- Vehicles & accessories
- Motor vehicle accessories & components
- Engine
- Westerbeke
- 7.5 BTDAR - 50 Hz
- Manual
advertisement
▼
Scroll to page 2
of 66
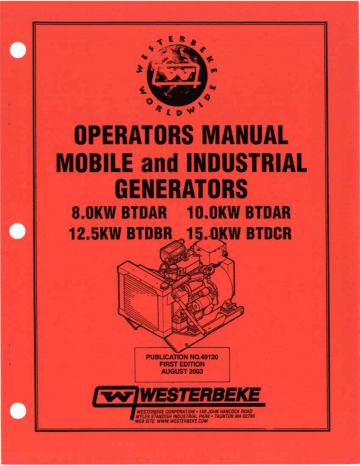
OPERATORS MANUAL MOBILE and INDUSTRIAL GENERATORS 8.0KW BTDAR —10.0KW BTDAR WESTERBEKE CORPORATION = 150 JOHN HANCOCK ROAD MYLES STANDISH INDUSTRIAL PARK « TAUNTON MA 02780 WEB SITE- WWW. WESTERBEKE COM dA WARNING Exhaust gasses contam Carbon Monoxide, an odorless and colorless gas. Carbon Monoride is poisonous and Can Cause unconsciousness and death. Symptoms of Carbon Monoride exposure can include: » Dizriness * Throbbing in Temples = Narcea » Muscular Twitching » Headache » Vamiting » Weakness and Sleepiness» Inability to Think Coherentiy IF YOU OR ANYONE ELSE EXPERIENCE ANY OF THESE SYMPTOMS, GET DUT INTD THE FRESH AIR IMMEDIATELY. If symptoms persist, seek medical attention. Shut down the anit and do aol restart until i has been inspecied and repaired. SAFETY INSTRUCTIONS INTRODUCTION Read this safety manual carefully. Most accidents are caused by failure to follow fundamental rules and precautions. Know when dangerous condifions exist and take the necessary precautions Io protect yourself, your personnel, and your machinery. The following safety instructions are in compliance with the American Boat and Yacht Council (ABYC) standards. ÁN WARNING: Do not touch AC electrical connections while engine is running. Lethal voltage is present at these connections! Em Do not operate this machinery without electrical enciosures and covers in place. E Shut off electrical power before accessing electrical equipment. E Use insulated mats whenever working on electrical equipment. B Make sure your clothing and skin are dry, not damp (particularly shoes) when handling electrical equipment. E Remove wristwatch and all jewelry when working on lion E Electrical shock results from handling a charged capacitor. Discharge capacitor by shorting terminals together. PREVENT BURNS — HOT ENGINE ÁAN WARNING: Do not touch hot engine parts or exhaust system components. A running engine gets very hot! E Always check the engine coolant level at the coolant recovery tank ÁN WARNING: Steam can cause injury or death! E In case of an engine overheat, allow the engine to cool before touching the engine or checking the coolant. PREVENT BURNS — FIRE ÁA WARNING: Fire can cause injury or death! M Prevent flash fires. Do not smoke or permit flames or sparks to occur near the carburetor, fuel line, filter, fuel pump, or other potential sources of spilled fuel or fuel vapors. Use a suitable container to catch all fuel when removing the fuel line, carburetor, or fuel filters. Eu Do not operate with the air cleaner/silencer removed. Backfire can cause severe injury or death. B Do not smoke or permit flames or sparks to occur near the fuel system. Keep the compartment and the engine/senerator clean and free of debris to minimize the chances of fire. Wipe up all spilled fuel and engine oil. № Be aware — diesel fuel will bum. ÁN WARNING: Explosions from fuel vapors can cause injury or death! E Al fuel vapors are highly explosive. Use extreme care when handling and storing fuels. Store fuel ina well-ventilated ares away from spark-producing equipment and out of the reach of children. m Do not fill the fuel tank(s) while the engine 15 running. № Shut off the fuel service valve at the engine when servicing the fuel system. Take care in catching any fuel that might spill. DO NOT allow any smoking, open flames, or other sources of fire near the fuel system or engine when the fuel system. ® Do not alter or modify the fuel system. E Be sure all fuel supplies have a positive shutoff valve. © Be certain fuel line fittings are adequately tightened and free of leaks. № Make sure a fire extinguisher is installed pearby and is properly maintained. Be familiar with its proper use. Extinguishers rated ABC by the NFPA are appropriate for all applications encountered in this environment. ACCIDENTAL STARTING dA WARNING: Accidental starting can cause injury or death! № To prevent accidental starting when servicing the generator, remove the 8 amp fuse from the control panel. № Disconnect the battery cables before servicing the engine/ generator. Remove the negative lead first and reconnect it last № Make certain all personnel are clear of the engine before startine. E Make certain all covers, guards, and hatches are re-installed before starting the engine. WESTERBEKE Engines á Generators SAFETY INSTRUCTIONS BATTERY EXPLOSION AA WARNING: Battery explosion can cause injury or death! mu Do not smoke or allow an open flame near the battery being serviced. Lead acid barteries emit hydrogen, à highly explosive gas, which can be ignited by electrical arcing or by lit tobacco products. Shut off all electrical equipment in the vicinity to prevent electrical arcing during servicing. Never connect the negative (—) battery cable to the positive (+) connection terminal of the starter solenoid. Do not test the battery condition by shorting the terminals together. Sparks could ignite battery gases or fuel vapors, Ventilate any compartment containing battenes to prevent accumulation of explosive gases. To avoid sparks, do not disturb the battery charger connections while the battery is being charged. Avoid contacting the terminals with tools, etc., to prevent burns or sparks that could cause an explosion. Remove wristwatch, nings, and any other jewelry before handling the battery. Always tum the battery charger off before disconnecting the battery connections. Remove the negative lead first and reconnect it last when disconnecting the battery. BATTERY ACID A\ WARNING: Sulfuric acid in batteries can cause | severe injury or death! E When servicing the battery or checking the electrolyts level, wear robber gloves, a rubber apron, and eye jon. Batteries contain sulfunc acid which 15 destructive. If it comes in contact with your skin, wash if off at once with water. Acid may splash on the skin or caps. dA WARNING: Carbon monoxide (CO) is 2 deadly gas! mM Ensure that the exhaust system is adequate to expel gases discharged from the engine. Check the exhaust system regularly for leaks and make sure the exhaust manifolds are securely attached and no warpmg exists. Pay close attention to the manifold and exhaust. Be sure the unit and its surroundings are well venblated In addition to routine inspection of the exhausi system, AA WARNING: Carbon monoxide (CO) is an invisible odorless gas. Inhalation produces flu-like symptoms, nausea or death! m Do not use copper tubing in diesel exhaust systems. Diesel fumes can rapidly destroy copper tubing in exhaust systems. Exhaust sulfur causes rapid detenoration of copper twbing resulting in exhaust/water leakage. Do not install exhaust outlet where exhaust can be drawn through vents, or air conditioners. Although diesel engine exhaust gases are not as toxic as exhaust fumes from gasoline engines, carbon monoxide gas is present in diesel exhaust fumes. Some of the symptoms or signs of carbon monoxide inhalation or an Vomiting Muscular twitching Dizziness Intense headache Throbbing in temples Weakness and sleepmess AVOID MOVING PARTS ÁN WARNING: Rotating parts can cause injury or death! E Do not service the engine while it is runming. If a situation arises in which it is absolutely necessary 10 make operating adjustments, use extreme care to avoid touching moving parts and hot exhaust system components. Do not wear loose clothing or jewelry when servicing equipment; tie back long hair and avoid wearing loose jackets, shirts, sleeves, rings, necklaces or bracelets that could be caught in moving parts. Make sure all attaching hardware is properly tightened. Keep protective shields and guards in their respective places at all umes. Do not check fluid levels or the drive belts tension while the engine 15 operating. HAZARDOUS NOISE ÁN WARNING: High noise levels can cause hearing loss! № Never operate an engine without its muffler installed. ® Do nol run an engine with the air intake (silencer) removed. ® Do not run engines for long periods with their enclosures Open. dA WARNING: Do not work on machinery when you are mentally or physically incapacitated by fatigue! | e o TABLE OF CONTENTS Parts Identification... 2 introduction mm... aia nana Warranty Procedures... me. .e....... 3 Serial Number Location ..........e-—. ===. ......s 4 Diesel Fuel, Engine Dil, and Coolant................ Generator Control Panels...................... Description of Switches.............—w=—... Description of Gauges... Remote Panel... Preparations for Initial Start-Up.. Prestart Inspection .... MERE Generator Voltage... EN Starting/Stopping Precodare. STA Safety Shutdown Switches ........————e——.- Generator Break-in Procedure.......................... The Daily Operation... Maintenance Schedule Cooling System... wwe... Changing Coolant ....c.ccccccisiimmisssussssrmsssansios Thermostat:—. a Fuel System .... Fuel Filter/Water Separator Laa Fuel Injection Pump ... Fuel Exft POP. coc siniisiiasisissiiipmisrrei Fuel Lift Pump Filter... ccissrérssssenssiese Fuel File ever es | Engine Fuel PUT ers Engine Lubricating Oil... ВИ Engine Oil 2 EERO Remote Oil Filter... Dil Pressure ... me... Testing a Pressure... Alternator Troubleshooting .... aora se 12 Volt DC Control Circuif ...............ese= .w.—. Slob LYS SAMBA un bi frm er En LA Ja +6 Bd > el Ee fa fi Ch On E AREA ве а | = — Go po, pe Wo ND by | ko ho НН о EEE EA AAA EE EE A A Glow Plugs... es pico Й Generator Wiring Diagram #44735... u 25 Generator Wiring Diagram #044927... E 25A Generator Wiring Schematic $44735............... 26 ho 1-3 Generator Wiring Schematic #044927..........26A Remote Instrument Panel ...............................27 Engine Troubleshooting [Chart] .......................28 Engine Adjustments..................—————————) Valve Clearance Adjustment ...........e——..... 30 Testing Engine Compression ..................w... 31 Fuel Imjectors:.—-=--— 222 as 31 Drive Belt Adjustment... a ve 31 Control Panel Troubleshooting ‘Chart... 29 Electronic Governor Adjustments... 33 Description... NE iat Controller Adi ustment . canssnnacsemenennnenreneneananes 33 Inspect and Adjust... i 33 Linear Actuator Troubleshooting [Chart].. coa 34 GenRemote Calibration ......................———————.) GenRemote Control Station ............................. 36 GenRemote Wiring Diagram ........................37 GenRemote Installation Diagram ....................38 Stop/Start Rocker Switch ...........ww... 20 GenRemote Specifications ...........................29 Generator Information ..................——— 0 Power Take Off Systems..................—.————————..+] BT Generator verser 42 BT Generator Wiring SchematiC......................43 BT Generator Single Phase...............................4 Generator Voltage Adjustment ........................ 45 BT Generator Voltage Regulator.......................47 BT Generator Internal Wiring ... emana 48 Regulator Sensing Wye-Delta Confi igurations. 49 BT Generator Troubleshooting [Chart] ............50 Specifications 10.0KW/8.0KW BTDA................51 Specifications 15KW/12.5KWBTDB ................ 52 Generator Specifications 10.0KW/8.0KW........53 Generator Specifications 15KW BTDC..............54 Generator Specifications 12.5KW BTDB........... 54 Engine Torque O oa О Sealants and Labricants:.. Komo 56 Metric Conversion Data .....................——————-7 Engines E Generators PARTS IDENTIFICATION INTRODUCTION This WESTERBEKE Diesel Generator is a product of WESTERBEKE's long years of experience and advanced technology. We take great pride in the superior durability and dependable performance of our engines and generalors. Thank vou for selecting WESTERBEKE. In order to get the full use and benefit from your generator it manual is designed to help you do this. Please, read this manual carefully and observe all the safety precautions your nearest WESTERBEKE dealer for assistance. This is vour operators manual. À parts catalog is also provided and a technical manual is available from your WESTERBEKE dealer. If you are planning to install this equipment contact your WESTERBEKE dealer for WESTERBEKE'S installation manual WARRANTY PROCEDURES Your WESTERBEKE Warranty is included in a separate folder. If, after 60 days of submitting the Warranty Registry form you have not received a customer identification card registering your warranty, please contact the factory in writing with model information, including the unit's serial Customer Identification Card WESTERBEKE Engines & Generators Customer Identification MR. GENERATOR OWNER MAIN STREET HOMETOWN, USA Model ISBTDAR — Ser 4U0000-E302 Expires 7/20/2004 PRODUCT SOFTWARE Product software, (tech data, parts lists, manuals, brochures and cataloes). provided from sources other than WESTERBEKE are not within WESTERBEKE's control. WESTERBEKE CANNOT BE RESPONSIBLE FOR THE CONTENT OF SUCH SOFTWARE, MAKES NO WARRANTIES OR REPRESENTATIONS WITH RESPECT THERETO. INCLUDING ACCURACY, TIMELINESS OR COMPLETENESS THEREOF AND WILL IN NO EVENT BE LIABLE FOR ANY TYPE OF DAMAGE OR INJURY INCURRED IN CONNECTION WITH OR ARISING OUT OF THE FURNISHING OR USE OF SUCH SOFTWARE. WESTERBEKE customers should also keep in mind the time span between printings of WESTERBEKE product software and the unavoidable existence of earlier WESTERBEKE manuals. In summation, product software provided with WESTERBEKE products, whether from WESTERBEKE or other suppliers. must not and cannot be relied upon exclusively as the defimitive authority on the respective product. It not only makes good sense but is imperative that appropriate representatives of WESTERBEKE or the supplier in question be consulted to determine the accuracy and currentness of the product software being consulted by the customer. NOTES, CAUTIONS AND WARNINGS As this manual takes vou through the operating procedures, maintenance schedules, and troubleshooting of your marine engine, critical information will be highlighted by NOTES, CAUTIONS, and WARNINGS. An explanation follows: NOTE: An operating procedure essential to note. Âà CAUTION: Procedures, which if not strictly observed, can result in the damage or destruction of your engine. A WARNING: Procedures, which if not properly followed, can result in personal injury or loss of life. JWESTERBERS INTRODUCTION SERIAL NUMBER LOCATION The engine and generator serial numbers and model numbers are located on a decal on the generator housing. Take the time to enter this information on the illustration of the name- plate shown below, as this will provide a quick reference when seeking technical information and/or ordering repair parts. SPECIFICATION] 50 HZ. 60 HZ The engine serial number can also be found stamped nto the engine block just above the mjection pump. The generator serial number is stamped into the generator housing on the flat surface on the left side of the generator. WESTERBEKE Нате An identification plate on the engine mamfold also displays the engine model and senal number. NOTE: A carbon monoxide warning decal has been provided by WESTERBEKE. Affix this decal in a visible position in the engine room. UNDERSTANDING THE DIESEL ENGINE The diesel engine closely resembles the gasoline engine, since the mechanism is essentially the same. The cylinders are arranged above a closed crankcase;the crankshaft is of the same general type as that of a gasoline engine, and the diesel engine has the same type of valves, camshaft, pistons, connecting rods and lubricating system. Therefore, to a great extent, a diesel engine requires the same preventive maintenance as a gasoline engine. The most important factors are proper ventilation and proper maintenance of the fuel, lubncating and coohng systems. Replacement of fuel and lubricating filter elements at the time periods specified is a must, and frequent checking for contamination (that is water, sediment, etc.) in the foel sys- tem is also essential. Another important factor is the use of the same brand of ugh detergent diesei lubrication oil designed specifically for diesel engines. The diesel engine does differ from the gasoline engine, however, in its method of handling and firing of fuel. The carburetor and ignition systems are replaced by a single component — the fuel injection pump — which performs the function of both. ORDERING PARTS Whenever replacement parts are needed, always provide the generator model number, engine serial number, and generator serial number as they appear on the silver and black name- plate located on the generator end. You must provide us with this information. so we may properly identify your generator set In addition, include à complete