- Entertainment & hobby
- Musical instruments
- Modulator
- BENDIX
- MC-30 TRAILER ABS CONTROLLER
- Product information
Product information | BENDIX MC-30 TRAILER ABS CONTROLLER System information
Add to My manuals32 Pages
advertisement
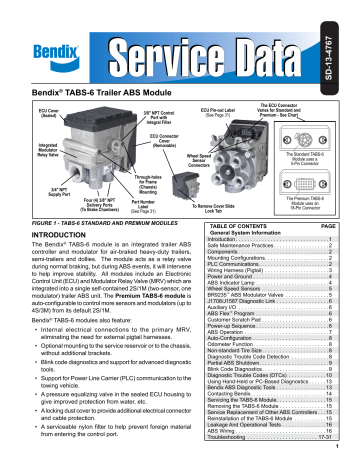
®
Bendix
®
TABS-6 Trailer ABS Module
ECU Cover
(Sealed)
3/8" NPT Control
Port with
Integral Filter
ECU Pin-out Label
(See Page 31)
The ECU Connector
Varies for Standard and
Premium - See Chart
Integrated
Modulator
Relay Valve
ECU Connector
Cover
(Removable)
Wheel Speed
Sensor
Connectors
The Standard TABS-6
Module uses a
5-Pin Connector
3/4" NPT
Supply Port
Four (4) 3/8" NPT
Delivery Ports
(To Brake Chambers)
Through-holes for Frame
(Chassis)
Mounting
Part Number
Label
(See Page 31)
FIGURE 1 - TABS-6 STANDARD AND PREMIUM MODULES
INTRODUCTION
The Bendix
®
TABS-6 module is an integrated trailer ABS controller and modulator for air-braked heavy-duty trailers, semi-trailers and dollies. The module acts as a relay valve during normal braking, but during ABS events, it will intervene to help improve stability. All modules include an Electronic
Control Unit (ECU) and Modulator Relay Valve (MRV) which are integrated into a single self-contained 2S/1M (two-sensor, one modulator) trailer ABS unit. The
Premium TABS-6 module
is auto-con fi gurable to control more sensors and modulators (up to
4S/3M) from its default 2S/1M.
Bendix
®
TABS-6 modules also feature:
• Internal electrical connections to the primary MRV, eliminating the need for external pigtail harnesses.
• Optional mounting to the service reservoir or to the chassis, without additional brackets.
• Blink code diagnostics and support for advanced diagnostic tools.
• Support for Power Line Carrier (PLC) communication to the towing vehicle.
• A pressure equalizing valve in the sealed ECU housing to give improved protection from water, etc.
• A locking dust cover to provide additional electrical connector and cable protection.
• A serviceable nylon fi lter to help prevent foreign material from entering the control port.
To Remove Cover Slide
Lock Tab
The Premium TABS-6
Module uses an
18-Pin Connector
TABLE OF CONTENTS
General System Information
PAGE
Introduction. . . . . . . . . . . . . . . . . . . . . . . . . . . . . . . .1
Safe Maintenance Practices. . . . . . . . . . . . . . . . . . .2
Components . . . . . . . . . . . . . . . . . . . . . . . . . . . . . . .2
Mounting Con fi gurations. . . . . . . . . . . . . . . . . . . . . .2
PLC Communications. . . . . . . . . . . . . . . . . . . . . . . .2
Wiring Harness (Pigtail) . . . . . . . . . . . . . . . . . . . . . .3
Power and Ground . . . . . . . . . . . . . . . . . . . . . . . . . .4
ABS Indicator Lamp . . . . . . . . . . . . . . . . . . . . . . . . .4
Wheel Speed Sensors . . . . . . . . . . . . . . . . . . . . . . .5
BR9235
™
ABS Modulator Valves . . . . . . . . . . . . . . .5
J1708/J1587 Diagnostic Link . . . . . . . . . . . . . . . . . .6
Auxiliary I/O . . . . . . . . . . . . . . . . . . . . . . . . . . . . . . .6
ABS Flex
™
Program . . . . . . . . . . . . . . . . . . . . . . . . .6
Customer Scratch Pad . . . . . . . . . . . . . . . . . . . . . . .6
Power-up Sequence . . . . . . . . . . . . . . . . . . . . . . . . .6
ABS Operation . . . . . . . . . . . . . . . . . . . . . . . . . . . . .7
Auto-Con fi guration . . . . . . . . . . . . . . . . . . . . . . . . . .8
Odometer Function. . . . . . . . . . . . . . . . . . . . . . . . . .8
Non-standard Tire Size. . . . . . . . . . . . . . . . . . . . . . .8
Diagnostic Trouble Code Detection . . . . . . . . . . . . .8
Partial ABS Shutdown. . . . . . . . . . . . . . . . . . . . . . . .9
Blink Code Diagnostics. . . . . . . . . . . . . . . . . . . . . . .9
Diagnostic Trouble Codes (DTCs) . . . . . . . . . . . . .10
Using Hand-Held or PC-Based Diagnostics . . . . . .13
Bendix ABS Diagnostic Tools . . . . . . . . . . . . . . . . .13
Contacting Bendix. . . . . . . . . . . . . . . . . . . . . . . . . .14
Servicing the TABS-6 Module. . . . . . . . . . . . . . . . .15
Removing the TABS-6 Module . . . . . . . . . . . . . . . .15
Service Replacement of Other ABS Controllers . . .15
Reinstallation of the TABS-6 Module . . . . . . . . . . .15
Leakage And Operational Tests . . . . . . . . . . . . . . .16
ABS Wiring . . . . . . . . . . . . . . . . . . . . . . . . . . . . . . .16
Troubleshooting . . . . . . . . . . . . . . . . . . . . . . . . 17-31
1
SAFE MAINTENANCE PRACTICES
WARNING! PLEASE READ AND FOLLOW
THESE INSTRUCTIONS TO AVOID
PERSONAL INJURY OR DEATH:
When working on or around a vehicle, the following general precautions should be observed at all times:
1. Park the vehicle on a level surface, apply the parking brakes, and always block the wheels. Always wear safety glasses.
2. Stop the engine and remove ignition key when working under or around the vehicle. When working in the engine compartment, the engine should be shut off and the ignition key should be removed.
Where circumstances require that the engine be in operation, EXTREME CAUTION should be used to prevent personal injury resulting from contact with moving, rotating, leaking, heated or electrically charged components.
3. Do not attempt to install, remove, disassemble or assemble a component until you have read and thoroughly understand the recommended procedures. Use only the proper tools and observe all precautions pertaining to use of those tools.
4. If the work is being performed on the vehicle’s air brake system, or any auxiliary pressurized air systems, make certain to drain the air pressure from all reservoirs before beginning ANY work on the vehicle. If the vehicle is equipped with a Bendix
®
AD-IS
®
air dryer system or a dryer reservoir module, be sure to drain the purge reservoir.
5. Following the vehicle manufacturer’s recommended procedures, deactivate the electrical system in a manner that safely removes all electrical power from the vehicle.
6. Never exceed manufacturer’s recommended pressures.
7. Never connect or disconnect a hose or line containing pressure; it may whip. Never remove a component or plug unless you are certain all system pressure has been depleted.
8. Use only genuine Bendix ® brand replacement parts, components and kits. Replacement hardware, tubing, hose, fi size, type and strength as original equipment and be designed speci fi cally for such applications and systems.
9. Components with stripped threads or damaged parts should be replaced rather than repaired. Do not attempt repairs requiring machining or welding unless specifically stated and approved by the vehicle and component manufacturer.
10. Prior to returning the vehicle to service, make certain all components and systems are restored to their proper operating condition.
11. For vehicles with Automatic Traction Control (ATC), the ATC function must be disabled (ATC indicator lamp should be ON) prior to performing any vehicle maintenance where one or more wheels on a drive axle are lifted off the ground and moving.
2
COMPONENTS
Installations of the TABS-6 Module typically utilize the following components:
• Bendix
®
WS-24
™
wheel speed sensors (2 or 4, depending on con fi guration). Each sensor is installed with a Bendix Sensor Clamping Sleeve. See page 5.
• Bendix
®
BR9235
™
Pressure Modulator Valves (0, 1, or
2 depending on con fi guration). See page 5.
• Trailer-mounted ABS indicator lamp. See page 4.
• Pigtail wiring harness(es) as needed. See page 3.
MOUNTING CONFIGURATIONS
Tank (Nipple) Mount
The TABS-6 modules can be tank-mounted using a schedule 80 (heavy gauge steel) 3/4" NPT nipple directly between the trailer supply tank and the module's supply port. A tank with a reinforced port must be used.
Frame (Chassis) Mount
The TABS-6 module provides through-holes for frame mounting directly to the trailer frame rail or cross-member.
It is recommended to use two Grade 5 3/8-16 bolts, typical length 5", torqued to 180-220 in-lbs.
POWER LINE CARRIER (PLC)
COMMUNICATIONS
Since March 1, 2001, all new towed vehicles transmit a signal over the power line to an in-cab trailer ABS Indicator
Lamp. The signal, using a heavy vehicle industry standard known as “PLC4Trucks,” is typically broadcast by the trailer ABS ECU over the blue wire (power line) of the J560 connector. See Figures 2 and 3.
TABS-6 modules support PLC communications in accordance with SAE J2497.
Identifying and Measuring the PLC Signal
A TABS-6 module will continuously broadcast PLC messages that indicate trailer ABS status. At power-up or during a trailer ABS fault condition, the TABS-6 module will signal the tractor ABS unit to illuminate the dash-mounted trailer ABS indicator lamp.
Diagnostic tools are available that detect the presence of a PLC signal and perform further system diagnostics directly on the power line. For more information on these diagnostic tools, contact Bendix or refer to your local authorized Bendix dealer or distributor.
An oscilloscope can also be used to verify the presence and strength of a PLC signal on the power line. The PLC signal is an amplitude and frequency modulated signal.
Depending on the load on the power line, the amplitude of the PLC signal can range from 5.0 mV p-p to 7.0 V p-p.
FIGURE 2 - POWER LINE WITHOUT PLC SIGNAL
FIGURE 3 - POWER LINE WITH PLC SIGNAL
Suggested oscilloscope settings are (AC coupling, 1 volt/ div, 100 μ sec/div). The signal should be measured on pin
7 of the J560 connector at the nose of the trailer.
