Performance Data. Maytag MQU1556AEW, AFU2067BW, MQU1554AEW, AQU1525AEW, AFU1505BW, AFU1767BW, MQU2056ARW, AFU1567BW, AFU1705BW, AFU2005BW
Add to my manuals
51 Pages
advertisement
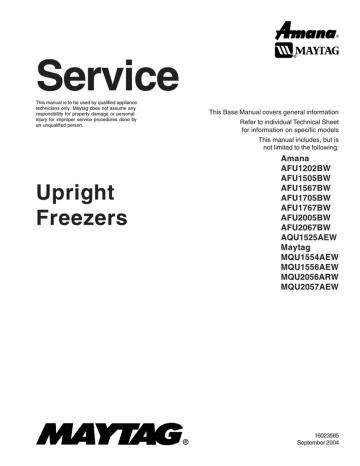
Component Testing
!
WARNING
To avoid risk electrical shock, personal injury, or death, always disconnect electrical power source to the freezer before attempting to service, unless test procedures require power to be connected. When removing any wiring from terminals they must be replaced on the same terminals.
Ensure all ground wires are connected before certifying unit as repaired and/or operational.
Capacity Insulation Amb Wattage %
Cu. Ft. Type
11.6 Foam 70 °
90
°
110
°
15.2 Foam 70 °
90
°
110
°
16.8 Foam 70
°
90
°
110 °
19.6 Foam 70
°
90 °
110
°
90
95
−110
−115
100
130
−120
95 −115
100
−120
105
−125
105
−125
110
−130
115 −135
120
−140
125 −145
−150
Running
35 −45
50
−60
80
−90
35 −45
55
−65
90
−100
40
−50
55
−65
90 −100
40
−50
55 −65
90
−100
15.0 Foam 70 °
90
°
110 °
16.8 Foam 70
°
90
110
19.6 Foam 70
90
°
°
°
110
°
°
Performance Data at Control Setting # 4
Manual Defrost
High
Side
95 −115
125
−145
170
−190
95 −115
125
−145
165
−185
95
−115
130
−150
165 −185
100
−120
135 −155
175
−195
Performance Data at Control Setting # 4
125
−145
130
−150
135 −155
135
−155
140
145
135
140
145
−160
−165
−155
−160
−165
Auto Defrost
45
−55
60
−70
90 −100
35
−45
45 −55
90
−100
40 −50
60
−70
90
−100
105
−125
140
−160
185 −205
100
−120
135 −155
175
−195
95 −115
130
−150
175
−195
−3 −1
−3 −1
−1 1
−3 −1
−2 0
−2 0
−4 −2
−4 −2
−2 0
Low
Side
−5 −3
−4 −2
−2 0
−4 −2
−3 −1
−3 −1
−4 −2
−3 −1
−2 1
−4 −2
−3 −1
−1 −1
Amps Running
Capacitor
0.7
−1.0
0.8
−1.1
0.8
−1.1
0.9
−1.2
0.9
−1.2
1.0
−1.3
0.9
−1.2
0.9
−1.2
1.0
−1.3
1.0
−1.3
1.0
−1.3
1.2
−1.5
12 uF
210 V
12 uF
210 V
12 uF
210 V
12 uF
210 V
1.0
−1.3
1.1
−1.4
1.2
−1.5
1.2
−1.5
1.2
1.2
1.2
1.2
1.3
−1.5
−1.6
−1.5
−1.5
−1.6
12 uF
210 V
12 uF
210 V
12 uF
210 V
22 16023585 ©2004 Maytag Services
Disassembly Procedures
!
WARNING
To avoid risk of electrical shock, personal injury or death; disconnect power to unit before following any disassembly procedures.
Replacing Drier
NOTE: A new drier must be installed whenever any system component is replaced, or whenever the system is opened.
The replacement drier is sealed at both ends to prevent entrance of moisture. Do not break these seals until all preparations for the installation have been completed.
1. Disconnect line cord from electrical outlet.
2. Clean the process tube using steel wool or fine emery cloth.
3. Install service valve as close as possible to the tip of the process tube, for easy pinch-off after recharging the system.
4. Connect a hose to the service valve and capture the charge.
NOTE: Effective July 1, 1992, before opening any refrigeration system it is the responsibility of the service technician to capture the refrigerant for safe disposal.
5. Remove all paint and scale from the capillary tube for a distance of approximately three inches from the original joint, (use steel wool or emery cloth).
6. Cut the capillary tube approximately one inch from the old joint. Verify the cut is uniform around the tubing, then break it with the fingers.
1"
Score here then snap tube
Cutting Capillary Tube
7. Cut the drier from condenser outlet and thoroughly clean the end of the tube.
8. Make an offset 1/2 inch (13 mm) from the end of the capillary tube to prevent its penetrating too far into drier tubing. When forming the offset, use a radius large enough so the inside diameter of the tubing is not reduced.
Condenser end
inlet end
Capillary end
outlet end
Flow direction
Form offset
Capillary Tube Insertion
9. Cut the inlet tube on the new drier.
10.Snap off the scored end of replacement drier with your fingers.
11. Install new drier and solder all joints. Use sil-fos on all copper to copper joints. On copper to steel joints, silver solder with proper flux must be used. Excess flux must be wiped off after soldering.
12.Visually check all soldered joints, evacuate and recharge the system.
13.Test run the unit to verify proper operation.
14.Pinch process tube and cut off the service valve.
Solder the joint and test for leaks.
Replacing Compressor
Replacement compressors are charged with the correct amount of oil and contain a holding charge of either dry nitrogen or a refrigerant.
The replacement compressor will be similar to the type of compressor originally used and may or may not have an oil cooler. If the sealed system does not use the oil cooler, do not disturb the oil cooler plugs. Simply disregard the oil cooler.
The holding charge assures compressor is dry. A compressor which shows no evidence of internal pressure when cutting the line or pulling the plugs, should be returned for replacement.
When replacing a compressor, cut as close to the soldered joints as possible. If tubes are not long enough, it may be necessary to unsolder the joints to allow connections to the replacement compressor.
When replacing compressor, proceed as follows:
1. Disconnect line cord from electrical outlet.
2. Install a service valve on the process tube.
3. Connect a hose to the service valve and capture the charge.
NOTE: Effective July 1, 1992, before opening any refrigeration system it is the responsibility of the service technician to capture the refrigerant for safe disposal.
4. Clean the tubing approximately three inches (76 mm) at the point of intended cut. Before cutting the tube, verify it will be long enough to reconnect to the replacement compressor. If not, unsolder the joints.
26 16023585 ©2004 Maytag Services
Disassembly Procedures
!
WARNING
To avoid risk of electrical shock, personal injury or death; disconnect power to unit before following any disassembly procedures.
5. Disconnect wire from compressor terminals
6. Remove retaining clips from compressor mounts. Lift compressor from mounting rails and transfer the rubber grommets to replacement compressor.
7. Set replacement compressor into position and install retaining clips.
8. Remove all rubber plugs, clean the stubs of the compressor and compare the size of tubing to stubs of replacement compressor. It may be necessary to swage the copper tubing in order to make the joints.
9. Install a six inch (152 mm) long copper tube to low side process tube on the compressor. Add service valve to end of this tube.
10.Connect all tubing, apply flux to compressor stubs and solder all the joints. Excess flux must be wiped off after soldering.
11. Install a new drier.
12.Visually check all joints for leaks. Evacuate and recharge the system.
13.Reconnect wire leads to compressor terminals and test run the unit to verify proper operation.
14.Pinch process tube and cut off the service valve.
Solder the joint and test for leaks.
12.Pull entire shelving assembly out of cabinet and position to allow detachment of heat exchanger.
Replacing Heat Exchanger Refrigerated
Shelf Models
1. Disconnect line cord from electrical outlet.
2. Install a service valve as close as possible to the tip of process tube, for easy pinch-off after recharging the system.
3. Connect a hose to the service valve and capture the charge.
NOTE: Effective July 1, 1992, before opening any refrigeration system it is the responsibility of the service technician to capture the refrigerant for safe disposal.
4. Remove butyl sealer from around the tube entry hole.
5. Unsolder suction tubing at compressor stub or cut tubing three inches (76 mm) from compressor stub.
6. Cut drier from condenser tubing. Then cut drier from capillary tube.
7. Straighten heat exchanger tubing to slide tube through entry hole from inside the cabinet.
8. Remove clamp retaining the control feeler tube to underside of second shelf (counting downward).
9. Carefully bend feeler tube down against liner side to be out of the way.
10.Remove screws securing top freezer plate to liner top. As front edge of plate drops clearing the liner.
11. Carefully remove each shelf from food liner support rails. Push outward on liner side just above front retainer embossment. Lift shelf front free of retainer.
If necessary, repeat this operation on opposite side.
©2004 Maytag Services 16023585
Freezer Shelf Assembly Joints
Refrigerated Shelf Model
13. Unsolder capillary tube and suction line (cut suction line away from original joint and swedge the end of it for new tubing, if desired).
14.Clean joints and solder new heat exchanger to shelving assembly. Clean & paint soldered joints before reinstalling evaporator.
15.Transfer vinyl insulating sleeve to new heat exchanger. Tape the same points.
16.Carefully position assembly back in the cabinet, verify heat exchanger tubing passes through the opening without damaging the vinyl sleeve.
17.Carefully work each shelf into its proper support rails.
Replace non-refrigerated shelf in the same manner.
