advertisement
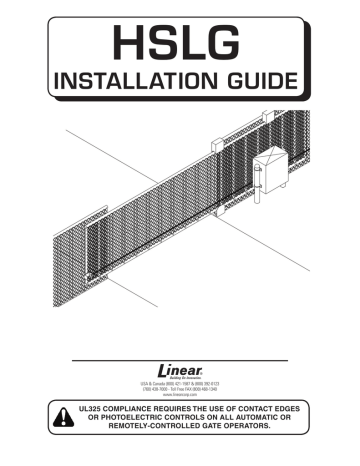
HSLG
INSTALLATION GUIDE
USA & Canada (800) 421-1587 & (800) 392-0123
(760) 438-7000 - Toll Free FAX (800) 468-1340 www.linearcorp.com
UL325 COMPLIANCE REQUIRES THE USE OF CONTACT EDGES
OR PHOTOELECTRIC CONTROLS ON ALL AUTOMATIC OR
REMOTELY-CONTROLLED GATE OPERATORS.
HSLG OPERATOR INSTALLATION GUIDE
TABLE OF CONTENTS
PRE-INSTALLATION INFORMATION
Gate Operator Classifi cations ...................................................................................................................................... 3
Safety Information and Warnings ................................................................................................................................. 3
Pre-Installation Information .......................................................................................................................................... 3
INSTALLATION
Wiring Specifi cations .................................................................................................................................................... 4
Post Mounting Instructions ........................................................................................................................................... 5
Gate Bracket and Chain Assembly Instructions ........................................................................................................... 6
Torque Limiter Adjustments .......................................................................................................................................... 7
Electrical Connection and Adjustments ........................................................................................................................ 8
Limit Nut Adjustments .................................................................................................................................................. 8
CONTROL BOARD ADJUSTMENTS and ACCESSORY CONNECTIONS
Control Board Adjustments .......................................................................................................................................... 9
Terminal Connection Descriptions .............................................................................................................................. 10
Current Sensing Adjustments .................................................................................................................................... 11
Close Direction Current Sense Adjustment ................................................................................................................ 11
Open Direction Current Sense Adjustment ................................................................................................................ 11
Maximum Run Timer Adjustment ............................................................................................................................... 11
Auto Close Timer Adjustment ..................................................................................................................................... 11
Master/Slave Connection ........................................................................................................................................... 11
Onboard L.E.D. Indicator Descriptions ....................................................................................................................... 12
Important Notes for Installation of Master/Slave Applications .................................................................................... 13
Surge Protector Instructions ....................................................................................................................................... 13
Control and Accessory Connection Illustrations .................................................................................................... 14-17
ILLUSTRATIONS
Loop Layout Illustration .............................................................................................................................................. 18
Edge Layout Illustration #1 ......................................................................................................................................... 19
Edge Layout Illustration #2 ......................................................................................................................................... 20
Photo Eye Illustration ................................................................................................................................................. 21
Picket Gate Illustration ............................................................................................................................................... 22
Track Gate Illustration ................................................................................................................................................. 23
TROUBLESHOOTING .................................................................................................................................................. 24
PARTS LISTS
How to Order Replacement Parts .............................................................................................................................. 24
Model HSLG Mechanical Parts Exploded View.......................................................................................................... 25
Model HSLG Mechanical Parts List ........................................................................................................................... 26
Model HSLG Single Phase Control Box Exploded View and Parts List ..................................................................... 27
Model HSLG Three Phase Control Box Exploded View and Parts List ...................................................................... 28
PREVENTATIVE MAINTENANCE ................................................................................................................................ 29
GATE OPERATOR INSTALLATION CHECKLIST ........................................................................................................ 30
CAUTION!
DO NOT INSTALL
CONTROLS ON A
GATE OR FENCE
LINE
CAUTION!
ONLY QUALIFIED SERVICE
TECHNICIANS SHOULD
WORK ON AN LINEAR
SLIDE GATE OPERATOR
- 2 -
CAUTION!
DO NOT INSTALL
CONTROLS
ON THE OPERATOR
HSLG OPERATOR INSTALLATION GUIDE
GATE OPERATOR
CLASSIFICATIONS
All gate operators can be divided into one of four different classifi cations, depending on their design and usage.
SAFETY INFORMATION
AND WARNINGS
Read the following before beginning to install LINEAR slide gate operators:
Class I: Residential
A vehicle gate operator (or system) intended for use in a home of one to four single-family dwellings, or a garage or parking area associated therewith.
Class II: Commercial or General Public Access
A vehicular gate operator (or system) intended for use in a commercial location or building such as a multi-family housing unit (fi ve or more single-family units), hotel, garage, retail store, or other building servicing the general public.
Class III: Industrial or Limited Access
A vehicular gate operator (or system) intended for use in an industrial location or building such as a factory or loading dock area or other locations not intended to service the general public.
Class IV: Restricted Access
A vehicular gate operator (or system) intended for use in a guarded industrial location or building such as an airport security area or other restricted access locations not servicing the general public, in which unauthorized access is prevented via supervision by security personnel.
IMPORTANT!!
Before installing the gate operator, make sure the gate’s slide is free and level throughout the entire opening distance. If the gate does not seem to operate properly, it may affect the operator performance or greatly shorten the life of the unit.
The gate should be designed so that airfl ow through the fabric is ample to prevent wind resistance and drag.
1. Read the yellow “Safety Instructions” brochure enclosed with the packet of information. If you do not have one, please call LINEAR at 1-800-333-1717 to request one.
Read and follow all instructions.
2. All electrical connections to the power supply must be made by a licensed electrician and must observe all national and local electrical codes.
3. A separate power-disconnect switch should be located near the operator so that primary power can be turned off when necessary.
4. A minimum of two (2) WARNING SIGNS shall be installed, one on each side of the gate where easily visible.
5. Never reach between, through or around the fence to operate the gate.
6. You must install all required safety equipment.
PRE-INSTALLATION INFORMATION
Before unpacking, inspect the carton for exterior damage. If you fi nd damage, advise the delivery carrier of a potential claim.
Inspect your package carefully. You can check your accessory box parts with the enclosed packing slip for your convenience.
Claims for shortages will be honored for only 30 days from the date of shipment.
Before installing the operator, read this manual completely to ensure all requirements for proper installation are present. Verify that the voltage to be used matches the voltage of the operator.
The following contact or non-contact obstruction detection devices have been approved for use with LINEAR slide gate operators as part of a UL325 compliant installation:
Contact Edges:
Miller Models*: MG0-20, MGR-20, MGS-20, and
ME-120
Photoeyes:
2520-441 MMTC Model IR-55 photoeye, 165’ with mounting hardware mounting hardware
*for LINEAR part numbers, contact a sales representative for details
- 3 -
HSLG OPERATOR INSTALLATION GUIDE
WIRING SPECIFICATIONS
1. Select from the chart at the bottom of this page corresponding to the model, voltage and horsepower rating of your operator.
