advertisement
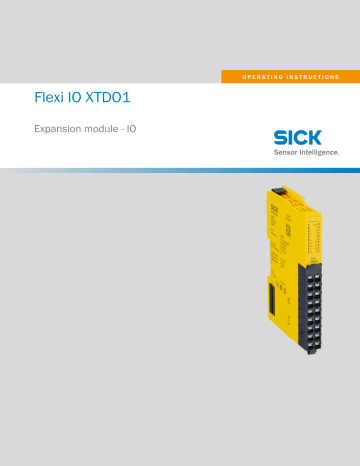
Flexi IO XTDO1
Expansion module - IO
O P E R A T I N G I N S T R U C T I O N S
Described product
Flexi IO XTDO1
Manufacturer
SICK AG
Erwin-Sick-Str. 1
79183 Waldkirch
Germany
Legal information
This work is protected by copyright. Any rights derived from the copyright shall be reserved for SICK AG. Reproduction of this document or parts of this document is only permissible within the limits of the legal determination of Copyright Law. Any modi‐ fication, abridgment or translation of this document is prohibited without the express written permission of SICK AG.
The trademarks stated in this document are the property of their respective owner.
© SICK AG. All rights reserved.
Original document
This document is an original document of SICK AG.
2 O P E R A T I N G I N S T R U C T I O N S | Flexi IO XTDO1 8024583/2020-11-10 | SICK
Subject to change without notice
CONTENTS
Contents
8024583/2020-11-10 | SICK
Subject to change without notice
1
About this document........................................................................
1.1
Purpose of this document........................................................................
1.2
1.3
Target groups and structure of these operating instructions................
1.4
1.5
Symbols and document conventions......................................................
2
Safety information............................................................................
2.1
General safety notes................................................................................
2.2
2.3
2.4
Requirements for the qualification of personnel....................................
3
Product description........................................................................... 10
3.1
Configuration of the safety controller......................................................
3.2
Overview of the module............................................................................
3.3
Configuration and function......................................................................
3.4
4
Project planning................................................................................ 13
4.1
Manufacturer of the machine..................................................................
4.2
Operating entity of the machine..............................................................
4.3
4.4
4.4.1
4.4.2
Internal circuitry.......................................................................
Safety outputs..........................................................................
4.5
5
5.1
5.2
Mounting procedure.................................................................................
5.3
6
Electrical installation........................................................................ 19
6.1
6.2
6.3
6.3.1
Coding front connector and module.......................................
7
Commissioning.................................................................................. 23
7.1
Check during commissioning and modifications....................................
8
8.1
Regular thorough check...........................................................................
O P E R A T I N G I N S T R U C T I O N S | Flexi IO XTDO1 3
CONTENTS
9
Maintenance...................................................................................... 25
9.1
Regular thorough check...........................................................................
10
Troubleshooting................................................................................. 26
11
Decommissioning............................................................................. 31
12
13
Ordering information........................................................................ 37
13.2 Ordering information for main module....................................................
13.3 Ordering information for expansion module...........................................
13.4 Ordering information for accessories......................................................
14
14.1 Compliance with EU directives.................................................................
15
16
4 O P E R A T I N G I N S T R U C T I O N S | Flexi IO XTDO1 8024583/2020-11-10 | SICK
Subject to change without notice
1
1.1
1.2
1.3
ABOUT THIS DOCUMENT
1
About this document
Purpose of this document
These operating instructions contain the information required during the life cycle of the safety controller.
Operating instructions of the safety controller must be made available to all people who work with the device.
Scope
These operating instructions apply to the Flexi Compact safety controller.
This document is included with the following SICK part numbers (this document in all available language versions):
• 8024570
Furthermore, the following documents contain information about the safety controller:
Table 1: Available documents
Document
Operating instructions
Operating instructions
Operating instructions
Operating instructions
Operating instructions
Operating instructions
Competence brochure
Title
FLX3-XTDI1 expansion module for safety controllers
FLX3-XTDO1 expansion mod‐ ule for safety controllers
FLX0-GPNT1 expansion mod‐ ule for safety controllers
FLX0-GETC1 expansion mod‐ ule for safety controllers
Flexi Loop Safe Series Con‐ nection Hardware
Flexi Loop in the Safety
Designer Software
Guide for Safe Machinery
Part number
8024571
8024570
8024567
8024566
8015834
8018174
8008007
Target groups and structure of these operating instructions
These operating instructions are intended for the following target groups: project devel‐ opers (planners, developers, designers), installers, electricians, safety experts (such as
CE authorized representatives, compliance officers, people who test and approve the application), operators, and maintenance personnel.
These operating instructions are organized by the life phases of the device: project planning, mounting, electrical installation, commissioning, operation and maintenance.
The table below shows the target groups and how – for many applications – these are typically divided up between the manufacturer and the entity operating the machine in which the device is to be integrated:
8024583/2020-11-10 | SICK
Subject to change without notice
O P E R A T I N G I N S T R U C T I O N S | Flexi IO XTDO1 5
1
ABOUT THIS DOCUMENT
1.4
1.5
Area of responsibility
Manufacturer
Operating entity
Target group
Project developers
(planners, developers, designers)
Installers
Electricians
Safety experts
Operators
Maintenance staff
Specific chapters of these operating instruc‐ tions
1)
,
,
,
,
,
,
Ordering information , page 37
1) Chapters not listed here are intended for all target groups. All target groups must follow all of the safety and warning instructions in all chapters of the operating instructions!
In other applications, the operating organization is also the manufacturer of the equip‐ ment with the corresponding allocation of the target groups.
Further information
www.sick.com
The following information is available via the Internet:
•
This document in other languages
•
Data sheets and application examples
•
CAD files and dimensional drawings
•
Certificates (such as the EU declaration of conformity)
•
Guide for Safe Machinery. Six steps to a safe machine
•
Safety Designer (software for configuring safety solutions made by SICK AG)
Symbols and document conventions
The following symbols and conventions are used in this document:
Safety notes and other notes
DANGER
Indicates a situation presenting imminent danger, which will lead to death or serious injuries if not prevented.
WARNING
Indicates a situation presenting possible danger, which may lead to death or serious injuries if not prevented.
CAUTION
Indicates a situation presenting possible danger, which may lead to moderate or minor injuries if not prevented.
NOTICE
Indicates a situation presenting possible danger, which may lead to property damage if not prevented.
6 O P E R A T I N G I N S T R U C T I O N S | Flexi IO XTDO1 8024583/2020-11-10 | SICK
Subject to change without notice
ABOUT THIS DOCUMENT
1
NOTE
Indicates useful tips and recommendations.
Instructions to action
b
The arrow denotes instructions to action.
1.
The sequence of instructions for action is numbered.
2.
Follow the order in which the numbered instructions are given.
✓
The check mark denotes the result of an instruction.
