- Home
- Domestic appliances
- Large home appliances
- Washing machines
- Electrolux
- EWM3000new
- Service manual
advertisement
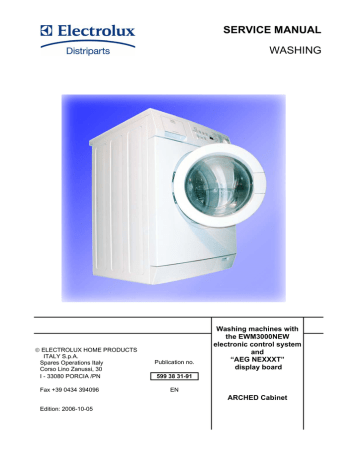
SERVICE MANUAL
WASHING
© ELECTROLUX HOME PRODUCTS
ITALY S.p.A.
Spares Operations Italy
Corso Lino Zanussi, 30
I - 33080 PORCIA /PN
Fax +39 0434 394096
Edition: 2006-10-05
Publication no.
599 38 31-91
EN
Washing machines with the EWM3000NEW electronic control system and
“AEG NEXXXT”
display board
ARCHED Cabinet
SOI/DT 2006-10 dmm 2/48 599 38 31-91
CONTENTS
1 Purpose of this manual ............................................................................................................................ 3
2 IMPORTANT ............................................................................................................................................ 3
3 GENERAL SPECIFICATIONS................................................................................................................. 3
4 CONTROL PANEL................................................................................................................................... 3
4.1
CONTROL/DISPLAY BOARD .......................................................................................................... 3
4.1.1
Version with display................................................................................................................... 3
5 Washing programmes .............................................................................................................................. 3
5.1.1
Configuration of the programmes .............................................................................................. 3
5.2
Programme selector ......................................................................................................................... 3
5.3
Start/Pause ....................................................................................................................................... 3
5.4
Functions of the buttons ................................................................................................................... 3
6 WASH PROGRAMMES AND OPTIONS ................................................................................................. 3
6.1
Possible programmes ....................................................................................................................... 3
6.2
Options for the wash cycle................................................................................................................ 3
6.3
Description of options ....................................................................................................................... 3
6.3.1
Night cycle ................................................................................................................................. 3
6.3.2
Stop with water in the tub .......................................................................................................... 3
6.3.3
Prewash..................................................................................................................................... 3
6.3.4
Soak........................................................................................................................................... 3
6.3.5
Stain removal............................................................................................................................. 3
6.3.6
Short Daily ................................................................................................................................. 3
6.3.7
Very Short (Quick) ..................................................................................................................... 3
6.3.8
Heavy-duty ................................................................................................................................ 3
6.3.9
Energy saving / Energy label..................................................................................................... 3
6.3.10
Sensitive .................................................................................................................................... 3
6.3.11
Extra rinse ................................................................................................................................. 3
6.3.12
“Half load” button ....................................................................................................................... 3
6.3.13
Easy-Iron ................................................................................................................................... 3
6.3.14
Reduced spin speed.................................................................................................................. 3
6.3.15
No spin....................................................................................................................................... 3
6.3.16
Spin speed adjustment .............................................................................................................. 3
6.3.17
Reduced times (Quick) .............................................................................................................. 3
6.3.18
Temperature adjustment ........................................................................................................... 3
6.3.19
Delayed-start time ..................................................................................................................... 3
6.3.20
Exclusion of the buzzer” ............................................................................................................ 3
6.4
Variation of rinses when options are selected .................................................................................. 3
6.5
Display (some models) ..................................................................................................................... 3
6.6
LEDs ................................................................................................................................................. 3
7 TECHNICAL CHARACTERISTICS.......................................................................................................... 3
7.1
EWM3000NEW Electronic control system ....................................................................................... 3
7.1.1
Functions provided by the electronic board............................................................................... 3
7.1.2
Memories contained in the electronic control system ............................................................... 3
7.2
Analogue pressure switch (electronic).............................................................................................. 3
7.3
Pressure switch ................................................................................................................................ 3
7.3.1
Calibration of the levels on the pressure switch ........................................................................ 3
7.4
Power supply and programme selection .......................................................................................... 3
7.5
Door interlock system ....................................................................................................................... 3
7.5.1
Voltmetric device with PTC........................................................................................................ 3
7.5.2
Instantaneous door interlock ..................................................................................................... 3
7.6
Water fill system ............................................................................................................................... 3
7.6.1
Flow meter ................................................................................................................................. 3
7.6.2
Operating principle of flow meter............................................................................................... 3
7.7
Drain pump ....................................................................................................................................... 3
7.8
Recirculation pump ........................................................................................................................... 3
7.9
Water Control.................................................................................................................................... 3
7.10
Heating system ............................................................................................................................. 3
7.10.1
Heating element ........................................................................................................................ 3
7.10.2
Temperature sensor .................................................................................................................. 3
7.11
Turbidity sensor............................................................................................................................. 3
7.12
Inverter .......................................................................................................................................... 3
7.13
Motor ............................................................................................................................................. 3
7.14
Power feed to motor...................................................................................................................... 3
SOI/DT 2006-10 dmm 3/48 599 38 31-91
7.15
Anti-foam control ........................................................................................................................... 3
7.16
FUCS (Fast Unbalance Control System) ...................................................................................... 3
8 DEMO Mode ............................................................................................................................................ 3
8.1
Demo mode setting........................................................................................................................... 3
8.2
Exiting demo mode ........................................................................................................................... 3
9 DIAGNOSTICS SYSTEM ........................................................................................................................ 3
9.1
Access to diagnostics system........................................................................................................... 3
9.2
Exiting diagnostics system................................................................................................................ 3
9.3
Phases of the diagnostics test .......................................................................................................... 3
9.3.1
LEDs display board diagnostics ................................................................................................ 3
9.3.2
Programme selector .................................................................................................................. 3
10 ALARMS............................................................................................................................................... 3
10.1
Displaying the alarms to the user.................................................................................................. 3
10.1.1
Alarms displayed during normal operation ................................................................................ 3
10.2
Reading the alarm codes .............................................................................................................. 3
10.2.1
Displaying the alarm .................................................................................................................. 3
10.2.2
Examples of alarm displays....................................................................................................... 3
10.2.3
Operation of alarms during diagnostics..................................................................................... 3
10.3
Notes about some alarms ............................................................................................................. 3
10.4
Rapid reading of alarm codes ....................................................................................................... 3
10.5
Cancelling the last alarm............................................................................................................... 3
10.6
Table of alarm codes..................................................................................................................... 3
11 Operating time counter......................................................................................................................... 3
11.1.1
Operating time reading .............................................................................................................. 3
11.1.2
Displaying the operating time .................................................................................................... 3
12 ACCESSING COMPONENTS ............................................................................................................. 3
12.1
Flow mete...................................................................................................................................... 3
12.2
Aqua control .................................................................................................................................. 3
12.3
Motor ............................................................................................................................................. 3
13 Contacts on Main Board....................................................................................................................... 3
14 Contacts on inverter board ................................................................................................................... 3
15 BASIC CIRCUIT DIAGRAM WITH SENSORS .................................................................................... 3
15.1
Key for circuit diagram .................................................................................................................. 3
SOI/DT 2006-10 dmm 4/48 599 38 31-91
1 Purpose of this manual
The purpose of this manual is to provide service personnel (who already have the basic knowledge required for repairing washing machines) with information on washers with the EWM3000NEW electronic control system.
The EWM3000NEW is a new electronic control system which includes:
ª a new two-pole, brushless asynchronous motor
ª a new inverter board for controlling the motor
ª a main board
ª a display board
The subjects dealt with in the manual are:
• General
• Control panel and programmes specifications
• Troubleshooting
For detailed information on the water circuits and structural characteristics of these appliances, and on gaining access to their internal components, see the Service Manual with ARCHED cabinet (Publication no. 599 37 67-82).
