- Computers & electronics
- Software
- Remote Automation Solutions
- OpenEnterprise NW3000 Advanced
- Reference guide
Remote Automation Solutions OpenEnterprise NW3000 Advanced Reference Guide
Add to My manuals23 Pages
Remote Automation Solutions OpenEnterprise NW3000 Advanced
The NW3000 Advanced Configuration Tool is a valuable tool for managing your NW3000 Drivers, Networks, and Devices. With this tool, you can:
- View and modify general Driver properties, including the Address, Disable NW3000 Driver, and OpenBSI Connectivity Timeout.
- Configure Network properties, such as the Disable Network and Device Statistics Update Period.
- Manage Device properties, including the Device Disable, Device Connectivity Check Period, and Scan rate.
- Create and manage Schedules, which allow you to define the collection period (interval) and offset for data collection.
advertisement
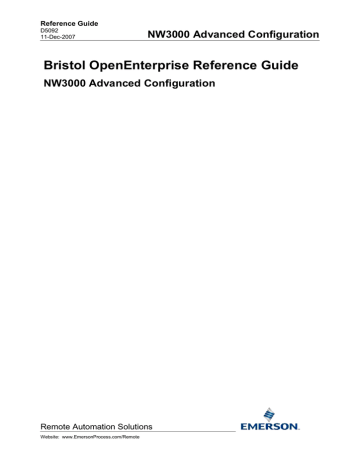
Reference Guide
D5092
11-Dec-2007
NW3000 Advanced Configuration
Bristol OpenEnterprise Reference Guide
NW3000 Advanced Configuration
Remote Automation Solutions
Website: www.EmersonProcess.com/Remote
Reference Guide
D5092
11-Dec-2007 - Page 2
NW3000 Advanced Configuration
Contents
1 NW3000 Advanced Configuration Tool ................................................................................. 4
2 NW3000 Driver Tab .................................................................................................................. 5
Maximum Allowable Number of Connection Fails .................................................... 8
Maximum number of pending requests per device ................................................... 9
3 Network Tab ........................................................................................................................... 11
4 Device Tab .............................................................................................................................. 13
Remote Automation Solutions
Website: www.EmersonProcess.com/Remote
Reference Guide
D5092
11-Dec-2007 - Page 3
NW3000 Advanced Configuration
5 Schedules Tab........................................................................................................................ 17
6 Index ....................................................................................................................................... 22
Remote Automation Solutions
Website: www.EmersonProcess.com/Remote
Reference Guide
D5092
11-Dec-2007 - Page 4
NW3000 Advanced Configuration
1 NW3000 Advanced Configuration Tool
The NW3000 Configuration Tool allows the user to view and modify the following properties: -
• General Driver properties;
• Network properties;
• Device properties;
• Schedules.
Remote Automation Solutions
Website: www.EmersonProcess.com/Remote
Reference Guide
D5092
11-Dec-2007 - Page 5
NW3000 Advanced Configuration
2 NW3000 Driver Tab
The Driver Tab displays a list of all available NW3000 Drivers. The [Properties] button is activated when the NW3000 Driver is selected. Selecting this button opens the NW3000 Driver Property page dialog.
2.1 NW3000 Driver Property Dialog
This dialog enables the user to edit NW3000 Driver connectivity settings.
Remote Automation Solutions
Website: www.EmersonProcess.com/Remote
Reference Guide
D5092
11-Dec-2007 - Page 6
NW3000 Advanced Configuration
2.1.1 Address
This is the name of the TCP/IP service offered by the NW3000 RDI. The default name is 'rdi3000'.
There is a line in the 'Services' file, found in the 'C:\Winnt\System32\Drivers\etc' directory which links the rdi3000 driver name with a TCP/IP service number: - e.g. rdi3000 11004/tcp RDI3000
2.1.2 Disable NW3000 Driver
If checked, the NW3000 Driver (and therefore all associated networks, devices and datum) is disabled. If left unchecked, the NW3000 Driver is enabled. The default value is NULL.
2.1.3 database to NW3000 Driver Retry Period
This is the frequency in seconds at which the the database will attempt to connect to the NW3000
Driver if connection is lost. The default value is 15 seconds.
