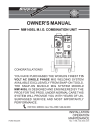
advertisement
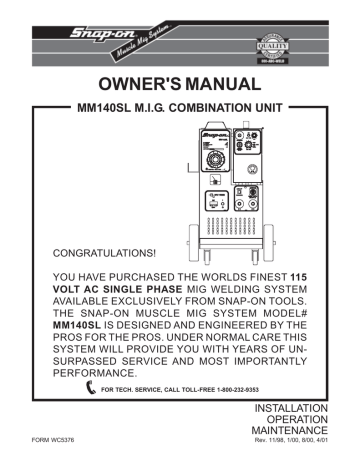
BURN BACK
OPERATING HINTS
In the event the welding wire burns back into the contact tip:
1. Remove the nozzle from the torch.
2. Unscrew the contact tip from the gas diffuser using a pair of pliers as the tip will be very hot.
3. Free the wire from the contact tip and clean the end of the tip so the new wire will slide smoothly through the hole. DO
NOT use a drill or reamer to clean the hole as they will enlarge it and cause an erratic arc. Replace the contact tip if it is badly damaged.
4. Install the contact tip in the torch and tighten it firmly with an appropriate wrench.
5. Reinstall the torch nozzle.
6. If the wire continues to burn back, check for erratic wire feed, or speed up the wire by increasing the WIRE SPEED control setting or reducing the
VOLTAGE control setting.
SPATTER
Before beginning to weld and periodically during welding, the torch nozzle must be removed and the spatter (small globules of melted metal) cleared from the inside of the nozzle and the outside of the contact tip and the gas diffuser.
Spatter buildup between the contact tip and the nozzle can cause a short circuit and consequently, failure of the torch or welding machine.
The frequent use of anti-spatter spray will help prevent the adherence of spatter to the torch components.
NOTE
DO NOT use any anti-spatter spray when welding aluminum or stainless steel.
Restricted gas flow, holding the torch too far from the work piece, and the use of CO2 gas rather than
75% Argon - 25% CO2 will increase the spatter levels.
MAINTENANCE
To ensure that this equipment maintains its operating efficiency, the following maintenance schedule and procedures are recommended. These routines should be performed regularly by the operator.
REGULARLY - Usage and shop conditions determine frequency.
1. Remove and clean the torch nozzle and contact tip. The use of anti-spatter spray will reduce the adherence of spatter and makes its removal easier.
2. Blow out the torch liner prior to the installation of each new spool of wire. The contact tip and gas diffuser must be removed, but it is not necessary to remove the liner.
3. If the torch cable assembly is bent severely, a kink may develop in the steel liner. This can cause wire feeding problems so a new liner should be installed.
WEEKLY
Remove dirt and dust from the wire feed compartment. Use low pressure dry compressed air.
(continued on following page)
Snap-on Tools Corporation Kenosha, WI 53141-1410 13
MAINTENANCE (Cont.)
2. Remove dirt and metal deposits from the grooves in the feed roll. If the grooves are badly worn, the feed roll should be replaced. If the pressure roll does not turn freely, it should be replaced.
3. Check all gas fittings for leaks. Tighten or repair as required.
EVERY SIX MONTHS
1. Disconnect the welder from its main power supply.
2. Remove the machine’s side panels.
3. Using low pressure dry compressed air, remove dust and dirt from all components.
4. Check for loose or frayed wiring. Particularly check welding current wire connections.
5. Replace torch liner if necessary.
RECOMMENDED
CUSTOMER SPARE PARTS
The Snap-on Tools MM140SL is a machine of proven design and reliability. Following is a list of consumable items recommended as spare parts for this unit.
contact tips ....... M3-T30, etc.
gas nozzles ............. M3T-N50 nozzle insulators ......... M3T-B gas diffusers ............. M3T-D steel liner(.020-.030) .. M103L-B steel liner(.035-.045) .. M104L-N
In the event of the failure of any part of this equipment, contact your Snap-On Tools representative for replacement parts and service.
When ordering parts from Snap-On
Tools Corporation, order numbers should be preceded by "CKS".
WARNING
DO NOT lift the unit when a gas cylinder is installed or attached.
DO NOT weld on any item that has a common electrical ground.
DO NOT operate the unit with the side panels removed.
Overheating will occur.
DO NOT weld upon the case of the welding machine.
ONLY a qualified electrician should perform work inside the welding machine.
ALWAYS wear protective clothing, leather gloves and a full cover welding hood while welding.
DO NOT weld in a closed in area. Proper ventilation is a necessity, or a fresh air supplied hood should be worn.
W H E N w e l d i n g n e a r c o m b u s t i b l e s , a h e l p e r o r
"watcher" should stand by with a fire extinguisher or other fire protective device.
NEVER weld on a closed vessel or one that has contained combustibles.
IF IN DOUBT - DON’T DO IT!
BE SAFE - DON’T BE SORRY!
14 Snap-on Tools Corporation Kenosha, WI 53141-1410
advertisement
Related manuals
advertisement
Table of contents
- 3 ELECTRICAL SUPPLY REQUIREMENTS
- 4 INTRODUCTION
- 5 DESCRIPTION, SPECIFICATIONS
- 6 CHECK LIST (CONTENTS)
- 6 INSTALLATION
- 10 OPERATION
- 15 MAINTENANCE
- 17 TROUBLE SHOOTING CHART
- 22 CONNECTING FLEX-TIG OR SPOOL GUN
- 23 LINER INSTALLATION
- 24 PARTS BREAKDOWN - MIG TORCH
- 26 OPTIONS - FLEX-TIG OR SPOOL GUN
- 27 PARAMETER CHARTS