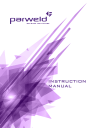
advertisement
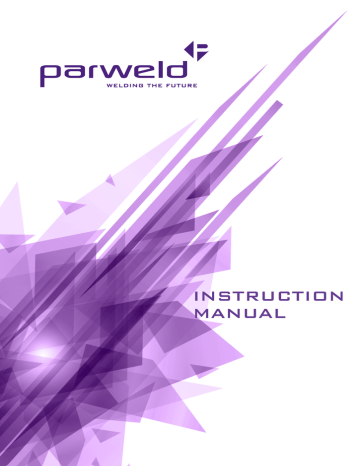
INSTRUCTION
MANUAL
XTI-202P AC/DC
OperatOr Manual
ISSue 3
Welcome
Thank you and congratulations on choosing Parweld. This Owner’s Manual is designed to help you get the most out of your Parweld products. Please take time to read the Safety precautions. They will help you protect yourself against potential hazards in the workplace. With proper maintenance this equipment should provide years of reliable service. All our systems conform to ISO9001: 2000 and are independently audited by NQA.
The entire product range carries the CE mark, and is constructed in accordance with European directives and the product specific standards where they apply.
Further Information
Parweld is the UK’s leading manufacturer of MIG, TIG and Plasma torches and consumables.
For more information about Parweld’s complete range visit: www.parweld.com
Contents
Page
5.3 Input and grounding connection 8
5.4 Output Polarity Connections 8
5.6 Work return lead connection
6.3 Machine setup for TIG welding 10
6.3.1 DC TIG Welding (no Pulse)
6.3.2 AC TIG Welding (no Pulse)
6.3.3 Pulse TIG welding
6.4 MMA welding setup
9.0 Statement of warranty
12
12
11
11
17
1.0 Safety Precautions
ELECTRIC SHOCK can kill.
Touching live electrical parts can cause fatal shocks or severe burns. The electrode and work circuit is electrically live whenever the output is on. The input power circuit and machine internal circuits are also live when power is on.
Do not touch live electrical parts.
Wear dry, sound insulating gloves and body protection.
Insulate yourself from work and ground using dry insulating mats or covers big enough to prevent any physical contact with the work ground.
Wear a safety harness if working above floor level.
Keep all panels and covers securely in place.
Clamp work cable with good metal-to-metal contact to work piece or worktable as near the weld as practical.
Insulate work clamp when not connected to work piece to prevent contact with any metal object.
Welding produces fumes and gases. Breathing these fumes and gases can be hazardous to your health.
Additional safety precautions are required when any of the following electrically hazardous conditions are present: in damp locations or while wearing wet clothing; on metal structures such as floors, gratings, or scaffolds; when in cramped positions such as sitting, kneeling, or lying; or when there is a high risk of unavoidable or accidental contact with the work piece or ground.
Disconnect input power before installing or servicing this equipment. Lockout/tagout input power according to Safety Standards.
Properly install and ground this equipment according to national and local standards.
Always verify the supply ground - check and ensure that input power cable ground wire is properly connected to ground terminal in the receptacle outlet.
When making input connections, attach proper grounding conductor first - double-check connections.
Frequently inspect input power cable for damage or bare wiring - replace cable immediately if damaged - bare wiring can kill.
Turn off all equipment when not in use.
Do not use worn, damaged, under sized, or poorly spliced cables.
Do not drape cables over your body.
If earth grounding of the work piece is required, ground it directly with a separate cable.
Do not touch electrode if you are in contact with the work, ground, or another electrode from a different machine.
Use only well-maintained equipment. Repair or replace damaged parts at once. Maintain unit according to manual.
FUMES AND GASES can be hazardous.
Keep your head out of the fumes. Do not breathe the fumes.
If inside, ventilate the area and/or use local forced ventilation at the arc to remove welding fumes and gases.
If ventilation is poor, wear an approved respirator.
Read and understand the Material Safety Data Sheets
(MSDS’s) and the manufacturer’s instructions for metals, consumable, coatings, cleaners, and degreasers.
Work in a confined space only if it is well ventilated, or while wearing an air-supplied respirator. Always have a trained watch person nearby. Welding fumes and gases can displace air and lower the oxygen level causing injury or death. Be sure the breathing air is safe.
Do not weld in locations near de-greasing, cleaning, or spraying operations. The heat and rays of the arc can react with vapours to form highly toxic and irritating gases.
Do not weld on coated metals, such as galvanized, lead, or cadmium plated steel, unless the coating is removed from the weld area, the area is well ventilated, and while wearing an air-supplied respirator. The coatings and any metals containing these elements can give off toxic fumes if welded.
ARC RAYS can burn eyes and skin.