Remote Automation Solutions
Website: www.EmersonProcess.com/Remote
Reference Guide
D5092
11-Dec-2007 - Page 7
NW3000 Advanced Configuration
This is the frequency in seconds at which the database will poll the NW3000 Driver if no messages are received from it. The default is 10 seconds.
2.1.5 NW3000 Driver to Device Check Period
This is the frequency in seconds at which the health of the number of NW3000 devices defined in the
'Slice' field will be checked. The default value is 60 seconds.
2.1.6 Slice - (Number of Devices to Check)
The number of NW3000 devices to health check at the rate defined in the 'Period' field. The default value is -1 (all devices).
2.1.7 Auto Start OpenBSI
If checked, the NW3000 RDI will start OpenBSI, if it not already running, when the NW3000 RDI starts. If unchecked, the NW3000 RDI will not auto start OpenBSI.
Note that if the above option is set, then you will have to also create and set two values on the
RDI3000 registry key. Open the Settings Editor and find the OpenEnterprise\Tasks\RDI3000 key.
Then on it create the following values: -
Name Data
EnableBSAUTO
BSAUTOFormatString
Set to 1 to use BSAUTO to start OpenBSI. Used in conjunction with BSAUTOFormatString.
When set to 0, the BSIStartSys API call will be used to start OpenBSI.
Default value is 0.
The format string used as the BSAUTO command line.
Default value is "BSAUTO -std SYSTEM SYSTEM
%s" where %s represents the NDF filename specified within the nw3000driver. obsistartndf attribute.
2.1.8 Auto Stop OpenBSI
If checked, the NW3000 RDI will stop OpenBSI when it closes. If unchecked, the NW3000 RDI will not auto close OpenBSI.
2.1.9 OpenBSI Connectivity Timeout
The number of seconds after which attempts by the NW3000 Driver to register a Message Exchange
(MEX) with OpenBSI is abandoned.
The number of times to retry starting OpenBSI before abandoning OpenBSI start-up.
2.1.11 OpenBSI Configuration File Path
The absolute pathname for the OpenBSI configuration file to start.
Remote Automation Solutions
Website: www.EmersonProcess.com/Remote
Reference Guide
D5092
11-Dec-2007 - Page 8
NW3000 Advanced Configuration
2.1.12 Maximum Allowable Number of Connection Fails
The number of consecutive device communication failures before the device is marked as dead. The default value is 3.
2.1.13 Toggle RBE Processing
Check to enable Report by Exception (RBE) processing by the NW3000 Driver. Uncheck to disable
RBE processing.
Check to enable remote alarm processing in the NW3000 RDI. Uncheck to disable remote alarm processing.
2.1.15 Toggle Template Filtering
Check to enable template data filtering. Uncheck to disable template data filtering.
When filtering of template signal data is enabled, the NW3000 Driver ignores template signal data that is unchanged (i.e. does not report it to the database). The following signal properties are collected by templates:-
• Signal value
• Alarm Inhibit value
• Control Inhibit value
• Manual Inhibit value
• Questionable value
Enables the user to specifiy the amount of template collection statistics that the NW3000 Driver will update within the database.
• Partial Statistics - The default behaviour, which records the schedule id, enabled status, timestamp, unique request id and request status for each template. These values are overwritten with each new template request.
• Full Statistics - Includes all of the above, plus pollsdone and pollsfailed (since the last reset of template statistics).
• Full Statistics with History - Includes all of the above plus the PollsDeltaSuccess statistic, which gives a rolling percentage success rate for template data collection within the last hour.
• Exception only - Reports full statistics, but only when the collection status changes.
• None
Remote Automation Solutions
Website: www.EmersonProcess.com/Remote
Reference Guide
D5092
11-Dec-2007 - Page 9
NW3000 Advanced Configuration
2.1.17 Maximum total number of pending requests
The default value is zero (0), in which case NW3000 Driver will accept the pending message request buffers settings configured within OpenBSI. It should not be set to more than that set by OpenBSI.