18.Secure control feeler tube to correct shelf with the clamp. Verify feeler tube rests firmly against shelf surface to obtain thermal contact.
19.Fasten top freezer plate, verifying all spacers are in place.
20.Form heat exchange so it is similar in position to the original. Be careful when bending the tubing at the entry hole to prevent kinks.
21.Pack entry hole with butyl sealer.
22.If suction tubing was cut from compressor when removed, swedge compressor suction tube to fit replacement suction tubing.
23.Solder the suction lines.
24.Install new drier.
25.Visually check all joints for leaks. Evacuate and recharge the system.
26.Test run the unit to verify proper operation.
27.Pinch process tube and cut off the service valve.
Solder the joint and test for leaks.
27
Disassembly Procedures
!
WARNING
To avoid risk of electrical shock, personal injury or death; disconnect power to unit before following any disassembly procedures.
Replacing Heat Exchanger No-Defrosting
Models
1. Disconnect line cord from electrical outlet.
2. Install service valve as close as possible to the tip of process tube for easy pinch-off after recharging the system.
3. Connect a hose to the service valve and capture the charge.
NOTE: Effective July 1, 1992, before opening any refrigeration system it is the responsibility of the service technician to capture the refrigerant for safe disposal.
4. Remove butyl sealer from around tube entry hole.
5. Unsolder suction tubing at compressor stub or cut tubing three inches (76 mm) from compressor stub.
6. Cut drier from condenser tubing. Then cut drier from capillary tube.
7. Remove screws securing freezer coil cover and detach green grounding wire.
Green
White
Red
Orange
White
Removing Defrost Thermostat
No Defrost Models
13. Detach green grounding wire from freezer coil header.
14. Remove screws securing freezer coil to coil mounting panel. Coil is now free to be removed.
15.Straighten heat exchanger tubing to pass through the opening in the cabinet back.
16.Pull entire assembly out of the cabinet.
17.Unsolder cap tube and suction line from freezer coil, careful not to overheat the epoxy joints.
Unsolder these joints
Circulating Fan and Wiring
With Coil Cover Removed
8. Remove styrofoam air block from each end of the coil.
9. Disconnect defrost heater lead from spade terminal on fan motor.
10.Spade connector is used to join the defrost heater lead to the lead-in wire. Separate these two wires at the spade connector. Release lead from the two clips on coil mounting panel.
11. Disconnect heater lead from defrost thermostat.
12.Remove defrost thermostat from coil header to release the front tang. See following illustration.
Protect these joints
Heat Exchanger To Freezer Coil Joints
No-Defrost Models
18. Transfer rubber insulating sleeve to replacement heat
28 16023585 ©2004 Maytag Services
Disassembly Procedures
!
WARNING
To avoid risk of electrical shock, personal injury or death; disconnect power to unit before following any disassembly procedures.
exchanger assembly and tape the same points.
19.Clean tubing and silver solder new heat exchanger to coil with proper flux. Excess flux must be wiped off after soldering.
20.Clean tubing and silver solder new heat exchanger to the coil.
21.Work new tubing through rear opening, careful not to tear rubber sleeve.
22.Position freezer coil and install mounting screws.
Replace styrofoam air blocks at the upper ends of the coil. This is necessary to channel the air flow properly through the coil.
23.Carefully form tubing and route it in the same manner as the original. Use extreme care when bending the tubing at entrance hole to prevent kinking. Pack entry with butyl sealer.
24.Clean the suction line and silver solder the joint with proper flux. Excess flux must be wiped off after soldering.
25.Install new drier.
26.Visually check all joints for leaks. Evacuate and recharge the system.
27.Lace the defrost heater leads to both ends of the freezer coil. Fasten wire leading to fan motor to the two clips on the mounting panel.
28.Connect white defrost heater lead to white lead-in wire with spade connector, attach other wire to spade terminal on fan motor.
29.Secure defrost thermostat to coil and connect lead wire.
30.Connect green grounding wire to fan motor and to freezer coil cover.
31.Reinstall coil cover and secure with screws.
32.Test run the unit to verify proper operation.
33.Pinch process tube and cut off the service valve.
Solder the joint and test for leaks.
Replacing Freezer Shelving Refrigerated
Shelf Models
Current freezer models are equipped with steel shelves and can be individually repaired or replaced as follows:
1. Disconnect line cord from electrical outlet.
2. Install service valve as close as possible to the tip of process tube, for easy pinch-off after recharging the system.
3. Connect a hose to service valve and capture the charge.
NOTE: Effective July 1, 1992, before opening any refrigeration system it is the responsibility of the service technician to capture the refrigerant for safe disposal.
4. Remove butyl sealer from tube entry hole in the
©2004 Maytag Services cabinet back.
5. Cut the end off of compressor process tube after the refrigerant has been captured. Attach a service valve to it, and leave the valve open.
6. Cut drier from condenser tubing. Cut drier from capillary tube. To cut capillary tube, score the walls with a knife or file. Cut around entire tube uniformly, then break it with your fingers.
1"
Score here then snap tube
16023585
Cutting Capillary Tube
7. Straighten heat exchanger tubing to slide tube through entry hole from inside the cabinet.
8. Remove clamp securing control feeler tube to underside of second shelf (counting downward).
9. Carefully bend feeler tube down against liner side to be out of the way.
10.Remove screws securing top freezer plate to liner top. Front edge of the plate, drops clear of the liner, disconnect lead wires from interior light, if equipped.
11. Carefully remove each shelf from the food liner support rails. Push out on liner side just above front retainer embossment. Lift the shelf front free of the retainer. If necessary, repeat this operation on the opposite side.
12.Carefully pull entire shelving assembly out of cabinet and position to allow detachment of failed shelf.
13.Cut or unsolder failed shelf and remove.
14.Clean joints and solder new shelf to assembly and paint new joints.
15.Carefully position assembly back in the cabinet, verifying heat exchanger tubing passes through rear opening without damaging the rubber sleeve.
16.Carefully work each shelf into its proper support rails.
Replace non-refrigerant shelf in the same manner.
17.Connect wiring to freezer light, if equipped, and fasten top freezer plate, verifying all spacers are in place.
18. Secure control feeler tube to correct shelf with the
29
Disassembly Procedures
!
WARNING
To avoid risk of electrical shock, personal injury or death; disconnect power to unit before following any disassembly procedures.
clamp. Verify feeler tube rests firmly against shelf surface to obtain thermal contact.
19.Form heat exchanger tubing so it is similar in position to the original. Be careful when bending tubing at the entry hole to prevent kinks.
20.Pack tube entry hole with butyl sealer.
21.If cut when remove, swedge compressor suction tubing to fit replacement tubing
22.Install new drier and connect all tubing. Silver solder the joints with proper flux. Excess flux must be wiped off tubing after soldering.
23.Visually check all joints for leaks. Evacuate and recharge the system.
24.Test run the unit to verify proper operation.
25.Pinch process tube and cut off the service valve.
Solder the joint and test for leaks.
White
Green
Red
Orange
White
Replacing Freezer Coil No-Defrosting
Models
Because of freezer coil location, do not attempt replacement without first removing coil and heat exchanger from the cabinet. Even though an experienced silver brazer can control a torch flame, possibility of overheating and distorting plastic is high.
1. Disconnect line cord from electrical outlet.
2. Install service valve as close as possible to tip of process tube for easy pinch-off after recharging the system.
3. Connect a hose to service valve and capture the charge.
NOTE: Effective July 1, 1992, before opening any refrigeration system it is the responsibility of the service technician to capture the refrigerant for safe disposal.
4. Remove butyl sealer from tube entry hole in the cabinet back.
5. Clean approximately three inches (76 mm) of the heat exchanger tubing at the compressor stub.
Unsolder at the joint or cut three inches (76 mm) from the stub.
6. Unsolder drier from condenser outlet tube and clean the outlet. Remove drier from capillary tube so tubing assembly can be pulled through the tube entry opening.
7. Remove screws securing freezer coil cover. Lift cover out and detach green grounding wire.
8. Remove styrofoam air block from each end of the coil.
9. Disconnect defrost heater lead from spade terminal on fan motor.
Circulating Fan and Wiring With
Coil Cover Removed
10. Spade connector is used to join the white defrost heater lead to the white lead-in wire. Separate these wires at the spade connector. Release heater lead from the two clips on the coil mounting panel and unlace it from the coil.
11. Disconnect white defrost heater lead from defrost thermostat and unlace it from freezer coil.
12.Remove defrost thermostat from coil header to release the front tang.
Removing Defrost Thermostat
No-Defrost Models
13. Detach green grounding wire from freezer coil header.
14. Remove screws securing freezer coil to coil mounting panel. The coil is now free to be removed.
15. Straighten heat exchanger tubing to pass through the
30 16023585 ©2004 Maytag Services
Disassembly Procedures
!
WARNING
To avoid risk of electrical shock, personal injury or death; disconnect power to unit before following any disassembly procedures.
opening in the cabinet back.
16.Pull entire assembly out through the front. Position to allow detachment of heat exchanger.
17.Unsolder suction and capillary tube from the coil.
to freezer coil header.
29.Connect green grounding wire to fan motor and to freezer coil cover.
30.Test run the unit to verify proper operation.
31.Pinch process tube and cut off the service valve.
Solder the joint and test for leaks.