8024583/2020-11-10 | SICK
Subject to change without notice
O P E R A T I N G I N S T R U C T I O N S | Flexi IO XTDO1 7
2
SAFETY INFORMATION
2
2.1
2.2
2.3
2.4
Safety information
General safety notes
This chapter contains general safety information about the safety controller.
Further safety information is provided in the respective chapters to cover the specific situations in which the product may be used.
DANGER
If the device is not integrated in the way intended by the manufacturer, the protective function of the device can be impaired. The dangerous state may be ended too late.
b
Plan the integration of the safety component in accordance with the machine requirements,
see "Project planning", page 13
.
Intended use
The Flexi Compact safety controller is a freely configurable control for safety applica‐ tions. Sensors and switching elements (e.g. light curtains, laser scanners, switches, sensors, encoders, emergency stop pushbuttons) are connected to the safety controller and are linked logically. The corresponding actuators of the machines or systems can be switched off safely via the switching outputs of the safety controller.
Incorrect use, improper modification or manipulation of the module will invalidate any warranty from SICK; in addition, any responsibility and liability of SICK AG for damage and secondary damage caused by this is excluded.
The safety controller system is only suitable for use in industrial environments.
Improper use
Among others, the safety controller is not suitable for the following applications:
• Outdoors
• Underwater
• In explosion-hazardous areas
• In residential areas
Requirements for the qualification of personnel
The protective device must be configured, installed, connected, commissioned, and serviced by qualified safety personnel only.
Project planning
For project planning, a person is considered competent when he/she has expertise and experience in the selection and use of protective devices on machines and is familiar with the relevant technical rules and national work safety regulations.
Mechanical mounting, electrical installation, and commissioning
For the task, a person is considered qualified when he/she has the expertise and experience in the relevant field and is sufficiently familiar with the application of the protective device on the machine to be able to assess whether it is in an operationally safe state.
8 O P E R A T I N G I N S T R U C T I O N S | Flexi IO XTDO1 8024583/2020-11-10 | SICK
Subject to change without notice
SAFETY INFORMATION
2
Operation and maintenance
For operation and maintenance, a person is considered competent when he/she has the expertise and experience in the relevant field and is sufficiently familiar with the application of the protective device on the machine and has been instructed by the machine operator in its operation.
8024583/2020-11-10 | SICK
Subject to change without notice
O P E R A T I N G I N S T R U C T I O N S | Flexi IO XTDO1 9
3
PRODUCT DESCRIPTION
3
3.1
Product description
Configuration of the safety controller
Configuration of the safety controller
A safety controller comprises the following components:
• A main module
• Up to 12 optional expansion modules (excluding maximum 1 gateway)
CV
I1
I3
I5
I7
I9
I11
X1
X3
I2
I4
I6
I8
I10
I12
X2
X4
I13
I15
I17
PW
R
I14
I16
I18
I19
X5
X7
Q1
I20
X6
X8
Q2
Q4
A2
Q3
A1
I1
I3
I5
I7
Q1
Q3
Q5
Q7
A1
PW
R
I2
I4
I6
I8
Q2
Q4
Q6
Q8
A2
Q1
Q3
Q5
Q7
A1
I1
I3
I5
I7 Q2
Q4
Q6
Q8
A2
PW
R
I2
I4
I6
I8
Q1
Q3
Q5
Q7
A1
I1
I3
I5
I7
R
PW
I2
I4
I6
I8
Q2
Q4
Q6
Q8
A2
I1
I3
I5
I7
Q1
Q3
Q5
Q7
A1
PW
R
Q2
Q4
Q6
Q8
A2
I4
I6
I8
I3
I5
I7
Q1
Q3
Q5
Q7
A1
I1
R
PW
I2
I4
Q2
Q4
I6
I8
Q6
Q8
A2
I1
I3
I5
I7
Q1
Q3
PW
R
I2
I4
I6
I8
Q5
Q7
A1
Q2
Q4
Q6
Q8
A2
Q1
Q3
Q5
Q7
A1
I1
I3
I5
I7
PW
R
I2
I4
I6
I8
Q2
Q4
Q6
Q8
A2
Q1
Q3
Q5
Q7
A1
I1
I3
I5
I7
PW
R
I2
I4
I6
I8
Q2
Q4
Q6
Q8
A2
I1
I3
I5
I7
Q1
Q3
Q5
Q7
A1
R
PW
I2
I4
I6
I8
Q2
Q4
Q6
Q8
A2
I5
I7
Q1
Q3
I1
I3
R
PW
I2
I4
I6
I8
Q2
Q4
Q5
Q7
A1
Q6
Q8
A2
I3
I5
I7
Q1
Q3
Q5
Q7
A1
I1
R
PW
I2
I4
Q2
Q4
I6
I8
Q6
Q8
A2
3
2
1
1
2
3
Figure 1: Example maximum configuration
Main module
Expansion module - gateway
IO expansion module
Complementary information
• The gateway and IO expansion modules can be arranged arbitrarily.
10 O P E R A T I N G I N S T R U C T I O N S | Flexi IO XTDO1 8024583/2020-11-10 | SICK
Subject to change without notice
PRODUCT DESCRIPTION
3
3.2
Overview of the module
1
I1
I3
I5
I7
Q1
Q3
Q5
Q7
A1
PW
R
Q2
Q4
Q6
Q8
A2
I4
I6
I8
2
3
4
3.3
8024583/2020-11-10 | SICK
Subject to change without notice
5
1
2
3
4
5
Figure 2: FLX3-XTDO1 IO expansion module
Release element of the module
Status indicators (LEDs)
Front connector unlocking
Front connector with terminals
Backplane bus
Configuration and function
Prerequisites
• The module can only be operated with a main module.
Configuration
Table 2: Interfaces of the module
Description
Safety capable inputs
Safety capable outputs
RJ45 female connector
Quantity
8
8
Function
The module is a safe digital input/output expansion module.
The module offers the following functions:
• Monitoring of the connected safety devices
• Switching of the connected safety devices
• Special IO functions (e.g., fast shut off)
Complementary information
•
Safety outputs have test pulses for detecting short-circuits in the wiring.
•
Voltage is supplied to the module via the backplane bus. Communication with the main module of the safety controller also occurs via the backplane bus.
•
Voltage is supplied directly to the safety outputs Q via A1 / A2 on the module.
O P E R A T I N G I N S T R U C T I O N S | Flexi IO XTDO1 11
3
PRODUCT DESCRIPTION
3.4
Status indicators
Status indicators
I1
I3
I5
I7
Q1
Q3
PW
R
I2
I4
I6
I8
Q5
Q7
A1
Q2
Q4
Q6
Q8
A2
I1
I3
I5
I7
Q1
Q3
PWR
I2
I4
I6
I8
Q2
Q4
Q5 Q6
Q7 Q8
A1 A2
XTDO1
1085354
Figure 3: LEDs for indicating the status
The arrangement of the status indicators corresponds to the arrangement of the termi‐ nals.
