- Home
- Domestic appliances
- Climate control
- Temperature & humidity sensors
- Spirax Sarco
- elm
- User manual
advertisement
▼
Scroll to page 2
of
80
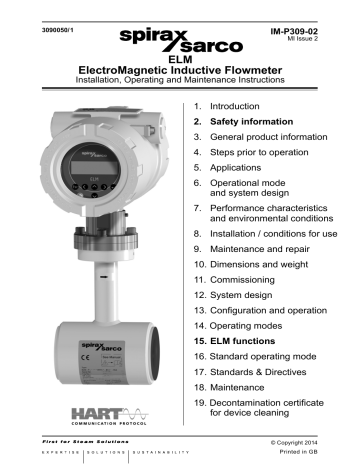
IM-P309-02 3090050/1 MI Issue 2 ELM ElectroMagnetic Inductive Flowmeter Installation, Operating and Maintenance Instructions 1.Introduction 2. Safety information 3. General product information 4. Steps prior to operation 5.Applications 6. Operational mode and system design 7. Performance characteristics and environmental conditions 8. Installation / conditions for use 9. Maintenance and repair 10.Dimensions and weight 11.Commissioning 12.System design 13.Configuration and operation 14. Operating modes 15.ELM functions 16. Standard operating mode 17.Standards & Directives 18.Maintenance 19. Decontamination certificate for device cleaning IM-P309-02 MI Issue 2 © Copyright 2014 1 Printed in GB 2 IM-P309-02 MI Issue 2 1. Introduction This installation and operating manual explains how to operate, install and perform maintenance on the flowmeter. Please read the manual carefully before installing the device and putting it into operation. The manual does not apply to non-standard versions or applications. All devices are thoroughly tested and checked for order compliance prior to shipping. Upon receipt of the device, check it for shipping damage. If any problem comes to light, contact your local Spirax Sarco representative. Please describe the problem and indicate type and serial number of the device. We extend no guarantee of any kind for repair work that is undertaken without notifying us in advance of the intention to carry out such work. Unless otherwise agreed, any part or component for which a claim is lodged is to be sent to us for examination. 2. Safety information Safe operation of this unit can only be guaranteed if it is properly installed, commissioned and maintained by a qualified person (see Section 1.11) in compliance with the operating instructions. General installation and safety instructions for pipeline and plant construction, as well as the proper use of tools and safety equipment must also be complied with. Supplier: Spirax-Sarco Limited Charlton House Charlton Kings Cheltenham Glos GL53 8ER The product is designed and constructed to withstand the forces encountered during normal use. Use of the product for any other purpose, or failure to install the product in accordance with these Installation and Maintenance Instructions, could cause damage to the product, will invalidate the marking, and may cause injury or fatality to personnel. The following conditions should be avoided as they may create interference above the heavy industrial limits if: - The product or its wiring is located near a radio transmitter. - Cellular telephones and mobile radios may cause interference if used within approximately 1 metre (39") of the product or its wiring. The actual separation distance necessary will vary according to the surroundings of the installation and the power of the transmitter. If this product is not used in the manner specified by this IMI, then the protection provided may be impaired. IM-P309-02 MI Issue 2 3 Installation, commissioning, operating personnel Mechanical and electrical installation, as well as commissioning, maintenance and operation, are to be realized solely by qualified personnel that are authorized by the installation operator to perform such work. All such personnel must read and understand the content of the applicable operating instructions before working with the device. In general, follow the conditions and provisions applicable in your country. The present document contains the information that you need in order to operate the product described herein properly. The document is intended for use by qualified personnel. This means personnel who are qualified to operate the device described herein safely, including electronics engineers, electrical engineers, or service technicians who are conversant with the safety regulations pertaining to the use of electrical and automated technical devices and with the applicable laws and regulations in their own country. Such personnel must be authorized by the facility operator to install, commission and service the product described herein, and are to read and understand the contents of the present operating instructions before working with the device. 2.1 Hazard warnings The purpose of the hazard warnings listed below is to ensure that device operators and maintenance personnel are not injured and that the flowmeter and any devices connected to it are not damaged. The safety advisories and hazard warnings in the present document that aim to avoid placing operators and maintenance personnel at risk and to avoid material damage are prioritized using the terms listed below, which are defined as follows in regard to these instructions herein and the advisories pertaining to the device itself. 2.2Danger means that failure to take the prescribed precautions will result in death, severe bodily injury, or substantial material damage. 2.3Warning means that failure to take the prescribed precautions could result in death, severe bodily injury, or substantial material damage. 2.4Caution means that the accompanying text contains important information about the product, handling the product or about a section of the documentation that is of particular importance. Note means that the accompanying text contains important information about the product, handling the product or about a section of the documentation that is of particular importance. 4 IM-P309-02 MI Issue 2 2.5 Proper use of the device Warning The operator is responsible for ensuring that the material used in the sensor and housing is suitable and that such material meets the requirements for the fluid being used and the ambient site conditions. The manufacturer accepts no responsibility in regard to such material and housing. Warning In order for the device to perform correctly and safely, it must be shipped, stored, set up, mounted, operated and maintained properly. 2.6 Returning your flowmeter for servicing or calibration Before sending your flowmeter back to us for servicing or calibration, make sure it is completely clean. Any residues of substances that could be hazardous to the environment or human health are to be removed from all crevices, recesses, gaskets, and cavities of the housing before the device is shipped. Warning The operator is liable for any loss or damage of any kind, including personal injury, decontamination measures, removal operations and the like that are attributable to inadequate cleaning of the device. Any device sent in for servicing is to be accompanied by a certificate as specified in Section 18! The device is to be accompanied by a document describing the problem with the device. Please include in this document the name of a contact person that our technical service department can get in touch with so that we can repair your device as expeditiously as possible and therefore minimize the cost of repairing it. 2.7 Replacement of the transmitter electronics Before replacing the transmitter electronics, read the safety instructions in Section 10 Installation and servicing. Warning Make sure that you abide by the applicable standards and regulations pertaining to electrical devices, device installation and process technology when replacing the transmitter electronics. The highly integrated electronic components in the device carry the risk of ESD hazards and are only protected when installed in the device pursuant to EMC standards. The exchange of electronic components or board is described in details in Section 9 Maintenance and repair. IM-P309-02 MI Issue 2 5 Caution The complete insert is to be replaced with all of its printed boards (except for the memory chip (DSM)). This is particularly important for the explosion-proof transmitter. The specified precision and interchangeability of the electronics are only guaranteed if the complete insert is replaced. 2.8 Intended purpose The electromagnetic flowmeter is to be used solely for measuring the volume flow of liquids, suspensions and pastes with conductivity ≥ 5 µS/cm (≥ 20 µS/cm demineralized cold water). The manufacturer accepts no responsibility for any damage or loss resulting from any other use or from improper use. Before using corrosive or abrasive fluids, the operator must test the resistance of all wetted materials. We will be happy to assist you in testing the corrosion resistance of wetted parts (for special fluids including cleaning fluids). However, sole responsibility for ensuring that the device is used in accordance with the manufacturer’s recommendations rests with the system operator. Minor changes of temperature, concentration or the degree of contamination in the process may cause changes in corrosion resistance. The manufacturer accepts no responsibility for any damage with respect to corrosion resistance of wetted materials in a certain application. Intended use Referring to the Installation and Maintenance Instructions, name-plate and Technical Information Sheet, check that the product is suitable for the intended use / application. The product listed complies with the requirements of the European Pressure Equipment Directive 97 / 23 / EC, carries the mark when so required. The product falls within the following Pressure Equipment Directive categories: Group 1 Gases Group 2 Gases Group 1 Liquids Group 2 Liquids ELM DN50 - - 2 - ELM DN150 – DN200 - - 2 - Product i) The ELM flow meter range has been designed for use on water / condensate which are in Group 2 liquids of the above mentioned Pressure Equipment Directive. The product’s use on other liquids in Group 1 or Group 2 may be possible but, if this is contemplated, Spirax Sarco should be contacted to confirm the suitability of the product for the application being considered. ii) Check material suitability, pressure and temperature and their maximum and minimum values. If the maximum operating limits of the product are lower than those of the system in which it is being fitted, or if malfunction of the product could result in a dangerous overpressure or overtemperature occurrence, ensure a safety device is included in the system to prevent such over-limit situations. iii) Determine the correct installation situation and direction of fluid flow. iv) This product is not intended to withstand external stresses that may be induced by any system to which they are fitted. It is the responsibility of the installer to consider these stresses and take adequate precautions to minimise them. v) Remove all protective covers from all connections and protective packaging where appropriate, before installation on high temperature applications. 