- Home
- Domestic appliances
- Climate control
- Split-system air conditioners
- Fedders
- AFPC60B1
- Instruction manual
advertisement
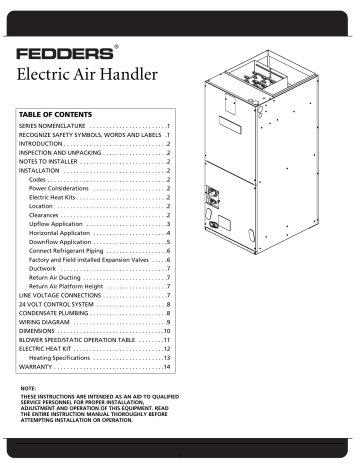
Electric Air Handler
TABLE OF CONTENTS
SERIES NOMENCLATURE . . . . . . . . . . . . . . . . . . . . . . . .1
RECOGNIZE SAFETY SYMBOLS, WORDS AND LABELS .1
INTRODUCTION . . . . . . . . . . . . . . . . . . . . . . . . . . . . . . . .2
INSPECTION AND UNPACKING . . . . . . . . . . . . . . . . . . . .2
NOTES TO INSTALLER . . . . . . . . . . . . . . . . . . . . . . . . . . .2
INSTALLATION . . . . . . . . . . . . . . . . . . . . . . . . . . . . . . . .2
Codes . . . . . . . . . . . . . . . . . . . . . . . . . . . . . . . . . . . . .2
Power Considerations . . . . . . . . . . . . . . . . . . . . . . .2
Electric Heat Kits . . . . . . . . . . . . . . . . . . . . . . . . . . . .2
Location . . . . . . . . . . . . . . . . . . . . . . . . . . . . . . . . . .2
Clearances . . . . . . . . . . . . . . . . . . . . . . . . . . . . . . . . .2
Upflow Application . . . . . . . . . . . . . . . . . . . . . . . . .3
Horizontal Applicaton . . . . . . . . . . . . . . . . . . . . . . .4
Downflow Application . . . . . . . . . . . . . . . . . . . . . . .5
Connect Refrigerant Piping . . . . . . . . . . . . . . . . . . .6
Factory and Field installed Expansion Valves . . . . .6
Ductwork . . . . . . . . . . . . . . . . . . . . . . . . . . . . . . . . .7
Return Air Ducting . . . . . . . . . . . . . . . . . . . . . . . . . .7
Return Air Platform Height . . . . . . . . . . . . . . . . . . .7
LINE VOLTAGE CONNECTIONS . . . . . . . . . . . . . . . . . . . .7
24 VOLT CONTROL SYSTEM . . . . . . . . . . . . . . . . . . . . . .8
CONDENSATE PLUMBING . . . . . . . . . . . . . . . . . . . . . . . .8
WIRING DIAGRAM . . . . . . . . . . . . . . . . . . . . . . . . . . . . .9
DIMENSIONS . . . . . . . . . . . . . . . . . . . . . . . . . . . . . . . . .10
BLOWER SPEED/STATIC OPERATION TABLE . . . . . . . .11
ELECTRIC HEAT KIT . . . . . . . . . . . . . . . . . . . . . . . . . . . .12
Heating Specifications . . . . . . . . . . . . . . . . . . . . . .13
WARRANTY . . . . . . . . . . . . . . . . . . . . . . . . . . . . . . . . . .14
NOTE:
THESE INSTRUCTIONS ARE INTENDED AS AN AID TO QUALIFIED
SERVICE PERSONNEL FOR PROPER INSTALLATION,
ADJUSTMENT AND OPERATION OF THIS EQUIPMENT. READ
THE ENTIRE INSTRUCTION MANUAL THOROUGHLY BEFORE
ATTEMPTING INSTALLATION OR OPERATION.
1
SERIES NOMENCLATURE
Product Type
A = Air handler
Brand
Motor
E = ECM
P = PSC
Chassis Size
B = 43 3/8” H x 18” W x 22” D
C = 48 1/8” H x 22” W x 26” D
Nominal BTUH
18 = 18,000 BTU/H (5.28 kW)
24 = 24,000 BTU/H (7.03 kW)
30 = 30,000 BTU/H (8.79 kW)
36 = 36,000 BTU/H (10.55 kW)
42 = 42,000 BTU/H (12.31 kW)
48 = 48,000 BTU/H (14.07 kW)
60 = 60,000 BTU/H (17.58 kW)
A F P B 24 A 1 * A
RECOGNIZE SAFETY SYMBOLS, WORDS AND LABELS
What You Need To Know About Safety Instructions
Warning and Important Safety Instructions appearing in this manual are not meant to cover all possible conditions and situations that may occur. Common sense, caution and care must be exercised when operating or cleaning tools and equipment.
