advertisement
▼
Scroll to page 2
of 40
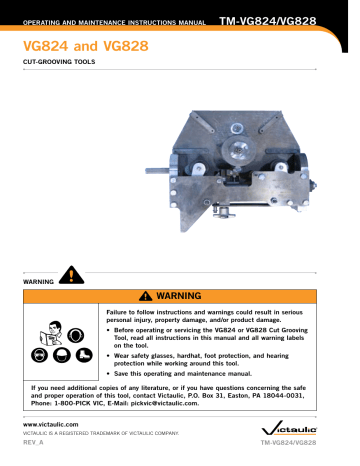
Operating and Maintenance Instructions Manual TM-VG824/VG828 VG824 and VG828 cut-grooving tools warning WARNING Failure to follow instructions and warnings could result in serious personal injury, property damage, and/or product damage. • Before operating or servicing the VG824 or VG828 Cut Grooving Tool, read all instructions in this manual and all warning labels on the tool. • Wear safety glasses, hardhat, foot protection, and hearing ­protection while working around this tool. • Save this operating and maintenance manual. If you need additional copies of any literature, or if you have questions concerning the safe and proper operation of this tool, contact Victaulic, P.O. Box 31, Easton, PA 18044-0031, Phone: 1‑800‑PICK VIC, E-Mail: [email protected]. www.victaulic.com Victaulic is a registered trademark of Victaulic Company. REV_A TM-VG824/VG828 Operating and Maintenance Instructions Manual TM-VG824/VG828 INDEX Tool Bit Removal . . . . . . . . . . . . . . . . . . . . . . 18 Hazard Identification . . . . . . . . . . . . . . . . . . . . 1 Tool Bit Installation . . . . . . . . . . . . . . . . . . . . 19 Operator Safety Instructions . . . . . . . . . . . . . . 1 Tool Bit Projection Adjustment . . . . . . . . . . . 20 Introduction . . . . . . . . . . . . . . . . . . . . . . . . . . 3 Pipe Stop Removal and Installation . . . . . . . . 21 Tool Bit Information for VG824 Tools . . . . . . . . 3 Adjusting the Center Adjustable Pipe Stop . . . . . . . . . . . . . . . . . . . . . . . . . 22 Tool Bit Information for VG828 Tools . . . . . . . . 3 Receiving the VG824 and VG828 Tools . . . . . . 4 Top and Bottom Pipe Stop Removal and Installation . . . . . . . . . . . . . . . . . . . . . 23 Container Contents . . . . . . . . . . . . . . . . . . . 4 Drive Roll Removal and Installation . . . . . . . . 23 Factory Settings for the VG824 Tool . . . . . . 4 Drive Roll Removal . . . . . . . . . . . . . . . . . . 23 Factory Settings for the VG828 Tool . . . . . . 4 Drive Roll Installation . . . . . . . . . . . . . . . . 23 Additional Tools that may be Required for Tool Setup, Adjustment, or Operation . . . . . . . . . 5 Maintenance . . . . . . . . . . . . . . . . . . . . . . . . . 24 Re-Sharpening Tool Bits . . . . . . . . . . . . . . . . 24 Power Requirements for the Victaulic Power Mule II or Power Drive . . . . . . . . . . . . . . . . 6 Parts Ordering Information . . . . . . . . . . . . . . 25 Extension Cord Requirements . . . . . . . . . . . 6 Recommended Accessories . . . . . . . . . . . . . 25 Tool Nomenclature . . . . . . . . . . . . . . . . . . . . . 7 Victaulic Power Mule II . . . . . . . . . . . . . . . 25 Chain-Type Pipe Vise Setup . . . . . . . . . . . . . . 8 Troubleshooting . . . . . . . . . . . . . . . . . . . . . . 26 Preparing Pipe for Grooving . . . . . . . . . . . . . . 8 Explanation of Critical Cut Groove Dimensions . . . . . . . . . . . . . . . . . . . . . . . . 28 Pipe Length Requirements . . . . . . . . . . . . . . . 9 Mounting Pipe in the Chain-Type Pipe Vise . . . 9 Checking and Adjusting the Tool Prior to Grooving . . . . . . . . . . . . . . . . . . . . . . . . . . 10 Mounting the VG824 or VG828 Tool Onto the Pipe . . . . . . . . . . . . . . . . . . . . . . 10 Attaching the Victaulic Power Mule II to the VG824 or VG828 Tool . . . . . . . . . . . . . . . . 11 Attaching a Power Drive to the VG824 or VG828 Tool . . . . . . . . . . . . . . . . . . . . . . . . 12 Grooving Operation . . . . . . . . . . . . . . . . . . . . 13 Preparing to Dismount the VG824 or VG828 Tool . . . . . . . . . . . . . . . . . . . . . . . . 15 Dismounting the VG824 or VG828 Tool when Used with the Victaulic Power Mule II . . . . 16 Dismounting the VG824 or VG828 Tool when Used with a Power Drive . . . . . . . . . . . . . . 16 Standard Cut Groove Specifications for Steel and Other NPS Pipe Grooved with the VG824 Tool . . . . . . . . . . . . . . . . . . . . . 30 Rigid Radius-Cut Groove Specifications for Ductile Iron Pipe Grooved with the VG824 Tool . . . . . . . . . . . . . . . . . . . . . . . . 32 Flexible Radius-Cut Groove Specifications for Ductile Iron Pipe Grooved with the VG824 Tool . . . . . . . . . . . . . . . . . . . . . . . . 33 Cut Groove Specifications for Standard or Heavier-Wall Pipe or Plastic-Coated Pipe Grooved with the VG824 Tool and Joined with Style HP-70ES Couplings . . . . . . . . . . 34 Advanced Groove System (AGS) Cut Grooving Specifications for Carbon Steel Pipe Grooved with the VG828 Tool . . . . . . . . . . . . . . . . . 35 VG824 Tool Bit/Pipe Stop Specifications . . . . 36 VG828 Tool Bit/Pipe Stop Specifications . . . . 37 Groove Diameter Adjustment . . . . . . . . . . . . 17 www.victaulic.com Victaulic is a registered trademark of Victaulic Company. TM-VE450FSD REV_A Operating and Maintenance Instructions Manual TM-VG824/VG828 Hazard Identification OPERATOR SAFETY INSTRUCTIONS Definitions for identifying the various hazard ­levels are ­provided below. VG824 and VG828 Cut-Grooving Tools are designed only for cut grooving pipe. Use of these tools requires dexterity and mechanical skills, as well as sound safety habits. Although these tools are designed for safe, dependable operation, it is impossible to anticipate all combinations of circumstances that could result in an accident. The following instructions are recommended for safe operation of these tools. The operator is cautioned always to practice “safety first” during each phase of use, including setup and maintenance. It is the responsibility of the owner, lessee, or user to ensure that all operators read this manual and fully understand the operation of these tools. This safety alert symbol indicates important safety messages. When you see this symbol, be alert to the possibility of personal injury. Carefully read and fully understand the message that follows. DANGER • The use of the word “DANGER” ­identifies an immediate hazard with a likelihood of death or serious personal injury if instructions, including recommended precautions, are not followed. WARNING • The use of the word “WARNING” ­identifies the presence of hazards or unsafe practices that could result in death or ­serious personal injury if instructions, including recommended precautions, are not followed. CAUTION • The use of the word “CAUTION” identifies possible hazards or unsafe practices that could result in personal injury and product or property damage if instructions, including recommended ­precautions, are not followed. NOTICE • The use of the word “NOTICE” identifies special instructions that are important but not related to hazards. Read this operating and maintenance instructions manual and the operating and maintenance instructions manual for the Victaulic Power Mule II or power drive before operating or servicing these tools. Become familiar with the tools’ operations, applications, and limitations. Be particularly aware of their specific hazards. Store this manual in a clean area where it is always readily available. Additional copies of this manual are available upon request through Victaulic. 1. These tools are designed ONLY for cut ­grooving pipe sizes, materials, and wall thicknesses listed in this manual. 2. Avoid using tools in dangerous ­environments. Do not expose tools to rain, and do not use tools in damp or wet locations. Do not use tools on sloped or uneven surfaces. Keep the work area well lit. Allow sufficient space to ­operate tools properly. 3. Prevent back injury. Use proper lifting techniques when handling heavy tool components. 4. Inspect the equipment. Before using any tools, check all moveable parts for any obstructions. Make sure tool components are installed and adjusted properly. www.victaulic.com Victaulic is a registered trademark of Victaulic Company. REV_A TM-VG824/VG828_1 Operating and Maintenance Instructions Manual 5. 6. Prevent accidental startups. Always unplug the Victaulic Power Mule II or power drive from the electrical source. The rotation control switch of the Victaulic Power Mule II DOES NOT feature a “neutral” or “off” position. Depressing the safety foot switch will energize the tool immediately if it is not unplugged. ALWAYS USE THE SAFETY FOOT SWITCH TO OPERATE THE VICTAULIC POWER MULE II OR POWER DRIVE. Wear proper apparel. Do not wear loose clothing, jewelry, or anything that can become entangled in moving parts. 7. Wear protective items when working with tools. Always wear safety glasses, hardhat, foot protection, and hearing protection. 8. Stay alert. Do not operate the tool if you are drowsy from medication or fatigue. Avoid horseplay around the equipment. 9. Keep visitors away from the immediate work area. All visitors should be kept a safe distance from equipment at all times. 10. Keep work areas clean. Keep the work area around the tool clear of any obstructions that could limit the movement of the operator. Clean up any metal shavings and oil or other spills. TM-VG824/VG828 14. Align the Victaulic Power Mule II with the cut-groover’s drive shaft. Always position the Victaulic Power Mule II 90° to the cut groover’s drive shaft. Make sure there is no binding between the drive head of the Victaulic Power Mule II and the drive shaft of the cut groover. 15. Keep hands and tools away from the pipe, cut-grooving tool, Victaulic Power Mule II/ power drive during operation. 16. Do not reach inside the pipe end during tool operation. 17. Do not over-reach. Maintain proper footing and balance at all times. Make sure the safety foot switch is easily accessible for the operator. 18. Do not force the tool. Do not force the tool or accessories to perform any functions beyond their capabilities. Do not overload the tool. 19. Do not abuse the safety foot switch cord. Never yank the cord out of the receptacle. Keep the cord away from heat, oil, and sharp objects. 