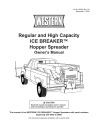
advertisement
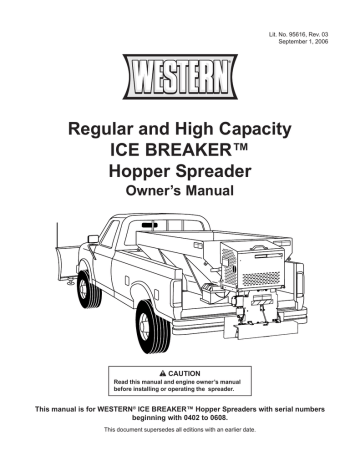
Lit. No. 95616, Rev. 03
September 1, 2006
Regular and High Capacity
ICE BREAKER™
Hopper Spreader
Owner’s Manual
CAUTION
Read this manual and engine owner’s manual before installing or operating the spreader.
This manual is for WESTERN
®
ICE BREAKER™ Hopper Spreaders with serial numbers beginning with 0402 to 0608.
This document supersedes all editions with an earlier date.
TABLE OF CONTENTS
PREFACE ................................................................................................................................................................ 1
SAFETY INFORMATION ......................................................................................................................................... 2
Before You Begin .............................................................................................................................................. 2
Torque Chart ..................................................................................................................................................... 3
Gasoline Warning Label .................................................................................................................................... 4
Warning/Caution Label ...................................................................................................................................... 4
LOADING ................................................................................................................................................................ 5
Certification ....................................................................................................................................................... 5
Material Weights ............................................................................................................................................... 5
Regular Capacity Load Weight .......................................................................................................................... 5
High Capacity Load Weight ............................................................................................................................... 5
Spreader Specifications ..................................................................................................................................... 6
Determining Vehicle Payload............................................................................................................................. 7
OPERATING THE SPREADER - CAB CONTROL .................................................................................................. 9
Cab Control Identification .................................................................................................................................. 9
Engine Operation .............................................................................................................................................. 9
Starting the Engine ............................................................................................................................................ 9
Stopping the Engine .......................................................................................................................................... 9
OPERATING THE HYDRAULIC SPREADER - DUAL CAB CONTROL ................................................................ 10
Cab Control Identification ................................................................................................................................ 10
Operating the Cab Control .............................................................................................................................. 10
Clutch Operation (Gas Engine Only) ............................................................................................................... 10
OPERATING THE SPREADER ............................................................................................................................. 11
Tecumseh Choke Adjustment Procedure ........................................................................................................ 11
Honda Choke Adjustment Procedure .............................................................................................................. 11
Baffle Adjustment ............................................................................................................................................ 12
Spread Patterns – Center Belt Drive ............................................................................................................... 13
Internal Baffles – Center Belt Drive ................................................................................................................. 13
External Baffles – Center Belt Drive ................................................................................................................ 13
MAINTENANCE .................................................................................................................................................... 14
Grease ............................................................................................................................................................ 14
Gear Oil Specification ...................................................................................................................................... 14
Drive Belts and Conveyor Chain Tension ........................................................................................................ 14
Electric Clutch ................................................................................................................................................. 15
Engine Service and Repair .............................................................................................................................. 15
Hydraulic Hopper Spreaders ........................................................................................................................... 16
After each use: ................................................................................................................................................ 16
At the end of each season:.............................................................................................................................. 16
Troubleshooting .............................................................................................................................................. 16
WIRING DIAGRAM (SPREADER BATTERY KIT) ................................................................................................. 17
WIRING DIAGRAM (VEHICLE BATTERY KIT) ..................................................................................................... 18
ELECTRIC THROTTLE MOTOR REPLACEMENT ............................................................................................... 19
Removal Instructions....................................................................................................................................... 19
Installation Instructions .................................................................................................................................... 19
DUAL HYDRAULIC CIRCUIT DIAGRAM .............................................................................................................. 20
September 1, 2006 Lit. No. 95616/95617, Rev. 03
PREFACE
This manual has been prepared to acquaint you with the safety information, operation and maintenance of your new hopper spreader. Please read this manual carefully and follow all recommendations. This will help ensure profitable and trouble-free operation of your hopper spreader. Keep this manual accessible. It is a handy reference in case minor service is required.
When service is necessary, bring your hopper spreader to your local outlet. They know your spreader best and are interested in your complete satisfaction.
NOTE: This spreader is designed to spread snow and ice control materials only. Do not use it for purposes other than those specified in this manual.
OWNER’S INFORMATION
Owner’s Name: _____________________________________________________________________
Date Purchased: _____________________________________________________________________
Outlet Name: ______________________________________________ Phone: _________________
Outlet Address: _______________________________________________________________________
Vehicle Model: _______________________________________________ Year: _______________
Spreader Type (Model): _______________________________________ Serial # ________________
Length: _______________________ Weight __________________ LBS/KG _______________
Lit. No. 95616/95617, Rev. 03 1 September 1, 2006
SAFETY INFORMATION
WARNING
Indicates a potentially hazardous situation that, if not avoided, could result in death or serious personal injury.