Unsolder these joints
Replacing Light Switch
1. Unplug line cord from electrical outlet and pry light switch from liner.
2. Pull lead wires out far enough to disconnect connectors.
3. Connect new switch, plug in line cord, and check the light.
4. Push new switch and wiring into position.
Protect these joints
Heat Exchanger To Freezer Coil Joints
No-Defrost Models
18.Remove freezer coil and replace with new coil.
19.Clean and connect tubes and silver solder the joints with proper flux. Excess flux must be wiped off tubing after soldering.
20.Work heat exchanger tubing through rear opening, careful not to tear rubber sleeve.
21.Position freezer coil and install mounting screws.
Replace styrofoam air blocks at the upper ends of freezer coil. This is necessary in order to channel air flow through the coil.
22.Carefully form tubing and route in the same manner as the original. Use extreme caution when bending tubing at the entrance hole to prevent a possible kink.
Pack entry hole with butyl sealer.
23.If cut when removed, swedge compressor suction tube to reconnect suction tubing.
24.Clean all the tubes. Install new drier and silver solder the joints with proper flux. Excess flux must be wiped off tubing after soldering.
25.Visually check the joints for leaks. Evacuate and recharge the system.
26.Lace white heater leads to both ends of the freezer coil. Fasten wire leading to fan motor to the two clips on the mount-panel.
27.Join white defrost heater lead and white lead-in wire with spade connector and attach spade terminal on fan motor.
28. Connect defrost thermostat lead and fasten thermostat
©2004 Maytag Services 16023585
Replacing Control
1. Unplug the power cord.
2. Pull control knob off, remove control mounting screws, and disconnect all wires.
3. On refrigerated shelf models, remove feeler tube from underside of shelf front by loosening the clamp.
On no-defrosting models, disconnect control feeler tube cover from the liner side by pulling straight out at its center.
4. On refrigerated shelf models, securely tape a piece of heavy string to the end of the feeler tube.
On no-defrosting models, observe feeler tube is coiled behind the cover, then straighten it.
5. Pull complete assembly out of cabinet, (on refrigerated shelf models, string end should follow through the hole in the liner side so it can be used to pull replacement back through.
6. Transfer plastic sleeve to new feeler tube.
7. On refrigerated shelf models, tape string to new feeler tube. Pull tube through the hole in the liner side.
On no-defrosting models, work feeler tube through the opening and reshape it so it will not contact the inner side or cover.
8. Connect all wires, including grounding wire, and push control into position.
9. Reinstall mounting screws.
10.On refrigerated shelf models, secure feeler tube to underside of shelf front.
On no-defrosting models, attach feeler tube cover by bowing it out at the center until tabs on the cover can be fitted into slots in the liner.
11. Reinstall control knob. Plug in power cord and check freezer operation.
Replacing Heater
31
Disassembly Procedures
!
WARNING
To avoid risk of electrical shock, personal injury or death; disconnect power to unit before following any disassembly procedures.
Remove defrost heater as follows:
1. Remove freezer coil cover.
2. Detach heater leads and unlace from freezer coil.
3. Remove clips at each end of heater. Push downward on heater shield grasping radiant heater at both ends and lifting outward.
Retaining
clip
Defrost Heater and Retaining Clips
4. Replace heater in reverse of removal.
!
CAUTION
When installing radiant heater do not touch the heater glass. Salt and oil on the hands may cause serious damage.
Replacing Freezer Fan Motor
Remove screws from coil cover and disconnect ground wire from cover. Remove freezer coil cover.
Before checking fan circuit for failures, spin the fan blade to verify nothing has lodged against it which could prevent normal fan operation. If blade spins freely, check fan motor as follows:
1. Unplug line cord.
2. Attach test cord leads to fan motor leads. If motor runs, check all cabinet wiring for an open circuit. If motor fails to operate, remove and replace it in the following manner.
3. Disconnect lead and ground wire from fan motor.
4. Remove complete fan motor assembly by removing screws securing fan motor bracket to mounting panel. Remove motor from bracket. Replace assembly in reverse order of removal.
5. Attach ground wire to freezer coil cover and replace the cover.
No alignment is necessary when replacing fan blade. Fit blade on the shaft and push. Blade is equipped with a built-in stop.
Thermostat may be loosened for replacement by merely spreading front tangs of retainer clips.
32
Defrost Thermostat and Mounting Clip
16023585 ©2004 Maytag Services
Disassembly Procedures
!
WARNING
To avoid risk of electrical shock, personal injury or death; disconnect power to unit before following any disassembly procedures.
Cabinet Door Assembly
Cabinet door assembly consists of outer door panel, bezel and nameplate insert, door handle and insert, door lock assembly (if equipped), hinge bushings, fiberglass insulation, inner door liner, door shelf trim, and door seal gasket.
Top door hinge
Tapping plate
Washer
Outer door panel
Bezel
Serial plate
Bushing
Door handle
Door gasket
Lock assembly
Insert
Door shelf
trim
©2004 Maytag Services
Inner door liner
Clip
Bottom
hinge
nut
16023585
Kickplate
Spacer
Bushing
Washer
Lower door hinge
33
Disassembly Procedures
!
WARNING
To avoid risk of electrical shock, personal injury or death; disconnect power to unit before following any disassembly procedures.
Removing Cabinet Door Assembly
1. Remove screws securing upper hinge to cabinet top.
2. Open door assembly and lift door off lower hinge pin.
Install Cabinet Door Assembly
1. Hold door assembly in open position and place on lower hinge with hinge pin entering the hinge bushing at the door bottom.
2. Close door and install upper hinge mounting screws.
Check gasket seal.
Install Door Liner And Gasket
The DURA-LAST inner door liner and gasket are mounted to outer door panel by screws place every 4 inches (102 mm) around the door flange perimeter.
Removing Inner Liner and Gasket.
1. Remove cabinet door assembly as previously described.
2. Lay door assembly on a flat, padded surface.
3. Remove all mounting screws and lift off inner liner and gasket.
Installing Inner Liner and Gasket
1. Position gasket around inner panel so gasket lip will be sandwiched between inner liner and outer door panel flange.
2. Replace and tighten all inner liner mounting screws until snug.
NOTE: Do not over tighten screws, this could crack liner or cause screw head to pull through the hole.
3. Always align door.
Door Handle
Door handle and insert are attached to outer door panel by mounting screws which are located under the insert.
Removing the Door Handle
1. Bow insert slightly and unhook top and bottom from door handle.
2. Remove mounting screws which secure the handle.
NOTE: Longer mounting screw must be used to attach the bottom of door handle.
Door Lock Assembly
Door lock assembly (if equipped) is attached to outer door panel and consists of the cam and bolt (lock bolt).
Illustration below indicates movement of the lock bolt as the key is turned clockwise to locked position. An ejector spring in the lock forces the key out. Key will not remain in the lock once it is released, regardless of position the lock is in.
Locked
Unlocked
Lock design is simple and no major operating difficulties should be encountered. If the lock is not locking in a positive enough manner, position the door to verify it is high enough for the bolt to catch firmly. Side way movement to the door may also improve lock operation.
Sometimes leveling the freezer will eliminate need for cabinet door adjustments. Verify freezer is level from side to side, and from front to back, with a carpenters level. Adjust leveling glide until freezer is in a true vertical position.
34 16023585 ©2004 Maytag Services
Disassembly Procedures
!
WARNING
To avoid risk of electrical shock, personal injury or death; disconnect power to unit before following any disassembly procedures.
Removing Door Lock Assembly
1. Remove all inner door liner mounting screws on door lock side, and four from the top and bottom, working in from the lock side.
2. Pull inner door liner out far enough to reach the lock bolt.
3. Using a screw driver pushed through foam block.
Remove screw securing lock cam. Lock cam then can be removed.
4. Remove clip holding lock to outer door panel. Push lock out of door panel.
5. Reassemble in reverse order.
Improving Gasket Seal
In order for gasket to compress evenly around the entire door, it must make contact at the top and bottom at the same time. For this reason the door, should not toe-in or toe-out.
To correct a toe-in or toe-out condition verify hinge side of door is parallel to the cabinet.
1. Check cabinet levelers. Turning leveler in or out may correct a toe-in or toe-out condition.
2. Loosen all inner door panel mounting screws along the top, bottom, and latch side of the door.
NOTE: Do not loosen screws along hinge side.
3. Hold the corner that toes-in stationary; push in on the toe-out corner until door is lined up parallel with the cabinet. Tighten a few screws on latch side to hold door in position.
4. Open and close door several times to insure proper fit. If necessary, repeat steps 2 and 3.
5. Tighten all loosened screws until they are snug. Do not tighten screws too much, heads may pull through screw hole.
Cabinet Door Alignment
Cabinet door on each model is in correct alignment when:
• Hinge side of door is equidistant from cabinet flange at the top and bottom.
• Gasket seals smoothly and is compressed no more than 1/16 inch (1.6 mm) along the hinge side with door closed.
• Handle side of door should be 1/16 inch (1.6 mm) above the handle side of the cabinet (viewed from the front). Upper hinge side corner of door should be 1/16 inch (1.6 mm) above the cabinet top.
In many cases, leveling the freezer will eliminate needed for cabinet door adjustments. Verify freezer is level by checking both front edges as well as both sides of the cabinet, with a carpenter’s level. Adjust levelers until cabinet is in a true vertical position.
Checking Gasket Seal
Door gasket seals effectively with its normal pull. Visual inspection will usually reveal any point of poor seal.