2 IMPORTANT
The electrical components must be serviced by qualified personnel only
Unplug the appliance before accessing internal components
Programme selection
Serial port
Voltage requirement
Type of washing system
Type of rinsing system
Motor
Spin speed
Anti-unbalancing control
Water fill control
Detergent dispenser
Control of water level in tub
Door interlocks
Power of heating element
Temperature control
Audible signalling system
Sensors
SOI/DT 2006-10 dmm
24 positions with incorporated main switch
Communications protocol DAAS-EAP up to 38400 baud
Jet-system
Jet-system
900 - 1600 RPM
FUCS
3 compartments: prewash/stain remover, washing, softener
4 compartments: prewash, washing, softener, stain remover
Two anti-boiling pressure switches
Anti-overflow pressure switch, Aqua control system
Traditional (with PTC)
Instantaneous (with or without microswitch)
Magnetic
Up to 1950 W
Traditional, included on display board
Water level sensor sensor
5/48 599 38 31-91
The configuration of the control panel depends on the following:
ª Type of control/display board
ª Design of the control panel (no. of buttons, LEDs)
ª Different configuration of the buttons
Example of control panel:
Buttons:
- max. 8, horizontally
LEDs:
- max. 27
Display:
- 3 digits with 24 red LEDs
SOI/DT 2006-10 dmm 6/48 599 38 31-91
4.1 CONTROL/DISPLAY BOARD
Ö 3 digits
Ö 26 LEDs: 24 red, one bicolour (red and green)
Ö 9 buttons
Version without display:
Ö 26 LEDs: 24 red, one bicolour (red and green) buttons
SOI/DT 2006-10 dmm 7/48 599 38 31-91
5.1.1 Configuration of the programmes
The table below lists the parameters that can be used to define the washing programmes.
Types of fabrics
Special programmes
Cotton/linen, Synthetics, Delicates, Wool, Hand-wash, Mini
Soak, Rinses, Spin, Drain, Conditioner
Temperature
Spin
Options (Normal/Possible)
Programme phases
Normal, Maximum: the initial temperature is the maximum that can be selected for a specific washing programme
Normal, Minimum, Maximum
Bleach, Economy (energy label), Stains, Short, Very short,
Reduced spin speed, Night-time cycle, Half-load, Easy-Iron,
Rinse Hold, Extra rinse, Pre-wash, Soak and Sensitive
Pre-wash, Wash, Rinses, Spin, Cycle end
The programme selector defines the type of washing cycle (ex: water level, drum movement, no of rinses) and washing temperature to be selected according to the type of wash.
The programme selector can be rotated both clockwise and anti-clockwise.
The first position is used to cancel the current programme (and to switch the appliance off, if the main switch is incorporated in the selector).
5.3 Start/Pause
Start: after selecting the programme and the desired options, press this button to start. If the delay time ahs been selected, the countdown will begin and the display will indicate it. The LED stops flashing and remains lit for the whole duration of the programme.
Pause: by pressing the button again, the current programme is interrupted and the display or the corresponding LED starts flashing. During the pause phase it is possible to open the door only if the machine is not during the heating phase, the water level is not high and the drum is not moving.
During the pause it is possible to modify the programme as follows:
- the OPTIONS of the cycle can be modified before the phase by which they have to be performed
- the SPIN can be modified before the final spin
To re-start the programme press the START/PAUSE button again.
5.4 Functions of the buttons
The washing programmes and the functions of the single buttons vary for the different models, since they are determined by the configuration operation of the appliance.
SOI/DT 2006-10 dmm 8/48 599 38 31-91
6 WASH PROGRAMMES AND OPTIONS
6.1 Possible programmes
The wash programmes can be configured to suit personal needs. The table below lists the standard programmes:
Programme
90
90E
60
60E
Temperature (
°C)
No. of rinses Final spin (RPM)
85 3
67 2
60 3
Cotton 50
50/40E
57 (*)(**) 2
450/650/850/1000/1200/
1300/1400/1600
44 (*) 2
40
30
42
30 3
Synthetics
Delicate fabrics cold
60
60/50E
50
40
30 cold
40
20
60
42 (*)
50
40
30
20
40
30
20
3 450/700
Wool
Hand wash
30 cold
40
30 cold
40
30 cold
40
35
20
40
35
20
Soak
Rinse
Rinse for delicate
fabrics
Softener
Drain
Spin
Delicate spin
Short cycle
Automatic
(*) “energy label” programmes
(**)
30/20 ----
---- ----
----
----
60 E COTTON
G20 51-54
G22 54-57
SOI/DT 2006-10 dmm 9/48 599 38 31-91
6.2 Options for the wash cycle
Options are selected after the appliance is switched on and the desired programme is selected, but before the Start/Pause button is pressed.
When an option button is pressed, the corresponding LED lights up. When the button is pressed again, the option is cancelled and the LED switches off. The number and types of these buttons vary with the configuration of the appliance.
Possible options for programmes selected
OPTIONS
COTTON
COTTON /
UNIVERSAL
AUTOMATIC
SYNTHETICS
90°C
X X X X X X X X X X X X X X X X X
60°C X X X X X X X X X X X X X X X X X
50°C X X X X X X X X X X X X X X X X X
40°C X X X X X X X X X X X X X X X X X
30°C X X X X X X X X X X X X X X X
Cold X X X X X X X X X X X X X X X
40°C X X X X X X
60°C X X X X X X X X X X X X X X
50°C X X X X X X X X X X X X X X
40°C X X X X X X X X X X X X X X
30°C X X X X X X X X X X X X
Cold X X X X X X X X X X X X
MINI
PROGRAMME
FRESH UP
DELICATE
FABRICS
30°C X X X
40°C X X X X X X X X X
30°C X X X X X X X X
Cold X X X X X X X X
SILK
WOOL - HAND
WASH
VISCOSE
(Fashion)
SOAK
RINSES
SOFTENER
40°C X X X X X X X X
DRAIN
SPIN
STOP W/WATER IN TUB
NIGHT CYCLE
X X
X X
X X
X X X X X X X X X X X X X X X
X X X X X X X X X X X X
PREWASH
SOAK
STAIN REMOVAL
HEAVY-DUTY
DAILY
SHORT
ENERGY SAVING
SENSITIVE
EXTRA RINSE
BLEACH
HALF-LOAD
EASY IRON
LOWER SPIN SPEED
NO SPIN
DELICATE SPIN
PRESELECTION
PREWASH
WASH
RINSES
SPIN
X X X
X X
X X
X X X X X X
X X X X X
X X X X X
X X X X X
X X X X X X X X X
X X X X X X X X X X
X X X X X X X X
X X X X X X X X X X X X
X X X X X X X X X X X X
X X X X X X X X X X X X X
X X X X X X X X X X X X X
X X X X X X X X X X X X X X X X X
X X X X X X X X X X X X X X X
X X X X X X X X X X X X X X X
X
X X X X X X X X X X X
X X X X X X X X X X X
X X X X X X X X X X X
X X X X X X X X
X X X X X X X X
X X X X X X X X
X X X X X X X X
X X X X X X
X X X X X X
X X X X X
X X X X
X X
X
X X
X X
X
X
SOI/DT 2006-10 dmm 10/48 599 38 31-91
6.3 Description of options
ª No spin phases. Three rinses are added to COTTON cycles and one rinse is added to SYNTHETICS cycles
ª The appliance is shut down with water in the tub before the final spin
ª No buzzer (if appliance is configured with a buzzer)
ª To drain the water, select a drain or spin cycle
6.3.2 Stop with water in the tub
ª The appliance is shut down with water in the drum before the final spin
ª To drain the water, select a drain or spin cycle.
6.3.3 Prewash
ª A prewash phase is added at the beginning of the cycle. The water is heated to 30°C (or may be cold, if selected)
ª In COTTON and SYNTHETICS cycles, a short spin (pulse spin) is performed before the wash phase
ª This option is not available in WOOL and HAND WASH cycles
6.3.4 Soak
ª A prewash phase is added (lasting 30’, with the same agitation as in the wool cycle) at the beginning of the programme. The water is heated to 30°C (or may be cold, if selected)
ª In COTTON and SYNTHETICS cycles, a short spin (pulse spin) is performed before the wash phase
ª When combined with the delayed start option, a soak time from 30 minutes to 10 hours can be selected
ª This option is not available in WOOL and HAND WASH cycles
ª The motor operates for 5 minutes after the water is heated to 4 0°C
ª Water is run through the prewash/stain remover compartment to withdraw special stain removing product
ª This option is not available in DELICATE FABRICS, WOOL and HAND WASH cycles
ª Agitation during washing changes from vigorous to normal
ª The wash phase in the COTTON - SYNTHETICS programmes is modified to obtain good performance in a short time (optimized for small loads)
6.3.7 Very Short (Quick)
ª The COTTON – SYNTHETICS – DELICATE FABRICS programmes are modified to obtain very short time wash times (optimized for small, lightly soiled loads)
ª The number of rinses is reduced (one less rinse)
ª The water level in the other two rinses is increased
6.3.8 Heavy-duty
ª 10 minutes of normal agitation are added to the wash phase in the cotton programme
SOI/DT 2006-10 dmm 11/48 599 38 31-91
6.3.9 Energy saving / Energy label
ª The COTTON 40°/50°/60°/90° - SYNTHETICS 50°/60° programmes are modified to reduce energy consumption
ª The wash temperature in the 90°/60°/50° programmes is reduced; the temperature in the 40° programme is increased by 4°.
