- No category
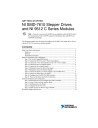
Getting Started With NI SMD-7610 Stepper Drives and NI 9512 C Series Modules
Add to my manuals
22 Pages
advertisement
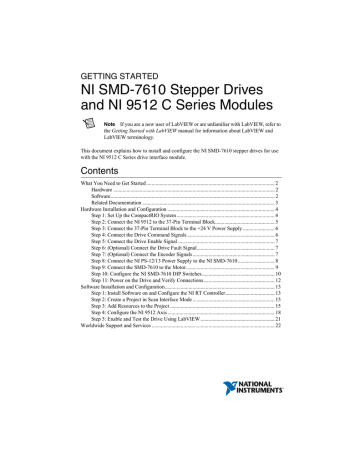
GETTING STARTED
NI SMD-7610 Stepper Drives and NI 9512 C Series Modules
Note
If you are a new user of LabVIEW or are unfamiliar with LabVIEW, refer to the Getting Started with LabVIEW manual for information about LabVIEW and
LabVIEW terminology.
This document explains how to install and configure the NI SMD-7610 stepper drives for use with the NI 9512 C Series drive interface module.
Contents
Step 3: Connect the 37-Pin Terminal Block to the +24 V Power Supply ........................ 6
Step 8: Connect the NI PS-12/13 Power Supply to the NI SMD-7610............................ 8
What You Need to Get Started
You need the following items to get started.
Hardware
NI 9512 C Series stepper drive interface module
NI real-time controller
– CompactRIO controller and chassis that support the RIO Scan Interface
Tip
To determine if your controller and chassis support the RIO Scan Interface go to ni.com/info
and enter the Info Code rdsoftwareversion
.
or
– NI 9144 distributed chassis and compatible RT controller
+24 V power supply (such as the NI PS-15) for the CompactRIO controller
(NI part number 781093-01)
Separate +24 V power supply for the NI 9512 (such as the NI PS-15)
NI PS-12 or NI PS-13 power supply for the NI SMD-7610
NI SMD-7610 stepper drive
NI or third-party stepper motor
Note
NI offers stepper motors matched to the NI SMD-7610. Refer to ni.com/ motion
for motor options. National Instruments highly recommends using these motors for the best user experience.
(Optional) ENC-7740 encoder for ST17 motors (NI part number 748991-01) or ENC-7741 encoder for ST23 motors (NI part number 748992-01)
NI-7748 encoder cable to connect the encoder to the NI 951x terminal block
(NI part number 748994-01)
Ethernet connection and cable for the CompactRIO controller
NI 951x Cable and Terminal Block bundle
(NI part number 780553-01)
Software
LabVIEW 2010 or later
LabVIEW 2010 Real-Time Module or later
LabVIEW 2010 NI SoftMotion Module or later
NI-RIO 3.5.1 or later
2 | ni.com
| Getting Started with NI SMD-7610 and NI 9512 Modules
Figure 1 shows a simplified connection diagram.
Figure 1. NI 9512 to NI SMD-7610 Connections
+24 V Power Supply
(NI PS-15 Shown)
37-pin Terminal
Block +24 V Power Supply
(NI PS-15 Shown)
Ethernet
Cable
NI RT Controller
(NI cRIO-9014 shown) and NI 9512 Module
I/O
Connections
1 2 3 4 5 6 7 8
NI SMD-7610
Stepper Drive
+ +
OUTPUT: 48V 6.7A
+V -V
INPUT: 100-240VAC 5A 50/60Hz
N N L L
NI PS-12/13
Power Supply
Encoder
Connections
NI Stepper Motor
Related Documentation
The following documents contain additional information that you may find helpful. All referenced documents ship with the product and are available at ni.com/manuals
.
• Operating instructions for the controller and C Series module.
• NI SMD-7610 User Manual
•
LabVIEW NI SoftMotion Module Help
—Use this help file to learn about using the
NI SoftMotion Module in LabVIEW including information about function blocks and using the NI SoftMotion Module with the LabVIEW Project. To access this help file from
LabVIEW, select Help»LabVIEW Help, then expand the LabVIEW NI SoftMotion
Module
book on the Contents tab.