Double check locations which are questionable by closing the door on a narrow strip of paper. Any areas that will not support the weight of the paper are considered areas of poor gasket seal.
On areas which cannot be checked visually or with a paper, rub blue carpenter’s chalk on the gasket, or dampen the gasket, and close door several times.
Examine the cabinet flange for transfer of chalk or dampness. Failure of the transfer indicates areas of poor seal.
©2004 Maytag Services 16023585
Hinge Adjustments
Hinge adjustments are necessary when:
• Gasket is not sealing sufficiently along hinge side of door.
• Gasket is compressed more than 1/16 inch (1.6 mm) on hinge side (causing a poor seal elsewhere around the door).
• Distance between the door and cabinet is greater at the top than it is at the bottom, or vice versa.
• Handle side of the door does not line up with cabinet side (when viewed from the front), or upper latch side corner is higher or lower than the cabinet top.
If one or more of these conditions exist, verify cabinet is level and make necessary hinge adjustments as instructed below.
Turning out the hinge side front leveler may correct a door sag.
Oversized holes in the cabinet top permit some sideways, or in and out adjustments of the top hinge.
Raise top hinge by placing a 1/32 inch (0.8 mm) shim beneath it.
Lower hinge can be moved out by adding a 1/32 inch
(0.8 mm) shim between it and the cabinet.
35
Disassembly Procedures
!
WARNING
To avoid risk of electrical shock, personal injury or death; disconnect power to unit before following any disassembly procedures.
Cabinet Assembly
Cabinet shell
Light switch
Temperature control knob
Temperature control plate
Light assembly
Cabinet
inner
liner
Drain tube and grommet
Temperature control
Cabinet shell
Light switch
Temperature control knob
Temperature control plate
Temperature control
Light assembly
Shelve
Cover gasket
Cabinet
inner
liner
Drain tube cap
Gate brackets
Drain tube and grommet
Evaportator cover
Gate brackets
Cabinet leveller
Wire gate
Wire gate
Cabinet leveller
36 16023585 ©2004 Maytag Services
Service Information
!
WARNING before attempting to service unless test procedures require power to be connected. When removing any wiring from terminals, replace on the same terminals. Ensure all ground wires are connected before certifying unit as repaired and/or operational.
To avoid risk of electrical shock, personal injury or death, always disconnect electrical power source to the freezer
System Operation
If freezer is not operating properly and electrical failure is not ruled out, refer to the electrical system and perform the necessary electrical tests before making any test which requires opening the system.
If there is no electrical failure and system does not operate properly, such as long run periods or warmer than normal compartment temperatures, the cause may be one of the following.
When first opening the door no refrigerant circulating sound is heard, but after several minutes it is noticeable, there is probably moisture in the system which is freezing at the capillary tube outlet. Install a new drier, evacuate, and recharge.
If no moisture is in the system and no leaks, check for kinked tubing. Sometimes a kink in a large tube will not affect the system operation. Kink in the capillary tube could cause erratic operation. It cannot be straightened without cracking its walls.
Failed Compressor
A compressor which is not pumping adequately will produce very little cooling effect. The shelf tubing may be covered with a thin film of frost, but the temperature will not reach control cut-off level, even with continuous running.
Because these conditions are similar to those for a refrigerant leak, perform leak test. If no leak is found, install gauges and check the operating pressures. If high side pressures are lower than those in the table in the “Specification” section and low side pressures are higher than specified, the compressor must be replaced.
Incorrect Refrigerant Charge
An overcharged system may have a frost back condition appearing outside the insulation sleeve on the suction line at the rear of the cabinet. When the compressor stops, frost melts and drips on the floor.
System must be purged, evacuated, and recharged with the correct amount of refrigerant.
An undercharged system will operate with temperatures above normal and compressor operating time will be increased. The greater the undercharge, higher the temperatures and longer the operating time.
Restricted Capillary Tube
The inner diameter of a capillary tube is about the same size as the period at the end of this sentence. It doesn’t take much to restrict this area. Use care when moving or touching the capillary tube, slight kink can cause a restriction.
Restrictions of capillary tube may be caused by moisture freeze-up, foreign particles lodged in the tube, or a kink.
If capillary tube is restricted, there will be noticeable lack of frost on the refrigerated shelves or evaporator. The compressor will operate for a short time then cycle on the overload.
The system must be purged, evacuated, and recharged with the correct amount of refrigerant. Before recharging, test for refrigerant leaks.
Partial Restriction in Low Side Tubing
Bent tubing, foreign matter, or moisture in the system, may cause a partial restriction in the low side tubing.
This usually results in frost-free tubing between the restriction and capillary tube and frost-covered tubing between the restriction and suction line. This restrictions acts like a second capillary tube, increasing pressure behind it (warming) and decreasing pressure beyond it
(cooling). Replace component if there is a partial restriction in the refrigerant tubing.
Moisture in the System
Any moisture in the system will usually freeze at the outlet end of the capillary tube, where it enters the evaporator coil. Preventing refrigerant from entering the coil. This results in loss of cooling with the compressor continuously operating. When the evaporator temperature rises above freezing, moisture restriction will melt and refrigerant will circulate through the system.
Freezer will operate normally until another freeze-up occurs, which depends upon the amount of moisture in the system.
Pressure Unloading in System
Compressor may stall and cycle on overload if an attempt is made to restart unit immediately after it has stopped. Compressor is trying to start while refrigerant pressure is high on condenser side and low on evaporator side. When the compressor stops operating, pressure in both sides equalizes as the liquid slowly passes through the capillary tube. When this occurs the pressures are said to be “unloaded”. Pressure unloading in the system will usually take from 3 to 6 minutes.
If compressor is operating but evaporator coil or refrigerated shelves are not refrigerated, stop the compressor and listen for refrigerant surging through tubing. If a “gurgling” sound is heard, capillary tube is not restricted. Check for a leak or check operating pressures.
©2004 Maytag Services 16023585
Pull Down Over Load
If cabinet interior is warm when compressor starts, “pull down” may overheat the compressor and cause cycling on the overload protector.
37
Service Information
!
WARNING before attempting to service unless test procedures require power to be connected. When removing any wiring from terminals, replace on the same terminals. Ensure all ground wires are connected before certifying unit as repaired and/or operational.
To avoid risk of electrical shock, personal injury or death, always disconnect electrical power source to the freezer
Checking Operating Pressures
If refrigeration system is not operating properly, check operating pressures.
Install a piercing valve on compressor process tube and on high side process tube.
NOTE: Piercing valve should not be left on the tubing after tests are complete. Remove the valve from discharge line and repair the opening. Evacuate and recharge the system.
When using gauges to verify operating pressures, observe the following precautions.
1. Verify gauges are accurately calibrated. When not connected into a system, gauge pointers should indicate 0 pressure. If necessary, turn the recalibrating screw on the dial until the pointer indicates 0.
2. Verify temperature control is set to normally maintain a 0°F (-17°C) temperature.
3. Remove all unfrozen food from the freezer.
4. Before taking final gauge readings, allow freezer to run through several cycles with the door closed. This will allow the temperature and pressures to stabilize.
5. Compare the final gauge readings for the model being serviced, see the category which applies to the readings indicated.
High Side—near normal pressure
Low Side—lower pressure (possible vacuum)
Wattage—lower than normal
Freezer shelf tubing or other low side tubing is probably restricted (kinked or blocked with foreign particle). This condition is usually accompanied with a frost build-up on the low side of the restriction. High side pressures will not unload and balance with the low side within the prescribed seven to ten minutes after the compressor is stopped.
High Side—much higher pressure
Low Side—slightly lower pressure
Wattage—higher than normal
Indicates a leak in the low side of the system. High side pressures will continually increase drawing through the leak becoming trapped in the high side tubing. Low side gauge will show a slight pressure being drawn in through the leak.
High Side—lower pressure
Low Side—lower pressure (possible vacuum)
Wattage—lower than normal
Indicates restriction at the entrance of the capillary tube.
High side pressures will take much longer than the prescribed seven to ten minutes to unload and balance with the low side after compressor has stopped.
High Side—higher pressure
Low Side—higher pressure
Wattage—higher than normal
Indicates an overcharge of refrigerant. Pressure increasing depends on the amount of overcharge and room temperature.
A slight overcharge may not cause trouble in 70°F (21°C) temperatures, where as in 90°F (32°C) temperatures a considerable rise in pressure will result.
An overcharge may also cause the suction line under the cabinet to be frosted during the run cycle. This condition will confirm the existence of an overcharge.
High Side—low pressure
Low Side—lower pressure (possible vacuum)
Wattage—lower than normal
Indicates a leak in the high side of the system. Both gauges will show progressively less pressure.
High Side—higher pressure
Low Side—near normal pressure
Wattage—higher than normal
Indicates air in the system. Resulting from a low side leak being repaired without the system being thoroughly evacuated and purged before recharging.
In most cases, you will find that the freezer is not as cold as it should be, because the efficiency of the system is greatly reduced by the presence of air.
Simply purging air from the system is not practical. The system being undercharged due to the loss of refrigerant. Evacuate, purge, and recharge the system
38 16023585 ©2004 Maytag Services
Service Information
!
WARNING before attempting to service unless test procedures require power to be connected. When removing any wiring from terminals, replace on the same terminals. Ensure all ground wires are connected before certifying unit as repaired and/or operational.
To avoid risk of electrical shock, personal injury or death, always disconnect electrical power source to the freezer
Operational Testing
Thorough operational checking of freezer will minimize future service calls.