2-Pin Additional
Wheel Speed
Sensor
Connectors
(SAL & SAR)
5-Pin Power and
Indicator
Lamp (POWER/
WL)
3-Pin Modulator 2
(MOD2)
PIGTAIL WIRING HARNESSES
Several pigtail wire harnesses are available to connect the TABS-6 module with ABS and other trailer system components. Pigtail harness are weather sealed at the connector interface and are clearly labeled for proper installation. Because of the over-molded design of the
TABS-6 module wiring harnesses, Bendix recommends that the complete harness be replaced if damage or corrosion occurs.
The following connector options may be present:
Modulator 2 (MOD2), Modulator 3 (MOD3), auxiliary, diagnostic, and additional axle wheel speed sensors.
Note: All TABS-6 modules include the two primary wheel speed sensor connections and therefore these are separate from the pigtail harness.
ECU Connectors
Standard TABS-6 module ECU connectors use a TTMA
97-99 5-pin Packard Weather Pack connector for brake light power, constant power, ground, the trailer-mounted
ABS indicator lamp and a single auxiliary input/output (I/O).
Premium TABS-6 module ECU connectors use an 18-pin
Deutsch DT series connector for the same function as above, plus additional modulators, wheel speed sensors and auxiliary I/O’s.
18-Pin ECU Connector
Premium Pigtail Harness
(4S/2M with diagnostic)
4-Pin Diagnostic
Auxiliary
(Optional)
3-Pin Modulator 3
(MOD3) (Optional)
5XXX....
5XXX...
A
D
B
C
E
To TABS-6 Module
Pigtail
Modulator Extension Harness
To BR9235
™
ABS Modulator
Relay Valve
5-Pin Power and
Indicator Lamp
(POWER/WL)
Optional
Diagnostic
To Diagnostic
Tool
To TABS-6 Module
Pigtail
5XXX...
To ECU or Pigtail
Diagnostic Tool Harness
FIGURE 4 - EXAMPLES OF PIGTAIL WIRE HARNESSES AVAILABLE
Wheel Speed Sensor
Extension Harness
5-Pin ECU
Connector
Standard Pigtail Harness
(2S/1M) with optional diagnostic
To WS-24 ™ Wheel
Speed Sensor
3
Power/ABS Indicator Lamp Connector
The TABS-6 module pigtail uses a TTMA RP 97-99 5-pin
Packard Weather Pack connector for brake light power, constant power, ground and the trailer-mounted ABS indicator lamp.
The Power/ABS indicator lamp lead of the pigtail harness is available in several lengths to satisfy most installation requirements (e.g. slider axles).
Wheel Speed Sensor Connectors
Two 2-pin connectors are provided for additional wheel speed sensors for 4S ABS applications. These 2-pin connectors are labeled Additional Sensor Left (SAL), and
Additional Sensor Right (SAR). Extension cables are available in various lengths from Bendix.
ABS Modulator Connectors
On Premium TABS-6 module pigtail harnesses, one or two modulator connectors are provided for trailers using two or three modulators. These 3-pin connectors are labeled
MOD2 and MOD3. (Note: MOD1 designates the internal modulator of the TABS-6 module). Remote modulator harnesses are available in many lengths to satisfy most installation requirements.
Diagnostic Connector
Premium TABS-6 module pigtail harnesses provide a 4-pin diagnostic connection for a diagnostic tool to monitor ECU ignition power, ground and data information. Remote diagnostic cables are available from Bendix to provide a standard J1708/J1587 diagnostic port at the side of the trailer.
Auxiliary I/O Connector
Standard TABS-6 module pigtails provide an option for a single auxiliary I/O. An optional auxiliary connector provides a connection to the TABS-6 module auxiliary I/O
ECU pins. Premium ECU pigtails provides an option for up to six auxiliary I/O’s.
POWER AND GROUND
Trailer electrical power is supplied to the TABS-6 module from the ignition and brake light circuits. See Charts 1 and
2 for output values and pin locations.
Function Mode
Operating Range
ECU Active
Value
8.0 to 16.0 VDC
135 mA @ 12 VDC
ABS Active
(1 Modulator)
ABS Active
(2 Modulators)
3.7 A @ 12 VDC
5.2 A @ 12 VDC
CHART 1 – VALUES FOR OUTPUTS
Circuit
7-Pin 5-Pin 5-Pin 18-Pin
Trailer ABS ECU ECU
PLC
(Blue Wire)
Brake Light
Power
(Red Wire)
Ground
(White Wire)
Indicator Lamp
(White/green
Wire)
4
N/A
A A
E
D
CHART 2 – POWER AND GROUND
D
12
18
5
FIGURE 5 - TRAILER-MOUNTED ABS INDICATOR LAMP
ABS INDICATOR LAMP
Trailer-mounted Lamp
The TABS-6 module controls an ABS indicator lamp to show the trailer ABS status. With power supplied by the towing vehicle, the module illuminates the ABS indicator lamp by providing a 12.0 VDC signal. (The other side of the lamp is grounded.) The ABS indicator lamp output uses Pin D of the 5-pin Standard module connector, and Pin 5 of the
18-pin Premium module connector.
Dash-mounted Lamp (PLC Controlled)
TABS-6 modules use SAE J2497 standards to support
Power Line Carrier (PLC) communication. The TABS-6 module transmits a signal over the power line to the towing vehicle. This information is used by towing vehicle’s
ABS controller to know when to illuminate the trailer ABS indicator lamp mounted on the dash.
The status of the trailer ABS is transmitted over the ignition power wire (blue wire of the J560 connector), Pin B of the
5-pin Standard module connector, or Pin 6 of the 18-pin
Premium module connector.
4
BENDIX
®
WS-24
™
WHEEL SPEED SENSORS
Wheel speed data is provided to the TABS-6 module from the WS-24
™
wheel speed sensors (see Figure 6). Vehicles have an exciter ring (or “tone ring”) as part of the wheel assembly, and as the wheel turns, the teeth of the exciter ring pass the wheel speed sensor, generating an AC signal.
The TABS-6 module receives the AC signal, which varies in voltage and frequency as the wheel speed changes. (The default setting expects a 100-tooth tone ring to be used.)
Vehicle axle and ABS control con fi gurations determine if two or four wheel speed sensors are required. See page
17 for electrical system schematics showing wheel speed sensor connector pin locations.
A proper sensor installation is critical to correct ABS operation.
Typically, the WS-24
™
sensor is installed in mounting blocks that are welded to the axle housing. WS-24 ™ wheel speed sensors are protected by a stainless steel sheath. They are designed to be used with beryllium copper clamping sleeves (sometimes referred to as a “retainer bushing”,
“friction sleeve” or “clip”) (See Figure 6). The clamping sleeve provides a friction fi t between the mounting block bore and the WS-24
™
sensor.
90° Speed
Sensors
Straight Speed
Sensors
Sensor
Clamping
Sleeve
Logo Stamped into Sleeve
5. Engage the connectors, and push together until the lock tab snaps into place.
NOTE: It is important for the wheel bearings to be adjusted per the manufacturer's recommendations.
The friction fi t allows the WS-24
™
sensor to slide back and forth under force but to retain its position when the force is removed. When the WS-24 ™ sensor is inserted all the way into the mounting block and the wheel is installed on the axle, the hub exciter contacts the sensor, which pushes the sensor back. Also, normal bearing play will “bump” the sensor away from the exciter. The combination of these two actions will establish a running clearance or air gap between the sensor and exciter.
Excessive wheel end play can result in diagnostic trouble codes in cases where the sensor is pushed too far away from the tone ring.
BENDIX
®
BR9235
™
ABS
MODULATOR RELAY VALVES
Bendix ® BR9235 ™ modulator relay valves (MRV) are required when additional modulator relay valves are needed for multichannel brake systems (e.g. 2S/2M, 4S/3M
ABS con fi gurations).
The MRV is an electro-pneumatic control valve and is the last valve that air passes through on the way to the brake chambers. The normally-open hold solenoid and normallyclosed exhaust solenoid are activated to precisely modify the brake pressure on command. During normal braking, the BR9235 ™ MRV functions as a standard relay valve. As brakes are applied or released by the driver, the control signal from the tractor foot valve causes the BR9235
™
MRV to apply proportional pressure to the trailer brake chambers.
The BR9235
™
MRV is available in both tank and bracket mounting styles.
FIGURE 6 - BENDIX ® WS-24 ™ WHEEL SPEED SENSORS
1. For increased corrosion protection we recommend that a high-temperature rated silicon- or lithium-based grease be applied to the interior of the mounting block, the sensor, and to a new clamping sleeve.
2. Install the new clamping sleeve fully into the block, with the retaining tabs toward the inside of the vehicle.
Please note that WS-24 ™ wheel speed sensors must use the correct clamping sleeve to avoid problems associated with reduced retention force, such as sensor movement and resulting ABS trouble codes.
3. Gently push (DO NOT STRIKE) the sensor into the mounting block hole until it bottoms out on the face of the tone ring. Secure the cable lead wire to the knuckle/ axle housing 3-6 inches from the sensor.
4. Apply a moderate amount of dielectric non-conductive grease to both the sensor connector and harness connector.
3-Pin Modulator
Solenoid
Connector
3/8" NPT Supply
Port with Integral
Filter
Four 3/8" NPT Delivery Ports
(to Brake Chambers)
FIGURE 7 - BENDIX
®
BR9235
™
MODULATOR RELAY
VALVE
5
Tank (Nipple) Mounted
The BR9235 ™ MRV can be tank-mounted using a schedule
80 (heavy gauge steel) 3/4" NPT nipple directly between the trailer supply tank and the supply port. A tank with a reinforced port must be used.
Bracket (Chassis) Mounted
The BR9235
™
MRV provides an option with a bracket for frame mounting directly to the trailer frame rail or crossmember. It is recommended to use two Grade 5,
3/8-16 bolts, torqued to 180 – 220 in-lbs.