6. Connect power in accordance with local codes. The green ground wire must be properly connected.
2. The distance shown on the chart is measured in feet from the operator to the power source. DO NOT EXCEED THE MAXIMUM DISTANCE.
These calculations have been based on standard 115V and 230V supplies with a 10% drop allowable. If your supply is under the standard rating, the runs listed may be longer than what your application will handle, and you should not run wire too near the upper end of the chart for the gauge of wire you are using.
3. When large-gauge wire is used, a separate junction box (not supplied) may be needed for the operator power connection.
4. All control devices are now 24VDC, which can be run considerable distances. 24VAC is available for other devices, such as loop detectors and photo eyes.
5. Wire run calculations are based on the National Electrical Code, Article
430 and have been carefully determined based on motor inrush, brake solenoids, and operator requirements.
7. Wire insulation must be suitable to the application.
8. Control wiring must be run in a separate conduit from power wiring.
Running them together may cause interference and faulty signals in some accessories.
9. Electrical outlets are supplied in all 115VAC models for convenience with occasional use or low power consumption devices only. If you choose to run dedicated equipment from these devices, it will decrease the distance for maximum run and the charts will no longer be accurate.
10. A three-wire shielded conductor cable is required to connect master and slave operators. You must use Belden 8760 Twisted Pair Shielded Cable
(or equivalent) only – LINEAR part number 2500-1982, per foot). See page 9 for details of this connection, as well as dip switch selection.
Note: The SHIELD wire should be connected in both the master and slave operators.
V o l t s
& H P
1 1 5 V
1 / 2
H P
1 1 5 V
3 / 4
H P
1 1 5 V
1 H P
USE COPPER WIRE ONLY!
MODEL HSLG – SINGLE PHASE
M a x
S i n
D g l e i s t a n c e
D u a l G
W i r e a u g e
V o
& l t s
H P
2 0 8 V 2 2 2
3 5 4
5 6 6
9 0 0
1 4 3 0
1 7 8
2 8 2
4 5 0
7 1 6
1 1 4 0
1 6 0
2 5 4
4 0 6
6 4 6
1 0 2 6
1 2
1 0
8
6
4
1 2
1 0
8
6
4
1 2
1 0
8
6
4
8 0
1 2 7
2 0 3
3 2 3
5 1 3
1 1 1
1 7 7
2 8 3
4 5 0
7 1 5
8 9
1 4 1
2 2 5
3 5 8
5 7 0
1
H
2
3
H
2
1
/
/
2
P
0 8
4
P
0
H
8
P
V
P o w e r W i r i n g
M a x
S i n
D g l e i s t a n c e
D u a l G
W i r e a u g e
V o l t s
& H P
2 3 0 V 7 6 0
1 2 0 0
1 9 2 4
3 0 6 0
4 8 6 4
6 0 4
9 5 8
1 5 2 6
2 4 2 4
3 8 5 6
5 4 4
8 6 4
1 3 7 4
2 1 8 4
3 4 7 6
1 2
1 0
8
6
4
1 2
1 0
8
6
4
1 2
1 0
8
6
4
3 8 0
6 0 0
9 6 2
1 8 3 0
2 4 3 2
3 0 2
4 7 8
7 6 3
1 2 1 2
1 9 2 8
2 7 2
4 3 2
6 8 6
1 0 9 2
1 7 3 8
1
H
2
3
H
2
1
/
/
2
P
3 0
4
P
3
H
0
P
V
V
M a x
S i n g l
D i e s t a n c e
D u a l G
W i r e a u g e
8 9 4
1 4 2 2
2 2 6 4
3 6 0 0
5 7 2 4
7 1 0
1 1 2 8
1 7 9 6
2 8 5 2
4 5 3 8
6 4 0
1 0 1 6
1 6 1 6
2 5 7 0
4 0 9 0
1 2
1 0
8
6
4
1 2
1 0
8
6
4
1 2
1 0
8
6
4
4 4 7
7 1 1
1 1 3 2
1 8 0 0
2 8 6 2
3 5 5
5 6 4
8 9 8
1 4 2 6
2 2 6 9
3 2 0
5 0 8
8 0 8
1 2 8 5
2 0 4 5
ACCESSORY WIRING
All Models
Volts
24VAC
Maximum
Distance (ft.)
250
350*
Wire
Gauge
14
12
24VDC 0-2000
*Over 350 ft. use DC power.
14
V o l t s
& H P
2 0 8 V
1 / 2
H P
MODEL HSLG – THREE PHASE
P o w e r W i r i n g : 3 P h a s e
M a x
S i n g
D l e i s t a n c e
D u a l G
W a i r e u g e
1
1
2
1
8
8
4
1
9
2
6
0
5
9
1 4
7 1
0 8
4 5
1
1
8
2
0
V o
& l t s
H P
2 3 0 V
1 / 2
H P
M a x
S i n
D g l e i s t a n c e
D u a l G
W a i r e u g e
1
2
3
3
1
4
4
3
0
4
7
0
6
1 0
1 7
7 2
6 9
0 0
1
1
8
2
0
V o
& l t s
H P
4 6 0 V
1 / 2
H P
M a x
S i n
D g l e i s t a n c e
D u a l
3 8 4 1
6 1 0 6
9 7 1 2
1
3
4
9
0
8
2
5
5
1
3
6
G
W i r e a u g e
1 2
1 0
8
2 0 8 V
3 / 4
H P
9 2 0
1 4 6 4
2 3 3 0
4 6 0
7 3 2
1 1 6 5
1 2
1 0
8
2 3 0 V
3 / 4
H P
1 0 8 4
1 7 2 3
2 7 4 1
5 4 2
8 6 2
1 3 7 1
1 2
1 0
8
4 6 0 V
3 / 4
H P
3 2 7 9
5 2 1 2
8 2 9 1
1 6 4 0
2 6 0 6
4 1 4 6
1 2
1 0
8
2 0 8 V
1 H P
7 1 4
1 1 3 6
1 8 0 4
3 5 7
5 6 8
9 0 2
1 2
1 0
8
2 3 0 V
1 H P
8 4 0
1 3 3 6
2 1 2 4
4 2 0
6 6 8
1 0 6 2
1 2
1 0
8
4 6 0 V
1 H P
2 6 8 9
4 2 7 4
6 7 9 8
1 3 4 5
2 4 3 7
3 3 9 9
1 2
1 0
8
- 4 -
HSLG OPERATOR INSTALLATION GUIDE
POST MOUNTING INSTRUCTIONS FOR MODEL
HSLG
Before installing, make sure the gate rolls or slides freely, and that all exposed rollers are properly covered. The gate must be covered with fabric with openings no larger than
2 1/4” in size, to a minimum height of 48 inches from ground level. On picket-style gates, if pickets are spaced less than
2 1/4” apart, mesh is optional.
