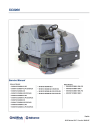
advertisement
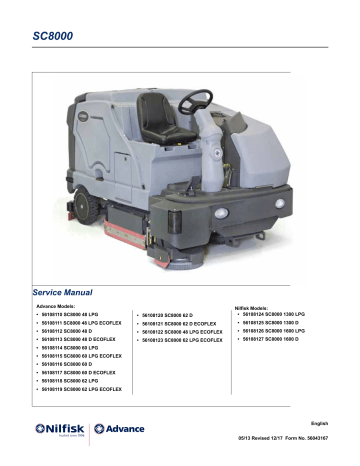
Service Manual – SC8000
Engine System, LPG
Functional Description
The LPG SC8000 machines use a four-cylinder 1.6L Kubota WG1605-L-E3 engine that is liquid cooled and and naturally aspirated to power the two hydraulic pumps that run the machine drive wheel, scrub/ sweep systems, vacuum fan motor, the scrub/sweep and squeegee lift actuators and the steering system.
An E-controls Engine Management System modifies the fuel mixture based on feedback input from oxygen sensors, and also controls the electonic throttle and ignition system.
Overview
The LPG SC8000 machines use a four-cylinder 1.6L WG 1605 Kubota engine to drive two hydraulic pumps.
Note: Also refer to the following manufacturer’s technical literature for the WG 1605 Kubota Engine:
• Engine Operator’s Manual WG1605 EG523-89162ENG.pdf
• Engine Specifications WG1605 9Y110-01770.pdf
• Engine Workshop Manual WG1605 9Y111-06610.pdf
• Diagnosis Manual ECM System WG1605 9Y110-01760.pdf
94
Kubota 1.6L LPG Fuel System Description
The fuel system on LPG engines includes an LPG Fuel Lock-off device, Dual Stage Regulator (DSR), Direct
Electronic Pressure Regulator (DEPR), Mixer Assembly and Electronic Throttle Body (ETB).
An LPG Fuel Lock-off device, consisting of a 12 volt solenoid and a normally-closed valve, opens during cranking and engine run cycles. The ECM controls the voltage to the LPG Fuel Lock-off device.
The DSR is a two-stage regulator that is a combination vaporizer, pressure regulating device. The DSR is normally closed when the engine is not running. When the engine is cranking or running, a partial vacuum is created in the fuel line which connects the regulator to the DEPR and Mixer Assembly. This partial vacuum opens the second stage regulator, permitting fuel to flow to the DEPR and Mixer Assembly.
The DEPR controls the fuel flow, and provides the correct air/fuel mixture to maintain performance and emissions control. The DEPR uses an internal computer, and fuel pressure and temperature sensors to provide input to the ECM for fuel calculation, fault detection and diagnostics.
The Mixer Assembly is a self-contained air/fuel metering device that utilizes a relatively constant pressure drop to draw fuel into the mixer from cranking to full load. The Mixer Assembly is mounted in the air stream, ahead of the ETB.
The ETB uses an electric motor, connected to the throttle shaft, to increase or decrease the angle of the throttle blade. The ECM sends electrical signals to the motor in the ETB to increase or decrease the airflow to the engine to control the engine speed.
Note: For a more detailed and thorough description of the LPG fuel systems, refer to the Diagnosis
Manual ECM System WG1605 9Y110-01760.pdf.
Service Manual – SC8000 Engine System, LPG 95
Engine Start and Run Circuit Description
In between the Drive Box and the Engine system is a “Relay PCB”. It is a small printed circuit board with two relays on it. One of the relays provides power out to the engine system to turn it on (or off). The other relay provides power out to the engine starter when the key is turned to the crank position and the drive pedal is in the neutral position.
