Danfoss 300 A Current Sensor Kit, D1h/D3h/D5h/D6 Installation Guide
Add to My manuals10 Pages
Danfoss VLT HVAC Drive FC 102 is a versatile frequency converter designed for a wide range of HVAC applications. With its advanced features and robust construction, it offers precise control, energy savings, and reliable operation. The compact design and easy-to-use interface make it suitable for various heating, ventilation, and air conditioning systems. From fan and pump control to compressor applications, the VLT HVAC Drive FC 102 provides efficient and flexible solutions.
advertisement
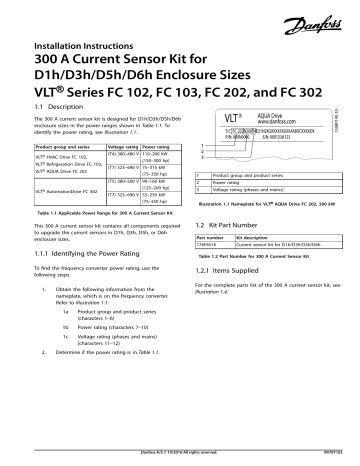
Installation Instructions
300 A Current Sensor Kit for
D1h/D3h/D5h/D6h Enclosure Sizes
VLT
®
Series FC 102, FC 103, FC 202, and FC 302
1.1 Description
The 300 A current sensor kit is designed for D1h/D3h/D5h/D6h enclosure sizes in the power ranges shown in
identify the power rating, see
Product group and series
VLT
®
HVAC Drive FC 102,
VLT
®
Refrigeration Drive FC 103,
VLT
®
AQUA Drive FC 202
VLT
®
AutomationDrive FC 302
Voltage rating Power rating
(T4) 380–480 V 110–200 kW
(150–300 hp)
(T7) 525–690 V 75–315 kW
(75–350 hp)
(T5) 380–500 V 90–160 kW
(125–200 hp)
(T7) 525–690 V 55–250 kW
(75–350 hp)
Table 1.1 Applicable Power Range for 300 A Current Sensor Kit
This 300 A current sensor kit contains all components required to upgrade the current sensors in D1h, D3h, D5h, or D6h enclosure sizes.
1.1.1 Identifying the Power Rating
To find the frequency converter power rating, use the following steps.
1
2
3
Product group and product series
Power rating
Voltage rating (phases and mains)
Illustration 1.1 Nameplate for VLT
®
AQUA Drive FC 202, 200 kW
Part number
176F6516
Kit description
Current sensor kit for D1h/D3h/D5h/D6h
Table 1.2 Part Number for 300 A Current Sensor Kit
1.2.1 Items Supplied
For the complete parts list of the 300 A current sensor kit, see
.
1.
2.
Obtain the following information from the nameplate, which is on the frequency converter.
Refer to
.
1a Product group and product series
(characters 1–6)
1b Power rating (characters 7–10)
1c Voltage rating (phases and mains)
(characters 11–12)
Determine if the power rating is in
Danfoss A/S © 10/2016 All rights reserved.
MI70Y102
Installation Instructions
CAUTION
TRAINING REQUIRED
300 A Current Sensor Kit for
D1h/D3h/D5h/D6h Enclosure Sizes
VLT
®
Series FC 102, FC 103, FC 202, and FC 302
Only certified technicians trained by Danfoss are allowed to replace the parts described in these installation instructions.
Installation work done by non-qualified personnel can result in personal injury or equipment damage. Make sure to read and save these instructions.
WARNING
ELECTRICAL SHOCK HAZARD
VLT
®
frequency converters contain dangerous voltages when connected to mains voltage. Improper installation, and installing or servicing with power connected, can cause death, serious injury, or equipment failure.
To avoid death, serious injury, or equipment failure:
• Only use qualified electricians for the installation.
• Disconnect the frequency converter from all power sources before installation or service.
• Treat the frequency converter as live whenever the mains voltage is connected.
• Follow the guidelines in these instructions and local electrical safety codes.
WARNING
DISCHARGE TIME
The frequency converter contains DC-link capacitors, which can remain charged even when the unit is off. High voltage can be present even when the warning indicator lights are off. Failure to wait a minimum of 20 minutes after power is removed before performing service work can result in death or serious injury.
1.
2.
3.
4.
5.
Stop the motor.
Disconnect AC mains and remote DC-link supplies, including battery back-ups, UPS, and DC-link connections to other frequency converters.
Disconnect or lock PM motor.
Wait 20 minutes for the capacitors to discharge.
To verify full discharge, measure the voltage level.
NOTICE
The current sensor kit includes an extra set of fasteners in case any fasteners are missing or unusable. To make the disassembly/reassembly process easier, use these general guidelines:
1.
2.
3.
4.
5.
Follow the disassembly instructions for each component.