•
LabVIEW Help
—Use the LabVIEW Help to access information about LabVIEW programming concepts, step-by-step instructions for using LabVIEW, and reference information about LabVIEW VIs, functions, palettes, menus, tools, properties, methods, events, dialog boxes, and so on. The LabVIEW Help also lists the LabVIEW documentation resources available from National Instruments. Access the LabVIEW Help by selecting
Help»LabVIEW Help
.
•
Getting Started with LabVIEW
—Use this document as a tutorial to familiarize yourself with the LabVIEW graphical programming environment and the basic LabVIEW features you use to build data acquisition and instrument control applications. Access the Getting
Started with LabVIEW
PDF by selecting Start»All Programs»National Instruments»
LabVIEW»LabVIEW Manuals»LV_Getting_Started.pdf
.
Getting Started with NI SMD-7610 and NI 9512 Modules | © National Instruments | 3
Hardware Installation and Configuration
This section covers the hardware setup for the CompactRIO system, NI 9512 C Series module, and NI SMD-7610 stepper drive.
Step 1: Set Up the CompactRIO System
Complete the following steps to set up the CompactRIO hardware.
1. Install the real-time CompactRIO controller on the chassis if you are not using an integrated controller and chassis.
Note
Write down the controller serial number before installing the controller onto the chassis. You will be unable to read the serial number after you install the controller.
a. Make sure that no power is connected to the controller or the chassis.
b. Align the controller with the chassis as shown in Figure 2.
Figure 2. Installing the Controller on the Chassis (Eight-Slot Chassis Shown)
1
4
3
2
1 Controller
2 Captive Screws
3 Controller Slot
4
5
Reconfigurable Embedded Chassis
Grounding Screw
4 | ni.com
| Getting Started with NI SMD-7610 and NI 9512 Modules
5
c. Slide the controller onto the controller slot on the chassis. Press firmly to ensure the chassis connector and the controller connector are mated. d. Using a number 2 Phillips screwdriver, tighten the two captive screws on the front of the controller.
2. Connect the controller to a power supply and an Ethernet network on the same subnet as the development computer. Refer to the controller operating instructions for information about wiring the controller to the power supply and Ethernet network.
Note
Do not plug in or turn on any power to the system until after you complete
Step 11: Power on the Drive and Verify Connections
3. Install the NI 9512 module in slot 1, 2, 3, or 4 of the chassis.
Step 2: Connect the NI 9512 to the 37-Pin Terminal
Block
1. Connect the MDR and DSUB connectors on the NI 951x Y-cable to the MDR and DSUB connectors on the NI 9512 module.
2. Connect the 37-pin DSUB to the DSUB connector on the NI 951x terminal block.
Figure 3 shows the 37-pin terminal block pin assignments.
Figure 3. NI 9512 37-Pin Terminal Block Pin Assignments
Forward Limit
Home
COM
Digital Input 0
COM
Encoder 0 Index+
Encoder 0 Index–
COM
+5V OUT
Position Compare
Reserved
Reserved
Digital Output 0 †
Vsup †
Digital Input 1 †
Direction (CCW)+ †
COM †
Step (CW)+ †
Shield
† Indicates DSUB connector signals.
Digital Output 1 †
Reverse Limit
Reserved
Vsup
Reserved
COM
Encoder 0 Phase A+
Encoder 0 Phase A–
Encoder 0 Phase B+
Position Capture
Encoder 0 Phase B–
Reserved
Reserved
COM †
Drive Enable †
Digital Input 3 †
Direction (CCW)– †
Digital Input 2 †
Step (CW)– †
Getting Started with NI SMD-7610 and NI 9512 Modules | © National Instruments | 5
Step 3: Connect the 37-Pin Terminal Block to the +24 V
Power Supply
Note
Do not plug in or turn on the power supply until after you complete
Power on the Drive and Verify Connections
.
1. Connect the V+ terminal from the 24 V power supply to one of the two V sup
37-pin terminal block. The 37-pin terminal block provides a V sup pin 14 and pin 22.
inputs on the
input for the NI 9512 on
2. Connect the V- terminal from the 24 V power supply to one of the COM terminals on the
37-pin terminal block. The 37-pin terminal block provides COM on pins 3, 5, 8, 17, 24, and 32.
