Sharp R-301FK Service manual
Add to my manuals
16 Pages
Sharp R-301FK is a microwave oven with advanced features that make cooking and reheating food a breeze. Here are some of its capabilities:
-
Cooking Power and Capacity: With 900 watts of power, the Sharp R-301FK heats food quickly and evenly. It has a spacious 1.1 cubic feet capacity, allowing you to cook a variety of dishes, from small snacks to large family meals.
-
Preset Cooking Programs: The oven comes with 10 preset cooking programs that eliminate the guesswork from cooking common foods like popcorn, pizza, and vegetables. Simply select the desired program, and the oven automatically adjusts the cooking time and power level to achieve perfect results.
advertisement
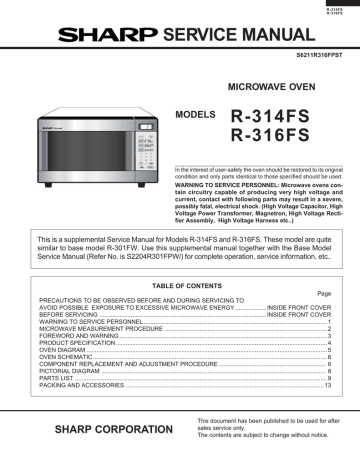
R- 314FS
R- 316FS
SERVICE MANUAL
S6211R316FPST
MICROWAVE OVEN
MODELS
R-314FS
R-316FS
In the interest of user-safety the oven should be restored to its original condition and only parts identical to those specified should be used.
WARNING TO SERVICE PERSONNEL: Microwave ovens contain circuitry capable of producing very high voltage and current, contact with following parts may result in a severe, possibly fatal, electrical shock. (High Voltage Capacitor, High
Voltage Power Transformer, Magnetron, High Voltage Rectifier Assembly, High Voltage Harness etc..)
This is a supplemental Service Manual for Models R-314FS and R-316FS. These model are quite similar to base model R-301FW. Use this supplemental manual together with the Base Model
Service Manual (Refer No. is S2204R301FPW/) for complete operation, service information, etc..
TABLE OF CONTENTS
Page
PRECAUTIONS TO BE OBSERVED BEFORE AND DURING SERVICING TO
AVOID POSSIBLE EXPOSURE TO EXCESSIVE MICROWAVE ENERGY ................... INSIDE FRONT COVER
BEFORE SERVICING ...................................................................................................... INSIDE FRONT COVER
WARNING TO SERVICE PERSONNEL ................................................................................................................ 1
MICROWAVE MEASUREMENT PROCEDURE ................................................................................................... 2
FOREWORD AND WARNING ............................................................................................................................... 3
PRODUCT SPECIFICATION ................................................................................................................................. 4
OVEN DIAGRAM ................................................................................................................................................... 5
OVEN SCHEMATIC ............................................................................................................................................... 6
COMPONENT REPLACEMENT AND ADJUSTMENT PROCEDURE ................................................................. 6
PICTORIAL DIAGRAM ......................................................................................................................................... 8
PARTS LIST .......................................................................................................................................................... 9
PACKING AND ACCESSORIES ......................................................................................................................... 13
SHARP CORPORATION
15
This document has been published to be used for after sales service only.
The contents are subject to change without notice.
R - 31 4 F S
R - 31 6 F S
PRECAUTIONS TO BE OBSERVED BEFORE AND
DURING SERVICING TO AVOID POSSIBLE
EXPOSURE TO EXCESSIVE MICROWAVE
ENERGY
(a) Do not operate or allow the oven to be operated with the door open.
(b) Make the following safety checks on all ovens to be serviced before activating the magnetron or other microwave source, and make repairs as necessary: (1) interlock operation, (2) proper door closing, (3) seal and sealing surfaces (arcing, wear, and other damage), (4) damage to or loosening of hinges and latches, (5) evidence of dropping or abuse.
(c) Before turning on microwave power for any service test or inspection within the microwave generating compartments, check the magnetron, wave guide or transmission line, and cavity for proper alignment, integrity, and connections.
(d) Any defective or misadjusted components in the interlock, monitor, door seal, and microwave generation and transmission systems shall be repaired, replaced, or adjusted by procedures described in this manual before the oven is released to the owner.
(e) A microwave leakage check to verify compliance with the Federal Performance Standard should be performed on each oven prior to release to the owner.
BEFORE SERVICING
Before servicing an operative unit, perform a microwave emission check as per the Microwave
Measurement Procedure outlined in this service manual.
