advertisement
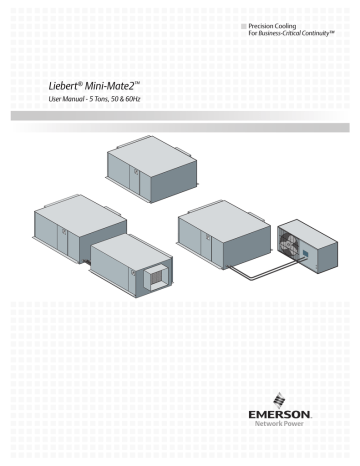
System Operation, Testing and Maintenance
Replacing the Humidifier Canister
!
CAUTION
Risk of contact with extremely hot surfaces. Can cause injury.
Canister and steam hose may be hot. Do not attempt to replace parts until the humidifier has cooled down to a temperature that is safe for human contact. Use extreme caution and wear thermally insulated gloves and arm protection when replacing the humidifier canister.
The proper procedure to replace the humidifier canister is:
1. Turn off the humidifier by lowering the humidity setpoint below the ambient humidity level.
Record the original setpoint.
2. Place the RUN/DRAIN switch in the DRAIN position to drain the water from the canister.
3. Return the RUN/DRAIN switch to the RUN position after the canister has drained.
4. Turn OFF the power at the main unit.
5. Remove the cover from the humidifier cabinet.
6. Locate the power wires to the steam canister. They are connected to the canister with 1/4" quick connects. Make note of the wiring configuration before removing any wires. Refer to schematic on unit. Slide the rubber boot back to expose the connections. Remove the two (2) power wires and the canister-full wire. Do not loosen the screws that secure the electrodes.
7. Loosen the steam outlet hose clamps and slide the steam hose away from the canister fitting.
Release the canister clamp along the base of the canister.
8. Remove the canister.
9. Reverse previous steps to re-assemble humidifier, paying special attention to the following:
• When replacing the wiring, connect the red wire from terminal #1 on the interface to the red tip terminal on the canister. Reconnect the power wires as before (#2 on the left and #1 on the right)
• When replacing the canister, always check the fill and drain solenoids for proper operation.
9.3.4 Humidifier Circuit Board Adjustments
!
WARNING
Risk of electric shock. Can cause injury or death.
Open all local and remote electric power disconnect switches before working on the humidifier printed circuit board.
Verify that electric power is Off with a voltmeter prior to the procedure.
The humidifier control board governs humidifier operation. There are three potentiometers mounted on the board and can be used to adjust for extreme water conductivity conditions.
POT2 controls the amperage at which the drain will energize and is clearly marked in percentages.
This adjustment is factory-set at 85%, which indicates that the unit will drain when the amperage falls off to 85% of the capacity set point. Raising the value increases the frequency of drain cycles.
Lowering the value decreases the frequency of drain cycles.
The frequency should be increased for highly conductive water and decreased for less conductive water. If adjustment is necessary and a change of three to four percent in either direction does not permit normal operation of the unit, consult your Liebert supplier.
The POT1 controls the duration of the drain cycle. This adjustment is factory-set at 60 seconds
(1 VDC) and should not be readjusted without consulting your Liebert supplier.
The DIP switch settings are used to set the capacity of the humidifier. If the humidifier is replaced in the field the DIP switches should be set to the required settings described below.
Table 24 Humidifier control board DIP switch settings
Voltage SW1 SW2 SW3 SW4 Amps
208
240
380/415
460
575
On
Off
Off
On
On
On
On
Off
On
On
On
On
Off
Off
Off
Off
On Off
Off Off
8.9
8.5
5.2
4.5
3.4
Liebert
®
Mini-Mate2
™
62
Maintenance Inspection Checklist
10.0 M
AINTENANCE
I
NSPECTION
C
HECKLIST
Liebert Mini-Mate2
Date:____________________________________
Model #:_________________________________
Prepared By:____________________________________
Serial Number:__________________________________
NOTE
Reheat element sheaths and fins are manufactured with stainless steel. Regular inspections are necessary to assure proper cleanliness of the reheating element. Should inspection reveal corrosion particles on the reheating element or adjoining surfaces (including ducts and plenums), appropriate cleaning should be performed. Periodic reheating element replacement may be required to meet specific application requirements.
