advertisement
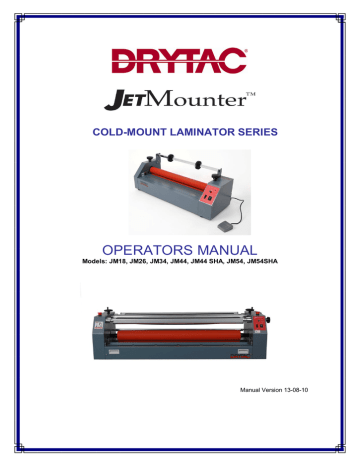
COLD-MOUNT LAMINATOR SERIES
OPERATORS MANUAL
Models: JM18, JM26, JM34, JM44, JM44 SHA, JM54, JM54SHA
Manual Version 13-08-10
Copyright © 2006 Drytac Corporation / Revised © 2008 Drytac Corporation
All rights reserved. No part of this publication may be utilized or reproduced in a retrieval system, or transmitted in any form or by any means; electronic, mechanical, photocopying, recording, or otherwise, without prior written permission from Drytac Corporation.
2
Welcome to the World of Drytac
Ove r the past three decades, Drytac has evolved into one of the world‟s most highly regarded manufacturers of products for graphics finishing and display. Our core product line consists of a wide range of pressure-sensitive, heatset and thermal overlaminating films. In addition, we offer an extensive line of mounting adhesives, backing films, inkjet media, finishing equipment, accessories, and banner stands.
3
Our “Start To Finish” strategy sums up Drytac‟s unique ability to manage all phases of the customer experience: product quality and performance, manufacturing and distribution, training and technical support and the industry‟s best customer service.
Jet
Mounter™ Professional Quality Entry-Level Models
JM18, JM26, and JM34
These solid mid-size models deliver superior results for beginners and experienced users alike. Easy to set up and operate, the JM18‟s and JM26‟s are widely used by photography studios, picture framers, digital art studios and other creative shops, and our newest model the JM34 are sure to also be as popular. Standard features include: all-steel construction, variable speed electric drive, forward and reverse, foot pedal control, silicone rollers, photoelectric safety stop and supply shaft.
Since all three models have many of the same features, consider references in this manual pertaining to the JM26 to be applicable to the JM18 and the JM34.
Jet
Mounter™ Wide Format Laminators
Drytac‟s Pressure-Sensitive Cold-Mount Models deliver economy and versatility for graphics finishing. The JetMounter ™ motorized laminator series is engineered by Drytac to deliver a combination of performance and value unequalled in the finishing industry. Compatible with any pressure-sensitive overlaminating film, JetMounters are also ideal for permanently mounting graphics onto cardstock, foam board, MDF or rigid PVC board.
All electric models include variable-speed electric drive, silicone rollers, all-steel construction, forward and reverse, supply shaft, foot pedal and photo-electric safety stop.
The three heavy-duty wide-format models, (JM44, JM54, and the new JM63) are the culmination of our three decades in the mounting and laminating business. Equipped with the performance features our customers demand, JetMounter ™ wide format models are unmatched for value.
4
Table of Contents
Overview .......................................................................................................................... 6
Important Safety Information ......................................................................................... 6
Specific Moving Instructions .................................................................................. 10
Unpacking and Installation..................................................................................... 11
JM Components .................................................................................................... 12
Component Illustrations ........................................................................................ 14
Setting Roller Pressure .......................................................................................... 15
JM44SHA/JM54SHA Roller Pressure Adjustment ................................................. 16
Adjusting Shaft Tensions ....................................................................................... 17
Mounting With the JetMounter ™ Laminators
Mounting Board Selection...................................................................................... 18
Adhesive Selection ................................................................................................ 18
Pre-coating the Mounting Board ............................................................................ 18
Mounting a Graphic to a Pre-Coated Board ........................................................... 20
L a m inating with the JetMounter ™ Laminators
Selecting a Laminate Film ..................................................................................... 21
Single Unmounted Graphic .................................................................................... 22
Single Mounted Graphic ........................................................................................ 23
Laminating Multiple Mounted Images .................................................................... 24
Using a Leader Board ............................................................................................ 25
Carrier Boards ....................................................................................................... 26
Preparing Mounting Boards ................................................................................... 26
Care and Maintenance .................................................................................................... 27
Service .................................................................................................................. 28
Technical Specifications ........................................................................................ 29
Contact Information ............................................................................................... 30
Warranty .......................................................................................................................... 31
Appendix
Replacement Parts ................................................................................................ 32
B Revision Functional Requirements ..................................................................... 33
JM44SHA/JM54SHA Nip Adjustment Procedure ......................................................34
5
Overview
Thank you for purchasing a Drytac JetMounter ™ Cold Mount Laminator. The information contained in this manual will familiarize you with the basic methods of mounting and laminating using this easy-to-use two roller laminator. This manual covers five JetMounter ™ models:
Model
JM18
JM26
Width
25.5” (64.8 cm)
33.25” (84.5 cm)
Maximum Laminate
18.25” (46.4 cm)
26.25” (66.7 cm)
JM34
JM44/JM44SHA
TBA
52.75” (134.0 cm)
TBA
44.125” (112.1 cm)
JM54/54SHA 62.5” (135.3 cm) 54.125” 137.5 cm)
These models are similar in operation, but not identical. Unless otherwise indicated, the instructions are for the JM26 model. Specific comments regarding the JM44, JM54 and
JM54SHA models are made where differences occur.