CAUTION
If rear directional, CHMSL light or brake stoplights are obstructed by the spreader, the lights shall be relocated, or auxiliary directional or brake stoplights shall be installed.
CAUTION
Indicates a situation that, if not avoided, could result in damage to product or property.
NOTE: Identifies tips, helpful hints and maintenance information the owner/operator should know.
Before You Begin
• Park the vehicle on a level surface, place shift lever in PARK or NEUTRAL and set the parking brake. Turn off the engine and remove keys.
WARNING
• Driver to keep bystanders minimum of 25 feet away from operating spreader.
• Before working with the spreader, secure all loose-fitting clothing and unrestrained hair.
• Before operating the spreader, verify all safety guards are in place.
• Before servicing the spreader, wait for conveyor and spinner to stop.
• Do not climb into or ride on spreader.
CAUTION
During the hopper spreader installation we recommend the addition of an OSHA compliant
Backup Alarm. This alarm is required for OSHA governed employers.
CAUTION
• Do not operate a spreader in need of maintenance.
• Before operating the spreader, reassemble any parts or hardware removed for cleaning or adjusting.
• Before operating the spreader, remove materials such as cleaning rags, brushes, and hand tools from the spreader.
• Before operating the spreader, read the engine owner’s manual.
• While operating the spreader, use auxiliary warning lights, except when prohibited by law.
• Tighten all fasteners according to the Torque
Chart. Refer to Torque Chart for the recommended torque values.
WARNING
Overloading could result in an accident or damage. Do not exceed GVWR or GAWR ratings as found on the driver-side door cornerpost of the vehicle. See Loading Section to determine maximum volumes of spreading material.
CAUTION
Disconnect electric and/or hydraulic power and tag out if required before servicing or performing maintenance.
WARNING
Do not install the control for this product in the deployment path of an air bag. Refer to vehicle manufacturer’s manual for air bag deployment area(s).
WARNING
Hydraulic fluid under pressure could cause skin injection injury. If you are injured by hydraulic fluid, get medical attention immediately.
September 1, 2006 2
CAUTION
DO NOT leave unused material in hopper.
Material can freeze or solidify, causing unit to not work properly. Empty and clean after each use.
NOTE: Lubricate grease fittings after each use.
Use a good quality multi-purpose grease.
Lit. No. 95616/95617, Rev. 03
SAFETY INFORMATION
CAUTION
Batteries normally produce explosive gases that can cause personal injury. Therefore, do not allow flames, sparks, or lit tobacco to come near battery. When charging or working near a battery, always cover your face and protect your eyes, and also provide ventilation.
• Batteries contain sulfuric acid that burns skin, eyes, and clothing.
• Disconnect the battery before removing or replacing any electrical components.
WARNING
Gasoline is highly flammable and gasoline vapor is explosive. Never smoke while working on vehicle. Keep all open flames away from gasoline tanks and lines. Wipe up any spilled gasoline immediately.
Torque Chart
CAUTION
Read instructions before assembling.
Fasteners should be finger tight until instructed to tighten according to the torque chart. Use standard methods and practices when attaching spreader including proper personal protective safety equipment.
Size
Recommended Fastener Torque
Chart (Ft.-Lb.)
SAE
Grade 2
SAE
Grade 5
SAE
Grade 8
1/4-20
5/16-18
3/8-16
3/8-24
7/16-14
1/2-13
9/16-12
5/8-11
3/4-10
7/8-9
1-8
Size
M 6
M 8
M 10
30
45
66
93
6
11
19
24
150
150
220
9
18
31
46
50
75
110
150
250
378
583
Metric Grade 8.8 (Ft.-Lb.)
Torque
Size
7
17
35
M 12
M 14
M 16
These torque values apply to fasteners except those noted in the instruction.
Torque
60
95
155
13
28
46
68
75
115
165
225
370
591
893
Lit. No. 95616/95617, Rev. 03 3 September 1, 2006
SAFETY INFORMATION
Gasoline Warning Label
WARNING
Gasoline is flammable.
• Turn off engine and allow it to cool before filling gas tank.
• DO NOT smoke or use open flame within 25 feet of spreader.
• Allow spilled gas to evaporate completely before starting engine.
• Gasoline engine produces poisonous gases while running.
DO NOT operate in an enclosed area.
• Gasoline engine has hot and moving parts that can cause injury.
Use care when working with or near the gasoline engine and its parts.
• Shut off engine when not in use, even for short periods of time,
to avoid damage to equipment or property.
65097
Please become familiar with the Warning and Caution labels on the spreader!