J1708/J1587 DIAGNOSTIC LINK
The Premium TABS-6 module provides a J1708/J1587 diagnostic link with data and power to communicate with the vehicle and various diagnostic tools. Diagnostics, testing, con fi guration, data transfer and other functions can be performed using this link. Diagnostic tools such as the MPSI Pro-Link ™ device and Bendix ® ACom ® Diagnostic
Software (version 4.0 and higher) support the TABS-6
Module.
Ignition power must be provided to the TABS-6 module for the diagnostic link to be active.
AUXILIARY I/O
The Standard module provides for one auxiliary I/O function.
The Premium module provides for up to fi ve auxiliary functions and one additional ground. See Chart 3, below.
Bendix
®
ACom
®
Diagnostic Software (version 4.0 and higher) supports the con fi guration of the TABS-6 module auxiliary I/O’s.
ABS FLEX
™
PROGRAM
The ABS Flex
™
program uses Auxiliary Design Language
(ADL) to allow customized auxiliary functions to be carried out by the TABS-6 module. Programs developed in the ABS
Flex ™ program may be downloaded at the production line or in the fi eld to control non-braking functions of the trailer.
For example, ABS Flex ™ program can potentially communicate the status of: tire in fl ation and/or temperature; reefer temperature; load presence; slider pin position; lift axle position; proximity/reverse alarm; and vehicle weight.
ABS Flex
™
programs monitor the auxiliary I/Os and/or the
SAE J1587 diagnostics and SAE J2497 PLC data links.
Contact your Bendix Account Manager to discuss an ABS
Flex
™
program for your vehicle(s).
CUSTOMER SCRATCH PAD
The TABS-6 module has a Customer Scratch Pad feature which allows the customer, or end-user, to store up to 756 bytes of information. This information can then be read using the Bendix ® ACom ® Diagnostic Software (version
4.0 and higher).
If additional scratch pad space is needed, this storage space can be expanded to 1K (1,008 bytes total of data).
Contact Bendix for further details.
POWER-UP SEQUENCE
At power-up, the TABS-6 module performs a series of selfchecks that can assist a technician to determine the ABS system status and con fi guration.
Name ECU ECU Pin Auxiliary Functions
AUX Standard C
• High-Side Driver… or Digital Input… or • Analog Input
AUX1 Premium
AUX2
AUX3
AUX4
AUX5
Premium
Premium
Premium
Premium
16 • High-Side Driver… or Digital Input
10 • High-Side Driver… or Digital Input
15 • High-Side Driver… or Digital Input
9 • High-Side Driver… or Digital Input
4 • Low-Side Driver… or Analog Input
AUX6 Premium 3 • High-Side Driver… or Digital Input
CHART 3 – AUXILIARY I/OS AND DEFAULT FUNCTIONS
Default Function
None
Modulator 3 (MOD3)
Modulator 3 (MOD3)
Modulator 2 (MOD2)
Modulator 2 (MOD2)
Modulator 3 (MOD3)
Common
J1587 Diagnostic Power
6
ABS System
Status Indicators
Trailer-mounted ABS
Indicator Lamp
ON
OFF
Dash-mounted Trailer
ABS Indicator Lamp
(PLC Detected)*
ON
OFF
Dash-mounted Trailer
ABS Indicator Lamp
(PLC Not Detected)
ON
OFF
Power
Application
0.5
1.5
2.0 2.5 3.0 (sec.)
*Some vehicle manufacturers may illuminate the trailer ABS indicator lamp at power-up regardless of whether a PLC signal is detected from the trailer or not. Consult the vehicle manufacturer’s documentation for more details.
FIGURE 8 - TRAILER ABS LAMP START UP SEQUENCE
Trailer ABS Indicator Lamp
At power-up without detected faults, the trailer ABS indicator lamp will turn on for 2.5 seconds as a bulb check and then turn off. See Figure 8.
If a PLC-ready towing vehicle and trailer are powered at the same time, the TABS-6 module will also trigger a bulb check on the dash-mounted trailer ABS indicator lamp.
Modulator Chuff Test at Power-Up
At power-up, the TABS-6 module activates a modulator chuff test. This electrical and pneumatic ABS modulator test can help the technician identify problems with modulator installations and/or wiring.
With brake pressure applied, a properly installed modulator will cause fi ve rapid audible chuffs of air pressure. If additional modulators are installed, the TABS-6 module activates 5 chuffs at the internal modulator (MOD1) then for each additional modulator in sequence (e.g. MOD1, then MOD2, and then MOD3). The chuff sequence is then repeated.
If the modulator is wired incorrectly, the modulator will only produce one chuff, or no chuff at all. If an issue is detected during the modulator chuff test, compare the modulator wiring and plumbing to the TABS-6 module’s electrical system schematic (see page 17) and make repairs.
ABS OPERATION
The TABS-6 module uses wheel speed sensors, modulator relay valves and an ECU to control trailer wheels by axle or by side. By monitoring individual wheel turning motion during braking, and adjusting or pulsing the brake pressure at each wheel, the TABS-6 module is able to optimize slip between the tires and the road surface. When excessive wheel slip, or wheel lock-up, is detected, the ECU will activate the Pressure Modulator Valves to modulate braking pressure at the wheel ends. The ECU is able to pump the brakes on individual wheels (or pairs of wheels), independently, and with greater speed and accuracy than a driver.
Axle Control
TABS-6 module axle control uses a single modulator relay valve to control wheels on both sides of a given axle or axles. In the case of an ABS event on road surfaces with poor traction (worn, slippery, or loose gravel roads) or areas of poor traction, (e.g. asphalt road surfaces with patches of ice), axle control will maintain the wheel that is not slipping at just under the speed that will lock the wheel. Temporary periods of wheel lock are permitted on the other wheel that is experiencing slippage.
Axle control should not be used on 5th wheel dollies or steerable axles. When braking on even surfaces, an axle-control system will perform similar to a side control, two-modulator system. Axle control is available in 2S/1M,
2S/2M and 4S/2M installations, and for Modulator 3
(MOD3) in a 4S/3M installation.
Dolly-Axle Control (Select Low)
TABS-6 module dolly-axle control uses a single ABS modulator valve to control wheels from both sides of a given axle or axles. In the case of an unbalanced braking surface, (e.g. asphalt road surfaces with patches of ice), dolly axle control will control the low coef fi cient (slipping) wheel just under the lock limit. Vehicle stability is assisted by not allowing the high coef fi cient wheel (where traction is still being maintained) to sustain wheel lock.
When braking on even surfaces, a dolly axle control system will perform similar to side control or axle control system.
Dolly axle control is only available in 2S/1M installations.
Side Control
The TABS-6 module uses a single modulator relay valve to control one or more wheels on a given vehicle side. In the case of an unbalanced braking surface, the side control will individually control wheels on each side just under the point where they would lock up.
Side control is available in 2S/2M and 4S/2M installations, and for the internal modulator (MOD1) and Modulator 2
(MOD2) in the 4S/3M installation.
Normal Braking
During normal braking, the TABS-6 module functions as a standard relay valve. If the ECU does not detect excessive wheel slip, it will not activate ABS control, and the vehicle stops with normal braking.
7
AUTO-CONFIGURATION
The Standard TABS-6 module is available only in the 2S/1M
ABS con fi guration and does not use auto-con fi guration.
For the Premium TABS-6 module, the default ABS con fi guration is 2S/1M. At power-up, if a Premium ECU detects additional sensors and modulators it will perform an auto-con fi guration. Auto-con fi guration only adjusts upward (e.g. 2S/2M Side to a 4S/2M Side con fi guration).
Additional detected components that do not conform to a legitimate con fi guration will generate the appropriate faults.
If the vehicle begins moving before the new con fi guration has been accepted, the recon fi guration will not take place at this time.
Default
Sensors
2S/1M
Dolly Axle
2S/1M
Axle
-
2
-
2
2
1
1
1
1
2
Auto-Confi guration
to 2S/2M (Side) to 4S/2M (Side) to 4S/3M (Side/Axle) to 2S/2M (Axle) to 4S/2M (Axle)
CHART 4 – PREMIUM TABS-6 MODULE AUTO-
CONFIGURATION MATRIX
ODOMETER FUNCTION
Odometer
The TABS-6 module includes an odometer function to provide a means of storing the accumulated mileage of the vehicle. The mileage is computed by utilizing information calculated from the vehicle wheel speeds.
This feature is accurate to within 0.62 miles per power-up and will typically store mileage up to 1,000,000 miles. The mileage can be displayed using PC diagnostics or through blink codes.
Whenever the module is towed using a pre-1997 tractor, the electronic odometer does not function, and the mileage can be considered out-of-calibration.
Trip Counter
The module provides a counter to record the trip mileage.
The feature is accessed through PC or hand-held diagnostic tools.
Service Interval
The TABS-6 module provides a feature that can be used to indicate a service interval for the trailer. The service interval can be accessed via PC or hand-held diagnostic tools. If con fi gured, the TABS-6 module can fl ash the indicator lamp when the vehicle is at standstill to indicate when the service interval has been exceeded.
NON-STANDARD TIRE SIZE
The module allows for tire rolling radius and tone ring tooth count parameters to be set for each axle using a diagnostic tool. These adjustments may be necessary for the module to accurately calculate the vehicle velocity and odometer mileage. Wheels of the same axle must be set to the same rolling radius and tone ring tooth count. In most cases, these parameters are set by the trailer OEM and do not need to be adjusted. In the case of a service replacement unit, always check that these parameters are set to match the vehicle.
The tire-rolling radius is defaulted to 500 revs/mile and can be adjusted from 300 to 700 revolutions per mile. Refer to the manufacturer’s tire speci fi cation for correct values.
Tone ring tooth count is defaulted to 100 teeth and can be set from 60 to 140 teeth.
DIAGNOSTIC TROUBLE CODE DETECTION
The TABS-6 module contains self-testing diagnostic circuitry that monitors the ABS components and wiring.
When the module senses an erroneous system condition, it activates the external trailer-mounted ABS indicator lamp, disables all or part of the affected ABS functions, and it stores the fault code in memory, even when the power is removed. The module also uses PLC communications to send the system status to the towing vehicle.