Important Safety Information
Before operating this equipment for the first time, it is crucial that you take the time to read and understand all of the following safety-related information. Failure to follow these procedures could result in serious personal injury and/or damage to the equipment and work piece.
Safety Signal Words and Symbols
Danger symbols indicate imminently hazardous situations that, if not avoided, will result in serious injury or death.
6
!
Pinch
Hazard
Inside
Panel
Warning symbols indicate a potentially hazardous situation that, if not avoided, could result in severe injury or death.
Caution headings indicate a potentially hazardous situation that, if not avoided, may result in minor or moderate injury.
This symbol indicates a statement of company policy directly or indirectly related to the safety of personnel or protection of property.
!
!
Pinch
Hazard
Inside
Panel
These symbols indicate a dangerous pinch hazard exists.
Pinch point.
Keep hands clear during operation.
This caution label indicates that a heavy object is involved and assistance is needed to avoid injury.
The JetMounter ™ performs mounting and laminating using two rollers to apply uniform pressure to adhesives and overlaminating films. The point where the rollers touch the material is called the Nip. This area creates a potential pinch hazard for fingers or other
7
objects. DO NOT OPERATE THIS EQUIPMENT IF YOU ARE UNWILLING TO ACCEPT
THIS HAZARD! TO AVOID INJURY, ALWAYS KEEP YOUR FINGERS AWAY FROM THE
NIP AREA.
No persons under the age of 16 should be allowed to operate the equipment.
The following safety features are designed to offer a reasonable measure of protection against injury while maintaining an operator-friendly machine. Please do not attempt to disable or alter their functionality in any way. Any modifications will void the
warranty and pose a serious risk to the operator. Contact Drytac Technical Services if any malfunction of the equipment occurs and stop using the machine immediately!
Models are equipped with an electric eye in front of the roller Nip which, when interrupted, will stop the rollers immediately and sound a buzzer as a warning to indicate that an object is breaking the photocell circuit. This occurs when t he mode switch is set to “Auto”. Please be particularly cautious when operating the JetMounter ™ in the Foot Pedal mode because in this mode the rollers WILL NOT STOP when the photocells are interrupted. An audible alarm will sound, but the rollers will continue to turn at a reduced speed.
Prior to operating the laminator, always check that the photocell and buzzer are working properly. Select the Auto mode and use a piece of cardboard to block the photocells to confirm that the alarm sounds and the rollers stop.
8
All JetMounter s are also equipped with red Emergency Stop buttons located on the top on one or both sides of the laminator. The Emergency Stop button will stop the machine instantly. Stopping the machine in the Foot mode can also be accomplished by lifting your foot off the pedal, turning the speed to zero (0) OR turning off the power switch.
DO NOT operate this equipment when you are alone. As with all motorized equipment, it is advisable that other adults be present to assist if required.
DO NOT operate the JetMounter ™ while under the influence of alcohol, prescription drugs or any other substance that could impair your judgment or reaction time.
Remove any jewelry such as rings, bracelets and necklaces prior to operating the equipment. Keep loose clothing, neckties, artificial fingernails, long hair and anything else that might easily be drawn into the rollers away from the machine.
Turn the JetMounter ™ power OFF if you are loading adhesives or film, cleaning the rollers or performing other activities that require close proximity of your fingers to the Nip. This will avoid the possibility of inadvertently starting the machine. Keep all safety guards in place and your fingers away from the Nip area when the machine is operating.
Always work at a slow speed until you become familiar with the machine.
Exercise caution when lifting rolls of laminate and adhesive due to their weight. Use assistance to avoid personal injury or damage to the equipment and materials.
9
Prior to lifting a supply shaft into the laminator, position the T-Slot in the hub on the machine‟s right side to receive the shaft. The use of an assistant is strongly recommended.
Always disconnect the laminator from the power supply before removing any panels for service.
When using a large supply roll, be aware that a pinch hazard can exist between the top roller and the supply shaft. When working from the rear of the laminator the operator must be aware of the Nip point of the contacting rollers and exercise extreme caution to avoid injury.
The sound pressure level this machine generates at the operators‟ position is less than
70dB.
Keep this manual near the machine for future reference. Also check our website for any additional or updated safety information. (www.drytac.com)
An instructional DVD and a demonstration/training session from a Drytac representative are also available so you can become familiar with all the features of your new JetMounter ™ .
Contact our Customer Service Department for details or if you have any questions about the operation of this equipment. (Contact information can be found on page 30).
Specific Moving Instructions:
The Drytac JetMounter ™ 44 and 54 should be handled with care to avoid personal injury or collateral damage.
Whenever the machine is moved, we strongly recommend utilizing at least two people. The adage: “Better safe than sorry,” applies here.
The JetMounter ™ stands are designed with fixed wheels on one side and lockable swivel casters on the other for a very good reason. When moving the machine, the movers should be positioned at both sides. Do not push the JetMounter ™ from the front or
back! This eliminates the possibility of having the machine tip over onto the mover or their helper.
10
Unpacking and Installation
Upon receipt of your new JetMounter ™ , inspect the carton(s) carefully for signs of physical damage or mishandling. Report any damage to the shipping company immediately and contact Drytac Corporation if replacement parts are needed. If no damage is apparent, proceed with the unpacking.
