advertisement
▼
Scroll to page 2
of
92
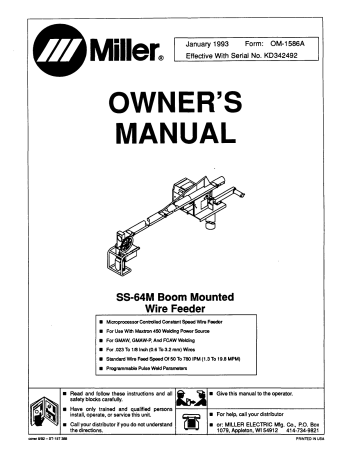
Millerfi January1993 Form: OM-1586A Effective With Serial No. KD342492 OWNERS MANUAL SS-64M Boom Mounted Wire Feeder Miaoprocessor ConPol led Constant Speed Wire Feeder For Use With Maxtron 450 Welding Power Source GMAW, GMAW-P, And FCAW Welding For For .023 To 1/8 Inch (0.6 To 3.2 mm) Wires Standard Wire Feed Programmable SpeedOf 5OTo 780 1PM (1.3To 19.8 MPM) Pulse Weld Parameters Give this manual to the operator. Read and follow these instructions and all safety blocks carefully. Have only trained install, operate, or and qualified persons service this unit. Call your distributor if you do not understand the directions. cover 8192 ST-157 388 For f~) or: help, call your distributor MILLER ELECTRIC Mfg. Co., 1079, Appleton, WI 54912 P.O. Box 414-734-9821 PRINTED IN USA I I J MILLERS TRUE BLU ElM LIMITED WARRANTY (Equipment This limited warranty with Effective January 1, 1992 serial number preface of KC a supersedes all previous MILLER warranties and is aaclusive with below, MILLER Electric Mfg. Co.. Appleton, Wisconsin, warrants to its original retail purchaser that new MILLER eouipment sold after the effective date of this limited warranty is tree of de tects in material and workmanship at the time it is shipped by MILLER. THIS WAR RANTY IS EXPRESSLY IN LIEU OF ALL OTHER WARRANTIES, EXPRESS OR IMPLIED, INCLUDING THE WARRANTIES OF MERCHANTABILITY AND FIT Subject LIMITED WARRANTY to the tarms and conditions MILLERS NESS. the or warrantieo expressed or implied Kits Replacement Fans Withis the warranty periods listed below, MILLER wilt repair or replace any war ranted parts or components that fail due to such detects is material or workmanship MILLER must be notified in writing within thirty (30) days of such detect or failure, at on newer) othar guarantaes Accessory I which time MILLER will provide instructions no or True eiuenM Limited Warranty shall not apply to. Items furnished by MILLER. but manufactured by others, ouch as engines or trade accessories. These items are covered by the manutacturers warranty, if any. 2. Consumable components: such and warranty claim procedures lobe as contact tips, cutting nozzles. contactors relays followed. 3. start on the date that the and are I. as was delivered to the original Plasma Arc Cutting Power Sources Parts and Labor Engine Driven Welding Generators (NOTE: Engines are warranted separately by the engine manufacturer.) TO THE EXTENT PERMtTTEO BY LAW, THE REMEDIES PROVIDED HEREIN ARE THE SOLE AND EXCLUSIVE REMEDIES. IN NO EVENT SHALL MILLER BE LIABLE FOR DIRECt INDIRECT SPECIAL, INCIDENTAL OR CONSEOUENTIAL DAMAGES (INCLUDING LOSS OF PROFIT). WHETHER BASED ON CON TRACT, TORT OR ANY OTHER LEGAL THEORY. Pans and Labor Motor Driven Guns Process Controllers Water Coolant * Systems HF Units ANY EXPRESS WARRANTY NOT PROVIDED HEREIN AND ANY tMFLIEO WAR Grids Spot * RANTY, GUARANTY OR REPRESENTATION AS TO PERFORMANCE, AND ANY REMEDY FOR BREACH OF CONTRACT TORT OR ANY OTHER LEGAL THEORY WHICH, BUT FOR THIS PROVISION. MIGHT ARISE BY IMFLtCATtON, OPERATION OF LAW, CUSTOM OF TRADE OR COURSE OF DEALING. IN CLUDING ANY IMFLtEO WARRANTY OF MERCHANTABILITY OR FITNESS FOR PARTICULAR FURFOSE. WITH RESPECT TO ANY AND ALL EOUIFMENT Welders * Load Banks * SDX Transformers * Running Gear/Trailers Field Options FURNISHED BY MILLER IS EXCLUDED AND DISCLAIMED BY MILLER. (NOTE: Field options are covered under True BtuenM for warranty period of the product they are installed in, or for whichever in greater.) one year 5. 6 Months B. 90 Days warranty claim covered by this warranty, the esclusive remedies option: (I) repair: or (2) replacement: or, where authorized in writing by MILLER in appropriate cases, (3) the reasonable cost of repair or replace ment at an authorized MILLER service station: or (4) payment of or credit for the pur chase price (less reaaonabie depreciation based upon actual use) upon return ot the goods at customers risk and eepsnss. MILLERS option of repair or reptecement will be FOB.. Factory at Appleton, Wisconsin, or FOB. at a MILLER authorized ser vice facility as determined by MILLER. Therefore no compensation or reimburse ment br transportation costs of any kind will be allowed. Robots 2 Years Year not had reasonable shall be, at MILLERS Semi-Automatic and Automatic Wire Feeders I equipment which has MILLER PRODUCTS ARE INTENDED FOR PURCHASE AND USE BY COMMER In the event of a 4. or Parts and Labor 3 Yearn * industry standards, CIALIINDUSTRIAL USERS AND PERSONS TRAINED AND EXFERtENCED tN THE USE AND MAINTENANCE OF WELDING EOUIFMENT main power rectitisrs Transformer/Rectifier Power Sources 3. by any party other than MILLER. or equip improperly installed, improperly operated or misused and necessary maintenance, or equipment which has been used for operation outside of the specifications tor the equipment. 3 Years Labor 5 Years Parts that has been modified based upon retail purchaser, follows: Original 2. equipment Equipment ment that has been MILLER shall honor warranty claims on warranted equipment listed below in the event of such a failure within the warranty time periods. All warranty time periods the a remaining Some states in the U.S.A. do not allow limitations of how long an implied warranty lasts, or the exclusion of incidental. indirect. special or consequential demeges, so minimum ot the above limitation or escluaion may not apply to you. This warranty orovidea spe cific legal rights. and other rights may be aveilable, but may vary from state to stete. Batteries In Parts and Labor or MIG Guns/TIG Torches Cutting * Plasma * Remote Controls Canada. legislation in some remedies other than as provinces provides for certain additional werranties stated herein, and to the extent that they may not be waived, the limitations and exclusions set out above may not apply. This Limited Warranty provides specific legal rights, and other rights may be available, but may Torches vary from province to province. a~1- I RECEIVING-HANDLING Before Unpacking eqUipment, check carton for any damage that may have occurred during shipment. File any claims for )oss or damage delivering carrier. Assistance for filing or settling claims may be obta)ned from distributor and/or equipment manufacturers Transportation Department. with the When requesting information about this equipment, always provide Model Designation Use the or following spaces to record Model Designation and Serial or and Serial Style Number of your unit. or Style Number. The information is located on the rating label nameplate. Model _________ Serial or Style No. Date of Purchase miller 5/92 ERRATA SHEET January 14, 1993 FORM: OM-1586-A Use above FORM number when After this manual to data appearing was printed, refinements as Dia. **First ... This sheet Ii sts exceptions PARTS LIST follows: Part No. Mkgs. 77-28 equipment design occurred. extra manuals. later in this manual. AMENDMENT TO SECTION 16 Amend Parts List in ordering PC8O,RC8O ... digit represents page 158 578 no Replaced With ... 159 477 Description .. CIRCUIT CARD, HF filter (Eff digits following dash represent item Quantity w/KD348472) no. BE SURE TO PROVIDE MODEL AND SERIAL NUMBER WHEN ORDERING REPLACEMENT PARTS. 1 ARC WELDING SAFETY PRECAUTIONS WARNING a ARC WELDING be hazardous. can PROTECT YOURSELF AND OTHERS FROM POSSIBLE SERIOUS INJURY OR DEATH. KEEP CHILDREN AWAY. PACEMAKER WEARERS KEEP AWAY UNTIL CONSULTING YOUR DOCTOR. In welding, as in most jobs, exposure to certain hazards occurs. Welding is safe when precautions are taken. The safety information given below is only a summary of the more complete safety information that will be found in the Safety Standards listed on the next page. Read and follow all Safety Standards. INSTALLATION, OPERATION, MAINTENANCE, AND REPAIR WORK PERFORMED ONLY BY HAVE ALL QUALIFIED PEOPLE. ELECTRIC SHOCK can kill. live electrical parts can cause fatal shocks burns. The electrode and work circuit is electrically live whenever the output is on. The input power circuit and machine internal circuits are also live when power is on. In semiautomatic or automatic wire welding. the wire, wire reel, drive roll housing, and all metal parts touching the welding wire are electrically live. Incorrectly installed or improperly grounded equipment is a hazard. Properly 6. When Touching or 1. 2. 3. severe making input connections, 7. Turn off all 8. Do not cables. equipment when not in Disconnect input power equipment. or stop engine before installing or servicing ARC RAYS can burn eyes and skIn; NOISE can damage hearIng. ~ or poorly spliced Do not wrap cables around your body. 10. Ground the electrical 11. Do not touch electrode if in contact with the work 12. only well-maintained equipment. damaged parts at once. 13. Wear a Keep all 9. 14. this grounding use. damaged, undersized, worn, use workpiece to good a Do not touch live electrical parts. Wear dry, hole-free insulating gloves and body protection. Insulate yourself from work and ground using dry insulating attach proper conductor first. mats or covers. 4. install and ground this equipment according to its Owners Manual and national, state, and local codes. 5. (earth) ground. safety harness if and panels ground. replace or above floor level. working covers or Repair Use securely in place. ARC RAYS 2. Wear helmet fitted with welding a a proper shade of filter (see ANSI Z49. 1 listed in Arc rays from the welding process produce intense heat and strong ultraviolet rays that can burn eyes and skin. Noise from some processes can damage .. hearing. 3. 4. Safety Standards) to protect your face and eyes when welding or watching. Wear approved safety glasses. Side shields recommended. protective screens or barriers to protect others from flash glare; warn others not to watch the arc. Wear protective clothing made from durable, flame-resistant material (wool and leather) and foot protection. Use and NOISE 5. 1. Use approved ear plugs or ear muffs if noise level is FUMES AND GASES to your health. I Welding produces fumes I these fumes and gases health. can high. be hazardous Work in 6. Do not weld in locations and gases. Breathing be hazardous to your can £...~. your head out of the fumes. Do not breathe the fumes. area and/or use exhaust at the arc to 1. Keep 2. If inside, ventilate the remove 7. fumes and gases. welding If ventilation is poor, use 4. Read the Material an instruction for metals, consumables, manufacturers burns. Accidental contact of electrode or welding wire to metal objects can cause sparks, overheating, or fire. and others from flying sparks 1. Protect 2. Do not weld where 3. Remove all flammables within 35 ft yourself flying sparks can Watch for fire, and 6. Be aware that can cause unless the fire keep welding on a fire on a extinguisher nearby. 7. Do not weld Connect work cable to the work practical possibly on closed containers such prevent welding to unknown paths and as Do not use welder to thaw frozen I Chipping and can grinding drums. electric shock and fire or cut off protective garments such heavy shirt, cuffless trousers, high shoes, 1. Wear approved face shield or as and welding wire at leather gloves. a safety goggles. cap. Side shields recommended. injury, cool, they or welding area as traveling long, pipes. Wear oil-free 4 partition hazards. 9. 11. FLYING SPARKS AND HOT METAL can tanks from current causing possible, tightly cover them with approved covers, Be alert that welding sparks and hot materials from welding can easily go through small cracks and openings to adjacent areas. cause as close to the Remove stick electrode from holder contact tip when not in use. welding or the hidden side. 10. of the or is removed from the ceiling, floor, bulkhead, arc. (10.7 m) galvanized, lead, as coating is well ventilated, and if necessary, while 8. If this is not 4. area 5. and hot metal. strike flammable material. coated metals, such on plated steel, wearing an air-supplied respirator. The coatings and any metals containing these elements can give off toxic fumes if welded. and cleaners, can cause fire or explosion. Sparks and spatter fly off from the welding arc. The flying sparks and hot metal, weld spatter, hot workpiece, and hot equipment can cause fires and Do not weld weld area, the coatings, WELDING near degreasing, cleaning, or spraying operations. The heat and rays of the arc can react with vapors to form highly toxic and irritating gases. cadmium approved air-supplied respirator. Safety Data Sheets (MSDSs) and the 3. a confined space only if it is well ventilated, or while wearing an air-supplied respirator. Shielding gases used for welding can displace air causing injury or death. Be sure the breathing air is safe. 5. cause throw off flying metal. As welds 2. Wear proper body protection to protect skin. slag. srI 9/92 ~J ~~ CYLINDERS explode if damaged. can Keep cylinders 3. Shielding gas cylinders contain gas under high pressure. If damaged, a cylinder can explode. Since gas cylinders are normally part of the welding process, be sure to treat them carefully. or other electrical a welding electrode to touch any cylinder. only correct shielding gas cylinders, regulators, hoses, and fittings designed for the specific application: maintain them and associated parts in good condition. Turn face away from valve outlet when opening cylinder valve. Keep protective cap in place over valve except when cylinder is 5. from excessive heat, 7. upright position by chaining equipment cylinder rack to 8. compressed gas cylinders mechanical shocks, and 2. welding Never allow 4. Use 6. Protect 1. away from any circuits. in arcs. cylinders in them to a stationary support prevent falling or tipping. Install and secure an or connected for use or use. Read and follow instructions associated equipment, compressed gas cylinders, publication P-i listed in Safety on and CGA Standards. A__WARNING ENGINES can be hazardous. ___ ENGINE EXHAUST GASES Engines produce harmful ENGINE FUEL can kill. Use If used in closed area, vent engine exhaust outside and away from any building air intakes. 1. Stop engine before checking or adding fuel. Do not add fuel while smoking or if unit is near exhaust gases. can cause fire or explosion. outside in open, well-ventilated areas. 1. 2. 2. equipment a any sparks or open flames. 3. Engine fuel is highly flammable. engine to cool before fueling. If possible, check and add engine before beginning job. allow room for fuel to expand. Do not overfill tank Do not spill fuel. If fuel is spilled, clean up before starting Allow fuel to cold 4. 5. engine. MOVING PARTS can cause 3. injury. Have only qualified people maintenance and Moving parts, such as fans, rotors, and belts can fingers and hands and catch loose clothing. 4. cut 5. 