For some trouble codes, the TABS-6 module will automatically reset (“self-heal”) the active diagnostic trouble code when the error is corrected (e.g. when a wheel speed sensor is re-aligned). However, repeated occurrences of a given trouble code can cause the code to
“latch” - that is, be retained as active, even if the condition is only intermittent. Once the code is latched, a manual reset will be necessary. Technicians can use these latched codes to assist them in troubleshooting intermittent errors.
After the problem is repaired, trouble codes can be reset using blink code diagnostics or with a diagnostic tool.
When a trouble code self-heals or is manually reset, the code remains stored in the ECU memory. This trouble code history can be retrieved using blink code diagnostics or with a diagnostic tool.
8
PARTIAL ABS SHUTDOWN
Depending on the trouble code detected, the ABS ECU partly or completely disables the ABS functionality.
The trailer ABS system, for vehicles that only have one modulator, are disabled by any single fault. In the case of vehicles with two or three modulators, depending on the trouble code, the trailer ABS system may still provide some level of ABS function on axles/wheels that are not affected by the fault, but the ABS indicator lamp will remain on. In cases where the ABS is completely disabled, the vehicle reverts to normal braking (without ABS interventions).
Always repair ABS shutdowns at the earliest opportunity.
ECU Diagnostic Trouble Codes
All ABS functions are completely disabled. The system reverts to normal braking.
Voltage Diagnostic Trouble Code
While voltage is out of range, the ABS functionality is disabled and the system reverts to normal braking. When the correct voltage level is restored, full ABS is typically available again. The operating voltage range is 8.0 to
16.0 VDC.
BLINK CODE DIAGNOSTICS
The TABS-6 module provides diagnostic and con fi guration functions through blink code diagnostics. This means that the technician, even without diagnostic tools, can read a series of ABS indicator lamp blinks to diagnose the trouble codes being generated.
The blink code diagnostics mode is entered by providing constant power to the ignition circuit and toggling the brake light power input three times. With a parked towing vehicle attached, this is done by applying ignition power and after the power up sequence is complete, depressing and releasing the brake pedal three or more times, see chart 5 below.
Depending on the blink code mode activated, the TABS-6 module will blink the trailer-mounted ABS indicator lamp to display: active fault codes; fault code history;
ABS con fi gurations; and odometer mileage. Blink code diagnostics can also be used to reset active fault codes.
With Ignition Power
Applied, Cycle Brake
Blink Code
Action
Wait until after the modulator chuff test before activating the brake light power. Following a single display of all available messages, the ABS indicator lamp will remain on for fi ve seconds and then return to normal operating mode.
Blink code diagnostics can only be activated following a power-up, where wheel speeds have not been detected. If the vehicle moves during blink code diagnostics mode, the module will cancel the blink code diagnostics and return to normal operating mode.
Blink code diagnostics must be activated within the fi rst 15 seconds of ignition power being applied.
If brake light power is continuously applied for greater than fi ve seconds, blink code diagnostics will be disabled until the next time the ignition power is cycled.
Display Active Diagnostic Trouble Codes
To display active codes, apply ignition power and depress
/ release the brake pedal 3 times within 15 seconds.
Following activation, there will be a 5-second delay followed by a blink code display of all active fault codes. (See pages
10-12 for more information.)
Display Diagnostic Trouble Code History
To display trouble code history, apply ignition power and depress / release the brake pedal 4 times within 15 seconds. Following activation, there will be a 5-second delay followed by a blink code display of all history fault codes. (See pages 10-12 for more information.)
Reset Active Diagnostic Trouble Codes
To reset active codes, apply ignition power and depress
/ release the brake pedal 5 times within 15 seconds.
Following activation, there will be a 5-second delay followed by a blink code message of:
1-1, (System Fully Operational - No Codes Detected) or a blink code display of all remaining active fault codes.
The ABS indicator lamp will stay on if active DTCs are still present.
Resetting active fault codes with blink code diagnostics does not clear information from trouble code history. Both blink code diagnostics or diagnostic tools can retrieve trouble code history, but only diagnostic tools can erase this information.
3 times
4 times
5 times
6 times
7 times
8 times
Display Active DTCs
Display Inactive DTCs
Clear Active DTCs
Display Con
Display Odometer Mileage
Reset Con
CHART 5 – BLINK CODE INFORMATION
fi fi guration
guration
9
Display Con
fi
guration
To check the ABS con fi guration, apply ignition power and depress / release the brake pedal 6 times within 15 seconds. Following activation, there will be a 5-second delay followed by a blink code display of the module's current ABS con fi guration.
1st Digit Sensors
2
2
4
4
2nd Digit Modulators
1
1
2
2
3
3
3rd Digit ABS Control Mode
1
Axle
2
Side
3
Dolly-Axle
4
5
MOD1 Axle - MOD2 Dolly-Axle
MOD1 Axle - MOD2 Lift Axle
6
Side (MOD1, MOD2) - MOD3 Dolly-Axle
CHART 6 – ABS CONFIGURATIONS
Display Odometer Mileage
To display the trailer odometer mileage, apply ignition power and depress / release the brake pedal 7 times within
15 seconds. Following activation, there will be a 5-second delay followed by a blink code display of the odometer information (x1000).
Example: 152,431 miles will be displayed as: 152 (x1000) or 1 blink (pause), 5 blinks (pause), 2 blinks.
Zeros will be displayed by the ABS indicator lamp strobing twice.
Odometer mileage cannot be altered with blink code diagnostics. Complete odometer information can be retrieved using a diagnostic tool.
Resetting ABS Con
fi
guration
To reset the ABS con fi guration to the default con fi guration, apply ignition power and depress / release the brake pedal 8 times within 15 seconds. Following activation, the TABS-6 ABS con fi guration will reset to the default ABS con fi guration (2S/1M).
Diagnostic Trouble Codes
(DTCs)
1
2
3
4
5
2
3
4
5
4
5
2
3
4
5
2
3
4
5
2
3
4
5
1st 2nd Fault Description
Digit Digit
Repair Information
1 No faults • ABS system fully operational – no faults detected
WHEEL SPEED SENSORS (WSS)
1 SL Sensor signal valid - large air gap
1 SR Sensor signal valid - large air gap
1 SAL Sensor signal valid - large air gap
1 SAR Sensor signal valid - large air gap
2 SL Sensor signal valid - loss of signal
2 SR Sensor signal valid - loss of signal Dynamic Wheel Speed Sensor Fault.
2 SAL Sensor signal valid - loss of signal
2 SAR Sensor signal valid - loss of signal
Go to Section G, on Page 29.
3 SL Sensor signal valid – noisy
3 SR Sensor signal valid – noisy
3 SAL Sensor signal valid – noisy
3 SAR Sensor signal valid – noisy
4 SL Sensor shorted or open
4 SR Sensor shorted or open
4 SAL Sensor shorted or open
4 SAR Sensor shorted or open
5 SL Tire diameter out of range
5 SR Tire diameter out of range
5 SAL Tire diameter out of range
5 SAR Tire diameter out of range
6 SAL Sensor con fi guration error
6 SAR Sensor con fi guration error
Static Wheel Speed Sensor Fault.
Go to Section G, on Page 29.
• Verify correct tire size as desired.
• Verify proper tire in fl ation.
• Verify correct number of exciter ring teeth.
• Verify that the ECU has the proper tire size settings.
• Verify correct ABS con fi guration using blink codes
or other diagnostic tools.
• If needed, reset to the default ABS con fi guration and
power-up to initiate auto-con fi guration.
J1587 J1587
(SID) (FMI)
1 0
1
2
3
4
1
2
3
4
1
2
3
4
1
2
3
4
1 4 or 5
2 4 or 5
3 4 or 5
4 4 or 5
3
13
13
13
13
13
1
1
1
1
0
0
0
0
2
2
2
2
4 13
10
Diagnostic Trouble Codes
(DTCs)
(continued)
1st 2nd
Fault Description
Digit Digit
Repair Information
J1587
(SID) (FMI)
6
6
6
10
10
10
10
7
7
8
9
8
9
7
8
9
8
9
1 Over-voltage
2 Low-voltage
3 Excessive power line resistance
1 MOD1 Hold solenoid shorted or open
2 MOD1 Release solenoid shorted or open
1 MOD2 Hold solenoid shorted or open
1 MOD3 Hold solenoid shorted or open
2 MOD2 Release solenoid shorted or open
2 MOD3 Release solenoid shorted or open
3 MOD1 ABS modulator dynamic error
3 MOD2 ABS modulator dynamic error
3 MOD3 ABS modulator dynamic error
4 MOD2 Valve con fi guration error
4 MOD3 Valve con fi guration error
1 Valve MOD1/2 low-side switch shorted to ground
2 Valve MOD3 low-side switch shorted
to ground
3 ABS modulator dynamic error - all valves
4 Excessive ABS activity
POWER
• Power supply diagnostic trouble code.
Go to Section F, page 28.
• Power supply diagnostic trouble code.
Go to Section F, page 28.
• Power supply diagnostic trouble code.
Go to Section F, page 28.
MODULATOR (MOD)
• Clear faults.
• If faults return, replace the TABS-6 Module.
Static ABS Modulator Fault.
Go to Section H, on Page 30.
Dynamic ABS Modulator Fault.
Go to Section H, on Page 30.
• Verify correct ABS con fi guration using blink codes
or other diagnostic tools.
• If needed, reset to the default ABS con fi guration
and power-up to initiate auto-con fi guration.
COMMON
• Check for corroded/damaged wiring or connectors
between the ECU and MOD.
At the MOD harness connector, verify:
• No continuity from modulator/AUX leads to ground.
• After repairs or if no issues found, then clear faults.
• If faults return, replace the TABS-6 Module.
Dynamic ABS Modulator Fault.
Go to Section H, on Page 30.
Dynamic Wheel Speed Sensor Fault.
Go to Section G, on Page 29.
11 1 ECU internal error
11 2 ECU fi guration error
ELECTRONIC CONTROL UNIT (ECU)
• Check for damaged or corroded connectors.
• Check for damaged wiring.
• After repairs or if no issues found, then clear faults.
• If faults return, replace the TABS-6 Module.
• Verify correct ABS con fi guration using blink codes,
PC-diagnostics or other off-board diagnostic tools.
• If needed, reset to the default ABS con fi guration and
power-up to initiate auto-con fi guration.