ENGINE START/RUN RELAY PCB J7
Requirements:
1. First turn the S1 Key Switch to “Start” position, then released to it’s “Run” position.
2. Foot pedal in Neutral.
DRIVE
BOX
Battery (+) From
F1 Fuse 100A & CB6 15A
+
+
+
+
+
+
+
+
+
+
+
+
+
+
+
+
+
+
+
+
+
+
+ + + + + +
+ + + + + +
+
+
+
+
+
+
+
+
+
+
J7-8
S1
+ + + + + + + + +
J7-6
START
3
B1
IGN
+ + + + + + + + + +
K2
K3
- - -
- -
+
+
+
+
+
+
+
+
+
+
+
+
+
+
+
+
+
J7-1
+
+
+
+
+ +
K2
K3
+
+
J7-5
+
+ + + + + + +
+
+
J7-2
+
+ + + + + + +
+
+
+
+
+
+
+ + +
+
+
+
+ +
+
START COM-
MAND TO
STARTER RELAY
IGN. SW INPUT
ALT. EXCITE
PIN J1-22
PIN J1-34
START INHIBIT
J7-3
J7-7
RUN INHIBIT
RELAY
PCB
J7-4
BAT -
PIN J1-10
PIN J1-31
PIN J1-11
1
R1
2
3
DRIVE PEDAL SENSOR
BAT -
Circuit Description
• For the engine to start:
• The
Key Switch S1
must provide positive voltage to the
START
relay coil
K3
and the
IGN
relay coil
K2
.
• The
K2 RELAY CONTROL SWITCH
must be closed to provide a ground to the
IGN
relay coil
K2
. This closes the
K2
relay contacts to provide positive voltage to the
IGN. SW INPUT
. Note that if the
Driver Box
sends a
RUN INHIBIT
signal from
J1-34
to the
K2 RELAY CONTROL SWITCH
to open the switch, no ground will be provided to the
IGN
relay coil
K2
, the
K2
contacts will not close and no positive voltage will be sent to the
IGN. SW INPUT
.
• The
K3 RELAY CONTROL SWITCH
must be closed to provide a ground to the
START
relay coil
K3
. This closes the
K3
relay contacts to provide positive voltage to the
START COMMAND TO STARTER RELAY
.
Service Manual – SC8000 Engine System, LPG 96
Note that if the
Driver Box
sends a
START INHIBIT
signal from
J1-22
to the
K3 RELAY CONTROL SWITCH
to open the switch, no ground will be provided to the
START
relay coil
K3
, the
K3
contacts will not close and no positive voltage will be sent to the
START COMMAND TO STARTER RELAY
.
• The drive pedal must be in the neutral position and the
Drive Pedal Sensor
must be in the deadband range.
• For the engine to run:
• The
K2 RELAY CONTROL SWITCH
must remain closed to provide a ground to the
IGN
relay coil
K2
. This keeps the
K2
relay contacts closed to maintain positive voltage to the
IGN. SW INPUT
.
• The
Coolant Temperature Output
must not provide an “overheat” signal to pin
J1-30
on the
Driver Box
.
The engine coolant temperature sensor is a temperature-sensitive resistor. If the engine coolant temperature exceeds 225 degrees F. for more than five seconds, the Engine System senses the threshold resistance in the coolant temperature sensor. The Engine System then provides a
Coolant
Temperature Output
signal to pin
J1-30
to generate a fault code and shut the engine off.
• The
Low LP Pressure Switch S5
must be open to indicate adequate LP fuel supply (LPG engines only).
Note: LPG engines will continue to run for a few seconds after the key switch is turned off. This burns any fuel remaining in the engine to prevent backfires the next time the engine is started. When the key switch is turned off, the Engine System switches off the fuel supply to the engine, but keeps the ignition system on until it senses that the engine has stopped running.
Engine Protection – Low Oil Pressure Shutdown
The engine controller monitors the oil pressure switch. If it sees a loss of oil pressure, it will shut down the engine immediately.
Engine Protection – High Temperature
The engine controller monitors the engine coolant temperature. If the temperature reaches 230 deg. F. (110 deg. C.), it will derate the engine power by 30%. If the temperature reaches 240 deg. F. (115 deg. C.), it will shut down the engine.
Engine Speed Control
The operator can request three engine speeds, “idle” (1200 RPM), “run” (2200 RPM) and “maximum”
(2400 RPM). The Engine Controller operates an Electronic Throttle Body to adjust and maintain engine speed according to the requested input of the Main Machine Controller. To request the three different engine speeds, the Main Machine Controller (Driver Box) uses two wires that are connected to the Engine
Controller. It either applies 0v or 12v to each wire to request the specific speeds. See table below.