11. Secure the work, tool, and accessories. 20. Always unplug the Victaulic Power Mule II or power drive from the electrical source before servicing or adjusting the tool. Only authorized personnel should attempt to perform maintenance on the tool. 12. Support the work. Support the pipe in a pipe vise that is mounted to a workbench or a stand. The workbench or stand must be secured to the floor. 21. Maintain tools with care. Keep tools clean at all times to ensure proper and safe performance. Follow all maintenance instructions. 13. OPERATE THE VICTAULIC POWER MULE II ON THE HANDLE SIDE ONLY. The Victaulic Power Mule II must be operated with a safety foot switch that is located for easy operator access. Never reach across moving parts. If the Victaulic Power Mule II or power drive does not contain a safety foot switch, contact Victaulic. 22. Store tools in a dry, secure place when not in use. 23. Use only Victaulic replacement parts and accessories. Use of any other parts may result in a voided warranty, improper operation, and hazardous situations. 24. Do not remove any labels from the tool. Replace any damaged or worn labels. www.victaulic.com Victaulic is a registered trademark of Victaulic Company. TM-VG824/VG828_2 REV_A Operating and Maintenance Instructions Manual INTRODUCTION TM-VG824/VG828 CAUTION NOTICE • Drawings and/or pictures in this manual may be exaggerated for clarity. • The tool, along with this operating and maintenance instructions manual, ­contains trademarks, copyrights, and/or patented features that are the exclusive property of Victaulic. Victaulic VG824 Cut-Grooving Tools are designed for cut grooving 8 – 24-inch IPS carbon steel and AWWA size cast or ductile iron pipe. Wall thickness capacity for the VG824 is 0.238 – 0.750 inch (thicknesses include any linings). Victaulic VG828 Cut-Grooving Tools for specifications Advanced Groove System are designed for cut grooving 14 – 24-inch carbon steel pipe only. The minimum pipe wall thickness requirement for the VG828 is “XS” (Extra Strong, 0.500 inch/12.7 mm). The maximum pipe wall thickness capacity of the VG828 is 0.750 inch/19.1 mm. • VG824 and VG828 tools are designed ONLY for cut ­grooving pipe sizes, materials, and wall thicknesses listed in this manual. Failure to follow this instruction could overload the tool, resulting in reduced tool life and/or damage to the tool. TOOL BIT INFORMATION FOR VG824 TOOLS Standard, high-speed tool bits for VG824 tools are designed with two cutting edges (with the exception of tool bits for 22 – 24-inch sizes) to provide long tool bit life. These tool bits are re-sharpenable. TM During operation, the tool grips the pipe wall between two external support rolls and an internal drive roll. The tool travels around the pipe circumference in a clockwise direction. While being driven in a clockwise direction, the tool pulls itself tightly against the pipe end. The tool bit, which cuts the groove into the pipe, is spring-loaded against the pipe and removes material until the depth stop, mounted directly adjacent to the tool bit, contact the pipe surface. The pipe stop, mounted in the same arm as the tool bit, prevents the tool bit from cutting further into the pipe and ensures uniform groove depth. VG824 tool bits for grooving iron pipe (gray or ductile) are a single-edge, carbide-tipped design This design is not suitable for re-sharpening. Refer to the “VG824 Tool Bit/Pipe Stop Specifications” table for further information. TOOL BIT INFORMATION FOR VG828 TOOLS WARNING • DO NOT attempt to re-sharpen VG828 tool bits for cut grooving to Advanced Groove System (AGS) specifications. • Use of re-sharpened tool bits for cut grooving to AGS specifications may produce improper groove profiles. Failure to follow these instructions may cause improper product installation and product failure, resulting serious personal injury and/or property damage. VG828 tool bits for cut grooving to AGS specifications are high-speed steel and ARE NOT suitable for re-sharpening. Contact Victaulic for replacement tool bits. Refer to the “VG828 Tool Bit/Pipe Stop Specifications” table for further information. www.victaulic.com Victaulic is a registered trademark of Victaulic Company. REV_A TM-VG824/VG828_3 Operating and Maintenance Instructions Manual RECEIVING THE VG824 AND VG828 TOOLS container contents Qty. Permanent Shipping Chest 1 Cut-Grooving Tool (VG824 or VG828) Tool Bit Removal Kit (Includes 3/8 x 7/16-inch Open-End Wrench, 1/4-inch Combination Wrench, and Steel Push Rod) Extra Tool Bit for VG824 Tool (8 – 24-inch Pipe)* Extra Tool Bit for VG828 Tool (14 – 24-inch Pipe Grooved to AGS Specifications)‡ Operating and Maintenance Manual 1 1 2 2 1 1 Upon receipt of the tool, make sure all necessary parts are included. If any parts are missing, contact Victaulic. Description 1 1 VG824 and VG828 tools are packed in wooden chests that are designed for repeated shipping. Save the original chest for return shipment of rental tools. TM-VG824/VG828 Repair Parts List AGS 14-24 Pipe Wall No-Go Gauge (Shipped with the VG828 Tool Only) Victaulic Go/No-Go Pipe Tape * Factory Settings for the VG824 Tool VG824 tool are set at the factory prior to shipment for trial grooving of 10-inch IPS steel pipe, unless specified otherwise on the order. If the VG824 tool is ordered for other types of pipe, sizes, and styles of groove, the tool will be set at the factory, as ordered. NOTE: Additional lead time is required for For grooving to specifications other than those set “as shipped,” follow all sections in this manual to ensure proper tool setup. VG824 tools ordered for cut grooving to other than standard IPS specifications are provided set, as ordered, with the correct tool bit and pipe stops mounted on the tool. In addition, one extra tool bit of the same type is supplied. EXAMPLE: A tool ordered for 10 – 12-inch cast iron rigid grooving would be supplied with one 10 – 12-inch CIR bit mounted in the tool and one extra 10 – 12-inch CIR tool bit supplied loose. A 0.562-inch width groove is required for 22 – 24-inch pipe sizes in order to obtain the maximum allowable pipe end movement. The 0.500-inch groove width will provide half the maximum allowance for 22 – 24-inch pipe sizes. For the 8-inch pipe size, the 0.500 groove width does not change the allowable pipe-end movement. ‡ Factory Settings for the VG828 Tool VG828 Tool are shipped from the factory for grooving 14 – 24-inch pipe to AGS specifications. The VG828 is intended ONLY for cut grooving pipe to AGS specifications. www.victaulic.com Victaulic is a registered trademark of Victaulic Company. TM-VG824/VG828_4 REV_A Operating and Maintenance Instructions Manual ADDITIONAL TOOLS THAT MAY BE REQUIRED FOR TOOL SETUP, adjustment, or operation TM-VG824/VG828 machinist’s end rule The following is a list of items that are not included in the shipment but may be required during tool setup, adjustment, or operation. speed reduction control Slotted screwdriver (thin) Victaulic recommends a speed reduction control unit (115-volt, 15-amp AC) for various universal power drive sources to provide proper grooving tool rotation speed. The speed reduction control plugs in between the electrical supply and the power drive’s electrical plug. NOTE: A speed reduction control is not required when the Victaulic Power Mule II is used as the power drive. DO NOT use a speed reduction control with induction-type motors. 9/16-inch COMBINATION wrench chain-type Pipe vise and vise stand 11/16-inch COMBINATION wrench oiler crescent wrench www.victaulic.com Victaulic is a registered trademark of Victaulic Company. REV_A TM-VG824/VG828_5 TM-VG824/VG828 Operating and Maintenance Instructions Manual POWER REQUIREMENTS FOR THE VICTAULIC POWER MULE II OR POWER DRIVE DANGER • To reduce the risk of electric shock, check the electrical source for proper grounding. • Before performing any maintenance on the Power Mule II or power drive, disconnect the power cord from the electrical source. Failure to follow these instructions could result in death or serious personal injury. The VG824 and VG828 tools are designed for use with the Victaulic Power Mule II and power drives in conjunction with a secure pipe support system. Power, speed, and safety requirements must be verified before attempting to use any power source other than the Victaulic Power Mule II. All power sources must be equipped with a safety foot switch for safe and proper operation. If the power source is shipped without a safety foot switch, contact the manufacturer. The Victaulic Power Mule II is designed to operate on a 115-volt, 20-Amp, 25 – 60 Hz, single-phase power supply. In addition, a 220-volt, 8-Amp model is available. Most other power drives are designed to operate on a 115-volt, 15-Amp, 50/60-Hz power supply or 220-volt, 8-Amp, 50/60-Hz power supply. Victaulic recommends a speed control reducer that is designed to operate on a 115-volt, 15-Amp, 50/60-Hz power supply. NOTE: Speed control reducers work only with AC universal motors that have brushes. DO NOT use speed control reducers with induction-type AC motors. The speed control reducer and the safety foot switch for the Power Mule II or power drive MUST be plugged into an internally-grounded electrical outlet, in accordance with Article 250 of the National Electrical Code. Extension Cord Requirements When pre-wired outlets are not available and an extension cord must be used, it is important to use the proper cord size (i.e. Conductor Size American Wire Gauge). Cord size selection is based upon tool rating (amps) and cord length (feet). Use of a cord size (gauge) thinner than required will cause significant voltage