advertisement
▼
Scroll to page 2
of
102
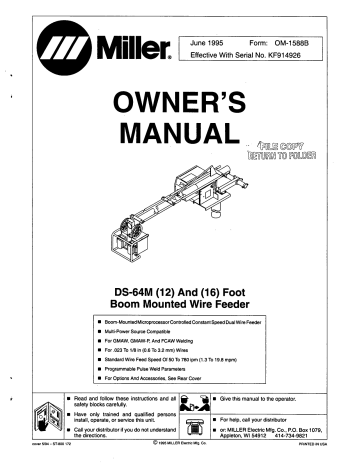
Miller. June 1995 Form: OM-1588B Effective With Serial No. KF91 4926 1 OWNERS MANUAL ~ c~~' ~F'L DS-64M (12) And (16) Foot Boom Mounted Wire Feeder Boom-Mounted Microprocessor Controlled Constant S Multi-Power Source Compatible For GMAW, GMAW-P, And FCAW For .023 To 1/8 in (0.6 Standard Wire Feed Programmable For S Options To 3.2 Speed Of 50 To 780 ipm (1.3 To cover 5/94 ST-800 172 mpm) And Accessories, See Rear Cover ~- ~ ~i1~A trained and qualified persons or service this unit. Call your distributor if you do not understand the directions. ' Give this manual to the operator. For install, operate, S 19.8 Pulse Weld Parameters Read and follow these instructions and all blocks carefully. only Welding mm) Wires safety Have Speed Dual Wire Feeder I~J 1995 MILLER Electric or: help, call your distributor MILLER Electric Mfg. Co., P.O. Box 1079, WI 54912 414-734-9821 Appleton, MIg. Co. PRINTED IN USA l I J L MILLERS TRUE BLUETM LIMITED WARRANTY (Equipment with This limited warranty Effective January 1,1995 serial number preface of KD a supersedes sli previous MILLER warranties and is exclusive LIMITED WARRANTY Subiect to the terms and conditions below, MILLER Electric MIg. Co., Appleton, Wisconsin, warrants to its original retsil purchaser that new 6. periods listed below, MILLER wilt repair or replace any war components that fail due to such defects in material or workmanship. MILLER must be notified in writing within thirty (30) days of such defect or failure, at which time MILLER will provide instructions on the warranty claim procedures to be ranted parts newer) with no other guarantees or warranties 90 expressed or implied. Parts and Labor Days MIG Gufls/TIG Torches MILLER equipment sold after the effective date of this limited warranty is free of de tects in material and workmanship at the time it is shipped by MILLER. THIS WAR RANTY IS EXPRESSLY IN LIEU OF ALL OTHER WARRANTIES, EXPRESS OR IMPLIED, INCLUDING THE WARRANTIES OF MERCHANTABILITY AND FIT NESS. Within the warranty or APT, ZIPCUT & PLAZCUT Model Plasma Cutting Torches Remote Controls Accessory Kits Replacement Parts MILLERS True BIueTM Limited or 1. Items furnished Warranty by MILLER, shall not but manufactured trade accessories. These items are covered lollowed. apply by to: by others, such as the manulacturers engines or warranty, if any. MILLER shall honor warranty claims on warranted equipment listed below in the event of Such a failure within the warranty time periods. All warranty time periods start on the date that the equipment was delivered to the original retail purchaser, or one year after the equipment is sent to a North American distributor or eighteen months after the equipment is sent to an International distributor. 5 Years Parts 3 Original 3 Years Consumable components; such as contact tips, cutting nozzles, contactors and relays or parts that fail due to normal wear. 3. Equipment Years Labor (input and output rectifiers or equip Power Sources In the event of Semi-Automatic and Automatic Wire Feeders warranty claim covered by this warranty, the exclusive remedies option: (1) repair; or (2) replacement; or, where authorized in appropriate cases, (3) the reasonable cost of repair or replace Stan authorized MILLER service station; or (4) payment of orcredit for the pur a shall be, at MILLERS writing by MILLER in Supplies Inverter Power other than MILLER. MILLER PRODUCTS ARE INTENDED FOR PURCHASE AND USE BY COMMER CIAL/INDUSTRIAL USERS AND PERSONS TRAINED AND EXPERIENCED IN THE USE AND MAINTENANCE OF WELDING EQUIPMENT. Transformer/Rectifier Power Sources Cutting by any party only) Parts and Labor Plasma Arc that has been modified ment that has been improperly installed, improperly operated or misused based upon industry standards, or equipment which has not had reasonable and necessary maintenance, or equipment which has been used for operation outside of the specifications for the equipment. main power rectifiers Inverters 2. 2. Intellitigs ment Robots chase price (less reasonable depreciation based upon actual use) upon return of the at customers risk and expense. MILLERS option of repair or replacement F.O.B., Factory at Appleton. Wisconsin, or FOB, ala MILLER authorized ser vice facility as determined by MILLER. Therefore no compensation or reimburse goods 3. 2 Years Parts and Labor Engine Driven 4. Generators Welding (NOTE: Engines Air will be are warranted ment for separately by the engine manufacturer.) Compressors 1 Year transportation costs of any kind will be allowed. TO THE EXTENT PERMITTED BY LAW, THE REMEDIES PROVIDED HEREIN ARE THE SOLE AND EXCLUSIVE REMEDIES. IN NO EVENT SHALL MILLER BE Parts and Labor LIABLE FOR DIRECT, INDIRECT, SPECIAL, INCIDENTAL OR CONSEQUENTIAL DAMAGES (INCLUDING LOSS OF PROFIT), WHETHER BASED ON CON TRACT, TORT OR ANY OTHER LEGAL THEORY, Motor Driven Guns Process Controllers IHP5 Power Sources Water Coolant ANY EXPRESS WARRANTY NOT PROVIDED HEREIN AND ANY IMPLIED WAR RANTj, GUARANTY OR REPRESENTATION AS TO PERFORMANCE, AND ANY REMEDY FOR BREACH OF CONTRACT TORT OR ANY OTHER LEGAL Systems HF Units THEORY WHICH, BUT FOR THIS PROVISION, MIGHT ARISE BY IMPLICATION, OPERATION OF LAW, CUSTOM OF TRADE OR COURSE OF DEALING, IN CLUDING ANY IMPLIED WARRANTY OF MERCHANTABILITY OR FITNESS Grids Spot Welders Load Banks FOR PARTICULAR PURPOSE, WITH RESPECT TO ANY AND ALL EQUIPMENT FURNISHED BY MILLER IS EXCLUDED AND DISCLAIMED BY MILLER. SDX Transformers Running Gear/Trailers Plasma Cutting Torches (except APT, ZIPCUT Tecurnseh Engines Deutz Engines (outside North America) Field Options & PLAZCUT Models) Some states in the U.S.A. do not allow limitations of how lasts, or the exclusion of incidental, indirect, special or long an implied warranty consequential damages, so the above limitation or exclusion may not apply to you. This warranty provides spe cific legal rights, and other rights may be available, but may vary from state to state. (NOTE: Field options are covered under True BIueTM for the remaining warranty period of the product they are installed in, or for a minimum of whichever is greater.) one year In Canada, legislation in some provinces provides for certain additional warranties remedies other than as stated herein, and to the extent that they may not be waived, the limitations and exclusions set ouf above may not apply. This Limited Warranty provides specific legal rights, and Other rights may be available, but may or 6 Months Batteries province to province. 1. RECEIVING-HANDLING unpacking equipment, check carton for any damage that may have occurred during shipment. File any claims for loss or damage delivering carrier. Assistance for filing or settling claims may be obtained from distributor and/or equipment manufacturers Transportation Department. Before with the When requesting following spaces to nameplate. Use the or information about this record Model equipment, always provide Model Designation and Serial or Style Number. Designation and Serial or Style Number of your unit. The information is located on the rating label Model _________ Serial or Style No. Date of Purchase miller 6/95 ERRATA SHEET September 22, FORM: OM-1588B 1995 Use above FORM number when L After this manual appearing was printed, refinements in ** Parts List as exceptions to data Replaced No. With 89-3.... 139 590 Added 89- PARTS LIST follows: Part 89-2.... 010910 **First occurred. This sheet lists extra manuals. later in this manual. CHANGES TO SECTION 16 Change equipment design ordering Description .... 010910 .. .... 079 621 .. .... 079 622 .. WASHER, (qtychg) (Effw/KF970957) PULLEY, V sgl grv (Eff w/KF970957) WASHER, shld .318 ID x .750 OD x .254thk (Eff w/KF970957) digit represents page no digits following dash represent item no. BE SURE TO PROVIDE MODEL AND SERIAL NUMBER WHEN ORDERING REPLACEMENT PARTS. Quantity 6 1 .... 4 ARC WELDING SAFETY PRECAUTIONS WARNING a ARC WELDING be hazardous. can PROTECT YOURSELF AND OTHERS FROM POSSIBLE SERIOUS INJURY OR DEATH. KEEP CHILDREN AWAY. PACEMAKER WEARERS KEEP AWAY UNTIL CONSULTING YOUR DOCTOR. Inwelding, as in most jobs, exposure to certain hazards occurs. Welding is safe when precautions are taken. The safety information given below is only a summary of the more complete safety information that will be found in the Safety Standards listed on the next page. Read and follow all Safety Standards. HAVE ALL INSTALLATION, OPERATION, MAINTENANCE, AND REPAIR WORK PERFORMED ONLY BY QUALIFIED PEOPLE. ELECTRIC SHOCK can terminal in disconnect box kill. Touching live electrical parts can cause fatal shocks or severe bums. The electrode and work circuit is electrically live whenever the output is on. The input power circuit and machine internal circuits are also live when power is on. In semiautomatic or automatic wire welding, the wire, wire reel, drive roll housing, and all metal parts touching the welding wire are electrically live. Incorrectly installed or improperly grounded equipment is a hazard. 7. When Do not Do not If earth 6. Always verify the supply ground power cord ~ check and be sure ground wire is properly connected input Arc rays from the welding process produce intense visible and invisible (ultraviolet and infrared) rays that can bum eyes and skin. Noise from some processes can damage hearing. Chipping, grinding, and welds cooling throw off pieces of metal or slag. NOISE 1. Use with r ear plugs or ear muffs if noise level is fumes and gases can 17. If inside, ventilate the 2. area and/or use exhaust at the arc 3. 4. CYLINDERS can explode if damaged. 1. Protect compressed gas cylinders from excessive heat. slag, open flames, sparks, and arcs. mechanical shocks, 2. Installcylindersinanuprightpositionbysecuringtoastationary 3. support or cylinder rack to prevent falling or tipping. Keep cylinders away from any welding or other electrical circuits. or with cable wonc worktable good as near Wear a welding metal-to-metal the weld helmet fitted with Z49.1 and Z87.1 listed in 3. 4. as contact to oractical. a proper shade of filter to Wear Safety Standards). approved safety glasses with side shields. Use protective screens or barriers to protect others from flash glare; wam others not to watch the arc. Wear protective clothing made from durable, flame-resistant material (wool and leather) and foot protection. and 5. Work in only if it is well ventilated, or while air-supplied respirator. Always have a trained watchperson nearby. Welding fumes and gases can displace air and lower the oxygen level causing injury or death. Be sure the breathing air is safe. Do not weld in locations near degreasing, cleaning, or spraying operations. The heat and rays of the arc can react with vapors to form highly toxic and irritating gases. Do not weld on coated metals, such as galvanized, lead, or cadmium plated steel, unless the coating is removed from the wearing to Shielding gas cylinders contain gas under high pressure. If damaged, a cylinder can explode. Since gas cylinders are normally part of the welding process, be sure to treat them carefully. Clamp protect your face and eyes when welding or watching (see ANSI out of the fumes. Do not breathe the fumes. welding fumes and gases. If ventilation is poor, use an approved air-supplied respirator. Read the Material Safety Data Sheets (MSDS5) and the manufacturers instruction for metals, consumables, coatings, cleaners, and degreasers. a safety hamess if working above floor level. Keep all panels and covers securely in place. ARC RAYS be hazardous to your health. remove a workpiece 6. 2. your body. over grounding of the workpiece is required, ground it directly separate cable do not use work clamp or work cable. Wear . Keep your head drape cables 15. £~ 1. poorly spliced Use only well-maintained equipment. Repair or replace damaged parts at once. Maintain unit according to manual. high. FUMES AND GASES can be hazardous to your health. Welding produces fumes and gases. Breathing these or 14. 5. approved use. damaged, undersized, Do not touch electrode if you are in contact with the work, ground, or another electrode from a different machine. ground ARC RAYS can burn eyes and skin; NOISE can damage hearing; FLYING SLAG OR SPARKS can injure eyes. worn, 13. 16. that to use cables. 11. Manual and national, state, and local codes. grounding Turn off all equipment when not in 12. Owners attach proper double-check connections. 9. 10. Do not touch live electrical parts. 5. to a Frequently inspect input power cord for damage or bare wiring replace cord immediately if damaged bare wiring can kill. Wear dry, hole-free 4. plug is connected outlet. 8. 1. 3. that cord making input connections, conductor first 2. insulating gloves and body protection. Insulate yourself from work and ground using dry insulating mats or covers big enough to prevent any physical contact with the work or ground. Disconnect input power or stop engine before installing or servicing this equipment. Lockout/tagout input power according to OSHA 29 CFR 1910.147 (see Safety Standards). Properly install and ground this equipment according to its or properly grounded receptacle 7. a confined space an weld area, the area is well ventilated, and if necessary, while wearingan air-supplied respirator. The coatings and any metals containing these elements can give off toxic fumes if welded. 4. 5. 6. 7. Never drape welding torch over a gas cylinder. welding electrode to touch any cylinder. Never weld on a pressurized cylinder explosion will result. Use only correct shielding gas cylinders, regulators, hoses, and fittings designed for the specific application; maintain them and associated parts in good condition. Never allow a a 8. Turn face away from valve outlet when 9. Keep protective cap in 10. use in opening cylinder valve. place over valve except when cylinder is orconnected for use. Read and follow instructions on compressed gas cylinders, associated equipment, and CGA publication P-i listed in Safety Standards. 5:1.1.1 2194 WELDING can cause fire explosion. or closed containers, such as tanks, drums, Welding or pipes, can cause them to blow up. Sparks can fly off from the welding arc. The flying sparks, hot workpiece, and hot equipment can cause fires and burns. Accidental contact of electrode to metal Be 6. aware that can cause welding fire ceiling, floor, bulkhead, on a or partition the hidden side. on on objects can cause sparks, explosion, overheating, or fire. Check and be sure the area is safe before doing any welding. 1. Protect yourself and others from 2. Do not weld where 3. Remove all flammables within 35 ft 4. 5. flying sparks and hot metal. flying sparks can strike flammable material. (10.7 m) of the welding arc, If this is not possible, tightly cover them with approved covers. Be alert that welding sparks and hot materials from welding can easily go through small cracks and openings to adjacent areas. Watch for fire, and keep a fire extinguisher nearby. Do not weld 7. Connect work cable to the work 8. ENGINE EXHAUST GASES unknown Do not 9. Engines produce paths can kill: tanks, drums, close to the as and causing or welding area as electric shock and fire hazards. welder to thaw frozen use pipes. Remove stick electrode from holder 10. contact tip cut off or welding wire at when not in use. 11. Wearoil-free protective garments such as leather gloves, shirt, cuffless trousers, high shoes, and a cap. 12. Remove any combustibles, such as a butane lighter or matches, from your person before doing any welding. ENGINES harmful exhaust gases. as practical to prevent welding current from traveling long, possibly WARNING a closed containers such on pipes, unless they are properly prepared according toAWS F4.1 (see Safety Standards). 1. Use 2. If used in equipment can heavy be hazardous. outside in open, well-ventilated a closed area, vent engine areas. exhaust outside and away from any building air intakes. ENGINE FUEL cause can fire or explosion. Engine fuel is 1. Stop engine and 2. Do not add fuel while open flames. 3. Do not overfill tank 4. Do not engine. highly flammable. let it cool off before smoking or MOVING PARTS checking if unit is allow room for fuel to expand. spill fuel. If fuel is spilled, clean up before starting or near adding fuel. any sparks or Injury. can cause 3. Have 4. troubleshooting as necessary. To prevent accidental starting during servicing, negative () battery cable from battery. only qualified people guards remove or covers for maintenance and Moving parts, such as fans, rotors, and belts can fingers and hands and catch loose clothing. cut 1. Keep all doors, panels, securely in place. 2. Stop eng ne before covers, and installing or Batteries contain acid and generate explosive iases. STEAM AND COOLANT can PRESSURIZED HOT burn face, eyes, and 6. Reinstall panels or guards and close doors when servicing is finished and before starting engine. 1. Always wear Stop engine 2. It is best to check coolant level when to avoid scalding. engine is cold a clothing, face shield when before working disconnecting or on a battery. connecting battery cables. 3. Do not allow tools to 4. Do not 5. Observe correct polarity (+ and ) 1. If the use cause welder to engine is warm sparks when working on a battery. charge and batteries checking on or jump start vehicles. batteries. is needed, follow steps 2 and 3. 2. skIn. moving Keep hands, hair, parts. connecting unit. SPARKS can cause BATTERY GASES TO EXPLODE; BATTERY ACID can burn eyes and skin, and tools away from 5. guards closed and loose disconnect 3. safety glasses and gloves and put a rag over cap. slightly and let pressure escape slowly before completely removing cap. Wear Turn cap PRINCIPAL SAFETY STANDARDS Safety in Welding and Cutting, ANSI Standard Z49. 1, from American Welding Society, 550 N.W. LeJeune Rd, Miami FL 33126 Safety and Health Standards, OSHA 29 CFR 1910, from Superinten dent of Documents, U.S. Government Printing Office, Washington, D.C. 20402. Recommended Safe Practices for the Preparation for Welding and Cutting of Containers That Have Held Hazardous Substances, Ameri can Welding Society Standard AWS F4. 1, from American Welding So Safe Handling of Compressed Gases in Cylinders. CGA Pamphlet P-1,from Compressed Gas Association, 1235 Jefferson Davis High way, Suite 501, Arlington, VA 22202. Code for Safety in Welding and Cutting, GSA Standard Wi 17.2. from Canadian Standards Association. Standards Sales. 178 Rexdale Bou levard. Rexdale. Ontario, Canada M9W 1 R3. ciety, 550 N.W. LeJeune Ad, Miami, FL 33126 Safe Practices For Occupation And Educational Eye And Face Protec tion, ANSI Standard Z87. 