It is recommended that two people unpack the JM18, JM 26 and
JM34 to avoid damage to the equipment or personal injury. To unpack the JM44 and 54 you must follow the instructions affixed to the top of the crate in the sequence described. If the instructions are missing be sure to contact Drytac Technical Services before attempting to unpack or install the machine.
Due to the weight of the JM44 and JM54 laminators a hoist or suitable lift must be used to position the machine on an appropriate table or stand.
Select a clean, well-lighted working area that allows access to both the front and back of the machine. Position the machine on a level, sturdy surface that can support the weight of the machine and is at an optimum working height for the operator. (See Technical Specifications
Chart on page 30 for individual weight and size dimensions). The JM 44‟s and JM54‟s are available with optional stands that have casters for ease of movement as well as a storage rack for preloaded supply shafts.
JetMounter ™ laminators, depending on the country in which the machine was purchased, a re supplied in either a 115 VAC or 230 VAC versions. The power requirements for your particular machine are marked on the rear panel adjacent to the power connector. Please confirm that you have the correct power source available at the chosen location. If there are any questions about electrical requirements for the equipment, please contact a qualified electrician prior to attempting to power up the machine! Be absolutely certain that the voltage supplied at the outlet corresponds with the voltage marked on the plate attached to your machine. Do not rely on the cord or outlet configuration to determine the correct power supply voltage!
ALLOW ENOUGH WORKSPACE AROUND THE MACHINE TO BE ABLE
TO FEED AND REMOVE YOUR WORKPIECE SAFELY!
11
It is recommended that the machine be placed so that at least three feet of space from the front and back beyond the largest piece of material you will use be provided to insure adequate accessibility and safety. For example, if your work piece were a four-foot by eightfoot foam board, you would need to allow a minimum of eleven feet of space in front and eleven feet of space in the rear of your machine. Always consider this rule a necessity prior to beginning your work. (Converted figures in the illustration below in metric are 3 meters and .6 meter).
JetMounter ™
Components
1. The main On-Off switch is a rocker switch located on the back of the machine near the power cord entry . This switch should be in the “OFF” position when loading or unloading adhesives or film, cleaning the rollers or performing other activities that require close proximity of your fingers to the Nip.
2. The Auto/Foot/Reset switch. This two-position rocker switch on the front control panel is used to choose the mode of operation between “Foot” and “Auto”. The photocell safety feature functions differently in each position. It is important to review the safety information prior to selecting the mode of operation. This switch also serves as a Reset.
Upon powering up the machine, when the photocell is tripped or one of the Emergency
Stops has been activated, you must toggle the switch before proceeding. Be sure to first remove the obstruction, reposition the emergency stop or correct the cause for the shut down in order to effectively Reset the machine. If the shut down was caused by a thermal overload condition, you must first allow the circuit breaker on the back of the machine to cool (approximately 20-30 seconds), then reset the breaker and then reset the machine by toggling the Auto/Foot/Reset switch.
12
Original JM44/JM54 Control Panel JM44/44SHA/54/54SHA Push Button
Control Panel
3. The Foot Pedal switch should be positioned on the floor within easy reach of the operator. It is used to activate the roller when the Auto/Foot switch is in the “Foot” mode. NOTE: The Foot Pedal acts as a safety device. When the mode switch is set to the Foot position, the laminator will not operate unless the Foot Pedal is depressed.
4. On the original front control panel, the Forward/Reverse rocker switch is used to select the direction of the roller rotation. Upon start up, place the switch in the “OFF” position.
On the models with the push button control panel, simply push the desired button to initiate roller movement.
Reverse only operates in Foot mode.
5. The Speed Control switch. Rotating the knob to the right will increase the speed of the roller in either “Foot” or “Auto” mode. Upon start up, rotate the knob all the way to the left to the off position.
6. The Pressure Control Knobs are located on the top of each side. They adjust the top roller height and pressure. Rotate both Pressure Control Knobs counter-clockwise to raise the top roller. (See “Setting Roller Pressure” to adjust the pressure properly). On the SHA (Single Height Adjustment) models, the single hand wheel is located on the right end case. Simply turn the hand wheel to raise or lower the top roller. The LED readouts on the SHA, (located either on the top or the front of the right end case), will show the roller height in millimeters and the pressure on a bar graph as percentage.
7. The Supply Shaft holds the adhesive or laminate material, while the Take Up or windup shaft holds the release liner.
13
When either of the shafts is installed, the T-slot end must be oriented properly to fit in the drive mechanism located on the right end of the machine, as you face it from the front. The operator and the assistant should consider this prior to lifting the loaded shaft into position.
Once in position, be alert to the possible pinch hazard at the left or un-driven end.
14
Setting Roller Pressure
This procedure begins with the main power switch off, the mode switch set to Auto, the directional switch set to the OFF position and the speed knob fully counterclockwise. The following steps apply to setting the roller pressure ONLY on models with dual pressure sets.
1. Rotate both Pressure Control Knobs counterclockwise to raise the top roller.
2. Slide a section of the mounting board into the roller Nip.
3. Rotate both Pressure Control Knobs clockwise to lower the top roller until it makes light contact with the mounting board.
4. Turn the main switch to the ON position; the power indicator light will come on.
5. Turn the mode switch to the Foot position.
6. Turn the Forward/Reverse switch to the Reverse position.
7. Depress the Foot Pedal.
8. Slowly turn the Speed Control knob to remove the board from the rollers (reverse).
9. Switch the Forward/Reverse switch to the OFF position.
10. For optimal results, rotate both Pressure Control knobs approximately 1/8 of a turn clockwise to slightly lower the roller (after the board has been removed).