Arc rays from the welding process produce intense, visible and invisible (ultraviolet and infrared) rays that can burn eyes and skin. Sparks fly off from the weld.
Wear an approved welding helmet fitted with a proper shade of filter lense to protect your face and eyes when welding or watching
Wear approved safety glasses with side shields under your helmet.
Use protective screens or barriers to protect others from flash, glare and sparks; warn others not to watch the arc.
Wear protective clothing made from durable, flame
4 www.parweld.com
www.parweld.com
resistant material (leather, heavy cotton, or wool) and foot protection. Welding on closed containers, such as tanks, drums, or pipes, can cause them to blow up. Sparks can fly off from the welding arc. The flying sparks, hot work piece, and hot equipment can cause fires and burns. Accidental contact of electrode to metal objects can cause sparks, explosion, overheating, or fire. Check and be sure the area is safe before doing any welding.
MAGNETIC FIELDS can affect pacemakers.
Pacemaker wearers keep away.
Wearers should consult their doctor before going near arc welding, gouging, or spot welding operations.
WELDING can cause fire or explosion.
Remove all flammables within 10m of the welding arc. If this is not possible, tightly cover them with approved covers.
Do not weld where flying sparks can strike flammable material.
Protect yourself and others from flying sparks and hot metal.
Be alert that welding sparks and hot materials from welding can easily go through small cracks and openings to adjacent areas.
Watch for fire, and keep a fire extinguisher nearby. Be aware that welding on a ceiling, floor, bulkhead, or partition can cause fire on the hidden side.
Do not weld on closed containers such as tanks, drums, or pipes, unless they are properly prepared according to local regulations
Connect work cable to the work as close to the welding area as practical to prevent welding current from travelling along, possibly unknown paths and causing electric shock, sparks, and fire hazards.
Wear oil-free protective garments such as leather gloves, heavy shirt, cuffless trousers, high shoes, and a cap. Remove any combustibles, such as a butane lighter or matches, from your person before doing any welding.
NOISE can damage hearing.
Noise from some processes or equipment can damage hearing.
Wear approved ear protection if noise level is high.
Shielding gas cylinders contain gas under high pressure.
CYLINDERS can explode if damaged.
Protect compressed gas cylinders from excessive heat, mechanical shocks, physical damage, slag, open flames, sparks, and arcs. Install cylinders in an upright position by securing to a stationary support or cylinder rack to prevent falling or tipping. Keep cylinders away from any welding or other electrical circuits. Never drape a welding torch over a gas cylinder. Never allow a welding electrode to touch any cylinder. Never weld on a pressurized cylinder - explosion will result. Use only correct shielding gas cylinders, regulators, hoses, and fittings designed for the specific application; maintain them and associated parts in good condition.
Turn face away from valve outlet when opening cylinder valve.
Use the right equipment, correct procedures, and sufficient number of persons to lift and move cylinders.
Read and follow instructions on compressed gas cylinders, associated equipment, and Compressed Gas
Association (CGA) recommendations.
FLYING METAL can injure eyes.
Welding, chipping, wire brushing, and grinding cause sparks and flying metal. As welds cool they can throw off slag. Wear approved safety glasses with side shields even under your welding helmet.
BUILDUP OF GAS can injure or kill.
Shut off shielding gas supply when not in use. Always ventilate confined spaces or use approved air-supplied respirator.
HOT PARTS can cause severe burns.
Do not touch hot parts with bare hands.
Allow cooling period before working on gun or torch.
To handle hot parts, use proper tools and/or wear heavy, insulated welding gloves and clothing to prevent burns.
Foot Control
3 Button Trigger Control
www.parweld.com
5
8
9
1
2
3
4
5
6
7
15
10
11
12
13
14
19 18 19
3.0 Technical Specifications
17
Press
Pre Gas
Release
Post Gas
Press Release
2.0 Product Description
This welding machine is manufactured using advanced inverter technology. The input voltage is rectified to DC and then inverted to high frequency AC voltage. before being converted back to DC for the output .This allows the use of a much smaller transformer and so allowing weight saving and improved power efficiency.
Pre Gas
Initial
Current
Current Adjustment Press Release
Final
Current
Post Gas
6 www.parweld.com
www.parweld.com
Input voltage
Frequency
Input current
Fuse rating
Output OCV
Output load voltage
Output Current
XTI-202 AC/DC
230V +/- 10%
50/60Hz
35.4A max
17.7 eff
16A
70
10.2-18V
5-200A DC 10-
200A AC
Control Plug wiring
Wiring should be completed in accordance with the diagrams below wire colours refer to Parweld ERGO/
Pro TIG torches
4.0 Description of Controls
1) ON OFF Switch for switching on or off the mains supply to the machine. Note the output of the machine is permanently on in MMA mode unless the on/off switch is in the off position.
