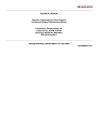
advertisement
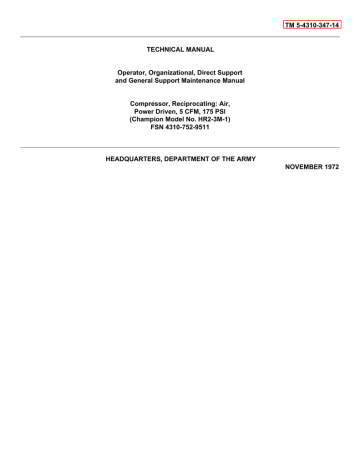
SECTION XI
REPAIR AND OVERHAUL INSTRUCTIONS
AIR COMPRESSOR ASSEMBLY AND ELECTRIC MOTOR
COMPRESSOR REPAIR AND REPLACEMENT STANDARDS
Desired Clearance
Min.
Cylinders
Bore low - pressure
Bore high - pressure
Out of round .-
Taper
Crankshaft
Journal rod) die-
Taper
Out-of-round
End play
Pistons end Pins
1.370
Piston, low-pressure 4.619
Piston, high-pressure2.4965
Pin, low-pressure
Pin, high-pressure
Bearings, Connecting Rod
Bearing, id
Bearing, side clearance
4.6245
2.4995
2.125
2.125
.8125
Manufacturer’s dimensions and tolerances in inches
Max.
4.6255
2.5005
1.3765
4.620
2.4975
2.135
2.135
8130
0.010
A. PISTONS, PISTON RINGS, CONNECTING RODS,
AND CYLINDER BLOCK
1.
Removal and Dissembly.
a.
Remove the compressor assembly Section VIII,
C1.
b.
Refer to figure 16 and disassemble tube
assemblies, cooler tubes, manifolds and air cleaner a shown.
c.
Refer to figure 17 and remove hand hole plate.
d.
Refer to figure 18 and remove connecting rod
bearing caps
Min.
Max.
CAUTION: Mark the connecting rod from which the caps were removed, and reassemble caps on the same rod.
Do not inter-mix the connecting rods and cap.
e.
f.
Disassemble cylinder block from crankcase as
Dissemble connecting rods, pistons and rings as
NOTE: Mark connecting rod and piston to assure correct relationship at reassembly.
NOTE: Do not remove the connecting rod bushings unless inspection reveal them defective.
Maximum allowable wear amd clearance
0.004
0.002
0.001
0.001
0.001
0.005
0.000
0.003
0.0015
0.0001
0.0001
0.001
0.017
0.002
0.005
0.0035
0.0005
0.0005
0.007
0.006
0.003
2.
Cleaning, Inspection and Repair.
a.
Clean all parts with an approved cleaning solvent and dry thoroughly.
b.
Inspect the cylinder block for broken cooling fins and cracks. Inspect the cylinder bore for wear, scoring, pitting, or other damage. Replace the block if defective.
c.
Measure the clearance of the piston pin to the piston pin bushing. Check for proper fit. Aline or replace, connecting rods, if necessary.
d.
Place the piston rings in the cylinder bore with the piston ring square in the cylinder bore about
1/2 inch from the top.
e.
If the ring gap is less than the specified width, file across but ends of the rings to increase the gap to, the required tolerance. If the ring gap is greater than required, replace the entire set of rings.
f.
Measure the ring groove in the piston for wear.
Replace pistons if necessary.
3. Reassembly and Installation.
a. Refer to figures 16, 17, and 18 and re assemble.
and install the pistons, piston rings, connecting rods and cylinder block taking the following precautions:
1.
If new connecting rod bushings are to be installed, and are not prefit, ream the bushings.
2.
When installing piston rings expand them carefully and sufficiently to allow the ring to
17
1. Crankcase
2. Plate, hand hole
3. Gasket, hand hole plate
4. Screw, cap
S. Plug, pipe
6. Seal, oil
7. Plug, pip:
8. Nipple, pipe
9. Cap, pipe
10. Gauge,, oil level
11. Flywheel
12. Key
13: Bolt, machine
14. Nut, hex
15. Gasket set
16. Fitting, compression
17. Housing governor
18. Plate, baffle
19. Gasket, governor cover
20. Spindle, governor
21. Pin, spring
22. Washer, spring lock
23. Screw, cap
24. Washer, flat
25. Spring governor main
26. Sleeve, spring
27. Screw, cap
28. Weight, governor
29. Cover, governor housing
30. Kit, release valve assembly
31. Plunger, release valve
32. Ball, release valve
33. Spring, release valve
34. Body, release valve
35. Elbow, 900
36. Screw, machine
S37. Muffler assembly, unloader
38. Body, unloader muffler
39. Felt
40. Screen
41. Gasket, cylinder flange
42. Cylinder
43. Screw, cap
Figure 17. Crank Case and unloader assembly, exploded view.