Always contact your dealer, distributor, service agent or manufacturer about problems or conditions you do not understand.
This is the safety alert symbol. It is used to alert you to potential personal injury hazards. Obey all safety messages that follow this symbol to avoid possible injury or death.
DANGER
DANGER
indicates an imminently hazardous situation which, if not avoided, will result in death or serious injury.
WARNING
WARNING
indicates a potentially hazardous situation which, if not avoided, could result in death or serious injury.
CAUTION
CAUTION
indicates a potentially hazardous situation which, if not avoided, may result in minor or moderate injury.
CAUTION
CAUTION
used without the safety alert symbol indicates a potentially hazardous situation which, if not avoided, may result in property damage.
Revision Letter
Electrical Designation
1 = 208 / 230 Volts, 1Phase, 60 Hz
2 = 230 Volts, 1 Phase, 50 Hz
3 = 208 / 230 Volts, 3 Phase, 60 Hz
4 = 460 Volts, 3 Phase, 60 Hz
5 = 230 Volts, 3 Phase, 50 Hz
6 = 380 Volts, 3 Phase, 50 Hz
Design Series
WARNING
IMPROPER INSTALLATION, ADJUSTMENT,
ALTERATION, SERVICE OR MAINTENANCE CAN
CAUSE INJURY, PROPERTY DAMAGE OR LOSS OF LIFE.
READ THIS MANUAL COMPLETELY BEFORE
BEGINNING ANY WORK AND FOLLOW ALL SAFETY
PRECAUTIONS.
A QUALIFIED INSTALLER MUST PERFORM
INSTALLATION AND SERVICE.
DO NOT DESTROY THIS MANUAL. PLEASE READ
CAREFULLY AND KEEP IN A SAFE PLACE FOR FUTURE
REFERENCE BY A SERVICE TECHNICIAN.
THESE INSTRUCTIONS ARE INTENDED AS AN AID TO
QUALIFIED SERVICE PERSONNEL FOR PROPER
INSTALLATION, ADJUSTMENT AND OPERATION OF
THIS COMPONENT. READ THESE INSTRUCTIONS
THOROUGHLY BEFORE ATTEMPTING INSTALLATION
OR OPERATION. FAILURE TO FOLLOW THESE
INSTRUCTIONS MAY RESULT IN IMPROPER
INSTALLATION, ADJUSTMENT, SERVICE OR
MAINTENANCE, POSSIBLY RESULTING IN FIRE,
ELECTRICAL SHOCK, PROPERTY DAMAGE, PERSONAL
INJURY OR DEATH.
B E F O R E P E R F O R M I N G A N Y W O R K O N T H I S
EQUIPMENT, POWER SUPPLY MUST BE TURNED OFF AT
T H E H O U S E H O L D S E R V I C E B O X T O A V O I D T H E
P O S S I B I L I T Y O F S H O C K , I N J U R Y , D A M A G E T O
EQUIPMENT, OR DEATH.
DO NOT STORE OR USE GASOLINE OR OTHER
FLAMMABLE VAPORS AND LIQUIDS, OR OTHER
COMBUSTIBLE MATERIALS IN THE VICINITY OF THIS
AIR HANDLER OR ANY OF ITS MATCHING SYSTEM
COMPONENTS (CONDENSING UNIT, HEAT PUMP OR
FURNACE).
1
NOTES TO INSTALLER
The words “SHALL” and “MUST” indicate a requirement which is essential to satisfactory and safe product performance. The words “SHOULD” and “MAY” indicate a recommendation or advice which is not essential and not required but which may be useful or helpful.
The instructions are for the use of qualified individuals specially trained and experienced in the installation of this type equipment and related system components.
Installation and service personnel are required by some locales to be licensed. Persons not qualified shall not install this equipment nor interpret these instructions.
INTRODUCTION
Models AFPB and Plare designed for flexibility and can be used for upflow, horizontal or downflow applications. These units are available for systems of 18,000 through 60,000 BTUH nominal cooling capacity. Factory authorized electric heater kits are available in 5 kW through 20 kW sizes. See product specifications for available accessory kits.