part description and part number for each pant needed (see the separately fumished Parts List). Insist upon WESTERBEKE packaged parts because will fir or generic parts are frequently not made to the same specifications as original equipment. SPARES AND ACCESSORIES Certain spares will be needed to support and maintain your WESTERBEKE engine. Your local WESTERBEKE dealer will assist you in preparing an mventory of spare parts. See the SPARE PARTS page in this manual. For engine accessones, see WESTERBEKE'S ACCESSORIES brochure. INSTALLATION MANUAL Publication #43400 provides detailed information for installing generators and is available at your WESTERBEKE dealer. Engines & Generators DIESEL FUEL, ENGINE OIL AND ENGINE COOLANT DIESEL FUEL Use fuel that meets the requirements or specification of Class 2-D (ASTM), and has a cetane rating of 445 or better Care Of The Fuel Supply Use only clean diesel fuel! The clearance of the components in your fuel injection pump 15 very critical: invisible dirt particles which might pass through the filter can damage these finely finished parts. It is important to buy clean fuel. and keep it clean. The best fuel can be rendered unsatisfactory by careless handling or improper storage facilities. To assure that the fuel going into the tank for your engine's daily use is clean and pure, the following practice is advisable: Purchase a well-known brand of fuel. Use a heavy duty engine oil with an API classification of CF or CG-4 or better. Change the engine oil after an initial 50 hours of break-in operation, and every 100 hours of operation thereafter For recommended oil viscosity, see the following chart: Operating Temperature Dil Viscosity Above 68°F (20°C) SAE 30, 10W-30 or 15W-40 41°-68°F (520°C) SAE 20, 10W-30 or 15W-40 Below 41°F (5°C) SAE 10W-30 or 15W-40 A CAUTION: Do not allow two or more brands of engine oil to mix. Each brand contains its own additives; additives of different brands could react in the mixture fo produce properties harmful to your engine. OIL PRESSURE The engine's oil pressure, during operation, is indicated by the oil pressure gauge on the instrument panel. During normal operation, the oil pressure will range between 35 and T5 psi (241.3 and 517.1 Epa). NOTE: A newly started, cold engine can have an vil pressure reading upwards of 60 psi (4.2 ke/cm”. A warmed engine can have an oil pressure reading as low as 23 psi (1.8 kg/cm”. These readings will vary depending upon the temperature of the engine, the load placed on the engine, and the RPMs. ENGINE COOLANT WESTERBEKE recommends a mixture of 50% antifreeze and 50% distilled water. Distilled water 15 free from the The antifreeze performs double duty. It allows the engine to run at proper temperatures by transferring heat away from the engine to the coolant, and lubricates and protects the cooling circuit from rust and comosion. Look for a good quality antifreeze that contains Supplemental Cooling Additives (SCAs) that keep the antifreeze chemically bal- anced, crucial to long term protection. The distilled water and antifreeze should be premixed before antifreeze that is now available. Antifreeze mixtures will protect against an unexpected freeze and they are beneficial to the engine's cooling system. They retard rust and add to the life of the circulating pump seal. ANTIFREEZE PROTECTION Freezing Temperatur: | 14% | SF | 4F | 40°F (5%) | (13°C) (20°C) | (40°C) COOLANT RECOVERY TANK A coolant recovery tank kit is supplied with each WESTERBEKE diesel engine. The purpose of this recovery tank is to allow for engine coolant expansion and contracton during engine operation, without the loss of coolant and without introducing air into the cooling system. This kat 1s provided and must be installed before operating the engine. NOTE: This tank, with its short run of plastic hose, is best located at or above the level of the engine's manifold, but it can be located below the level of the engine * manifold if the WESTERBEKE Engines & Generators GENERATOR CONTROL PANELS DESCRIPTION OF SWITCHES This manually controlled series of WESTERBEKE manne diesel generators is equipped with toggle switches on the engine control panel and, optionally, at remote panels. All three switches are momentary contact type and serve the following functions: PREHEAT: The PREHEAT toggle serves two purposes: preheating the engine for easy starting and bypassing the engine oil pressure switch. The PREHEAT function closes the K2 relay. as well as supplies current to the fuel solenoid pull coil. When the PREHEAT switch is depressed, the voltmeter, panel lights, gauges and meters and the hold coil of the fuel solenoid. START: The START toggle switch closes the Kl relay that energizes the starter solenoid and activates the starter. While the PREHEAT switch is still depressed, depressing the START switch engages the start solenoid. When the engine begins to fire, the START switch should be released. The PREHEAT switch should not be released until the oil pressure reaches 5 - 10 psi. STOP: The STOP toggle switch is a normally closed switch providing power to the K2 relay. Opening of this switch opens the power circuit to the fuel solenoid, stopping the flow of fuel to the engine and shuts down the engine. To stop the engine, depress the STOP switch. When the STOP switch is depressed, the power feed to the fuel sole- noid is opened, and the fuel flow to the engine is stopped. The STOP switch should be depressed until the generator stops rotating NOTE: When the engine is shut down, the water temperature gauge and the oil pressure gauge will continue to register the last temperature and oil pressure readings displayed. They will return to zero once electrical power is restored EMERGENCY STOP: The EMERGENCY stop switch on the side of the control box is normally closed When depressed, it will open the DC circuit to the control panel and shut the engine down. As the switch 15 not toggled it can be used when performing mamtenance. DESCRIPTION OF GAUGES Coolant Temperature Engine coolant (water) temperature should normally indicate 175° to 195° F (80° 10 90° C). Engine Oil Pressure Oil pressure (psi) may fluctuate depending on the generator load but should range between between 30 to 60 psi. DC Voltmeter Indicates the amount the battery is being charged should show 13V to 14V. Hourmeter Registers elapsed time and is used as a guide for when to perform scheduled maintenance. REMOTE PANEL For remote operation of the generator system, the same three switches are used. The PREHEAT and START switches are connected in parallel with the gauge panel's switches and serve the same functions as in the gauge panel. The STOP switch is in series with the gauge panel's STOP switch and serves the same function. There is a REMOTE START/STOP WIRING DIAGRAM in this manual. GENERATOR WESTERBEKE NOTE: For additional information on Control Panels. Refer io: STARTING/STOPPING PROCEDURE, DC WIRING DIAGRAMS and TROUBLESHOOTING GAUGES. WESTERBEKE Engines E Generators PREPARATIONS FOR INITIAL START-UP PRESTART INSPECTION This section of the manual provides the operator with prepa- ration, initial starting, break-in, starting (warm or cold) and stopping procedures. Follow the procedures as presented for the conditions indicated and your WESTERBEKE generator set will give reliable performance and long service life. Before starting your generator set for the first time or after à prolonged layoff, check the following items: LJ] Check the engine oil level. Add oil to maintain the level at the high mark on the dipsack. [] Check the fuel supply and examine the fuel filten'separa- tor bowis for contaminants. [J Check the DC electrical system. Inspect wire connections and battery cable connections. Make certain the (+) bat- tery cable is connected to the starter solenoid and the negative (=) cable is connected to the engine ground stud (this location is tagged), [J Check the coolant level in both the plastic recovery tank and at the manifold. Visually examine the unit. Look for loose or missing parts, disconnected wires, unattached hoses, and check threaded connections. Check load leads for correct connection as specified in the winng diagrams. Examine air inlet and outlet for air flow obstructions. Be sure no other generator or utility power is connected to load lines. Be sure that in power systems with a neutral line that the neutral is properly grounded (or ungrounded) as the system requires, and that the generator neutral is properly connected to the load neutral. In single phase and some 3-phase systems an incomplete or open neutral can sup- ply the wrong line-to-neutral voltage on unbalanced loads. [1 Make sure the mounting installation is secure. [1 Make sure that the generator is properly grounded. Li [ОВ Ed ÁA CAUTION: wher starting the generator, it is | recommended that all AC loads, especially large motors, | be swilched DFF until the engine has come up fo speed and, in cold climates, staris to warm up. This precaufion will prevent damage caused by unanticipated operation of the AC machinery and will prevent a cold engine from | stalling. | The speed of the generator engine 1s adjusted at the factory, however, 1t is advisable to verify. 60 Hz The engine no-load speed is set a1 61.5 - 62 Hz Al rated amperage hertz output may decrease to 48.6 - 59.0 Hz. 50 Hz The engine no-load speed 15 set at 61.5 Hz. At rated amperage hertz output may decrease to 48.5 - 49.0 Hz The speed of the generator engine 15 adjusted at the factory, however it is advisable to verify. The voltages are easily adjusted to optimum values no-load and full load (refer to VOLTAGE ADJUSTMENT in thus manual). If possible, apply actual service or test load of the same power factor as the load to be used in service. If the voltage cannot be adjusted to suitable values and fault seems evident, contact vour authorized WESTERBEKE service dealer. STARTING/STOPPING PROCEDURE THE STARTING SYSTEM Westerbeke diesel generators use electric starters assisted by glow plugs for both normal and cold weather starting. The illustration below shows a cross-sectional view of one cylinder. The glow plug is located in the combustion cham- ber so that its tip is in the injector nozzie's spray path. When the glow plug is energized by the PREHEAT burton, the plug glows red at the tip and assists in igniting the fuel. The result is a rapid start with less wear on the starter. This system is common to WESTERBEKE diesels. The start circuitry is designed so that the PREHEAT button must be depressed for the time specified in the preheat chart. Then, while keeping the PREHEAT button engaged, the START button is depressed to crank the engine. PREHEAT switch is depressed. Depressing the PREHEAT switch activates the glow plugs in the cylinder head so use the PREHEAT intermittenily to avoid overheating the glow plugs. PREHEAT: Depress the PREHEAT switch. The voltmeter and panel lights, gauges and meters will be activated. The PREHEAT switch should be depressed in accordance with the following chart: Temperature/Preheat Atmospheric Temperature Preheating Time +41°F{+5°C) or higher Approx. 10 seconds +41 F(+5"C) to 23°F (-5°C) Approx. 15 seconds +23"F{-5"C) or lower Approx. 20 seconds Limit of contiduoes use 30 saconds before cranking Upon engine starting, release the START switch. Do not release the PREHEAT switch until the oil pressure reaches 15 psi. Then as long as the high water temperature and low oil pressure protective circuits do not activate, the engine will remain energized and continue to run. Should the engine not start when the START switch is depressed for 10 to 20 seconds, release both switches and wait 30 seconds; repeat the procedure above and preheat longer. Never run the starter for more than 30 seconds. Remote Starting Procedure The remote start panel is the same as the engine-mounted start panel except that it has a green LED hight and no guages. When starting at a remote location, the green LED lights when the generator is running at approximately 600 rpm. This indicates when the START switch can be released since the starting of the generator may not be audible. A. When the PREHEAT switch is depressed at the remote start/stop panel the LED hight will illuminate. When the START switch is depressed and the starter cranks the engine this LED light will dim. When the engme starts the LED light will brighten signaling to release the START switch. Continue to hold the PREHEAT depressed for a few seconds to allow oil pressure to build up which closes the oil pressure safety switch that is in the series path for 12V B+ to the fuel run solenoid. The de B. After the generator is started and the START switch is released, the generator’s starter will not crank unless the PREHEAT switch 15 operated first because this switch supplies voltage to the START switch. Once the engine starts, check the engine's instruments for proper oil pressure and battery charging voltage. Apply a light load to the generator and allow the engine's eperating temperature to come up to 140-150"F (60-66*C) before applying heavy loads. NOTE: Some unstable running may occur in a cold engine. Depressing the PREHEAT switch for 10-15 second intervals will help stabilize the engine RPM until the operating temperature reaches the 140-150°F and a load is applied to the engine. STARTING/STOPPING PROCEDURE STARTING UNDER COLD CONDITIONS Make sure the lubricating oil conforms with the ratings for the prevailing temperature. Check the table in the ENGINE OIL section in this manual. The battery should be fully charged to minimize voltage STOPPING PROCEDURE 1. Remove the AC electrical load from the generator and allow the generator to run for three to five minutes to stabilize its operating temperatures. 2. Depress the STOP switch and hold it until the generator is completely stopped. 3. Now release the STOP switch. SAFETY SHUTDOWN SWITCHES The engine is protected by three automatic shutdown switches. Should shutdown occur, do not attempt to restart without finding and correcting the cause. Refer to the heading “Engine Stops” in the TROUBLESHOOTING section of this manual. The following is a description of these automatic shutdown switches: Coolant Temperature Switch A high water temperature switch is located on the thermostat housing. Normally closed, this switch, should the fresh water coolant's operating temperature reach approximately 210°F (99°C), will open and interrupt the DC voltage to the K2 relay, thereby shutting off the engine. This switch resets at 195°F (107°C). e. COOLANT COOLANT SENSOR TEMPERATURE SWITCH Remote Stopping Procedure To stop the generator, depress the STOP switch which opens the normally closed B+ path for voltage to the engine's run circuit. The STOP switch must be held open until the generator comes to a complete stop and the green LED light goes out. Low Oil Pressure Switch A low oil pressure shutdown switch is located off the engine's oil gallery. Normally open in a static state, thus switch's sensor monitors the engine's oil pressure. Should the engine's oil pressure fall to 5-10 psi, this switch will open, interrupting the DC voltage to the K2 relay, thereby shutting off the engine. == The generator's engine is protected by an engine mounted draw or electrical overload anywhere in the instrument panel wiring or engine wiring will cause the breaker to trip. In this event the generator will shut down and the voltage to the K2 relay is terminated. If this should occur, check and repair the source of the problem. After repairing the fault, reset the breaker and restart the generator Engines á Generators GENERATOR BREAK-IN PROCEDURE Although your engine has experienced a minimum of one hour of test operations af the factory to make sure accurate assembly procedures were followed and that the engine operated properly, a break-in time is required. The service life of your engine is dependent upon how the engine 15 operated and serviced during its mitial hours of use. Breaking-in a new engine basically involves seating the piston rings to the cylinder walls. Excessive oil consumption and smoky operation indicate that the cylinder walls are Erd vr à canso be: ovedosdiug te anni des the break-in period. Your new engine requires approximately 50 hours of initial conditioning operation to break in each moving part in order to maximize the performance and service life of the engme. Perform this conditioning carefully, keeping in mind the following: Start the engine according to the STARTING PROCEDURE (water pump, oil pressure, battery charging) are functioning. AFTER START-UP Once the generator has been started, check for proper operation and then encourage a fast warm-up. Run the