1, from American National Standards Institute, 1430 Broadway, New York, NY 10018. National Electrical Code, NFPA Standard 70, from National Fire Pro tection Association, Batterymarch Park, Quincy, MA 02269. Fire Protection Association, srl.1.1 V94 Cutting And Welding Processes, NFPA Standard 51 B, from National Batterymarch Park, Quincy, MA 02269. CONSIGNES DE SECURITE MISE EN GARDE a A LARC POUR LE SOUDAGE A LARC LE SOUDAGE pout Œtre dangereux. SE PROTEGER ET PROTEGER LES AUTRES CONTRE LES BLESSURES GRAVES VOIRE MORTELLES. TENIR LES ENFANTS A LECART. LES PERSONNES QUI PORTENT UN STIMULATEUR CARDIAQUE NE DOIVENT PAS NON PLUS SAPPROCIIER DU POSTEDE SOUDAGE A MOINS DAVOIR CONSULTE UN MEDECIN. Le soudage, comme Ia plupart des travaux, prØsente certains dangers. Par contre, to soudage peut Øtre ettectuØ en toute sØcuntØ quand on prend los qui simposent. Los consignes de sØcuntØ donnŁes ci-aprŁs ne font quo rØsumor linformation contonue dans los normes do sØcuntØ OnumOrØes mesures a Ia page suivante. Lire et respecter toutes ces normes do sØcuntO. LINSTALLATION, LUTILISATION, LENTRETIEN El LES REPARATIONS NE DOIVENT UN CHOC ELEcTRIQUE pout simple 1. Ne Porter des gants et dos vØtements do protection Jamais toucher los piŁces etectnques sous 7. En offectuant los raccordemonts dontrØe fixer dabord 10 conducteur do mise a Ia terre appropnØ 01 contro-vŁnfier les connexions. 8. Verifier frØquomment to cordon datimentation pour voir sit nest pas endommage ou dØnudØ romplacer le cordon immØdiatoment sit cable dOnudØ pout provoquer uno est endommagØ un electrocution. 9. Mettre secs no comportant Iatimentation ou arrŒtor le moteur avant do procØdor a do tapparoil. linstatlation, a Ia reparation ou a lentretien DØverrouiller latimontation selon Ia norme OSHA 29 CFR 1910.147 (voir normes do sØcuntØ). 5. 6. Ne pas enrouler les cables autour du corps. Si Ia piŁce soudØe doit Œtre miso ala terre, le faire directement avec no pas utiliser to connecteur do piŁce ou 10 cØble un cable distinct do retour. 13. Ne pas toucher lØlectrodo quand on est en contact avec Ia terre ou une electrode provenant dune autre machine. 14. Nutiliser 15. municipaux. Toujours vØnfior 17. . ~ . - 16. Ia terre du cordon datimentation Verifier et Quo 10 fit do terre du cordon dalimontation est bien LE RAYONNEMENT DE LARC pout brler les yeux et Ia peau. Le BRUIT pout endommager IouIe; les PROJECTIONS DE LAITIER OU LES ETINCELLES peuvent blesser les yeux. Larc do soudage produit des rayons visibles et invisiblos intenses (ultraviolots et infrarougos) qui pouvent brlor los yeux et Ia peau. Le bruit produit par certains procŁdŁs pout endommagor IouIe. Des projections de metal ou de laitier sont produites par le piquago, le meulage ou le refroidissemont dos soudures. Utiliser des boucho-oroittes ou des serre-tOto antibruit to niveau de bruit est ØlovØ. I ~Q V approuvØs vapeurs et des fumOes 2. quit 2. no pas les ventiler le posto de travail ou utiliser un dispositif place niveau do Iarc pour Øvacuer los vapeurs et fumŁes de soudage. masque a serre-tØte muni dun vorre filtrant do nuance pour proteger Ia visage et los yeux quand on soudo ou observe Ia travail do soudago (voir los normes ANSI Z49. 1 01 Z87. I donnØes sous Ia rubrique Principales norrnes de sØcurite). Porter un 3. Porter des lunettes do sØcuntŁ 4. Utitiser des paravents ou des barriŁres do protection pour proteger los personnes a proximitØ contre les coups darc et lØblouissement; avertir los autres personnes do ne pas regarder larc. 5. 5. 4. Consulter los fichos signafetiques et les consignes du fabncant relatives au mØtaux, produits dapport. revŒtements. nettoyants et un 6. approuvØos Porter dos vŒtomenls do protection en tissu et des chaussures do sOcuntØ. avoc Øcrans latOraux. ignifugo durable (tame ot Ne travailler dans un espace confine que sit est bien ventilØ, ou en portant un appareit respiratoire a adduction dairpur. Demander a un observateur ayant recu Ia bonne formation do toujours so lenir a proximitØ. Los vapeurs et fumØes de soudage peuvent doplacer lair 7. pas souder a proximitO dopOrations de dOgraissage, de Ne pas souder sur des mØtaux revŒtus comme lacier galvanisŁ, au p10mb ou cadmiØ a moms quota piŁce nait ØtØ ontiŁrement dØcapOe. quote posto do travail soit bion vontilØ. Sit y a lieu, porter un appareil respiratoire a adduction dair pur. Les revØtements et los mŁtaux qui contiennont do tels ŁlŁments pouvont dogager des vapeurs toxiquos lors du soudage. degraissants. LES BOUTEILLES peuvent exploser sI elles No nettoyage ou de pulvØnsation. La chateur et los rayons do larc peuvent reagir avec los vapours pour former des gaz hautement toxiques et irritants. appareil respiratoire a Si Ia ventilation ost mauvaiso, utiliser adduction dair pur approuvØ. jamais jamais jamais poser un chatumeau soudeur sur une bouteille do gaz. laisser une electrode do soudago toucher une bouteille. 4. Ne 5. Ne Los bouteillos contenant des gaz do protection sont a Une bouteillo endommagee pout haute pression. exploser. Etant donnØ que los bouloilles do gaz font norrnalement partie du materiel de soudage. les traitor avec le plus grand soin. 6. No 7. Nutilisor quo dos boutoilles do gaz de protection, des dØtendeurs, des tuyaux souplos ot dos raccords appropriŁs concus pour application particuliŁre; consorvor ces matØriels at leurs piŁces en los bouteillos do gaz comprimØ contre Ia chaleur intense, les chocs, te tail ier, les flammes nues. les Øtincetles el larc. 8. ~ sont .z~. endommagØes. ProtØgor Placer los bouteiltes a Ia vorticale un 3. en appropnee est 3. 2. un Maintenir solidement do~gene et causer dos blessures graves voire mortelles. Sassurer que lair est propre a Ia respiration. respirer. A linlØnour, 1. hamais de sŁcuntØ quand on travaille en hauteur. place tous los panneaux at capots. Fixer le cable do retour do faon ~ obtonir un bon contact mØtal-mØtal avec Ia piŁce a souderou Ia table do travail, le plus pres possible de Ia Porter et abaisser le niveau Garder Ia tŒte a lextrieur des vapeurs et des fumŁos et ~ remplacer lappareil cuir) LES VAPEURS ET LES FUMEES peuvent ºtre pour Ia sante. Le soudage produit des dangereux do respirer. Ia RAVONNEMENT DE LARC dangereuses 1. au si piŁce. soudure. BRUIT 1. RØparer ou quun materiel en bon Øtat. Entretenir les piŁces endommagØes. conformØment a ce manuel. sur-le-champ Installer et mettre a Ia terre correctoment cet appareit confomiØment a son manuel dulilisation et au codes nationaux, provinciaux et sassurer quand on ne lutilise pas. uses, endommagØs. do grosseur 11. Couper 4. hors tension No pas utiliser des cables insuffisante ou mal ØpissOs. 12. Sisoler do Ia piŁce et de Ia terre au moyen de tapis ou dautros moyens isolants suffisamment grands pour empecher le contact physique Øventuel avec Ia piŁce ou Ia terre. lappareil 10. tension. pas de trous. 3. OUALIFIEES est raccordŁe a uno pnso correctoment mise a Ia terre. contact avec des 2. DES PERSONNES raccordO a Ia borne do terre du sectionnour ou quo Ia fiche du cordon tuer. piŁces Ølectnques pout provoquer une Olectrocution ou des blessures graves. LØlectrode et to circuit de soudago sont sous tension des que Iapparoil est surON. Le circuit dentrØe et les circuits intemos de Iappareit sont egalement sous tension a ce moment-l. En soudage semi-automatique ou automatique, le fit, le dØvidoir. to logement dos galets dentrainemont ot los piŁces mØtalliques en contact avec to fit do soudago sont sous tension. Des matØnels ma! installØs ou mat mis a Ia terre prØsentont un danger. Un ETRE CONFIES QuA chariot pour Øviter quelles ne en les fixant a tombent Tenir les bouteitles a IØcart du poste de electriques. un ou no soudage support fixe ou a bascuient. ou dautres sur une bouteille sous pression : elte oxploserait. bon Łtat. Eloigner 10 visage de Ia sortie du robinet do Ia bouteille quand on louvre. 9. 10. circuits souder Replacer to chapeau sur Ia bouteille aprŁs utilisation. Lire at suivre los consignes relatives aux bouteitles do gaz compnme, au materiel connexe ainsi quo Ia publication P-l de Ia CGA donnØe sous Ia rubnque Pnncipales normes de scuritØ. srl.I,1 2/94 LE SOUDAGE Incendle ou une 5. Prondre garde proximitØ. No pas soudor sur des recipients fermØs comme des reservoirs, dos fts ou des tuyaux: us pouvent exploser. Des Larc do soudage pout produire des Øtincelles. Øtincelles, une piŁce chaudo et un materiel chaud des incendios et des blossures. Le peuvent provoquor do lŁlectrode des objets contact accidentel sur motalliques pout produire dos Øtincelles, lexplosion, Ia surchaufte ou un incendie. Sassurer quo 10 lieu no prØsonte pas do danger avant deflectuer le soudago. 6. Se rappelerquo si Ion soude sur un plafond, un planchor, ou autre, lo lou peut prendre do lautre ctØ. 7. No pas souder sur des recipients fermØs commo des reservoirs, des fOts ou dos tuyaux a moms quils ne soient prepares do facon appropnee conformØmont ala norme F4.1 do lAWS (voir Ia rubnque peut causer un explosion. 1. So protØgeretprotegerles personnos a metal chaud. 2. Ne pas souder dans un ondroit o des matOriaux inflammables. los Øtincollos pouvent atteindro Prendro 4. garde quo los Øtincollos et los projections no pØnØtront dans adjacentos en sinfiltrant dans dos petites fissures et No pas utiliser le chalumoau soudeur pour 11. produisent LE CARBURANT DES MOTEURS ou une des gaz de 12. 1. peut provoquer un Incendie peuvent causer piŁces en mouvomont comme los ventilateurs, los rotors et los courroles peuvent couper los doigts otles mains ot happer los vŒtements amples. place. ArrŒter 10 moteur avant do mettro disoositif. place ou do raccorder soi comme un bnquet a un Øcran facial utilise 4. un danger. moteur dans un local ferrnO, Øvacuer los gaz a lextØneur et loin des pnses dair du btiment. in ras lappareil bord se trouve prØvoir de a proximitØ lospace pour Ia Ne pas renverser du carburant. Si on ronverso du carburant, avant do faire dØmarrer 10 moteur. nottoyer los Iieux 3. Seules des personnes 4. qualifiees los capots pour faire lentretien doivent dØmonter los protoctours ou los reparations nØcessairos. Pour ompOcher un demarrage accidontol dun systŁme pendant lontrotion ou los reparations, dØbranchor lo cable negatif () do Ia battono. Eloigner los des un piŁces mains, los chevoux, los vŒtemonts amplos et los outils en mouvement. Replacer los capots ou les protecteurs et reformer les portes uno fois Ientrotion ot los reparations terminØs ot avant de faire dØmarrer 10 moteur. Los batteries contiennent des vapeurs explosives. Toujours ~ on Ne pas remplir le reservoir a dilatation du combustible. 6. en Si 3. Sassurer quo los portes, los panneaux, los capots et los protectours LES ETINCELLES peuvent faIre EXPLOSER LE GAZ DES BA1TER~ES; LELECTROLYTE peut brler Ia peau et es yeux. 1. tuyaux. dans dos lioux ouvorts at bien Ne pas fumer en faisant le. plein ou si dØtincelles ou do flammos nues. 5. sont bien fermØs ot bion A leur Utiliser le materiel a IoxtØneur, ventilØs. ou Los + sur presenter 2. explosion. LES PIECES EN MOUVEMENT des blessures. 2. Ne pas porter des matiŁres combustibles ou des allumettes quand on soude. dechappement chapp oment focus. ArrOter lo moteur ot 10 laissor refroidir avant de verifier lo nivoau de carburant ou de rofaire le plein. 1. dos Porter dos vOtoments do protection non huileux comme dos gants en une chemise Øpaisse, dos pantalons sans rovers, dos chaussures montantos of un casque. LES MOTEURS peuvent Le carburant est hautemont inflammable. 1. degoler Enlever lØlectrode enrobØo du porte-electrode ou couper le fil de soudage au ras dii bec contact quand on no Iutilise pas. cuir, 2. Les motours ~ sØcuntØ). gaz LES GAZ DECHAPPEMENT peuvent tre mortels. r cloison 9. MISE EN GARDE a do une Raccorder 10 cable do retour a Ia piŁce, lo plus prØs possible do Ia zone do soudage, pour empOcher quo le courant do soudago ne suive une trajoctoiro longue et Øventuollemont inconnue at quil no provoque dos nsques dØlectrocution et dincondio. 10. dos zones ouverturos. normes avoir Un extinctour ~ 8. proximitØ dos Øtincelles etdu Enlovertoutes los matiŁres inflammablos dans un rayon do moms do 10 m de larc. Si cola nest pas possible, bien los rocouvnren utilisant dos bathes approuvees. 3. Pnncipalos toujours incendios et aux un quand on produit acido et travaille sur une degagent battene. VAPEUR ET LE DE LIQUIDE REFROIDISSEMENT BRULANT SOUS PRESSION peuvent brler Ia peau et lee yeux. LA II vaut mioux verifier 10 nivoau du liquide do ref roidissoment quand 10 moteur ost froid af in &Øviter les brUlures. 2. ArrØter le motour avant do brancher Ia battene. 3. Ne pas faire dos Øtincolles battene. 4. No pas utiliser Ia source do courant do soudage pour batteries ou pour faire dØmarror un vØhicule. 5. Ne pas intervertir Ia lAmoflcan Welding polaritØ do dØbrancher los cAbles do los outits quand on travaille sur une charger los des batteries. 1. Si Ion doit verifier 10 nivoau quand le motour est chaud, suivro los 2. Øtapos 2013. Porterdoslunottesdosecuflteetdosgantsetplacorunchiffonsurle bouchon. 3. Toumor lentoment 10 bouchon et laissor Ia prossion lontement avant donlever complOtoment lo bouchon. PRINCIPALES NORMES DE Safety in Welding and Cutting, normo ANSI Z49.1,do Society, 550 N.W. Lojoune Rd, Miami FL 33126 avec ou sechapper SECURITE Safe Handling of Compressed Gases in Cylinders, CGA Pamphlet P-ide Ia Compressed Gas Association. 1235 Jefferson Davis Highway, Suite 501, Arlington, VA 22202. and Health Sandards, OSHA 29 CFR 1910, du Supenntondonl of Documents, U.S. Government Pnnting Office, Washington, D.C. 20402. Safety Recommended Safe Practice for the Preparation for Welding and Cutting of Containers That Have Held Hazardous Substances, norrne AWS F4.1. do IArnoncan Welding Society, 550 N.W. Lojoune Rd, Miami FL 33126 NationalElectncal Code, NFPA Standard 70, do Ia National Fire Protection Association. Batterymarch Park, Quincy, MA 02269. srl.1.1 2/94 Regles de sØcunfØ en soudage. coupage et procddds connexes, norme CSA W117.2, do lAssociation canadienne do norrnalisation, vento do normes, 178 Rexdalo Boulovard, Roxdale (Ontario) Canada M9W 1 R3. Safe Practices For Occupation And Educational Eye And Face Protection, ANSI Z87.1, de IArnencan National Standards Institute. 1430 Broadway, Now York, NY 10018. norrne and Welding Processes, norme NFPA 51 B, do Ia National Fire Protection Association, Batterymarch Park, Qumncy, MA 02269. Cutting EMF INFORMATION Considerations About Fields NOTE ~ Welding And The Effects Of Low Frequency Electric And Magnetic The To reduce of the U.S. following is a quotation from the General Conclusions Section Congress, Office of Technology Assessment, Biological Effects of Power Frequency Electric & Magnetic Fields OTA-BP-E-53 (Washington, DC: U.S. Background Pape4 Government Printing Office, May 1989): . there is now a very large volume of scientific findings based on experiments at the procedures: . magnetic fields in the workplace, 1. Keep cables close together by twisting 2. Arrange 3. Do not coil 4. Keep welding practical. 5. Connect work clamp to workpiece cables to one or use taping the following them. side and away from the operator. . or drape cables around the body. cellular level and from studies with animals and people which clearly establish that low frequency magnetic fields can interact with, and produce changes in, biological systems. While most of this work is of very high quality, the results are complex. Current scientific understanding does not yet allow us to interpret the evidence in a single coherent framework. Even more frustrating, it does not yet allow us to draw definite conclusions about questions of possible risk or or to offer clear science-based advice on avoid strategies to power source and cables as as far away as close to the weld as possible. About Pacemakers: The above procedures are among those also normally recommended for pacemaker wearers. Consult your doctor for complete information. minimize potential risks. modlO.1 4/93 TABLE OF CONTENTS SECTION 1 SAFETY INFORMATION SECTION 2 SPECIFICATIONS SECTION 3 INSTALLATION 2 3-5. Equipment Connection Diagram Installing Swivel Into Pipe Post Installing Control Box Onto Swivel Installing Boom And Reel Support Installing Wire Guide Extension 3-6. Wire Guide And Drive Roll Installation 3-7. Welding 3-8. Wire Feed Motor And Gas Valve Control Connections 6 3-9. Control Connection 7 3-1. 3-2. 3-3. 3-4. 3-10. 2 3 3 4 4 6 Gas And Weld Cable Connections 3-12. Shielding Removing Safety Collar And Adjusting Welding Wire Installation 3-13. Motor Start Control 3-11. 3-14. 3-15. 5 Gun Connections 8 Boom 9 10 11 Control Tilt Bracket Adjusting Threading Welding 12 Wire 12 SECTION 4- GLOSSARY 14 SECTION 5- OPERATION 16 5-1. Front Panel Controls 5-2. Side Panel Controls 19 5-3. Rear Panel Controls 20 5-4. Setting SECTION 6 Switches On 450 Ampere lnverter Model Welding Power Source STEPPING THROUGH THE MICROPROCESSOR CONTROLS 6-1. Front Panel 6-2. Side Panel SECTION 7 17 Microprocessor Controls Microprocessor Push Buttons STANDARD PULSE WELDING PROGRAMS SECTION 8- GE111NG STARTED 8-1. 8-2. Welding With Only Front Panel Controls Setting Sequence Pulse Welding Parameters On Side Panel Display 21 22 22 24 27 35 36 37 OM-15885 -6/95 SECTION 9 9-1. 9-2. 9-3. 9-4. TEACHING A PULSE WELDING PROGRAM Pulse Waveform 41 Teach Points 42 Explained Explained Teaching A Pulse Welding Program Changing To Adaptive Pulse Welding SECTION 10TEACHING 10-1. 10-2. 41 43 46 A MIG WELDING PROGRAM Changing To MIG Welding Setting Sequence MIG Welding 47 47 Parameters On Side Panel Display 48 SECTION 11 SETTING DUAL SCHEDULE PARAMETERS 51 SECTION 12 USING THE OPTIONAL DATA CARD 53 12-1. 12-2. Installing Data Card Using The Data Card 53 53 SECTION 13SETUP 13-1. 57 Setup Flow Chart Using Setup Displays 57 58 13-13. Selecting Process Capability Selecting Welding Power Source Range Selecting Security Lock Selecting Or Changing Access Code Selecting Voltage Correction Selecting Voltage Sensing Method Selecting Regular Or Hot Arc Start Selecting Type Of Dual Schedule Switch Selecting Trigger Program Select Selecting Remote Increase/Decrease Capability ResettingArcTime 13-14. Using Self Test 13-2. 13-3. 13-4. 13-5. 13-6. 13-7. 13-8. 13-9. 13-10. 13-11. 13-12. 13-15. 13-16. 13-17. 13-18. 13-19. 58 59 60 61 62 62 63 63 64 65 65 66 Units For Wire Feed And Motor Selecting Speed Selecting Bench Or Boom Model Type Resetting Memory Selecting Arc Start/Volt Sense Error Shutdown Selecting Program Name Feature 13-20. Software Version Number SECTION 14- MAINTENANCE & TROUBLESHOOTING Type 67 67 68 68 69 69 70 14-1. Routine Maintenance 14-2. Replacing 14-3. Overload Protection 71 14-4. Error Displays Troubleshooting 72 14-5. The Hub 70 Assembly 71 73 SECTION 15 ELECTRICAL DIAGRAMS 74 SECTION 16 PARTS LIST 78 Figure Figure Figure Figure Figure Figure Figure 16-1. Main 78 16-2. 80 16-3. Assembly Support, Hub & Reel Panel, Front w/Components 16-5. Drive 16-6. 16-7. 81 82 16-4. Control Box Wire Assembly, Panel, Side w/Components Boom Assembly Table 16-1. Drive Roll And Wire Guide Kits 84 87 88 86 SECTION 1 SAFETY INFORMATION - modl.1 2/93 Read all safety messages throughout Obey all safety messages Learn the 1 to avoid this manual. injury. meaning of WARNING and CAUTION. 2 1 Safety Alert 2 Signal Word 2 Symbol WARNING moans possiblo death or serious injury can happen. ;1~ll~Ie~ a CAUTION 3 ELECTRIC SHOCK can kiIi.~ ~ )~ Do not touch live electrical parts. Disconnect input power installing or servicing. 