2) Mains input Cable
3) Shielding Gas input connection
4) Power light This indicates mains power is applied to the machine and that the machine is currently switched on when the light is illuminated
5) Fault light This indicates a fault or over temperature condition with the machine refer to the fault finding section for further information
6) Gas Output connection
This is a 3/8 BSP connection for the gas output connection to the welding torch (TIG welding)
7) Negative connection This is used to connect the electrode holder in MMA or the earth lead in TIG welding.
8) Positive connection This is used to connect the electrode holder in MMA or the earth lead in TIG welding.
9) control socket This is used to control the machine remotely using a trigger or amperage control
10) Output power button. This button has 2 positions the top position selects AC output in TIG or MMA mode and the bottom position selects DC output in
TIG or MMA mode as indicated by the illuminated LED.
Pressing the button toggles between the 2 positions.
11) Switch mode (TIG), this toggles between 2 step and 4 step operation of the torch trigger. In 2 step mode the trigger should be pressed and held down until the end of the weld. In 4 step mode (lower led) the trigger is pressed and released to start and pressed and released to finish the weld. In order to
TIG weld one of these functions must be illuminated.
Not all functions are available in 2T mode.
2T mode
4T mode
12) Gas test (TIG), Pressing this button switches on the shielding gas for 15s to allow purging of the torch and checking of the gas flow. Pressing the button before 15s has expired will stop the gas flow.
13) HF ignition. When illuminated the TIG torch will start with High frequency ignition not requiring contact of the Tungsten electrode with the work (TIG
Mode).
14) Power Pulsing. When illuminated the output power will be pulsed in accordance with the variables selected on the main control
15) Amperage Display. Displays the preselected or actual welding amperage.
16) Multifunction Display. Displays other parameter as as indicated by the illuminated LED at the side of the display V=Voltage, S= Seconds, Hz= Hertz
(frequency), %=Percentage value.
17) MMA selector. This button selects MMA welding and will latch on the power output when the LED is illuminated.
18) Parameter adjustment Dial. This knob is used to adjust multiple parameters dependant upon the parameter selected on the pictogram above the knob.
18) Parameter toggle buttons. These buttons toggle the selected parameter and can be used to select the require parameter as indicated by the LED on the
Pictogram.
5.0 Installation
Read entire installation section before starting installation.
SAFETY PRECAUTIONS
• ELECTRIC SHOCK can kill.
• Only qualified personnel should perform this installation.
• Only personnel that have read and understood the
Operating Manual should install and operate this equipment.
• Machine must be grounded per any national, local or other applicable electrical regulations.
• The power switch is to be in the OFF position when installing work cable and electrode cable and when connecting other equipment.
5.1 Unpacking the Machine
Carefully remove the machine from the packaging, we recommend you retain the packaging until the
8 www.parweld.com
machine has been fully installed and tested incase it has been damaged in transit and has to be returned to the re-seller.
be used. The green/yellow wire in the input cable connects to the frame of the machine. This ensures proper grounding of the machine when the machine plug is inserted into the receptacle.
5.2 Location
Be sure to locate the welder according to the following guidelines:
In areas, free from moisture and dust.
Ambient temperature between 0-40
0
C.
In areas, free from oil, steam and corrosive gases.
In areas, not subjected to abnormal vibration or shock.
In areas not exposed to direct sunlight or rain.
Place at a distance of 12” (300 mm) or more from walls or similar that could restrict natural airflow for cooling.
5.4 Output Polarity Connections
Electrode polarity
MMA electrodes are generally connected to the ‘+’ terminal and the work lead to the ‘-‘terminal
But if in doubt consult the electrode manufacturer’s literature.
IF TIG welding the torch should always be connected to the ‘-’ terminal.
5.5 Torch installation
MMA cable connections
Connect electrode lead to positive terminal
TIG welding cable connection
Connect the TIG torch to the - terminal
5.3 Input and grounding connection
WARNING
Before starting the installation, check that your power supply is adequate for the voltage, amperage, phase, and frequency specified on the Machine nameplate.
Operate the welding power source from a singlephase 50/60 Hz, AC power supply. The input voltage must match one of the electrical input voltages shown on the input data label on the unit nameplate. The
XTI-202P ACDC machine should only be used on 230V supply. Refer to the specifications table for voltage tolerances.
Have a qualified electrician connect the input plug.
For long runs over 30m , larger copper wires should
5.6 Work return lead connection
MMA cable connections
Connect work lead to negative terminal
TIG welding
Connect the work return lead to the + terminal
6.0 Operation
WARNING
When using an open arc process, it is necessary to use correct eye, head, and body protection.