Step 4: Connect the Drive Command Signals
Complete the following steps to connect the Drive Command signals to the NI 9512 terminal block.
1. Connect the SMD-7610 COM+ terminal to the 37-pin terminal block +5V OUT terminal
(pin 9).
2. Connect the SMD-7610 STEP terminal to the 37-pin terminal block Step (CW)+ terminal
(pin 18).
3. Connect the SMD-7610 DIR terminal to the 37-pin terminal block Direction (CCW)+ terminal (pin 16).
Figure 4 shows the SMD-7610 Drive Command and I/O Connector location and pinout.
Figure 4. SMD-7610 Drive Command and I/O Connector
1 2 3 4 5 6 7 8
6 | ni.com
| Getting Started with NI SMD-7610 and NI 9512 Modules
Step 5: Connect the Drive Enable Signal
The Drive Enable signal controls the enable function of the drive. To use this signal, connect the
SMD-7610 EN terminal wire to the 37-pin terminal block Drive Enable terminal (pin 33).
Step 6: (Optional) Connect the Drive Fault Signal
Complete the following steps to map an NI 9512 digital input to the SMD-7610 fault output signal to monitor the NI SMD-7610 stepper drive for faults:
1. Connect the OUT+ terminal to the 37-pin terminal block Vsup terminal (pin 22).
2. Connect the OUT- terminal to the 37-pin terminal block DI 0 terminal (pin 4).
Step 7: (Optional) Connect the Encoder Signals
If your motor includes an encoder, complete the following steps to connect the encoder to the
NI 951x terminal block:
1. Connect one end of the encoder cable to the encoder.
2. Cut the 15-pin DSUB connector off of the other end of the cable and expose the encoder wires.
3. Connect the encoder wires to the 37-pin terminal block as indicated in Table 1.
4. Insulate any unused wires.
Table 1. NI SMD-7610 to 37-Pin Terminal Block Connections
Encoder
Signal Name
CH A
CH A-
CH B
CH B-
INDEX
INDEX-
GND
+Vcc
Encoder Cable
Wire Color blue blue/white yellow yellow/white orange orange/white black red
8
9
6
7
25
26
27
29
37-Pin
Terminal Block
Pin Number
37-Pin
Terminal Block
Signal Name
Encoder 0 Phase A+
Encoder 0 Phase A-
Encoder 0 Phase B+
Encoder 0 Phase B-
Encoder 0 Index+
Encoder 0 Index-
COM
+5V OUT
Getting Started with NI SMD-7610 and NI 9512 Modules | © National Instruments | 7
Step 8: Connect the NI PS-12/13 Power Supply to the
NI SMD-7610
Note
Do not plug in or turn on the power supply until after you complete
Power on the Drive and Verify Connections
.
Complete the following steps to connect the power supply to AC input power and to the
NI SMD-7610. Figure 5 shows the power supply terminals.
Figure 5. NI PS-12/13 Power Supply Terminals
+ +
OUTPUT: 48V 6.7A
.
INPUT: 100-240VAC 5A 50/60Hz
N N L L
1 2 3 4 5
1 +24 V (NI PS-12) or +48 V (NI PS-13) Output
2 +24 V (NI PS-12) or +48 V (NI PS-13) Ground
3 AC Input Ground (Protective Earth)
4 AC Input Neutral
5 AC Input Line
Figure 6 shows the SMD-7610 Power and Motor Connector location and pinout.
Figure 6. SMD-7610 Power and Motor Connector
V+ V- A+ AB+ B-
Ground
Screw
1 2 3 4 5 6 7 8
1. Connect an AC input cable to the line, neutral, and protective earth connectors.
2. Connect the SMD-7610 V+ terminal to the power supply +V connector.
3. Connect the SMD-7610 V- terminal to the power supply -V connector.
8 | ni.com
| Getting Started with NI SMD-7610 and NI 9512 Modules
4. Connect the SMD-7610 green ground screw to earth ground.
5. Connect the NI 9512 COM to the NI PS-12/13 -V terminal to ensure a common reference.
Note
Refer to the NI SMD-7610 User Manual for more information about connecting the power supply.