15
Supply/ Unwind
Tensioner
Wind up/Take up
Tensioner
Hand Wheel
Height Adjust
JM54 Single Height Adjustment (SHA)
JM44SHA/ JM54SHA Roller Pressure Adjustment
The nip gap is the space between the upper and lower main rollers. Both the nip gap and the processing pressure are controlled by the Height Adjust Hand Wheel, which raises or lowers the upper roller. The Hand Wheel is located on the end of the right cabinet. The upper roller height should be adjusted according to the images or substrates being processed.
Overlaminating and Encapsulation: To process thin images the nip gap should be closed with the pressure set to 40%.
Mounting: When mounting on substrates the nip gap should be set to the thickness of the substrate by turning the Hand Wheel. The leading edge of the substrate should be inserted and the pressure set according to the density of the substrate. Hard substrates such as
Masonite® or Sintra® should be set to 40% to 60%. In order to avoid compressing soft substrates such as foamboard pressure should be set from 10% to 30%.
16
Narrow Graphics: Usually narrow graphics take less pressure to apply the image or laminate correctly.
Checking Roller Parallelism:
C ut two 2”x4” strips of paper or cardstock of the same thickness. Raise the upper roller and insert the strips of pap er between the upper and lower rollers about 2” from each end. Lower the upper roller until it just contacts one of the strips of paper. There should be resistance while pulling the paper out from between the roller, but it should not turn the roller. Check the strip of paper on the other end of the roller and it should have the exact same resistance while sliding it in and out of the roller. If the resistance is less on one side than the other, the rollers should be paralleled. (See Appendix for detailed procedure.)
Adjusting Shaft Tensions on JM44 and JM54 Models:
JetMounter ™ JM44 and JM54 models are equipped with a motorized Take Up shaft on the front of the machine. This shaft winds up the release liner from mounting adhesive and overlaminating film rolls during processing. Also on these models, both the Take Up haft and the Supply shaft are equipped with Tension Control Knobs. By adjusting these knobs you control the speed of the shafts as they unwind or wind up material.
It is important to adjust these settings so that there is an even tension on the adhesive or film during processing. The objective is to apply enough resistance on the film to keep it firm and flat, but not so much as to stretch or distort it. It is also critical to maintain even tension
settings on both sides of the film. Turn the Tension Control Knobs clockwise to increase roll tension and counter-clockwise to reduce tension.
Supply shaft tension: When feeding adhesive or film into the rollers, the primary objective is to maintain the feed at the same rate as the rollers pull the material through the Nip.
Take Up shaft tension: The Release Liner should be pulled away from the adhesive at a steady rate that allows it to “lift” at a point just before the material enters the Nip.
17
Mounting with
JetMounter
™
Laminators
Mounting Board (Substrate) Selection:
The selection of a proper mounting board/substrate is very important. Common materials used are:
• Foam Boards: (FomeCor®, GatorBoard®, HartBoard® etc.)
• Illustration Board
• Rag Board
• MDF (medium density fiberboard)
• Corrugated plastic boards: CoroPlast®
• Rigid Plastic Boards (Sintra®, styrene, etc.)
• Tempered hardboard: Masonite®
Adhesive Selection
Once the mounting board has been selected, determine whether to pre-coat the material with adhesive or to purchase pre-cut and pre-coated boards. While the use of pre-cut, pre-coated materials will save time, coating your own mounting board is more economical and allows for maximum flexibility in terms of sizing and substrate selection.
Pre-coating the Mounting Board
Pre-coating a mounting board means applying a mounting adhesive to one side of the board so that a graphic image can be mounted to the board later). The use of a Leader Board is recommended for this process.
1. Adjust rollers for proper pressure (see pages 15-16).
2. Load the roll of PSA (pressure-sensitive adhesive) onto the Supply shaft so that the material can be pulled toward the user from the underside of the roll with the adhesive side facing UP (the release liner side should be in contact with the roller as shown in the
Illustration).
3. Pull the adhesive off of the roll so that about 4” lies flat on the worktable and is draped in front of the rollers.
18
6.
4. Lay your Leader Board on top of the exposed adhesive material on the worktable; then push the Leader Board and adhesive into the Nip (the „Nip‟ of your laminator is the point where the rollers make contact). When pushing the Leader Board into the adhesive, make sure it is parallel to the rollers.
5. Position your first mounting board behind and against the Leader Board. Check for proper alignment, and feed through the rollers (in either AUTO mode or via FOOT switch). Feed one board after another as needed.
Trim the excess adhesive off of the board.
6. Your mounting boards are now pre-coated with pressure-sensitive adhesive, which is still protected by the release paper. The pre-coated boards can be used for immediate mounting or stored for future use.
TIP: When an image is going to be laminated with a gloss overlaminating film, the use of very smooth substrates with glossy surfaces (such as Masonite®) is preferred. This will minimize the effect of board imperfections, (i.e. “orange peel”) in the finished product.
19
For models JM44 and JM54, adjust the Supply shaft tension properly (page 17).
NOTE: We recommend placing a „Tail Board‟ behind the last production board (this can be the same board used as a leader board/starting panel). This is especially important when pre-coating foam board.