Warning/Caution Label
Gasoline Warning
Label (on Engine
Cover)
Warning/Caution Label
Warning/Caution Label
WARNING CAUTION
• DO NOT EXCEED GVWR OR GAWR WITH SPREADER AND LOAD.
• TURN OFF SPREADER BEFORE FILLING, ADJUSTING, OR CLEANING.
• BYSTANDERS TO STAY A MINIMUM OF 25 FEET AWAY FROM
OPERATING SPREADER.
• DO NOT CLIMB INTO OR RIDE ON SPREADER.
• KEEP HANDS, FEET, CLOTHING AWAY FROM MOVING CONVEYOR
AND SPINNER.
• READ OWNER'S MANUAL AND ENGINE MANUAL BEFORE
OPERATING OR SERVICING SPREADER.
• EMPTY AND CLEAN SPREADER AFTER EACH USE.
68595
September 1, 2006 4 Lit. No. 95616/95617, Rev. 03
LOADING
This Manual covers vehicles which have been recommended for carrying the hopper spreader.
Please see your local dealer for proper vehicle applications.
WARNING
Overloading could result in an accident or damage. Do not exceed GVWR or GAWR as found on the driver-side cornerpost of vehicle.
Certification
WARNING
New untitled vehicle installation of a spreader requires National Highway Traffic Safety
Administration altered vehicle certification labeling. Installer to verify that struck load of snow or ice control material does not exceed GVWR or
GAWR rating label and complies with FMVSS.
CAUTION
Material Weights
Read and adhere to manufacturer’s ice control package labeling including Material Safety Data
Sheet requirements.
Material
Fine Salt - Dry
Coarse Salt – Dry
Coarse Sand – Dry
Coarse Sand – Wet
Cinders
Density
(lb. per cubic yd.)
1,350
1,215
2,700
3,240
1,080
7’ Spreader
Regular Capacity Load Volume
26.5”
8’ Spreader
1.6
Cu. Yd.
.88
Cu. Yd.
0.44
Cu. Yd.
18”
12”
0.5
Cu. Yd.
1.0
Cu. Yd.
2.0
Cu. Yd.
9’ Spreader 8’ Spreader
3.0
Cu. Yd.
1.8
Cu. Yd.
0.6
Cu. Yd.
2.6
Cu. Yd.
1.6
Cu. Yd.
0.5
Cu. Yd.
High Capacity Load Volume
32.5”
24”
12”
10’ Spreader
0.7
Cu. Yd.
3.3
2.0
Cu. Yd.
Cu. Yd.
Lit. No. 95616/95617, Rev. 03 5 September 1, 2006
LOADING
Spreader Specifications
Spreader
Description
Regular Capacity
7’ Hopper Body
14 Gauge Stainless Steel
Regular Capacity
7’ Hopper Body
12 Gauge Mild Steel
Regular Capacity
8’ Hopper Body
14 Gauge Stainless Steel
Regular Capacity
8’ Hopper Body
12 Gauge Mild Steel
High Capacity
8’ Hopper Body
12 Gauge Stainless Steel
High Capacity
9’ Hopper Body
12 Gauge Stainless Steel
High Capacity
10’ Hopper Body
12 Gauge Stainless Steel
High Capacity
8’ Hopper Body
12 Gauge Mild Steel
High Capacity
9’ Hopper Body
12 Gauge Mild Steel
High Capacity
10’ Hopper Body
12 Gauge Mild Steel
Regular Capacity - Hyd
8’ Hopper Body
14 Gauge Stainless Steel
Regular Capacity - Hyd
8’ Hopper Body
12 Gauge Mild Steel
High Capacity – Hyd
8’ Hopper Body
12 Gauge Stainless Steel
High Capacity – Hyd
10’ Hopper Body
12 Gauge Stainless Steel
High Capacity - Hyd
8’ Hopper Body
12 Gauge Mild Steel
High Capacity - Hyd
10’ Hopper Body
12 Gauge Mild Steel
Overall
Spreader
Length
(inches)
Empty
Weight (lb.)
(No screen or battery)
Capacity
Struck
(cu. yd.)
Capacity
Rounded
(cu. yd.)
Pick-up
Trucks
Above 8500
116 600 2.0 2.5 50-3/4 32 lb. GVWR
Dump or
Trucks
Above
GVWR
Dump or
Trucks
Above
GVWR
Overall
Width
(inches)
Overall
Height
(inches)
Recommended
Use
Pick-up
Trucks above 8500
104 680 1.7 2.2 50-3/4 32 lb. GVWR
Pick-up
Trucks above 8500
116 750 2.0 2.5 50-3/4 32 lb. GVWR
116 830 2.6 3.2 58 37-1/2
Dump or
Flat Bed
Trucks
128 890 3.0 3.7 58 37-1/2
Above
15,000 lb.
