advertisement
▼
Scroll to page 2
of
8
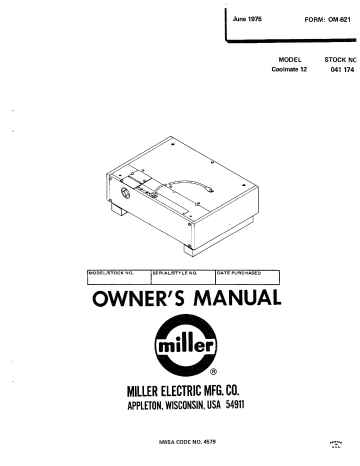
| June 1975 FORM: OM-621 MODEL STOCK NC Coolmate 12 041 174 MODEL/STOCK NO. |SERIAL /STYLE NO. DATE OWNER'S MANUAL MILLER ELECTRIC MFG. CO. APPLETON, WISCONSIN, USA 54911 NWSA CODE NO. 4579 LA CE LR UN CU EF A EF EF RF A СОШО Пооо Оооо ооо ОсОО E - - - - 75 = - a [5 - - La С) че - 5 - - - - - - ES == - [5 - -— ™ Ч = = - - - = - #5 E ” 3 = 3 С - - - - - - - E m Ly 47 oF LF UF LI) LA EJ oF UL) oF Lr LF BL) IJ EE NOC O00000000000D00000000000000D0CG0000RODOO00O 0 00 WEE LLOQ C1 OOO U0 Oy |) DU OUR C5 CI OB J || Li | | 3 0 LU |] LJ £3 U LU LU LU LA oF LU |] |] Ly CE Lh.) Г] lJ] LJ |] UL WARRANTY MILLER Electric Mfg. Co., Appleton, Wisconsin, warrants all new equipment to be free from defects in material and factory workmanship for the periods indicated below, provided the equipment is installed and operated according to manufacturer's instructions. MILLER Electric Mfg. Co.'s obligation, under this warranty, is limited to replacing or repairing any defective part or correcting any manufacturing defect without charge during the warranty period if MILLER’S inspec- tion confirms the existence of such defects. MILLERS option of repair or replacement will be f.o.b. factory at Appleton, Wisconsin or f.0.b. a MILLER authorized service facility, and therefore no compensation for trans- portation costs of any kind will be allowed. The warranty period, beginning on the date of sale to the original purchaser-user of the equipment, will be as follows: | 1. Arcwelders, power sources, and components —— 1 year 2. Original main power rectifiers — 3 years (unconditionally) 3. MHFC-L1 Feeder, MHG-35C1, 20E, 20K, and all guns and torches — 90 days 4. All other Millermatic Feeders — 1 year 5. Mag-Diesel engine on DEL-200 — 6 months 6. All other engines — 1 year Engine Warranties are covered by the engine manufacturers, subject to their procedures and to be handled through their authorized local Service Stations or agencies. No warranty will be made in respect to trade accessories, such being subject to the warranties of their respective manufacturers. MILLER Electric Mfg. Co. will not be liable for any loss or consequential damage or expense accruing directly or indirectly from the use of equipment covered in this warranty. This warranty supersedes all previous MILLER warranties and is exclusive with no other guarantees or warranties expressed or implied. мысу ово Оооо С Оооо ОсОО оО НОНО ОВОС ЙН ООО ii le af yi по лата alte ram pollo pla gms ys po] JU QUU DL JUUVOUUQOUQOGOUDOOUUQGUUUOQOUUOGOGOODUOOGDDSOL DOU QUO DOUUUVODUOGOUU UV QUODOUDQDOUUDOGOUOUOGOOL OR O0000000000Q00000Q00000000000000D0000000000000000000000D0 0 —— SECTION ; - INTRODUCTION 1-1. 1-2. Overali Dimensions Motor Motor | Ampere Tank {Inches} Weight | Input Frequency | Speed Input | Capacity Width | Height | Length | (Pounds) | Voltage | Phase | (Hertz) |I(RPM) | (Full Load} | (US Gallons} 31-1/4 | 11-1/16 23 112 |115VACI Single 60 1725 5.0 12 Figure 1-1. Specifications GENERAL 1-4. SAFETY This manual has been prepared especially for use in familiar- izing personnel with the design, instaltation, operation, main- tenance, and troubleshooting of this equipment. All informa- tion presented herein should be given careful consideration to assure optimum performance of this equipment. RECEIVING-HANDLING Prior to installing this equipment, clean all packing material from around the unit and carefully inspect for any damage that may have occurred during shipment. Any claims for loss or damage that may have occurred in transit must be filed by the purchaser with the carrier. A copy of the bill of lading and freight bill will be furnished by the carrier on request if occasion to file claim arises. When requesting information concerning this equipment, it is essential that Model Description and/or Stock Number and Serial lor Style) Numbers of the equipment be supplied. DESCRIPTION This coolant system consists of an electric motor, steel tank, and a high pressure pump to circulate the coolant. A bypass valve is installed in the pump discharge line as a pressure relief, The delivery rate is as follows: {Water Coolant — 60°0F) 0 pounds pressure 1.49 gallons per minute 20 pounds pressure 1.35 gallons per minute 40 pounds pressure 1.21 gallons per minute 60 pounds pressure 1.07 gallons per minute 80 pounds pressure 0.94 gallons per minute 100 pounds pressure 0.80 gallons per minute LOCATION (Figure 2-1) Holes are provided in the coolant system top and bottom for mounting purposes. The top holes are provided to mount the welding power source onto the coolant system. The bottom holes are provided to mount the coolant system onto a sta- tionary object or optional running gear, if desired. Figure 2-1 gives overall dimensions and mounting hole layout. 