6 IM-P309-02 MI Issue 2 2.9 Packaging, storaging, transport Be careful not to damage the device while unpacking it. The device should be stored in a clean, dry room until it is installed so as to prevent particulate matter from entering the device. Make certain that the ambient temperature in the room in which the device is stored lies within the prescribed range. Check to ensure that the technical product data indicated on the delivery note is consistent with the stipulated requirements. If, after the device is unpacked, it is sent elsewhere to be installed, the original packaging and transport protection inserts should be used. 2.10Returning the device for repair and servicing Note: According to German waste disposal legislation, it is the owner’s or customer’s responsibility to dispose of hazardous waste. Thus, any devices sent to us for servicing, including their crevices and cavities, must be devoid of any such material. When sending a device for repair, please confirm your compliance with this regulation in writing. In the event any hazardous material is detected on or inside any device sent to us for servicing, we reserve the right to bill the customer for the cost of disposing of such material (see Section 19 "Decontamination certificate"). IM-P309-02 MI Issue 2 7 3. General product information 3.1Manufacturer Manufactured for Spirax Sarco by Heinrichs Messtechnik GmbH Robert-Perthel-Str. 9 · D-50739 Köln Telephone: +49 221 49708 – 0, Fax: +49 221 49708 - 178 Internet: http://www.heinrichs.eu, Email: mailto:[email protected] 3.2 Product type Magnetic-inductive flowmeter based on Faraday’s law of induction 3.3 Product name ELM 3.4 Designation/rating plate Fig. 1 Transmitter Label The rating plate states the following information: Logo Supplier’s logo CE CE Marking in accordance with the applied EC Directives Type Type designation Ser. No. Serial number (for tracking reasons) Tag No. Operator’s measuring point number (if stated in the order) MF-Date Year of manufacture DN Flange designation PN Pressure stage of flange Materials Material of wetted parts such as pipe lining, material of electrodes and seal Tm Medium temperature range T amb Ambient temperature range C Sensor constant Fig. 2 Main Label Degrees Degrees of protection in of accordance with DIN EN protection 60529:2000 8 IM-P309-02 MI Issue 2 4. Steps prior to operation It is essential that you read these operating instructions before installing and operating the device. The device is to be installed and serviced by a qualified technician only. No instructions, wiring diagrams, and/or supplied software, or any portion thereof, may be produced, stored, in a retrieval system or transmitted by any means, electronic, mechanical, photocopying or otherwise, without prior written permission. Although the materials in the present document were prepared with extreme care, errors cannot be ruled out. Hence, neither the company, nor the programmer nor the author can be held legally or otherwise responsible for any erroneous information and/or any loss or damage arising from the use of the information enclo No express or implied warranty is extended in regard to the applicability of the present document for any purpose other than that described. We plan to optimize and improve the products described and in so doing will incorporate not only our own ideas but also, and in particular, any suggestions for improvement made by our customers. We reserve the right to change the technical data in this manual in the light of any technical progress that might be made. 5. Applications The electromagnetic flowmeter is used to measure or monitor the volume flow of fluids with and without solids concentration, slurries, pastes and other electrically conductive media while minimizing pressure drops. The conductivity of the medium must be at least 5 µS/cm. Pressure, temperature, density and viscosity do not affect the volume measurements. Small quantities of solid particles and small gas pockets are also measured as part of the volume flow. A larger number of solid particles or gas pockets will result in failures and/or inaccuracy of measurement. IM-P309-02 MI Issue 2 9 6. Operational mode and system design 6.1 Operational mode In 1832 Faraday suggested utilizing the principle of electrodynamic induction for measuring flow velocities. His experiments in the Thames, though unsuccessful due to superimposed polarization effects, are nonetheless regarded as the first in the field of magnetic-inductive flow measurement. According to Faraday's law of electromagnetic induction, an electrical field E is produced in a conductive liquid moving through a magnetic field B at a velocity v in accordance with the vector product E = [v x B]. A fluid with a flow velocity v and a flow rate Q flowing through a tube (1) with an insulating lining (2) produces a measuring-circuit voltage Um at the two electrodes (4) at right angles to the direction of flow and the magnetic field B generated by the field coils (3). The strength of this measuring-circuit voltage is proportional to the mean flow velocity and therefore the volume flow rate. 6.2 System design The electromagnetic ELM-*** flowmeter consists of a sensor, which picks up an induced measuring signal from the medium flowing through the pipe, and a transmitter which transforms this signal into standardized output signals (4-20 mA or pulses). The sensor is installed in the pipe while the transmitter is mounted directly on the sensor. 3 B UM 1 2 D V 4 UM Q B Fig. 3 10 IM-P309-02 MI Issue 2 7. Performance characteristics and environmental conditions 7.1 Measuring accuracy 7.1.1 Measured error +/- [0.3% of actual value + 0.0001 * (Q at 10 m/s)] Accuracy Flow velocity v [m/s] Fig. 4 7.1.2 Repeatability +/- [0.15% of actual value + 0.00005 * (Q at 10 m/s)] 7.1.3 Reference conditions In accordance with DIN EN 29104 Fluid temperature 22°C ± 4 K Ambient temperature 22°C ± 2 K Inlet section of ≥ 10 x DN and outlet section of ≥ 5 x DN 7.2 Fluid conductivity ≥ 5 µS/cm (≥ 20 µS/cm for demineralized water) 7.3 Influence of ambient temperature -20°C to +60°C 7.4 Ambient temperature - 20° Celsius to + 60°Celsius (-4°F to 140°F), below 0degC the readability of the LC display will be limited IM-P309-02 MI Issue 2 11 7.5 Ambient temperature range -20°Celsius to + 60°Celsius (-4°F to 140°F) In the case of an outdoor installation, the device must be protected against direct solar irradiation with a weather shield. 7.6 Storage temperature - 25°Celsius to + 60°Celsius (-13°F to 140°F) 7.7 Degree of protection SG2b standard housing, IP68 (NEMA 6P). Caution: Ingress protection IP 68 is only achieved if suitable and tightly screwed down cable glands or conduits are used. If the cable glands are only tightened manually water may leak into the terminal compartment in the housing. Danger: Particular care must be taken if the window in the housing becomes fogged over or discolored because moisture, water or product might seep through the wire sheath into the terminal compartment in the housing! Warning: Electromagnetic compatibility is only achieved if the electronics housing is closed. Leaving the enclosure open can lead to electromagnetic disturbances. 12 IM-P309-02 MI Issue 2 7.8 Process conditions 7.8.1 Fluid temperature The data sheet/rating plate of the connected transmitter must be observed. With directly mounted transmitter on the sensor the heat entry must be considered from the process to the transmitter. 7.8.2 State of aggregation Liquid 7.8.3 Viscosity No restrictions. The data sheet/rating plate of the connected transmitter must be observed. 7.8.4 Fluid temperature limit The data sheet/rating plate of the connected transmitter must be observed. medium and the cleanliness of the electrodes. 7.8.5 Flow rate limit The data sheet/rating plate of the connected transmitter must be observed. 7.8.6 Pressure loss The data sheet/rating plate of the connected transmitter must be observed. 7.8.7 Empty pipe detection Transmitters, which are equipped with a control unit BE3, have an on and off switch able empty pipe detection. The operating reliability depends on the conductivity of the liquid medium and the cleanliness of the electrodes. 7.9 Materials 7.9.1 Wetted parts Parts Standard Lining PTFE Measuring and grounding electrodes St. st. 1.4571, Hastelloy C4 7.9.2 Non-wetted parts Parts Standard Flow tube Stainless steel 1.4571 Housing St. st. 1.4571, Hastelloy C4 DN 10 – 300 Varnished steel Flange Varnished steel Terminal box for remote mount transmitter Aluminum pressure casting, varnished IM-P309-02 MI Issue 2 13 8. Installation/conditions for use 8.1 Receipt of goods and transport 8.1.1 Receipt of goods Check the packaging and contents for damage. Inspect the supplied goods to ensure complete delivery and compare the consignment with your order specifications. 8.1.2 Transport The protection caps should only be removed immediately before installation of the device in the pipe. Never lift the devices by the mounted transmitter housing or terminal box for transport. When transporting heavy devices, use slings. Place these around both process connections. Do not use chains as these can damage the surface coating and the housing. When transporting devices without lugs, and when looping the slings around the flow tube, the center of gravity of the entire device can be higher than both attachment points of the slings. When transporting the device ensure that it does not rotate or slip accidentally. This could cause injury. Sensors with a nominal width of more than DN 150 should not be lifted by the sheet metal of the shell with a forklift truck. This could dent the sheet metal of the shell and damage the internal solenoid coils. There is also the risk that the device could roll off the forks. Fig. 5 14 IM-P309-02 MI Issue 2 8.2 Installation conditions The installation location in the pipe must be selected so that the sensor is always fully filled with the fluid and cannot run empty. This can best be guaranteed if it is installed in an ascending pipe or drain. The measuring principle is generally independent of the flow profile of the fluid provided no standing vortices reach into the area where the value is measured, such as downstream from elbows or half-open sliding valves upstream from the sensor. In these cases measures must be taken to normalize the flow profile. Practical experience ¬has shown that in most cases a straight inlet section of ≥ 5 x DN and an outlet section of ≥ 2 x DN of the rated width of the sensor is sufficient. The occurrence of strong electromagnetic fields in the vicinity of the installed sensor is not permitted. In order to be able to perform flow and return measurements, both sides of the sensor must be provided with a straight pipe section with the rated width of the sensor and a length of 5 DN of the rated width of the sensor. It is advisable to install actuators, such as regulating or shut-off devices, downstream from the sensor. The flow direction is marked on the sensor with an arrow. When mounting sensors, always observe the specified screw torques. The electrical system can be taken into operation when the sensor and the cables have been installed and connected. In order to prevent measuring errors caused by gas pockets in the fluid and damage lining of the sensor caused by negative pressure, the following points must be observed. 8.2.1 Long pipe systems As pressure surges may occur in long pipes systems, the regulating and shut-off devices must be installed downstream from the sensor. When mounted in vertical pipes - in particular in flow tubes with PTFE lining and in case of higher operating temperatures - the regulating and shut-off devices must be installed upstream from the sensor. (Danger of vacuum might be involved!) 8.2.2 Pumps Do not mount the sensor on the suction side of a pump. (Danger of vacuum!) 8.2.3 Bypass In order to easily dismount, empty and clean the sensor, a bypass pipe may be installed. The bypass with a blind flange permits the fluid pipe to be cleaned without having to dismount the flowmeter. This is recommended for highly soiling fluids. 8.2.4 Flow tube lining As the flow tube is lined with PTFE, the flowmeter must be installed with special care. The tube lining is bordered at the flanges (seal). This must not be damaged or removed as it prevents the fluid from penetrating between flange and flow tube destroying the electrode insulation. IM-P309-02 MI Issue 2 15 8.3 Installation Screws, bolts, nuts and seals are not supplied and must therefore be provided by the operator. Install the sensor between the pipes. Please observe the required torques stated Section 8.3.4. The installation of additional grounding rings is described in Section 8.3.3. Use for the flanges only seals in accordance with DIN 2690. Mounted seals must not reach into the pipe cross section. Caution! Do not use conductive sealing compounds such as graphite. This could result in a conductive layer on the inside of the flow tube that shortcircuits the measuring signal. 8.3.1 Installation in pipes with larger nominal sizes The flowmeter can also be installed in pipes with larger nominal sizes by using pipe tapers (e.g. flange transition pieces in accordance with DIN EN 545). However, the resulting pressure loss must be taken into consideration. In order to avoid flow interruptions in the flow tube, a reducing angle ≤ 8° for the tapers should be adhered to. 8.3.2 Horizontal and vertical installation The flowmeter can be installed wherever required, whereby the intended x-y electrode axis should run almost horizontal. A vertical Electrode axis should be avoided as otherwise the accuracy could be affected by the gas pockets or the solid particles in the fluid. Incorrect installation for horizontal pipe system Correct installation system X Y X Y Fig. 6 16 IM-P309-02 MI Issue 2 Installation examples In order to avoid measuring errors caused by gas pockets and lining damage caused by negative pressure, the following points must be observed: Horizontal lining Installation in a slightly ascending pipe. Highest point in pipe system. Air bubbles will accumulate in the tube. Incorrect measurement! Fig. 8 Fig. 7 Preferred assembly locations Free inlet or outlet section Preferably install the device in a drain. The empty pipe detection circuit in the transmitter is an additional safety feature for recognizing empty or partially filled pipes. Fig. 9 Caution! There is the danger of accumulations of solids in the drain. It is advisable to arrange for a cleaning aperture in the pipe. Fall pipe over five meters long In case of fall pipes that are more than five meters long, arrange for a syphon or a venting valve in order to avoid a negative pressure in the pipe and damage to the lining. In addition, this measure prevents the flow from stopping so that air pockets can be avoided. > 5m Fig. 10 IM-P309-02 MI Issue 2 17 Long pipes Always install regulating and shut-off devices downstream from the sensor. (Danger of vacuum!) Fig. 11 Installation of pumps Do not install flowmeters on the suction side of pumps in order to avoid a negative pressure and damage to the tube lining. Fig. 12 If necessary, arrange for pulsation dampeners when using piston, diaphragm or hose pumps. Please consider space requirements with respect to a potential uninstallation of the device. 