generator between 20% and 60% of full load for the first 10 hours. A CAUTION: Do not attempt to break-in your generator by running without a load. After the first 10 hours of the generator's operation, the load can be increased to the full-load rated output, then periodically vary the load [I Monitor the control panel gauges. [) Check for leaks of fuel and engine oil. [3 Check for abnormal noise such as knocking, fnction, vibration and blow-back sounds. [J Confirm exhaust smoke: When the engine is cold — White Smoke. When the engine is warm — almost Smokeless, When the engine is overloaded — some Black Smoke. To protect against unintentional overloading of the generator, the generators output leads should be routed through a circuit breaker that is rated at the rated output of the generator. NOTE: Be aware of motor starting loads and the high current draw can be 3 to 5 times normal running amperage. See GENERATOR INFORMATION in this manual. Once the generator has been placed in operation, there may be adjustments required for engine speed (henz) during the engine's break-in period (first 50 hours) or after this period. A no-load voltage adjustment may also be required in conjunction with the engine's speed adjustment. See GENERATOR INFORMATION in this manual. Ces] WESTERBEKE. Engines 4 Generators 10 THE DAILY OPERATION CHECK LIST C] Record the hourmeter reading in your log (engine hours relate to the maintenance schedule.) [J Visually inspect the generator for fuel, oil, or water leaks. (O Check the oil level (dipstick). I] Check the coolant level in the coolant recovery tankradiator. [I Check your diesel fuel supply. [] Look for clean fuel in the fuel/separator transparent bowl. [I Check for loose wires at the altemator. DO] Check the startine batteries (weekly). [J Check drive belts for wear and proper tension (weekly). START THE GENERATOR (See STARTING PROCEDURES on previous pages). Allow the engine to warm up for 5 to 10 minutes to reach an operating temperaturesof 140° to 150°F (60°-66°C) before bie AC lool Apply loads systematically allowing the generator to adjust to each load before applying the next Check the gauges for proper oil pressure, operating temperature, and DC voltage. NOTE: Some unstable running may occur in a cold engine. This condition should lessen as normal operating temperature is reached and loads are applied dA CAUTION: Do not operate the generator for long periods of time without a load being placed on the generator. STOPPING THE GENERATOR Remove the major AC loads from the generator one at a time. Allow the generator to run for a few minutes to stabilize the operating temperature and depress the stop switch. (See STOPPING PROCEDURES on previous manu- als). JWESTERBEKE 11 MAINTENANCE SCHEDULE ÁA WARNING: Never attempt to perform any service while the engine is running. Wear the proper safety equipment such as goggles and gloves, and use the correct tools for each job. Disconnect the battery terminals when servicing any of the enging’s DC electrical equipment. NOTE: Many of the following maintenance jobs are simple but others are more difficult and may require the expert knowledge of a service mechanic. CHECK HOURS OF OPERATION SCHEDULED EACH a : EXPLANATION OF SCHEDULED MAINTENANCE DAY | 50 100 250 500 750 1000 1250 MAINTENANCE | Fuel Supply U Diesel No. 2 rating of 45 cetane or higher. Fuel/Water Separator E Check for water and dirt in fuel (drain/replace fifter : Te = Engine Oil Level Li Oil level should indicate between MAX. and LOW on — = dipstick = Coolant Level Г | Check at recovery tank; if empty, check at manifold | and radiator. Add coolant if needed. Drive Belts 0 | Inspect for proper tension (3/8 to 1/7” defiection) _ = Weekly | | | and adjust if needed. Check belt edges for wear. Visual Inspection of Engine DO] | NOTE: Please keep engine surface clean. Dirt | Check for fuel, oil and water leaks. Inspect wiring and oil will inhibit the engines ability fo and electrical connections. Keep bolis 4 nuts tight. remain cool. Check for loose belt tension. Fuel Filter o | ОТО ГО | О | O | initial change at 50 hrs, then change every 250 hrs. Starting Batteries Ll] Every 50 operating hours check electrolyte levels weekly and make sure connections are very fight Clean off | Engine Oil (and filter) gra DO | OO | Initial engine oil & filter change at 50 hrs., then _ | change both every 100 hours. Generator Ojo) 8 0 Check that AC connections are clean and secure with no chafing. See GENERATOR SECTION | for additional information. Fuel/Water Separator О |2 |0 | 0 | 0 |0 | Change every 200 hours. — Electronic Governor Control [] Г] | Check and or adjust the no-load speed in the panel, (if applicable) | required (hertz) and the regulator board adjustment as needed. NOTE: These adjustment are not a warrantable adjustment during or after the unit's break-in. Exhaust System С О | O CJ] | Initial check at 50 hrs., then every 250 hrs. inspect for leaks. Check the exhaust elbow for carbon and/or corrosion buildup on inside passages; clean and replace as necessary. Check that all connections are fight | Engine Hoses Ol Ol O| Ol O| O | Hoseshould be hard & tight Replace if soft or | | sponoy. Check and fighten all hosé camps. (IN ]WESTERBEKE Engines & Generators 12 MAINTENANCE SCHEDULE NOTE: Use the engine hour meter gauge to log your engine hours or record your engine hours by running rime. CHECK SCHEDULED | EACH HOURS OF OPERATION EXPLANATION OF SCHEDULED MAINTENANCE DAY 50 100 250 500 750 1000 1250 MAINTENANCE Coolant System O Г] | Drain, flush, and refill cooling system with Air intake Filter alar a|O|o| O | Cieaneveny 100 hours. Replace as needed Electric Fuel Lift O Ol Ol OO] O | Penodcally check the wiring connections. Pump DC Alternator О] L] [] | Check DC charge from alternator, Check mounting bracket; Tighten electrical connections. “Fuel Injectors 0 Check and adjust injection opening pressure and "Starter Motor = CO | Check solenoid and motor for corrosion. Remove | and lubricate. Clean and lubricate the starter motor *Preheat Circuit = J | Check operation of preheat solenoid. Remove and clean glow plugs; check resistance (4-6 ohms). Reinstall with anti-seize compound on threads. "Engine Cylinder [1 | Check compression pressure and timing (see Compression | ENGINE ADJUSTMENTS). *Torque Cylinder Head O | 0 | At first 50 hours, then every 500 hours (see Hold-down bolts = — ENGINE ADJUSTMENTS). _ *Adjust the Vaive Clesrances Cl LJ Adjust Valve Clearances (see ENGINE *Radiator Г) | Remove, have professionally cleaned and pressure tested. *WESTERBEKE recommends this service be performed by an authonzed mechanic. WESTERBEKE Engines & Generalors 13 COOLING SYSTEM DESCRIPTION Westerbeke diesel engines are designed and equipped for fresh water cooling. Heat produced in the engine by combustion and friction is transferred to fresh water coolant which circulates throughout the engine. This circulating fresh water coolant cools the engine block and its internal moving parts and the engine oil. Fresh water coolant is pumped through the engine by a circulating pump, absorbing heat from the engine. The coolant then passes through the thermostat into the manifold, to the radiator where it is cooled, and returned to the engine block via the suction side of the circulating pump. FRESH WATER COOLING CIRCUIT NOTE: Refer ro ENGINE COOLANT section for the recommended antifreeze and water mixture to be used as the fresh water coolant. When the engine is started cold, external coolant fiow 15 prevented by the closed thermostat (although some coolant flow is bypassed sround the thermostat to prevent the engine manifold from overheating). As the engine warms up, the thermostat gradually opens, allowing full flow of the engine's coolant to flow unrestricted to the external portion of the cooling system. Coolant Recovery Tank A coolant recovery tank allows for engine coolant expansion and contraction during engine operation, without any significant loss of coolant and without introducing air mto the cooling system. This tank should be located at or above the engine mamfold level and should be easily accessible. CHANGING COOLANT The engine's coolant must be changed according to thé MAINTENANCE SCHEDULE. If the coolant 15 allowed to become contaminated, it can lead to overheating problems. AA CAUTION: Proper cooling system maintenance is critical; a substantial number of engine failures can be traced back to cooling system corrosion. Drain the engine coolant by loosening the drain plug on the engine block and opening the radiator pressure cap. Flush the system with fresh water, then start the refill process. NOTE: The percock on the radiator can also be used to drain engine coolant. AA WARNING: Beware of the hot engine coolant. COOLING SYSTEM Refilling the Coolant Afier replacing the engine block drain plug. close the radiator coolant petcock. then pour clean, premixed coolant into the radiator and when the coolant is visible, start the engine. Monitor the coolant in the radiator and add as needed. Fill the radiator to the filler neck and install the pressure cap. Remove the cap on the coolant recovery tank and fill with coolant mix to halfway between LOW and MAX and replace the cap. Run the engine, observe the coolant expansion flow into the recovery tank. After checking for leaks, stop the engine and allow it to cool. Coolant should draw back into the cooling system as the engine cools down. Add coolant to the recovery tank if needed. Clean up any spilled coolant. NOTE: Periodically check the condition of the radiator pressure cap. Ensure that the upper and lower rubber seals are in good condition and check that the vacuum valve opens and closes tightly. Carry a spare cap. THERMOSTAT A thermostat, located near the manifold at the front of the engine, controls the coolant temperature as the coolant continuously flows through the closed cooling circuit. When the engine is first started, the closed thermostat prevents coolant from flowing (some coolant is by-passed through a hole in the thermostat to prevent overheating). As the engine warms up, the thermostat gradually opens. The thermostat is accessible and can be checked, cleaned, or replaced easily. Carry a spare thermostat and gasket Replacing the Thermostat Remove the cap screws and disassemble the thermostat housing as shown. When installing the new thermostat and gasket, apply a thin coat of sealant on both sides of the gasket before pressing it into place. Do nor over-tighten the Cap SCIEWS, Run the engine and check for normal temperatures and that there are no leaks at the thermostat housing. The air filter cartridee prevents engine room dust and dut from entering the engine, it also extends engine life, and quiets the engine. MAINTENANCE The filter should be cleaned every 100 operating hours. Tap the cartridge on a flat surface to dislodge loose dirt or clean off with compressed air. If the cartridge is badly contaminated FUEL SYSTEM DIESEL FUEL Use No. 2 diesel fuel with a cetane rating of 45 or higher. Do not use kerosene or home heating fuel. FUEL FILTER/WATER SEPARATOR A primary fuel filter of the water separating type must be installed between the fuel tank and the engine to remove water and other contaminants from the fuel before they can be carried to the fuel system on the engine. The ownerfoperator is responsible for making certain the fuel reaching the engine's injection equipment is free of impurities. This process is accomplished by installing and maintaining a proper fuel filter/water separator betwen the fuel tank and the generator‘engine, Westerbeke recommends а 10 micron filter be used. The fuel injection pump is a very importan! component of the diesel engine, requiring the utmost care in handling. The fuel injection pump has been thoroughly bench-tested and the owner-operator is cautioned not to attempt to service it. If it requires servicing, remove it and take it to an authorized fuel injection pump service facility. Do not attempt to disassem- ble and repair it The only adjustment the servicing mechanic should make to the fuel injection pump is the adjustment for engine idle speed (see IDLE SPEED ADJUSTMENT under ENGINE ADJUSTMENTS). FUEL LIFT PUMP Periodically check the fuel connections to and out of the pump and make sure that no leakage is present and that the fittings are tight and secure. The DC ground connection at one of the pumps mounting bolts should be clean and well secured by the mounting bolt to ensure proper pump opera- tions. will purge air from the fuel system and provide a continuous flow of fuel as the engine is running. FUEL LIFT PUMP FILTER To ensure clean fuel into the fuel tft pump, there 15 a small inline fuel filter connected to the fuel lift pump elbow. This filter should be replaced every 200 hours of operation. FUEL FILTERS The fuel injection pump and the fuel injectors are precisely manufactured and they must receive clean diesel fuel, free from water and dirt. To ensure this flow of clean fuel, the fuel must pass through at least two fuel filters, à fuel filter/water separator and the engine’s spin-on fuel filter. Visually inspect, clean, and change these filters according to the mamienance schedule in this manual ÁA WARNING: Shut off the fuel valve at the tank when servicing the fuel system. Take care in caching any fuel that may spill. DO NOT allow any smoking, open flames or other sources of fire near the fuel ENGINE FUEL FILTER ' | Periodically check the fuel connections and the bowl for leakage. Replace the filter clement after the first 50 hours then follow the MAINTENANCE SCHEDULE. Changing/cleaning the filter element 1. Shut off the fuel supply. 2. Unscrew the retainer ring that holds the filter bowl to the housing and allow the bowl to come away from the housing, 3. Remove and replace the filter element and clean the bowl. 4. Replace the sealing “O0” ring and reassemble the bowl to the housing. Thread the retainer ring on carefully so as not to cross thread. When retainer contacts the “07 ring, tighten 1/4 - 1/2 tums by hand. Open the fuel supply and run the engine to inspect for leaks. ENGINE LUBRICATING OIL D | Г. | 2. Replacing the Oil Filter. When removing the used oil | filter, you may find it helpful and cleaner to punch à hole Oil PRESSURE — : in the upper and lower portion of the old filter to drain the SENDOR | | oil from it into 2 container before removing it. This helps 10 lessen spillage. A small style automotive filter wrench should be helpful in removing the old ail filter. O 7 . PRESSURE NOTE: Do not punch this hole without first loosening the Sw filter to make certain it can be removed! = Place some paper towels and a plastic bag around the OIL filter when unscrewing it to catch amy oil left in the filter. (Oil or any other fluid on the engine reduces the engine's OIL PRESSURE cooling ability. Please keep your engine clean.) Inspect the old oil filter as it is removed to make sure that the rubber sealing gasket came off with the old oil filter. If thus block, gently remove it. on OIL SUMP OIL SCREEN 1. Draining the Oil Sump. Discharge the used oil through the sump drain hose (attached to the front of the engine) while the engine is still warm. Drain the used oil completely, replace the hose in its bracket, and replace the end cap securely. gasker's sealing surface on the engine block free of oil and apply a thin coat of clean engine oil to the rubber gasket on the new oil filter. Screw the filter onto the threaded oil о filter nipple, and then tighten the filter firmly by hand. yellow/gray emulsion indicates the presence of water in NOTE: Generic filters are not recommended. as the do e e E ir Sl kines of po Baws on o TE generic parts mi entirely different genuine qualified mechanic should water be present in the oil. parts. Immediately after an oil filter change and oil fill exhaust, filling the engine. run the engine io make sure the cil pressure is normal and that there are no oil leaks around the new oil filter: 3. Filling the Oil Sump. Add new oil through the oil filler cap on the top of the engine or through the side oil fill. After refilling, run the engine for a few moments while checking the 1 nressure. Make sure there is no leakage around the new oil filter or from the oil drain system, and stop the engine. Then check the quantity of val with the lube oil dipstick. Fill to, but not over the high mark on the dipstick, should the engine require additional oil. ps dt 17 REMOTE OIL FILTER (OPTIONAL) INSTALLATION This popular accessory is used to relocate the engine's oil fil- ter from the engine to a mor convenient location such as an engine room bulkhead. NOTE: Refer to ENGINE OIL CHANGE in this manual for