ª The length of the wash phase is increased
6.3.10 Sensitive
ª A rinse is added to the COTTON – SYNTHETICS cycles
ª During cotton cycles, agitation is reduced from vigorous to normal
ª Intermediate spin phases are eliminated except for the final two, whose speed is reduced
ª Two rinses are added to COTTON cycles, and one rinse is added to SYNTHETICS – DELICATE
FABRICS cycles
ª Intermediate spin phases are eliminated except for the final two, which are reduced to 450 RPM.
For the appliances without this button, press it and the corresponding LED lights.
For the appliances with this button, proceed as follows:
To activate it, after selecting a COTTON or SYNTHETICS or DELICATES cycle, press the buttons (no. 1) and button no. 3 simultaneously for at least 2 seconds, till the corresponding phase LED switches on.
This option remains always active, also in the following cycles; to deactivate it, repeat the same procedure: press button (no. 1) and button no. 3 simultaneously for at least 2 seconds, till the extra rinse LED switches off.
6.3.12 “Half load” button
ª Eliminates a rinse in the COTTONS programmes.
6.3.13 Easy-Iron
• In COTTON programmes:
ª Adds three rinses.
ª Eliminates the intermediate spins.
ª Performs an impulse spin phase.
ª Adds an “untangling” phase after the spin cycle.
• In SYNTHETICS cycles:
ª Reduces the heating temperature in 50/60° cycles to 40°C.
ª Increases the washing time.
ª Prolongs the cooling phase at the end of the washing phase.
ª Adds one rinse without spin cycle.
ª Adds an “untangling” phase after the impulse spin cycle
SOI/DT 2006-10 dmm 12/48 599 38 31-91
6.3.14 Reduced spin speed
ª Reduces the speed of all spins as shown in the table
Maximum spin speed (rpm)
Reduction for COTTON (rpm)
600 700 800 900 1000 1100 1200 1300 1400 1500 1600
450 450 450 450 500 550 600 650 700 750 800
(rpm)
ª All spin phases are eliminated
ª Three rinses are added to the COTTON cycle and one rinse is added to the SYNTHETICS cycle
ª The speed of all spin phases in the cycle is lowered
ª The last selected position can be used for no spin and stop with water in the drum
ª No spin adds three rinses to the COTTON cycle and one rinse to the SYNTHETICS cycle
6.3.17 Reduced times (Quick)
ª The COTTON – SYNTHETICS – DELICATE FABRICS programmes are modified to obtain very short time wash times (optimized for small, lightly soiled loads)
ª The number of rinses is reduced (one less rinse)
ª The water level in the other two rinses is increased
ª When this option is selected, machine configuration is the same as in the SHORT – VERY SHORT programmes
ª Allows wash temperature to be adjusted up to the max. temperature allowed for the cycle.
ª Available when the cycle is selected; temperature can be adjusted (with machine in the pause mode) only if the heating phase has not yet begun.
6.3.19 Delayed-start time
• Models with digit
ª It is possible to select, during the programme selection phase, a delayed start from 30 minutes up to
23 hours ( ) 30’) 60’) 90’) 2h) 3h...) 23h) 0h).
ª During the delay phase, the time decreases every hour up to 2h, then by 30minutes.
ª To start the cycle immediately, after the delay time began: press the Start/Pause button, cancel the delay time by pressing the relative button and press Start/Pause again.
• Models with led
ª Insert a pause before the start of the programme, the delay time is indicated by the corresponding
LEDs.
ª To start the cycle immediately, after the delay time began: press the Start/Pause button, cancel the delay time by pressing the relative button and press Start/Pause again.
6.3.20 Exclusion of the buzzer”
In models with the buzzer it is possible to exclude the acoustic signal during the selection or at the end of the cycle, but the alarm remains on.
ª Press buttons no. 1 and no. 2 simultaneously to deactivate the buzzer for 2 seconds; this option will be memorised until it will be deactivated with the same procedure.
SOI/DT 2006-10 dmm 13/48 599 38 31-91
6.4 Variation of rinses when options are selected
No. of rinses with options
COTTON
SYNTHETICS
Very short (Quick)
Short (79 min.)
2 3 4
(Daily 6
2 3 4
5
5
2 3 4 5
Normal 3 4 5 6
Very short (Quick) 2 3 3 3
3 4 4 4
2 3 3 3
3 4 4 4
6
7
6
6
7
4
5
4
5
DELICATE
FABRICS
Normal
Very short (Quick)
WOOL Normal
HAND WASH Normal
3 4 4 4
2 - 3
Normal 3
3
-
- -
-
-
5
-
-
-
-
SILK Normal 2 3 3 3
N.B.: The HALF-LOAD option subtracts one rinse from all COTTON programmes, except for the
VERY SHORT programme.
5
SOI/DT 2006-10 dmm 14/48 599 38 31-91
6.5 Display (some models)
The display shows the following information:
Ö three
Ö the duration of the washing programme, which appears after selecting it. This time corresponds to that necessary for the maximum load for every type of programme. After starting the programme, the time diminishes (and updates) by every minute.
Ö the end of the programme indicated by a "0" (when it is possible to open the door). countdown starts and the delayed time diminishes by every hour. In the last 2 hours diminishes by
30min.
Ö an alarm code, indicating anomalies in the functioning of the machine.
6.6 LEDs
The LEDs indicate different information according to the type of configuration; the End-of-cycle Led is featured in all models.
Type of Led Functions
Pre-wash
Wash
Lights during selection mode if the programme includes the pre-wash phase, and during the execution of the pre-wash.
Lights during selection mode if the programme includes the wash phase, and during the execution of the wash.
Pre-wash/Wash
Lights during selection mode if the programme includes the pre-wash or wash phases, and during the execution of these phases.
Rinse
Lights during selection mode if the programme includes rinse phases, and during the execution of the rinse.
Spin
Drain
Extra rinse
Rinse hold
Lights during selection mode if the programme includes the spin phase, and during the execution of the spin.
Lights during selection mode if the programme includes the drain phase, and during the execution of the drain
Lights when this option has been memorized (if included in the cycle) during the execution of the rinse.
Lights if the programme includes the rinse-hold option and at the end of the cycle, when the appliance stops with water in the tub.
Current cycle Lights during execution of the cycle
End of cycle Lights when the programme has been completed; also used to display alarm conditions
Blocked filter Lights at the end of the cycle if the drain filter is blocked.
Overdosing Lights at the end of the cycle if an overdosing alarm of detergent occurs.
ON/OFF
Lights when the appliance is switched on
Door
ª Lights when the door is locked by the interlock.
ª Switches off when the door is locked.
ª Flashes when the door is about to unlock (it is clear above all in models with safety device with PTC)
Door locked Lights when the display shows the time-to-end
SOI/DT 2006-10 dmm 15/48 599 38 31-91
7 TECHNICAL CHARACTERISTICS
7.1 EWM3000NEW Electronic control system
The EWM3000NEW electronic control system consists of a main board (1), a control / display board (2) and an inverter board which controls motor speed.
7.1.1 Functions provided by the electronic board
PROGRAMME
SELECTOR
DISPLAY BOARD
LEDs Buttons
μP
Display
Buzzer
μP
INVERTER
&
SENSORS
MOTOR
MAIN BOARD
ELECTRICAL
LOADS
The electronic board:
Ö Receives cycle settings from the control/display board. The buttons, LEDs and display are located on this board.
Ö Powers all the electrical components (solenoids, drain pump, heating element, door lock unit).
Ö Controls the temperature of the wash water using a signal from an NTC sensor, and controls the speed of the motor through the inverter board (using a signal from a tachometric generator).
Ö Controls the water level in the tub by monitoring the level pressure switch and safety switch.
Ö Controls the water level in the tub by monitoring the flow meter.