Pin#
Wire
Color
Function
J2-30 on Driver Box GRA/BLU Input from Driver Box
J2-29 on Driver Box GRA/ORN Input from Driver Box
Voltage at
1200 RPM
0
0
Voltage at
2200 RPM
0
+12 VDC
Voltage at
2400 RPM
+12 VDC
0
Service Manual – SC8000 Engine System, LPG 97
Component Locations
LPG Electrical Components
Note: Some of the photos in this section are of an engine before it is installed in the machine for better visual clarity.The engine is fitted for a different model machine (SW8000) so some details are slightly different like the air cleaner, air inlet and exhaust.
The following components are included in this section:
• Alternator
• Electronic Throttle Body
• Cam Position Sensor
• Connector 1
• Connector 2
• Crank Position Sensor
• DEPR - Direct Electronic Pressure Regulator
• Diagnostic Connector
• Engine Control Module
• Engine Coolant Sensor
• Fuel Lockoff Solenoid
• Ground
• Ignition Coils
• Knock Sensor
• LP Dual Stage Pressure Regulator
• Mixer Assembly
• Oil Pressure Switch
• Post Catalyst O
2
Sensor
• Power Relay (Inside Engine Fuse/Relay Box)
• Pre Catalyst O
2
Sensor
• Starter
• Starter Relay (Inside Engine Fuse/Relay Box)
• TMAP Sensor
Figure 1. Left Side
Connector 1 and
Connector 2
Engine Control
Module
Crank Position
Sensor
Knock Sensor
Electronic
Throttle Body
Service Manual – SC8000
Alternator
Oil Pressure
Switch
Oil Filter
Figure 2. Right Side
Diagnostic
Connector
TMAP
Sensor
Starter
Engine Fuse/
Relay Box
Engine System, LPG 98
Figure 3. Top
Ignition Coils
Service Manual – SC8000
Figure 4. Top, Front
Ground
Pre-Catalyst
O
2
Sensor
Engine System, LPG 99
Figure 5. Top, Rear
Engine Coolant
Sensor
Alternator
Mixer Assembly
Direct Electronic
Pressure Regulator
(DEPR)
Cam Position
Sensor
Oil Filter
Figure 6. Oxygen Sensors
Post-Catalyst
O
2
Sensor
Right Rear
Wheel
Fuel Lockoff
Solenoid
LP Dual Stage
Pressure Regulator
Figure 7. Top, Left Front
Service Manual – SC8000
Maintenance and Adjustments
Engine System, LPG 100
Warning! Before performing any machine maintenance or adjustments, make sure the key switch is off, the key is removed from the machine and the parking brake is engaged.
Maintenance Schedule
Item
Check engine oil level
Check and replenish coolant
Check and clean air filter element
Check LPG tank setting condition
Every
8 hrs
(daily).
X
X
if necessary if necessary
X
Every
50 hrs
(weekly)
Check LPG fuel connector
* Change engine oil
* Replace oil filter cartridge
Check LPG fuel hose and clamp bands
Clean spark plugs
Check fuel filter
Check fan belt tension and for damage
Check battery electrolyte level
Replace fuel filter
X
Every
100 hrs
X
X
X
X
if necessary
Check LPG tank setting condition
Check radiator hoses and clamp bands
Check PCV valve
Check coolant hose of LPG vaporizer
Check LPG Lock off valve
Check valve clearance
Replace spark plugs
** Replace air cleaner element
Clean water jacket and radiator interior
Replace intake air line
Replace breather hose
Replace LPG fuel hose and clamp bands
Replace coolant hose of LPG vaporizer
Service Interval
Every
150 hrs
Every
1000 hrs
Every
2000 hrs
X
X
X
X
X
X
X
X
X
Every
Year
X
X
Every
Two
Years
X
X
X
X
Service Manual – SC8000 Engine System, LPG 101
Item
*** Check LPG vaporizer
Replace radiator hoses and clamp bands
Change radiator coolant
Replace battery
Every
8 hrs
(daily).
Every
50 hrs
(weekly)
Every
100 hrs
Service Interval
Every
150 hrs
Every
1000 hrs
Every
2000 hrs
Every
Year
Every
Two
Years
X
X
X
X
* Change the engine oil and filter cartridge after the first 35 hours of operation.
