- Home
- Domestic appliances
- Climate control
- Temperature & humidity sensors
- Mettler Toledo
- conductivity transmitter CondI7100-PA
- Operating instructions
Mettler Toledo conductivity transmitter CondI7100-PA Operating Instruction
Add to My manualsadvertisement
◉
Touch to zoom
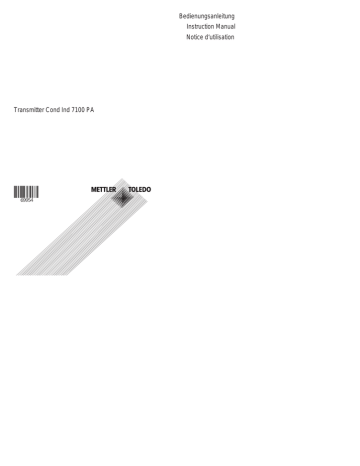
Bedienungsanleitung Instruction Manual Notice d‘utilisation Transmitter Cond Ind 7100 PA Deutsch Mettler-Toledo GmbH Process Analytics Im Hackacker 15, P.O. Box CH-8902 Urdorf Switzerland Phone: +41-1-736 22 11 Fax: +41-1-736 26 36 www.mtpro.com Gewährleistung Innerhalb von 1 Jahr ab Lieferung auftretende Mängel werden bei freier Anlieferung im Werk kostenlos behoben. Softwareversion: 2.x Stand Bedienungsanleitung: 06.06.2005 Warranty Defects occurring within 1 year from delivery date shall be remedied free of charge at our plant (carriage and insurance paid by sender). Software release: 2.x Date of issue: June 6, 2005 Garantie Tout défaut constaté dans les 1 an à dater de la livraison sera réparé gratuitement dans notre usine à réception franco de l‘appareil. Version logiciel : 2.x Version du mode d‘emploi : 06.06.2005 TA-194.360-MTX02 Contents Information on this instruction manual . . . . . . . . . . . . . . E-3 7 Markings . . . . . . . . . . . . . . . . . . . . . . . . . . . . . . . . . . . . . E-3 2 Safety information . . . . . . . . . . . . . . . . . . . . . . . . . . . . . . . E-4 Checklist . . . . . . . . . . . . . . . . . . . . . . . . . . . . . . . . . . . .E-21 8 Be sure to read and observe the following instructions!. E-4 3 Operation using keypad on the device . . . . . . . . . . . . .E-23 PROFIBUS technology . . . . . . . . . . . . . . . . . . . . . . . . . . . E-5 Mode code . . . . . . . . . . . . . . . . . . . . . . . . . . . . . . . . . .E-25 Safety functions . . . . . . . . . . . . . . . . . . . . . . . . . . . . . .E-25 Variants and basic characteristics . . . . . . . . . . . . . . . . . E-5 Mode indicators. . . . . . . . . . . . . . . . . . . . . . . . . . . . . . .E-26 Definitions for PROFIBUS-PA. . . . . . . . . . . . . . . . . . . . E-6 Configuration. . . . . . . . . . . . . . . . . . . . . . . . . . . . . . . . .E-27 PROFIBUS-PA with the Transmitter . . . . . . . . . . . . . . . E-6 Calibration . . . . . . . . . . . . . . . . . . . . . . . . . . . . . . . . . . E-30 Description . . . . . . . . . . . . . . . . . . . . . . . . . . . . . . . . . . . . . E-7 Operating tool . . . . . . . . . . . . . . . . . . . . . . . . . . . . . . . E-36 Intended use . . . . . . . . . . . . . . . . . . . . . . . . . . . . . . . . . E-7 Measurement . . . . . . . . . . . . . . . . . . . . . . . . . . . . . . . .E-36 Technical features . . . . . . . . . . . . . . . . . . . . . . . . . . . . . E-7 Communication model . . . . . . . . . . . . . . . . . . . . . . . . . . E-8 9 6 Diagnostics . . . . . . . . . . . . . . . . . . . . . . . . . . . . . . . . . . . .E-37 Sensoface, Sensocheck . . . . . . . . . . . . . . . . . . . . . . . .E-37 Profile for Process Control Devices (extract) . . . . . . . . . E-9 5 Operation . . . . . . . . . . . . . . . . . . . . . . . . . . . . . . . . . . . . .E-22 Operation possibilities . . . . . . . . . . . . . . . . . . . . . . . . . .E-22 General . . . . . . . . . . . . . . . . . . . . . . . . . . . . . . . . . . . . . E-5 4 Commissioning . . . . . . . . . . . . . . . . . . . . . . . . . . . . . . . .E-21 PROFIBUS-PA limit monitoring . . . . . . . . . . . . . . . . . .E-37 Assembly . . . . . . . . . . . . . . . . . . . . . . . . . . . . . . . . . . . . . E-11 Error message . . . . . . . . . . . . . . . . . . . . . . . . . . . . . . . E-38 Package contents and unpacking . . . . . . . . . . . . . . . . E-11 Display messages and PROFIBUS communication . . E-40 Mounting plan. . . . . . . . . . . . . . . . . . . . . . . . . . . . . . . . E-12 Diagnostics functions . . . . . . . . . . . . . . . . . . . . . . . . . .E-42 Installation and connection . . . . . . . . . . . . . . . . . . . . . . E-15 10 Maintenance and Cleaning . . . . . . . . . . . . . . . . . . . . . . .E-45 Information on installation . . . . . . . . . . . . . . . . . . . . . . E-15 Maintenance . . . . . . . . . . . . . . . . . . . . . . . . . . . . . . . . .E-45 Terminal assignments . . . . . . . . . . . . . . . . . . . . . . . . . E-17 Cleaning . . . . . . . . . . . . . . . . . . . . . . . . . . . . . . . . . . . .E-45 Overview of the Transmitter . . . . . . . . . . . . . . . . . . . . . E-17 Typical wiring . . . . . . . . . . . . . . . . . . . . . . . . . . . . . . . . E-18 11 Appendix . . . . . . . . . . . . . . . . . . . . . . . . . . . . . . . . . . . . . .E-46 Product line . . . . . . . . . . . . . . . . . . . . . . . . . . . . . . . . . .E-46 Contents E-1 English 1 Specifications . . . . . . . . . . . . . . . . . . . . . . . . . . . . . . . .E-46 ATEX EC-Type-Examination Certificate . . . . . . . . . . . .E-51 Declaration of Conformity . . . . . . . . . . . . . . . . . . . . . . .E-54 FM Control Drawing . . . . . . . . . . . . . . . . . . . . . . . . . . .E-55 Sensors. . . . . . . . . . . . . . . . . . . . . . . . . . . . . . . . . . . . .E-56 Certificate of Conformity InPro 7250 Series. . . . . . . . .E-58 Calibration solutions . . . . . . . . . . . . . . . . . . . . . . . . . . .E-61 Concentration curves . . . . . . . . . . . . . . . . . . . . . . . . . .E-62 Glossary. . . . . . . . . . . . . . . . . . . . . . . . . . . . . . . . . . . . E-68 12 E-2 Index . . . . . . . . . . . . . . . . . . . . . . . . . . . . . . . . . . . . . . . . .E-69 Contents Information on this instruction manual 1.1 Markings The warning symbol means that the instructions given must always be followed for your own safety. Failure to follow these instructions may result in injuries Notes provide important information that should be strictly followed when using the device. Trademarks The following names are registered trademarks. For practical reasons they are shown without trademark symbol in this manual. - Registered trademarks - Sensocheck® Sensoface® GainCheck® InPro® When a key is shown, its function is explained. When a display is shown, the corresponding information or operating instructions are provided. Operating instructions • Each operating instruction is preceded by a dot. Enumerations - Each enumeration is preceded by a dash. Model designation For practical purposes, the Transmitter Cond Inc 7100 PA is simply referred to as Transmitter in this instruction manual. Information on this instruction manual E-3 English 1 2 Safety information 2.1 Be sure to read and observe the following instructions! The device has been designed in accordance with the state of the art and complying with the applicable safety regulations. When operating the device, certain conditions may nevertheless be dangerous for the operator or cause damage to the device. Whenever it is likely that protection has been impaired, the device shall be made inoperative and secured against unintended operation. The protection is likely to be impaired if, for example: For hazardous-area applications, the Transmitter may only be connected to explosion-proof segment couplers, power supplies, .... The Transmitter may be operated in accordance with the FISCO model. The stipulations of EN 60079 - 10 : 1996 and the following must be observed for the installation. - the device shows visible damage - the device fails to perform the intended measurements - after prolonged storage at temperatures above 70 ˚C - after severe transport stress Before recommissioning