If the default value is not chosen, the selected maximum number of pending requests should be less than the total number available within OpenBSI. The value chosen should not be so high that it could adversely affect other OpenBSI clients or cause excessive network loading.
2.1.18 Maximum number of pending requests per device
Specifies the maximum number of pending requests that a device can have at any one time. The default value is 5. When changing the value the following points should be taken into account:-
1. The value should be significantly less than the number of message buffers allocated within the device.
2. The nature of the network communications between the Server and the connected devices. A single serial link would, for instance, indicate a lower buffer value than a 10BaseT IP network link.
3. The number of devices and network levels used. More devices and network levels would indicate a lower pending request buffer number per device.
Rolling Scan data collection is an alternative method of collecting data normally collected by scheduled templates. Scheduled template collection is governed by a Timeclass, which can be assigned to an RTU, or specific signals in an RTU. The Timeclass specifies a maximum number of seconds between successive polls.
Rolling Scan uses templates, but instead of polling at a predefined interval, polls a device enabled for
Rolling Scan on a continuous basis. Successive scans are initiated only when all templates for the device have been collected, and a predefined 'sleep' period has expired (which must be at least 1 second).
2.1.19.1.1 Group Rolling Scan Collection
Rolling Scan can be enabled for a single NW3000 RTUs or can be applied to groups of RTUs. A group Rolling Scan works on all devices within the group such that all templates are collected for each
RTU in turn before the Rolling Scan cycle begins again with the first RTU in the group.
2.1.20 Rolling Scan Type
Controls what templates are collected each rolling scan. A value of Normal will result in all non-254 templates being collected. A value of All will result in all templates being collected. The default value will be Normal.
2.1.21 Rolling Scan Max Devices
The maximum number of devices allowed to have rolling scan enabled at any given time. Set to –1 to allow an unlimited number of rolling scan devices. A value of zero will effectively disable rolling scan.
Defaults to all devices (-1).
Remote Automation Solutions
Website: www.EmersonProcess.com/Remote
Reference Guide
D5092
11-Dec-2007 - Page 10
NW3000 Advanced Configuration
2.1.22 Rolling Scan Max Duration
Specifies the maximum number of seconds that rolling scan should be enabled for all devices. When the time period expires, rolling scan for the appropriate device will be automatically cancelled. A value of -1 indicates that Rolling Scan operation, once initiated, will continue until it is manually stopped. No default value.
2.1.23 Rolling Scan Sleep
The number of seconds to sleep following the successful receipt of all templates. This value cannot be less than 1 second.
2.1.24 Rolling Scan Dead Sleep
The maximum number of seconds to wait for all rolling scan template requests to complete before the current scan is cancelled. This timer prevents devices from hanging rolling scan collection due to template responses not being received. Under normal circumstances, responses will be received for all requests, including communication errors and time-outs. Therefore, this value should be set to a relatively large value. Defaults to 300 (5 minutes).
2.1.25 Rolling Scan Start Up Sleep
The number of seconds to delay rolling scan collection (for all devices) at rdi3000 start-up. This prevents initial template collection from occurring at rdi3000 start-up when RBE and alarms will be collected. Defaults to 15 seconds.
Remote Automation Solutions
Website: www.EmersonProcess.com/Remote
Reference Guide
D5092
11-Dec-2007 - Page 11
3 Network Tab
NW3000 Advanced Configuration
The Network Tab displays a list of the NW3000 Networks available. The [Properties] button becomes available when a NW3000 Network is selected. Selecting this button opens the NW3000 Network
Property page dialog.
This dialog enables administrative configuration of the NW3000 Network.
If checked, the network and all associated devices are disabled. If unchecked, the network and all its associated devices are enabled.
Remote Automation Solutions
Website: www.EmersonProcess.com/Remote
Reference Guide
D5092
11-Dec-2007 - Page 12
NW3000 Advanced Configuration
3.1.2 Device Statistics Update Period
The time value entered here specifies the frequency at which NW3000 Device statistics are updated by the NW3000 Driver. A value of zero indicates that statistics are never to be updated. The controls provided may be used to alter the values, or new values may be typed directly in.