Monthly
Filters
___ 1. Check for restricted airflow
___ 2. Check for filter
___ 3. Wipe section clean
Fan Section
___ 1. Impellers free of debris and move freely
___ 2. Bearings in good condition
___ 3. Check belt tension and condition
Semiannually
Compressor Section
___ 1. Signs of oil leaks
___ 2. Vibration isolation
Refrigeration Cycle
___ 1. Suction pressure
___ 2. Head pressure
___ 3. Superheat
___ 4. Evaporator coil clean
___ 5. Insulation intact
Air-Cooled Condensing Unit (if applicable)
___ 1. Condenser coil clean
___ 2. Motor mount tight
___ 3. Refrigerant lines properly supported
Humidifier
___ 1. Check canister for mineral deposits
___ 2. Check condition of electrodes
___ 3. All hoses and fittings tight
___ 4. Check water make-up valve for leaks
Drain lines
___ 1. Check for obstructions and sediment buildup.
___ 2. Check for damage and/or corrosion.
___ 3. Check for leaks
Flood Back Head Pressure Control
___ 1. Check refrigerant level
Water- or Glycol-Cooled Condensing Unit
___ 1. Water valve adjustment
___ 2. Water flow
___ 3. Water leaks
Glycol Pump (if applicable)
___ 1. Glycol leaks
___ 2. Pump operation
___ 3. Glycol solution
___ 4. pH level
Electric Panel
___ 1. Check electrical connections
___ 2. Operational sequence
Electric Reheat
1. Check element for corrosion
Signature:________________________________________________________________
Make photocopies of this form for your records
63 Liebert
®
Mini-Mate2
™
Troubleshooting
11.0 T
ROUBLESHOOTING
Table 25 Troubleshooting
Symptom
Unit will not start
No cooling
Compressor high head pressure
Humidifier does not operate
Reheat will not operate
Possible Cause Check Or Remedy
No power to unit
Control voltage circuit breaker (at transformer) open
Float switch relay closed because of high water in the condensate pan
Jumper not in place
Check voltage at input terminal block.
Locate short and reset circuit breaker.
Cooling not displayed at the control panel
Adjust TEMP control set point and sensitivity to require cooling.
Short cycle prevention control
Compressor contactor not pulling in
Control software delays compressor 3 minutes cooling, from stop to start
Check for 24 VAC ± 2 VAC at terminals P4-8 and P4-4. If voltage, check contactor. If no voltage at P4-8 and P4-4, check at terminals P2-3 and P2-8. If voltage, check freeze stat.
Compressor high head pressure See below for cause.
Plugged filter/dryer
Low refrigerant charge
Has rubber band been removed from float switch? Check drain and line. Access through left panel. Power must be cycled at the disconnect to reset.
Check terminal TB1-4 and TB1-5 for jumper or N/C contact.
Check pins 1-8 and 1-9 for jumper or N/C high temperature sensor contact. Check pins 5-4 and 5-5 for jumper or N/C smoke sensor contact.
Replace filter/dryer
Check pressure gauges. At low ambient temperatures, proper refrigerant charge is very important on units with Lee-Temp receivers.
Insufficient air flow across condenser coil
Water/Glycol Cooled only: No fluid flowing through condenser
Condenser fan not operating
DIP switch not set to enable humidifier option
“HUMIDIFY” not displayed at control panel
Remove debris from coil and air inlets.
Check fluid supply to regulating valve. Adjust valve if necessary.
Check fan operation.
See DIP switch settings Table 24.
Defective board
Failed humidity sensor
No water flow
Increase humidity control humidification. set point and sensitivity to require
Check voltage at P3-1 and P1-9 on interface board for 24 VAC
± 2 VAC. If no voltage, check wiring and/or replace board. Check wiring from control panel to board.
Humidity display will indicate dashes. Check wiring from temperature/humidity board to the control board and from the wall box to the control board. Replace wallbox or temperature/humidity circuit board (if remote).
Make sure switch is in Run position. Check humidifier water supply (including filter screen) and check nylon overflow line if canister is full.
Check fill valve screen opening and capillary tube for obstructions. Check water supply pressure (minimum 10 PSIG).
Canister fill rate is not keeping up with the steam output
DIP switch not set to enable reheat option
HEAT not displayed at the control panel
See DIP switch settings Table 24.
Increase temperature set point to require heating.