the device, a professional routine test in accordance with EN 61010-1 must be performed. This test should be carried out by the manufacturer. The Transmitter is approved for installa tion in ATEX, FM Zone 1 with measurement in Zone 0, and FM Class I Div 1. The electrodeless conductivity sensors of the InPro 7250 series are approved for operation in hazardous locations. Before commissioning it must be proved that the intrinsic safety is maintained when connecting the device to other equipment, such as segment coupler and cable. E-4 Safety information In hazardous locations the Transmitter may only be cleaned with a damp cloth to prevent electrostatic discharge. PROFIBUS technology 3.1 General PROFIBUS is a digital communication system that connects different field devices over a common cable and integrates them into a control system. In the long term, PROFIBUS will replace the 4-20 mA technology, which only supplies pure measured values. Advantages of the PROFIBUS technology are: - easy and cost-saving cabling - convenient operation over a central control station - transmission, evaluation and control of high amounts of data from field device to control station. 3.2 - devices installed in hazardous locations are configured and maintained from the control station PROFIBUS is the leading open fieldbus system in Europe. Its application range covers manufacturing, process and building automation. As open fieldbus standard to EN 50170, PROFIBUS ensures communication of different devices over one bus. The PROFIBUS User Organization provides for further development and maintenance of the PROFIBUS technology. It combines the interests of users and manufacturers. Variants and basic characteristics PROFIBUS determines the technical and functional characteristics of a serial bus system. There are three PROFIBUS variants: - PROFIBUS-FMS (FMS protocol) - is particularly suited for exchanging large amounts of data between control devices. It operates according to the RS 485 standard with transmission rates up to 12 MBits/sec. - PROFIBUS-DP (decentralized peripherals) - Masters - control the data traffic on the bus. They send messages without external request. - Slaves - are peripheral devices such as valves, drives, transmitters and analyzers. They can react acyclically to servicing, configuration and diagnostic tasks of the master. The central controller cyclically reads the measurement data with status. - is tailored for communication of automation systems and distributed peripherals. It operates according to the RS 485 standard with transmission rates up to 12 MBits/sec. - PROFIBUS-PA (process automation) - is dedicated to the process industry. It permits connection of sensors and actuators to a common bus even in hazardous locations. PROFIBUS-PA has a transmission rate of 31.25 kBits/sec. PROFIBUS distinguishes between two types of devices: PROFIBUS technology E-5 English 3 3.3 Definitions for PROFIBUS-PA The bus protocol defines type and speed of the data exchange between master and slave devices and determines the transmission protocol of the respective PROFIBUS system. PROFIBUS-PA permits cyclic and acyclic services. - Cyclic services are used for transmission of measurement data and actuating commands with status information. 3.4 - Acyclic services are used for device configuration, maintenance and diagnostics during operation. The device profile defines the device class and typical functionalities with parameters, ranges and limit values. The FISCO model developed by the German PTB for hazardous locations permits connection of several devices to one common bus and defines permissible limits for device and cable parameters. PROFIBUS-PA with the Transmitter Process control Service/Configuration Master Class 1 Cyclic services Master Class 2 PROFIBUS-DP Acyclic services Segment coupler PROFIBUS-PA Slave 1 Fig. 3.1 E-6 Slave 2 Typical configuration of a PROFIBUS system with the Transmitter PROFIBUS technology Bus termination Slave n Description 4.1 Intended use The Transmitter is a PROFIBUS-PA analyzer. It is used for conductivity measurement with electrodeless sensor in the field of water/waste-water treatment, electroplating, biotechnology, food processing, pharmaceutical, chemical and paper industry. The protective hood provides additional protection against direct weather exposure and mechanical damage. The rugged molded enclosure can be wall mounted or fixed into a control panel. It can also be mounted at a post or pipe. The device is designed for concentration determination of NaCl, HCl, NaOH, H2SO4, HNO3. 4.2 The device can be easily replaced since the terminals are of a plug-in design. Technical features Communication between measuring point and control room is via PROFIBUS-PA. The data exchange (cyclic and acyclic) is performed in accordance with the PROFIBUS-DP/V1 protocol. CondI measurement EEx ia IIC EEx ia IIC + – mS, %, SAL Sensocheck Temperature Fig. 4.1 P R O F I B U S P A Segment coupler P R O F I B U S Control room PROFIBUS master D P Transmitter Cond Ind 7100 PA System functions (hardware) Description E-7 English 4 Communication model The device performance is described by function blocks according to the PNO profile for Process Control Devices. The respective blocks contain different parameters and functions. Physical Block Global Status Control Transducer Block meas/cal Logbook Function Block Transfer Transducer Block Analyzer Transducer Block Analog Input CondI/%/SAL Ext. temp. Temperature Transducer Block Analog Input Temperature CondI/ %/SAL ˚C CondI/ %/SAL ˚C Transducer Limit Block Discrete Input Limit 1 Transducer Limit Block Discrete Input Limit 1 Transmitter Cond Ind 7100 PA Fig. 4.2 E-8 Communication model Transmitter Cond Ind 7100 PA according to the PNO Profile Description PROFIBUS Transducer Alarm Block Cyclic services 4.3 Profile for Process Control Devices (extract) Type of block Block contents (general) Block contents (detailed) Physical Block (PB) Description of de- Measurement procedure, device configuration vice Serial number, manufacturer name English 4.4 Operating state (run, maintenance, ...) Global status, diagnostics information Transducer Block (TB) Measurement procedure with interpretation Process variable (plain text and unit) Number of measurement ranges (MR), start and end value of MR, active MR Autorange function On/Off Sampling rate of measured values Uncorrected measured value with status Control Transducer Block Control of device Status of function execution of respective Transducer Blocks functions Slope of sensor characteristic (cell factor) Transfer Transducer Block Pre-processing of a measured value Measured value pre-processing Temperature compensation Selection of pre-processing function Transducer Limit Limit monitoring Block Block (TB) for limit setting (select input variable) Threshold, effective direction, hysteresis On-delay, off-delay Reset behavior, reset confirmation Limit status (active, not active) Description E-9 Type of block Block contents (general) Block contents (detailed) Analog Input (AI) Measured value Currently measured value with status and scale Function Block Rise time, hysteresis of AI limits Upper/lower alarm limit Upper/lower warning limit Switchover manual/automatic operation, measured value simulation Fail-safe behavior Discrete Input (DI) Digital input Switchover manual/automatic operation Signal inversion Function Block Fail-safe behavior Limit value message/status Transducer Alarm Block Signaling of Required maintenance, function