If microwave emissions level is in excess of the specified limit, contact SHARP ELECTRONICS
CORPORATION immediately @1-800-237-4277.
If the unit operates with the door open, service person should 1) tell the user not to operate the oven and 2) contact SHARP ELECTRONICS CORPORATION and Food and Drug Administration's
Center for Devices and Radiological Health immediately.
Service personnel should inform SHARP ELECTRONICS CORPORATION of any certified unit found with emissions in excess of 4mW/cm
2
. The owner of the unit should be instructed not to use the unit until the oven has been brought into compliance.
16
WARNING TO SERVICE PERSONNEL
Microwave ovens contain circuitry capable of producing very high voltage and current, contact with following parts may result in a severe, possibly fatal, electrical shock.
(Example)
High Voltage Capacitor, High Voltage Power Transformer, Magnetron, High Voltage Rectifier Assembly, High Voltage Harness etc..
Read the Service Manual carefully and follow all instructions.
Don't Touch !
Danger High Voltage
R- 314FS
R- 316FS
Before Servicing
1. Disconnect the power supply cord , and then remove outer case.
2. Open the door and block it open.
3. Discharge high voltage capacitor.
WARNING:RISK OF ELECTRIC SHOCK.
DISCHARGE THE HIGH-VOLTAGE
CAPACITOR BEFORE SERVICING.
The high-voltage capacitor remains charged about 60 seconds after the oven has been switched off. Wait for 60 seconds and then short-circuit the connection of the highvoltage capacitor (that is the connecting lead of the highvoltage rectifier) against the chassis with the use of an insulated screwdriver.
Whenever troubleshooting is performed the power supply must be disconnected. It may, in some cases, be necessary to connect the power supply after the outer case has been removed, in this event,
1. Disconnect the power supply cord, and then remove outer case.
2. Open the door and block it open.
3. Discharge high voltage capacitor.
4. Disconnect the leads to the primary of the power transformer.
5. Ensure that the leads remain isolated from other components and oven chassis by using insulation tape.
6. After that procedure, reconnect the power supply cord.
When the testing is completed,
1. Disconnect the power supply cord, and then remove outer case.
2. Open the door and block it open.
3. Discharge high voltage capacitor.
4. Reconnect the leads to the primary of the power transformer.
5. Reinstall the outer case (cabinet).
6. Reconnect the power supply cord after the outer case is installed.
7. Run the oven and check all functions.
After repairing
1. Reconnect all leads removed from components during testing.
2. Reinstall the outer case (cabinet).
3. Reconnect the power supply cord after the outer case is installed.
4. Run the oven and check all functions.
Microwave ovens should not be run empty. To test for the presence of microwave energy within a cavity, place a cup of cold water on the oven turntable, close the door and set the power to HIGH and set the microwave timer for two (2) minutes. When the two minutes has elapsed (timer at zero) carefully check that the water is now hot. If the water remains cold carry out Before Servicing procedure and reexamine the connections to the component being tested.
When all service work is completed and the oven is fully assembled, the microwave power output should be checked and a microwave leakage test should be carried out.
1
R - 31 4 F S
R - 31 6 F S
MICROWAVE MEASUREMENT PROCEDURE
A. Requirements:
1) Microwave leakage limit (Power density limit): The power density of microwave radiation emitted by a microwave oven should not exceed 1mW/cm 2 at any point 5cm or more from the external surface of the oven, measured prior to acquisition by a purchaser, and thereafter (through the useful life of the oven), 5 mW/cm 2 at any point 5cm or more from the external surface of the oven.
2) Safety interlock switches:
Primary interlock relay and door sensing switch shall prevent microwave radiation emission in excess of the requirement as above mentioned, secondary interlock switch shall prevent microwave radiation emission in excess of 5 mW/cm 2 at any point 5cm or more from the external surface of the oven.
B. Preparation for testing:
Before beginning the actual measurement of leakage, proceed as follows:
1) Make sure that the actual instrument is operating normally as specified in its instruction booklet.
Important:
Survey instruments that comply with the requirement for instrumentation as prescribed by the performance standard for microwave ovens, 21 CFR 1030.10(c)(3)(i), must be used for testing.
2) Place the oven tray in the oven cavity.
3) Place the load of 275
±
15 ml (9.8 oz) of tap water initially at 20
±
5˚C (68˚F) in the center of the oven cavity.