1. Keep all doors, panels, securely in place. 2. Stop engine before installing covers, or and guards closed and connecting AND COOLANT can skrn. The coolant in the radiator under pressure. can To loose clothing, for disconnect prevent accidental starting during servicing, negative () battery cable from battery. Keep hands, hair, covers and tools away from moving 1. Always servicing is wear a face shield when working on a battery. Stop engine before disconnecting or connecting battery cables. explosive PRESSURIZED HOT burn face, eyes, and or Reinstall panels or guards and close doors when finished and before starting engine. 2. gases. STEAM guards necessary. 6. unit. and generate as parts. SPARKS can cause BATTERY GASES TO EXPLODE; BATTERY ACID can burn eyes and skin, Batteries contain acid remove troubleshooting . 3. Do not allow tools to 4. Do not 5. Observe correct polarity (+ and ) 1. use cause welder to sparks when working charge batteries Do not remove radiator cap when on on a battery. jump start vehicles. or batteries. engine is hot. Allow engine to cool. 2. Wear gloves and put 3. Allow pressure to escape before a rag over cap area when removing cap. be very hot and completely removing cap. PRINCIPAL SAFETY STANDARDS Safety in Welding and Cutting, ANSI Standard Z49. 1, from American Welding Society, 550 N.W. LeJeune Rd, Miami FL 33126 Safety and Health Standards, OSHA 29 CFR 1910. from dent of Documents, U.S. Government D.C. 20402. Safe Handling of Compressed Gases in Cylinders, CGA Pamphlet P-i, from Compressed Gas Association, 1235 Jefferson Davis High way, Suite 501, Arlington, VA 22202. Superinten Printing Office, Washington, Code for Safety in Welding and Cutting, CSA Standard Wi 17.2, from Canadian Standards Association, Standards Sales, 178 Rexdale Bou levard, Rexdale, Ontario, Canada M9W 1 R3. Recommended Safe Practices for the Preparation for Welding and Cutting of Containers That Have Held Hazardous Substances. Ameri can Welding Society Standard AWS F4. 1, from American Welding So ciety, 550 NW. LeJeune Rd, Miami, FL 33126 National Electrical Code, NFPA Standard 70, from National Fire Pro tection Association, Batterymarch Park, Quincy, MA 02269. sri 9/92 Safe Practices For Occupation And Educational Eye And Face Protec tion, ANSI Standard Z87.1, from American National Standards Institute, 1430 Broadway, New York, NY 10018. Cutting And Welding Processes, Fire Protection Association, NFPA Standard 51B, from National MA 02269. Batterymarch Park, Quincy, TABLE OF CONTENTS SAFETY INFORMATION SECTION 1 1 SECTION 2- SPECIFICATIONS SECTION 3 1 INSTALLATION 2 3-3. Installing Swivel Into Pipe Post Installing Boom And Reel Support Installing Wire Guide Extension 3-4. Wire Guide And Drive Roll Installation 3 3-1. 3-2. 2 3 Gun Connections 3-5. Welding 3-6. Wire Feed Motor, Gas Valve, And Reed 3-7. Control Connection 6 3-8. 7 3-10. Shielding Gas And Weld Cable Connections Removing Safety Collar And Adjusting Boom Welding Wire Installation 3-11. Motor Start Control 3-12. Threading Welding 3-9. SECTION 4 4 Relay Connections 5 8 8 10 Wire 11 GLOSSARY 12 SECTION 5OPERATION 5-1. Front Panel Controls 14 5-2. Side Panel Controls 16 5-3. Rear Panel Controls 16 SECTION 6- STEPPING THROUGH THE MICROPROCESSOR CONTROLS 6-1. Front Panel 6-2. Side Panel Microprocessor Push Buttons Microprocessor Controls 18 20 SECTION 7 STANDARD PULSE WELDING PROGRAMS SECTION 8 GETTING STARTED 8-1. 8-2. Welding With Only Front Panel Controls Setting Sequence Pulse Welding Parameters SECTION 9TEACHING 9-1. 9-2. 9-3. 9-4. 32 On Side Panel Display 33 A PULSE WELDING PROGRAM Pulse Waveform 37 Teach Points 38 Explained Explained Teaching A Pulse Welding Program Changing To Adaptive Pulse Welding 39 41 SECTION 10- TEACHING A MIG WELDING PROGRAM 42 SECTION 11 SETTING DUAL SCHEDULE PARAMETERS 46 SECTION 12 USING THE DATA CARD 12-1. 12-2. 12-3. Installing Data Card Using The Data Card Naming Programs SECTION 13 13-1. 13-2. 13-3. 48 48 50 SECURITY & SETUP Security/Setup Flow Chart Using Security/Setup Screens Selecting Security Lock 52 53 54 OM.1588A 1/93 SECURITY & SETUP SECTION 13 13-4. 13-5. 13-6. 13-7. 13-8. 13-9. 13-10. 13-11. 13-12. 13-13. 13-14. 13-15. 13-16. 13-17. (Continued) Selecting Or Changing Access Code Selecting Type Of Dual Schedule Switch Selecting Trigger Program Select Selecting Remote Increase/Decrease Capability Using Self Test Resetting Memory Selecting Program Name Feature Selecting Units For Wire Feed Speed And Motor Type Method Selecting Voltage Sensing Selecting Voftage Error Shutdown Resetting Arc Time Selecting Bench Or Boom Model Type Selecting Regular Or Hot Arc Start Selecting Voltage Correction 13-18. Software Version Number 55 56 57 57 58 59 59 60 60 61 61 61 62 62 62 SECTION 14- MAINTENANCE & TROUBLESHOOTING 14-1. 63 Routine Maintenance The Hub 63 14-2. Replacing 14-3. Overload Protection 64 14-4. Error Screens 64 Assembly Indicator LEDs 14-5. Diagnostic 14-6. Troubleshooting 66 SECTION 15 ELECTRICAL DIAGRAMS SECTION 16 PARTS LIST Figure Figure Figure Figure Figure 16-1. Main 16-2. Assembly Support, Hub & 65 68 72 Reel 75 16-3. Control Box 76 16-4. Wire Drive 79 16-5. Boom 80 Assembly Assembly Table 16-1. Drive Roll And Wire Drive Kits 82 MOVING SAFETY INFORMATION SECTION 1 modi.1 8~2 safety messages throughout Read all U Obey all to avoid safety messages Learn the meaning this manual. injury. of WARNING and CAUTION. Safety Alert Signal Word 2 2 1 I 2 I ~!1~1~ll~eU ELECTRIC SHOCK can WARN INC means possible death or serious injury can happen. ~, a CAUTION 3 klIV h,etaIilng or Input p~& serv~lng. CAUTION PARTS Keep away Do not touth lIve electrical pane. Ola~nnect 4 before from Keep all panels when operating. can I rraMng pane. and means possible minor injury or equipment damage can happen. Injure ~era dosed I I / 3 Statement Of Hazard And Result 4 Safety Instructions To Avoid Hazard 5 £~ READ SAFETY BLOCKS at start of Section 3-1 before proceedIng. WARNING 6 5 Hazard 6 Safety NOTE J Turn OFFswitch when using high frequency. SECTION 2 Symbol (If Available) Banner Read safety blocks for each sym bol shown. 7 7~I Symbol NOTE Special instructions for best ation not related to safety. oper SPECIFICATIONS Table 2-1. WIre Feeder SpecIfIcation Of Input Power From Power Source Type Maximum Weld Circuit DescriptIon Welding Rating Single-Phase 100 24 Volts AC, 10 Amperes, 50/60 Hertz Volts, 750 Amperes, 100% Duty Cycle Welding Power Source Type Constant Wire Feed Standard: 50 To 780 upm (1.3 To 19.8 mpm) High Speed: 92 To 1435 ipm (2.3 To 36.5 mpm) Low Speed: 13 To 213 ipm (0.34 To 5.38 mpm) Speed Range Wire Diameter Range Voltage (CV) DC, .023 Thru 1/8 in. Welding Process Gas Metal Arc Input Power Cord 10 ft. (0.6 To 3.2 mm) (GMAW), Gas Height With Weight 4 ft (1.2 m) 17 ft. Vertical Uft Of Boom - Pulse (GMAW-P), flux Cored Arc (3.7 m) Boom (5.2 m) 280 lbs. 16 ft. 21 ft. Net: 160 lbs. (73 Ship: Metal Arc Welding (FCAW) (3.1 m) 12 ft. Maximum Post With Contactor kg) (127 kg) Horizontal To 60 Above Horizontal (4.9 m) Boom (6.4m) Net: 210 lbs. (95 kg) Ship: 350 lbs. (159 kg) Horizontal To 60 Above Horizontal OM-1586 Page 1 SECTION 3INSTALLATION 3-1. Installing Swivel PIpe Post WARNING a I, Into FALLING OF SPRING PRESSURE RELEASE WITHOUT BOOM ATTACHED can cause serious personal Injury. Do not remove safety collar until instructed to do BOOM serIous cause can personal Injury and equIpment damage. Securely mount pipe post to base that can support weight of unit with boom in horizontal position. Use proper equipment for lifting swivel and boom into place. so. Swingpak Base 1 or CBC Cart 5 4 Post With Base 2 Pipe 3 Steel Bolt Secure as shown using as a mini mum 1/2 in. diameter SAE grade 5 steel bolts. Swivel 4 Insert into swivel. Safety 5 Do not 3 Assembly pipe post. Lubricate Collar remove until instructed to. Tools Needed: 3/4in. ST-i 52 268 FIgure 3-2. 4~ Installing Boom And Reel WARNING 3-1. SwIvel InstallatIon Support RELEASE OF SPRING PRESSURE A ND FALLING BOOM HAZARDS. Read begInnIng of Section 3-1 before proceedIng. safety Infor mation at 3 1 SwivelPiates 2 Yoke Remove hardware from swivel plates and yoke. 3 Boom Set boom into swivel 4 as shown. Yoke Pin Install pin through yoke. Install cot spread ends. ter pin and 2 5 Bolt Install bolt tighten hardware, and backboltoffone half turn. 6 Locking Knob Install locking knob but do not tighten. 7 3/4in.,3/8in. ST-142 596-B FIgure OM-1586 Page 2 ReelSupport Install reel support. Tools Needed: 3-2. Boom installation 3-3. Installing Wire Guide Extension Fitting 1 Wire Guide 2 Bolt 3 MonocoilLiner 4 Wire Guide Extension 4 flghten bolt to secure liner in wire guide fitting. Do not overtighten belt and crush liner. Tools Needed: C~J=O 3/8 in. ST-152 323 Figure 3-4. 3-3. Wire Guide Extension installation WIre Guide And Drive Roll Installation A~ WARNING ELECTRIC SHOCK can kill. Do not touch live electrical parts. Turn OFF wire feeder and welding power source, and disconnect input power before inspecting or installing. wfwaznl.1 W91 A. Wire Guide instailatlon Figure 3-4. Wire Guide instailation OM-1586 Page 3 B. Drive Roil Installation When changing wire size or type, check roll size drive (see Table 16-1). 1 Spnng Shaft Carrier Close spring shaft carrier. 2 Drive RoU Nut 3 Drive Roll Carrier Turn all nuts one click until lobes of nut line up with lobes of drive roll carner. Open spring shaft carrier. 4 Drive Roll Slide drive rolls onto drive roll cam ers. Close spring shaft carrier. Turn nut one click. 4 2 3 5 Drive Close Figure 3-5. Assembly Cover cover. ST.142 597.A 3-5. Drive Roll installation WeldIng Gun Connections WARNING A~ ___ ELECTRIC SHOCK can kill. Do not touch live electrical parts. Turn OFF wire feeder and welding power source, and disconnect input power before inspecting or installing. I Drive 2 Gun 3 Gun Connector Loosen Assembly Securing securing Cover Knob knob. Insert gun connector until it bottoms drive 4 assembly. Tighten Gun Trigger Plug 5 Gun against knob. Trigger Receptade Insert plug into free-hanging recep tacle and tighten threaded collar. 6 Trigger 7 Trigger Plug 8 Weld Con~ol Cord Trigger Receptadie 3 Insert tighten into receptacle and threaded collar. plug R&.ST-152460/ST.152321 /Rd.ST-157434 Figure OM-1586 Page 4 3-6. Gun And Thgger Lead Connections 3-6. A. Wire Feed Motor, Gas Valve, And Reed Wire Feed Motor, Gas Valve, And Reed Relay Relay Connections Connections 1 3 Wire Feed Motor And Gas Valve Control Receptacle 2 Plug From Boom 3 Cord From Boom Insert plug from boom cord into re ceptacle on rear of control, and tighten threaded collar. 4 Relay Receptacle Reed Insert plug from reed relay mounted on swivel into receptacle, and tighten threaded collar. Ref. ST-ISO 931-Al Ref. ST-157 434 Figure 3-7. Boom Connections B. Shielding Gas Connections To Regulator/Fiowmeter Obtain gas cylinder and chain to running gear, wall, or other station ary support so cylinder cannot fall and break off valve. 1 Cap 2 Cylinder Valve 2 Remove cap, stand to side of valve, and open valve slightly. Gas flow blows dust and cart from valve. Close valve. 8 3 3 Cylinder 4 CO2 5 Regulator Washer Install onto gas face is vertical. CO2 Fiowmeter/Regulator cylinder 6 Gas Hose Connection 7 Flowmeter so that has 5~-18 right-hand Obtain gas hose with fittings, and install between flowmeter and welding power source. Fitting threads. 8 Flow Adjust 2 Typical flow rate is 20 cfh feet per hour). (cubic 3 Tools Needed: 1-lI8in.5/8in. Argon Or Mixed Gas Fiowmeter/Regulator Figure 3-8. Gas ub3l 2/92SB-lOg 492-A OM-1586 Page Supply Connections 5 3-7. Control Connection 1 17-Pin Receptacle 2 Keyway interconnecting cord to receptacle, align keyway, insert plug, and tighten threaded collar. To connect 3 Reed Relay Section 3-6) 4 35 ft. (10.6 ing Lead Connect Receptacle (See m) Voltage Sens workpieco to (see Figure 3-10). 5 Threaded Collar 6 14-Pin Plug To connect plug to matching recep tade on welding power source, align keyway, insert plug, and tight en threaded collar. To Signals Supplied 14-PIn Plug: WeldIng Power Source Through Contactor Control A 24 volts B Contact closure to pin A tactor control circuit G Circuit ac. common completes the 24 volts ac con for 24 volts ac circuit. Voltage Control +10 volts dc. C Command D Control circuit E Remote power source voltage command signal from feeder (potentiometer wiper or 0 to +10 volts dc). H Nonfunctional at this time. signal; common. 6 5 The remaining pins are not Signals Supplied 17-Pin Receptacle: Remote To used. Welding Power Source Output Control C CC/CV select; +l3thru +24 volts dc CC. G Arc controldinductance Signals Supplied By Welding Remote Through control; 0 = CV, Ovoltsdc = to +10 volts dc. Power Source: Metering E Actual weld current output amps. M Actualweldvoltageoutputsignal;+1 signal; +1 volt dc = 100 voltdc= lOvolts do. The remaining pins are not used. Ref. ST-158 931A/ Figure OM-1 586 Page 6 3-9. Control Connections With Pin Information Ref. S-0612/ S-0003-AI S~O628 3-8. ShIelding Gas AA And Weld Cable Connections WARNING CYLINDERS can explode from Keep cylinders away If ELECTRIC SHOCK damaged. welding and other electrical circuits. Never touch Turn OFF wire feeder and welding power source. and disconnect input power before inspecting or cylinder with welding electrode. Always secure cylinder other stationary support. to kill. can Do not touch live electrical parts. installing. running gear, wall, BUILDUP OF SHIELDING GAS can harm health or kill. Shut off shielding gas supply when not in use. warn4.r 9/91 The weld cable and shielding gas hose extend 10 ft. (3 m) from the boom. Route through weld reed cable from boom relay. If the welding power source or gas supply are further from the boom, extend cable tI~I~2 or 1 Weld Cable 2 Insulated hose as follows: Sleeving together weld cables from welding power source and boom. Bolt Use electrical tape and insulated sleeving to cover connection. 