check, errors, limit values incl. summing states and events Binary messages (error messages) Logbook Function Block Registration of Power on, power off, reset states and events State of execution (Logbook status) Number of entries Navigation through entries Tab. 4.1: E-10 Profile for Process Control Devices (function contents) Description Assembly 5.1 Package contents and unpacking Unpack the device carefully. Check the shipment for transport damage and completeness. - This instruction manual The package should contain: - Floppy disk with GSD file Mett7533.GSD - Front unit of Transmitter - Bag containing small parts: English 5 - Short instruction sheet - Lower case 1 12 1 Jumper (1 piece) 2 Washer (1 piece): for conduit mounting: Place washer between enclosure and nut 3 Cable ties (3 pieces) 4 Hinge pin (1 piece): insertable from either side 11 5 Enclosure screws (4 pieces) 2 6 Sealing inserts (3 pieces) 10 9 3 7 Rubber reducer (1 piece) 8 Cable glands (3 pieces) 9 Filler plugs (3 pieces) 10 Gaskets (3 pieces) 8 11 Hexagon nuts (3 pieces) 12 Sealing plugs (2 pieces): for sealing in case of wall mounting 7 6 Fig. 5.1 5 4 Assembling the enclosure Assembly E-11 5.2 Mounting plan 1 Cable glands (3 pieces) 105 144 2 Breakthroughs for cable gland or conduit 1/2”, ø = 21.5 mm (2 breakthroughs) 27 Conduits not included! 144 3 Breakthroughs for pipe mounting (4 breakthroughs) 4 Breakthroughs for wall mounting (2 breakthroughs) 18 42 84 21 43 1 80 6.2 72 32 3 4 Fig. 5.2 E-12 Mounting plan Assembly 2 max. 25 78 1 Screws (4 pieces) 27 2 Gasket (1 piece) 3 Panel 4 Span pieces (4 pieces) 5 5 Threaded sleeves (4 pieces) English 1 4 2 1...22 Fig. 5.3 3 ZU 0275 panel-mount kit, panel cutout 138 x 138 mm (DIN 43700) 1 ZU 0276 protective hood (if required) 40 132 60 1 2 3 4 2 Hose clamps with worm gear drive to DIN 3017 (2 pieces) 3 Pipe-mount plate (1 piece) 4 For vertical or horizontal posts or pipes 5 Self-tapping screws (4 pieces) 5 Fig. 5.4 ZU 0274 pipe-mount kit Assembly E-13 1 Protective hood 165 132 173 1 Fig. 5.5 E-14 ZU 0276 protective hood for wall and pipe mounting Assembly 1 6 Installation and connection 6.1 Information on installation Be sure to observe the technical specifica tions and input ratings. English Installation may only be carried out by trained experts in accordance with this instruction manual and as per applicable local and national codes. - According to the PTB FISCO model, the limits of the permissible parameter range must be observed for connection in a hazardous location. See PROFIBUS Technical Guidelines PNO Order No.: 2.091 Be sure not to notch the conductor when stripping the insulation. For easier installation, the terminal strips are of a plug-in design. The terminals are suitable for single wires and flexible leads up to 2.5 mm2 (AWG 14). A special twisted and shielded two-wire cable (e.g. Siemens) is used as bus cable. Division 2 wiring The connections to the Transmitter must be installed in accordance with the National Electric Code (ANSI-NFPA 70) Division 2 hazardous (classified) location non-incendive wiring techniques. Installation and connection E-15 1 Connection leads PROFIBUS-PA 2 Area for placing the screwdriver to pull out the terminals 3 Cover for sensor and temperature probe terminals 1 4 Pulling out the terminal blocks using a screwdriver 2 5 Recommended stripping lengths for multi-core cables 7 6 Recommended stripping lengths for coaxial cables 7 Cable laying in the device 20 7 3 280 6 4 5 Fig. 6.1 E-16 Information on installation Installation and connection Terminal assignments English 6.2 Fig. 6.2 6.3 Terminal assignments of Transmitter Overview of the Transmitter EEx ia IIC 1 Input for electrodeless conductivity sensor EEx ia IIC 2 Input for temperature probe + 1 – mS, %, SAL Sensocheck 2 Temp Fig. 6.3 3 3 Bus connection Transmitter Cond Ind 7100 PA Inputs and outputs Installation and connection E-17 Typical wiring white gray green green/yellow brown red 7250 ST electrodeless coax black core Conductivity measurement with the InPro conductivity sensor blue 6.4 Fig. 6.4 Conductivity measurement with the InPro 7250 ST electrodeless conductivity sensor The electrodeless conductivity sensor is used to measure low to highest conductivity values. E-18 Installation and connection 7250 HT electrodeless Abb. 6.5 white gray green green/yellow violet yellow core coax black coax red core English Conductivity measurement with the InPro conductivity sensor Conductivity measurement with the InPro 7250 HT electrodeless conductivity sensor The electrodeless conductivity sensor is used to measure low to highest conductivity values. Installation and connection E-19 E-20 Installation and connection 7 Commissioning 7.1 Checklist English Commissioning may only be carried out by trained experts. Before commissioning the Transmitter, the following requirements must be met: - The device must not show any damage. - When recommissioning the device after a repair, a professional routine test in accordance with EN 61010-1 must be performed. - It must be proved that the intrinsic safety is maintained when connecting the device to other equipment. - It must be ensured that the device is configured in accordance with the connected peripherals. - All connected voltage and current sources must correspond to the technical data of the device. - The device must only be connected to explosion-proof segment couplers, power supplies, ... Commissioning E-21 8 Operation 8.1 Operation possibilities Process control Service/Configuration Master Class 1 Cyclic services Master Class 2 PROFIBUS-DP Acyclic services Segment coupler PROFIBUS-PA Slave 1 Fig. 8.1 System configuration The device can be operated as follows: - using the keypad on the device - using an operating tool in the service station E-22 Operation Slave 2 Bus termination Slave n 8.2 Operation using keypad on the device 1 Display 2 Mode indicators METTLER TOLEDO English - Measuring mode - Calibration mode - Alarm - PROFIBUS-PA communication - Configuration mode 1 3 Keypad 4 Coding 5 Rating plate 2 3 4 5 Fig. 8.2 Front view of Transmitter Operation E-23 Display 1 2 3 4 5 6 7 8 9 1 Mode code entry 10 10 Not connected 2 Display of measured vari- 11 Unit symbol able 3 Temperature 13 Bar for device status 5 Limit values 14 Manual temp indicator 6 Alarm 15 Hold state active 7 Sensocheck 16 Wait 12 8 Calibration 17 Sensor data 13 9 Interval/response time 18 Sensoface 18 11 17 12 Proceed with enter 4 Not connected 16 15 14 Fig. 8.3 Display of Transmitter Keypad functions Change digit Measurement Calibration Configuration conf Select digit position Selected position flashes E-24 Operation Prompt in display: Continue in program sequence Calibration/configuration: Confirm entries, next configuration step Further key combinations are explained in the respective function descriptions. Mode code After pressing meas and/or cal you can enter one of the following mode codes to access the designated mode: conf conf, 0000 conf, 1200 Error Info Configuration mode cal, 0000 cal, 1001 cal, 1015 cal, 1100 cal, 1125 Cal Info Zero point calibration Adjusting temp probe Calibration mode Input/adjustment of transfer ratio Test mode cal, 2222 8.4 Safety functions Sensocheck, Sensoface sensor monitoring Automatic device self-test Sensocheck continuously monitors the sensor. The automatic device self-test checks the memory and measuredvalue transfer. It runs automatically in the background at fixed intervals. Sensocheck can be switched off. Sensoface provides information on the conductivity sensor