drop while the tool is operating. Voltage drops may cause damage to the power source and can result in improper tool operation. NOTE: It is acceptable to use a cord size (gauge) that is heavier than required. The required cord sizes (gauges) for cord lengths up to and including 100 feet/31 m are listed in the table below. Use of extension cords longer than 100 feet/31 m must be avoided. Always refer to the operating and maintenance instructions for the Victaulic Power Mule II or the applicable power drive for detailed information. Power Source Rating Always refer to the operating and maintenance instructions for the Victaulic Power Mule II or the applicable power drive for detailed information. Cord Lengths 25 feet/ 8 m 50 feet/ 15 m 100 feet/ 31 m Volts Amps 115 15 12 gauge 12 gauge 10 gauge 220 8 14 gauge 14 gauge 12 gauge VG824 and VG828 tools must be driven at 32 revolutions per minute (RPM) or less (under load). If the power source runs too fast, tool bit chatter may occur. Use of a speed reduction controller is recommended to reduce the speed of the power source. www.victaulic.com Victaulic is a registered trademark of Victaulic Company. TM-VG824/VG828_6 REV_A TM-VG824/VG828 Operating and Maintenance Instructions Manual TOOL NOMENCLATURE NOTICE • Drawings and/or pictures in this manual may be exaggerated for clarity. • The tool, along with this operating and maintenance instructions manual, contains ­trademarks, copyrights, and/or patented features that are the exclusive property of Victaulic. Top Pipe Stops Drive Roll Bottom Pipe Stop Bottom Pipe Stop Tool Bit External Support Roll External Support Roll Lubricant Port Tool Bit Set Screw Jam Nut and Tool Bit Set Screw Depth Stop External Support Roll Feed Nut Tool Bit Feed Knob Cutting Side 1 15⁄16-inch Square Drive Top Pipe Stop Bolts Top Pipe Stop Bolts Bottom Pipe Stop Bolts Bottom Pipe Stop Bolts Handle Drive Gear Box Center Adjustable Pipe Stop Tool Bit Feed Knob 1 WARNING tFor cut grooving to Victaulic specifications, the minimum pipe wall thickness requirement is “XS” (Extra Strong, 0.500 inch/12.7 mm). tThe maximum pipe wall thickness capacity of this tool is 0.750 inch/19.1 mm. Failure to follow this instruction could cause joint separation, resulting in serious personal injury and/or property damage. 4889 Rev. A R007828LBL Label shown above applies only to the VG828 Tool for cut grooving to AGS specifications Leaf Spring Adjustment Assembly Drive Side 15⁄16-inch Square Drive Drive Gear Box Center Adjustable Pipe Stop Center Pipe Stop Lock Screw Handle Leaf Spring Tool Bit Removal Access Port Depth Stop Adjustment Access Port Bottom View www.victaulic.com Victaulic is a registered trademark of Victaulic Company. REV_A TM-VG824/VG828_7 Operating and Maintenance Instructions Manual CHAIN-TYPE PIPE VISE SETUP CAUTION • The stand or workbench must be secured to the floor, and the chain-type pipe vise must be secured to the stand or workbench. Failure to follow this instruction could result in personal injury and product damage. 1.The VG824 and VG828 Cut Grooving Tools are designed for field or shop use. Select a location for the grooving operation by taking into consideration the following factors: 1a.The required power supply (refer to the operating instructions for the Victaulic Power Mule II or the applicable power drive) 1b.Adequate space to handle pipe lengths 1c.A firm and level surface for tool operation 1d.Anchoring requirements for the power drive (if applicable) and pipe vise 2.Fasten a stand or workbench securely to the floor. 3.Mount a chain-type pipe vise to the secured stand or workbench. The chain-type pipe vise must be capable of supporting the weight of the pipe and tool (tool weighs approximately 82 – 85 pounds). The chain-type pipe vise should be flush with or slightly overhang the edge of the stand or workbench to permit the tool to rotate freely without being obstructed. TM-VG824/VG828 preparing pipe for grooving For proper tool operation and production of grooves that are within Victaulic specifications, the following pipe preparation steps must be followed. Victaulic recommends square-cut pipe for use with grooved-end pipe products. Square-cut pipe MUST be used with Victaulic FlushSeal® and EndSeal® gaskets. Victaulic VG824 Cut-Grooving Tools are designed for cut grooving 8 – 24-inch IPS and AWWA size case or ductile iron pipe. Wall thickness capacity for the VG824 is 0.238 – 0.750 inch (thicknesses include any linings). For pipe sizes grooved to original specifications with the VG824 tool, raised internal and external weld beads and seams must be ground flush with the pipe surface 31/2 inches/89 mm back from the pipe ends. CAUTION • DO NOT attempt to groove standard-wall or lighter-wall pipe with the VG828 tool for AGS specifications. Failure to follow this instruction will cause the pipe wall to be too thin at the groove, resulting in improper joint performance. Victaulic VG828 Cut-Grooving Tools for specifications are designed for cut grooving 14 – 24-inch carbon steel pipe only. The minimum pipe wall thickness requirement for the VG828 is “XS” (Extra Strong, 0.500 inch/12.7 mm). The maximum pipe wall thickness capacity of the VG828 is 0.750 inch/19.1 mm. For 14 - 24-inch/355.6 - 610.0-mm pipe grooved to AGS specifications with the VG828 tool, raised internal and external weld beads and seams must be ground flush with the pipe surface 4 inches/100 mm back from the pipe ends. TM www.victaulic.com Victaulic is a registered trademark of Victaulic Company. TM-VG824/VG828_8 REV_A Operating and Maintenance Instructions Manual TM-VG824/VG828 MOUNTING PIPE in the chain-type pipe vise 1.Make sure all instructions in the “ChainType Pipe Vise Setup” section have been followed. VG828 tools are shipped with an “AGS 14-24 Pipe Wall No-Go Gauge” that should be used to determine if the pipe wall thickness meets the requirements for cut grooving to AGS specifications. If the pipe wall thickness fits between the two pegs of the gauge, the wall thickness is too thin and the pipe must not be used for cut grooving to AGS specifications. If the pipe wall thickness does not fit between the two pegs of the gauge, the pipe can be used for cut grooving to AGS specifications, up to a maximum wall thickness of 0.750 inch/19.1 mm using the VG828 tool. 6 - 12 inches/ 152 - 305 mm Minimum CAUTION • Foreign material and loose rust must be removed from the interior and exterior surfaces of the pipe ends. Foreign material may interfere with or damage the drive roll, resulting in improper tool operation. All coarse scale, dirt, and other foreign material must be removed from the interior and exterior surfaces of the pipe ends. 2.Position the pipe to overhang the pipe vise approximately 6 – 12 inches/152 – 305 mm so that the tool can groove the pipe without being obstructed by the pipe vise, pipe vise stand, or workbench. pipe length requirements The minimum pipe length that can be grooved with VG824 or VG828 tools is 18 inches/ 457 mm. www.victaulic.com Victaulic is a registered trademark of Victaulic Company. REV_A TM-VG824/VG828_9 Operating and Maintenance Instructions Manual CHECKING AND ADJUSTING THE TOOL PRIOR TO GROOVING TM-VG824/VG828 external support rolls fully by turning the external support roll feed nut (B) counterclockwise. 1.Make sure the proper tool bit is installed for the pipe size and type of grooving required. Refer to the applicable “Tool Bit/Pipe Stop Specifications” table. If the incorrect tool bit is installed, refer to the “Tool Bit Removal” and “Tool Bit Installation” sections. 2.Lift the tool and mount it onto the pipe end. The tool bit feed knob should be facing downward, and the drive roll should be inside the pipe. Use caution to prevent the tool bit from hitting the pipe during mounting. 2.Make sure the proper pipe stops are installed for the pipe size and type of grooving required. Refer to the applicable “Tool Bit/Pipe Stop Specifications” table. If the incorrect pipe stops are installed, refer to the “Pipe Stop Removal and Installation” section. 3. MOUNTING THE VG824 OR VG828 TOOL ONTo THE PIPE Hold the tool firmly against the pipe end, making sure the pipe stops are in complete contact with the pipe end. Tighten the external support roll feed nut by turning clockwise to bring the external support rolls into contact with the outside pipe surface. Load the external support rolls against the pipe by turning the external support roll feed nut with a 15-inch crescent wrench, as shown. Tighten the external support roll feed nut to approximately 75 – 85 ft-lbs. NOTICE B A 1. Before mounting the tool onto the pipe, retract the tool bit feed knob (A) fully by turning counterclockwise. Retract the • DO NOT over-tighten the external support rolls, since damage to the pipe and/ or the tool may result. This is extremely important when the VG824 tool is used on gray cast iron pipe or glass-lined pipe, since these materials are brittle and may crack under too much compression. • If the external support rolls are not tightened sufficiently, the tool may not “track” properly, resulting in improper grooves. www.victaulic.com Victaulic is a registered trademark of Victaulic Company. TM-VG824/VG828_10 REV_A Operating and Maintenance Instructions Manual ATTACHING THE VICTAULIC POWER MULE II TO THE VG824 OR VG828 TOOL TM-VG824/VG828 power head of the Power Mule II onto the square drive of the tool, as shown. Make sure the Power Mule II is positioned 90° to the pipe centerline. Refer to the drawings below. WARNING Centerline of Pipe • Make sure the Power Mule II is disconnected from the electrical source before attempting to attach the VG824 or VG828 tool. Failure to follow this instruction could result in serious personal injury. Workbench or Vise