advertisement
▼
Scroll to page 2
of
85
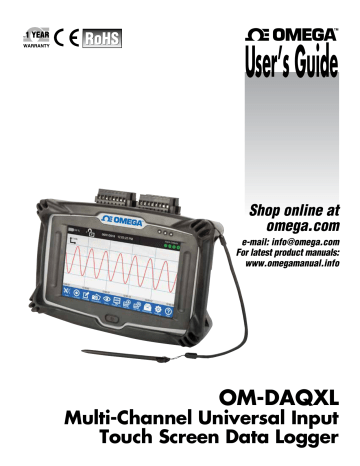
TM User’s Guide Shop online at omega.com e-mail: [email protected] For latest product manuals: www.omegamanual.info OM-DAQXL Multi-Channel Universal Input Touch Screen Data Logger omega.com [email protected] Servicing North America: U.S.A.: Omega Engineering, Inc., Toll-Free: 1-800-826-6342 (USA & Canada only) Customer Service: 1-800-622-2378 (USA & Canada only) Engineering Service: 1-800-872-9436 (USA & Canada only) Tel: (203) 359-1660 Fax: (203) 359-7700 e-mail: [email protected] For Other Locations Visit omega.com/worldwide The information contained in this document is believed to be correct, but OMEGA accepts no liability for any errors it contains, and reserves the right to alter specifications without notice. OM-DAQXL Multi Channel Touch Screen Data Logger TABLE OF CONTENTS Section Page Section 1 - Introduction ........................................................................ 1-1 1.1 Precautions .............................................................................................................. 1-1 1.2 Safety Warnings and IEC Symbols ...................................................................... 1-1 1.3 Statement on CE Marking ..................................................................................... 1-1 1.4 Overview ................................................................................................................. 1-2 1.4.1 Operating Environment................................................................................ 1-2 Section 2 - Hardware........................................................................... 2-1 2.1 Package Inspection................................................................................................. 2-1 2.2 Included Items......................................................................................................... 2-1 2.3 Part Names and Functions ................................................................................... 2-2 2.3.1 Front................................................................................................................. 2-2 2.3.2 Back.................................................................................................................. 2-3 2.3.3 Left Side........................................................................................................... 2-3 2.3.4 Right Side........................................................................................................ 2-4 2.3.5 Top................................................................................................................... 2-4 2.3.6 Bottom............................................................................................................. 2-4 2.4 Removing and Installing Rubber Boot ............................................................... 2-5 2.5 Wall Mounting ....................................................................................................... 2-5 2.6 Sensor Connections................................................................................................ 2-6 2.6.1 Two Wire Sensors .......................................................................................... 2-6 2.6.1.1 Thermocouples........................................................................................ 2-6 2.6.1.2 Voltage Wiring ....................................................................................... 2-6 2.6.1.3 Current Wiring ....................................................................................... 2-7 2.6.2 Three and Four Wire Sensors............................................................................. 2-7 2.6.2.1 Two Wire RTD Wiring ........................................................................... 2-7 2.6.2.2 Three Wire RTD Wiring ......................................................................... 2-8 2.6.2.3 Four Wire RTD Wiring ........................................................................... 2-8 2.6.2.4 Thermistor Wiring .................................................................................. 2-9 2.6.2.5 Bridge Sensor Wiring ............................................................................. 2-9 2.7 Digital I/O Connections...................................................................................... 2-10 2.8 Alarm, Excitation and Trigger............................................................................ 2-11 2.9 USB Device and Host Ports................................................................................. 2-11 2.10 LED Indication.................................................................................................... 2-12 2.11 Battery Pack and Power Adapter..................................................................... 2-13 2.11.1 Connecting the Battery Pack .................................................................... 2-13 2.11.2 Connecting the AC Adaptor .................................................................... 2-14 2.11.3 Powering on the Data Logger .................................................................. 2-14 Section 3 - Standalone Operation ........................................................ 3-1 3.1 Login Window ........................................................................................................ 3-1 3.2 Home Screen ........................................................................................................... 3-2 3.2.1 Status/Information Display ........................................................................ 3-2 3.2.2 Data Display Area ......................................................................................... 3-3 3.2.3 Home Toolbar ................................................................................................ 3-3 3.2.4 User Interface Flowchart .............................................................................. 3-4 i TABLE OF CONTENTS ii OM-DAQXL Multi Channel Touch Screen Data Logger 3.3 Setting Screens ........................................................................................................ 3-5 3.3.1 Add Channels ................................................................................................ 3-5 Input Type–Physical Input Channel................................................................ 3-5 Temperature Inputs............................................................................................ 3-5 Strain Gage Inputs.............................................................................................. 3-7 Voltage Inputs..................................................................................................... 3-9 Current Inputs................................................................................................... 3-11 Digital Inputs..................................................................................................... 3-13 Totalizer.............................................................................................................. 3-16 Resettable Counter............................................................................................ 3-18 Input Setup - Virtual Math Channel.............................................................. 3-19 3.3.2 Channel List ................................................................................................. 3-21 3.3.3 Trigger Settings ........................................................................................... 3-22 Timer Trigger Events........................................................................................ 3-23 Date and Time Trigger Events........................................................................ 3-23 Weekday and Time Trigger Events................................................................ 3-24 Alarm Output Trigger Events......................................................................... 3-24 External Trigger Events................................................................................... 3-25 3.3.5 Data Session Settings .................................................................................. 3-26 3.3.6 Alarm Settings ............................................................................................. 3-27 Main Alarm Screen........................................................................................... 3-27 Alarm Status...................................................................................................... 3-27 Alarm Table....................................................................................................... 3-27 Alarm Toolbar................................................................................................... 3-28 Add/Edit Alarm Screen................................................................................... 3-29 3.3.7 Device Settings ............................................................................................ 3-30 General/Data and Time................................................................................... 3-30 Display Options................................................................................................ 3-31 Communication Settings.................................................................................. 3-32 Diagnostics......................................................................................................... 3-34 User Management............................................................................................. 3-35 Change Password............................................................................................. 3-37 About Your Logger/Firmware....................................................................... 3-38 3.4 Viewing Data ........................................................................................................ 3-40 3.4.1 Select Channels ............................................................................................ 3-41 3.4.2 Waveform View .......................................................................................... 3-42 3.4.3 Waveform and Table View ........................................................................ 3-43 3.4.4 Table Only View ......................................................................................... 3-44 3.4.5 Digital View ................................................................................................. 3-45 3.4.6 Screenshot .................................................................................................... 3-46 3.4.7 Annotate........................................................................................................ 3-46 3.5 Operating Modes ................................................................................................. 3-47 3.5.1 Free-Running................................................................................................ 3-47 3.5.2 Armed Mode................................................................................................ 3-47 3.5.3 Logging Mode.............................................................................................. 3-47 3.5.4 Data Review Mode...................................................................................... 3-47 OM-DAQXL Multi Channel Touch Screen Data Logger TABLE OF CONTENTS Section 4 - Notes page ........................................................................ 4-1 Section 5 - Troubleshooting .................................................................. 5-1 5.1 Hardware Issues .................................................................................................... 5-1 5.2 Error Messages ....................................................................................................... 5-1 Section 6 - Service and Calibration ....................................................... 6-1 Section 7 - Specifications ...................................................................... 7-1 7.1 General .................................................................................................................... 7-1 7.2 Inputs ....................................................................................................................... 7-2 7.3 Functions ................................................................................................................. 7-3 7.4 Communication....................................................................................................... 7-4 7.5 External I/O............................................................................................................. 7-4 7.6 Dimensions.............................................................................................................. 7-5 Section 8 - International Approvals ...................................................... 8-1 OM-DAQXL Multi Channel Touch Screen Data Logger LIST OF TABLES List of Tables TableDescription .......................................................................................... Page Table 2-1 OM-DAQXL Models................................................................................ 2-1 Table 2-2 OM-DAQXL Included Items .................................................................. 2-1 Table 2-3 Two Wire Sensor Connections............................................................... 2-6 Table 2-4 Three and Four Wire Sensor Connections............................................ 2-7 Table 2-5 Digital I/O Cable Pinout....................................................................... 2-10 Table 2-6 Alarm Terminal Block Signals.............................................................. 2-11 Table 2-7 Status LED States.................................................................................... 2-12 Table 3-1 Alarm Type/Status Indicator Color.................................................... 3-27 OM-DAQXL Multi Channel Touch Screen Data Logger LIST OF FIGURES List of Figures Figure Figure 2-1 Figure 2-2 Figure 2-3 Figure 2-4 Figure 2-5 Figure 2-6 Figure 2-7 Description .......................................................................................... Page Included Items.......................................................................................... 