18
1. Kit connecting rod assembly L.P.
2. Kit connecting rod assembly H.P.
3. Rod, connecting w/bolt L.P.
4. Rod, connecting w/bolt H.P.
5. Bearing, piston pin
6. Bolt, connecting rod
7. Dipper, oil H.P.
8. Dipper, oil L.P.
9. Kit, piston assembly H.P.
10. Kit, piston assembly L.P.
11. Ring, piston pin retaining
12. Pin, piston
13. Piston, high pressure
14. Ring set, H.P. piston
15. Piston, low pressure
16. Ring set, L.P. piston
17. Assembly, main bearing
18. Cup, bearing,
19. Cone & roller, bearing
20. Crankshaft
Figure 18. Crankshaft, piston and connecting rod assemblies, exploded view.
to slide freely over the piston to the proper position. Starting with the bottom ring, install piston rings in their proper grooves
Stagger ring gaps so that they are not lined up.
3.
Lubricate each piston and connecting rod assembly with a light cost of engine oil before installing in cylinder block.
Compress the piston rings carefully when installing in cylinder.
4.
When installing cylinder block to crankcase always use new flange gasket and torque nuts to 45 ft.-lbs. torque.
5.
Torque connecting rod nuts to 25 ft.-lbs.
torque.
B. CRANKSHAFT AND CRANKCASE
1.
Removal and Disassembly.
a.
Refer to figure 7 and remove the unloader
assembly.
b.
Remove the hand hole plate and flywheel.
c.
Remove bearing caps (figure 18) and push
connecting rods and pistons up to the top of the cylinder bore. Remove the cap screws that secure unloader housing to crankcase.
d.
Drive the crankshaft, bearings, and unloader housing from the crankcase.
CAUTION: Before driving the crankshaft from the crankcase, be sure the connecting rod journals are in an upright position.
e. Using suitable puller remove the unloader housing and bearing from the shaft.
f.
Remove the oil seal from the crankcase.
NOTE: Do not remove the oil level gage from the crankcase unless the gage is leaking or defective.
19
1. Body assembly
2. Stator wedge kit
3. Bracket, front
4. Bracket, rear
5. Rotor assembly
6. Bolt, stud
7. Bearing
8. Flinger, external
9. Key
10. Shaft L
11. Conduit box assembly
12. Bearing
13. Spring, loading
14. Flinger, external
15. Fan, external
16. Nut
17. Cover, fan
18. Fan
Figure 19. Electric motor assembly.
2.
Cleaning, Inspection, and Repair.
a.
Clean all parts in an approved cleaning solvent and dry thoroughly.
b.
Inspect the crankshaft for cracks, scores, and distortion Measure the crankshaft journals for wear. If the connecting rod journals measure
0.0005 inch out-of-round, replace the.
crankshaft.
c.
Inspect the crankshaft bearings for rough, pitted, or scored rollers. Replace a defective hearing.
d.
Inspect the crankcase for cracks, breaks or other defects. Replace the crankcase if defective.
3.
Reassembly and Installation., a.
Refer to figures 17 and 18 reassemble and
install cry shaft in crankcase using the following procedures:
1.
Always install new oil seal in crankcase.
2. Press bearing cup in the unloader housing.
3. Install new gasket on the unloader homing.
C. ELECTRIC MOTOR
1.
Removal and Disassembly.
a.
Remove the electric motor, Section VIII, B1.
b.
Refer to figure 19 and disassemble electric
motor.
2.
Cleaning, Inspection, and Repair.
a.
Clean all parts with an approved cleaning solvent and dry thoroughly.
b.
Inspect all parts for wear or damage and replace worn defective part
3.
Reassembly and Installation.
a.
Refer to figure 19 and reassemble the electric
motor.
b.
Install the electric motor, Section VIII, B2.
20
advertisement
* Your assessment is very important for improving the workof artificial intelligence, which forms the content of this project
Related manuals
advertisement
Table of contents
- 11 SECTION I. General Description
- 12 Table of Specifications
- 14 II. Service Upon Receipt of Equipment
- 16 III. Controls and Instruments
- 17 IV. Operation Under Usual Conditions
- 18 V. Operation Under Unusual Conditions
- 18 VI. Lubrication Instructions
- 19 VII. Troubleshooting
- 22 VIII. Maintenance Electric Motor and Compressor
- 23 IX. Electrical Accessories and Components
- 23 X. Air Compressor Assembly and Related Components
- 27 XI. Repair and Overhaul Instructions
- 27 Compressor Assembly and Electric Motor
- 31 XII. Preparation for Shipment and Storage