1
Status indicator
Table 3: Status indicator
Labeling
PWR
I1 … I8
Q1 … Q8
Color
Green/Red
Green
Green
Function
Device status 1
Safety capable input 1 … 8
Safety capable output 1 … 8
Does not indicate whether the local auxiliary supply at A1 and A2 for the safety outputs is currently within the supply voltage range.
Further topics
•
12 O P E R A T I N G I N S T R U C T I O N S | Flexi IO XTDO1 8024583/2020-11-10 | SICK
Subject to change without notice
4
4.1
4.2
4.3
PROJECT PLANNING
4
Project planning
Manufacturer of the machine
DANGER
Failure to comply with manufacturer’s obligations
Hazard due to lack of effectiveness of the protective device b
Carry out a risk assessment before using the safety controller.
b
Do not manipulate, open or modify the components of the safety controller.
b
Make sure the safety controller is only repaired by the manufacturer or by some‐ one authorized by the manufacturer. Improper repair can lead to a loss of the protective function.
Operating entity of the machine
DANGER
Failure to observe operator obligations
Hazard due to lack of effectiveness of the protective device b
Changes to the machine and changes to the hardware or the logic programming of the safety controller necessitate a new risk assessment. The results of this risk assessment may require the entity operating the machine to meet the obligations of a manufacturer.
b
Apart from the procedures described in this document, the components of the safety controller must not be opened or modified.
b
Do not carry out any repair work on components. Improper repair of the safety controller can lead to a loss of the protective function.
Design
Mounting
• Environment meets the requirements of IP54 or higher, e.g., IP54 control cabinet.
• Mounting on a 35 mm × 7.5 mm mounting rail in accordance with IEC 60715.
• The mounting rail is connected to the functional earth.
• Mounting rail is mounted on a mounting plate.
• Mounting plate is connected to functional earth.
• Mounting in a vertical orientation (on a horizontal mounting rail).
• Take suitable ESD protection measures.
Air circulation
To ensure sufficient air circulation and cooling, sufficient distance must be kept in the control cabinet above and below the module.
Provide an adequate clearance in front of the module (front side) for the connected cables.
8024583/2020-11-10 | SICK
Subject to change without notice
O P E R A T I N G I N S T R U C T I O N S | Flexi IO XTDO1 13
4
PROJECT PLANNING
≥ 25
Figure 4: Clearances for adequate air circulation
Required distance:
•
Above and below the module: ≥ 30 mm
•
In front of the module: ≥ 25 mm
14 O P E R A T I N G I N S T R U C T I O N S | Flexi IO XTDO1 8024583/2020-11-10 | SICK
Subject to change without notice
4.4
4.4.1
Electrical integration
Internal circuitry
PROJECT PLANNING
4
4.4.2
Figure 5: Internal circuitry XTDO
Safety outputs
Important information
WARNING
Ineffectiveness of the protective device
In the event of a fault, a single safety output (Q) can switch off after a delay or briefly switch to High. The response time increases depending on the configuration of the output. The dangerous state may not be stopped or not be stopped in a timely manner in the event of non-compliance.
b
Take the increased response time into consideration in the risk analysis.
b
Take the possible reduced safety level into consideration in the risk analysis.
Fault detection by testing
The following faults can be detected by testing an element:
•
Short-circuits between any of the safety outputs.
You can detect a cross-circuit between the safety outputs of 12 sequential mod‐ ules.
•
Short circuits to 24 V DC (to High) on safety outputs.
•
Actuator wiring short-circuits to 24 V.
8024583/2020-11-10 | SICK
Subject to change without notice
O P E R A T I N G I N S T R U C T I O N S | Flexi IO XTDO1 15
4
PROJECT PLANNING
4.5
Further topics
•
• "Configuring elements"
Testing plan
Testing plan
The manufacturer of the machine and the operating entity must define all required thorough checks. The definition must be based on the application conditions and the risk assessment and must be documented in a traceable manner.
In addition, the device must be checked for correct functioning after each change to the configuration.
b
When defining the thorough check, please note the following:
°
°
°
Define the type and execution of the thorough check.
Define the frequency of the thorough check.
Notify the machine operators of the thorough check and instruct them accordingly.
The following thorough checks are often defined in connection with a protective device:
• Thorough check during commissioning and modifications
• Regular thorough check
Thorough check during commissioning and modifications
The following points are helpful when planning the thorough check:
• Does the thorough check have to be completed by qualified safety personnel?
• Can the thorough check be completed by personnel specially qualified and autho‐ rized to do so?
• Does the thorough check have to be documented in a traceable manner?
• Can the thorough check be carried out according to a check list?
• Do the machine operators know the function of the protective device?
• Have the machine operators been trained to work on the machine?
• Have the machine operators been notified about modifications to the machine?
b
Define all guidelines for the thorough check.
Regular thorough check
The following points are helpful when planning the thorough check:
• Which thorough check must be carried out and how is it carried out?
• How often does the thorough check have to be carried out?
• Do the machine operators have to be notified of the thorough check and do they need to be instructed accordingly?
b
Define all guidelines for the thorough check.
16 O P E R A T I N G I N S T R U C T I O N S | Flexi IO XTDO1 8024583/2020-11-10 | SICK
Subject to change without notice
5
5.1
5.2
5.3
MOUNTING
5
Mounting
Safety
WARNING
Electrical voltage
There is a risk of injury from electrocution while connecting the devices.
b
Disconnect the power for the entire plant/machine.
WARNING
Unintended start of the plant/machine
The plant/machine could inadvertently start while you are connecting the devices.
b
Disconnect the power for the entire plant/machine.
NOTICE
Enclosure rating IP20 only applies if the front connector is mounted.
Mounting procedure
For information on the mounting process, please see the operating instructions:
• “Flexi Compact” (SICK part number 8024573)
Module exchange
Approach
1.
Disconnect module and the connected components from all voltage sources.
2.
Take front connector with connected cables off the defective device: Press the unlocking mechanism of the front connector downwards and pull out the front connector.
8024583/2020-11-10 | SICK
Subject to change without notice
Figure 6: Dismantle front connector
3.
Dismantle the defective module.
O P E R A T I N G I N S T R U C T I O N S | Flexi IO XTDO1 17
5
MOUNTING
4.
Mount new module.
5.
Mount front connector with connected cables to the new module: First mount in the module with bent hook and then engage in the housing.
Click
Figure 7: Mount the front connector
✓
The front connector engages with an audible click.
18 O P E R A T I N G I N S T R U C T I O N S | Flexi IO XTDO1 8024583/2020-11-10 | SICK
Subject to change without notice
6
6.1
6.2
ELECTRICAL INSTALLATION
6
Electrical installation
Safety
WARNING
Electrical voltage
There is a risk of injury from electrocution while connecting the devices.
b
Disconnect the power for the entire plant/machine.