Step 9: Connect the SMD-7610 to the Motor
NI offers stepper motors matched to the SMD-7610. The ST8-1, ST8-2, ST11-1, ST11-2, and
ST14-1 are four lead motors. Connect them as shown in Figure 7.
Figure 7. Four Lead Motor Connection
A+
Red
A–
Blue
4
Lead
Motor
Yellow
B+ B–
White
The ST17-1, ST17-2, and ST17-3 are eight lead motors that are connected using a parallel
configuration. Connect them as shown in Figure 8.
Figure 8. Eight Lead Motor Parallel Connection
A+
Blk/Wht
Orange
Org/
Wht
A–
Black
Red
B+
Yel/
Wht
8
Lead
Motor
Yellow
Red/Wht
B–
Getting Started with NI SMD-7610 and NI 9512 Modules | © National Instruments | 9
The ST23-2, ST23-4, and ST23-6 are eight lead motors that are connected using a series
configuration. Connect them as shown in Figure 9.
Figure 9. Eight Lead Motor Series Connection
A+
Orange
Org/Wht
Blk/Wht
8
Lead
Motor
A–
Black
Red
B+
Red/
Wht
Yel/
Wht B–
Yellow
Step 10: Configure the NI SMD-7610 DIP Switches
The NI SMD-7610 provides two sets of drive configuration DIP switches. Refer to the NI
SMD-7610 User Manual
for more information about the DIP switch options. The following figure shows the DIP switch locations and functions.
Note
If you change the DIP switch settings you must power cycle the
NI SMD-7610 for the new settings to take effect.
Figure 10. NI SMD-7610 DIP Switches
Switch A
Steps/rev
Run Current
Idle Current
Step Noise Filter
Self Test
1 2 3 4 5 6 7 8
Switch B
Load Inertia
Motor
Selection
1 2 3 4
10 | ni.com
| Getting Started with NI SMD-7610 and NI 9512 Modules
Refer to Table 2 for the DIP switch settings that this document uses.
Table 2. Switch A DIP Switch Settings
Setting Name
Self Test
Switch Position Corresponding Value
Off
1
Step Noise Filter 2 MHz
2
Idle Current 50%
3
Running Current 100%
4 5
Steps/rev 20000
6 7 8
Getting Started with NI SMD-7610 and NI 9512 Modules | © National Instruments | 11
Setting Name
Motor Selection
Load Inertia
Table 3. Switch B DIP Switch Settings
Switch Position
Corresponding
Value
ST8-1
ST8-2
1 2 3
ST11-1
ST11-2
1 2 3
ST14-1
1 2 3
ST17-1
1 2 3
ST17-2
ST17-3
1 2 3
1 2 3
ST23-2
ST23-4
ST23-6
0 - 4X
4
Wiring
4 leads
4 leads
4 leads parallel parallel series
—
Step 11: Power on the Drive and Verify Connections
After all hardware connections have been made complete the following steps to confirm the hardware setup.
1. Turn on all power supplies.
12 | ni.com
| Getting Started with NI SMD-7610 and NI 9512 Modules
2. Verify that the Drive Status LED on the NI SMD-7610 flashes or is solid green. Figure 11
shows the location of the Drive Status LED.
Figure 11. Drive Status LED Location
Status LEDs
1 2 3 4 5 6 7 8
If the Drive Status LED does not flash or turn solid green, turn off all power, verify the connections, and try again. Refer to the
Worldwide Support and Services
tips.
Software Installation and Configuration
This section covers installing and configuring software for the NI 9512 C Series module.
Note
These instructions assume you have installed all required software from the
section on your development machine.
Step 1: Install Software on and Configure the NI RT
Controller
Complete the following steps to configure the controller and install software on it.
Note
The Measurement & Automation Explorer (MAX) user interface may not match these steps exactly depending on which version of MAX you are using.