2-2 OM-DAQXL Front View......................................................................... 2-2 OM-DAQXL Back View.......................................................................... 2-3 OM-DAQXL Left Side View................................................................... 2-3 OM-DAQXL Right Side View................................................................. 2-4 OM-DAQXL Top View............................................................................ 2-4 OM-DAQXL Bottom View...................................................................... 2-4 iii LIST OF FIGURES OM-DAQXL Multi Channel Touch Screen Data Logger List of Figures (Continued) Figure Figure 2-8 Figure 2-9 Figure 2-10 Figure 2-11 Figure 2-12 Figure 2-13 Figure 2-14 Figure 2-15 Figure 2-16 Figure 2-17 Figure 2-18 Figure 2-19 Figure 2-20 Figure 2-21 Figure 2-22 Figure 2-23 Figure 2-24 Figure 2-25 Figure 2-26 Figure 3-1 Figure 3-2 Figure 3-3 Figure 3-4 Figure 3-5 Figure 3-6 Figure 3-7 Figure 3-8 Figure 3-9 Figure 3-10 Figure 3-11 Figure 3-12 Figure 3-13 Figure 3-14 Figure 3-15 Figure 3-16 Figure 3-17 Figure 3-18 Figure 3-19 Figure 3-20 iv Description .......................................................................................... Page Removing and Installing Rubber Boot.................................................. 2-5 OM-DAQXL Wall Mounting.................................................................. 2-5 Thermocouple Wiring Example............................................................. 2-6 Voltage Wiring Example......................................................................... 2-6 DC Current Wiring Example - External Excitation............................. 2-7 2-Wire RTD Wiring Example.................................................................. 2-7 3-Wire RTD Wiring Example.................................................................. 2-8 4-Wire RTD Wiring Example.................................................................. 2-8 Thermistor Wiring Example................................................................... 2-9 Bridge Sensor Wiring Example.............................................................. 2-9 Digital I/O Connector Pin Numbers................................................... 2-10 Connecting the Digital I/O Cable........................................................ 2-10 Alarm Terminal Block............................................................................ 2-11 USB Cable Connection to Data Logger............................................... 2-11 USB Cable Connection to PC................................................................ 2-11 Inserting USB Accessories..................................................................... 2-11 Status LED Locations............................................................................. 2-12 Removing Battery Door......................................................................... 2-13 Connecting Battery................................................................................. 2-13 Login Window.......................................................................................... 3-1 Home Screen............................................................................................. 3-2 Status Display........................................................................................... 3-2 Home Toolbar........................................................................................... 3-3 Menu Flowchart........................................................................................ 3-4 Settings Fly-Out Menu............................................................................. 3-5 Input Type - Temperature....................................................................... 3-5 Data Ranges - Temperature.................................................................... 3-6 Input Type - Strain Gage......................................................................... 3-7 Data Ranges - Strain Gage....................................................................... 3-8 Input Type - Voltage................................................................................ 3-9 Data Ranges - Voltage............................................................................ 3-10 Input Type - Current.............................................................................. 3-11 Data Ranges - Current........................................................................... 3-12 Input Type - Digital Frequency............................................................ 3-13 Data Ranges - Digital Frequency.......................................................... 3-14 Data Range - Volumetric Flow............................................................. 3-15 Input Type Digital Totalizer................................................................. 3-16 Data Ranges - Digital Totalizer............................................................ 3-17 Input Type Digital Resettable Counter............................................... 3-18 OM-DAQXL Multi Channel Touch Screen Data Logger LIST OF FIGURES List of Figures (Continued) Figure Figure 3-21 Figure 3-22 Figure 3-23 Figure 3-24 Figure 3-25 Figure 3-26 Figure 3-27 Figure 3-28 Figure 3-29 Figure 3-30 Figure 3-31 Figure 3-32 Figure 3-33 Figure 3-34 Figure 3-35 Figure 3-36 Figure 3-37 Figure 3-38 Figure 3-39 Figure 3-40 Figure 3-41 Figure 3-42 Figure 3-43 Figure 3-44 Figure 3-45 Figure 3-46 Figure 3-47 Figure 3-48 Figure 3-49 Figure 3-50 Figure 3-51 Figure 3-52 Figure 3-53 Figure 3-54 Figure 3-55 Figure 3-56 Figure 3-57 Figure 3-58 Figure 3-59 Figure 3-60 Description .......................................................................................... Page Data Ranges - Resettable Counter........................................................ 3-18 Input Type - Virtual Math..................................................................... 3-19 Data Ranges - Virtual Math.................................................................. 3-20 Channel List screen................................................................................ 3-21 Trigger Settings....................................................................................... 3-22 Timer Trigger Event............................................................................... 3-23 Date and Time Trigger Event............................................................... 3-23 Weekday and Time Trigger Event....................................................... 3-24 Alarm Trigger Event.............................................................................. 3-24 External Trigger Event........................................................................... 3-25 Data Session Screen................................................................................ 3-26 Main Alarm Screen................................................................................. 3-27 Alarm Toolbar......................................................................................... 3-28 Add/Edit Alarm Screen........................................................................ 3-29 Device Settings........................................................................................ 3-30 General Settings Screen......................................................................... 3-30 Display Options Screen......................................................................... 3-31 Communication Setting - Ethernet...................................................... 3-32 Communication Setting - Wi-Fi............................................................ 3-33 Device Settings Diagnostics Screen..................................................... 3-34 User Management Screen...................................................................... 3-35 Add User.................................................................................................. 3-36 Change Password Screen...................................................................... 3-37 About Screen........................................................................................... 3-38 Firmware Upgrade Screen.................................................................... 3-39 Firmware Upgrade Success.................................................................. 3-39 Display Channel Fly-Out Menu........................................................... 3-40 Views Fly-Out Menu.............................................................................. 3-40 Select Channels Screen.......................................................................... 3-41 Waveform View...................................................................................... 3-42 Graph Scale Selector............................................................................... 3-42 Waveform and Table View................................................................... 3-43 Table Only View..................................................................................... 3-44 Four Channel Digital View................................................................... 3-45 Single Channel Digital View................................................................. 3-45 Annotate.................................................................................................. 3-46 Stored File Directories........................................................................... 3-48 Stored Files List....................................................................................... 3-49 Data Review Screen................................................................................ 3-50 Review Mode Channel List................................................................... 3-51 v 1 Introduction Section 1 - Introduction Thank you for purchasing the OMEGATM OM-DAQXL portable data logger. This User’s Guide describes the functions of the OM-DAQXL as well as its operating methods and handling precautions. Read this manual thoroughly before using the OM-DAQXL to ensure correct use. In addition to this manual a Quick Start Guide is available separately for download at omega.com/manuals. The Quick Start Guide briefly describes the main functions and the basic procedures for performing such tasks as setup and measurement operations. Use the Quick Setup Manual together with this in-depth User’s Guide. After reading this manual, keep it in an easily accessible place for later reference. This manual will come in handy when you are unsure of how to operate the product. Please read this manual completely before installing and operating your OMEGA data logger system. It’s important to read and follow all notes, cautions, warnings and safety precautions before operating this device. “Device” refers to your data logger device. 1.1 Precautions • This device is not designed for use in any medical or nuclear applications. • Do not operate this device in flammable or explosive environments. • Never operate with a power source other than the one recommended in this manual or listed on product labels. • This device has been designed for dry, moisture free applications only. • Do not operate this device outside of the recommended use outlined in this manual. • Do not connect an Ethernet cable that is 30 meter or longer. • Do not connect an Ethernet cable that is outdoors. •E SD Warning—The following parts are ESD sensitive: Ground lug metal connectors for the USB host, USB device, mini-DIN, and Ethernet Jack (if applicable). 1.2 Safety Warnings and IEC Symbols This device is marked with international safety and hazard symbols in accordance with IEC standards. It is important to read and follow all precautions and instructions in this manual before operating or commissioning this device as it contains important information relating to safety and EMC. Failure to follow all safety precautions may result in injury and or damage to your device. Use of this device in a manner not specified will void your warranty. 1.3 Statement on CE Marking It is the policy of OMEGATM to comply with all worldwide safety and EMI/ EMC regulations that apply. OMEGA is constantly pursuing certification of its products to the European New Approach Directives. OMEGA will add the CE mark to every appropriate device upon certification. For additional information see Section 8 - International Approvals. 1-1 Introduction 1 1.4 Overview The OM-DAQXL is an 8 or 16 analog input portable data logger with a color 7” resistive touch screen display. It has user programmable inputs that can be configured for several different types of sensors including temperature sensors (thermocouple, RTD, thermistor), strain gage, process inputs (voltage and current) and digital pulse inputs. All configurable options (including individual channel input type and range) are software programmable. The device is powered by a 7.2V, 4.8 Ah Li-ion battery. In addition an external 12V, 5A AC adapter can be used to power the device for extended periods. The compact, portable packaging ensures ease of use in a variety of applications. Devices can be wall mounted using the provided keyhole mount or easily operated on a bench. The device has four operating modes: 1. Free Running – In this mode the device measures and displays configured analog / digital inputs. No Logging is performed. No Trigger conditions are set. 2. Armed Mode – In this mode the device measures and displays configured analog / digital inputs. A Start Trigger condition is set. No Logging is performed until the Start trigger condition is met. 3. Logging Mode – In this mode the device measures and displays configured analog / digital inputs. The device is also logging data from the input channels to the designated memory location, either the SD card or the USB drive or the internal memory. 4. Data Review Mode – In this mode users can review previously recorded data in a graphical view. Zoom in and out. Scroll through the data back and forth in time. Review recorded data from any 4 channels on one screen. 1.4.1 Operating Environment The OM-DAQXL has been designed to meet its stated specifications when operating within the ambient conditions outlined below. Temperature: 0 to 50 deg C (32 to 122 deg F) Humidity: 0 to 95% RH non-condensing In addition to restricting operation of the data logger to the given temperature and humidity ranges, a warmup period of 30 minutes is recommended to ensure best accuracy of measurements. 1-2 2 Hardware 2 Hardware 2.1 Package Inspection Remove the packing list and verify that you have received all your equipment. If you have any questions about the shipment, please call our Customer Service Department at the number listed on the first page of this manual or reaching us on the Internet at omega.com, e-mail: [email protected]. When you receive the shipment, inspect the container and equipment for any signs of damage. Note: Report any evidence of rough handling in transit. Immediately report any damage to the shipping agent. The carrier will not honor any damage claims unless all the shipping materials are saved for inspection. After examination and removal of contents, save packing material and carton in the event that reshipment is necessary. 