251
251
251
3
4
13
42 3, 4, 5
6 or 12
48 3, 4, 5
6 or 12
43 3, 4, 5
6 or 12
44 3, 4, 5
6 or 12
49 3, 4, 5
6 or 12
50 3, 4, 5
6 or 12
7
8
9
7
7
7
8 13
9 13
7
9
7
1
254
254
4
4
7
7
12
13
(Continued over . . .)
11
Diagnostic Trouble Codes
(DTCs)
(continued)
1st 2nd
Fault Description
Digit Digit
Repair Information
J1587
(SID) (FMI)
12
13
1 J1587 diagnostics shorted or open
1 ABS lamp shorted or open
J1587 DIAGNOSTIC
• Check for corroded/damaged wiring or connectors
between the ECU and J1587 Diagnostic.
• Verify the following:
- At the 18-pin ECU harness connector:
(a) Continuity of the J1587 Diagnostic wiring to the
lamp (auxiliary device).
(b) +12V is not measured at J1587 Diagnostic lead.
- At J1587 Diagnostic connector:
(a) No continuity of the J1587 Diagnostic lead to
ground.
(b) No continuity from J1587 Diagnostic lead to any
other ECU pin(s).
(c) Replace/repair J1587 Diagnostic wiring or
components as required.
TRAILER-MOUNTED ABS INDICATOR LAMP
• Check for corroded/damaged wiring or connectors
between the ECU and ABS Indicator Lamp.
• Verify the following:
- At the 5-pin or 18-pin ECU harness connector:
(a) Continuity of the ABS Indicator Lamp wiring
to the lamp (auxiliary device).
(b) +12V is not measured at ABS Indicator Lamp lead.
- At ABS Indicator Lamp connector:
(a) No continuity of the ABS Indicator Lamp lead to
ground.
(b) No continuity from ABS Indicator Lamp lead to any
other ECU pin(s).
(c) Replace/repair ABS Indicator Lamp wiring or
components as required.
250 3, 4, 5
or 12
81 3, 4, 5
or 12
12
Troubleshooting: Using Hand-Held or
PC-Based Diagnostic Tools
USING HAND-HELD OR PC-
BASED DIAGNOSTICS
Troubleshooting and diagnostic trouble code clearing, as well as beginning a recon fi guration, may also be carried out using hand-held or PC-based diagnostic tools such as the Bendix
®
Trailer Remote Diagnostic Unit (TRDU
™
),
Bendix
®
ACom
®
Diagnostics software, or the ProLink tool.
BENDIX ABS DIAGNOSTIC TOOLS
Bendix ® ACom ® Diagnostic Software
Bendix ® ACom ® Diagnostic Software (version 4.0 or higher) is an RP-1210A compliant PC-based diagnostic software program that provides the highest level of diagnostic support for the TABS-6 module. With Bendix
®
ACom
®
Diagnostic Software, maintenance personnel can:
• Obtain fault information (both active and inactive faults)
• Retrieve event history
• Clear inactive faults and event history
• Verify ECU con fi guration
• Perform system and component tests
• Read/write customer information on scratch pads
• Save and print information
• Receive troubleshooting assistance
When diagnosing the TABS-6 module using a PC and
Bendix
®
ACom
®
Diagnostic Software, the computer’s serial or parallel port can be connected to the vehicle’s diagnostic connector through a RP-1210A compliant communications device.
For more information on the Bendix ® ACom ® Diagnostic
Software, or RP-1210A compliant tools, contact Bendix or refer to your local authorized Bendix parts outlet.
LED lights illuminate
Diagnostic
Trouble Codes
(10 LEDs)
FIGURE 10
-
THE BENDIX ® TRAILER REMOTE
DIAGNOSTIC UNIT
Bendix
®
TRDU
™
(Trailer Remote Diagnostic Unit)
Tool
The Bendix
®
TRDU
™
tool provides the technician with a visual indication of Antilock Braking System (ABS) component
Diagnostic Trouble Code (DTC)
information.
The TRDU
™
tool is speci fi cally designed for use with
Bendix
®
Trailer ABS systems and Bendix makes no claims for its operation and/or usability with other brands of trailer
ABS.
Features of the Bendix
®
TRDU
™
Tool
The TRDU
™
tool attaches to a 7-pin to 7-pin adapter (See
Figure 12) and then into the J560 of the towing vehicle.
The TRDU ™ tool communicates across PLC.
The TRDU ™ tool allows the technician to:
• Troubleshoot ABS system component problems using
Diagnostic Trouble Code reporting via LEDs.
• Reset Diagnostic Trouble Codes on Bendix ® ABS ECUs by holding a magnet over the reset of the TRDU ™ tool for less than 6 seconds.
• Initiate a self-con fi guration event Mode used by Bendix
®
ABS ECUs by holding a magnet over the reset area for greater than 6 seconds but less than 11 seconds.
Lap Top Computer
J1708/J1587 or J1939
PDM (RP-1210A)
Parallel or Serial
Cable
FIGURE 9 - BENDIX ABS DIAGNOSTIC SOFTWARE
LED Diagnostic Trouble Codes
VLT - Power
ECU - ABS Controller
SEN - Wheel Speed
Sensor
MOD1 - Modulator 1
MOD2 - Modulator 2
MOD3 - Modulator 3
LFT - Left
RHT - Right
ADD - Additional
ODO - Odometer
Example: If the Diagnostic
Trouble Code is "Right
Additional Sensor", the
TRDU ™ tool will display one green and three red
LEDs
LEDs
Green
VLT
Blue
ODO
All others are
Red
FIGURE 11 - DIAGNOSTIC TROUBLE CODES
13
to Trailer
Connector
TRDU
™
Tool
to Towing
Vehicle
J560
Connector
Adapter
FIGURE 12 - TRDU ™ TOOL AND ADAPTER
How the Bendix
®
TRDU
™
Tool Operates
When the TRDU
™
tool is plugged into the adapter, and the adapter/TRDU
™
tool is installed between the trailer connector and the J560 connector of the towing vehicle, all the LEDs will illuminate, and the green LED will fl ash 4 times to indicate communications have been established.
If the ABS ECU has no active Diagnostic Trouble Codes, only the green LED will remain illuminated.
If the ABS ECU has at least one active Diagnostic
Trouble Code the TRDU ™ tool displays the fi rst diagnostic trouble code by illuminating the red LEDs, indicating the malfunctioning ABS component and its location on the vehicle. (See Figure 13.) If there are multiple diagnostic trouble codes on the ABS system, the TRDU ™ tool will display one diagnostic trouble code fi rst, then once that
Diagnostic Trouble Code has been repaired and cleared, the next code will be displayed.
The TRDU
™
tool repeatedly blinks out the mileage stored once communications have been established. By counting the sequence of blinks and/or strobes on the blue LED the odometer reading is given. See page 10 for more details.
•
VLT (Flashing indicates either over- or under-voltage condition)
To pinpoint the root cause and to ensure the system diagnostic trouble code is properly corrected the fi rst time, additional troubleshooting may be necessary.
Bendix
®
TRDU
™
Tool Reset Function
The magnetic reset switch is located by the letter "B" in the Bendix logo on the top of the TRDU ™ tool. Activation requires a magnet with 30 gauss minimum.
The reset operations are:
1. If the magnet is held over the switch for less than 6 seconds the "clear diagnostic trouble codes" command is sent.
2. If the magnet is held over the switch for more than 6 seconds, but less than 11 seconds, the Bendix
®
ABS
"self-con fi guration command" is sent.
Additionally, it is recommended at the end of any inspection that the user switches off and restores the power to the
ABS ECU, then check the ABS Indicator Lamp operation and TRDU ™ tool to see if they indicate any remaining
Diagnostic Trouble Codes.
MPSI Bendix Cartridge
MPSI provides a Bendix cartridge for use with the
Pro-Link ™ tool. For more information on the Bendix diagnostic cartridge from MPSI, contact Bendix or refer to your local authorized Bendix parts outlet.
PLC Diagnostic Tool
Diagnostic tools are available that detect the presence of a PLC signal and perform further system diagnostics directly on the power line. For more information on these diagnostic tools, contact Bendix or refer to your local authorized Bendix parts outlet.
CONTACTING BENDIX
www.Bendix.com
The Bendix on-line troubleshooting guide will help you determine the cause performance issues with your braking system.
Pro-Link
Heavy Duty
Multi Protocol
Cartridge
PC Card MPSI
Part Number
805013
FIGURE 14 - NEXIQ (MPSI) PRO-LINK TOOL
The Bendix on-line contacts directory will make it easy for you to fi nd the Bendix contacts you need. From this page, you can navigate to technical support contacts, service engineers, Bendix account managers, international contacts and more. Bendix.com is your complete Bendix resource.
Bendix Technical Assistance Team
For direct personal technical support, call the Bendix technical assistance team at:
1-800-AIR-BRAKE
(1-800-247-2725),
FIGURE 13 - TRDU ™ TOOL LED LOCATIONS
14
Monday through Friday, 8:00 A.M. to 6:00 P.M. EST, and follow the instructions in the recorded message.
Alternatively, you may e-mail the Bendix technical assistance team at: [email protected].
To better serve you, please record the following information before you call the Bendix Tech Team, or include this information in your e-mail:
• Bendix product model number, part number and con fi guration.
• Vehicle make and model.
• Vehicle con fi guration. (Number of axles, tire size, etc.)
• System performance symptoms: When do they occur?
• What faults have been identi fi ed using LEDs, blink codes or diagnostic tools?
• What troubleshooting/measurements have been performed?
• What Bendix service data literature do you have or need?
SERVICING THE TABS-6 MODULE
CAUTION: All TABS-6 modules are initially defaulted to 2S/1M and may auto-con
fi
gure to another ABS con
fi
guration if additional sensors and/or ABS modulators are detected. An incorrect
ABS con
fi
guration may cause fault indication or degraded ABS performance. Before and after activating a self-con
fi
guration, always check the current ABS con
fi
guration by using blink code diagnostics or a diagnostic tool.