condition. The primary coil and its lines are checked for short circuits, the secondary coil and its lines are checked for open circuits. GainCheck manual device self-test A display test is carried out, the software version is displayed and the memory and measured value transfer are checked. The GainCheck function ensures device operability. Start GainCheck manual device self-test Operation E-25 English 8.3 Hold state - Configuration The Hold state is a safety state that is activated in the case of interventions such as configuration and calibration. The Transmitter freezes the last valid measured value and sends a status message to the control system. - Mode code 1200 The measured value and Hold are displayed alternately • Check whether the measured value is plausible This symbol indicates that the device is in the ”Hold” state. • End the Hold state The Hold state is activated by the following mode codes: - Calibration - 8.5 Mode code 1001 Mode code 1015 Mode code 1100 Mode code 1125 Mode code 2222 After 20 sec (for measured value stabilization) the device returns to measuring mode. Mode indicators Measuring mode The alarm response time is permanently set to 10 sec. The Transmitter is in measuring mode. PROFIBUS-PA communication The Transmitter communicates via PROFIBUS-PA and can be configured from the service station. Measured values, messages and device identification can be downloaded at any time. This allows integration in fully automatic process cycles. Calibration mode Calibration mode is active. Configuration mode Alarm During an error message the red alarm LED beneath the display flashes. E-26 Operation The Transmitter is in configuration mode. 8.6 Configuration In the configuration mode the device parameters are set. conf • Activate configuration English In the case of an incorrect input ”Err” is displayed for 3 sec. The incorrect parameters cannot be stored. Input must be repeated. The following steps must be executed: • End configuration • Enter mode code ”1200” The measured value and Hold are displayed alternately • End the Hold state / accept configuration or • Confirm entry Welcome text 3 sec conf • Repeat configuration • End the Hold state During configuration the Transmitter remains in the Hold state for reasons of safety. The menus are cyclically displayed. • Select or edit parameter • Confirm entries All configurable parameters are shown in the ”Configuration parameters” table (See Page 28). The configuration parameters are checked during the input. Operation E-27 Configuration parameters ≈ Pictograph/display Parameter Selection/input Comment Factory setting Process variable 00.00 mS / 000.0 mS / 0000 mS The selected process variable is shown in the display. 000.0 mS With % only -01- Temperature display selection ˚C Selection of temperature probe Pt 1000 000.0 % 000.0 SAL Concentration -01- NaCl -02- HCl -03- NaOH -04- H2SO4 (0 to 35 % by wt) -05- HNO3 -06- H2SO4 (95 to 99 % by wt) Temperature ˚C ˚F Temperature probe Pt 100 Pt 1000 NTC 30 NTC 100 BUS EXT External temperature detection Temperature value is transmitted to the device via PROFIBUS. Temperature compensation OFF (Step LIN omitted for % and NLF SAL.) E-28 Operation Temperature compensation selection: OFF Linear Nonlinear, natural waters Parameter Selection/input Temperature co- xx.xx %/K efficient Sensocheck ON OFF PROFIBUS device address Tab. 8.1: 0001 ... 0126 Comment Factory setting Input of temperature coefficient 02.00 %/K Only with temperature compensation LIN Sensor monitoring on or off OFF Input of PROFIBUS device address Not possible if device is communicating via PROFIBUS. 0126 English Pictograph/display Configuration parameters Operation E-29 8.7 Calibration Calibration procedures (configurable) - Calibration by specifying the cell factor of the sensor used (See Page 31) - Zero point calibration in air (See Page 32) - Calibration with calibration solution (See Page 33) - Input and adjustment of transfer ratio (See Page 34) The calibration is directly conducted on the device. Calibration via PROFIBUS-PA is not provided. During calibration the Transmitter remains in the Hold state for reasons of safety. - Adjustment of temperature probe (See Page 35) Information on calibration Calibration is performed by entering the cell factor or by determining the cell factor with a known calibration solution under consideration of the temperature. If the sensor is used for measurements with a wall distance A < 110 mm, it must be calibrated with a similar wall distance. A All calibration procedures must be performed by trained personnel. When another sensor is used, its transfer ratio must be entered before calibration (see “Input and adjustment of transfer ratio” Pg. 34). Incorrectly set parameters may go unnoticed, but change the measuring properties. E-30 Operation In the case of an incorrect input ”Err” is displayed for approx. 3 sec. The incorrect parameters cannot be stored. Input must be repeated. For keypad functions see Pg. 24. Calibration by input of cell factor • Activate calibration • End the Hold state After 20 sec (for measured value stabilization) the device returns to measuring mode. English The following steps must be executed: • Enter mode code ”1100” • Confirm entry Welcome text 3 sec • Enter cell factor The lower display shows the conductivity value. A change in the cell factor also changes the conductivity value. When there has not been an entry for 6 sec, the lower display alternately shows the conductivity and temperature value. • Confirm cell factor Operation E-31 Zero point calibration in air Zero point calibration is required when low conductivity values are to be measured. When there has not been an entry for 6 sec, the lower display alternately shows the zerocorrected conductivity value and the temperature value. Before you start calibration, remove the sensor from the process, clean it and dry it up. • Confirm zero point The following steps must be executed: • End the Hold state • Activate calibration • Enter mode code ”1001” • Confirm entry Welcome text 3 sec • Modify the zero point until the lower display reads 0 µS. If required, change the sign of the zero point. E-32 Operation After 20 sec (for measured value stabilization) the device returns to measuring mode. Calibration with calibration solution During the calibration procedure the temperature must be kept constant. Observe the response time of the temperature probe. When there has not been an entry for 6 sec, the lower display alternately shows the conductivity and temperature value. • Read the conductivity value corresponding to the displayed temperature from the table of the calibration solution used (see “Calibration solutions” Pg. 61) • Change cell factor until the display shows the conductivity value from the table The following steps must be executed: • Activate calibration • Confirm cell factor • Enter mode code ”1100” • End the Hold state After 20 sec (for measured value stabilization) the device returns to measuring mode. • Confirm entry Welcome text 3 sec • Immerse sensor in calibration solution Operation E-33 English Be sure to use known calibration solutions and the respective temperature-corrected conductivity values (see “Calibration solutions” Pg. 61). Input and adjustment of transfer ratio The Transmitter comes with a preset transfer ratio. If another sensor is used, you must enter a different transfer ratio. If you do not know the transfer ratio, it must be determined in the test mode using a comparison resistor (see “Test mode” Pg. 