2-7/8" 3/8"-1 6 4 Threaded Holes 9/16" Dia. 4 Holes 25-1/2" а|| 1-1/4" TC-003 557 Figure 2-1. Overall Dimensions and Mounting Hole Layout SECTION 2- INSTALLATION The following definitions apply to CAUTION, IMPORTANT, and NOTE blocks found throughout this manual: ERTL \ Under this heading, installation, operating, and main- tenance procedures or practices will be found that if not carefully followed may create a safety hazard to | personnel, ] IMPORTANT Under this heading, installation, operating, and main- tenance procedures or practices will be found that if not carefully followed may result in damage to equip- i ment. ] Under this heading, explanatory statements wiil be found that need special emphasis to obtain the most efficient operation of the equipment. 2-2. ELECTRICAL INPUT CONNECTIONS {Figure 2-2) Motor/Pumpb Access Panel Viewing Pump Bypass Valve & Pump Qutlet Receptacie Return Line Receptacle Coolant Tank Access Door e Cap Nut » . voor мег quer cord Lubrication 8 Ритр Cups TC-003 558 Figure 2-2. Component Location OM-621 Page 1 2-3. A three foot cord with attached three prong piug is provided to conduct power from a 115 volts ac, 60 hertz power supply to the coolant system. It is recommended that the welding power source 115 VAC receptacle be utilized to provide 115 VAC power for the coolant system. By doing thusly, the coolant system will be operative whenever the welding power source is energized. COOLANT CONNECTIONS (Figure 2-2) A PUMP OUTLET receptacle and a RETURN LINE recep- tacle are provided to connect the welding gun coolant hoses. Both of these receptacles have left-handed threading. 3-1. BYPASS VALVE (Figure 2-2) A bypass valve is installed in the pump discharge line for providing pressure relief, if the discharge line should be closed for any reason. Factory setting of the bypass valve is at 45 Ibs. pressure. Pressures up to 100 Ibs. may be used for elevating coolant to approximately 100 feet. Pressures in excess of 100 PSI should be avoided as this will overload the motor. To adjust the bypass valve pressure, remove the motor/pump access panel. Remove the cap nut and turn the pressure 2-4, COOLANT AND {Figure 2-2) | LUBRICANT INSTALLATION Coolant system pumps require some lubricant in the coolant to lubricate the packings of the pump. The suggested ratio is about one quart to every twelve gallons of coolant. This unit 15 shipped with the proper amount of lubricant which is to be added to the solution when the coolant system is first placed into operation. The coolant tank may be filled by 100sening the access door screw and lifting the access door. The tank should then be filled with coolant until the coolant level is to the center of the viewing port. Replace the access door. 3-2. adjustment screw clockwise to increase pressure. Replace cap nut to lock the pressure adjustment screw at the desired pressure. Replace the motor/pump access panel. VIEWING PORT (Figure 2-2) The viewing port purposes are twofold: When the coolant ievel is in the center of the viewing port the coolant tank is filled to the proper capacity. In addition, the splashing of the coolant against the viewing port indicates that the coolant system is functioning properly. 4-1, Page 2 COOLANT SYSTEM TANK Coolant system tanks should be cleaned and fresh coolant and lubricant added periodically. For every twelve gallons of coolant, a single teaspoonful of common laundry bleach should be added to the coolant system after fresh coolant and lubricant are added. The bleach prevents bacteria growth. Useful life of the coolant mixture will be measurably extended. The use of demineralized coolant is also advised in the i coolant system, if available. ] 4-2. 