** Change more often when operating under dusty conditions.
*** If you do not have the correct tools and/or are not mechanically proficient, contact your local KUBOTA dealer.
Engine Oil
Check the engine oil level when the machine is parked on a level surface and the engine is cool. Change the engine oil after the first 35 hours of operation and every 150 hours after that. Engine oil should have properties of API classification SL or higher and be suited to the ambient temperature as listed below. Refer to the engine manufacturer’s service manuals for oil capacities and additional engine specifications. Replace the oil filter with every oil change.
Temperature Range
Above 77° F [25° C]
32° F to 77° F [0° C to 25° C]
-4° F to 32° F [-20° C to 0° C]
Oil Weight
SAE30, SAE10W-30 or SAE15W-40
SAE20 or SAE 10W-30
SAE10 or SAE 10W-30
Engine Coolant
Checking Engine Coolant
Caution! Do not remove the radiator cap when the engine is hot.
To check the engine coolant level, open the engine cover and observe the coolant level in the coolant overflow tank. If the level is low, add a 50/50 mix of water and the recommended type antifreeze. Clean the radiator and oil cooler exteriors every 150 hours by washing with low-pressure water or using compressed air.
High-pressure water will damage the radiator.
Service Note: The oil cooler tips out for easy cleaning of both the oil cooler and the radiator.
Service Manual – SC8000 Engine System, LPG 102
Replacing Engine Coolant
One possible cause of engine overheating is trapped air in the cooling system. It’s recommended that you use a Cooling System Tool when changing the engine coolant. The Cooling System Tool pulls a vacuum on the cooling system prior to filling to prevent air from being trapped in the cooling system.
Note that there are several types of Cooling System Tools. The following instructions describe how to use a typical type of tool. Refer to the operating instructions included with your particular tool if different than the example shown here.
1. Connect a
Compressed Air Supply Line
to the fitting on the Cooling System
Tool.
Compressed Air
Supply Line
Gauge
Air
Switch
Coolant
Valve
(closed)
2. Connect the
Coolant Supply Line
to the
Cooling System Tool. Make sure the
Coolant Valve
is closed.
3. Insert and hold the Cooling System
Tool onto the radiator filler neck, then press the
Air Switch
. The compressed air travelling through the
Venturi Tube
Assembly
will pull a vacuum on the cooling system to remove air from the system.
Venturi
Tube
Assembly
Coolant
Supply
Line
4. Once the vacuum reading on the
Gauge
reaches approximately 25 on the green scale, release the
Air Switch
.
Note that this also a good opportunity to check for cooling system leaks,
Removing the Air from the Cooling System with Cooling System Tool
5. Continue to hold the Cooling System
Tool onto the radiator filler neck and open the
Coolant Valve
to allow coolant to flow into the radiator.
Gauge
Coolant
Valve
(open)
6. Once the pressure on the
Gauge
reaches approximately 5 on the red scale and the radiator is almost full, shut off the
Coolant Valve
and remove the Cooling System Tool from the radiator filler neck.
7. Top off the radiator and overflow tank as necessary.
Filling Cooling System with Coolant
Service Manual – SC8000 Engine System, LPG 103
Engine Air Filter Maintenance
Caution! When servicing the engine air filter elements, use extreme care to prevent loose dust from entering the engine. Dust can severely damage the engine.
Service the air cleaner more frequently under severe dusty or dirty conditions.
1. Remove the air cleaner elements from the air cleaner assembly and inspect them for foreign material restrictions or signs of excessive wear or damage. Replace the elements if necessary.
2. Remove all dust and foreign matter from the air cleaner housing.
3. Reinstall the air cleaner elements.
4. Reinstall the air cleaner cup, then securely fasten the retaining clips
Troubleshooting
The EControls engine management package supports robust self diagnostics and is capable of setting scores of Diagnostic Trouble Codes (DTCs). DTCs and sensor data can be viewed on a coputer using the “GCP
Display” software along with an “ECom” communication cable. See the Diagnosis Manual ECM System
WG1605 9Y110-01760.pdf for the diagnostic tool connection procedure.
The ECom cable can be purchased through Nilfisk-Advance. (See Special Tools in this section for the part number). It is the same cable that has been used on other recent Nilfisk-Advance machines using the GM
1.6L and GM 3.0L engines. You will need a new version of the GCP software to work with the Kubota
WG1605 engine along with the correlating password. The software, password and installation instructions can all be downloaded from “Customer Zone”at www.advance-us.com.