2.2 Included Items The following items are supplied in the box: Data Logging Instrument Verify the model number shown on the rear label of your data logger matches what was ordered. Model OM-DAQXL-1-* OM-DAQXL-2-* OM-DAQXL-1-EW-* Specifications 8 channel data logger with USB Host/Device 16 channel data logger with USB Host/Device 8 channel data logger with USB Host/Device, Ethernet and Wi-Fi OM-DAQXL-2-EW-* 16 channel data logger with USB Host/Device, Ethernet and Wi-Fi Table 2-1 OM-DAQXL Models Included Items (see figure 2-1) No. Model No. 1 OM-DAQXL-RB 2 SD32GB 3 OM-DAQXL-USB 4 OM-DAQXL-CABLE6 5 OM-DAQXL-TB8 6 OM-DAQXL-ADAPTOR-* 7 SCREWDRIVER-2.5mm 8 MQS-5570 9 5TC-TT-K-20-36 10 11 12 13 NA PT-USB-1 OM-DAQXL-RF N/A * Specifies the country code. 2-1 Description Rubber boot for impact resistance 32GB SD card 6' USB cable Digital I/O cable ,6 ft. Alarm/excitation terminal block 12Vdc, 5A power adaptor Omega screwdriver OM-DAQXL Series quick start guide Type K thermocouples 5 pack with stripped leads Crimp on ground lug 1GB Flash drive Snap-on round cable ferrite 50Ω shunt resistor Table 2-2 OM-DAQXL Included items. Hardware 3 2 4 5 2 11 6 1 12 7 10 8 13 9 Figure 2-1 Included Items. 2.3 Part Names and Functions The figures in this section show the different parts of the data logger and provide a brief description of their functions. 2.3.1 Front The front of the data logger is comprised of 3 user interface elements. These are the 7” touch screen LCD, three status LEDs and the home button. The touch screen display is used to display all measured data, settings & configuration menus and status information. The three status LEDs provide visible indications of power & battery charging status, data logging status, and alarm status. Depending on the current status the color of the LEDs will vary. For LED color indications, see Section 2.10. The Home button is the single hardware button for the user interface. It provides a quick and easy way to return to the Home screen from any other screen with one button press. STATUS LEDS LCD DISPLAY TM HOME BUTTON Figure 2-2 OM-DAQXL Front View. 2-2 2 Hardware 2.3.2 Back The back side of the data logger has a kickstand which allows the device to sit at a 30 degree angle when sitting on a hard surface and snaps into place when not in use. The kickstand has 2 keyhole slots allowing it to act as a wall mounting bracket. See Section 2.5 for information on how to wall mount the device. The battery compartment door is also located on the back of the device. See Section 2.11 for information on how to replace the battery. Figure 2-3 OM-DAQXL Back View. 2.3.3 Left Side The left side of the data logger features connections for alarm outputs, digital I/O and DC power. $/$50(;7(51$/75,**(59 (;&,7$7,217(50,1$/ 32:(56:,7&+ ',*,7$/,2 9'&,1387 Figure 2-4 OM-DAQXL Left Side View 2-3 Hardware 2 2.3.4 Right Side The right side of the data logger features the USB host and device connectors as well as the shield ground terminal. The shield ground terminal may be connected to earth ground to minimize sensor noise pickup. In addition the stylus is stored in a slot on this side of the device. For -EW models, the Ethernet Port is present on the right side of the data logger. SHELL GROUND TERMINAL USB DEVICE PORT USB HOST PORT 2.3.5 Top ETHERNET PORT Figure 2-5 OM-DAQXL Right Side View The top of the data logger provides analog input terminal blocks for either 8 or 16 channels depending on the model. The terminal blocks are designed to accommodate wire between sizes 26 -14 AWG. See Section 2.6 for information on how to connect sensors. $1$/2*,13877(50,1$/6 Figure 2-6 OM-DAQXL Top View 2.3.6 Bottom 6'&$5'6/27 Figure 2-7 OM-DAQXL Bottom View 2-4 2 Hardware 2.4 Removing & Installing Rubber Boot The data logger ships with an impact resistant rubber boot pre-installed. OMEGA recommends leaving the protective rubber boot installed, but it can be removed for convenience. When removing the rubber boot be sure to do so with a support surface not more than 1 foot beneath the device to protect in the case of an accidental drop. To remove the device from the rubber boot first power off the device and disconnect all external connections including power, analog & digital inputs, and communication interfaces. Next while holding the device with one hand gripping the top of the device, use the other hand to pry one of the bottom corners of the rubber boot outward and downward until the corner of the device pops free from the boot. Repeat for the other bottom corner of the device. With both of the bottom corners free of the boot, continue to tilt the bottom of device upward and pull it outward until it is free from the boot. Installation is the reverse of removal. Figure 2-8 Removing Rubber Boot 2.5 Wall Mounting The data logger features a built in kick stand with keyhole screw slots that fit #6 (M3.5 metric) sized screws for wall mounting. 2-5 Figure 2-9 OM-DAXL Wall Mounting. Hardware 2 2.6 Sensor Connections This section shows how to connect sensors to your analog input terminals. There are 8 or 16 analog input channels (depending on the model) each having one positive terminal and one negative terminal clearly shown on the input label. Depending on the type of sensor being connected 2 input channels may be required. Input tables and figures are shown for each type of input. Bridged based sensors (strain gages, load cells and mV output pressure transducers) require excitation voltage which is provided on channels 1 and 2, 3 and 4, 9 and 10, 11 and 12 only. See tables 2-3 and 2-4 for wiring information. 2.6.1 Two wire sensors For two wire sensors any open channel can be configured to read the sensor. Sensor Type Temperature Thermocouple Voltage Process Current + TC+ V+ I+ Any Channel Table 2-3 Two wire sensor connections. – TCVI- 2.6.1.1 Thermocouples For thermocouple sensors the negative lead is always colored red (USA and Canada) or white (IEC 584-3). Figure 2-10 Thermocouple Wiring Example 2.6.1.2 Voltage Wiring Figure 2-11 DC Voltage Wiring Example 2-6 2 Hardware 2.6.1.3 Current Wiring For current measurement a 50Ω shunt resistor is provided. Figure 2-12 DC Current Wiring Example - External Excitation 2.6.2 Two, Three & Four Wire Sensors Sensor Type Temperature Bridge 2 Wire RTD 3 Wire RTD 4 Wire RTD Thermistor Strain Gage Load Cell Pressure Transducer Odd Channel + RTD+ RTD– RTD+ RTD– RTD+ RTD– Th+ ThEXC+ EXCEXC+ EXCEXC+ EXC- Table 2-4 Three and Four Wire Sensor Connections Even Channel + RTDRTDRTD+ RTDThV+ VV+ VV+ V- 2.6.2.1 Two-Wire RTD Wiring For RTD sensors the positive colored red and the common lead can be either black or white. A jumper wire must be connected between the negative leads of the two assigned channels as shown in figure 2-13. Figure 2-13 Two-Wire RTD Wiring Example 2-7 Hardware 2 2.6.2.2 Three-Wire RTD Wiring For 3-wire RTD sensors the second common lead must be connected to the negative terminal of the next consecutive even channel. Figure 2-14 Three-Wire RTD Wiring Example 2.6.2.3 Four-Wire RTD Wiring For 4-wire RTD sensors the data logger performs a Kelvin resistance measurement using 1 channel to supply excitation voltage and the next channel to sense the voltage across the RTD. Figure 2-15 Four-Wire RTD Wiring Example 2-8 2 Hardware 2.6.2.4 Thermistor Wiring For thermistor sensors connection, 2 channels are required as shown in Figure 2-16. Figure 2-16 Thermistor Wiring Example 2.6.2.5 Bridge Sensor Wiring For bridge based sensors excitation voltage is supplied on channels 1, 3, 9 and 11. The next consecutive even channels must be used to measure the sensor output. Bridge based sensor inputs are only available on channels 1-2, 3-4, 9-10 and 11-12. Figure 2-17 Bridge Sensor Wiring Example 2-9 Hardware 2 2.7 Digital I/O Connections The included 6’ digital I/O cable with stripped leads and mini-DIN connector makes connecting digital I/O to the data logger quick and simple. Table 2-5 shows the cable pinout and figure 2-18 shows the corresponding pins on the data logger connector. Signal Name Digital Input 1 Digital Input 2 Digital Input 3 Digital Input 4 Digital Output 1 Digital Output 2 Digital Output 3 Digital Output 4 Isolated Ground Pin # 1 2 3 4 5 6 7 8 9 Table 2-5 Digital I/O cable pinout. Wire Color White Red Orange Purple Brown Black Blue Green Yellow Figure 2-18 Digital I/O Connector Pin Numbers. Figure 2-19 Connecting the Digital I/O Cable. 2-10 2 Hardware 2.8 Alarm, Excitation & Trigger The eight position terminal block on the left side of the device has terminal positions for four alarm outputs, an isolated 24 VDC excitation supply and an external trigger input. Connections are made easy through the included pluggable terminal block. Follow the terminal indications on the label and connect to the appropriate position Signal Name Alarm 1 Alarm 2 Alarm 3 Alarm 4 Ground External Trigger Isolated Ground +24 Vdc Terminal # 1 2 3 4 5 6 7 8 Table 2-6 Alarm Terminal Block Signals Figure 2-20 Alarm Terminal Block 2.9 USB Device & Host ports The data logger features a USB device port for communication with a PC using the supplied USB cable. Figure 2-21 USB Cable Connection to Data Logger. Figure 2-22 USB Cable Connection to PC. There is also a USB host port which allows external USB memory to be used for data storage. USB Memory up to 64GB in size can be used with the data logger. The USB host can also be used to connect a USB mouse. For -EW models, the USB WiFi dongle accessory plugs into the USB host for WiFi capabilities. USB WiFi Figure 2-23 Inserting USB Accessories. 2-11 Hardware 2 2.10 LED Indication The three status LEDs on the front of the data logger provide an easy to see visual indication of the status of the device. This is useful when the LCD has been turned off or is difficult to read due to glare or distance. See figure 2-24 and table 2-7 for information on the different LED indications. Figure 2-24 Status LED Locations Led 1 – Power/ Charging 2 – Logging 3 - Alarm Status DC Adapter Battery Connected Charged Connected Charging Not connected Discharging Connected No battery Logging Not logging - Error Armed mode Free running Alarm condition No alarm Alarms disabled Color and State Green Green Flashing Green, amber battery <40% remaining, red battery <15% remaining. Flashing amber Flashing Green Red Amber Green Red Green Off Table 2-7 Status LED States 2-12 2 Hardware 2.11 Battery Pack and Power Adapter The data logger is a portable device and can operate on battery power for several hours before requiring recharging. The included battery is a 7.2V, 4.8 Ah Li-Ion battery. Also included is an AC adapter to provide 12VDC power for battery recharging. 2.11.1 Connecting the battery pack The data logger ships with the battery installed, but disconnected to keep it from completely draining during shipment. To connect the battery pack: 1. Remove the four screws securing the battery door using the included screw driver. Figure 2-25 Removing Battery Door. 2. Remove the battery from the compartment. 3. Plug the keyed connector on the end of the battery leads into the power connector in the battery compartment. IMPORTANT! Observe the correct polarity when plugging the battery into the data logger. ,16(57%$77(5< 3/8*+(5( Figure 2-26 Connecting Battery Close-Up of Battery Plug 4. Reinstall the battery in the compartment placing the leads under the battery. Be sure not to crimp the battery leads. 5. Reinstall the battery compartment door and tighten the 4 battery door screws. 2-13 Hardware 2 It is recommended to fully charge the battery using the included AC adapter after installation. When the device is powered off the LED next to the power switch will be illuminated to indicate that the battery is charging. In addition, when the device is powered on, the Power/Charging LED will be flashing green and the battery life indication on the LCD will show a lightning bolt symbol over the battery to indicate that it is being charged. 2.11.2 Connecting the AC Adapter The AC adapter is a universal input (100 – 240 VAC) adapter that provides 12 VDC output to power the data logger. The device ships with a power cord with the appropriate plug for the outlet type in your country or region. 1. Plug the AC cord into the AC adapter. 2. Connect the DC output plug of the adapter into the OM-DAQXL power port. 3. Plug the AC cord into the AC power outlet. 4. Turn on the power switch on the OM-DAQXL. 2.11.3 Powering on the Data Logger. After you have connected the battery and/or AC adapter you can now power on the data logger by pushing the power switch to the on position. The data logger will begin the boot process at which time a boot splash screen showing the OMEGA logo and a progress bar will appear. After approximately 30 seconds the data logger login screen will be shown. At this point you can login and begin configuring the data logger. The following chapter details all of the configuration steps necessary to begin using the data logger. 2-14 3 Standalone Operation 3 Standalone Operation The OM-DAQXL’s touch screen user interface makes configuring the data logger for operation straight forward and simple. The touch screen UI and associated menu screens allows the user to configure all of the parameters for data collection, while the home screen’s data display area provides a convenient and versatile indication of the data being monitored. It also facilitates easy review and analysis of previously recorded data without the need of a laptop or PC. 3.1 Login Window When the OM-DAQXL first boots up, the user is greeted with the login window. Here the user can either login with their username and password, login as a guest or hit Forgot Password to go to the Reset Password window. Login Window Normal user login Guest login Forgot Password Home Screen Figure 3-1 Login Window NOTE: For initial login use the default account with user name and password: omega, omega. This is an administrator account allowing additional users to be created. 3-1 Standalone Opteration 3 3.2 Home Screen After logging in, the home screen is displayed. The home screen is the main screen of the data logger user interface. It is divided into 3 distinct sections as shown in figure 3-2. Status/ Information display Data display area Navigation toolbar Figure 3-2 Home Screen 3.2.1 Status/Information Display The small black strip at the top of the home screen is the status and information display. It has indications for battery life, current user, data & time, operating mode and alarm outputs. 