7.1.2 Memories contained in the electronic control system
ROM
μP
Power failure and machine status
External serial port
(Asynchronous)
RAM
Internal serial port
(Synchronous)
EEPROM
(not included in processor)
Configuration of appliance
Description of cycle
The main board is equipped with an EEPROM that is not included in the microprocessor. It is used to store data on machine configuration, description of the cycle, and status of the cycle in case of a power failure or alarm.
Configuration data is programmed at the factory by a computer with a DAAS interface. This data determines the operation of the appliance (number and types of programmes, options, LEDs, etc.).
SOI/DT 2006-10 dmm 16/48 599 38 31-91
The memory for the microprocessor on the main board is divided into three parts:
ROM This area of memory contains the general instructions that control the functions of the appliance, such as managing electronic components and alarms. It is written by the manufacturer of the microprocessor and cannot be changed.
RAM This memory contains all the variables used to execute the wash programme, which are written in a dynamic manner. It can be read using a DAAS interface.
EEPROM This area of memory contains:
⇒ The data required for restarting the appliance after a power failure.
⇒ Wash cycle parameters such as fill level, speed and type of motor movement, and temperatures during the various wash phases. Once they are written, these parameters are protected and can normally be read only with a DAAS interface. The parameters can be modified using a special command that unprotects them.
⇒ Configuration parameters such as final spin speed, tub volume, type of wash, etc. These parameters can be programmed using a DAAS interface.
SOI/DT 2006-10 dmm 17/48 599 38 31-91
7.2 Analogue pressure switch (electronic)
The electronic pressure switch is an analogue device that controls the water level in the tub. It is directly connected to the main board.
1. air intake tube
2. diaphragm
3. coil
4. electronic circuit
(oscillator)
5. core
6. spring
7. calibration screw
8. connector
A tube connects the pressure switch to an internal pressure takeoff.
When water is loaded into the tub, pressure is created in the water circuit, which moves the diaphragm. When the diaphragm moves, the position of the core inside the coil changes, which varies the inductance and, as a result, changes the frequency of the oscillator. The main board measures this frequency and determines the amount of water that has been loaded into the tub.
Variation of frequency depending on the pressure.
SOI/DT 2006-10 dmm 18/48 599 38 31-91
A two-level pressure switch is used as a safety device with the following functions:
• contact 11-14: antiboiling safety level
• contact 21-24: antiboiling safety level
7.3.1 Calibration of the levels on the pressure switch
Antiboiling levels
Antiboiling levels
Full (mm)
50
± 3
50
± 3
Top-up (mm)
30
± 3
30
± 3
7.4 Power supply and programme selection
The main board (3) is powered by the interference suppressor (1) and by the closure of the contacts of the main switch
(2). The affected connectors are J6-2
(neutral) and J10-1 (line).
The control/display board (4) is powered at 5V by the main board: through the programme selector (5) it is possible to select the programme. The selection of the options / start is performed through the board buttons (4).
The buzzer (if featured) (6) is powered by the display board.
SOI/DT 2006-10 dmm 19/48 599 38 31-91
7.5 Door interlock system
The appliance may be equipped with any of the following types of systems:
• Voltmetric with PTC: when the cycle ends, the user must wait 1 − 3 minutes before opening the door
• Instantaneous: the door can be opened immediately when the cycle ends
• Instantaneous with microswitch (that switches on a lamp or displays the weight of the laundry)
7.5.1 Voltmetric device with PTC
3. Safety lock on door
5. “Door locked” indicator light
• Operating principle
ª When the programme is started by pushing the Start/Pause button, the triac on the main board
(connector J10-2) supplies power to the bimetallic PTC switch (contacts 3-5). After 2-4 seconds, the switch closes (5-4) that feeds power to the electronic components on the machine (but only if the door is closed).
ª This device keeps the door from opening while the machine is operating.
ª When the wash programme ends, the main board removes power from the device, but the door stays locked for 1- 2 minutes (the time required by the PTC to cool down).
• “Door locked” indicator light
ª Some models are equipped with an indicator light which indicates that the door is locked. The light switches off when the door can be opened.
SOI/DT 2006-10 dmm 20/48 599 38 31-91
7.5.2 Instantaneous door interlock
2. Main switch
3. Door interlock device
5. “Door locked” indicator light
• Operating principle
ª When the ON/OFF switch closes and the appliance is switched on, power is applied to the bimetallic
PTC switch (contact 4-2), but the door remains unlocked.
ª When the programme starts (Start/Pause button), the main board sends a 20 msec pulse to contacts
4-3 on the solenoid (connector J10-2 on the board) (at least 6 seconds must have passed since the appliance was switched on). This locks the door and simultaneously closes the main switch (contacts
4-5), thus applying power to all components on the appliance.
ª When the programme ends, the main board sends two additional 20 msec pulses (200 msec apart):
- the first pulse does not unlock the door
- the second pulse (which is sent only if the appliance is operating properly) unlocks the door lock device and simultaneously opens the contacts on the main switch.
• Conditions required for opening the door
ª Before pulses are sent to open the door, the main board checks for the following conditions:
- The drum must not be moving (no signal from the tachometric generator).
- The water level must not be higher than the bottom of the door.
- The water temperature must not exceed 50º C.
• Automatic unlock
ª If a power failure occurs, if the appliance is shut off, or if the solenoid malfunctions, the bimetallic PTC will cool down and the door will unlock in 1 - 4 minutes.
• “Door locked” indicator light
ª Some models are equipped with an indicator light which indicates that the door is locked. The light switches off when the door can be opened.
SOI/DT 2006-10 dmm 21/48 599 38 31-91
7.6 Water fill system
The solenoid valves are powered by the main board through two or three triacs. The state of the pressure switch (full-empty) is detected over two sensing lines.
2. Antiboiling level switch
3. Antiboiling level switch
4. Solenoid valve for prewash
5. Solenoid valve for wash
6. Solenoid valve for bleach (on some models)
Some models of solenoid valves have a built-in flow sensor which measures the quantity of water in litres that is loaded into the appliance.
If the sensor malfunctions, the water level is controlled by the analogue pressure switch.
Solenoid valve – exploded view Main board Turbine
6- Reed switch 7-Magnet
3-Deflector
SOI/DT 2006-10 dmm 22/48 599 38 31-91
7.6.2 Operating principle of flow meter
The main components of the flow sensor are:
1 – Turbine (with magnet and counterweight mounted on the outside)
2 –Reed switch (normally open)
3 – Magnet
Contact closed Contact open
4 – Counterweight
Signal 0 Signal 1
Water entering the solenoid valve rotates the turbine (1) and magnet (3), which passes in front of the reed switch (2), thus closing it. As this contact opens and closes, it generates pulses at a frequency that is a function of water flow.
The turbine completes 230 revolutions for each litre of water. The operating range of the flow sensor is 0.2-
10 bar.
Using the signal it receives, the microprocessor can calculate the number of litres of water passing through the solenoid valve.
Mechanical jamming of solenoid valve
The solenoid valve may jam open without being actuated (which will cause flooding if the pressure switch controlling the water level does not trip). If this occurs, the electronic control system (which continuously monitors the flow sensor) will lock the door, start the drain pump and display an alarm.
Low water pressure
If the flow sensor does not generate a signal during water fill even though power is being applied to the solenoid valve, the cause of this condition may be a closed water tap or clogged filter on the solenoid valve
(with consequent low water pressure). If this occurs, a warning will be displayed and the cycle will continue for five minutes, after which time an alarm will be signalled.
The solenoid valve controlling residual condensed water operates during the drying phase on washerdryers. The alarm is deactivated because the amount of water flow is very small.
SOI/DT 2006-10 dmm 23/48 599 38 31-91
2. Antiboiling pressure switch
AE2
3. Antiboiling pressure switch
AE1
The main board powers the drain pump through a triac in the following way:
ª For a programmed time
ª Until the antiboiling pressure switch closes in the empty position, after which time the pump operates briefly or the programme moves to the next phase.
On jetsystem models, the main board powers the recirculation pump through a triac.
2. Antiboiling pressure switch AE 2
3. Antiboiling pressure switch AE 1
SOI/DT 2006-10 dmm 24/48 599 38 31-91
The Water Control system is a sensor located in contact with the base frame. The sensor detects water leaks inside the machine (not only during normal operation, but also when the unit is off and plugged in) and starts the drain pump if a leak occurs.