GVWR
140 950 3.3 4.1 58 37-1/2
116 810 2.6 3.2 58 37-1/2
Dump or
Flat Bed
Trucks
128 870 3.0 3.7 58 37-1/2
Above
15,000 lb.
GVWR
140 930 3.3 4.1 58 37-1/2
September 1, 2006 6 Lit. No. 95616/95617, Rev. 03
LOADING
Determining Vehicle Payload
WARNING
Overloading could result in an accident or damage. Do not exceed GVWR or GAWR ratings as found on the driver-side door cornerpost of the vehicle. See Loading Section to determine maximum volumes of spreading material.
1. Install hopper spreader and optional equipment according to the instructions.
2. Install or attach any other equipment that will be on the vehicle while the hopper spreader will be in use
(step bumper, trailer hitch, snowplows, etc.). Fill gas tanks.
3. Obtain the Gross Vehicle Weight Rating (GVWR),
Front Gross Axle Weight Rating (FGAWR), and
Rear Gross Axle Weight Rating (RGAWR) from the certification label located inside the driver-side door jam.
4. With the occupants in the truck for normal hopper spreader operation, weigh the vehicle to obtain gross vehicle weight (GVW).
5. Subtract the GVW from the GVWR to determine the available material payload.
6. Obtain the weight per cubic yard (lb./cu. yd.) of the desired material. Divide the weight into the payload to determine the maximum volume of material that can be carried.
7. Compare the maximum volume to determine the maximum height of the material in the hopper spreader.
8. Fill hopper with the material to the calculated height. Re-weigh vehicle with occupants and verify the GVW, Front Gross Axle Weight, and Rear
Gross Axle Weight are less than the vehicle’s ratings.
9. Repeat steps 7 and 8 for each type of material.
Refer to “Determining Vehicle Payload” worksheet for an example and worksheet.
Lit. No. 95616/95617, Rev. 03 7 September 1, 2006
LOADING
Determining Vehicle Payload
Material Type
Equipment installed when vehicle was weighed
Front Gross Axle Weight Rating
(FGAWR)
Rear Gross Axle Weight Rating
(RGAWR)
Gross Vehicle Weight Rating
(GVWR) (lb.)
Gross Vehicle Weight (lb.)
(empty)
Payload Available (lb.)
Material Density (lb./cu. yd.)
Maximum Volume
(cu. yd.)
Maximum Height (approximate)
(in.)
Loaded Front Gross Axle Weight
(FGAW) (lb.)
Loaded Rear Gross Axle Weight
(RGAW) (lb.)
Loaded Gross Vehicle Weight
(GVW)
Example:
Coarse Salt - Dry
RC Mild Steel 8’
Hopper Spreader
8600
- 6500
= 2100
÷ 1215
= 1.73
24”
September 1, 2006 8 Lit. No. 95616/95617, Rev. 03
OPERATING THE SPREADER - CAB CONTROL
Cab Control Identification
Electric
Clutch
Switch
Spreader
Ignition
Switch
Electric
Throttle
Switch
Choke
Light
NOTE: Do not hold the throttle switch in the FAST position until the choke re-engages. The engine will not run with the choke 100% engaged. See
Choke Adjustment Procedure for instructions for tuning the maximum choke point.
ON
OFF
BLAST
SPINNER
ON
OFF
START
E
N
G
I
N
E
CHOKE
F
S
8. To control the engine speed:
• Increase: hold the throttle switch at CHOKE/FAST.
Do not operate engine with choke light on.
• Decrease: hold the throttle switch at SLOW.
NOTE: If the engine does not start after 10 seconds of cranking, turn both vehicle and spreader ignition switches to OFF and see the engine manual that is shipped with the spreader.
NOTE: The conveyor and spinner will operate when the spinner switch is in the ON or BLAST position.
NOTE: Maximum engine speed is obtained just prior to choking the engine.
Engine Operation
Refer to above drawing as a reference for starting and stopping the engine.
Starting the Engine
CAUTION
Read Owner’s and Engine Manual before operating or servicing spreader.
1. Turn the vehicle ignition switch to ON.
2. Verify the spinner switch is OFF.
3. Move the spreader ignition switch to START.
4. While the engine is cranking, move the throttle switch to CHOKE/FAST. (Choke light will come on when the choke begins to close. Hold in FAST for
1/2 second after light comes on.)
5. When the engine starts to fire, move the throttle switch towards the SLOW position. The engine will then start.
6. When the engine starts, release the ignition switch.
7. After the engine starts, move the throttle switch toward FAST to bring the engine up to maximum speed. Allow the engine to warm up to proper operating temperature before attempting to spread.