8.3.3 Grounding For safety reasons and to ensure faultless operation of the electromagnetic flowmeter, the sensor must be grounded. In accordance with VDE 0100 Part 410 and VDE 0100 Part 540 the grounding connections must be at protective conductor potential. For metrological reasons, the potential should be identical to the potential of the fluid. The grounding cable should not transmit any interference voltage. For this reason do not ground other electrical devices with this cable at the same time. The measuring signal tapped at the electrodes is only a few millivolts. Correct grounding of the electromagnetic flowmeter is therefore an important prerequisite for exact measurement. The transmitter requires a reference potential to evaluate the measured voltage on the electrodes. In the simplest case the non-insulated metal pipe and/or the connecting flange may be used as a reference potential. In case of pipes with an electrically insulating lining or pipes made of plastic, the reference potential is picked up from a grounding electrode. This establishes the necessary conductive connection to the fluid and is made of a chemical-resistant material. The grounding cables are not included in the scope of supply and must be provided by the plant operator. 18 IM-P309-02 MI Issue 2 8.3.3.1 Grounding the ELM flowmeter Ground Wire: Min 4mm2 Cu Earth bonding - Uninsulated metal pipes only (not required for plastic pipe installations) Protective Earth Seal Pipe Seal ELM Pipe Pipe Flanges Fig. 13 IM-P309-02 MI Issue 2 19 8.3.4 Torques for studs and nuts Electromagnetic flowmeters must be installed in the pipe system with special care due to the fact that the flow pipe lining is made of PTFE which is malleable under pressure. If the flange nuts are tightened too much, the sealing surface will deform. If the seals are supposed to function properly, the correct torque is highly important. Tighten the nuts crosswise, so that the process connections are tight. When tightening the nuts for the first time, approximately 50% of the required torque should be reached, and for the second time, the torque should be 80%. The required torque should reach 100% when the nuts are tightened for the third time. For higher torques it is advisable to use protectors. The following tables state the maximum torques: 20 Nominal size (mm) DIN Pressure rating (bar) Studs Maximum torques (Nm) DN25 PN40 4 x M12 25 DN32-40 PN40 4 x M16 45 DN50 PN40 4 x M16 65 DN65 PN16 4 x M16 85 DN80 PN16 8 x M16 55 DN100 PN16 8 x M16 55 DN150 PN16 8 x M20 100 DN200 PN16 12 x M20 95 Nominal size (inch) ASME Pressure rating (lbs) Studs Maximum torques (Nm) 1" Class 300 4 x ⅝" 15 1 ¼"-1 ½" Class 300 4 x ¾" 35 2" Class 300 8 x ⅝" 25 2 ½" Class 150 4 x ⅝" 85 3" Class 150 4 x ⅝" 80 4" Class 150 8 x ⅝" 55 6" Class 150 8 x ¾" 105 8" Class 150 8 x ¾" 145 IM-P309-02 MI Issue 2 8.4 Wiring Caution! Installation and wiring may only be performed when the auxiliary power is switched off. Non-compliance can result in electric shock and irreparable damage to electronic parts. 8.5 Nominal size and ranges Volume flow depends on the flow velocity and the nominal size of the flowmeter. The electromagnetic flowmeter has been designed in such a way that it operates within the range of the flow velocities occurring in practical applications. The flow velocities have an upper range value of between 0.5 m/s and 10 m/s. The nominal size DN of the sensor must be selected, if possible, in such a way that the flow velocity does not drop below the upper range value of 0.5 m/s. In case of fluids with solid particles, the flow velocity should range between 3 m/s and 5 m/s in order to prevent sedimentation in the sensor. Size Litres / sec. m3/h Qmin Qmax Qmin Qmax DN25 (1") 0.24 4.89 0.88 17.6 DN32 (1¼") 0.40 8.03 1.45 28.9 DN40 (1½") 0.54 10.75 1.94 38.7 DN50 (2") 0.87 17.33 3.12 62.4 DN65 (2½") 1.56 31.11 5.61 112 DN80 (3") 2.27 45.28 8.17 163 DN100 (4") 4 80 14.42 288 DN150 (6") 9 186 33.96 671 DN200 (8") 17 330 59.99 1188 IM-P309-02 MI Issue 2 21 8.6 Ambient conditions Ambient temperature range For fluid temperatures > 60°C As the sensors are an element of the pipe, these are normally thermally isolated when installed to save energy and prevent accidental physical contact. Due to the process temperature heat is introduced through the support for securing the integral mount transmitter or the terminal box. For this reason the thermal insulation of the sensor should not extend over more than half of the support. It is essential to prevent inclusion of the installed transmitter or the terminal box in the thermal insulation. The maximum permissible fluid temperature range is stated on the rating plate of the respective version. 8.6.1 Maximum ambient temperature depending on the fluid temperature Max. ambient temperature (°C) 70 65 60 55 50 45 40 35 30 25 20 60 70 80 90 100 110 120 Max. fluid temperature (°C) 130 140 150 Fig. 14 8.6.2 Storage temperature range The storage temperature range is identical to the ambient temperature range. 8.6.3 Climatic category In accordance with DIN EN 60654-1; not weather-protected Class D1 locations exposed directly to open-air climate. 22 IM-P309-02 MI Issue 2 8.6.4 Ingress protection The sensor meets the requirements of the protection class IP 67. The following must be observed to ensure compliance with protection class IP 67 when the device has been installed or serviced: - The housing seals must be clean and undamaged when placed in the sealing groove. If necessary the seals must be cleaned or replaced. Tighten the screw cap of the transmitter. The cables used for connection must comply with the specified outer diameter for the cable glands used. Tighten the cable glands firmly. Loop the cable in front of the cable gland. Any moisture running along the cable can then drip off and not penetrate the device. Always install the device so that the cable gland does not face upwards. Any unused cable glands must be closed with a plug which is suitable for the respective protection class. Fig. 15 8.6.5 Shock resistance/vibration resistance The flowmeter should be protected from extreme shocks and vibrations, which could cause damage. Maximum permissible shock/vibration: 15 m/s2 (10 to150 Hz). IM-P309-02 MI Issue 2 23 8.7 Process pressure The maximum permissible process pressure PS is stated on the rating plate and depends on the fluid temperature. PN40 bar PN25 PN16 PN10 PN6 °C Fig. 16 8.8 Fluid temperature The maximum permissible fluid temperature of the device depends on the version and the lining material of the flow tube and is stated on the rating plate. The German Industrial Safety Act stipulates that very cold or hot components of working equipment must be provided with guards which prevent physical contact of workers with the respective parts. For this reason and also to save energy, in practical applications at temperatures of > 60°C, all pipes and installed measuring instruments are normally thermally insulated. Refer to Section 8.6 for information on the relation between the fluid temperature and the ambient temperature limits. The temperature ranges for use of the device are listed below for the lining materials Lining material Fluid temperature ranges PTFE - 20°C to 150°C 24 IM-P309-02 MI Issue 2 8.9 Electrical connection Mains: 24 Vdc Power input: 10 VA Fuse: 5x20mm DIN 41571-3 Voltage = 24 Vdc Current = 1 AT Rated voltage = 250 Vac Breaking capacity = 80A / 250Vac e. g. Fa. Wickmann series 201 ±15% 8.10 Process terminals Terminals located at the rear side of the transmitter’s housing. Fig. 17 IM-P309-02 MI Issue 2 25 8.11 Output Signal 8.11.1 Isolation All signal outputs are electronically isolated from each other and ground (PE) 8.11.2 Analog output A single 0/4-20mA current output is fitted with optional HART communications and can be configured to output flow rate in volumetric or velocity units. 8.11.3 Pulse output A single pulse output is fitted. Passive via optocoupler: U = 24 V Umax = 30 V Imax = 60 mA Pmax = 1.8 W Pulse duration: 50ms (default value) Pulse duration adjustable from: 0.1 to 2000ms Mark-to-space ratio: 1 to 1 if the maximum pulse duration is not met When adjusting the pulse duration, a check is carried out to ensure the pulse duration does not exceed the upper limit. If the upper limit is exceeded an error message will be displayed. Frequency: fmax = 1 kHz Pulse value: 1 pulse/unit. The pulse value can be multiplied by a factor between 0.001 and 100.0 in decade increments of the selected units e.g. m3 Status output: for forward and reverse flow, MIN and MAX flow rate or alarm 8.11.4 Failure signal A failure in the meter can be indicated via the current output or the status output. The current output can be set to alarm of I < 3.8mA of I > 22mA. The status output can be configure as a make or break output. 8.11.5 Current output load Standard version: 600 Ohms HART version: minimum load > 250 Ohms 8.11.6 Damping Programmable: from 0 to 60 seconds 8.11.7 Low flow cut-off Configurable: from 0 to 20% of maximum flow. If the measured value is lower than the low flow cut-off set value the flow rate will show zero and the analogue output will switch to 0/4 mA and the pulse output will stop generating pulses. The configurable hysteresis only takes effect on one side of this limit. 26 IM-P309-02 MI Issue 2 8.12 Mains and signal terminals +Loop -Loop +Status -Status +Pulse -Pulse ELM mains and signal terminals Fuse Fig. 18 Process terminals Terminal Label 1 PE 2 N Polarity Function Protective conductor Mains 3 L 4 Pulse - Pulse output (passive) 5 Pulse + Pulse output (passive) 6 Status - Status output (passive) 7 Status + Status output (passive) 8 Current Out. - Current output (active) 9 Current Out. + Current output (active) IM-P309-02 MI Issue 2 Mains 27 8.13 HART® connection A number of options are available for HART® communication. However, for all these options loop resistance must be less than the maximum load specified in Section Error! Reference source not found. Error! Reference source not found. (Error! Bookmark not defined. ). The HART® -Interface is connected via terminals 8 and 9 of the active current output. The minimum load impedance must be 250 Ω. 8.14 Wiring diagram for the separate version For cable specification see section 8.16. The outer shield has to be connected to the metalized cable glands at both ends. The inner shields are connected to each other and are plugged into the terminal labeled "Schirm / shield". They are related to the potential of the function earth FE. (See also section 11.2 Potentials.) E2 E1 FE SP+ FE SP- Transmitter Note: terminal diagram Schematic representation of a wiring between flow sensor and remote mounted transmitter. Terminal diagram is always shown is the documentation of flow sensor. Caution: E2 E1 FE SP+ FE SP- Do not connect or disconnect the field coil cable before the primary power of the meter has been disconnected! Sensor Fig. 19 28 IM-P309-02 MI Issue 2 8.15 ELM sensor terminals Terminal 1 2 3 4 5 6 Label FE SP SP + FE E1 E2 Sensor terminals Polarity + Function Screen field coil Field coil Field coil Shield / Functional ground Elektrod 1 Elektrod 2 1 2 3 4 5 6 FE SP- SP+ FE E1 E2 Observe also the advice in chapter 7 Environmental conditions. Fig. 20 8.16 Cable specification If the transmitter is mounted separately from the sensor, the following cables must be used: Electrode cable and field coil cable as shielded twisted pair. In order to protect the cable from external interference, the twisted-pair wires are covered by an additional, overall shield e.g. LIYCY-CY TP 2 x 2 x 0.25 mm². At cable length more than 10m a wire cross section of at least 0.75 mm² is required e.g. SLIYCY-C11Y ( 2 x ( 2 x 0.75 mm²)). The outer shield is grounded by means of special EMC-compliant cable glands at both ends of the cable. IM-P309-02 MI Issue 2 29 9. Maintenance and repair The transmitter ELM is designed as maintenance-free performance. It contains no parts, which have to be replaced or adjusted cyclically. While commissioning or maintenance, mains power must be switched off. Do not connect or disconnect the wirings between sensor and transmitter while power is on! 9.1 Mains fuse The mains fuse is located in the terminal compartment. Before exchanging the fuse, the power has to be switched off. Check, if voltage free. The fuse may only be exchanged by the exactly same kind of fuse! (See also section 8.9 Electrical connection.) 