4 before CAUTION MOVING PARTS Keep away from Keep all when panels operaling. can injury Injure. or means possible minor equipment damage can happen. moving parts. and covers closed 57 3 Statement Of Hazard And Result 4 Safety Instructions To Avoid Hazard a READ SAFETY BLOCKS at start of Section 3-1 before proceeding. WARNING 6 5 Hazard 6 Safety Banner Read safety blocks for each sym bol shown. 7 7~{ NOTE Turn Off switch when Symbol (If Available) using high frequency NOTE Special instructions for best not related to safety. oper ation 1-1. Figure Safety Information SECTION 2- SPECIFICATIONS Table 2-1. Wire Feeder Specification Type Of Input Power From Welding Description Single-Phase 24 Volts AC, 10 Amperes, 50/60 Hertz Power Source Maximum Weld Circuit Welding Power Source Rating 100 Volts, 750 Type Constant Amperes, Speed Range Wire Diameter Welding (CC) DC, Standard: 50 To 780 ipm (1.3 To 19.8 mpm) High Speed: 92 To 1435 ipm (2.3 To 36.5 mpm) .023 To 1/8 in Range Processes Gas Metal Arc input Power Cord (0.6 To Height With 4 ft (1.2 m) Net: 207 lb Vertical Lift Of Boom wire feed Metal Arc - Pulse (GMAW-P), Flux Cored (3.7 m) Boom 16 ft 17ft(5.2 m) Ship: are mm) Arc Welding (FCAW) lOft(3.1 m) Weight *These 3.2 (GMAW), Gas 12 ft Maximum Post Duty Cycle With Contactor For GMAW Welding With Contactor For GMAW-P Welding Voltage (CV) DC, Constant Current Wire Feed 100% 21 ft (144 kg) Horizontal To 60 (6.4 m) Horizontal To 60 Above Horizontal speed ranges for GMAW. While Pulse welding, Boom Net: 280 lb (127 kg) Ship: 411 lb (186 kg) (94 kg) 318 lb (4.9 m) wire feed speed ranges may be more Above Horizontal limited (see Section 9). OM-1588 Page 1 SECTION 3-INSTALLATION 3-1. Equipment Connection Diagram WARNING £~ CYLINDERS can Keep cylinders explode if damaged. away trom welding and ELECTRIC SHOCK electrical circuits. Never touch cylinder with HOT SURFACES can Allow gun to cool before kill. TurnOffwirefeederandwelding power source, and before disconnect input making power welding electrode. Always secure cylinder to running gear, wall, other stationary support. can Do not touch live electrical parts. other connections. or The welding wire, drive rolls, drive assembly, and all metal parts touching the welding wire are electrically live when welding or feeding wire using gun trigger. burn skin. touching. Have only qualified persons install this unit. wfwam9.1 1 2/93 Welding Power Source 2 Remote 14 Connections 3 Negative () Weld Output Cable 2 4 (+) 4 Positive Cable 5 Workpiece Weld Output 6 Voltage Sensing Clamp 7 Weld Control 8 Boom 9 Gun 10 Swivel Post And Base 11 Pipe 12 Gas Hoses 13 Gas 12 Supplies 11 9 5T-800 173 Figure OM-1588 Page 2 3-1. Typical System Connections 3-2. Installing Swivel a Into Pipe Post WARNING FALLING OF SPRING PRESSURE RELEASE WITHOUT BOOM ATTACHED can cause serious personal injury. S Do not remove BOOM can serious cause personal injury and equipment damage. Securely mount pipe post to base that can support weight of unit with boom in horizontal position. Use proper equipment for lifting swivel and boom into place. satety collar until instructed to do so. 1 Swingpak 2 Pipe 3 Steel Bolt Base or CBC Cart 5 4 Post With Base Secure as shown using as a mini mum 1/2 in diameter SAE grade 5 steel bolts. 4 Swivel Assembly Insert into pipe post. Lubricate swivel. 2 5 3 Safety Collar Do not remove until instructed to. Tools Needed: ~ 3/4 in 5T.152 382 Figure 3-3. Installing Control 3-2. Swivel Installation Box Onto Swivel 1 Weld Control 2 Bracket 3 Screw Bracket and screws are installed onto bottom of control at factory. 4 Swivel Loosen screws. Place control on swivel and slide forward. Tighten screws. 2 3~ Tools Needed: 4 5T.800 174 Figure 3-3. Control Box Installation OM-1 588 Page 3 3-4. Installing Boom And Reel Support READ SAFETY BLOCKS at start of Sectio n 3-2 bef ore proceeding. 1 Swivel Plates 2 Yoke Remove plates hardware and Set boom into swivel Install pin 5 Bolt bolt, washers, and nut. Tighten hardware, and back bolt off one half tum. 6 Locking Install 1 shown. pin through yoke. Install cot and spread ends. Install 2 as Yoke Pin 4 ter swivel Boom 3 4 from yoke. Knob locking knob but do not tighten. 7 Reel Support Install reel support. Tools Needed: 3/8,3/4in ST-153 170 Figure 3-5. Installing 3-4. Boom Installation Wire Guide Extension 1 1 Wire Guide 2 Bolt Fitting 3 Monocoil Liner 4 Wire Guide Extension Tighten bolt to secure liner in wire guide fitting. Do not overtighten bolt and crush liner. Repeat procedure for opposite side. Tools Needed: ~O 3/Bin 5T-152 383 Figure OM-1 588 Page 4 3-5. WIre Guide Extension Installation 3-6. Wire Guide And Drive Roll Installation A~ WARNING ___ ELECTRIC SHOCK can kill. Do not touch live electrical parts. Turn Off wire feeder and welding power source, and disconnect input power before inspecting or installing. wfwaml.1 2/93 A. Wire Guide Installation When changing wire size or type, check guide size (see Table 16-1). I Drive Rolls Remove drive rolls before install ing wire guides (see Figure 3-7). 2 Wire Guide Loosen wire Securing guide Screws screws. 3 Inlet Wire Guide 4 Intermediate Wire Guide Insert intermediate guide until flange on guide rests against cast ing, and secure with guide screw. Install drive rolls (see Figure 3-7). Repeat procedure for opposite side of wire feeder. 1 Tools Needed: Ref. ST-137 391-F / ST.142 597-A Figure B. 3-6. Wire Guide Installation Drive Roll Installation When check Table 5 changing wire size drive roll or size type, (see 16-1). Carrier 1 Spring Shaft 2 Drive Roll Nut 3 Drive Roll Carrier Turn all nuts one click until lobes of nut line up with lobes of drive roll carrier. 4 Drive Roll Slide drive rolls onto drive roll carri ers. Turn nut one click. 5 Drive Assembly Cover Close 4 cover. Repeat procedure .---1~i for opposite side of wire feeder. 2 3 ST-142 597-A Figure 3-7. Drive Roll Installation OM-1 588 Page 5 3-7. Welding Gun Connections WARNING a ELECTRIC SHOCK can Do not touch live electrical Turn Off wire feeder and kill. parts. welding power source, and disconnect input power before inspecting installing. or wfwaml.1 2/93 1 Drive 2 Gun 3 Gun Connector Assembly Cover Securing Knob Loosen securing knob. Insert gun connector until it bottoms against drive assembly. Tighten knob. 4 Gun Trigger Plug 5 Gun Trigger Receptacle plug into free-hanging re ceptacle and tighten threaded col Insert lar. 6 Trigger Cord 7 Trigger Plug 8 Weld Control 3 Trigger Receptacle 4 Insert plug into receptacle and tighten threaded collar. Repeat procedure for gun on oppo drive assembly. Ref. ST-152 466 / Ref. ST-800 178/ Ref. ST-800 175 Figure 3-8. 3-8. Gun And Trigger Lead Connections Wire Feed Motor And Gas Valve Control Connections I Wire Feed Motor And Gas Valve Control Receptacle 2 Plug From Boom 3 Cord From Boom Insert plug from boom cord into re ceptacle on rear of control, and tighten threaded collar. Repeat procedure for opposite side of weld control. ST-$OO 177/Ref. ST-800 175 Figure 3-9. Boom Connections OM-1 588 Page 6 3-9. Control Connection 1 17-Pin Receptacle Table 3-1) 2 Keyway (See To connect interconnecting cord to receptacle, align keyway, insert plug, and tighten threaded collar. 3 Weld Current Sensor Recep tacle (For Use With Field Op tion Only) 4 35 ft (10.6 m) ing Lead Connect to Voltage Sens workpiece (see Figure 3-1). 5 Threaded Collar 6 14-Pin Plug (see Table 3-2) To connect plug to matching recep tacle on welding power source, align keyway, insert plug, and tight en threaded collar. ST-800 177 / Ref. S-0512 / $-0003-A / S-0628 Figure 3-10. Control Connections With Pin Information Table 3-1. Remote 17 Socket Information REMOTE 17 E ~1b The remaining ~ sockets are SOCket* Socket Information C CC/CV select; +13 to +24 volts dc is CV, 0 volts dc is CC. G Arc control/inductance control; 0 to +10 volts dc. E Actual weld current output M Actual weld F Current feedback from H Voltage signal; +1 volt dc is 100 amps. voltage output signal; feedback from +1 volt dc is 10 volts dc. power source; 0 to +10 volts dc, 1 volt per 100 amperes. welding welding power source; 0 to +10 volts dc, 1 volt per 10 arc volts. not used. Table 3-2. Remote 14-Pin Information REMOTE 14 (3, a ~ ~l~ The OUTPUT Pin Information ~j~* A 24 volts B Contact closure to A G Circuit C +10 volts dc ac. completes 24 volts ac contactor control circuit. (CONTACTOR) AMPERAGE VOLTAGE remaining pins are common for 24 volts input ac circuits. to remote control. 0 Remote control circuit common. E 0 to +10 volts dc output command signal from feeder voltage control. not used. OM-1 588 Page 7 3-10. Shielding Gas And Weld Cable Connections a WARNING CYLINDERS can Keep cylinders explode away from if ELECTRIC SHOCK damaged. welding and other electrical circuits. Never touch cylinder with welding electrode. Always secure cylinder to running gear, wall, other stationary support. can Do not touch live electrical kill. parts. TurnOffwirefeederandwelding powersource,and disconnect input power before inspecting or installing. or BUILDUP OF SHIELDING GAS health or kill. Shut off shielding gas supply can when not in harm use. wam4.1 9/91 /wfwaml.1 2/93 A. Connecting Weld Cables And Gas Hose Tools Needed: ~iI -~ 5/8in Ref. ST-153 175-A The weld cables and shielding gas hoses ex tend lOft (3m) from the boom. If the welding power source or gas supply further from the boom, extend cables and hoses as follows: Bolt together weld cables from welding pow- and boom. Use electrical tape and insulated sleeving to cover connection. er source 5 are 1 Weld Cables 2 Insulated Sleeving Figure OM-1588 Page 8 3-11. Connect boom shielding gas hoses to gas or extension. The hoses from the boom have 5/8-18 right-hand threads. supplies 3 Shielding 4 Boom Y Adapter Connect single end filling of V adapter to gas supply, and connect boom shielding gas Shielding Shielding Supplied Shielding Gas Gas Extension Hose Gas Hose(s) hoses to fittings Gas And Weld Cable Connections on V end of adapter. B. Shielding Gas Connections To Regulator/Flowmeter Obtain gas cylinder and chain to running gear, wall, or other station ary support so cylinder cannot fall and break off valve. 1 1 2 Cap Cylinder Valve Remove cap, stand to side of valve, and open valve slightly. Gas flow blows dust and dirt from valve. Close valve. .2 3 4 Cylinder Regulator/Flowmeter Install 5 so face is vertical. Gas Hose Connection Fitting has 5/8-18 right-hand threads. Install gas hose according to Figure 3-11. Flow Adjust Typical flow rate is 20 cfh (cubic feet per hour). Check wire manufactur 6 OR 6 .2 Argon Gas ers recommended flow rate. Make when 5 4 flow adjust opening cylinder is closed to avoid sure damage to the flowmeter. 7 CO2 Adapter 8 0-Ring Install adapter with 0-ring between and CO2 regulator/flowmeter cylinder. ~ 5T-158 697-A Tools Needed: ~ 5/8,1-1/8 in CO2 Gas - Figure 3-11. Removing Safety a L_~J 3-12. Typical Regulator/Flowmeter Collar And Adjusting Boom WARNING OF SPRING RELEASE PRESSURE WITHOUT BOOM ATTACHED can cause serious personal injury. Do not Installation remove FALLING BOOM can cause serIous personal injury and equipment damage. Adjustment yoke. safety collar until instructed to do so. rod must be threaded 1 fully through Locking Knob Tighten knob to prevent boom movement. Loosen knob to allow boom movement. Change knob position to limit upward movement. Pull boom down slightly and re move safety collar. Boom should balance in any position from hori zontal to 60 degrees above hori zontal. If necessary, adjust boom as follows: Q j Rod~ E Tools Needed: ~ 4 3 2 Increasing Spring Decreasing Spring Pressure For A Pressure For A HeavyGun LightGun 1-1/8in Figure 3-13. Boom 2 Threaded Rod 3 Jam Nut Loosen jam nut and turn threaded rod until boom balances. Tighten jam nut. Be sure several full threads are through yoke to pre vent boom falling. 4 Yoke Retain safety collar for use in dis assembling or moving boom. 8T-142599-B Adjustments OM-1 588 Page 9 3-12. A. Welding Wire Installation Installation Of Spool-Type Wire 1 Retaining Ring 2 Wire 3 Hub Remove 4 spool 4 Spool retaining ring and slide onto hub. Hub Pin Turn spool until hub pin fits hole spool. Reinstall retaining ring. in Repeat procedure for opposite side. 3 2 E ST-153 171 Figure B. Installation Of Optional 3-14. Installation Of Wire Reel And Reel Type Spool-Type Wire Wire 1 Retaining Ring 2 Spanner 8 Nut 3 Lock 4 Wire Retainer 5 Wire Reel 6 Hub 7 Hub Pin 8 Reel 4 Support Remove retaining ring. Pull lock and turn. Remove spanner nut, wire retainer, and wire reel from hub. Lay wire reel assembly face, and install wire as on flat sur shown. spanner nut until lock is in over hole in wire retainer. Pull lock and turn to insert locking pin into wire retainer. Tighten position Slide wire reel assembly onto hub, ~1IIIiI~ . and turn assembly until hub pin is seated in hole in reel. Reinstall re taining ring. fD~ Wire Installation ST-143 478-A / ST-152 463 Figure 3-15. Installation Of Optional Wire Reel And Reel Type Wire OM-1 588 Page 10 C. Hub Tension Adjusting Turn Off unit and welding power source. 1 Hex Nut 2 Spool 2 Grasp spool in one hand and turn while using a wrench to adjust hex nut. When a slight force is needed to turn spool, tension is set. Repeat procedure for opposite side. Tools Needed: ~ 5/8in ST-153 173 Figure 3-16. Adjusting Hub Tension 3-13. Motor Start Control WARNING a E LECTRIC SHOCK S S can kill. STATIC ELECTRICITY can damage parts Do not touch live electrical parts. on TurnOffwirefeederandweldingpowersource,and disconnect input power before inspecting or S circuit boards. Put on boards grounded wrist strap BEFORE handling or parts. installing. wfwaml.r 2/93 To Right change wire feed starting speed proceed as follows: Side Turn Off wire feeder and welding source. power Remove wrapper. 1 Motor Board PCi 2 Motor Start Control Poten tiometer R70 Turn potentiometer clockwise to in time it takes the motor to ramp up to speed. Remove protec tive white rubber cap before mak crease ing adjustment. Adjust potentiome using a small nonconduc ter R70 tive screwdriver. Reinstall wrapper. Tools Needed: 1/4 in Non-conductive Figure Ref. ST-162 132 / Ref. 5B-148 862-D 3-17. Motor Start Control On Motor Control Board PCi OM-1588 Page 11 3-14. Adjusting Control Tilt Bracket 1 Tilt Bracket 2 Rear Pivot Screw 3 Front Screw Loosen screw. Remove Pivot control down ward to desired viewing angle. Re place and tighten front screw. front rear pivot screw. Tighten pivot screw. 2 ST-801 278 Figure 3-15. Threading Welding 4~ 3-18. Changing Control Tilt Angle Wire WARNING CYLINDERS can explode if damaged. Keep cylinders away from welding and other electrical Circuits. Never touch cylinder £9 WELDING WIRE wounds. Do not press gun with welding electrode. Always secure cylinder to running gear, wall, other stationary support. ELECTRIC SHOCK can or can cause puncture trigger until instructed to do so. Do not point gun toward any part of the body, other people, or any metal when threading welding wire. kill. Do not touch live electrical parts. The welding wire, drive rolls, drive assembly, and all metal parts touching the welding wire are electrically live when welding or feeding wire using gun trigger. HOT SURFACES can Allow gun to cool before burn skin. touching. wfwam2.1 / wfwam7.1 9/91 OM-1 588 Page 12 1 Wire 2 Wire Tube Spool/Reel 6 2 3 Pulley 4 Wire Guides 5 Drive Rolls 6 Jog Button 7 Gun Conduit Cable 8 Pressure Adjustment Knob 9 Drive Roll Pressure Indicator Scale Tools Needed: I~I See Figure 5-13 for switch positions of 450 Ampere Inverter model welding power source or welding see power Owners Manual for other models. OFF source Wire Feeder (see Figure 5-10) Welding Power Source Pull and hold wire; cutoff end. Set switches. feed wire thru tube, over and up to wire inlet guide. Manually pulley, JOG ~*00 Push wire thru guides up to drive rolls; continue to hold welding wire.Press Select button (see Figure 5-6) to choose active side of wire feeder. Press Jog button (see Figure 5-8) until drive rolls grab wire. Adjust tension until wire does not slip. Indicator is for reference only. Press jog button until wire comes out gun. p -~ Feed wire to check drive roll pressure. Adjust knob enough to prevent slipping. Cut off wire. Close cover. for opposite side. Repeat procedure Ref. ST-800 178 / Ret. ST.150 922 / 5T-153 073/ Ret. 5T-157 432 Figure 3-18. Threading Welding Wire CM-i 588 Page 13 SECTION 4- GLOSSARY The is following a list of terms and their definitions they apply as to this wire feeder: General Terms Adaptive Pulse Background Cold Wire When the adaptive pulse welding process is selected, the unit will automatically regulate pulse frequency in order to maintain a constant arc length, regardless of change in welding wire stickout. Current The lower of the two current levels in the pulsing wavetorm. When current is not sensed, wire feeds for about three seconds at set wire feed speed and then automatically opens the contactor while continuing to feed wire at the wire jog speed. Jog Inductance In short circuit welding, an increase in inductance will decrease the number of short circuit metal transfers per second (provided no other changes are made) and in crease the arc-on time. The increased arc-on time makes the pool more fluid. Peak Current The Pulses Per Second Number of (PPS Or Pulse Pulse Width higher of the two current levels in the peak current pulses which pulsing occur in waveform. one second of time. Frequency) (Or Peak Time) Trim Duration of the peak current level. Term used to represent arc by volts in MIG programs. Synergic refers to the Synergic length adjustments in pulse programs. Trim is replaced ability to use preprogrammed pulse parameters in order pulse settings of Peak Amperage, Background Amperage, Pulse Width at any specific wire feed speed setting. units to determine the actual Pulse Frequency and Front Panel Terms Display Control Knob Digital Display Gas Purge Control Is used for all 2-line by adjustable front panel displays. 