Use two 3 - 3 1/2” OD galvanized posts and secure with concrete footings as shown, length to be determined by local codes, frost line depth and soil conditions. Secure the operator to the posts using the 4” U-bolts, side plates, and hardware. There are a total of eight side plates. There are six 3/16” side plates which should be mounted on the outside top and bottom of the cabinet, two 3/16” side plates which go on the top inside and two 1/2” side plates which should be mounted on the inside top of the cabinet as shown in the illustration at the right.
To assemble the drive chain and gate brackets, refer to page 6.
Make sure that the chain sag does not exceed recommended sizes and that the chain does not come into contact with the moving parts of the gate or ground.
For optional pad mounting instructions, see LINEAR drawing
#2700-360.
- 5 -
The operator is intended for installation only on gates used for vehicles. Pedestrians must be supplied with a separate access opening. The pedestrian access opening shall be designed to promote pedestrian usage. Locate the gate such that persons will not come in contact with the vehicular gate during the entire path of travel of the vehicular gate.
SIDE PLATE INSTALLATION
HSLG OPERATOR INSTALLATION GUIDE
GATE BRACKET AND CHAIN ASSEMBLY INSTRUCTIONS
Numbered items in these drawings are for instructional reference only. For actual part numbers, go to the parts lists in the back of this booklet.
Assemble a gate bracket (1) to the front edge of the gate, using two U-bolts (2), and mounting hardware (3). Before tightening down completely, be sure the bracket is parallel to the gate. Tighten the U-bolt hardware the rest of the way, then screw the square head bolts (4) into the threaded holes in the gate plate until they bottom out against the gate. These will help keep the bracket from twisting on the pipe.
Slide a threaded chain pin (5) through the bracket as shown, with spring (6), fl at washer (10), and two hex nuts (7).
Attach one end of the drive chain (8) to the chain pin using master link (9) and begin unrolling it toward the operator.
Remove the rain cover from the back of the slide gate operator. Carefully thread the drive chain under the fi rst idler, over the drive sprocket, and then under the last idler. Make sure you feed most of the chain through the sprockets for attaching to the back end of the gate.
Assemble the other gate bracket on the rear edge of the gate, using the same process as you did with the front gate bracket. Once this is done, take the other chain pin, spring and jam nuts and assemble with the end of drive chain and the other master link.
At this point you should be able to adjust the chain tension by tightening the jam nuts on each end. Approximately 1/4” to 3/8” of slack per foot of drive chain is acceptable. Make sure the chain does not drag on the ground, across the gate rollers or the idler frame of the operator.
Additional mounting holes have been provided in the gate bracket for installer convenience.
- 6 -
HSLG OPERATOR INSTALLATION GUIDE
TORQUE LIMITER ADJUSTMENTS
Before adjusting the torque limiter, make sure the gate is in good working condition. One person should be able to move the gate by hand. Be certain the gate moves freely and without binding throughout its travel. Torque limiters are set light at the factory and must be adjusted during installation. Adjust the torque limiter tight enough to keep it from slipping during normal operation.
To adjust the torque limiter in model HSLG:
1. Loosen the jam nut.
2. To increase the output, turn the adjustment nut clockwise one fl at, or 1/6 turn, at a time until desired output is obtained.
To reduce the output, turn the adjustment nut counterclockwise one fl at, or 1/6 turn, at a time until desired output is obtained.
3. Tighten the jam nut against the adjustment nut when fi nished.
MODEL HSLG
- 7 -
HSLG OPERATOR INSTALLATION GUIDE
ELECTRICAL CONNECTION AND ADJUSTMENTS
Power supply must be of correct voltage and phase.
Always disconnect power from operator before servicing.
Keep clear of gate during operation.
All LINEAR gate operators are supplied with a power disconnect switch to turn on and off the power supply available to the operator. Incoming power should be brought into the operator and connected to the labeled pigtails in the disconnect box following wiring specifi cations on page 4. A wiring connections print can be found on the inside cover of the operator.
Proper thermal protection is supplied with the operator. The motor contains a thermal overload protector to protect from overheating the motor due to overload or high-frequency operation. This overload will automatically reset after the motor cools down.
LIMIT NUT ADJUSTMENTS
The limit nuts are not preset at the factory and must be adjusted for the length of the gate the operator is installed on. The limit switches are activated by two threaded nylon rotary limit nuts which are attached to a threaded shaft and driven by chain and sprockets from the main drive shaft. Remove the cardboard fi ller before attempting to adjust the limit nuts.
With the gate connected to the gate operator in a mid-travel position, and the power disconnect switch turned OFF, disconnect the operator by using the manual disconnect lever. Instructions for the manual disconnect can be found in the individual operator owner’s guides. Once the operator has been disconnected, manually move the gate by hand to within a foot of its fully open position (the foot of distance is necessary to allow for coasting of the operator after the limit switch is tripped).
Once the gate is in this position, adjust the open limit nut until it activates the limit switch for open, LSO-1. Press down on the detent plate and rotate the nut along the threaded shaft. Refer to the illustration below for additional details.
Once the open limit nut is set, repeat the above process for the close direction nut and the LSC-1 limit switch.
After fi nishing the initial limit nut adjustments, reposition the gate to approximately its center of travel. Re-engage the operator and turn the power disconnect ON. Stand clear of any moving parts and press the OPEN button on the three-button station.
If the gate begins to close instead of open, press the STOP button immediately. Find the dip switch block on the main control board and switch the hand of operation (dip switch #4, see page 9) and try to open the gate again. Observe the gate as it runs through a complete cycle in both directions, and adjust your limits again if necessary. Fine levels of adjustment can also be achieved by adjusting a few teeth on the nut at a time. If the gate stops in mid travel, the open or close current sensor adjustment or the maximum run timer may need adjustment (see page 11).
LIMIT NUTS
POWER DISCONNECT BOX
(115VAC VERSION SHOWN)
ROTARY LIMIT BOX ASS’Y
(SWITCHES AND BOX MAY
LOOK SLIGHTLY DIFFERENT
DEPENDING ON MODEL)
LIMIT SWITCHES
L2
(BLACK)
GROUND
(GREEN)
L1
(WHITE)
ON A RIGHT-HAND OPERATOR:
OPEN LIMIT SWITCH IS THE ONE CLOSER
TO THE FRONT OF THE OPERATOR. ON A
LEFT-HAND OPERATOR, THE OPEN LIMIT
SWITCH IS THE ONE FURTHEST AWAY
FROM THE FRONT OF THE OPERATOR.
- 8 -
HSLG OPERATOR INSTALLATION GUIDE
CONTROL BOARD ADJUSTMENTS
LIMIT SWITCH
L.E.D.s
LIMIT SWITCH
CONNECTOR
TERMINAL STRIP #1
CONNECTOR
3A Fuse
Contr ol Boar with A
C d d
Motor Boar
2A Fuse
TERMINAL STRIP #2
CONNECTOR
DIAGNOSTIC
L.E.D.s
NOTE: DO NOT FORCE 270-DEGREE POTENTIOMETERS
BEYOND THEIR NORMAL RANGE OF MOTION
OR DAMAGE MAY RESULT!