instructions on removing the oil filter APPLY A THIN COAT OF CLEAN OIL TO THE O-RING WHEN INSTALLING THIS KIT. THREAD THE KIT ON, THEN HAND TIGHTEN AN ADDITIONAL 3/4 TURN AFTER THE O-RING CONTACTS THE BASE. To install, simply remove the engine où filter and thread on WESTERBEKF'S remote oil filter kit as shown. Always install this kit with the oil filter facing down as illustrated. Contact your WESTERBERE dealer for more information. NOTE: Westerbeke is not responsible for engine failure due 10 incorrect installation of the Remote Oil Filter. ÁA CAUTION: mis vital to install the oil lines correctly. If the oil flows in the reverse direction, the by-pass valve in the fitter assembly will prevent the oil from reaching the engine causing an internal engine [WESTERBERS 18 OIL PRESSURE DESCRIPTION TESTING OIL PRESSURE The lubricating system is a pressure feeding system using To test the oil pressure, remove the oil pressure sender, then an oil pump. The engine oil is drawn from the oil sump by install a mechanical oil pressure gauge in it's place. After the oil pump, which drives the oil, under pressure, trough warmine up the engine, set the engine speed at 1800 rpm the oil filter, oil cooler and various lubricating points in the and read the oil pressure gauge. engine. The oil then returns to the oil sump to repeat the continuous cycle. When the oil pressure exceeds the speci- Dil Pressure — 35.0 Iv (3.8 kpca”) or more al 1800 mm. fied pressure, the oil pushes open the relief valve in the oil Sender and Switch Toque — 9-13M40(17-1.8m-ikg) pump and returns to the oil sump, keeping the oil pressure within its specified range. OIL PRESSURE The engine's oil pressure, during operation, 15 indicated by the oil pressure gauge on the instrument panel. During normal operation, thé oil pressure will range between 40 and 60 psi (2.8 and 4.2 kg/cm). NOTE: À newly started, cold engine can have an oil pressure reading up to 60 psi (4.2 kg/cm). A warmed engine can have an oil pressure reading as low as 35 psi (2.5 kg/cm). These LOW OIL PRESSURE The specified safe minimum oil pressure is 4.3 + 14 psi (03 + 0.1 kg/cm”). A gradual loss of oil pressure usually indicates a wom bearings. For additional information on low oil pres- sure readines, ses the ENGINE TROUBLESHOOTING chart OIL PRESSURE RELIEF VALVE An oil pressure relief valve is located on the engine block just below the injection pump. This valve opens at appoximately 50 psi [343 kpa] and maintains that pressure. DC ELECTRICAL SYSTEM ALTERNATOR The charging system consists of 2 DC belt dnven alternator with a voltage regulator, an engine DC winng hamess, a mounted DC circuit breaker and a battery with connecting cables. Because of the use of integrated circuits (IC's), the electronic voltage regulator is very compact and 15 mounted internally or on the back of the alternator. ÁN WARNING: A failed altemator can become very hot. Do not touch until the alternator has cooled down. Use this troubleshooting section to determine if a problem exists with the charging circuit or with the alternator. If it 1s determined that the alternator or voltage regulator 1s faulty, have a qualified technician check it The alternator charging circuit charges the starting battery and any accessory battery. An isolator with a diode, a solenoid or a battery selector switch is usually mounted m the circuit io isolate the batteries so the starting battery 15 not discharged along with the accessory battery. If the alternator is charging the starting battery but not the accessory battery, the problem is in the service battery's charging circuit and not with the alternator. Testing the Alternator AA CAUTION: Before starting the engine make certain that everyone is clear of moving parts! Keep away from sheaves and belts during test procedures. Â\ WARNING: When testing with a multimeter: DC and AC circuits are often mixed together. Always isolate DC and AC converters, and shut down the engine before performing DC testing. No AC tests should be made without a proper knowledge of AC circuits. 1. Start the engine. 2. After the engine has run for a few minutes, measure the starting battery voltage at the battery terminals using a multimeter set on DC volts. a. If the voltage is increasing toward 14 volts, the alternator 1s working. b.If the voltage remains around 12 volts, a problem exists with either the altemator or the charging circuit; continue with Steps 3 through 8. MULTIMETER Cou © $ | Tum off the engine. Inspect all wiring and connections. Ensure that the battery terminals and the engine ground connections are tight and clean. A CAUTION: 70 avoid damage to the BC charging alternator, never shut off the engine battery switch when the engine is running! Tum on the ignition switch, but do not start the engine. Check the battery voltage. If the bamery is in good condition, the reading should be 12 to 13 volts. TIMETER &+ TESTING THE ALTERNATOR VOLTAGE (IGNITION ON - ENGINE OFF) (IN ]WESTERBEKE Engines & Generators 20 DC ELECTRICAL SYSTEM 6. Now check the voltage between the alternator output terminal {B+} and ground. If the circuit 15 good, the volt- age at the alternator will be the same as the battery, or if an isolator is in the circuit the alternator voltage will be zero. If neither of the above is true, a problem exists in the cir- cuit between the alternator and the battery. Check all the connections — look for an opening in the charging circuit GROUND 7. Start the engine again. Check the voltage between the altemator output and ground. The voltage reading for a properly operating alternator should be between 13.5 and 14.5 volts. If your alternator is over- or under-chargine, have it repaired at a reliable service facility. NOTE: Before removing the alternator for repair, use a voltmeter to ensure that 12 volts DC excitation is present ar the EXC terminal if the previous test showed only bat- tery voltage at the B output terminal. If 12 vols is not present at the EXC terminal, trace the wiring and look for breaks and poor connections. do not use a high voltage tester (i.e. 2 megger) when performing tests on the alternator charging circuit. AA CAUTION: To avoid damaging the alternator diodes, 12 VOLT DC CONTROL CIRCUIT The engine has a 12 volt DC electrical control circuit that 1s shown on the wining diagrams that follow. Refer to these diagrams when troubleshooting or when servicing the DC electrical system. ÁA CAUTION: 70 avoid damage to the battery charging circuit, never shut off the engine battery switch while the engine is renning. Shut off the engine battery switch, however, to avoid electrical shorts when working on the engine's electrical Circuit. BATTERY The minimum recommended capacity of the battery used in the engine's 12 volt DC control circuit is 600 — 500 Cold Cranking Amps (CCA). Battery Care Review the manufacturer's recommendations and then establish a systematic maintenance schedule for your engine's starting battenes. [1 Monitor your voltmeter for proper charging during engine operation. [] Check the electrolyte level and specific gravity with a hydrometer. Use only distilled water to bring electrolytes to a proper level. Г] Маке certain that battery cable connections are clean and tight to the battery posts (and to your engine). [1] Keep vour batteries clean and free of corrosion. | À WARNING: Sulfuric acid in lead batteries can — cause severe burns on skin and damage clothing. Wear protective gear. [ex ]WESTERBEKE Engines 4 Generators 21 DESCRIPTION and starter button When the starter button on the mstrument panel 15 depressad, current flows and energizes the starters solenoid coil. The energized coil becomes an electromagnet, which pulls the plunger into the coil, and closes a set of contacts which allow high current to reach the starter motor. At the same time, the plunger also serves to push that starter pinion to mesh with the teeth on the fiywheel To prevent damage to the starter motor when the engine starts, the pinion gear incorporates an over-running (one-way) clutch which is splined to the starter armature shaft The rotation of the running engine may speed the rotation of the pinion but not the starter motor itself. Once the started button 15 released, the current fiow cesses, stop- ping the activation of the solenoid The plunger is pulled out of contact with the battery-to-start cables by = coil spring, and the flow of electricity is interrupted to the starter. This weakens the magnetic fields and the starter ceases iis rotation. As the solenoid plunger is relezsed, its movement also pulls the starter drive gear from its engagement with the engine fiywheel TROUBLESHOOTING Prior to testing, male certain the ships battenes are aí full charge and that the Starting system wiring connections (terminals) are clean and tight Pay particular attention to the ground wire connections on the engine block To check the wiring, trv cranking the starter for a few seconds, never mare than 10 seconds at a time, then run your hand along resistance. Repair or replace any trouble spots. Using a multimetes, test the voltage between the positive terminal stud on the start solenoid and the engine block (ground). If you read 12 volts, the starter is faulty. ( | () To test the ignition circuit, locate the ignition(s) terminal (it 15 one of the small terminal studs and is wired to the ignition circuit). Use a screwdriver, don't touch the blade, to jump from that ignition terminal to the positive battery connection terminal on the solenmd. If the starter cranks, the fault lies with the ignition circuit If the solenoid clicks but nothing else happens, the starter и If nothing at all happens the solenoid isn’t getting current. connections. It is also possible that the solenoid is defective. ÂÀ WARNING: There will be arching and sparks will fiy when jumping terminals. Be certain-the engine space is free of potentially explosive fumes, especially | gasoline. Engines & Generators 22 Test again by jumping the two large terminal studs. Hold the screwdriver blade famiv berween the studs. Do not allow the screwdriver blade to touch the solencid or starter casing, this would cause a short dA WARNING: There will be arching as the full | starting current should be flowing thru the blade of the screwdriver. If the starter spins, the solenoid is faulty. If the starter fails to spin, the motor is probably faulty. If no arching occurred. There is no juice reaching the solenoid. NOTE: Starter motors are either inertia type or pre-engaged. In the pre-engaged model, the solenoid also moves an arm that engages the starter motor io the flywheel of the engine. Using a screwdriver to bypass the solenoid on such a starter will run the motor without engaging the flywheel. Turn the starter switch on to provide the power to the solenoid. Hopefully it will create enough magnetic field for the arm to move even though the contacts inside the solenoid are bad 23 STARTER MOTOR SERVICE Westerbele uses 2 standsrd marine starter motor wisch can be serviced or rebuilt at any starter motor automotive service center. If replacing the starter motor, make certam the new motor is certified for marine use. Automotive starters do not meet USCG standards. If in doubt, contact your WESTERBEKE dealer TO REMOVE FOR SERVICE 1. Disconnect the negative battery cable. 2. If necessary, remove any components to gain full access to the starter motor 3. Label and disconnect the wimg from the starter. (Do not allow wires to touch, tape over the termomals ). 4. Remove the starter mounting bolts. 5. Remove the starter from the engine. In some cases the starter will have to be turned to a different angle to clear obstructions. Engines £ Generators GLOW PLUGS DESCRIPTION The glow plugs are wired through the preheat solenoid. When PREHEAT is pressed at the control panel this solenoid should “click” on and the glow plug should begin to get hot. To inspect the plug, remove the electrical terminal connec- tions, then unscrew or unclamp each plug from the cylinder head. Thoroughly clean each plug’s tip and threads with a soft brush and cleaning solution to remove all the carbon and oil deposits. While cleaning, examine the tip for wear and burn erosion; if it has eroded too much, replace the plug. TESTING An accurate way to test glow plugs is with an chmmeter. Touch one prod to the glow plug's wire connection, and the other to the body of the glow plug, as shown. A good glow plug will have a 0.4 - 0.6 ohm resistance. This method can be used with the plug in or out of the engine. You can also use an ammeter to test the power drain (5 - 6 amps per plug). ÁN WARNING: These glow plugs will become very hot to the touch. Be careful not to burn your fingers when testing the plugs. Re-install the plugs in the engine and test them agam. The plugs should get very hot (at the terminal end) within 7 to 15 seconds. If the plugs don't heat up quickly, check for a short circuit. When reinstalling the glow plugs, use anii-seize com- pound on the threads. ÁA WARNING: Do not keep a glow plug on for more than 30 seconds. Glow Plug Tightening Tome ~~ 7-11 Ab (1.89-1.5 mig) ce CTS Cpr GENERATOR WIRING DIAGRAM Tl Ll ENEE 1 BATE ELE | = === RETA. Da WE E Fa E Pc PR > AECA BATTERY SWITCH [ee EE | 17-28 TEC e + EE |. KIN Seri Ma COTA A CRE TE Filed] 2 Cae 7 Ts OF Pete” SSL DACIÓ 2 Few SITE Jeet 1 3 | L LE T | : e mue | ma $ Mae = : | f : E 3 |0 = . |. ay mes = | GENERATOR WIRING DIAGRAM #044927 (OPTIONAL ELECTRONIC GOVERNING) Te EP m > # —— "и == —— uTif ga E - 1. Upa weil da COCTELES E EC. TE PE. 1 E 1 TE OF PEDIDA vs pesré de Je TE GRY. GENERATOR WIRING SCHEMATIC TY E, ICE 11: MAD — a EaTToE* A I swites | ETARTIE | EFT EFF AT Pr == ( 3 рн Я | О Ц | Е т | O | —— SL Cri AT Ep JU 4 Y | seg asin ela | РТ. Че | | Lat] iL Tana TOR y TEE 1 2-9 Ca 1 — — Ста, TIE. aR Gil PRESS — TE = Cu SHITE dei TO a ao = 68 Le it FUEL ды’ | - | - | ré | a... tE LEJ La | jm zn 1 Ce {te LU mi ms: M wr тн mei] mE © T © ra ri 1.3. | are Twi TEE Wires | систе» mg бя | | a+ Led ry — = i * ; - Teta REET Cia TO Pai CONÉCTICES- и vou TRE TLE С) нот! Состоя гов | | | | носаветов | PRESTESERNS 26 GENERATOR WIRING SCHEMATIC #044927 (OPTIONAL ELECTRONIC GOVERNING) ©- RATTINT 11.200 + re rr cm AE au 1 ; a TE a —( — ! EE | е "ай | | = | == &æ iS: tE JUL» ope == | O a ALTETEATCE x L nera = aa | 1 e + 0 | | E (a Г fa dis a ra | Tr £2) O ® mue meto Er Ma | ст —etss ван | ro ra [ет 53 : reel ENCE Fatty Fl CET ED О METE. woo Ee TEE OO CE core Tort | ) 4 и "> TJ = "2 ¢ T р ul - ЕТ $ WESTERBEXE 26A REMOTE INSTRUMENT PANEL REMOTE CONTROL PANEL {REAR VIEW) #44329 — —— - ® 5 #22 MED — | PREMEAT й / FECHIAT ë SWITLE | SWITCH STAZT suit MIE RED #2 NLACA ELE BE Bik FLO WMT | | == | On O O 1: Они нтв тов осин обои #;; — =; — =; —= ; BOOK OOGG GOOG - | | | | | [ = 7 | | | | | | | | | | ее 1 ПО БЫ Ч По — — — A E a | | FREREAT START SWITCH | (50303) SWITCH | | À | Il | Г 816 WWT/ÆT0 | -— € | Bin RED BEAR У) | ela BED _ — M6 TELARER = —o PN. AAJIE Engines 4 Generators 27 ENGINE TROUBLESHOOTING The following troubleshooting table describes certain problems — Mote: The engine's electrical system is protected by a 20 amp relating to engine service, the probable causes of these prob- manual resei circuil breaker located on a bracket ar the rear lems. and the recommendations to overcome these problems. of the engine. — Problem Probable Cause Verification Remedy Key switch on, PREHEAT switch 1. Batiery Swikch not on. 1. Check switch and/or battery connections. depressed: no panel dications: tue! solenoid or electrica! fuel pump 2. Emergency stop Switch oll. 2. Check emergency stop Switch position. 3. 20-Amp circuit breskær tripped. 3. Reset breaker; if breaker trips again, check preheat solenosd circoil and check circuit for shorts to ground 4. K2 relay 4. Check K2 relay 5. Loose battery connechons. 5. Check (+) connection to starter solenoid and (-) connection to | engine ground stud. Check battery cable connechons. | 6. Preheat solencid not operating. 6. Check solenoid 5” terminal for voltage START SWITCH DEPRESSED, no starter 1. Connection to solenoid faulty. | 1. Check connection. engagement 2. Fautty switch. 2. Check switch with chmmeter, 3. Faulty solenoid 3. Check that 12 volts are present at the solencid connection. 4. Loose battery connections. 4. Check battery connections. 5. Low battery. 5. Check battery charge state 6. Ki relay. 6. Check Ki relay. START switch is depressed; pans 1. Poor connections to fuel solenoid. 1. Check connections. indications OK; starter solenoid OK fuel solenoid not functioning. 2. Defective fusi solenoid. 2. Check that 12 volts are present at the (+) connection on the fuel run solencid. 3. Current miter. 