The water container shall be a low form of 600 ml (20 oz) beaker with an inside diameter of approx. 8.5 cm (3-1/2 in.) and made of an electrically nonconductive material such as glass or plastic.
The placing of this standard load in the oven is important not only to protect the oven, but also to insure that any leakage is measured accurately.
4) Set the cooking control on Full Power Cooking Mode.
5) Close the door and select a cook cycle of several minutes. If the water begins to boil before the survey is completed, replace it with 275 ml of cool water.
C. Leakage test:
Closed-door leakage test (microwave measurement)
1) Grasp the probe of the survey instrument and hold it perpendicular to the gap between the door and the body of the oven.
2) Move the probe slowly, not faster than 1 in./sec. (2.5 cm/sec.) along the gap, watching for the maximum indication on the meter.
3) Check for leakage at the door screen, sheet metal seams and other accessible positions where the continuity of the metal has been breached (eg., around the switches, indicator, and vents).
While testing for leakage around the door pull the door away from the front of the oven as far as is permitted by the closed latch assembly.
4) Measure carefully at the point of highest leakage and make sure that the highest leakage is no greater than 4mW/cm 2 , and that the secondary interlock switch and the primary interlock relay do turn the oven OFF before any door movement.
NOTE: After servicing, record data on service invoice and microwave leakage report.
2
R- 314FS
R- 316FS
SERVICE MANUAL
MICROWAVE OVEN
R-314FS/ R-316FS
FOREWORD
This Manual has been prepared to provide Sharp Electronics Corp. Service Personnel with Operation and Service
Information for the SHARP MICROWAVE OVENS, R-314FS and R-316FS.
The models R-314FS and R-316FS are quite similar to base model R-301FW (Refer No. is S2204R301FPW/).
It is recommended that service personnel carefully study the entire text of this manual and the base model's manual so that they will be qualified to render satisfactory customer service.
Check the interlock switches and the door seal carefully. Special attention should be given to avoid electrical shock and microwave radiation hazard.
WARNING
Never operate the oven until the following points are ensured.
(A) The door is tightly closed.
(B) The door brackets and hinges are not defective.
(C) The door packing is not damaged.
(D) The door is not deformed or warped.
(E) There is no other visible damage with the oven.
Servicing and repair work must be carried out only by trained service personnel.
DANGER
Certain initial parts are intentionally not grounded and present a risk of electrical shock only during servicing.
Service personnel - Do not contact the following parts while the appliance is energized;
High Voltage Capacitor, Power Transformer, Magnetron, High Voltage Rectifier Assembly, High Voltage
Harness;
If provided, Vent Hood, Fan assembly, Cooling Fan Motor.
All the parts marked “*” on parts list are used at voltages more than 250V.
Removal of the outer wrap gives access to voltage above 250V.
All the parts marked “
∆
” on parts list may cause undue microwave exposure, by themselves, or when they are damaged, loosened or removed.
SHARP ELECTRONICS CORPORATION
SHARP PLAZA, MAHWAH,
NEW JERSEY 07430-2135
3
R - 31 4 F S
R - 31 6 F S
ITEM
Power Requirements
Power Output
Case Dimensions
Cooking Cavity Dimensions
1.2 Cubic Feet
Control Complement
Oven Cavity Light
Safety Standard
SPECIFICATION
DESCRIPTION
120 Volts / 13 Amperes
60 Hertz
Single phase, 3 wire grounded
1000 watts (IEC TEST PROCEDURE)
Operating frequency of 2450MHz
Width 20-1/2"
Height 11-7/8"
Depth 16-3/4"
Width 14-3/4"
Height 8-3/4"
Depth 15-3/4"
Touch Control System
Clock ( 1:00 - 12:59 )
Timer (0 - 99 min. 99 seconds)
Microwave Power for Variable Cooking
Repetition Rate;
P-HI .................................................. Full power throughout the cooking time
P-90 .................................................................... approx. 90% of Full Power
P-80 .................................................................... approx. 80% of Full Power
P-70 .................................................................... approx. 70% of Full Power
P-60 .................................................................... approx. 60% of Full Power
P-50 .................................................................... approx. 50% of Full Power
P-40 .................................................................... approx. 40% of Full Power
P-30 .................................................................... approx. 30% of Full Power
P-20 .................................................................... approx. 20% of Full Power
P-10 .................................................................... approx. 10% of Full Power
P-0 .................................................... No power throughout the cooking time
POPCORN pad, MINUTE PLUS pad
REHEAT pad, COOK pad
DEFROST pad, Number selection pads
POWER LEVEL pad, TIMER/CLOCK pad
STOP/CLEAR pad, START pad
Yes
UL Listed FCC Authorized
DHHS Rules, CFR, Title 21, Chapter 1, Subchapter J
GENERAL INFORMATION
GROUNDING INSTRUCTIONS
This oven is equipped with a three prong grounding plug. It must be plugged into a wall receptacle that is properly installed and grounded in accordance with the National Electrical Code and local codes and ordinances.