9.2 Replacement of terminal board The terminal board is located in the terminal compartment. Before exchanging the board, the power has to be switched off. Check, if voltage free. The board may only be exchanged by the exactly same kind of board. To exchange the terminal board, all pluggable connectors have to be released. The board is fixed by 4 screws. To exchange the board, these screws have to be loosened. Installing the board, the screws have to be secured again by toothed washers. Only after all connectors are plugged in, the power can be switched on again. 9.3 Exchange of transmitter electronic The transmitter electronic may be exchanged only as complete module. With the exchange of individual components the transmitter is afterwards no longer calibrated neither regarding its measuring characteristics nor its analog outputs. The exchange has to be done as described in the following: - Mains power off. Unclamp the 6 pole tab connector in the terminal compartment. Remove the control unit BE2 or decoration foil inside the electronic compartment. Unplug the green connector on the power supply board. Disconnect the sensor’s wires on the power supply board. Screw out all 3 studs consistently and simultaneously. Pull out carefully the electronic boards. The data memory chip (DSM) has to be plug out of the socket and to be placed into the same socket of the new electronic stack. Insert the new electronics and feed the tab connection again into the terminal compartment through the hole in the compartment partitions wall. Reverse to item 1 to 6 of this list assemble the transmitter. Before powering on, check all connectors to be plugged in correctly and all wires and devices are fixed. After the exchange the transmitter is calibrated by the take-over of the data memory chip (DSM) for the sensor. All totalized counts and settings are taken on. 30 IM-P309-02 MI Issue 2 10. Dimensions and weight 10.1 Dimension drawing of meter assemblies 205 115 108 Ø110 B M20 X 1.5 cable entry point (2) ØC D ØA ØA DN25 (1") PN40 ASME Class 300 PN16 ASME Class 150 DN32 (1¼") B 284 ØC D Weight (kg) (approximate values) 72 82 4.4 DN40 (1½") 290 92 DN50 (2") 295.5 107 DN65 (2½") 307 127 DN80 (3") 313 138 DN100 (4") 323 162 DN150 (6") 351 218 134 10.4 DN200 (8") 379 274 219 12.4 IM-P309-02 MI Issue 2 104 5.4 5.4 6.4 31 10.2 Installation and servicing The devices described in this manual are to be installed and serviced only by qualified technical personnel. Warning Before servicing the device, it must be completely switched off, and disconnected from all peripheral devices. The technician must also check to ensure that the device is completely off-circuit. Only original replacement parts are to be used. Spirax Sarco accepts no liability for any loss or damage of any kind arising from improper operation of any product, improper handling or use of any replacement part, or from external electrical or mechanical effects, overvoltage or lightning. Any such improper operation, use or handling shall automatically invalidate the warranty for the product concerned. Contact our customer service department if your device needs repair or if you need assistance in diagnosing a problem with your device 11. Commissioning 11.1 Installation of magnetic-inductive flowmeters At the installation of the magnetic-inductive flow sensor the instructions and notes of the assembly instructions and operating manuals have to be followed. Also, observe the grounding, potential equalization and internal grounding guidelines. 11.2 Potentials All outputs are electrically isolated from the auxiliary power, the sensor circuit and from each other. The housing and the interference suppression filters of the power supply are connected to PE. The electrodes and measuring electronics are related to the potential of the function earth FE of the sensor. FE is not connected to PE, but may be connected with each other in the sensor junction box. If the sensor is grounded by using ground disks (earthing rings), these must in connected with the function earth FE. At a separate assembly of sensor and transmitter the outer screen of the connecting cable is connected to the transmitter housing and has PE potential. The inner screens of the electrode line are connected to FE inside the junction box of the sensor and to the mass (Gnd) of the transmitters electronics. Details of all wirings, terminals and drawing can be found in the section 8.9 Electrical connection . 32 IM-P309-02 MI Issue 2 11.3 Cathodic protective units Using a cathodic protective unit to avoid corrosion, which put a voltage to the tube wall, it must be connected to terminal FE. The transmitter boards, control panel and internal switches are on the same potential as FE. Warning According to EN 50178:1997 all electrical circuits with protective safety isolation without any protection against contacts must observe the following maximum voltages: Maximum AC voltage (root mean square value) 25 V Maximum DC voltage 60 V It is strictly forbidden to connect FE to any higher voltage! 11.4 Zero point calibration In order to ensure that precise measurements are obtained, zero point calibration is to be realized the first time the device is put into operation and before any regular operations are carried out. Zero point calibration is to be carried out using a fluid. The zero calibration procedure is as follows: - Install the sensor as described in the manufacturer’s instructions. - Check to ensure that the sensor is completely filled with fluid and that there are no gas bubbles in the flow tubes. - Define the process conditions such as pressure, temperature and density. - Close a potential shut-off device behind the sensor. - Operate the transmitter in accordance with the instructions in chapter 11.4 Zero point calibration. - Make sure that sufficient time is allowed for the electronics to warm up. - Allowing fluid to flow through the sensor during the zero calibration procedure will skew the zero point and result in false readings. 11.5 Startup conditions The device is not subject to specific startup conditions. However, pressure surges should be avoided. IM-P309-02 MI Issue 2 33 12. System design The meter can be used to perform measurements with any liquid, conductive media, providing that the sensor’s material is suitable for the product being used. 12.1 Standard version As standard ELM has 1 active 0/4 … 20 mA analogue output, 1 passive pulse or frequency output and 1 passive status output. 12.2 Display and Keypad A LCD display with backlight is a standard feature. The display shows measured values as well as diagnostics. With 6 keypads customers are able to configure comfortable and simple the transmitter without any other tool. Fig. 21 12.3 Optional equipment 12.3.1 HART-Interface An analog 0/4–20 mA output is a standard feature and digital data transmission via HART® protocol as an optional feature of the device. A retrofit by customer is not possible. 12.3.2 Empty pipe detection Transmitters, which are equipped with a control unit BE3, have an on and off switch able empty pipe detection. The operating reliability depends on the conductivity of the liquid medium and the cleanliness of the electrodes. As bigger the conductivity is, as more reliable operates the empty pipe detection. Insulation coatings on the electrodes surface worse the empty pipe detection. 34 IM-P309-02 MI Issue 2 12.3.3 Data memory chip DSM The replaceable data memory chip (DSM) is an EEPROM device in DIL-8 housing, located in a socket on the power supply board. It contains all characteristic data of the sensor e.g. sensor constant, version or serial number. Consequently, the memory module is linked to the sensor and in case of a transmitter replacement it has to remain by the sensor! After replacing the transmitter or its electronics, the DSM will be installed in the new transmitter. After the measuring system has been started, the measuring point will continue working with the characteristic values stored in the DSM. Thus, the DSM offers maximum safety and high comfort when exchanging device components. Electronic, Power supply board ELM Slot DSM Fig. 22 At any exchange watch the polarity of the memory chip. Pin 1 is signed by a dot or a notch. 12.3.4 Safety of operation A comprehensive self-monitoring system ensures maximum safety of operation. Potential errors can be reported immediately via the configurable status output. The corresponding error messages will also be displayed on the transmitter display. A failure of the auxiliary power can also be detected via the status output. When the auxiliary power fails, all data of the measuring system will remain in the DSM (without back-up battery). All outputs are electrically isolated from the auxiliary power, the sensor circuit and from each other. IM-P309-02 MI Issue 2 35 13. Configuration and operation 13.1 Introduction The ELM can be operated depending on equipment by using the HART® interface. In the following, the ELM operation and parameterization using the keypad are described. The keypad is located in the electronic compartment and covered by an inspection window. LC Display Keypad Enter Escape Cursor up Cursor left Cursor down Cursor right Fig. 23 13.2 Display The ELM has an integrated back lighted, alphanumeric display with two 16-character lines (format 16 x 60 mm). Measurement data and settings can be read directly from this display. The LCD display is designed be operated at temperatures ranging from − 20°C to + 60°C (-4° F to 140°F) without incurring any damage. However, at freezing or near-freezing temperatures, the display becomes slow and readability of the measured values is reduced. At temperatures below − 10 C° (14°F), only static values (parameter settings) can be displayed. At temperatures exceeding 60 C° (140°F), contrast decreases substantially on the LCD and the liquid crystals can dry out. 36 IM-P309-02 MI Issue 2 14. Operating modes The ELM can be operated in the following modes: 1. Display mode: In display mode, measured values can be displayed in various combinations and ELM settings can also be displayed. Parameter settings cannot be changed in this mode. Display mode is the standard (default) operating mode when the device is switched on. Programming mode: In programming mode, ELM parameters can be redefined. After entering the correct password, changes that are permissible for the customer (customer password) or all functions (service password for technicians) can be realized. 