Mounting a Graphic to a Pre-Coated Board
1. Adjust the rollers for proper pressure (see Page 17).
2. Expose the adhesive on the board by folding back approximately 1” (2.5cm) of the release liner.
3. Using the folded-back release paper as a temporary support bridge, align the print onto the board and then proceed to “tack” (stick or press down) the leading edge of the print onto the exposed adhesive.
4. Run a Leader Board of the same thickness as your mounting board through the rollers so that the back edge of the Leader Board is at the nip of your machine.
20
5. Square your mounting board with the tacked print against the edge of the Leader Board and drape the print over the top roller.
6. Run the mounting board/adhesive/image through the rollers while simultaneously pulling the release liner away from and off of the board.
(JM44 and JM54 models have automatic Take Up shafts on the front of the chassis. You may choose to unwind the Release Liner onto the Take Up shaft during this process, rather than pulling it by hand. See page 17 for information on setting the Take Up Shaft tension).
L a m inating with
JetMounter ™
Laminators
Selecting a Laminating Film
Select an appropriate overlaminating film for the surface of your image based on aesthetics and the conditions under which it will be displayed. Drytac offers a wide variety of films to match your specific output and application. Please consult your Drytac catalog for descriptions of available film choices.
There are several types of laminating jobs that can be performed on JetMounter ™ laminators. The following are the most common applications. To prevent adhesives from sticking to the rollers and to provide a reusable, standard working surface, the use of a siliconecoated board (also known as a “Carrier Board”) is highly recommended. (See page
26 for instructions).
21
Laminating a Single Unmounted Image
Before processing, make sure that the image is clean and free of dust or specks of lint (an
Anti-Static cloth or Anti-Static Wisk is recommended for this purpose).
1. Raise the top roller and insert the Carrier Board. Set roller pressure as described on pages 15-16.
2. Pre-cut a sheet of overlaminating film from the roll. (The sheet should be larger than the image by approximately 1” on each side and bottom, and 2” on the top).
3. Peel and fold back approximately 2” of release liner from the top edge of the overlaminating film. Tack the film on the Carrier Board by pressing the exposed section of film onto the leading edge of the board.
4. Start the Carrier Board into your laminator using the Foot Pedal mode. Stop before the edge of the laminating film reaches the rollers.
5. Lift up the remainder of the overlaminating film (which is still protected by the release liner) and slide the image face up underneath it. Stop before it makes contact with the exposed part of the adhesive. It is important to keep the film adhesive away from the artwork until the whole assembly is under pressure and traveling through the
JetMounter
™
.
22
6. Lay the laminating film over the top of the upper roller. While holding up the edge of the peeled back release liner with one hand, start the rollers and apply the overlaminating film to the surface of the image. Pull up and away on the release paper as your work piece travels through the laminator. Ensure that the release paper does not reach the point where the image makes contact with the top roller. Be sure to complete this step with a consistent motion and do not stop until the entire image has passed through the rollers.
7. The laminated image can now be easily removed from the silicone-coated Carrier Board for trimming and mounting.
L a m inating a Single Mounted Im age
Before processing, make sure that the images are clean and free of dust or specks of lint (an
Anti-Static cloth or Anti-Static Wisk is recommended for this purpose).
1. Raise the top roller and insert the mounted image into the roller Nip. Adjust the roller pressure as described on pages 15-16.
2. Pre-cut a sheet of overlaminating film from the roll. The sheet should be larger than the image by approximately 1/4” on the sides and bottom and 3” longer on the top.
3. Peel and fold back 2” of release paper liner exposing the adhesive of the laminating film.
4. Tack approximately 11/2” of the laminating film to the Leader Board, but not over the mounted image.
5. Insert the Leader Board with the laminating film tacked to it into the Nip. Advance the
Leader Board and the film through the Nip until the upper laminating roller securely pinches the film. (The trailing edge of the Leader Board should be at the pinch point of the rollers.)
6. Lay the laminating film over the top of the upper laminating roller. Make sure that the folded release paper liner is easily accessible.
23
7. Slide the mounted image into the Nip area and allow its edge to make contact with the edge of the Leader Board.
8. While holding up the folded edge of the peeled back release paper with one hand, start the rollers and apply the laminating film to the surface of the image. Pull up and away on the release liner as you advance to ensure that the liner does not reach the Nip area.
Process your work with a consistent motion and do not stop until the entire image has passed through the rollers.
9. Trim excess overlaminating film from the edges of the image.
L a m inating Multiple Mounted Im age s
1. For higher volume jobs, select a roll of laminating film slightly wider than the mounted images you intend to laminate.
2. Install the overlaminating film on the Supply shaft so that the material can be pulled toward the user from the bottom of the roll with the Release Liner side facing up.
3. Adjust the rollers for proper pressure (see pages 15-16).
4. Pull several inches of the overlaminating film off the roll. Separate the overlaminating film from its release liner (approximately 34”) and drape it onto the in-feed table in front of the rollers. Keep the release liner away from the film while pushing the Leader Board and film into the roller Nip.
24
5. Position the first mounted image to be laminated against the back of the Leader Board.
Check for proper alignment, and feed through the rollers of your laminator (in Auto mode or with foot pedal). Feed one print in right after another, as needed.
6. Carefully separate prints with a razor blade or utility knife. Trim off the excess film.
JM44 and JM54 models have automatic Take Up shafts on the front of the chassis. You may choose to unwind the Release Liner onto the Take Up shaft during this process, rather than pulling it by hand. (See page 17 for information on setting Take Up Shaft tension).