16-character liquid crystal display Allows the gas line and gun to be purged with built-in LED without of parameters that Parameter Select Button Is used to select Trigger Hold Control When selected, allows the system to remain to hold the gun trigger. Wire Jog Control a variety Allows the wire to feed without can energizing be set on backlight. the wire feeder. the front panel display. energized without the operator having energizing the welding power source contactor and independent from actual wire feed speed, and is gas valve. The wire jog speed is displayed on the front panel. Side Panel Terms Digital Display OM-1 588 Page 14 4-line by 20-character liquid crystal display with built-in LED backlight. Dual Schedule Allows two weld programs to be linked together when two different tions, such as hotter and colder, are required on one wire. Process Mode Is used to select the type of process to be used, welding condi including Pulse, Adaptive Pulse, or Mig. Remote Parameter When Increase/Decrease decrease Sequence Mode Setup Screen feature this is turned on, the operator selected weld parameter with the momentary-contact switch. a use can of the remotely increase and optional DSS-10 2-pole Allows a variety of sequences to be used within a weld program it required. Se quences include, pref low gas control from 0 to 9.9 seconds, run-in control of voltage or trim and wire feed speed from 0 to 2.5 seconds, weld time from 0 to 25 seconds, crater control of voltage or trim and wire feed speed from 0 to 2.5 seconds, burnback time from 0 to 0.25 seconds, and posttlow gas control from 0 to 9.9 seconds. Terms Access Mode can be programmed in the access mode which restricts unautho personnel from changing any of the security/set-up screens. NOTE: The optional Data Card is required to activate this feature. A three-letter code rized Arc Start Provides the option Arc Time Allows actual arc cumulated and Dual Schedule of a higher arc starting amperage for large wires. time up to 9,999.99 hours and weld cycles up to 999,999 to be ac and can be reset to zero as required. displayed on the digital display, Is used to select the type of dual schedule switch that will be used when the dual schedule feature is selected. Mig Type Selects whether Model Allows selection of voltage correction is used boom-type feeder or or not. bench mount feeder pulse program parameters. Name Feature When using the optional Data Card programs written to the card Program Reset Range can and turning the name feature on, customized by name, number, job number, etc. be identified By selecting program reset in the memory reset mode, factory program settings for the program last active. The wire feeder source requires that the voltage the unit defaults to and amperage range of the be entered. Obtain this information from the welding power original welding power source Owners Manual. Remote Parameter When the Remote Parameter Inc/Dec is on, a dual schedule switch can also be used increasing or decreasing weld parameters when the front panel display cursor is for at Security Trim, Volts, or 1PM. Is used to limit what the operator can control. This includes accessing the number of the program, 1 through 8, and also the range of welding parameters within the pro gram selected. NOTE: The optional Data Card is required to activate this feature. Software Screen Selection of this function will System This unit can display be used either with GMAW (Pulse/Mig) pulse Only) welding only. and a the software version of the unit. welding power source capable of regular GMAW welding power source capable of GMAW (Mig or a OM-1588 Page 15 System Reset By selecting system reset in the memory reset mode, the unit defaults to original fac tory settings for all programs and all set up excluding System, Arc Time, and Model Type. Trigger Program Select Allows programs to be selected Self Test Mode Voltage Control Feedback remotely with the gun trigger. A built-in diagnostic feature to check a variety of wire feeder and power source func tions if malfunction a occurs. Allows voltage to be monitored at the output terminals by two methods. This can be through the 17-pin cord connection if the welding power source has a 17-pin receptacle, or through the use of the units optional external voltage sense selected lead. Arc StartlVolt Sense When this feature is on, the system immediately shuts down if no arc voltage is sensed. An error message is displayed. When this feature is off, wire feeds even when there is no arc voltage sensed. Shutdown Wire Feed Mode Allows the selection of inches per minute or meters per minute for wire feed speed. This mode is also used to select motor type; standard speed, low speed, or high speed. High and low speed motors are available as factory options. SECTION 5-OPERATION WARNING A~ ____ ELECTRIC SHOCK can kill. ARC RAYS can burn eyes and skin; NOISE can damage hearing. Do not touch live electrical parts. Always wear yourself Keep panels all Wear dry insulating gloves. Insulate from work and and covers FUMES AND GASES to your health. Keep your head Ventilate area, S ground. securely in out of the fumes. or use breathing MOVING PARTS ,~~~IIItii~ can cause Do not weld fire S or explosion. Keep away from Keep all doors, and securely in device. Read Material Safety Data Sheets (MSDS5) and manufacturers instructions for material used. WELDING body protection. can cause pinch points panels, place. injury. such covers, and as drive rolls. guards closed MAGNETIC FIELDS FROM HIGH CUR RENTS can affect pacemaker operation. Pacemaker wearers flammable material. near with correct shade of filter. place be hazardous can welding helmet Wear correct eye, ear, and keep away. Wearers should consult their doctor before Watch for fire; keep extinguisher nearby. Do not locate unit Do not weld on Allow work and over near any going welding operations. combustible surfaces. closed containers. equipment to cool before handling. See Safety Precautions at beginning of manual forba sic welding safety information. ~am3 1 8/92 Wear the following while welding: 1 Dry, Insulating Gloves 2 Safety Glasses 12 With Side Shields 3 Welding Helmet With Correct Shade Of Filter (See ANSI Z49.1) ______ ~b3.1 1194 Figure OM-1588 Page 16 5-1. Safety Equipment 1 Work Clamp Connect work clamp to a clean, paint-f ree location on workpiece, as close to weld area as possible. Use wire brush or sandpaper to clean metal at weld joint area. Use chipping hammer after welding. Tools Needed: 2 to remove slag Voltage Sensing Clamp Connect to workpiece, if applicable (see Section 3-9). Use chipping hammer slag after welding. to remove sb41 Figure 5-1. 5-2. Work And 2/93 Voltage Sensing Clamps Front Panel Controls _iI~ 2 3 10 1 Display 2 Parameter Select Button 3 Display Control 4 Right 5 Right Side Trigger Hold Button And Indicator Light 6 Side Select Button 7 Left Side Trigger Hold Button And Indicator Light 8 Left Side Indicator 9 Jog 10 Purge Button Knob Side Indicator Light Light ~ ckO~ 9 8 o/pss\o Iv Button See Section 6 for information 4 using microprocessor on controls. \\\\ 7 6 5 ST-162 127 Figure 5-3. Front Panel Controls 1 Parameter Select Button Press button to move indicator on display. R.f. 91.187 703 Figure 5-4. Parameter Select Button OM-1588 Page 17 1 Display Control Turn knob selected. Spin to knob to parameters by clicks Knob value change quickly or move to fine tune change slowly parameters. knob 1 Figure 5-5. Display Control Knob 2 \ ~ 6 ' Side Select Button 2 Side Indicator Light Push button to select active side of wire feeder. Indicator light is on for active side. The feeder remembers the last used program for each side, and returns to that program when the active side is changed. TRIGGER r= 1 HOLD 0 Note: gun trigger may also be used change active side of to select or wire feeder. RECEPTACLE %__~_ -~ Figure 5-6. Select Button And Side Indicator Lights Trigger 2 2 o,>~ 0 Hold Button Indicator Light To weld without holding gun trigger throughout weld cycle, press and release button to turn on indicator light and hold circuit. To start weld cycle, and feed weld ing wire, press and release gun trigger within the first three sec TRIGGER onds after an arc has been struck. If gun trigger is not released within the first three seconds after arc ini tiation, trigger hold stops, but is still active for next weld cycle. To end weld cycle, press and release gun HOLD trigger. Trigger hold while gun cannot be started trigger is pressed. If the Trigger hold button is pushed for the nonactive side of the feeder (see Figure 5-6), the trigger hold RECEPTACLE indicator light turns on, but Trigger Hold does not become active until that side is selected. Figure OM-1 588 Page 18 5-7. Trigger Hold Button I Jog Jog Push Button works side active, or selected feeder only (see on of Figure 5-6). Separate jog speeds be set for each side of the feeder. can Push to momentarily feed welding wire without energizing welding cir cuit or shielding gas valve. Jog speed is varied using the Dis play Control knob while Jog button is pressed. Default setting is 200 2. 1pm. When Jog button is released, unit displays preset wire feed speed, and previously selected parameter is active. Jog does not work when gun trig ger is pressed. Jog 2 50 Tr im Prg Push Button Purge Purge works on active, or selected -. side >200 I PM Tr im Jog of feeder only (see Figure 5-6). Push to Jog momentarily energize gas purging of air from gun shielding gas line, and adjusting shielding gas regulator without energizing the welding valve. This allows >50 260 Prg I Pulse circuit. Front panel controls, side panel controls, and gun trigger do not work when Jog or Purge button is pressed. Figure 5-2. 5-8. Jog And Purge Buttons Side Panel Controls 1 Parameter Increase Button 2 Parameter Decrease Button 3 Parameter Select Button 4 Mode Select Button 5 Mode 6 Parameter Display Display See Section 6 for information using microprocessor controls. on 3 Ref. ST-182 133 Figure 5-9. Side Panel Controls OM-1588 Page 19 5-3. Rear Panel Controls Power Switch 1 Use power switch to turn unit On and Ott. 2 Circuit Breaker (See Section 2 14-3) 1 5T-800 177 Figure 5-10. Power Switch I BUILDUP OF SHIE LDING GAS can harm health t Shut off when not in shielding gas supply or kill. use. waml.1 2/93 1 Shielding Gas Cylinder 2 Valve 3 Gun Trigger Open vave welding. on Gun turns weld and off. trigger gas flow on cylinder just before output and 3 Close valve on ished welding. cylinder when fin sb5.1 6/92S-0621-C Figure H IGH FREQUENCY will Turn Off J high frequency Completely disconnect this ~\ ) Page 20 Gas using unit from power source when ~~\ System ) ) II (See Figure 3-~J , ) unit. this unit. Install Welding ) using high frequency. Put On Personal Safety Equipment ~~Turn On Shiel~i~\\ Turn On Feeder And ) ) Power Source JJ ) ) Wire JJ Gas ) ) (If Applicable) J J Set All Controls (See Figure 5-13 Begin Welding Figure OM-1588 damage this when Install & Connect Wire Feeder Shielding CAUTION a S 5-11. 5-12. Metal Arc (GMAW), Gas Metal Arc And Flux Cored Arc Welding (FCAW) Sequence Of Gas - Pulse (GMAW-P), 5-4. Setting Switches On 450 Ampere Inverter Model Welding Power Source Always use switch settings shown for all welding processes when using this wire feeder. / A/V o PANEL ~J~I7 ~D~JZ ONI G*ouTPuT~oR o PAP~L ARC FOR~ /INDUCTAN~ N~ ~C/CV 4 Ref. ST-150 171-C/Ref. SC-154 197 Figure 5-13. Setting Switches On 450 Ampere Inverter Model Welding Power Source OM-1588 Page 21 SECTION 6- STEPPING THROUGH THE MICROPROCESSOR CONTROLS WARNING £~ . ELECTRIC SHOCK S S can kill. WELDING WIRE Control circuit and feeder operational power are On when using or changing the can cause puncture wounds. Do not touch live electrical parts. S Do not point gun towards any part of the body, other people, or any metal when programming. The welding wire is electrically live and moves out of microprocessor settings. the gun whenever the power switch is On and the gun trigger is pressed. N OT E LI~T~ This unit is equipped with eight (8) pulse welding programs (see Section 7). When the unit is turned On for the first time program 1 comes up, therefore, program 1 is i/lustrated throughout this manual. Instructions are given later in this manual (see Section 9) on how to select or change a program. 6-1. Front Panel Micr oprocessor Controls Turn On welding power source and wire feeder. Follow along with the controls as shown. 1 Front Panel 2 Parameter Select Button Display Press parameter select button to indicator. move The indicator points to parameters that are selected for change. ooO 00 0 Parameter select button can move indicator between Trim (arc length) and 1PM while welding. 0 Go to 00000 50 200 Tr im >Prg I PM Pulse Trim >50 200 1PM Prg Figure 6-2. 1 Pulse e Trim 50 >200 1PM Prg 1 Pulse ST-162 127 Figure OM-1 588 Page 22 6-1. Front Panel Parameter Select Button 1 Front Panel Display Select parameter to be changed (see Figure 6-1). 2 __ Display Control Knob Turning knob one click causes the following changes to selected 2 setting: 00 Trim 00 00 (arc length) increases/de by one. creases 00000 The trim (arc length) value being changed also changes on the side panel parameter display (see Figure 8-3). Wire feed speed (1PM) increases/ decreases by one inch per minute. >50 200 Trim Prg 1PM 1 The wire feed speed value being changed also changes on the side Pulse panel parameter Figure 8-3). Program number ses/decreases by j~5~ >55 200 ~ The program number cannot be changed while welding, with ex ception of Dual Schedule Mode (see Section 11). Front Panel Parameter Select All accessible are programs either side of the feeder, and any program is available to ei ther side of the feeder at the same time. through e 55 >200 Trim Prg Display Control knob can be used Jog speed when Jog button is pressed (see Figure 5-8). to set Puls~J 1PM Pulse is a default setting. To change type of program (Pulse, Adaptive Pulse, or MIG) use side panel controls (see Sections 9-4 and 10-1). Display Control Go to 55 >300 Trim~ IPMJ Prg increa one. number program being changed also changes on the side panel parameter display (see Figure 6-5). Prg 1PM (Prg #) (see The ii Pulse] Trim display Figure 6-3. 1 Pulse Front Panel Parameter Select 55 300 50 200 Trim 1PM Trim 1PM >Prg 1 Pulse >Prg 2 Pulse ST-162 127 Figure 6-2. Front Panel Display Control Knob CM-i 588 Page 23 6-2. Side Panel Microprocessor Push Buttons 1 Mode 2 Mode Select Button Display Press Mode button to tor in left window Go to Figure move indica display. 6-4. Side Panel Process >S e q u e n c e Dua I Schd Card Process Sequence >Du a IS c h d Card Process Sequence L..__i Dual Schd >C a r d Ref. ST-154 109 Figure OM-1 588 Page 24 6-3. Side Panel Mode Select Button 1 Parameter 2 Moving Display Line Moving line is be changed. under value that can Side Panel Parameter Select Button 3 Press side panel parameter select button to move indicator in right window display. Side Panel Prg >E u I 1 ~ e O35~SteeI ArgonO I L Figure xy Pulse I 035Steel 7 ArgonOxy I>Teach Qff 6-4. Side Panel Parameter Select Button OM-1588 Page 25 Use side panel mode select button changed (see Figure 6-3). to select mode to be Use side panel parameter select button to select parameter to be changed (see Figure 6-4). 1 Increase Button Press button to increase value that is underlined by the moving line. 2 Decrease Button Press button to decrease value that is underlined by the moving line. Side Panel 1 ~ >Prg ~ I Increase Increase >Prg 3 Pulse 2 052Stee ArgonO I xy Decrease >Prg 2 Pulse 045Steel ArgonO xy Ref. ST-154 109 Figure OM-1 588 Page 26 6-5. Side Panel Parameter Increase And Decrease Buttons SECTION 7- STANDARD PULSE WELDING PROGRAMS The following eight (8) pulse welding programs are in the memory of the wire feeder. Use this information if it is neces sary to change a standard program, or as a basis to build your own custom program. If at any time while changing a standard program, or while building your own custom program, you want to revert back to the standard program in the wire feeder memory, see Section 13-17, Resetting Memory. Program Program # 1 Program Name: .035 Wire Size/Type: .035 Steel, Argon - 1 S-3 Gas: 98 Ar - 2 Oxy or 95Ar - 5 Oxy Card #_________________________ Oxy Gun Model: MILLER GW Flowrate: 40 CFM 1PM I MPM ApK AbK PPS PWms 750/19.1 490 105 200 2.0 700/17.8 480 100 190 1.9 650/16.5 470 95 185 1.9 600 / 15.2 465 93 180 1.9 550/14.0 460 90 175 1.8 500/12.7 450 85 170 1.8 450/11.4 430 80 160 1.8 400/10.2 410 75 150 1.7 350 / 8.9 390 70 140 1.7 300/7.6 370 65 130 1.6 250/6.4 350 50 120 1.6 200/5.1 330 47 110 1.6 150/3.8 315 45 90 1.5 100/2.5 300 45 40 1.5 80/2.0 290 40 35 1.5 COMMENTS Preflow: 0 Sec. Run-In Trim: 50 1PM: 200 Sec.:__________________________ CraterTrim:50 1PM: 200 Sec.:______________________ Postflow: 0 Sec. OM-1588 Page 27 Program Program Wire #2 SizeiType: Program Name: .045 Steel, Argon - .045 2 S-3 Gas: 98Ar Oxy - 2 Oxy or 95 Ar - 5 Oxy Card #_________________________ Gun Model: MILLER GW Flowrate: 40 CFM 1PM I MPM ApK AbK PPS PWms 750/19.1 540 110 220 3.2 700/17.8 530 110 210 3.2 650/16.5 520 110 200 3.2 600/15.2 510 110 190 3.2 550/14.0 500 110 180 3.1 500/12.7 490 105 170 3.0 450/11.4 470 105 160 2.9 400/10.2 450 100 150 2.8 350/8.9 440 100 140 2.7 300/7.6 430 95 130 2.6 250/6.4 420 90 120 2.5 200/5.1 400 80 100 2.5 150/3.8 380 70 80 2.4 100/2.5 345 50 60 2.4 80/2.0 310 30 38 2.2 COMMENTS . Preflow: 0 Sec. Run-In Trim: 50 1PM: 200 Sec.:__________________________ Crater Trim: 50 1PM: 200 Sec.:___________________________ Postf low: 0 Sec. OM-1588 Page 28 Program Program # 3 Program Name: .052 Wire Size/Type: Steel, Argon - .052 3 S-3 Gas: 98Ar Oxy - 2 Oxy or 95 Ar - 5 Oxy Card #_________________________ Gun Model: MILLER GW Flowrate: 40 CFM 1PM / MPM ApK AbK PPS PWms 750/19.1 565 145 260 3.1 700/17.8 565 140 260 3.1 650/16.5 560 135 260 3.1 600 /15.2 560 130 255 3.1 550/14.0 560 125 240 3.1 500/12.7 550 120 225 3.0 450/11.4 540 115 210 2.9 400/10.2 530 110 195 2.8 350/8.9 520 105 170 2.7 300/7.6 510 100 155 2.7 250/6.4 500 90 140 2.6 200/5.1 480 80 120 2.6 150/3.8 460 70 100 2.5 100/2.5 420 50 80 2.4 50/1.3 350 32 50 2.2 COMMENTS Preflow: 0 Sec. Run-In Trim: 50 1PM: 200 Sec.:__________________________ Crater Trim: 50 1PM: 200 Sec.:___________________________ Postf low: 0 Sec. OM-1588 Page 29 Program Program # 4 Wire Program Name: .035 Size/Type: 309, Argon - .035 4 309 Gas: 98 Ar CO2 - 2 CO2 or 95Ar - 5 CO2 Card #________________________ Gun Model: MILLER GW Flowrate: 40 CFM 1PM I MPM ApK AbK PPS PWms 750/19.1 390 95 210 2.2 700/17.8 380 95 200 2.1 650/16.5 370 90 190 2.0 600/15.2 360 85 180 1.9 550/14.0 350 80 170 1.9 500 / 12.7 340 75 160 1.9 450/11.4 330 70 150 1.8 400/10.2 320 65 140 1.8 350/8.9 310 60 130 1.7 300/7.6 300 55 120 1.6 250/6.4 290 50 100 1.6 200/5.1 280 45 80 1.6 150/3.8 270 40 60 1.6 100/2.5 270 36 40 1.5 80/2.0 260 30 30 1.5 COMMENTS Pref low: 0 Sec. Run-In Trim: 50 1PM: 200 Sec.:___________________________ Crater Trim: 50 1PM: 200 Sec.:__________________________ Postf low: 0 Sec. OM-1 588 Page 30 Program Program # 5 Wire Program Name: .045 Size/Type: Steel, 309, Argon .045 - 5 Gas: 98 Ar 309 - 2 CO2 or 95Ar - 5 Co2 Card #_________________________ CO2 Gun Model: MILLER GW Flowrate: 40 CFM 1PM / MPM ApK AbK PPS PWms 750/19.1 490 115 290 2.3 700/17.8 480 115 280 2.3 650/16.5 450 115 270 2.1 600/15.2 435 112 260 2.0 550/14.0 430 110 240 2.0 500/12.7 425 105 230 1.9 450/11.4 420 105 220 1.9 400/10.2 415 105 200 1.8 350/8.9 410 100 180 1.8 300/7.6 400 95 160 1.7 250/6.4 380 88 140 1.7 200/5.1 360 85 115 1.7 150/3.8 340 68 88 1.6 100/2.5 320 50 70 1.6 80/2.0 310 45 60 1.5 COMMENTS Preflow: 0 Sec. Run-In Trim: 50 1PM: 200 Sec.:__________________________ Crater Trim: 50 1PM: 200 Sec.:__________________________ Postflow: 0 Sec. OM-1 588 Page 31 Program Program # 6 Program Name: 3/64 Wire Size/Type: 3/64 6 4043 Gas: Argon Card #_________________________ 4043, Argon Gun Model: MILLER GW Flowrate: 40 CFM 1PM / MPM ApK AbK PPS PWms 750/19.1 510 150 190 3.5 700/17.8 485 150 180 3.4 650/16.5 485 150 180 3.4 600 / 15.2 470 145 180 3.3 550/14.0 445 140 170 3.1 500/12.7 420 135 160 2.9 450/11.4 400 130 150 2.8 400/10.2 360 120 140 2.7 350/8.9 340 115 130 2.6 300/7.6 310 100 120 2.5 250/6.4 277 87 110 2.4 