Note: The statistics fields include the writesdone, pollsfailed and writesfailed device attributes.
Remote Automation Solutions
Website: www.EmersonProcess.com/Remote
Reference Guide
D5092
11-Dec-2007 - Page 13
4 Device Tab
NW3000 Advanced Configuration
The Device Tab displays a list of the NW3000 Devices that have been configured. The [Properties] and [Delete] buttons become available when a NW3000 Device is selected.
4.1 Device Property Dialog
The Device dialog enables the user to make changes to any NW3000 Device configuration.
Remote Automation Solutions
Website: www.EmersonProcess.com/Remote
Reference Guide
D5092
11-Dec-2007 - Page 14
NW3000 Advanced Configuration
Check to disable this device and all associated signals. Uncheck to enable the device and all associated signals.
4.1.2 Device Connectivity Check Period
This signifies the time period after which the Server database will request a device sanity check if the device has not been heard from.
Check to disable sanity checking for the selected device. Uncheck to enable sanity checking for the device.
This field displays the associated Plant Area for the selected device. A new Plant Area for the device may be selected from the drop-down list
4.1.5 Disable Alarm Summary Purge
If this control is checked it disables the automatic purge of the Alarm Summary table when a change in version number of the device application-load is detected. If it is unchecked it enables a purge of the Alarm Summary table when a load version change is detected. The Alarm Summary table is purged of all alarms that differ from the current device load version.
Remote Automation Solutions
Website: www.EmersonProcess.com/Remote
Reference Guide
D5092
11-Dec-2007 - Page 15
NW3000 Advanced Configuration
This is the priority associated with the device's optional failure alarm.
The default schedule associated with this device. By default all global application load signals that are neither Report By Exception (RBE), or remote alarms will be collected by templates at the collection intervals specified by this schedule id.
4.1.8 New Schedule Button
Selecting this button will open the Add Schedule dialog, which enables the user to add a new schedule for the selected device.
Note: When opened from here, the Add Schedule dialog's 'Add Consecutive Range' check box will be disabled, since only one schedule can be applied to a single device.
4.1.9 Scanrate
The scan rate is the minimum delay between successive starts of the RBE scans. The value is in tenths of a second and may range from 1 (0.1) seconds to 65535 (6553.5) seconds.
4.1.10 Scanslice
This value is used to divide the work done during a single RBE scan into an equal number of blocks known as slices so that the lower priority tasks are able to gain some processing time between each slice. It can range from 1 to the value of the 'Scanrate' field. If this value is set to 1 or 0, then slicing is inactive. It is normally set to 1 unless RBE is causing performance related problems.
4.1.11 Timeout
The timeout period, in tenths of seconds, between the device informing the Server that an RBE initialise is required or the RBE Task is going active. Specified as a count of 0.1 seconds. The valid range for this field is any integer between 300 (30.0 seconds) and 65535 (6553.5 seconds).
4.1.12 StopXmit
This parameter is used by the RBE task within the device as a limit to temporarily stop sending
Exception Report Messages (ERM's). It refers to the difference between the current Report Sequence
Number (RSN) and the RSN in the last Report Acknowledged (REPORT_ACK) message from the
RBE Manager. When this difference exceeds the 'StopXmit' value, the RBE task suspends the scan process and waits for a valid REPORT_ACK where the RSN difference drops lower than the value specified in this field. The valid range for this field is an integer between 0 (no suspension of ERM's), and 127.
4.1.13 Rolling Scan Enable
When checked, all templates belonging to the device will be collected by rolling scan.
4.1.14 Rolling Scan Group
The optional group number for the device. Set to zero for no group. Group numbers should be greater than zero. Defaults to zero, no group.
Remote Automation Solutions
Website: www.EmersonProcess.com/Remote
Reference Guide
D5092
11-Dec-2007 - Page 16
NW3000 Advanced Configuration
4.1.15 Rolling Scan Sleep Device Override
The number of seconds to sleep following the successful receipt of all templates for the device. This value cannot be less than 1 second. This value overrides the Rolling Scan Sleep value specified on the Driver Property Dialog.