In the event of an electrical short circuit, grounding reduces the risk of electric shock by providing an escape wire for the electric current.
WARNING: Improper use of the grounding plug can result in a risk of electric shock.
Electrical Requirements
The electrical requirements are a 120 volt 60 Hz, AC only,
15 or 20 amp. fused electrical supply. It is recommended that a separate circuit serving only this appliance be provided. When installing this appliance, observe all applicable codes and ordinances.
A short power-supply cord is provided to reduce risks of becoming entangled in or tripping over a longer cord.
Where a two-pronged wall-receptacle is encountered, it is the personal responsibility and obligation of the customer to
4
contact a qualified electrician and have it replaced with a properly grounded three-pronged wall receptacle or have a grounding adapter properly grounded and polarized. If the extension cord must be used, it should be a 3-wire, 15 amp. or higher rated cord. Do not drape over a countertop or table where it can be pulled on by children or tripped over accidentally.
CAUTION: DO NOT UNDER ANY CIRCUMSTANCES CUT OR RE-
MOVE THE ROUND GROUNDING PRONG FROM THIS
PLUG.
OVEN DIAGRAM
6
9
2
10
1. Door open button.
Push to open door.
2. Door latches.
The oven will not operate unless the door is securely closed.
3. Removable turntable support.
4. Removable turntable.
The turntable will rotate clockwise or counterclockwise.
5. Oven lamp.
It will light when oven is operating or door is opened.
5
11
8
12
1
4
3
6. Oven door with see-through window.
7. Ventilation openings. (Rear)
8. Auto-Touch control panel.
9. Time display: Digital display, 99 minutes 99 seconds.
10. Coupling.
11. Waveguide cover.
12. Power supply cord
Grounded
Receptacle Box
3-Pronged
Plug
Grounding Pin
3-Pronged Receptacle
7
TOUCH CONTROL PANEL
COOK DEF.
START CHECK
R- 314FS
R- 316FS
NOTE:
Some one-touch cooking features such as "MINUTE PLUS" are disabled after three minutes when the oven is not in use. These features are automatically enabled when the door is opened and closed or the STOP/ CLEAR pad is pressed.
5
R - 31 4 F S
R - 31 6 F S
SCHEMATIC
NOTE: CONDITION OF OVEN
1. DOOR CLOSED
2. CLOCK APPEARS ON DISPLAY
NOTE: " " indicates components with potential above 250V.
MONITOR
FUSE 20A
OVEN THERMAL
CUT-OUT MG. THERMAL CUT-OUT
POWER
TRANSFORMER
N.O.
PRIMARY
INTERLOCK
RELAY
(RY2)
120V AC
60 Hz
CONTROL UNIT
CAPACITOR
0.94
µ
F
AC 2200V
GRN
N.O.
OVEN LAMP
RELAY (RY1)
OL OVEN
LAMP
SECONDARY
INTERLOCK
SWITCH
TTM
TURN-
TABLE
MOTOR
FM
FAN
MOTOR
COM.
COM.
B2
DOOR
SENSING
SWITCH
B1
Figure O-1. Oven Schematic-Off Condition
RECTIFIER
MAGNETRON
COMPONENT REPLACEMENT AND ADJUSTMENT PROCEDURE
GRAPHIC SHEET AND MEMBRANE SWITCH REPLACEMENT
Control panel frame
Removal
1. Disconnect the power supply cord and then remove outer case.
2. Open the door and block it open.
3. Discharge high voltage capacitor.
4. Remove the control panel assembly, referring to chapter of CONTROL PANEL ASSEMBLY REMOVAL.
5. Remove the three (3) screws holding the control unit to the control panel frame. And remove the control unit.
6. Remove the rubber connector from the long slit on the control panel frame.
7. Tear away the graphic sheet from the control panel frame.
8. Tear away the membrane switch from the control panel frame.
Installation
1. Remove remaining adhesive on the control panel frame surfaces with a soft cloth soaked in alcohol.
2. Tear the backing paper from the new membrane switch.
3. Insert the ribbon cable of the membrane switch into the slit of the control panel frame.
4. Adjust the upper edge and right edge of the membrane switch to the small depression on the surface of the control panel frame.