200/5.1 250 68 100 2.3 150/3.8 215 50 90 2.1 100/2.5 190 30 80 2.0 80/2.0 190 27 45 2.0 COMMENTS Preflow: 0 Sec. Run-In Trim: 50 1PM: 200 Sec.:___________________________ CraterTrim:50 1PM: 200 Sec.:_____________________ Postf low: 0 Sec. OM-1588 Page 32 Program Wire Program # 7 Program Name: 3/64 Size/Type: 3/64 7 5356 Gas: Argon Card #_________________________ 5356, Argon Gun Model: MILLER GW Flowrate: 40 CFM 1PM I MPM ApK AbK PPS PWms 750/19.1 515 130 190 2.8 700/17.8 510 120 190 2.8 650/16.5 490 120 180 2.7 600/15.2 470 115 170 2.7 550/14.0 450 110 160 2.6 500/12.7 430 100 150 2.5 450/11.4 410 90 140 2.5 400 / 10.2 390 80 130 2.4 350/8.9 370 65 112 2.4 300 / 7.6 340 52 103 2.3 250 / 6.4 325 47 90 2.3 200/5.1 300 40 80 2.2 150/3.8 277 35 53 2.2 100/2.5 260 24 40 2.2 50/1.3 230 20 35 2.0 COMMENTS Preflow: 0 Sec. Run-In Trim: 50 1PM: 200 Sec.:__________________________ CraterTrim:50 1PM: 200 Sec.:______________________ Postflow: 0 Sec. OM-1 588 Page 33 Program Wire Program # 8 Program Name: .035 Size/Type: Nickl, Argon - .035 8 Gas: 75 Ar Nickl He - 25 He Card #________________________ Gun Model: MILLER GW Flowrate: 40 CFM 1PM / MPM ApK AbK PPS PWms 750/19.1 390 110 130 3.5 700/17.8 380 105 130 3.5 650 / 16.5 370 100 125 3.4 600/15.2 360 90 120 3.4 550/14.0 350 85 115 3.3 500/12.7 345 80 110 3.3 450/11.4 340 75 105 3.3 400 / 10.2 335 65 90 3.2 350/8.9 332 60 75 3.1 300 / 7.6 320 55 65 3.0 250 / 6.4 310 50 58 3.0 200/5.1 297 44 52 2.9 150/3.8 282 37 42 2.9 100/2.5 262 29 33 2.8 50/1.3 225 23 30 2.7 COMMENTS Preflow: 0 Sec. Run-In Trim: 50 1PM: 200 Sec.:__________________________ CraterTrim:50 1PM: 200 Sec.:_____________________ Posti low: 0 Sec. OM-1 588 Page 34 SECTION 8- GETTING STARTED WARNING a ELECTRIC SHOCK can ARC RAYS can burn eyes and skin; NOISE can damage hearing. kill. Do not touch live electrical parts. Always wear Insulate Wear dry insulating gloves. yourself from work and Keep all panels and covers or use MOVING PARTS near fire or can cause Keep all doors, panels, and securely in place. breathing device. can cause Do not weld body protection. Keep away from pinch points Read Material Safety Data Sheets (MSDSs) and manufacturers instructions for material used. WELDING helmet with correct shade of filter. securely in place. FUMES AND GASES can be hazardous to your health. Keep your head out of the fumes. Ventilate area, welding Wear correct eye, ear, and ground. injury. such covers, and as drive rolls. guards closed MAGNETIC FIELDS FROM HIGH CUR RENTS can affect pacemaker operation. explosion. Pacemaker wearers keep away. flammable material. Wearers should consult their doctor before going Watch for fire; keep extinguisher nearby. Do not locate unit Do not weld on Allow work and NOTE ~ over near arc welding, gouging, or spot welding opera tions. combustible surfaces. closed containers. See Safety Precautions at beginning of manual for ba sic welding safety information. ~am61 8/92 equipment to cool before handling. Set up equipment according to Figure 5-12. Use the standard program in Section 7 that is closest to your application gas type) when setting up. (by wire pulse welding type and size and OM-1 588 Page 35 8-1. Welding With Only Front Panel Controls Turn On wire welding power source, feeder, and gas. Use Select button or gun trigger to select active side of feeder. 1 ~1 Display Program 1 is the default program the first time the unit is turned on, at other times the last program -p >Prg 200 Front Panel number selected is displayed. Use the front panel parameter select button to select the Prg #. Pulse 2 Display Control 2 Prg3 Select the weld program from Section 7 (1 through 8) which is closest to your needs (by wire and gas). Strike an arc and try a sample weld. Trim 50 200 >Prg 1PM 3 3 Pulse If Trim (Arc Length) necessary, select Trim, and to achieve the best arc. adjust 4 U Front Panel Parameter Select If 1PM necessary, select 1PM, and the best arc. adjust to achieve Go to Section 8-2. I F50 Trim 200 Prg 1PM 3 Pulse Display 3 Control ~Ij I I Trim >55 200 Prg 1PM 3 Pulse Front Panel U Parameter Select Trimi 1>200 J 1PM Prg 3 Pulse g~ Trim 55 >250 1PM Prg 3 Pulse - / Figure OM-1 588 Page 36 8-1. Welding With Only Front Panel Controls 8-2. Pulse Setting Sequence Welding Parameters On Side Panel Display WARNING a ELECTRIC SHOCK can WELDING WIRE can cause wounds. kill. Do not touch live electrical parts. Do not point gun towards any part of the body, other people, or any metal when programming. The welding wire is electrically live and moves out of the gun whenever the power switch is On and the gun trigger is pressed. S Control circuit and feeder operational power are On when using or changing the microprocessor settings. NOTE ~ puncture Figure 8-2 is a graphic layout of a weld cycle. Follow examples in Figure 8-3 through Figure 8-8 to adjust sequence welding parameters to fit your needs. Weld Time 0-25 Sec. Run-In Time 0-2.5 Sec. a, a) o. CraterTime 0-2.5 Sec. Run-In a) Speed a) I / a. ci ~a,I a) Pref low 0-9.9 Sec. Oci Tim!_,J Trigger Arc Start U Trigger Released Bumback Time 0-0.25 Sec. /~ Postflow Time 0-9.9 Arc Ot u Sec.~ ~ Time Pressed Ref. S-0271 Figure 8-2. Weld Cycle OM-1588 Page 37 Mode Select Button 1 Process >S e q When unit is turned On, Process is the default mode, at other times, use mode select button to select >WQ I ~ 50. u e n c e Trim Dual Schd 200 1PM Card 0.0 Sec Sequence. 2 Side Panel Parameter Select Button Use side panel parameter select button to select parameters. 2 3 Weld Parameters Display Parameter ranges are as Trim 0-99 (Arc Length), Changes are also to Weld displayed follows: Sequence Trim on front panel display. Wire Feed Speed, 50-780 Inches Per Minute, 1PM Changes are also to Weld displayed display. Set Desired Weld Sequence Voltage Seconds, 0-25.0 Sec. If value set is (0), welding will continue until welding gun trigger is released. zero Or lncrease/ Decrease use I front We I d panel parameter 1>50 select to move indicator to trim. I Trim be fine tuned while welding, see Figure 6-2. can Trim 200 1PM 0.0 Sec Side Panel Parameter Select Set Desired Weld Sequence Wire Feed Speed Or ~ use front panel parameter select to move indicator to 1PM. lncrease/ Decrease 1PM can be fine tuned while welding, see Figure 6-2. Side Panel Parameter Select Set Desired Weld Sequence Time, If Applicable We I d Trim 60 300 1PM >0.0 Sec lncrease/ Decrease ~ Side Panel Parameter Select We I d 60 Increase Proceed to next Figure OM-1588 Page 38 Sequence 1PM on front panel 8-3. Trim 300 1PM >3.5 Sec figure. Setting Weld Sequence Display Go to Figure 8-4. 1 Crater Parameters Parameter ranges >Gr~ter 50 I I Triml 200 1PM 0.00 Sec ~ 7 Crater I>~Q ~ 200 ~ 1PM 0.00 Trim Crater I Trim Sec 60 0.00 1PM 1 Sec I (Arc Length), 0-99 Seconds, 0-2.50 Sec. If value set is (0), zero Side Panel Parameter Select Side Panel Parameter Select Set Desired Trim lncrease/ >Cr~t~r 150 Go to I is Crater no Figure 8-5. Side Panel Parameter Select TrimLJ 60 ~ 1PM 0.20 there sequence. Crater TrimL 60 Set Desired Wire Feed Speed lncrease/ Decrease Decrease follows: Wire Feed Speed, 50-780 Inches Per Minute, 1PM Trim >2Q0 Display are as Sec 150 1PM > Sec Side Panel Set Desired lime Parameter Select Increase Proceed to next figure. Figure 8-4. lncrease/ Decrease Setting Crater Sequence Display 1 Burnback Parameters Dis play __/ __ __ i~~urn.b~Qh Bu rnback ii r n Sec 0.12 b ~ Ic Burnback can be adjusted from 0-0.25 seconds. If value set is zero there is Burnback no (0), sequence. 0.00 Sec >Q~QQ Sec Go to Figure 8-6. ____________ Side Panel Parameter Select Set Desired lime Side Panel Parameter Select Increase Proceed to next lncrease/ Decrease Figure 8-5. SettIng Burnback figure. Sequence Display 1 ______/ ______ ______ Postflow >~Q~tfIQW 0.0 Sec ~ Side Panel Parameter Select >~Q~IfIQ~ Postf low Parameters Go to Sec Set Desired lime 1.2 Increase Proceed to next Setting 8-7. Sec ~ncrease/ 8-6. Figure Side Panel Parameter Select Decrease Figure Display Postflow can be adjusted from 0-9.9 seconds. If value set is zero (0), there is no Postf low sequence. Postf low figure. Sequence Display OM-1 588 Page 39 Pref low Parameters 1 Display Pref low can be adjusted from 0-9.9 seconds. It value set is zero (0), there is no Pref low sequence. Go to Figure 8-8. / ______ L0 ______ Preflow Sec ~ >?reJlQw Sec Side Panel Parameter Select lncrease/ Decrease Figure 8-7. Setting Preflow Sec 1.2 Side Panel Parameter Select Set Desired Time Increase Proceed to next figure. Sequence Display Run-In Parameters 1 Parameter ranges Display are as follows: Trim, 0-99. Wire Feed Speed, 50-780 inches per minute, 1PM Seconds, 0-2.5 Sec. If value set is (0), there is no Run-In zero sequence. ~ Side Panel Parameter Select Set Desired Wire Feed Speed O Increase! Decrease Increase! Decrease I Runin Trim 55 Side Panel Parameter Select Increase 150 1PM ~ Sec Set Desired Time Increase! Decrease Figure OM-1 588 Page 40 8-8. Setting Run-in ~ Sequence Display Side Panel Parameter Select SECTION 9 TEACHING A PULSE WELDING PROGRAM WARNING a ELECTRIC SHOCK can 4 kill. Do not touch live electrical parts. Control circuit and feeder operational power are On when using or changing the microprocessor I settings. NOTE ~ 9-1. L~( ~ ~/I See GMAW-P information. Pulse Waveform (Pulsed MIG) WELDING WIRE can cause puncture wounds. Do not point gun towards any part of the body, other people, or any metal when programming. The welding wire is electrically live and moves out of the gun whenever the power switch is On and the gun trigger is pressed. Process Guide supplied with unit for more Explained The wire feeder, not the welding power source, controls weld output for pulsed welds. 1 Peak Current Of 100-565 Amperes Apl( is the high pulse of welding Peak current melts the ApK current. welding wire and forms a droplet. The droplet is forced into the weld puddle. 2 AbK Background Current Of 10-200 Amperes AbK is the low weld current. Back ground C 0 (0 0. E ;~\3~ current preheats welding wire and maintains the arc. When background current Is too low, the is unstable and hard to arc maintain. I _/ ~ PPS 3 Pulses Per Second Of 20-400 PPS, pulse rate, and frequency are used interchangeably. A PPS or pulse rate of 60 Hz means 60 pulses of current are produced each second. (Hz) 4 PWms Pulse Width Of 1.0-5.0 Milliseconds Time PWms is the time spent at peak (1.2 ms is .0012 seconds). This time must be long enough to form a droplet of welding wire. The stiffness or fluidity of the molten weld puddle is controlled by PWms. current Ast. S.0259 Figure 9-1. Pulse Waveforms And Explanation Of Terms OM-1 588 Page 41 Teach Points 9-2. Explained 1PM 780 750 700 650 600 550 Example Of A Synergic Setting For 425 1PM With 500 All Teach Points Set At 50 1PM Increments 450 400 350 300 250 r 200 o AbK o pps 150 100 PWms 50 100 180 210 240 270 300 330 360 370 420 450 480 510 540 565 ApK 10 20 30 40 50 60 70 80 90 100 110 120 130 140 200 AbK 20 55 80 105 130 160 185 210 235 260 290 315 340 365 400 PPS 1 2 The teach mode allows the user to create custom pulse MIG welding programs. The teach mode has 15 teach points. At each point, the user can adjust four parameters: peak amperage (ApK), background amperage (AbK), pulses per second (PPS), and pulse width in milliseconds (PWms) to shape the pulse waveform of the weld teach output. teach points can range from the minimum to the maximum wire feed speed of the feeder. When using a standard speed motor, wire feed speed teach points typically range from 50 to 750 ipm. The wire Wire feed speed 4 3 speed of the lowermost teach point, and above the wire feed speed of the uppermost teach point, the unit may limit wire feed speed settings in pulse MIG to maintain all pulse parameters within the caBelow the wire feed pability tered for all 15 teach points. The operator can relocate and modify the setting of one, or any number of the 15 teach points if the factory set information is not appropriate for a specific application, pulse parameters at any wire feed speed setting. wire feeder to learn the arc voltage length associated with the taught pulse parame- OM-1588 Page 9-2. Typical arc length represents a Trim (arc of 50. Increasing the value of Trim, increases the actual arc length. Like wise, decreasing the value of Trim will de length) setting crease actual arc length. In the Pulse mode, the unit does not maina constant arc length with variations in tam electrical stick-out. In the After the parameters for each teach point are established, an arc must be struck and maintamed for at least 5 seconds. This allows the Figure a proper arc length reading, electrical stick-out must be carefully maintamed, and the weld must be terminated by releasing the gun trigger, not by pulling the welding gun away from the workpiece. The taught Pulse MIG programs made by the manufacturer have pulse waveform information en- speed of a teach point can be redefined to any wire speed setting between adjacent teach points (see Section 9-3). The feeder uses pulse parameters at teach points to es- 42 ters. To ensure of the unit. feed tablish the PWms 5 Adaptive Pulse mode, the unit adjusts pulse frequency Teach Point Settings And maintain a constant arc to length regardless of variations in electrical stick-out. Proceed to next figure to teach a program. Resulting Synergic Setting pulse MIG 9-3. Teaching A Pulse Welding Program ~H~i A. Selecting And/Or Redefining READ SAFETY BLOCKS at start of Section 9 before proceeding. Teach Point Wire Feed Speed 1 point (1PM) can be selected on either the side panel or front panel displays, but the wire feed speed of a teach point can only be redefined with the Purge button and Display Control knob while 1PM is selected on the front panel display. A teach Process Display When unit is first turned On, Pro cess is the default screen, at other times use mode select button to select Process. 2 Teach Display Use parameter select button to lect Teach. se Use increase/decrease buttons to select On. 3 1PM (Teach Point) You can also select a teach point with the front panel Display Control knob if the cursor on the front panel display is pointing at 1PM. To redefine the wire feed speed of a teach point, proceed as follows: Increase/ Decrease 4 >Teach Qfl Display se Press and hold Purge button while turning Display Control knob to re define the teach point wire feed speed. For example, if teach points reside at 150, 200, and 250 ipm, the teach point at 200 can be ad justed to a wire feed speed of 151 to 249 ipm. Side Panel Parameter Select Selecting A Teach Front Panel Use parameter select button to lect 1PM (teach point). Repeat the procedure for as many of the 15 teach points as desired. Point To set or adjust teach point parameters, go to Figure 9-4. Redefining A Teach Point 50 450 Trim 1PM i~ >Prg Pu Tr 50 I_ser9j>45 0 im 1PM Front Panel Parameter Select And 50 >4 6 0 Figure 9-3. T rim 1PM Selecting And/Or Prg iL i Puse Redefining A Teach Point OM-1588 Page 43 B. Setting Teach Point Parameters On The Side Panel Side Panel Parameter Select I2 3 I U Side Panel Parameter Select lncrease/ Decrease I 343 I U] Apk~ 92 Abk 280 PPS > PWm 9 _______ ~ Or -.~I I 343 Apk 92 Abk 280 PPS ~ PWm S ____ ~ ~Teach Pulse ~ 460 1PM 343 Apk 92 Abk 035~Stee Argon-Oxyi >Teach Qf ____________ Side Panel Parameter Select I I lncrease/ Decrease ~ 4 Side Panel Parameter Select 5 IPrgl I Pulse I 035Steel I Argon-Ox~j When the Process Teach mode is On, and one of the following pulse parameters is se lected: ApK, AbK, PPS, or PWms, the front panel displays the selected pulse parameter instead of Trim (arc length). When the pulse parameter is selected on the front panel, the value can be changed with the front panel Display Control knob, or the side panel as follows: Figure OM-1588 Page 44 9-4. 1 ApK Display 2 AbK Display 3 PPS Display 4 PWms until custom program is complete (see Figure 9-2). Turn Teach mode Off. Display When values have been set for a teach point, strike and maintain an arc for five sec onds. Repeat procedure at each teach point Setting Teach 5 Custom Pulse Screen The letter C will appear in the upper ner of all customized programs. To set Sequence Section 8-2. Point Parameters On The Side Panel right cor Welding Parameters, see N OTE LI~ Program #__________ Make Wire copies of this chart for future use. Size/Type________________________ Gas__________________________ Program Name__________________________________________ Card #_______________________ Gun Model_____________________________________________ Flowrate 1PM ApK AbK PPS PWms CFM COMMENTS Pret low:__________________ Sec. Run-In Trim:_______________ 1PM:___________________________ Sec.:_________________________ Crater Trim:_______________ 1PM:___________________________ Sec.:_________________________ Postf low:________________ Sec. OM-1588 Page 45 9-4. Changing To Adaptive Pulse Welding i~~H~J READ SAFETY BLOCKS at start of Section 9 before proceeding. Welding parameters are the same for both a Pulse and an Adaptive Pulse welding program. While welding adaptively, the unit uses feedback to attempt to maintain a constant arc length. To change to Adaptive Pulse welding, proceed as shown: 1 Side Panel Mode Select / >Process >Prg 1 Pulse Sequence DualSchd 035Steel Card ArgonOxy ~ >Process Side Panel Parameter Select 1 Prg Sequence >?u1~e DualSchd 035Steel Card ArgonOxy Increase/ Decrease , >Process Prg 1 >A~aptEuLs.e Sequence DualSchd 035Steel Card ArgonOxy Figure OM-1 588 Page 46 9-5. Side Panel Display Default display when unit is first turned On, at other times use side panel mode select button to select Process. Changing To Adaptive Pulse Welding SECTION 10-TEACHING A MIG WELDING PROGRAM WARNING a ELECTRIC SHOCK can kill. WELDING WIRE wounds. Do not touch live electrical parts. Control circuit and feeder operational power are~ using or changing the microproces~ can cause puncture Do not point gun towards any part of the body, other people, or any metal when programming. The welding wire is electrically live and moves out of when settings. the gun whenever the power switch is On and the gun trigger is pressed. 10-1. Changing To MIG Welding 1 L.J Side Panel Display Default display when unit is first turned On, at other times use side panel mode select button to select Process. Side Panel Mode Select 1 Goto Figure 10-2. / >Process >Prg Sequence 1 Pulse DualSchd 035Steel Card ArgonOxy Side Panel Parameter Select , >Process Prg Sequence 1 >EiaI~ DualSchd 035Steel Card ArgonOxy Increase/ Decrease e >Process Prg Sequence 1 >M1~ Dual Schd Card Figure 10-1. Changing To MUG In The Process Mode OM1588 Page 47 10-2. Setting Sequence MIG Welding Parameters On Side Panel Display Side Panel 1 Display When unit is turned On, Process is the default mode. Use mode select button to select Sequence. Side Panel Parameter Select Button 2 >Process >Prg Sequence 1 Use side panel parameter select button to select parameters. MIG Dual Schd Ca r 3 d Weld Parameters Parameter ranges Display are as follows: Volts, 10.0-38.0 Volts C1J Wire Feed Speed, 50-780 Inches Per Minute, 1PM Mode Select Seconds, 0-25.0 Sec. If value set is (0), welding continues until welding gun trigger is released. zero ~ Inductance, 0-99% Process >Sequence >WeI Changes to voltage and wire feed speed (1PM) parameters in the weld sequence are also displayed on front panel display. 