Most or all engine troubleshooting is covered in Kubota manuals. There are some things specific to the
SW8000 engine application which are covered here in this manual section such as, engine speed control and engine starter operation.
Note: Refer to the Diagnosis Manual ECM System WG1605 9Y110-01760.pdf, for engine
troubleshooting information and procedures including all fault code diagnosis.
General Troubleshooting
Problem
The engine will not crank.
Cause
Weak battery, poor battery cable connections.
No power to the Starter
Solenoid (Starter Command circuit)
Correction
• Check the battery and connections and clean/repair as necessary.
• Check the wiring from the battery to the Starter B+ terminal on the A3 Engine System and repair as necessary.
• Make sure the foot pedal is in the neutral position.
• Reset the foot pedal deadband position if necessary.
(Refer to the
Control System, / Main Machine
Controller Programming
section.)
• Make sure there is continuity through the Neutral
Relay K4 contacts 30 and 87a (relay off).
• Check the starter relay operation
• Check circuit breaker CB1 and reset if necessary.
• Check circuit breaker CB3 and reset if necessary.
Service Manual – SC8000 Engine System, LPG 104
Problem
The engine will not start.
Engine will not run at high speed.
The engine stops running, check engine light is on.
Cause
No power to the Ign. Switch
Input terminal on the A3
Engine System.
Loss of throttle input from
Main Machine Controller to
Engine Controller
Engine System Problem
The coolant temperature is too high.
Correction
• Check circuit breaker CB5 and reset if necessary.
• Check the continuity from the Ignition Switch to the
Ign. Switch Input terminal on the A3 Engine System and repair as necessary.
• Check that a voltage signal is being sent to the engine controller when the Throttle Switch is set to operating speed.
• Refer to Diagnosis Manual ECM System WG1605
9Y110-01760.pdf
Refer to the Engine Overheating Problems section below.
The oil pressure has dropped too low.
Refer to the Loss of Oil Pressure Protection section below.
Engine Management System
Problem
Consult Diagnosis Manual ECM System WG1605
9Y110-01760.pdf
Engine Overheating Problems
Use the checklist below as a guide to thoroughly check the engine cooling system.
• Check the coolant level in the overflow tank and radiator.
• Inspect and clean the radiator and hydraulic oil cooler.
• Check for correct operation of the belt-driven engine cooling fan (slippage).
• Check to see that the engine thermostat opens.
• Check for correct water pump operation.
• Check the engine crankcase oil level.
• Check for air trapped in the cooling system. (Refer to the
Engine Coolant/Replacing Engine Coolant
section.)
• Check the engine coolant sensor for correct function as replace if necessary.
• Check for combustion gasses in the coolaning system.
Service Manual – SC8000 Engine System, LPG 105
Specifications
Number of Cylinders
Type
Bore × Stroke
Total Displacement
Cylinder Head
Ignition System
Governor
Direction of Rotation
Spark Plug Type/Spark Plug Gap
Ignition Timing.
Firing Order
Model
Compression Ratio
Lubricating System
Oil Pressure Indication
Engine Oil Pressure (Hot)
At Idle Speed
At Rated Speed
Lubricating Filter
Cooling System Type
Starting System
Starting Motor
Battery
Charging Alternator
Fuel
Lubricating Oil
Lubricating Oil Capacity
Catalytic Muffler / Converter
Weight (Dry)
Kubota Recommended LPG Fuel
Specifications
WG1605-L-E3
LPG fuel
Four
Vertical, water cooled, four-cycle LPG engine
79.0 × 78.4 mm (3.11 × 3.09 in.)
1.537 L (93.79 cu.in.)
Overhead-Valve
Full Transistor Battery Ignition Type
Electronic Governor
Counterclockwise (Viewed from Flywheel Side)
NGK IFR6F8DN; 0.70 to 0.80 mm (0.028 to 0.031 in.)
0.35 rad (20 °) before T.D.C.
3000 min-1 (rpm), 3600 min-1 (rpm)
0.17 rad (10 °) before T.D.C.