4.1.16 Rolling Scan Max Duration Device Override
Specifies the maximum number of seconds that rolling scan should be enabled for the selected device. When the time period expires, rolling scan for the selected device will be automatically cancelled. No default value. This value overrides the global Rolling Scan Max Duration value specified on the Driver Property dialog.
4.2 Delete Device Button
Selecting this button will delete the currently selected NW3000 Device from the database. There is a confirmation dialog, which presents the user with the opportunity to cancel the deletion by selecting the [No] button. If the [Yes] button is selected the Device will be deleted from the database.
Remote Automation Solutions
Website: www.EmersonProcess.com/Remote
Reference Guide
D5092
11-Dec-2007 - Page 17
5 Schedules Tab
NW3000 Advanced Configuration
The Schedule Tab displays a list of the NW3000 Schedules that have been configured. The
[Properties], and [Delete] buttons become available when a NW3000 Schedule is selected. The
[Add] button is available at all times.
5.1 Schedule Properties Dialog
This dialog enables the user to configure the settings for the selected Schedule. The dialog below shows only one selected Schedule. If more than one Schedule is selected for editing, some of the check boxes of the Schedule Properties dialog may be greyed out. See the Multiple Schedule
Selection topic for more information.
Remote Automation Solutions
Website: www.EmersonProcess.com/Remote
Reference Guide
D5092
11-Dec-2007 - Page 18
NW3000 Advanced Configuration
When checked, the timeclass and all associated templates are disabled. If unchecked, the timeclass is enabled. The dialog is presented differently, depending on whether one or more Schedules have been selected or more than one Schedule is selected with different settings. Click the links below for extra information on this.
5.1.2 Multiple Schedule Selection
A number of schedules may be selected for editing by using the [Shift] and [Control] keyboard keys in conjunction with the mouse to make changes to a block of schedules. The dialog below shows how the selected schedules are displayed on the title bar of the Schedule Properties dialog when more than one object has been selected and their 'Disable' setting is different.
Multiple Schedules Selected
The dialog displays detailed information relating to the first selected schedule. The check boxes on the dialog have three states - unchecked, checked and greyed state. The greyed state means that the
Schedules selected have different values. When the 'One Shot Schedule' box is greyed, the period and offset controls will also be greyed and disabled.
To change the state of the 'Disable' or 'One Shot Schedule' boxes, they must be selected with the left mouse button. This will toggle the boxes through the three states. If one of the boxes that was previously greyed out becomes either checked or unchecked this will change the state of all the selected Schedules.
For example, it would be possible to change all the above selected Schedules to be disabled and one shot by checking the correct check boxes, as shown below.
Changing the Checkboxes for all Selected Schedules
Remote Automation Solutions
Website: www.EmersonProcess.com/Remote
Reference Guide
D5092
11-Dec-2007 - Page 19
NW3000 Advanced Configuration
Changing the selected objects and selecting the [OK] button on the dialog above will update the
Schedules list on the Schedules Tab. Note that the changes will not be committed to the OE Server database until the [OK] or [Apply] buttons have been selected from the bottom of the main
Schedules Tab.
5.1.3 One Shot Schedule
If checked, the templates associated with this schedule will only be collected at system start-up, when a previously offline device comes online, or when the 'collecttemplates' attribute of the device which owns this Schedule is set to TRUE.
5.1.4 Collection Period (Interval)
This value refers to the collection period. A value of 0 indicates a one shot schedule. Any other value will force a poll at that given interval.
5.1.5 Offset
This attribute is used to offset one-shot template collection by the specified offset seconds. This is used to prevent low bandwidth networks being saturated with template requests and hence causing time-outs to occur. The offset can also be applied to one-shot schedules. Once the initial one-shot template collection has completed, the offset value will have no effect.
5.2 Add Schedule Dialog
The 'Add Schedule' dialog can be used to add a new schedule or a range of new schedules.