18. OVol t DualSchd 200 1PM Card 0.0 Sec Go to Set Desired Figure 10-3. 3 Voltage We I d >1~QVoI Increase/ Weld Sequence Volts Decrease can be fine tuned while 200 1PM 0.0 Sec welding t Side Panel Parameter Select Set Desired Wire Feed Set Desired Weld Time, If Applicable Speed rWe 20.OVolt ~ lncrease/ Decrease >2QQ 1PM 0.0 Sec Increase! Decrease Side Panel Parameter Select 1PM be fine tuned while welding Weld Sequence can Set Desired Inductance, If Applicable Increase/ Decrease Side Panel Parameter Select Figure OM-1 588 Page 48 10-2. Increase Proceed to next Setting Weld Sequence Display figure. 1 Crater Parameters Parameter ranges Display are as follows: Volts, 10.0-38.0 Volts 1 Wire Feed Speed, 50-780 Inches Per Minute, 1PM r a I 18.OVolt I 2 0 0 Seconds, 0-2.50 Sec. If value set is I PM (0), zero 0.OOSec there is Crater no sequence. Go to I U I R~ater Crater I>1~QVolt 1PM 1PM 0.OOSec Crater 24.OVolt 24.OVolt 0.OOSec 200 10-4. Side Panel Parameter Select rV1 I Figure I 1PM 400 __ __ Side Panel Parameter Select Set Desired Voltage __ Side Panel Parameter Select Set Desired Wire Feed lncrease/ Decrease Speed I Set Desired Time Increase/ Decrease I I Increase/ Decrease I I I > ~ a I ~ r 24. OVo I 400 1 . t 1PM l2Sec Side Panel Parameter Select ~ Increase Proceed to next Figure 10-3. Setting Crater figure. Sequence Display 1 Burnback Parameters Dis play Parameter ranges are as follows: Volts, 10.0-38.0 Volts Seconds, 0-0.25 seconds. If value (0), there is no Burnback set is zero sequence. I Goto _______________I,,, I>~urn~aQk I 18.0 I Burnback Volt~ 0.00 > 0.00 Sec I Burnback Vo~t~ 16.0 Sec > Figure I 10-5. ~>~ufnbaQk VoltL Sec I 16.0 VoltI 0.12 Sec ___________ __________ __________ Side Panel Parameter Select Set Desired Bumback Volts ___________ Side Panel Parameter Select lncrease/ Decrease lncrease/ Decrease Figure 10-4. Setting Set Desired Bumback Time Burnback Side Panel Parameter Select Increase Proceed to next figure. Sequence Display OM-1588 Page 49 1 ______/ ______ ______ Postflow Sec_F ~ 0.0 Sec_F Side Panel Parameter Select Go to Increase Proceed to next SettIng Postf low Sequence Display ______ ______ Preflow Sec sec]~H >Q__0 ___ _______________ Pref low Parameters Display Pref low can be adjusted from 0-9.9 seconds. If value set is zero (0), there is no Pref low sequence. ______/ 0.0 10-6. figure. 1 >Er~f IQW Figure Sec 1.2 lncrease/ Decrease 10-5. Display Side Panel Parameter Select Set Desired Time Figure Posttlow Parameters Postflow can be adjusted from 0-9.9 seconds. If value set is zero (0), there is no Postf low sequence. Go to Figure 10-7. Sec 1.2 _______________ Side Panel Parameter Select Side Panel Parameter Select Set Desired Time Increase Proceed to next figure. Increase! Decrease Figure 10-6. Setting Preflow Sequence Display 1 1 Run-In Parameters Parameter ranges Display are as fo!~ows: Volts, 10.0-38.0 Volts Wire Feed Speed, 50-780 inches per minute, 1PM Side Panel Parameter Select Set Desired Voltage Side Panel Parameter Select Increase/ Decrease I>W~I~ I 20.OVoIt I 420 1PM 2.2 Sec F I H Increase >Bunin 20.OVoIt 150 1PM 0.5 Sec Set Desired Wire Feed Speed Increase! Decrease Runin F 20.OVoIt Side Panel Parameter Select 150 1PM >0~ Sec Set Desired Time Increase! Decrease Figure 10-7. Setting Run-In Sequence Display OM-1588 Page 50 I I Seconds, 0-2.5 Sec. If value zero (0), there sequence. Side Panel Parameter Select is no set is Run-In SECTION 11 a - SETTING DUAL SCHEDULE PARAMETERS WARNING ELECTRIC SHOCK can kill. Do not touch live electrical parts. Control circuit and feeder operational power are On when using settings. or changing the microprocessor WELDING WIRE wounds. can cause puncture Do not point gun towards any part of the body, other people, or any metal when programming. The welding wire is electrically live and moves out of the gun whenever the power switch is On and the gun trigger is pressed. Dual Schedule can only be used with two consecutive weld pro grams such as: 1 & 2, or 3 & 4, or 5 & 6, or 7 & 8. Any program type MIG, Adaptive Pulse, or Pulse can be combined in dual schedule. For example, Prg I is MIG, Pig 2 is Pulse, or Prg 1 is Adaptive Pulse, and Prg 2 is Pulse, etc. 1 Mode Select Button 2 Mode Display Use mode select button to select Dual Schedule, then proceed as shown: 3 Dual Schedule Parameters Display panel increase/decrease Display Control knob (see Figure 11.2) to select dual schedule pairs. Use side buttons, or lncrease/ Decrease ~&4~ Display Control If the two desired welding programs are not in the proper program order (1 & 2, or 3 & 4, etc.), the get them in the proper order would be to write one program to a data card, most common method to and then read the program from the card into the desired program number. See Section 12 for data card information. Figure 11-1. SettIng Dual Schedule Pairs On Side Panel Display OM-1 588 Page 51 1 Front Panel Parameter Select Button 2 Front Panel Display Press parameter select button to select program number on front panel display. -1 24. 1 OV 1PM 250 >Prg 1 Dual A -3 Display Welding Gun Trigger OR Control Knob Welding Gun DSS-Type Switch 3 Front Panel Knob 4 Welding Gun Trigger, Or DSS-Type Switch ~I ~>Prg 2 Dual Ar~~1Dual B ~ Control The dual schedule programs can be alternately selected between active programs A or B by turning the Display Control knob one click clockwise or counterclockwise, or by squeezing and releasing the welding gun trigger, or by an exter nal mounted DSS-type switch mounted on the welding gun. See Section 13-10 for specific switchtype instructions. The settings shown on the front panel display are >Prg Display for the active weld program. When program B is active, turn Display Control knob one click clockwise to select another pair of dual schedule programs. Display Control Knob When dual schedule is On, and Process is selected on the side panel display, then the side panel increase/decrease buttons can be used to change program numbers. Figure OM-1 588 Page 11-2. 52 Selecting Between Active Dual Schedule Programs A And B On Front Panel Display SECTION 12 12-1. Installing USING THE OPTIONAL DATA CARD Data Card 1 Label Peel backing from label and apply by to data card with THIS SIDE UP metal pins. Write the names of the programs stored on the card on the label. Write the name of the piece of equipment the card is used with on the label. 2 Data Card 3 Card Slot Insert card into slot. To format card, turn On power to the unit. Select Card from menu. Data card for mats when unit enters Card mode. Exit Card mode and turn Off power. 2 ST.156 266-B I Ref. S-155 823 Figure 12-2. Using The 12-1. Installing Data Card Data Card Use Mode Select button to select Card. Process Sequence DualSchd Press 6 Card Display Write Used to transfer program data from unit to card. The program card can hold up to 32 programs. When writ ing to the card, the next available program number is automatically Below >Card 1 2 Side Panel Parameter Select Once assigned. 3 Read Used to transfer program data from card to unit. 4 Delete Used to delete program data from card. 3 5 Done Used to exit card display. 4 6 Moving Line Moving line is be changed. Figure 12-2. Card under value that can Displays OM-1 588 Page 53 NOTE ~ Al/program types (Pulse, Adaptive Pulse, _____________________ and MIG) can be stored on a data card and retrieved. Card 1 Display Use Mode Select button to select Card. Moving 2 Line Moving line is under value that can changed. Process be Sequence DualSchd Pr >Card 3 ess If Name Display is desired, press side panel Parameter Select button to continue the write procedure. Be low no name naming a program, the front panel Display Control knob can be used to speed selection of charac When Side Panel Parameter Select 2 ters. *1~ulse >Write Read 035Stee Dele te ArgonOxy Done ..--J I Press Allowable characters include: 0 thru 9, :, >?, ,AthruZFJ,A,_,,athruz,!,#,$, %,&,,(,),*,+,_,.,I, Side Panel Parameter Select Name? Name? NQ ~ 035~Steel Yes ArgonOxy Press Increase No 0 ~I TWr Side Panel Parameter Select Side Panel Side Panel Parameter Select I teDone to Prg 1 CardPrg Parameter Select Name? Wr i teDone fj~ 502 1 Press Side Panel Parameter Select Q c Side Panel Parameter Select Pulse #1 I 035Stee ArgonOx y Pulse #1 5007992 F 54 r ame Press Figure Page Side Panel Parameter Select ~ Press OM-1588 Increase 12-3. Naming Programs And Writing To Card Use Mode Select button to select Card. Process Sequence DualSchd Pr >Card ess 1 Card Display 2 Moving Line Moving line is be changed. Be low 3 Mode Select Once Read under value that can Display Select desired card program to download. Select feeder program number where the card program Side Panel Parameter Select Once goes. WARNING: Wi Prgl ~ I Prgl Lost Be Lose? Be Will Lost NO~~Lose? y~ Press NQ Increase Pulse 035Steel ~ Argon-Oxy J Press Yes 1 # ,~ Press Side Panel Parameter Select Side Panel Parameter Select ________________ I I Read Done~ Card I Side Panel Parameter Select # 12-4. I Pu I set ArgonOxyl Press Figure 1 035Steell Prgl Prg 1 to ________________ Press Reading From Card 1 Wr i t e >Re ad De I e WARNING: Car dEmp t y Press t e Be I Done ow ~rI Wr i Side Panel Parameter Select Once >Process t e Sequence Read De I Warning Display If there are no programs on the card, this series of displays appear. >Pr g Ml G 2 Dual Schd e t e Press >Done Card Side Panel Parameter Select Figure 12-5. Reading (Or Deleting) From An Empty Card OM-1 588 Page 55 Use Mode Select button to select Card. 1 Card 2 Moving Display Line Moving line is be changed. 3 Process DualSchd Pr ess Be low Mode Select Twice ~J Side Panel Parameter Select Once ---~ WARN I NG: -t-j___ I Side Panel Parameter Select De let e Card Prg2 Lose? Ye~ I No Press Increase Yes ~ Side Panel Parameter Select Side Panel Parameter Select #.~ MIG Press Side Panel Parameter Select Figure OM-1 588 Page 56 12-6. can Display Select program number to be de leted from card. Sequence >Card Delete under value that Deleting Programs From Card SECTION 13SETUP Setup 13-1. Flow Chart 2 r~ >Pulse/Mi1~ i~~~_ >s y s p t e m Range Secu r Display 2 Features 3 Settings e ~ Selections To set up features that customize b I a I 1 operation, y use the setup displays. Features that can be customized are as follows: Access Example Of Setup Display On Side Panel Features Display Settings Features Display Section Selection Section Settings Selection >System Process Capability Pulse/Mig Mig Only >Remote 13-3 Off/On Parameter 13-12 lncrease/ Decrease Press Mode Se lect To Go To Next Setup Display >Arc Time Run Hours ~ >Range Volt Mm 0.0- 25.0 V Volt Max 25.0 AmpMin 0-50A AmpMax 50-999A Program Number Lock Off/On - 13-4 Hours 0999,999 Cycles 13-13 No Reset 99.9 V Reset F >Self Test + } } 13-14 , >Secunty 13-5 >Wire Feed IPM/MPM Display Type Motor >Access Code Off/On 13-6 >Mig Type Voltage DVC On/Off 13-7 Speed High Speed >Model Model Type Correction ~r~ontrol 13-15 Standard Low + >Voltage 09999.99 Bench 13-16 Boom 17-Pin Feedback Volt Sense >Arc Start Arc Start Standard Hot Start >Dual Schedule Switch ~1emorY }~ese~f__ 13-8 13-17 I Type Type ~Shutdown 13-9 Momentary 2-Pole ~Jame 13-10 Maintained 2-Pole Maintained 1-Pole >Software No Volt Sense Off/On 13-18 Card Off/On 13-19 Programs Version Number) ) 13-20 Trigger >Trigger Program Select Off/On 13-11 _J I Figure 13-1. Setup Flow Chart OM-1588 Page 57 13-2. Using Setup Displays 1 Front Panel Front Setup Display panel display during setup. 2 Side Panel Mode And Para meter Select Buttons 3 Power Switch On Rear Panel Press and hold down both buttons while turning On unit. 4 Side Panel Setup Display Follow this procedure any time ac cess is required. Once in the setup displays, use the Mode Select but ton to select a / / / / I I I / / particular display. To save any or all of the changes made while in the setup dispays, and/or to exit the setup displays, turn power to the unit off and back on or press the gun trigger to retum to the Process display. 4 / .1 >System Range Security Process Capab i I i t y >Pulse/Mig Access Side Panel Display 13-2. Figure 13-3. Selecting N OTE ~ Process Accessing Setup Displays Capability This selection allows the wire feeder to be used with a variety of welding power Pulse This selection also determines whether Gas Metal Arc Welding sources. (Pu!se/Mig) GMAW-P Is available. 1 Example Welding Power Sources: Pulse/Mig 450 Ampere lnverter Model Mig Only 450 Ampere Non-Inverter Model = System Display When Process Capability is Pulse/ Mig, the wire feeder works with the = welding power source to produce either pulse GMAW-P or regular GMAW welds. When in Mig Only, the wire feeder works with the welding power source to produce regular GMAW welds. 1 Select the process the welding power source is able to do. When Mig Only is selected, some of the setup choices are automati cally made and are not available for selection by the operator. Figure OM-1588 Page 58 13-3. System Display 13-4. Selecting Welding N OTE ~ Power Source Range Welding power source minimum and maximum voltage required. Amperage values are required for pulse welding. 1 I Acces ~lay~ Setup >Vo 11 Range Display age ranges. Set values to match welding power source ranges. Mm 2 Minimum Range Access 3 Press Mode Select 0 Side Panel Parameter Select ~ 4 Mm >1Q~flVol Voltage Display is 25.0 to 99.9 volts. Minimum Amperage Display (Available When System Set For Pulse/Mig) Range 5 Voltage Display is 0 to 25.0 volts. Maximum Range Volt always welding power source Own ers Manual for voltage and amper 10 .OVo It Default values are for 450 Ampere Inverter Model. Do not change values if using 450 Ampere Inverter ModeL are See I System >Range Security values is 0 to 50 amperes. Maximum Amperage Display (Available When System Set For Pulse/Mig) Range is 150 to 999 amperes. 2 Increase/Decrease Side Panel Parameter Select Increase 3. ~ Side Panel Parameter Select ~ ~ Arnp~~ Side Panel ________________ Parameter Select *Use side Parameter Select panel button to select voltage or amperage. Use Increase/Decrease buttons to change value. Figure 13-4. Range Display OM-1 588 Page 59 13-5. Selecting Security NOTE ~ Lock Security lock works when only a data card is inserted (see Section 12-1). I Security Display Use this display to lock a programs weld parameters so that changes not be made controls. can 2 Program using front panel Number Choose the program number (1 through 8) to be locked. A program can be locked on one or both sides. 2 3 Program Lock When lock is off of operator Increase a program, the change all weld pa rameters of that program without restriction. The operator can also change Press Mode Select can Display sides without restriction. With lock on a program, the opera change parameters of that program but the range of change is restricted. If only one side is tor can locked, the operator cannot sides or program number. If both sides are locked, the opera change changes sides but change program number. tor can I Prog l>Lock 21 ~~~>Lock ~Hirim OJ 1PM 21 Prog Q~I In the ~ft~ cannot example displays in this fig operator could change the ure, the value of trim –10% and wire feed speed –100 ipm from programmed ___________ values, If the settings are left at 0, the operator cannot change values ~ from those programmed. If both sides are locked, they automatical Side Panel Parameter Select ly have the Prog 2 Lock On >Trim Q 1PM 0 ci 31 I>Prog Lock Of ~ 21 On 10~~ >Prog Lock Trim 1PM iool Figure Page 60 ,~ Prog Lock Trim > Side Panel Parameter Select Increase OM-1588 range of change. If dual schedule is on, the paired programs are locked and unlocked together. L...J same 13-5. Security Display lncrease/ Decrease 21 OnI iOI 1QQ~ 13-6. Selecting NOTE ~ Or Changing Access Code Access code works only when data card is inserted a (see Section 12-1). 1 Code With code displays ~1 Display off, access to With code on, the know and enter the i the setup is not restricted. access or change must code to any of the setup operator access displays. Range Cod Securi ty >Qf f >A e 2 Access With Display code set, this display ap pears when power is turned on while holding the side panel Mode and Parameter Select buttons. c c e S s Mig__Type Press Mode Select a Press side panel Parameter Select button to enter access code. When the correct letter is entered, the Increase automatically moves to the next character. When the final ac cursor code letter is entered, the dis play automatically changes to the initial setup display. cess Code >Qn AAA $ Cod Increase/Decrease To Set Code Parameter Select To Move Cursor a On >ZW?~ ~P r a $ S Turn Power Off And Back On And Access Security Display 2 I / Enter >Code AAA Access Code ~P Figure 13-6. r a s S Access Code Display OM-1588 Page 61 13-7. Selecting Voltage Correction 1 Mig Type Display With DVC Voltage Correction On, the unit uses closed-loop feedback from the 17-pin cord or voltage sensing leads to maintain set volt age parameters. Press Mode Select I Setup With DVC Voltage Correction Off, feedback from the arc is not used for closed-loop feedback to main tain voltage parameters. Feed back from the arc is still used for other functions. L \~isp~,,1~ Be sure voltage sensing leads are connected or voltage feedback is available from welding power source through the 17-pin recep tacle. Vo I t Co r g e t >D~ FIgure 13-8. Selecting Voltage Sensing NOTE 13-7. a r e c i o n Off Mig Type Display Method Voltage sensing feedback setting is Mig Only. is automatically set for V. Sense when the 1 System Voltage Feedback Display When using the 17 Pin setting, arc voltage feedback is through the welding power source, and the feedback signal is sent through the 17-pin cord ~_~ / Access~\ Press Mode Select to the feeder. If the 17 Pin setting is used, it is rec ommended that the voltage sens ing terminals on the welding power source be used to monitor arc volt age at the workpiece. Setup Display using the V. Sense setting, voltage feedback is through the voltage sense leads connected to the feeder. Use this setting when there is more than 50 ft (15 m) of When arc weld cable used. Figure OM-1588 Page 62 13-8. Voltage Feedback Display 13-9. Selecting Regular NOTE ~ Or Hot Arc Start Arc Start selection is not available when th e Do not use the Hot Start setting for .035 in System setting (9 mm) 1 or is Mig Only. smaller wire. 1 Arc Start Display Use the Hot Start mode for pulse welding with 450 Ampere Inverter Model when high initial weld cur rent is necessary to start large diameter welding wires. When in Hot Start, the 450 Ampere Inverter Model starts the arc in the CV mode and switches to CC once the arc is started. Do not use Hot Start unless using 450 Ampere lnverter Access Setup Display Model. Figure 13-10. Selecting Type 13-9. Arc Start Display Of Dual Schedule Switch 1 1 Dual Schedule Display Choose type of external dual schedule switch or use of the trigger as the dual schedule switch. -I L~ Swi ITyp ~>Ir tch e !gg~r F Increase Figure 13-10. Dual Schedule Displays OM-1588 Page 63 Momen 2P (Momentary Contact 2-Pole Switch Or 1 (DSS-10) 1 > 1 (DSS-9M) 1 > 1 DSS-10) > Maint 2P (Maintained-Contact 2-Pole Switch Or DSS-9M) 2 2 2 2 > 2 > Maint 1 P Or 3 Trigger (Maintai ned-Contact 1-Pole Switch Or DSS-9 Or DSS-8) A 3 1 2 0 C B 4 A 3 B 4 p 3 L (DSS-9) 1 > Adapter ~, 2 2 >~ 3 2 > 2 2 3 3 A\y~~> Figure 13-11. 