44). If the transfer ratio has been changed after a cell factor calibration, this calibration must be repeated. The following steps must be executed: • loop conductivity comparison resistor (simulator) through the sensor bore • Adjust transfer ratio of sensor Recommended resistance value for adjustment: R = 100 Ω. • Modify the transfer ratio until the lower display shows the corresponding resistance value (without considering the cell factor) • Activate calibration • Confirm transfer ratio • Enter mode code ”1125” • End the Hold state After 20 sec (for measured value stabilization) the device returns to measuring mode. • Confirm entry Welcome text 3 sec • Enter transfer ratio of the sensor or E-34 Operation Adjustment of temperature probe • End the Hold state The following steps must be executed: After 20 sec (for measured value stabilization) the device returns to measuring mode. English Especially for Pt 100 temperature probes, it is advisable to perform an adjustment. • Activate calibration • Enter mode code ”1015” • Confirm entry Welcome text 3 sec • Measure the temperature of the process medium using an external thermometer • Enter the determined temperature value in the main display The lower display shows the measured temperature without adjustment. If this value is taken over for the upper display, the adjustment is without effect. • Confirm the temperature value Operation E-35 8.8 Operating tool For parameter setting, commissioning and diagnostics of the Transmitter, we recommend operating tools such as SIMATIC-PDM Version 5 or higher. 8.9 The current device description is included. DTM for tools with FDT interface on request. Measurement Measuring mode Error Info In the measuring mode the main display shows the configured process variable and the lower display the temperature. ”Error Info” shows the most recent error message. conf The Transmitter returns to measuring mode, also from configuration or calibration mode (after a relax time for measured-value stabilization, if required). • Activate ”Error Info” function • Mode code Cal Info The ”Cal info” shows the current cell factor and the zero point. • Activate ”Cal Info” function • Mode code • Confirm The last error message is displayed for approx. 20 sec. After that the message will be deleted. • End ”Error Info” • Confirm The current cell factor and the zero point are shown for approx. 20 sec. • End ”Cal Info” E-36 Operation 9 Diagnostics 9.1 Sensoface, Sensocheck Sensocheck can be switched off. Sensoface provides information on the conductivity sensor condition. The primary coil and its lines are checked for short circuits, the secondary coil and its lines are checked for open circuits. 9.2 A friendly Smiley can only be displayed when Sensocheck has been activated. The Sensoface status does not influence the measured value display. PROFIBUS-PA limit monitoring The Transmitter is equipped with two limit blocks that can be separately configured for the process variables conductivity, resistivity, salinity or temperature. Configuration is only performed via the bus. The limit conditions are transmitted cyclically. Hysteresis, effective direction, on and off delay can be configured. Limit value setting and output of limit messages is via the PROFIBUS-PA. When this symbol is displayed, limit block 1 is active. When this symbol is displayed, limit block 2 is active. Diagnostics E-37 English Sensocheck continuously monitors the sensor. 9.3 Error message When one of the following error messages is displayed, the device can no longer determine the measured variable correctly. The alarm response time is permanently set to 10 sec. During an error message the red alarm LED beneath the display flashes. Error No. Display (flashing) Err 01 Problem Sensor The error messages in the display are sorted according to their priority. A higher-priority message overlays a lower-priority message. Possible causes - Wrong cell factor - Measurement range exceeded - SAL > 45 ‰ - Sensor connection or cable defective Err 02 Measured value Err 03 Sensor - Unsuitable sensor Temperature probe - Outside temp range - Outside temp range for TC - Outside temp range for TC - Outside temp range for concentration Err 33 Err 34 Err 98 Sensocheck primary coil - Short circuit in primary coil Sensocheck secondary coil - Open circuit in secondary coil System error - Short circuit of lines - Lines interrupted - Memory error in device program - Measured value transmission defective - Configuration or calibration data defective • Completely reconfigure and calibrate the device E-38 Diagnostics Error No. Display (flashing) Err 99 Problem Factory settings Possible causes - EEPROM or RAM defective - Error in factory settings English This error message normally should not occur as the data are protected from loss by multiple safety functions. • Send in the device for repair and recalibration. Tab. 9.1: Error messages Diagnostics E-39 Display messages and PROFIBUS communication Err 98 X Configuration data defective, Gaincheck 2 0000 11xx Failure ERR PARAMETERS X Err 98 X Memory error (RAM, ROM, EPROM) 3 0000 11xx Failure ERR MEMORY X Err 01 X Cond, conc, sal range violation 4 0101 01xx Failure ERR MEAS VALUE X Err 02 X Measurement range Conductance range violation 5 0100 0111 Failure ERR COND VALUE X Failure ERR TEMP VALUE X Failure CHK SENSOR X Err 33 Diagnostics X X 0100 1111 Temp range violation 6 Temperature probe Sensocheck Primary coil 7 0100 0111 0100 1111 0100 0111 0100 1111 (factory setting) X Logbook entry ERR SYSTEM (factory setting) Failure Text of binary message Physical Block (PB) 0000 11xx Global status Analog input status 1 LED Factory settings defective Sensoface No. of binary message (logbook) Communication via PROFIBUS X Err 03 E-40 Cause Err 99 Display message Display pictograph User interface / display of device For comments see Pg. 38 9.4 8 Zero point 9 1010 01xx Maintenance CHK ZERO req. X Cell factor 10 1010 01xx Maintenance CHK SLOPE req. X Calibration 11 0100 0111 Function check CAL RUNNING X Function check CONF RUNNING X Function check HOLD X 0100 1111 Configuration CHK SENSOR X 0100 1111 12 0100 0111 0100 1111 HOLD (Device state = Maintenance) 13 0100 0111 HI_HI_LIM FB analysis Cond/Conc/SAL 14 1000 1110 Limit 1 Bit 1 HI_HI_LIMIT COND HI_HI_LIMIT CONC HI_HI_LIMIT SAL HI_LIM FB analysis Cond/Conc/SAL 15 1000 1010 Limit 1 Bit 2 HI_LIMIT COND HI_LIMIT CONC HI_LIMIT SAL 0100 1111 Diagnostics E-41 English Sensocheck Secondary coil (factory setting) Logbook entry (factory setting) Failure Text of binary message 0100 0111 Global status No. of binary message (logbook) Communication via PROFIBUS Physical Block (PB) X For comments see Pg. 38 LED Cause Analog input status Err 34 Sensoface Display message Display pictograph User interface / display of device 9.5 LO_LO_LIM FB analysis Cond/Conc/SAL 17 1000 1101 Limit 1 Bit 4 LO_LO_LIMIT COND LO_LO_LIMIT CONC LO_LO_LIMIT SAL HI_HI_LIM FB temperature 18 1000 1110 Limit 2 Bit 1 HI_HI_LIMIT TEMP HI_LIM FB temperature 19 1000 1010 Limit 2 Bit 2 HI_LIMIT TEMP LO_LIM FB temperature 20 1000 1001 Limit 2 Bit 3 LO_LIMIT TEMP LO_LO_LIM FB temperature 21 1000 1101 Limit 2 Bit 4 LO_LO_LIMIT TEMP Logbook empty 22 Function check EMPTY LOGBOOK Diagnostics functions Cal Info The ”Cal info” shows the current cell factor and the zero point. • Activate ”Cal Info” function E-42 Diagnostics • Mode code (factory setting) LO_LIMIT COND LO_LIMIT CONC LO_LIMIT SAL Logbook entry Limit 1 Bit 3 (factory setting) 1000 1001 Text of binary message 16 Global status Physical Block (PB) LO_LIM FB analysis Cond/Conc/SAL For comments see Pg. 38 Analog input status Communication via PROFIBUS No. of binary message (logbook) Cause LED Sensoface Display message Display pictograph User interface / display of device Error Info • Confirm The current cell factor and the zero point are shown for approx. 