Auto Close Timer Adjustment: This 270-degree adjustable potentiometer will signal the operator to close automatically, provided no open, reversing or obstruction signals are present from the fully-open position. This timer is adjustable from 0 to 124 seconds. This feature is turned on or off using dip switch #1.
Maximum Run Timer Adjustment: This 270-degree adjustable potentiometer will signal the operator to stop running once it counts down, unless a limit switch is reached or an input is received fi rst. Each time the motor starts, this timer will begin counting. This timer is adjustable from 15 to 100 seconds. If the timer expires, the unit locks out and the emergency alarm sounds.
Open Direction Current Sense Adjustment: This multi turn potentiometer is used to calibrate the built-in current sensing feature for detection of obstructions while running in the open direction.
Close Direction Current Sense Adjustment: This multi turn potentiometer is used to calibrate the built in current sensing feature for detection of obstructions while running in the closed direction.
Master/Slave Connection Block: This terminal block is used in conjunction with two operators to confi gure two gates to open and close together.
Dip Switches:
#1 This switch turns the auto close timer off/on.
#2 This switch is used in conjunction with alarms and fl ashing lights that may be added to the operator. When the switch is in the ON position, these devices will start approximately two seconds prior to the operator starting. In the OFF position, the devices will only work while the operator is running.
#3 This switch is used in conjunction with single-button controls and radio receivers. In the ON position, successive inputs will cause signals in the order of OPEN-STOP-CLOSE-STOP. In the OFF position, inputs will cause an OPEN signal unless the gate is fully open, in which case it will signal CLOSE.
#4 This switch determines right-hand vs. left-hand behavior. When looking from inside the protected area toward the gate, the side of the drive the operator is on determines its hand of operation. In the OFF position, the operator is set for right-hand.
(provided the R2 brake resistor is cut, see picture above). In the OFF position, the reverse delay is 1 1/2 seconds and the DC inherent brake is enabled.
#7 Not used at this time.
#8 This switch is used to set Master/Slave confi guration. Operators which are stand-alone or master units should be set to OFF, while only slave units should have this switch set to ON.
- 9 -
HSLG OPERATOR INSTALLATION GUIDE
TERMINALS FUNCTION
24VAC
24VAC N
24VAC
24VDC+
24VDC- COMM.
24VDC
1 & 4 OPEN
TERMINAL CONNECTION DESCRIPTIONS
DESCRIPTION OF FUNCTION
Provides 24Volt AC power for accessories.
Note: DC models will NOT have 24Volt AC power available.
Provides 24Volt DC power for accessories.
3 & 4
4 & 5
2 & 4
4 & 6
4 & 50
4 & 51
4 & 11
CLOSE
SINGLE-BUTTON
STOP
REVERSE
OPEN
OBSTRUCTION
CLOSE
OBSTRUCTION
SHADOW/HOLD
24VDC+ & 60 RUN/PRE-START
Opens the operator. Several accessories such as button stations, keypads, transmitters and card readers can be wired to open.
Closes the operator. Use caution when wiring accessories to these terminals. The gate must be clearly visible from the location of any accessories wired to close.
Performs the single-button function which will alternate between open and close or open, stop and close - depending on dip switch #3. (See page 9 for details.)
Stops the operator. If no stop button is used, a jumper is required across 2&4.
This function will cause a reversal when the gate is traveling closed and will travel back to the fully open position. Loop detectors are often wired for reverse.
This function works only while the operator is opening. Any signal to this function will cause the gate to stop, reverse a short distance, and then stop again. At this time the auto close timer is disabled, and a renewed input will be required to start the gate again. Should the gate be restarted and the signal occur again prior to reaching a limit, the gate will stop again, and this time will sound the emergency alarm and lock out.
This function works exactly like the OPEN OBSTRUCTION, except that it will only work in the closing direction.
This function will keep the gate in its fully open position while the signal is present.
This is typically used with a loop and loop detector to keep a large swing gate open while vehicular traffi c is passing through.
A 24Volt DC device such as a strobe light or alarm can be wired to these terminals.
Depending on dip switch #2, these devices will either begin three seconds before the operator starts, or only while the motor is running. (See page 9 for details.)
You must follow all required safety precautions and instructions at all times. Review the safety brochure included with the operator. If any pages are missing or unreadable, contact LINEAR at 1-800-333-1717 to request additional copies.
Controls intended for user activation must be located at least six feet (6’) away from any moving part of the gate and where the user is prevented from reaching over, under, around or through the gate to operate the controls. Outdoor or easily accessible controls shall have a security feature to prevent unauthorized use.
Do not adjust the circuit board current sensing feature too high. It should be adjusted high enough to keep the gate from falsely triggering the sensing, but no higher than necessary for the gate to operate. Do not defeat the purpose of this function!
- 10 -
HSLG OPERATOR INSTALLATION GUIDE
CURRENT SENSING ADJUSTMENTS
Because gates vary in construction and may have different force requirements in the open and close directions to move, the
LINEAR control board has separate Multi-turn potentiometers for adjusting in both directions independently. The adjustment should be set light enough to maintain minimal force (50-75 lbs.) should an obstruction occur, but high enough to keep the gate moving under normal conditions without interruption.
Prior to adjusting the operator current sensing functions, make sure the gate moves freely in both directions. A badly aligned or poorly maintained gate may cause false triggering of the current sensor. Refer to page 9 when following the instructions below. A factory adjustment tool has been supplied to make these adjustments easier. This tool has been taped to the control box for your convenience.
CLOSE DIRECTION CURRENT SENSE ADJUSTMENT
When the gate operator leaves the factory, it has been preset for a relatively light gate function and will require additional adjustment. Begin by starting the gate going closed. If the operator stops and reverses, turn the close direction potentiometer
(see page 9) one turn higher, press the STOP button, and try again. Repeat this process until the gate no longer causes false tripping of the current sensor. Note that each time the gate operator reverses, the STOP button must be pressed. Next, turn the close direction potentiometer lower slowly while the operator is running the gate closed until the gate operator stops and reverses again. From this point, turn the close direction potentiometer higher by 1 1/2 turns for all 115 Volt AC and 24
Volt DC operators, and by 3/4 of a turn higher for all 230 Volt AC operators. Additional fi ne adjustment by 1/4 turns may be necessary to eliminate false triggering.
OPEN DIRECTION CURRENT SENSE ADJUSTMENT
Repeat the same process with the open direction potentiometer while running the gate in the open direction. Once this is done, run the gate through several complete cycles and make sure the gate does not false trip in either direction.
Multi-turn Potentiometer
Remember it is important not to set the adjustment too high! Doing so will defeat the purpose of the current sensing as an obstruction detecting feature.