14.1 Operation 14.1.1 Operation interface Functional classes are displayed as headings beneath which displays and parameters are shown in logical groups. Beneath this is the menu level, which lists all measured value displays or the headings for their underlying parameters (parameter level). All functional classes are interlinked horizontally, while all subpoints that are assigned to a functional class are displayed beneath the relevant class. Legend Headline Main menu Functional class Functional class Functionial class Functionial class Function with Function with numerical Input numerical Input Numerical Input 153.40 Parameter level Display Display Menu level subpoint Selection [no] ___________ no yes Function valueFunction selected value selected from list from list Fig. 24 14.1.2 The keys and their functions There are sic keys to change the settings. Caution! Do not press these keys with sharp or sharp-edged objects such as pencils or screwdrivers! IM-P309-02 MI Issue 2 37 Cursor keys: Using the cursor keys, the operator can change numerical values, give YES/ NO answers and select parameters. Each key is assigned a symbol in the following table: Descriptor Symbol Cursor key, arrow to the right > Cursor key, arrow to the left < Cursor key, arrow to the top > Cursor key, arrow to the bottom < Esc key: The "Esc" key allows you to cancel the current action. Pressing Esc moves you to the next higher level where the operator can repeat the action. Pressing Esc twice moves you directly to the MEASURED VALUES functional class. ENTER key: Pressing (ENTER key) moves you from the menu level to the parameter level. You confirm all entries with the key. LC Display Keypad Enter Escape Fig. 25 Cursor up Cursor left Cursor down Cursor right 14.1.3 Functional classes, functions and parameters Functional classes are written in all upper case letters (headings). The functions beneath each functional class are written in upper and lower case. The various functional classes and functions are describes in Section 15.11„ UMF2 (B) transmitter functions". The lower lines contain the following elements: - Informational texts - YES/NO answers - Alternative values - Numerical values (with dimensions, if applicable) - Error messages. If the user attempts to modify values for any of these parameters without entering the required password, the message "Access denied" will be displayed (see also section 14 Operating modes and 14.1.3.3 Passwords) 38 IM-P309-02 MI Issue 2 14.1.3.1 Selection window / make a selection In the selection window, the first line of the LCD always contains the heading, while the second line displays the current setting. This setting is shown in square brackets if the system is in Programming mode. Function name [Selection] In Programming mode (see section 14 Operating modes), i.e. after a password has been entered (see 14.1.3.3 Passwords and 15.2 PASSWORD functional class ), the operator can navigate to the desired setting by using the key or the key and the operator can then confirm your selection by pressing (ENTER key). To retain the current setting, press Esc. 14.1.3.2 Input window / modify a value In the input window, the first line of the LCD always shows the heading, while the second line shows the current setting. Example: Function name -4,567 Unit These modifications can only be made in Programming mode (refer to 14 Operating modes), which means that a correct password (see 14.1.3.3 Passwords and 15.2 PASSWORD functional clas) must be entered. To move the cursor from one decimal place to the next, use the < or > keys. To increase the value of the decimal place just under the cursor by "1," use the key, and use key to lower the number by 1. To change the minus and plus sign, place the cursor in front of the first digit. To confirm and apply the change, press enter. To retain the current value, press Esc. 14.1.3.3 Passwords Programming mode is password protected. The customer password allows all changes to be made that are permissible for customers. This password can be changed when the device is first put into operation. Such changes should be kept in a safe place. The ELM customer password in the device when delivered is 0002. The service password allows for modification of all ELM functions. This password is not given to customers. For further information on customer passwords, see Section 15.2 PASSWORD functional class. IM-P309-02 MI Issue 2 39 15. ELM functions The software functions of the ELM transmitter are divided into functional classes, are arrayed in a circle and can be navigated by using the < or > cursor keys. To go back to your starting point (the measured values functional class) press Esc. Fig. 26 40 IM-P309-02 MI Issue 2 In the following, all software functions that can be accessed using the customer password are described. Functions that are only accessible to the vendor (service functions) are not described in the present document. 15.1 Measured values functional class The measured values functional class contains all functions for displaying the measured values. Fig. 27 IM-P309-02 MI Issue 2 41 15.1.1 Volume flow rate If you select the function "volume flow," the following will be displayed (example): Volume flow 100.0 l/h The LCD shows the current volume flow rate. You define the display unit in the functional class FLOW using the function "volume flow unit". 15.1.2 Forward flow counter 1 Forward flow counter 1 and forward flow counter 2 are independent counters that can also be reset separately. With counter 1, for example, you can measure the yearly or monthly volume. If you select the function "forward flow counter 1", the following will be displayed (example): Counter 1 forw. + 000001.0 l The LCD shows the current value of forward flow counter 1. You define the display unit in the functional class COUNTERS using the function "unit of counter". 15.1.3 Forward flow counter 2 The function is identical with the function of forward flow counter 1. For example, forward flow counter 2 can be used as a daily counter. If you select the function "forward flow counter 2", the following will be displayed (example): Counter 2 forw. + 000001.0 l The LCD shows the current value of forward flow counter 2. You define the display unit in the functional class COUNTERS using the function "unit of counter". 15.1.4 Reverse flow counter If you select the function "reverse flow counter," the following will be displayed (example): Counter reverse 000000.0 l The LCD shows the current value of the reverse flow counter. You define the display unit in the functional class COUNTERS using the function "unit of counter". 15.1.5 Flow velocity If you select the function "flow velocity," the following will be displayed (example): flow velocity 1.5 m/s The LCD shows the current value of the mean flow velocity of the medium. The display unit is always meters per second (m/s). The mean velocity is calculated from the measured volume flow and the flow area of the meter tube. In order to calculate the flow area of the meter tube, enter the inside diameter of the meter tube. To do so, use the "inside diameter" function in the functional class SETTINGS SENSOR + ELM. 42 IM-P309-02 MI Issue 2 15.1.6 Relative flow rate The relative flow rate is the percentage ratio of the (current) volume flow and the entered upper range value of the volume flow. You set this upper range value in the functional class FLOW using the function "volume flow QV URV." The calculation of the relative flow rate is based on the following formula: relative flow rate = 100% x (Qabs – lower range limit) / (upper range limit – lower range limit) If you select the function "relative flow," the following will be displayed (example): Relative flow 95.3% 15.1.7 QV + Forward flow counter If the function "QV+ forward flow counter 1" is selected, in the first line the actual flow will be displayed: XXX.X l XXX.XX l/h In the second line the LCD shows the current value of the forward flow counter 1. The displayed unit is defined in the functional class FLOW using the function "volume flow unit". The unit of the counter is defined in the functional class COUNTER using the function "counter unit". 15.1.8 QV + Forward flow counter 2 If the function "QV+ forward flow counter 2" is selected, in the first line the content of the actual flow will be displayed: XXX.X l XXX.XX l/h In the second line the LCD shows the current value of the forward flow counter 2. The displayed unit is defined in the functional class FLOW using the function "volume flow unit". The unit of the counter is defined in the functional class COUNTER using the function "counter unit". 15.1.9 QV + flow velocity If the function "QV + flow velocity" is selected, the following will be displayed: XXX.X l/h XXX.X m/s The first line shows the actual volume flow rate and the second line the mean flow velocity of the medium. The displayed volume flow unit is defined in the functional class FLOW using the function "volume flow unit", the unit of the medium’s velocity is always m/s. IM-P309-02 MI Issue 2 43 15.1.10 Display mode during startup By choosing the Display mode during startup function the operator can define the default display. After the operator switched the device on and did not touch any keys for a longer period of time, the defined default display will be shown. Display mode (QV) According to the description in Section 14.1.3.1 "Selection window / make a selection", one of the following default displays can be selected. QV (volume flow rate), Counter 1 forward flow, Counter 2 forward flow, Counter reverse flow, Velocity, QVabs + QVrel, QV + counter 1, QV + counter 2, QV + velocity, and raw values. 15.1.11 Raw values The "Raw value display" supports fault diagnostics and trouble shooting. Please inform our service department about the clear text error messages and contents of the "Raw value display". xxx.xxx ggooo iiii gguuu The displayed values are decimals and have the following meaning: xxx.xxx: ggooo: iiii: gguuu: 44 Is a gauge for the measured electrode voltage. Is a gauge for the upper value of the reference calibration. Is a gauge for the current to generate the field coil’s magnetic field. Is a gauge for the lower value of the reference calibration. IM-P309-02 MI Issue 2 15.2 Password functional class The password functional class is comprised of the functions for entering and changing the customer password and entering the service password. To cancel the current action, press Esc. Fig. 28 15.2.1 Customer-password After selecting the Customer password function and pressing enter, the following will be displayed: Password? 0000 According to the description in Section 14.1.3.2 "Input window / modify a value ", the password can be changed. If the entered password is correct, the following message will be displayed: Password valid If the entered password is not correct, the following message will be displayed: Password invalid IM-P309-02 MI Issue 2 45 The customer password in the device when delivered is 0002. A valid customer password allows all software parameter changes to be made that are permissible for customers. After the operator switched the device off or did not touch any keys for about 15 minutes, the authorization to change settings related to password entry will automatically be canceled. If the operator does not enter a valid password, all settings can be displayed but not changed. Parameter changes via HART may be carried out any time without entering password. 15.2.2 Change customer password After entering a valid customer password, you may change the existing password and enter a new one. After selecting the Change customer password function and pressing enter, the following will be display Enter New password 0000 According to the description in Section 1.2.3.2 "value" the current value can be changed. Press to confirm and save the new password. Make sure that you entered the desired password! A copy of the password should be kept in a safe place. Reactivation of a transmitter at the vendor’s site due to a lost password is not part of our warranty! 15.2.3 Service password You do not need the service password for setting the functions necessary for operation. The service password is reserved for service technicians and not provided to customers. Correct settings are essential for proper operation of the device (e.g. parameterization and calibration values). 46 IM-P309-02 MI Issue 2 15.3 Counter functional class The counters functional class is comprised of the following functions: Fig. 29 To change the current settings, enter the customer password. Otherwise, the settings can only be displayed but not changed. To cancel the current action, press Esc. IM-P309-02 MI Issue 2 47 15.3.1 Unit of counters After choosing the Unit of counters function and pressing enter, the current forward and reverse counter unit will be displayed: Accumulation of: (kg) According to the description in Section 14.1.3.1 Selection window / make a selection, one of the following units can be selected. Volume units: Mass units: m³ and l, kg and t. as well as USG, UKG, ft³ or When the unit is changed, the counters will be reset to 0.00 automatically. The mass unit only makes sense if density factor has been programmed for mass flow calculation. Press to confirm and save the selection. Forward and reverse counters will now show the selected unit. 15.3.2 Reset counter The ELM has 3 independent totalizing counters. Counter 1 and Counter 2 for forward flow and a reverse flow counter. Each of them can be reset individually on the initial value 0.00. To reset one of the totalizing counters, you definitely need to toggle to [yes]. Reset counter (no) According to the description in Section 14.1.3.1 Selection window / make a selection, "yes" or "no" can be selected. By pressing Esc or toggling to (no) the operator can cancel the current action without changing the counter readings. 