3. Check limiter = Generator engine cranks, but does not 1. Faulty fusling system. 1. Check that fuel valves are open. start fuel solenoid energized. 1a. Switch to combine house and start batieries. 1b. Replace batteries. 1e. Check fuel IM pump. 2. Preheat solenoid faulty. 2. Check solenoid. 3. Low batiery 3. Replace batienes. Engine can't be stopped. 1. Faulty DC alternator | 1. Remove Exc. connection at aîternator, repair altemator Battery runs down. 1. Oil Pressure sich. 1. Observe i gauges and pansl lights are acthvalad when engine is not running. Test the all pressure swilch, 2. High resistance leak fo ground. 2. Check wiring. Insert sensitive (0 - 25 amp) meter in battery fines. (Do not start engine.) Remove connections and replace after short is located. 3. Low resistance leak 3. Check ail wires for temperature nss to locats the fauit 4. Poor battery connections. 4. Check cable connections at battery for loose connections, corrosion. 5. DC alternator not charging. 5. Check connections, check belt tension, test altemator See DE ELECTRICAL SYSTEMIALTERNATOR | Battery not charging 1. DC charge circuit faulty. 1. Pertorm D.C. voltage check of generator charging circuit. See DC ELECTRICAL SYSTEM/ALTERNATOR in this manual. 2. Alternator drive. 2. Check drive belt tension. Alternator should tum freely. Check for loose connections. Check output with voltmeter. Ensure 12 volts are present at the Be. termanal. Generator engine sions. 1. Fuel feed pump stainer & dirty. 1. Clean stainer 2. Switches and'or wiring loose 2. Inspect wiring for short circuits and loose connechons. or disconnected. inspect swiiches for proper operation. 3. Fuel starvation 3. Check fuel supply, fuel valves, fuel feed sirziner. 4. 20 Amp circuit bresker trpping. 4. Check for high DC amperage draw during operation. Ensure breaker is not overly sensitive to heat which would cause tripping. 5. Exhaust system & restricted. 5. Check for blockage, collapsed hose, carbon busidup at exhaust elbow. 6. Water in fuel 6. Pump water from fuel tank(s); change fifters and bleed fuel system. 7. Alt intake obstruction 7. Check air intake filter cartridge. 28 ENGINE TROUBLESHOOTING Probable Cause Verification Remedy 1. Coolant not circulating. 1. Thermostat — remove and test in hot water Replace thermostat 2. Loss of coolant — check hoses, hose clamps, drain plug, sir for lesks 2c. Broken or loose belts — fighten/replace. 2d. Air zak in system; run engine and open the pressure cap to bleed air. Add coolant as nesded. Generator engine shuts down, Low oi pressure. 1. Lossofal 2. Oi pressure switch 1. Check dipstick, lock for of leaks at of filtar and at ol drain hose connection. 2. Replace oil pressure swilch. Exhaust smoking problems 1. Blues smoke. 2. Whitz smoke. 3. Black smoke. 1. Incomect grade of engine oil. fa. Crankcase is overfilled with engine oil (oll is blowing ou through the exhaust). 2. Engine is running cold. da. Faulty injector or incomact mector timing 3. Improper grade of fuel 3a. Fuel bum incomplete due to high back pressure in exaust or insufficient air tor proper combustion (Check tor restrictions in eduust system; check arr intake.) 3b. improperiy timad injectors or valves or poor compression. 3c. Lack of air — check air intake and air filter. Check for proper ventilation. 30. Overigad. Engine alarm sounds, pulsates. 1. Loss of on. 2. Ol pressure Switch. 1. Check dipstick, look for ol leales at oil filer and al gil drain hose connection. 2. Replace oil pressure switch, 1. Engine cooant 2. High temperature switch opens al too low a temperature. 1. Check engine coolant level 2. Check for safistaciory operation with switch by-passed, check with ohmmeter, replace if faulty. Cpe 29 ENGINE ADJUSTMENTS NOTE: WESTERBEKE recommends that the following engine adjust- ments be performed by a competent engine mechanic. The information below is provided to assist the mecharic. VALVE CLEARANCE ADJUSTMENT Make the following adjustments when the engine is cold. 1. Remove the cylinder head cover 2 Slightly loosen the cylinder bead belts and retighten them to the specified torgue in the number sequence shown Tighiening Torque — 65=4/6-1(68=5 Nm) Qw a 02 Q5 “ol AS Mae x a 0 см On mM OB os a o ond — THREE CYUNDER 3. Find top dead center compression position for No.1 piston by using the procedure that follows: (a) Turn the crankshaft until TDC mark on the crankshaft pulley is aligned with the mark on the timing gear case. TOC (TOP DEAD CENTER) MARK FOR HO.1 AND NO.4 PISTORS TDC MARK FOF NO.Z AND MND.3 PISTONS (b) With No.1 piston at top dead center on the compression stroke, the rocker arms will not be moved when the crankshaft is turned approximately 20° in both directions. (с) the rocker arms move, No.1 piston is at top dead center on the intake or exhaust stroke. In such a case, turn the crankshaft 360° in the direction of engine rotation again. No.1 piston is now at top dead center on the compression stroke. 4. Loosen the lock nut for the adjusting screw. With a feeler causé inserted between the rocker arm and valve cap, adjust the valve clearance by tuming the adjusting screw. Make certain to adjust all the valves. | 0.25mm (0.0098 INCHES) | INTAKE & EXHAUST E. — Install the cylinder head cover. Head Cover Boll Torque 2 - 3 f-ib (0.3 - 0.45 mig) IWESTERBEKE 30 ENGINE ADJUSTMENTS NOTE: WESTERBEKE recommends that the following engine adjustments be performed by a competent engine mechanic. The information below is provided to assist the mechanic. TESTING ENGINE COMPRESSION Make certain the oil level (dipstick) is at the correct level and the air intake filter is clean. The battery and starter motor must also be in good condition. 1. Warm the engine to normal operating temperature. 2. Move the control lever to a position for shutting off the fuel. (Disconnect the wires if a fuel shutdown solenoid 15 used). Remove all the glow plugs from the engine and install the compression gauge/adapter combination to the cylinder on which the compression is to be measured. Crank the engine and allow the gauge to reach a Repeat this process for each cylinder. COMPRESSION PRESSURE 427 psi (30 Kgl/cm”) al 290 rpm. MAXIMUM PERMISSIBLE DIFFERENCE BETWEEN CYLINDERS 47.7 psi (3.0 Kglcm) NOTE: If the readings are below the limit, the engine needs repair. 6. Re-install the glow plugs and reset the fuel shut-off to the pie LOW COMPRESSION When low compression is found, determine the cause by applying a small amount of oil in the cylinder thru the glow plug hole. Allow the oil to settle. Install the pressure gauge and repeal the above test. If the compression reading rises dramatically, the fault is with the rings. If the compression valve does not nse, the problem is with the valves. A slight rise in compression would indicate a problem with both the rings and the valves. In case of severe vibrations and detonation noise, have the injectors checked and overhauled by an authorized fuel injection service center. Poor fuel quality, contaminant's and loss of positive fuel pressure to the injection pump can result in injector faults. Since fuel injectors must be serviced in a clean room environment, 1t 15 best to carry at léast one extra injector as a spare should a problem occur. Before removing the old injector, clean the area around the base of the injector to help prevent any rust or debsis from falling down into the injector hole. If the injector will not Lift out easily and 15 held in by carbon build-up or the like, work the injector side-to-side with the ad of the socket wrench to free it, and then ft it out. The injector seats in the cylinder head on a copper sealing washer. This washer should be removed with the injector and replaced with a new washer when the new injector Is installed. INJECTOR TO CYLINDER HEAD TIGHTENING TORQUE 404 6-15 (5.5£ 0.5 kgi-m) DRIVE BELT ADJUSTMENT (FAN BELT) Proper inspection, service and maintenance of the drive belts is important for the efficient operation of your engine (see Drive Belts under MAINTENANCE SCHEDULE). Drive belts must be properly tensioned. Loose drive belts will not provide proper altemator chargme and will eventually damage the altemator Drive belts that are too tight will pull the alternator out of alignment and/or cance the alternator to wear out prematurely. Excessive drive belt tension can also cause rapid wear of the belt and reduce the service life of the fresh water pumps bearing. A slack belt or the presence of oil on the belt can cause belt slipping, resulting in high operating temperatures. The drive belt is properly adjusted 1f the belt can be defiected no less than 3/8 inch (10mm) and no more than 1/2 inch (12mm) as the belt is depressed with the thumb at the mid- point between the two pulleys on the longest span of the belt. A spare belt or belts should always be camed on board. A WARNING: Never attempt to check or adjust the drive belt's tension while the engine is in operation. | Adjusting Belt Tension 1. Loosen the alternator adjusting strap bolt and the base mounting boit. With the belt loose, inspect for wear, cracks and fraved edges. Pivo: the altemator on the base mounting belt to the left or right as required, to loosen or tighten. Tighten the base mounting bolt and the adjusting strap bolt . Run the engine for about 5 minutes, then shut down and recheck the belt tensions. i 3. 4. 5 (IN ]WESTERBEKE Engines & Generators 31 CONTROL PANEL TROUBLESHOOTING MANUAL STARTER DISCONNECT (TOGGLE SWITCHES) NOTE: The engine control system is protected by a 20 amp manual reset circuit breaker located on the engine as close as possible to the power source. | Problem Probable Cause Verification/Remedy PREHEAT depressed. no panél indications | 1. Qi Pressure switch. 1. Check semiches and/or bettery connections. preheat solenoid not energized. 2. 20 amp circuit bresker tripped. | 2. Reset breaker If it opens again, check preheat solenoid circuit and run circuit for shorts to ground. | 3. K2 relay faulty. 3. Check relay. | START SWITCH DEPRESSED, no starter | 1. Connection to solenoid faulty, 1. Check connection. engagement 2. Faulty switch. 2. Check switch with ohmmeter. 3.. Fauity solencid. 3. Check that 12 volts are present ai the solenoid connection. 4. Loose battery connections. 4. Check battery connections. 5 Low battery. 5. Check battery charge state. | 6. Ki relzy 16. Check relay. NO IGNITION, cranks. does not start 1. Faulty fusing system. 1. Check for fuel 2. Check for air in the fuel system. 2. Allow system to bleed 3. Faulty fuel ER pump. | 3. Replace fuel if pump. | NOT CHARGING BATTERY 1. Fauity alternator drive. 1. Check the drive belt and its tension. Be sure the aliemator turns freely. Check for loose connections. Chack the output with 2 voltmeter. Ensure 12V are present at the BATTERY RUNS DOWN 1. Ci pressure switch. 1. Observe if the gauges and panel Sights are activated when the 2. High resistance leak to ground. | 3. Low resistance leak to ground. 4. Faulty aiemator engine 15 not running. Test he ol pressure switch Check the wiring, insert sensitive (0-25 amp) meter in battery ines (Do NOT start engine). Remove connections and replace after short is located. Check ail wires for temperature rise fo locale the tauit After 2 good battery charging, disconnect altemator at output. | If lealage stops. Remove añemator and bench test Repair or replace. TROUBLESHOOTING WATER TEMPERATURE AND OIL PRESSURE GAUGES If the gauge reading is other than what is normally indicated by the gauge when the instrument panel is energized, the first step is to check for 12 volts DC between the ignition (B+) and the Negative (B-) terminals of the gauge. Assuming that there is 12 volts as required, leave the instrument panel energized and perform the following steps: 1. Disconnect the sender wire at the gauge and see if the gauge reads zero, which is the normal reading for this simanon. 2. Remove the wire attached to the sender terminal at the sauce and connect it to ground. See if the gauge reads full If both of the above gauge tests are positive, the gauge 15 undoubtedly OK and the problem hes esther with the conductor from the sender to the gauge or with the sender. If eather of the above gauge tests are negative, the gauge is probably defective and should be replaced. Assuming the gauge is OK, check the conductor from the sender to the sender terminal at the gauge for continuity. Check that the engine block 15 connected to the ground. Some starters have isolated sround terminals and ıf the battery is connected to the starter (both plus and minus terminals), the ground side will not necessarily be connected to the block. 32 ELECTRIC GOVERNOR ADJUSTMENTS DESCRIPTION The system is composed of three basic components: 1. Controller. Mounted in the instrument panel. 2 Sensor. Installed on the bellhousing over the flywheel ming geal 3. Actuator. Mounted at the front of the engine and attached with linkage to the throtile arm of the injection = = LINEAR ACTUATOR CONTROLLER ADJUSTMENT 1. Speed. This adjustment is used to raise or lower the engine's speed to the desired hertz. 2. Gain. This adjustment affects the reaction time of the actuator to fhe generator/engine load changes. NOTE: A high gain adjustment can induce an oscillating of the actuator producing a hunting mode. In such cases lessen the gain adjustment. Calibration 1. With no power to the govemor, adjust the GAIN to 9:00 o'clock. 2. Start the engine and adjust the speed by turning the speed pot clockwise to desired speed. ROTE: Controllers are factory adjusted to minimum rpm. However. for safety, one should be capable of disabling the engine if an overspeed should exist. 3. At no-load, turn the GAIN potentiometer clockwise until the engine begins to hunt. if the engine does not hunt, physically upset the govemor linkage. 4. Turn the GAIN potentiometer counterclockwise until stable. NOTE: The controller operates on 12VDC. The voltage range is + 20% (9.6VDC 12VDC 14.4VDC). If voltage varies above or below these ranges, the controller will not operate and the engine will run in an idle mode until proper voltage is supplied to the controller PRISION TN FNEZST4É 24V TE ELECTRON CONTROLES L TERMINAL BOARD #2 REFER TU WIRINS DIAERAIET INSPECTION AND ADJUSTMENT The controller has two adjustment pods. You need à mini screw driver to adjust these. One is speed and the gain These are noted on the drawing of the controller. When you press the preheat switch the actuator linkage attached to the throttle arm of the injection pump should move outward towards the injection pump and retum back into the actuator in a quick motion. Start the engine. The speed should be in the low idle range 600-700 rpm. If the engine speed is higher than tus idle range, shut the engine down. Check the linkage between the actuator and throttle arm. The throtie arm stop should be shout touching the open idle stop screw boss. Adjust the link- age to position the throttle lever. The controller has an adjust- ment screw for speed adjustment. Turn this screw outward (counter clockwise) a few tums. Restart the engine. NOTE: If there is any oscillating of the actuator linkage producing hunting, adjust the gain towards zero “O” until this hunting is removed. Increase the engine speed slowly with the speed adjusting screw turning it inwand (clockwise). In some instances this screw may need to be turned 6-10 tums before an increase In engine speed is noted. Bring the engine speed to 1800 rpm (60 Hz), 1500 rpm (50 Hz). Momentarily push the actuator lirikape towards the actuator and release. The actuator should quickly regain proper speed. If there is any hunting adjust the gain towards zero 0” until this hunting is removed. When the gain is adjusted you may need to readjust the speed at no load, shut the generator down. Push the DC exciter circuit breaker in. Start the generator. Check speed (Hertz) set at 60 Hz. Load the generator. If the govemor is slow to react and maintain 60 Hertz adjust the gain clockwise. Again you may need to adjust the speed at no load. You will find the governor will maintain 60 + 0.5 Hertz right up to the full rated amperage output for the generator. (ES WESTERBEKE Engines & Generators 33 LINEAR ACTUATOR TROUBLESHOOTING 1. Check the battery volzge al the controller termine! block with the Prebezl/On sumich depressed 2. Inspect the linkage for binding or sticking a. M there i= no signal or 2 weak signal from the WIRE a ea tu Sa wie and biack'whit wire leads from the MPU on the controler terminal block. Whiz cranking the engine or with the engine running at idle. voltage should be 1.5-2 5 VAC. NOTE: The AC input impedance of meter mist be 2000 ohwmsAvolts or greater ; ROTE: When making this test pr discal units, dab the preheat solencao by disconnecting the “S- ела! connection 50 às not lo damage the glow pings. 