Stand Secured to Floor Victaulic Power Mule II Positioned 90° to Pipe Centerline 6 - 12 inches/ 152 - 305 mm • DO NOT connect the Power Mule II to the electrical source until instructed otherwise. Chain-Type Pipe Vise Secured to Workbench or Vise Stand VG824 or VG828 Safety Foot Switch Workbench or Vise Stand Secured to Floor Victaulic Power Mule II VG824 or VG828 Safety Foot Switch 1.Insert the square drive adapter into the power head of the Victaulic Power Mule II. 2.Align the square drive adapter with the 15/16-inch square drive on the tool. Slide the 3.Tighten the two set screws on the square drive adapter of the Power Mule II. www.victaulic.com Victaulic is a registered trademark of Victaulic Company. REV_A TM-VG824/VG828_11 Operating and Maintenance Instructions Manual Centerline of Pipe and Power Drive TM-VG824/VG828 Power Drive and Power Drive Stand VG824 or VG828 Safety Foot Switch 4.The tool is set up and ready for grooving. Refer to the “Grooving Operation” section. ATTACHING A POWER DRIVE TO THE VG824 OR VG828 TOOL WARNING • Make sure the power drive is disconnected from the electrical source before attempting to attach the VG824 or VG828 tool. • DO NOT connect the power drive to the electrical source until instructed otherwise. Failure to follow this instruction could result in serious personal injury. This procedure applies to a power drive that utilizes a universal drive shaft to attach to the VG824 or VG828 tools. Chain-Type Pipe Vise Typical Power Drive Secured Secured to Workbench to Power Drive Stand or Vise Stand 6 - 12 inches/ Centerline of Pipe 152 - 305 mm and Power Drive Centerline of Pipe Universal and Power Drive Drive Shaft Level Level Workbench or Vise Stand Secured to Floor VG824 or VG828 Safety Foot Switch Power Drive Stand Secured to Floor 1.Mount the power drive securely to a power drive stand. 2.Position the power drive/stand so that the centerline of the power drive chuck aligns with the pipe centerline both horizontally and vertically. Refer to the drawings on this page. The power drive/stand must be located far enough away from the pipe so that the universal drive shaft will fit properly between the power drive/stand and VG824 or VG828. 3.Mount the chuck end of the universal drive shaft into the power drive chuck. Tighten the chuck securely. 4.Collapse the universal drive shaft far enough to fit the square hole end (tool end) of the shaft onto the 15/16-inch square drive of the VG824 or VG828 tool. Slide the end of the universal drive shaft over the 15/16-inch square drive of the VG824 or VG828 tool. Tighten the set screw of the universal drive shaft securely. Make sure the universal drive shaft is not extended further than the power drive manufacturer’s recommendations. Always refer to the power drive manufacturer’s operating and maintenance manual for detailed information and lubrication requirements. 5.Fasten the power drive stand securely to the floor before attempting to perform the grooving operation. 6.The tool is set up and ready for grooving. Refer to the “Grooving Operation” section. www.victaulic.com Victaulic is a registered trademark of Victaulic Company. TM-VG824/VG828_12 REV_A Operating and Maintenance Instructions Manual grooving operation Always refer to the operating and maintenance instructions for the Victaulic Power Mule II or the applicable power drive for detailed operating information. 1.Plug the safety foot switch cord of the Power Mule II or power drive into an internally-grounded electrical outlet. Refer to the “Power Requirements for the Victaulic Power Mule II or Power Drive” section. If an extension cord is used, refer to the “Extension Cord Requirements” section. If a speed control reducer is being utilized, plug the speed control reducer into an internally-grounded electrical outlet, and plug the safety foot switch for the Power Mule II or power drive into the speed control reducer. WARNING • Never attempt to operate the tool in the counterclockwise direction. Failure to follow this instruction may cause the tool to come off the pipe end, resulting in serious personal injury and/or product damage. TM-VG824/VG828 For grooving operations utilizing a power drive: Set the control switch on the power drive to produce CLOCKWISE rotation of the tool when viewed from the 15/16-inch square drive shaft side of the tool (FORWARD setting on most power drives). 2.Check tool rotation by depressing the safety foot switch momentarily. Proper rotation direction of the tool must be CLOCKWISE when viewed from the 15/16-inch square drive shaft side of the tool. 3.If tool rotation direction is clockwise, proceed to step 4. 3a.If tool rotation direction is counterclockwise, flip the control switch on the Power Mule II or power drive to the opposite direction. Re-test tool rotation direction, and make sure the tool rotates CLOCKWISE. If problems persist, contact Victaulic. 4.Depress the safety foot switch to drive the tool in the CLOCKWISE direction for several revolutions. Observe the stability of the tool. The tool should rotate around the pipe smoothly without slipping when approaching the top of the pipe or dropping when approaching the bottom of the pipe. If the tool does not rotate smoothly, remove foot from the safety foot switch, and tighten the external support roll feed nut an additional 1/8 turn. Re-test tool for stability, and tighten the external support roll feed nut in 1/8-turn increments, as needed. NOTICE For grooving operations utilizing a Victaulic Power Mule II: Set the rotation control switch to the FORWARD position. VG824 and VG828 tools are designed to operate in a CLOCKWISE direction when viewed from the 15/16-inch square drive shaft side of the tool. • DO NOT over-tighten the external support rolls, since damage to the pipe and/ or the tool may result. This is extremely important when the VG824 tool is used on gray cast iron pipe or glass-lined pipe, since these materials are brittle and may crack under too much compression. 5.Prepare a trial groove by depressing the safety foot switch to drive the tool in the CLOCKWISE direction. www.victaulic.com Victaulic is a registered trademark of Victaulic Company. REV_A TM-VG824/VG828_13 Operating and Maintenance Instructions Manual TM-VG824/VG828 Proper Spacing 6.As the tool rotates, generously oil the area where the groove will be cut, as shown above. Use a good-grade cutting oil (i.e. Ridgid* dark thread cutting oil or equivalent) on steel pipe only. For aluminum or stainless steel pipe, use a thread cutting oil that is formulated specifically for these materials. DO NOT apply oil on cast iron (gray or ductile) pipe. 7a.The tool bit is advanced properly when the leaf spring is approximately 3/8 inch open from the stop nut on the leaf spring adjustment post. Using the hand knob, continue advancing the tool bit in 1/4-turn increments every three or four rotations of the pipe to maintain the proper spacing, as shown above. CAUTION • An opening MUST be maintained between the stop nut on the leaf spring adjustment post and the leaf spring. If the hand knob is turned enough to eliminate this opening, the tool bit will cut a chip that is too large, which may jam the tool, overload the power drive, and/or shear the serrated drive roll key. 7.Turn the tool bit feed knob gradually in the CLOCKWISE direction to advance the tool bit against the pipe while the tool is rotating. 8.Continue grooving and oiling the pipe until the groove is complete. The groove is complete when the tool bit stops removing material around the entire circumference of the pipe. Indications of a complete groove or a nearly complete groove are: 8a.Oil remaining in the bottom of the groove after the tool bit passes 8b.The Power Mule II or power drive picks up speed 8c.Chips stop falling to the floor * Ridgid is a registered trademark of the Ridge Tool Company. 8d.The groove depth stop lightly contacts the pipe directly behind the groove www.victaulic.com Victaulic is a registered trademark of Victaulic Company. TM-VG824/VG828_14 REV_A Operating and Maintenance Instructions Manual NOTICE • Some portions of the groove will be complete before others. Make sure the entire groove is complete before dismounting the tool. 9.Follow the instructions in the “Preparing to Dismount the VG824 or VG828 Tool” section on this page and the applicable “Dismounting” section on the following page. TM-VG824/VG828 CAUTION • The “C” dimension (groove diameter) must conform to Victaulic specifications to ensure proper joint performance. Failure to follow this instruction could cause joint failure, resulting in personal injury and/ or property damage. 10a.If the groove diameter (“C” dimension) is not within Victaulic specifications, the diameter stop must be adjusted. Refer to the “Groove Diameter Adjustment” section. 11.Prepare another trial groove, and check the groove diameter (“C” dimension), as described in step 10 on this page. Repeat these steps, as necessary, until the groove diameter is within specification. PREPARING TO DISMOUNT the VG824 or VG828 Tool 10.After a trial groove is prepared and the pipe is removed from the tool, check the groove diameter (“C” dimension) carefully with a pipe tape. Refer to the applicable “Cut Groove Specifications” table in this manual. In addition, a vernier caliper or narrow-land micrometer can be used to check the “C” dimension at two locations (90° apart) within the groove. The average reading must be within the required groove diameter specification. 1.Stop the tool at the top side of the pipe with the tool bit feed knob facing upward. 2.Retract the tool bit completely by turning the tool bit feed knob counterclockwise. 