Us ing a L eader B oard
A Lead er Board (also referred to as a “starting panel”) is recommended for use when mounting and laminating with JetMounter ™ laminators. A Leader Board is fed into the roller
Nip first, followed by the actual mounting/laminating project to be processed. We highly recommend this tool to help set proper pressure for both mounting and laminating prior to processing your work.
The Leader Board should be the same width and thickness of your production mounting board and about 68” long. You should also make a Tail Board, which is used behind the last production board. The Tail Board is especially recommended for mounting to foam board.
25
Carrier Board s
When processing un-mounted images, we recommend you use a silicone-coated board to prevent adhesives from sticking to the rollers. This board is called a Carrier Board, and it provides a re-usable, standard working surface. It will be used when laminating your image prior to mounting it onto a mounting board/substrate. It is common practice for finishing professionals to stock Carrier Boards in several different sizes to accommodate various artwork formats.
Manufacturing Carrier Boards
Making a Carrier Board is basically the same process as pre-coating a mounting board.
Instructions for this process are found on page 15. When the mount board is coated with the adhesive, the silicone-coated release liner provides a slick, non-stick surface on which to laminate images. Be sure to use a “self-wound” adhesive with a silicone treated liner for this purpose.
2: Preparing Mounting Boards
Preparing Mounting Boards
Once you have decided on the most appropriate adhesive/mounting board combination for your application, it is important that you properly prepare your board before coating.
Although often overlooked, this can be the most important step when mounting a print or artwork for display.
Foam Boards
(E.G. FOME-COR®, ETC.)
The surface of these types of substrates is porous and often contains particles that can spoil an otherwise perfect mount. Clay-coated surfaces such as Fome-Cor®, Foam-X® and similar boards should simply be wiped with a Tac
Cloth™ to remove dust particles.
Mat Boards/Mill Boards
To prepare mat board or mill board for mounting, use the AntiStatic Wisk™ brush to remove dust particles and other debris.
Hardboard
(E.G. MEDIUM DENSITY FIBERBOARD, MASONITE, ETC.)
26
To prepare hardboard substrates for mounting, wipe down the surface with a TacCloth. If the surface contains irregularities, use sandpaper to remove them, and then wipe the surface with a Tac Cloth.
Please note: Due to their highly absorbent properties, do not wipe down the surfaces of any of these substrates (i.e. foam board, mat/millboard or hardboard) with a moist rag.
Use a Tac Cloth to wipe down foam board.
Tip: It is important that you remove dust and other debris from your prints prior to mounting.
Care and Maintenan c e
CAUTION: Unplug the machine before performing any service or maintenance.
Cleaning: In order for your JetMounter ™ to operate efficiently, be sure to clean it
regularly with a soft cloth. A neutral mixture of soap and water can be used for this purpose. To remove heavy dirt and adhesive residue we suggest the use of 99% isopropyl alcohol.
Do not use thinner or a metal brush to clean the rollers.
Rollers: In order to extend the life of your JetMounter ™ laminator it is strongly recommended that the rollers be separated when the machine is not in use.
Fuses: There are two replaceable fuses on your JetMounter ™ located on the rear panel where the power cord enters the machine. One is actually in the power cord receptacle. The other is in a separate holder next to the power cord. Fuses are
5x20mm 1, 2 or 8 Amp depending on the particular machines‟ voltage requirements.
The use of any other fuse may endanger the operator and/or machine and invalidate the warranty.
Lubrication: Lubricate the drive chain located behind the right hand end cover every
27
Servi c e
six months, with a premium brand chain lubricant. Disconnect power before lubricating the chain.
No other parts require lubrication.
Before contacting Drytac for service assistance, please double-check to make sure that the
JetMounter ™ is still connected to a live power outlet. Next, check both fuses. For further troubleshooting assistance, please contact Drytac Technical Services. See Contact
Information on page 30.
Our Drytac Facility in Toronto, Canada
28
JetMounter
TM
18- 54 TECHNICAL SPECIFICATIONS
Specification JM18 JM26 JM34 JM44/JM44SHA JM54/JM54SHA
Roller Width
Roller
Diameter
Roller
Construction
Width
Depth
Height
18.25”/46.4 cm
2.5”/ 6.35 cm
25.5”/64.8 cm
11.75”/29.9 cm
13”/33.0 cm
26.25”/ 66.7 cm
2.4”/ 6.1 cm
44.50”/ 113.0 cm
4”/ 10.2 cm
Steel-with high-release silicone covering.
33.25”/ 84.5 cm
12.2”/ 31 cm
12.2”/ 31 cm
TBA
TBA
TBA
TBA
TBA
61”/ 154.9 cm
19”/ 48 cm
19”/ 48 cm
54.50”/ 134.4 cm
5”/ 12.7 cm
70.5”/ 179.1 cm
19”/ 48 cm
19”/ 48 cm
Weight
Max. Opening
*Non
Photocell
Photocell
Max. Material
Diameter
Power
Requirements
Speed Range
51 lbs/23 kg
*0.375”/ 0.95 cm
.75” / 1.9 cm
8.0/20.32 cm
53 lbs/24 kg
*0.375”/ 0.95 cm
.75” / 1.9 cm
10”/ 25.4 cm
TBA
TBA
TBA
243 lbs/110 kg
1”/ 2.5 cm
10 “/ 25.4 cm
331 lbs/ 150 kg
1”/ 2.5 cm
10”/ 25.4 cm
2.5
–18 fpm /
0.8-3.0 mpm
3”/ 7.6 cm
115 VAC or 230 VAC 50/60 Hz
2.5
–18 fpm /
0.8-3.0 mpm
3”/ 7.6 cm
TBA
TBA
3 –10 fpm /
0.9-3.0 mpm
3”/ 7.6 cm
2 –10 fpm /
0.9-3.0 mpm
3”/ 7.6 cm Core Size
Power
Consumption
Fuse
Specifications
Weight
Width
Depth
Height
50W
30”/ 76 cm
One 1A for Europe or 2A for North America in the power receptacle.