Prior to performing service to the TABS-6 module, always perform the following steps:
1. Follow all Safe Maintenance Practices including, but not limited to, those on page 2 of this document.
2. Turn power off.
3. Drain the air pressure from all reservoirs.
4. Remove as much contamination as possible prior to disconnecting electrical connections and air hoses.
5. Note the TABS-6 module's mounting position on the vehicle.
REMOVING THE TABS-6 MODULE
1. Open the cover by sliding the locking tab to the left.
Retain the cover.
2. Disconnect the 5- or 18-pin ECU connector and the two
2-pin wheel speed sensor connectors.
3. Mark for reinstallation and then remove all air hoses and plugs connected to the module.
4. Remove the module from the vehicle by removing the mounting fasteners or by rotating the entire assembly counter-clockwise from the tank mount.
SERVICING THE CONTROL PORT FILTER
The TABS-6 module has an in-line fi lter in the control port
(See Figure 1). This fi lter should be inspected and cleaned
(if any contamination is found), every four months, 34,000 miles or 1,200 operating hours. For severe applications, this inspection interval may be reduced. If the fi lter is found to be damaged, install a replacement. The fi lter should also be inspected as part of any troubleshooting where the service brakes are slow to apply and other possible causes have been ruled out.
SERVICE REPLACEMENT OF
OTHER ABS CONTROLLERS
The TABS-6 module is designed to be used as the service replacement part for the Bendix ® MC-12 ™ ,
MC-30 ™ and A-18 ™ trailer ABS controllers. When controller service replacement parts are required, a
TABS-6 module and pigtail harness must replace the entire MC-12 ™ , MC-30 ™ or A-18 ™ controller assembly and pigtail harness. When replacing an MCE-12 ™ controller, the integral emergency function (EV-2
™ valve) must be replaced by a DC-4
®
and TR-3
™
valve combination. See pages 18-21 for plumbing details. TABS-6 module kits are available to replace MC-12 ™ , MC-30 ™ and A-18 ™ controller assemblies and harnesses. For more information, contact
Bendix or your local authorized Bendix parts outlet.
1. Disconnect the power connector and wheel speed sensors from the MC-12
™
, MC-30
™
or A-18
™
controller pigtail harness.
2. Remove all air hoses and plugs connected to the unit.
3. Remove the MC-12
™
, MC-30
™
or A-18
™
controller assembly and pigtail from the vehicle by removing the mounting bracket nuts or by rotating the entire assembly counter clockwise from the tank nipple mount.
4. Install the new pigtail, starting at the power connector and properly securing the harness every 18 inches to the ECU location.
5. Next, refer to the Reinstallation of the TABS-6 Module section.
REINSTALLATION OF THE TABS-6 MODULE
CAUTION! All TABS-6 module service replacement parts are initially defaulted to 2S/1M and may autocon fi gure to another ABS con fi guration if additional sensors and/or ABS modulators are detected. An incorrect ABS con fi guration may cause fault indication or degraded ABS performance. Before and after activating a self-con fi guration, always determine the current ABS con fi guration by activating blink code diagnostics.
Inspect the original mounting hardware: If it is in good condition, it can be reused for installation. If replacement hardware is needed, use grade-5 3/8-18 bolts, nuts and
15
lock washers for the frame-mount unit, or a schedule 80
(heavy gauge steel) ¾" nipple for the tank-mount unit.
Inspect the location selected for installation and clean as necessary.
NOTE: Inspect all components, including the replacement trailer ABS module, for any external damage, such as cracked valve ports, electronic housings, etc. Any components found to be damaged should not be installed on the vehicle and must be replaced.
1. Position and secure the unit in the original mounting orientation (the exhaust port must point straight down):
For tank-mount modules:
Install the nipple fi tting into the modulator-valve supply port. Then rotate the entire assembly into the tank port until secure. Over-torquing of the tank nipple could cause damage to the valve body.
For frame-mount modules:
Torque the mounting nuts to 180-220 in-lbs.
2. Reconnect all air hoses and plugs to the module.
Depending on the installation, additional plugs may be necessary. Make certain that no thread sealing material enters the valve. All air hoses and fi ttings should be checked for leaks prior to returning the vehicle to service.
3. Reconnect the ECU and wheel speed sensor electrical connectors to the unit. Apply a moderate amount of non-conductive electrical grease to each connector pin before reconnecting.
4. The new TABS-6 module may need to be recon fi gured for proper operation. See page 8.
5. Leakage and Operational Tests must be performed before returning the vehicle to service.
LEAKAGE AND OPERATIONAL TESTS
1. Before performing leak tests, block the wheels.
2. Fully charge air brake system and verify proper brake adjustment.
3. Make several trailer brake applications and check for prompt application and release at each wheel.
4. Check the module, modulator valve(s) and all air hose fi ttings for leakage using a soap solution:
Check the ABS solenoid body with the trailer service brakes fully applied. If leakage is excessive, more than a single 1" bubble within 1 minute, replace the module.
Check the relay exhaust port with the trailer service brakes released to be sure that leakage is less than a single 1" bubble within 3 seconds. If excessive leakage is detected at the relay exhaust port, perform the following test before replacing the module:
• Apply the trailer spring brakes. Recheck for leakage around the relay exhaust port. If the exhaust port stops leaking, this indicates a leak between the emergency and service sides of the spring brake chamber. However, if the relay exhaust port continues to leak excessively, replace the TABS-6 module.
5. Apply power and monitor the power-up sequence to verify proper system operation. See page 6.
6. Determine the current ABS con fi guration by activating blink code diagnostics or using a diagnostic tool. If necessary, reset the ABS con fi guration and allow the module to auto-con fi gure. See page 8.
7. Calibrate and set odometer parameters if necessary using a diagnostic tool. Refer to the Odometer Function section on page 8.
8. Where a safe location (e.g. restricted access area or test track) is available, it is possible to road test the ABS function by making an abrupt stop from a vehicle speed of about 20 MPH to check for proper function. The wheels should not enter a prolonged lock condition and ABS function should be audible. It is the responsibility of the technician to perform this test in a safe location.
ABS WIRING
All connector leads of the TABS-6 module pigtail harness are weather sealed at the connector interface and are clearly labeled for proper installation.
Bendix provides over-molded versions of the TABS-6 wiring harness and Bendix recommends that the complete harness be replaced if corrosion or damage occurs.
When troubleshooting ABS wiring, some general rules should be followed where applicable.
1. Check all wiring and connectors to ensure they are secure and free from visible damage (e.g. cuts, abrasions, etc.).
2. Check for evidence of wire cha fi ng due to poor routing, or poor securing, of wires.
3. Check connectors for proper insertion and locking.
4. Verify that the connector pins are properly greased with a non-conductive electrical grease compound.
5. Connector terminals must not show signs of corrosion or exposure to the environment.
6. Never pierce wire insulation when checking for continuity.
7. Do not deform individual pins or sockets during probing with a volt/ohm meter.
8. It is strongly recommended to properly secure all wiring harness and sensor leads at least every 18 inches.
9. Apply a moderate amount of non-conductive electrical grease to each connector pin before reconnecting.
16
Troubleshooting: Electrical Schematics
STANDARD
TABS-6
Trailer
ABS
Controller
FIGURE 15 - STANDARD TABS-6 MODULE (5-PIN ECU CONNECTOR) ELECTRICAL SCHEMATIC - 2S/1M
7-WAY SAE J560
CONNECTOR
1
7
4
SENSOR
RIGHT SR
1
2
TRAILER-MOUNTED
ABS WARNING LAMP
6-WAY SAE J1587
CONNECTOR
C
B
A
E
SENSOR ADD.
RIGHT SAR
MODULATOR VALVE
SENSOR ADD.
LEFT SAL
MOD2
1
2
MODULATOR VALVE
MOD3
1
2
1
2
3
SENSOR
LEFT SL
1
2
SENSOR RIGHT SR (+)
1
SENSOR RIGHT SR (-)
2
GROUND
18
IGNITION VOLTAGE
6
BRAKE LAMP VOLTAGE
12
ABS WARNING LAMP (AUX7)
5
SENSOR ADD. RIGHT SAR (+)
11
1
2
3
SENSOR ADD. RIGHT SAR (-)
17
MOD2 RELEASE
9
MOD1/2 COMMON
3
MOD2 HOLD
15
MOD3 RELEASE
10
MOD3 COMMON
4
MOD3 HOLD
16
SENSOR ADD. LEFT SAL (+)
8
SENSOR ADD. LEFT SAL (-)
14
J1587 (B)
7
J1587 (A)
1
J1587 GROUND
13
J1587 VOLTAGE (AUX6)
2
SENSOR LEFT SL (+)
1
SENSOR LEFT SL (-)
2
PREMIUM
TABS-6
Trailer
ABS
Controller
FIGURE 16 - PREMIUM TABS-6 MODULE (18-PIN ECU CONNECTOR) ELECTRICAL SCHEMATIC - 4S/3M
17
Troubleshooting: System Schematics
2S/1M - AXLE
CONTROL
Right -
“Curb-Side”
A Brake Light Power
B Ignition Power
C NC
D Warning Lamp
E Ground
A
D
B
C
E
Bendix WS-24
™
Wheel Speed
Sensor "SR"
CONTROL
LINE
Trailer
Chassis
Harness
Ignition
Power
7-PIN
CONNECTOR
Ground
SUPPLY
LINE
Brake
Light
Power
Dual Axle Trailer
5-PIN
CONNECTOR
Trailer ABS
Pigtail
Harness
ABS
ABS
Indicator Lamp
Bendix
®
SR-5 ™ Trailer
Spring Brake
Valve
Bendix
®
TABS-6
Trailer
ABS
Module
Left -
“Road-Side”
Bendix WS-24
™
Wheel Speed
Sensor "SL"
18
2S/1M - DOLLY AXLE CONTROL
A Brake Light Power
B Ignition Power
C NC
D Warning Lamp
E Ground
A
D
B
C
E
Right - “Curb-Side”
Coupling - Control
WS-24 ™ Wheel Speed Sensor
"SR"
Ignition
Power
7-PIN
CONNECTOR
CONTROL
LINE
Trailer
Chassis Harness
5-PIN
CONNECTOR
Trailer ABS
Pigtail Harness
SC-3
™
Single
Check Valve
R-12P
™
Pilot Relay Valve
Ground
SUPPLY
LINE
PR-3 ™ Pressure
Protection Valve
SV-4
™
Synchronizing
Valve
Brake Light
Power
Dolly
Coupling - Supply
A B S
ABS Light
Left - “Road-Side”
DC-4 ® Double
Check Valve
Trailer
ABS
Module
TABS-6
TR-3
™
Inversion
Valve
WS-24 ™ Wheel Speed Sensor
"SL"
Ignition
Power
Troubleshooting: System Schematics
(continued)
2S/2M - AXLE CONTROL
WS-24 ™ Wheel Speed Sensor
"SR"
Right - “Curb-Side”
A Brake Light Power
B Ignition Power
C NC
D Warning Lamp
E Ground
A
D
B
C
E
7-PIN
CONNECTOR
CONTROL
LINE
Trailer
Chassis Harness
5-PIN
CONNECTOR
Trailer ABS
Pigtail Harness
Ground
SUPPLY
LINE
SR-5
™
Trailer
Spring Brake
Valve
BR9235
™
“MOD2”
Modulator
Relay
Valve
TABS6
“MOD1”
Trailer
ABS
Module
Brake Light
Power
Dual Axle Trailer
ABS Light
A B S
Left - “Road-Side”
WS-24
™
Wheel Speed Sensor
Installation Guidelines for the TABS-6 2S/2M Axle ABS Con fi guration:
• MOD1 (TABS-6 ABS Unit) controls the wheel(s) of a primary axle(s).