5. Attach the membrane switch to the control panel frame by rubbing with a soft cloth not to scratch.
Small backing paper
Ribbon cable
Graphic sheet
Ribbon cable of membrane switch
Membrane switch
Long slit
Slit
Small depression
Control panel frame
(Rear side)
Conductor portions
Rubber connector
Figure C-2. Graphic Sheet and Membrane Switch
Replacement
6
6. Tear the backing paper from the new graphic sheet.
7. Adjust the upper edge and right edge of the graphic sheet to the large depression on the surface of the control panel frame.
8. Attach the graphic sheet to the control panel frame by rubbing with a soft cloth not to scratch.
9. Tear the small backing paper from the ribbon cable of the membrane switch.
10. Attach the ribbon cable to the control panel frame rear side.
R- 314FS
R- 316FS
12. Place the edge of the membrane switch’s ribbon cable on the lower portion of the liquid crystal display.
12. Insert the rubber connector into the long slit on the control panel frame.
13. Reinstall the control unit to the control panel frame with the three (3) screws.
NOTE:
Do not contact the conductor portion of the ribbon cable (edge) and the rubber connector directly with your fingers. This is to avoid oxidized.
DOOR REPLACEMENT
REMOVAL
1. Disconnect the power supply cord.
2. Open the door slightly.
3. Insert a putty knife (thickness of about 0.5mm) into the gap between the choke cover and door frame as shown in Figure C-4 to free engaging parts.
4. Pry the choke cover by inserting a putty knife as shown
Figure C-4.
5. Release choke cover from door panel.
6. Now choke cover is free.
NOTE: When carrying out any repair to the door, do not bend or warp the slit choke (tabs on the door panel assembly) to prevent microwave leakage.
7. Release two (2) pins of door panel from two (2) holes of upper and lower oven hinges by lifting up.
8. Now, door panel with door frame is free from oven cavity.
Door Frame
Putty Knife
Choke Cover
Figure C-4. Door Disassembly
9. Release door panel from eight (8) tabs of door frame.
10.Now, door panel with sealer film is free.
11.Tear sealer film from door panel.
12.Now, door panel is free.
13.Slide latch head upward and remove it from door frame with releasing latch spring from door frame and latch head.
14.Now, latch head and latch spring are free.
15.Remove door screen from door frame.
16.Now, door screen is free.
17.Unfold each eleven (11) tab of the door decoration upper and lower by using a pair of needle-nose pliers. Now the door frame is loose.
REINSTALLATION
1. Insert each eleven (11) tab of the door decoration upper and lower into each slit of the door frame by using a pair of needle-nose pliers.
2. Reinstall door screen to door frame .
3. Reinstall the latch spring to the latch head. Reinstall the latch spring to the door frame. Reinstall latch head to door frame.
4. Reinstall door panel to door frame by fitting eight (8) tabs of door frame to eight (8) holes of door panel.
5. Put sealer film on door panel. Refer to “Sealer Film” about how to handle new one.
6. Catch two (2) pins of door panel on two (2) hole of upper and lower oven hinges.
7. Reinstall choke cover to door panel by pushing.
Note: After any service to the door;
(A) Make sure that door sensing switch and secondary interlock switch are operating properly. (Refer to chapter “Test Procedures”.).
(B) An approved microwave survey meter should be used to assure compliance with proper microwave radiation emission limitation standards.
After any service, make sure of the following :
1. Door latch heads smoothly catch latch hook through latch holes and that latch head goes through center of latch hole.
2. Deviation of door alignment from horizontal line of cavity face plate is to be less than 1.0mm.
3. Door is positioned with its face pressed toward cavity face plate.
4. Check for microwave leakage around door with an approved microwave survey meter. (Refer to Microwave
Measurement Procedure.)
Note: The door on a microwave oven is designed to act as an electronic seal preventing the leakage of microwave energy from oven cavity during cook cycle. This function does not require that door be airtight, moisture (condensation)-tight or light-tight.
Therefore, occasional appearance of moisture, light or sensing of gentle warm air movement around oven door is not abnormal and do not of themselves indicate a leakage of microwave energy from oven cavity.
7
D
E
F
B
C
R - 31 4 F S
R - 31 6 F S
1
A
2 3 4 5
RECTIFIER
H.V.