3 13-11. Dual Schedule Switch 3 > BO > 2 > 3 4 ~ > 2 TB > 4 Adapter 1 > > BO A (DSS-8) 1 4 > Diagrams Selecting Trigger Program Select 1 / I Press Mode Select Access Setup Display -~--~ ArcStar t Prog DualSch d Sele Ct >Q1f >Trigger Remo t ram e Trigger Display When Program trigger can Select is On, the be used to switch be tween programs that have at least 0.2 seconds of preflow time. Briefly pressing and releasing the trigger switches programs. For example: it programs 1, 2, and 6 have preflow time of at least 0.2 se conds, pressing the trigger will gun switch from program ito 2, 2 to 6, and 6 to 1. Figure OM-1588 Page 64 13-12. Trigger Display 13-12. Selecting Remote Increase/Decrease Capability 1 Remote Display When Parameter Inc/Dec is On, the dual momentary-contact schedule switch can be used for weld parameters as well for between as switching changing programs. For example: when the the front panel display is cursor on on Trim Volts, the dual schedule switch or can be used to remotely change the value. When the front panel pa rameter select is on Prg, the dual schedule switch can be used to change the program number. A DSS-1O dual schedule switch is recommended for this purpose. Figure 13-13. Resetting 13-13. Remote Display Arc Time 1 Arc Time Display The unit accumulates arc hours up to 9999.99 hours or 999999 weld cycles before rolling over to zero (0). The arc timer can be reset us ing this display. Press Mode Select Figure 13-14. Arc Time Display OM-1588 Page 65 13-14. Using Self Test 1 Have only Factory Authorized perform tests or persons Switch A This checks the gun switch in replace parts. crease 2 position. Switch B This checks the gun switch de crease 3 position. Trigger This checks the gun Press Mode Select 4 trigger. Wire Feed This checks the wire feed motor. 5 Gas This checks the gas valve. 6 Contactor This checks the source 7 welding power contactor. CVICC This tests the pin at the 17-pin re ceptacle that controls whether the unit is in CC (constant current) or CV (constant voltage). 3 >1 r I g g s £ Off 5 ~ >Wi £ S f s Press d Increase ~ >~s s Of f~ Press Side Panel Parameter Select I~ ~ p ~. The welding wire and all metal parts in contact with it carry weld output when the welding power source contactor is energized. r e ~ On p _______ ~ Side Panel Parameter Select 7 6 ________________ _________________ I~n I Increase I Press >~V Side Panel Parameter Select Onft~H I ~ ___ Figure OM-1588 Page 66 I Increase ~ ~ 13-15. Self Test Procedure 1 oj r e s si 13-15. Selecting Units For Wire Feed Speed And Motor Type Wirefeed 1 Display The displayed unit of wire speed (1PM or MPM) can be changed along with the wire feed motor type (Standard, Low Speed, or High Speed). A low speed motor is not available for this unit. 1 Increase Display Display L 1PM 1PM Motor ype~ Motor > ~ > Type ~ Increase Figure 13-16. Selecting NOTE ~ Parameter Select Increase 13-16. Wirefeed Bench Or Boom Model Decrease Display Type This selection is not available when the System setting 1 is Mig Only. Model The unit is Type Display shipped from the factory set to Bench for bench feeders Boom for or Swingarc model feeders. The set ting loads the proper pulse param eters into memory for the model used. properly model This selection does not change when a memory reset is done. Figure 13-17. Model Type Display OM-1588 Page 67 13-17. Resetting Memory 1 No Reset Memory Setup cannot be reset. 1 Press Mode Select 2 Program Reset Press Parameter Select button to )-_- reset last active program to \~Display~lay factory program settings. original All other program and setup information mains the same. 3 re System Reset Press Parameter Select button to reset programs and setup to origi nal factory settings. System, Arc Time, and Model Type settings are not affected by the system reset. 4 r 4\ Reset (Default) Displays 2 >Process >Prg Sequence Pul Side Panel Parameter Select 1 se DualSchd 035 St ee Card Argon Oxy I Increase! Decrease 3 Side Panel Parameter Select Figure 13-18. Selecting 13-18. Resetting Memory Arc StartNolt Sense Error Shutdown 1 I Arc StartNolt Sense Shut down Display With Arc StartNolt Sense on, the unit shuts down when no arc volt age is sensed. If the unit shuts Press Mode Select down, an error message appears (see Section 14-4). With Arc Start/Volt Sense off, the unit continues to feed wire even when there is no arc voltage sensed. Figure OM-1588 Page 68 13-19. Voltage Shutdown Display 13-19. Selecting Program Name Feature 1 Name When Display program card is used, the programs written from the unit to the card can be named. Press Mode Select ~ Setup a )__. \~Dis~ay,/ Figure 13-20. 13-20. Naming Card Programs Software Version Number 1 1 / I Press Mode Select Setup 1. \~Dis~a~,J Memory Shutdo Ver sian wn #12 3456Z Example Version Display Number When talking with service person nel, this number may be required. (Check actual unit display for num ber.) The factory keeps this num ber on file with the serial number of the unit. Name >Sof twa Figure re 13-21. Version Number Display OM-1 588 Page 69 SECTION 14- MAINTENANCE & TROUBLESHOOTING a WARNING ELECTRIC SHOCK can Do not touch live electrical kill. HOT PARTS Allow parts. can cause severe cooling period before burns. servicing gun or unit. Turn Off wire feeder and welding power source, and disconnect input power before inspecting, maintaining, or servicing. MOVING PARTS can cause Keep away from moving parts. Keep away from pinch points injury. Maintenance such as drive rolls. to be performed only by qualified persons. wfwam4.1 8/92 14-1. Routine Maintenance = 3 Months Turn Ott all power before maintaining. Tape Or Replace Cracked Weld Cable Replace ~ Cracked Parts 14-Pin Cord ~ose~ Figure OM-1 588 Page 70 Gun Cable 14-1. Maintenance -~ 6 Months 14-2. Replacing The Hub Assembly I~*P~i~ READ SAFETY BLOCKS at start of Section 14 before proceeding. Turn Off wire feeder and welding power source. Retract wire onto reel and remove. Take hub apart as shown. 1 Retaining Ring 2 Hex Nut 3 Washer 4 Spring 5 Keyed Washer 6 Fiber Washer 7 Brake Washer 8 Hub 9 HubSupportShaft Replace worn or broken parts, and slide parts onto shaft in order shown. 9 Tighten hex nut until a slight force is needed to turn hub. Install welding wire (see Section 3-12). 6 7 7 6 5 4 Tools Needed: ~ 15/16 in 1 ST.142 709 Figure 14-2. Hub Assembly 14-3. Overload Protection i~H READ SAFETY BLOCKS at start of Section 14 before proceeding. Turn Off wire feeder and power 1 1 welding source. Circuit Breaker CB1 CB1 protects the wire feeder from overload, If CB1 trips, the wire feeder shuts down. Allow cooling period and manually reset breaker. Ref. ST-800 177 Figure 14-3. CircuIt Breaker CB1 OM-1588 Page 71 14-4. Error Displays I Release Trigger Error Display This appears if the trigger is closed when the unit power is turned on, or if the trigger is stuck or defective. 2 The No Volt Sensed Error Display circuit is not receiving feedback. Check voltage sensing connections. Check con nections at 17-position plugs/recep tacles at the unit and welding power voltage arc sense source. Turn unit off and back on after cor recting problem. Release If this error continues to Trigger pulse welding, it may help to select Hot Start (see Section 13-9). 2 3 No Memory CRC Perform Er Display a system reset. ror 4 :~ when The data in the program indicated is not the same data that was saved. Volt S ensed Error occur Memory Range Error Display The data in the program indicated is out of usable range. Memory CRC Prg Er 00 ror Go through pulse parameters to make sure they do not exceed set tings of the Range display (see Sec tion 13-4 and Section 7) or perform a system 5 Memory No Tach Sensed Error Prg The Range reset. reaching Error Display tach feedback is not the control. Check connec motor tions. Press front panel Parameter Select to clear error. No Tach Sensed 6 Er Arc Start Error Display This appears when pulse welding and current is detected but the arc cannot be started. Check and correct program pulse parameters and volt age settings. Check voltage sensing ror connections. Press front panel Parameter Select to clear error. 7 Arc Stop Error Display This appears when pulse welding and the motor does not stop at the end of the weld. If there is high fre quency being used in the area, turn it off. A motor brake circuit problem can also cause this error. Press front panel Parameter Select to clear error. Ref. ST.155 222 Figure OM-1588 Page 72 14-4. Error Displays 14-5. Troubleshooting £~ WARNING ELECTRIC SHOCK can Do not touch live electrical kill. HOT PARTS Allow parts. can cause severe burns. cooling period before servicing gun or unit. Turn Oft wire feeder and welding power source, and disconnect input power before inspecting, maintaining, or servicing. MOVING PARTS can cause injury. shooting to be performed only by qualified Keep away from moving parts. Keep away from pinch points such as drive rolls. Table 14-1. wtwam4.1 8/92 Troubleshooting Trouble Wire Remedy feeds, shielding gas flows, but energized. ~. -~ Section I Check interconnecting cord connections. electrode wire is not 3-9 -~ I ______________ 1 Wire feeder is on, meter(s) do not light up, motor does not run, gas valve and welding power source contactor do not pull in. ~ -~ Check and reset CB1. Electrode wire i. -~ Check gun trigger connection. feeding stops erratically during welding. or feeds -~ 14-3 -~ 3-7 Readjust drive roll pressure. -~ 3-14 Readjust hub tension. -~ Check gun trigger. Change Clean or to correct size drive roll. replace dirty Incorrect size Replace -~ or worn contact tip or or worn wire drive roll. guides. liner. Remove weld spatter or -~ 3-6B -~ 3-6B -~ 3-6A -~ foreign * matter from around nozzle -~ opening. Have Factory Authorized Service Station/Service Distributor check drive motor or motor control board PCi. i.. IP Wire does not feed until trigger is pulled, but continues to feed after trigger is released, and trigger hold is not on. ~ -~ Gas valve in feeder is rattling loudly along with possible erratic or slow wire 1 -~ feed J Motor runs slowly. speed. -~ ~ - Check for a short between welding gun trigger leads and weld cable. Repair short or replace welding gun. ~ -~ Check for a short between welding gun trigger leads and weld cable. Repair short or replace welding gun. 1 Check for correct input voltage. * * -~ _____________________________________________ Unit does not switch out of Run-In ~ Speed. I -~ Install, reconnect, or ___________ ~. replace voltage sensing lead. I -~ 3-9 I ____________ Wire feeder power is on, displays up, but unit is inoperative. light ~ -~ Check welding gun replace gun. trigger leads for continuity, and repair leads or * -~ I _____________ See gun Owners Manual. OM-1588 Page 73 SECTION 15- ELECTRICAL DIAGRAMS I CU~6CTIGH FOG RE(CTE PROGRAM SELECT (SEE L DSPL2 SIDE DISPLAY TLJ DSPL I FRONT DISPLAY lCd1 01 ~19~ H~H+i IOOTO 1 I~E~TGEGRDe~ DATA 0 0 P841 0 P642 ~U)E SELECT PARASETER SELECT ~rMf~iH~L I ~I .1-i ~lL~L ___________ ~ PLPGE 0 0 P821 0 0 P822 SC I 0/PLC 10 LEFT RIGHT ~OD TRIGGER ~O 0 0 P824 0 0 P823 LEFT TRIGGER ~D LED RCI 1/PIGI I SC I 2/PIG I 2 SC IS/PLO IS /0 RC26 >) SC I 6/PLC 16 2 PcI RCIi-S>>~~55 PcI I~S >>___*I5V PcI RIGHT N SELECT LED ____________ > PLG83I ~ 3> I I >...........~ - - - SC25-I~ 4 RC256 I SI0A8V~&K>I II N I> 2 I II 5020 PC2O ~4~024RC25-7 >>-~- I L'J r -i USED WITH SWDGARC OG CTAOIENT OGTIGH I I ~g ~ P1027/PIGS I 2~-<I I 2 ~ 2~-~2 >~l2~ 7 ~ i~-~i ~~ ~~ 1 Ii OGTICAL DEOGER GSI~ 16 ~ ~i 4~4~4>~<14~L ~ I I I I I I I i;~ 0 ~o ~ I UI P1G57/PIGS7 ~ p TK2 <24-~.<~ 2 <I 7 E~-< ~-~--~ >-~-< ~ ~ 5 AR RIGHT <:1 &K 2 GS2~ Figure OM-1 588 Page 74 N N vvvvvv 5025-I ~I MIT)I21> P1029 IflENT - RC2I > N - ~I 4 (OGTIGHAL) N ~T1J~ TRIGGER GECREINT /7 I 1P1G81 N Rd PcI L 5025-2 ~ I-8>>--~ >>~~~ PcI I-I LED LEFT SELECT LED I N J I ~~ I4>~ SC 11-4 SC I 7/PLC Ii RIGHT RC27> TRIGGER ~O 3 II L PC 10 MIEROGR~SSOG ROARD SC I 0 RC24 TRIGGER _______ P1028 CABLE ___ 14> 3>5JI3>~ I) 34 RC23 ~ 2>2>-~~ I ~ I)~I >.~.~~IOAB~&*.)I> RCIOO-5>> _________~ ~ ~OQANT FLOW SWIT0I GRW RCIOO-6>> c0~.ETOG 0 0 P825 1 r GRV RCIOO/PLGIOO RCIOI/PLGIOI RCIOO-3 > ~AAAAAA C.ETOG P10831 ARC St ~ Cd RC2O (GRTIOGAL) FILTER LEFT/RIGHT SELECT RC29 4?9114> 6 00000000 SELECT CA8LE P1023, 6 ~ ~ ______________ I 2 ~~1t~TGG ~T. I 6 RC4I/PLG4 ___ ______________ I IPLG8I i 6 PCIOO PC4O Cd p944 00 P831 IfETM)INT i 6 RC6I/DATACARD ~ ~ 00 ~ SUIPG~BC ~ i RCIOO-l>> CARD ~o I ~ 0 p843 PARAIETER wr~ ~im ? i SC 100-2 > Vvvvvvvvvvvvvvv __ ~ II ~ I 23406 I pC30 FIELD I~GTRI.CTIGH) I 15-1. Circuit ~ I 6 <IIE-~.~II>.LL<:I ~ <I ~ .E_.L.< 44~)~4 >_L<I4 ~ I (IS~ Diagram ~ 2 For Wire Feeder 5 I-7))--~ -I POCTE PEI~CANT I RPS-8 (OPTION) I PCII0 BPS-B SWITCH BOARD I RCIIO/Pt.GIl0 I ISHIELD .w,, RCI 104 - Ii i ~-((RCl I ID-I ~< PC 110-5 I 0PE~OANT ~ PC 110-2 L J PCBO FILTER BOARD PCR2/PLG82 ~jp~8~ RC89/PLG7S RC90.PIG9O i ~F Ic>~!~.c RC8I-C>~C/CV .24V-CVI RC8I-E>Q.J1RENT FEEO6AO( (IV/I0OA)IE).~E RC8I-G > DO.CTAl~ b-by) ~ ~ RCRI-H V~TA~ FEEDBAcK (IV/IOVI I ~ ~ RC8I-F > 17 I PIN ~34~4 I I I I I I UFAPPLICA&EIJ I r 45RC70 I ~o C~PENT ~ I > PC5O INTERFACE -i P1070 BOARD L RCSO/PL000 rIJSED.!Th SWIP1~A ~ DBTADINT ~TIDB RCS I/PIGS I RCS2/PLGS2 I I L ~ l~?r~ RCS3/PLGS3 ~ PC04/PIGS4 Rc554 Fi I~TID4AL) (SEE FIELD D~TRt~TICNS) DBIVE ASSY _______ Rc25/PIG5S PID(-LP(RISHT) -(< FEED-I <<Rcos-5 ,<<PcSS-2 >8 ________ -<<ps-6.~C~,.2W~_~. :~,C RC83>) L ~ DBIVE ASSY >~? PID(-LP(LEFT) a_Alp RCO9- I >>- RCR9-2>> I_____ RCB9-3>> acw RC8O)HF STUD PIN . ~ ccwAA~ I aot PLLAI Pt.69 )C ) E P.S. C , ,~ C N ,~ ~ acw F .0 P1019 191L0V ) F 2>I> I PCI MOTOR BOARD PCI/PIG I io POWER PC2/PLG2 PC3/PLG3 PC4/PLG4 RCD/PLG5 RCA/PLED L SD.164 541-B OM-1588 Page 75 PC 10 MICROPROCESSOR PC2O FRONT DISPLAY RC37 PLG33 OM-1588 Page 76 15-2. Wiring Diagram 4 ii~Oa TE~TP~ Figure PLG37 For Wire Feeder ~ PC, MOTOR BOARD PLG28 LEFT PLG38 RIGHT SD-164 540-B OM-1 588 Page 77 SECTION 16- PARTS LIST Co / N-. C~) r Co 0) C., CD U- C~J Co = Co Co C) Co U- CO C) U- ST-800 272-B Figure OM-1 588 Page 78 16-1. Main Assembly Quantity Item No. Model Part No. Dia. Mkgs. Figure 1 1 PLG21 ,23 . . 12 Description 16-1. Main Assembly CABLE, trigger (consisting of) CABLE, trigger (consisting of) 079 878.... CONNECTOR & PINS, (consisting of) 079 535 CONNECTOR, circ pin push-in 14-l8ga Amp 66359-6 079 531 CONNECTOR, circ clamp str rlf sz 11 Amp 206358-2 605 156.... CABLE, port No. 184/c (order by ft) 080 328.... CONNECTOR w/SOCKETS, (consisting of) 079 534 CONNECTOR, circ skt push-in 14-l8ga Amp 66358-6 See Note CONTROL BOX, (Fig 16-4) 164 475 CABLE, interconnecting (consisting of) 164 474... CABLE, interconnecting (consisting of) 149 251 ... 149 252 ... 2 2 1 . .. . . 2 3 3 1 2 CONNECTOR & PINS, 4 5 5 CONNECTOR, circ clamp .... str rlf sz 17-20 7 8 9 10 10 11 12 13 13 .. . . PLG11,17 PLG33,34 20 31 .... 2 17ft 1 .... .. .... 8 .... 4 ... 4 ... 1 ... 1 ... 1 .... .... 30ft 8 4 4 .... .... 4 1 1 1 1 1 .... .... .... .... 2 .... 2 .... 1 1 1 2 2 14.... 14 2 .... 2 2 .... 2 8 .... 8 ... 2 .... 2 .... 8 .... 8 ... ... ... 1 2 1 2 2 8 2 2 ... LINER, monocoil inlet wire BUS BAR, connecting weld current .... .... .... 1 2 1 .... 2 .... 2 .... 8 .... .... 2 2 3ft.... 3ff 1 1 2 4 ... 082 050... 164 969 2 21ft 1 (consisting of) ... GS1 ,2 2 1 1 ... 1 1 4 16-7... BOOM ASSEMBLY CONNECTOR, circ skt push-in 14-l8ga Amp 66358-6 048 144... CONNECTOR, circ pin plug keying Amp 200821-1 115 092 CONNECTOR & SOCKETS, (consisting of) 113 746.... CONNECTOR, rect skt 24-l8ga Molex 39-00-0038 CONNECTOR & PINS, (consisting of) 135 409 114 656 CONNECTOR, rect pin 24-l8ga Molex 39-00-0040 139 813 COVER, protector motor 125 785 VALVE, 24VAC 2 way custom port 1/8 orE 139816... PANEL,endcover 159 647... INSULATOR, motor clamp 156243... CLAMP, motortop 159 360 INSULATOR, screw machine 159 646 CLAMP, motor base 145 639... STRIP, buna N compressed sheet .062 x 4.000sq 134 834... HOSE, SAE .187 ID x .410 OD (order by ft) 167 774... DRIVE ASSEMBLY, wire RH (Fig 16-5) .167 776... DRIVE ASSEMBLY, wire RH (high speed) (Fig 16-5) 157295...GUIDE,monocoil 604 612 SCREW, set stl sch 8-32 x .125 cup point 1 4 2 ... ... 2 2lft 14.... 14 ... 079 534.... 1 4 2 ... 17.... RC27,37 32 .... .. 605227... NUT, nyl hex jam .75ONPST CONNECTOR & SOCKETS, 047 637 29 .... 26ft 16 28 29 .... ... Fig 26 27 .. .... 15 25 .. ... 14 ...24 .... ... 13 23 206322-2 .. ... 13 ...22 Amp .... ... 6 21 2 (consisting of) CONNECTOR, circ pin push-in 14-l8ga Amp 66359-6 .... 2 CABLE, port No. 18/14 8/c (order by ft) 159 297... HOSE ASSEMBLY, gas 139600... HOSE, gas 139 599 HOSE, gas 600 324 CABLE, weld cop strd No. 4/0 (order by ft) 602 243 WASHER, flat stl std .375 602 213 WASHER, lock stl split .375 601 872 NUT, sti hex full .375-16 080 947 BRACKET, spring retaining 151 626... BRACKET, spring retaining 132053... SCREW, cap stl hexhd .375-16 x 1.500 Ig SUPPORT, hub & reel Fig 16-2 .149838... PIPE POST, 4ft w/base or .149 839... PIPE POST, 6ft w/base PIPE POST, 4ft w/base or .078 264 PIPE POST, 6ft w/base 079 216 PIPE POST, 4ff w/o base .075 078 079217...PIPEPOST,6ftw/obase 163 519 4 ... 047 636.... 079 739 19... 1 .. ... 079 535 18... l7tt . PLG27,28, 37,38 4 2 .... PLG28,29 16 2 1 .... .... .... .... .... .... 1 1 2 4 2 1 OM-1 588 Page 79 Quantity Item No. Model Part No. Dia. Mkgs. Description Figure 16-1. Main 33 .167 782 ... NOTE: When ordering Control Box contact OPTIONAL Factory 16 Assembly (Continued) 167780... DRIVE ASSEMBLY, wire LH DRIVE ASSEMBLY, wire LH ..33 12 Service 1 (Fig 16-5) (high speed) (Fig 16-5) Department 1 .... .... 1 1 for proper number. BE SURE TO PROVIDE MODEL AND SERIAL NUMBER WHEN ORDERING REPLACEMENT PARTS. Item No. Part No. Description Figure 1 .... 2 .... 3 .... 2 WASHER, flat stl keyed 1.500dia x .l25thk WASHER, fbr .656 ID x 1.500 OD x .125thk WASHER, brake stl 2 HUB, spool SUPPORT, reel REEL, wire 60 lb (consisting of) SUPPORT~ reel spool RETAINER, spool support (consisting of) LABEL, caution falling wire reel can cause damage 2 010191 .... 058628 .... 058428 080393 10... 108008 ...11.... 124900 .... 12... +168 104 13.... 12) 2 .... 9 16-1 Item slflkg hex reg .625-11 w/nyl insert WASHER, flat stl .640 ID x 1.000 OD x l4ga thk SPRING, cprsn .970 OD x .120 wire x 1.250 6 8 (Fig RING, retaining spool .... 7 Hub & Reel NU1 stl 5 .... Support, 058427 136684 605941 010233 057971 4 16-2. Quantity 166594 168103 NU1 spanner 2 2 4 4 1 2 1 1 1 1 retaining 2 8 7 9 ST-081 760-C Figure . 16-2. Support, Hub & Reel OPTIONAL +When ordering a component originally displaying a precautionary label, the label should also be ordered. BE SURE TO PROVIDE MODEL AND SERIAL NUMBER WHEN ORDERING REPLACEMENT PARTS. OM-1 588 Page 80 Item Dia. No. Mkgs. Part No. Figure 2 167697.. . 