WARNING
Unintended start of the plant/machine
The plant/machine could inadvertently start while you are connecting the devices.
b
Disconnect the power for the entire plant/machine.
NOTICE
Enclosure rating IP20 only applies if the front connector is mounted.
Device connection
Prerequisites
Electrical connection requirement:
• Electrical installation is performed in accordance with EN 60204-1.
• The mounting rail is connected to the functional earth.
• The voltage supply and connected signals meet the requirements for extra-low voltages with safe separation (EN 60664) or NEC Class 2 (UL 1310).
• The external voltage supply must be capable of buffering brief power failures of
20 ms as specified in EN 60204-1. Suitable power supply units are available as accessories from SICK.
• The GND of all connected devices must have the same potential as A2 of the main module. Exceptions are actuators which are connected to an expansion module with its own voltage supply.
• The GND connections of the actuators to the safety outputs are in star formation with the GND connection of the voltage supply.
Pin assignment
1
3
5
7
13
15
9
11
17
Q1
Q3
Q5
Q7
A1
I1
I3
I5
I7
2
4
6
8
14
16
10
12
18
Q2
Q4
Q6
Q8
A2
I2
I4
I6
I8
Figure 8: Terminals on front connector
8024583/2020-11-10 | SICK
Subject to change without notice
O P E R A T I N G I N S T R U C T I O N S | Flexi IO XTDO1 19
6
ELECTRICAL INSTALLATION
Table 4: Front connector pin assignment
6
7
8
4
5
2
3
Terminal
1
13
14
15
16
9
10
11
12
17
18
Q5
Q6
Q7
Q8
Q1
Q2
Q3
Q4
A1
A2
I6
I7
I8
I4
I5
I2
I3
Pin assignment
I1
Description
Safety capable input
Safety output
24 V voltage supply of outputs Q1 to Q8
1)
GND voltage supply of outputs Q1 to Q8
1)
1) The voltage can be supplied using a separate power supply unit without a reference potential to the main module.
Complementary information
13
15
16
6.3
Figure 9: Eyelet on front connector
1
Eyelet for cable tie
Connected cables can be fastened to the front connector eyelet using a cable tie. This relieves the strain on the cables.
Further topics
•
"Electrical integration", page 15
Coding
Overview
You can code the front connector and its modules. A uniquely coded front connector only fits a uniquely coded module. Coding prevents the front connectors from getting mixed up.
20 O P E R A T I N G I N S T R U C T I O N S | Flexi IO XTDO1 8024583/2020-11-10 | SICK
Subject to change without notice
6.3.1
ELECTRICAL INSTALLATION
6
Coding options
• 1-of-7 coding: 7 front connectors can be uniquely coded.
Front connector 1
Front connector 2
…
Front connector 6
Front connector 7
…
Coding
Front connector 1
Front connector 2
…
Front connector 7
1 2 3 4 5 6 7
⃞
C C C C C C
C
⃞
C C C C C
…
C C C C C C
⃞
• 2-of-7 coding: 21 front connectors can be uniquely coded.
Coding
1 2 3 4 5 6 7
⃞ ⃞
C C C C C
C
⃞ ⃞
C C C C
…
C C C C C
⃞ ⃞
⃞
C C C C C
⃞
…
• 3-of-7 coding: 35 front connectors can be uniquely coded.
Front connector 1
Front connector 2
…
Front connector 5
Front connector 6
…
Coding
1 2 3 4 5 6 7
⃞ ⃞ ⃞
C C C C
C
⃞ ⃞ ⃞
C C C
…
C C C C
⃞ ⃞ ⃞
⃞ ⃞
C C C C
⃞
…
Coding front connector and module
Prerequisites
• Slotted screwdriver 3.5 mm × 0.6 mm
• Diagonal cutter
Approach
Each front connector contains seven coding ribs. The modules have seven coding elements each for each front connector.
1.
Remove the coding ribs on the front connector with wire cutters.
2.
Insert the slotted screwdriver vertically on the left next to the respective coding element.
8024583/2020-11-10 | SICK
Subject to change without notice
O P E R A T I N G I N S T R U C T I O N S | Flexi IO XTDO1 21
6
ELECTRICAL INSTALLATION
3.
Tip the coding element to the right with a slotted screwdriver.
✓
The coding element engages.
Complementary information
You can not reattach a removed coding rib to the front connector.
If you turn a coding element on a module several times, it can break off. This means there is no active coding function in this case. However, you can continue to use the module.
22 O P E R A T I N G I N S T R U C T I O N S | Flexi IO XTDO1 8024583/2020-11-10 | SICK
Subject to change without notice
7
7.1
COMMISSIONING
7
Commissioning
Check during commissioning and modifications
The test is intended to ensure that the hazardous area is monitored by the protective device and that unprotected access to the hazardous area is prevented.
b
Carry out the checks according to the instructions from the manufacturer of the machine and from the operating entity.
8024583/2020-11-10 | SICK
Subject to change without notice
O P E R A T I N G I N S T R U C T I O N S | Flexi IO XTDO1 23
8
OPERATION
8
8.1
Operation
Regular thorough check
The test is intended to ensure that the hazardous area is monitored by the protective device and that unprotected access to the hazardous area is prevented.
b
Carry out the checks according to the instructions from the manufacturer of the machine and from the operating entity.
24 O P E R A T I N G I N S T R U C T I O N S | Flexi IO XTDO1 8024583/2020-11-10 | SICK
Subject to change without notice
9
9.1
MAINTENANCE
9
Maintenance
Regular thorough check
The test is intended to ensure that the hazardous area is monitored by the protective device and that unprotected access to the hazardous area is prevented.
b
Carry out the checks according to the instructions from the manufacturer of the machine and from the operating entity.
8024583/2020-11-10 | SICK
Subject to change without notice
O P E R A T I N G I N S T R U C T I O N S | Flexi IO XTDO1 25
10
TROUBLESHOOTING
10 Troubleshooting
10.1
Status indicators
Possible indications
Table 5: PWR and CV indications
Display
PWR
Display
CV
Main module o o
Description Measures
Ö
Ö
Yellow (2 Hz)
Yellow (lights up every 2 s)
No supply voltage b
Check terminals A1 and A2.
b
Switch on the supply voltage to the main module.
Ö
Red / green
(1 Hz) o
Ö
Green (1 Hz)
Ö
Red / green
(1 Hz)
Self-test is in progress or the safety con‐ troller is being initializing.
Application is ready to run.
Application is running.
A recoverable external error is present at this module.
Application is running.
b
Press the start button in the configura‐ tion software.
b
Check the cabling of the flashing inputs and outputs.
O
Green
o Ö
Ö
O
Red (1 Hz)
Red (2 Hz)
Red o o
Configuration is invalid.
Critical error, presumably at this module.
The application was stopped. All outputs of the safety controller are switched off.
Critical error, presumably at another mod‐ ule.