1. Set control to No. 4 position.
2. Place thermometer in the center of the freezer.
Operating temperatures should cycle between +3°F
(cut in) to -2°F (cut out) in an empty cabinet.
3. Check thoroughly with reliable leak detector for leaks.
4. Attach a cycle recorder and plug into outlet. Verify power source is not overloaded with other appliances.
Compare test results with "Performance Data" table, see
"Component Testing" section.
Running time will vary according to design characteristics of the system and will be influenced by conditions listed below:
• Temperature control setting
• Room temperature
• Length of time and number of lid openings
• Quantity and temperature of food placed in freezer
Service Hints
Owner's Manual
If you find customer is not familiar with "Owner's
Manual", acquaint customer with manual.
Usage
Common types of abnormal usage that may lead to service calls include the following:
1. Excessive unfrozen food load:
• Amount of unfrozen food to be placed in freezer should not exceed approximately 3 pounds per cubic foot in 24 hours, unless otherwise noted.
• Recommend to customer that larger quantities of food be frozen commercially before placing in freezer.
• Larger unfrozen food loads may cause customer complaints of "continuous running" or may raise temperature of frozen food. Larger unfrozen food loads may also result in longer freezing times.
2. Excessive Lid Opening:
• Freezer is not designed to be operated as a refrigerator. Length of time and number of lid openings should be kept to minimum.
Compressor "On" And "Off" Periods
Variations in compressor cycles per hour are affected by factors such as usage, ambient conditions, electric power supply and others. Compressor off period is at least 8 minutes. Tripping on overload may occur.
Noise
Some noise, especially during starting and stopping of compressor, is normal. In some cases noise, described by customer as "gurgling," is experienced. This "gurgling" noise is caused by liquid entering evaporator.
Voids In Urethane Foam Insulation
• Some condensation occurs on outer casing of freezer, when humidity is 85% or higher, which is considered normal.
• If condensation occurs at lower humidity level or persistently causes dripping water, there may be a void in the foam insulation where condensation occurs. Theoretically, voids can occur in any part of the freezer insulation.
1. Diagnosing presence of a void: a. Freezer should be operating and food-liner temperature should be close to 0°F.
b. Disconnect power supply to freezer and wait 10 minutes. This will allow condenser and skin of outer casing to cool down to room temperature.
c. Move your palm around skin of outer casing, searching for cold spots.
• If a void exists, area will feel colder than neighboring area. To access that "cold spot" is a void, try to flex sheet metal with your thumb.
Metal over a void will be more flexible than metal backed with foam.
• If no void is found, observed condensation or dripping, which is caused by insulation void on the food-liner side of the foam insulation.
2. Action to be taken:
• If void is in an area which can be repaired in the field (bottom or back) using the "foam kit", proceed with the repair. If void is found in an area which is exposed to view, then freezer should be returned to source.
©2004 Maytag Services 16023585 39
Service Information
!
WARNING before attempting to service unless test procedures require power to be connected. When removing any wiring from terminals, replace on the same terminals. Ensure all ground wires are connected before certifying unit as repaired and/or operational.
To avoid risk of electrical shock, personal injury or death, always disconnect electrical power source to the freezer
Refrigeration System Complaints
Common occasions for customer requesting service are listed below with possible reasons and tests to diagnose problem before replacements are made.
1. Cabinet temperature does not come down: a. Refrigerant charge is low. Examine frost line at tail end of the evaporator.
b. Compressor is inoperative (see compressor sections).
c. Control has been turned to "OFF" position.
d. Freeze-up
2. Compressor will not start: a. Lack of power. Verify power availability at compressor terminals.
b. Starting relay has failed. Connecting starting relay contacts L & S for 1 second should result in a normal start. Replace starting relay.
c. Overload protector has failed in open position.
Replace overload.
d. One of compressor windings is open. Check winding resistances. Resistance between CDS and CDR should be less than 100 ohms.
e. Compressor is locked (seized). If voltage is normal, there is no failure in the relay protector or any connections leading to the compressor terminals, and the amperage drawn is high.
Compressor has failed.
3. Compressor overload thermostat is operating frequently but cabinet temperature has not risen noticeably.
a. Voltage under 10 VAC.
b. Voltage over 127 VAC.
c. Lid is being opened frequently so compressor
"OFF" time is too short for pressure equalization.
d. Installation condition is causing compressor to run hotter than usual (for example, lack of air circulation around freezer shell).
e. Overload thermostat has failed.
4. Continuous running: a. Freezer has been filled with unfrozen or warm food.
b. Room temperature exceeds recommended maximum.
c. Cabinet is placed near radiator or other heat source, such as strong sunlight.
d. Temperature control is incorrectly adjusted or has failed.
e. Refrigerant charge is low f. Freeze-up
5. Compressor runs too long:
• This is usually a statement of opinion by customer. For a normal storage temperature at
0°F, expected running times are shown in
"Performance Data" table, see "Component
Testing" section.
• Running times can vary substantially depending on usage and conditions.
6. Freeze-up:
Moisture freezing in the sealed system is extremely rare; however, it may be encountered when sealed system is opened for service.
a. Moisture freeze-up is indicated by continuous running and high cabinet temperatures. Use a suction pressure gauge to diagnose problem. As freezer pulls down, back pressure drops to a vacuum. By pulling freezer plug and warming cabinet until evaporate exceeds 0°C the ice will melt and cause a rapid rise in pressure. This can be duplicated any number of times.
b. Freeze-up can only be corrected by evacuating system with a vacuum pump, and by installing a new, oversized, high side drier.
NOTE: Effective July 1, 1992, it is responsibility of service technician to capture refrigerant for safe disposal.
c. In case of freeze-ups, the unit's current draw
(amperage) will usually be low, about 70 percent of serial plate.
40 16023585 ©2004 Maytag Services
Service Information
!
WARNING before attempting to service unless test procedures require power to be connected. When removing any wiring from terminals, replace on the same terminals. Ensure all ground wires are connected before certifying unit as repaired and/or operational.
To avoid risk of electrical shock, personal injury or death, always disconnect electrical power source to the freezer
Refrigerant Leaks
!
DANGER
Free oxygen will explode on contact with oil. Acetylene will explode spontaneously when put under pressure.
To prevent violent explosions that may result in serious injury or death to persons in or near the immediate vicinity, NEVER use oxygen or acetylene for pressure testing or cleanout of refrigeration systems.
Before attempting to locate a leak, study the diagrams showing the route of refrigeration tubing and serviceable joints.
NOTE: Urethane foam cells are filled with trapped gas and if cells are broken (by removing a piece of foam, etc.) a leak detector will indicate a strong leak. When foam cells are broken, liberated gas should be blown off surface or allow unit to stand for at least 5 minutes before testing.
Symptoms of refrigerant leaks
1. Frost-line, visible inside food-liner, does not extend to tail-end of evaporator. In properly refrigerated system frost-line, on the food-liner back wall of the chest freezer, will extend down to 5–6 inches from the foodliner bottom. In slow leaks, this frost-line gradually recedes upward.
When an internal refrigerant leak is suspected, recharge freezer with proper amount of refrigerant and mark end of the frost-line (nearest spot to the bottom) with a crayon. Leave freezer running
(sometimes for months) and observe mark periodically. If frost-line moves away from mark, a leak (external or internal) is certain.
2. Feeler bulb of thermostat, is located toward tail-end of evaporator. In case of shortage in refrigerant, tail-end of evaporator will not be refrigerated and thermostat will not cut out causing freezer to run continuously.
(This can be confused with a faulty thermostat.)
3. Although compressor is running continuously, foodliner temperature will rise.
4. Low suction pressures.
External Or Internal Leak
• "Internal leaks" are refrigerant leaks inside foam insulation. All other leaks are considered "external".
• Once presence of a leak has been determined (from symptoms described above), locate leak.
• First, test all joints in compressor compartment. Hold nozzle of detector on every joint for at least 1 minute.
If no leak can be found at these joints, check for internal leak.
Finding Internal Leak
Confirm existence of an internal leak by pressure testing.
NOTE: For this test, evaporator and condenser must be disconnected and individually pressure tested with dry air or dry nitrogen at pressures between
200–300 psi.
Leave the components under pressure for a minimum of
3 days. If after 3 days, pressure drop is more than 10 psig, at approximately same room temperature, presence of an internal leak can be assumed.
• Be sure there are no leaks in connections between pressurizing device and gauge or between gauge and cabinet. A leak at these joints could be misinterpreted as an internal leak.
• Apply soap solution to all joints and connections to check for leaks (bubbles).
• If pressure drop after 3 days is not more than 10 psig, there is no internal leak.
Pressure test described above will indicate:
• leaking condenser; or
• leaking evaporator; or
• no leak.
Condenser Leak (Internal)
If indications are that internal leak is in condenser, leak is considered to be nonrepairable. If unit is under warranty, contact factory for permission to replace unit.
Evaporator Leak (Internal)
If pressure test indicates leak in the evaporator, the leak could be:
• at the evaporator/suction line; or
• at the evaporator inlet joints, or
• at an unknown location.
Joint is located approximately 2–4 inches below breaker strip at back left corner. After breaker strip has been removed, carefully search for capillary by gradually removing foam insulation.
Evaporator inlet can be lifted above cabinet flange for examination and repair. After leak has been repaired, repack void with fiberglass insulation.
NOTE: Removal of breaker strip will destroy it. Replace breaker strip with new one.