MAXIMUM RUN TIMER ADJUSTMENT
This adjustable potentiometer sets the maximum length of time the motor will run before shutting down. It should be confi gured for the time it takes to run the gate fully open or closed, plus an additional 15 seconds. See page 9 for details.
AUTO CLOSE TIMER ADJUSTMENT
This adjustable potentiometer sets the length of time which elapses before the gate operator automatically closes the gate, from the fully open position, provided no open, reversing, or obstruction signals are present. This feature can be turned on or off via dip switch selection. See page 9 for details. Do not use the auto close timer without an appropriate reversing device installed!
MASTER/SLAVE CONNECTION
A three-wire shielded conductor cable is required to connect master and slave operators. You must use Belden 8760 Twisted
Pair Shielded Cable (or equivalent) only – LINEAR part number 2500-1982, per foot). See page 9 for details of this connection, as well as dip switch selection. Note: The SHIELD wire should be connected in both the master and slave operators. In addition, you must run power to both the master and slave operators.
- 11 -
HSLG OPERATOR INSTALLATION GUIDE
ONBOARD L.E.D. INDICATOR DESCRIPTIONS
Control Board L.E.D. Indicators:
OPEN This indicator is lit when an open signal is present. This signal can come from such devices as button stations, radio receivers, keypads and telephone entry systems.
CLOSE
STOP
This indicator is lit when a closed signal is present. This signal typically comes from three-button stations.
This indicator is lit when there is a break in the stop circuit. Make sure there is a stop button wired in andworking properly.
This indicator is lit when a signal from a single-button station or radio receiver is present.
SINGLE
CLOSE OBST This indicator is lit when a close obstruction signal is present. This signal can come from edges and photo eyes which have been wired to the close obstruction inputs.
OPEN OBST This indicator is lit when an open obstruction signal is present. This signal can come from edges and photo eyes which have been wired to the open obstruction inputs.
SAFETY LOOP This indicator is lit when a reversing signal is present. This signal is generated by a loop detector wired to the safety loop terminals.
SHADOW LOOP This indicator is lit when a shadow/hold open signal is present. This signal is generated by a loop detector wired to the shadow loop terminals.
LH
LSC-1
RH
LSO-1
This indicator is lit when the open #1 limit switch is activated on a right-hand operator, or the close #1 switch on a left-hand. If this indicator is lit and the gate is not in its full open/closed position, the limit may need adjusting or the limit switch may need replacing.
LSC-2 LSO-2
LSO-1 LSC-1
This indicator is lit when the open #2 limit switch is activated on a right-hand operator, or the close #2 switch on a left-hand.
This indicator is lit when the close #1 limit switch is activated on a right-hand operator, or the open #1 on a left-hand. If this indicator is lit and the gate is not in its full open/closed position, the limit may need adjusting or the limit switch may need replacing.
LSO-2 LSC-2
This indicator is lit when the close #2 limit switch is activated on a right-hand operator, or the open #2 switch on a left-hand.
Motor Board L.E.D. Indicators:
NON LABELED One of these two indicators will be lit when the motor is running the gate open, and the other is lit when the motor is running the gate closed.
BRAKE REL. This indicator is lit when the brake is NOT applied.
- 12 -
HSLG OPERATOR INSTALLATION GUIDE
IMPORTANT NOTES FOR
INSTALLATION OF MASTER/SLAVE APPLICATIONS
When setting up Master/Slave gate operators, it is best to make adjustments and run each operator individually. To do this, simply: a. Set Dip Switch #4 to proper hand of operation (right-hand or left-hand) b. Set Dip Switch #8 as Master (off)
Run each operator making current sensing adjustments as necessary, as indicated on the Control Board Adjustments page of this installation guide. When both operators have been adjusted, turn power off, then turn on Dip Switch #8 in the operator chosen as the Slave.
The timer to close and radio/single button behavior are set in the Master operator.
The following selections are set individually:
One-Second Lock Release
SURGE PROTECTOR INSTRUCTIONS
The optional surge protector should be connected to any inputs that have an accessory connected to it. This includes the 3-button station, so it must be connected to 1, 2A and 3 in all cases. The green wire connected to ground, which is electrically the same as terminal 4. The red wires connect to terminals 2A and 24VDC+. This will cause the
2 amp fuse to blow if this section of the module becomes shorted. With any of the other inputs connected to the surge protector, if their protection line becomes shorted due to a surge over the rating of the module, the corresponding LED on the main board will remain lit, causing a constant signal to the controller. If this is found, please replace the entire surge protector with a new unit.
Do not simply unhook the shorted wire, as this removes the protection from the circuit that was saved by the protector in the fi rst place!
- 13 -
HSLG OPERATOR INSTALLATION GUIDE
CONTROL and ACCESSORY CONNECTION ILLUSTRATIONS
- 14 -
HSLG OPERATOR INSTALLATION GUIDE
CONTROL and ACCESSORY CONNECTION ILLUSTRATIONS
- 15 -
HSLG OPERATOR INSTALLATION GUIDE
CONTROL and ACCESSORY CONNECTION ILLUSTRATIONS
- 16 -
HSLG OPERATOR INSTALLATION GUIDE
CONTROL and ACCESSORY CONNECTION ILLUSTRATIONS
- 17 -
HSLG OPERATOR INSTALLATION GUIDE
LOOP LAYOUT ILLUSTRATION
Refer to Connection Descriptions on page 10 and Loop Accessory Connections on page 17 for details.
- 18 -
HSLG OPERATOR INSTALLATION GUIDE
EDGE LAYOUT ILLUSTRATION #1
Refer to Connection Descriptions on page 10 and Contact Edge Connections on page 16 for details.
- 19 -
HSLG OPERATOR INSTALLATION GUIDE
EDGE LAYOUT ILLUSTRATION #2
Refer to Connection Descriptions on page 10 and Contact Edge Connections on page 16 for details.
- 20 -
HSLG OPERATOR INSTALLATION GUIDE
PHOTO EYE ILLUSTRATION
Refer to Connection Descriptions on page 10 and Photo Eye Connections on page 16 for details.
- 21 -
HSLG OPERATOR INSTALLATION GUIDE
PICKET GATE ILLUSTRATION
Refer to Connection Descriptions on page 10 and Accessory Connections on pages 14-17 for additional details.
- 22 -
HSLG OPERATOR INSTALLATION GUIDE
TRACK GATE ILLUSTRATION
- 23 -
HSLG OPERATOR INSTALLATION GUIDE
TROUBLESHOOTING
Operator fails to start:
A. If the operator has been running a large number of cycles, the motor may have gotten hot and tripped the overload.
Allow the motor to cool down and the overload will reset automatically.
B. Make sure you have power at the master distribution panel and that the power has not been turned off.
C. The secondary fuse on the control board may have blown.
Replace the fuse (refer to control box parts list on pages
27 [single phase] or 28 [three phase] for part number information).