The application was stopped. All outputs of the safety controller are switched off.
b
Check the module type and version.
b
Adjust the configuration using the con‐ figuration software.
b
Run diagnostics using the configuration software.
b
Switch the supply voltage off and then on again.
b
If the fault persists, replace the mod‐ ule.
b
Run diagnostics using the configuration software.
b
Switch the supply voltage off and then on again.
b
If the fault persists, replace the mod‐ ule where the PWR
Ö
is showing red
(2 Hz).
b
Run diagnostics using the configuration software.
o
LED off.
Ö
LED flashes.
O
LED illuminates.
Table 6: CV indications
Display
CV o
O
Yellow
Ö
Yellow (1 Hz)
Description
Configuration is verified.
Configuration is not verified.
Measures b
Verify the configuration using the configura‐ tion software.
See the Flexi Compact Safety Controller operat‐ ing instructions (8024573)
See the Flexi Compact Safety Controller operat‐ ing instructions (8024573) o LED off. Ö LED flashes. O LED illuminates.
26 O P E R A T I N G I N S T R U C T I O N S | Flexi IO XTDO1 8024583/2020-11-10 | SICK
Subject to change without notice
TROUBLESHOOTING
10
Table 7: I indications (safety capable input)
Description
I
Display o
O
Green
Ö
Green (1 Hz) in sync with the red PWR indi‐ cation
Ö
Green (1 Hz) in sync with the green PWR indication
Input is inactive (LOW).
Input is active (HIGH).
Input is inactive (LOW) and a recoverable exter‐ nal error is present.
Input is active (HIGH) and a recoverable external error is present.
Measures b b
Check cabling of the flashing inputs. A shortcircuit to GND or cable break may be present.
Check cabling of the flashing inputs. A shortcircuit to 24 V or a cross-circuit to another signal may be present.
o
LED off.
Ö
LED flashes.
O
LED illuminates.
Table 8: Q indications (safety output)
Display
Q
Description o
O
Green
Ö
Green (1 Hz) in sync with the red PWR indi‐ cation
Output is inactive (LOW).
Output is active (HIGH).
Output is inactive (LOW) and a recoverable exter‐ nal error is present.
Ö
Green (1 Hz) in sync with the green PWR indication
Output is active (HIGH) and a recoverable exter‐ nal error is present.
Measures b
Check cabling of the flashing outputs. A shortcircuit to GND or a cross-circuit between out‐ puts may be present.
b
If all indicators of the configured outputs are flashing, check the supply voltage of the A1 and A2 terminals.
b
Check cabling of the flashing outputs. A shortcircuit to 24 V or a cross-circuit between out‐ puts may be present.
o
LED off.
Ö
LED flashes.
O
LED illuminates.
Complementary information
The input and output indicators display the status of the terminals with a refresh rate of approx. 50 ms.
Further topics
•
10.2
Possible faults
Important information
NOTE
If a fault response can result in an undesired valid status, you should evaluate the associated status bits in the logic to initiate suitable measures.
Possible faults and their causes
Table 9: Faults in the logic
Fault
Voltage supply A1 / A2 of the main module is lower than the operat‐ ing range
Responses
• Safety controller switches to the
No supply voltage status
• Voltage supply module status bit =
0
•
Status indicators are off
Causes
• Fault in the voltage supply
• Line break
• Interruption due to a fuse
8024583/2020-11-10 | SICK
Subject to change without notice
O P E R A T I N G I N S T R U C T I O N S | Flexi IO XTDO1 27
10
TROUBLESHOOTING
Fault
Voltage supply of the main module is higher than the operating range
Responses
• Safety controller switches to the critical error status
• Internal error module status bit = 0
Causes
• Fault in the voltage supply
• Short-circuit to other volt‐ age-carrying line
Table 10: Faults in the safety capable inputs (I)
Fault Responses
Electro-mechanical switch/safety switch
(EMSS), safety sen‐ sors with test input,
Flexi Loop: safety capable input is Low instead of High
Electro-mechanical switch/safety switch
(EMSS), safety sen‐ sors with test input,
Flexi Loop: test pulses from the asso‐ ciated test output
X are not detected correctly (short-circuit detection)
•
• Process data bit of the affected input = 0
• Process data bit of the affected input = 0
•
Status Ix process data status bit =
0
Module status bit of the affected
Status Ix input = 0
Dual-channel elec‐ tro-mechanical safety switch (EMSS), safety sensors with moni‐ tored semiconductor outputs (OSSD): equiv‐ alent/complementary safety capable inputs exhibit different/the same values.
Safety pressure mats: safety capable input is Low instead of test pulse signal from the associated test output
X
Safety pressure mats: safety capable input is
High instead of test pulse signal from the associated test output
X
Internal error detected in input evaluation
•
• Process data bit of the affected input = 0
• Status Ix, ly dual-channel evaluation process data status bit = 0
•
Module status bit of the affected
Status Ix, ly dual-channel evaluation input = 0
•
Process data bit of the affected input pair = 0
• Status Ix process data status bit =
0
Module status bit of the affected
Status Ix input = 0
•
Process data bit of the affected input = 0
• Status Ix, ly dual-channel evaluation process data status bit = 0
• Module status bit of the affected
Status Ix, ly dual-channel evaluation input = 0
• Safety controller switches to the critical error status
• Internal error module status bit = 0
Causes
• Short-circuit to another line e.g., GND
• Error in the sensor
• Line break
•
•
•
•
Short-circuit to other volt‐ age-carrying line
•
Error in the sensor (for exter‐ nally tested sensors)
Short-circuit to another line e.g., GND
• Error in the sensor
• Line break
• Discrepancy time
• Sequence error
•
Line break
Test output → sensor
• Line break
Sensor → safety capable input
Short-circuit to other volt‐ age-carrying line
Internal device error
28 O P E R A T I N G I N S T R U C T I O N S | Flexi IO XTDO1 8024583/2020-11-10 | SICK
Subject to change without notice
8024583/2020-11-10 | SICK
Subject to change without notice
TROUBLESHOOTING
10
1)
2)
3)
Table 11: Faults in the safety outputs (Q)
Fault
Auxiliary voltage sup‐ ply A1 / A2 for the safety outputs is lower than the operating range
Responses
• All safety outputs of the module are switched off
• Output voltage supply process data status bit = 0
•
Auxiliary voltage supply module sta‐ tus bit = 0
• Internal error module status bit = 0
• Auxiliary voltage supply module sta‐ tus bit = 0
Auxiliary voltage sup‐ ply A1 / A2 for the safety outputs is higher than the oper‐ ating range
Output voltage level is Low instead of
High when the output is “On”, overload/over‐ current
1) 2)
Output voltage level is
High instead of Low when the output is
“Off” 3)
Test pulses are not detected correctly when the output is
“On”
3) 5)
Internal error detected
•
Associated output/associated output pair is switched off
• Depending on the load, the affected output may pulsate tem‐ porarily until the final switch-off
•
Status Qx short-circuit to Low process data status bit = 0
• Status Qx short-circuit to Low module status bit = 0
• All safety outputs of the module are switched off
• Output voltage supply process data status bit = 0 4)
• Status Qx short-circuit to High process data status bit = 0
• Status Qx short-circuit to High mod‐ ule status bit = 0
• Safety controller switches to the critical error status
•
Internal error module status bit = 0
Causes
• Fault in the voltage supply
• Line break
• Interruption due to a fuse
•
•
•
•
•
•
• Fault in the voltage supply
• Short-circuit to other volt‐ age-carrying line
Short-circuit or resistance drop under load
• Short-circuit to another line e.g., GND
Short-circuit to other volt‐ age-carrying line
Short-circuit to other volt‐ age-carrying line
Capacitive load too high
Internal device error
Capacitive load too high
4)
5)
Depending on the voltage supply used, an overcurrent can also result in the voltage supply dropping out.