If evaporator leak is at unknown location, contact factory for permission to replace unit if product is under warranty.
©2004 Maytag Services 16023585 41
Service Information
!
WARNING before attempting to service unless test procedures require power to be connected. When removing any wiring from terminals, replace on the same terminals. Ensure all ground wires are connected before certifying unit as repaired and/or operational.
To avoid risk of electrical shock, personal injury or death, always disconnect electrical power source to the freezer
Evacuation and Charging Procedures
!
WARNING
Sealed system on these freezer models use R134a refrigerant. If sealed system work on these models is required, used approved equipment and follow service procedures. See HFC134a Service Information section of this manual for service procedures.
!
CAUTION
To minimize contamination, exercise extreme care when servicing HFC134a sealed systems.
• No trace of other refrigerants is allowed in HFC134a systems. Chlorinated molecules in other refrigerants such as CFC12, etc. lead to capillary tube plugging.
• Ester oil is used in HFC134a systems. Do not use mineral oil. HFC134a and mineral oils cannot be mixed. If mineral oils are used in HFC134a systems, lubricant would not return to compressor and would cause early compressor failure. If significant amount of oil has been lost from compressor, replace oil rather than adding oil.
• Low-side leak repairs of HFC134a systems are different from those of CFC-12 systems. Ester oils used in
HFC134a systems are so hydroscopic that by the time an inadequate system performance is detected, oil will be saturated with moisture.
• CFC12 has much higher tolerance to system processing materials, such as drawing compounds, rust inhibitors, and cleaning compounds, than HFC134a. Such materials are not soluble in HFC134a systems. If materials were to be washed from system surfaces by ester oils, they could accumulate and eventually plug capillary tube.
• Care must be taken to minimize moisture from entering HFC134a system. Do not leave compressor or system open to atmosphere for more than 10 minutes. Excessive moisture in HFC134a system will react with compressor oil and generate acid.
• Compressor must always be replaced when performing low side leak repair.
• Drier filter must be replaced whenever seal system is opened.
Important: Unbrazing drier filter from tubing will drive moisture from desiccant and into system, causing acids to form. Do not unbraze filter drier from tubing. If CFC12 service drier was installed in HFC134a system, drier could overload due to excessive moisture.
• Clean, dry HFC134a compatible copper tubing must be used when replacing tubing.
• Avoid system contamination by using Towerdraw E610 evaporating oil, when flaring, swaging, or cutting refrigeration tubing.
42 16023585 ©2004 Maytag Services
Service Information
!
WARNING before attempting to service unless test procedures require power to be connected. When removing any wiring from terminals, replace on the same terminals. Ensure all ground wires are connected before certifying unit as repaired and/or operational.
To avoid risk of electrical shock, personal injury or death, always disconnect electrical power source to the freezer
HFC134a Service Information
HFC134a Refrigerant
HFC134a is alternative refrigerant for CFC12. HFC134a has an ozone depletion potential (ODP) factor of 0.0 and a global warming potential (GWP) factor of 0.27.
HFC134a is not flammable and has acceptable toxicity levels. HFC134a is not interchangeable with CFC12.
There are significant differences between HFC134a and
CFC12 which must be considered when handling and processing refrigeration system.
Health, Safety, and Handling
Health, safety and handling considerations for HFC134a are virtually no different than those for CFC12.
Comparison of CFC12 and HFC134a:
Properties/Characteristics
Ozone Depletion Potential (ODP)
Global Warming Potential (GPW)
Molecular weight
Boiling point at 1 atmosphere
CFC12
1.0*
HFC134a
0.0*
3.2*
121
0.27*
102
-22°F (-30°C) -15°F (-26°C)
Vapor pressure at 77°F (25°C)
Liquid density at 77°F (25°C)
80 psig
82 lb/ft3
82 psig
75 lb/ft3
Flammability No No
High-side system operating HFC134a approximately 3 psig
Pressure at 65°F (18°C) ambient higher than CFC12
Low-side system operating HFC134a approximately 2 psig
Pressure at 65°F (18°C) ambient lower than CFC12
* Compared to CFC 11 = 1
Health, Safety, and Handling
Allowable overall exposure limit
Vapor exposure to skin
Liquid exposure to skin
Vapor exposure to eye
Liquid exposure to eye
Above minimum exposure limit
Safety and handling
Spill management
Fire and explosion hazards
Storage conditions
Disposal procedures
CFC12
1,000 ppm
No effect
Can cause frostbite
Very slight irritant
Can cause frostbite
Can cause Asphyxiation,
Tachycardis, and Cardia
Arrhythmias
Wear appropriate skin and eye protection. Use with adequate ventilation.
Remove or extinguish ignition or combustion sources. Evacuate or ventilate area.
May decompose if contact with flames and heating elements.
Container may explode if heated due to resulting pressure rise.
Combustion products are toxic.
Procedures/rules for
CFC12 also apply for
HFC134a.
Recycle or reclaim
Same
Same
Same
Same
Same
Same
Same
Same
Same
Same
HFC134a
©2004 Maytag Services 16023585 43
Service Information
!
WARNING before attempting to service unless test procedures require power to be connected. When removing any wiring from terminals, replace on the same terminals. Ensure all ground wires are connected before certifying unit as repaired and/or operational.
To avoid risk of electrical shock, personal injury or death, always disconnect electrical power source to the freezer
Service Equipment
!
CAUTION
Service equipment for HFC134a systems must be used exclusively with HFC134a refrigerant. Do not use this equipment to service devices using other types of refrigerant (for example, CFC12 or CFC22 refrigerants).
Listed below are the tools and equipment needed for proper servicing of HFC134a systems.
NOTE: Once equipment is designated for HFC134a use, it must be exclusively use for HFC134a only. An * will identify the following equipment.
• * Evacuation pump Check with vacuum pump supplier to verify equipment is compatible for
HFC134a. Robinair, Model 15600, 2 stage, 170 liters
(6 cubic feet) per minute pump is recommended.
• * Four-way manifold gauge set with low loss quick couplers
• Leak detector
• * Charging cylinder
• * Line piercing saddle valve Seals must be
HFC134a and ester oil compatible. Line piercing valves may be used for diagnosis but are not suitable for evacuation or charging, due to minute holes pierced in tubing. Do not leave mechanical access valves on system. Valves eventually will leak.
Molecules of HFC134a are smaller than other refrigerants and will leak where other refrigerants would not.
• * Swaging tools
• * Flaring tools
• * Tubing cutter
• Flux
• Sil-Fos
• Silver solder
• * Oil for swaging and flaring
• * Copper tubing
• Dry nitrogen
99.5% minimum purity, with -40°C (-40°F) or lower dew point
• Crimp tool
• Tube bender
• Micron vacuum gauge
• * Process tube adaptor kit
• Heat trap paste
• * Appliance grade HFC134a
Drier Replacement
Before opening sealed system, recover HFC134a refrigerant for safe disposal.
Every time sealed HFC134a system is repaired, drier filter must be replaced. Cut drier out of system by completing the following steps. Do not unbraze drier filter. Applying heat to remove drier will allow moisture into system.
1. Score capillary tube close to drier and break.
2. Reform inlet tube to drier allowing enough space for large tube cutter.
3. Cut circumference of drier 1-1/4" (3.175 cm), below condenser inlet tube joint to drier.
4. Remove drier.
5. Unbraze remaining part of drier. Remove drier from system.
6. Discard drier in safe place. Do not leave drier with customer.
44 16023585 ©2004 Maytag Services
Service Information
!
WARNING before attempting to service unless test procedures require power to be connected. When removing any wiring from terminals, replace on the same terminals. Ensure all ground wires are connected before certifying unit as repaired and/or operational.
To avoid risk of electrical shock, personal injury or death, always disconnect electrical power source to the freezer
!
WARNING
To avoid death or severe personal injury, cut drier at correct location. Cutting drier at incorrect location will allow desiccant beads to scatter. Completely clean area of beads, if spilled.
12. Visually check all joints for leaks. Evacuate and recharge the system.
13.Reconnect wire leads to compressor terminals and test unit to make sure it is operating properly.
14. Pinch the process tube and cut off service valve.
Braze joint and test for leaks.
Replacement HFC134a Service Compressor
HFC134a service compressors are charged with ester oil and pressurized with dry nitrogen. Before replacement compressor is installed, pull out one rubber plug. A pop from pressure release should be heard. If a pop sound is not heard, do not use compressor. Positive pressure in compressor is vital to keep moisture out of ester oil. Do not leave compressor open to atmosphere for more than
10 minutes.
The holding charge assures the compressor is dry. A compressor, it is recommended that the tubes be cut close to the soldered joints where they are connected to the compressor tube. If the tubes are not long enough, it may be necessary to unsolder the joints to allow connections to the replacement compressor. When replacing compressor, proceed as follows:
1. Disconnect power cord from electrical outlet.
2. Install a service valve on process tube.
3. Connect a hose to service valve and capture charge.
4. Clean the tubing for about 3 inches (76 mm) at the points to be cut. Before cutting tube, be sure it will be long enough to reconnect to replacement compressor. If not, unbraze joints.
5. Disconnect wires from compressor terminals.
6. Remove retaining clips from compressor mounts. Lift compressor from mounting rails and transfer rubber grommets to replacement compressor.
7. Set replacement compressor into position and install retaining clips.
8. Remove all rubber plugs. Clean stubs of compressor and compare the size of tubing to stubs of replacement compressor. It may be necessary to swag copper tubing to make the joints.