Motor operates, but gate does not move:
A. In operators with torque limiters and friction pad clutches, check for signs of slipping. You can mark the sprocket and clutch with a yellow or white grease pen and watch for the lines to move apart if slipping is taking place. Adjust the torque limiter tighter if this is the problem.
B. Check for broken chain or worn belts.
C. Check all setscrews on pulleys and sprockets and tighten them if necessary, and check for keys which may have fallen loose from keyways.
Motor sounds like it is working harder than normal:
A. Make sure the gate is moving freely and without binding throughout its entire travel.
B. Check the drive chain for obstructions (if the operator has one).
C. If the operator has an internal brake mechanism, make sure it is releasing.
Limit switch getting out of time:
A. Check for proper tension on all limit chains to be sure there is no jumping taking place. Mark one tooth and its corresponding link and run the gate. If the marks have moved, the chain is skipping.
B. Check the setscrews in limit cams and limit sprockets for tightness. In rotary limit boxes, check the rotary limit nut for sloppiness or stripped threads. Replace if necessary.
C. Check the chain tension along the output sprocket and idlers. Mark the chain and one tooth of the sprocket as described above and run the gate. Check for jumping.
Gate stopping part way open or closed
(but no visible obstruction):
A. The control board may have received a false obstruction input triggered by current sensing set too low. Make sure the gate moves freely through its entire travel before adjusting the current sensing.
B. The maximum run timer may have counted down and expired. This can be caused by having the timer set too low, if a chain or belt is broken, or if a sprocket or pulley is slipping. When the timer expires, the gate stops and an alarm will sound.
C. An obstruction signal from an accessory wired to the obstruction input may have triggered falsely. Check the control board for lit L.E.D. indicators for any of the following inputs: safety, shadow, open obstruction, close obstruction, stop, etc. If any are lit when the operator should be running, remove all devices hooked to that function and hook them up one at a time and try to run the operator until the problem device is found. Refer to page 12 for details on the control board indicators.
Gate staying open with automatic system:
A. If there are vehicle detectors in your machine which are set up for reverse, one of your loops or loop detectors may be sending a false signal. Disconnect the wire harness and try running the operator.
B. An opening or reversing device may be stuck or malfunctioning. Try disconnecting these devices and hook them back up one at a time and try running the operator until the malfunctioning device is found.
C. Make sure the close limit switch isn’t activated. If it is, the operator will think the gate is already closed.
HOW TO ORDER REPLACEMENT PARTS
Use the part numbers listed on the following pages. Contact your local LINEAR dealer or distributor to order parts.
1. Supply the model number and serial number of your operator.
2. Specify the quantity of pieces needed and order by part number and name of part.
3. State whether to ship by freight, truck, parcel post, UPS or air express.
4. State whether transportation charges are to be prepaid or collect.
5. Specify name and address of person or company to whom parts are to be shipped.
6. Specify name and address of person or company to whom invoice is to be sent.
- 24 -
HSLG OPERATOR INSTALLATION GUIDE
MODEL
HSLG
MECHANICAL PARTS EXPLODED VIEW
- 25 -
HSLG OPERATOR INSTALLATION GUIDE
15
20
93
21
25
97
37
26
73
30
28
31
78
79
32
33
89
81
27
11
70
82
16
18
7
34
36
Wires
6
MODEL
HSLG
MECHANICAL PARTS LIST
REF REF
NO. PART DESCRIPTION
10
2110-240
2100-765
Intermediate Shaft Assembly
Pulley Shaft
NO. PART DESCRIPTION
95 2500-2307
Motors
1/2 HP, 115V, 1 Phase
14
9
2200-213
2200-309
Sprocket, 41-B-9, 5/8” bore
Double Pulley, 7”
2500-2308
2500-2309
1/2 HP, 208/230V, 1 Phase
3/4 HP, 115V, 1 Phase
11
92
2200-233
2200-215
Set Collar Set, 5/8”
Precision Bearing, 5/8”
2500-2310
2500-2311
3/4 HP, 208/230V, 1 Phase
1 HP, 115V, 1 Phase
72
71
2200-333
2100-1750
Key, 3/16” x 1 1/2”
Key, 3/16” x 1 1/4”
2500-2312
2500-2313
1 HP, 208/230V, 1 Phase
1/2 HP, 208/230/460V, 3 Phase
12 2100-547 Brake Disc 2500-2314
2500-2315
3/4 HP, 208/230/460V, 3 Phase
1 HP, 208/230/460V, 3 Phase
102
103
2110-274
2100-1008
2200-294
2100-669
2100-1007
2100-564
2200-306
2400-061
2400-062
2400-187
2400-088
2200-292
2200-215
2200-233
2400-238
2400-273
2110-236
2100-917
2220-022
2200-119
2110-131
2200-274
2100-1737
2200-014
2200-091
2400-201
2200-968
2400-026
2110-700
2520-173R
2500-764
2100-057
2200-030
2100-261
2110-162
2100-756
2200-029
2200-193
2400-203
2200-008
2200-008
2200-654
2200-041
2200-654
2200-276
2200-654
2200-202
2400-038
2100-1756
2100-1781
Clutch Shaft Assembly
Clutch Shaft
Sprocket, 41-A-36, 1” bore
Clutch Hub (pinned)
Clutch Hub (keyed)
Clutch Facing
Clutch Spring
Hex Nut, 5/8”-18
Jam Nut, 5/8”-18
Thrust Washer, 1” x 1/8”
Roll Pin, 3/16” x 1 3/8”
Sprocket, 41-B-12, 5/8” bore
Precision Bearing, 5/8”
Set Collar, 5/8”
Key, 3/16” x 1 1/4”
Key, 3/16” x 1/4”
Output Shaft Assembly
Output Shaft, 1”
Sprocket, 41-A-24 with Bearing
Bearing only for 41-A-24 Sprocket
Shifter Block with Pins
Pillow Block Bearing, 1”
Pillow Block Retaining Plate
Set Collar, 1” x 3/8” LTB
Set Collar, 1” x 5/8” LTB
Key, 1/4” x 1 1/2”
Sprocket, 40-B-22, 1” bore
Spring Pin, 3/16” x 1”
(Predrilled for Pillow Block)
Idler Assembly
Rotary Limit Box Assembly
Standard Limit Shaft
Limit Box Enclosure with Cover
Limit Box Cover only
Flange Bearing, 1/2” ID
Limit Drive Sprocket, 48-B-10, 1/2” bore