Reheat safety open, defective reheat contact or defective board
Element is burned out
Check voltage at P2-1 and P1-9 on interface board for 24 VAC ±
2 VAC. If voltage, check reheat contactor and reheat safety. If no voltage, check wiring and/or replace board.
Turn off power. Check element continuity with an Ohmmeter.
Liebert
®
Mini-Mate2
™
64
Troubleshooting
Table 25 Troubleshooting
Symptom
Cooling cycle too short
Possible Cause Check Or Remedy
Sensor response delay too short
Increase sensor response delay. See 6.11 - Calibrate Sensors.
Display freezes and control pads do not respond
Static discharge
During period of low humidity, static electricity can cause the control program to freeze or display incorrect information.
Although this is unlikely, the control can be reset by cycling power from the disconnect switch.
Condensate pump does not operate
Open or short circuit in wiring Find open or short circuit and repair power to pump.
Continuous
Cooling
Failed temperature sensor
Temperature display will indicate dashes. Check wiring from temperature/humidity board (remote sensors) to the control board or from control board to wallbox. Replace temperature/humidity circuit board (remote sensors) or wallbox.
Continuous
Heating
Dehumidification
Humidification
Shorted wiring or failed control board
Check wiring and/or replace control board.
Display Problem Incorrect wiring
Review 5.4.4 - Electrical Connections. Verify VDC between 5
to 6 Volts at TB-3 Pin 1 (Ground) and TB-3 Pin 2 of the control board and wall box. If the transmit lines (TB-3 Pin 3 & 4) are not connected, only the POWER LED will be lit. It will flash once every 10-12 sec. If T- is connected, but not T+, TX1 will flash approximately every 2-3 sec. And the POWER LED will flash once every 10-12 sec. If T+ and T- are reversed, the POWER
LED and RX1 Will be lit and flash every 10-12 sec.
NOTE: Erratic operation of the unit could occur. If no LED is lit, there is no power or the +5VDC polarity is reversed. If any of these conditions occur, remove power from the evaporator using the disconnect switch, and correct wiring from the control board to the wall box.
NOTE: It may take up to 20 seconds for the display to appear on the wall box LCD after power is applied.
65 Liebert
®
Mini-Mate2
™
Ensuring The High Availability
Of Mission-Critical Data And Applications.
Emerson Network Power, a business of Emerson (NYSE:EMR), is the global leader in enabling Business-Critical Continuity
™
from grid to chip for telecommunication networks, data centers, health care and industrial facilities. Emerson Network Power provides innovative solutions and expertise in areas including
AC and DC power and precision cooling systems, embedded computing and power, integrated racks and enclosures, power switching and controls, infrastructure management, and connectivity. All solutions are supported globally by local
Emerson Network Power service technicians. Liebert AC power, precision cooling and monitoring products and services from Emerson Network Power deliver Efficiency Without
Compromise
™
by helping customers optimize their data center
infrastructure to reduce costs and deliver high availability.
While every precaution has been taken to ensure the accuracy and completeness of this literature, Liebert Corporation assumes no responsibility and disclaims all liability for damages resulting from use of this information or for any errors or omissions.
© 2009 Liebert Corporation
All rights reserved throughout the world. Specifications subject to change without notice.
® Liebert is a registered trademark of Liebert Corporation.
All names referred to are trademarks or registered trademarks of their respective owners.
SL-10532_REV3_02-13
Emerson Network Power.
The global leader in enabling Business-Critical Continuity ™
AC Power
Connectivity
DC Power
Embedded Computing
Embedded Power
Infrastructure Management & Monitoring
Outside Plant
Power Switching & Controls
Precision Cooling
Technical Support / Service
Web Site www.liebert.com
Monitoring [email protected]
800-222-5877
Outside North America: +00800 1155 4499
Single-Phase UPS & Server Cabinets [email protected]
800-222-5877
Outside North America: +00800 1155 4499
Three-Phase UPS & Power Systems
800-543-2378
Outside North America: 614-841-6598
Environmental Systems
800-543-2778
Outside the United States: 614-888-0246
Locations
United States
1050 Dearborn Drive
P.O. Box 29186
Columbus, OH 43229
Europe
Via Leonardo Da Vinci 8
Zona Industriale Tognana
35028 Piove Di Sacco (PD) Italy
+39 049 9719 111
Fax: +39 049 5841 257
Asia
29/F, The Orient Square Building
F. Ortigas Jr. Road, Ortigas Center
Pasig City 1605
Philippines
+63 2 687 6615
Fax: +63 2 730 9572
EmersonNetworkPower.com
Racks & Integrated Cabinets
Services
Surge Protection
Emerson, Business-Critical Continuity, Emerson Network Power and the Emerson Network Power logo are trademarks of Emerson Electric Co. or one of its affiliated companies.