Remote Automation Solutions
Website: www.EmersonProcess.com/Remote
Reference Guide
D5092
11-Dec-2007 - Page 20
NW3000 Advanced Configuration
5.2.1 New Schedule Id
This is the unique Id number of the Schedule that is being added to the database. If the number is not unique and the [OK] button is selected, a message box will inform the user that this is so. The user will then be returned to the dialog on selecting the [OK] button on the message box.
5.2.2 Add Consecutive Range
If this box is checked, then it will indicate that the user wishes to add a range of Schedules which begin with the Id number in the 'Schedule Id' field and end with the Id number in the 'Last id' field.
This will be the last Schedule number if a range of Schedules is being added.
5.2.4 One Shot Schedule Check Box
If checked, the templates associated with this schedule will only be collected at system start-up, when a previously offline device comes online, or when the 'collecttemplates' attribute of the device which owns this Schedule is set to TRUE.
5.2.5 Disable Schedule Check Box
When checked, the timeclass and all associated templates are disabled. If unchecked, the timeclass is enabled.
5.2.6 New Schedule Collection Period (Interval)
This value refers to the collection period. A value of 0 indicates a one shot schedule. Any other value will force a poll at that given interval.
Remote Automation Solutions
Website: www.EmersonProcess.com/Remote
Reference Guide
D5092
11-Dec-2007 - Page 21
NW3000 Advanced Configuration
This field specifies an offset time to be applied when a range of Schedules is due to be added. If the
'Add Consecutive Range' option is enabled, then the 'Increment' time fields will become available. The user may enter a value by which each successive Schedule in the new range will be offset from the one before it. This is used to prevent low bandwidth networks from being saturated with template requests and hence causing time-outs to occur.
Selecting this button will delete the currently selected NW3000 Schedule from the database. There is a confirmation dialog, which presents the user with the opportunity to cancel the deletion by selecting the [No] button. If the [Yes] button is selected the Schedule will be deleted from the database.
Remote Automation Solutions
Website: www.EmersonProcess.com/Remote
Reference Guide
D5092
11-Dec-2007 - Page 22
6 Index
NW3000 Advanced Configuration
A
Add Consecutive Range ........................... 20
Add Schedule Dialog................................. 20
Address ....................................................... 4
Auto Start OpenBSI..................................... 5
Auto Stop OpenBSI..................................... 6
C
Check .......................................................... 5
Collection Period ....................................... 19
Connection Fails ......................................... 6
D
Database ..................................................... 5
Delete Device Button ................................ 16
Delete Schedule Button ............................ 21
Device Check Period................................... 5
Device Connectivity Check Period............ 14
Device Disable .......................................... 14
Device Plant Area ..................................... 14
Device Property Dialog ............................. 13
Device Statistics Update Period................ 12
Device Tab ................................................ 13
Devices........................................................ 5
Disable Alarm Summary Purge................. 14
Disable Network ........................................ 12
Disable NW3000 RDI .................................. 4
Disable Sanity Check ................................ 14
Disable Schedule ...................................... 18
Disable Schedule Check Box.................... 21
Driver Property Dialog................................. 3
Driver Tab.................................................... 3
F
Failure Alarm Priority................................. 15
L
Last Id........................................................ 21
M
Maximum Allowable Number ...................... 6
Maximum number ........................................7
Maximum total number ................................7
Multiple Schedule Selection ......................18
N
Network Property Dialog............................11
Network Tab ..............................................11
New Schedule Button ................................15
New Schedule Collection Period ...............21
New Schedule Id........................................20
Number ........................................................5
O
Offset .........................................................20
OpenBSI Configuration File Path ................6
OpenBSI Connectivity Retries .....................6
OpenBSI Connectivity Timeout ...................6
Overview......................................................1
R
Range Increment .......................................21
RDI...............................................................5
RDI Check Period ........................................5
RDI Retry Period..........................................5
Requests......................................................7
Requests per device....................................7
S
Scanrate ....................................................15
Scanslice ...................................................15
Schedule Id................................................15
Schedule Properties Dialog .......................17
Schedules Tab...........................................17
Shot Schedule ...........................................19
Shot Schedule Check Box.........................21
Slice .............................................................5
StopXmit ....................................................15
T
Template Statistics ......................................7
Timeout......................................................15
Toggle Alarms Processing...........................6
Toggle RBE Processing ..............................6
Toggle Template Filtering............................6
Remote Automation Solutions
Website: www.EmersonProcess.com/Remote
Reference Guide
D5092
11-Dec-2007
NW3000 Advanced Configuration
NOTICE
Remote Automation Solutions (“RAS”), division of Emerson Process Management shall not be liable for technical or editorial errors in this manual or omissions from this manual. RAS MAKES NO WARRANTIES, EXPRESSED OR IMPLIED, INCLUDING THE IMPLIED WARRANTIES OF MERCHANTABILITY AND FITNESS FOR A
PARTICULAR PURPOSE WITH RESPECT TO THIS MANUAL AND, IN NO EVENT SHALL RAS BE LIABLE FOR ANY INCIDENTAL, PUNITIVE, SPECIAL OR
CONSEQUENTIAL DAMAGES INCLUDING, BUT NOT LIMITED TO, LOSS OF PRODUCTION, LOSS OF PROFITS, LOSS OF REVENUE OR USE AND COSTS
INCURRED INLCUDING WITHOUT LIMITATION FOR CAPITAL, FUEL AND POWER, AND CLAIMS OF THIRD PARTIES.