3 Shielding Gas Hose Connect hose to gas supply or ex tension hose. The hose from the has boom 5/8-18 right-hand threads. Tools Needed: ~ 5/8in. ST-i 52 800-A Figure 3-10. Shielding Gas And Weld Cable Connections OM-1586 Page 7 Removing Safety 3-9. Collar And Adjusting Boom WARNING A~ FALLING RELEASE OF SPRING PRESSURE WITHOUT BOOM ATTACHED can cause serious personal Injury. Do not remove BOOM can cause serious personal Injury and equIpment damage. Adjustment yoke. safety collar until instructed to do so. rod must be threaded Locking 1 fully through Knob knob to prevent boom movement. Loosen knob to allow boom movement Change knob position to limit upward movement. Tighten 3 Pull boom down slightly and re safety collar. Boom should balance in any position from hori zontal to 60 degrees above hori zontal. If necessary, adjust boom as follows: move 2 Threaded Rod 3 Jam Nut Loosen jam nut and turn threaded rod until boom balances. Tighten jam nut Be sure several full threads are through yoke to pre vent boom falling. Tools Needed: ~ -,~ 1-1/8 in. 4 E safety collar for use in assembling or moving boom. FIgure 3-10. A. WeldIng Yoke Retain Increasing Spring Decreasing Spring Pressure ForA Heavy Gun Pressure For A Light Gun 3-11. Boom dis Ref. ST-I 52380 Adjustments Wire Installation installation Of Spool-Type Wire 1 Retaining Ring 2 WureSpool 3 Hub Remove spool 4 retaining ring and slide onto hub. Hub Pin Turn spool until hub pin fits hole in spool. Reinstall retaining ring. 2 E ST.152 FIgure OM-1586 Page 8 3.12. InstallatIon Of Spool-Type Wire B. installation Of Optional Wire Reel And Reel Type Wire 6 7 1 Retaining Ring 2 Spanner Nut 3 Wire Retainer 4 WireReel 5 Hub 6 Hub Pin 7 Reel Support Remove retaining ring and wire reel assembly (wire reel, wire re tainer, and spanner nut) from hub. 8 Wire Installation 4 Lay wire reel assembly on face, and install wire as flat sur shown. Slide wire reel assembly onto hub, and turn assembly until hub pin is seated in hole in reel. Reinstall re taining ring. 3 2 /Da fflj ac~ ST.143 478/ ST.152 483 Figure 3-13. Installation Of Optlonai C. Adjusting Wire Reel And Reel Type Wire Hub Tension Turn OFF unit and welding power source. 1 Hex Nut 2 Spool Grasp spool in one hand and turn while using a wrenth to adjust hex nut. When a slight force is needed to turn spool, tension is set. 2 E Tools Needed: 5/8 in. ST.152 649 Figure 3-14. AdjustIng Hub Tension OM-1 586 Page 9 3-11. Motor Start Control WARNING a ELECTRIC SHOCK can kill. Do not touch live electiical parts. Turn OFF wire feeder and welding power source, and disconnect input power before inspecting or STATIC ELECTRICITY circuit boards. can damage parts on Put on boards grounded wrist sUap BEFORE handling or parts. installing. wfwaml.V ~91 To change wire feed starting speed proceed as follows: Turn OFF unit and welding power source. Remove wrapper. 1 Front Panel Remove screw from upper left cor ner, and open hinged front panel. 2 MotorBoard PCi 3 Motor Start Control Poten tionieter R70 Rotate potentiometer clockwise to increase time it takes the motor to ramp up to speed. Remove protec tive white rubber cap before 2 making adjustment. Adjust poten tiometer R70 using a small conductive screwdriver. Close and se~ire front reinstall wrapper. panel, non- and Tools Needed: 1/4 in. ST-1574~O/ R&. SB-148 862 Figure OM-1586 Page 10 3-15. Motor Start Control On Motor Control Board PCi 3-12. Threading Welding A~ Wire WARNING CYLINDERS can explode Keep cylinders away from If WELDING WIRE wounds. damaged. welding and other can cause puncture electrical circuits. Do not press gun cylinder with welding electrode. Always secure cylinder to running gear, wall, other stationary support. point gun toward any part of the body, other people, or any metal when threading welding wire. Never touch ELECTRIC SHOCK can trigger until instructed to do so. Do not or kill. HOT SURFACES can burn skIn. Do not touch live electrical parts. Allow gun to cool before The welding wire, drive rolls, drive assembly, and all metal parts touching the welding wire are electrically live when welding or feeding wire using gun Uigger. touching. wfwarn2.l Fwfwam7.~ 9f9i 1 Wire Spool/Reel Loosen wire from spooVreel, cut off bent wire, and pull 6 in. (150 mm) of wire off spooVreel. 2 Wire Tube Manually feed wire through tube, over pulley and into monocoil liner at wire inlet guide. 3 Wire Guides 4 Drive Rolls Manually feed wire through wire guide(s), up to drive rolls. Turn wire feeder and welding pow er source ON (see Figure 5-9), and OUTPUT/CONTACTOR place switch on welding power source in REMOTE position, if applicable. 2 5 Jog Button 6 Gun Condeit Cable Lay gun condeit cable out straight. Press JOG button to feed welding wire. Apply enough hand pressure to wire to allow drive rolls to grab 3 wire to start jogging. Release switch when approximately 1 in. (25 mm) of wire extends out end of 4 gun. 6 7 Knob 7 Pressure 8 Drive Roll Pressure Indicator Scale 9 Adjusting Pressure A~ustment Check drive roll pressure by feed ing wire against a wood board or concrete surface; wire should feed steadily without slipping. Increase drive roll pressure by turning pres sure ac~ustment knob clodwise. The drive roll pressure indicator scale is for reference only. Tools Needed: ST-157432/ST-153o73/ R~. S.0627-AI Re4. SC-150 922 Figure 3-16. ThreadIng Welding Wire OM-1586 Page 11 SECTION 4 The following is a list of terms and their definitions as GLOSSARY they apply to this wire feeder: General Terms Adaptive Pulse When the adaptive pulse welding process is selected, the unit will automatically ad just pulse frequency in order to maintain a constant arc length, regardless of change in welding wire stickout. Background Current Typically Is the electrical influence exerted Inductance field, on adjacent Pulses Per Second Number of peak current Pulse Width in a of the two current levels in the Typically (PPS the by current flow conductor, through a magnetic conductors. Peak Current Or Pulse pulsing waveform. the lower of the two current levels in the higher pulses which pulsing waveform. in one second of time. occur Frequency) (Or Peak Time) Duration of the peak current level. Term used to represent arc Trim length in pulse programs. Trim is replaced by volts in MIG programs. Synergic refers to the units ability to use preprogrammed pulse parameters in order pulse settings of Peak Amperage, Background Amperage, Pulse Frequency and Pulse Width at any specific wire feed speed setting. Synergic to determine the actual Front Panel Terms Display Control Knob Digital Display Gas Purge Control Parameter Select Button Trigger Wire Hold Control Jog Control Is used for all 2-line adjustable front panel displays. by 16-character liquid crystal display Allows the gas line and gun to be Is used to select a variety purged with built-in LED without of parameters that When selected, allows the system to remain to hold the gun trigger. can energizing be set on backlight. the wire feeder. the front panel display. energized without the operator having Allows the wire to feed without gas valve. The wire on the front panel. energizing the welding power source contactor and jog is independent from actual wire feed speed, and is displayed Side Panel Terms Digital Display 4-line Dual Schedule Allows two weld programs to be linked together when two different tions (i.e. hotter and colder) are required on one wire. Process Mode Is used to select the type of process to be used, Mig. OM-1586 Page 12 by 20-character liquid crystal display with built-in LED backlight. welding condi including Pulse, Adaptive Pulse, or Remote Parameter When Increase/Decrease decrease Sequence Allows this feature is turned on, Mode operator use can of the remotely increase and optional DSS-10 2-pole a variety of sequences to be used within a weld program if required. Se quences include, preflow gas control from 0 to 9.9 seconds, run-in control of voltage or trim and wire feed speed from 0 to 2.5 seconds, weld time from 0 to 25 seconds, crater control of voltage or trim and wire feed time from 0 to 0.25 seconds, and Security/Set-Up the selected weld parameter with the momentary-contact switch. a speed from 0 to 2.5 seconds, burnback postflow gas control from 0 to 9.9 seconds. Screen Terms Access Mode A three-letter code can be programmed in the access mode which will restrict unau thorized personnel from changing any of the security/set-up screens. NOTE: The optional Data Card is required to activate this feature. Arc Time Dual Schedule Allows actual arc mulated and displayed time up to 9,999.99 hours and weld cycles up to 999,999 to be accu on the digital display, and can be reset to zero as required. Is used to select the type of dual schedule switch that will be used when the dual schedule feature is selected. Memory Reset By selecting yes in the memory reset mode, the unit will default to original factory pro gram settings. Name Feature When using the optional Data Card programs written to the card Security can and turning be identified by the name feature on, customized name, number, job number, etc. Is used to limit what the operator can control. This includes the number of programs 1 through 8, and also the range of welding parameters. NOTE: The option available, al Data Card is required to activate this feature. Software Screen Selection of this function will Trigger Program Select Allows programs to be selected Self Test Mode A built-in diagnostic feature to check a variety of wire feeder and power source func tions if a malfunction Allows a choice of two methods of display the software version of the unit. remotely with the gun trigger. occurs. Voltage Control Feedback lected sensing voltage for regulation. This can be se the through 17-pin cord connection to the Maxtron 450 which monitors voltage at the output terminals, or the selection of an external voltage sense lead. Voltage Sense Shutdown When this feature is on, the system will immediately shutdown if no upon gun trigger actuation. When this feature is off, the system (wire arc is initiated feeder), when actuated by the gun trigger, will feed wire for approximately three seconds at set welding speed and then automatically switch to cold wire jog speed for approximately one minute. The off feature is normally selected to allow threading wire with the gun trigger. Wire Feed Mode Allows the selection of inches per minute or meters per minute for wire feed speed. This mode is also used to select motor type; standard speed, low speed, or high speed. High and low speed motors are available as factory options. OM-1586 Page 13 OPERATION SECTION 5 WARNING a ELECTRIC SHOCK Always Insulate wear kill. can Do not touch live electrical p parts. ~ dry insulating gloves. yourself from work and Keep all panels and covers FUMES AND GASES ARC RAYS can burn eyes and skin; NOISE can damage hearing. Wear ~ ground. securely in place be hazardous Keep or use breathing device. can cause fire or on Allow work and Injury. over drive rolls. as covers, and guards closed MAGNETIC FIELDS FROM HIGH CUR RENTS can affect pacemaker operation. Pacemaker =9. keep extinguisher nearby. Do not locate unit I explosion. Do not weld near flammable material. Do not weld can cause Keep all doors, panels, and securely in place. Read Material Safety Data Sheets (MSDS5) and manufacturers instructions for material used. Watch for fire; body protection. Keep away from pinch points such your head out of the fumes. WELDING helmet with correct shade of filter. MOVING PARTS can to your health. Ventilate area, welding Wear correct eye, ear, and keep away. wearers Wearers should consult their doctor before ~. near any going welding operations. combustible surfaces. closed containers. equipment to cool before 1 See Safety Precautions at beginning of manual for ba sic welding safety information. ~am3.l 10191 handling. 3 2 / ~~ 1 Insulating 2 Safety Glasses With Side Shields 3 Welding Gloves Helmet Wear dry insulating gloves, safety glasses with side shields, and a welding helmet with a correct shade of filter (see ANSI Z49.1). sb3.l 10/91 Figure 5 -1. Safety Equipment 1 Work Clamp Use wire brush or clean metal at weld sandpaper joint area. Connect work clamp to a to clean, paint-free Tools Needed: as location on workpiece, close to weld area as possible. 2 Voltage Sensing Clamp Connect to workpiece, (see Figure 3-10). Use slag Fig ure 5-1. 5-2. Work And if chipping hammer welding. R&. after applicable to remove ST-158 931-A Voltage Sensing Clamps Front Panel Controls 1 :J,I_ ......_______ 6 0 3 ~: Display 2 Parameter Select Button 3 Jog 4 Display Control 5 Trigger Hold cator Light 6 Purge Button Knob Button And Indi Button See Section 6 for information using microprocessor controls. on Ref. ST-155 222 Figure 5-3. Front Panel Controls OM-1586 Page 14 Parameter Select Button 1 Press button to move indicator> on display. Ref. ST.153 976 Figure 5-4. Parameter Select Button Display Control 1 Turning knob Knob changes value se lected. Spin knob to quickly change pa by clicks to rameters or move knob fine tune parameters. Figure 5-5. Display Control Knob 1 ,~- PURGE Jog Push Button Push to JOG momentarily feed welding energizing welding cir shielding gas valve. wire without ~ 030 cuit or Jog speed is varied using the DIS PLAY CONTROL knob while JOG button is pressed. Default setting is 200 7,__o N 2 1pm. When JOG button is released, unit displays preset wire feed speed, and previously selected parameter is active. 1 ~ JOG does not work when gun ger is pulled. Jog 2 15. OV Prg -a >200 I PM Jog Purge >1 5 . 260 OV I Prg PM MIG justing 5-6. shielding gas regulator energizing the welding Front panel controls, side panel controls, and gun trigger do not work when JOG or PURGE button is Figure Push Button Push to momentarily energize gas valve. This allows purging of air from gun shielding gas line, and ad without circuit. Jog trig pressed. Jog And Purge Buttons OM-1 586 Page 15 I Trigger 2 Indicator Hold Button Light To weld without throughout holding gun trigger cycle, press and weld release button to turn 2 on indicator light. To start weld cycle, and feed weld. ing wire, press and release gun trigger within the first three sec onds after an arc has been struck. If gun tri~9er is not released within the first three seconds after arc ini tiation, trigger hold stops, but is still active for next weld weld cycle, trigger. cycle. To end press and release gun Trigger hold can not be started while gun trigger is pressed. Figure 5-2. Trigger 5-7. Hold Button Side Panel Controls o~ \ / \ 5 \ 4 Figure 5-3. Parameter Increase Button Parameter Decrease Button 3 Parameter 4 Parameter Select Button 5 Mode Select Button 6 Mode Display Display See Section 6 for information using microprocessor controls. /9 9\~ 6 1 2 on \ 3 Ref. ST-I 55 223-A 2 5-8. Side Panel Controls Rear Panel Controls 1 2 Power Switch Use power switch to tum unit ON and OFF. 2 CIrcuit Breaker (See Section 14-3) Ref. ST-I56 931-A Figure OM.1586 Page 16 5-9. Power Switch WARNING a BUILDUP OF SHIELDING GAS harm health can Shut off shielding gas supply when not in or kill. use. w~m1I QIgl 1 Shielding Gas Cylinder 2 Valve 3 Gun Trigger Open valve welding. on cylinder just before Gun trigger turns weld Output and gas flow on and off. 3 Close valve on cylinder when fin ished welding. sb5.1 0/82 Figure H IGH FREQUENCY will Turn off high frequency Completely Install & J damage when using ) Gas this unit. this unit. disconnect this unit from power source when Connect Wire Feeder Shielding CAUTION a S 5-10. 