48 IM-P309-02 MI Issue 2 15.4 Measurement processing functional class The measurement processing functional class is comprised of all functions that affect the processing of the measured values. To change the current settings, enter the customer password. Otherwise, the settings can only be displayed but not changed. To cancel the current action, press Esc. Fig. 30 IM-P309-02 MI Issue 2 49 15.4.1 Damping The damping value is intended to dampen abrupt flow rate changes or disturbances. It affects the measured value display and the current and pulse outputs. It can be set in intervals of 1 second from 1 to 60 seconds. After choosing the Damping value function and pressing enter, the following selection field will be display Damping 03 s The current damping value will be displayed. According to the description in Section 14.1.3.2 "Input window / modify a value", the current value can be changed. After setting the new damping value, press to confirm your entry. 15.4.2 Low flow cut-off The value for low flow cut-off (low flow volume) is a limiting value stated as a percentage that relates to the upper-range value of the flow rate. If the volume drops below this value (e.g. leakage), the displayed value and the current outputs will be set to "ZERO." The value for low flow cut-off can be set from 0 to 20% in 1-percent increments. After choosing the Low flow cut-off function and pressing enter, the following selection field will be displa Low flow cut-off 00% The low flow volume will be displayed. According to the description in Section 14.1.3.2 Input window / modify a value, the current value can be changed. After setting the new low flow volume, you confirm your entry with en 15.4.3 Low flow cut-off hysteresis The hysteresis of the low flow volume is the flow rate expressed as a percentage of the upper range value by which the volume must fall below or surpass the set low flow volume in order to activate or deactivate the function. The hysteresis of the low flow volume can be set in 1-percent increments from 0 to 10%. After selecting the Low flow cut-off hysteresis function and pressing enter, the following selection field will be display Low flow cut-off hysteresis 00% The current hysteresis will be displayed. According to the description in Section 14.1.3.2 "Input window / modify a value", the current value can be changed. After setting the new hysteresis value, you confirm your entry with en 50 IM-P309-02 MI Issue 2 15.4.4 Zero point calibration Using the Zero point calibration function the operator can recalibrate the zero point of your meter in the measuring system. Zero point calibration is to be realized after any installation procedure or after any type of work has been performed on in the pipes near the sensor. Refer also Section 11.4 Zero point calibration. CAUTION: This function may only be carried out if it is certain that the fluid in the sensor is not flowing. Otherwise, the flow rates measured subsequently will be incorrect. The sensor must be completely filled with fluid. A partially filled sensor or air bubbles will lead to an incorrect zero point calibration. After choosing the Zero point calibration function and pressing enter, the current remaining flow will be display 0.00 l/h cal.? (no) According to the description in Section 14.1.3.2 Selection window / make a selection, "yes" or "no" can be selected. By pressing Esc or toggling to [no] the operator can cancel the current action. Enter [yes] to have the zero point recalibrated. 15.4.5 Filter For a noise reduction of the actual readings a signal filter can be used. Following settings are available: • none • weak • mid (standard factory setting) • strong Selecting "weak" or "mid" influences the dynamics of the actual readings not or just very less. The setting of damping time (see section 8.11.6 "Damping") determines the dynamic behaviour of sensor and transmitter. Filter "strong" operates as an intense low pass filter to reduce the noise of the actual readings. Then if setting the damping time shorter than 3 seconds, the low pass filter determines the dynamic behavior to actual reading’s variations. According to the description in Section 14.1.3.2 Selection window / make a selection, noise filter type can be selected. IM-P309-02 MI Issue 2 51 15.5 Flow functional class The FLOW functional class is comprised of functions that affect lower- and upper-range values and the processing of the measured flow rates. In Programming mode (see section 14 Operating modes), i.e. after a password has been entered (see 14.1.3.3 Passwords, 15.2 PASSWORD functional class), the operator can change the settings regarding flow. Fig. 31 To change the current settings, enter the customer password. Otherwise, the settings can only be displayed but not changed. To cancel the current action, press Esc. 52 IM-P309-02 MI Issue 2 15.5.1 Volume flow QV unit Using this function, the operator can define the physical unit for all display functions, limit values and the upper-range value of volume flow. After choosing the Volume flow QV unit function and pressing enter, the following selection field will be displa Volume flow QV in (l/h) According to the description in Section 14.1.3.1 Selection window / make a selection, one of the following units can be selected: l/h, l/min, l/s m³/h, m³/min, m³/s USG/h, USG/min, USG/s, UKG/h, UKG/min, UKG/s, Kg/h, t/h, ft³/s, MGD (Mega US Gallons / day). Press to confirm and save the selection. 15.5.2 Volume flow lower-range value This function allows the operator to set the lower-range value for volume flow. The lower-range value takes on the unit defined using the Volume flow unit function. The lower-range value will scale the current and frequency outputs assigned to volume flow. After choosing the Volume flow lower-range value function and pressing enter, the following selection field will be display QV LRV = 0% XXXXX.XX l/h The current lower-range value for volume flow will be displayed. According to the description in Section 14.1.3.2 Input window / modify a value, the current value can be changed. 15.5.3 Volume flow upper-range value This function allows the operator to set the upper-range value for volume flow. The upperrange value takes on the unit defined using the Volume flow unit function. The upper-range value will scale the current and frequency outputs assigned to volume flow. After choosing the Volume flow upper-range value function and pressing enter, the following selection field will be display QV URV = 0% XXXXX.XX l/h The current upper-range value for volume flow will be displayed. According to the description in Section 1.2.3.2 Input window / modify a value, the current value can be changed. IM-P309-02 MI Issue 2 53 15.5.4 Volume flow limit MIN The MIN limiting value for volume flow can be evaluated via the status output. You enter the value as a percentage of the set upper-range value. If the volume flow is lower than that limit value, the status output will be set in case the corresponding assignment has been made. If the alarm function has also been activated for the current output, the applied current will change to < 3.2 mA or > 20.5 mA / 22 mA. After choosing the Volume flow limit MIN function and pressing enter, the following selection field will be display Volume flow limit MIN = 10% The current MIN upper-range value for volume flow will be displayed. According to the description in Section 14.1.3.2 "Input window / modify a value", the current value can be changed. 15.5.5 Volume flow limit MAX The MAX limiting value for volume flow can be evaluated via the status output. You enter the value as a percentage of the set upper-range value. If the volume flow surpasses this limit value, the status output will be set in case the corresponding assignment has been made. If the alarm function has also been activated for the current output, the applied current will change to < 3.2 mA or > 20.5 mA / 22 mA. After choosing the Volume flow limit MAX function and pressing enter, the following selection field will be display Volume flow limit MAX = 90% The current MAX upper-range value for volume flow will be displayed. According to the description in Section 14.1.3.2 "Input window / modify a value", the current value can be changed. 15.5.6 QV limit hysteresis The hysteresis of the QV limiting values is the flow rate in percent based on the upper-range value and indicates the value which must fall below or surpass the set limiting values in order to activate or deactivate the function. The hysteresis of the QV limiting values can be set in 1-percent increments from 0 to 10%. After choosing the QV limit hysteresis function and pressing enter, the following selection field will be display QV limit Hysteresis 00% The current hysteresis value will be displayed. According to the description in Section 14.1.3.2 "Input window / modify a value", the current value can be changed. 54 IM-P309-02 MI Issue 2 15.5.7 Density If a mass unit in kg or t is used as flow unit (2.5.1 Volume flow QV unit), the density of the medium must be entered in the unit of g/l. Using the entered density value, the mass flow is calculated from the volume flow measurement. After choosing the Density function and pressing enter, the following selection field will be display Density 998.2 g/l The current density value will be displayed. According to the description in Section 14.1.3.2 "Input window / modify a value", the current value can be changed. The value of the density is not measured. It is a parameter. 15.5.8 Volume flow LSL (information field) This value represents the minimum lower range value based on the inside diameter of the sensor. This value is normally set for a flow velocity of 0.25 m/s. QV LSL XX.XXX l/h 15.5.9 Volume flow USL (information field) This value represents the maximum upper range value based on the inside diameter of the sensor. This value is normally set for a flow velocity of 11 m/s. QV USL XX.XXX l/h IM-P309-02 MI Issue 2 55 15.6 Pulse output functional class The pulse output functional class is comprised of the functions regarding the pulse output. Fig. 32 56 IM-P309-02 MI Issue 2 15.6.1 Pulse or frequency output The Pulse or frequency output function allows the operator to define whether pulses per represent a unit of flow or a frequency between 0 and 1 kHz that represents an analog output over the measuring range. After selecting the frequency setting, the maximum frequency of 1 kHz will be generated when the upper-range value for mass or volume flow is reached (depending on the selected pulse unit). If the flow rate falls below the low flow volume, the actual frequency is 0 Hz. After selecting the pulse setting, pulse value and unit the transmitter will determine the number of pulses per flow volume. When choosing a combination of these settings that cannot be fulfilled in real time for the upper-range value (e.g. the number of pulses per time unit cannot be generated due to the pulse width which is too large), the error message "Pulse width too large" or "Inconsistent parameter" will be displayed. Press to display the current setting: Output of (Pulses) According to the description in Section 14.1.3.1 Selection window / make a selection, the operator can toggle between frequency and pulse output (default setting). 