3.Drive the tool clockwise. Stop the tool at the bottom of the pipe with the tool bit feed knob facing downward. www.victaulic.com Victaulic is a registered trademark of Victaulic Company. REV_A TM-VG824/VG828_15 Operating and Maintenance Instructions Manual DISMOUNTING THE VG824 OR VG828 TOOL WHEN USED WITH THE Victaulic Power Mule II TM-VG824/VG828 DISMOUNTING THE VG824 OR VG828 TOOL WHEN USED WITH A Power Drive 1.Loosen the universal drive shaft set screw. Slide the tool end of the universal drive shaft off the tool. Move the universal drive shaft out of the way. 1.Loosen the two set screws that are located at the square drive adapter. 2.Flip the rotation control switch on the Victaulic Power Mule II to the opposite position. 3.Momentarily depress the safety foot switch. 2.Loosen the external support roll feed nut so that the external support rolls are not contacting the pipe. 4.Gently pull on the handle of the power head. 3.Slide the tool off the pipe. Set the tool on a workbench or the floor. 5.Disengage the Victaulic Power Mule II from the VG824 or VG828 tool. 4.Using a rag, wipe any oil and chips off the pipe end. 6.Roll the Victaulic Power Mule II to the RIGHT and out of the way. 7.Loosen the external support roll feed nut so that the external support rolls are not contacting the pipe. 8.Slide the tool off the pipe. Set the tool on a workbench or the floor. 9.Using a rag, wipe any oil and chips off the pipe end. www.victaulic.com Victaulic is a registered trademark of Victaulic Company. TM-VG824/VG828_16 REV_A Operating and Maintenance Instructions Manual TM-VG824/VG828 Groove Diameter Adjustment 3.Tighten the groove diameter stop lock nut. 1. With the 7/16-inch open-end wrench (supplied with the tool), loosen the groove diameter stop lock nut, as shown above. 4.If the original groove diameter was oversized, complete the groove and re-check the groove diameter. If the original groove diameter was undersized, prepare another trial groove and check the groove diameter. 5.Repeat the steps in this section until the groove diameter is within specification. 2. With a regular-head screwdriver, adjust the groove diameter stop adjustment screw, as shown above. When viewed from the bottom of the tool, turn the groove diameter stop adjustment screw clockwise to increase the groove diameter (decrease groove depth). Turn the groove diameter stop adjustment screw counterclockwise to decrease the groove diameter (increase groove depth). One full turn of the groove diameter stop adjustment screw changes the groove diameter by 0.040 inch. www.victaulic.com Victaulic is a registered trademark of Victaulic Company. REV_A TM-VG824/VG828_17 Operating and Maintenance Instructions Manual TM-VG824/VG828 TOOL BIT removal A Groove Diameter Stop Adjustment Screw 1.Fully retract the tool bit by turning the tool bit feed knob (A) counterclockwise. Tool Bit Projection Adjustment Screw Jam Nut Tool Bit Projection Adjustment Screw Hole for Tool Bit Push Rod 2. With the 7/16-inch open-end wrench (supplied with the tool), loosen the tool bit set screw jam nut, as shown above. 3. With the 1/4-inch combination wrench (supplied with the tool), loosen the tool bit set screw, as shown above. 4.Insert the 1/8-inch diameter steel push rod (supplied with the tool) through the rear hole in the leaf spring and into the hollow tool bit adjustment screw, as shown above. Use the push rod to push the tool bit out. Refer to the drawing above for tool bit adjustment screw location. www.victaulic.com Victaulic is a registered trademark of Victaulic Company. TM-VG824/VG828_18 REV_A Operating and Maintenance Instructions Manual TM-VG824/VG828 tool bit installation Select the size and type of tool bit required for grooving the pipe. Tool bits are marked with the size and type (Example: 8-24 Std.). Refer to the applicable “Tool Bit/Pipe Stop Specifications” table. Projection for Carbide-Tip Tool Bits ½ inch + 1⁄32 inch/-0 inch (13 mm + 0.8 mm/-0 mm) Projection for Standard Tool Bits 7⁄16 inch ± 1⁄32 inch (11 mm ± 0.8 mm) Tool Bit Cutting Edge 2. Hold the tool bit down against the tool bit adjustment screw. Tighten the tool bit set screw. Projection for AGS Tool Bits 9⁄16 inch ± 1⁄32 inch (14 mm ± 0.8 mm) Tool Bit Cutting Edge 3.Tighten the tool bit set screw jam nut. 4.Check tool bit projection with an end rule between the cutting edge of the tool bit and the tool bit arm. If the projection is out of specification, refer to the “Tool Bit Projection Adjustment” section. 1.Insert the tool bit into the tool bit arm with the cutting edge of the bit toward the external support roll, feed-nut side of the tool. Refer to the drawings above. www.victaulic.com Victaulic is a registered trademark of Victaulic Company. REV_A TM-VG824/VG828_19 Operating and Maintenance Instructions Manual tool bit projection adjustment TM-VG824/VG828 Groove Diameter Stop Adjustment Screw Tool Bit Projection Adjustment Screw Jam Nut Tool Bit Projection Adjustment Screw Hole for Tool Bit Push Rod 1. With the 7/16-inch open-end wrench (supplied with the tool), loosen the tool bit set screw jam nut, as shown above. 3. With a 9/16-inch open-end wrench, loosen the tool bit projection adjustment screw jam nut. Refer to the drawing above. 4.Adjust tool bit projection by turning the tool bit projection adjustment screw with a regular-head screwdriver. Refer to the drawing above NOTE: Half a turn of the tool bit projection adjustment screw will change the projection by 1/32 inch. 4a.Turning the tool bit projection adjustment screw clockwise increases tool bit projection. 2. With the 1/4-inch combination wrench (supplied with the tool), loosen the tool bit set screw, as shown above. 4b.Turning the tool bit projection adjustment screw counterclockwise decreases tool bit projection. NOTE: It may be necessary to push the tool bit down against the tool bit projection adjustment screw when decreasing the projection. 5.Tighten the tool bit projection adjustment screw jam nut. NOTE: Use a screwdriver to prevent the tool bit projection adjustment screw from turning while tightening the tool bit projection adjustment screw jam nut. www.victaulic.com Victaulic is a registered trademark of Victaulic Company. TM-VG824/VG828_20 REV_A Operating and Maintenance Instructions Manual TM-VG824/VG828 Top Pipe Stops Bottom Pipe Stop Top Pipe Stop Bolts 6.Tighten the tool bit set screw. Bottom Pipe Stop Bolts Bottom Pipe Stop Top Pipe Stop Bolts Bottom Pipe Stop Bolts Center Adjustable Pipe Stop VG824 and VG828 tools are designed with five pipe stops. All pipe sizes contact the single, center adjustable pipe stop, which is adjustable for all sizes and styles of grooving. 7.Tighten the tool bit set screw jam nut. pipe stop removal and installation VG824 and VG828 tools are designed to “hug” the pipe end when driven in a clockwise direction. The tool tries to pull itself as far as possible onto the pipe end. The pipe stops limit the distance the tool can pull itself onto the pipe end, therefore controlling the “A” dimension (distance from the groove to the pipe end). The pulling action of the tool forces the pipe stops against the pipe end, resulting in a rubbing action between the pipe end and pipe stops. Eventually, this rubbing action wears down the hardened steel pipe stops, resulting in longer “A” dimensions. When the wear results in “A” dimensions that are not within Victaulic specifications, the pipe stops must be replaced. The two top and two bottom pipe stops are not adjustable, but each of these pipe stops cover many sizes. The top pipe stops contact 8 – 12-inch IPS and 8-inch CI pipe sizes and must be removed for larger CI sizes. IPS pipe in 14-inch and larger sizes clears the top pipe stops, which do not need to be removed. The bottom pipe stops contact 14 – 24-inch IPS pipe and 10-inch and larger CI pipe. When grooving certain sizes of CI pipe, the top and/or bottom pipe stops must be changed or removed. Refer to the applicable “Tool Bit/Pipe Stop Specifications” table. www.victaulic.com Victaulic is a registered trademark of Victaulic Company. REV_A TM-VG824/VG828_21 Operating and Maintenance Instructions Manual TM-VG824/VG828 ADJUSTING THE Center ADJUSTABLE Pipe Stop 1.Loosen the center adjustable pipe stop lock screw, as shown above, and back it out to clear the center adjustable pipe stop (approximately 3/8 inch). 3.Tighten the center adjustable pipe stop lock screw, making sure it engages the hole in the center adjustable pipe stop. When engaged properly, no threads on the center adjustable pipe stop lock screw will be showing. 2.Rotate the center adjustable pipe stop so that the arrow on the center adjustable pipe stop block aligns with the correct markings on the center adjustable pipe stop. Refer to the applicable “Tool Bit/Pipe Stop Specifications” table. Push in or pull out the center adjustable pipe stop so that the flat on the pipe stop is flush with the pipe stop block adjacent to the arrow. www.victaulic.com Victaulic is a registered trademark of Victaulic Company. TM-VG824/VG828_22 REV_A Operating and Maintenance Instructions Manual top and bottom pipe stop removal and installation 1.Remove the two bolts per pipe stop with the 7/16-inch open-end wrench (supplied with the tool), as shown above. 