9. Install a 6 inch (152 mm) copper tube to low side process tube on compressor. Add a service valve to end of this tube.
10.Connect all tubing. Apply flux to compressor stubs and braze all the joints. Flux must be wiped off after brazing.
11. Install a new drier.
Refrigerant Charge
Refrigerant charge in all capillary tube systems is critical and exact amount is required for proper performance.
Factory charges are shown on serial plate. Do not use refrigerant other than shown on serial plate.
Leak Testing
Undetected leaks lead to repeated service calls and eventually result in system contaminations, restrictions, and burned out compressors.
After recharging, sealed system must be thoroughly tested for leaks. If a very small leak is difficult to isolate, coat area with soap suds and observe. Bubbles will form in location of leak.
Evacuation and Charging
!
DANGER
Free oxygen will explode on contact with oil. Acetylene will explode spontaneously when put under pressure.
To prevent violent explosions that may result in serious injury or death to persons in or near the immediate vicinity, NEVER use oxygen or acetylene for pressure testing or cleanout of refrigeration systems.
!
WARNING
To avoid severe personal injury or death from fire keep system free from contamination due to presence of air. Follow instructions exactly.
!
WARNING
To reduce risk of fire, sealed refrigeration system must be air free. To reduce risk of air contamination follow evacuation procedures exactly.
©2004 Maytag Services 16023585 45
Service Information
!
WARNING before attempting to service unless test procedures require power to be connected. When removing any wiring from terminals, replace on the same terminals. Ensure all ground wires are connected before certifying unit as repaired and/or operational.
To avoid risk of electrical shock, personal injury or death, always disconnect electrical power source to the freezer
Thermistor
Vacuum Gauge
Low Side Gauge
High Side Gauge
E
Valve
D
Valve Drier/Process Tube
Compressor
Charging Hose
Compressor
Process
Tube
.6 cm Copper
Tubing
Vacuum Pump
C
B
A
Charging Hose
Evacuation and Charging
Typical Setup
Charging
Cylinder
F
Valve
Before opening system, evaporator coil must be at ambient temperature to minimize moisture infiltration into system.
NOTE: It is the responsibility of the service technician to capture refrigerant in system for safe disposal, before opening any refrigeration system.
1. After capturing refrigerant, replacing drier and making any repairs, evacuate system from high side through drier/process tube and low side through compressor process tube simultaneously. Evacuation should not be done through line piercing valve but through I.D.
opening of tubes.
2. With valves “C” and “F” closed to thermistor vacuum gauge and charging cylinder, open all other valves and start vacuum pump.
3. At approximately 77.66 cm (29") of vacuum, open valve “C” to thermistor vacuum gauge and take micron reading.
4. Continue evacuating system until thermistor vacuum gauge registers 600 microns.
5. At 600 microns close valve “A” to vacuum pump to allow micron reading in system to balance. Micron level will rise. If in 2 minutes, micron level stabilizes at
1000 microns or below, system is ready for charging.
• If micron rises above 1000 micron level and stabilizes, open valve “A” to vacuum pump and continue evacuating.
• If micron reading rises rapidly and does not stabilize, a leak still exists in system. Close valve
“A” to vacuum pump and “C” to thermistor vacuum gauge. Invert charging cylinder and open charging cylinder valve “F” to add partial charge for leak checking. With leak detector, check manifold connections and system for leaks. After locating leak, capture refrigerant charge, repair leak, and begin at step 1.
6. Once system is ready to charge, close valve “A”
(vacuum pump), “C” (thermistor vacuum gauge), and
“E” (low side manifold gauge).
7. Check serial plate for correct charge and set scale on dial-a-charge cylinder for corresponding HFC134a pressure reading.
NOTE: Do not use captured or recycled refrigerant in units. Captured or recycled refrigerant voids any compressor manufacture's warranty.
8. Open valve “F” to charging cylinder and let exact amount of refrigerant out of cylinder. Close valve.
Low side gauge pressure should rise shortly after opening charging cylinder valve as system pressure equalizes through capillary tube. If pressure does not equalize, a restriction typically exists at capillary/drier braze joint.
9. If no restriction exists, open valve “E” (low side manifold gauge) and pinch off high side drier process tube.
10.Start compressor and draw remaining refrigerant in charging hoses and manifold into compressor through compressor process tube. To check high side pinch-off drier process tube, close valve “D”
(high side gauge). If pinch-off is not leaking, high side pressure will not rise. If high side pressure gauge shows an increase, repeat high side pinch-off and open valve “D”. Repeat until high side pinch-off no longer leaks.
11. Pinch-off compressor process tube and remove charging hose. Braze stub closed while compressor is operating.
12.Unplug dehumidifier from electrical outlet. Remove charging hose and braze high side drier process tube closed.
46 16023585 ©2004 Maytag Services
Service Information
!
WARNING before attempting to service unless test procedures require power to be connected. When removing any wiring from terminals, replace on the same terminals. Ensure all ground wires are connected before certifying unit as repaired and/or operational.
To avoid risk of electrical shock, personal injury or death, always disconnect electrical power source to the freezer
Dehydrating Sealed Refrigeration System
It is a misconception that moisture in a sealed refrigerant system is harmless. Moisture in a sealed refrigerant system, when exposed to heat generated by the compressor and motor, reacts chemically with refrigerant and oil in the system and forms corrosive hydrochloric and hydrofluoric acids. These acids contribute to the breakdown of motor winding insulation and corrosion of compressor working parts, causing compressor failure.
In addition, sludge, a residue of the chemical reaction, coats all surfaces in the sealed system, and will eventually restrict refrigerant flow through the capillary tube.
To dehydrate the sealed system:
1. Perform the leak test.
2. Capture refrigerant in system.
NOTE: It is the responsibility of the service technician to capture refrigerant in system for safe disposal, before opening any refrigeration system.
3. Repair any leaks in system.
4. Evacuate system.
5. Recharge to specification with new refrigerant.
NOTE: Do not use captured or recycled refrigerant in units. Captured or recycled refrigerant voids any compressor manufacturers warranty.
30% silver, 38% copper, 32% zinc). Use with fluoride based flux. Recommended brazing temperature is approximately 1200°F.
• Steel to steel joints: SILVER SOLDER (see above).
• Brass to copper joints: SILVER SOLDER (see copper to steel connections).
• Brass to steel joints: SILVER SOLDER (see copper to steel connections).
Refrigerant Precautions
!
To avoid personal injury do not allow refrigerant to contact eyes or skin. Do not burn refrigerant.
!
WARNING
CAUTION
Do not use refrigerant other than that shown on unit serial number identification plate.
NOTE: All precautionary measures recommended by refrigerant manufacturers and suppliers apply and should be observed.
Brazing
!
CAUTION
Brazing requires high temperatures. Take all necessary precautions to protect against personal injury and property damage.
Open Lines
During any processing of refrigeration system, never leave lines open to the atmosphere. Open lines allow water vapor to enter system, making proper evacuation more difficult.
Satisfactory results require cleanliness, experience, and use of proper materials and equipment.
Connections to be brazed must be properly sized, free of rough edges, and clean.
Generally accepted brazing materials are:
• Copper to copper joints: SIL-FOS (alloy of 15% silver, 80% copper, and 5% phosphorous). Use without flux. Recommended brazing temperature is approximately 1400°F. DO NOT USE FOR COPPER
TO STEEL CONNECTION.
• Copper to steel joints: SILVER SOLDER (alloy of
©2004 Maytag Services 16023585 47
Service Information
!
WARNING before attempting to service unless test procedures require power to be connected. When removing any wiring from terminals, replace on the same terminals. Ensure all ground wires are connected before certifying unit as repaired and/or operational.
To avoid risk of electrical shock, personal injury or death, always disconnect electrical power source to the freezer
Line Piercing Valves
Line piercing valves may be used for diagnosis, but are not suitable for evacuating or charging due to the minute holes pierced in the tubing.
!
WARNING
Line piercing valve should not be left on the system, connection to tubing is not hermetically sealed and eventually a leak will occur.
has a positive pressure. Using it where a vacuum is present could pull moisture or soap bubbles into the system.
Brush liquid detergent over testing area and watch for bubbles. This may take a few minutes for a bubble to appear if leaks are extremely small.
After replacing a component always evacuate, add refrigerant, and test for leaks on all joints before recharging. Clean excess soldering flux from new joints before testing to prevent pinhole leaks at a later time.
Upright freezers which are insulated with foamed-in polyurethane foam have their condenser tubing embedded in this foamed insulation within the cabinet wall. Liner cannot be removed and there is no access to the tubing to removed, repaired, or replaced.
NOTE: Polyurethane insulation contains refrigerant
R–11/R141B/R22. Care must be taken when testing. Isolate the area as much as possible so that the leak detector will not falsely indicate a leak of R–11/R141B/R22 vapor.
If there is an undercharge of refrigerant and the system has not been recently opened, there is probably a leak in the system. First locate and repair the leak. Evacuate and recharge with the proper amount of refrigerant. Replace the dryer whenever a new charge of refrigerant is added.
NOTE: Effective July 1, 1992, before opening any refrigeration system it is the responsibility of the service technician to capture the refrigerant for safe disposal.
Presence of oil around a tubing joint usually indicates a leak. Always use a leak detector to determine if the joint is leaking.