1 2 6 Lock Data Logger Change Password Logout 3 4 7 5 Show Alarm Figure 3-3 Status Display 1. Battery Status – A single tap on this icon will provide remaining run time information. 2. Username/Login – A single tap on this icon will invoke a fly-out menu. 3. System Clock – Displays the current date and time. 4. Data Logging Mode/Status – Shows the current logging mode: Free running, armed or logging. 5. Alarm Status – Shows the current status of the alarm outputs. A single tap on this icon will invoke the Show Alarm fly-out menu. 6. User Options Fly-Out Menu – This menu allows the current user to lock the data logger, change their password or logout. 7. Show Alarm Fly-Out Menu – A single tap on this show alarm menu will bring up the Alarm Settings menu. 3-2 3 Standalone Operation 3.2.2 Data Display Area The data display area shows the current values of the measure data for up to 4 channels simultaneously. There are four views available for this area: waveform, waveform & table, table only and digital. 3.2.3 Home Toolbar At the bottom of the home screen is the toolbar. The toolbar is where all the major functions and menus of the data logger can be accessed. It consists of 11 buttons each with a distinctive icon and text to provide a quick visual indication of the associated function. The buttons on the toolbar either perform an action or navigate to additional screens where settings can be configured 1 2 3 4 5 6 7 8 9 10 11 Figure 3-4 Home Toolbar 1. Tools Button - Extends or retracts the toolbar with each tap. When the toolbar is retracted there is additional channel information displayed in the toolbar area. 2. Log Data - The log data button is used to change the logging state of the data logger. Depending upon the current state this button will appear white (free running), red (logging) or orange (armed). 3. Annotate – The annotate button freezes the current display and allows the user the ability to make annotations on the display using the stylus. A screenshot will then be saved showing the annotation. 4. Screen Shot – Takes a screenshot of the current display and saves it to the memory location specified in the data session settings. 5. Views – Invokes a fly-out menu list with selections for the 4 different view modes as well as a selection for toggling the slide show feature. 6. Display Channels – Invokes a fly-out menu list with selections for the four channel groups as well as selection to bring the user to the channel group channel selection screen. 7. Add Channel – Opens the add channel screen with the next available channel selected for configuration. 8. Channel List - Opens the channel list screen which lists all the currently configured channels. 9. Stored Files – Opens the stored files screen to perform various operations on files in stored in memory. 10. Settings – Invokes a fly-out menu list with selections for trigger, alarm, and data session and device settings. Each selection opens a screen where settings related to that function can be set and saved. 11. Help – Opens a context sensitive help screen which will display content appropriate to the current screen. This button is present in all of the various UI screens. 3-3 Standalone Operation 3 3.2.4 User Interface Flowchart Log Data Depending on current state, starts logging or arms data logger. Annotate Pauses display and allows annotation on the display using the stylus. Screenshot Views Display Channel Toolbar Immediately takes a screenshot. Select data view or Toggle slide show Select channel group or Assign channels to groups Add Channel Channel List Shows a tabular list of all currently configured channels Stored Files Allows access to all stored data files for reviewing or copying. Settings Help Select the type of settings you wish to change. Provides access to context appropriate help screens Allows assignment of channels to 4 groups. Channel Groups Input Type Configure a new channels input type setting. Data Ranges Configure a new channels data range settings. Trigger Settings Alarm Settings Data Session Settings Device Settings Figure 3-5 Menu Flowchart 3-4 3 Standalone Operation 3.3 Settings Screens Most of the data logger settings are accessible through the settings button on the toolbar. Hitting the settings button invokes a small fly-out menu for selecting the specific settings screen to navigate to. Additional settings related to specific toolbar buttons functions are found in the associated screens or menus. Figure 3-6 Settings Fly-Out Menu 3.3.1 Add Channels Channel settings can be configured for new channels using the Input Type and Data Ranges screens. To add a new input channel and configure its settings, hit the Add Channel button on the toolbar to navigate to the Input Type screen. There are two types of channels which can be configured, physical input channels and virtual math channels. Depending on the type of channel being configured, the Input Type screen will have different settings available. The toolbar appears as shown below when adding channels. Input Setup – Physical Input Channel The Input Type screen is used to configure the basic settings for an input channel. For physical input channels the input type selected will determine the settings available. Temperature Inputs For temperature input types the Input Type screen will appear as shown below. 1 2 3 Figure 3-7 Input Type - Temperature 3-5 Standalone Operation 3 1. Channel Type Button The channel type selects between physical and math channel input types. Temperature inputs are physical input channels. 2. Input Type Settings For temperature inputs there are multiple sensor types available. These include thermocouple, RTD and thermistor. Each of these sensor types have additional sensor sub types available. The sub type drop-down list will populate with the appropriate subtypes for each sensor type. A channel number, color and name must be assigned for each channel. 3. Channel Map The channel map provides a quick view of which channels have already been configured (blue) and the currently selected channel (orange). Some temperature input types require the use of two input channels. The Data Ranges screen appears the same for all temperature input types. Depending on the sensor type selected the fixed values shown for the input and display range will vary. 1 7 2 6 3 4 5 Figure 3-8 Data Ranges - Temperature 1. Engineering Units The two drop downs allow selection of various engineering units for display. 2. Input Range The input range boxes show the full measureable input of the data logger for the sensor type being configured. These are not editable. 3. Display Range The display range boxes show the full display range available on the data logger. The graph range can be any subset of this range. This range is fixed for all temperature inputs. 4. Zero Adjust The zero adjust provides a user configurable offset adjustment, in engineering units, which will be applied to measurements across the full range of input. 3-6 3 Standalone Operation 5. Moving Average Filter This setting provides the option to average an individual channels input samples. 6. G raph Range The graph range is the y-axis range that will be shown on the waveform view of the data logger. This can be any subset of the display range and is defined in the assigned engineering units. It can also be adjusted on the waveform view. 7. D ecimal Places Selects the number of decimal place to display. Strain Gage Inputs For stain gage inputs the Input Type screen will appear as shown below. 1 2 3 Figure 3-9 Input Type - Strain Gage 1. Channel Type Button The channel type selects between physical and math channel input types. Strain gage inputs are physical input channels. 2. I nput Type Settings For strain gage inputs there are two sensor types available. These are full bridge 100Ω or full bridge 350Ω. In addition to the sensor type, an excitation voltage must be selected. You can select between 5V and 10V excitation. Two channels are required per strain gauge and excitation is provided on channel 1 or channel 3. A channel number, color and name must be assigned for each channel. 3. C hannel Map The channel map provides a quick view of which channels have already been configured (blue) and the currently selected channel (orange). 3-7 Standalone Operation 3 For strain gage inputs the data ranges screen has user editable input and display ranges. The input range values should correspond to the millivolt output of the transducer at 0% and 100% of the transducers range. The display range values should be set to the corresponding 0% and 100% values of the selected engineering units. The graph range can be a subset of the display range. 7 1 2 6 4 5 3 Figure 3-10 Data Ranges - Strain Gage 1. Engineering Units The two drop downs allow selection of various engineering units for display. 2. I nput Range The input range boxes show the full measureable input of the data logger for the sensor type being configured. For the case of strain gage, it is the full scale output of the bridge which is equal to bridge sensitivity (mV/V) multiplied by the excitation voltage across the bridge. 3. Display Range The display range boxes show the full display range available on the data logger. This should correspond the full scale output the sensor in terms of engineering units. The graph range can be any subset of this range. 4. Zero Adjust The zero adjust provides a user configurable offset adjustment, in engineering units, which will be applied to measurements across the full range of input. 5. Moving Average Filter This setting provides the option to average an individual channels input samples. 6. Graph Range The graph range is the y-axis range that will be shown on the waveform view of the data logger. This can be any subset of the display range and is defined in the assigned engineering units. It can also be adjusted on the waveform view. 7. Decimal Places Selects the number of decimal place to display. 3-8 3 Standalone Operation Voltage Inputs For voltage inputs the Input Type screen appears as shown below. 1 2 3 Figure 3-11 Input Type - Voltage 1. Channel Type Button The channel type selects between physical and math channel input types. Voltage inputs are physical input channels. 2. I nput Type Settings For voltage inputs there no sensor types or sub types available. Only 1 channel is required per voltage input. A channel number, color and name must be assigned for each channel. 3. C hannel Map The channel map provides a quick view of which channels have already been configured (blue) and the currently selected channel (orange). 3-9 3 Standalone Operation The Data Ranges screen for voltage inputs has several user editable fields which are used for linear scaling of a voltage input to the desired engineering units for display. 1 7 2 6 3 4 5 Figure 3-12 Data Ranges - Voltage 1. Engineering Units The three drop downs allow selection of various engineering units for display depending on the type parameter being measured. 2. Input Range The input range drop down shows the full measureable input of the data logger. For voltage inputs there are seven ranges available. In addition a custom input range can be assigned as a subset of any of the standard ranges. This allows easier scaling of transducer output that is a subset of the standard ranges to the display range. 3. Display Range The display range boxes show the full range in engineering units for the voltage input being configured. The graph range can be any subset of this range. 4. Zero Adjust The zero adjust provides a user configurable offset adjustment, in engineering units, which will be applied to measurements across the full range of input. 5. Moving Average Filter This setting provides the option to average an individual channels input samples. 6. Graph Range The graph range is the y-axis range that will be shown on the waveform view of the data logger. This can be any subset of the display range and is defined in the assigned engineering units. It can also be adjusted on the waveform view. 7. Decimal Places Selects the number of decimal place to display. Example: In this channel configuration, 0 to 5V input corresponds to 0 to 100 PSI. Engineering Unit = PSI Input Range = -5V to +5V Custom Input Range = 0 to +5V Display Range = 0 to 100 3-10 Graph Range = 3 to 15 3 Standalone Operation Current Inputs For current inputs the Input Type screen appears as shown below. A 50 Ω shunt resistor is required across the input terminals for current inputs. 1 2 3 Figure 3-13 Input Type – Current 1. Channel Type Button The channel type selects between physical and math channel input types. Current inputs are physical input channels. 2. I nput Type Settings For current inputs there no sensor types or sub types available. Only 1 channel is required per current input, but a 50 Ω shunt resistor must be installed across the input terminal. A channel number, color and name must be assigned for each channel. 3. C hannel Map The channel map provides a quick view of which channels have already been configured (blue) and the currently selected channel (orange). 3-11 3 Standalone Operation The Data Ranges screen for current inputs has several user editable fields which are used for linear scaling of a current input to the desired engineering units for display. 1 7 2 6 3 4 5 Figure 3-14 Data Ranges – Current 1. Engineering Units These drop downs allow selection of various engineering units for display depending on the type parameter being measured. 2. Input Range The input range drop down shows the full measureable input of the data logger. For current inputs there is a single range available. In addition a custom input range can be assigned as a subset of any of the standard ranges. This allows easier scaling of transducer output that is a subset of the standard ranges to the display range. 3. Display Range The display range boxes show the full range in engineering units for the current input being configured. The graph range can be any subset of this range. 4. Zero Adjust The zero adjust provides a user configurable offset adjustment, in engineering units, which will be applied to measurements across the full range of input. 5. Moving Average Filter This setting provides the option to average an individual channels input samples. 6. Graph Range The graph range is the y-axis range that will be shown on the waveform view of the data logger. This can be any subset of the display range and is defined in the assigned engineering units. It can also be adjusted on the waveform view. 7. Decimal Places Selects the number of decimal place to display. 3-12 3 Standalone Operation Digital Inputs For digital inputs a sensor type must first be selected. The available selections are frequency, totalizer and resettable counter. Frequency For frequency type digital inputs, the Input Type screen will appear as shown below. Additional measurement type drop-down selections are available. 