For Drives up to 30 feet wide:
Limit Box Sprocket, 48-B-10, 1/2” bore
#48 Chain, per foot, 27 Links required
For Drives from 31 to 45 feet wide:
Limit Box Sprocket, 48-B-15, 1/2” bore
#48 Chain, per foot, 29 Links required
For Drives over 45 feet wide:
Limit Box Sprocket, 48-B-20, 1/2” bore
#48 Chain, per foot, 30 Links required
#40 Chain, per foot
U-Bolt, 4 5/8”
2510-064 Three-Button Station with Lead
Control Box Mounting Plate
Accessory Shelf for Single Phase
2120-359-BT
2120-360-BT
2300-716
2110-643
2200-540
2110-234
2100-573
2200-207
2400-149
2120-132
2100-910
2200-291
2100-657-BT
2400-088
2100-2007
2400-170
2100-258
2200-306
2400-090
2400-045
2500-867
2200-234
2100-553
2200-150
2200-027
2100-656-BT
2100-059-BT
2200-006
2200-654
2200-010
2400-422
2510-248
2100-1760
2500-1495
2510-251-D
2500-1956
2500-1957
5
90
76
96
8
77
91
100
101
23
24
19
75
87
88
84
85
86
1
53
3
94
29
22
40
41
42
44
46
45
13
2500-2336
2500-2337
2500-1926
2500-1930
2500-1931
2500-2338
2500-1932
Magnetic Brakes (includes 41, 42, 44, 45 and 46)
2510-398 115V
2510-399 230V
2510-400
2220-983
2500-177
2500-178
460V
Brake and Puck Assembly
Brake Solenoid, 230 VAC
Brake Solenoid, 115 VAC
2500-1351
2200-243
2100-548
2100-541
2100-2091
Brake Solenoid, 460 VAC
Brake Spring (short)
Brake Rod
Brake Plate
Bracket for Brake
2510-252-D
2500-2205
Capacitors
Capacitor for 2500-2307 Motor
Capacitor for 2500-2308 Motor
Capacitor #1 for 2500-2309 Motor
Capacitor #2 for 2500-2309 Motor
Capacitor for 2500-2310 Motor
Capacitor for 2500-2311 Motor
Capacitor for 2500-2312 Motor
Enclosure Assembly Complete with Door
Door Assembly only
Stop/Reset Button Cover
Lock Assembly with Keys
Rail Assembly
Spacer Plate
Double Pulley, 2”
Chain, #41, 30 Links
Shifter Lever
Locking Disconnect Lever
Disconnect Spring
Rain Cover
Roll Pin
Gate Bracket
U-Bolt, 3”
Chain Tension Bolt, 1/2”
Clutch/Chain Tension Spring
Hex Nut, 1/2”-13 (4)
V-Belt, 28”
#41 Chain, per foot (20 links required)
#41 Master Link
Side Plate, 1/2”
Side Plate, 3/16”
#40 Master Link
#48 Chain, per foot (27 links required)
#48 Master Link
5/16-18 U-Nut (4)
Stop/Reset Button and Bracket Assembly
Stop/Reset Button Mounting Bracket
Power On/Off Disconnect Assembly with Receptacles (115V Models only)
115VAC Duplex Receptacles only
115VAC Switch only
Power On/Off Disconnect Assembly for 230VAC Models
230VAC Switch only
101
- 26 -
2510-294
2500-034
Power On/Off Disconnect Assembly for 3 Phase Operators
Power Switch only
HSLG OPERATOR INSTALLATION GUIDE
MODEL
HSLG
SINGLE PHASE CONTROL BOX PARTS LIST
REF
NO. PART DESCRIPTION
9
10
11
12
13
14
1
2
3
4
5
6
7
8
2100-1778
2100-1757
2100-1762
2100-1761
2200-122
2500-1948
2510-268
2500-1946
2510-244
2510-253
2510-249
2510-250
2510-261
2500-071
2500-212
2500-791
Control Box Wrapper
Control Box Mounting Plate
Terminal Strip Bracket, Output Side
Terminal Strip Bracket, Input Side
Heyco Bushing, .87 diameter
Control Board Standoff
Control Board
AC Motor Drive Board
Control Board with AC Motor Board
Limit Switch Harness Assembly
Input Wire Harness Assembly
Output Wire Harness Assembly
Control Box Motor Harness Assembly
Terminal Strip, 16-141
Transformer, 115/24VAC 40VA
Transformer, 230/24VAC 40VA
REF
NO. PART DESCRIPTION
15
16
2300-696
2300-735
Clear Control Box Cover
Heyco Bushing, 1.09 diameter
17
18
19
2200-876
2500-867
2500-1966
2500-1975
2520-391-D
2520-392-D
Plunger, Spring Loaded
Alarm, 24VAC (not shown)
2 Amp Fuse for Control Board
3 Amp Fuse for Control Board
Complete Controller Assembly
115VAC (order limit harness and mounting brackets separately)
Complete Controller Assembly
230VAC (order limit harness and mounting brackets separately)
- 27 -
HSLG OPERATOR INSTALLATION GUIDE
MODEL
HSLG
THREE PHASE CONTROL BOX PARTS LIST
REF
NO. PART DESCRIPTION
1
2
3
4
5
7
8
9
2100-1865
2100-1866
2100-1864
2100-1762
2510-293
2510-355
2300-735
2500-1948
2510-295
2510-268
Control Box Cover
Terminal Strip Bracket
Terminal Strip Bracket
Control Box Motor Harness Assembly
Control Box Motor Harness Assembly
(AO Smith motors)
Heyco Bushing, 1.09 diameter
Control Board Standoff
Control Board with 3 Phase Motor Board
Control Board only
REF
NO. PART DESCRIPTION
14
15
16
17
18
2500-071
2500-270
2500-185
2300-488
2300-585
2510-250
2510-249
Terminal Strip, 16-141
Terminal Strip, 9-142 OR
Terminal Strip, 13-142
Terminal Strip Barrier for 9-142 OR
Terminal Strip Barrier for 13-142
Output Wire Harness Assembly
Input Wire Harness Assembly
2500-768
10
11
12
13
2500-1980
2500-1966
2500-1975
2510-253
3 Phase Motor Board
2 Amp Fuse for Control Board
3 Amp Fuse for Control Board
Limit Switch Harness
2520-400
2520-401
Controller, 208/230, 3 Phase
Controller, 460, 3 Phase
(order limit harness and mounting
- 28 -
HSLG OPERATOR INSTALLATION GUIDE
PREVENTATIVE MAINTENANCE
IMPORTANT!
• Always disconnect power from operator before servicing.
• Keep clear of gate during operation.
GENERAL:
LINEAR gate operators are designed for many years of trouble-free operation and, under recommended operating conditions, will require only minimal maintenance. To ensure that your unit is ready for operation at all times--and to preclude serious damage or failure--inspect the unit systematically. Proper adjustments and lubrication should be made as recommended.
LUBRICATION:
Bearings. For models which have pillow block style bearings with greaseable fi ttings, lubricate at least twice a year with a lithium complex based, petroleum oil NLGI 2 rated grease. Oilite and precision sealed bearings do not require additional lubrication.
Motor. Motors have sealed ball bearings and do not require further lubrication. If bearing noise develops after several years of operation, bearings should be replaced by a motor repair company, or the motor should be replaced if necessary.