5-0821.C D)(See System Figure 3-1O)JJ Do ~ Readjust Install Sample Weld FIgure Welding ) ) J) ) 1 using high frequency. Put On Personal Safety Equipment Set All 4-12)) Turn On ) ) Controls JJ ( Figure Shieldi~\ Gas (If Applicable) )~Source 1 Turn On Wire Feeder And Control~\ And Prepare For Production J 5-11. Gas Metal Arc (GMAW), Gas Metal Arc Pulse (GMAW-P), Welding (FCAW) - And Flux Cored Arc 0 ~jii NC CC/~ Ret ST-150 Ill-B / Ref. SC-I45 332-0 Figure 5-12. Setting Switches On Welding Power Source OM-1586 Page 17 SECTION 6 STEPPING THROUGH THE MICROPROCESSOR CONTROLS WARNING 4~ ELECTRIC SHOCK can WELDING WIRE can cause puncture wounds. kill. Do not touch live electhcal parts. Do not point gun towards any part of the body, other people, or any metal when programming. The welding wire is electrically live and moves out of Control circuit and feeder operationai power are ON when using or changing the microprocessor settings. the gun whenever the power switch is ON and the gun thgger is pressed. NOTE 6-1. This unit is equipped with eight (8) pulse welding programs (see Section 7). When the unit is turned ON for the first time program I comes up, therefore, program 1 is illustrated throughout this manuaL Instructions are given later in this manual on how to select or change a program. Front Panel Micr oprocessor Controls Turn ON welding power source and wire feeder. Follow along with the controls as shown. 1 Front Panel 2 Parameter Select Button Display Press parameter select button to indicator>. move The indicator> points to parame ters that are selected for change. Parameter select button can move indicator > between Trim (arc length) and 1PM while welding. Go to 150 120 Trim 0 >50 1PM >200 Pulse Tr im Prg I PM Pulse Tr im Prg I PM Pulse 200 50 >Prg Figure 6-2. ii 1 1 ST-155 222 Figure OM-1586 Page 18 6-1. Front Panel Parameter Select Button 1 Front Panel Display Select parameter (see Figure 6-1). 2 Display to be changed Control Knob one dick causes the Turning following changes to selected set ting: knob Trim 2 (arc length) increases/de creases by one. The trim (arc changed also length) value being changes on the side panel parameter display (see Figure 8-3). Wire feed speed (1PM) increases/ decreases by one inch per minute. >50 200 Trim 1PM The wire feed speed value being changed also changes on the side panel parameter display (see Figure 8-3). Prg Pulse Program number (Prg #) increa ses/decreases by one. The number being program changed also changes on the side panel parameter display (see Section 11). >55 200 Trim 1PM The program number can not be changed while welding, with ex caption of Dual Schedule Mode (see Section 11). Prg Pulse DISPLAY CONTROL knob can be used to set JOG speed when JOG button is pressed (see Figure 5-6). (C) Front Panel Q 55 >200 Trim 1PM Trim k300 1PM Parameter Select Go to Figure 6-3. Prg Pulse Prg Pulse Front Panel Parameter Select I 55 300 50 200 Trim 1PM Trim 1PM >Prg Pulse >Prg Put 2 se ST-155 ~ FIgure 6-2. Front Panel Display Control Knob OM-1586 Page 19 6-2. Side Panel Microprocessor Push Buttons 1 Mode 2 Mode Select Button Display Press Mode button to tor> in left window Go to Figure move indica display. 6-4. Side Panel Process >S e q u e n c e Dual Schd Ca r d Process Sequence >D u a Ca r I S c h d d Process Sequence L Dual Schd >C a r d Ref. ST-154 109 Figure OM-1586 Page 20 6-3. SIde Panel Mode Select Button I~ I Parameter 2 Moving Moving line is be changed. 3 Display Line under value that can Side Panel Parameter Select Button Press side panel parameter select button to move indicator> in right window Go to display. Figure 6-5. Side Panel 1 2 Prg ~ 1 035Steel 98Ar 2oxy Pulse 035Steel 98Ar 2oxy >Teach OH Ref. ST-154 109 Figure 6-4. Side Panel Parameter Select Button OM-1586 Page 21 panel mode select button mode to be changed (see Figure 6-3). Use side to select> Use side panel parameter button to select> select parameter to be changed (see Figure 6-4). I IIJ 1 Increase Button Press button to increase value that is underlined by the moving line. c~c~9 2 Decrease Button Press button to decrease value that is underlined by the moving line. Side Panel 2 Re4. ST-154 109 FIgure 6-5. Side Panel Parameter Increase And Decrease Buttons SECTION 7- STANDARD PULSE WELDING PROGRAMS following eight (8) pulse welding programs are in the memory of the wire feeder. Use these programs if it is neces sary to customize a standard program, or as a basis to build yourown custom program. If at any time while customizing a standard program, orwhile building your own custom program, you want to return to the standard program in the wire feeder memory, see Section 13-9, Resetting Memory. NOTE: Resetting the memory erases all customized pro grams and returns them to the appropriate standard factory-set pulse welding programs. Two model types of factory programs exIst, see SectIon 13-15 for model type settIngs. The OM-1586 Page 22 Program Wire Program #1 Program Name: .035 Size/Type: .035 1 Gas: 98 Ar 2 S-3 Card #_______________________ Steel, 98 Ar- 2 oxy Flowrate: Gun Model: MILLER GW 1PM ApK AbK PPS PWms 750 560 115 180 2.0 700 550 110 175 2.0 650 540 105 170 2.0 600 520 100 165 2.0 550 510 95 160 1.9 500 480 90 150 1.9 450 460 85 140 1.9 400 440 80 130 1.9 350 420 75 120 1.8 300 400 70 110 1.8 250 380 65 90 1.8 200 360 60 80 1.7 150 350 55 60 1.7 100 340 45 40 1.7 50 330 30 30 1.6 Preflow: COMMENTS Sec. Run-in Thm: 1PM: Crater Trim: 1PM: Postfiow: oxy Sec. OM-1586 Page 23 Program WIre Program #2 Program Name: .045 Size/Type: .045 2 Gas: 95 Ar 5 S-3 Card #_______________________ Steel, 95 Ar -5 oxy Fiowrate: 40 CFM Gun Model: MILLER GW 1PM ApK AbK PPS PWms 750 560 140 230 3.0 700 560 130 230 2.9 650 560 120 220 2.8 600 550 115 210 2.7 550 550 105 200 2.6 500 540 100 190 2.5 450 530 90 180 2.4 400 520 90 170 2.4 350 510 80 160 2.4 300 490 80 150 2.3 250 470 70 130 2.3 200 440 70 110 2.2 150 410 60 90 2.2 100 380 40 70 2.1 50 330 30 50 1.9 Preflow: Sec. Run-in Trim: 1PM: Crater Trim: 1PM: Postf low: OM-1586 Page Sec. 24 oxy COMMENTS . Program WIre Program #3 Program Name: .052 Size/Type: .052 3 Gas: 95 Ar 5 S-3 Card #_______________________ Steel, 95 Ar -5 oxy Flowrate: Gun Model: MILLER GW 1PM ApK AbK PPS PWms 750 560 145 250 3.0 700 560 145 250 3.0 650 560 145 240 3.0 600 560 145 230 2.9 550 560 135 220 2.8 500 560 125 200 2.7 450 550 120 190 2.7 400 540 115 180 2.6 350 530 100 170 2.5 300 520 90 160 2.4 250 510 80 140 2.4 200 490 70 120 2.3 150 460 60 100 2.3 100 430 45 80 2.2 50 370 30 50 2.2 Prefiow: COMMENTS Sec. Run-In Trim: 1PM: Crater Trim: 1PM: Postflow: oxy Sec. OM-1586 Page 25 Program WIre Program #4 Program Name: .035 Size/Type: 309 L, 98 Ar 2 .035 4 Gas: 98 Ar 2 308 L Card #_______________________ oxy Gun Model: MILLER GW Flowrate: 35 CFM 1PM ApK AbK PPS PWms 750 420 100 140 2.1 700 410 100 140 2.0 650 400 90 140 2.0 600 390 90 130 2.0 550 380 90 130 1.9 500 370 80 120 1.9 450 360 80 110 1.9 400 350 70 100 1.9 350 330 70 90 1.8 300 310 70 80 1.8 250 290 60 70 1.8 200 270 60 60 1.7 150 250 50 50 1.7 100 240 35 40 1.7 50 220 20 30 1.6 Preflow: Sec. Run-In Trim: 1PM: Crater Trim: 1PM: Postf low: OM-1586 Page Sec. 26 oxy COMMENTS Program Wire Program #5 Program Name: .045 Size/Type: .045 5 Gas: 98 Ar 2 309 L Card #_______________________ Steel, 309 L, 98 Ar -2 oxy Flowrate: 35 CFM Gun Model: MILLER GW 1PM ApK AbK PPS PWms 750 530 145 180 3.0 700 520 145 170 2.9 650 510 140 160 2.8 600 500 135 150 2.7 550 490 130 150 2.6 500 480 125 140 2.6 450 470 120 130 2.5 400 460 115 120 2.4 350 440 110 110 2.4 300 420 100 100 2.3 250 400 90 90 2.2 200 380 80 80 2.2 150 350 70 70 2.2 100 320 50 60 2.1 50 280 30 40 1.9 Preflow: COMMENTS Sec. Run-In Trim: 1PM: Crater Trim: 1PM: Postflow: oxy Sec. OM-1586 Page 27 Program WIre Program #6 Program Name: 3/64 Size/Type: 3/64 6 Gas: 4043 Card #_______________________ 4043, Argon Fiowrate: 40 CFM Gun Model: MILLER GW 1PM ApK AbK PPS PWms 750 560 145 200 3.0 700 550 145 190 2.9 650 540 145 180 2.8 600 510 145 170 2.8 550 480 145 160 2.7 500 460 135 160 2.6 450 440 130 150 2.6 400 400 120 140 2.6 350 360 110 130 2.5 300 320 100 120 2.4 250 280 85 110 2.3 200 250 65 100 2.2 150 220 50 90 2.2 100 200 32 80 2.1 50 160 20 50 2.0 Pref low: Sec. Run-In Trim: 1PM: Crater Trim: 1PM: Postflow: OM-1586 Page Sec. 28 Argon COMMENTS Program Wire Program #7 Program Name: 3/64 Size/Type: 3/64 7 Gas: Argon 5356 Card #_______________________ 5356 1PM ApK AbK PPS PWms 750 510 140 180 3.0 700 500 140 180 2.9 650 490 130 170 2.8 600 470 125 170 2.7 550 450 115 160 2.7 500 430 105 150 2.6 450 410 95 140 2.6 400 390 85 130 2.5 350 370 75 120 2.4 300 350 60 110 2.3 250 330 48 100 2.2 200 300 43 90 2.1 150 280 32 80 2.0 100 260 17 65 2.0 50 230 15 40 1.9 Pref low: COMMENTS Sec. Run-In Trim: 1PM: Crater Trim: 1PM: Postf low: CFM Flowrate: Gun Model: MILLER GW Sec. OM-1586 Page 29 Program Wire Program # 8 Program Name: .045 Size/Type: .045 8 NI3Cr Gas: Ar-25He Or Argon NI3Cr Card #________________________ Flowrate: 35 CFM Gun Model: MILLER GW 1PM ApK AbK PPS PWms 750 470 120 150 4.1 700 460 115 140 4.0 650 450 110 135 4.0 600 440 110 130 3.9 550 430 100 125 3.9 500 420 90 120 3.9 450 410 80 115 3.8 400 400 70 110 3.7 350 390 65 105 3.6 300 380 60 100 3.5 250 360 55 90 3.4 200 340 45 80 3.3 150 320 35 70 3.2 100 300 30 60 3.1 50 260 20 40 2.9 Sec. Preflow: Run-In Trim: 1PM: Crater Trim: 1PM: Sec. Postflow: OM-1586 Page 30 COMMENTS SECTION 8- GETTING STARTED WARNING a ELECTRIC SHOCK can Do not touch live electrical Always wear Insulate kill. p parts. ~ dry insulating gloves. yourself from work and and all panels Keep FUMES AND GASES to your health. covers ground. ,.:. or use Read Material Safety WELDING securely place be hazardous can near Watch for fire; Do not weld on Allow work and ~ fire body protection. or can cause Keep away from pinch points Keep all doors, panels, and securely in place. I \ explosion. flammable material. over helmet with correct shade of filter. MOVING PARTS 0 device. keep extinguisher nearby. Do not locate unit N OTE breathing can cause Do not weld welding in Data Sheets (MSDS5) and instructions for material used. manufacturers Wear Wear correct eye, ear, and Keep your head out of the fumes. Ventilate area, ARC RAYS can burn eyes and skin; NOISE can damage hearing. i. injury. such covers, and as drive rolls. guards closed MAGNETIC FIELDS FROM HIGH CUR RENTS can affect pacemaker operation. Pacemaker wearers keep away. Wearers should consult their doctor before near any going welding operations. combustible surfaces. closed containers. equipment to cool before handling. See Safety Precautions at beginning of manual for ba sic welding safety information. wfwam3.l 10/91 Set up equipment according to Figure 5-11. Find the standard pulse welding program in Section 7 that is closest to your application (by wire size and type and gas type), and use these when setting up. OM.1586 Page 31 8-1. Welding With Only Front Panel Controls Turn ON welding power source, wire feeder, and gas. I Front Panel Display Program 5 0 Tr im I PM >Prg 1 is the default program the first time the unit is turned on, 1 at other times the 200 last program number selected is displayed. Use the front panel parameter select button to select> the Prg #. Pulse 2 2 Prg3 Select the weld program from Section 7 (1 through 8) which is closest to your needs (by wire and gas). Tr 5 0 200 I im PM >Prg Strike 3 Pulsel an arc Trim and try a sample weld. (Arc Length) If necessary, select> Trim, and ad to achieve the best arc. just U 4 Front Panel Mode Select 1PM If necessary, select> 1PM, and ad just to achieve the best arc. Go to Section 8-2. Trim >50 200 1PM Prg 3 Pulse Display Control 3 I> Trim 55 200 1PM U 55 Trim >200 1PM Trim 55 >2 5 0 1PM Prg 3 Pulse Front Panel Mode Select Prg 3 Pulse Prg 3 Pulse / Figure OM-1586 Page 32 8-1. WeldIng With Only Front Panel Controls 8-2. Pulse Setting Sequence Welding Parameters On Side Panel Display WARNING a ELECTRIC SHOCK can Do not touch live electrical WELDING WIRE kill. can cause puncture wounds. parts. Do not point gun towards any part of the body, other people, or any metal when programming. The welding wire is electrically live and moves out of Control circuit and feeder operational power are ON when using or changing the microprocessor settings. the gun whenever the power switch is ON and the gun trigger is pressed. NOTE ~ ] Figure 8-2 is a graphic layout of a weld cycle. Follow examples in Figure through Figure 8-8 to adjust sequence welding parameters to fit your needs. 8-3 Weld Time 0.25 Sec. Run-In Time 0-2.5 Sec. a) a) a. Run-In Speed ~ I I I Preflow Time 0-9.9 Sec.~ Trigger Arc Start Crater Time 0-2.5 Sec. / Bumback Time 0-0.25 Sec. / a) Posthow Time 0-9.9 /~ I Li Arc Trigger Sec.~ 0~ Time Out Released Pressed Rłt. S-0271 FIgure 8-2. Weld Cycle OM-1 586 Page 33 I Side Panel Mode Select Button When unit is turned ON, Process is the default mode, at other times, use side panel mode select button to select> 2 Sequence. Side Panel Parameter Select Button Use side panel parameter select button to select > parameters. 3 Process >Sequence Parameter ranges >W~ld 50. Weld Parameters Trim DualSchd 250 1PM Card 0.0 Sec Trim follows: (Arc Length), 0-99 Changes are Display are as also to Weld displayed Sequence Trim on front panel display. Wire Feed Speed, 50-780 Inches Per Minute, 1PM Changes are Set Desired Weld Go to Figure 8-4. Weld Trim >50 Trim be fine tuned while welding, see Figure 6-2. can 200 1PM 0.0 Sec ~ Set Desired Weld Sequence Wire Feed Speed Side Panel Parameter Select We I d ~orQ~j Increase/ Decrease 60 Trim >200 1PM 0.0 Sec 1PM can be fine tuned while see welding, Figure 6-2. ~J Side Panel Parameter Select Set Desired Weld Sequence Weld Time, If Applicable We I d 60 Trim 300 1PM >0.0 Sec Increase/ Decrease Side Panel Parameter Select Proceedtonextflgure. We I d ~ 60 Trim 300 1PM >3.5 Sec Increase FIgure OM-1586 Page 34 8-3. SettIng Sequence 1PM on front panel Seconds, 0-25.0 Sec. I lncrease/ to Weld displayed display. Sequence Voltage Decrease also Weld Sequence Display 1 Crater Parameters Parameter ranges Trim Display are as follows: (Arc Length), 0-99 Wire Feed Speed, 50-780 Inches Per Minute, 1PM Seconds, 0-2.5 Sec. If value zero Set Desired Trim Set Desired Wire Feed (O),no Crater sequence formed. Speed Go to Increase! Trim ~ Sec 0.20 8-5. Side Panel Parameter Select Proceed to next TrimLJ 60 1PM 150 Figure Crater £ a I ~ 60 ~ Increase! Decrease Decrease set is is per Side Panel Parameter Select figure. 150 1PM >Q~QQ Sec Set Desired Crater Time Increase Increase! Decrease Figure 8-4. Setting Crater Sequence Display I 1 >~utnba~K Burnback >a u £ fl D a C k Burnback Parameters Burnback can be 0-0.25 seconds. Display adjusted from GotoFigure8-6. 