1 2 3 Figure 3-15 Input Type - Digital Frequency 1. Channel Type Button The channel type selects between physical and math channel input types. Frequency inputs are physical input channels. 2. I nput Type Settings For digital inputs there are 3 different sensor types to choose from. The frequency type has two sub-types which affect the selects in the Data Ranges screen. Select frequency if you are measuring purely frequency and do not wish to convert to an engineering unit. Select volumetric flow rate if you are measuring flow using a frequency or pulse output flowmeter. 3. C hannel Map The channel map provides a quick view of which channels have already been configured (blue) and the currently selected channel (orange). 3-13 Standalone Operation 3 When configured for frequency measurement mode and measurement type frequency, the data ranges screen will appear as shown below. 1 5 2 4 3 Figure 3-16 Data Ranges - Digital Frequency 1. Engineering Unit Allows selection of various units for frequency measurement. 2. Input Frequency Shows the input range in terms of the selected engineering units. 3. Display Range Shows the display range also in terms of the selected engineering units. 4. Graph Range This is a subset of the display range. This determines what portion of the full display range will be shown initially in the waveform views. This range can also be adjusted from the waveform view. 5. Decimal Places Select the number of decimal places for display here. 3-14 3 Standalone Operation The frequency measurement mode can also be configured for a volumetric flow measurement type in which case the data ranges screen will have different configuration options as shown below. 1 6 2 5 3 4 Figure 3-17 Data Range - Volumetric Flow 1. Engineering Units Allows selection of various flow measurement units. 2. K Factor Enter the K factor provided on by the flow meter manufacturer. 3. Display Range This is the linear mapping of the input range in terms of engineering units. This determines what will be shown in the data display area for a given input value. 4. Zero Adjust This allows for a single offset value to be entered which will be applied to all readings in terms of the selected engineering units. 5. Graph Range This is a subset of the display range. This determines what portion of the full display range will be displayed initially in the waveform views. This range can also be adjusted from the waveform view. 6. Decimal Places Select the number of decimal places for display here. Example: F requency=250 Hz. Flow Rate Engineering Unit=GPM K Factor=135.6 Pulse/Gallon Flow Rate=(Frequency / K) *60=110.6 GPM 3-15 Standalone Operation 3 Totalizer For totalizer type digital inputs the device will keep a running total of the volumetric flow monitored by the digitals input until the reset count is reached. The reset count is in terms of the engineering units assigned on the Data Ranges screen. 1 2 3 Figure 3-18 Input Type Digital Totalizer 1. Channel Type button The channel type selects between physical and math channel input types. Frequency inputs are physical input channels. 2. Input Type Settings For digital inputs there are 3 different sensor types to choose from. The totalizer type requires a reset count to be entered as well. The reset count is the volumetric flow total at which you wish to have the totalizer reset back to zero. 3. Channel Map The channel map provides a quick view of which channels have already been configured (blue) and the currently selected channel (orange). 3-16 3 Standalone Operation Totalizer inputs type must be configured in terms of volumetric flow. The Data Ranges screen provides configuration options as shown below. 1 6 2 5 3 4 Figure 3-19 Data Ranges - Digital Totalizer 1. Engineering Units Allows selection of various flow measurement units. 2. K Factor Enter the K factor provided on by the flow meter manufacturer. 3. Display Range This is the linear mapping of the input range in terms of engineering units. This determines what will be shown in the data display area for a given input value. 4. Zero Adjust This allows for a single offset value to be entered which will be applied to all readings in terms of the selected engineering units. 5. Graph Range This is a subset of the display range. This determines what portion of the full display range will be displayed initially in the waveform views. This range can also be adjusted from the waveform view. 6. Decimal Places Select the number of decimal places for display here. 3-17 Standalone Operation 3 Resettable Counter For resettable counter digital inputs the device will count the number of pulses received on the digital input until the reset time is reached. 1 2 3 Figure 3-20 Input Type Digital Resettable Counter 1. Channel Type Button The channel type selects between physical and math channel input types. Frequency inputs are physical input channels. 2. I nput Type Settings For digital inputs there are 3 different sensor types to choose from. The resettable counter type requires a reset time to be entered as well. The reset time is the period after which you wish to have the counter reset back to zero. 3. C hannel Map The channel map provides a quick view of which channels have already been configured (blue) and the currently selected channel (orange). For resettable counter digital inputs, the only additional settings required on the Data Ranges screen are the graph and display ranges. 1 2 Figure 3-21 Data Ranges - Resettable Counter 1. Graph Range The graph range is the y-axis range that will be shown on the waveform view. It defaults to the same value as the display range, but must be a subset of the display range. This can be adjusted from the waveform display as well. 2. Display Range The display range is the full range value that the device will display. This is a user editable setting. 3-18 3 Standalone Operation Input Setup – Virtual Math Channel Virtual math channels allow you to perform math functions on the data from two physical channels and store the calculated result as a virtual channel. Up to 16 virtual channels can be configured. 1 2 3 4 5 Figure 3-22 Input Type - Virtual Math 1. Channel Type Buttons Allows selection of either a real physical input channel or a virtual Math channel. 2. Math Channel Settings Selects the channel number, color and name to assign to the new math channel. 3. Channel Operations Selects the two physical channels and math operation to perform. 4. Scaling Factors Multiplies the channel value by the selected scale factor before performing the math operation to the two channels. The scaling factor can be either whole or decimal numbers. 5. Channel Map The channel map provides a visual indication of the previously configured channels (shown in blue) and the currently selected channel (shown in orange). 3-19 3 Standalone Operation After configuring the channels and math operations for the virtual math channel on the Input Type screen, you can set up the engineering units and ranges for the calculated results on the Data Ranges screen. 6 1 5 2 4 3 Figure 3-23 Data Ranges - Virtual Math 1.Engineering Units These drop downs allow selection of various engineering units for display. 2.Display Range The display range boxes show the full display range available on the data logger. The graph range can be any subset of this range. This range should be set to cover all possible values of the calculated results based on the scaling and math operations. 3.Zero Adjust The zero adjust provides a user configurable offset adjustment, in engineering units, which will be applied to measurements across the full range of input. 4.Moving Average Filter This setting provides the option to average an individual channels input samples. 5.Graph Range The graph range is the y-axis range that will be shown on the waveform view of the data logger. This can be any subset of the display range and is defined in the assigned engineering units. It can also be adjusted on the waveform view. 6. D ecimal Places Selects the number of decimal place to display. 3-20 3 Standalone Operation 3.3.2 Channel List The Channel List screen can be used to edit channels after their initial configuration as long as the data logger is in the free running mode of operation. To edit channels hit the Channel List button on the Home Screen toolbar to go to the Channel List screen. Then select the channel you would like to edit and hit the Edit Channel button. 1 2 3 4 5 6 7 8 Figure 3-24 Channel List screen 1. Table Header – Indicates the channel settings shown in each column of the channel list. 2. Channel List – A table showing all of the currently configured channels and their values for each of the settings in the table header. 3. Back – The back button returns to the Home Screen. 4. Channel Groups – This button navigates to the Select Channels screen where channel groups can be configured. 5. Edit – The edit button is used to edit a channels settings. Only one channel can be edited at a time. 6. Copy – The copy button copies the currently select channels settings to the next available channel and navigates to the Input Type screen where the new channel can be further edited or saved. Only one channel can be copied at a time. 7. Delete – The delete button can be used to delete one or more channels using the checkboxes. 8. Help - Provides context-sensitive help based on the current screen. 3-21 Standalone Operation 3 3.3.3 Trigger Settings The Trigger settings screen can be accessed through settings button of the home screen toolbar. Trigger events can be used to start and stop a data logging session. It is even possible to trigger multiple sessions using repeat trigger events. Start and stop trigger events can be used independently or together, allowing many different ways to control data logging sessions. There are five types of trigger events available. When no start trigger event is configured, data logging will commence immediately upon pressing the Log Data button. Otherwise the data logger will enter into the Armed mode and it will await a start trigger event before commencing data logging. When no stop trigger event is configured, data logging will continue until the user presses the Stop Log button or the selected memory device is full. 1 2 3 Figure 3-25 - Trigger Settings 1. Start Trigger Event The Start Trigger Event drop down menu is used to select the type of trigger to use for starting a logging session. 2. Repeat Trigger Event The Repeat Trigger Events checkbox determines whether or not the device will trigger (log) more than once. This also depends on the type of trigger events configured. 3. Stop Trigger Event This drop down menu is used to select the type of stop trigger event to use to end a data logging session. 3-22 3 Standalone Operation Timer Trigger Events When used as a start trigger event the logging session will commence after the data logger has been armed and the configured time period has elapsed. When used as a stop trigger the timer sets the duration of the logging session. 2 1 3 Figure 3-26 Timer Trigger Event 1. Start Timer The Start Timer sets the delay before logging commences in HH:MM:SS format. 2. Logging Duration The logging during determines how long the logging session continues in HH:MM:SS. 3. Repeat Trigger Events If repeat trigger events are enabled, the device will automatically re-arm itself after each logging session ends. Date and Time Trigger Events This trigger event option allows a specific date and time to be selected to start and/or stop a logging session. Repeat triggers are not available for this event. 1 2 Figure 3-27 Date and Time Trigger Event 1. Trigger Time Sets the time that the start or stop trigger occurs. 2. Trigger Date Sets the date for the start or stop trigger. 3-23 Standalone Operation 3 Weekday and Time Trigger Events Using this option a time and day of the week can be configured as a start or stop trigger. 1 2 3 Figure 3-28 Weekday and Time Trigger Event 1. Trigger Time Sets the time that the trigger event occurs. 2. Trigger Day Sets the day of the week that the trigger even will occur on. 3. Repeat Trigger Events If repeat trigger events are enabled the device will automatically re-arm itself after the logging session ends. A stop trigger event must be configured for this to occur. Alarm Output Trigger Events The Alarm output option allows any of the alarms currently configured and enabled to activate an alarm output to also trigger a logging session. 1 2 Figure 3-29 Alarm Trigger Event 1. Alarm Output Selects the alarm output to be used as a trigger event. When an alarm mapped to the corresponding output is generated, the trigger condition is met. 2. Repeat Trigger Events If repeat trigger events are enabled the device will automatically re-arm itself after the logging session ends. A stop trigger event must be configured for this to occur. 3-24 3 Standalone Operation External Trigger Events This option allows the external trigger input to be used as a start and stop trigger. The external trigger input can accept signals from 0 to 24 Vdc. The input threshold voltage is ≥ 2.5 Vdc for a logic high level and ≤ 1.5 Vdc for a logic low level. There are four detection options which determine when an external trigger event is generated. 1 2 Figure 3-30 External Trigger Event 1. External Trigger Detection Options These options determine when a logging session is triggered by the external trigger input. For the high and low options, a trigger event is generated immediately if the trigger condition is met when the Log Data button is pressed. For the rising and falling edge options, the corresponding edge transition must be seen on the external trigger input before a logging session will begin. 2. Repeat Trigger Events If repeat trigger events are enabled the device will automatically re-arm itself after the logging session ends. A stop trigger event must be configured for this to occur. 3-25 3 Standalone Operation 3.3.5 Data Session Settings The Data Session Settings screen is accessible from the settings button on the home screen toolbar. This screen is where you configure all the settings that control how data is logged. 1 5 2 6 3 7 4 Figure 3-31 Data Session Screen 1. Sample Rate The sample rate setting determines how often the data logger takes a reading on each of its inputs and updates its display. The sample rates available will vary depending on the number and type of sensors configured. 