Verify the NI RT Controller
1. Launch Measurement & Automation Explorer (MAX) on the development computer by clicking the MAX icon on the desktop ( ), or by selecting Start»All Programs»
National Instruments»Measurement & Automation
.
2. Expand the Remote Systems tree.
3. Highlight the system.
Note
If you do not see the controller, you may need to disable the firewall on the development computer. Go to ni.com/info
and enter
RIOMAXTroubleshoot for more information.
Getting Started with NI SMD-7610 and NI 9512 Modules | © National Instruments | 13
4. Verify that the Serial Number in the General Settings section matches the serial number on the device.
If you do not want to format the disk on the controller, eliminating all installed software and files,
skip to Install Software on the NI RT Controller.
Reformat the NI RT Controller (Optional)
1. Set the Safe Mode switch on the controller to the On position.
2. Power on the controller. If it is already powered on, press the Reset button on the controller to reboot it.
3. Right-click the controller under Remote Systems in the Configuration pane in MAX and select Format Disk.
4. (Optional) Enable the Keep Network Settings checkbox if you want to retain the same target name and IP address.
5. Click Format to start formatting the disk.
6. When MAX finishes formatting the disk, set the Safe Mode switch to the Off position and click OK.
7. Select the System Settings tab on the bottom and type a descriptive name for the system in the Hostname field.
8. (Optional) Complete this step only if the target has an empty IP address (0.0.0.0). Select the
Network Settings
tab and select DHCP or Link Local from the Configure IPv4 Address list to assign an IP address or select the Static to specify a static IP address in the IPv4
Address
section.
9. Click Save on the toolbar and let MAX reboot the system. You may not need to complete this step if you did not change the IP address or name.
Install Software on the NI RT Controller
1. When the new system name appears under Remote Systems, expand the controller item in the tree, right-click Software, and select Add/Remove Software.
2. Select a recommended software set that includes NI-RIO 3.5.1 or later.
3. Click Next.
4. Select LabVIEW NI SoftMotion Module from the add-ons list.
Note
If you are using NI SoftMotion Module 2010 SP1 or earlier, also select
LabVIEW NI SoftMotion Module Scan Engine Support
from the list.
5. Click Next to install the selected software on the controller. Click Help if you need information about installing recommended software sets.
6. When the software installation completes, click Finish to reboot the controller.
7. Close MAX.
14 | ni.com
| Getting Started with NI SMD-7610 and NI 9512 Modules
Step 2: Create a Project in Scan Interface Mode
Scan Interface mode enables you to use C Series modules directly from LabVIEW Real-Time.
Modules that you use in Scan Interface mode appear directly under the chassis item in the
Project Explorer
window. Unlike most C Series modules, NI 951x modules are not directly configurable from the Project Explorer window and no I/O variables are directly available under the module.
Tip
Refer to the Select Programming Mode Dialog Box topic of the CompactRIO
Reference and Procedures (Scan Interface)
help file for more information about Scan
Interface mode.
Use a LabVIEW project to manage VIs, targets, and I/O modules on the development computer.
Complete the following steps to create a LabVIEW project.
1. Launch LabVIEW.
2. Select File»Create Project or Project»Create Project to display the Create Project dialog box. You can also click the Create Project button on the Getting Started window.
The Create Project dialog box includes a list of templates and sample projects you can use to ensure that the project you create uses reliable designs and programming practices.
3. Select Blank Project from the list of templates.
4. Click Finish.
5. Select Help and make sure that Show Context Help is checked. You can refer to the context help throughout the tutorial for information about items on the block diagram.
Step 3: Add Resources to the Project
1. Right-click the top-level project item in the Project Explorer window and select New»
Targets and Devices
from the shortcut menu to display the Add Targets and Devices dialog box.
2. Make sure that the Existing target or device radio button is selected.
3. Expand Real-Time CompactRIO.
4. Select the CompactRIO controller to add to the project and click OK.
5. If you have LabVIEW FPGA installed, the Select Programming Mode dialog box appears. Select Scan Interface to put the system into Scan Interface mode.
Tip
Use the CompactRIO Chassis Properties dialog box to change the programming mode in an existing project. Right-click the CompactRIO chassis in the
Project Explorer
window and select Properties from the shortcut menu to display this dialog box.