Pressurize the system to a minimum of 75 PSIG, by running the compressor for high side testing. To pressurise the low side, allow entire system to warm up to room temperature.
If pressure is low enough a leak test will be impossible to perform. Install a service valve to compressor process tube and check pressure. Recover remaining refrigerant. Separate and pressurize high & low side independently, allowing unit to settle.Check gauges for pressure drop.
Leak detector can insolate larger leaks and generally locate small ones, but to actually pinpoint extremely small leaks in the high side, soap bubble solution will need to be performed.
NOTE: Use soap bubble solution only when the system
Altitude Adjustment
All models covered in this manual are equipped with a
Cutler Hammer temperature control. It has two adjustment screws, both of which must be turned to compensate for variance in altitude. Screw turns are very critical, use circular scale as a guide.
Cut-out screw
Cut-in screw
Temperature Control
Alititude
in feet
2,000
3,000
4,000
5,000
6,000
7,000
8,000
9,000
10,000
Counter Clockwise
turns
7 / 60
13 / 60
19 / 60
25 / 60
31 / 60
37 / 60
43 / 60
49 / 60
55 / 60
10
15
20
05
00
55
25
30
35
50
45
40
Altitude Correction Both “Cut-In” and
“Cut-Out” Screws Must Be Adjusted
This scale may be used as a guide for measuring degrees of rotation required for altitude correction. The arrows indicate direction of screw rotation 1/60 of a turn equals 6° of rotation.
Turn cut-in or cut-out screws clockwise to obtain colder operating temperatures.
48 16023585 ©2004 Maytag Services
Service Information
!
WARNING before attempting to service unless test procedures require power to be connected. When removing any wiring from terminals, replace on the same terminals. Ensure all ground wires are connected before certifying unit as repaired and/or operational.
To avoid risk of electrical shock, personal injury or death, always disconnect electrical power source to the freezer
Cabinet Shell
Cabinet shell is made of steel, with all seams welded and all points of stress adequately braced.
Refrigeration system condenser tubes are attached to the inner surfaces of the cabinet shell by means of spot welded clamps. Forming a shell-type condenser which provides quiet operation and efficient heat dissipation.
This method of dissipating the condenser heat eliminates the formation of condensation on exterior surfaces of the cabinet.
Steel base rails provide a platform on which the cabinet shell is mounted. Two adjustable levelling glides are inserted into the base rails, one at each front corner.
Door lock retainer and strike are also attached to the cabinet shell (if equipped).
Cabinet Liner (Food)
Cabinet liner is made of a tough, flexible, plastic or high impact polystyrene material and is secured to the cabinet shell with retaining clips.
Following components are attached to the cabinet liner by utilising special snap nuts, clips and other fasteners; interior light and switch, cold control assembly and cover, evaporator coil and cover (no-frost models), shelves and gate mounting hardware, and drain tube and grommet.
Once system components and cabinet liner have been assembled to the cabinet shell, polyurethane insulation is
“foamed in” to fill the void between the shell and liner.
NOTE: Cabinet (food) liner cannot be removed on the current models with foam insulation.
Drain System Refrigerated Shelf Models
On no-defrost models, drain grommet and sleeve are located in the center of drain trough which has been formed in the cabinet liner. During defrost cycle, water is carried through the drain hose and tube into the moisture pan which is located under the cabinet. Heat from the precooler condenser hastens the evaporation process.
Drain System
Freezer drain system consists of a drain grommet and sleeve at the liner and cabinet bottom, and a drain hose and tube that carries the defrost water.
NOTE: Refrigerated shelf models are equipped with a drain cap that must be removed before defrosting and replaced securely afterwards.
On refrigerated shelf models, defrost water is carried through the front face plate of the cabinet where it can be collected into a container for disposal.
Drain System No-Defrost Models
Drain tube grommets should never need replacing unless it has deteriorated.
If drain system becomes clogged, push a length of plastic cloths line completely through and flush with warm water.
©2004 Maytag Services 16023585 49
Wiring Diagram and Schematic
!
WARNING
To avoid risk of electrical shock, personal injury, or death, disconnect power to freezer before servicing, unless testing requires it. Wires removed during disassembly must be replaced on proper terminals to insure correct grounding and polarization.
!
CAUTION
High Voltage
To 115 VAC plug
Light Plate (ground)
Black
Light
Light Switch
White
Black
Green
Control
Red
Black
Black
Black
Light switch
Control
Overload protector
Red
Black
C
Compressor
R
S
Interior
light
White
PTC relay
Black
Service Cord
50
Capacitor
Ground
Compressor
Red
White
Red
Black
Green
No Interior Light (Optional)
Ground schematic
1 - Outer case
2 - Compressor
3 - Control
4 - Light plate
Manual Defrost Models
AFU1202BW
AFU1505BW
AQU1525AEW
MQU1554AEW
MQU1556AEW
AFU1705BW
AFU2005BW
MQU2056ARW
MQU2057AEW
16023585 ©2004 Maytag Services
Wiring Diagram and Schematic
!
WARNING
To avoid risk of electrical shock, personal injury, or death, disconnect power to freezer before servicing, unless testing requires it. Wires removed during disassembly must be replaced on proper terminals to insure correct grounding and polarization.
!
BLACK
BLACK
CAUTION
High Voltage
1
SCHEMATIC
BLACK
DOOR
SWITCH
BLUE
DEFROST
TIMER
4 2
YELLOW
LAMP- REFRIGERATOR CABINET
ORANGE
34.6/37.5 OHMS
DEFROST
HEATER
DEFROST
THERMOSTAT
4000
OHMS
WHITE
3
112.4 OHMS
RED WHITE
WHITE
WHITE
OVERLOAD
PROTECTOR
C
COMPRESSOR
EVAPORATOR
FAN MOTOR
RELAY
RUN
START
R
S
3 2
WHITE
CAPACITOR
BLACK
LH/LV
POWER
SUPPLY
LN IDENTIFIED CONDUCTOR
GREEN
Control
3
Light Plate
4
GROUND
1 - Outer Case
2 - Compressor
3 - Control
4 - Light Plate
5 - Fan Motor
6- Coil Cover
Fan Motor
5
Compressor
1 2
Outer Case
Coil Cover
6
AFU1567BW
Frost Free Models
AFU1767BW AFU2067BW
©2004 Maytag Services 16023585 51
advertisement
* Your assessment is very important for improving the workof artificial intelligence, which forms the content of this project
Related manuals
advertisement
Table of contents
- 2 Important Information
- 4 Model Identification
- 5 Unpacking
- 5 General
- 5 Location
- 5 Electrical Connection
- 6 Door Handle
- 6 Leveling
- 6 Test After Installation
- 7 Electrical Requirements
- 7 Proper Disposal of your Freezer
- 7 Model Identification
- 8 Setting Controls
- 8 Temperature Control
- 9 Features
- 9 Reversible Rack (some models)
- 9 Freezing Guide
- 10 General
- 10 Adhesives
- 10 Door Gaskets
- 10 Odor Removal
- 11 Defrosting
- 11 Light Bulb (some models)
- 12 Energy Tips
- 12 Vacation Tips
- 12 Normal Operating Sounds
- 12 Before Calling For Service
- 13 Operating Sounds
- 14 Refrigeration System Test Procedures
- 15 Testing Main Condenser
- 16 Testing for Leaks
- 16 Electrical System
- 16 Compressor Electrical Tests
- 16 Testing Compressor Direct
- 17 Capacitor
- 17 Overload Protector
- 17 Testing Overload Protector
- 18 PTC Relay
- 18 Testing PTC Relay
- 18 Interior Light and Switch
- 18 Checking Control Operation
- 19 Temperature Control
- 19 Defrost Timer
- 20 Checking Timer
- 20 No-Defrosting Models
- 21 Freezer Fan No-Defrosting Models
- 21 Testing Freezer Fan Motor
- 22 Performance Data
- 23 Troubleshooting
- 26 Replacing Drier
- 26 Replacing Compressor
- 27 Refrigerated Shelf Model
- 28 No-Defrosting Models
- 29 Refrigerated Shelf Models
- 30 Replacing Freezer Coil No-Defrosting Models
- 31 Replacing Light Switch
- 31 Replacing Control
- 32 Replacing Heater
- 32 Replacing Freezer Fan Motor
- 33 Cabinet Door Assembly
- 34 Door Handle
- 34 Door Lock Assembly
- 35 Removing Door Lock Assembly
- 35 Cabinet Door Alignment
- 35 Checking Gasket Seal
- 35 Improving Gasket Seal
- 35 Hinge Adjustments
- 36 Cabinet Assembly
- 37 System Operation
- 38 Checking Operating Pressures
- 39 Operational Testing
- 39 Service Hints
- 40 Refrigeration System Complaints
- 41 Refrigerant Leaks
- 42 Evacuation and Charging Procedures
- 43 HFC134a Service Information
- 43 Health, Safety, and Handling
- 44 Service Equipment
- 44 Drier Replacement
- 45 Replacement HFC134a Service Compressor
- 45 Refrigerant Charge
- 45 Leak Testing
- 45 Evacuation and Charging
- 47 Dehydrating Sealed Refrigeration System
- 47 Brazing
- 47 Refrigerant Precautions
- 47 Open Lines
- 48 Line Piercing Valves
- 48 Altitude Adjustment
- 49 Cabinet Shell
- 49 Cabinet Liner (Food)
- 49 Drain System
- 50 Wiring Diagram and Schematic