2. Logging Rate The logging rate determines how often sampled data is saved to the log file. Allowable selections are always less than or equal to the sampling rate. 3. Logging Mode The logging mode determines what data is saved to the log file at each logging interval. If set to Interval, the most recent data sample is saved in the log file. If set to Average, all of the data samples taken over the logging interval are averaged and the average value is saved to the log file. 4. External 24V Excitation This selection turns on the built in 24 Vdc excitation. This excitation voltage is available at the alarm/excitation terminal block on pins 7 & 8. This voltage can power one external transmitter. 5. F ile Type Data session logs can be saved as either CSV or text files. 6. F ile Location The file location setting determines which memory location log files are saved to. In addition, any screenshots will be saved in the same location. 7. F ile Naming This setting determines if the system generates log file names automatically or the user enters a name. Auto generated file names have the OM-DAQXL_ (MM_DD_YYYY HH_MM_SS_AM/PM). The manual file naming option allows the user to enter a prefix for all log files which will be followed by the same date and time stamp as the automatic setting. 3-26 3 Standalone Operation 3.3.6 Alarms Settings Alarms can be generated when the measured/calculated value meets an alarm condition. If an alarm is mapped to one of the four physical alarm outputs, the alarm status indicator will display the alarm condition. When in alarm condition the status indicator for the corresponding alarm output changes color as shown in the following table. In addition, an alarm signal (open collector) is delivered to the alarm output terminal block and the digital I/O connector on the left side of the OM-DAQXL. Alarm Settings are accessible through the settings button of the home screen toolbar. There are two screens associated with the alarms settings, the main alarm screen and the add/edit alarm screen. Main Alarm Screen The main alarm screen shows all of the currently configured alarms in a table format. From this screen you can perform various task including adding new alarms, editing existing alarms, enabling or disabling alarms and deleting alarms. Alarm Type Alarm Status Indicator-Color Low Blue Window In Blue High Window Out Open Sensor 2 alarms mapped to one alarm output Latched Alarm Red Red Purple Orange Flashing Table 3-1 Alarm Type/Status Indicator Color. Alarm Status Alarm Table Alarm Toolbar Alarm Status Figure 3-32 Main Alarm Screen Shows the current status of the alarm outputs. A single tap on this icon will invoke the Show Alarm fly-out menu. Alarm Table The alarm table provides a quick view of all of the currently configured alarms and their settings. Alarms can be selected for editing or deletion using the checkboxes in the leftmost column of the table. 3-27 Standalone Operation 3 Alarm Toolbar The alarm toolbar features buttons for performing all of the actions related to alarm settings. 1 2 3 4 5 6 7 Figure 3-33 Alarm Toolbar 1. Back Returns to the home screen. 2. Add Alarm The Add Alarm button takes you to the screen where new alarms are set up. Several settings can be configured to determine when alarms are generated and what actions the data logger performs in response to those alarms. 3. Edit Alarm Returns to the alarm setup screen allowing change to be made to a previously configured alarm. This options is only available when a single alarm is selected from the table. 4. Enable Enables any alarms currently selected in the alarm table. Alarms must be enabled before their settings become active and will generate an alarm. 5. Disable Disables any alarms currently selected in the alarm table. If an alarm is disabled, no alarm will be generated even if its alarm conditions are met. 6. Delete Deletes any alarms currently selected in the alarm table. A confirmation will be required before alarms are deleted. 7. Help Provides context-sensitive help based on the current screen. 3-28 3 Standalone Operation Add/Edit Alarm Screen The add/edit alarm screen is where alarm settings are configured. Here you can select the type of alarm you wish to create and also the actions the data logger will take when an alarm occurs. 2 5 7 1 3 4 6 8 Figure 3-34 Add/Edit Alarm Screen 1. Channel Name - This drop down list is used to select the channel which you would like to configure and alarm. Up to two alarms can be configured for each channel. 2. Alarm Type - The alarm type drop down list is used to select from High, Low, Window In and Window Out, and Open Sensor type alarms. For window alarms there will be both a high and low threshold value configured. Window In alarms will be generated when the process value is within the window set by the two thresholds and Window Out alarms will be generated when the process value is outside that window. 3. Threshold Value - The threshold value sets the limit at which, when exceeded, an alarm will be generated. 4. Hysteresis - The hysteresis setting determines the difference between the alarm threshold value and the value at which the alarm will be deactivated. It is always in the same engineering units as the channel for which the alarm is being configured. 5. Alarm Output - The alarm output setting maps the alarm to one of the four physical alarm outputs. This allows an alarm control an external event such as sounding a buzzer, turning on a warning light or relay. 6. Latching - The latching setting determines the action taken once an alarm condition has cleared. Normally an alarm will deactivate when the alarm condition has cleared based on the hysteresis value set. When latching is selected and alarm will not deactivate until the user manually disables by selecting it in the alarm table and pressing the disable button on the alarm toolbar. 7. Screenshot - The screenshot setting will take a screenshot of the current display when an alarm condition is met and saves it to the same memory location selected for the logging session files. 8. Buzzer - The buzzer setting allows the internal buzzer to be used when an alarm condition is met. There are two distinct tones used to distinguish the two alarms for each channel. 3-29 Standalone Operation 3 3.3.7 Device Settings The device settings are five different screens which allow you to configure the way your device looks and works in addition to setting the date & time, managing users, running diagnostics and performing firmware updates. The device settings screens are accessible through the settings button of the home screen toolbar. Figure 3-35 Device Settings After selecting device settings from the settings fly-out menu, you will navigate to the settings menus. By default the General settings screen is shown and additional device settings screens are available through the toolbar buttons. General/Data and Time The General settings screen is where you set the system date & time. Use the drop down menus to select the appropriate values for each field. You can also select a clock format. 3 1 2 Figure 3-36 General Settings Screen 1. Time Use these three drop down menus to set the system time for the data logger. 2. Date Use these three drop down menus to set the system date for the data logger. 3. Clock Format Use the clock format buttons to select 12 or 24 hour time format. NOTE: You must press the save button to save the new data and time. 3-30 3 Standalone Operation Display Options The Display Options screen is where you can make changes to the settings related to the 7” touch screen in addition to settings for the color scheme and other user interface related settings. 1 4 2 5 3 6 Figure 3-37 Display Options Screen 1. Screen Timeout When operating on battery power this setting determines how long the display will stay on after the last user interaction. After this time period the display will shut off to conserve battery life. The current user will also be logged out. Within the first 5 minutes after the display is turned off, the user can turn the display on and get back to Login screen by touching the screen or pressing the Home button. After the 5 minute period without user interaction the data logger will automatically power off. The device can be restarted by cycling the power switch. When an AC adapter is connected the screen will remain on, but the current user will still be logged out and the login screen will be displayed. Any data logging sessions under way or awaiting a trigger will proceed as normal. 2. Background and Grid Color These options set the background color for the menu screens and the grid color for the Waveform views. 3. Brightness This slider sets the display brightness. Using a reduce brightness can increase battery life. 4. Slide Show Timing This setting controls the amount of time each channel group is displayed when the slide show options is enabled in the views fly-out menu. 5. Key Sound This setting allows you to select a number of different feedback sounds to provide additional indication that a touch input on the display was detected. 3-31 6. Calibrate Touch Screen Occasionally the touch screen may need to be calibrated to ensure more accurate detection of touch inputs. This button allows you to run a calibration routine for the touch screen. Standalone Operation 3 Communication Settings (if applicable) If you purchased a model 3 or 4 data logger, your tool bar will have a communications settings button. The Comm settings screen is where you can configure the Ethernet or optional WiFi communication settings. 1 2 4 3 5 6 Figure 3-38 Comm Settings – Ethernet 1. Connection Selection This button is used to select the network adapter. The settings for the currently selected network adapter will be shown below. 2. DHCP This checkbox is used to enable or disable DHCP for the currently selected network adapter. DHCP Dynamic Host Configuration Protocol (DHCP) is a client/server protocol that automatically provides an Internet Protocol (IP) host with its IP address and other related configuration information such as the subnet mask and default gateway. 3. IP Address If DHCP is checked the DHCP assigned IP address is shown for the selected adapter. If DHCP is not checked, a static IP address can be entered using the keypad. 4. Subnet Mask If DHCP is checked the DHCP assigned subnet mask is shown for the selected adapter. If DHCP is not checked, a subnet mask can be entered using the keypad. 5. Gateway 6. If DHCP is checked the DHCP assigned gateway IP is shown for the selected adapter. If DHCP is not checked, a gateway IP can be entered using the keypad. 7. 6. Update After configuring the settings, hit the update button to apply the settings to the selected network adapter. 3-32 3 Standalone Operation 7 8 9 Figure 3-39 Comm Settings - WiFi 7. SSID – Select Network This dropdown selection will show all of the WiFi networks within range. 8. Security Key Enter the passphrase or security key for the selected network. If it is an open network, leave this field blank. 9. Connect Hit the connect button to connect to the selected network. 3-33 Standalone Operation 3 Diagnostics The diagnostics screen is where you can run the built in diagnostics routine and view reports from previous diagnostic runs. The diagnostic routine will run several tests on the various sub-systems of the data logger and provide a status indication for each test. At the end, you can perform the Power shut down test (Optional) which will require recycling power to the unit. 1 3 4 2 5 Figure 3-40 Device Settings Diagnostics Screen 1. Run Diagnostics This button runs the system diagnostics tests. 2. Diagnostic Report Hitting this button will display a report of the most recent diagnostics results. 3. Overall Progress Bar This progress bar shows the progress of the overall system diagnostics currently being run. 4. C ancel Button Hitting this button will cancel the current system diagnostics run. 5. T est Information This table shows the progress of each test as it is being run as well as the status and result of the test. 3-34 3 Standalone Operation User Management All settings related to user accounts are accessible from the user management screen. The user management setting screens are only available for Admin users. 1 2 4 3 5 6 7 8 Figure 3-41 User Management Screen 1. Table Header Indicates the type of information in each column of the user table. 2. User Table Provides a list of all the current user accounts set up on the data logger. 3. Back This button returns to the General settings screen of the device settings. 4. Add User This button navigates to the Add User screen to allow a new user account to be created. 5. Change Password This button navigates to the Change Password screen. Here the user can enter a new password. 6. Delete Files This button will delete all of the configuration file for the currently selected users. 7. Delete User This button will permanently delete the currently selected user accounts. Only Admin users can delete or add users. 3-35 8. Help Provide context sensitive help information. Standalone Operation 3 Add User This screen is where new user accounts can be added to the data logger. 1 2 3 4 6 5 7 Figure 3-42 Add User 1. User Role Here you can assign new user a role of either Admin or Normal. Admin users have the ability to create or delete new users or their files. Normal users only have access to their own files. 2. Username The name assigned to the new user account. Username’s must be between 4 and 10 characters in length. 3. Password The password for the new user account. Passwords must be between 4 and 10 characters in length. 4. Confirm Password Re-enter the password for the new user account. It must match the password entered in the previous field. 5. Save Saves the new user account. 6. Cancel Cancels new user account creation and returns to the User Management screen. 7. Help Provides context sensitive help information about the current screen. 3-36 3 Standalone Operation Change Password This screen is where you can change the password for any user. Normal users can change their password from using the change password option in the status bar fly-out menu. 1 2 4 3 5 Figure 3-43 Change Password Screen 1. New Password Enter the new password for the user account. Password must be between 4 to 10 characters in length. 2. Confirm Password Enter the same password as the previous field. 3. Submit Submit and save the new password. 4. Cancel Return to the User Management screen without saving the new password. 5. Help Provides context sensitive help for the current screen. Note: o mega Admin user can not be deleted. Only Admin users can add or delete users. Guest users do not require any Password. 