6.1 MMA Welding Guide
E ffects of MMA welding various materials
High tensile and alloy steels
The two most prominent effects of welding these steels are the formation of a hardened zone in the weld area, and, if suitable precautions are not taken, the occurrence in this zone of under-bead cracks.
Hardened zone and under-bead cracks in the weld area may be reduced by using the correct electrodes, preheating, using higher current settings, using larger electrodes sizes, short runs for larger electrode deposits or tempering in a furnace.
9 www.parweld.com
www.parweld.com
Manganese steels
The effect on manganese steel of slow cooling from high temperatures is enbrittlement. For this reason it is absolutely essential to keep manganese steel cool during welding by quenching after each weld or skip welding to distribute the heat.
6013 ideal electrodes for all general purpose work.
Features include outstanding operator appeal, easy arc starting and low spatter.
Cast iron
Most types of cast iron, except white iron, are weldable. White iron, because of its extreme brittleness, generally cracks when attempts are made to weld it. Trouble may also be experienced when welding white-heart malleable, due to the porosity caused by gas held in this type of iron.
Copper and alloys
The most important factor is the high rate of heat conductivity of copper, making preheating of heavy sections necessary to give proper fusion of weld and base metal.
Types of electrodes
Arc welding electrodes are classified into a number of groups depending on their applications. There are a great number of electrodes used for specialized industrial purposes which are not of particular interest for everyday general work. These include some low
Mild steel
7014 all positional electrode for use on mild and galvanized steel furniture, plates, fences, gates, pipes and tanks etc. Especially suitable for vertical down welding.
Cast iron
99% nickel suitable for joining all cast irons except white cast iron
Stainless steel
318l-16 high corrosion resistance. Ideal for dairy work, etc. On stainless steels.
6.2 Basic TIG Welding guide
Tig welding cable connection
Connect the TIG torch to the - terminal and the work lead to the + terminal for direct current straight polarity. Direct current straight polarity is the most widely used polarity for DC TIG welding. It allows limited wear of the electrode since 70% of the heat is concentrated at the work piece. Connect the gas hose on the TIG torch to the gas outlet on the gas regulator.
Move the selector switch on the front panel of the machine to the LIFT-TIG position.
B
A
E
O
H
I
J
C
D
F
G
K
L
D
M hydrogen types for high tensile steel, cellulose types for welding large diameter pipes, etc. The range of electrodes dealt with in this publication will cover the vast majority of applications likely to be encountered; are all easy to use and all will work on even the most basic of welding machines.
Metals being joined & electrode comments
Mild steel
Torch starting in Lift TIG mode
Ensure the gas supply is switched on to the machine.
Briefly contact the tip of the tungsten electrode down onto the work piece with the torch at around 70
0
from vertical. Depress the trigger to start the gas flow and switch on the power, lift the torch up from the work piece to draw out an arc. To prevent melting of the end of the tungsten the machine will increase the output current when it detects the rise in arc voltage as the tungsten is lifted from the work piece. At the end of the weld release the torch trigger and the power will slope down and switch off.
Torch starting in HF mode
Ensure the gas supply is switched on to the machine.
Hold the torch with the tip of the tungsten approx 2-3 mm from the job. Depress the trigger to start the gas flow and switch on the power. At the end of the weld release the torch trigger and the power will slope down and switch off.
10 www.parweld.com
B
A
E
O
H
I
J
P
C
D
F
G
Q
K
L
M
D
TIG welding guide ranges
Electrode diameter AC current
(amps)
0.040” (1.0mm)
1/16” (1.6mm)
15-30
60-120
3/32” (2.4mm) 100-180
Tungsten electrode types
DC current
(amps)
20-60
75-150
150-250
Type
Thoriated 2%
Ceriated 2%
Zirconiated
Application
DC welding of mild steel,
Stainless steel and Copper
DC welding of mild steel,
Stainless steel,
Copper
AC welding of aluminium, magnesium and their alloys
AC welding of aluminium, magnesium and their alloys
Colour
Red
Grey
White
Guide for selecting filler wire diameter
Filler wire diameter
1/16” (1.6 mm)
3/32” (2.4 mm)
Current range
20 - 90
65 - 115
1/8” (3.2 mm)
3/16” (4.8 mm)
100 - 165
200-350
The filler wire diameter specified is a guide only, other diameter wires may be used according to the welding application.
Shielding gas selection
Alloy
Aluminium & alloys
Carbon steel
Stainless steel
Nickel alloy
Copper
Titanium
Shielding gas
Pure Argon
Pure Argon
Pure Argon
Pure Argon
Pure Argon
Pure Argon
6.3 Machine setup for TIG welding
6.3.1 DC TIG welding (No Pulse)
Note:- shorting or dipping the electrode into the weld pool for more than 1 second will cause the machine to reduce the welding power to zero in order to protect the tungsten and minimise contamination
1)Connect the torch to the - connection and the gas hose to the gas outlet.