4-3. COLD WEATHER MAINTENANCE Where freezing conditions may be encountered, permanent antifreeze may be substituted for the lubricant mentioned above except that the mixture will be determined by the temperature conditions anticipated. Permanent antifreeze has sufficient lubricity for adequate pump lubrication. The pump has graphite bearings which require no more lubrication than that contained in the coolant. MOTOR LUBRICATION {Figure 2-2) The motor is provided with lubrication cups which shouid be filled with SAE 20 oil periodically. | June 1975 FORM: OM-621 MODEL STOCK NO. Coolmate 12 041 174 MODE L/STOCK NO. SERIAL/STYLE NO. DATE PURCHASED PARTS LIST ® MILLER ELECTRIC MFG. CO. APPLETON, WISCONSIN, USA 54911 NWSA CODE NO. 4579 G66 £00-ad4 AJquassy aje|duroo — y aanbig OM-621 Page 1 Item Factory No. Part No. Description Quantity Figure A Complete Assembly 1 010494 BUSHING, snap 1-3/8 ID X 1-3/4 hole .. oo oti re ite ee RR a LL 1 2 601890 RIVET, blind 1/8 dia 1/8 grip ................. 00.000 000íererrereorevocararede. 1 3 1000679 COVER, tank ......... eareracianedaorererereorneraranedaroeroererono oroeecue ramo 1 4 604 804 SCREW, sheet metal -hex washer hd No. 8X 3/8... citi ie te ee eee eee eee an 6 5 000678 TANK Lt ee ee La aan LL FE 1 6 603105 HOSE, braided 5/16 ID x 1 {order by foot) ........ ee ee La ea 4 4 44 La ea ee 5 ft. / 023562 CLAMP, hose 5/16 to 7/8 clamp dia.........222222 21001 a LL LL La a La a La aa aa A 5 8 602958 COUPLING, brass - male 1/4 ID hose 1/4 MPT .........., Ce ee ee ee. 4 9 035632 STRAINER ......... RR RR RR aa 1 10 602240 WASHER, flat - steel standard 1/4 ................ RER era LL 4 17 601 954 SCREW, cap - steel hex hd 1/4-20 x 3/4 1111111100 0 4440 0 44 a à ae a a La Rad ALL eae 5 12 000654 CORD SET, power 3ft.....22210 00102 LA 4e 44 4 4 a a a 8 ee a de 4 4 0 a a ea ea da a La aa ae 1 13 010610 CONNECTOR, clamp - cable 1/72 ......... 2... нее кники ee aa a de ee a a a aa aa a a an a 1 14 027803 MOTOR ......212 104 64484 4 a 4 844 RR A RAR Aa 4 4 4e a 4 4 A ee a 4 a eee a a aa ue 1 15 6010357 RECEPTACLE, clip on No. 2screw .....12212000 00124 a ea a a 8 a 8 a 8 a 4 0 a 4 eau a 4 ea a 0 aan 5 16 602 207 WASHER, lock - steel Split 1/4 1.000000 ite ee te ee eee ee ee ee eee ee ieee eens 5 17 601865 NUT, steel - hex {#011 1/4-20 .. 5... 5.5... ie ee RER RER ea 0 5 18 (010594 GROMMET, rubber 1/2 1D x 1 inch hole 1/16 groove ...........m_e.reavedadadnoaaonea 1 19 010678 ELBOW, brass - pipe street 90 degree 1/4 PT ..............e000- so nricorr rarecnerereo 3 20 010428 COUPLER, motor to pump ..........ee se. 9unedareaaaareada raro» eee hee 1 21 602180 SCREW, set - steel socket hd 5/16-18 x 1/4 ooo viii. ee 4 22 000848 PUMP, coolant «titre ee ee ee eee ee ee ne eee 1 23 000868 BRACKET, mounting- pump........qeew_woeeeroeerernroraoroooroeovarooranonedaoo 1 24 015715 GROMMET, rubber 11/16 1D x 1 inch hole 5/64 groove ...............eeesaexv e e eea, 1 25 010853 FASTENER, screw - slotted hd No. 2........e _ec-merredorreraaaroceararene na nena 5 26 000664 DOOR, access ..............eo—.—.memaroaaecrereraororoooaaooorodredraradrvarneererere. 1 27: 010855 RETAINER, screw NO. 2 ..........e es ]neeooreroorere.enerearanenmerónenennaea 5 28 000655 BLOCK, connecting ...........ñeeesxnenoonronanedarerenaneoonoaaoraarocornora co 1 29 010378 GROMMET, rubber 9/16 ID x 3/4 hole 1/16 groove ..........._eeoereroonooorooooaa. | 1 30 605795 SCREW, self tapping - flat hd 8-32 x 1/2 ..,....................,.. eee, 4 31 000741 PORTHOLE, view - Gauge oo oot tt ites tt tree tees tate etree eee etree ann, 1 32 000660 COVER, filler box iti ttt tt tet eee ete ee eee ees een 1 33 NAMEPLATE (order by stock, model and style numbers) ............eorrecvoerooreeras 1 34 602200 WASHER, lock - steel split No. 8 ............—...0r0-...r0n0a eerie 3 35 602082 SCREW, machine - steel round hd 8-32 X 1/2 «oir ee eee ieee 3 601 965 SCREW, cap - steel hex hd 3/8-16 x 1 {attaching tank to weldingunit) ................... 4 602 243 WASHER, flat - steel standard 3/8 {attaching tank to weldingunit) ...................... 4 602 224 WASHER, lock - steel split 3/8 {attaching tank to weldingunit} ........................ 4 BE SURE TO PROVIDE STOCK, MODEL, AND STYLE NUMBERS WHEN ORDERING REPLACEMENT PARTS. OM-621 Page 2
advertisement