Reset of the error: set the process data bit of the safety output to 0.
Reset of the error: the process data bits for all safety outputs of the module are simultaneously 0 and the output level is Low.
In the case of a High instead of a Low on a safety output, the supply to all safety outputs is switched off internally. If the cause of a short-circuit is in the wiring to 24 V, then the affected signal remains High and all other signals switch to Low.
Check if this is an undesired but valid signal value for the receiver, e.g., for the switching of the monitoring case of a SICK safety laser scanner by means of a complementary signal.
Depending on the size of the capacitive load, this may lead in certain cases to an incorrect interpretation as an internal error since the effect on the output voltage is only temporary.
Critical error status
Consequences of the critical error status:
• All applications are stopped.
• All safety outputs are switched off.
• All process data = 0
• Evaluation of the process data status bits in the logic is no longer possible.
• Only limited diagnostics can be performed in the critical error status.
Alternatives to resetting the critical error status:
• Restart by switching the voltage supply off and on again
• Software reset using the configuration software
O P E R A T I N G I N S T R U C T I O N S | Flexi IO XTDO1 29
10
TROUBLESHOOTING
Complementary information
The status indicators and diagnostic messages may provide additional information.
Further topics
•
• "Input elements"
30 O P E R A T I N G I N S T R U C T I O N S | Flexi IO XTDO1 8024583/2020-11-10 | SICK
Subject to change without notice
11
11.1
DECOMMISSIONING
11
Decommissioning
Disposal
Approach
b
Always dispose of unusable devices in accordance with national waste disposal regulations.
Complementary information
SICK will be glad to help you dispose of these devices on request.
8024583/2020-11-10 | SICK
Subject to change without notice
O P E R A T I N G I N S T R U C T I O N S | Flexi IO XTDO1 31
12
TECHNICAL DATA
12
12.1
Technical data
Data sheet
Safety-related parameters
Table 12: Safety-related characteristic data - safety capable inputs (I)
Safety capable inputs (I)
Safety integrity level (IEC 61508)
SIL claim limit
(IEC 62061)
Single-channel
Without test pulses
1)
SIL 2
SILCL 2
Dual channel
With test pulses Without test
SIL 3
SILCL 3 pulses
2)
SIL 3
SILCL 3
Category 3 Category 4 Category 4 Cate‐ gory (ISO 13849-
1)
Performance level (ISO
13849-1)
PFH
D
(h
-1
)
PFD avg
PL d
1 × 10
4 × 10
-9
-5
PL e
1 × 10
4 × 10
-9
-5
PL e
0.5 × 10
4 × 10
-5
-9
MTTF
D
ISO
13849-1
[years]
T
M
ISO 13849-1
[years]
500
20
500
20
500
20
With test pulses
SIL 3
SILCL 3
Category 4
PL e
0.5 × 10
-9
4 × 10
-5
500
20
1)
2)
If you are using single-channel safety inputs (I) without test pulses for a safety-related application, then a protected or separate cabling is required for these safety inputs in order to achieve the safety-related characteristics. Reason: Short-circuits to the supply voltage or cross-circuits are not detected.
If you are using dual-channel safety capable inputs (I) without test pulses, the safety function must be requested at least once a year.
Table 13: Safety-related characteristic data - CPU logic processing
CPU logic processing
Safety integrity level (IEC 61508)
SIL claim limit (IEC 62061)
SIL 3
SILCL 3
Category (ISO 13849-1)
Performance level (ISO 13849-1)
PFH
D
(h -1 )
PFD avg
Category 4
PL e
3 × 10 -9
20 × 10 -5
MTTF
D
ISO 13849-1
[years]
T
M
ISO 13849-1
[years]
500
20
32 O P E R A T I N G I N S T R U C T I O N S | Flexi IO XTDO1 8024583/2020-11-10 | SICK
Subject to change without notice
8024583/2020-11-10 | SICK
Subject to change without notice
TECHNICAL DATA
12
Table 14: Safety-related characteristic data - safety outputs (Q)
Safety outputs (Q)
Single-channel 1)
Without test pulses
SIL 3
2) 3)
Dual channel
With test pulses Without test pulses
2) 3)
SIL 3 SIL 3 Safety integrity level (IEC 61508)
SIL claim limit
(IEC 62061)
SILCL 3
Category (ISO 13849-1)
SILCL 3 SILCL 3
Category 4 With test pulses on all safety outputs of a module
Without test pulses on one or more safety outputs of a module
Performance level (ISO
13849-1)
PFH
D
(h -1 )
Category 3
PL e
5 × 10 -9
Category 3
PL e
0.5 × 10 -9
Category 4
PL e
5 × 10 -9
PFD avg
MTTF
D
ISO
13849-1
[years]
T
M
ISO 13849-1
[years]
30 × 10 -5
500
20
4 × 10 -5
500
20
30 × 10 -5
500
20
1)
2)
3)
With test pulses
SIL 3
SILCL 3
Category 4
Category 4
PL e
0.5 × 10 -9
4 × 10 -5
500
20
If you are using single-channel safety outputs (Q) for a safety-related application, then a protected or separate cabling is required for these safety outputs in order to achieve the safety-related characteristics.
Reason: While short-circuits to the supply voltage or cross-circuits to other outputs can be detected, no other option to switch-off the device exist.
If you are using single-channel or dual-channel safety outputs (Q) without test pulses, then a protected or separate cabling is required for these safety outputs in order to achieve the safety-related characteristics.
Reason: Short-circuits to the supply voltage or cross-circuits to other outputs are not detected in the switched-on state without test pulses.
This also applies if an output is used for a non-safety related application. Reason: Even if an internal hardware error is detected, the switch-off capability of the other safety outputs may be impaired by reverse currents.
If you are using single-channel/dual-channel safety outputs (Q) without test pulses for a safety-related application, then one of the following measures is required in order to achieve the safety-related charac‐ teristics:
• Restart the safety controller once a year.