20 sec. ”Error Info” shows the most recent error message. conf • Activate ”Error Info” function English • End ”Cal Info” • Mode code • Confirm The error message is displayed for approx. 20 sec. After that the message will be deleted. • End ”Error Info” Diagnostics E-43 Test mode memory and measured value transfer are checked. In the test mode you can check the measuring equipment with a resistor. Start GainCheck manual device self-test • Activate ”Test Mode” function Automatic device self-test • Enter mode code • Confirm entry • loop conductivity comparison resistor (simulator) through the sensor bore The conductivity comparison resistance is indicated in Ω - without consideration of the cell factor (c = 1) and - without temperature compensation in the main display. The basis for accurate resistance measurement is a correctly specified transfer ratio (see “Input and adjustment of transfer ratio” Pg. 34). • End Test Mode The device is in Hold state. GainCheck manual device self-test A display test is carried out, the software version is displayed and the E-44 Diagnostics The automatic device self-test checks the memory and measuredvalue transfer. It runs automatically in the background at fixed intervals. 10 Maintenance and Cleaning 10.1 Maintenance English The Transmitter contains no user repairable components. 10.2 Cleaning To remove dust, dirt and spots, the external surfaces of the Transmitter may be wiped with a soft cloth moistened with water. A mild household cleaner may also be used if necessary. Maintenance and Cleaning E-45 11 Appendix 11.1 Product line Devices Model designation Ref. No. Transmitter CondI 7100 PA for hazardous- and safe-area applications 52121273 Mounting accessories Accessories Ref. No. ZU 0274 pipe-mount kit 52120741 ZU 0275 panel-mount kit 52120740 Accessories Ref. No. ZU 0276 protective hood 52120739 Sensors Mettler-Toledo GmbH, Process Analytics offers a wide range of electrodeless sensors for the following fields of applications: - Chemical process industry - Pharmaceutical industry - Food and beverage industry - Pulp and paper industry - Water/waste-water treatment For more information concerning our sensors and housings program, please refer to our website: http://www.mtpro.com 11.2 Specifications General Manufacturer Mettler-Toledo GmbH / METT Model designation/ID Transmitter Cond Ind 7100 PA / 7533 Applications Conductivity and temperature measurement E-46 Appendix Input Process variable Cond Ind input Display/measurement range Conductivity 00.00 to 99.99 µS/cm 000.0 to 999.9 µS/cm Temperature input Concentration 0.0 to 100.0 % by wt Salinity 0.0 to 45.0 ‰ (0 to 35 ˚C) Temperature sensor a) Pt100 / Pt1000 / NTC 30 kΩ / NTC 100 kΩ (2-wire connection, adjustable) Measurement range Pt100 / Pt1000 -20.0 to +150.0 ˚C / -4 to +302 ˚F NTC 30 kΩ / NTC 100 kΩ -20.0 to +130.0 ˚C / -4 to +266 ˚F Resolution 0,1 ˚C / 1 ˚F Temperature compensation a) (ref. temperature 25 ˚C) Linear characteristic (LIN) English 0000 to 1999 mS/cm 00.00 to 19.99 %/K Nonlinear temperature compensation (NLF) for natural waters to EN 27888 (0 to 36 ˚C) a) Configurable Accuracy (± 1 count) Conductivity value < 1 % of meas. value + 0.02 mS/cm Temperature < 0.5 K (for Pt 100 ± 1 K, for NTC: Temp. > 100 ˚C < 1 K) Monitoring function Sensor Sensocheck Monitoring of primary and lines for short circuit (can be disabled) Monitoring of secondary and lines for open circuit Appendix E-47 Concentration determination Operating modes Standardization Concentration determination Sensor standardization -01- NaCl 0 to 26 % by wt (0 ˚C) 0 to 28 % by wt (100 ˚C) -02- HCl 0 to 18 % by wt (-20 ˚C) 0 to 18 % by wt (50 ˚C) -03- NaOH 0 to 13 % by wt (0 ˚C) 0 to 24 % by wt (100 ˚C) -04- H2SO4 0 to 26 % by wt (-17 ˚C) 0 to 37 % by wt (110 ˚C) -05- HNO3 0 to 30 % by wt (-20 ˚C) 0 to 30 % by wt (50 ˚C) -06- H2SO4 94 to 99 % by wt (-17 ˚C) 89 to 99 % by wt (115 ˚C) Permissible cell factor 00.100 to 19.999 Permissible transfer ratio 01.00 to 99.99 Permissible offset ± 0.5 mS/cm Conditions for use Temperature Electromagnetic compatibility Operation / environment -20 to +55 ˚C Transport / storage -20 to +70 ˚C RFI suppression EN 50 081-1, EN 61 326-1 Immunity to interference EN 50 082-2, EN 61 326-1 Ingress protection Enclosure IP65 Explosion protection ATEX II 2(1) G EEx ia IIC T4, FISCO FM IS, Class I Div1, Group A, B, C, D T4 FISCO I / 1[0] / AEx ib [ia] / IIC / T4 FISCO NI, Class I Div2, Group A, B, C, D T4 NIFW Parameters and calibration data > 10 years Data retention E-48 Appendix EEPROM Dimensions Height 144 mm Width 144 mm Depth 105 mm Weight English Construction Approx. 1 kg Material PBT (polybutylene terephtalate) Color Bluish gray Assembly Wall mounting Post/pipe mounting Panel mounting RAL 7031 On pipe with 40 to 60 mm diameter On square post with 30 to 45 mm edge length Cutout to DIN 43 700 Sealed against panel Electrical connection Cable glands 3 breakthroughs for included cable glands 2 breakthroughs for NPT 1/2” or Rigid Metallic Conduit or cable glands Display and user interface Display Operation Operating tool LC display, 7-segment Measured value display Conductivity value, temperature 3 Sensoface states Good / average / poor 5 mode indicators meas / cal / alarm / online / conf Alarm LED Error message 5 keys meas / cal / up / right / enter Device description (DD) implemented in SIMATIC PDM Appendix E-49 Remote interface PROFIBUS-PA com- Digital communication by current modulation of supply current munication Reading of device identification, measured values, status and message Reading and writing of parameter and configuration data E-50 Appendix Protocol PROFIBUS-PA (DPV 1) Connection Via segment coupler to SPC, PC, PCS Profile PNO directive: PROFIBUS-PA, Profile for Process Control Devices, Version 3.0 Physical interface To IEC 1158-2 Address range 1 to 126, default: 126 Supply voltage FISCO bus supply: 9 to 17.5 V Linear barrier: 9 to 24 V Current consumption < 16.1 mA Max. current in case of fault (FDE) ≤ 21.8 mA English 11.3 ATEX EC-Type-Examination Certificate Appendix E-51 E-52 Appendix English Appendix E-53 11.4 Declaration of Conformity Declaration of conformity Konformitätserklärung Déclaration de conformité We/Wir/Nous 0820 Mettler-Toledo GmbH, Process Analytics Im Hackacker 15 8902 Urdorf Switzerland declare under our sole responsibility that the product, erklären in alleiniger Verantwortung, dass dieses Produkt, déclarons sous notre seule responsabilité que le produit, Description Beschreibung/Description CondI 7100 PA to which this declaration relates is in conformity with the following standard(s) or other normative document(s). auf welches sich diese Erklärung bezieht, mit der/den folgenden Norm(en) oder Richtlinie(n) übereinstimmt. auquel se réfère cette déclaration est conforme à la (aux) norme(s) ou au(x) document(s) normatif(s). Explosionsschutzrichtlinie Explosion Protection / Protection contre les explosions 94/9/EG Prüf- und Zertifizierungsstelle ZELM ZELM 00 ATEX 0038 D-38124 Braunschweig, ZELM 0820 EMC Directive/EMV-Richtlinie Directive concernant la CEM 89/336/EWG SR 734.5, VEMV Low-voltage directve/Niederspannungs-Richtlinie/ Directive basse tension 73/23/EWG SR 734.26, NEV