One 8A in adjacent holder. Both are 5x20mm Fast-Acting glass fuses.
PACKAGED FOR SHIPMENT
57 lbs/ 25.8 kg 58.5 lbs/ 26.5 kg
37.5”/ 95.25 cm
TBA
TBA
287 lbs/ 130.2 kg
66”/ 167.6 cm
390 lbs/ 176.9 kg
403 lbs/ 182.8 kg
76”/ 193 cm
15”/ 38 cm 15”/ 38 cm 15”/ 38 cm 23.5”/ 59.7 cm 23.5”/ 59.7 cm
15”/ 38 cm 15”/ 38 cm 15”/ 38 cm 25”/ 63.5 cm 25”/ 63.5 cm
13-08-10
Notes: 1) The JetMounter
TM
Stands are 29.7” (75.5 cm) tall, making the overall height of the assembled unit 48.7” (123.7 cm). On a JM44/54 attached to a stand, the distance from the floor to the feed table is 34.58” (878.33 cm). 2) The JM44SHA and JM54SHA comes with a Front Feed
Tray assembly inside the crate.
29
CONTACT INFORMATION
Drytac Corporation (USA)
5383 Glen Alden Drive
Richmond, VA 23231
Toll Free Phone: 800-280-6013
Toll Free Fax: 800-622-8839
E-mail: [email protected]
Drytac Canada, Inc.
220 Caldari Road
Concord, Ontario
Canada L4K 4L1
Toll Free Phone: 800-353-2883
Toll Free Fax: 877-437-9822
E-mail: [email protected]
JetMounter ™
Registration Information
Drytac Europe (UK)
Filwood Road, Fishponds
Bristol BS16 3RY, United Kingdom
Phone: +44 (0) 117-958-6500
UK Toll Free Phone: 0845-070-0660
E-mail: [email protected]
C OMPANY N AME :
A DDRESS :
C ITY / S TATE :
M ODEL #:
S ERIAL #:
P URCHASE D ATE :
W ARRANTY C ARD R ETURNED ON : BY:
30
WARRANTY
We thank you for your purchase of the JetMounter ™ laminator and want to assure you that we will do our best to see that your experience with your new machine is a positive one.
Every Drytac machine is designed and manufactured to give many years of dependable service.
To achieve the best results from your JetMounter ™ , the machine should be set up and operated in accordance with the instructions included in this manual.
Should the original JetMounter ™ purchaser experience any problem due to faulty materials or workmanship within 12 months of the purchase date, Drytac or their dealer will arrange for the machine to be repaired, replaced or refunded at Drytac‟s discretion.
After the warranty period has elapsed, Drytac will provide all reasonable assistance and product support to resolve any problems that may arise.
Please return your warranty card as soon as possible. This will help us more efficiently assist with any problem you may encounter. You will find a section for recording this important information for your records and any future parts or service requests on page 30 of this manual.
Normal wear and tear, any damage to the silicone rollers, damage due to abuse, improper operation or installation is not covered by this warranty. Conditions that will void the warranty include, but are not limited to: failure to follow the instructions contained in this manual, unauthorized changes or modifications to the machine or the stand (where applicable) in any manner or misuse of the machine for purposes other than specified in the
Operators Manual. Drytac will not be responsible for any damage or consequential damage caused by the machine.
Please feel free to contact Drytac if you have any questions or problems.
Before calling Drytac Technical Services, complete the JetMounter ™ Registration
Information on the previous page and have it available for reference.
31
Appendix A
Replacement Parts for the JetMounter ™ Laminators
Parts Applicable to Most Models Part Number
Pressure/Tension Knob
Speed Control Switch with Knob
Motor Switch, Fwd./Rev
Mode/Reset Switch
On/Off Switch
Power Cord
JMS-01
JMS-03
JMS-04
JMS-05
JMS-09
JMS-10, JMS-10E for European
JMS-10UK for UK application
JM 18/26/34 Parts
JM 8 Silicone Roller
JM 8 Roll Shaft
Core Adapter for JM 18/26/34
Foot Control for JM 18/26/34
Part Number
JMS UK fo
JMS1-01
JMS1-02
JMS12-03
JMS12-04
JMS2-01
JMS2-02
JM26 Silicone Roller
JM26 Roll Shaft
JM44 Parts
Silicone Roller
Supply Shaft
JM54 Parts
Silicone Roller
Part Number
JMS4-01
JMS4-03
Part Number
Supply Shaft
JM44/54 Parts
1A Fuse- European Models
2A Fuse- All Other Models
8A Fuse- All Models
JMS5-01
JMS5-03
Part Number
JMS45-04
JMS45-02
JMS45-03
Pressure Adjustment Handle JMS45-13
Circuit Breaker JMS45-15
The list above does not include all service parts available. For further parts or service information please contact Drytac Technical Services (see page 30 for Contact Information).