15.6.2 Pulse output unit This function allows the operator to define the unit to be counted. After selecting the Pulse output unit function, press to display the following selection field: Accumulation of 1.0 l The current value will be displayed. As mentioned in Section 14.1.3.1 Selection window / make a selection, the operator can choose between the following units: Mass units: kg, t Volume units: m³, l, USG, UKG, ft³. 15.6.3 Pulse value This function allows the operator to define how many pulses will be output per unit counted. After selecting the Pulse value function, press to display the current unit: 1 pulse per (1.0) unit As mentioned in Section 14.1.3.1 Selection window / make a selection, the operator can choose between the following pulse values: Values: 0.001, 0.01, 0.1, 1.0, 10.0, 100.0 IM-P309-02 MI Issue 2 57 15.6.4 Pulse width This function allows the operator to change the width of the output pulse to be output. If the pulse width is too large for the actual pulse number, it will be reduced automatically. In this case the warning "Pulse output saturated" will be displayed. After selecting the Pulse width function, press to display the following selection field: Pulse width 0050.0 ms The current pulse width will be displayed. As mentioned in Section 14.1.3.2 "Input window / modify a value", the operator can change the current value. The maximum output frequency can be calculated from the following formula: f= 1 2 * pulse width [ ms ] ≤ 1000Hz If connecting to electrical counter relays, we recommend pulse widths greater than 4 ms; for electromechanical counter relays the preset value should be 50 ms. 15.7 Status output functional class The functional class output is comprised of the functions for setting the status output. Fig. 33 58 IM-P309-02 MI Issue 2 15.7.1 Status output active state The status output can be compared to an electrical relay that can function as make or break contact. For safety-relevant applications, the operator will choose the break contact setting so that a power failure or failure of the electronics can be detected like an alarm. In standard applications, the output is used as make contact. The Status output state active state function allows the operator to define the behavior of the status output. Output active (closed) As mentioned in Section 14.1.3.1 Selection window / make a selection, the operator can choose between the following settings: - closed open. 15.7.2 Status output assignment This function allows the operator to define to which event the status output is to be assigned. The most general assignment is the reverse flow assignment. After selecting the Status output assignment function, press to display the current assignment. Output assigned to (Reverse flow) As mentioned in Section 14.1.3.1 Selection window / make a selection, the operator can choose between the following settings: - Flow direction recognition Forward flow Reverse flow Limiting values: - MIN QV - MAX QV - All limiting values and error detection - Alarm. IM-P309-02 MI Issue 2 59 15.8 Current output functional class The current output functional class allows the operator to perform the settings for the current outputs of the transmitter. Fig. 34 The current output is always assigned to volume flow. 60 IM-P309-02 MI Issue 2 15.8.1 Current output 0/4 - 20 mA The Current output 0/4 to 20 mA function allows the operator to define the range in which the current output is to be operated. Within the range from 0 to 21.6 mA (= 0 ... 110%) HART® communication is not possible. The range from 4 to 20.5 mA follows the NAMUR recommendation and covers the range from 0 to 104% of the measuring range. The standard range from 4 to 21.6 mA allows for a control of the measuring range of up to 110%. Press to display the current setting. Current output I1 (4) – 21.6 mA As mentioned in Section 14.1.3.1 Selection window / make a selection, the operator can choose between the following settings: 0 – 21.6 mA 4 – 21.6 mA 4 – 20.5 mA Output current - 4-21.6 mA only 4-20.5 mA and 4-21.6 mA Fig. 35 0-20 (21.5) mA Measured value 15.8.2 Current output alarm This function allows the operator to define the state taken on by the current output when a state of alarm is detected. This information can be analyzed in the control system. Press to display the current setting: Alarm (>22mA) As mentioned in Section 14.1.3.1 Selection window / make a selection, the operator can choose between the following settings: - not used no alarm function > 22 mA current rise in the case of an alarm < 3.8 mA current reduction in the case of an alarm IM-P309-02 MI Issue 2 61 15.9 Simulation functional class The functional class simulation is comprised of the functions for simulating the outputs. If simulation is activated, all output signals will be generated based on the selected type of simulation. The peripherals connected to the device can be tested without a flowing product. Simulation will be deactivated automatically if the operator switched the device off or did not touch any control unit keys for about 10 minutes. Simulation can also be activated and controlled via HART® commands. Fig. 36 15.9.1 Simulation on / off The Simulation on/off function allows the operator to activate or deactivate simulation. If simulation is activated, all output signals will be generated based on the selected type of simulation. The peripherals connected to the device can be tested without a flowing product. Press to display the current status. Simulation (off) As mentioned in Section 14.1.3.1 Selection window / make a selection, the operator toggles between the "on" and "off." Simulation will be deactivated automatically if the operator switched the device off or did not touch any control unit keys for about 10 minutes. 62 IM-P309-02 MI Issue 2 15.9.2 Simulation direct / preset value Q This function allows the operator to define whether simulation is comprised of the measurement of the volume flow or whether the outputs will be set directly. Press to display the selected type of simulation. Simulation [direct] As mentioned in Section 14.1.3.1 Selection window / make a selection, the operator can choose between the following settings: - Direct QVabs pulse and current outputs are programmed directly a measurement is simulated If "direct" simulation is activated, any output will perform based on the settings described in Sections 15.9.5 Status output simulation to 15.9.5.7 Current output simulation. It is therefore recommended that the settings be defined before starting simulation. They can then be purposefully changed during simulation. Simulation will be deactivated automatically if the operator switched the device off or did not touch any control unit keys for about 10 minutes. 15.9.3 Simulation measured flow Q If the operator selected the setting "QVabs" described in Section 15.9.2, the following settings of a volume flow will affect the output behavior during measured value simulation. In order to simulate volume flow, the operator can define a "measured value." The flow rates will be simulated in both directions. All outputs will perform based on the simulated measured value. Preset QVabs ±0900.0 l/h The simulation value is entered as described in Section 14.1.3.2 "Input window / modify a value". 15.9.4 Direct simulation of outputs If the operator selected the setting "Direct simulation" described in Section 15.9.2 „Simulation direct ", the following 3 possible settings will affect the output. All outputs are simulated at the same time by these settings. IM-P309-02 MI Issue 2 63 15.9.5 Status output simulation The Status output simulation function allows the operator to purposefully activate the status output. Press to display the current state. Status output (off) As mentioned in Section 14.1.3.1 Selection window / make a selection, the operator can toggle between "on" and "off". 15.9.6 Pulse output simulation The Pulse output simulation function allows the operator to define a frequency to be assigned to the pulse output. After selecting this function and pressing enter, the following selection field will be display Set frequency 0210.0 Hz This field shows the current frequency. As mentioned in Section 14.1.3.2 "Input window / modify a value", the definable frequency ranges from 6 Hz to 1100 Hz. 15.9.7 Current output simulation This function allows the operator to define a current for current interface 1. Press to display the set current. Set I1 I1 = 10.50 mA As mentioned in Section 14.1.3.2 "Input window / modify a value", the current value can be changed. 64 IM-P309-02 MI Issue 2 15.10 Self-test functional class The self-test function class is comprised of the functions relating to the self-test of the sensor. The diagnostic functions of the transmitter, which monitor the proper functioning of the electronics and the software, are always active and cannot be switched off. The excitation current can be monitored in addition. Fig. 37 IM-P309-02 MI Issue 2 65 15.10.1 Self-test test on / off The Self-test on/off function allows the operator to activate or deactivate the monitoring function of the field coil current. Self-test (off) According to the description in Section 14.1.3.1 Selection window / make a selection, the operator can toggle between "on" and "off." The standard factory setting is "on." The measurement is intended to suppress temperature dependences of the transmitter. During the sampling time of 0.5 seconds, the transmitter is offline; the last measured value will be displayed at the signal outputs. Self-test period (STP) With the help of this function, you set the time period after which the field coil current will be measured periodically. You can set periods between 35 seconds and 999 seconds. Self-test STP = 040 s This field shows the current self-test period. As mentioned in Section 14.1.3.2 "Input window / modify a value", the current value can be changed. 15.10.2 Reference calibration on / off With the help of the function Reference calibration on/off, the periodic recalibration of the transmitter can be activated or deactivated. The objectives of the function are periodic selfmonitoring and an increase in long-term stability. During the automatic reference calibration of 30 seconds, the transmitter is offline; the last measured value will be displayed at the signal outputs. After choosing this function and pressing enter, the following selection field will be display Reference calibration (off) According to the description in Section 14.1.3.1 Selection window / make a selection, the operator can toggle between "on" and "off." If switched on, the reference calibration will be done periodically. 66 IM-P309-02 MI Issue 2 15.10.3 Reference calibration period (GAP) The function Reference calibration period is a multiplication of the function "self-test period" .With the help of this function, you define after how many STP’s the reference calibration is to be performed. Reference calibration GAP = 540 * STP This field shows the current reference calibration period. As mentioned in Section 14.1.3.2 "Input window / modify a value", the current value can be changed. Example:The "self-test period" has been set to 40 seconds; a reference calibration is to be carried out every 6 hours. GAP = 6 * 3600s / 40s = 540 15.10.4 Empty pipe detection on / off With the help of the function Empty pipe detection on / off, continuous empty-pipe detection can be activated or deactivated. After selecting this function and pressing enter, the following selection field will be display Empty pipe detection (off) According to the description in Section 14.1.3.1 Selection window / make a selection, the operator can toggle between "on" and "off." If switched on, the empty pipe detection will be done periodically. 15.10.5 Empty pipe detection period With the help of the function Empty pipe detection period, the time after which the detection will be carried out can be set. When entered 00 minutes, the detection will be performed continuously. After choosing this function and pressing enter, the following selection field will be display Leerrohrprüfung alle 10 Min This field shows the current empty pipe detection period. As mentioned in Section 14.1.3.2 "Input window / modify a value", the current value can be changed. IM-P309-02 MI Issue 2 67 15.11 Settings sensor + UMF2 (B) functional class This functional class is comprised of the general settings affecting the behavior of the transmitter. SETTINGS SENSOR + UMF2 functional class SETTINGS SETTINGS SENSOR + UMF2 SENSOR + UMF2 Sensor constant C Sensor constant C Sensor type Sensor type Sensor constant /mV 03321.9 l/h Sensor type [PITY] _______________ EPY EPYE EPS PIT-520 PIT-571 PIT-573 PIK PITY other Version of UMF2 Version of UMF2 software software Serial number Serial number Inside diameter Inside diameter Language Language Excitation Excitation frequency frequency Mains frequency Mains frequency Flow direction [forward & reverse] _________________ forward & reverse forward reverse Flow Flow direction direction Version of UMF 001.06 Serial number 123456 Inside diameter 0125.5 mm LAnguage [English] _________________ German English Excitation frequency [6.25] Hz _________________ 1.56 3.125 6.25 12.5 25 Show system Show errorssystem errors Reset system Reset errorsystem error System error 0000000 Reset [no] _________________ yes no Mains frequency [50] Hz _________________ 50 60 Fig. 38 68 IM-P309-02 MI Issue 2 15.11.1 Sensor constant C The sensor constant C is the calibration value of the sensor connected to the transmitter. The calibration value must be entered in the ELM transmitter to ensure a correct measurement. The constant will be defined after the calibration of the meters and can be found on the rating plate of the sensor. After selecting the Sensor constant function, press to display the current setting. Sensor constant /mV 01234.56 l/h As mentioned in Section 14.1.3.2 "Input window / modify a value", the current value can be changed. CAUTION: Changing sensor constant C to a value that differs from the value on the rating plate of the sensor connected to the flowmeter will result in false readings! Note: The sensor constant must always be preceded by a plus or minus sign. The delivery default setting is a plus sign. If inlet and outlet section are interchanged when the device is installed (the flow direction is indicated by an arrow on the sensor), the transmitter will display a "forward flow" negative measurement value. If the (plus or minus) sign of the sensor constant is then changed without changing the actual value, a plus sign will again be displayed. No changes need be made in the disposition of the electrical connections (wires). 