Norm/Standard/Standard Place and Date of issue Ausstellungsort / - Datum Lieu et date d’émission EN 50 014: 1997 + A1 + A2 EN 50 020: 1994 EN 50284: 1999 DIN EN 61326 / VDE 0843 Teil 20: DIN EN 61326 / A1 / VDE 0843 Teil 20 / A1: EN 61010 Teil 1 / 03.93 / VDE 0411 Teil 1: EN 61010-1/ A2 / 07.95 / VDE 0411 Teil 1 / A1: 1998-01 1999-05 1994-03 1996-05 Urdorf, August 3, 2004 Mettler-Toledo GmbH, Process Analytics Waldemar Rauch General Manager PO Urdorf Artikel Nr.: 52960174 KE E-54 Appendix Christian Zwicky Head of Marketing 52960174KE-I7100-PA-Internet-2.doc Version b 11.5 FM Control Drawing ),6&2UXOHV English 7KH),6&2&RQFHSWDOORZVWKHLQWHUFRQQHFWLRQRILQWULQVLFDOO\VDIHDSSDUDWXVWRDVVRFLDWHGDSSDUDWXV QRWVSHFLILFDOO\H[DPLQHGLQVXFKFRPELQDWLRQ7KHFULWHULRQIRUVXFKLQWHUFRQQHFWLRQLVWKDWWKH YROWDJH9PD[WKHFXUUHQW,PD[DQGWKHSRZHU3LZKLFKLQWULQVLFDOO\VDIHDSSDUDWXVFDQUHFHLYHDQG UHPDLQLQWULQVLFDOO\VDIHFRQVLGHULQJIDXOWVPXVWEHHTXDORUJUHDWHUWKDQWKHYROWDJH8R9RF9WWKH FXUUHQW,R,VF,WDQGWKHSRZHU3RZKLFKFDQEHSURYLGHGE\WKHDVVRFLDWHGDSSDUDWXVVXSSO\XQLW ,QDGGLWLRQWKHPD[LPXPXQSURWHFWHGUHVLGXDOFDSDFLWDQFH& LDQGLQGXFWDQFH/ LRIHDFKDSSDUDWXV RWKHUWKDQWKHWHUPLQDWRUVFRQQHFWHGWRWKH)LHOGEXVPXVWEHOHVVWKDQRUHTXDOWRQ)DQG+ UHVSHFWLYHO\ ,QHDFK,6)LHOGEXVVHJPHQWRQO\RQHDFWLYHVRXUFHQRUPDOO\WKHDVVRFLDWHGDSSDUDWXVLVDOORZHGWR SURYLGHWKHQHFHVVDU\SRZHUIRUWKH)LHOGEXVV\VWHP7KHDOORZHGYROWDJH8R9RF9WRIWKH DVVRFLDWHGDSSDUDWXVXVHGWRVXSSO\WKHEXVPXVWEHOLPLWHGWRWKHUDQJHRI9GFWR9GF$OO RWKHUHTXLSPHQWFRQQHFWHGWRWKHEXVFDEOHKDVWREHSDVVLYHPHDQLQJWKDWWKHDSSDUDWXVLVQRW DOORZHGWRSURYLGHHQHUJ\WRWKHV\VWHPH[FHSWWRDOHDNDJHFXUUHQWRI$IRUHDFKFRQQHFWHG GHYLFH6HSDUDWHO\SRZHUHGHTXLSPHQWQHHGVDJDOYDQLFLVRODWLRQWRLQVXUHWKDWWKHLQWULQVLFDOO\VDIH )LHOGEXVFLUFXLWUHPDLQVSDVVLYH 7KHFDEOHXVHGWRLQWHUFRQQHFWWKHGHYLFHVQHHGVWRFRPSO\ZLWKWKHIROORZLQJSDUDPHWHUV /RRSUHVLVWDQFH5 NP ,QGXFWDQFHSHUXQLWOHQJWK/ P+NP &DSDFLWDQFHSHUXQLWOHQJWK& Q)NP & & OLQHOLQH& OLQHVFUHHQLIERWKOLQHVDUHIORDWLQJ RU & & OLQHOLQH& OLQHVFUHHQLIWKHVFUHHQLVFRQQHFWHGWRRQHOLQH /HQJWKRIVSXU&DEOHPD[P /HQJWKRIWUXQNFDEOHPD[NP /HQJWKRIVSOLFHPD[P 7HUPLQDWRUV $WHDFKHQGRIWKHWUXQNFDEOHDQDSSURYHGOLQHWHUPLQDWRUZLWKWKHIROORZLQJSDUDPHWHUVLVVXLWDEOH 5 & ) 6\VWHPHYDOXDWLRQ 7KHQXPEHURISDVVLYHGHYLFHVOLNHWUDQVPLWWHUVDFWXDWRUVFRQQHFWHGWRDVLQJOHEXVVHJPHQWLVQRW OLPLWHGGXHWR,6UHDVRQV)XUWKHUPRUHLIWKHDERYHUXOHVDUHUHVSHFWHGWKHLQGXFWDQFHDQG FDSDFLWDQFHRIWKHFDEOHQHHGQRWWREHFRQVLGHUHGDQGZLOOQRWLPSDLUWKHLQWULQVLFVDIHW\RIWKH LQVWDOODWLRQ IQVWDOODWLRQ1RWHV)RU),6&2DQG(QWLW\&RQFHSWV 6DIHW\ (QWLW\ FRQFHSW DOORZV WKH LQWHUFRQQHFWLRQ RI )0 $SSURYHG ,QWULQVLFDOO\ VDIH 7KH ,QWULQVLF GHYLFHV ZLWK HQWLW\ SDUDPHWHUV QRW VSHFLILFDOO\ H[DPLQHG LQ FRPELQDWLRQ DV D V\VWHPV ZKHQ 8 R RU 9RF RU 9 W 9 PD[ ,R RU ,VF RU ,W ,PD[3R 3 L & D RU &L &FDEOH & R )RU LQGXFWDQFH XVH HLWKHU / D RU /R / L / FDEOH RU /H5H /D5 D RU /R5R DQG / L5L / D5 D RU /R5R 6DIHW\ ),6&2 FRQFHSW DOORZV WKH LQWHUFRQQHFWLRQ RI )0 DSSURYHG ,QWULQVLFDOO\ VDIH 7KH ,QWULQVLF GHYLFHV ZLWK ),6&2 SDUDPHWHUV QRW VSHFLILFDOO\ H[DPLQHG LQ FRPELQDWLRQ DV D V\VWHP ZKHQ 8 R RU 9RF RU 9 W 9 PD[ ,R RU ,VF RU ,W ,PD[ 3L 3 R FRQGXLW VHDOV PXVW EH XVHG ZKHQ LQVWDOOHG LQ &ODVV ,, DQG &ODVV ,,, HQYLURQPHQWV 'XVWWLJKW &RQWURO HTXLSPHQW FRQQHFWHG WR WKH $VVRFLDWHG $SSDUDWXV PXVW QRW XVH RU JHQHUDWH PRUH WKDQ 9UPV RU 9GF VKRXOG EH LQ DFFRUGDQFH ZLWK $16,,6$ 53 H[FHSW FKDSWHU IRU ),6&2 ,QVWDOODWLRQV ,QVWDOODWLRQ ,QVWDOODWLRQ RI ,QWULQVLFDOO\ 6DIH 6\VWHPV IRU +D]DUGRXV &ODVVLILHG /RFDWLRQVµ DQG WKH 1DWLRQDO (OHFWULFDO &RGH $16,1)3$ 6HFWLRQV DQG 7KH FRQILJXUDWLRQ RI DVVRFLDWHG $SSDUDWXV PXVW EH )0 $SSURYHG XQGHU WKH DVVRFLDWHG FRQFHSW $VVRFLDWHG $SSDUDWXV PDQXIDFWXUHU V LQVWDOODWLRQ GUDZLQJ PXVW EH IROORZHG ZKHQ LQVWDOOLQJ WKLV HTXLSPHQW 6HULHV DUH $SSURYHG IRU &ODVV =RQH DSSOLFDWLRQV ,I FRQQHFWLQJ &RQG,QG3$&RQG,QGH)) $([ >LE@DVVRFLDWHG $SSDUDWXV RU $([ LE ,6 $SSDUDWXV WR WKH &RQG,QG3$&RQG,QGH)) 6HULHV WKH ,6 FLUFXLW LV RQO\VXLWDEOH IRU &ODVV =RQH RU &ODVV =RQH DQG LV QRW VXLWDEOH IRU &ODVV =RQH RU &ODVV 'LYLVLRQ +D]DUGRXV &ODVVLILHG /RFDWLRQV WR GUDZLQJ ZLWKRXW SULRU )0 $SSURYDOVDXWKRULVDWLRQ 1R UHYLVLRQ 6LPSOH $SSDUDWXV LV GHILQHG DV D GHYLFH WKDW GRHV QRW JHQHUDWHV PRUH WKDQ 9 $ RU P: Appendix E-55 11.6 Sensors Specifications Construction InPro 7250 electrodeless conductivity sensors Dimensions Conductivity Meas. range Resolution 0.01 mS/cm Meas. error InPro 7250 ST ± (0.5 % of meas. value, + 25 µS) Meas. error InPro 7250 HT ± (0.5 % of meas. value, + 1 µS) Temperature Temp probe InPro 7250 ST Process temp Temperature Temp probe InPro 7250 HT Process temp Pressurea) Basic settings 0 to 2000 mS/cm Pt 1000 -20 to +100 ˚C (-4 to +212 ˚F) Pt 1000 -20 to +180 ˚C (-4 to 356 ˚F) Process temp (within Ex range) -20 to +130 ˚C (-4 to +266 ˚F) Process pressure InPro 7250 ST max. 8 bars Process pressure InPro 7250 HT max. 20 bars Cell factor 2.175b) Transfer ratio 120 c) a) Depending on the installation. b) Typical value, may differ for each individual sensor and depends on the installation conditions. The exact value must be determined with a calbration. c) Typical value, may differ for each individual sensor. The exact value must be determined with a calbration. E-56 Appendix Total length Body length Diameter Sensor bore Mounting Material Sensor (medium wetted)a) Sensor mounting thread (G 3/4“) O-ring Cable Type InPro 7250 ST Type InPro 7250 HT Available cable lengths Explosion pro- ATEX tection InPro 7250 HT FM a) This material is not FDA listed. 185.5 mm (incl. fixing thread) 125.5 mm ø = 47 mm ø = 15 mm G 3/4” Glass-filled PEEK (GF30) stainless steel (1.4435) Viton® single coaxial cable double coaxial cable 3, 5 and 10 m (9.80, 16.40 and 32.80 ft) SEV 05 ATEX 016 X II 1/2G EEx ia IIC T6/T5/T4/T3 I.S. Cl 1, Div 1, GR ABCD / T6 Dimension drawing 125.5 4.94 Fig. 11.1 G 3/4" 1.45 Ø 37 47 5 1.8 0.79 Ø Ø 20 1 0. 5 59 SW 35 28.5 1.12 English mm inch 60 2.36 Dimension drawing InPro 7250 electrodeless conductivity sensors Appendix E-57 11.7 Certificate of Conformity InPro 7250 Series E-58 Appendix English Appendix E-59 E-60 Appendix 11.8 Calibration solutions Concentration 0.01 mol/l a) 0.1 mol/l 1 mol/l 0 0.776 7.15 65.41 5 0.896 8.22 74.14 10 1.020 9.33 83.19 15 1.147 10.48 92.52 16 1.173 10.72 94.41 17 1.199 10.95 96.31 18 1.225 11.19 98.22 19 1.251 11.43 100.14 20 1.278 11.67 102.07 21 1.305 11.91 104.00 22 1.332 12.15 105.94 23 1.359 12.39 107.89 24 1.386 12.64 109.84 25 1.413 12.88 111.80 26 1.441 13.13 113.77 27 1.468 13.37 115.74 28 1.496 13.62 29 1.524 13.87 30 1.552 14.12 31 1.581 14.37 32 1.609 14.62 33 1.638 14.88 34 1.667 15.13 35 1.696 15.39 36 15.64 a) Data source: K. H. Hellwege (Editor), H. Landolt, R. Börnstein: Zahlenwerte und Funktionen ..., Volume 2, Part. Volume 6 Tab. 11.1: Potassium chloride solutions, conductivity in mS/cm Temperature [˚C] Concentration Saturated a) 0.1 mol/l b) 0.01 mol/l b) 0 134.5 5.786 0.631 1 138.6 5.965 0.651 2 142.7 6.145 0.671 3 146.9 6.327 0.692 4 151.2 6.510 0.712 5 155.5 6.695 0.733 6 159.9 6.881 0.754 7 164.3 7.068 0.775 8 168.8 7.257 0.796 9 173.4 7.447 0.818 10 177.9 7.638 0.839 11 182.6 7.831 0.861 12 187.2 8.025 0.883 13 191.9 8.221 0.905 14 196.7 8.418 0.927 15 201.5 8.617 0.950 16 206.3 8.816 0.972 17 211.2 9.018 0.995 18 216.1 9.221 1.018 19 221.0 9.425 1.041 20 226.0 9.631 1.064 21 231.0 9.838 1.087 22 236.1 10.047 1.111 23 241.1 10.258 1.135 24 246.2 10.469 1.159 25 251.3 10.683 1.183 26 256.5 10.898 1.207 27 261.6 11.114 1.232 28 266.9 11.332 1.256 29 272.1 11.552 1.281 30 277.4 11.773 1.306 31 282.7 11.995 1.331 32 288.0 12.220 1.357 33 293.3 12.445 1.382 34 298.7 12.673 1.408 35 304.1 12.902 1.434 