2. Antiboiling pressure switch
AE2
3. Antiboiling pressure switch
AE1
Besides supporting the various components on the appliance (drain pump, recirculation pump, shock absorbers, etc.), the base frame is designed to be a container that collects any water leaks that may occur
(from the tub, from a tube or pipe, etc.). These leaks are directed into an area where a float is installed.
When this float is raised by water, it actuates a microswitch that starts the drain pump. When the switch is tripped, an alarm is also signalled (if the machine is switched on).
1. microswitch
2. float
SOI/DT 2006-10 dmm 25/48 599 38 31-91
2. Antiboiling pressure switch AE
2
3. Antiboiling pressure switch
AE1
5. NTC temperature sensor
The heating element is powered by a relay on the main board through the contacts on the pressure switches, which must be closed on “full”.
(1950W)
2. NTC sensor
The temperature is controlled by the main board using an NTC temperature sensor.
TEMPERATURE
(ºC) Nominal value
RESISTANCE (
Ω)
Maximum value Minimum value
20
60
80
6050
1250
640
6335
1278
620
5765
1222
660
SOI/DT 2006-10 dmm 26/48 599 38 31-91
This sensor is installed only on machines equipped with a recirculation pump.
1. Housing
2. Electronic circuit
3. Transparent tube
The sensor consists of a transparent tube installed in the water circulation circuit. A diode (4) on the side of the tube emits infrared rays (at a frequency of 2.3 KHz, as generated by the electronic circuit) and a phototransistor (5) on the other side of the tube is hit by the rays. The amount of current conducted by the phototransistor depends on the how clear the water is: the clearer the water, the more current the phototransistor conducts and, as a result, the higher the voltage output from the electronic circuit.
Low Conduction Medium Conduction Maximum Conduction
The turbidity sensor operates during the Whites and Colours programmes (COTTON).
It does not operate during the 60°C and 40°C Energy Saving programmes and the Night cycle.
The sensor is calibrated at the end of the wash cycle.
The sensor detects the turbidity of the water at the end of the first rinse and again at the beginning of the second rinse. The relationship between the two measurements is compared with values programmed on the board, and the result of the comparison determines whether another rinse is carried out.
SOI/DT 2006-10 dmm 27/48 599 38 31-91
7.12 Inverter
The EWM3000 electronic control system uses a new 2-pole, three-phase, asynchronous motor offering high performance at low noise levels.
L = Phase
N = Neutral
General schematic of the inverter
A = Inverter board
B = Motor
C = Condenser
D = Diodes
I1-6 = Switches
F1-3 = Motor connectors
μ
P =
A newly designed circuit board (A) is used to convert single-phase power (available in homes) into threephase power. The amplitude and frequency of the three-phase power can be varied to adjust motor power and RPM, respectively.
Single-phase power (applied to connectors L-N) is rectified by a diode bridge (D) to generate 310 VDC at the poles of condenser C. The combined opening and closing of switches I1-I6 (this switching is performed by the microprocessor) determines the voltage and frequency of the power applied to the motor.
Clockwise motor operation Counter-clockwise operation
Motor speed is controlled using the signal from a tachometric generator (T).
During spin phases, the microprocessor may perform (depending on the configuration of the software) checks for antifoam (if available on the machine) and anti-unbalancing.
The electrical components must be serviced by qualified personnel only
Unplug the appliance before accessing internal components
SOI/DT 2006-10 dmm 28/48 599 38 31-91
7.13 Motor
2. Antiboiling pressure switch AE2
3. Antiboiling pressure switch AE1
4. Inverter
5. Motor
T = tachometric generator
X-Y-X = motor windings
7.14 Power feed to motor
Three-phase power is fed by the inverter (4) to connectors 5-6-8, which are connected to connectors 5-6-4 on the motor (nodes V-W-U), where the windings (Y-X-Z-) are connected. The phase shift between the phases is 120° and peak amplitude is 310V.
The condition of the motor can be determined by measuring the resistance of the windings:
Winding y:
∼
5.4 ohms ±7% (contacts 1-2)
Winding x:
∼
5.4 ohms ±7% (contacts 2-3)
Winding z:
∼
5.4 ohms ±7% (contacts 1-3)
Winding T (tachometric):
∼
121 ohms ±7% (contacts 4-5)
The electrical components must be serviced by qualified personnel only
Unplug the appliance before accessing internal components
SOI/DT 2006-10 dmm 29/48 599 38 31-91
The anti-foam system (if installed) is controlled by the antiboiling pressure switch (AB).
Spin phase without foam Spin phase with little foam
Spin
Pulse at 300 RPM
Pulse at 300
RPM
Antifoam
(Level AB)
Spin
FUCS FUCS
• Spin phase with little foam: if the contact of pressure switch AB closes on “full”, the spin phase is interrupted and the drain pump continues to operate. When the contact returns to “empty”, the spin phase resumes.
• Spin with too much foam in the tub (critical situation): this condition is signalled if the pressure switch moves to “full” 5 times. If this occurs, the spin phase is skipped and the appliance drains for one minute with the motor stopped. If the spin at the end of the wash phase is skipped, an extra rinse phase is added.
SOI/DT 2006-10 dmm 30/48 599 38 31-91
7.16 FUCS (Fast Unbalance Control System)
The control procedure for unbalanced loads is performed dynamically, before each spin cycle, as follows:
ª The phase begins at a speed of 55 RPM. The speed may not drop below this threshold; if it does, the check is repeated.
ª At intervals of 300 ms, the balance is calculated and compared with established limits. If the value is lower than the limit, drum speed is increased by a certain amount that depends on the transmission ratio between the motor pulley and the drum. If unbalance is greater than the limit, the speed is decreased by the same amount, which enables the laundry to arrange itself correctly. The process continues until the load is completely balanced.
ª Correct balancing of the load occurs at 115 RPM. After this speed is reached, the spin cycle begins.
Selected speed
True speed
The unbalance control procedure may be performed in a number of phases. Each phase involves:
ª an unbalancing rating (0-1-2-3)
ª an unbalancing threshold (ex: 350, 650, 850, 1200g)
ª a timeout
• Conclusion of the FUCS procedure
The FUCS procedure is considered to be concluded when:
ª The speed of drum rotation is 115 RPM (or 85 RPM for certain unbalance ratings). At this point, the scheduled spin phase is carried out.
ª In some cases, optimum balance is not reached and the spin is performed at a lower speed that depends on the level of unbalance.
ª In the worst case scenario, a minimum level of balance is not achieved after all the FUCS phases have been performed and the spin phase is skipped.
• Situation of ideal balancing
Phase 0,
Timeout = 60 sec
115 RPM
Phase 1
Timeout = 120 sec
55
RPM
SOI/DT 2006-10 dmm 31/48 599 38 31-91
• An example of drum balancing in the longest interval of time available
1 2 3 4 5 6 7
1 0 60
2 1 120
3 2
4 3
60
90
5 1 120
6 2 60
7 3 90
• An example of unbalancing after all FUCS phases have been performed
In this case, the spin (or pulse operation) is skipped.
SOI/DT 2006-10 dmm 32/48 599 38 31-91
8 DEMO Mode
A special cycle has been created for demonstration of the operation of these appliances in retail outlets without connecting the appliance to the water supply. In this way, the salesman can select any programme; after starting the cycle by pressing START, the appliance will perform certain phases only, and will skip those which cannot be performed (water fill, drain, heating).
The cycle takes place as follows:
ª the door locking device is actioned in the normal way (i.e. the door remains locked while the appliance is in operation, and can be opened at the end of the cycle or in pause mode)
ª motor: all low-speed movements are enabled, while the pulse signals and the spin cycle are excluded
ª the water fill solenoids and the drain pump are disabled
ª display: since the phases of the cycle take place in rapid succession (1 second of the demo cycle is equivalent to 1 minute of the actual cycle), the time-to-elapse decreases by 1 unit per second.
Remember that the time-to-elapse does not always correspond to the actual cycle time
ª alarms: for reasons of safety, the following groups of alarms remain enabled: E40 (door closed), E50 and E90 (communication between the boards/configuration).
8.1 Demo mode setting
ª Switch the appliance off
ª Press rotating the programme selector of two positions clockwise
ª Hold
8.2 Exiting demo mode
ª To exit demo mode, switch the appliance off.
SOI/DT 2006-10 dmm 33/48 599 38 31-91
9.1 Access to diagnostics system
Using a single procedure, it is possible to access to the diagnostics system. After accessing this function, the following operations can be performed:
control of the operation of each of the components in the appliance
read / cancel the alarms
The diagnostics cycles are available only if the communication between the main PCB and the display board is correct; moreover there should not be configuration errors of the appliance.