000 Sec Sec Side Panel Parameter Select Set Desired Burnback Time 0.12 Side Panel Parameter Select Sec Proceed to next figure. Increase Increase! Decrease Figure 8-5. Setting Burnback Sequence Display 1 >EQaIf!Qw 1 Postflow >EQa if I Q~ Poetfiow Parameters Postflow can be 0-9.9seconds. Display adjusted from GotoFigure8-7. ~_0.0 Sec Sec Side Panel Parameter Select Set Desired Postflow Time 1.2 Side Panel Parameter Select Sec Proceed to next figure. (~ Increase! Decrease Figure 8-6. Setting Increase Postfiow Sequence Display OM-1586 Page 35 Preflow Parameters 1 Preflow can be Display adjusted from 0.9.9 seconds. Go to Figure 8-8. __/ Pr e f >~rQf!Q~ 0.0 I f I __H!H__ ow Sec >Q~Q Sec Side Panel a 1.2 Side Panel Parameter Select Set Desired Preflow Time Parameter Select Q~ Sec Proceed to next figure. Increase lncrease/ Decrease Figure 8-7. Setting Preflow Sequence Display 1 Run-In Parameters Parameter ranges Display are as follows: Trim, 0-99. Wire Feed Speed, 50-780 inches per minute, 1PM Seconds, 0-2.5 Sec. If value set is (0), no Run-In sequence is performed. zero >B t~ 0 50. 0 Trim 200 1PM 0.0 Sec ~nin >~Q ~ Side Panel Parameter Select I ~ Trim1 200 1PM 0.0 Sec ~ Side Panel Parameter Select Set Desired Trim Runin Trim1 55 >ZQQ 1PM 0.0 Sec Set Desired Wire Feed Speed lncrease/ Decrease lncrease/ Decrease I >Bunin Runin 150 Triml 1PM ~ 1 Sec 55 .1 ~ ~ Side Panel Parameter Select Trim 150 1PM I>~~ Sec Set Desired Run-In Time lncrease/ Decrease Figure OM-1586 Page 36 8-8. SettIng Run-In Sequence Display ?~ Side Panel Parameter Select SECTION 9- TEACHING A PULSE WELDING PROGRAM WARNING A ELECTRIC SHOCK can Do not touch live electrical WELDING WIRE wounds. kill. parts. can cause puncture Do not point gun towards any part of the body, other people, or any metal when programming. The welding wire is electrically live and moves out of Control circuit and feeder operational power are ON using or changing the microprocessor when settings. the gun whenever the power switch is ON and the gun trigger is pressed. NOTE ~ See GMAW-P (Pulsed MIG) Process Guide supplied with unit for more information. ______________________ 9-1. Pulse Waveform Explained The wire feeder, not the welding power source, controls weld output for pulsed welds. Peak Current Of ApK 1 150-565 ApK Amperes is the high pulse of welding Peak current melts the welding wire and forms a droplet. The droplet is forced into the weld current. puddle. 2 AbK Background Current Of 10-150 Amperes AbK is the low weld current. Back ground current preheats welding wire and maintains the background When low, the Is unstable and hard to main arc C arc. current Is too tain. a) PPS Pulses Per Second Of 30-400 3 C) U, 0. E 1 2 e * PPS, pulse rate, and frequency -~ (Hz) are PPS or 60 Time used interchangeably. A pulse rate of 60 Hz means pulses of current are produced each second. 4 PWms Pulse Width Of 1.0-5.0 Milliseconds PWms is the time spent at peak (1.2 ms is .0012 seconds). This time must be long enough to form a droplet of welding wire. The stiffness or fluidity of the molten weld puddle is controlled by PWms. current R&. S-0259 Figure 9-1. Pulse Waveforms And Explanation Of Terms OM-1 586 Page 37 Teach Points 9-2. Explained 1PM 780 750 700 650 600 550 500 Example Of A Synergic Setting 450 For 425 1PM 400 350 300 250 200 ~ Apk o Abk o Pps 150 100 Pwms 50 150 180 210 240 270 300 330 360 370 420 450 480 510 540 565 Apk 10 20 30 40 50 60 70 80 90 100 110 120 130 140 150 Abk 30 55 80 105 130 160 185 210 235 260 290 315 340 365 400 Pps 1 2 The teach mode allows the custom user to create pulse MIG welding programs. The teach mode has 15 teach points. At each point, the user can adjust four parame ters: peak amperage (ApK), background amperage (AbK), pulses per second (PPS), and pulse width in milliseconds (PWms) to shape the pulse waveform of the weld out put. Each teach point corresponds to a wire feed speed. The wire feed speeds (ipm) teach range between 50 and 750 inches per min ute, are set at fifty inch increments, and specific characteristics suitable for certain joints and/or shielding gas mixtures. create Once the parameters have been setfor all 15 teach points, the unit will adjust the four pa rameters for any wire feed speed beiween the minimum and maximum teach points. Pulse MIG programs made Page 38 Figure OM-1586 by 9-2. MILLER 3 4 ELECTRIC have pulse waveform intormation entered for all 15 teach points. The oper. ator can modify the setting of one, or any number of the 15 teach points if the factory set information is not appropriate for a specific application, 5 Pwms Trim, increases the actual arc length. Like wise, decreasing the value of Trim will de crease actual arc length. lnthePulsemode,theunitdoesnotmaintain length with variations in elec Adaptive Pulse mode, the unit adjusts pulse frequency to maintain a constant arc length regardless of vana a constant arc trical stick-out. In the After the parameters at any teach point(s) are established, the arc must be struck and maintained for at least 5 seconds. This allows the wire feeder to learn the arc voltage tions in electrical stick-out. associated with the When ters. To ensure a proper arc electrical stick-out must be feed taught pulse paramelength reading, carefully maintamed, and the weld must be terminated by releasing the gun trigger, not by pulling the welding gun away from the work piece. The taught arc length represents a Trim (arc length) setting of 50. Increasing the value of Typical Teach Point Settings And using pulse MIG programs, any wire speed from 50 to 750 inches per minute at one ipm increments, can be selected. Be yond 750 ipm, the unit limits wire feed speed settings in pulse MIG to maintain all pulse parameters within the capability of the unit. Proceed to next figure to teach a program. Resulting Synergic Setting pulse MIG 035Steel Teaching 9-3. A Pulse Welding Program READ SAFETY BLOCKS at start of Section 9 before proceeding. >P r Prg 0 C e S S Pulse 1_ Pulse Dual Schd 035Steel Card 98Ar 98Ar 2oxy >Teach 2oxy Qff Side Panel Parameter Select Side Panel Mode Select 450 >~4~ 70 I 320 Apk 70 Abk ~J lncrease/ Decrease Decrease I I 1PM ?ncrease/ Decrease I ncrease/ Teach Q~ 400 ~>Teach 035Steel Sequence ~ Apk1L_or_]>a4g On Teach 1PM Abk 70 \Teach I>4~Q On On 1PM 1PM 450 1 Apk 340 70 Abk ApK L_0r Teach AbK On >4QQ 1PM 340 Apk 70 Abk Side Panel Parameter Select I I __________ __________ __________ SidePanel Parameter Select ~~Side U Panel Parameter Select i_~J I ncrease/ Decrease 1PM 343 Apk ZQ Abk ~ 160 PPS 1.9 PWms 343 Apk 92 Abk 280 PPS 343 Or > Pulse ] El 035steel 98Ar2oxy~ >Teach ~ 92 Abk/I ~ PWms Parameter 7 6 Select ~~oxy Pulse Process Display on When unit is first turned ON, Process is the default screen, at other times use mode select button to select> Process. Use parameter select button to select Teach. > Use increase/decrease buttons to select ON. 2 I Qff L 1 ApkA 450 1PM lPMcanalsobechangedwiththefrontpanel DISPLAY CONTROL knob if 1PM is selected Figure 9-3. Setting Side the front panel display. When the Process Teach mode is ON, and one of the following pulse parameters is Selected >: ApK, AbK, PPS, or PWms, the front panelwitldisplaytheselectedpulseparame(arc length). When the pulse parameter is selected > on the front panel, the value can also be changed with the front panel DISPLAY CONTROL knob. ter instead of Trim 3 ApK 4 AbK 5 PPS 6 PWms When values have been set at each teach point, strike and maintain an arc for five see onds. Repeat procedure at each teach point until custom program is complete (see Figure 9.2). 7 Custom Pulse Screen The letter C will appear In the upper ner of all customized programs. To set right cor Sequence WeldIng Parameters, see Section 8.2. Panel Teach Mode Parameters For A Pulse Welding Program OM-1586 Page 39 N OlE ~ Program #___________ Program Make Wire copies of this chart for future use. Size/Type_________________________ Gas__________________________ Name__________________________________________ Card #______________________ Gun Model_____________________________________________ Flowrate 1PM ApK AbK PPS PWms CFM COMMENTS 750 700 650 600 550 500 450 400 350 300 250 200 150 100 50 Preflow:___________________ Sec. Run-In Trim:______________ 1PM:_________________________ Sec.:________________________ Crater Trim:________________ 1PM:____________________________ Sec.:__________________________ Postflow:________________ Sec. OM-1586 Page 40 9-4. Changing To Adaptive Pulse Welding I READ SAFETY BLOCKS at start of Section 9 before proceeding. Welding parameters are the same for both a Pulse and an Adaptive Pulse welding program. While welding adaptively, the unit uses feedback to attempt to maintain a constant arc Adaptive as 1 U Side Panel Mode Select shown: Side Panel >Prg >Process Display Default first turned side display when unit is ON, at other times use panel mode > /1 length. To change to welding, proceed Pulse select button to select Process. 1_ Sequence Pulse DualSchd 035Steel Card 98Ar 2oxy Side Panel Parameter Select V Prg >Process 1 >EuI~~ Sequence DualSchd 035Steel Card 9BAr U 2oxy lncrease/ Decrease >Process Sequence Prg 1 >AduptEuL~~ DualSchd 035Steel Card 98Ar Figure 9-4. Changing To 2oxy Adaptive Pulse Welding OM-1586 Page 41 SECTION 10-TEACHING A MIG WELDING PROGRAM a WARNING ELECTRIC SHOCK can Do not touch live electrical kill. WELDING WIRE wounds. parts. Controlcircuitandfeederoperationalpowerare ON using or changing the microprocessor settings. can cause puncture Do not point gun towards any part of the body, other people, or any metal when programming. The welding wire is electrically live and moves out of when the gun whenever the power switch is ON and the gun trigger is pressed. A. Changing To MIG Welding 1 U Side Panel Mode Select panel > 1 / >Process~] Sequence >Prg 1 Pulse DualSchd 035Steel Card 98Ar q 2oxy Side Panel Parameter Select + >Process Prg Sequence I >EuI~e DualSchd 035Steel Card 98Ar 2oxy lncrease/ Decrease I >Process Prg 1 Sequence DualSchd Card Figure OM-1586 Page 42 Side Panel Display Default display when unit is first turned ON, at other times use side 10-1. ChangIng To MIG In The Process Mode mode select button to select Process. Go to Figure 10-2. B. Setting Sequence MIG Welding Parameters On Side Panel Display 1 >Process >W.sI 18. OVal DualSchd 200 1PM Card 0.0 Sec 2 t Side Panel Parameter Select Button Use side panel parameter select button to select > parameters. 3 ~ Display When unit is turned ON. Process is the default mode, at other times, use side panel mode select button to select> Sequence. Sequence (~) Side Panel Weld Parameters Parameter ranges Side Panel Mode Select Display are as follows: Volts, 10.038.0 Volts Wire Feed Speed, 50-780 Inches Per Minute, 1PM I Seconds, 0-25.0 Sec. If value set is (0), welding will continue until zero Process >W~I welding gun trigger 18. OVol >Sequence DualSchd 200 1PM Card 0.0 Sec t Changes to voltage and wire feed speed (1PM) parameters in the weld sequence are also displayed on front panel display. Go to Set Desired Figure 10-3. Voltage Side Panel Parameter Select We I d 1>18. Inc rease/ Weld Sequence Volts Decrease can be fine tuned while . >We I d QVo It I PM 2 0 0 0 I _________________ S 0 e C welding 18.OVoI ~ 200 1PM 0.0 Sec Side Panel Parameter Select Set Desired Wire Feed Set Desired Weld Time, If is released. Inductance, 0-99 % Applicable Weld 420 1PM I>o..~ Sec ~Weld 20.OVoIt 30%lnduc lncrease/ Decrease >2QQ 1PM 0.0 Sec I lncrease/ Weld Sequence 1PM Decrease can be fine tuned while welding I Side Panel Parameter Select Side Panel Parameter Select Speed I Set Desired Inductance, If Applicable Proceed to next Weld I I ncrease/ 420 1PM 2.2 Sec , figure. 20.OVoltsl I 1PM 420 > 2.2 Sec Increase Decrease Side Panel Parameter Select Figure 10-2. Setting Weld Sequence Display OM.1586 Page 43 1 Crater Parameters Parameter ranges Display are as follows: Volts, 10.0-38.0 Volts Wire Feed Per Speed, 50-780 Inches Minute, 1PM Seconds, 0-2.5 Sec. If value a zero 18.OVol 200 1PM 0.0 Sec (0), set is Crater sequence is per formed. Go to ~ no Figure 10-4. Side Panel Parameter Select Crater Crater >1~QVol t Crater 24.OVoIt 24.OVott ~ 250 1PM 0. OOSec Set Desired Voltage 1PM >2~0 250 0. OOSec Side Panel Parameter Select Side Panel Parameter Select Set Desired Wire Feed Speed Increase/ Decrease 1PM >Q~QQSec Set Desired Crater Time lncrease/ Decrease Increase/ Decrease 28. OVo I 400 1 . t J 1PM I 2Sec Proceed to next figure. Side Panel Parameter Select Increase Figure 10-3. Setting Crater Sequence Display I Bumback Parameters Parameter ranges are as Display follows: Volts, 10.0-38.0 Volts Seconds, 0-0.25 seconds. If value set is zero (0), no Burnback quence is performed. Go to I>~uru~~ch 18.0 0.00 Volt Sec Burnback ~ J>16.Q 0.00 Side Panel Parameter Select 16.0 10-5. >~urnbaQk Volt Sec 10-4. Sec Side Panel Parameter Select Set Desired Bumback Time lncrease/ Decrease SettIng Burnback Sequence Display Side Panel Parameter Select I 16.0 Volt~ 0.12 Sec -.~ lncrease/ Decrease OM-1586 Page 44 Burnback Volt Set Desired Burnback Volts Figure Figure se Proceed To Next Figure Increase 1 Postflow Parameters Postfiow ______/ 0-9.9 seconds. ______ I f >P~ ______ Post f low ! ow >E~ I f I Side Panel Side Panel Set Desired Postflow Time Parameter Select Proceed to next Parameter Select I ncrease/ Decrease Figure 10-5. Go to 2W Increase Setting Postflow Sequence Display e 0.0 f Prefiow Parameters Prefiow can be seconds. / r 10-6. figure. 1 >P Figure Sec 1.2 Sec Sec 0.0 Display adjusted from be can Pref low I ow Sec >E 1.2 Sec Side Panel Parameter Select Side Panel Parameter Select Set Desired Prefiow Time 10-6. I I Q~tL Go to Figure 10-7. Sec Proceed to next figure. Increase Increase/ Decrease Figure £ ~ Setting Preflow Sequence Display 1 Run-In Parameters Parameter ranges >Ru n I Display adjusted from 0-9.9 Display are as follows: n Volts, 10.0-38.0 Volts 18. OVo I 200 1PM 0.0 Sec ~ Wire Feed Run in Run in J >j8~QVoI 1PM 0.0 Sec 50-780 inches Seconds, 0-2.5 Sec. (0), no Run-In performed. zero Side Panel Parameter Select 200 Speed, per minute, 1PM Run in 18.OVolt 1PM 0.0 For Conventional MIG Welding Set Desired Voltage Side Panel Parameter Select Sec Set Desired Wire Feed Speed 18.OVolt --~-Side Panel Parameter Select Increase! Decrease I ncrease/ Decrease Figure 10-7. SettIng Run-In If value set is sequence is ~j 200 1PM Sec Set Desired Run-In Time Increase! Decrease Sequence Display OM-1586 Page 45 SETTING DUAL SCHEDULE PARAMETERS SECTION 11 WARNING a ELECTRIC SHOCK can kill. Do not touch live electrical parts. ~ Control circuit and feeder operational power are ON when using or changing the microprocessor WELDING WIRE wounds. ~ ~/ I cause puncture Do not point gun towards any part of the body, other people, or any metal when programming. The welding wire is electrically live and moves out of I settings. can the gun whenever the power switch is ON and the gun trigger is pressed. Dual Schedule can only be used two consecutive weld pro with grams such as: I & 2, or 3 & 4, or 5 & 6, or 7 & 8. Any program type MIG, Adaptive Pulse, or Pulse can be combined in dual schedule. For MIG, Prg 2 is Adaptive Pulse, and Prg 2 is Pulse, etc. example, Prg Pulse, 1 or Prg 1 is I is Side Panel Mode Select But ton 2 Mode Display Use mode select button to select> Dual Schedule, then proceed 1 ~nel /3 Dual Schedule Parameters Display panel increase/decrease buttons, or DISPLAY CONTROL knob (see Figure 11-2) to select dual schedule pairs. >011 Sequence -I I>DualSchd Mode Select r d Increase lncrease/ Decrease LPrg On ~ 3 Use side Process 1& 2 0r ~ ~f~r9 1&2~ Side Panel Parameter Select Display Control If the two desired welding programs most common method to are not in the proper program order (1 & 2, or 3 & 4 etc..). the in the proper order would be to write one program to a data card, and then read the program from the card into the desired program number, see Section 12 for data card information. Figure OM-1586 Page 46 get them 11-1. Setting as shown: Dual Schedule Pairs On Side Panel Display 1 Front Panel Parameter Select Button 2 Front Panel Display Press parameter select button to select> program number on front panel display. Front Panel 3 24. 