2.Remove the pipe stops. TM-VG824/VG828 drive roll removal and installation The standard drive roll supplied on VG824 tools is designed for use with steel, aluminum, stainless steel, and cast iron pipe (with no linings). When lined pipe is required for grooving, the drive roll must be replaced with a urethane-coated drive roll. THE URETHANE-COATED DRIVE ROLL IS NOT RECOMMENDED WHEN GROOVING CEMENTLINED DUCTILE IRON PIPE. NOTE: If the tool was special ordered for grooving lined pipe, the tool will be shipped with the urethane-coated drive roll mounted on the tool. Longer lead times are required for special-order tools. The VG828 tool is designed for grooving steel pipe to AGS specifications; therefore, the drive roll supplied on the VG828 tool is designed for use with steel pipe (with no linings). DRIVE ROLL REMOVAL Cotter Pin 3.Install the pipe stops with the correct markings for the pipe size and type of grooving required. Refer to the applicable “Tool Bit/Pipe Stop Specifications” table. The pipe stops are marked on the end, as shown above. NOTE: In this photo, the VG828 tool for grooving pipe to AGS specifications is shown, which is installed with pipe stops that are marked“14-24 STD/10-12 CI.” NOTE: Pipe stops are reversible and can be turned over when one side is worn out. The top pipe stops must be switched right-toleft when reversed. The “Tool Bit/Pipe Stop Specifications” tables specify removal of top pipe stops for certain types of grooving. When removed, the pipe stop bolts should be installed loosely into the removed pipe stops to prevent loss. Nut 1.Remove the cotter pin and nut that secure the drive roll to the tool. NOTE: Victaulic recommends replacement of the cotter pin after it is removed. Use the 15/16-inch square drive on the back of the tool to keep the drive roll from turning while loosening the nut. Slide the drive roll off the tool’s shaft. Be careful not to lose the key on the tool’s shaft. drive roll installation 1.Align the keyway of the drive roll with the key on the tool’s shaft. Slide the drive roll onto the tool’s shaft. Install the nut and cotter pin (provided with the new drive roll). www.victaulic.com Victaulic is a registered trademark of Victaulic Company. REV_A TM-VG824/VG828_23 Operating and Maintenance Instructions Manual Always keep the tool free from chips and grindings. External Support Roll Lubricant Port 3.Re-install the tool bit into the tool by referring to the “Tool Bit Installation” section. 4.Adjust tool bit projection by referring to the “Tool Bit Projection Adjustment” section. 0.437 inch/ 11 mm maintenance TM-VG824/VG828 External Support Roll Lubricant Port G 0.156-inch/ 4.0-mm Minimum 8 STD M Regular lubrication of the external support rolls is required. Lubrication fittings are located on the front of the external support roll studs. A #2EP general-purpose, extreme-pressure lithium grease should be pumped into the lubrication fittings approximately once per week. 0.156-inch/ 4.0-mm Minimum G 1.601-inch/ 41-mm Minimum Tool Bit for Standard Grooving of 8-inch/219.1-mm Pipe 0.500 inch/ 13 mm RE-SHARPENING TOOL BITS CAUTION Failure to follow this instruction will create a tool bit that will not produce grooves within Victaulic specifications, resulting in improper joint performance, joint failure, and property damage. ± 30’ 30° Typ. G 0.500 inch/ 13 mm Typ. • DO NOT attempt to re-sharpen tool bits for cast iron pipe and tool bits for AGS specifications. 8-24 STD M ± 30’ 30° Typ. G 1.601-inch/ 41-mm Minimum Tool Bit for Standard Grooving of 8 - 24-inch/219.1 - 610.0-mm Pipe 0.563 inch/ 14 mm Only standard and “ES” tool bits can be re-sharpened. Tool bits for cast iron pipe and tool bits for grooving to AGS specifications MUST NOT be re-sharpened. 1.Remove the tool bit from the tool by following the “Tool Bit Removal” section. 2.Sharpen the edge(s) of the tool bit to the specifications listed in the drawing on this page. Re-grind the “G” surfaces to obtain sharp cutting edges that are free of nicks and discoloration. If the minimum length dimension cannot be maintained, the tool bit must be discarded. DO NOT attempt to use a tool bit that cannot be re-sharpened to the proper dimensions. 0.375-inch/ 10-mm Minimum 22-24 STD M G Standard Grooving Knife for 22 - 24-inch/559.0 - 610.0-mm Pipe www.victaulic.com Victaulic is a registered trademark of Victaulic Company. TM-VG824/VG828_24 REV_A Operating and Maintenance Instructions Manual Parts Ordering Information TM-VG824/VG828 RECOMMENDED Accessories victaulic power mule ii When ordering parts, the following information is required for Victaulic to process the order and send the correct part(s). Request the Repair Parts List for detailed drawings and parts listings. 1.Tool Model Number – VG824 or VG828 2.Tool Serial Number 3. Quantity, Part Number, and Description of Item 4. Where to Send the Part(s) – Company name and address 5.To Whose Attention to Send the Part(s) 6.Purchase Order Number 7. Billing Address The Victaulic Power Mule II is a high-torque power drive for driving Victaulic Cut Grooving Tools. The power mule operates at 13 amps with a no-load operating speed of 32 rpm. Under load, the power mule runs at slower speeds. This is a very desirable feature, since heavier loads and slower speeds greatly reduce tool-bit chatter. www.victaulic.com Victaulic is a registered trademark of Victaulic Company. REV_A TM-VG824/VG828_25 Operating and Maintenance Instructions Manual TM-VG824/VG828 Troubleshooting Problem Tool will not fit onto pipe end. Tool will not rotate. Tool will not cut. Tool chatters during the cutting operation. Possible Cause The external support rolls are not retracted sufficiently. Solution Turn the external roll feed nut fully counterclockwise. The tool bit is not retracted sufficiently. Turn the tool bit feed knob fully counterclockwise. Pipe diameter exceeds the tool’s capacity. Refer to the “Introduction” section. Pipe wall thickness exceeds the tool’s capacity. Refer to the “Introduction” section. The external support rolls are not tightened sufficiently. Refer to the “Mounting the VG824 or VG828 Tool Onto the Pipe” section. Chips are wedged between the external support rolls and the pipe. Loosen the external support rolls and remove any chips. Re-tighten the external support rolls. The power mule or power drive is not connected to the electrical source. Plug the power drive into an internally-grounded electrical source. The power drive switch is in the OFF position. Place the power drive switch in the position to produce clockwise rotation of the tool. Dirt or rust accumulated on the drive roll. Remove dirt, grime, and rust accumulation with a stiff wire brush. The drive roll is worn out. Replace the drive roll. Contact Victaulic for replacement parts. The drive roll key is missing or sheared. Replace the key. Contact Victaulic for replacement parts. The tool is being driven counterclockwise. Reverse the control switch on the power drive, and drive the tool in a clockwise direction. The tool bit is not loaded against the pipe properly. Refer to the “Grooving Operation” section. The tool bit is dull. Replace or re-sharpen the tool bit. Refer to the “Re-Sharpening Tool Bits” section. The tool bit is installed backward. Refer to the “Tool Bit Installation” section. Tool bit projection is not set properly. Refer to the “Tool Bit Projection Adjustment” section. Chips have accumulated between the tool bit arm and pipe. Retract the tool bit and remove any chips. Re-load the tool bit against the pipe while the tool is rotating. The tool bit is not loaded properly against the pipe. Refer to the “Grooving Operation” section. The power drive is running at a speed that exceeds the tool’s capacity. Refer to the “Power Requirements for the Victaulic Power Mule II or Power Drive” section. Not enough cutting oil is being used during the cutting operation. Refer to the “Grooving Operation” section. Tool bit projection is not set properly. Refer to the “Tool Bit Projection Adjustment” section. Pipe has a hard spot or hard weld seam. Increase the tool bit load slightly and oil the groove generously. The tool bit is starting to dull. Replace or re-sharpen the tool bit. Refer to the “Re-Sharpening Tool Bits” section. www.victaulic.com Victaulic is a registered trademark of Victaulic Company. TM-VG824/VG828_26 REV_A Operating and Maintenance Instructions Manual TM-VG824/VG828 Troubleshooting (CONTINUED) Problem Tool will not “hug” pipe end. Possible Cause The tool is being driven counterclockwise. Solution Reverse the control switch on the power drive, and drive the tool in a clockwise direction. The power mule is not positioned 90° to the pipe. Refer to the “Attaching the Victaulic Power Mule II to the VG824 or VG828 Tool” section. The power drive is not aligned with the pipe centerline. Refer to the “Attaching a Power Drive to the VG824 or VG828 Tool” section. The pipe is not square cut. Cut the pipe end square. Refer to the “Preparing Pipe for Grooving” section. Tool cannot be dismounted from the pipe. The external support rolls are not retracted. Turn the external support roll feed nut fully counterclockwise. The tool bit is not retracted. Turn the tool bit feed knob fully counterclockwise. Groove diameter “C” dimension is incorrect. The groove diameter is out of adjustment. Refer to the “Groove Diameter Adjustment” section. Tool bit projection is out of adjustment. Refer to the “Tool Bit Projection Adjustment” section. The pipe outside diameter varies widely from piece to piece. The groove diameter adjustment must be made for each piece to ensure correct groove diameter “C” dimensions. Chips have built up between the tool bit arm and the pipe. Retract the tool bit arm and remove any chips. Re-load the tool bit against the pipe while the tool is rotating. The tool bit has been re-sharpened beyond the specified tool bit length. Replace the tool bit. Contact Victaulic for replacement parts. The depth stop has worn to a point where it can’t be adjusted. Replace the worn depth stop. Contact Victaulic for replacement parts. The incorrect tool bit and/or pipe stops are installed in the tool. Refer to the applicable “Tool Bit/Pipe Stop Specifications” table. The pipe stops are worn. Replace the pipe stops. Contact Victaulic for replacement parts. The pipe is not square cut. Cut the pipe end square. Refer to the “Preparing Pipe for Grooving” section. The power mule is not positioned 90° to the pipe. Refer to the “Attaching the Victaulic Power Mule II to the VG824 or VG828 Tool” section. The power drive is not aligned with the pipe centerline. Refer to the “Attaching a Power Drive to the VG824 or VG828 Tool” section. The incorrect tool bit is installed in the tool. Refer to the applicable “Tool Bit/Pipe Stop Specifications” table. The power mule is not positioned 90° to the pipe. Refer to the “Attaching the Victaulic Power Mule II to the VG824 or VG828 Tool” section. The power drive is not aligned with the pipe centerline. Refer to the “Attaching a Power Drive to the VG824 or VG828 Tool” section. Gasket seat “A” dimension is incorrect. Groove width “B” dimension is incorrect. www.victaulic.com Victaulic is a registered trademark of Victaulic Company. REV_A TM-VG824/VG828_27 TM-VG824/VG828 Operating and Maintenance Instructions Manual EXPLANATION OF CRITICAL CUT GROOVE DIMENSIONS WARNING • Pipe dimensions and groove dimensions must be within the tolerances specified in the tables on the following pages to ensure proper joint performance. Failure to follow these specifications could result in serious personal injury, property damage, joint leakage, and/or joint failure. B OD A B B R T C OD A B A T C B OD C D Standard Cut Groove Radius Cut Groove AGS Cut Groove Illustrations are Exaggerated for Clarity Pipe Outside Diameter – Nominal NPS Pipe Size (ANSI B36.10) and Basic Metric Pipe Size (ISO 4200) – The average pipe outside diameter must not vary from the specifications listed in the tables on the following pages. Maximum allowable pipe ovality should not vary by more than 1%. Greater variations between the major and minor diameters will result in difficult coupling assembly. For IPS pipe, the maximum allowable tolerance from square-cut pipe ends is 0.060-inch/1.5-mm for 8-inch/200-mm and larger sizes. This is measured from the true square line. Any internal and external weld beads or seams must be ground flush to the pipe surface. The inside diameter of the pipe end must be cleaned to remove coarse scale, dirt, and other foreign material that might interfere with or damage the drive roll. For pipe being grooved to Advanced Groove System (AGS) specifications, the outside diameter must not vary from the specifications listed in this manual (API 5L end tolerance). The maximum allowable tolerance from square-cut ends is 0.063 inch/1.5 mm. This is measured from the true square line. “A” Dimension – The “A” dimension, or the distance from the pipe end to the groove, identifies the gasket seating area. This area must be free from indentations, projections (including weld seams), deep pits, swells, and roll marks from the pipe end to the groove to ensure a leak-tight seal. All foreign material, such as loose paint, scale, oil, grease, chips, rust, and dirt must be removed. For cast pipe, peened surfaces may require corrective action to ensure a leak-tight seal. “B” Dimension – The “B” dimension, or groove width, controls expansion, contraction, and angular deflection of flexible couplings by the distance it is located from the pipe and its width in relation to the coupling housings’ “key” width. The bottom of the groove must be free of all foreign material, such as dirt, chips, rust, and scale that may interfere with proper coupling assembly. For pipe being grooved to AGS specifications, the corners at the bottom of the groove must be radiused. The Groove Width “B” dimension will be achieved with properly maintained Victaulic VG828 tools that are equipped with a Victaulic-supplied AGS tool bit. www.victaulic.com Victaulic is a registered trademark of Victaulic Company. TM-VG824/VG828_28 REV_A TM-VG824/VG828 Operating and Maintenance Instructions Manual “C” Dimension – The “C” dimension is the proper diameter at the base of the groove. This dimension must be within the diameter’s tolerance and concentric with the OD for proper coupling fit. The groove must be of uniform depth for the entire pipe circumference. For pipe being grooved to AGS specifications, the VG828 tool must be equipped with a Victaulic-supplied AGS tool bit. “D” Dimension – The “D” dimension is the normal depth of the groove and is a reference for a “trial groove” only. Variations in pipe OD affect this dimension and must be altered, if necessary, to keep the “C” dimension within tolerance. This groove must conform to the “C” dimension described above. “T” Dimension – The “T” dimension is the lightest grade (minimum, nominal wall thickness) of pipe that is suitable for cut grooving. Pipe that is less than the minimum, nominal wall thickness for cut grooving may be roll grooved. For AWWA pipe, the tolerances must conform to Class 53 ANSI/AWWA C151/A21.51. For pipe being grooved to AGS specifications, the absolute minimum wall thickness is 0.500 inch/12.7 mm. The maximum allowable wall thickness is 0.750 inch/19.1 mm. “R” Dimension – The “R” dimension is the radius necessary at the bottom of the groove to eliminate a point of stress concentration for cast pipe (gray and ductile) and PVC plastic pipe. rigid and flexible radius cut grooves Rigid Radius Cut Groove Exaggerated for Clarity Flexible Radius Cut Groove Victaulic groove specifications for cast pipe (gray and ductile) conform to the requirements of ANSI/ AWWA Standard C-606 and CSA B242. For cast pipe, the groove is cut with a radius (“R” dimension) at the corners of the groove base to reduce stress concentration. Grooving dimensions are the same for any pipe OD, regardless of pipe class and pressure. Standard preparation is with a rigid radius cut groove. Flexible radius cut groove dimensions may be used to provide expansion/contraction or angular movement allowance at the joint. www.victaulic.com Victaulic is a registered trademark of Victaulic Company. REV_A TM-VG824/VG828_29 TM-VG824/VG828_30 8.578 217.9 8.688 220.7 10.063 255.6 10.591 269.0 10.813 274.7 12.063 306.4 12.602 320.1 8.515 216.3 8.625 219.1 10.000 254.0 10.528 267.4 10.750 273.0 12.000 304.8 12.539 318.5 12.750 323.9 216.3 mm 8 200 10 OD 267.4 mm 10 250 304.8 mm 318.5 mm 12 300 12.813 325.5 8.063 204.8 8.000 203.2 Max. 12.719 323.1 12.508 317.7 11.969 304.0 10.719 272.3 10.497 266.6 9.969 253.2 8.594 218.3 8.484 215.5 7.969 202.4 Min. Pipe Outside Diameter 8 OD Nom. Size Act. OD inches/mm inches/mm Size Basic 0.750 19.1 0.750 19.1 0.750 19.1 0.750 19.1 0.750 19.1 0.750 19.1 0.750 19.1 0.750 19.1 0.750 19.1 0.781 19.8 0.781 19.8 0.781 19.8 0.781 19.8 0.781 19.8 0.781 19.8 0.781 19.8 0.781 19.8 0.781 19.8 Max. Gasket Seat “A” Min. 0.719 18.3 0.719 18.3 0.719 18.3 0.719 18.3 0.719 18.3 0.719 18.3 0.719 18.3 0.719 18.3 0.719 18.3 Basic 0.500 12.7 0.500 12.7 0.500 12.7 0.500 12.7 0.500 12.7 0.500 12.7 0.438 11.1 0.438 11.1 0.438 11.1 0.531 13.5 0.531 13.5 0.531 13.5 0.531 13.5 0.531 13.5 0.531 13.5 0.469 11.9 0.469 11.9 0.469 11.9 Max. Groove Width “B” Dimensions – inches/millimeters Min. 0.469 11.9 0.469 11..9 0.469 11.9 0.469 11.9 0.469 11.9 0.469 11.9 0.407 10.3 0.407 10.3 0.407 10.3 12.531 318.3 12.321 313.0 11.781 299.2 10.562 268.3 10.340 262.6 9.812 249.2 8.441 214.4 8.331 211.6 7.816 198.5 Max. 12.501 317.5 12.291 312.2 11.751 298.5 10.535 267.6 10.313 262.0 9.785 248.5 8.416 213.8 8.306 211.0 7.791 197.9 Min. Groove Diameter “C” Standard Cut Groove Specifications for Steel and Other NPS Pipe Grooved with the VG824 Tool † OD B 0.109 2.8 0.109 2.8 0.109 2.8 0.094 2.4 0.094 2.4 0.094 2.4 0.092 2.4 0.092 2.4 0.092 2.4 Groove Depth “D” (ref.) A C B 0.279 7.1 0.279 7.1 0.279 7.1 0.250 6.4 0.250 6.4 0.250 6.4 0.238 6.1 0.238 6.1 0.238 6.1 Min. Allow. Wall Thick. “T” D T Operating and Maintenance Instructions Manual TM-VG824/VG828 www.victaulic.com Victaulic is a registered trademark of Victaulic Company. REV_A REV_A 14.063 357.2 14.937 379.4 15.063 382.6 16.063 408.0 16.866 428.4 18.063 458.8 20.063 509.6 22.063 560.4 24.063 611.2 14.000 355.6 14.843 377.0 15.000 381.0 16.000 406.4 16.772 426.0 18.000 457.0 20.000 508.0 22.000 559.0 24.000 610.0 377.0 mm 15 OD 16 OD 426.0 mm 18 OD 20 OD 22 OD 24 OD Max. 23.969 608.8 21.969 558.0 19.969 507.2 17.969 456.4 16.740 425.2 15.969 405.6 14.969 380.2 14.811 376.2 13.969 354.8 Min. Pipe Outside Diameter 14 OD Nom. Size Act. OD inches/mm inches/mm Size Basic 1.000 25.4 1.000 25.4 1.000 25.4 1.000 25.4 0.938 23.8 0.938 23.8 0.938 23.8 0.938 23.8 0.938 23.8 1.031 26.2 1.031 26.2 1.031 26.2 1.031 26.2 0.969 24.6 0.969 24.6 0.969 24.6 0.969 24.6 0.969 24.6 Max. Gasket Seat “A” Min. 0.969 24.6 0.969 24.6 0.969 24.6 0.969 24.6 0.907 23.0 0.907 23.0 0.907 23.0 0.907 23.0 0.907 23.0 Basic 0.563 14.3 0.563 14.3 0.500 12.7 0.500 12.7 0.500 12.7 0.500 12.7 0.500 12.7 0.500 12.7 0.500 12.7 0.594 15.1 0.594 15.1 0.531 13.5 0.531 13.5 0.531 13.5 0.531 13.5 0.531 13.5 0.531 13.5 0.531 13.5 Max. Groove Width “B” Dimensions – inches/millimeters Min. 0.532 13.5 0.532 13.5 0.469 11.9 0.469 11.9 0.469 11.9 0.469 11.9 0.469 11.9 0.469 11.9 0.469 11.9 23.656 600.9 21.656 550.1 19.781 502.4 17.781 451.6 16.514 419.5 15.781 400.8 14.781 375.4 14.611 371.1 13.781 350.0 Max. 23.626 600.1 21.626 549.3 19.751 501.7 17.751 450.9 16.479 418.6 15.751 400.1 14.751 374.7 14.581 370.4 13.751 349.3 Min. Groove Diameter “C” Standard Cut Groove Specifications for Steel and Other NPS Pipe Grooved with the VG824 Tool † OD B 0.172 4.4 0.172 4.4 0.109 2.8 0.109 2.8 0.129 3.3 0.109 2.8 0.109 2.8 0.116 2.9 0.109 2.8 Groove Depth “D” (ref.) A C B 0.375 9.5 0.375 9.5 0.312 7.9 0.312 7.9 0.335 8.5 0.312 7.9 0.312 7.9 0.315 8.0 0.281 7.1 Min. Allow. Wall Thick. “T” D T Operating and Maintenance Instructions Manual TM-VG824/VG828 www.victaulic.com Victaulic is a registered trademark of Victaulic Company. TM-VG824/VG828_31 TM-VG824/VG828_32 Actual