2) Connect the trigger control plug on the torch to the trigger socket.
3) Connect the Earth lead to the + connection.
4) Set the process mode to 2T or 4T if you prefer a latching trigger action. (Note in 4T position you must press and release to start the process and press and release again to stop the process) (A)
5) Select DC output (B)
6) Select HF start (C)
7) Using the toggle buttons (D)move the illuminated
LED to the gas pre-flow position (E)
10 www.parweld.com
www.parweld.com
O
G
B
C
E
H
B
O G
D
F
D
A
8) Adjust the parameter value by rotating the knob
(F) This can be adjusted from 0.1 to 0.3 seconds. The value is displayed on the Multifunction display (G)
9) Press the toggle button (D) to move the LED to the initial current (H) This can be adjusted from 5 to 100% of the main welding current. The value is displayed on the Multifunction display (G). 50% is a good initial setting. Note this function only operates in 4T switch
mode
10) Press the toggle button (D) to move the LED to the slope up time (I) This can be adjusted from 0 to 10s.
The value is displayed on the Multifunction display
(G). 2s is a good initial setting.
11) Press the toggle button (D) to move the LED to the main welding current (J) This can be adjusted from
5 to 200A. The value is displayed on the amperage display (O). Refer to the TIG welding guide for a recommended welding current.
12) Press the toggle button (D) to move the LED to the slope down time (K) This can be adjusted from 0 to 10s. The value is displayed on the Multifunction display (G). 2s is a good initial setting.
13) Press the toggle button (D) to move the LED to the final current (L) This can be adjusted from 5 to 100% of the main welding current. The value is displayed on the Multifunction display (G). 10% is a good initial setting. Note this function only operates in 4T switch
mode
1
4) Press the toggle button (D) to move the LED to the Post Gas time (M) This can be adjusted from 0.1 to 10s. The value is displayed on the Multifunction display (G). 3s is a good initial setting.
You are now ready to weld. The above settings are a guide and you should adjust to suit the job you are welding if you are unfamiliar with the machine try to adjust only one parameter at a time so you become familiar with its effect.
J
D
F
D H
C
E
A
6.3.2 AC TIG welding (No Pulse)
1)Connect the torch to the - connection and the gas hose to the gas outlet.
2) Connect the trigger control plug on the torch to the trigger socket.
3) Connect the Earth lead to the + connection.
4) Set the process mode to 2T or 4T if you prefer a latching trigger action. (Note in 4T position you must press and release to start the process and press and release again to stop the process) (A)
5) Select AC output (B)
6) Select HF start (C)
7) Using the toggle buttons (D)move the illuminated
LED to the gas pre-flow position (E)
8) Adjust the parameter value by rotating the knob
(F) This can be adjusted from 0.1 to 0.3 seconds. The value is displayed on the Multifunction display (G)
9) Press the toggle button (D) to move the LED to the initial current (H) This can be adjusted from 5 to 100% of the main welding current. The value is displayed on the Multifunction display (G). 50% is a good initial setting.
10) Press the toggle button (D) to move the LED to the slope up time (I) This can be adjusted from 0 to 10s.
The value is displayed on the Multifunction display
(G). 2s is a good initial setting.
11) Press the toggle button (D) to move the LED to the main welding current (J) This can be adjusted from
5 to 200A. The value is displayed on the amperage display (O). Refer to the TIG welding guide for a recommended welding current.
11 www.parweld.com
12
12) Press the toggle button (D) to move the LED to the slope down time (K) This can be adjusted from 0 to 10s. The value is displayed on the Multifunction display (G). 2s is a good initial setting.
13) Press the toggle button (D) to move the LED to the final current (L) This can be adjusted from 5 to 100% of the main welding current. The value is displayed on the Multifunction display (G). 10% is a good initial setting.
14) Press the toggle button (D) to move the LED to the Post Gas time (M) This can be adjusted from 0.1 to 10s. The value is displayed on the Multifunction display (G). 3s is a good initial setting.
15) Press the toggle button (D) to move the LED to the AC frequency (P) This can be adjusted from 50 to
250Hz dependant on the welding amperage. The value is displayed on the Multifunction display (G). 60hz is a good initial setting. Increaseing the frequency has the effect of stiffening and focussing the arc making it good for welding close to threads or for crater filling
Note the maximum frequency available depends upon the welding amperage selected
<50A 50 to 250Hz
50-100A 50-200Hz
100-150A max 150Hz
150-200A max 100Hz
16) Press the toggle button (D) to move the LED to the AC balance (Q) This can be adjusted from 15 to
50% . The value is displayed on the Multifunction display (G). 15% is a good initial setting. Increasing the percentage has the effect of increasing the time the arc spends in the electrode positive state which gives a greater cleaning effect on the material but will reduce weld speed. For good clean material you should be able to keep the cleaning percentage set at 15 to 20%
You are now ready to weld. The above settings are a guide and you should adjust to suit the job you are welding if you are unfamiliar with the machine try to adjust only one parameter at a time so you become familiar with its effect.