4 250 Display Control Knob OV 1PM Welding Gun Trigger. Or DSS-Type Switch The dual schedule programs can be alternately selected between active programs A or B by turning 3 the DISPLAY CONTROL knob Welding Gun Welding Gun OR Trigger click clockwise Display wise, or Control Knob ing DSS-lype Switch >Prg Dual 2 Ar~~1ouai B one counterclock by squeezing and releas welding gun trigger, or by an external mounted OSS-type switch mounted on the welding gun. See Section 13-5 for specific switchinstructions.The type settings shown on the front panel display are I>Pr~ ~ or the for the active weld program. When program B is active, turn dis play control knob one click clock wise to select another schedule programs. pair of dual Display Control Knob ON, and PROCESS is selected on the panel display, then the side panel increase/decrease When dual schedule is side buttons Figure 11-2. can be used to Selecting change program numbers. Between Active Dual Schedule Programs A And B On Front Panel Display OM-1 586 Page 47 SECTION 12- USING THE DATA CARD 12-1. Installing Data Card 1 Data Card The gold contacts need to be up when card is inserted into slot. 2 Card Slot 3 Label Use the label to record names of programs stored on card. 3 ST-i 56 268-Al Ref. S-155 923 Figure 12-2. Using 12-1. Installing Data Card The Data Card Use Mode Select button to select Card. I Card Screen 2 Moving Line Process Sequence DualSchd Press >Card Moving line is under value be changed. Below 3 Card that can Program Number ____________________ The program card can holdup to 32 programs. When writing to the 0 ~ >Write Side Panel Parameter Select Once card, the next available program number is ,j/press iH___ MIG ~!ZEte WriteDone ____ 2 FIgure OM-1586 Page 48 12-2. Writing Side Panel Parameter Select To Card / 3 automatically assigned. 2 MIG Press Side Panel Parameter Select (Name Card Program Off) Use Mode Select button to select Card. ~~~~~~~1 Process 1 Card Screen Sequence 2 Moving DualSchd Press Below >Card Line Moving line is be changed. can Read Screen 3 Side Panel Parameter And Select Once under value that Select desired card program to download. Select feeder program Mode Select Once number where the card program goes. Side Panel Parameter Select J WARN I NG: Prgl ] Be Will Prgl Lost Lose? Be Wi Lose? Yea I Lost l~ # 1 NQ Press Press Pulse Press Increase Side Panel Parameter Select Side Panel Parameter Select Side Panel ________________ ________________ I I I I Donel Card Prg1~~~ # Select Press Figure 1 Pulsel 1 Prg to I I Parameter Read 12-3. Reading Press From Card 1 1 Write WARNING Warning If there Screen no programs on the card, this series of screens appear. : are CardEmp ty >Read Delete Press Done Below Side Panel Parameter Select Once Wr i t e >Process Read De I e >Prg Sequence t e 2 Ml G Dual Schd >Done Press Card Side Panel Parameter Select Figure 12-4. Reading (Or Deleting) From An Empty Card OM-1586 Page 49 _____________________ Use Mode Select button to select Card. _____________________ _________________ _________________ Process 1 Card Screen Sequence 2 Moving Line DualSchd Press Moving line is be changed. Below >Card _________________ under value that can _________________ 3 Delete Screen Select program number to be de leted from card. Side Panel Parameter And Select Once ~ L~!;te Write # Mode Select Twice WARN I NG: MIG ~Press ____--1--H___ ~ Side Panel Parameter Select ____ 2 I J Delete Delete MIG #2 rd~ Press ___ Increase I ~ Card Side Panel Parameter Select Side Panel Parameter Select #3 Prg2 MIG J Deleted Press Press Side Panel Parameter Select Figure 12-3. 12-5. Deleting Programs From Card Naming Programs 1 1 ~ Se I fle St Card M em o P r y r o g Thedefaultsettingisoff.Toname r am s programs r f e written e e d Press gun trigger power off and back the Process Figure OM-1586 Page 50 to the card, changetoOn. >Name W i Name Card Programs Screen (See Section 13-10) 12-6. Default System Setting For Naming Programs briefly screen. on or turn to return to 1 ~-1 Section 13-2) 2 Selflest Security/Setup Screen (See Card Screen Card Use Mode Select button to select Card. Pr ograms Memory I>Name >~n 3 ref eed Moving Line Moving line is changed. under value that can be 2 __ 4 Name Screen If no name is desired, writing a pro gram to the card is the same as Figure 12-2. Process Sequence Pr Dual Schd >C r a When naming a program, the front panel DISPLAY CONTROL knob can be used to speed selection of es S Be low d -n characters. Side Panel Parameter Select >Wr I t e Read De I e 3 t e Done Allowable characters include: 0, 1, 2, 3, 4, 5, Press 6,7,8,9,:,;, <,=,>,?, ~, A, B, C, D, E, F, G, HI, J, K, L, M, N, 0, P, 0, R, S, T, U, V, W, X, Y, Z, (. V,],~,_,,a,b,c,d,e,f,g,h,i,j,k,l,m,n,o,p,q, r,s,t,u,v,w,x,y,z,!,,#,$,%,&,,(,),*,+,_,.,/, lncrease/ Decrease Side Panel Parameter Select Name? Name? ~ ~es Name? Yes 5007992 -~ Frame Press Press I ~P Increase I ~ Wr i teDone ~ Wr i teDone Name? Name? ti~ F 2 #2 r ame Parameter Select Side Panel Parameter ~ # 2 Increase Side Panel (~) Side Panel Parameter Select MIG ~ea Press I I ~J Side Panel Parameter Select 5007992 Press ' e S s 0 Side Panel Parameter Select to Prg 2 CardPrg r Side Panel Parameter Select Select MIG 5007992 F Press r ame Press Figure 12.7. Naming Programs And Writing To Card OM-1586 Page 51 SECTION 13 Security/Setup 13-1. SECURITY & SETUP Flow Chart ,2 1 ~Li >s e c u r i t y g Lock Access D u a T r I S c i g g e Features / 1 Screen Selections Features 3 Settings screens. r Settings Screen Section Features Program Number Lock Off/On >Wire Feed 13-3 Display IPM/MPM Motor Standard Type Low Section 13-11 Speed High Speed Off/On Press Mode Select 13-4 ~p~J Press Mode Select >Voltage Switch Type Momentary 2-Pole 13.5 Maintained 2-Pole ,L~1 Maintained 1-Pole YtJ ~J Select Off/On 17-Pin Feedback Volt Sense No Volt Sense Off/On Run Hours 09999.99 Hours 0999,999 Cycles 13-12 Press Mode Select ~Shutdown Press Mode Select Program Control ~ Trigger >Trigger Settings Selection Code >Dual Schedule be Panel Press Mode Select >Access Features that can are as follows: customized Selection >Security 1 2 Tosetupfeaturesthatcustomize operation, use the Security/Setup Of f h d Example Of Security Screen On Side Screen ~3 / r Press Mode Select >Arc Time 13-6 13-13 Press Mode Select 13-14 ~ No Reset Reset >Remote Parameter lncrease/ Decrease Off/On 13-7 I I Press Mode Select ~A~1 Press ~P~J Select Mode >Model Model I >Self Test 13-8 ~J Press Mode Select No Reset I I Arc Start Type 13-9 Reset ~ Press Mode Select I Bench Boom 13-15 Standard Hot Start 13-16 DVC On/Off 13-17 Press Mode Select >Arc Start >Memory Type L Press Mode Select >Mig Type Voltage Correction >Name Card Programs Off/On 13-10 Press Mode Select >Software Figure OM-1586 Page 52 13-1. Security/Setup Version Flow Chart Numberl 13-18 13-2. Using Security/Setup Screens 1 Setup Screen Front panel 2 display during setup. Side Panel Mode And Para meter Select Buttons Press and hold down both buttons turning ON unit. while 3 Power Switch On Rear Panel 4 Security/Setup Screen Follow this procedure any time ac required. Once in the secu rity/setup screens, use the Mode cess is Select button to select a particular screen. To save any or all of the changes made while in the security/setup screens, turn power to the unit oft and back on or press the gun trig ger to return to the Process screen. 2 3 / / / / 4 / >Secur ity Access >Prog Lock ii Of f Dual Schd Trigger Side Panel FIgure 13-2. Display Accessing Security/Setup Screens OM-1586 Page 53 Selecting Security 13-3. NOTE ~ Lock Security lock works only when a data card is inserted (see Section 12-1). Security Screen I Use this screen to lock a programs weld parameters so that changes can not be made using front panel controls. 2 2 Program Number Choose the program number (1 through 8) to be locked. Program 3 Lock Screen Security/Setup Screen According To Section 13-2 Increase When lock is off, the operator can change all weld parameters with out restriction. With lock on, the operator can but the range change parameters of change In the is restricted. example ure, the screens in this fig operator could change the value of trim –10 and wire feed speed –100 ipm from programmed settings are left at 0, the operator cannot change values from those programmed. values. If the Prog I>Lock Tr rn 21 Q~J 0l 1PM I ~~>Lock Qff~~~ Increase ~ 21 l>Prog Prog Lock Of fi /~i Side Panel Parameter Select 3 Side Panel Parameter Select Prog 2 Lock On >Trim Q 1PM 0 ~Prog 2~ Lock On >Trim 10 1PM On lo~ Trim 0 lncrease/ Decrease 21 Prog Lock >IPM Side Panel Parameter Select I Increase/ Decrease >Prog al Lock >Prog 2~ Lock Onj Trim ioj~~ 1PM 1001 Increase Page 54 Prog 2 Lock On Trim >IPM Side Panel Parameter Select Figure OM-1586 ~ 13-3. SecurIty Screen 10 100 If dual schedule is on, the paired are locked and unlocked programs together. 13-4. Selecting Or Changing N OTE ~ Access Code Access code works only when a data card is inserted (see Section 12-1). 1 ~ity/Setup~ Code Screen With code Access ty/setup off, access screens to the securi is not restricted. With code on, the operator must know and enter the access code to access or change any of the securi Press Mode I ty/setup Select Once 2 screens. Access Screen With a code set, this screen ap pears when power is turned on while holding the side panel Mode and Parameter select buttons. Code I I>Qn AAA ~ Side Panel Parameter Select I Code Ion I I >AAA ~Press ~ Increase/Decrease To Set Code Parameter Select To Move Cursor Code I On I hzWx I ~Press Turn Power Off And Back On And Access Security Screen 2 I Ente Ac r >Code / ~AA c e $ s Code ~P_r_e_S_5 Figure 13-4. Access Code Screen OM-1 586 Page 55 13-5. Selecting Type Of Dual Schedule Switch 1 Dual Schedule Screen Choose type of external dual schedule switch or use of the trig ger as the dual schedule switch. Increase ~ ~>Maint Sw i Increase Increase Increase Figure 13-5. Dual Schedule Screens 1 Momen 2P (Momentary Contact 2-Pole Switch Or DSS-1 0) > 2 Maint 2P (Maintained-Contact 2-Pole Switch Or DSS-9M) 2 3 Maint 1 P Or Trigger (Maintai ned-Contact 1-Pole Switch Or DSS-9 Or DSS-8) (055-gM) (DSS- 10) 1 1 ~ 2 > 2 1 A B 2E~ I c h 3 4 p 3 1 (DSS-9) 1 Adapter 1 (DSS-8) 1 1 1 Adapter 1 > 2 2 3 2 2 3 TRI\____ 3 3 > A~>~$ 4 > Figure OM-1586 Page 56 BO A~>cQ~> 13-6. Dual Schedule Switch Diagrams 2 2 > 3 > 4 > 3 13-6. Selecting Trigger Program Select 1 Trigger Screen When Program Select trigger can is On, the be used to switch be tween programs that have at least 0.2 seconds of preflow time. Briefly pressing and releasing the trigger switches programs. For gun if programs 1, 2, and 6 example: preflow time of at least 0.2 se conds, pressing the trigger will have switch from program 1 to 2, 2 to 6, and6to 1. Access Program Security/Setup Screen According Se I e c ~>Qn To Section 13-2 Increase Press Mode Select 3 Times Figure 13-7. Trigger Screen 13-7. Selecting Remote Increase/Decrease Capability 1 Remote Screen When Parameter Inc/Dec is On, the dual momentary-contact schedule switch can be used for changing weld for as parameters switching as well between programs. For example: when the front panel parameter select is on Trim or Volts, the dual schedule switch can be used to remotely change the value. When the front panel param eter select is on Prg, the dual schedule Switch be used to can change the program number. A OSS-lO dual schedule switch is recommended for this purpose. Pa I r n c a m e t e r / Dec >Q 0 Increase FIgure 13-8. Remote Screen OM-1586 Page 57 Using 13-8. Self Test I Switch A This checks the gun crease 2 Access Security/Setup Screen According 1 Gun Increase Switch > I> ~ 6 Of f flest Gas This checks the gas valve. Remote >Sel trigger. Wire feed This checks the wire feed motor. 5 i gger position. Trigger This checks the gun 4 Tr Switch B crease 3 Li in This checks the gun switch de To Section 13.2 Press Mode Select 5 Times switch position. On Contactor This checks the source Memory 7 Increase 3 welding power contactor. CV/CC This tests the physical connection to the pin at the 17-pin receptacle that controls whether the unit is in CC (constant current) voltage). or CV (con stant >1 Increase I g g a ! Of ffr~ T~gug~r 4 5 I Side Panel Parameter Select _________________ >1 i g g ! Increase a On _____________ -~ >Wi _________________ _________________ ~ £ 0 f a 0 ~ Press Increase Press I>~5 ~ Of Pre fi ss _____________ _____________ Side Panel Parameter Select Increase o t a Q t Q r a o f p r e ~ The welding wire and all metal parts in contact with itcarryweid outputwhenthewelding power source contactor is energized. _____________ ~ Side Panel Parameter Select 6 __On~ >GQcta~tQt Side Panel Parameter Select Increase Press Figure OM-1586 Page 58 13-9. Self Test Procedure 0 r e ss 13-9. Resetting Memory a CAUTION Resetting the memory erases all 8 programs and they revert back to original factory settings. If programs need to be saved, record desired programs on data card first. All security/setup features also reset except Model Type (see Section 13-15). 1 No Reset Memory 2 cannot be reset. Reset Press Parameter Select button to reset (clear) memory. Unit defaults original factory settings. Model Type setting is not affected by the to memory reset (see Section 13-15). Access Security/Setup Screen According 3 Reset 1 Name Screen (Default) Displays To Section 13-2 2 Side Panel Parameter Select Figure 13-10. Selecting Program 13-10. ResettIng Memory Name Feature When a program card is used, the programs written from the unit to the card can be named. ~.