"SL"
• MOD2 (BR9235
™
Modulator Unit) controls the wheels of an additional axle(s).
• SL & SR (Primary Sensors) senses wheels on the primary axle (always on ground) that MOD1 controls.
• For lift axle applications, MOD2 controls the wheels for the lift-able axle
Ignition
Power
2S/2M - SIDE CONTROL
A Brake Light Power
B Ignition Power
C NC
D Warning Lamp
E Ground
A
D
B
C
E
Right - “Curb-Side”
7-PIN
CONNECTOR
CONTROL
LINE
Trailer
Chassis Harness
5-PIN
CONNECTOR
Trailer ABS
Pigtail Harness
Ground
SUPPLY
LINE
SR-5
™
Trailer
Spring Brake
Valve
Brake Light
Power
WS-24 ™ Wheel Speed Sensor
"SR"
BR9235 ™
“MOD2”
Modulator
Relay
Valve
TABS6 “MOD1”
Trailer ABS
Module
Dual Axle Trailer
ABS Light
A B S
Left - “Road-Side”
WS-24 ™ Wheel Speed Sensor
"SL"
Installation Guidelines for the TABS-6 2S/2M Side ABS Con fi guration:
• MOD1 (TABS-6 ABS Unit) controls the left “road-side” wheel(s) of a primary axle(s).
• MOD2 (BR9235
™
Modulator Unit) controls the right “curb-side” wheel(s) of a primary axle(s).
• For lift axle applications, SL & SR (Primary Sensors) senses the wheels of the stationary, non lift-able axle
19
Troubleshooting: System Schematics
(continued)
4S/2M - AXLE CONTROL
WS Sensor
"SAR"
A Brake Light Power
B Ignition Power
C NC
D Warning Lamp
E Ground
A
D
B
C
E
WS-24
™
Wheel Speed Sensor
"SR"
Right -
“Curb-Side”
20
7-PIN
CONNECTOR
CONTROL
LINE
Trailer
Chassis Harness
5-PIN
CONNECTOR
Trailer ABS
Pigtail Harness
Ignition
Power
Ground
SUPPLY
LINE
SR-5 ™ Trailer
Spring Brake
Valve
BR9235 ™
“MOD2”
Modulator
Relay
Valve
TABS6
Trailer ABS
Module
“MOD1”
Brake Light
Power
ABS Light
Full Trailer
A B S
WS Sensor
"SAL"
Left -
“Road-Side”
"SL"
WS-24 ™ Wheel Speed Sensor
Installation Guidelines for the TABS-6 4S/2M Axle ABS Con fi guration:
• MOD1 (TABS-6 ABS Unit) controls the wheel(s) of a primary axle(s).
• MOD2 (BR9235
™
Modulator Unit) controls the wheels of an additional axle(s).
• SL & SR (Primary Sensors) senses wheels on the primary axle (always on the ground) that MOD1 controls, and are connected to the dedicated 2-pin connector on the TABS-6 ECU.
• SAL & SAR (Additional Sensors) senses the wheels that MOD2 controls, and are connected to the
18-pin connector on the TABS-6 ECU.
• For lift axle applications, MOD2 controls the wheels for the lift-able axle
Ignition
Power
4S/2M - SIDE CONTROL
A Brake Light Power
B Ignition Power
C NC
D Warning Lamp
E Ground
A
D
B
C
E
Right - “Curb-Side”
7-PIN
CONNECTOR
CONTROL
LINE
Trailer
Chassis Harness
5-PIN
CONNECTOR
Trailer ABS
Pigtail Harness
Ground
SUPPLY
LINE
SR-5
™
Trailer
Spring Brake
Valve
WS-24 ™ Wheel Speed Sensors
"SAR" "SR"
BR9235
™
“MOD2”
Modulator
Relay
Valve
TABS6
Trailer ABS
Module
“MOD1”
Brake Light
Power
Dual Axle Trailer
ABS Light
A B S
Left - “Road-Side”
"SAL" "SL"
WS-24
™
Wheel Speed Sensors
Installation Guidelines for the TABS-6 4S/2M Side ABS Con fi guration:
• MOD1 (TABS-6 ABS Unit) controls the left “road-side” wheel(s) of a primary axle(s).
• MOD2 (BR9235
™
Modulator Unit) controls the right “curb-side” wheel(s) of a primary axle(s).
• SL & SR (Primary Sensors) are connected to the dedicated 2-pin connector on the TABS-6 ECU.
• SAL & SAR (Additional Sensors) are connected to the 18-pin connector on the TABS-6 ECU.
• For lift axle applications, SAL & SAR (Additional Sensors) senses the wheels of the lift-able axle.
Troubleshooting: System Schematics
(continued)
4S/3M - SIDE/AXLE CONTROL
A Brake Light Power
B Ignition Power
C NC
D Warning Lamp
E Ground
A
D
B
C
E
Right -
“Curb-Side”
CONTROL
LINE
Trailer
Chassis Harness
5-PIN
CONNECTOR
Trailer ABS
Pigtail Harness
7-PIN
CONNECTOR
"SAR"
WS-24 ™ Wheel Speed Sensors
"SR"
BR9235 ™ “MOD3”
BR9235 ™
Modulator
Relay Valve
“MOD2”
Ignition
Power
Ground
SUPPLY
LINE
SR-5 ™ Trailer
Spring Brake
Valve
TABS-6
Trailer ABS
Module
“MOD1”
Brake Light
Power
Tri-Axle Trailer
A B S
ABS Light
Left -
“Road-Side”
"SAL"
WS-24 ™ Wheel Speed Sensors
"SL"
Installation Guidelines for the TABS-6 4S/3M Side/Axle ABS Con fi guration:
• MOD1 (TABS-6 ABS Unit) controls the left “road-side” wheel(s) of a primary axle(s).
• MOD2 (BR9235
™
Modulator Unit) controls the right “curb-side” wheel(s) of a primary axle(s).
• MOD3 (BR9235
™
Modulator Unit) controls the wheels of an additional axle(s).
• SL & SR (Primary Sensors) senses wheels on the primary axle (always on the ground) that MOD1 controls, and are connected to the dedicated 2-pin connector on the TABS-6 ECU.
• SAL & SAR (Additional Sensors) senses the wheels that MOD3 controls, and are connected to the
18-pin connector on the TABS-6 ECU.
• For lift axle applications, MOD3 controls the wheels for the lift-able axle.
21
Troubleshooting Flowcharts
Diagnostic trouble code information can be retrieved from the TABS-6 module by using blink code diagnostics, or a diagnostic tool. The following troubleshooting fl ow charts will help the technician isolate the cause of the fault and con fi rm whether the fault resides in the component, wiring or connectors.
Troubleshooting should always begin by observing the dash or trailer-mounted ABS indicator lamp during the
TABS-6 module's power-up sequence. If it is necessary to make electrical measurements, always begin by taking voltage and resistance measurements at the 5- or 18-pin
ECU pigtail harness connector.
Once the circuit fault is found, isolate the area needing repair by repeating the measurements at all connections in the affected circuit towards the modulator, wheel speed sensor, etc.
No voltage or resistance measurements are to be made on the bulkhead connector pins of the module.
Troubleshooting Flowcharts
Section A : (Power-Up Sequence)
Trailer-Mounted ABS Indicator Lamp . . . . . . . Page 23
Section B: (Power-Up Sequence)
Dash-Mounted ABS Indicator Lamp . . . . . . . . Page 24
Section C:
Diagnostic Trouble Code (DTC) Blink
Code Quick Reference . . . . . . . . . . . . . . . . . . . Page 25
Section D:
Diagnostic Trouble Code
TRDU
™
Tool LED Quick Reference . . . . . . . . . Page 26
Section E:
Troubleshooting the Trailer-Mounted
ABS Indicator Lamp Circuitry . . . . . . . . . . . . . Page 27
Section F:
Troubleshooting the Power Supply . . . . . . . . . Page 28
Section G:
Troubleshooting the WS-24
™
Wheel
Speed Sensors . . . . . . . . . . . . . . . . . . . . . . . . . Page 29
Section H:
Troubleshooting the BR9235
™
Modulator
Relay Valves. . . . . . . . . . . . . . . . . . . . . . . . . . . Page 30
22
SECTION A: (POWER-UP SEQUENCE)
TRAILER-MOUNTED ABS INDICATOR LAMP
23
24
SECTION B: (POWER-UP SEQUENCE)
DASH-MOUNTED ABS INDICATOR LAMP
SECTION C: DIAGNOSTIC TROUBLE CODE (DTC)
BLINK CODE QUICK REFERENCE
1st Blink Code
Code Location
1 All
2 Sensor SL
3 Sensor SR
4 Sensor SAL
5 Sensor SAR
6 Power
7 Valve MOD1
8 Valve MOD2
9 Valve MOD3
10 Common
11 ECU
12 Diagnostics
13 Indicator Lamp
2nd Blink Code
Code Description
1 No Diagnostic Trouble Codes
1 Sensor signal valid - large air gap
2 Sensor signal valid - loss of signal
3 Sensor signal valid - noisy
4 Sensor shorted or open
5 Tire diameter out of range
6 Sensor confi guration error
1 Over-voltage
2 Low-voltage
3 Excessive power line resistance
1 Hold solenoid (AUX) shorted or open
2 Release solenoid (AUX) shorted or open
3 ABS modulator dynamic error
4 Valve confi guration error
1 Valve MOD1/2 low-side switch shorted to ground
2 Valve MOD3 (AUX) low-side switch shorted to ground
3 ABS modulator dynamic error - all valves
4 Excessive ABS activity
1 ECU internal error
2 ECU confi guration error
1 J1587 diagnostics (AUX6) shorted or open
1 ABS lamp (AUX7) shorted or open
• System fully operational - no faults detected
• Go to Section G - Dynamic WSS DTCs
• Go to Section G - Dynamic WSS DTCs
• Go to Section G - Dynamic WSS DTCs
• Go to Section G - Static WSS DTCs
• Verify correct tire size, proper tire infl ation & correct
number of exciter ring teeth. Verify that the ECU
has the proper tire size settings.