4. Checx the actuator with the preheaton switch depressed. This provides DC voltage to fre controller. Mezsare the DE voltage between the actuator connections on the System appears dead (No actusior movement) Engine runs, but at ¡die speed à Purple lead to Black DC (-). В. Purple iead/purple/white lead to Black DC (+). MOTE: Continue thés test (ONLY) 7 the battery voltage = not present. E The following checks ère performed between the connections at the actuator and the Black DC (-) connection on the controller termina! block. This is to determine rd there & à break in the fine between the controllers minal block connection and the actuator connections or the actuator leads themseives NOTE The actuator should fully extend and retract when the 1) Low voltage (1.0-2.0 VOC) àt either actuetor connections 2) Battery volage al both actuator connections. 3) Battery voliage & one actuator connection but mot at the second. Check the controller by removing the two. purple leads ona af a ime that come from the actuator off the controSar terminal block. Litt one actustor lead and depress the preheation switch. Reconnect and do the same with the second. NOTE: Eariy controllers had two solid purple leads for the actusior connections Later model controles have one solid lever goes to full 1. when the preheat ES depressed and says 4 Correct 1. inspect the DC circuit back to the Staring battery 2. Free up the Enis and clean and lubricate the linkage. 3. Check for damage to or improper adjustment of magnetic pick-up. Replace of re-adjust 4. Low voltage (1.0-2.0 VDC) el either actuator connections. b. Replace the controBier if battery voltage is not present ai both the Purple leads. 1) Broken actuator lead, repair. 2) Broken actuator lead, repa or replace actusioc 3) Check actuator winding for open. Replace actuator 1. Check for à shorted actuzior lead Replace Me controBer because it Should not cause the actuator lever to go to full fuel when fe engine is not running. pirrpie and 3 purpladwhite stripe for the actuator connection The purpleMtil sad is designatad (+) and le specii amy in gasoëne DC circus a Actuator 10 tul extension (Diesel) & Check for shorted actuator load. Does fot retract (Gasoline). E Actuator does not extend (Diesel). b Replace controller _ Actuator funts éuring operation 1. Linkage or rod end bearings are sticking or binding 1. Lubricate or replace. 2 Improper governor adjustment z Reañus! the calibration. 3. LEAS PRET LAN VAE à i actuator doesn't fully edend (diesels) or retract a Connect a DC voltmeter to Red (+) and Black (-) leads (A SEE pl at the controlizr terminal block. the voltage is less than specified, check for b. Disconnect both leads coming from actuator from юо5е or poor connections in the DC circuit back to Controller terminal block. Me bañery, check the K2 relay and its connections. E Connect one lead from the actuator to the Red (+) on the terminal block and the other actualor lead to the Black (-lon the terminal block. d Mementariy the should extend and sky extended extenden (diese) ans retract (gasoline) 35 long as the switch te ads wae performing is Is across the fied {+ } nd Back €) leads whis this test be greater than 60% OC velo: mentar поро чей „ареной 24 VIC E 60% = 19.2 VDC 12 VDC & 80% = 36 VOC NOTE: Reconnect Me actusior lesds propeniy after completing this hast & MPU positioned marginafiy too tar away from fiywfes! teeth giving erraic AC input 10 controler. e Check te position of the MPU. If problems continue to persist, contact your WESTERBEXE dealer for additional assistance. y 34 GenRemote CALIBRATION лодок, The unit consists of a Power Logic Module, Display Panel and six conductor shielded Display Cable. The shielded cable links the display to the module and can be up to 300 feet long. Two display panels can be daisy chained to one (1) module output. The module supports two display cable outputs allowing for a total of four (4) displays per module. Total allowed cable length per module, including both display cable outputs, is six-hundred (600') feet The logic module is powered directly from the generator’s cranking battery and consumes less than 70 milli amps (70/1000 of an amp) when the generator is idle. DC operating voltage can be 12 or 24 volts. The AC generator output can be 115V, 240V, 50/60 Hz, single phase (1) or three (3 ©) phase. Generator and Engine Monitoring 1. DC Voltage Cil Pressure Water Temperature AC Voltage AC Current L-1 AC Current 1-2 Line Frequency Hz Engine Hours Up to 10,000 Hours E 307 NN A Y NN Exhaust Over Temperature Alarm GenRemote is designed to safely interface with the existing engine sensors. The digital display is easily calibrated to match the readings of the manufacturer supplied mechanical gauge package. The GenRemote circuitry is isolated from the generators OEM electrical system. This assures that GenRemote will not interfere with the manufacturers supplied gauge package. Electrical isolation also allows normal generator operation should the GenRe- mote be accidentally disconnected from the generator. Electrical Hook-Up Electrical hookup includes interconnecting with both the generators AC and DC systems. The AC wires Required: The 115 volt Line One [L-1 Jis Black Line Two [1-2] is White. The 220 volt Line-2[L-2]is Black witha Red Stripe. The 220 VAC Neutral connection is White and is Not connected to the GenRemote, The 220 VAC Generator Neutral is the same as Green Ground wire. The 115/220 VAC Neutral [White Color] is connected to the generator frame. The DC Wire Harness Supplied Color Code as follows: Green is Ground, White is ESS [Emergency Stop Switch], White/Black is the Stop Switch, Black is Preheat, Orange is Oil Pressure, Red is Water Temperature, Yellow is the Exhaust High Temperature Alarm [marine applications only] and Black/Red is the Start Button. IMPORTANT ! The Exhaust High Temp terminal is connected to the ESS terminal when it isnotused. Cv] WESTERBERE Engines E Generators 39 GenRemote CONTROL STATION IMPORTANT! The generator must be running and the system fully operational before the calibration mode can be accessed Enter the Calibration Mode: Press and holding the Mode Button for 10 seconds. Entry 1s indicated when the hundreds place decimal of the 3-digit, 7-scgment display turns on. Calibration Button Functions Mode Button: Press and hold the mode button to enter the calibration mode. Preheat Button: Use the Preheat Button to manually advance through the AutoGauge Scroll functions until the desired gauge is reached Stop Button: Use the Stop Button to decrement or reduce the gauge value. Start Button: Use the Start Button to increment or increase the gauge value, Mode Button: Press the mode button to exit the calibration mode. Not pressing any button for 30 seconds will also exit the calibration mode. Firmware LD. The firmware identification number will appear in the display when the calibration mode is exited. A typical firmware identification number is Calibration Method A Calibrate the AutoGangeScroll by using the values derived from 9% PRESSURE Es the mechanical gange package supplied with the generator. Tr т 518 Calibrate the AC Volt and Current Meter with à standard Amp ef mts fms and Voltmeter normally carried by most service technicians. No calibration of the Frequency Meter is required or allowed. The Frequency Meter 1s factory calibrated to = one (1) Hz. NOTE: The unit will automatically exit the Calibration Mode if no buttons are pressed for thirty (30) seconds. Firmware identification When calling for service or warranty repair it is useful to have the firmware Fret identification number. The unit's age, software revision level and the systems [ (7 aC hardware can be identified from this number. The firmware identification {| Ol number is also placed on the 28 pin microprocessor located in the control module assembly. The firmware number appears in the display when the calibration mode 1s exited ` FAIL SAFE PROCEDURES The fail-safe system is setup to display potential failures approximately 10% lower than the OEM settings. This allows time for the operator to manually shut down the generator before serious damage OCCUTS. Failures are displayed by turning on the appropriate warning LED. For Example, the high coolant temperature alarm will appear at 195 * F and the OEM safety switch will stop the generator at 210 °F. The alarm LED will remain lit after the generator shuts down to provide indication as to why the unit stopped. The alarm LED can be cleared by pressing the stop button or by restarting the amt The Fail-Safe Protocols include: 1 - Oil Pressure 2 - Coolant Temperature 3 - Exhaust Over temperature KLIXON JWESTERBEXE 36 GenRemote WIRING DIAGRAM Figure - 20 Westerbeke Wiring for Westemeke Homess cnd Plug Assy. Federal and Local Electrical Code requirements for Proper Wie Sting. Important | Neutral Connection to Gentemote Is Not Required for 220 Voit Applications For 115 Volt sysiems L2 ls Neutral, this is usuoily the white wire. LT OUTPUT TO LOAD ol = — Distribution fonel ad — WESTERBEKE Engines & Generalors 37 GenRemote INSTALLATION DIAGRAM Hole: GenRemote uses engine Oil pressure ond AC vollage to recogrèe he Cenremote | engine sunning Hectical Box | Without AC nputihe generator wil in and GenRemoie will only moniiorn the Battery, Water Temp ond Oil Pressure. Mo AC readings will be displayed and the Run Indicator wil not um on 1 Socio * AC Lood con be comecied снесту Юю generotor, however, the L1 ond L2 curent reacings Westetbeke AC Output LI & L2 uit est fe Covi Neutral Not Required The AC signal MUST be wired — for 220 Voi Appicalors to GenRemote, STOP/START ROCKER SWITCH The One Iuminated Burton Start / Stop Rocker Switch is provided for areas where remote start stop fmetions are reguired and no spece Es available for the standard display panel Startthe generator by pressing and releasing the upper rocker once. The lamp will fiacker repidhy winle the generator is starting. The indicator lamp will remain on and steady while the generator is running. Stop the generator by pressing and releasing the lower rocker once. Trouble Indicator: The indicator lamp will flicker siowiy whil= the generator iS operating ifa service problem is developing Possible problems include, High Coolant Water Temperature, Low Oil Pressure and High Exhaust Temperature Safety Switch GenRemote SPECIFICATIONS DC OPERATING VOLTAGES «ori cacssiisrsnsisistsssassmnrsnessssssess ts sossstnnmssassnss 12 or 24 VDC DC Current REouremeNT MODULE e.======0==mneretooscaaticacicao teria roce 50 ma DC CURRENT REQUIREMENT —IISPLAY ...cemmrmmrsersrrrrsrssssssssssssssssnrensssnsensnsnsnssasss .. 20 MA DC CURRENT EACH ADDITIONAL DiSPLAY 5 15 ma DV TOO rte tree te 2222222222" 120 / 240 VAC PHASE ....cosrmenoos Td in" 19003 © STANDARD CURRENT METER sssreerrrreere rer e Ire os oa 60 amps REMOTE CURRENT METER FEN va .200 amps START RELAY occncarerressssssssosesssossimmmnmeanssssmssnssesssssrersssitomennmisnnes sess essere res ssssss 7 AMPS Stop RELAY m..... EEE EEE À AMPS Presa REG em E 7 AMPS Maomum $ or DispLAYs PER MODULE ceecesnccononenoas mem meta aan ЙЕ Maxomum # or DispLays Daisy CHAINED Lecvrussers da in in 2 Maamum DispLay CABLE LENGTH (ONE DIRECTION) cov…ouscensansannameanennaresenansessunnes 300 FT TortAL AuLoweo DispLay CanuE LENGTH ..………10…0sresserstansansmnnnenmensansessssssassnnaane 600 FT TEMPERATURE RANGE Cecaacemccner 0° F THROUGH 180° F NOTE: Each module will support a maximum of four displays. No more than two (2) displays should be dom chained to ont module output. The m e supports two (2) separate display output lines Cv ]MWESTERBEKE. Engines £ Generators 39 GENERATOR INFORMATION USE OF ELECTRIC MOTORS The power required to start an electric motor is considerably more than is required to keep it running after it is started. Some motors require much more current to start them than others. Split-phase (AC) motors require more current to start, monly used on easy-starting loads, such as washing machines, or where loads are applied after the motor is started, such as small power tools. Because they require 5 to 7 times as much current to start as to run, their use should be avoided, whenever possible, if the electric motor 15 to be dri- ven by a small generator. Capacitor and repulsion- induction motors require from 2 to 4 times as much current to start as to run. The current required to start any motor vanes with the load connected to it. An electric motor connected to an air compressor, for example, will require more current than a motor to which no load is connected. In general, the current required to start 115-Volt motors connected to medium starting loads will be approximately as follows: MOTOR SIZE AMPS FOR AMPS FoR FOR (HF) | RUNNING _ (AMPERES) (AMPERES) 16 | 32 6410224" 1/4 45 9210327" 13 52 10.4 to 725" 1/2 72 14.410292" au _ 102 | _ 20410408" 1 13 | 26 to 52 "NOTE: In the above table the maximum Amps for Siarting is more for some small motors than for larger ones. The reason for this is thar the hardest starting rypes (split-phase) are not made in larger sizes. Because the heavy surge of current needed for starting motors is required for only an mstant, the generator will not be damaged if it can bring the motor up to speed in a few seconds. If difficulty is expenenced in starting motors, tum off all other electrical loads and, if possible, reduce the load on the electric motor. REQUIRED OPERATING SPEED Run the generator first with no load applied, then at half the generators capacity, and finally loaded to 1s full capacity as indicted on the generators data plate. The output voltage should be checked periodically to ensure proper operation of the generating plant and the appliances it supplies. If an AC voltmeter or ampmeter is not installed to monitor voltage and load, check it with a portable meter and amp probe. NOTE: When the area in which the generator is installed contains AC equipment of 120 volts only, it is recommended that the generators AC terminal block be configured to provide one 120 vol: AC hot leg for the distribution panel. This will ensure good motor starting response from the generator. Generator Maintenance Ш Мана! ble clean ei Connections of terminal boards and rectifiers may become corroded, and insulation surfaces may start conducting if salts, dust, engine exhaust, carbon, etc. are allowed © build up. Clogged ventilation openings may cause excessive heating and reduced life of windings. E For unusually severe conditions, thin rust-inhibiting petroleum-base coatings, should be sprayed or brushed over all surfaces to reduce rusting and corrosion. HM In addition to periodic cleaning, the generator should be pestes METE Ae SE ANOS OA overheated terminals and loose or damaged wires. E The drive discs on single bearing generators should be checked periodically if possible for tightness of screws and for any evidence of incipient cracking failure. Discs should not be allowed to become rusty because rust may accelerate cracking. The bolts which fasten the dnve disc to the generator shaft must be hardened steel SAE grade 8, identified by 6 radial marks, one at each of the 6 comers of the head. . Bl The rear armature bearing is lubricated and sealed; no maintenance is required. However, if the beanng becomes noisy or rough-sounding, have it replaced. I Examine bearing at periodic intervals. No side movement of shaft should be detected when force is applied If side motion is detectable, inspect the bearing and shaft for wear. Repair must be made quickly or major components will rub and cause major damage to generator. CARBON MONOXIDE DETECTOR WESTERBEKE recommends mounting a carbon monoxide detector in the living quarters. Carbon Monoxide, even in small amounts is deadly. The presence of carbon monoxide indicates an exhaust leak from the engine or generator or from the exhaust elbow/exhaust hose, or that fumes from a nearby generator are lealane in your area. If carbon monoxide is present, ventilate the area with clean air and correct the problem immediately! e POWER TAKE OFF SYSTEMS POWER TAKE OFF ADAPTER A power take off adapter can be attached to the generator backend. This adapter allows access to the full power of the engine for à variety of hydraulic and electrical accessories. Contact vour WESTERBEKE COMMERCIAL GENERATOR SUPPLIER for additional information. XRT POWER SYSTEM The XRT power system combined with a Westerbeke generator provides electrical and hydraulic power for fire/emergency apparatus The system generates electrical power for auxillary lighting and provides continuous. operation of up to three extrication tools at the same time. SPECIFICATIONS Components Dual stage continuous duty pump, stainless high pressure fithings, three gallon reservoir with filter, pump enclosure with integral control blogk assemblies. System Avalabiity 5.000 psi phosphate ester fluid and mineral fluid systems up to 1050051 Dimensions COMB! pump in shroud. 