3-37 3 Standalone Operation About Your Logger/Firmware The About screen provides model number information, current firmware version, OMEGA’s contact information and a Firmware Upgrade option. Occasionally OMEGA releases updates to the data logger firmware. These updates can be downloaded from the OMEGA FTP site, which can be accessed through the main OMEGA website by visiting www.omega.com/ftp and navigating to the OM-DAQXL folder under Data Acquisition folder. 1 3 2 Figure 3-44 About Screen 1. Model Number Shows the model number of your data logger. 2. Firmware Version This shows the firmware version currently installed on your device. 3. Contact Information Omega Engineering contact information. 4. Firmware Update The firmware update button is used to initiate an update. Make sure you have a valid firmware update file on your SD or USB memory before proceeding. 3-38 3 Standalone Operation Firmware Upgrade When performing a firmware upgrade, be sure that you have at least 50% battery life remaining. To install a firmware upgrade, save the .zip file to either a USB Flash drive or an SD card. Be sure to save the .zip file in the root directory of the memory device and do not unzip the file. On the about screen press the Firmware Upgrade button to proceed to the Firmware Upgrade screen as shown in figure 3-43. On the firmware upgrade screen select the location (SD card or USB memory) of the firmware upgrade file by pressing the appropriate button. Then press the Upgrade button on the toolbar to begin the firmware upgrade process. The progress will be indicated on the progress bar. The device will reset itself to complete the firmware upgrade process. 1 2 3 Figure 3-45 Firmware Upgrade Screen 1. Memory Location Select the location of the firmware update file. 2. Update progress Bar Shows the progress of the firmware update. 3. Update Button Initiates the firmware update process. Once the device has rebooted you have logged in, you should see a message indicating that the upgrade was successful. You can verify that you have an update firmware version by returning to the About screen and checking the version number. Figure 3-46 Firmware Upgrade Success 3-39 Standalone Operation 3 3.4 Viewing Data To view data on the OM-DAQXL at least one input must be connected, configured and assigned to a channel group for display. There are two toolbar buttons which determine what data is shown in the data display area. Figure 3-47 Display Channel Fly-Out Menu The Display Channels button fly-out menu allows you to select which group of channels you would like to display and also provides quick access to the Select Channels screen where channel groups can be configured. The Views button fly-out menu allows you to select between four display modes to view data. It also has a selection to toggle the slide show feature on or off. Figure 3-48 Views Fly-Out Menu 3-40 3 Standalone Operation 3.4.1 Select Channels Before channel data can be viewed, it must first be assigned to a group. This is done through the Select Channels screen which can be accessed through the Display Channels button on the home toolbar or from the Channel List screen toolbar. The Select Channels screen will display all configured channels and indicate a check mark next to any channels assigned to the currently selected group. Channels can be assigned to multiple groups. 1 2 3 Figure 3-49 Select Channels Screen 4 5 1. Group Selection These buttons let you select one group at a time to assign channels to. 2. Channel Selection All currently configured channels are shown in this area. You can select four channels per group using the checkboxes. No two channels assigned to the same group can have the same color. 3-41 3. Apply This saves the current channels selections and returns to the previous screen. 4. Cancel Immediately cancel the operation and returns to the previous screen. 5. Help Provides context-sensitive help based on the current screen. 3 Standalone Operation 3.4.2 Waveform View The waveform view uses the full display width to plot a graph of the channel data. This maximizes the amount of data that can be viewed. 4 3 2 1 Figure 3-50 Waveform View 1. Time Stamp Indicator Shows the time stamp for each graph division. 2. Y-Axis Scale Shows the value at each division of the Y-Axis. With multiple channels visible, these values will be for the currently selected channel. 3. Channel Trace Shows the waveform for each input channel in the selected color. 4. Scale Selector Shows the current time per division for the X-Axis. A single tap on this arrow icon will invoke the scale selection fly-out. 1 2 3 Figure 3-51 Graph Scale Selector 1. Time Scale Shows the available time per division settings based on the currently selected sample interval. 2. Channel Selector Allows the user to select which channel to adjust the Y-axis scale for. 3. Y-Axis Graph Range Entry Allow entry of a custom graph range for each channel. 3-42 3 Standalone Operation 3.4.3 Waveform and Table view The waveform & table view has the same features as the waveform view with the addition of a table showing the current values for all configured channels can be displayed on the right third of the display area. The graph scales can be adjusted using the scale selector in the same way as in the waveform view. 1 2 Figure 3-52 Waveform and Table View 1. Channel Number and Name. 2. Channel Value Shows the current value for the measured or calculated data for each channel along with the selected engineering units. 3-43 3 Standalone Operation 3.4.4 Table Only view The table only view provides a tabular view of statistical values for all currently configured channels. 1 2 3 4 5 6 7 8 Figure 3-53 Table Only View 1. Channels This column shows the channel number and name assigned to each channel. 2. Value This column shows the current calculated value for each input in the engineering units configured. 3. Peak to Peak This column gives an indication of the difference between the maximum and minimum values of the data for each channel. 4. Average This column shows the average value of the data for each channel. 5. Minimum This column indicate the minimum value of the data for each channel. 6. Maximum This column indicates the maximum value of the data for each channel. 7. Root Mean Square This column indicates the RMS value of the data for each channel. 8. Table Shows the channel data for all currently configured channels. 3-44 3 Standalone Operation 3.4.5 Digital View The digital view shows the user a digital indication of up to four channels (1 group) simultaneously. It has two display modes, four channel or single channel. 1 3 2 Figure 3-54 Four Channel Digital View 1. Channel Display A single tap on any of the four digital displays will switch the display mode to show a single channel display for that channel. 2. Channel Number and Channel Name Shows the channel number and user assigned name for each channel. 3. Digital Display Shows the current value for each channel included user selected engineering units. Figure 3-55 Single Channel Digital View 3-45 Standalone Operation 3 3.4.6 Screenshot At any point during operation a screenshot of the current home screen can be captured simply by pressing the Screenshot button on the toolbar. This is a convenient way to capture information especially in the free-running mode when data is not being recorded to a file. Each time the button is pressed a message will appear for approximately 3 seconds indicating the path and name of the saved screenshot image. 3.4.7 Annotate The annotate button allows the user to freeze the current display and make annotations using the stylus. Then a screenshot including the annotation can be saved in the directory configured in the data session settings. 5 1 Figure 3-56 Annotate 2 3 4 1. Save Saves the screenshot with annotations to the user folder in the currently configured memory location. 2. Erase Erases the last annotation stroke made. Each additional press erases the previous stroke. 3. Cancel Clears all annotations and unfreezes the display. 4. Help Provides context-sensitive help based on the current screen. 5. Annotation Shows an example of a typical user annotation. 3-46 3 Standalone Operation 3.5 Operating Modes The OM-DAQXL has four modes of operation. They are described in the following section. 3.5.1 Free-Running This mode is used mainly for set up. The device measures and displays all configured analog and digital inputs. No data is logged and all settings can be edited. While in the free-running mode the data logging mode area of the status bar is blank. 3.5.2 Armed Mode The OM-DAQXL will enter the Armed mode when a start trigger is configured and the Log Data button is pressed. The data logging mode indicator in the status bar will show an orange dot and the toolbar icon will also be an orange color with the word Armed shown. When the configured trigger condition is met, the device will automatically enter the logging mode of operation. Pressing the Log Data button while in the armed mode will cause a fly-out menu to appear. You can either skip trigger detection and enter the logging mode automatically by pressing the red Log Data button or revert to the free running mode by pressing the white Free running button. 3.5.3 Logging Mode In the logging the OM-DAQXL will save data from all configured channels to the memory location specified in the Data Session Settings. This location must be specified prior to entering the logging mode. A maximum of 1 million data points will be logged to a file after which a new log file will be started. When in the logging mode new channels cannot be configured and trigger and data session settings cannot be changed. The OM-DAQXL features multiple options for logging data. It comes with 1GB of internal flash memory standard in addition to both an SD card slot and a USB host port allowing up to 64GB memory capacities to be used for storing user data. 3.5.4 Data Review Mode The data review mode allows you to review previously logged data or view previously captured screenshots. The Stored Files button on the toolbar gives access to all previously stored data for the currently logged in user. Pressing the Stored Files button will bring you to the directories screen as shown below. 3-47 Standalone Operation 3 1 2 3 4 5 6 7 8 9 Figure 3-57 Stored File Directories 1. Memory Type Shows the currently selected memory type. This defaults to the internal memory. 2. Screen Capture Directory Directory where all screen captures for the currently logged in user are stored. 3. Log Files Directory Directory where all data log files for the currently logged in user are stored. 4. Back Returns to the home screen. 5. Storage Invokes a fly-out menu that allows you to select which memory type to browse. If you select a memory type not present a pop-up message will indicate the memory type is not found. 6. Open Opens the selected directory. 7. Copy to SD Copies the selected file or directories to the SD card if present. 8. Copy to USB Copies the selected file or directories to the USB memory if present. 9. Help Provides context-sensitive help based on the current screen. 3-48 3 Standalone Operation To browse files in a particular directory you can select the directory using the checkbox and then press the Open button on the toolbar. The selected directory will be opened and all the files in the directory will be presented in a scrollable list as shown below. 1 2 3 4 5 6 7 8 9 10 Figure 3-58 Stored Files List 1. Memory Type Shows the currently selected memory type. Must be selected prior to opening the directory. 2. File List A scrollable list view of all data files or screen captures in the current directory. 3. Back Returns to the stored files directory list. 4. Storage Not selectable in the stored files list view. 5. Review Opens the selected file in the review screen, Depending on the size of the file it may take several seconds to load. Only one file can be selected at a time for review. 6. Rename Opens screen where you can rename a file. 7. Delete Deletes the selected files. You will be asked to confirm this action before any files are deleted. 8. Copy to SD Copies the selected file or files to the SD card if present. 9. Copy to USB Copies the selected file or files to the USB memory if present. 3-49 10. Help Provides context-sensitive help based on the current screen. 3 Standalone Operation After selecting a particular file for review and pressing the Review button, the data logger will load the file and show the data review screen. 2 1 4 5 6 7 8 9 3 10 11 12 13 14 Figure 3-59 Data Review Screen 1. Waveform Graph Shows a graphical plot of data for the file currently under review. Information displayed includes the y-axis scale for the channel currently highlighted, timestamp indicator, engineering unit value for the currently selected channel at each cursor location and time value at for each cursor. 2. Hide Table Hides or shows the table showing the channel data values at each cursor location. 3. Cursor Table Table showing the channel data values at each cursor location. Tapping on a channel name will show the corresponding channels data values at each cursor location on the top of the graph. 4. Page indicator Shows the current page displayed and the total number of pages at the current zoom level. 5. Back Returns to the stored files list for the currently selected memory location. 6. Waveform Shows the waveform view of the file under review. 7. Display Channels Navigates to the channel list for the file currently under review. Here you can select the channels you wish to have displayed on the waveform view. 8. Show slider Shows a slider tool that can be used to quickly move to different pages of the file under review. 9. Cursor Controls Moves the selected cursor forward or backward in time on the waveform display. 10. Cursor selection Selects the cursor you wish to move using the cursor controls. A single cursor or both cursors can be selected. 3-50 3 Standalone Operation 11. Previous and Next Advances to the next page or returns to the previous page of the waveform data. 12. Zoom In and Zoom Out Zooms in or out on the waveform graph. Zooming is controlled using the cursors. Position the cursors around the area of interest and use the Zoom In button to magnify the area. The Zoom Out button will return to the fully zoomed out view. 13. Annotate Allows annotation of the current waveform graph. Annotations can be saved as screenshots in the same directory as screenshots taken in the free running or logging modes. 14. Help Provides context-sensitive help based on the current screen. At any time while reviewing a data file, you can select which channels you would like to view on the waveform graph. Pressing the Display Channels button on the data review screen toolbar will take you to the review mode channel list screen where you can select the channels for display. 