To access:
1. Cancel the set programme and switch the appliance off.
2. Press buttons 1 and 2 simultaneously and then, holding them down, switch the appliance on by rotating the programme selector of one position clockwise.
In the first position the function test of the buttons and the corresponding LEDs is performed; by rotating the programme selector clockwise the operation diagnostics of each component and the reading of the alarms is carried out.
9.2 Exiting diagnostics system
ª To exit the diagnostics system switch the appliance off, on and then off again.
9.3 Phases of the diagnostics test
Independently of the type of selector, after activating the diagnostics system, the operation diagnostics of the different components and the reading of the alarms can be performed, by rotating the selector
clockwise.
In the diagnostics cycle all alarms are activated. If during the cycle operation an alarm occurs, the appliance blocks and the LEDs (and the display) flash indicating the relative code.
SOI/DT 2006-10 dmm 34/48 599 38 31-91
Selector position
1
2
3
4
5
6
7
8
9
Diagnostics phases
Components actioned Operating conditions
All the LEDs light in sequence. When a button is pressed, the corresponding
LED lights (and the buzzer, if featured, sounds)
Always activated
Door interlock
Washing solenoid
Door locked
Water level below anti-flooding level
Maximum time 5 minutes
Door interlock
Pre-wash solenoid
Door interlock
Pre-wash and wash solenoids
Door locked
Water level below anti-flooding level
Maximum time 5 minutes
Door locked
Water level below anti-flooding level
Maximum time 5 minutes
Door interlock.
Bleach/stains solenoid.
Door locked
Water level below anti-flooding level
Maximum time 5 minutes
Function checked
Operation of the user interface
Water ducted through washing compartment
Water ducted through pre-wash compartment
(bleach)
Water ducted through conditioner compartment
Water ducted through bleach/stains compartment
Door interlock
Washing solenoid if the level of water in the tub is below
1st level
Heating element.
Door locked.
Water at 1st level.
Maximum time 10 min. or up to 90ºC. (*)
Heating
Door interlock.
(Washing solenoid if the level
Door locked of water in the tub is below 1st
Water level at 1st level.
level). Motor (55 rpm clockwise, 55 rpm counterclockwise, 250 rpm impulse)
Check for leaks from the tub
Door interlock
Drain pump
Door locked
Water level lower than
Drain and spin; control of
Motor up to 650 rpm then at anti-boiling level for maximum spin speed spinning
--- --- congruence in closure of level pressure switches
--- ---
10 Reading/cancelling last alarm --- ---
11, 12 ...24
All LEDs light in sequence. Pressing a button the corresponding LED lights
(and the Buzzer sounds, if featured)
(*) In most cases, this time is sufficient to check the heating. However, the time can be increased by repeating the phase without draining the water: for a moment to a different phase of the diagnostics cycle and then back to the heating control phase (if the temperature is higher than 80°C, heating does not take place).
SOI/DT 2006-10 dmm 35/48 599 38 31-91
9.3.1 LEDs display board diagnostics
After entering the diagnostics system, the display board is checked: all LEDs and the display light in sequence (if featured).
Pressing all buttons, the corresponding
LEDs switch on or those closer; the display shows the hexadecimal code corresponding to the button codification.
In the table are indicated the closures between the contact C6
(common) and the other contacts (C
1−C5) of the programme selector in the different positions and the corresponding codification. The code is displayed only in the appliances with display.
Selector position
Closure of selector contacts
(C6 is the common)
Type 24 positions
1 - Cancel
2
3
4
5
6
7
C1 C2 C3 C4 C5
0 1 1 1 1
0 1 0 0 1
0 1 1 0 0
0 1 0 1 0
0 1 1 1 0
8
9
10
11
12
13
0 0 0 1 1
1 0 0 0 0
1 0 0 0 1
1 0 0 1 0
0 1 0 1 1
0 0 1 0 1
1 0 0 1 1
1 0 1 0 0
19
20
21
22
23
24
14
15
16
17
18
0 0 1 1 0
1 0 1 0 1
0 0 1 1 1
1 0 1 1 0
1 0 1 1 1
1 1 0 0 0
0 1 1 0 1
0 0 0 0 1
0 1 0 0 0
0 0 0 1 0
0 0 1 0 0
SOI/DT 2006-10 dmm 36/48 599 38 31-91
10 ALARMS
10.1 Displaying the alarms to the user
Control of the alarm system can be configured; according to the model, therefore, some or all of the alarms may be displayed to the user.
Normally all the alarms are displayed to the user except for:
- E10 – water fill
- E20 – drain water
- E40 – door closure
- E90 – configuration
The alarms are active during the execution of the washing programme; except for the alarms relative to the configuration and power/frequency supply which are displayed also in the selection phase.
The door can normally be opened (except where specified) when an alarm condition has occurred on condition that:
• The level of the water in the tub is below 1st level
• The temperature of the water is lower than 55°C
Certain alarm conditions require that a drain phase be performed before the door can be opened:
• Cooling water fill if the temperature is in excess of 65°C
• Drain until closure of both pressure switch contacts (1st level and anti-boiling safety system) on
EMPTY within a maximum of 3 minutes.
10.1.1 Alarms displayed during normal operation
The type of alarm condition is displayed to the user by the repeated flashing of the
END OF CYCLE LED (0.4 seconds lit, 0.4 seconds off, with an interval of 2.5 seconds between sequences). This LED is featured on ALL MODELS, though configured in different positions.
If, for example, the user should forget to close the door, the control system will detect alarm E41 about 15 seconds after the start of the cycle; the cycle remains in PAUSE mode and the display, if featured, would display E40.
Simultaneously the LED end-of-cycle flashes repeating the sequence indicated in the table.
The four flashing indicate the first of the two digits of the alarm
LED end of cycle
On/Off
Time
(Sec.)
Value
0.4 1
0.4
0.4 2
E
4
1 (the alarms relative to a same function are grouped by families).
In this case, once the door has been closed, it is sufficient to press the start button to start the programme.
0.4
0.4 3
0.4
4
0.4
0.4
2.5
Pause between sequences
SOI/DT 2006-10 dmm 37/48 599 38 31-91
10.2 Reading the alarm codes
In order to read the last alarm code memorized in the EEPROM on the PCB:
• Enter diagnostics mode
• Irrespective of the type of PCB and configuration, turn the programme selector clockwise to the tenth position.
10.2.1 Displaying the alarm
The alarm is displayed by a repeated flashing sequence of the two LEDs (0.4 seconds lit, 0.4 seconds off, with an interval of 2.5 seconds between sequences).
The buzzer (if featured) will sound “bips” in synchronization with the flashing of
the LEDs.
• END OF CYCLE LED → indicates the first digit of the alarm code (family)
• START/PAUSE → indicates the second digit of the alarm code (number within the family)
These two LEDs are featured on all models (though they are configured
differently), and flash simultaneously.
Notes:
• The first letter of the alarm code “E” (Error) is not displayed, since this letter is common to all alarm codes.
• The alarm code “families” are shown in hexadecimal; in other words:
→ A is represented by 10 flashes
→ B is represented by 11 flashes
→ ...
→ F is represented by 15 flashes
• Configuration errors are shown by the flashing of a series of LEDs.
10.2.2 Examples of alarm displays
Example: Alarm E43 will display the following:
• On the display, if featured, E
4 3
• The sequence of four flashes of the End-of-cycle LED indicates the first number E 4 3;
• The sequence of three flashes of the Start/Pause LED indicates the second number E4 3 ;
END-OF-CYCLE LED
On/Off
Time
(Sec.)
START/PAUSE LED
Time
Value On/Off
(Sec.)
Value
0.4 0.4
1 1
0.4 0.4
0.4 0.4
2 2
0.4 0.4
0.4 0.4
3 3
0.4 0.4
0.4
4
0.4 3,3 Pause
2.5 Pause
SOI/DT 2006-10 dmm 38/48 599 38 31-91
10.2.3 Operation of alarms during diagnostics
All alarms are enabled during the components diagnostics phase. Moving the selector to pass from one control phase to the other, the appliance exits the alarm condition and performs the selected phase (if the alarm does not occur again).