15.11.2 Sensor type The function Sensor type contains the type of the sensor with which the transmitter has been delivered. The distinction is necessary and required because the flow rate measurement uses different calculations depending on the type of the used sensor. After selecting this function, press to display the current setting. Sensor type (PITY) This type code can be found on the sensor rating plate. This setting is defined by the vendor when the device is first put into operation at the factory. It should only be changed if the transmitter is mounted onto another sensor. 15.11.3 Inside diameter The inside diameter of the sensor connected to the transmitter is necessary for calculating the mean flow velocity. The inside diameter must be checked in the ELM (on mm exact) to ensure a correct measurement. After choosing the function "inside diameter" and pressing enter, the following selection field will be displa Inside diameter 50 mm As mentioned in Section 14.1.3.2 "Input window / modify a value", the current value can be changed. IM-P309-02 MI Issue 2 69 15.11.4 Language Two languages are available in the ELM: German and English.. Language (English) As mentioned in Section 14.1.3.1 Selection window / make a selection, the operator can toggle between these languages: - German English. 15.11.5 Excitation frequency With the help of the function Excitation frequency, you can set the excitation frequency of the field coil current. Since the excitation frequency depends on the sensor, it cannot be assigned freely. The excitation frequency defaults to 6.25 Hz. Excitation frequency (6.25 Hz) The selection is confirmed and taken over with the key. Caution! If the excitation frequency is changed, then a reference calibration (Section 15.10.2 Reference calibration on / off ) must be accomplished! Otherwise the measuring accuracy is not ensured. 15.11.6 Mains frequency In order to ensure with mains frequency (50 Hz or 60 Hz per second) optimal interference suppression, the input of the frequency is necessary. The standard setting is 50 Hz After choosing the function Mains frequency and pressing enter, the following selection field will be display Mains frequency (50 Hz) The selection is confirmed and taken over with the key. 70 IM-P309-02 MI Issue 2 15.11.7 Flow direction This function allows the operator to define the flow direction that the transmitter will evaluate. Only "forward" should be selected so as to prevent reverse flow from being measured. The standard factory setting is "forward & reverse." After selecting the Flow direction function, press to display the current setting. Flow direction (forward) As mentioned in Section 14.1.3.1 Selection window / make a selection the operator can choose between: forward reverse forward & reverse Output (current, pulse) - Reverse flow Forward flow Fig. 39 Measured value 15.11.8 Software version (information field) After selecting this function, the version of the transmitter software will be shown (example: 1.06): Version of ELM 001.06 IM-P309-02 MI Issue 2 71 15.11.9 Serial number (information field) With the help of the Serial number function, the transmitter is assigned to an order. This number provides access to internal vendor data if the device needs servicing. The serial number is printed on the rating plate of the transmitter. After selecting this function, press to display the following information field: Serial number: 100683 This entry should never be changed so as to ensure that the sensor, the transmitter and the documents created within quality management are assigned correctly. 15.11.10 Show system errors With the help of this function, you can show the error code of the system errors that have occurred. The integrated diagnostic system of the ELM distinguishes between two types of errors (see also Section 15.11.12 "ELM error messages"). Self-test errors such as problems with a sensor line or inconsistent parameter inputs are displayed as textual error messages. Once the error has been eliminated, the message automatically disappears from the display. For further information, see Section 16.1.1 "Display of self-test errors". Errors that are attributable to system memory or software, division by zero, or a fault in the electronics unit are designated as system errors. These error messages are not reset automatically after the error (usually of very brief duration) is eliminated. 15.11.11 Reset system error Before resetting a system error manually, we advise that you contact our technical service department. For further information, see Section 16.1.2 "Display of system error". Reset error (no) If the operator toggles to [yes] and confirms the action according to the description in Section 14.1.3.1 Selection window / make a selection , the error messages disappears from the display. If the message reappears shortly after, do contact our technical service department. 15.11.12 ELM error messages The integrated diagnostic system of the ELM distinguishes between two types of errors. Selftest errors such as problems with a sensor line or inconsistent parameter inputs are displayed as textual error messages. Once the error has been eliminated, the message automatically disappears from the display. For further information, see Section 16.1.1 "Display of self-test errors". Errors that are attributable to system memory or software, division by zero, or a fault in the electronics unit are designated as system errors. These error messages are not reset automatically after the error (usually of very brief duration) is eliminated. Before resetting a system error manually, we advise that you contact our technical service department. For further information, see Section 16.1.2 "Display of system error". If the cause of any of the error messages described below cannot be eliminated, contact the device vendor. 72 IM-P309-02 MI Issue 2 16. Standard operating mode The transmitter operates as described above. After the cause of the error message has been eliminated, the message automatically disappears. 16.1 List of error messages 16.1.1 Display of self-test errors Self-test errors are displayed as plain text in the set language (German or English) on the second line of the LCD. Display (German) Display (English) Description Possible cause of error and remedy Rohr leer empty pipe Empty-pipe detection has been activated. Fluid density is below the limit value for density; empty-pipe detection, pipe is empty. Product contains air bubbles/pipe is empty. Bubblefree filling must be ensured. Spulenstrom Exciter current? Interruption / short circuit in the connection of excitation coil. All signal outputs will be set to no flow. Check the wiring between transmitter and sensor. Messkreis überst. meas. circ. sat. The flow measurement circuit is overloaded. The measured electrode voltage is too high. All signal outputs will be set to no flow. Flow rate exceeds the upper range value (URL). High electrostatic voltage at the electrodes. Strom überst. curr. saturated The output of current interface is overloaded. Based on the selected settings and the currently assigned measured variable, the current to be output is > 21.6 mA. Check the upperrange value and the flow rate settings. IMP übersteuert pulse out satur. The pulse output is overloaded. The current measured value requires a pulse rate, which can no longer be generated with the help of the set pulse duration and pulse value. Check pulse duration, pulse value, and measuring range. Check the flow rate. Table continued overleaf IM-P309-02 MI Issue 2 73 16.1.1 Display of self-test errors (continued) Display (German) Display (English) Description Possible cause of error and remedy Parameter inkons. params inconsist Parameter is inconsistent. Check the parameter settings. The set parameters are contradictory. Check the parameter settings. The set parameters are contradictory. Example: Upperrange value, pulse value and pulse duration must be matched in such a way that the combination fits for all measured values. ext EEPROM fehlt missing EEPROM The data memory module (DSM) with the calibration data of the sensor and the customerspecific settings of the transmitter is not plugged-in. Insert the data storage module (DSM) in the socket on the power supply board UMF2-20. Information: Error message: "Parameter is inconsistent" (system error 0x0400)? To generate a list of the inconsistencies, first enter a valid password and then an invalid password. The control unit will show a list of current errors (only once). The operator can then correct the inconsistent settings after entering a valid password. 74 IM-P309-02 MI Issue 2 16.1.2 Display of system error System errors consist of the message text "system error" and a 5-digit number in hexadecimal code. The meaning of the individual error codes is described in the following table. If several errors occur at the same time, the hexadecimal sum of the individual errors will be displayed. The errors are coded in such a way that the individual errors can be easily identified. The sums are unique. Descriptor label (never displayed) Constant/ display Description SystemfehlerExtEEProm 0x00002 External EEPROM (data memory chip DSM) plugged in but empty, not initialized SystemfehlerIntEEProm 0x00004 Internal EEPROM (calibration UMF2 (B) transmitter) erased, UMF2 uncalibrated SystemfehlerEEPROM 0x00010 Unsuccessful saving or reading of memory data / defective memory 16.1.3 Reset system error After the fault recovery the displayed system error message can be reset. For this purpose the customer password has to be entered. (Refer to 15.2.1 Customerpassword). Select the function Show system error. (Refer to 15.11.10 Show system error). Analyse the fault and repair the transmitter or sensor. Finally reset the system error message. (Refer to 15.11.11 Reset system error) 17. Standards & Directives General standards and directives EN 60529 Degrees of protection provided by enclosures (IP code) EN 61010-1:2010 Safety requirements for electrical equipment for measurement, control, and laboratory use. NAMUR guideline NE21, Version 2012-05-09 Directive 97/23/EC (Pressure Equipment Directive) AD-2000 Guidelines Electromagnetic compatibility EMC Directive 2004/108/EC EN 61000-6-2:2005 (immunity for industrial environments) EN 61000-6-3:2007 +A1:2011 (emission standard for residential, commercial and light-industrial environments) EN 55011:2009 +A1:2010 group 1, class B (emitted interference) DIN EN 61326-1:2013 IM-P309-02 MI Issue 2 75 18. Maintenance The device requires no maintenance if used according to its intended purpose. Cleaning might be necessary due to deposits and dirt on the electrodes or the flow tube. 76 IM-P309-02 MI Issue 2 19. Decontamination certificate for device cleaning Company name: ............................... Address: ............................................... Department: .................................... Name of contact person: .................... Phone: ................................. Information pertaining to the enclosed flowmeter Model ELM- ................ was operated using the following fluid: ........................................ In as much as this fluid is water-hazardous / toxic / corrosive / combustible we have done the following: Checked all cavities in the device to ensure that they are free of fluid residues* Washed and neutralized all cavities in the device* *cross out all non-applicable items We hereby warrant that no health or environmental hazard will arise from any fluid residues on or in the enclosed device. Date: ............................. Signature: ........................... Stamp IM-P309-02 MI Issue 2 77 78 IM-P309-02 MI Issue 2 IM-P309-02 MI Issue 2 79 80 IM-P309-02 MI Issue 2
advertisement