• Manually switch off all safety outputs simultaneously for min. 2 s once a year. The supply voltage to the outputs must be within the operating range during this manual test.
General data
Table 15: General data
Climatic conditions
Ambient operating temperature
At altitudes up to 2,000 m above sea level
–25 °C … +55 °C
O P E R A T I N G I N S T R U C T I O N S | Flexi IO XTDO1 33
12
TECHNICAL DATA
At altitudes up to 2,000 m above sea level … 3,000 m above sea level
At altitudes 3,000 m above sea level … 4,000 m above sea level
Storage temperature
Air humidity
Operating altitude
Mechanical strength
Vibration resistance
Shock resistance, single shock
Operating data
Protection class
Immunity to interference
Emitted interference
Connections
Connection type
–25 °C … +50 °C
–25 °C … +45 °C
–25 °C … +70 °C
10% … 95%, non-condensing
Max. 4,000 m above sea level
5 Hz … 200 Hz / 1 g (EN 60068-2-6)
15 g, 11 ms (EN 60068-2-27)
III (EN 61140)
EN 61000-6-2
EN 61000-6-4
Wire cross-section
Spring terminals
RJ45 female connectors
Single wire or fine-stranded wire: 0.14 mm² … 1.5 mm²
Fine-stranded wire with ferrule: a) with plastic ferrule max. 1.0 mm² b) without plastic ferrule max. 1.0 mm²
AWG according to UL/CSA: 26 … 14
For UL and CSA applications:
Use copper conductors only min. rated for 85°C.
Housing
Enclosure rating
Contamination rating
Control device type
Weight (± 5%)
IP20 (EN 60529)
2 (IEC 61010-1)
Open device (IEC 61010-2-201)
111 g
Voltage supply (A1 / A2)
Table 16: Voltage supply
Supply voltage U
B
Tolerance of supply voltage
Type of supply voltage
+24 V DC
–30% / +25% (16.8 V … 30 V)
PELV or SELV
The supply current must be limited externally to max. 4 A
– either by the voltage supply unit used, or by means of a fuse.
4.9 W
2.4 W
Max. power loss
Power consumption at nominal volt‐ age
(without outputs)
Short-circuit protection 1)
Overvoltage category
Max. 4 A/Min. 30 V
Safety fuse with triggering characteristic: slow-blow
UL/CSA applications: UL-listed fuse according to
UL 248-14 required
II (EN 61131-2)
34 O P E R A T I N G I N S T R U C T I O N S | Flexi IO XTDO1 8024583/2020-11-10 | SICK
Subject to change without notice
8024583/2020-11-10 | SICK
Subject to change without notice
TECHNICAL DATA
12
Type of terminal connections Spring terminals
1) When selecting the voltage supply for the safety controller, you need to take into the account the no load current of all modules of the station, and the peak current consumption of all electrical consumers connected to the outputs of the safety controller. The maximum permissible supply current depends, amongst other things, on the ambient temperature and must not exceed the permitted value of 8 A (Ta
= 55 °C). Take into consideration the effect of lack of ventilation or the power loss in cables or other devices on the ambient temperature in the control cabinet.
Safety capable inputs (I)
Table 17: Technical data for the safety capable inputs (I)
Input voltage High
Input voltage Low
Max. input voltage range
Input current high
Input current Low
Reverse current at input in case of loss of ground connection 2)
Input capacitance
Discrepancy time
1)
11 V DC … 30 V DC
–3 V DC … +5 V DC
–60 V DC … +60 V DC
2.1 mA … 6 mA
≤ 1.9 mA
≤ 100 µA
15 nF
4 ms … 30 s, configurable
1)
2)
No damage to the input in this voltage range.
Do not connect any other safety capable inputs in parallel if the reverse current could lead to a High state on the other input.
Safety outputs (Q)
Table 18: Technical data for the safety outputs (Q)
Type of output PNP semiconductor, short-circuit protected
Output voltage High
Max. output voltage Low
1)
Maximum reverse voltage at Low
2)
U
B
–3 V DC … U
B
–50 V DC … –30 V DC
3 V DC
Leakage current Low
Normal operation
Dual channel
Fault 3)
Output current
< 1 mA
< 2 mA
< 1 mA
Max. 2 A
Sum current I sum
T
U
≤ 55 °C
Test pulse duration
4)
4 A
Test pulse frequency
Cross-circuit detection using test pulses
5)
< 650 µs or deactivated
≥ 190 ms
Cable resistance
Output current, dual-channel out‐ puts
Load capacity
Load capacity when connected via diode
Max. 2.5 Ω (z. B. 100 m × 1.5 mm² = 1.2 Ω)
Max. 1 A per output
≤ 0.5 µF
≤ 1,000 µF
Inductive load at nominal voltage
@2 A
@1 A
100 mH
1.6 H
O P E R A T I N G I N S T R U C T I O N S | Flexi IO XTDO1 35
12
TECHNICAL DATA
12.2
@0.5 A 20 H
1)
2)
3)
4)
5)
Max. –30 V DC, to avoid damaging the output.
Max. –50 V DC, for fast switch-off of inductive loads.
Higher voltages are evaluated as a cross-circuit fault
In the event of a fault (GND line open circuit) and with a load resistance of at least 2.5 kΩ, no more than the specified leakage current flows on the safety output. For lower load resistances, the leakage current may be greater however the output voltage will be < 5 V in this case. A downstream device, for example a relay or a FPLC (fail-safe programmable logic controller) must detect this state as Low.
When activated, the outputs are tested regularly (brief switching to Low). When selecting the downstream control elements, ensure that the test pulses with the specified parameters do not result in a switch-off, or deactivate the test pulses on the outputs yourself.
Safety outputs (Q) with test pulses only detect cross-circuits reliably (i.e. already in the switched-on state and not just after a switch-off) if these values for the supply cable and the connected control element are not exceeded. Otherwise further measures will be required, for example protected or separate cabling.
(See also EN 60204 Electrical equipment of machines, Part 1: General requirements.)