750 min-1 (rpm), 800 min-1 (rpm)
1-3-4-2
9.1: 1
Forced Lubrication by Trochoid Pump
Electrical Type Switch
Allowable Limit Factory Specification
49 kPa
0.50 kgf/cm2
7.1 psi
–
196 to 441 kPa
2.00 to 4.49 kgf/cm2
28.5 to 63.9 psi
147 kPa
1.50 kgf/cm2
21.3 psi
Full Flow Paper Filter (Cartridge Type)
Pressurized Radiator, Forced Circulation with Water Pump
Electric Starting with Starter
12 V, 1.0 kW
12 V, 52 AH or Equivalent
12 V, 480 W, 720 W
Commercial LPG
Better than SL Class (API) SAE 10W-30
6.0 L (1.6 U.S.gals)
Three-way Catalyst
120 kg (265 lbs)
Commercial Propane gas only, Equivalent to Propanes H-D-5 of GPA* standards
Service Manual – SC8000 Engine System, LPG 106
Shop Measurements
The following information was gathered by measuring one machine. While the values recorded cannot serve as “true specifications” they may help you recognize what normal looks like and give you some standard of comparison.
Engine Vacuum
17.5-18 “HG (59-61kPa)-at warm idle. Measured at approximately 900 ft. elevation
LP Fuel Pressure
• Primary - Approximately 3 psi (20 kPa)
• Secondary - Approximately 1 psi (7 kPa)
Ignition Output
Cam Sensor and Crank Sensor Oscilloscope Pattern
Service Manual – SC8000
Special Tools
Diagnostic Communication Cable and software, p/n 56305647
Note: The “Ecom” cable is used but the software on the
CD is for the GM engines. New software must be ordered or downloaded from Customer Zone to use on the Kubota engine..
Cooling System Tool
CD containing Kubota Engine Software p/n 56107764
Engine System, LPG 107
Not Shown
advertisement
* Your assessment is very important for improving the workof artificial intelligence, which forms the content of this project
Related manuals
advertisement
Table of contents
- 8 General Information
- 8 General Machine Description
- 8 Service Manual Purpose and Application
- 8 Revision History
- 8 Other Reference Manuals and Information Sources
- 8 Nilfisk-Advance Publications
- 9 Engine Manufacturers’ Technical Manuals
- 9 Diagnostic and Service Tools
- 11 Conventions
- 11 Parts and Service
- 11 Nameplates
- 12 Cautions and Warning Symbols
- 12 General Safety Instructions
- 14 Jacking the Machine
- 14 Transporting the Machine
- 15 Towing the Machine
- 16 Technical Specifications
- 16 General Machine Dimensions and Capacities
- 17 Overall Dimensions
- 18 Engine and Machine Performance
- 18 Fastener Torque Specifications
- 18 Maintenance
- 18 Maintenance Schedule
- 19 Recommended Service Materials
- 19 Daily Maintenance
- 20 Maintenance Every 15 to 20 Hours
- 20 Monthly Maintenance
- 20 Maintenance Every 150 Hours
- 21 Maintenance Every 400 Hours
- 21 Maintenance Every 800 to 1000 Hours
- 21 Maintenance Every 2000 Hours
- 22 Lubrication Points
- 23 PM Check List - SC8000
- 26 General Machine Overview
- 26 Major Machine Components
- 28 Control Panel Switches
- 30 Control Panel Indicators
- 32 Liquid Crystal Display (LCD)
- 32 General Displays
- 32 Attention and Warning Displays
- 35 Chassis System
- 35 Major Chassis Components
- 37 Control System
- 37 Functional Description
- 37 Overview
- 37 Control System Wiring Diagram
- 37 Circuit Description
- 38 Component Locations
- 39 Control Board (Driver Box) Connectors
- 39 J1 Main Control Board Connectors
- 40 J2 Main Control Board Connectors
- 41 J3 Main Control Board Connectors
- 42 Control Board (Driver Box) Programming Options
- 42 Foot Pedal Neutral Position and Deadband Adjustment
- 43 Configuration Display Menu
- 45 User Options Menu
- 49 Configuration Menu
- 52 Operator Presence Control (OPC)