Outside Dia. Inches/mm 9.050 229.9 11.100 281.9 13.200 335.3 15.300 388.6 17.400 442.0 19.500 495.3 21.600 548.6 25.800 655.3 Nom. Dia. Inches/mm 8 200 10 250 12 300 14 350 16 400 18 450 20 500 24 600 9.110 231.4 11.160 283.5 13.260 336.8 15.350 389.9 17.450 443.2 19.550 496.6 21.650 549.9 25.850 656.6 Max. 8.990 228.3 11.040 280.4 13.140 333.8 15.220 386.6 17.320 439.9 19.420 493.3 21.520 546.6 25.720 653.3 Min. Pipe Outside Diameter 0.950 24.1 1.015 25.8 1.015 25.8 1.015 25.8 1.340 34.0 1.340 34.0 1.340 34.0 1.340 34.0 Max. 0.930 23.6 0.995 25.3 0.995 25.3 0.995 25.3 1.320 33.5 1.320 33.5 1.320 33.5 1.320 33.5 Min. Gasket Seat “A” 0.500 12.7 0.500 12.7 0.500 12.7 0.625 15.9 0.625 15.9 0.625 15.9 0.625 15.9 0.625 15.9 Basic 0.531 13.5 0.531 13.5 0.531 13.5 0.656 16.7 0.656 16.7 0.656 16.7 0.656 16.7 0.656 16.7 Max. Groove Width “B” 0.484 12.3 0.484 12.3 0.484 12.3 0.609 15.5 0.609 15.5 0.609 15.5 0.609 15.5 0.609 15.5 Min. Dimensions – Inches/mm 8.781 223.0 10.813 274.7 12.906 327.8 14.969 380.2 17.063 433.4 19.125 485.8 21.219 539.0 25.406 645.3 Max. 8.756 222.4 10.788 274.0 12.876 327.1 14.939 379.5 17.033 432.6 19.095 485.0 21.189 538.2 25.376 644.6 Min. Groove Diameter “C” Rigid Radius-Cut Groove Specifications FOR Ductile Iron Pipe GROOVED WITH THE VG824 TOOL 0.145 3.7 0.145 3.7 0.145 3.7 0.165 4.2 0.165 4.2 0.185 4.7 0.185 4.7 0.185 4.7 Radius “R” OD B R C B T 0.410 10.4 0.440 11.2 0.480 12.2 0.550 14.0 0.580 14.7 0.630 16.0 0.670 17.0 0.730 18.5 Cast Iron 0.360 9.1 0.380 9.7 0.400 10.2 0.420 10.7 0.430 10.9 0.440 11.2 0.450 11.4 0.470 11.9 Ductile Iron Minimum Allowable Wall Thickness “T” A Operating and Maintenance Instructions Manual TM-VG824/VG828 www.victaulic.com Victaulic is a registered trademark of Victaulic Company. REV_A REV_A Actual Outside Dia. Inches/mm 9.050 229.9 11.100 281.9 13.200 335.3 15.300 388.6 17.400 442.0 19.500 495.3 21.600 548.6 25.800 655.3 Nom. Dia. Inches/ mm 8 200 10 250 12 300 14 350 16 400 18 450 20 500 24 600 9.110 231.4 11.160 283.5 13.260 336.8 15.350 389.9 17.450 443.2 19.550 496.6 21.650 549.9 25.850 656.6 Max. 8.990 228.3 11.040 280.4 13.140 333.8 15.220 386.6 17.320 439.9 19.420 493.3 21.520 546.6 25.720 653.3 Min. Pipe Outside Diameter 0.875 22.2 0.938 23.8 0.938 23.8 0.938 23.8 1.188 30.2 1.188 30.2 1.188 30.2 1.188 30.2 Max 0.855 21.7 0.918 23.3 0.918 23.3 0.918 23.3 1.168 29.7 1.168 29.7 1.168 29.7 1.168 29.7 Min Gasket Seat “A” 0.500 12.7 0.500 12.7 0.500 12.7 0.625 15.9 0.625 15.9 0.625 15.9 0.625 15.9 0.625 15.9 Basic 0.531 13.5 0.531 13.5 0.531 13.5 0.656 16.7 0.656 16.7 0.656 16.7 0.656 16.7 0.656 16.7 Max Groove Width “B” 0.484 12.3 0.484 12.3 0.484 12.3 0.609 15.5 0.609 15.5 0.609 15.5 0.609 15.5 0.609 15.5 Min 8.781 223.0 10.813 274.7 12.906 327.8 14.969 380.2 17.063 433.4 19.125 485.8 21.219 539.0 25.406 645.3 Max 8.756 222.4 10.788 274.0 12.876 327.1 14.939 379.5 17.033 432.6 19.095 485.0 21.189 538.2 25.376 644.6 Min Groove Diameter “C” Dimensions – Inches/millimeters 0.145 3.7 0.145 3.7 0.145 3.7 0.165 4.2 0.165 4.2 0.185 4.7 0.185 4.7 0.185 4.7 Radius “R” Flexible Radius-Cut Groove Specifications FOR Ductile Iron Pipe GROOVED WITH THE VG824 TOOL OD B R C B T 0.410 10.4 0.440 11.2 0.480 12.2 0.550 14.0 0.580 14.7 0.630 16.0 0.670 17.0 0.730 18.5 Cast Iron 0.360 9.1 0.380 9.7 0.400 10.2 0.420 10.7 0.430 10.9 0.440 11.2 0.450 11.4 0.470 11.9 Ductile Iron Minimum Allowable Wall Thickness “T” A Operating and Maintenance Instructions Manual TM-VG824/VG828 www.victaulic.com Victaulic is a registered trademark of Victaulic Company. TM-VG824/VG828_33 TM-VG824/VG828_34 8 200 10 250 12 300 8.625 219.1 10.750 273.0 12.750 323.9 Actual Out. Dia. Nom. Size inches/mm inches/mm Size 8.688 220.7 10.813 274.7 12.813 325.5 Max. 8.594 218.3 10.719 272.3 12.719 323.1 Min. Pipe Outside Diameter 0.714 18.1 0.714 18.1 0.714 18.1 Basic 0.729 18.5 0.729 18.5 0.729 18.5 Max. Gasket Seat “A” Min. 0.699 17.8 0.699 17.8 0.699 17.8 Basic 0.400 10.2 0.400 10.2 0.400 10.2 0.410 10.4 0.410 10.4 0.410 10.4 Max. Groove Width “B” Dimensions – inches/millimeters Min. 0.390 9.9 0.390 9.9 0.390 9.9 8.441 214.4 10.562 268.3 12.531 318.3 Max. 8.416 213.8 10.535 267.6 12.501 317.5 Min. Groove Diameter “C” Cut Groove Specifications for Standard or Heavier-Wall Pipe or Plastic-Coated Pipe Grooved with the VG824 Tool and Joined with Style HP-70ES EndSeal Couplings OD B 0.092 2.3 0.094 2.4 0.109 2.8 Groove Depth “D” (ref.) A C B 0.322 8.2 0.365 9.3 0.375 9.5 Min. Allow. Wall Thick. “T” D T Operating and Maintenance Instructions Manual TM-VG824/VG828 www.victaulic.com Victaulic is a registered trademark of Victaulic Company. REV_A REV_A 16.063 408.0 18.063 458.8 20.063 509.6 24.063 611.2 16.000 406.4 18.000 457.0 20.000 508.0 24.000 610.0 16 18 20 24 23.969 608.8 19.969 507.2 17.969 456.4 15.969 405.6 13.969 354.8 1.500 38.1 1.500 38.1 1.500 38.1 1.500 38.1 1.500 38.1 Basic 1.531 38.9 1.531 338.9 1.531 38.9 1.531 38.9 1.531 38.9 Gasket Seat “A” Max. 1.437 36.5 1.437 36.5 1.437 36.5 1.437 36.5 1.437 36.5 Min. 0.455 11.6 0.455 11.6 0.455 11.6 0.455 11.6 0.455 11.6 Basic 0.460 11.7 0.460 11.7 0.460 11.7 0.460 11.7 0.460 11.7 Groove Width “B”‡ Max. Dimensions – inches/millimeters C 0.450 11.4 0.450 11.4 0.450 11.4 0.450 11.4 0.450 11.4 Min. B 23.485 596.5 19.485 494.9 17.485 444.1 15.485 393.3 13.485 342.5 23.455 595.8 19.455 494.2 17.455 443.4 15.455 392.6 13.455 341.8 Groove Diameter “C” Max. Min. ‡ The Groove Width “B” dimension is listed for information only. The Groove Width “B” dimension will be achieved with a properly maintained Victaulic VG828 tool that is equipped with a Victaulic-supplied AGS tool bit. 14.063 357.2 14.000 355.6 Outside Diameter “OD” Max. Min. 14 Nominal Size inches Actual Outside Diameter inches/mm Pipe Size OD A advanced groove system (AGS) CUT grooving specifications for carbon steel pipe grooved with the VG828 tool Operating and Maintenance Instructions Manual TM-VG824/VG828 www.victaulic.com Victaulic is a registered trademark of Victaulic Company. TM-VG824/VG828_35 Operating and Maintenance Instructions Manual TM-VG824/VG828 VG824 tool bit/pipe stop specifications Pipe Size Nominal Diameter inches/mm Actual Outside Diameter inches/ mm Groove Dimensions inches/millimeters “A” Pipe Stops Used (Marked As Shown) Tool Bits Width inches/ mm “B” Central (Adj.) Rect. (Top) Rect. (Bottom) 0.438 11.1 8.625 OD 12.750 OD 8-12 14-24 0.438 11.1 0.500 ‡ 8.625 OD 12.7 12.750 OD 8-12 14-24 0.500 12.7 8-24 STD R-K08-824-024 14-24 OD 10-12 CI 8-12 14-24 0.500 12.7 8-24 STD R-K08-824-024 0.562 ‡ 14-24 OD 14.3 10-12 CI 8-12 14-24 0.562 14.3 22-24 STD R-K22-824-024 Marking Part Number 8 STD R-K08-824-008 steel – standard groove 8 200 8.625 219.1 0.750 19.1 8 – 12 200 – 300 8.625 – 12.750 219.1 – 323.9 0.750 19.1 14 – 24 OD 14.000 – 24.000 355.6 – 610.0 0.968 24.6 22 – 24 OD 22.000 – 24.000 559.0 – 610.0 0.968 24.6 0.500 12.7 ‡ A 0.562-inch width groove is required for 22 – 24-inch pipe sizes in order to obtain the maximum allowable pipe end movement. The 0.500-inch groove width will provide half the maximum allowance for 22 – 24-inch pipe sizes. For the 8-inch pipe size, the 0.500 groove width does not change the allowable pipe-end movement. steel – “ES” GROOVE 8 – 12 200 – 300 8.625 – 12.750 219.1 – 323.9 0.714 18.1 0.400 10.2 8.625 OD 12.750 OD 8-12 14-24 0.400 10.2 8-12 ES R-K08-824-212 8 CI 14-24 0.500 12.7 8 CIR R-K08-824-G08 CAST IRON – RIGID GROOVE (STANDARD) 8 200 9.050 229.9 0.950 24.1 0.500 * 12.7 * 10 – 12 250 – 300 11.100 – 13.200 281.9 – 335.3 1.015 25.8 0.500 * 14-24 OD REMOVE 12.7 * 10-12 CI 14-24 0.500 12.7 14 350 15.300 388.6 1.015 25.8 0.625 * 15.9 * 14 CI 0.625 15.9 16 – 24 400 – 600 17.400 – 25.800 442.0 – 655.3 1.340 34.0 0.625 * 15.9 * 8 CI 14 CI REMOVE 16-24 CI REMOVE 16-24 CI 0.625 15.9 10-12 CIR R-K10-824-G12 14 CIR R-K14-824-G14 14-24 CIR R-K16-824-G24 * Measurement of groove width at top of groove only – bottom of groove is radiused CAST IRON – flexible GROOVE 8 200 9.050 229.9 0.8750 22.2 0.500 * 12.7 * 14-24 0.500 12.7 10 – 12 250 – 300 11.100 – 13.200 281.9 – 335.3 0.9375 23.8 8 CIF R-K08-824-E12 0.500 * 14-24 OD REMOVE 12.7 * 10-12 CI 14-24 0.500 12.7 8-12 CIF R-K08-824-E12 14 350 15.300 388.6 0.9375 23.8 0.625 * 15.9 * 14 CI 0.625 15.9 16 – 24 400 – 600 17.400 – 25.800 442.0 – 655.3 14-24 CIF R-K14-824-E24 1.1875 30.2 0.625 * 15.9 * 0.625 15.9 14-24 CIF R-K14-824-E24 8 CI 14 CI 8 CI REMOVE 16-24 CI REMOVE 16-24 CI * Measurement of groove width at top of groove only – bottom of groove is radiused www.victaulic.com Victaulic is a registered trademark of Victaulic Company. TM-VG824/VG828_36 REV_A Operating and Maintenance Instructions Manual TM-VG824/VG828 VG828 tool bit/pipe stop specifications Pipe Size Nominal Diameter inches/mm Actual Outside Diameter inches/ mm Groove Dimensions inches/millimeters “A” “B” Pipe Stops Used (Marked As Shown) Central (Adj.) Rect. (Top) Rect. (Bottom) N/A 14-24 Tool Bits Width inches/ mm Marking Part Number steel – AGS groove 14 – 24 OD 14.000 – 24.000 355.6 – 610.0 1.500 38.1 0.450 # 14-24 OD 11.4 10-12 CI 0.450 § 14-24 AGS R-K14-828-W24 11.4 # Measurement of groove width at bottom of groove only § Width of tool bit at the tip www.victaulic.com Victaulic is a registered trademark of Victaulic Company. REV_A TM-VG824/VG828_37 Operating and Maintenance Instructions Manual TM-VG824/VG828 VG824 and VG828 cut-grooving tools For complete contact information, visit www.victaulic.com TM-VG824/VG828 5218 REV A UPDATED 04/2008 RM00824828 VICTAULIC IS A REGISTERED TRADEMARK OF VICTAULIC COMPANY. © 2008 VICTAULIC COMPANY. ALL RIGHTS RESERVED. PRINTED IN THE USA. WCAS-7E8MHM
advertisement
* Your assessment is very important for improving the workof artificial intelligence, which forms the content of this project
Related manuals
advertisement