6
A
B
C
D
E
F
G
H
1
G
2 3
8
4
B L K
Y L W
R E D
R E D
5 6
H
R- 314FS
R- 316FS
∆
∆
*
*
*
*
*
*
*
1- 8
1- 9
1- 9
1-10
1-11
1-12
1-12
1-12
1-12
1-13
1-13
1- 1
1- 1
1- 2
1- 3
1- 4
1- 5
1- 5
1- 5
1- 6
1- 6
1- 7
1- 7
1- 8
∆
∆
4- 1
4- 2
4- 3
4- 4
4- 5
4- 6
4- 7
4- 8
4- 9
4-10
4-11
4-12
4-13
4-14
4-15
4-16
4-17
4-18
3- 1
3- 1
3- 1-1
3- 1-1
3- 1-2
3- 2
3- 2-1
3- 2-2
3- 3
3- 4
3- 5
3- 6
3- 7
3- 8
3- 9
3-10
PARTS LIST
Note: The parts marked “
∆
” may cause undue microwave exposure.
The parts marked “*” are used in voltage more than 250V.
REF. NO.
2- 1
2- 2
2- 3
PART NO.
DESCRIPTION
ELECTRIC PARTS
QSW-MA147WRZZ Secondary interlock switch/door sensing switch
QSW-MA137WRE0 Secondary interlock switch/door sensing switch (Interchangeable)
QFSHDA009WRE0 Fuse holder
FFS-BA023WRK0 Monitor fuse 20A and monitor switch(AM51620C53Y1) assembly
RTHM-A127WRZZ Thermal cut-out 125 deg.C (Oven)
FACCDA089WREZ Power supply cord
FACCDA082WRE0 Power supply cord (Interchangeable)
FACCDA086WREZ Power supply cord (Interchangeable)
FH-DZA092WRK0 High voltage rectifier assembly
FH-DZA088WRK0 High voltage rectifier assembly (Interchangeable)
RC-QZA211WRE0 High voltage capacitor
RC-QZA286WRZZ High voltage capacitor (Interchangeable)
RV-MZA308WRZZ Magnetron
RV-MZA288WRE0 Magnetron (Interchangeable)
RMOTEA383WRE0 Fan motor
RMOTEA408WRZZ Fan motor (Interchangeable) for production use
RTRN-A664WRZZ Power transformer
RLMPTA082WRZZ Oven lamp
RMOTDA211WRE0 Turntable motor
RMOTDA186WRE0 Turntable motor (Interchangeable)
RMOTDA161WRE0 Turntable motor (Interchangeable)
RMOTDA229WRE0 Turntable motor (Interchangeable)
RTHM-A120WRE0 Thermal cut-out 145 deg.C (MG.)
RTHM-A080WRE0 Thermal cut-out 145 deg.C(MG.) (Interchangeable)
CABINET PARTS
GCABUA861WRPZ Outer case cabinet
GDAI-A343WRWZ Bottom plate
GLEGPA074WRE0 Foot
CONTROL PANEL PARTS
FPNLCB665WRKZ Control panel frame with key unit [R-314FS]
FPNLCB666WRKZ Control panel frame with key unit [R-316FS]
PSHEPA850WRZZ Graphic sheet [R-314FS]
PSHEPA852WRZZ Graphic sheet [R-316FS]
QSW-KA021DRZZ Membrane switch
FBTN-A145WRKZ Open button assembly
JBTN-B185WRFZ Open button
HDECQA229WRRZ Button decoration
MSPRCA050WRE0 Open button spring
DPWBFC248WRUZ Control unit
PSHEPA851WREZ LED sheet
QCNC-A015WRZZ Rubber connector
RLCDSA108DRZZ Liquid crystal display
GMADIA116WRRZ Display window
HDECQA234WRPZ Conrol panel decoration
XEPSD30P08XS0 Screw; 3mm x 8mm
OVEN PARTS
PCUSUA235WRP0 Cushion
PPACGA084WRF0 TTM packing
PHOK-A114WRF0 Latch hook