6. Click Discover in the Discover C Series Modules? dialog box if it appears.
7. Click Continue.
8. Right-click the controller item in the Project Explorer window and select Properties from the shortcut menu to display the RT Target Properties dialog box. Select Scan Engine from the Category list to display the Scan Engine page.
Getting Started with NI SMD-7610 and NI 9512 Modules | © National Instruments | 15
9. Set the Scan Period to 5 ms, then click OK to close the RT Target Properties dialog box.
10. Right-click the controller item in the Project Explorer window and select New»
NI SoftMotion Axis
from the shortcut menu to open the Axis Manager dialog box, shown
11. Click Add New Axis to create an NI SoftMotion axis associated with the NI 9512 module.
Axes are automatically bound to an available module. You can double-click the axis name to rename the axis and give it a descriptive name.
Figure 12. Axis Manager Dialog Box
12. Click OK to close the Axis Manager dialog box. The new axis is added to the Project
Explorer
window.
Note
You cannot associate more than one axis with the same C Series module.
16 | ni.com
| Getting Started with NI SMD-7610 and NI 9512 Modules
When you have finished these steps your LabVIEW project should look similar to the
Figure 13. Project Explorer Window with Modules in Scan Interface Mode
Getting Started with NI SMD-7610 and NI 9512 Modules | © National Instruments | 17
Step 4: Configure the NI 9512 Axis
The Axis Configuration dialog box includes configuration options for stepper drive command
signals, feedback devices, motion and digital I/O, trajectory, and axis setup. Figure 14 shows the
parts of the Axis Configuration dialog box for the NI 9512 C Series module. Refer to the
NI SoftMotion Module
book of the LabVIEW Help for detailed information about each configuration option.
Figure 14. Axis Configuration Dialog Box
Note
The Axis Configuration dialog box user interface may not match this image exactly depending on which version of the LabVIEW NI SoftMotion Module you are using.
Complete the following steps to configure the axis I/O settings for use with the NI SMD-7610 stepper drive.
1. Right-click the axis in the Project Explorer window and select Properties from the shortcut menu to open the Axis Configuration dialog box.
2. Configure the following settings on the General Settings page ( ).
a. Confirm that Loop Mode is set to Open-Loop. Axes configured in open-loop mode produce step outputs but do not require feedback from the motor to verify position.
b. Set Feedback Source to Encoder 0, if you have connected an encoder, or None if you do not have an encoder connected.
c. Confirm that the Axis Enabled and Enable Drive on Transition to Active Mode checkboxes contain checkmarks. These selections configure the axes to automatically activate when the NI Scan Engine switches to Active mode.
Note
Disable these options to prevent axes from automatically activating when the
NI Scan Engine switches to Active mode.
18 | ni.com
| Getting Started with NI SMD-7610 and NI 9512 Modules
3. If you have connected an encoder, click the Encoder button (
Units and Counts Per Unit.
) and configure the a. In the Active State section set the Line State for A, B, and Index to High.
b. In the Index Reference Criteria section set the Line State for A and B to Inactive.
c. Select rev from the Units text box, or type revolutions if you prefer.
d. Set the Counts per rev to 8,000. This setting is the encoder resolution in quadrature counts per revolution and corresponds to the encoder lines per revolution multiplied by four.
When you are finished the Encoder Settings page will look similar to Figure 15.
Figure 15. Axis Configuration Encoder Page
4. Click the Stepper button ( ) to open the Stepper page.
a. Ensure that the Stepper Output settings match the following:
•
Output Mode
—Step and Direction
•
Output Type
—Single-Ended
•
Active State
—Low b. Configure the Units and Steps Per Unit.
• Select rev from the Units text box, or type revolutions if you prefer.
• Set Steps Per revolution to 20,000.
Note
The Steps Per revolution setting must match the Steps/Rev DIP switch setting. If you change the Steps/Rev setting using the DIP switches, update this setting to match.
c. (Optional) Click the Monitor button ( ) and make the following changes to enable NI SoftMotion to disable the drive and turn off the Drive Enable signal when the specified position error limit is exceeded.