Lit. No. 95616/95617, Rev. 03 9
Stopping the Engine
1. Move the throttle to SLOW and hold for two seconds.
2. Turn the spreader ignition switch to OFF.
CAUTION
When the engine will not be run for a period of 5 minutes or more, be sure to turn off the fuel supply valve, if the engine is equipped with a fuel shutoff. Refer to the engine Owner’s Manual.
CAUTION
Do not leave unused material in hopper.
Material can freeze or solidify, causing unit to not work properly. Empty and clean after each use.
CAUTION
Do not attempt to free the chain by using a pipe wrench or any other tool on the output shaft of the gear case. The gear case is designed to accept torque from the input shaft only.
Attempts to turn the output shaft will strip the gears and void any warranty.
September 1, 2006
OPERATING THE HYDRAULIC SPREADER - DUAL CAB CONTROL
Cab Control Identification
Typical Spreader Control Valve (Sold as an accessory)
10
11
8
7
1
E
S
A
6
2
I N
C
3
5
AUGER
ON Position
10
11
8
7
1
2
E
I N
C
S
A
E
3
5
6
SPINNER
OFF Position
WARNING
• Driver to keep bystanders minimum of 25 feet away from operating spreader.
• Before working with the spreader, secure all loose-fitting clothing and unrestrained hair.
• Before operating the spreader, verify all safety guards are in place.
• Before servicing the spreader, wait for conveyor and spinner to stop, then lock out power.
• Do not climb into or ride on spreader.
CAUTION
• Do not operate a spreader in need of maintenance.
• Before operating the spreader, reassemble any parts or hardware removed for cleaning or adjusting.
• Before operating the spreader, remove materials such as cleaning rags, brushes, and hand tools from the spreader.
• Before operating the spreader, read the owner’s manual.
• While operating the spreader, use auxiliary warning lights, except when prohibited by law.
• Tighten all fasteners according to the Torque
Chart. Refer to Torque Chart for the recommended torque values.
September 1, 2006 10
Operating the Cab Control
1. Engage the hydraulic system with the spreader lever in the “OFF” position.
2. To turn the spreader on, move the lever to the
“ON” position. The spinner and conveyor should begin to turn.
3. The spinner and auger speeds are independently adjusted by rotating the detented adjustment knobs. The knobs can be adjusted either during operation or with lever in the “OFF” position.
These speed settings will be maintained when the lever is placed in the “OFF” position.
Clutch Operation (Gas Engine Only)
1. Start the engine.
2. Adjust the speed to slightly above idle.
3. Move the clutch switch to ON.
4. Increase the engine speed to the desired RPM.
Lit. No. 95616/95617, Rev. 03
OPERATING THE SPREADER
Tecumseh Choke Adjustment Procedure
1. The choke linkage and choke adjustment screw is shipped from the factory with the choke butterfly set to 75% fully closed choke.
2. With the choke set at 100% the engine will not stay running in the choked position. This position is for
extremely cold conditions. Throttle linkage travel from 0% to 100% choke is 3/16". Four and onehalf turns of the Choke Adjustment Screw
(clockwise when viewed from above the engine) will take the maximum choke setting from fully closed to fully open (no choking at all).
3. To adjust your choke setting loosen the adjustment retainer screw and rotate the Choke Adjustment
Screw clockwise one full turn (scratch a mark on the knob to indicate position). This will generally allow the engine to run very roughly with the throttle linkage at maximum choke. This is approximately the equivalent of 75% fully closed choke. (This is the factory setting.)
Choke Butterfly
Choke Adjustment
Screw
Retainer Screw
100%
0%
3/16" Max.
Adjustment
4. Additional adjustments can be made by 1/4 turn increments until you reach the desired start/run in choke setting of your preference/need.
Honda Choke Adjustment Procedure
1. Engines are shipped with choke adjusted to the completely closed position when the choke is engaged. The choke only requires adjusting if inspection reveals the choke is not fully closing.
2. Move throttle control to full choke position.
3. Turn choke adjusting screw counter-clockwise five to seven turns.
4. Attempt to move choke rod in the direction of the choke adjusting screw. If the rod has no movement, no adjustment is necessary.
5. Return the choke adjusting screw to its original position or clockwise until it touches choke lever.
6. If the choke rod has movement, bend engaging tab in the direction away from choke adjusting screw until there is no choke rod movement.
7. In the event bending the tab fails to remove all choke rod movement, partially straighten out the bend in the choke rod. This bend is near the governor arm.
8. The choke adjusting screw, when properly adjusted, stops excessive force from being exerted on the choke actuator.
Choke
Adjustment
Screw
Lit. No. 95616/95617, Rev. 03 11 September 1, 2006
OPERATING THE SPREADER
Baffle Adjustment
Spread pattern and the amount of material dispensed depends on engine RPM, gate position, and baffle settings.
• Decreasing RPM and/or gate-opening will
decrease the amount of material coming to the spinner.
• Increasing RPM and/or gate-opening will increase the amount of material coming to the spinner.