LBNDKA099WRW0 Capacitor holder
NFANJA029WRE0 Fan blade
PDUC-A790WRWZ Fan duct
************* Oven cavity (Not a replaceable part)
LANGFA194WRW0 Chassis support
PCUSGA560WREZ Cushion
MLEVPA233WRF0 Switch lever
PCUSUA212WRP0 Cushion
NCPL-A053WRFZ Coupling
PCUSUA511WRP0 Cushion
PCOVPA349WRE0 Waveguide cover
PCUSGA339WRP0 Cushion
PCUSGA399WRE0 Cushion
PCUSUA512WRP0 Cushion
PCUSGA321WRP0 Cushion
Q'TY CODE
1
1
1
1
1
1
1
1
3
1
1
1
1
1
1
1
1
1
1
BE
AX
AC
AU
AB
BF
AW
AH
AU
AL
AU
AA
BB
BB
AW
AW
AQ
AS
AK
1
1
1
1
1
1
1
1
1
1
1
1
1
1
1
1
1
1
1
2
2
1
1
1
AS
AQ
AH
AP
BK
AV
--
BM
AL
AS
AW
AS
AV
AN
AK
AP
AV
AV
BL
AG
AH
AG
AS
AK
2
1
1
1
1
1
1
1
1
1
1
1
1
1
1
1
1
1
--
AU
AB
AG
AB
AE
AC
AE
AE
AF
AQ
AC
AL
AZ
AF
AF
AB
AH
9
R - 31 4 F S
R - 31 6 F S
∆
∆
∆
∆
∆
5- 1
5- 2
5- 3
5- 3
5- 3-1
5- 3-2
5- 3-3
5- 4
5- 4
5- 5
5- 6
5- 7
5- 8
7- 1
7- 2
7- 3
7- 4
7- 5
7- 6
7- 7
7- 7
7- 8
7- 9
7-10
REF. NO.
4-19
4-20
4-21
4-20
6- 1
6- 2
6- 3
6- 4
6- 5
6- 6
6- 7
PART NO.
DESCRIPTION
PCUSUA474WRP0 Cushion
PCUSGA562WREZ Cushion
PCUSUA190WRP0 Cushion
PCUSUA191WRP0 Cushion
DOOR PARTS
FDORFA332WRT0 Door panel
PSHEPA382WRE0 Sealer film
CDORFA962WRKZ Door assembly [R-314FS]
CDORFA963WRKZ Door assembly [R-316FS]
GWAKPA869WRFZ Door frame
HDECQA230WRRZ Door decoration U
HDECQA231WRRZ Door decoration L
HPNL-A781WRRZ Door screen [R-314FS]
HPNL-A783WRRZ Door screen [R-316FS]
LSTPPA188WRF0 Latch head
MSPRTA187WRE0 Latch spring
GCOVHA405WRF0 Choke cover
XCPSD40P08000 Screw : 3mm x 6mm
MISCELLANEOUS
FROLPA079WRK0 Turntable support
NTNT-A051WRE0 Turntable tray
FW-VZB905WRRZ Main wire harness
TINSEA930WRRZ Instruction book
PZET-A012WRE0 Terminal insulator
TCAUAA265WRRZ DHHS caution label
TCAUAA254WRR0 Monitor caution label
SCREWS,NUTS AND WASHERS
XHPSD40P08K00 Screw : 4mm x 8mm
XHPSD30P06000 Screw : 3mm x 6mm
XHTSD40P08RV0 Screw : 4mm x 8mm
XHTSD40P12RV0 Screw : 4mm x 12mm
XOTSD40P12RV0 Screw : 4mm x 12mm
XOTSD40P08000 Screw : 4mm x 8mm
XOTSF40P08000 Screw : 4mm x 8mm [R-301FK]
XOTSE40P08000 Screw : 4mm x 8mm [R-301FW]
LX-CZA070WRE0 Special screw (Torx tamper proof screw)
LX-CZ0052WRE0 Special screw
XHPSD40P08000 Screw : 4mm x 8mm
HOW TO ORDER REPLACEMENT PARTS
To have your order filled promptly and correctly, please furnish the following information.
1. MODEL NUMBER
2. REF. NO.
3. PART NO.
4. DESCRIPTION
Order Parts from the authorized SHARP parts Distributor for your area.
Defective parts requiring return should be returned as indicated in the Service Policy.
