shielding gas
- tank empty.
Loose or broken connections.
but contactor Faulty Gas solenoid operates & valve.
(GS) wire feeds.
Clogged gas flow path.
Loose spot timer circuit board.
(PC2)
Defective spot timer circuit board.
(CR2)(PC2)
Tighten or repair connections.
Repair or replace valve.
Locate & clean clog.
Install properly.
Replace board.
"Jerky" or
"slipping" wire feed.
FAULTY WELDS
Worn , kinked or dirty torch Clean or replace liner.
liner.
Wire spool turns too hard.
Lubricate spool hub with a dry lubricant
Worn double v-groove drive roll.
Weak pressure roll spring.
Worn or dirty contact tip.
Worn inlet guide(s).
Sticking pressure roll.
Replace drive roll.
Replace spring.
Replace contact tip.
Clean or replace guides.
Replace pressure roll.
Feed roll tension incorrect.
Adjust feed roll tension. See page 7.
(continued on following page)
Snap-on Tools Corporation Kenosha, WI 53141-1410 15
FAULT
"Birdnesting"
(Wire wrapping around drive rolls)
"Cold" weld puddle.
Heavy spatter.
Porous welds.
TROUBLE SHOOTING (Cont.)
(SYMBOL*)
FOR TECH. SERVICE, CALL TOLL-FREE 1-800-232-9353
POSSIBLE CAUSE
FAULTY WELDS (Cont.)
REMEDY
Excessive feed roll tension.
Reduce tension. See page
7.
Poor alignment.
Make sure wire is properly aligned
Oversize contact tip.
across roller.
Replace contact tip with correct size.
Incorrect machine settings.
Increase heat & wire speed.
Incorrect shielding gas.
Excessive wire stick-out.
Replace with proper gas.
Hold torch closer to
Poor connections.
Faulty diode.
(D1-D2) work.
Check and tighten all connections.
Test diodes, replace faulty diode(s). See page 17.
Incorrect machine settings.
Increase heat, decrease wire feed speed.
Incorrect shielding gas.
Excessive wire stick-out.
Replace with proper gas.
Hold torch closer to work.
No shielding gas.
Not enough gas flow.
Contaminated wire.
Faulty gas solenoid.
Turn on gas.
Check hoses for leaks, make sure cylinder is not empty. Increase flow rate.
Change wire.
Replace solenoid.
(GS)
Incorrect electrode wire.
Use correct wire.
Contaminated base material.
Clean or etch base material.
(SYMBOL*)
- USE THIS IDENTIFIER, ALONG WITH THE SCHEMATIC DIAGRAM FOUND IN THE SERVICE
MANUAL, FOR TROUBLE-SHOOTING PURPOSES.
16 Snap-on Tools Corporation Kenosha, WI 53141-1410
TESTING AND REPLACING DIODES
Silicon diodes have proven to be highly reliable. However, weld spatter build-up in the torch can short out and cause diode overload and consequent failure. The following information is provided as a guide should a failure be suspected.
Silicon diodes exhibit two main fault conditions:
1. "Open Circuit" - causes a reduction in welder output.
2. "Short Circuit" - causes the circuit breaker to trip.
If a fault is suspected, the diode may be tested as follows:
1. Remove the top connection of each diode to be tested.
2. Using a Volt-Ohm Meter set on
RX1K, check for continuity through the diode in both directions. If there is no continuity in either direction, the diode is in "open circuit" condition and must be replaced. If there is continuity in both directions, the diode is in "short circuit" condition and must be replaced. If there is continuity in one direction only, the diode is functioning properly.
3. If all the diodes check out satisfactorily with the Volt-
Ohm Meter, a load check must be made. This is easily accomplished using a twelve volt battery and a twelve volt light bulb connected as shown. Again test for electrical current flow in both directions. The bulb should light in one (1) direction only - not both.
CAUTION
NEVER use a "megger" or a high voltage device to test a diode.
12 VOLT
LIGHT BULB
DIODE
+ -
12 VOLT
BATTERY
12 VOLT
LIGHT BULB
+ -
DIODE 12 VOLT
BATTERY
FIGURE 15. DIODE LOAD CHECK
CONNECTION DIAGRAM
- TEST FOR FLOW IN BOTH DIRECTIONS
4. When replacing diodes, it is very important that a heat conductive compound (Radio Shack
#276-1372) be used where the diode makes contact with the aluminum heat sink. Do not grease the threads on the diode.
Snap-on Tools Corporation Kenosha, WI 53141-1410 17
WIRE FEED CALIBRATION
Due to INPUT LINE VOLTAGE variations supplied to the welding machine. The WIRE FEED SPEED should be checked for proper operation.
TO CHECK
1. Remove any tension on the drive roll.
2. Turn the wire speed dial (on the front of the machine) to "0".
3. Activate the torch trigger.
4. The bottom drive roll should rotate very slowly(non-jerky).
5. If this proves to be true, no adjustment is required.
IF ADJUSTMENT IS REQUIRED
1. Remove the top cover assembly from the unit.
2. Locate the printed circuit boards.
3. Referring to Figure 16, locate the trim resistor, this is located in the upper right hand corner of the wire feed PC board.
4. Turn the wire speed dial (on the front of the machine) to "0".
5. Remove any tension on the drive roll.
6. Activate the torch trigger.
TRIM
RESISTOR
FIGURE 16. WIRE FEED PC BOARD
7. Rotate the trim resistor, back and forth, until the bottom drive roll moves.
8. Calibrate so the bottom drive roll rotates very slowly (nonjerky).
9. If calibrated correctly the wire speed dial (on the front of the machine) should affect the speed of the drive roll from "0" thru
"10".
10. Adjustment is now complete!
18 Snap-on Tools Corporation Kenosha, WI 53141-1410
advertisement