Center Belt Drive Chute
Internal Baffle
Adjustment Handle
(both sides)
September 1, 2006 12 Lit. No. 95616/95617, Rev. 03
OPERATING THE SPREADER
Spread Patterns – Center Belt Drive
These figures are as viewed from the top of the spinner looking down.
Internal Baffles External Baffles
Both internal baffles out All baffles adjusted down for a confined spread pattern
Driver-side baffle in, curb-side baffle out Curb-side baffle deflects material down; heavy on curb side
Driver-side baffle out, curb-side baffle in
Lit. No. 95616/95617, Rev. 03 13
Driver-side baffle deflects material down; heavy on driver side
September 1, 2006
MAINTENANCE
CAUTION
Disconnect electric and/or hydraulic power and tag out if required before servicing or performing maintenance.
Grease
CAUTION
Over-greasing may cause seal damage. The gear case must be filled to the oil-level plug with Mobil SHC 632 or Exxon SHP 320 or equivalent synthetic gear-type lubricant. Keep the breather plug clean.
• Use dielectric grease on all electrical connections at the beginning and end of each season, and as required during the season.
• After every 10 hours of operation, grease the idler bearings on the idler shaft, flanged bearings on the drive shaft, and the spinner shaft bearing under the spinner.
• After every 50 hours of operation, grease the input shaft bearing on the gear case and verify the oil level of the gear case is level with the fill hole.
• Change gear case oil once a year. Drain oil by removing the side cover of the gear case. Refill with Mobil SHC 632 or Exxon SHP 320 or equivalent synthetic gear oil. Oil level should be even with the bottom of the fill hole.
Gear Oil Specification
Use Mobil SHC 632 or Exxon SHP 320 or equivalent.
Drive Belts and Conveyor Chain Tension
• At the beginning of each season, and once a month during the season, verify the drive pulley set screws and the clutch pulley mounting bolts are tight.
• Visually inspect the drive belts for cracks and wear.
If a belt is cracked or worn, replace the belt.
• Maintain correct belt tension. Correct tension allows for 1/4" - 5/16" of deflection midway between the pulleys.
To increase engine belt tension: Loosen the four bolts that secure the engine mount to the engine base and pull the engine away from the clutch.
After correct tension is achieved, retighten the engine mount bolts.
To increase spinner belt tension: Loosen spinner bearing bolts, and pull shaft assembly away from the clutch. After correct tension is achieved, retighten the bearing bolts.
• Periodically check the conveyor chain tension. To check the tension, measure in 20"-24" from the rear edge of the sills. Push up on the chain with your hand. The conveyor chain should lift up 1"-3" off the conveyor chain guide or cross angles.
Conveyor
Chain
Rear Edge of Sill
September 1, 2006
20" - 24"
1" - 3"
• Use the two 5/8" x 6" take-up bolts at the front of the spreader to adjust the conveyor chain tension.
Loosen the locknuts before attempting to adjust the take-up bolts. Turn both sides equal amounts to ensure the tension is equally distributed across both sides of the conveyor chain.
14
• Always empty the spreader when it is not in use to prevent a frozen conveyor chain.
Lit. No. 95616/95617, Rev. 03
MAINTENANCE
Electric Clutch
To minimize problems and extend the life of the electric clutch, do the following:
• At the end of each snow season, remove and clean the clutch.
• After cleaning the clutch, coat both mating surfaces of the clutch with oil or light grease.
• Remove oil and grease prior to using the clutch again.
Engine Service and Repair
Maintain the spreader engine according to the engine
Owner’s Manual that is shipped with the spreader.
Engine warranty is covered by the engine manufacturer and is described in the engine manual.
If service or repair is needed, contact an authorized engine manufacturer service center. To serve you promptly, the service center will need the make, model, type, and code number for your engine.
Your nearest service center is listed in the “Yellow
Pages” under “Engines, Gasoline” or “Gasoline
Engines.”
NOTE: The maximum choke point of the Tecumseh
Engine is adjustable. The unit is shipped with the choke adjusted to be 75% closed. See Choke
Adjustment Procedure for adjustment instructions.
Lit. No. 95616/95617, Rev. 03 15 September 1, 2006
MAINTENANCE
Hydraulic Hopper Spreaders
1. Check hydraulic fluid level before every use. Add fluid as required.
2. Periodically inspect the hoses and fittings for damage and possible leaks.
3. Change the hydraulic fluid after the first 50 hours of operation of a new unit.
4. Reservoir should be drained through the drain plug only, NOT through the suction outlet.
• Flush and refill reservoir annually, or sooner if fluid shows signs of break-down or contamination.
• The use of proper hydraulic fluid in the system is critical to satisfactory performance. Only clean, new hydraulic fluid, of the proper type and viscosity as recommended by the pump manufacturer, should be used.