1
17
1
6
1
4
1
1
2
2
4
1
1
1
1
1
1
1
1
1
1
1
1
1
2
1
1
1
1
1
1
Q'TY CODE
2
1
1
1
AC
AC
AC
AC
AU
AT
AT
AG
AC
AH
AA
BB
AH
BP
BP
AX
AU
AA
AA
AA
AA
AA
AA
AA
AA
AC
AA
AA
AQ
AR
AU
AP
AB
AC
AC
10
7-6
5
7-8
6
R- 314FS
R- 316FS
A
1 2
OVEN AND CABINET PARTS
3
2-1
4
A
7-6
B
C
4-19
4-17
1-4
4-21
4-9
4-20
6-7
4-13
4-7
4-11
7-10
4-22
1-8
6-6
7-7
7-8
B
C
D
4-12
E
6-2
4-14
F
G
6-1
7-3
1-5 7-6
D
7-4
4-1
4-2
1-12
7-1
2-2
4-18
4-15
7-9
4-10
4-11
1-6
1-1
1-2
7-1
1-7
1-3
4-4
7-6
4-5
1-10
4-3 1-1
7-5
7-1
1-13
7-6
4-19
7-2
7-3
4-8
7-6
E
F
4-6
4-16
1-9
1-11
7-1 G
7-6
H
1 2
2-3
3
7-6
11
7-6
7-6
4 5 6
H
R - 31 4 F S
R - 31 6 F S
1 2
CONTROL PANEL PARTS
A 3-9 3-8
3 4
Before attaching Control unit to Control panel, foil side of Control unit must be cleaned by ethyl-alcohol.
5
3-10
3-1
3-1-1
B
3-6
C
3-1-2
3-4
5-7
DOOR PARTS
3-2
3-2-1
3-3
D
5-2
E
3-2-2
5-3
5-3-1
5-3-2
5-1
6
5-8
5-4
5-3-3
F
5-5
5-6
A
B
C
D
E
F
G G
MISCELLANEOUS
6-3
6-5
H H
1 2 3
Actual wire harness may be different from illustration.
4 5
12
6
F
G
H
1
1 2
A
PACKING AND ACCESSORIES
3
B
DOOR PROTECTION SHEET
SPADPA204WRE0
4
C
D
INTO THE
OVEN CAVITY
6- 4 INSTRUCTION BOOK
& PRINTING MATTER
6- 2 TURNTABLE TRAY
6- 1 TURNTABLE SUPPORT
TRAY PACK
SPADFA527WREZ
Not replaceable items.
E
2 3
13
4 5
5 6
R- 314FS
R- 316FS
A
TOP PAD ASSEMBLY
FPADBA492WRKZ
B
PLASTIC BAG
SSAKHA034WRE0
C
BOTTOM PAD ASSEMBLY
FPADBA493WRKZ
D
PACKING CASE
FPAK-A435WRKZ [R-314FS]
FPAK-A436WRKZ [R-316FS]
E
F
G
6
H
R - 31 4 F S
R - 31 6 F S
COPYRIGHT © 2002 BY SHARP CORPORATION
ALL RIGHTS RESERVED.
No part of this publication may be reproduced, stored in retrieval systems, or transmitted in any form or by any means, electronic, mechanical, photocopying, recording, or otherwise, without prior written permission of the publisher.
14
2002 SHARP CORP. (2S1.700E) Printed in U.S.A
advertisement
* Your assessment is very important for improving the workof artificial intelligence, which forms the content of this project
Related manuals
Frequently Answers and Questions
What precautions should be taken before servicing the oven to avoid exposure to excessive microwave energy?
If the oven operates with the door open, what should the service person do?
How often should a microwave leakage check be performed?
What should be placed in the oven cavity during a microwave power output test?
What is the microwave power density limit for a microwave oven?
What type of instrument should be used for microwave leakage testing?
advertisement
Table of contents
- 1 TABLE OF CONTENTS
- 2 PRECAUTIONS TO BE OBSERVED BEFORE AND DURING SERVICING TO
- 2 BEFORE SERVICING
- 3 WARNING TO SERVICE PERSONNEL
- 4 MICROWAVE MEASUREMENT PROCEDURE
- 5 WARNING
- 6 SPECIFICATION
- 6 GENERAL INFORMATION
- 7 OVEN DIAGRAM
- 8 SCHEMATIC
- 8 COMPONENT REPLACEMENT AND ADJUSTMENT PROCEDURE
- 8 GRAPHIC SHEET AND MEMBRANE SWITCH REPLACEMENT
- 9 DOOR REPLACEMENT
- 10 PICTORIAL DIAGRAM PARTS LIST ..........................
- 11 PARTS LIST
- 12 HOW TO ORDER REPLACEMENT PARTS
- 13 OVEN AND CABINET PARTS
- 14 CONTROL PANEL / DOOR PARTS
- 15 PACKING AND ACCESSORIES