147 139 164 842 144 844 6 .... 171 814 PC2O,30. PLG25 165 484 147 995 PLG24.... ...8 167 633 10 089 032 153 169 010291 11 167 700 16-3. Panel, Front w/Components (Fig 16-4 Item 28) NAMEPLATE, (order by model and serial number) PANEL, front TAPE, adh acrylic double sided .010 x .500 x 3.000 METER LENS, w/gasket STAND-OFF, 6-32 x .875 Ig CIRCUIT CARD, schd front CONNECTOR & SOCKETS, (consisting of) CONNECTOR, rect skt 22-1 8ga Amp 770904-3 See 159 264 Quantity Description Figure 1 1 2 1 9 1 1 8 16-2 Item 35 RING, ext .625 shaft grv x .O4Sthk E style WASHER, shldr .612 ID LENS, LED 4341 red panel mtg ACTUATOR, switch WASHER, flat .625 ID nylafil KNOB, pointer 1 1 4 6 1 1 4 1 9 13 12 ST-800 112-C 11 Figure 16-3. Panel, Front w/Components BE SURE TO PROVIDE MODEL AND SERIAL NUMBER WHEN ORDERING REPLACEMENT PARTS. OM~1588 Page 81 N. cJ C 0) c~4 C.) Co 0) U- 0) C Co 0) U- 0 C) e C) C~J c5 C.) C) C.) ST-800 273-A Figure OM-1 588 Page 82 16-4. Control Box Dia. No. Mkgs. Part No. Description Quantity - Item Figure 2 .... RC3O,40. 162 253 047 637 079 534 048 144 PCi 134 201 155 114 PLG1 115 092 113 746 PLG2 115 093 113 746 PLG4 115 091 113 746 PLG6 CB1 8 .. Si PC8O, RC81 PLG75 PLG82 PLG9O 136810 114 066 161 706 083 432 111 997 163 921 131 204 113 746 158 720 147 995 153501 147 995 073756 10 151 187 ii +162 364 010 325 13 134 464 14 163519 141 162 PLG9 134 731 079 739 16 PLG19 17 158719 147 995 601 222 176 089 19 ...22 ...23 ...24 ...25 600 399 138 044 RC7O 000 527 CR101 SRi ...26 072 817 035 704 030 170 145 948 Fig 16-3 ...27 ...28 29 107 983 048 282 079 534 PLG12,50 155 629 154 938 ...32 PC5O PLG51 PLG52 PLG53 PLG54 097 132 163 917 158 720 147 995 158 719 147 995 131 204 113 746 148 439 147 995 16-4. Control Box (Fig 16-1 Item 2) PANEL, side lower CONNECTOR & SOCKETS, (consisting of) CONNECTOR, circ skt push-in 14-l8ga Amp 66358-6 CONNECTOR, circ pin plug keying in sockets Amp 200821-1 STAND-OFF SUPPORT, PC card .3121.375 CIRCUIT CARD, motor control CONNECTOR & SOCKETS, (consisting of) CONNECTOR, rect skt 24-1 Bga Molex 39-00-0038 CONNECTOR & SOCKETS, (consisting of) CONNECTOR, rect skt 24-1 8ga Molex 39-00-0038 CONNECTOR & SOCKETS, (consisting of) CONNECTOR, rect skt 24-l8ga Molex 39-00-0038 CONNECTOR & SOCKETS, (consisting of) 1 2 14 4 10 1 1 8 1 6 1 10 1 CONNECTOR, rect skt 20-l4ga Amp 350536-1 CASE SECTION, bottom/rear CIRCUIT BREAKER, man reset 1P 1OA 250V SWITCH, rocker SPST 1OA 25OVAC 4 1 CIRCUIT CARD, HF filter dual CONNECTOR & SOCKETS, (consisting 1 1 1 of) 24-l8ga Molex 39-00-0038 CONNECTOR & SOCKETS, (consisting of) CONNECTOR, rect skt 22-l8ga Amp 770904-3 CONNECTOR & SOCKETS, (consisting of) CONNECTOR, rect skt 22-l8ga Amp 770904-3 STAND-OFF, 6-32 x .625 Ig LATCH, slide flush mtg hole 1.000 wide x 1.500 Ig CONNECTOR, 1 rect skt 3 1 12 1 6 2 1 WRAPPER 1 BUSHING, strain relief .840 ID x .875mtg hole LABEL, warning general precautionary CABLE, port No. 18/14 8/c (order by if) CONNECTOR & PINS, (consisting of) CONNECTOR, circ pin push-in 14-lBga Amp 21 3603-1 CONNECTOR, circ clamp str rlf sz 17-20 Amp 206322-2 CONNECTOR & SOCKETS, (consisting of) CONNECTOR, rect skt 22-l8ga Amp 770904-3 CLAMP, univ5oA TUBING, plstc PVC .250 ID x .375 OD x 9.000 WIRE, strd l4ga blk 600V 105c (order by if) BUSHING, strain relief .120/.150 ID x .SOOmtg hole BLANK, snap-in nyl .500mtg hole CONNECTOR w/SOCKETS, (consisting of) CONNECTOR, circ skt push-in 14-lBga Amp 66358-6 BLANK, snap-in nyl .875mtg hole RELAY, encl24VAC DPDT RECTIFIER, integ 40A 800V BUSHING, snap-in nyl .750 ID x 1 .000mtg hole BRACKET, mtg control box PANEL, front w/components CABLE, ribbon l4posn STRIP, mtg PC card STAND-OFF, 6-32 x .375 Ig CIRCUIT CARD, interface CONNECTOR & SOCKETS, (consisting of) CONNECTOR, red skt 22-l8ga Amp 770904-3 CONNECTOR & SOCKETS, (consisting of) CONNECTOR, rect skt 22-l8ga Amp 770904-3 CONNECTOR & SOCKETS, (consisting of) CONNECTOR, rect skt 24-l8ga Molex 39-00-0038 CONNECTOR & SOCKETS, (consisting of) CONNECTOR, rect skt 22-l8ga Amp 770904-3 1 1 12ft 1 14 1 1 2 1 1 35ft 1 1 1 4 1 1 1 3 1 1 1 1 4 1 1 12 1 2 1 3 1 10 OM-1588 Page 83 Item No. Dia. Part Mkgs. No. Description Figure PLG55 115 092 113 746 PC1O 126 689 161 781 PLG11 115 092 113 746 PLG15 153 501 147 995 PLG17 115 093 113 746 35... 36... PLG1O,24 PLG16,41 170 980 155 023 Fig 16-6 158 373 097 868 116 964 600 343 097 866 059 712 010 145 +When ordering a Quantity 16-4. Control Box (Fig CONNECTOR & SOCKETS, 16-1 Item 2) (Continued) (consisting of) 1 CONNECTOR, rect skt 24-1 8ga Molex 39-00-0038 STAND-OFF, 6-32 x 1.500 Ig CIRCUIT CARD, processor w/proms CONNECTOR & SOCKETS, (consisting of) CONNECTOR, rect skt 24-l8ga Molex 39-00-0038 CONNECTOR & SOCKETS, (consisting of) CONNECTOR, rect skt 22-l8ga Amp 770904-3 CONNECTOR & SOCKETS, (consisting of) CONNECTOR, rect skt 24-l8ga Molex 39-00-0038 CABLE, ribbon 34posn CABLE, ribbon 24posn PANEL, side 8 4 1 1 8 1 6 1 6 1 1 1 w/components CABLE, interconnecting pwr (consisting of) CONNECTOR, circ l7skt plug Amphenol MS-3106A-20-29S CONNECTOR, circ clamp slf sz 20-22 Amphenol MS-3057-1012 CABLE, port No. 165/c (order by ft) CONNECTOR, circ 17 pin plug Amphenol MS-3106A-20-29P CLIP, component .437dia mtg adh back CLAMP, nyl .500 clamp dia 1 1 . .... component originally displaying a precautionary label, the label should also 2 lOft 1 2 1 be ordered. BE SURE TO PROVIDE MODEL AND SERIAL NUMBER WHEN ORDERING REPLACEMENT PARTS. 17 .18 9 20 SeeTablel6-1 For Drive Roll & Wire Guide Kits 16 22 6 8 10 12 24 25 7 31 6 4 5 2 ST-152 711-D Figure OM-1 588 Page 84 16-5. Drive Assembly, Wire Item No. Dia. Part No. Mkgs. Description Figure 3 4 Wire (Fig 16-1 Items 29 & 33) 6 6 7 8 9 10 11 M1,2 M1,2 ... 4 ... 4 4 PIN, rotation arm rocker NUT, .250-28 stl 163 281 SPRING, pressure arm retaining LH 165 798... SPRING, pressure arm retaining RH painted end (shown) 165 799 WASHER, flat .257 ID sti 132 750 ARM, pressure 150 520 SPACER, rotation pin 133 493 RING, retaining ext .250 shaft x .O25thk 133 350... PIN, hinge 156 354 MOTOR, gear 1/Bhp 24VDC 272RPM (consisting of) 156 353... MOTOR, gear 11Bhp 24VDC 500RPM (consisting of) 153 491 KIT, brush replacement (consisting of) 153 492 CAP, brush *153 493 BRUSH, carbon 155 098.... KIT, cover motor gearbox (consisting of) 153 550 COVER, motor gearbox (consisting of) 155 099 GASKET, cover 155 100 SCREW, cover 154 031 SPACER, locating 133493 RING, rtngext.2soshaftgrvx.O2Sthk 115 092 CONNECTOR & SOCKETS, (consisting of) 113 746 CONNECTOR, rect skt 24-1 8ga Molex 39-00-0038 131 203 CONNECTOR & PINS, (consisting of) 114 656 CONNECTOR, rect pin 24-l8ga Molex 39-00-0040 135 409 CONNECTOR & PINS, (consisting of) 114 656 CONNECTOR, rect pin 24-l8ga Molex 39-00-0040 010 837... PIN, spring CS .093 x .625 137 248... SPRING, indicator 129 351 SCREW, hexwhd-slt stl slffmg 8-32 x .500 602 200 WASHER, lock sti split No. 8 604 772 WASHER, flat stl SAE No.8 165 934 SPRING, cprsn .573OD x .088 wire x 1.062 Ig 149 486 163 282 5 12 Assembly, 010 668 SCREW, cap sti sch .250-20 x 1.500 172 075... CARRIER, drive roll w/components 149 962 SPACER, carrier drive roll 1 2 12 16-5. Drive Quantity ... 2 ... 2 ... 2 2 ... 2 ... 2 ... 2 ... 2 1 1 ... ... 1 1 .... 13 PLG29,39 ... 2 2 1 1 1 5 2 1 1 ... B .... PLG51,57 ... 1 ... 3 .... RC7,8 1 ... 8 .... 14 15 16 17 18 19 1 1 ... 1 ... 1 ... 1 ... 2 BUSHING, spring spring 132747...CARRIER,shaft 152 241 KNOB, extension 133 739 WASHER, fIat .375 ID x .625 OD x .062 CIRCUIT CARD, digital tach (consisting of) 153 631 131 204.... CONNECTOR & SOCKETS, (consisting of) 113 746 CONNECTOR, rect skt 24-lBga Molex 39-00-0038 604 311 GROMMET, rbr .250 ID x .375mtg hole 20 132 746... 2 21 132 824... SHAFT, 1 ...22 23 24 25 TK1 ,2/PC51 PLG57 .. .... 1 ... 1 ... 1 ... 1 1 3 1 .... ... OPTICAL ENCODER DISC FITTING, brs barbed M 3fl6tbg ADAPTER, gun/feeder LH 26 132 611 ... 27 149 959 ... 28 28 149 746 149 745 ... 29 108 940 ... 30 604 538 ... 31 151437... 32 128237... 149 527... COVER, drive roll 601 872 NUT, stl hex full .375-16 602 213 WASHER, lock stl split .375 33 34 35 36 37 38 ... 1 x .312-24 1 1 ADAPTER, gun/feeder RH SCREW, cap sti hexwhd .250-20 WASHER, flat stl SAE .312 1 x .750 4 1 KNOB,plstcTl.l25Igx.312-lBxl.500bar SCREW, hexwhd-slt stl slftmg 10-32 x .500 1 2 1 ... 1 ... 1 602 243 WASHER, flat stl .375 149 964... PIN, groove .25Odia x .500 Ig 601 966 SCREW, cap stl hexhd .375-16 1 ... ... 2 x 1.250 1 OM-1588 Page 85 Item No. Dia. Part No. Mkgs. Description Figure 16-5. (Continued) Drive Assembly, 167 387... SPACER, locating 168 825 DRIVE, pinion 133 308... RING, retaining ext .375 shaft 39 40 Quantity Wire (Fig 16-1 Items 29 & 33) 2 1 ... 41 x .O25thk 1 Optional High Speed Motor Spare Parts. *Recommended BE SURE TO PROVIDE MODEL AND SERIAL NUMBER WHEN ORDERING REPLACEMENT PARTS. Table 16-1. Drive Roll And Wire Guide Kits G) ~ Wire Size ~ ~ V-GROOVE U-GROOVE VK-GROOVE ~ 4 RoIl Kit Drive Roll 149518 151024 087130 150993 149518 151025 053695 0.9mm 150993 149518 151026 .045in. 1.1mm 150994 149519 .052in. 1.3mm 150994 1.6mm 1.8 4 RoIl Kit Drive Roll 4 Roll Kit Drive Roll 053700 151036 072000 151052 132958 151027 053697 151037 053701 151053 149519 151028 053698 151038 053702 150995 149520 151029 053699 151039 053706 mm 150995 149520 (.079in.) 2.0mm 150995 149520 151040 (.094in.) 2.4mm 150996 149521 2.8mm 150996 3.2mm 150997 Metric .023-.025in 0.6mm 150993 .03Gm. 0.8mm .035in. (.062in.) .068-072 in 4 RoIl Kit Drive Roll 132957 151070 083489 151054 132956 151071 083490 151055 132955 151072 053708 151 056 132959 053704 151057 132960 151073 053710 151041 053703 151058 132961 151074 053709 149521 151042 053705 151059 132962 151075 053711 149522 151043 053707 151060 132963 151076 053712 ~ Fraction UC-GROOVE E~ 5/64 in. S-0549-C Each Kit Contains An Intet Guide, Intermediate Guide, And 045 233 Antiwear Guide With 604612 Setscrew 8-32 With 4 Drive Rolls. 2 Kits Required For Dual Models. OM-1588 Page 86 x .125, Along Item No. Part No. Dia. Mkgs. Description Figure 147 139 155 024 154 933 PC6O PLG6O 156 623 153501 147 995 PLG41 ...6 PC4O 158 160 144 844 154 109 ...8 153 169 16-6. Panel, Side Quantity w/Components (Fig TAPE, adh acrylic double sided .010 LENS, clear anti-glare PANEL, inner control CIRCUIT CARD, data card x .500 x 16-4 Item 37) 3.000 2 1 1 1 CONNECTOR & SOCKETS, (consisting of) 1 CONNECTOR, rect skt 22-l8ga Amp 770904-3 6 See Figure 16-3, Item 40 CIRCUIT CARD, side display 1 STAND-OFF, 6-32 x .875 lg PLATE, ident inner control ACTUATOR, switch 4 1 4 5 6 7 9 8 9 ST-800 113-B Figure 16-6. Panel, Side w/Components BE SURE TO PROVIDE MODEL AND SERIAL NUMBER WHEN ORDERING REPLACEMENT PARTS. OM-1 588 Page 87 C) cJ c~, ~ \ u~ \ I- CD cJ c..J F c.J ST-142 306-F Figure OM-1588 Page 88 16-7. Boom Assembly Quantity Model Part Item No. No. Description Figure 16-7. Boom Assembly (Fig I 12 16-1 Item 16 15) .1. 010 313 PIN, cotter hair .072x1.437 4 .... 4 .2. 010 910 8 .... 8 .3. 139 590 2 .... 2 .4. 079 667 .4. 080 812 .5. 079 632 9 160 513 WASHER, flat stl SAE .375 PULLEY, V sgl grv 8.875dia x 8.000P x .375 bore PIPE, plstc .500 x 133.750 PIPE, plstc.500x181.750 BOLT, U stl .250-20 x .875 wide x 1.375 deep GUIDE, wire GUIDE, wire GUIDE, wire inlet LINER, monocoil 3/32-1/8 wire x 15.687 BOOM, dual BOOM, dual 10 073 742 PIN,clevis.7500Dx2.156Ig 1 11 073 741 1 12 079 029 13 075 462 14 602 250 15 079 020 16 155 335 17 149 858 17 151 625 18 19 150 258 024 605 20 075 101 21 079 030 22 +174 754 CLEVIS, .812 yoke 6.062 Ig .750-l6thd NUT, stl hex full fnsh .750-16 SHAFT, boom counterbalance WASHER, flat stl SAE .750 NUT, stl hex elastic stop .750-16 PIPE, blk 3.000 x .875 SPRING, cprsn 3.750 OD x .625 wire x 36.000 SPRING, cprsn 3.750 OD x .640 wire x 36.000 RETAINER, spring BEARING, ball thr sgl row .750 x 1.625 x .625 NUT, stl hex special .750-16 x 1.250 WASHER, lock stl ext tooth .750 BASE, swivel boom (consisting of) FITTING, grease 1/8NPT BRACKET, mtg control tilt LABEL, Swingarc caution heavy spring LABEL, warning general precautionary BOLT, mach stl hexhd .750-16 x 2.750 KNOB, T-bar .500-l3thd WASHER, flat stl std .500 BUSHING, snap-in nyl .625 ID x .875mtg hole GUARD, motor protector 6 079 665 6 080 811 7; 079 664 8 139 633 9 159 999 080 157 174 688 23 142 804 134 327 24 073 666 25 047 224 26 602 246 27 010 493 28 139 818 +When ordering a component originally displaying a precautionary label, 2 2 8 .... 10 2 2 2 .... 2 2 .... 2 1 1 2 1 2 1 .... .... .... .... .... .... 1 1 2 1 2 1 1 1 1 1 1 1 1 1 .... .... .... .... .... 1 .... 1 .... 1 1 .... .... 1 .... 1 .... 1 .... 1 .... 1 .... 1 1 1 1 1 1 1 1 1 1 1 1 1 1 the label should also be ordered. BE SURE TO PROVIDE MODEL AND SERIAL NUMBER WHEN ORDERING REPLACEMENT PARTS. OM-1 588 Page 89 OPTIONS AND ACCESSORIES WELD CURRENT SENSOR (#160 963) Required when using the 64M feeder with Miller conventional MIG power have sources that do not 17-pin receptacle. POWER SOURCE DATA CARDS RPS-8 REMOTE PROGRAM SELECTOR WATER FLOW SAFETY SWITCH (#160 977) Eight-position rotary switch used remotely select weld programs. Includes a 33 ft. (10 m) cord. Used with the water hose kits. Protects water-cooled gun from WIRE STRAIGHTENER For .035 .045 in. (0.9- 1.1 wire - Data card is inserted into feeder, and with a push of a button, the feeder is automatically programmed for the power source being used. Each data card contains eight factory-written programs and 24 unused spaces for customer-developed programs. (#164 583) to overheating by shutting system if DUAL SCHEDULE SWITCHES Used with Dual Schedule Control in 64M feeder. mm) DSS-8 (#141 580) For 1/16 - 1/Bin. (1.6- 3.2 For 10 ft. (3 m) gun (#079 691) For 15 ft. (3 m) gun (#079 693) Requires adapter cord (#157 364). Two-position trigger switch that eÆ~ily attaches to the welding gun. Used in place of the standard trigger for dual scheduling. mm) wire (#141 581) Reduces cast in wire. Improves wire feeding performance and increases life of gun liner and tip. contact Data Cards for Conventional MIG Power Sources: (#164 162) for Deltaweldfi 300 (#164 161) for Deltaweldfi 451 (#164 (#164 (#164 (#164 160) 163) 164) 165) HIGH-SPEED MOTOR For single and right side of dual for Dimensionfi 400 for Dimensionfi 650 for XMTfi 200 CC/CV DSS-9M For 10 ft. (3 models. for Deltaweldfi 651 (#132 129) Factory only For left side of dual wire models. (#132 130) Factory only speed range of 90 1400 1PM (2.3 35.6 rn/mm.). Not recommended for wire sizes larger than 5/64 in. (2.0 mm). Provides wire - - Data Card for Pulse MIG and Conventional MIG Power Source: (#164 166) for XMTfi 300 CC/CV XMT 300 CC/CV data card includes eight synergic pulse programs: .035 in. steel wire with Argon/Oxygen shielding gas each side of the dual wire Factory-written synergic Pulse MIG programs will not operate with high-speed motor. gas using Argon/CO shielding gas .045 in. 309L stainless steel wire using Argon/CO shielding gas 3/64 in. 4043 aluminum wire using Argon shielding gas 3/64 in. 5356 aluminum wire using Argon shielding gas .035 in. nickel wire using Argon/Helium shielding gas .035 in. silicon bronze wire using Argon shielding gas 64M DATA CARD Blank Card Stores up to 32 complete weld programs. Ideal for saving custom programs and transferring programs to other 64M feeders. (3 m) Swingarc style feeders (#159 288) 23 ft. (7 m) (4.9 m)Swingarc style For 16 ft. feeders (#159 289) 27 ft. m) gun (#041 792) For 15 ft. (4.6 m) gun (#041 793) Two-position slide switch that attaches to the welding gun. Selects welding condition when utilizing the dual schedule feature. Gun trigger operates as standard trigger. DSS-10 REMOTE INCREASE! DECREASE SWITCH (#042 749) Two-position, momentary WATER HOSE KIT .035 in. 309L stainless steel (#155 910) on modeis. For 12 ft. .045 in. steel wire with Argon/Oxygen shielding lmportant:Same speed motor must be used down water does not flow. (8.2 m) Used with Miller coolant systems and GW Series water-cooled welding guns. Can be used with or without optional water flow safety switch. contact switch that attaches to the welding gun. Used with the Remote Parameter Increase/Decrease feature to fine tune parameters at the welding gun while welding. Gun trigger operates as standard trigger. WIRE REEL ASSEMBLY (#108 008) Accommodates 60 lb. (27 kg) coil of wire. Note:If water kit is to be used on both sides of a dual wire feeder, a kit must be ordered for EACH side of the feeder. Y WATER HOSE KIT (#165 491) Required when using EXTENSION CORDS For optimum performance, do not extend 64M feeder more than 60 ft. (18 m) from power source. 14-Pin Extension Cord a water hose kit on each side of a dual wire feeder. Connects both kits to one water coolant system. (#122 973) 25 (#122974)50 ft. (#042 120)25 ft. (7.6 m) ft. (15 m) 17-Pin Extension Cord (7.6 m) 11n3 OPTIONS AND ACCESSORIES MILLER GMAW (MIG) GUNS Water-Cooled Guns Refer to literature Index No. Mu 3.4. Radiator 2A, 230 VAC COOLANT SOLUTION (#042 493) 1.5 gal. (5.7 L) (For Extra Freezing Protection) (#128 705) Resists freezing to 00 F (-18 C). capacity. Watermate~ 1A, 115 VAC Air-Cooled Guns Refer to literature Index No. M/9.O. tank 2 (#042 495) gal. (7.6 L) tank important: Distilled capacity. water is recommended. Coolmate~ 4, 115 VAC WATER COOLANT SYSTEMS (#042 288) gal. (15.1 L) tank Radiator 1A, 115 VAC 4 (#042 492) 1.5 gal. (5.7 L) Refer to Water Coolant Systems literature, Index No. AY/7.2. tank capacity. capacity. MOUNTING EQUIPMENT FOR SWINGARC BOOMS One of the following is required for mounting the SS-64M and DS-64M Swingarc~ booms: Swingpakmi Base and pipe post with base two gas better organize components and cables. Base includes a Note: To mount three-compartment storage locker. plate CBC Cart (for with 12 ft. 3.7 ml model only) and pipe post without base plate use Pipe Post The entire unit a forktift truck. can be moved with CBC CARTS For 12 ft. (3.7 m) boom only provide mobility and SWINGPAKm BASES Designed SWINGPAK-1 2 neat, orderly arrangement of (#085 276) for 12 ft. (3.7 m) to welding equipment. SWINGPAK-1 6 (#085 934) for 16 ft. (4.9 m) boom Note: A pipe post with a base plate Is required and must be ordered separately. a The CBC is (254 mm) diameter by 2 in. (51 mm) wide wheels. The CBC-HD heavy-duty model is designed for use on rough or uneven surfaces and features 12 in. (305 mm) diameter by 3 in. (76 mm) wide Accommodates wheels. Both models Swingarc accommodate a power source, feeder system, water a a 12 ft. and (3.7 m) Swlngarc feeder system on a CBC Cart, a 6 ft (1.8 m) pipe post is requIred (#079217). The 4 ft (1.2 m) pipe post Is NOT recommended. The 16 ft. (4.9 m) Swlngarc feeder cannot be used. CBC CART FEATURES 2000 lb. (907 kg) load capacity the standard model with 10 in. boom (3.7 m) Swingarc feeder, cylinders. coolant system, and gas cylinder. plate is solid to help ft. The base power source, 12 Multi-position boom Swing-out outriggers Wide front wheel stance and automotive type steering Mounting facilities for most Miller CV power sources Compartment in base of cart to add ballast weight when using lightweight power sources. Minimum ballast weight of 300 lbs. (136 kg) required Fold-up gas bottle loading ramp 11193
advertisement