• Keep all hydraulic fluids in original containers. Use only clean measuring containers and funnels when pouring fluids. Keep all containers closed when not in use.
To keep your spreader functioning properly, observe the following recommendations:
After each use:
• Wash out hopper and rinse off all external surfaces.
• Apply dielectric grease to all electrical connections to prevent corrosion.
• Lubricate all grease fittings. Use a good quality multi-purpose grease.
At the end of each season:
• Wash out hopper and all external surfaces.
• Apply dielectric grease to all electrical connections to prevent corrosion.
• Lubricate all grease fittings. Use a good quality multi-purpose grease.
• Oil or paint all bare metal surfaces.
Troubleshooting
PROBLEM
1. Unit speed does not increase with the dial setting.
2. Unit stalls under load.
3. Unit speed fluctuates momentarily when control is first turned on.
4. Pump blows seals at start up.
CORRECTION
A. Increase the truck engine speed.
B. Check condition of pump.
C. Check for adequate PTO percent.
Check circuit pressure. 900-1200 PSI maximum with relief valve lifting at 1500 PSI.
A. Oil is cold. Wait until oil has warmed up.
B. Change to lighter weight oil.
Pump installed backwards. Replace seals and reverse pump in driveline. (Note arrow on pump.)
September 1, 2006 16 Lit. No. 95616/95617, Rev. 03
WIRING DIAGRAM (SPREADER BATTERY KIT)
Red
Choke Light
Choke
Switch
Red
Start Switch
Black
White
Red
Red
Brown
Black
Green
Red
Clutch
Switch
Gray
Red
Red
Yellow
Blue
Violet
Note: Yellow, Blue, and Violet
wires are provided
for accessory use.
Note: 10 Amps MAX load per
wire or a combined total
of 12 Amps MAX load for
all three wires combined.
Vehicle
Harness
White/
Black
Black
Cab Control
Wiring
Red
(+)
To Switched
Accesory Circuit
(-)
To Ground Point
Orange
To Vehicle CHMSL Feed
1
Vehicle Side Wiring Harness
Spreader Side Wiring Harness
Ground to
Engine Base
Note: Yellow, Blue, and Violet
wires are provided
for accessory use.
7
7
1
6
11
11
6
1. Black
2. Brown
3. Red
4. Orange
5. Yellow
6. Green
7. Blue
8. Violet
9. Gray
10. White
11. White/black
Red
Solenoid
Not
Used
Lit. No. 95616/95617, Rev. 03
Engine
Clutch
17
Stoplight
Dark
Green
September 1, 2006
WIRING DIAGRAM (VEHICLE BATTERY KIT)
Red
Choke
Switch
Start Switch
Choke Light
Brown
Black
Red
Red
White
Red
Note: Yellow, Blue,
and Violet wires
are provided for
accessory use.
Note: 10 Amps MAX load
per wire or a
combined total of
12 Amps MAX load
for all three wires
combined.
Yellow
Blue
Violet
Green
Red
Clutch
Switch
Gray
Red
Red
White/
Black
Vehicle
Harness
Black
Cab Control
Wiring
Red
(+)
To Switched
Accesory Circuit
(-)
To Ground Point
Orange
To Vehicle CHMSL Feed
Solenoid
Vehicle Side Wiring Harness
Spreader Side Wiring Harness
September 1, 2006
Note: Yellow, Blue, and Violet wires
are provided for accessory use.
Ground to
Engine Base
Clutch
Stoplight
Not
Used
Engine
18
Dark
Green
Lit. No. 95616/95617, Rev. 03
ELECTRIC THROTTLE MOTOR REPLACEMENT
Crank (shown against the
Electric Throttle Bracket according to step 4 of the installation instructions below.)
Throttle Pin
#4-40 Locknut
#4 Plain Washer
Choke Light
Switch
1/4”-20 x 3/4”
Cap Screw
1/4” Plain Washer
Electric Throttle Arm
#6-32 Locknut
#6-32 x 5/8” Cap Screw
#4-40 x 3/4” Socket Button
Head Machine Screw
Electric Throttle Motor
Electric Throttle Bracket
Engine Mount
1/4” Plain Washer
1/4” Split Lock Washer
1/4”-20 Nut
Removal Instructions
1. Disconnect the battery cables.
2. Carefully observe the existing installation. Mark the electric throttle position on the engine mount.
3. Disconnect the brown and red spreader harness wires from the electric throttle motor leads.
4. Remove the 1/4"-20 fasteners that hold the electric throttle bracket to the engine mount.
5. Remove the #6-32 fasteners holding the electric throttle motor to the bracket. Remove the electric throttle motor.
Installation Instructions
CAUTION
Improper installation can result in damage to the engine choke/throttle linkage.
1. Connect the brown and red spreader harness wires (not shown) to the corresponding colored electric throttle motor leads.