It is possible to use the pulse function with both AC and DC TIG welding Power Pulsing can give significant advantages on thinner material to control heat and penetration.
1) Follow the setup as previously described for AC or
DC TIG welding.
2) Press button A to switch on the pulsing functions
3) Press the toggle button (D) to move the LED to the
Peak current (B) This can be adjusted from 5 to 200A
(10-200A for AC welding)dependant on the welding amperage. The value is displayed on the amperage display (O). Peak current is the maximum amperage that will be output.
4) Press the toggle button (D) to move the LED to the
Peak duration(C) This can be adjusted from 5 to 100%
Peak duration is the percentage of time the peak current is on relative to the background current. 30% is a good starting point.
5) Press the toggle button (D) to move the LED to the
Background current (H) This can be adjusted from 5 to
200A (10-200A for AC welding). The value is displayed on the amperage display (O). Background current is the minimum amperage that will be output. It cannot be higher than the peak current and generally will be set withing 50 to 70%Amps of the peak current.
6) Press the toggle button (D) to move the LED to the
Pulse Frequency (E) This can be adjusted from 0.5 to
200Hz. The value is displayed on the multifunction display (G). Pulse Frequency is the number of pulses per second generally a range of 50 to 150 hz will be used with 100Hz being a goo base setting.
30-40Hz will help agitate the weld puddle and allow you to weld at a lower amperage than without pulse.
50-150Hz really stiffen the arc and let you pinpoint the arc more than without pulse.
0.5-10Hz reduce heat input the most.
The selected amperage and the consistency of travel speed can negate some of the effects of Power pulsing
6.4 MMA welding setup
Note:- shorting or dipping the electrode into the weld pool for more than 2 seconds will cause the machine to reduce the welding power to zero in order to protect the electrode.
1) Press button A to select MMA welding
2) Press button B to select AC or DC output as required.
3) Press the toggle button (D) to move the LED to the
Output current (J) This can be adjusted from 5 to
170A DC (10-170A AC welding) . The value is displayed on the amperage display (O).
www.parweld.com
www.parweld.com
4) Press the toggle button (D) to move the LED to the Arc force (C) This can be adjusted from 0 to 10
Arc force prevents the electrode from sticking during welding. The value is displayed on the multifunction display (G). Arc force is a temporary increase of the output current during welding when the arc is too short. To have a smooth arc with less spatter, set the knob to minimum (Rutile,Basic). For a more crisp arc, with more penetration,set it to maximum.
5) Press the toggle button (D) to move the LED to the Hot start (E) The value is displayed on the multifunction display (G) and can be adjusted from
0 to 10. This is the temporary increase of the output current during the start of a weld, this helps ignite the arc quickly and reliably. Hot Start provides excellent arc ignition without the electrode sticking and avoiding any metallurgical default in the weld.
6) Press the toggle button (D) to move the LED to the Arc Length (H) The value is displayed on the multifunction display (G) and can be adjusted from 0 to 10. This control works to maintain a constant arc length by increasing or decreasing the current as the electrode is moved in and out helping prevent a short circuit during welding.
7.0 Fault Finding
MMA welding problem
Description
Gas pockets or voids in weld metal (porosity)
Possible cause
(a)
Electrodes are damp
(b) Welding current is too high.
(c) Surface impurities such as oil, grease, paint, etc
Remedy
(a) Dry electrodes before use
(b) Reduce welding current
(c) Clean joint before welding
Description
Crack occurring in weld metal soon after solidification.
A gap is left by failure of the weld metal to fill the root of the weld
Portions of the weld run do not fuse to the surface of the metal or edge of the joint.
(a) Small electrodes used on heavy cold plate
(b) Welding current is too low
(c) Wrong electrode angle
(d) Travel speed of electrode is too high
(e) Scale or dirt on joint surface
Possible cause
(a) Rigidity of joint.
(b)
Insufficient throat thickness.
(c) Cooling rate is too high.
(a) Welding current is too low.
(b)
Electrode too large for joint.
(c)
Insufficient gap
(d) Incorrect sequence
Remedy
(a) Redesign to relieve weld joint of severe stresses or use crack resistance electrodes.
(b) Travel slightly slower to allow greater build up in throat.
(c) Preheat plate and cool slowly.
(a) Increase welding current
(b) Use smaller diameter electrode.