Getting Started with NI SMD-7610 and NI 9512 Modules | © National Instruments | 19
Note
The Monitor button is greyed out if Feedback Source on the Axis Settings page is set to None.
• Enable the Enforce Position Error Limit checkbox.
• Set Position Error Limit to a reasonable tolerance for your system, such as 1.
5. Click the Drive Enable button ( following:
) and ensure that the Drive Enable settings match the
•
Output Type
—Sinking
•
Active State
—Off
•
Safe State
—On
6. If you connected the Out+/Out- signal, click the Digital I/O button ( the following steps to configure the DI 0 signal:
) and complete a. Double-click the text in the Mapping column and select Drive Fault/Alarm from the dropdown list. b. Ensure that the DI 0 settings match the following:
•
Input Type
—Sinking
•
Active State
—On
•
Digital Filter
—50 µs
7. Complete the following additional steps if you do not have limits and home connected at this time: a. Click the Limits & Home button ( ).
b. In the Forward Limit and Reverse Limit sections ensure that the settings match the following:
Note
These configuration settings disable limits for initial setup and testing purposes. National Instruments recommends connecting and enabling limits in your final application.
• Clear the Enable checkbox from both Forward Limit and Reverse Limit.
• Set the Active State for both Forward Limit and Reverse Limit to Off. This prevents a limit warning even though limits are turned off.
c. Open the Home section and clear the Enable checkbox.
8. Configure any additional I/O settings according to your system requirements, such as position compare or position capture signals.
9. Click OK to close the Axis Configuration dialog box.
10. Right-click the controller item in the Project Explorer window and select Deploy All to deploy the axis information.
11. Select File»Save Project to save the project.
20 | ni.com
| Getting Started with NI SMD-7610 and NI 9512 Modules
Step 5: Enable and Test the Drive Using LabVIEW
Use the Interactive Test Panel to test and debug your motion system and configuration settings on the selected axis. With the Interactive Test Panel you can perform a simple straight-line move and monitor feedback position and position error information, move and I/O status information, change move constraints, get information about software errors and faults, and view position or velocity plots of the move.
Complete the following steps to test your setup after configuring the axis using the Axis
Configuration
dialog box.
1. Right-click the axis in the Project Explorer window and select Interactive Test Panel from the shortcut menu. Opening this dialog box sends the axis settings to the hardware and activates the I/O on the module.
2. On the Move tab set Move Mode to Relative Position and Target Position to 20 rev.
3. On the Move Constraints tab set Velocity to 2 rev/sec, Acceleration and Deceleration to
20 rev/sec 2, and Acceleration Jerk and Deceleration Jerk to 200 rev/sec 3 . Using the encoder counts per revolution and stepper steps per revolution values specified in this tutorial the motor will move 20 revolutions at 120 rpm.
Tip
Click the Help button ( ) on the bottom of the dialog box for detailed information about the items available in this dialog box.
4. Click the Enable button ( ) on the bottom of the dialog box to enable the drive.
5. Click the Start button ( ) on the bottom of the dialog box to start the move with the configured options.
6. Use the Status and Plots tabs to monitor the move while it is in progress.
Finalize your motion system setup by connecting and configuring additional I/O such as limits as required by your system using the 37-pin terminal block.
Getting Started with NI SMD-7610 and NI 9512 Modules | © National Instruments | 21
Worldwide Support and Services
The National Instruments Web site is your complete resource for technical support. At ni.com/support
you have access to everything from troubleshooting and application development self-help resources to email and phone assistance from NI Application Engineers.
Visit ni.com/services
for NI Factory Installation Services, repairs, extended warranty, calibration, and other services.
Visit ni.com/register
to register your National Instruments product. Product registration facilitates technical support and ensures that you receive important information updates from NI.
A Declaration of Conformity (DoC) is our claim of compliance with the Council of the European
Communities using the manufacturer’s declaration of conformity. This system affords the user protection for electromagnetic compatibility (EMC) and product safety. You can obtain the DoC for your product by visiting ni.com/certification
. If your product supports calibration, you can obtain the calibration certificate for your product at ni.com/calibration
.