2. Using the electric throttle control, run the new motor until the crank reaches the 12 o’clock position. (A 9-volt battery can be used as a substitute for the control.)
Lit. No. 95616/95617, Rev. 03
3. Fasten the electric throttle motor to the bracket using the existing hardware.
4. Using the electric throttle control, run the new electric throttle motor until the crank is against the bracket as shown in above diagram.
5. Place the electric throttle arm on the crank as shown in the above diagram.
6. Place the electric throttle assembly onto the engine mount inserting the throttle pin into the engine choke/throttle linkage plastic slider (not shown).
7. Loosely bolt electric throttle assembly to the engine mount with the existing hardware.
8. Keeping the electric throttle arm parallel to and against the carburetor control bracket, move the electric throttle bracket forward putting the engine throttle into the full choke position.
9. Tighten the fasteners according to the Torque
Chart.
10. Reconnect the battery cables.
19
11. Verify the crank is stopped in both directions by the bracket, not the carburetor linkage.
September 1, 2006
Inlet Flow from Tank
DUAL HYDRAULIC CIRCUIT DIAGRAM
Typical Hydraulic Circuit
Dedicated Fixed Displacement Pump
PUMP
23 GPM Min
@
1500 PSI
VALVE
Rated to 40 GPM
@
1500 PSI
T
P
A
S
Excess Flow to Tank
Return Flow to Tank
Controlled Flow to
Conveyor Motor:
10 GPM @ 1500 PSI
Controlled Flow to
Spinner Motor:
10 GPM @ 1500 PSI
Spinner Motor
Return Flow to Tank
Conveyor Motor
TANK
September 1, 2006 20 Lit. No. 95616/95617, Rev. 03
WESTERN PRODUCTS
P.O. BOX 245038
MILWAUKEE, WISCONSIN 53224-9538 www.westernplows.com
A DIVISION OF DOUGLAS DYNAMICS, L.L.C.
Copyright
©
2006 Douglas Dynamics, L.L.C. All rights reserved. This material may not be reproduced or copied, in whole or in part, in any printed, mechanical, electronic, film or other distribution and storage media, without the written consent of Western Products. Authorization to photocopy items for internal or personal use by Western Products outlets or spreader owner is granted.
Western Products reserves the right under its product improvement policy to change construction or design details and furnish equipment when so altered without reference to illustrations or specifications used. Western Products or the vehicle manufacturer may require or recommend optional equipment for spreaders. Do not exceed vehicle ratings with a spreader. Western Products offers a limited warranty for all spreaders and accessories. See separately printed page for this important information. The following are registered (
®
) and unregistered (™) trademarks of Douglas Dynamics, L.L.C.: ICE BREAKER™, WESTERN ® .
Printed in U.S.A.
September 1, 2006 Lit. No. 95616, Rev. 03
advertisement
* Your assessment is very important for improving the workof artificial intelligence, which forms the content of this project
Related manuals
advertisement
Table of contents
- 3 PREFACE
- 4 SAFETY INFORMATION
- 4 Before You Begin
- 5 Torque Chart
- 6 Gasoline Warning Label
- 6 Warning/Caution Label
- 7 LOADING
- 7 Certification
- 7 Material Weights
- 7 Regular Capacity Load Weight
- 7 High Capacity Load Weight
- 8 Spreader Specifications
- 9 Determining Vehicle Payload
- 11 OPERATING THE SPREADER - CAB CONTROL
- 11 Cab Control Identification
- 11 Engine Operation
- 11 Starting the Engine
- 11 Stopping the Engine
- 12 OPERATING THE HYDRAULIC SPREADER - DUAL CAB CONTROL
- 12 Cab Control Identification
- 12 Operating the Cab Control
- 12 Clutch Operation (Gas Engine Only)
- 13 OPERATING THE SPREADER
- 13 Tecumseh Choke Adjustment Procedure
- 13 Honda Choke Adjustment Procedure
- 14 Baffle Adjustment
- 15 Spread Patterns – Center Belt Drive
- 15 Internal Baffles – Center Belt Drive
- 15 External Baffles – Center Belt Drive
- 16 MAINTENANCE
- 16 Grease
- 16 Gear Oil Specification
- 16 Drive Belts and Conveyor Chain Tension
- 17 Electric Clutch
- 17 Engine Service and Repair
- 18 Hydraulic Hopper Spreaders
- 18 After each use
- 18 At the end of each season
- 18 Troubleshooting
- 19 WIRING DIAGRAM (SPREADER BATTERY KIT)
- 20 WIRING DIAGRAM (VEHICLE BATTERY KIT)
- 21 ELECTRIC THROTTLE MOTOR REPLACEMENT
- 21 Removal Instructions
- 21 Installation Instructions
- 22 DUAL HYDRAULIC CIRCUIT DIAGRAM