• Verify correct ABS confi guration. If needed, reset to
the default ABS confi guration and power-up to
initiate auto-confi guration.
• Go to Section F - Power Supply
• Go to Section F - Power Supply
• Go to Section F - Power Supply
• Go to Section H - ABS Modulator DTCs
• Go to Section H - ABS Modulator DTCs
• Go to Section H - ABS Modulator DTCs
• Verify correct ABS confi guration. If needed, reset to
the default ABS confi guration and power-up to
initiate auto-confi guration.
• Go to Section H - ABS Modulator DTCs
• Go to Section H - ABS Modulator DTCs
• Go to Section H - ABS Modulator DTCs
• Go to Section G - Dynamic WSS DTCs
• Check for damaged or corroded connectors. Check
for damaged wiring. After repairs or if no issues
found, then clear faults. If faults return, replace the
module.
• Verify correct ABS confi guration. If needed, reset to
the default ABS confi guration and power-up to
initiate auto-confi guration.
• Check for corroded/damaged wiring or connectors
between the ECU and J1587 Diagnostic (AUX6).
Replace/repair J1587 Diagnostic (AUX6) wiring or
components as required.
• Go to Section E - Trailer ABS Indicator Lamp
To Read/Clear Diagnostic Troubleshooting Codes (DTCs):
1. Apply constant power to the trailer (ignition switch).
2. Within 15 seconds, apply/release the brake pedal at 1 second intervals:
(a) 3 times for displaying Active DTCs.
(b) 4 times for displaying Inactive DTCs.
(c) 5 times for clearing Active DTCs.
3. After 5 seconds delay, the blink codes will be displayed.
4. Observe the trailer-mounted ABS indicator lamp and record blink code(s).
5. Refer to blink code chart for description.
6. After making repairs and clearing Active DTCs, verify lamp is no longer illuminated.
25
SECTION D: DIAGNOSTIC TROUBLE CODE (DTC)
TRDU
™
TOOL LED QUICK REFERENCE
Power
System OK - A solid green VLT LED indicates proper voltage is reaching the module. If no red LEDs are on, then no DTC's are detected.
If the ABS indicator lamp is on with no red LEDs, Go To
Section E, page 27.
Voltage Out of Range - A flashing green VLT LED indicates ECU voltage below 8.0 VDC or above 16.0
VDC. The VLT LED will flash until power is brought into normal range. Go to Section F, page 28.
No Voltage - When the VLT LED is off, the module is receiving very low or no voltage, or there is no communication to TRDU. The ECU LED may be on in this case. Go to Section F, page 28.
Wheel Speed Sensor DTC
The red SEN LED is on to indicate a DTC with a wheel speed sensor. The example above shows the LEDs illuminated when there is an additional right sensor
(SAR) DTC.
Troubleshooting and repair are the same for a DTC on any wheel speed sensor. The indicated sensor DTC may be static or dynamic.
Static DTCs
are related to wiring or component failures such as open or short circuits.
Dynamic DTCs
are related to abnormal wheel speed signals or behaviors.
Go To Section G, page 29.
26
ABS Modulator DTC
The red M1, M2 and/or M3 LED is on to indicate a DTC with an ABS modulator. The example above shows the
LEDs illuminated when there is a DTC for a second ABS modulator (MOD2).
The indicated modulator DTC may be static or dynamic.
Static DTCs
are related to wiring or component failures such as open or short circuits.
Dynamic modulator DTCs
are related to abnormal wheel speed behaviors during ABS.
Go to Section H, page 30.
M1
ODO
Magnetic Reset -
All LEDs will be on while a magnet is held in place at the
RESET location near the “B” in Bendix.
When held for less than 6 seconds, the
DTCs are cleared. When held for more than 6 seconds,the ABS configuration is reset. If one or more LEDs do not illuminate, replace the TRDU
™
tool. Do not reset the
DTC codes until troubleshooting of the indicated component is complete.
ECU DTC
The red ECU LED is on to indicate a DTC internal to the
™
TABS-6 module. Reset the TRDU tool with a magnet. If the DTC returns, replace the module.
If the red ECU LED is on and the green VLT LED is off, the module may have very low voltage. In this case, go to Section F.
Odometer Mileage -
The TRDU will continously display the odometer information (x1000) by flashing the blue ODO LED. There will be a 20 second pause between ODO displays.
As an example: 152,431 miles will be displayed as:
152 (x1000) ... or 1 blink (pause), 5 blinks (pause), 2 blinks.
Zeros are displayed by the blue ODO
LED strobing twice.
SECTION E: TROUBLESHOOTING THE TRAILER-MOUNTED
ABS INDICATOR LAMP CIRCUITRY
Looking into Standard
TABS-6 Module Wire
Harness (Pin D ABS
Indicator Lamp)
Looking into Premium
TABS-6 Module Wire
Harness (Pin 5 ABS
Indicator Lamp)
27
SECTION F: TROUBLESHOOTING THE
POWER SUPPLY
Measure the loaded voltage across a type
1157 brake light bulb.
28
Looking into Premium TABS-6 Module Wire Harness,
ECU Connector Measure:
Pin 6 (Ignition Power) to Pin 18 (ground) and
Pin 12 (Brake Light Power) to Pin 18 (ground)
Looking into Standard TABS-6 Module Wire Harness,
ECU Connector Measure:
Pin B (Ignition Power) to Pin E (ground) and
Pin A (Brake Light Power) to Pin E (ground)
SECTION G: TROUBLESHOOTING THE
WS-24
™
WHEEL SPEED SENSORS (WSS)
Looking into Wire Harness(es)
SR Sensor
1 - Right (Curb) Sensor +
2 - Left (Curb) Sensor -
SL Sensor
1 - Left (Road) Sensor +
2 - Right (Road) Sensor -
Looking into Premium TABS-6 Module Wire Harness when Additional Wheel Speed Sensors are used:
SAR:
11 - Additional Right (Curb) Sensor +
17 - Additional Right (Curb) Sensor -
SAL:
8 - Additional Left (Road) Sensor +
14 - Additional Left (Road) Sensor -
29
SECTION H: TROUBLESHOOTING THE
MODULATOR RELAY VALVES
30
Premium TABS-6 Module Wire Harness for BR9235
™
Modulator Valve Connector
Looking into Modulator
Connector Pins:
Pin 1 (Release)
Pin 2 (Common)
Pin 3 (Hold)
(Optional)
Looking into ECU
Connector:
Pin 9 is MOD2 release
Pin 3 is MOD2 Common
Pin 15 is MOD2 Hold
Pin 10 is MOD3 release
Pin 4 is MOD3 Common
Pin 16 is MOD3 Hold
2-Pin Sensor Pin-Out and Routing Info
Date of Manufacture Code
5-Pin ECU Pin-Out
Bendix Part Number
Number Showing the Initial Software
Loaded
(Software may be revised on the production line or in the fi eld.)
Bendix Part Number
Bendix Part Number
2-Pin Sensor Pin-Out and Routing Info
18-Pin ECU Pin-Out
FIGURE 17 - LABEL INFORMATION
ECU Part Number Label
The external part number label is located on the relay valve portion of the module. Label shown above is located under the removable cover of the TABS-6 module. If the part number label is not readable or is painted over, the ECU part number and revision can be read using a diagnostic tool. The number of the initial software loaded on the ECU is also indicated.
The module part number, and pin-out information is shown on the label beneath the removable cover.
Software Revision Level
The current software revision number can be read using a diagnostic tool.
Document Revision Level
Please visit Bendix.com to ensure you have the latest version of this document.
31
32
BW2469 ©2010 Bendix Commercial Vehicle Systems LLC • All Rights Reserved • 7/10 • Printed in U.S.A. Printed on recycled paper
advertisement
Related manuals
advertisement
Table of contents
- 1 Introduction
- 2 Safe Maintenance Practices
- 2 Components
- 2 gurations
- 2 PLC Communications
- 3 Wiring Harness (Pigtail)
- 4 Power and Ground
- 4 ABS Indicator Lamp
- 5 Wheel Speed Sensors
- 5 ABS Modulator Valves
- 6 J1708/J1587 Diagnostic Link
- 6 Auxiliary I/O
- 6 Program
- 6 Customer Scratch Pad
- 6 Power-up Sequence
- 7 ABS Operation
- 8 guration
- 8 Odometer Function
- 8 Non-standard Tire Size
- 8 Diagnostic Trouble Code Detection
- 9 Partial ABS Shutdown
- 9 Blink Code Diagnostics
- 10 Diagnostic Trouble Codes (DTCs)
- 13 Using Hand-Held or PC-Based Diagnostics
- 13 Bendix ABS Diagnostic Tools
- 14 Contacting Bendix
- 15 Servicing the TABS-6 Module
- 15 Removing the TABS-6 Module
- 15 Service Replacement of Other ABS Controllers
- 15 Reinstallation of the TABS-6 Module
- 16 Leakage And Operational Tests
- 16 ABS Wiring
- 17 Troubleshooting