10m x WHS" x Hed” x 42 Tbs Reservoir HE 177 x W:177 xD: 65 Open Center Vaives LATS" xW 275" xH 40." For additional information, contact XRT POWER me Cm or call (800) 343-0480. XRT POWER SYSTEMS 32 Tioga Way Marblehead MA 01945 Engines 5 Generators 41 BT GENERATOR This generator is a four-pole, brushless, self-excited generator which requires only the driving force of the engine to pro- duce AC output. The copper and laminated iron in the exciter stator are responsible for the self-exciting feature of this gen- erator. The magnetic field produced causes an AC voltage to be induced into the related exciter rotor windings during rota- tion. Diodes located in the exciter rotor recufy dus voltage to DC and supply it to the windings of the rotating field. This creates an electromagnetic field which rotates through the windings of the main stator, inducing an AC voltage which 15 supplied to a load. A step down transformer is connected in parallel to the AC output of the main stator. An AC voltage is produced in the auxiliary windings of the transformer and the main stator and is, in turn, supplied to a full-wave bridge rec- tifier. The rectifier produces a DC voltage to further excite the exciter stator windings, enabling the generator to produce a rated AC output. An optional solid-state voltage regulator is available to work in tandem with the transformer regulator to A circuit breaker is installed on all WESTERBEKE genera- tors. This circuit breaker will automatically disconnect gener- ator power in case of an electrical overload. The circuit breaker can be manually shut off when servicing the genera- tor to ensure no power is coming into the boat NOTE: This circuit breaker is available as a WESTERBEKE add-on kit for earlier model generations; contact your WESTERBEKE dealer. BREAKER 7 re BLACK LI = 8.0KW - 42707 =) > 10.0KW - 42698 = WHTEN _ “E 12.50W-42709 (<. Ps BT GENERATOR / SINGLE PHASE [SIX STUD] A. EXCITER STATOR WINDINGS 1& 2 INTERNAL WIRING SCHEMATIC (SIX STUD) W/OPTIONAL VOLTAGE REGULATOR A-1 and A - 2 Exciter Stator Windings (Selector in COMP position) B. EXCITER ROTOR and FIELD |. Auxiliary Windings (A - B - C) 2. Diodes (6) 3. Rotating Field Windmes 4. Pos] Resistor C. MAIN STATOR 1. Main Stator Windings 2 Mazin Stator Windines 3. Main Stator Auxiliary Windings D. COMPOUND TRANSFORMER 1. Compound Transformer Windings 2. Compound Transformer Windings 3. Compound Transformer Auxiliary Windmes Resistance readines and voltage checks can be accessed easily for the components in the exciter circuit A, G, C-3 and D-3 by locating the color coded wires at the connection points shown on the above schematic. When checking winding resistance values be sure to Lift both of the component's electrical connections. G. BRIDGE RECTIFIER A.VR Do тоне т Ea 3 ESC 3 t+ QD ‘ : : ; 50 Hz TERMINAL | i ' - : - ZN #7 e5+560 Hz TERMINAL ' EOS =— $ \ W2 ; € ACE : N i Poo RR | 1 т = ‘ - 3 VI | Ч ея па : | ps +. ан La + E E 5 и ES | E ай | = km! VELOWE FED = RED a = ——— = GREEN AVR.| -—| PLUG = = AVR ED +1 | max | PLUG 1 Г BLUE FATE N || | кл E e te — mena Lun Fre | TO MERTIVOLIS Bm —Y Ne т | pe == AVR — La || Optional Automatic Voltage Regulator Plug (6 Prong). IWESTERBEKE 43 BT GENERATOR SINGLE PHASE OPTIONAL AUTOMATIC VOLTAGE REGULATOR (AVR) BT 6 STUD MODELS ONLY An optional solid-state voltage regulator (board #34410) is available for use with the BT series generators. When installed, and the regulation switch is moved to the ELEC - pound transformer regulator to regulate the generator’s volt- age output. In the EL EC mode, the regulator provides excitation to the group] exciter windings, and the trans- former provides excitation to the group 2 exciter windings. |. The regulator is mounted using existing tapped holes In the generator's case. Use two (2) M4 x 0.7mm screws, each 15mm long, with lock washers to mount the regula- tor board. 2. Connect the 6-prong generator plug to the receptacie on the regulator board. NOTE: The plug is keyed to engage the regulator receptacle in one direction. Check this and insert it correctly. = Before moving the selector switch to the ELEC position, the NO-Load voltage produced by the generator when in the COMP position will have to be adjusted. The NO- Load voltage should be admsted down between 114 - 118 volts (60Hz) or 224 - 228 volts (50Hz) following the procedures as explained earlier in tins manual. . With the generators no load voltage properly adjusted, the regulator board potentiometer to set NO-Load voltage at 120 - 122 volts at 61.5 - 62.0 Hertz (230 - 234 volts at 51.5 - 52.0 Hertz). The regulator board is operating In par- voltage output within +5 per cent from NO-Load to FULL-Load NOTE: Do not use the regulator to force NO-Load voliage down. Use the compound transformer for this function. Using the regulator to perform this causes the regulator to use more for loaded conditions. SL GENERATOR VOLTAGE ADJUSTMENT tests and adjustments be performed by a quailified technician Generator Frequency 1. Frequency is a direct result of engine/generalor speed: 1800 rpm = 60 hertz 1500 rpm = 50 hertz. 2. To change generator frequency follow the steps below. a Connect the AC output leads to the AC terminal block, following the illustrations on this page. b. If an AVR is installed, reposition the blue or blue/white lead to correspond to the hertz selected on the Voltace/Hertz Connection Bar. H there is no automatic voltage regulator (AVR Voltage/Hertz Connection Bar. Simply reconfigure the AC terminal for the hertz change. e Start the engine, monitor voltage and adjust engine no-load speed. Adjust diesel units by the linkage between the throttle arm and fuel solenoid or the throttle lever on the injection pump.. G hertz no-load speed, 61.5-62.0henz 0 her no-load speed, 515-520 henz d. After the no-load hertz adjustment is made, the no-load voltage may need to be readjusted. In most cases, if the generator was producing the comect no-load voltage at the previous hertz setting, it would be correct at the changed hertz setting. In the event it needs adjustment, adjust the shim thack- ness under the laminated steel bar of the transformer. 60 hertz: no-load voltage, 121-124 volts. 50 hertz no-load voltage, 232-236 volts. e. Load the generator to the rated amperage output corresponding to the hertz speed of the generator. Rated Loaded Speed 60 bertz: loaded speed, 58.5 - 59.0 hertz 50 hertz: loaded speed, 48.5 - 49.0 hertz The lowest acceptable voltage at full rated output (amps) 60 hertz: 108 - 110 volts 50 hertzz 205-210 volts be moved when changng + from 115 vois and 1107220 ë volts 50 hertr to 230 volts = 50 nartz. From maidng con- 6 nechons to the AC terminal biock, use terminal endsior | 14 ch studs hai wi accent muit-stand copper wire sed {rhe amperage rating from the hot lead con- nection. The frame ground wie © while or white with 2 green sinp. it Connecs bewee the neutral sid and the generator frame. GENERATOR VOLTAGE ADJUSTMENT NOTE: WESTERBEKE recommends that the following generator tests and adjustments be performed by a quailified technician. NO-LOAD VOLTAGE ADJUSTMENT Voltage adjustment is made with the generator regulation being governed by the compound transformer. 1. The selector switch, if installed, must be in the COMP position. To confirm no-load voltage, start the generator and apply a momentary (moderate) load to excite the transformer. The voltage produced by the generator after the momen- tary load is removed is no-load voltage. Note the voltage output from the generators 120 volt legís) (230 volt 50 heriz). The no-load voltage should be between 121-124 volts at 61.5-62 hertz (232- 236 volts at 51 5-52 hertz). NOTE: The no-load voltage should be adjusted to the voltage produced by the generator once started and a momentary load should be applied to excite the transformer and then removed. The voliage produced by the generator after this momentary load is removed is no-load voltage. 3. To raise or lower the voltage, shims of varying thickness (non-conductive material) are placed or removed from under the steel laminated bar on top of the compound soften at temperatures in the 176° F (80° C) range. A small reduction in no-load voltage (1 to 3 volts) can some times be accomplished by gently tapping the top of the laminated steel bar to reduce the gap between the existing shims and the transformer core. = NOTE: No-load voltage may be effected needing readjustment with the compound transformer. Do not use these adjustments to compensate for overload conditions being placed on the generator/engine {inductive-motor type loads). Loss of generator hertz/speed, the result of overload, will cause à drop in voltage oufpul. Shim thickness of 0.001 inch will change the no-load voltage by approximately 4 - 6 volts. Adding shim material raises the no-load voltage. Removing shim material lowers no-load voltage. FULL-LOAD VOLTAGE ADJUSTMENT The voltage hertz connection bar that is used when changing from 60Hz to-50Hz can also be used to increase or decrease the generators full-load output. Fine voltage adjustments can be performed by repositioning wires A to leads #1, #2, and #3 increasing the loaded voltage progressively in that order. A no-load voltage adjustment will have to be made as well. Should full-load output fall below 108 volts-60Hz (210 volz-50Hz), the voltage should be adjusted. NOTE: When the optional voltage regulator is installed and if the Blue/White (Blue) lead is not correctly positioned to correspond to the Hertz the unit is operating at, the regulator will sense incorrect voltage and cause the generator to produce abnormaily high output voltage. a = 46 BT GENERATOR VOLTAGE REGULATOR ADJUSTMENTS [THREE PHASE] Descrinti The voltage regulator is an advanced design which ensures optimum AC generator performance. It is equipped with complete protection circuitry 10 guard against operating conditions that could be detrimental to the AC generator. This potentiometer 15 used to adjust output voltage. Al proper engine operating speed the output voliage should be held at +1% from a no-load condition to a full rated generator output and from power factor 1.0 - 0.8 with engine drive speed variations up to -6%. Prior to starting the engine, tum the VOLT and STAB wimmers (using a mini phillips screw- driver) fullv in a counter clockwise (Mimimum) direction until you feel them hit their stops. Tum the AMP and HERTZ mmmers completely clockwise (Maximum) in the same manner. With the generator moning at no-load, at normal speed, and with VOLT adjust at minimum, it is possible that output voltage will oscillate. Slowly rotate the VOLT adjust clockwise. The voltage output will increase and stabilize Increase the voltage to the desired value. In this situation, only the green LED will stay lit. Stability This potentiometer permits variation of the regulator's response to generator load changes so as to lmit overcom- pensation and obtain a minimum recovery tume to the normal voltage outpul In order to adjust the regulator stability the generator must be running at no-load and the output must be monitored. Turn the STAB adjust slowly clockwise until the voltage starts to fluctuate. At this point rotate the STAB adjust coun- terclockwise until the voltage is stable within 1 or 2 tenths of a volo Ш En + eda] | | SE ges € | me = yellow &_ | = sio e 1-6 si = Srab 21 | || & |- = Von = | = otis : у E e (sie Amp-Hertz These two adjustments are used in conjunction with the two protection circuits in the voltage regulator that are indicated by the illumination of colored LED lights. 1. Delaved overload protection (yellow LED). 2 Low speed protection (red LED). Both systems have an intervention threshold winch can be adjusted using the respective potentiometer. Each of the two circuits are able to cause an adequate reduction in excitor valtage to safeguard the excitor windings and prevent their overheating. The overlosd protection system has a delay which permits temporary overloading of the generator dunng times such as motor start-up or other similar load surge demands. The regu- lator also has a third LED (green), that glows dunng genera tor operation to indicate correct operation of the regulator with the generator. Setting the Overload Protection In order to set the AMP overload protection, the generator must be loaded to its full output rang. 1. Load the generator to its rating, then decrease the speed of the engine by 10.10% (54 Hertz on 60 hertz units, 45 hertz on 50 hertz units). 2 Rotate the AMP adjustment counterclockwise until it ints its stop. Wait about 15-20 seconds after which the AC out- put of the generator should drop and the yellow LED hight should come on. 3. Slowly rotate the AMP adjustment clockwise until the output voltage increases to approximately 97% of the volt- age output at the start of the adjustment. At thus point the yellow LED light should come on. 4. Return to nominal speed, the yellow LED will tum off and the generator voltage will nse to its normal valve. Should this not happen, repeat the adjustment. NOTE: When changing from 60 hertz to 50 hertz operation, remove the 60 hertz jumper bar from the regulator board Setting the Underspeed Protection NOTE: If the unit is operating ar 60 Hertz ensure that the jumper strap is in place on the regulator board between the two 60 Hertz terminals. In order to adjust the underspeed setting, the generator should be running at no-load 1. To adjust the underspeed (low frequency) protection circuit, lower the engine speed at 90% of its normal running speed (54 hertz on 60 hertz units, 45 hertz on 50 hertz units. 2. Rotate the Hertz adjustment counterclockwise slowly until the generators AC output voltage starts to decrease and at the same time the red “LED” light comes on. 3. Increase the engine speed to ¡ts normal speed (frequency). The red “LED” light will go out and the AC voltage out- put will return to normal. With the above adjustments made, the regulator should func- поп normally. IWESTERBEKE 47 | Dsraton p--=———— =-------—-——- 0e BT GENERATOR INTERNAL WIRING 3 PHASE TWELVE WIRE RECONNECTABLE maim mel EEE MOVIE 5.3 BUS FUSE y E VOLTAGE REGULATOR HITT, ALL 8071 ame =: MOTIJA HET yh REGULATOR SENSING 3 PHASE WYE-DELTA CONFIGURATIONS NOTE: WESTERBEKE recommends that the following generator [ests and adjustments be performed by a qualified rechmician. Description The regulator is equipped with seven numbered terminals (0 to 6) and their related brass jumpers. The illustrations shown connection points and jumpers for the 3 phase config- uration of the generator. The sensing leads connect between pin #1 and pin #2 on the AC terminal block and connection #7 and #0 on the voltage regulator board. NOTE: Series Delta requires the installation of a jumper on the regulator board between terminal B and J. L 208 VAC 130 60 Hertz N 120 VAC 10 60 Hertz -L 1920 VAC 30 50 Herz N 115 VAC 1 50 Hertz SERIES WYE (STAR) L2 L3,-N 120 МАС L-L 230-VAC L2,L3,-N ПЗ МАС 10 60 Hertz 30 50 Hertz 1 50 Hertz BT GENERATOR TROUBLESHOOTING CHART NOTE: WESTERBEKE recommends that the following generator fests and adjustments be performed by a qualified technician. ~ Problem I Probable Cause — Verification Remedy | Low voltage at N/T and F/L No 1. Regulator board detective. 1. Replace the reguiator board. Adjust AVL voltage with adjustment from regulator potentiometer transiormer, then switch lo ELEC ang adjust with | AMP. polenbomeler. 2. Exciter stator winding A-1 open. 2. Check resistance values of C-3 and D-3 windings and я a their connections Low voltage af NL and voltage drops 1. Diode(s) in exciter rotor shorted (B-2) 1. Check the diodes in the exciter rotor. further a5 a load is apphed. 2. Audiary windings in exciter 2. Check the resistance values and continuity to ground | rotor shored (B-2). Voltage OK at NA and low at FL 1. Audiary windings in the exciter rotoc 1. Check the resistance values and confinufty to ground. | stator compound winding 2. Check the continuity and the connection of the winging. | E open 3. Awaizry windings D-3 or C-3 open. 3. Check the continuity and the connection of the winging. Voltage unstable 1. Defective regutator board. | 4. Check the stability of DC voltage from the reguiztor to the exciter stzior windings. Operaie the unit on COMP. Replace the | reguiator board. 2. Engine E hunting. 2. Check the engine operation and the fuel system. 3. Electrical connections. 