36 309.5 13.132 1.460 a) Data source: K. H. Hellwege (Editor), H. Landolt, R. Börnstein: Zahlenwerte und Funktionen ..., Volume 2, Part. Volume 6 b) Data source: Test solutions calculated according to DIN IEC 746-3 Tab. 11.2: Sodium chloride solutions, conductivity in mS/cm Appendix E-61 English Temperature [˚C] 11.9 Concentration curves Concentration calculation error [% by wt] < 0.5 <2 700 100 ˚C 91 ˚C Conductivity [mS/cm] 600 82 ˚C 73 ˚C 500 63 ˚C 53 ˚C 400 46 ˚C 300 34 ˚C 25 ˚C 15 ˚C 10 ˚C 200 0 ˚C 100 0 0 Fig. 11.2 E-62 5 10 15 Concentration [% by wt] Concentration curves NaCl (configuration: concentration -01-) Appendix 20 25 30 Concentration calculation error [% by wt] < 0.2 <1 <2 1200 50 ˚C English 40 ˚C 1000 Conductivity [mS/cm] 30 ˚C 25 ˚C 800 20 ˚C 10 ˚C 600 0 ˚C ±10 ˚C 400 ±20 ˚C 200 0 0 Fig. 11.3 2 4 6 8 10 12 Concentration [% by wt] 14 16 18 20 Appendix E-63 Concentration curves HCl (configuration: concentration -02-) < 0.2 Concentration calculation error [% by wt] 1600 1400 100 ˚C Conductivity [mS/cm] 1200 90 ˚C 80 ˚C 1000 70 ˚C 800 60 ˚C 50 ˚C 600 40 ˚C 30 ˚C 400 20 ˚C 10 ˚C 0 ˚C 200 0 5 0 10 Concentration [% by wt] Fig. 11.4 E-64 Concentration curves NaOH (configuration: concentration -03-) Appendix 15 20 25 Concentration calculation error [% by wt] < 0.5 <1 110 ˚C 100 ˚C 1600 90 ˚C 80 ˚C Conductivity [mS/cm] 1400 70 ˚C 60 ˚C 1200 50 ˚C 1000 40 ˚C 30 ˚C 800 20 ˚C 10 ˚C 600 0 ˚C ±10 ˚C 400 200 0 0 5 10 15 20 25 30 35 Concentration [% by wt] Fig. 11.5 Concentration curves H 2SO4 (configuration: concentration -04-) Appendix E-65 English 1800 Concentration calculation error [% by wt] < 0.2 <1 <2 1200 50 ˚C 40 ˚C 1000 Conductivity [mS/cm] 30 ˚C 25 ˚C 20 ˚C 800 10 ˚C 600 0 ˚C ±10 ˚C 400 ±20 ˚C 200 0 0 Fig. 11.6 E-66 5 Concentration curves HNO Appendix 10 15 Concentration [% by wt] 3 (configuration: concentration -05-) 20 25 30 < 0.2 Concentration calculation error [% by wt] English 600 500 Conductivity [mS/cm] 110 ˚C 100 ˚C 400 90 ˚C 80 ˚C 300 70 ˚C 60 ˚C 200 50 ˚C 40 ˚C 30 ˚C 100 0 95.0 20 ˚C 10 ˚C 0 ˚C ±10 ˚C 95.5 96.0 96.5 97.0 97.5 98.0 98.5 99.0 Concentration [% by wt] Fig. 11.7 Concentration curves H 2SO4 (range 95 to 99 % by wt), (configuration: concentration -06-) Appendix E-67 11.10 Glossary Conductance Conductance G [S] =1 / R [Ω] Conductivity Conductivity κ [S/cm] = G [S] · c [1/cm] DTM (Device Type Manager) Permits access to field device (acyclic services) via system with FDT interface. FDT (Field Device Tool) Standardized interface for data exchange with field devices, among others. FISCO Model (Fieldbus Intrinsically Safe Concept) Permits connection of several devices to a common bus line and defines limit values for device and cable parameters. This model developed by the German PTB assumes that only one ”active” device, i.e. the bus supply, is connected to the field bus. All other devices are ”passive” with regard to the power supply into the bus. Within the defined limits, the line characteristics have no influence on the intrinsic safety. GSD file (device database file) Contains the communication features of slave devices. During commissioning it is loaded in the process control system. PROFIBUS-DP (decentralized peripherals) Standardized specification (EN 50 170) of an open fieldbus system for binary and analog signals of sensors and actuators. It has been designed for high-speed data exchange at the device level. E-68 Appendix PROFIBUS-PA (process automation) Open fieldbus standard for process automation. It makes use of the transmission technology to IEC 1158-2 approved for operation in hazardous locations, which at the same time allows the field devices to be powered over the bus. SIMATIC-PDM Tool developed by Siemens for projecting, configuring, commissioning and diagnostic of smart process analyzers. The Transmitter device description (DD) is implemented in the SIMATIC-PDM. Temperature coefficient With temperature compensation activated, the measured value is calculated to the value at the reference temperature using the temperature coefficient. Temperature compensation Calculates the measured conductivity value for a reference temperature. 12 Index A Accuracy, E-47 Certificate of Conformity, E-51 Adjusting temp probe, E-35 Cleaning of device, E-45 Applications, E-46 Commissioning, E-21 Assembly Concentration curves Enclosure, E-11 Hydrogen chloride, E-63 Pipe-mount kit (ZU 0274), E-13 Nitric acid, E-66 Transmitter, E-12 Sodium chloride, E-62 ZU 0275 panel-mount kit, E-13 Sodium hydroxide, E-64 ZU 0276 protective hood, E-14 Sulphuric acid, E-65 B Beschaltung, Beispiel, E-19 English InPro 7250 sensors, E-58 Sulphuric acid (95 to 99 % by wt), E-67 Concentration determination, E-48 Conditions for use C Cal Info, E-36, E-42 Conductivity measurement, E-18 Calibration, E-30 Configuration, E-27 Transmitter, E-48 Adjusting temp probe, E-35 Configuration parameters, E-28 Input and adjustment of transfer ratio, E-34 Connecting lines, E-16 Input of cell factor, E-31 Construction Overview, E-30 InPro 7250 sensors, E-56 With calibration solution, E-33 Transmitter, E-49 Zero point calibration in air, E-32 Calibration solutions Potassium chloride, E-61 Sodium chloride, E-61 Cell factor, calibration, E-31 D Declaration of Conformity, E-54 Device description, E-7 Device self-test Automatic, E-25, E-44 Manual, E-25, E-44 Index E-69 Diagnostics functions, E-42 Display, E-24 L Leitfähigkeitsmessung, E-19 Display messages and PROFIBUS communication, E-40 Limit monitoring Division 2 wiring, E-15 PROFIBUS-PA, E-37 Logbook, E-10 E Electrode standardization, E-48 Error Info, E-36, E-43 M Maintenance of device, E-45 Error message, E-38 Measurement, E-36 Explosion protection Measuring mode, E-36 InPro 7250 sensors, E-4 Mode code, E-25, E-73 Transmitter, E-4 Mode indicators, E-26 Mounting plan, E-12 F FISCO model, E-4, E-6, E-15, E-68 FM Control Drawing, E-55 N Notes Calibration, E-30 G GainCheck, E-25, E-44 Installation, E-15 H Hold state, E-26 This instruction manual, E-3 I InPro 7250 sensors Safety, E-4 O Operating tool, E-36 Operation possibilities, E-22 Dimension drawing, E-57 Installation, E-15 Intended use, E-7 K Keypad functions, E-24 E-70 Index P Packing list, E-11 Pipe-mount kit (ZU 0274), E-13 Transfer ratio, calibration, E-34 Devices, E-46 Transmitter, overview, E-17 Further accessories, E-46 Type Examination Certificate, E-51 InPro 7250 sensors, E-46 Mounting accessories, E-46 PROFIBUS technology, E-5 U Unpacking, E-11 English Product line User interface, E-23 PROFIBUS, variants, E-5 PROFIBUS-PA Definitions, E-6 Limit monitoring, E-37 S Safety functions, E-25 W Wiring example, E-18, E-19 Z ZU 0275 panel-mount kit, E-13 ZU 0276 protective hood, E-14 Safety information, E-4 Sensocheck, E-25, E-37 On/off, E-29 Sensoface, E-25, E-37 Sensor monitoring, E-25 Specifications InPro 7250 sensors, E-56 Transmitter, E-46 Stripping lengths, E-16 T Technical features, E-7 Temp probe adjustment, E-35 Temperature compensation Configuring, E-28 Terminal assignments, E-17 Test mode, E-44 Index E-71 E-72 Index English Mode codes conf conf, 0000 conf, 1200 Error Info Configuration mode cal, 0000 cal, 1001 cal, 1015 cal, 1100 cal, 1125 cal, 2222 Cal Info Zero point calibration Temp probe adjustment Calibration mode Input/adjustment of transfer ratio Test mode E-73 Subject to technical changes. © Mettler-Toledo GmbH, Process Analytics 06/05 Printed in Switzerland. 52 121 066 Mettler-Toledo GmbH, Process Analytics Industrie Nord, CH-8902 Urdorf, Switzerland Phone + 41 44 736 22 11, Fax +41 44 736 26 36
advertisement