32
Appendix B
One of the reasons Drytac has earned a reputation for unmatched customer service is that we value our customers‟ opinions. The JetMounter™ has evolved in response to such input from the field. Our B Revision JetMounters, for example, have push button control panels with a redesigned user interface. The following chart is provided as a quick-reference guide.
AUTO MODE
Power Up or E-Stops Reset
FWD button pressed
Photocell interrupted
Photocell cleared
E-Stops Activated
ACTION
B Revision Functions
PROGRAMMED SOFTWARE FUNCTIONS
Alarm Photocell LED
Press and Hold Rev. Button JM63/JM44-54
FOOT MODE
FOOT pedal pressed, FWD mode
Photocell interrupted. FP still depressed
Photocell cleared. FP still depressed.
Photocell cleared. FP dep. Switch to Auto
FOOT pedal released
Restart by FP, no buttons pressed
Press and hold REV in Foot Mode,
Release REV button while depress FP
In Rev. with Foot on pedal- press AUTO
Table Down, FOOT pedal released. (JM63 only)
Table Down, FOOT pedal pressed. (JM63 only)
Operation
Will not Run
Needs Reset
Normal operation at set speed
Machine stops
Ready to start
Will not Run
Jog speed Rev./
Will not run
Set speed, FWD
Jog mode
Jog mode
FWD at set speed
Machine stops
Set speed FWD
Jog mode REV
Jog mode REV
Machine Stops,
Ready to start
Will not Run
Jog mode
No Yellow
No Green
Yes Flash Red
No
No
Green
Flash Yellow
Yes REV Green
No Green
Yes Flash Red
No Green
No
No
No
Green
Green
Green
Yes REV Green
Yes REV Green
No Green
No Flash Green
Yes Flash Green
33
Appendix C
TECHNICAL SERVICES DEPARTMENT
JM44 SHA/JM54SHA Nip Adjustment Procedure
1. Checking Roller Parallelism:
C ut two 2”x4” strips of paper or cardstock of the same thickness. Raise the upper roller and insert the stri ps of paper between the upper and lower rollers about 2” from each end. Lower the upper roller until it just contacts one of the strips of paper. There should be resistance while pulling the paper out from between the roller but it should not turn the roller. Check the strip of paper on the other end of the roller and it should have the exact same resistance while sliding it in and out of the roller. If the resistance is less on one side than the other, the rollers should be adjusted.
2. To make this adjustment, keep the strips of paper in the nip between the rollers 2” from each end. The necessary adjustments are made on the left end to avoid altering the pressure and height sensors on the right end. (The hand wheel and end panels must be removed to access the following adjustment points. Once the end panels are removed, the hand wheel can then be reinstalled to complete the procedure.) Lower the upper roller until it touches the strip on the right side of the machine. There should be resistance while pulling the strip, but the roller should not turn. Compare the amount of resistance on the left, using the same effort to pull the left strip of paper.
3. Locate the cross bar that goes across the top of the machine between the cabinets with a plate on each end that has 4 set screws on each plate and 2 mounting bolts coming from the inside of the cabinet. On the left side, loosen the four set screws in the plate (accessible from the outside) and the two mounting bolts (accessible from the inside). Inside the left end case you will see the two gears that raise and lower the upper roller at the top of the vertical height adjusting shaft. Slide the bar and plate toward the front of the machine disengaging the two gears. Adjust the roller height using the vertical height adjusting shaft which turns the larger (driven) gear. Rotate the shaft in the direction that will raise or lower the left end of the roller to achieve the same resistance on the left paper strip as the strip on the right side.
When the correct height is achieved, slide the cross bar and plate toward the rear of the machine to reengage the gears. Do not jam them together with force, but leave enough play for smooth operation. Tighten the two plate mounting bolts and then turn the four set screws until they are just snug. Double check the gap between the rollers with the paper strips.
Raise and lower the roller to make sure the hand wheel raises and lowers the roller
34
smoothly. If there is binding while cranking the rollers, the set screws can be used to adjust the plate. The plate gears and bar all need to be square so there is minimal resistance.
4. Setting the Working Pressure:
In the right and left cabinets where the upper roller comes through, there is a stack of spring washers used to provide the correct amount of application pressure. Raise the upper roller so that there is at least a 1/8” gap between the rollers. Bring jam nut #1 (see drawing below) up so that the stack of spring washers just touch the bracket and back off one full turn. Bring jam nut #2 up against nut #1 to lock them in place. Inspect the pressure readings. While the roller is up the 0% or first light should be lit on the pressure read out. If the light is not lit, locate the main circuit board inside the right cabinet. There is a small potentiometer (small blue square box with a screw adjustment located on the top) on the board that can be used to adjust the starting point where the light comes on. Lower the upper roller, the 20% or second light should come on when the rollers are just contacting. You will start to get flat rollers at 40%. Continue to crank the hand wheel until full pressure is achieved at 100% making certain all lights are operating.
Confirm that the height sensor is adjusted properly by comparing the nip opening with the figure on the digital readout. If adjustment is needed, loosen the mounting screws on the height sensor and position as required.
35
advertisement
* Your assessment is very important for improving the workof artificial intelligence, which forms the content of this project
Related manuals
advertisement