3. Check for clean and secure connections Engines & Generators 50 SPECIFICATIONS 10.0KW/8.0KW BTDA GENERAL CS ОАО Engine Type Diesel. four-cycle, three-cylinder, fresh water- | General Open flow, seif priming. | mechanism me ne Fuel No. 2 diesel ol (cetane rating of 45 or higher). Displacement 80.4 cubic inches (1.318 Ber) Fuel Injection Pump ee (055 Imecton Timi o Aspiration Naturally aspirated Fuel imecton Timing (Top Dead Canter) | Combustion Chamber Swirl type. Nozzle Troie type: Bore & Stroke 3.07 x 362 inches (78 x 92 mm) fect me Spin regiacesiie (PFO2E06Y), ys 30 | |: en ото Re Аг Виз 1 {3.9 cmm) at 3600 rpm. TRENT Clockwise, when viewed from the front. | im bustion) ни te Fuel Lit Pump 12 voit DC Et capacity of 5 (15 mm) sobd state | Wacht (Enge Only) 276 lbs (276 kos) without transmession. | inclination Continuous 15° ELECTRICAL SYSTEM Temporary 25° {not to exceed 30 min.) В 12 Vol. 3 TUNE-UP SPECIFICATIONS Batey Copey 400 — 600 Cold Cranking Amps (CCA) Compression Pressure 427 psi (30 kg/m”) at 280 pm DC Charging Atemator 57 Amp rated, belt-driven 354 psi (27 kg/cm") Starting Aid Giow plugs. sheathed type Valve Timing Intake Opens Starter 12 Volt, reduction gear ка Closes $T 1750 IS Valve Seat Angia 45° General Fresh water-cooled block, Thermostatically- Engine Timing 17" BTDC controlied with heat exchanger injector Pressure 1991 + 71 - 0 psi (140 + 5 - 0 kyon?) Operating Temperature TEC | Valve Seat Angie Intake 45° Fresh Water Pump Centrifugal type, metal mpeñar, beit-drrven. | Exhaust 30° System Capacity 1.9 LS ots (1.5 Mers) Valve Clearance 0.0098 inches 0.25 mm | (Fresh Water) | (engine Cold) г : LUBRICATION SYSTEM | General Pressure led system. СЯ Filter Full flow, paper element. spm-0n type. Sump Capacity 3905. ats (37 liters) (not including filter) Operating Où Pressure 50-60 ры (35-42 к/ст) (engine hot) Os Grade API Specification CF or CG=4, SAF 30, 10-30, 1777-40 CA WESTERBEKE 91 SPECIFICATIONS 15KW BTDC/12.5KW BTDB ama Engine Type Diesel. four-oycie. four-cyinder, fresh water- — | cooled, vertical in-Ene overhzad valve Mechas Displacement 107.3 cubic inches (1.755 Mer) Aspiration Naturally aspirated Combestion Chamber Swirl type. Bore & тоже 3.07 x 362 inches (78 x 92 mm) ring Order 1-3-4-2 [erection of Rotation Cloclowrse, when viewed from the front Compression Ratio 771 Dimensions - inches (mm) Height 24.0 inches (609.6 mm) Engine Only Width: 19.0 inches (482.6 mm) Length: 34.6 inches (878.8 mim) Weight (dry) 569 bs (258.10 kgs) Fusl Consumption 1.42 gir (5.38 ltrhr)al 1800 rpm HF @ 1800 RPM 25 НР | Compression | at 780 Spilled Timing (Static) 17" (spill) Valve Seat Angle Intake 45° Exhaust 30° o | Valve Seat Angle Intake 45% Exhaust 30° Valve Clearance 0.0098 inches ( 0.25 mm) injector Pressure 1991 + 71 - 0 psi (140 + 5 = О крат) Engine Timing 17° BTDC Starting Battery 12 Volt, {-) negative ground Battery Capacity 400 — 600 Cold Cranking Amps (CCA) DC Charging Altemator 51 Amp rated, beit-drven Starting Aid Glow plugs. sheathed type Starter 12 Volt, reduction gear 92 Fuel Fuel injection Pump Nozde Fuel Filter Air cieaner Fuel Lift Pump Genera Open flow, salf priming. | No. 2 diesel où (cetane rating of 45 or higher). | in-iine plunger type (BOSCH) Throttle type. Spm-on reptaceable (FMA0Z4365)_ Replaceable paper filter cartridge. 12 volt DC 6 capacity of 5° (1.5 mm) soñd state IVE General Operating Temperature Fresh Water Pump System Capacity (Fresh Water) General Ou Filter Sump Capacity (not including filter) Operating 0d Pressure {engine hot) O Grade Fresh water-cooled block, thermostatcally- controded with heat exchanger 170-190" F(77—86" C) 8.0 US gis (7.5 Hers) LUBRICATION SYSTEM Pressure fed system. Рый flow, paper element, spañ-on type 5515 gis (5.2 Rers) 50 — 60 psi (3.54.2 kg/cm) AP Specification CF or C54 WESTERBEKE Engines & Generalors SPECIFICATION 10.0KW BTDA SPECIFICATION 8.0KW BTDA AC GENERATOR (Single Phase) Single Phase Brushiess, tour-pole, revolving field. | General - 3 Phase Brushiess sic pole, revolving field. Sealed Pre-lubricated, singis bearing design 10.0 KW - 60 Hertz lubricatad single besnng design, 12 Lead Reconnectable, single phase transionmer | 75 KW-50 Hertr reconnectable for low voltage WYE, high regulation (optional sobd-5tzte voltage | voltage Delia. Sold State voltage regulalor regulation}. wich protection circuitry Voltage 120 or 1207240 Volts - 60 Hertz Voltage - 3 Phase Low voltage WYE 208 voës 220 Volts - 50 Hartz (60 Hartz) High vañage WYE 480 volts | Voltage regulation: + 5% no load to full load. oe “0 ЧН Voltage - 3 Phase High voltage WYE 360 volts Rating (Volks AL) Amperane-3 Phase — Low voltage WYE 35 Amps 10.060 120/240 Volls 83.341.6 Amps DELTA 30 Amps 50 Hertz [1500 mm) 220 Volts 3.1 Amps 7.5XW Amperage - 3 Phase High voltage WYE A. Generator Cooling 225 - 250 dim (5.66 - 6.37 emm) | AM e Air Requirements | Engine Combustion 32 cim (806 cm) (62 Hertz! at 1800 mm MOTE: increase ar supply 15% for 50 Hertz Air Reguirements орегайоп (1508) грип) (60 Hertz) at 1800 rpm | Single Phase Brushless. four-pole. revolving field Heconnectable, Singe phase tansiormer reguiabon (optional Sobo-Stais vomege regulation). Voltage 120 or 120/240 Vois - 60 Hertz 220 Vois - 50 Hertz Voltage requiation = 5% no load to fol load | Frequency regulation: +3 Hertz [55) no load to full load Rating (Volts AL) 60 Hertz (1800 rpm) 120 Volts E5 Amps E.0KW 120/24) Volts — 6633 Amps 50 Hertz {1300 rpm) 220 Vols ZT Amps BLOW Generator Cooling 175-200 cfm (4.95 - 5.66 cmm) Air Requirements [60 Hertz) at 1800 rpm NOTE Increase air supply 12% for 50 Herz operation (1500 rpm) Engine Combusaon 32 cim (.506 cmm) Ал Requirements (60 Hertz} ai 1800 rm Engine Compartments 100-200 dm (253 - 5.55 cmm) WESTERBEKE ee 93 SPECIFICATIONS 15KW BTDC AC GENERATOR (Single Phase) Three Phase Brushiess, sor-pole, resohang field Sealed 15.0 Kw - 60 Hertr lubricaled, single bearing desgn 17 Lead 12.0 Kw - 50 Hertz reconneciable Tor low voltage WYE, high | voltage Deñz Solid state volle requistor with protection circuftry Voltage 120 ог 120/240 Volts - 60 Hertz | Voltage - 3 phase 60 Hertz. Low Voltage WYE 208 Volts | 230 Volts - 50 Hertr High Voltage WYE 480 Voits | I DELTA 240 Volts | Voltage regulation: +5% no load 10 full load. 3 Phase50 Hertz Hioh Vokage WYE 380 Volts Frequency regulation: 3 Hertz (5%) no load to full load DELTA 230 Volts Rating (Volts AC) 60 Hertz (1800 rpm) 120 Vols 125 Amps | = Low Voltage WYE 52 Amps 60 Hertz (1500 rpm) 1207240 Vols 125/62 5 Amps | ee ei High Voltage WYE 22 Amos 50 Hertz [1500 mm) — 730 Volts 60 Amps DELTA 45 Ames | A 225 - 250 cim (6.37 - 7.08 cmm) Amperage - High Voltage WYE 22 AMOS Remarements DELTA 33 (60 Hertz) at 1800 rpm MOTE: Increase air supply 15% dor 50 Hertz LA | so | operation (1500 pm). SCPE 104°F (40°C) maxımum Engine ñ Comi sion 41 cim (1.16 cmm) ir NOTE: Foster ventilation should be provided Air Requirements lo maintain génerstor (60 Hertz), at 1800 rpm | temperatures below 104 07). Generator Compartment 104°F (40°C) maximum Ambient Temperature Recommendations NOTE: Forted ventilation should be provigad lo meintar) generator temperatures below 104" (OC) SPECIFICATIONS 12.5KW BTDB AC GENERATOR (Singe Phase Single Phase Brushless, four-pode, revolving fisid Three Phase Brushiess, sor-pole, revohang field. Seed Pre-lubricated, single-bearing design. 12.5 Kw - 60 Hertz lnbricated, singie-bearing design. 12 Lead Reconnecishls single-phase transformer 8.3 Kw - 50 Hertz reconnectable for low voitage WYE, hagh requistion (optional sobid-state voltage voitage Defiz. Sod state voltage reguistor with ) protection circuitry Voltage 120 or 120/240 Vols - 60 Hertz Voltage - 3 phase 60 Hertz Low Voltage WYE 203 Volts 230 Vol - 50 Hertz. High Voltage WYE 450 Vots | Voltage regulation: 25% no inad to full load. | DELTA 205 Voliage - 3 Phase 50 Hartz High Voltage WYE 380 Volts Frequency regulation: à Hertz (5%) по icad to fui icad DELTA 730) Vols Rating (Volts AC) | | Amperage- Low Voltage WYE 43 Amps 60 Herz (1800 rpm) 120 Voits 104 Amps 3 phase 60 Hartz High Voltage WYE 18 Amps 12-5KW 120/240 Vois 10452 Amps DELTA 37 Amps 50 Hertz (1300 rpm) 230 Volts 60 Amps | Generator Cookng 200- 225 cim (6.37 - 7.08 cmm) > puse 20 A Air Requirements Engine Combustion 41 cim (1.16 emm) (60 Hartz) at 1800 rpm NOTE: increase air supply 15% for 50 Hertz Air Requirements opersbon (1500 rpm) (50 Hertz), at 1800 mm Generator Compartment 104°F (40°C) mæadmum | | Generator Compartiment = 104°F (40°C) mædmum Ambien! Temperature | | Ambient Temperature | Recommendations NOTE: Forced ventilation should be provideo | Recommendations BOTE: Forced vention should be provided ip maintain generar compartment Io Mantas) generator compattment temperatures Delow 104" (40°C). temperivres below 104F (40°C) WESTERBEKE [SV WESTERBEKE 94 Bolt or Nut Altemator Bracket Back Plate Connecting Rod Cap Coclant Pump Coolant Pump Pulley Coolant Temperature Sender Coolant Temperature Switch Crankshaft Pulley Nut Cylinder Head Bolt Delivery Valve Holder Engine Mounts Exhaust Manifold Fiywheel Boit Fuel Filter Assembiy Fuel Injection Nozzle Holder Fuel Injection Pipe Nut Fuel Leak-Off Pipe Nut Fuel Solenoid Locknut Glow Plug | Glow Plug Connection Plate Intake Manifold Main Bearing Cap Bolt Oil Filter Oil Pan Bolt Dil Pan Drain Plug Dil Pressure Sender Dil Pressure Switch Pressure Refief Valve Rear Plate Bolt (stamping) Rear Plate Bolt (standard) Retaining Nut for Delivery Valve Holder Body Rocker Cover Bolt Rocker Shaft Bracket Bolt Sliding Sleeve Shaft Special Nut for Torque Spring Set Starter B Terminal Stor Solenoid Thermostat Housing Thermoswitch ENGINE TORQUE SPECIFICATIONS Mi6 M10 M12 MAJOR BOLTS AND NUTS Width Clamp Diameter Pitch acrossflats length 1.0 14 — 15 27 — 1.25 14 87 === 19 — 1.25 19 29 1.5 21 — 15 - — 15 18 1.25 12 60 0.7 8 vom 1.25 17 Bi 15 — _— 1.25 12 25 15 22 10 — 26 1 1.5 22 33 1.25 12 16 1.25 17 28 0.75 19 = 1.25 12 40 1.25 12 581 1.25 14 295 1.0 17 — 1.25 12 — 15 36 —= 1.5 17 315 MIG TORQUE kg -m fi-lb 3.853 27-38 3348 24-35 3a5+025 7772 16+24 12-17 16+24 12-17 12+1.8 9-13 121.8 9-13 17525 12x18 +05 65 = 4 45+05 32x54 32+47 23-34 16x24 12-17 135+05 983+4 46+ 6.8 33-49 55+05 40+44 3+05 22 = 4 275+025 20+ 2 40x50 289+ 36.2 175+025 12-72 0.125—0.025 09+02 16x24 12-17 525+025 38=x2 12x01 8.7+ 0.7 28+03 203x232 40+5 29+4 12+1.8 9-13 1+02 T2+14 50+5 3a5+4 1.152015 B3+11 65+1 47+] 375+025 272 115015 83x11 15+05 114 36x06 26+4 2+05 14=4 1.1 x01 8047 4505 32+54 0.3-0.45 2-3 23x04 166 £3 STANDARD HARDWARE BOLT HEAD MARKINGS Bolt strength classes are embossed on the head of each bolt Customary (inch) bolts zre identifed by markings two 10 grade ssi (strongest). The marks correspond to two marks less than the actual grace, Le: 2 grade seven bolt will desplay five embossed maris. Metric bolt class numbers identify boîts by their strength with 10.9 the strongest Grade 8 NOTES: 1. Use the torque values listed below when specific torque values are not avaliable. 9. These torques are based on clean, dry threads. Reduce torque by 10% when engine od is used. 3.- Reduce torgues by 30% or more, when threading capscrews info aluminum. METRIC BOLT & NUT TORQUE SPECIFICATIONS | SAEGrades SA Graie6&7 | SAME Grades od Capırew Body Size Torque Torque Torque Вой Grade df | Graded’ |Блайе 8-9. Grade 10.8 [Inches) - (Thread) АН (Ми) АЗЫ (№) | PH (Ма) Dia. | Wrench Sire | FHL (Nm) | Ab (Nm) | FHb{Mm) | АН (М) | 14-20 8 (11) 10 (14) 12 (15) _ -28 10 (14) 14 (19) va 55 mm 0509 05 on 103 o hal mm ; 1 nes nen 19 25) 7 an №5 | 8mm 1585 28 150 ES O) 35-16 a1 (42) 4 M6) 44 (60) Me | 10mm зы) 465) 7500) TU -24 35 (47) ЭР MS | 13mm 785) | 10/19 18725) 509 16-14 45 (66) 5 79) 70 (25) MIO | 16mm 14 (18) 18 (25) 37 50) 55 (75) % | 55 (75) 78 (106) | - = 12-13 75 102) 85 (115) 105 (14) | |MZ| Em | zB | 289 | SE | 909) A Mid | 21mm 37 50 55 (75) 103 (140) | 151 (205) 2 5 (19) RMS wes | 2mm | Se | sas | 1975) | 27619 | ¥16- 12 110 (149) 120 155) 155 (210) = | | == "e | ne Mis | 27mm ву (10) | 18060) | 225005) | 2s | 58-11 150 (203) 167 (225) 210 (285) м0 | 30mm 1180160) | 15725) | mes | 457 (620) -18 170 231) 240 (325) ¡NO | Emm 15015) | 25(05) | 425520 | 62000) | 34-10 270 (365) 280 (380) 375 (508) | | 16 205 (400) 42071569) MO | Bw ee nd | ra 7 МТ men 1 (11 (1555) ua a ón 440 (557) es MO | 44mm 402 545) | 568 (770) | 7103 (1405) | 1571 (2130) 1-8 90 (200) BEC (ES) 310 (1234) MES | 51mm 546 (740) | 77401050) | 1500 | 2129 (2000) -W 650 (855) 0 (1347) NOS | Smm | 700650) | 992 (1345) ET 2744 (3720) GASKETS/SEALANTS Use LIQUID TEFLON for sealing pipe plugs and filings that connect coolant Où based PERMATEX #2 and its HIGH TACK equivalent are excellent all passages. Do not use tape sealants! purpose sealers. They are effective in just about any joint in contact with BOLTS & FASTENERS/ASSEMBLIES coclant, raw water, of or fuel Lightly oil head bolis and ciber fasieners assemble them. Bolts and À light coating of OIL or LIQUID TEFLON can be used on rubber gaskets caos fal penstale the water jacket should be sealed with PERMATEN 22. and O-rings. HIGH TACK. + ls да on od adapter hoses and the oil When assembiing the flywheel, coat the bolt threads with LOCTITE blue Anti-seire compounds and thread locking adhesives such as LOCTITE protect threaded components yet allows them to came apart when necessary LOCTITE offers levels of locking according to the job. Coat both surfaces of the oil pan gasket with high temp RED SILICONE sealer When installing gaskets that seal around water (coolent) passages, Cost both sides with WHITE SILICONE grease. LITHIUM based grease is waterproci, ideal for water pump bearings and stuf High-copper ADHESIVE SPRAYS are useful for holding gaskets in position Gur- ing bes. ing essembiy. Heavity où all sïiding and recprocaing components when assembling. Always Specialized gasiet seslers such as HYLOMAR work wel in apolicafions requi- — use clean engine oil! ing non-herdening properties. HYLOMAR is particiariy efectve on copper cyiinder-head gaskets as it resists fuel, O8 and water CATWESTERBEKE Engines & Generators 26 STANDARD AND METRIC CONVERSION DATA LENGTH-DISTANCE Inches (in) x 25.4 = Millimeters (mm) x .0394 = Inches Feet (ft) x .305 = Meters (m) x 3.281 = Feet Miles x 1.809 = Kilometers (km) x .0621 = Miles VOLUME Cubic Inches (in*) x 16.387 = Cubic Centimeters x .061 =in imperial Pints (IMP pt) x -568 = Liters (L) x 1.76 = IMP pt imperial Quarts (IMP gt) x 1.137 = Liters (L) x.88 = IMP qt Imperial Gallons (IMP gal) x 4.546 = Liters (L) x .22 = ¡MP gal Imperial Quarts (IMP gt) x 1.201 = US Quarts (US qt) x .633 = IMP qt Imperial Gallons (IMP gal) x 1.201 = US Gallons (US gal) x .833 = IMP gal Fluid Ounces x 29.573 = Milliiiters x .034 = Ounces US Pints (US pt) x .473 = Liters(L) x 2.113 = Pints US Quarts {US gt) x .946 = Liters (L) x 1.057 = Quarts US Gallons (US gal) x 3.785 = Liters (L) x .264 = Gallons MASS-WEIGHT Ounces (oz) x 28.35 = Grams (g) x .035 = Ounces Pounds (Ib) x .454 = Kilograms (kg) x 2.205 = Pounds Pounds Per Sg In (psi) x 6.895 = Kilopascals (kPa) x 145 = psi inches of Mercury (Hg) x .4912 = psi x 2.036 = Hg Inches of Mercury (Hg) x 3.377 = Kilopascals (kPa) x 2961 = Hg Inches of Water (H:0) x 07355 = inches of Mercury x 13.783 = H:0 inches of Water (H:0) x .03613 = psi x 27.684 = H:0 inches of Water (H:0) x 248 = Kilopascals (kPa) х 4.026 = №0 TORQUE Pounds-Force Inches (in-ib) x .113 = Newton Meters (Nm) x 8.83 =in-ib Pounds-Force Feet (ft-Ib} x 1.356 = Newton Meters (Nm) x 738 = fib VELOCITY Miles Per Hour (MPH) x 1.609 = Kilometers Per Hour (KPH) x .621 = MPH POWER Horsepower (Hp) x .745 = Kilowatts (Kw) x 1.34 = MPH FUEL CONSUMPTION Miles Per Hour IMP (MPG) x .354 = Kilometers Per Liter (Km/L) Kilometers Per Liter (Km/L) x 2.352 = IMP MPG Miles Per Gallons US (MPG) x .425 = Kilometers Per Liter (KmJL) Kilometers Per Liter (Km/L) x 2.352 = US MPG TEMPERATURE Degree Fahrenheit (°F) = (°C X 1.8) + 32 Degree Celsius (°C) = (°F - 32) x 56 JWESTEREERS of SUGGESTED SPARE PARTS CONTACT YOUR WESTERBEKE DEALER FOR SUGGESTIONS AND ADDITIONAL INFORMATION WESTERBEKE RECOMMENDS CARRYING ENOUGH SPARE у Е > AS is + (INA CANVAS ENGINE OIL (YOUR BRAND) FOR AN OIL CHANGE $ AND A GALLON OF PREMIXED COOLANT. SPARE PARTS KITS WESTERBEKE also offers two Spare Parts Kits, [ KIT B each packaged in à rugged hinged toolbox. Kit “A” includes the basic spares. DRIVE BELTS Kit “B™ is more extensive OIL FILTER KIT À FUEL FILTER INJECTOR DRIVE BELTS OVERHAUL GASKET KIT OIL FILTER AIR FILTER FUEL FILTER GLOW PLUG FUEL SYSTEM HARDWARE KIT FUEL SYSTEM HARDWARE KIT FUEL PUMP INLET FILTER FUEL PUMP INLET FILTER
advertisement
* Your assessment is very important for improving the workof artificial intelligence, which forms the content of this project