Place the component along with the removed fasteners together in one place.
Replace old component with the new component provided in the kit.
If any fasteners are stripped or lost, replace with similar fastener from the kit.
Follow the installation instructions for replacing and securing each component.
2 Danfoss A/S © 10/2016 All rights reserved.
MI70Y102
Installation Instructions
1.4.1 Removing AC Input Busbars
300 A Current Sensor Kit for
D1h/D3h/D5h/D6h Enclosure Sizes
VLT
®
Series FC 102, FC 103, FC 202, and FC 302
Optional components mounted on the input terminal plate can result in differing configurations. These options include an
RFI filter and AC fuses. See Illustration 1.2
procedure based on the options present in the unit.
1 Input busbar
2 RFI filter (optional)
3 AC fuse (optional)
4 Terminal label
5 Mains input terminal
6 Power terminal mounting plate
7 Retaining nut
8 EMC shield
9 Output motor terminal
10 Mixing fan
Illustration 1.2 AC Input Busbars with Optional RFI Filter and AC Fuses
No options
1.
Remove the air baffle by removing 4 screws (T25), 1 from each corner.
2.
Remove 3 nuts (13 mm) at the top of the input busbars, 1 per busbar.
3.
Remove 6 nuts (13 mm) at the bottom of the input busbars, 2 per busbar.
Lift the input busbars from the unit.
4.
AC fuses only
1.
Remove the air baffle by removing 4 screws (T25), 1 from each corner.
2.
Remove the 3 AC fuses by removing 6 nuts (13 mm),
1 at each end of each fuse.
3.
Remove 3 nuts (13 mm) at the top of the busbars, 1 per phase.
Lift the input busbars from the unit.
4.
RFI filter only
1.
Remove the air baffle by removing 4 screws (T25), 1 from each corner.
2.
Remove 3 nuts (13 mm) at the top of the RFI filter, 1 per bus phase.
3.
4.
Remove 6 nuts (13 mm) at the bottom of the RFI filter, 2 per phase.
Remove 4 mounting screws (T20) connecting the RFI filter to the side channels of the frequency converter.
5.
AC fuses and RFI filter
1.
Remove the air baffle by removing 4 screws (T25), 1 from each corner.
2.
Remove the RFI filter and unplug the RFI cable from the MK100 connector on the RFI card.
3.
Remove AC fuses by removing 6 nuts (13 mm), 1 at each end of each fuse.
Remove 3 nuts (13 mm) at the top of the RFI filter, 1 per phase.
4.
5.
Remove 4 screws (T20) connecting the RFI filter to the side channels of the frequency converter.
Remove the RFI filter and unplug the RFI cable from
MK100 on the RFI card.
1.4.2 Removing Input Terminal Block
4.
5.
1.
2.
3.
Disconnect the input power wiring.
Remove 2 screws (T25) at the bottom of the terminal block.
Remove 1 screw (T25) at the bottom of the EMC shield.
Release the current sensor wiring from retaining clips.
To remove the terminal, slide the terminal down to disengage it from the metal clips holding it in place.
MI70Y102 Danfoss A/S © 10/2016 All rights reserved.
3
Installation Instructions
1.4.3 Removing EMC Partition
1.
2.
300 A Current Sensor Kit for
D1h/D3h/D5h/D6h Enclosure Sizes
VLT
®
Series FC 102, FC 103, FC 202, and FC 302
1.4.6 Removing Power Terminal Mounting
Plate
Remove 1 screw (T25) at the top of the EMC shield.
Remove the EMC shield from the unit.
1.
2.
1.4.4 Removing Brake Terminal (optional)
1.
2.
3.
4.
Disconnect the brake wiring, if any.
To detach the R (+) terminal, remove 1 screw (T25) at the terminal block, and 1 additional screw (T40).
To detach the R (-) terminal, remove 1 screw (T25) at the terminal block, and 1 additional nut (13 mm).
To detach the brake terminal block, remove 2 nuts
(13 mm).
3.
4.
Remove the 4 retaining screws (T20) from the plate.
Remove the 3 nuts (M8) from the bottom edge of the plate.
Unplug the current sensor cables.
While pulling the plate up, unplug the mixing fan cable, located under the mounting plate. The mixing fan can remain in place in the mounting plate.
1.4.5 Removing Output Terminal Block
1.
2.
3.
4.
5.
6.
7.
Disconnect motor wiring.
To detach the U output busbar, remove 1 screw (T25) from the busbar center and 1 bolt (T40) at the current sensor end.
To detach the V output busbar, remove 1 screw (T25) from the busbar center and 1 bolt (T40).
To detach the W output busbar, remove 1 screw
(T25) from the busbar center and 1 bolt (T40).
Remove the 3 cylindrical busbars from the current sensors.
Remove the 2 screws (T25) at the bottom of the terminal block.