Bristol, Inc., Bristol Babcock Ltd, Bristol Canada, BBI SA de CV and the Flow Computer Division are wholly owned subsidiaries of Emerson Electric Co. doing business as
Remote Automation Solutions (“RAS”), a division of Emerson Process Management. ROC, FloBoss, ROCLINK, Bristol, Bristol Babcock, ControlWave, TeleFlow and
Helicoid are trademarks of RAS. AMS, PlantWeb and the PlantWeb logo are marks of Emerson Electric Co. The Emerson logo is a trademark and service mark of the
Emerson Electric Co. All other trademarks are property of their respective owners.
The contents of this publication are presented for informational purposes only. While every effort has been made to ensure informational accuracy, they are not to be construed as warranties or guarantees, express or implied, regarding the products or services described herein or their use or applicability. RAS reserves the right to modify or improve the designs or specifications of such products at any time without notice. All sales are governed by RAS’ terms and conditions which are available upon request.
RAS does not assume responsibility for the selection, use or maintenance of any product. Responsibility for proper selection, use and maintenance of any RAS product remains solely with the purchaser and end-user.
Engineered and supported by:
Remote Automation Solutions,
Bristol Babcock Ltd. Blackpole Road, Worcester, WR3 8YB, UK
Reg office: 2nd Floor, Accurist House, 44 Baker Street, London, W1U 7AL
Registered in England and Wales, Reg No. 2580226
VAT Reg No. GB 880 9839 67
Emerson Process Management
Remote Automation Solutions
1100 Buckingham St
Watertown, CT 06795
T 1 (860) 945 2200
F 1 (860) 945 2278 www.EmersonProcess.com/Remote [email protected]
Emerson Process Management
Remote Automation Solutions
Blackpole Road
Worcester, WR3 8YB
T 44 (0) 1905 856848
F 44 (0) 1905 856930 www.EmersonProcess.com/Remote [email protected]
© 2007 Remote Automation Solutions, division of Emerson Process Management. All rights reserved.
advertisement
Related manuals
advertisement
Table of contents
- 5 NW3000 Driver Property Dialog
- 6 Address
- 6 Disable NW3000 Driver
- 6 database to NW3000 Driver Retry Period
- 7 Check Period
- 7 NW3000 Driver to Device Check Period
- 7 Slice - (Number of Devices to Check)
- 7 Auto Start OpenBSI
- 7 Auto Stop OpenBSI
- 7 OpenBSI Connectivity Timeout
- 7 OpenBSI Connectivity Retries
- 7 OpenBSI Configuration File Path
- 8 Maximum Allowable Number of Connection Fails
- 8 Toggle RBE Processing
- 8 Toggle Alarms Processing
- 8 Toggle Template Filtering
- 8 Template Statistics
- 9 Maximum total number of pending requests
- 9 Maximum number of pending requests per device
- 9 Rolling Scan