- 53 Troubleshooting
- 53 Main Control Board Fault Codes
- 57 Systems Disabled by Faults
- 59 Electrical System
- 59 Functional Description
- 59 Overview
- 59 Power Supplies
- 59 Circuit Description
- 60 Component Locations
- 60 K1 Power Relay
- 60 Circuit Breakers
- 61 100-amp Fuse F1
- 61 Troubleshooting
- 63 Specifications
- 63 Component Specifications
- 63 Connector Callout – Relay PCB
- 64 Input/Output Table
- 70 Shop Measurements - Driver Box
- 77 Shop Measurements - Relay PCB
- 78 Wiring Diagram - 56108185 Rev. A Sheet 1 Kubota LPG Engine
- 79 Wiring Diagram - 56108185 Rev. A Sheet 2 Kubota Diesel Engine
- 80 Wiring Diagram Kubota 1.6L LPG Engine 56107659 REV. A
- 81 Wiring Harness Schematic, Machine - 56108186 REV A Sheet 1 of 2
- 82 Wiring Harness Schematic, Engine Interface and Kubota Diesel - 56108186 REV A Sheet 2 of 2
- 83 Engine System, Diesel
- 83 Functional Description
- 83 Overview
- 83 Diesel Engine Starter Circuit Diagram
- 84 Circuit Description
- 85 Component Locations
- 86 Maintenance and Adjustments
- 86 Engine Oil
- 86 Engine Coolant
- 88 Engine Air Filter Maintenance
- 88 Troubleshooting
- 88 General Troubleshooting
- 88 Engine Overheating Problems
- 89 Loss of Oil Pressure Protection
- 89 Engine Will Not Crank - Start Inhibit Active
- 89 Engine Stops Running - Run InhibitActive
- 90 Diesel Engine Will Not Run at High Speed or Turbo Speed
- 91 Troubleshooting the Kubota Engine Speed Governing System
- 92 Specifications
- 92 Engine Specifications
- 93 Connector Callout – Relay PCB
- 93 Special Tools
- 94 Engine System, LPG
- 94 Functional Description
- 94 Kubota 1.6L LPG Fuel System Description
- 95 Engine Start and Run Circuit Description
- 95 Circuit Description
- 96 Engine Protection – Low Oil Pressure Shutdown
- 96 Engine Protection – High Temperature
- 96 Engine Speed Control
- 97 Component Locations
- 97 LPG Electrical Components
- 100 Maintenance and Adjustments
- 100 Maintenance Schedule
- 101 Engine Oil
- 101 Engine Coolant
- 103 Engine Air Filter Maintenance
- 103 Troubleshooting
- 103 General Troubleshooting
- 104 Engine Overheating Problems
- 106 Shop Measurements
- 107 Special Tools
- 108 Hydraulic System
- 108 Functional Description
- 108 Overview
- 109 Electrical Schematic
- 109 Electrical Circuit Description
- 110 Hydraulic Schematic
- 111 Component Locations
- 111 Major Components
- 112 Hydraulic Cylinders
- 112 Hydraulic Motors
- 113 Hydraulic Pumps
- 113 Hydraulic Valve Block/Manifold
- 116 Hydraulic Manifold Assembly Component Location Key
- 117 Maintenance and Adjustments
- 117 Hydraulic Oil
- 117 Hydraulic Oil FIlter
- 118 Troubleshooting
- 118 General Troubleshooting
- 118 General Information Regarding Checking Hydraulic Pressures
- 118 Test Port Nominal Pressure Readings
- 120 Hydraulic Pressure Tables
- 121 Hydraulic Truth Table
- 121 Specifications
- 123 Special Tools
- 124 Options and Accessories
- 130 Recovery System
- 130 Functional Description
- 130 System Overview
- 130 Recovery System Wiring Diagram
- 131 Electrical Circuit Description
- 131 Recovery System Hydraulic Diagram
- 133 Component Locations
- 133 Recovery Tank
- 134 Daily Maintenance
- 134 Troubleshooting
- 135 Removal and Installation
- 135 Recovery Tank
- 137 Specifications
- 137 Special Tools
- 138 Scrub System, Cylindrical
- 138 Functional Description
- 138 Overview
- 138 Cylindrical Scrub System Wiring Diagram
- 138 Circuit Description
- 140 Cylindrical Scrub System Hydraulic Diagrams
- 143 Component Locations
- 144 Maintenance
- 144 Scrub Deck Leveling Adjustment