National Instruments corporate headquarters is located at 11500 North Mopac Expressway,
Austin, Texas, 78759-3504. National Instruments also has offices located around the world to help address your support needs. For telephone support in the United States, create your service request at ni.com/support
and follow the calling instructions or dial 512 795 8248. For telephone support outside the United States, visit the Worldwide Offices section of ni.com/ niglobal
to access the branch office Web sites, which provide up-to-date contact information, support phone numbers, email addresses, and current events.
Refer to the NI Trademarks and Logo Guidelines at ni.com/trademarks for more information on National Instruments trademarks. Other product and company names mentioned herein are trademarks or trade names of their respective companies. For patents covering National
Instruments products/technology, refer to the appropriate location: Help»Patents in your software, the patents.txt file on your media, or the
National Instruments Patents Notice at ni.com/patents. You can find information about end-user license agreements (EULAs) and third-party legal notices in the readme file for your NI product. Refer to the Export Compliance Information at ni.com/legal/export-compliance for the National Instruments global trade compliance policy and how to obtain relevant HTS codes, ECCNs, and other import/export data.
© 2013 National Instruments. All rights reserved.
376092A-01 Aug13
advertisement
* Your assessment is very important for improving the workof artificial intelligence, which forms the content of this project
Related manuals
advertisement
Table of contents
- 1 Getting Started with NI SMD-7610 Stepper Drives and NI 9512 C Series Modules
- 1 Contents
- 2 What You Need to Get Started
- 2 Hardware
- 2 Software
- 3 Figure 1. NI 9512 to NI SMD-7610 Connections
- 3 Related Documentation
- 4 Hardware Installation and Configuration
- 4 Step 1: Set Up the CompactRIO System
- 4 Figure 2. Installing the Controller on the Chassis (Eight-Slot Chassis Shown)
- 5 Step 2: Connect the NI 9512 to the 37-Pin Terminal Block
- 5 Figure 3. NI 9512 37-Pin Terminal Block Pin Assignments
- 6 Step 3: Connect the 37-Pin Terminal Block to the +24 V Power Supply
- 6 Step 4: Connect the Drive Command Signals
- 6 Figure 4. SMD-7610 Drive Command and I/O Connector
- 7 Step 5: Connect the Drive Enable Signal
- 7 Step 6: (Optional) Connect the Drive Fault Signal
- 7 Step 7: (Optional) Connect the Encoder Signals
- 7 Table 1. NI SMD-7610 to 37-Pin Terminal Block Connections
- 8 Step 8: Connect the NI PS-12/13 Power Supply to the NI SMD-7610
- 8 Figure 5. NI PS-12/13 Power Supply Terminals
- 8 Figure 6. SMD-7610 Power and Motor Connector
- 9 Step 9: Connect the SMD-7610 to the Motor
- 9 Figure 7. Four Lead Motor Connection
- 9 Figure 8. Eight Lead Motor Parallel Connection
- 10 Figure 9. Eight Lead Motor Series Connection
- 10 Step 10: Configure the NI SMD-7610 DIP Switches
- 10 Figure 10. NI SMD-7610 DIP Switches
- 11 Table 2. Switch A DIP Switch Settings
- 12 Table 3. Switch B DIP Switch Settings
- 12 Step 11: Power on the Drive and Verify Connections
- 13 Figure 11. Drive Status LED Location
- 13 Software Installation and Configuration
- 13 Step 1: Install Software on and Configure the NI RT Controller
- 13 Verify the NI RT Controller
- 14 Reformat the NI RT Controller (Optional)
- 14 Install Software on the NI RT Controller
- 15 Step 2: Create a Project in Scan Interface Mode
- 15 Step 3: Add Resources to the Project
- 16 Figure 12. Axis Manager Dialog Box
- 17 Figure 13. Project Explorer Window with Modules in Scan Interface Mode
- 18 Step 4: Configure the NI 9512 Axis
- 18 Figure 14. Axis Configuration Dialog Box
- 19 Figure 15. Axis Configuration Encoder Page
- 21 Step 5: Enable and Test the Drive Using LabVIEW
- 22 Worldwide Support and Services