To remove the terminal, slide the terminal down to disengage it from the metal clips holding it in place.
1 Current sensor
2 Retaining screw (T20)
5 Mixing fan
6 Mixing fan slot
3 Power terminal mounting plate 7 Nut (8 mm)
4 Mixing fan cable – –
Illustration 1.3 Power Terminal Mounting Plate
4 Danfoss A/S © 10/2016 All rights reserved.
MI70Y102
Installation Instructions
300 A Current Sensor Kit for
D1h/D3h/D5h/D6h Enclosure Sizes
VLT
®
Series FC 102, FC 103, FC 202, and FC 302
7
8
5
6
3
4
1
2
M10x30 hex screw with captive washer (Qty 6)
M10 hex nut (Qty 6)
Input label
Input/mains terminal block
M5x12 machine screw with captive washer (Qty 11)
Partition
M5x16 Torx screw (Qty 3)
Output label
9 Output/motor terminal block
10 Input terminal mounting plate (Qty 2)
11 Mixing fan
12
13
14
15
16
17
18
19
–
–
–
M5x11 thread-cutting screw (Qty 4)
M8 hex nut with captive washer (Qty 3)
Busbar insulation sleeve
Motor busbar, U
Motor busbar, V
Motor busbar, W
300 A current sensor
M4x8 Torx screw (Qty 6)
M6x90 Torx screw (Qty 3) (not shown)
IGBT busbars, U,V,W (not shown)
Wire harness (See
.)
Illustration 1.4 Exploded View and Parts List of 300 A Current Sensor Kit
MI70Y102 Danfoss A/S © 10/2016 All rights reserved.
5
Installation Instructions
1.5.1 Installing Current Sensors
NOTICE
TERMINAL MOUNTING PLATE
There are 2 input terminal mounting plates included in the kit (1 for IP20 and 1 for IP21/IP54). Use the one that fits the enclosure size.
1.
2.
3.
4.
300 A Current Sensor Kit for
D1h/D3h/D5h/D6h Enclosure Sizes
VLT
®
Series FC 102, FC 103, FC 202, and FC 302
1.5.2 Installing Power Terminal Mounting
Plate
Align the current sensors so that the cable connectors face the back of the unit.
Attach each of the 3 new current sensors to the power terminal mounting plate using 2 screws
(M4x8) per sensor. Torque to 2.8 Nm (24 in-lb).
Connect the wire harness to the current sensors.
Run the wire harness through the wire guides.
1.
2.
3.
4.
5.
6.
7.
8.
Unplug the old wire harness from the power card and discard the harness.
Insert the power terminal mounting plate into the unit. To ease installation, insert the bottom of the plate near the bottom of the frequency converter.
Secure the plate with 4 thread-cutting screws
(M5x11). Torque to 1.7 Nm (15 in-lb).
Connect the top of the wire harness to the power
.
Connect the bottom of the wire harness to the mixing fan.
Insert the mixing fan into the fan housing, with the label facing the open side of the housing.
With the fan label facing up, snap the mixing fan assembly into the plate opening. When properly seated, the fan assembly is level with the plate.
Install 3 hex nuts with captive washer (M8) onto the power terminal mounting plate. Torque to 19 Nm
(169 in-lb).
6
1 Wire harness (current sensor)
2 Current sensor
3 Power terminal mounting plate
4 Wire harness (fan)
Illustration 1.5 Wire Harness Attached to Current Sensors on
Power Terminal Mounting Plate
Danfoss A/S © 10/2016 All rights reserved.
MI70Y102
Installation Instructions
300 A Current Sensor Kit for
D1h/D3h/D5h/D6h Enclosure Sizes
VLT
®
Series FC 102, FC 103, FC 202, and FC 302
3
4
1
2
Power card
Power card connector to current sensor wire harness
Wire harness (current sensor)
Current sensor
5
6
7
8
Power terminal mounting plate
Power card connector to RFI filter
Power card connector to fan wire harness
Wire harness (fan)
Illustration 1.6 Power Terminal Mounting Plate with Current Sensors and Wire Harness
MI70Y102 Danfoss A/S © 10/2016 All rights reserved.
7
8
Installation Instructions
300 A Current Sensor Kit for
D1h/D3h/D5h/D6h Enclosure Sizes
VLT
®
Series FC 102, FC 103, FC 202, and FC 302
1.5.3 Installing Output Terminal Block 1.5.7 Installing AC Input Busbars
1.
2.
3.
4.
5.
6.
7.
1.
2.
3.
4.
Place the output terminal label in its original position above the terminal connections U (T1), V (T2), W (T3).
Push the output terminal block up against the metal clips on the power terminal mounting plate until they engage.
Secure with 2 machine screws (M5x12) at the bottom of the terminal block. Torque to 2.3 Nm (20 in-lb).