~ro~rams Ca (s~r~~g)To Section 13-2 Press Mode Select 7 Times r d Increase FIgure 13-11. NamIng Card Programs OM-1586 Page 59 Selecting 13-il. Units For Wire Feed Speed And Motor Type Wirefeed Screen 1 The can displayed unit of wire speed changed along with the wire be feed motor type. Increase Display Display I 1PM Motor Type~~ > ~ . ~Motor > I Display I 1PM p~ Type~~ Motor ~ I 1PM Display ,~ >MEM ~ Type~~ Motor Parameter Decrease Increase Increase Type Standard > Select Figure 13-12. 13-12. Wirefeed Screen Selecting Voltage Sensing Method Voltage Feedback Screen 1 When using the 17 Pin setting, arc voltage feedback is through the welding power source and the feedback signal is sent through the 17-pin cord to the feeder. If the 17 Pin setting is used, it is rec ommended that the voltage sens ing terminals on the welding power source be used to monitor arc volt age at the workpiece. When using the V. Sense setting, voltage feedback is through the voltage sense leads connected to the feeder. Use this setting when there is more than 50 ft (15 m) of arc weld cable used. 1 Access Increase Security/Setup Screen According --(s To Section 13-2 Figure OM-1586 Page 60 13-13- Voltage Feedback Screen Con t 01 -~ Feedback r L._~en~a 13-13. Selecting Voltage Error Shutdown 1 Voltage Shutdown Screen With No Volt Sensed on, the unit shuts down when no arc voltage is sensed. An error message ap. pears (see Section 14-4). With No Volt Sensed off, the unit continues to feed wire even when there is no arc voltage sensed. 1 Access Increase Security/Setup Screen According --s To Section 13-2 Figure 13-14. Resetting 13-14. Voltage -~ No Vol Sen s e t d >0 f Shutdown Screen Arc Time 1 Arc Time Screen The unit accumulates arc hours up to 9999.99 hours or 999999 weld cycles before rolling over to zero (0). The arc timer ing this screen. l~ncrease~ Access Security/Setup Screen According To Section 13-2 Figure 13-15. Selecting be reset can us~ SI OCycli 0. OOH >BQ~et r I Press 13-15. Arc Time Screen Bench Or Boom Model Type 1 Model Type Screen The unit is shipped from the factory properly set. The setting loads the parameters into proper pulse memory for the model used. This selection does not change when a memory reset is done. Figure 13-16. Model Type Screen OM-1586 Page 61 13-16. Selecting Regular Or Hot Arc Start 1 Arc Start Screen Use the Hot Start mode when high initial weld current is necessary to start large Do not diameter welding wires. setting for (9 mm) welding wire. The use .035 in the Hot Start welding arc power source starts the in the CV mode and switches to CC once Increase the arc is started. ArcStart Type >1121 Figure 13-17. ~ta!t 13-17. Arc Start Screen Selecting Voltage Correction 1 Mig Type Screen With DVC the unit from the sensing Voltage Correction On, closed-loop feedback 17-pin cord or voltage uses leads to maintain set pa If on, be sure voltage rameters. sensing leads are connected or voltage feedback is available through the 17-pin receptacle via the welding power source. With DVC Voltage Correction Off, feedback from the arc is not used. Figure 13-18. 13-18. MIg Type Screen Software Version Number 1 Version Number Screen When talking with service person nel, this number may be required. The factory keeps this number on file with the serial number of the unit to provide the customer with updated software as necessary. FIgure OM-1586 Page 62 13-19. VersIon Number Screen SECTION 14 MAINTENANCE & TROUBLESHOOTING WARNING a ELECTRIC SHOCK can HOT PARTS kill. Do not touch live electrical parts. S Turn OFF wire feeder and welding power source, and disconnect input power before inspecting, maintaining, or servicing. MOVING PARTS I~ can cause away from pinch points burns. can cause severe cooling period before servicing gun or unit. 47~j~~ injury. Keep away from moving parts. Keep Allow Maintenance such as drive rolls, to be performed only by qualified persons. wtwarn4 1 9/92 14-1. Routine Maintenance OFF all a Turn maintaining. -~ before power 6 Months Blow Out Or Vacuum Inside Clean Drive Rolls Figure 14-2. Replacing The Hub I 14-1. MaIntenance Assembly ~ ~ READ SAFETY BLOCKS at start of Section 14 before proceedIng. VI Turn OFF wire feeder and welding power source. Retract wire onto spool and remove. Take hub apart as shown. 7 1 Retaining Ring 2 Nut 3 Flat Washer 4 Spring 5 Keyed 6 Fiber Washer 7 Brake Washer 8 Rub 9 HubSupportShaft 6 1 Replace slide Tools Needed: Washer worn or parts broken parts, and shaft in order onto shown. ~: ~ 15/16 in. Tighten hex nut until a slight force is needed to turn hub. Install wetd ing wire (see Section 3.10). ST.142 709 Figure 14-2. Hub Assembly OM-1 586 Page 63 14-3. Overload Protection &~ 1~ READ SAFETY BLOCKS at start of Section 14 before proceeding. Turn OFF wire feeder and power welding source. Circuit Breaker CB1 1 CB I protects the wire feeder motor from overload, If 081 trips, the wire feeder shuts down. Check for jammed wire, binding drive gear, or misaligned drive rolls. Correct problem. Allow cooling period and manually reset breaker. 134 905/Ret. ST-156 931.A Figure 14-3. Circuit Breaker CB1 14-4. Error Screens I Error Screen Trigger This appears if the trigger is closed when the Unit power is turned on, or if the trigger is stuck or defective. 1 2 R e I e a s e T i g g e r r No Volt Sensed Error Screen The I arc voltage sense circuit is not receiving feedback. Check voltage sensing connections. Check connections at 17-position plugs/recep 2 3 Release tacles at the unit and ~ ~ ~ welding power source. Tum unit off and back N on after cor recting problem. Sensed M e m o r y C R C E P E r r o r 3 Memory CRC Error Screen The data in the program indicated is not the same data that was saved. Press the front panel parameter Se r g Q r r 0 Q IectbuuontocIear(E~orremainson display). r Theprogramcanberunbuttheweld settings may vary from those last saved. M em R a n o g r e y j 1P E r r 1 g r 0 4 Memory Range Error Screen Thedata in theprogram indicated is out of usable range. Press the front r panel parameter select button (Error remains on display). to clear The program can be run but the pro gram may stop when it tries to weld with out-of-range settings. Ref. ST-155 222 Figure OM-1586 Page 64 14-4. Error Screens 14-5. Diagnostic a Indicator LEDs WARNING ELECTRIC SHOCK can kill. Do not touch live electrical parts. Turn OFF wire feeder and welding power source, and disconnect 97 input power before inspecting or maintaining. 81064532 I Tools Needed: CIIIII~J1J 1/4 in. ST.156 927 / ST-157 363 Turn OFF wire feeder and source. welding power Remove wrapper. There are nine LEDs on Interface Board PC5O. These LEDs can be used to check certain functions during troubleshooting. LED2 Indicates +5 VDC with board common. Indicates 15 VDC with respect to PS mon on the board. 4 7 to circuit LED6 On when the contactor is not LED3 board respect com Indicates +15 VDC with respect to circuit Circuit Board PC5O 1 3 common. 8 energized. LED7 On when the CV mode is used. LEDs 1 er 2 is through 5 should all be on when pow applied to the wire feeder. 5 Indicates 15 LED1 board Indicates mon on + 15 VDC with the board. respect 9 LED4 VDC with respect to circuit common. to PS com 6 LED5 Figure LED8 On when the gas valve is not energized. 10 LED9 On when the wire feed motor is not running. 14-5. IndIcator LEDs OM-1586 Page 65 14~6. Troubleshooting WARNING a ELECTRIC SHOCK kill. can Do not touch live electrical HOT PARTS IA? parts. Turn OFF wire feeder and welding power source, and disconnect input power before inspecting, maintaining, or servicing. MOVING PARTS ' Keep away from can cause Troubleshooting such drive rolls. as Table 14-1. shielding gas flows, energized. do not light -~ to be burns. gun or unit. performed only by qualified wfwam4.l 8/92 Troubleshooting Check Section cord connections. If secure, check cord for interconnecting and repair or replace. continuity electrode wire is not meter(s) servicing Remedy but Wire feeder is on, before persons. Trouble Wire feeds, can cause severe cooling period injury. moving parts. Keep away from pinch points Allow 1-Ii 3.7 Check and reset CBI. 14-3 up, motor does not run, gas valve and welding power contactor do not pull in. Electrode wire feeding stops or feeds -~ Check gun trigger Check gun trigger. connection. 3-5 -~ erratically during welding. * -- Readjust drive roll pressure. ~ 3-12 Readjust hub tension. --~ 3-10 -~ 3-4B -~ 14-1 -~ 3-4A Change Clean to correct size drive roll. or replace dirty Incorrect size Replace with Have wire or worn contact tube Remove weld ing or worn a spatter or or drive roll. guides. liner. * -~ foreign matter from around nozzle open * -~ wood stick. Factory Authorized Service Station check drive motor or mo -~ tor control board PCi. Motor runs Check for correct input slowly. Wire does not feed until trigger is pulled, trigger is re j -ł but continues to feed after leased, and trigger hold is not cable. a short between Repair short or welding gun trigger leads replace welding gun. --~~i and weld on. Gas valve in feeder is rattling loudly along with possible erratic or slow wire feed speed. ~i~t Check for - voltage. does not switch out of RUN-IN -0 Check for cable. i -~ a short between Repair short Install, reconnect, or or welding gun trigger replace welding gun. replace reed relay or leads and weld voltage sensing lead. -~ 3-6, 3-7, 3-8 I I SPEED. _________________________________________________ ___________ Wire feeder power is on, displays up, but unit is inoperative, *See gun Owners OM-1586 Page 66 Manual. light ~ -~ Check welding gun trigger leads for continuity, and repair leads replace gun. or -~ NOTES OM-1586 Page 67 SECTION 15- ELECTRICAL DIAGRAMS DSPL2 DISPLAY SIDE ~ ~ ,v!vii~ivvvvvvv~ DATA I IHOREMENT DECREMENT -a- S o P841 0 0 P842 o I I P843 P844 I -a- -a I 0 0 0 ~ I I 00000000~0000 RC6I PC6O I RC6GIPLG6G RC6I/DATACARD I I lIZ PC4O 666 ii~~~~&I /PLG4I 0 LvvvvvJ ~4I, PARHiETER SELECT CE SELECT ~ CARD ~ _____________ 111111111 QIQ lillillil I I I I I I I I I I I I I ifi ~i~I~I 1J ~ ~ PARAMETER ~ )~)RC36~ -i____________ 1RC29 0RC331 s_ ________ )>RC36 )> RC36 RB TRIGGER HOLD PIPGE -a- -a- ~ I 0 I E 7 080 _J B 0.~ 08 qj &i:~ U) DIz ))RC36 RC3III )> RC36 I I o6on6 &&&&~ 34 MICROPROCESSGE BO4PO ______________ REQ BC 10/PLO ID __________ 1RC22 RC321 )>RC36 ______________ _____________ RC24 I I )>RC36 COI~OJCTDE CABLE PCIO LEO I ~ CABLE tC/CAAA I ? I CaOXTDE 16 t*?~0) 0 P822 IRC2G II ) RC36 _____________ BC Il/PLO II I i __________ _R 10 II )>RC36 I )> RC36 DR I 2 CGD.CTDE CABLE 00 0 0 P823 P821 I R/W >- I P831 RC JOG SELECT )> RC3A - 12 )>RC36 13 )>RC36 __________ ~- )>RC3A I IS ___ 16 4.IV )>RC37 )>RC37 I I PC 30 I I I I I C~TDE CABLE L PC20 I I dSWIPG*RC~ <IIETAQIENT YT. I I RC2D/PLG25 4 3>~~3>3 ~ 2),)J2! >~J1S~ PLG2B PLG231 RCI6/PLGI6 RC27> RC23 ~i ~ RC26 >>-~- BC 17/PLO 17 4>)14> ______ BC I 5/PLO 15 I RC24/PLG24 wr~ ~im BC I 2/PLO I 2 I tIJ_1701I 2 ?t?T~7 I I ______________ I 0 00 0 0 0 ~ Mvvvi I I vv~vv I ~ TRIGGER ____ DECREMENT ________________ TRIGGER o 51 I I>i I~ r O.E.I I DCREANT 08TICAL I SWIMEARC 08 DETAO+NT I I 081108 I ~ I CQ4OI PLGB7/PL058 ~0 <2< BLU/ BOY ____ 17e>7>174-~ REO/ I 11< I BOY I I I I DEN 114> I >C~ I < / BOY oq6IE).6>.q6< . I RED 6S14 2~ 44~-)~4>~~:j4< I 5cjs4>s>-4sC L Figure OM-1586 Page 68 15-1. Circuit Diagram I BOY For Wire Feeder J 2 . SCSI-F> 7 SCSI-C> 1 PIN CC/CA COI44IY4 (+154-CY) PC8I-E>CUPPENT 4 PIN PCI 2 I IQ4cN CCPCB2-2 > I+IDVCVI << PCP2-4 ; FSZIBAO( I 14/184 PC54-IO>)~ IPe1~TA4tE (0-104 PC549>>~-~48 F~AO.1 (14/ISV kc PCB2-5 CURRENT ~ PC82-3 ~ ~ PCSO PC5O INTERFACE BOARD PCBI-G> PCS4-I PCBI-M>voL.TAGE PC54-7 I FEEDBACK I >>-~--< _________________<C (14/104) PEED ~ H1 4< r)JSEOwrm SWZ1CAPC ~ DETACI4NT ~1IDN C< RCS2- 10 PCS I/PLOD I (14/1006) (0-by) PC7O/Pt.070 PCP7 PCBB FEEDBACK IICIUCTAVCE NI~ ~ RC02/PLGD2 PCS3/PLG7D PCII-4>) PCII-8>>- ~ PCII-6>) PCI1-3)> PCII-7>) I 58.1St PCS2-2): PC55~055 - - - PC84>>P<B(~)8~~7~ - cc ~cas-i __________________________ cc:::: SEIcE CLAPc PC89-I <<REDS-I PCII-5>>~-8. I-2)~~ 42 POD4~G04 CCPCD84 ~ PCII-I>>PCI > PCS2- I SENSE ~ t~-c +154 15<cp~-o ciPcsS-s ~ ~I5V 503 RESS-2 <<P(~55-7 I ~ SCS3-2>>48 <CRESS-S I5V 2 ., 2. 2. 2. 2. 2 2. 2. 2. - N 1. 2. 2. 3~~%~4P 14 <<502-6 PIN PC89-3) 2. PC8O ~ § § § § § § § ~ PCBS-2) FILTER BOARD PC8O>HF ~ STUD /0 P109 +104 C, C ~ IOD4(APC ~ >E P.S. ~tO.1 ~ > D ) H > B > A > ~ T0T~5 4 A CCPC4-I 4 -~ .+APCA /CAA C I ~ ~ C PC49)>~ P.S. ? ~ PC6-I>> PC6-2 > 24VAC PC I MOTOR BOARD ~ 2 ~fl1T6CTDB CT ,~p ~ TAC AC1 24VAC ~ao N/~ PC I /PLG I Pc2/PLG2 C<PC4-6 P0/PIES RCA/PICA 50/PIGS PC6/PIG6 2 PC4-4 <<50-4 CC 50-158 848 OM-1586 Page 69 I PC2O FRONT DISPLAY PCI MOTOR BOARD YEl_(PI_G387~ BLU(P1G38-8) RED(Pt638-4) RW/EU( (Pt_G38-3] ~ ~N(PLG3B-I I) - (PLG38-~) Affi~l(PLG38-6) PLG37 PLG2B Figure OM-1586 Page 70 15-2. Wiring Diagram For Wire Feeder I I I I I I I I I DATA CARD I 28(PLG6-4) I 28(PC80-RC86 I0O)PC8O-RC85)~ RC6O/ PLG6O St~~ AC~I{j/J - CBI IOC(PI 2 63A)PLG)5-3) - ~Al~~I~-2l 0~*AIP~ IIIR-Rl 648 (PIG 15-4 1 ~4IrE)PLG9-Gfl I ~6IAIPIGI5~ ________ I8(PLG6-30A(PLGA-3)T I)~ ~~~L ~~I H _________ __________ : AC cICS POWER SIDE RC42 RC7O PC4O DISPLAY - - o 45A(PC PC8O 6O-RC87 ~flwL~I ~, C ~8O-~88~ 46A(PC 0 I / 1~ ~4fC ~ RIB8~~ 72A(PLGI -2) 70A)RC7-7) RCI6/PLGI6 0 RC) 5/ PLGI5 RI ~82/ O_~z,~OI G82 ~ H ~ --~~/IJ ~ 0. 0 8C80 ,~ L 1 * Lii 0 U C a 0 PC 0 MICROPROCESSOR ~09(~1-2) 4~1i1A(Pt.G25-4) I * RC Ill PLOII ~ Rd 7/ 0 W~4XTE)SR I-AC) ,,-,--,-, Rc53/~l PLc153~j~J A(PLGI-4) RA 10C7-R I 48A(P1G82-6) BL).RI(Pt.075-2) 49A(P1j382- II ~A1RIE(PLG75-3) 68A IPC7-R1 32A(PLGI-3) IOA)PLGI-8) 36A(PLG2-6) 1.L,4~4 LL8L~ ~ ~ RC5/ PIGS) 05EEN(Pt.G75-I) RC54/ PLG~4 ~)A ( 558 I P1082-3 _______ )50A I~7i~71. 52A(PLG82-9) RD(PLG4-9 ~ I~6A 1~G82 PC5O INTERFACE 1Z?~1~7L I 0 ' PLG9 BLAO((SI-~C 54A(Pt.G82-5 83A)PLGAS-I I I, PLG~5 ~(~I.082~) ~ 42A(PL082-8) C r o C RC 40 /G~ (QjX~fifi 5A(RC4O-S) PLG38 7B(RC4O-6) Id 0 70A(RC4O-7) a 65A(8C40-8) m~ wrj~ PLG39 : ~ RC7 SD~158 846 OM-1586 Page 71 SECTION 16- PARTS LIST 0 N In (I, In C,) In (0 (0 .~ C) E LI~ U) U) 4 U) U) C,) U. 0) (0 C) U- C) C) C,) C) C) In C) (0 nJ (~nj- (0 C) U- C,) OM-1586 Page 72 079216 145639 Quantity Mode Part No. Dia. Item No. Mkgs. Description Figure 1. 149251 1. 149252 079 878 PLG23 . 079 535 079531 605156 PLG28 ..2. ..3. ..3. PLG38 080 328 079 534 See Note 139597 139598 047 636 079 535 079 739 135 304 PLG37 135409 114 656 139 600 139 599 010 603 010 606 603106 056112 600 324 REED. .8 PLG7O 10 . 140 789 079531 079 878 079 535 149884 080 947 602 243 12 602213 601 872 13 132 053 14 Fig 15 149 838 15 .149 839 15 .078 264 11 16-2 15 16 075 16 079 217 17 Fig 16-5 18 19 . . GS1 20 21 22 . 078 605227 125785 139265 156243 020 279 23 24.. 153631 25.. 132611 26.. .M1.... 156354 26.. Ml.... 153491 27.. 153492 Fig 16-4 28.. 150998 29 604 612 . 