Drive Chain and Sprocket (slide gate models only). The main drive chain and sprockets should be inspected for wear, cleaned, and wiped down with a lightly oiled rag every six months.
Swing Gate Arm (swing gate models only). Check all bolts for proper tension and tighten if necessary. Make sure the arm folds overextends itself slightly against the over travel stop to reduce the chance that the gate can be back driven open. Adjust the close limit slightly if additional travel is required. Lightly lubricate all pivot points with a light machine oil.
Barrier Gate Arm (barrier gate models only). Check all bolts for proper tension and tighten if necessary. If the arm has been warped or damaged, replace as necessary.
ADDITIONAL SIX MONTH PREVENTATIVE MAINTENANCE:
1. For operators which utilize torque limiting clutches, check for proper tightness. If there appears to be dust from wear on the pads, inspect the pads and replace if necessary.
If the clutch cannot be adjusted tightly enough to move the gate without slipping, the pads must be replaced.
6. In operators which have a disconnect handle, inspect disconnect handle for proper function and lubricate if necessary. Use a lithium based grease on all moving parts.
7. Inspect all nuts and bolts for proper tightness and tighten as necessary.
2. For operators with V-belts, inspect for wear and replace as necessary. Check for proper tension and adjust if required. Check all pulley setscrews for tightness and tighten if necessary.
8. Check all reversing devices for proper function. Inspect all contact edges for wear and replace if required. Check photo-eyes for proper alignment and function.
9. Check current sensing for proper adjustment when fi nished with inspection and maintenance.
3. For operators with internal chain drives, inspect chain and sprockets for wear and replace if necessary. Check for proper tension and alignment, and adjust if required.
Check all hub sprocket setscrews and tighten if required.
4. Check limit switches and limit actuators (cams, limit nuts, etc.) for wear and replace as required. In rotary limit switch assemblies, wipe the limit shaft clean and apply a light coating of dry lubricant.
10. Inspect the installation area. Are all the warning signs intact and visible? If they are missing or need replaced, contact
LINEAR. Be sure there are no control stations mounted within reach of the gate. Review safety literature with the customer and advise them to remove any such stations found.
5. For operators with magnetic brakes, check for proper adjustment. Brake disc must run free when the brake is engaged. For brake assemblies other than C-face style, the brake should be adjusted so that the solenoid plunger throw is between 3/8” to 1/2”. Too much throw will damage the solenoid. If the solenoid emits a loud buzzing sound when the motor is run, the brake must be adjusted.
For slide and swing gate operators, you must inspect the gate for proper operation. The gate should move easily without binding through its entire travel. If the gate does bind, adjust or fi x as required. Failure to keep the gate in good working condition will have adverse effects on the operator.
- 29 -
HSLG OPERATOR INSTALLATION GUIDE
CUSTOMER
GATE OPERATOR INSTALLATION CHECKLIST
INSTALLER
________ ________
1. The gate has been checked to make sure it is level and moves freely in both directions.
________ ________
2. Potential pinch areas have been guarded so as to be inaccessible OR have contact and/or non-contact obstruction sensing devices installed.
________ ________
3. The installer has installed one or more contact or non-contact obstruction sensing devices, in compliance with UL325 requirements for this installation.
________ ________
4. The slide gate has been screened or secured from the bottom of the gate to a minimum of
48 inches above ground to prevent a 2 1/4-inch sphere from passing through the openings anywhere in the gate and in that portion of the adjacent fence that the gate covers when the gate is in the open and closed positions. Picket gates which have spacings less than 2
1/4 inches apart to the minimum height requirement are also acceptable.
________ ________
5. Roller covers have been installed on cantilever gates.
________ ________
6. Pedestrians have been supplied with a separate access opening. The customer has been informed that all pedestrian traffi c must use the pedestrian gate.
________ ________
7. Two (2) warning signs have been installed, one on each side of the gate in easily visible locations. The customer has been informed that these signs must remain at all times.
________ ________
8. Controls intended for user activation are located at least six feet (6’) away from any moving part of the gate and where the user is prevented from reaching over, under, around or through the gate to operate the controls. Outdoor or easily accessible controls have a security feature to prevent unauthorized use.
________ ________
9. The installer has properly adjusted the obstruction sensing feature and has tested the gate to make sure that the gate stops and reverses a short distance with minimal resistance applied (40 lbs. on a swing gate at the end of the gate, 75 lbs. on a slide gate)
________ ________
10. The installer has instructed the customer in the proper use of the gate operator and reviewed all of the operational functions, obstruction sensing devices, warning beeper and reset, etc.
________ ________
11. The installer has instructed the customer in the proper use of the operator’s manual disconnect feature. The manual disconnect must never be used while the gate is in motion. The power switch must be turned off before using the manual disconnect and disengaging the operator.
________ ________
12. The installer has reviewed all safety instructions with the customer, and has left the safety instructions and owner’s information sheets for their reference.
________ ________
13. The installer has answered any questions the customer has regarding the operation of the gate operator and gate operator safety precautions.
________ ________
14. The installer has explained to the customer that a regular maintenance schedule for both the gate and the gate operator is recommended.
By signing this installation checklist, I/we hereby certify that each item listed and checked above has been covered by the installer and is clearly understood by the customer.
______________________________________________ _____________________________
______________________________________________ _____________________________
- 30 -
P561 SEPT.08
advertisement
Related manuals
advertisement
Table of contents
- 3 Gate Operator Classifi cations
- 3 Safety Information and Warnings
- 3 Pre-Installation Information
- 4 Wiring Specifi cations
- 5 Post Mounting Instructions
- 6 Gate Bracket and Chain Assembly Instructions
- 7 Torque Limiter Adjustments
- 8 Electrical Connection and Adjustments
- 8 Limit Nut Adjustments
- 9 Control Board Adjustments
- 10 Terminal Connection Descriptions
- 11 Current Sensing Adjustments
- 11 Close Direction Current Sense Adjustment
- 11 Open Direction Current Sense Adjustment
- 11 Maximum Run Timer Adjustment
- 11 Auto Close Timer Adjustment
- 11 Master/Slave Connection
- 12 Onboard L.E.D. Indicator Descriptions
- 13 Important Notes for Installation of Master/Slave Applications
- 13 Surge Protector Instructions
- 14 Control and Accessory Connection Illustrations
- 18 Loop Layout Illustration
- 19 Edge Layout Illustration
- 21 Photo Eye Illustration
- 22 Picket Gate Illustration
- 23 Track Gate Illustration
- 24 TROUBLESHOOTING
- 24 How to Order Replacement Parts
- 25 Model HSLG Mechanical Parts Exploded View
- 26 Model HSLG Mechanical Parts List
- 27 Model HSLG Single Phase Control Box Exploded View and Parts List
- 28 Model HSLG Three Phase Control Box Exploded View and Parts List
- 29 PREVENTATIVE MAINTENANCE
- 30 GATE OPERATOR INSTALLATION CHECKLIST