10.3 Notes about some alarms
Configuration alarms
ª E91: the error is indicated by the flashing of all the LEDs, E90 is displayed on the display, if featured
ª E92: the error is indicated by the flashing of the LEDs placed over the buttons, E90 is displayed on the display, if featured
ª E93: the error is indicated by the flashing of the phase/warning LEDs, E90 is displayed on the display, if featured
ª E95: the error is indicated by the flashing of the LEDs, is displayed on the display, if featured
ª EB1-EB2-EB3 alarms: in case of problems with the power supply, the machine remains in alarm condition till the frequency or the power supply voltage returns to correct values or the appliance is switched off. “EB0” alarm family is displayed and it is not possible to enter the diagnostics or to use “alarm fast display” mode: the alarm complete can be read only when the abnormal situation terminated.
10.4 Rapid reading of alarm codes
The last alarm code can be displayed even if the programme selector is not in the tenth position
(diagnostics) or if the appliance is in normal operating mode (e.g. during the execution of the washing programme):
ª Press sequence of flashes indicating the alarm.
ª The alarm sequence is displayed for the time in which the buttons are hold down
ª The reading system is the same as that indicated in paragraph. 10.2
ª During the time the alarm is displayed, the appliance continues to perform the cycle or, if it is in the selection phase, it keeps in memory the options previously chosen.
10.5 Cancelling the last alarm
It is good practice to cancel the last alarm, after reading the alarm code to check whether the alarm reoccurs during the diagnostics control after the reparation of the appliance.
1. Select diagnostics mode and turn the programme selector to the tenth position (reading of alarm)
SOI/DT 2006-10 dmm 39/48 599 38 31-91
10.6 Table of alarm codes
Alarm
E11
E13
E21
E23
E24
E31
E32
E33
E34
E35
E36
Description
Poor water fill before wash cycle
Water leaks
Possible malfunction Action/status of machine
Tap closed or water pressure too low; Drain tube improperly positioned;
Water fill solenoid valve is defective; Leaks from water circuit on pressure switch; Pressure switch defective; Wiring defective; Main board
Cycle is paused with door locked. defective.
Drain tube improperly positioned; Water pressure too low;
Water fill solenoid valve is defective; Water circuit on pressure switch is leaking/clogged; Pressure switch defective.
Cycle is paused with door locked.
Poor draining
Defective triac for drain pump
Malfunction in sensing circuit on triac for drain pump
Drain tube kinked/clogged/improperly positioned; Drain filter clogged/dirty; Drain pump defective; Pressure switch defective; Wiring defective; Main board defective; Electrical current leak between heating element and ground.
Cycle is paused.
Drain pump defective; Wiring defective; Main board defective.
Main board defective.
Emergency drain procedure - Cycle stops with door unlocked.
Emergency drain procedure - Cycle stops with door unlocked.
Malfunction in pressure switch circuit
(frequency of signal from pressure switch out
Pressure switch;
Wiring; of limits) Main board.
Electronic pressure switch improperly calibrated (level on electronic pressure switch differs from 0-66 mm after initial calibration drain and when antiboiling pressure switch is on “empty”).
Tap is closed or water pressure is too low;
Solenoid valve;
Water circuit on pressure switches; pressure switches;
Wiring; main board.
Inconsistency between level on electronic pressure switch and level on antiboiling pressure switch 1-2 (fault persists for at least
60 sec.).
Pressure switch defective;
Electrical current leak between heating element and ground; Heating element; Wiring defective;
Main board defective.
Water circuit.
Cycle stops with door locked.
Cycle is paused.
Emergency drain procedure - Cycle stops with door unlocked.
Pressure switch defective;
Inconsistency between level on electronic
Electrical current leak between heating element and ground; Heating pressure switch and level on antiboiling pressure switch 2 (fault persists for at least 60 element; Wiring defective; sec.).
Main board defective.
Water circuit.
Overflow
Emergency drain procedure - Cycle stops with door unlocked.
Water fill solenoid valve is defective; Leaks from water circuit on
Cycle stops. Emergency drain pressure switch; Pressure switch defective; Wiring defective; Main board procedure. Drain pump continues to defective. operate (5 min. on, then 5 min. off, etc.).
Sensing circuit on antiboiling pressure switch
1 defective
Main board defective. Cycle stops with door locked.
Reset
Start
Start
Start
OFF/reset
OFF/reset
OFF/reset
Start
OFF/reset
OFF/reset
OFF/reset
OFF/reset
SOI/DT 2006-10 dmm 40/48 599 38 31-91
Alarm
E37
E38
E39
Description
Sensing circuit on antiboiling pressure switch
Main board defective.
2 defective
Internal pressure takeoff is clogged (water level does not change for at least 30 sec. of drum rotation).
Possible malfunction
Water circuit on pressure switches;
Pressure switches;
Motor belt broken.
Defective HV sensing on overflow prevention system
Main board defective.
E3A Faulty sensing by heating resistance relay Main board defective.
E41
E42
E43
E44
E45
Door unlocked
Problems closing the door
Door lock unit defective; Wiring defective;
Main board defective.
Door lock unit defective; Wiring defective;
Main board defective
Defective triac supplying power to door delay Door lock unit defective; Wiring defective; system Main board defective.
Defective sensing by door delay system Main board defective.
Defective sensing by triac on door delay system
Main board defective.
Action/status of machine
Cycle stops with door locked.
Heating phase is skipped.
Cycle stops with door locked.
Cycle stops with door locked.
Cycle is paused.
Cycle is paused.
(Safety drain cycle) Cycle stops.
(Safety drain cycle) Cycle stops.
(Safety drain cycle) Cycle stops.
E52
E57
E58
No signal from tachometric generator on motor
Inverter is drawing too much current (>15A)
Motor is drawing too much current (>4.5A)
Motor defective; Wiring defective on inverter for motor;
Inverter board defective.
Motor defective; Wiring defective on inverter for motor, inverter board defective.
Motor defective; Wiring defective on inverter for motor, inverter board defective, abnormal motor operation (motor overloaded).
E59
E5A
No signal from tachometric generator for more Motor defective; Wiring defective on inverter for motor; than 3 seconds Inverter board defective.
Overheating on heat dissipater for inverter
Inverter board defective. NTC open (on the inverter board).
Overheating caused by continuous operation or ambient conditions (let appliance cool down).
E5B
E5C
E5D
E5E
E5F
E61
Cycle stops with door locked (after 5 attempts).
Cycle stops with door locked (after 5 attempts).
Cycle stops with door locked (after 5 attempts).
Cycle stops with door locked (after 5 attempts).
Cycle stops with door locked (after 5 attempts).
Input voltage is lower than 175V Wiring defective, Inverter board defective.
Input voltage is too high
Inverter board defective, the mains voltage is too high (measure the mains voltage).
Data transfer error between inverter and main Line interference, Wiring defective, defective main board or inverter board board.
Communication error between inverter and main board
Defective wiring between main board and inverter board,
Defective inverter board, defective main board.
Inverter board fails to start the motor
Insufficient heating during wash cycle
Cycle stops with door locked (after 5 attempts).
Cycle stops with door locked (after 5 attempts).
Cycle stops with door locked (after 5 attempts).
Cycle stops.
Defective inverter board, Defective wiring, defective main board.
Cycle stops with door locked (after 5 attempts).
Defective NTC sensor for wash cycle; Heating element defective; Wiring
Heating phase is skipped. defective; Main board defective.
Reset
OFF/reset
---
OFF/reset
OFF/reset
Start
Start
OFF/reset
OFF/reset
OFF/reset
OFF/reset
OFF/reset
OFF/reset
OFF/reset
OFF/reset
OFF/reset
OFF/reset
OFF/reset
OFF
OFF/reset
Start
SOI/DT 2006-10 dmm 41/48 599 38 31-91
Alarm
E62
E66
E71
E74
E82
E83
E84
E85
E91
E92
E93
E94
E95
E97
EB1
EB2
EB3
EBE
EBF
EC1
EC2
Description
Overheating during wash cycle
Relay supplying power to heating element defective
NTC sensor for wash cycle defective
NTC sensor for wash cycle improperly positioned
Possible malfunction Action/status of machine
Defective NTC sensor for wash cycle; Heating element defective; Wiring Safety drain cycle - Cycle stops with defective; Main board defective. door unlocked.
Main board defective; Electrical current leak from heating element to ground.
Safety drain cycle - Cycle stops with door unlocked.
Defective NTC sensor; Wiring defective;
Main board defective.
NTC sensor improperly positioned; Defective NTC sensor; Wiring defective; Main board defective.