Dimensional drawings
16
14
89,6
85,5
78,4
Figure 10: Dimensional drawing
36 O P E R A T I N G I N S T R U C T I O N S | Flexi IO XTDO1 8024583/2020-11-10 | SICK
Subject to change without notice
13
13.1
13.2
13.3
13.4
ORDERING INFORMATION
13
Ordering information
Scope of delivery
• Expansion module - IO
• Front connector
• Safety note
• Operating instructions for download: www.sick.com
Ordering information for main module
Table 19: Ordering information for main module
Part
CPUc1 main module
•
20 safety capable inputs
•
8 test outputs
•
4 safety outputs
CPUc2 main module
• 20 safety capable inputs
• 8 test outputs
• 4 safety outputs
• Ethernet interface (female RJ45 Ethernet connector) for Modbus® TCP
Type code
FLX3-CPUC100
FLX3-CPUC200
Ordering information for expansion module
Ordering information for IO expansion module
Table 20: Ordering information for IO expansion module
Part Type code
Expansion module XTDI1 FLX3-XTDI100
• 8 safety capable inputs
• 8 test outputs
Expansion module XTDO1
• 8 safety capable inputs
• 8 safety outputs
FLX3-XTDO100
Ordering information for gateway expansion module
Table 21: Ordering information for gateway expansion module
Part
GPNT1 PROFINET-IO gateway
GETC1 EtherCAT® gateway
Type code
FLX0-GPNT100
FLX0-GETC100
Ordering information for accessories
Table 22: Ordering information for accessories
Part
Front connector with opening for SmartPlug
• 16 spring terminals
Type code
FLX0-ACC0300
Part number
1085349
1085351
Part number
1085353
1085354
Part number
1085356
1085357
Part number
6069666
8024583/2020-11-10 | SICK
Subject to change without notice
O P E R A T I N G I N S T R U C T I O N S | Flexi IO XTDO1 37
13
ORDERING INFORMATION
Part
Front connector
•
18 spring terminals
SmartPlug
Housing end cap
Type code
FLX0-ACC0200
FLX3-SMPL100
FLX0-ACC0400
Part number
6066285
2106852
5340579
38 O P E R A T I N G I N S T R U C T I O N S | Flexi IO XTDO1 8024583/2020-11-10 | SICK
Subject to change without notice
14
14.1
ANNEX
14
Annex
Compliance with EU directives
EU declaration of conformity (extract)
The undersigned, representing the manufacturer, herewith declares that the product is in conformity with the provisions of the following EU directive(s) (including all applicable amendments), and that the standards and/or technical specifications stated in the EU declaration of conformity have been used as a basis for this.
Complete EU declaration of conformity for download
You can call up the EU declaration of conformity and the current operating instruc‐ tions for the protective device by entering the part number in the search field at www.sick.com
(part number: see the type label entry in the “Ident. no.” field).
8024583/2020-11-10 | SICK
Subject to change without notice
O P E R A T I N G I N S T R U C T I O N S | Flexi IO XTDO1 39
15
LIST OF FIGURES
15 List of figures
1.
2.
3.
4.
5.
6.
7.
8.
9.
40 O P E R A T I N G I N S T R U C T I O N S | Flexi IO XTDO1 8024583/2020-11-10 | SICK
Subject to change without notice
16
LIST OF TABLES
16
List of tables
1.
2.
3.
4.
5.
6.
7.
8.
9.
8024583/2020-11-10 | SICK
Subject to change without notice
O P E R A T I N G I N S T R U C T I O N S | Flexi IO XTDO1 41
16
LIST OF TABLES
42 O P E R A T I N G I N S T R U C T I O N S | Flexi IO XTDO1 8024583/2020-11-10 | SICK
Subject to change without notice
LIST OF TABLES
16
8024583/2020-11-10 | SICK
Subject to change without notice
O P E R A T I N G I N S T R U C T I O N S | Flexi IO XTDO1 43
Australia
Phone +61 (3) 9457 0600
1800 33 48 02 – tollfree
E-Mail [email protected]
Austria
Phone +43 (0) 2236 62288-0
E-Mail [email protected]
Belgium/Luxembourg
Phone +32 (0) 2 466 55 66
E-Mail [email protected]
Brazil
Phone +55 11 3215-4900
E-Mail [email protected]
Canada
Phone +1 905.771.1444
E-Mail [email protected]
Czech Republic
Phone +420 234 719 500
E-Mail [email protected]
Chile
Phone +56 (2) 2274 7430
E-Mail [email protected]
China
Phone +86 20 2882 3600
E-Mail [email protected]
Denmark
Phone +45 45 82 64 00
E-Mail [email protected]
Finland
Phone +358-9-25 15 800
E-Mail [email protected]
France
Phone +33 1 64 62 35 00
E-Mail [email protected]
Germany
Phone +49 (0) 2 11 53 010
E-Mail [email protected]
Greece
Phone +30 210 6825100
E-Mail [email protected]
Hong Kong
Phone +852 2153 6300
E-Mail [email protected]
Hungary
Phone +36 1 371 2680
E-Mail [email protected]
India
Phone +91-22-6119 8900
E-Mail [email protected]
Israel
Phone +972 97110 11
E-Mail [email protected]
Italy
Phone +39 02 27 43 41
E-Mail [email protected]
Japan
Phone +81 3 5309 2112
E-Mail [email protected]
Malaysia
Phone +603-8080 7425
E-Mail [email protected]
Mexico
Phone +52 (472) 748 9451
E-Mail [email protected]
Netherlands
Phone +31 (0) 30 229 25 44
E-Mail [email protected]
New Zealand
Phone +64 9 415 0459
0800 222 278 – tollfree
E-Mail [email protected]
Norway
Phone +47 67 81 50 00
E-Mail [email protected]
Poland
Phone +48 22 539 41 00
E-Mail [email protected]
Romania
Phone +40 356-17 11 20
E-Mail [email protected]
Russia
Phone +7 495 283 09 90
E-Mail [email protected]
Singapore
Phone +65 6744 3732
E-Mail [email protected]
Detailed addresses and further locations at www.sick.com
Slovakia
Phone +421 482 901 201
E-Mail [email protected]
Slovenia
Phone +386 591 78849
E-Mail [email protected]
South Africa
Phone +27 10 060 0550
E-Mail [email protected]
South Korea
Phone +82 2 786 6321/4
E-Mail [email protected]
Spain
Phone +34 93 480 31 00
E-Mail [email protected]
Sweden
Phone +46 10 110 10 00
E-Mail [email protected]
Switzerland
Phone +41 41 619 29 39
E-Mail [email protected]
Taiwan
Phone +886-2-2375-6288
E-Mail [email protected]
Thailand
Phone +66 2 645 0009
E-Mail [email protected]
Turkey
Phone +90 (216) 528 50 00
E-Mail [email protected]
United Arab Emirates
Phone +971 (0) 4 88 65 878
E-Mail [email protected]
United Kingdom
Phone +44 (0)17278 31121
E-Mail [email protected]
USA
Phone +1 800.325.7425
E-Mail [email protected]
Vietnam
Phone +65 6744 3732
E-Mail [email protected]
SICK AG | Waldkirch | Germany | www.sick.com
advertisement
* Your assessment is very important for improving the workof artificial intelligence, which forms the content of this project
Related manuals
advertisement
Table of contents
- 3 Product description
- 6 Project planning
- 6 Design
- 10 Mounting
- 12 Electrical installation
- 13 Coding
- 16 Commissioning
- 17 Operation
- 25 Maintenance
- 26 Troubleshooting
- 27 10.2 Possible faults
- 31 Decommissioning
- 32 Technical data
- 37 Ordering information
- 37 13.1 Scope of delivery
- 39 Annex
- 40 List of figures
- 41 List of tables