(c) Allow wider gap
(d) Use correct build-up sequence
(a) Use larger electrodes and preheat the plate
(b) Increase welding current
(c) Adjust angle so the welding arc is directed more into the base metal
(d) Reduce travel speed of electrode
(e) Clean surface before welding.
www.parweld.com
13
Description
Non-metallic particles are trapped in the weld metal (slag inclusion).
TIG welding problems
Possible cause a) Non-metallic particles may be trapped in undercut from previous run
(b) Joint preparation too restricted
(c) Irregular deposits allow slag to be trapped.
(d) Lack of penetration with slag trapped beneath weld bead.
(e) Rust or mill scale is preventing full fusion.
(f) Wrong electrode for position in which welding is done.
Remedy a) If bad undercut is present, clean slag out and cover with a run from a smaller diameter electrode.
(b) Allow for adequate penetration and room for cleaning out the slag
(c) If very bad, chip or grind out Irregularities
(d) Use smaller electrode with sufficient current to give adequate penetration. adequate penetration. Use suitable tools to remove all slag from corners
(f) Use electrodes designed for position in which welding is done, otherwise proper control of slag is difficult.
Weld quality is dependent on the selection of the correct consumables, maintenance of equipment and proper welding technique.
Description Possible Cause
Excessive bead build up or poor penetration or poor fusion at edges of weld
Weld bead too wide and flat or undercut at edges of weld or excessive burn through
Welding current is too low
Welding current is too high
Remedy
Increase weld current and/ or faulty joint preparation
Decrease weld current
Description Possible Cause
Weld bead too small or insufficient penetration or ripples in bead are widely spaced apart
Travel speed too fast
Weld bead too wide or excessive bead build up or excessive penetration in butt joint
Travel speed too slow
Uneven leg length in fillet joint
Electrode melts when arc is struck
Dirty weld pool
Wrong placement of filler rod
Electrode is connected to the
‘+’ terminal
(a) Electrode contaminated through contact with work piece or filler rod material
(b) Gas contaminated with air
Remedy
Reduce travel speed
Increase travel speed
Re-position filler rod
Connect the electrode to the
‘-‘ terminal
(a) Clean the electrode by grinding off the contaminates
(b) Check gas lines for cuts and loose fitting or change gas cylinder
14
15 www.parweld.com
www.parweld.com
14
15
Description Possible Cause
Electrode melts or oxidizes when an arc is struck
(a) No gas flowing to welding region
(b) Torch is clogged with dust
(c) Gas hose is cut
(d) Gas passage contains impurities
(e) Gas regulator is turned off
(f) Torch valve is turned off
(g) The electrode is too small for the welding current
Poor weld finish
Arc flutters during TIG welding
Inadequate shielding gas
(a) Tungsten electrode is too large for the welding current
(b) Absence of oxides in the Weld pool.
Remedy
(a) Check the gas lines for kinks or breaks and gas cylinder contents
(b) Clean torch
(c) Replace gas hose
(d) Disconnect gas hose from torch then raise gas pressure to blow out impurities.
(e) Turn on
(f) Turn on
(g) Increase electrode diameter or reduce the welding current
Increase gas flow or check gas line for gas flow problems
(a) Select the right size electrode. Refer to basic TIG welding guide.
(b) Refer basic
TIG welding guide for ways to reduce arc flutter
Description Possible Cause
Welding arc cannot be established
Arc start is not smooth
(a) Work clamp is not connected to the work piece or the work/torch leads are not connected to the machine
(b) Torch lead is disconnected
(c) Gas flow incorrectly set, cylinder empty or the torch valve is off
(a) Tungsten electrode is too large for the welding current .
(b) The wrong electrode is being used for the welding job.
(c) Gas flow rate is too high.
(d) Incorrect shielding gas is being used.
(e) Poor work clamp connection to work piece
Remedy a) Connect the work clamp to the work piece or connect the work/torch leads to the right welding terminals.
(b) Connect it to the ‘.’ terminal.
(c) Select the right flow rate, change cylinders or turn torch valve on.
(a) Select the right size electrode
(b) Select the right electrode type. Refer to basic TIG welding guide
(c) Select the correct rate for the welding job.
Refer to basic
TIG welding guide
(d) Select the right shielding gas. Refer to basic TIG welding guide
(e) Improve connection to work piece
www.parweld.com
Power source problems
Description Possible cause
The welding arc cannot be established
(a) The primary supply voltage has not been switched on
(b) The welding power source switch is switched off
(c) Loose connections internally
Maximum output welding current cannot be achieved with nominal mains supply voltage
Welding current reduces when welding
Defective control circuit
Poor work lead connection to the work piece
A total loss of power, pilot lamp is off, no output, the fan is not operating
(a) Failure of input voltage
(b) Possible over voltage
(c) Internal fault with the machine
Remedy
(a) Switch on the primary supply voltage
(b) Switch on the welding power source.