16-1. Main 116 12 Assembly CABLE, trigger (consisting of) CABLE, trigger (consisting of) HOUSING PLUG & PINS, (consisting of) CONNECTOR, circ pin push-in 18-l4ga CONNECTOR, circ clamp str rif CABLE, port No. 18 4/c (order by ft) RECEPTACLE w/SOCKETS, free hanging (consisting of) CONNECTOR, circ skt push-in 24-l8ga CONTROL BOX, (Fig 16-3) CABLE, interconnecting (consisting of) CABLE, interconnecting (consisting of) HOUSING PLUG & PINS, (consisting of) CONNECTOR, circ pin push-in 18-l4ga CONNECTOR, circ clamp str rlf CABLE, port No. 18 8/c (order by ft) HOUSING PLUG & SOCKETS, (consisting of) CONNECTOR, rect pin 24-l8ga HOSE, gas (consisting of) HOSE, gas (consisting of) FITTING, hose brs barbed nipple 1/4tbg FITTING, hose brs nut .625-18RH HOSE, nprn brd No. 1 x .250 ID (order by if) FITTING, hose brs ferrule .475 ID x .718 Ig CABLE, weld cop strd No. 4/0 (order by if) SWITCH, reed (consisting of) CONNECTOR, circ clamp str rlf HOUSING PLUG & PINS, (consisting of) CONNECTOR, circ pin push-in 18-l4ga BRACKET, spring retaining BRACKET, spring retaining WASHER, flatstl std .375 WASHER, lock stl split .375 NUT, stl hex full .375-16 SCREW, cap stl hexhd .375-16 SUPPORT, hub & reel PIPE POST, 4ff w/base or PIPE POST, 6ff w/base PIPE POST, 4ff w/base or PIPE POST, 6ff w/base .4.4 .2.2 .l7ft.. 2lft 1 14. 1 1 14 . .... 1 6ff 8 .1 . 1 ... . . . 1 2Oft .. . 8 1 2 .2 .2.2 26tt 30ft .. .2....2 26ft .1 .1 .1 30ff .. .... .... 1 1 .... 1 .... 8 .... 4 1 1 8 4 4 x 1 .500 Ig PIPE POST, 4ff w/o base or PIPE POST, 6ff w/o base BOOM ASSEMBLY NUT, nyl hex jam .75ONPST VALVE, 24VAC 2 way custom port 1/8 oil COVER, motor & components CLAMP, motor top CLAMP, stl cush .7SOdia x .281 mtg hole STRIP, buna N compressed sheet .062 x 4.000sq CIRCUIT CARD, digital tach OPTICAL ENCODER DISC MOTOR, gear 1/8hp 24VDC 272RPM (consisting of) MOTOR, gear 1/8hp 24VDC 75RPM (consisting of) KIT, brush replacement (consisting of) CAP, brush WIRE DRIVE ASSEMBLY GUIDE, wire inlet SCREW, set stl sch 8-32 x .125 cup point 4 1 4 ... 4 .. .... 1 1 1 1 1 .1 .1 .1 .1 .1 1 .... .... .... .... .... 1 1 1 1 1 ....1 1 ....1 1 ....1 1 1 2 ....2 1 1 1 OM-1586 Page 73 Quantity Item No. Model Part No. Dia. Mkgs. Description Figure 082 050 30 .31.. PLG7.... 115092 113746 32..PLG57 131 204 . 113746 131 203 33..PLG58 114656 146544 34 Note: When ordering . 16-1. Main Assembly (Continued) LINER, monocoil inlet wire HOUSING PLUG & SOCKETS, (consisting of) CONNECTOR, rect skt 24-1 8ga HOUSING PLUG & SOCKETS, (consisting of) CONNECTOR, rect skt 24-l8ga HOUSING PLUG & PINS, (consisting of) CONNECTOR, rect pin 24-l8ga CLAMP, motor base Control Box contact factory service department 1 1 8 1 3 1 3 1 for proper number. OPTIONAL . Part of Option 156 725 Low Speed Motor. BE SURE TO PROVIDE MODEL AND SERIAL NUMBER WHEN ORDERING REPLACEMENT PARTS. OM-1586 Page 74 16 12 . . . .... .... .... .... . . . . .... 1 1 8 1 3 1 3 1 .. .. Item No. Part No. Description Figure 1 142399 2 010 191 3 058 628 058 428 4 5 6 7 8 008 900 905 904 9 057 971 10 010233 605 941 136684 058 427 .. 11 12 .. .. .108 124 124 124 13 . . . . . . .. . . . . . . . . . . . . .. . . .. .. . 16-2. Support, Hub & Reel SUPPORT, reel WASHER, fbr .656 ID x 1.500 OD WASHER, brake sti HUB, spool REEL, wire 60 lb (consisting of) SUPPORT, reel spool RETAINER, spool support NUT, spanner spool support (Fig Quantity 16.1 Item 14) 1 x .l25thk 2 2 1 1 1 . 1 . 1 . WASHER, flat stl keyed 1.500dia SPRING,cprsn .9700Dx x .l25thk 1 .l20wirex 1.250 1 .000 OD x 1 4ga thk 1 WASHER, flat stl .640 ID x NUT, stl slf 1kg hex reg .625-11 w/nylon insert RING, retaining spoo1 1 1 1 3 5 3 9 10 11 12 13 SC-146 339 Figure 16-2. Support, Hub & Reel OPTIONAL BE SURE TO PROVIDE MODEL AND SER1AL NUMBER WHEN ORDERING REPLACEMENT PARTS. OM-1 586 Page 75 508-A ST-157 21 22 19 ~ 28 27 18 26 Box 13 36 Control 37 16-3. 38 39 Figure 10 9 8 40 7 5 10 2 34 41 42 43 46 0 Ui 0) -o CD Ca CD a) 45- 44 PLG54 Item No. Dia. Mkgs. Part No. Description Figure .2 .3.... 4 ... PC4O.... PLG16,41 .5.... PC6O.... PLG6O .6....RC7O.... .7 .8.... PC5O... PLG51 PLG52 155024. 144844. 158160. 155023. 156623. 153501 147995. 048 282. 079 534. 079 532. 079 535 079531 154938. 158817. 158720. 147995. 158719. 147995. PLG53 PLG55 PC1O... PLG11 131204. 113746. 148439. 147995. 115092. 113746. 158921 115092. 113746. PLG15 153501. 147995. PLG17 115093. 113746. 155022. 10 PLG1O,24 11 159371 12 155629. PLG12,50 126689. 13 14 097132. 15 138044. 16 600399. 17 603106. 601222. 18 151187. 19 .20 134464. 21 +154927. 22 155261 SRi 035704. .23 CB1 .24 083432. Si.... 111997. .25 000527. 26 27 073756. 158578. 28 PC8O, RC8O PLG75 131204. 113746. PLG82 158720. 147995. 29 010325. 30 .110015. PLG9.... 141 162. .31 134731 32 079 739. .33.... RC4O.... 047637. 079 534. 048144. .9.... ... ... .. ... 16-3. Control Box Quantity (Fig 16-1 Item 2) LENS, clear anti glare .030 x 2.000 STAND-OFF, No. 6-32 x .875 Ig CIRCUIT CARD, schd side x 4.250 2 14 1 CABLE, ribbon 24posn 6.000 in CIRCUIT CARD, cyber card 1 HOUSING PLUG & SOCKETS, (consisting of) CONNECTOR, rect skt 22-lBga RECEPTACLE w/SOCKETS, (consisting of) i CONNECTOR, circ skt push-in 24-l8ga CONNECTOR, circ 4 pin Amp 211882-1 CONNECTOR, circ pin push-in 18-l4ga Amp 66359-6 CONNECTOR, circ clamp str rlf Amp 206358-2 STRIP, mtg PC card CIRCUIT CARD, interface HOUSING PLUG & SOCKETS, (consisting of) CONNECTOR, rect skt 22-lBga HOUSING PLUG & SOCKETS, (consisting of) CONNECTOR, rect skt 22-1 8ga HOUSING PLUG & SOCKETS, (consisting of) CONNECTOR, rect skt 24-l8ga HOUS1NG PLUG & SOCKETS, (consisting of) CONNECTOR, rect skt 22-1 8ga HOUSING PLUG & SOCKETS, (consisting of) CONNECTOR, rect skt 24-l8ga CIRCUIT CARD, processor w/proms HOUSING PLUG & SOCKETS, (consisting of) CONNECTOR, rect skt 24-l8ga HOUSING PLUG & SOCKETS, (consisting of) CONNECTOR, rect skt 22-1 8ga HOUSING PLUG & SOCKETS, (consisting of) CONNECTOR, rect skt 24-l8ga CABLE, ribbon 34posn 12.000 in KIT, EPROM service (part of PC1O Processor Circuit Card) CABLE, ribbon l4posn 3.000 in STAND-OFF, No. 6-32 x 1.500 Ig STAND-OFF, No. 6-32 x .375 Ig BUSHING, strain relief .120/.150 ID x .500mtg hole. WIRE, strd 1 4ga blk 600V 1 05C (order by ft) HOSE, nprn brd No. 1 x .250 ID (order by ft) CLAMP, univ 50A LATCH, slide flush mtg hole 1 .000 wide x 1 .500 1g.. LABEL, warning general precautionary 4 1 1 1 1 12 1 2 1 3 1 10 1 8 .8 1 6 1 6 1 1 . 1 4 4 1 . 35ft ift 1 1 1 WRAPPER PANEL, side lower 1 RECTIFIER, integ 40A 800V CIRCUIT BREAKER, man reset 1 P 1 OA 250V SWITCH, rocker SPST 1OA 250 VAC BLANK, snap-in nyl .875mtg hole STAND-OFF, No. 6-32 x .625 Ig CIRCUIT CARD, HF filter HOUSING PLUG & SOCKETS, (consisting of) CONNECTOR, rect skt 24-l8ga HOUSING PLUG & SOCKETS, (consisting of) CONNECTOR, rect skt 22-l8ga BUSHING, strain relief .840 ID x .875mtg hole CABLE, port No. 18 7/c (order by ft) HOUSING PLUG & PINS, (consisting of) CONNECTOR, circ pin push-in 18-l4ga CONNECTOR, circ clamp str rlf HOUSING RECEPTACLE & SOCKETS, (consisting of) CONNECTOR, circ skt push-in 24-l8ga CONNECTOR, circ pin plug keying in sockets 1 1 1 1 1 4 1 1 3 1 12 1 l2ft 1 14 1 1 14 2 OM-1586 Page 77 Item No. Part No. Dia. Mkgs Description Figure 134 201 34 PCi PLG1 .35 .. 155114.. PLG2 PLG3 115 092 . . 113 746 . . 115 093 . . 113 746 . . . . 115 094 . PLG6 . . . 115 091 113 746 . . . . 136 810 . . . 1 . . .... PLG39 .... RC7 37 .... . 38 40 ... PC2O,30 PLG25 .41 .42 .43 .44 .45 .46 .47 .48 .49 When ordering a .. ... CONNECTOR, . CONNECTOR, CONNECTOR, HOUSING PLUG . . 135409.. 114 656 . . CONNECTOR, HOUSING PLUG (consisting of) 1 24-l8ga & SOCKETS, (consisting of) rect skt 24-l8ga & SOCKETS, (consisting of) rectskt24-l8ga & SOCKETS, (consisting of) 8 rect skt rect skt 24-l8ga & SOCKETS, (consisting of) rectskt20-l4ga & SOCKETS, (consisting of) rect skt 24-1 8ga & SOCKETS, (consisting of) rect pin 24-l8ga CONNECTOR, 158702.. CASE SECTION, bottom/rear 145948.. BRACKET, mtg control box 158 104.. CIRCUIT CARD, schd front 150317.. HOUSING, term plug nyl 4cont 147995.~ CONNECTOR, rect skt 22-l8ga 154932.. PANEL, front 157113.. WASHER, shldr delrin .257 ID x .500 OD x .343 x .187 shldr 097924.. KNOB, pointer 144842.. ACTUATOR, switch 089032.. LENS, LED 4341 red NAMEPLATE, (order by model and serial number) 030170.. BUSHING, snap-in nyl .750 ID x 1 .000mtg hole 154933.. PANEL, inner control 154109.. PLATE, ident inner control 059712.. CLIP, component .437dia mtg adh back 158373.. CABLE, interconnecting (consisting of) 097868.. CONNECTOR, circ 1 7skt MS-31 06A-20-29S 039734.. CONNECTOR, circ clamp str rlf AN-3057-1 2 600343.. CABLE, port No. 16 5/c (order by ft) 097866.. CONNECTOR, circ 17 pin MS-3106A-20-29P . .39 CONNECTOR, HOUSING PLUG 115092.. 113 746 CONNECTOR, HOUSING PLUG 114066.... 36 2) (Continued) 8 HOUSING PLUG . 16-1 Item CIRCUIT CARD, motor control HOUSING PLUG & SOCKETS, HOUSING PLUG . (Fig STAND-OFF SUPPORT, PC card .312/.375 113746.... PLG4 16-3. Control Box Quantity . . component originally displaying a precautionary label, the label should also be ordered. BE SURE TO PROVIDE MODEL AND SERIAL NUMBER WHEN ORDERING REPLACEMENT PARTS. OM-1586 Page 78 1 6 1 4 1 10 1 4 1 8 1 8 1 1 1 1 4 1 1 1 8 1 1 1 1 1 2 1 1 2 1 Oft 1 Item No. Part No. Description Figure 1 .... 2.... 3.... 4.... 5.... 6 7 8 9.... 10.... 11.... 12.... 13.... .... .... .... 14.... .15.... 16.... 17.... 18.... 19.... 20.... 21.... 22.... 23.... 24.... 25.... 26.... 27.... 28.... 29.... 30.... .31.... 32.... 33.... 34.... 35.... 010668.. 150147.. 149962.. 149486.. 132750.. 150520.. 133493.. 133350.. 152241.. 133739.. 132824.. 010837.. 132747.. 132746.. 133603.. 137248.. 604772.. 602200.. 602082.. 154031.. 133530.. 133308.. 134834.. 149959.. 149746.. 108940.. 604538.. 151437.. 151290.. 149527.. 601872.. 602213.. 602243.. 149964.. 601966.. 16-4. Wire Drive Quantity Assembly (Fig 16-1 Item 27) SCREW, cap sti sch .250-20 x 1 .500 CARRIER, drive roll w/components SPACER, carrier drive roll PIN, rotation arm rocker ARM, pressure SPACER, rotation pin RING, retaining ext .250 shaft x 4 4 4 2 2 2 2 .O25thk PIN, hinge KNOB, w/extension WASHER, flat buna .375 ID x .625 OD x .O62thk SHAFT, spring PIN, spring cs .093 x .625 CARRIER, shaft BUSHING, spring SPRING, cpsrn .724 OD x .082 wire x 1.000 SPRING, indicator WASHER, flat stl SAE No. 8 WASHER, lock stl split No. 8 SCREW, mach stl rdh 8-32 x .500 SPACER, locating DRIVE, pinion RING, retaining ext .375 shaft x .025 thk HOSE, SAE .187 ID x .410 OD (order by ft) FITTING, brs barbed M 3/l6tbg x .312-24 ADAPTER, gun/feeder LH SCREW, cap stl hexhd .250-20 x .750 WASHER, flat stl SAE .312 KNOB, plstcT 1.125 Ig x .312-18 x 1.500 SCREW, mach stl hexwhd 10-32 x .500 COVER, drive roll NUT, sti hex full fnsh .375-16 WASHER, lock stl split .375 WASHER, flat stl std .375 PIN, groove type H .25Odia x .500 Ig SCREW, cap stl hexhd .375-16 x 1 .250 See Table 16-1, Page 82 For Drive Roll & Wire Drive Kits 1 1 1 1 1 1 2 2 1 1 1 1 2 1 1 2ft 1 1 4 1 1 2 1 1 1 1 2 1 9 15 16 18 19 6 5 2 SC-137 222-D Figure 16-4. Wire Drive Assembly BE SURE TO PROVIDE MODEL AND SERIAL NUMBER WHEN ORDERING REPLACEMENT PARTS. OM-1586 Page 79 0 cJ Lt) (0 N- ~ >. C) E C) C,, C,, 4 0 E U, 0 0 ((5 C) I C) (0 c,J cJ CU OM-1586 Page 80 LI~ Quantity Model Part No. Item No. Description Figure .. .. .. .. .. .. .. .. 1 . . . . . . . . . . . . 2 2 3 3 4 5 .. . .. . 6 . .. .. .. 8 9 10 11 . . . . . . . . . . . . . . . . . . . . .. .. .. .. .. .. .. . . . . . . . . . 079 030 .. .. .. .. .. .. .. .. .. .. .. . 16. . 17.. 18 +139 831 080 157 . . . . . . . 19 . 20 . 21 .. . . . . . . . . . . . . . 22 23 23 24 25 .. . . . . 27.. . 28 . 26 +When 079 029 075 462 . 14. 15 073 742 073 741 . 12 13 . 080811 079 664 139 633 602 250 079 020 149 858 080 723 150 258 024 605 075 101 12 .. . . 7 .. . 057 357 139 338 139 643 079 665 . . 142 804 134 327 602 246 047 224 073 666 079 080 079 602 139 667 812 632 243 590 010313 139 336 ordering a .. .. .. .. .. .. .. .. .. .. .. .. .. .. .. .. .. .. .. .. .. .. .. .. .. .. .. . 1.l25mtg hole . . . .. . 1 . . . 1 1 1 x 15.687 . a . 1 1 1 PIN, clevis .750 OD x 2.156 Ig CLEVIS, .812 yoke 6.062 Ig .750-l6thd NUT, stl hex full fnsh .750-16 SHAFT, boom counterbalance WASHER, flat stl SAE .750 NUT, stl hex elastic stop .750-16 SPRING, cprsn 3.750 OD x .625 wire x 36.000 SPRING, cprsn 3.750 OD x .687 wire x 33.750 RETAINER, spring BEARING, ball thr sgl row .750 x 1 .625 x .625 NUT, stl hex special .750-16 x 1.250 WASHER, lock stl ext tooth .750 BASE, swivel boom (consisting of) FITTING, grease 1/SNPT LABEL, Swingarc caution heavy spring LABEL, warning general precautionary WASHER, flat stl std .500 KNOB, T-bar .500-13 thd SCREW, mach sti hexhd .750-16 x 2.750 PIPE, plstc .500 x 133.750 PIPE, plstc .500 x 181 .750 BOLT, U stl .250-20 x .875 wide x 1 .375 deep WASHER, flat stl std .375 PULLEY, V sgl grv 8.875dia x 8.000P x .375 bore PIN,cotterhair.072x1.437 GUARD, motor protector component originally displaying 16 17) 1 LINER, monocoil 3/32-1/8 wire .. . x 16-1 Item GUIDE, wire inlet .. .. Assembly (Fig BUSHING, snap-in nyl .937 ID BOOM, single BOOM, single GUIDE, wire GUIDE, wire .. .. . 16-5. Boom I 12 precautionary label, . .. 1 1 2 1 2 1 1 ... . .. . 1 . 1 . .. . . . . 1 . 2 .. . . .. . . . . . . . . . . . . . . . . . . 1 2 1 1 1 1 1 1 1 1 1 1 1 1 1 1 1 1 1 . . . .. . . . . . . . . . . . . . . . . . . . . . . . . . . 1 .. . 1 1 1 1 1 1 . . . . 1 1 1 4 4 1 . . 5 4 ... . . . . 1 . 2 .... 1 .. 2 1 . . the label should also be ordered. BE SURE TO PROVIDE MODEL AND SERIAL NUMBER WHEN ORDERING REPLACEMENT PARTS. OM-1586 Page 81 Drive Roll 083489 083490 053708 Roll Kit 070 . UC-GROVE 151 4 077 Roll Kit 151 2 . Roll Kit 4 Kits 2 Drive . U-GROVE Roll Roll Kit 151 151 061 151 062 151 4 Roll Kit Drive 151 2 16-1. 151 Table 151 15 063 064 151 132960 132961 132962 15 057 15 058 15 059 132963 15 06 151 Roll Kit 15 024 15 025 15 03 15 031 026 027 151 151 032 033 151 151 2 .~E~-o .~ .E E~c~ 149518 149518 1509 3 1509 3 053704 053703 053705 15 04 15 041 15 042 15 048 15 049 15 05 . 151 05370 053697 053698 05369 Roll Kit 15 06 15 067 15 068 151 087130 053695 4 15 065 151 Drive Roll . a) 079 0720 053701 053702 053706 037 036 15 038 039 045 044 15 046 047 Drive Roll And 15 078 151 053712 15 076 -0527-B S 15 083 Rol s Drive 4 Or 2 Roll Kit Wire 072 132958 132957 132956 13295 13295 053 052 15 054 055151 15 056 Drive Roll VK-GROE 15 071 053710 053709 05371 15 073 15 074 15 075 15 08 15 081 15 082 15 028 15 034 15 069 with along .125, 05370 8-32 15 043 Setscrew x 15 051 612 w/604 Guide Aritwear 029 233 045 151 And 035 Guide, 151 149518 149519 149519 149520 149520 1509 3 1509 4 1509 4 1509 5 1509 5 149520 149521 149521 1509 5 1509 6 1509 6 14952 Intermdia 1509 7 Guide, D-64 Inlet Metric . Size Wire 0.6m 0.8m Fraction .023- 5in .03 in. 0.9m .035in. 1. m .045in. 1.3m 1.6m .052in. ~ 2.0m 1.8m .068-72in in. 5/64 2.4m 2.8m (.079in.) (.0941n.) 3.2m (15) An & D-62 for Contains Required Kit Each Kits 2 0 (n 0) -D 0) (0 CD 0) I)
advertisement
Related manuals
advertisement