©2009 Emerson Electric Co.
advertisement
Related manuals
advertisement
Table of contents
- 21 Figure 8 Air-cooled systems
- 22 Figure 9 Water/glycol cooled systems
- 22 Figure 10 Chilled water systems
- 23 Filter Box
- 24 Connections for Ducted Systems
- 24 Table 7 Evaporator external static pressure
- 24 Drain Line
- 24 Humidifier Water Supply Line
- 25 Table 8 Recommended refrigerant line sizes
- 25 Table 9 Equivalent lengths for various pipe fittings, ft (m)
- 26 Figure 11 Refrigerant piping diagram
- 26 Table 10 Pipe length and condenser elevation relative to evaporator
- 27 Total refrigerant = Units and Lines*
- 27 Table 11 Refrigerant charge
- 27 Table 12 Line charges - refrigerant per 100 ft. (30m) of Type L copper tube
- 27 Quick Connect Fittings
- 27 Table 13 Refrigerant quick connect sizes and torque
- 28 Figure 12 Evaporator unit dimensional data
- 29 Figure 13 Threaded rod and hardware kit installation
- 30 Power Connections
- 30 Control Connections
- 31 Figure 14 Evaporator unit electrical connections
- 32 Figure 15 Close coupled installation
- 33 Power Connections
- 33 Control Connections
- 33 General Considerations
- 33 Considerations for Specific Applications
- 34 Figure 16 Indoor air-cooled centrifugal condensing unit dimensions and pipe connections
- 35 Figure 17 Indoor air-cooled centrifugal condenser electrical connections
- 36 Figure 18 System piping with indoor or outdoor air-cooled condensing unit
- 37 Figure 19 Dimensions—Air-cooled systems, standard ambient outdoor condensing module
- 37 Table 14 Weights for standard ambient outdoor condensing modules, air-cooled systems
- 38 Figure 20 Dimensions—Air-cooled systems, high ambient and Quiet-Line condensing module
- 38 Table 15 Net weight, high ambient and Quiet-Line condensing modules, air-cooled systems
- 38 Power Connections
- 38 Control Connections
- 39 Control Connections
- 39 Water/Glycol Piping Considerations
- 39 Condensing Unit Fluid Requirements
- 39 Regulating Valve
- 40 Figure 21 Indoor water/glycol condensing unit dimensional data
- 41 Figure 22 Indoor water/glycol condensing unit electrical field connections
- 42 Figure 23 System piping with indoor water/glycol cooled condensing unit
- 43 Figure 24 Optional free-cooling coil (3-way valve) on water/glycol units
- 43 Figure 25 Optional hot water reheat (two-way valve)
- 49 Table 18 Setup functions, default values and allowable ranges
- 52 Table 20 Equipment switch settings (unit control board)
- 52 Table 21 Switch settings (wall box board)
- 54 Figure 27 Control menu
- 55 Figure 28 Control board—inside evaporator
- 55 Figure 29 Wall box board
- 56 Table 22 Cooling and dehumidification load response of hot gas bypass
- 56 Electric Heat or Hot Water
- 56 SCR Electric Reheat
- 59 Air-Cooled Systems
- 59 Water/Glycol/ Systems
- 62 Air Distribution
- 62 Suction Pressure
- 63 Discharge Pressure
- 63 Table 23 Typical discharge pressure
- 63 Thermostatic Expansion Valve
- 63 Air-Cooled Condensing Units
- 63 Coaxial Condensers (Water/Glycol-Cooled Condensing Units)
- 63 Regulating Valves (Water/Glycol Condensing Units)
- 63 Glycol Solution Maintenance
- 64 Hot Gas Bypass
- 64 Figure 30 Hot gas bypass
- 65 Mechanical Failure
- 66 Replace a Failed Compressor
- 68 Replacing the Humidifier Canister
- 68 Table 24 Humidifier control board DIP switch settings