- 145 Troubleshooting
- 145 General Troubleshooting
- 147 Main Scrub Deck and Right Side Scrub Down
- 148 Main Scrub Deck and Right Side Scrub Pressure
- 149 Main Scrub and Side Sweep/Scrub On
- 150 Specifications
- 150 General Specifications
- 150 Scrub Pressures
- 151 Special Tools
- 152 Scrub System, Right Side
- 152 Functional Description
- 152 Overview
- 152 Right Side Scrub System Wiring Diagram
- 152 Circuit Description
- 153 Right Side Scrub System Hydraulic Diagrams
- 155 Component Locations
- 157 Maintenance and Adjustments
- 157 Side Brush Tilt Adjustment
- 158 Troubleshooting
- 158 General Troubleshooting
- 159 Main Scrub Deck and Right Side Scrub Down
- 160 Main Scrub and Side Sweep/Scrub On
- 161 Specifications
- 161 Special Tools
- 162 Solution System
- 162 Functional Description
- 162 Overview
- 162 Solution Flow Control
- 163 Detergent System
- 164 Extended Scrub System
- 165 Right Side Scrub Brush
- 165 Wash Hose
- 166 DustGuard™ Spray Nozzles
- 166 Solution System Wiring Diagram
- 167 Circuit Descriptions
- 173 Component Locations
- 175 Maintenance and Adjustments
- 175 To Clean the Solution Filter Screen
- 176 To Clean the Extended Scrub System Strainer
- 176 To Clean the Solution Delivery Trough
- 176 To Clean the DustGuard™ Spray Nozzles
- 176 To Adjust the DustGuard™ Spray Nozzles
- 177 Detergent System Maintenance
- 180 Troubleshooting
- 180 General Troubleshooting
- 183 Main and Right Side Solution Valves and Solution Pump
- 184 Specifications
- 184 Component Specifications
- 185 Solution and Detergent Delivery Rates
- 186 Squeegee System
- 186 Functional Description
- 186 Overview
- 186 Squeegee System Wiring Diagram
- 186 Circuit Description
- 187 Squeegee System Hydraulic Diagrams
- 189 Component Locations
- 190 Troubleshooting
- 190 General Troubleshooting
- 191 Vacuum Fan On and Squeegee Down
- 192 Vacuum Fan Off and Squeegee Up
- 193 Specifications
- 194 Steering System
- 194 Functional Description
- 194 Overview
- 195 Hydraulic Diagrams
- 196 Component Locations
- 196 Steering Unit
- 197 Steer Cylinder
- 198 Troubleshooting
- 198 Removal and Installation
- 198 Specifications
- 199 Sweep System, Side Broom
- 199 Functional Description
- 199 Overview
- 199 Side Broom Sweep System Wiring Diagram
- 199 Circuit Description
- 200 Side Broom Sweep System Hydraulic Diagrams
- 202 Component Locations
- 202 Single (left-hand) Sweep
- 203 Dual Sweep
- 204 Maintenance and Adjustments
- 204 To Adjust the Side Broom Lift Actuator Motor
- 206 Troubleshooting
- 206 General Troubleshooting
- 207 Main Scrub and Side Sweep/Scrub On
- 208 Specifications
- 209 Wheel System, Non-traction
- 209 Functional Description
- 210 Maintenance and Adjustments
- 210 Brake Tension Adjustment
- 211 Troubleshooting
- 211 Specifications
- 212 Wheel System, Traction
- 212 Functional Description
- 212 Overview
- 212 Piston Pump
- 212 Foot Pedal, Hydroback and Rotary Sensor
- 213 Traction Drive Motor
- 213 Electrical Schematic
- 214 Electrical Circuit Description
- 214 Hydraulic Diagrams
- 216 Component Locations
- 216 Piston Pump, Hydroback and Rotary Sensor
- 216 Traction Drive Motor
- 217 Maintenance and Adjustments
- 217 Foot Pedal/Hydroback Neutral Adjustment
- 218 Foot Pedal Neutral Deadband Adjustment
- 219 Troubleshooting
- 220 Removal and Installation
- 220 Push/Pull Control Cable Replacement
- 222 Hydroback Replacement
- 223 Traction Drive Motor Hose Routing
- 224 Specifications
- 224 Component Specifications
- 225 Wheel Drive System Torque Specifications