1 2 3 4 5 6 Figure 3-60 Review Mode Channel List 1. Channel List List of all channels with data in the file under review. Select that channels you wish to view on the waveform graph. 2. Back Returns to the stored files list. 3. Waveform After selecting the channels you would like to view, pressing the Waveform button returns to the waveform graph. 4. Display Channels Takes you to the review mode channel list to select channels to display. 3-51 5. Up/Down When the channel list has more channels than can fit on the display, these buttons allow you to scroll through the list. 6. Help Provides context-sensitive help based on the current screen. 4 NOTES 4-1 5 Troubleshooting 5 Troubleshooting 5.1 Hardware Issues Symptom Possible Solution Erratic input signal. heck signal lines and terminal connections. Connections C must be free of corrosion. Signal lines should be undamaged and free of sharp bends and twists. Signal paths should avoid potential sources of noise (high voltage and electromagnetic interference). You can also connect the Shield ground to Earth ground to minimize sensor noise pickup. The device does not power up when the power switch is on. ake sure the battery or AC adapter is properly M connected. See section 2.11. 5.2 Error Messages Symptom Firmware update fails. 5-1 Possible Solution erify that the firmware update file is a V later release than the currently installed firmware. Service and Calibration 6 6 Service and Calibration Your OM-DAQXL components have been built and factory calibrated to meet or exceed the specifications listed here in this manual. If your OM-DAQXL system requires service or calibration, please call our Customer Service Department at 1-800-622-2378 or 203-359-1660. They will assist you in arranging the return and service of your device. We can also be reached at www.omega.com, e-mail: [email protected] 6-1 7 Specifications 7 Specifications 7.1 General Display: 7.0" TFT color LCD (WVGA: 800 x 480 pixels) with chemically hardened touch panel. Internal Memory: 1 GB FLASH Memory SD Memory Card: 32 GB USB Flash Drive: 1GB Ethernet**: 10/100 Base-T, TCP/IP USB Wi-Fi Dongle**: 802.11 b/g/n, USB2.0 interface, Up to 150Mbps, WEP and WPA/WPA2 encryption schemes Operating Environment: 0 to 50°C (32 to 122°F), 0 to 95% RH non-condensing Storage Conditions: -10 to 60°C (32 to 140°F) Computer Interface: USB Dimensions With Rubber Boot: (9.00 X 6.5 X 3.5") Without Rubber Boot: (8.75 X 5.75 X 2.42') Weight: 3.2 lbs (1.45 kg)* Power Supply: AC Adapter Input:100 to 240 Vac, 50 to 60 Hz, 1.5 A max AC Adapter Output: 12 Vdc, 5A max Battery: Lithium Ion Rechargeable (7.2 V, 4800 mAh) Battery Life: Approximately 4-8 hours depending on display settings before recharge Screen Time Out: 30 sec, 1 min, 2 min, 5 min, 10 min, Never Slide Show Timing: 5 sec, 10 sec, 15 sec, 20 sec, 30 sec Auto Power Shut Down: 5 minutes after screen time out Line Graph Time Scale: From 400 msec/div up to 1 hr/div External Excitation Output: 24 Vdc, regulated (±2%) isolated. Maximum current output 50 mA. External I/O: 4 digital inputs, 4 digital outputs, 4 alarm outputs, 1 external trigger input. *Includes battery and rubber boot **Only available for -EW models 7-1 U W W Specifications 7 7.2 Inputs Number of Analog Inputs: 8 or 16 Sampling Rate Maximum Sampling Rate per Number of Channels (Analog and Digital): 1 Channel: 125 s/sec 2 Channels: 50 s/sec 4 Channels: 25 s/sec 8 Channels: 10 s/sec 16 Channels: 5 s/sec Logging Rate Maximum logging Rate per Number of Channels (Analog and Digital): 1 Channel: 125 s/sec 2 Channels: 50 s/sec 4 Channels: 25 s/sec 8 Channels: 10 s/sec 16 Channels: 5 s/sec Thermocouple Type J T WU U -200 to 1370°C -328 to 2300°F W -200 to 1000°C -328 to 1832°F S UU UU B W 32 to 3200°F 0 to 1760°C C 32 to 3200°F 0 to 1760°C 32 to 4200°F Type Range (°C) Pt 100, Pt 500, Pt 1000 (0.00385 curve) -200 to 850°C Pt 100, Pt 500, Pt 1000 (0.00392 curve) UU UU Thermistor Type Range -30 to 150°C 10,000 Ω Current Range 20mA -200 to 660°C W W 2252 Ω Accuracy ±1°C -5 to 150°C Measurement Range -20 to 20mA Frequency Measurement Range 0 to 250 KHz ±(0.15% of reading + 2.0°C) 932 to 3308°F 500 to 1820°C 0 to 2315°C RTD ±(0.15% of reading + 1.7°C) -148 to 2372°F -100 to 1300°C W ±(0.15% of reading +1.1°C) -328 to 752°F -200 to 400°C R Accuracy -328 to 2012°F -200 to 1100°C K UE U W N Range (°F) Range (°C) ±1°C ±0.1% of FS Accuracy ±2 Hz Range (°F) -328 to 1562°F -328 to 1220°F Voltage Accuracy ±(0.25% of reading +1°C) ±(0.25% of reading +1°C) Range Measurement Range 100mV -100 to 100mV 5V -5.00 to 5.00V 50mV 1V -50 to 50mV -1.00 to 1.00V 10V -10.00 to 10.00V 50V -50.00 to 50.00V 20V Accuracy ±0.1% of FS -20.00 to 20.00V 7-2 7 Specifications Measurement Accuracy *At room temperature after 30 minute warm up period. Input Type: Thermocouple, RTD, Thermistor, Voltage, Current, Strain Gage Strain Gage Input: Only Channels 1, 2, 3, 4, 9, 10, 11, 12 are available. Frequency Update Rate: 250 msec Digital Input and Functions: Frequency, volumetric flow rate, totalization, resettable counter Virtual Math Channels 1 to 16: Math equation of any two physical channels Filter: •Per channel selectable moving average filter: None, 2, 5, 10, 20 or 50 samples Resolution: One to four decimal places depending on the Input type Statistics: Peak to peak, average, minimum, maximum, RMS Input Sampling/Logging Rate: 125 s/sec (1 Channel), 50 s/sec (2 Channels), 25 s/sec (4 Channels), 10 s/sec (8 Channels), 5 s/sec, 1 s/sec, 12 s/min, 6 s/min, 2 s/min, 1 s/min, 12 s/hr, 6 s/hr, 2 s/hr, 1 s/hr (For All Channels) Logging Mode: Interval, average Trigger Conditions (Start & Stop): Timer, date and time, weekday and time, alarm output, external trigger Logging Condition: On command or trigger condition 7.3 Functions Display Views: Waveform, waveform and table, table only, digital, slide show Display Channels: 4 channels per group – 4 groups Stored Files: Screen capture and log (internal, SD card, USB drive) Data Review: Up to any 4 channels – scroll or page right and left, zoom in, zoom out, annotate Device Settings: • General – Set current Time & Date • Display Option – Screen Timeout, Background & Grid color, Brightness, Slide show timing, Key sound, Calibrate Touch screen • Diagnostics – Analog, Digital, Power shut down test & generate report • User Management – Admin, Normal User (Set User ID & Password) • About – Firmware Upgrade Help: • Help screen for every menu screen 7-3 Specifications 7 Virtual Math Channels: Up to 16 virtual channels can be created. Statistics: Peak to Peak, Average, Minimum, Maximum, RMS Triggers Trigger Types: • Start, Stop, Repeat Trigger Conditions: • Timer, Date & Time, Weekday & Time, Alarm Output, External Trigger Logging Logging Modes: • Interval, Average Logging Conditions: • On demand or trigger condition Digital input functions: Frequency, Volumetric flow, Totalization, Resettable counter 7.4 Communication USB: High speed USB 2.0 host for external Flash drive; USB device for external PC communications. Protocol: Modbus TCP/IP 7.5 External I/O: Alarm Outputs: 4 open collector alarm outputs rated for 0.5A @ 30 Vdc with audible alarm buzzer Digital Outputs: 4 open collector digital outputs rated to 30 mA @ 5 Vdc logically tied to alarm outputs Digital Inputs: 4 Schmitt trigger based inputs • 0 to 24 Vdc single ended, grounded input range • Logic high threshold 2.5 V; Logic low threshold 1.5 V • Contact closure detection • Maximum input frequency: 250 kHz Power Input to Digital I/O Isolation: 1.5 kVrms Alarm Condition: High, Low, Window In, Window Out, Open Sensor On Alarm Event: Map to 4 Alarm outputs, Sound Buzzer, Take Screen shot Alarm Type: Latch, Non-Latch Alarm per Channel: Two 7-4 7 Specifications 7.6 Dimensions Dimensions: mm (inch) Note: Ethernet port is only present on -EW models. 61.4 (2.42) 146 (5.75) EVISIONS ECN DATE DR CHK ENG 222 (8.75) M4 INSERT SCREW 7-5 International Approvals 8 8 International Approvals CE Conformity: The OM-DAQXL has been designed to meet requirements as outlined in European Community EMC Directive EN61326. Five ferrite cores (PN: OM-DAQXL-RF) are included in the OM-DAQXL package. When using thermocouple temperature sensors with the OM-DAQXL it is recommended to pass the thermocouple through the supplied ferrite 2 turns before connecting it to the device. When communicating with the OM-DAQXL via Ethernet it is recommended to pass the Ethernet cable through a ferrite 2 turns before connecting it to the OM-DAQXL. It is not recommended to have the AC adapter plugged in during normal operation. The AC adapter is intended to charge the battery only. Emissions: EN 61326-1 Class A Immunity: EN 61000-4-3 EN 61000-4-4 EN 61000-4-6 8-1 WARRANTY/DISCLAIMER OMEGA ENGINEERING, INC. warrants this unit to be free of defects in materials and workmanship for a period of 13 months from date of purchase. OMEGA’s WARRANTY adds an additional one (1) month grace period to the normal one (1) year product warranty to cover handling and shipping time. This ensures that OMEGA’s customers receive maximum coverage on each product. If the unit malfunctions, it must be returned to the factory for evaluation. OMEGA’s Customer Service Department will issue an Authorized Return (AR) number immediately upon phone or written request. Upon examination by OMEGA, if the unit is found to be defective, it will be repaired or replaced at no charge. OMEGA’s WARRANTY does not apply to defects resulting from any action of the purchaser, including but not limited to mishandling, improper interfacing, operation outside of design limits, improper repair, or unauthorized modification. This WARRANTY is VOID if the unit shows evidence of having been tampered with or shows evidence of having been damaged as a result of excessive corrosion; or current, heat, moisture or vibration; improper specification; misapplication; misuse or other operating conditions outside of OMEGA’s control. Components in which wear is not warranted, include but are not limited to contact points, fuses, and triacs. OMEGA is pleased to offer suggestions on the use of its various products. However, OMEGA neither assumes responsibility for any omissions or errors nor assumes liability for any damages that result from the use of its products in accordance with information provided by OMEGA, either verbal or written. OMEGA warrants only that the parts manufactured by the company will be as specified and free of defects. OMEGA MAKES NO OTHER WARRANTIES OR REPRESENTATIONS OF ANY KIND WHATSOEVER, EXPRESSED OR IMPLIED, EXCEPT THAT OF TITLE, AND ALL IMPLIED WARRANTIES INCLUDING ANY WARRANTY OF MERCHANTABILITY AND FITNESS FOR A PARTICULAR PURPOSE ARE HEREBY DISCLAIMED. LIMITATION OF LIABILITY: The remedies of purchaser set forth herein are exclusive, and the total liability of OMEGA with respect to this order, whether based on contract, warranty, negligence, indemnification, strict liability or otherwise, shall not exceed the purchase price of the component upon which liability is based. In no event shall OMEGA be liable for consequential, incidental or special damages. CONDITIONS: Equipment sold by OMEGA is not intended to be used, nor shall it be used: (1) as a “Basic Component” under 10 CFR 21 (NRC), used in or with any nuclear installation or activity; or (2) in medical applications or used on humans. Should any Product(s) be used in or with any nuclear installation or activity, medical application, used on humans, or misused in any way, OMEGA assumes no responsibility as set forth in our basic WARRANTY/DISCLAIMER language, and, additionally, purchaser will indemnify OMEGA and hold OMEGA harmless from any liability or damage whatsoever arising out of the use of the Product(s) in such a manner. RETURN REQUESTS/INQUIRIES Direct all warranty and repair requests/inquiries to the OMEGA Customer Service Department. BEFORE RETURNING ANY PRODUCT(S) TO OMEGA, PURCHASER MUST OBTAIN AN AUTHORIZED RETURN (AR) NUMBER FROM OMEGA’S CUSTOMER SERVICE DEPARTMENT (IN ORDER TO AVOID PROCESSING DELAYS). The assigned AR number should then be marked on the outside of the return package and on any correspondence. The purchaser is responsible for shipping charges, freight, insurance and proper packaging to prevent breakage in transit. FOR NON-WARRANTY REPAIRS, consult FOR WARRANTY RETURNS, please have the OMEGA for current repair charges. Have following information available BEFORE contacting the following information available BEFORE OMEGA: contacting OMEGA: 1.Purchase Order number under which the product 1. Purchase Order number to cover the COST was PURCHASED, of the repair, 2.Model and serial number of the product under 2. Model and serial number of the product, and warranty, and 3. Repair instructions and/or specific problems 3. Repair instructions and/or specific problems relative to the product. relative to the product. OMEGA’s policy is to make running changes, not model changes, whenever an improvement is possible. This affords our customers the latest in technology and engineering. OMEGA is a trademark of OMEGA ENGINEERING, INC. © Copyright 2018 OMEGA ENGINEERING, INC. All rights reserved. This document may not be copied, photocopied, reproduced, translated, or reduced to any electronic medium or machine-readable form, in whole or in part, without the prior written consent of OMEGA ENGINEERING, INC. Where Do I Find Everything I Need for Process Measurement and Control? OMEGA…Of Course! Shop online at omega.com TEMPERATURE M U Thermocouple, RTD & Thermistor Probes, Connectors, Panels & Assemblies M U Wire: Thermocouple, RTD & Thermistor M U Calibrators & Ice Point References M U Recorders, Controllers & Process Monitors M U Infrared Pyrometers PRESSURE, STRAIN AND FORCE M U Transducers & Strain Gages M U Load Cells & Pressure Gages M U Displacement Transducers M U Instrumentation & Accessories FLOW/LEVEL M U Rotameters, Gas Mass Flowmeters & Flow Computers M U Air Velocity Indicators M U Turbine/Paddlewheel Systems M U Totalizers & Batch Controllers pH/CONDUCTIVITY M U pH Electrodes, Testers & Accessories M U Benchtop/Laboratory Meters M U Controllers, Calibrators, Simulators & Pumps M U Industrial pH & Conductivity Equipment DATA ACQUISITION M U Communications-Based Acquisition Systems M U Data Logging Systems M U Wireless Sensors, Transmitters, & Receivers M U Signal Conditioners M U Data Acquisition Software HEATERS M U Heating Cable M U Cartridge & Strip Heaters M U Immersion & Band Heaters M U Flexible Heaters M U Laboratory Heaters ENVIRONMENTAL MONITORING AND CONTROL M U Metering & Control Instrumentation M U Refractometers M U Pumps & Tubing M U Air, Soil & Water Monitors M U Industrial Water & Wastewater Treatment M U pH, Conductivity & Dissolved Oxygen Instruments M5570/0318
advertisement