Roll up the insulator sheet and insert it into the middle of each current sensor.
Insert the cylindrical busbar inside the insulator sheet.
Slide the insulation sleeve over the U-phase busbar.
Secure each motor busbar with 1 Torx screw (M5x16) near the current sensor and 1 thread-forming screw in the busbar center. Torque the Torx screw to 2.3
Nm (20 in-lb) and the thread-forming screw to
4.0 Nm (35 in-lb).
1.5.4 Installing Brake Terminal (optional)
Install the optional brake terminal block using 2 nuts
(M8). Torque to 9.6 Nm (85 in-lb).
Install the R (-) terminal using 1 thread-forming screw
(M4x8) at the terminal block, and 1 nut (M8). Torque the thread-forming screw to 2.8 Nm (24 in-lb) and the nut to 9.6 Nm (85 in-lb).
Install the R (+) terminal using 1 thread-forming screw (M4x8) at the terminal block, and 1 screw
(T40). Torque the thread-forming screw to 2.8 Nm
(24 in-lb) and the T40 screw to 9.6 Nm (85 in-lb).
Connect the brake wiring.
1.5.5 Installing Partition with EMC Shield
1.
2.
Install the partition to the left of the motor terminal block.
Secure with 2 machine screws (M5x12). Torque to
2.3 Nm (20 in-lb).
Optional components mounted on the input terminal plate can result in differing configurations. These options include an
RFI filter and AC fuses. See Illustration 1.2
procedure based on the options present in the unit.
No options
1.
Attach the busbars.
2.
Secure each busbar with 1 nut (M8) at the top of the busbar and 2 nuts (M8) at the bottom of the busbar.
Torque to 9.6 Nm (85 in-lb).
AC fuses only
1.
Secure each busbar at the top with 1 nut (M8).
Torque to 9.6 Nm (85 in-lb).
2.
Install the AC fuses using 6 nuts (M8), 1 at each end of each fuse. Torque to 9.6 Nm (85 in-lb).
RFI filter only
1.
Connect the RFI filter cable from MK100 on the RFI card to the RFI filter.
2.
Attach the RFI filter to the side channels of the frequency converter with 4 thread-cutting screws
(T20). Torque to 5.7 Nm (50 in-lb).
3.
4.
Secure the top of the RFI filter using 3 nuts (M8), 1 per phase. Torque to 9.6 Nm (85 in-lb).
Secure the bottom of the RFI filter using 6 nuts (M8),
2 per phase. Torque to 9.6 Nm (85 in-lb).
AC fuses and RFI filter
1.
Connect the RFI filter cable from MK100 on the RFI card to the RFI filter.
2.
Attach the RFI filter to the side channels of the frequency converter with 4 thread-cutting screws
(T20). Torque to 5.7 Nm (50 in-lb).
3.
4.
Secure the RFI filter using 3 nuts (M8) at the top of the RFI filter, 1 per phase. Torque to 9.6 Nm (85 inlb).
Install AC fuses using 6 nuts (M8), 1 at each end of each fuse. Torque to 9.6 Nm (85 in-lb).
1.5.6 Installing Input Terminal Block
1.
2.
3.
Place the input terminal label in its original position above the terminal connections R (L1), S (L2), T (L3).
Push the input terminal block up against the metal clips on the power terminal mounting plate until they engage.
Secure with 2 machine screws (M5x12) at the bottom of the terminal block. Torque to 2.3 Nm (20 in-lb).
1.5.8 Reconnecting the Mains and Motor
Wiring
1.
2.
3.
4.
Reconnect the motor wiring to the U, V, and W terminals.
If a brake terminal is present, reconnect the brake wiring.
Reconnect the mains wiring to the R, S, and T terminals.
Install the air baffle using 4 screws (T25) and 2 nuts
(M8). Torque to 2.3 Nm (20 in-lb).
Danfoss A/S © 10/2016 All rights reserved.
MI70Y102
Installation Instructions
300 A Current Sensor Kit for
D1h/D3h/D5h/D6h Enclosure Sizes
VLT
®
Series FC 102, FC 103, FC 202, and FC 302
MI70Y102 Danfoss A/S © 10/2016 All rights reserved.
9
Danfoss can accept no responsibility for possible errors in catalogues, brochures and other printed material. Danfoss reserves the right to alter its products without notice. This also applies to products already on order provided that such alterations can be made without subsequential changes being necessary in specifications already agreed. All trademarks in this material are property of the respective companies. Danfoss and the Danfoss logotype are trademarks of Danfoss A/S. All rights reserved.
Danfoss A/S
Ulsnaes 1
DK-6300 Graasten vlt-drives.danfoss.com
130R0721 10/2016 MI70Y102 *MI70Y102*
advertisement
Related manuals
advertisement