Heating is skipped.
Heating is skipped.
Error in selector reset position
Error in reading selector
PCB faulty (Wrong configuration data). Selector, wiring.
PCB faulty (Wrong configuration data). Selector, wiring.
Recirculation pump defective (inconsistency Recirculation pump; between the state of the sensing circuit for the Wiring; recirculation pump and the state of the triac) Main board.
Defective sensing circuit on triac for recirculation pump (input voltage on microprocessor remains at 0 or 5 V).
Main board.
Cycle cancelled.
Machine drains and cycle stops (with door unlocked).
Machine drains and cycle stops (with door unlocked).
---
Communication error between main board and Wiring defective; Control/display board defective display board Main board defective.
Inconsistency in communication between main
Wrong control/display board; board and display board
(versions not compatible)
Wrong main board (not right for model).
Configuration error on appliance
Configuration error on wash cycle
Main board defective (Improper programming).
Main board defective (Improper programming).
Communication error between microprocessor and EEPROM
Main board defective.
Inconsistency between list of programmes and
Main board defective (Improper programming). configuration of cycle
Cycle stops.
Cycle stops.
Cycle stops.
Cycle stops
Cycle stops.
Cycle stops.
Frequency of power supplied to appliance out Problems with the power mains (wrong power/interference); Main board of limits defective.
Cycle stops.
Input voltage too high
Problems with the power mains (wrong power/interference); Main board defective.
Cycle stops.
Input voltage too low
Inconsistency between safety relay and sensing circuit
Sensing circuit on safety system defective
Problems with the power mains (wrong power/interference); Main board
Cycle stops. defective.
Main board defective, defective wiring.
(input voltage on microprocessor remains at 0 Main board defective. or 5 V).
Machine drains and cycle stops (with door unlocked).
Machine drains and cycle stops (with door unlocked).
Solenoid valve inoperative but flow meter operating
Main board defective, Solenoid valve defective.
Signal from turbidity sensor out of limits Turbidity sensor defective, Main board defective, Wiring defective.
Cycle stops with door locked (after 5 attempts).
-----------------------
Reset
OFF/reset
OFF/reset
Start
Start
OFF/reset
---
OFF/reset
OFF/reset
---
---
OFF/reset
OFF/reset
OFF/reset
OFF/reset
---
---
---
OFF/reset
OFF/reset
OFF/reset
Start/reset
SOI/DT 2006-10 dmm 42/48 599 38 31-91
Alarm
EF1
EF2
EF3
EF4
Description Possible malfunction
Drain filter clogged
(drain cycle too long)
Too much detergent
(too much foam during drain cycles)
Drain tube clogged/kinked/placed too high;
Drain filter dirty/clogged.
Too much detergent used; Drain tube clogged/kinked;
Drain filter dirty/clogged.
“Water Control” system tripped Water leaks onto base frame; water control system defective.
Water fill pressure too low, no signal from flow
Tap closed, water pressure too low. meter and solenoid valve is open
E00 No alarm
Action/status of machine
Warning is displayed at end of cycle
(relative LED is lit).
Warning is displayed at end of cycle
(relative LED is lit).
Machine drains and cycle stops.
---------------------------
Reset
---
---
OFF/reset
Reset
SOI/DT 2006-10 dmm 43/48 599 38 31-91
11 Operating time counter
It is possible to display, with a specific procedure, the operating time of the appliance, which is counted from the first switching on.
This option is available only in models with display. The maximum memorization capacity is 6550 operating hours.
Only the operating time of normal programmes is displayed (not diagnostics cycles)
The actual time of the cycle performed is counted (not the pauses, the delayed start time, rinse hold and the soak phases)
The memorization is 30 seconds for each programme
Only operating hours are displayed (1h and 59min = 1h)
11.1.1 Operating time reading
1. Switch the appliance off. the programme selector by three positions clockwise.
1. Hold the buttons 1 and 5 down for about 5 seconds.
11.1.2 Displaying the operating time
The operating time is displayed two digits at a time: the first pair of digits shows the thousands and hundreds; the second pair shows tens and units.
For example, a total operating time of 6,550 hours will be displayed as follows:
1
→ 2 →
Blank display for two seconds
The first pair of digits is displayed for two seconds:
- thousands (6)
- hundreds (5)
The second pair of two digits is displayed for two seconds:
- tens (5)
- units (0)
SOI/DT 2006-10 dmm 44/48 599 38 31-91
12 ACCESSING COMPONENTS
Procedures for accessing specific components on the appliance are described in this section. For information on other procedures, see the general service manual for ARCHED washing machines
ARCHED (599 37 67-82).
The electrical components must be serviced by qualified personnel only
Unplug the appliance before accessing internal components
If the flow meter malfunctions, the entire solenoid valve assembly must be replaced.
12.2 Aqua control
Insert a screwdriver into the holes indicated by the arrows.
Extract it and detach the connectors.
12.3 Motor
Detach the connectors.
Release the rear screws and loosen the front ones.
Remove the motor from the supports.
Remove the front screws.
Extract the motor.
SOI/DT 2006-10 dmm 45/48 599 38 31-91
13 Contacts on Main Board
14 Contacts on inverter board
SOI/DT 2006-10 dmm 46/48 599 38 31-91
15 BASIC CIRCUIT DIAGRAM WITH SENSORS
SOI/DT 2006-10 dmm 47/48 599 38 31-91
15.1 Key for circuit diagram
Electrical components on appliance
6. Antiboiling pressure switch AE2
7. Door lock unit
9. Antiboiling pressure switch AE1
10. Recirculation pump
11. Solenoid valve for prewash
12. Solenoid valve for wash
13. Solenoid valve for bleach
14. Selector
15. Door opening lamp
16. Control/display board
17. Flow meter
18. Analogue pressure switch
19. Turbidity sensor
20. NTC temperature sensor
21. Tachometric generator (on motor)
22. Windings (on motor)
23. Inverter (for motor speed control)
BELV_TY
DOOR_TY
DRAIN_TY
K1
PWELV_TY
REC_TY
WELV_TY
Components on main board
Triac for solenoid valve for bleach dispenser
Triac for door lock unit
Triac for drain pump
Relay controlling heating element
Triac for solenoid valve for prewash
Triac for recirculation pump
Triac for solenoid valve for wash
SOI/DT 2006-10 dmm 48/48 599 38 31-91
advertisement
* Your assessment is very important for improving the workof artificial intelligence, which forms the content of this project
Related manuals
advertisement
Table of contents
- 13 Purpose of this manual
- 13 IMPORTANT
- 13 GENERAL SPECIFICATIONS
- 13 CONTROL PANEL
- 13 CONTROL/DISPLAY BOARD
- 13 Version with display
- 13 Washing programmes
- 13 Configuration of the programmes
- 13 Programme selector
- 13 Start/Pause
- 13 Functions of the buttons
- 13 WASH PROGRAMMES AND OPTIONS
- 13 Possible programmes
- 13 Options for the wash cycle
- 13 Description of options
- 13 Night cycle
- 13 Stop with water in the tub
- 13 Prewash
- 13 Stain removal
- 13 Short Daily
- 13 Very Short (Quick)
- 13 Heavy-duty
- 13 Energy saving / Energy label
- 13 Sensitive
- 13 Extra rinse
- 13 “Half load” button
- 13 Easy-Iron
- 13 Reduced spin speed
- 13 No spin
- 13 Spin speed adjustment
- 13 Reduced times (Quick)
- 13 Temperature adjustment
- 13 Delayed-start time
- 13 Exclusion of the buzzer
- 13 Variation of rinses when options are selected
- 13 Display (some models)
- 13 TECHNICAL CHARACTERISTICS
- 13 EWM3000NEW Electronic control system
- 13 Functions provided by the electronic board
- 13 Memories contained in the electronic control system
- 13 Analogue pressure switch (electronic)
- 13 Pressure switch
- 13 Calibration of the levels on the pressure switch
- 13 Power supply and programme selection
- 13 Door interlock system
- 13 Voltmetric device with PTC
- 13 Instantaneous door interlock
- 13 Water fill system
- 13 Flow meter
- 13 Operating principle of flow meter
- 13 Drain pump
- 13 Recirculation pump
- 13 Water Control
- 13 Heating system
- 13 Heating element
- 13 Temperature sensor
- 13 Turbidity sensor
- 13 Inverter
- 13 Motor
- 13 Power feed to motor