(c) Have a qualified service engineer repair the connection
Have a qualified service engineer inspect then repair the welder
Ensure that the work lead has a reliable electrical connection to the work piece
(a) Re-establish mains supply
(b) Check voltage and if necessary move machine to alternative supply
(c) Have a qualified service engineer inspect then repair the welder
Description Possible cause
Fault lamp is on, no power output
(a) Machine overheated
(b) Over current state
(c) Internal fault with machine
Remedy
(a) Allow to cool with fan running
(b) Switch off mains power to the machine and re start
(c) Have a qualified service engineer inspect then repair the welder
ROUTINE MAINTENANCE
The only routine maintenance required for the power supply is a thorough cleaning and inspection, with the frequency depending on the usage and the operating environment.
Warning
Disconnect primary power at the source before removing the cover. Wait at least two minutes before opening the cover to allow the primary capacitors to discharge.
To clean the unit, remove the screws securing the outer cover, lift off the outer cover and use a vacuum cleaner to remove any accumulated dirt and dust. The unit should also be wiped clean, if necessary; with solvents that are recommended for cleaning electrical apparatus.
16 www.parweld.com
www.parweld.com
8.0 accessories
8.1 torch spares
Stock Code
CKE403
CKC403
Description
Electrode Holder with 3m Lead
Earth Lead 3m with Clamp
IV26-12S3BD18 Pro Tig Torch with 3 button switch
WP26AK Tig Spares Kit in Plastic Case
8.2 Gas equipment
Everyday Gas Regulators – 300
BAR
Single Stage
Features
Flow rate up to 96m
3
/h (3389 ft
3
/h)
• Full 300 bar capability
• Outlet pressure indicated on the bonnet
• Bottom entry design suited for top outlet cylinder valves
Fittings
• Fitted with standard 3/8” BSP outlet
• Fitted with 5/8” BSP inlet connections
Stock Code Description
Pressure
Maximum Outlet
E700140 Argon Preset Regulator 3.0 Bar
E700141 Argon Indicator Regulator 3.0 Bar
E700113 1 Gauge Argon
E700123 2 Gauge Argon
30 lpm flow
30 lpm flow
Flow Meters
Features
• Designed from brass bar whilst the tube and cover are moulded from high quality polycarbonate to ensure high impact resistance and clarity
• Calibrated to operate at an inlet pressure of 30PSI
• Sensitive needle valve provides easy adjustment and the downward facing outlet connection eliminates hose kinking.
Fittings
• Fitted with standard 3/89 BSP inlet and outlet connections
Stock Code Description
706100 Flow Meter Mixed Gas 15 lpm
9.0 Statement of Warranty
Limited Warranty:
Parweld Ltd, hereafter, “Parweld” warrants its customers that its products will be free of defects in workmanship or material. Should any failure to conform to this warranty appear within the time period applicable to the Parweld products as stated below, Parweld shall, upon notification thereof and substantiation that the product has been stored, installed, operated, and maintained in accordance with Parweld’s specifications, instructions, recommendations and recognized standard industry practice, and not subject to misuse, repair, neglect, alteration, or accident, correct such defects by suitable repair or replacement, at Parweld’s sole option, of any components or parts of the product determined by Parweld to be defective.
Parweld makes no other warranty, express or implied. This warranty is exclusive and in lieu of all others, including, but not limited to any warranty of merchantability or fitness for any particular purpose.
Limitation of Liability:
Parweld shall not under any circumstances be liable for special, indirect or consequential damages, such as, but not limited to, lost profits and business interruption. The remedies of the purchaser set forth herein are exclusive and the liability of Parweld with respect to any contract, or anything done in connection therewith such as the performance or breach thereof, or from the manufacture, sale, delivery, resale, or use of any goods covered by or furnished by Parweld whether arising out of contract, negligence, strict tort, or under any warranty, or otherwise, shall not, except as expressly provided herein, exceed the price of the goods upon which such liability is based. No employee, agent, or representative of Parweld is authorized to change this warranty in any way or grant any other warranty.
Purchaser’s rights under this warranty are void if replacement parts or accessories are used which in
Parweld’s sole judgement may impair the safety or performance of any Parweld product.
Purchaser’s rights under this warranty are void if the product is sold to purchaser by non-authorized persons.
The warranty is effective for the time stated below beginning on the date that the authorized
Distributor delivers the products to the purchaser.
Notwithstanding the foregoing, in no event shall the warranty period extend more than the time stated plus one year from the date Parweld delivered the product to the authorized distributor.
www.parweld.com
17
advertisement
Related manuals
advertisement