INSPECTION AND UNPACKING
A thorough inspection of the shipping container must be made immediately upon receiving your unit. Look for any punctures or openings, and if it appears damage has occurred, note it on the freight bill before signing. Contact delivering carrier immediately to inspect damage. Do not begin installation work should begin until this inspection is completed.
INSTALLATION
Codes
The installer must comply with all local, state and federal codes and/or regulations pertaining to this type of equipment and its installation. Such codes and/or regulations shall take precedent over any recommendations contained herein. If there are no local codes on the subject, installations shall be made in accordance with the National Electrical Code (NEC) and recommendations made by the National Board of Fire
Underwriters.
Power Considerations
The installer shall check available power to make certain it matches the unit name plate rating and that constant voltage can be maintained on the unit. Unsatisfactory performance or a possible hazard could otherwise result. The local power company should be contacted with questions concerning power supply.
Electric Heater Kits
Only EEB/EEC series electric heater kit may be installed into the air handler. See Electric Heat section on page 12 for more information.
Location
All models are approved for alcove, closet, and attic installation in the upflow, downflow or horizontal position. Refer to the applicable section of this manual on pages 3-5 for specific installation instructions on each position.
The air handler must be installed in a level position and should be located for ease in connecting air duct with proper air distribution.
Exterior surface of cabinet may sweat when unit is installed in non-air-conditioned space such as attic or garage. Installer must provide protection such as full-size auxiliary drain pan on all units. Be sure to allow for filter access for periodic user servicing.
In addition, caulking must be applied around the power and control wires entering the control box. This will prevent air leakage into and condensate from forming inside the control box.
Clearances
Clearances from the air handler to the combustibles are zero inches from all sides, top, and bottom; one inch from discharge air plenum; and the duct within 36 inches of the plenum.
Provide adequate space for servicing the air handler; at least 30 inches. All service and maintenance can be performed from the front access doors of the air handler.
WARNING
DO NOT, UNDER ANY CIRCUMSTANCES, CONNECT
RETURN DUCTWORK TO ANY OTHER HEAT-PRODUCING
DEVICE SUCH AS FIREPLACE INSERT, STOVE, ETC.
UNAUTHORIZED USE OF SUCH DEVICES MAY RESULT IN
FIRE, CARBON MONOXIDE POISONING, EXPLOSION,
PERSONAL INJURY, OR PROPERTY DAMAGE.
2
Upflow Applicaton
In an upflow application normally a duct is employed as a return air means as shown in Figure 1 below or a platform is installed as in Figure 2.
Upflow Installation With Return Duct
DISCHARGE DUCT (600 FPM)
DISCHARGE DUCT (600 FPM)
24” MINIMUM
24” MINIMUM
AIR
AIR
HANDLER
(MAY ALSO BE
DOWNFLOW)
(MAY ALSO BE
DOWNFLOW)
RETURN DUCT WITH A MINIMUM OF
1/2” FIBERGLASS DUCT LINER (500 FPM).
REFER TO LOCAL CODES.
1/2” FIBERGLASS DUCT LINER (500 FPM).
REFER TO LOCAL CODES.
Upflow Installation With Return Platform
DISCHARGE DUCT (600 FPM)
DISCHARGE DUCT (600 FPM)
CLOSET
CLOSET
24” MINIMUM
24” MINIMUM
AIR HANDLER
AIR HANDLER
RETURN
GRILLE
(500FPM)
GRILLE
(500FPM)
RETURN PLATFORM LINED WITH
1” FIBERGLASS INSULATION.
REFER TO LOCAL CODES.
1” FIBERGLASS INSULATION.
REFER TO LOCAL CODES.
3
Horizontal Application
This type of position is usually used in an attic or crawl space. The air handler may be laid on the left or right side for horizontal applications.
The factory-installed coil is intended for left-side-down installation.
This type of installation requires a return air duct to be attached to the air handler inlet. The opposite end of the return air duct is then routed to a return air grille mounted to the ceiling or wall. This duct MUST be no smaller than the inlet opening of the air handler.
For Horizontal Right Application:
1. Remove front panels from the air handler.
2. Remove coil assembly from the air handler.
3. Remove horizontal drain pan from left hand side of air handler and re-install on right hand side. Change splash baffle location from left hand to right hand side of drain pan flange.
4. Remove the horizontal coil support bracket from the right hand side of the air handler.
5. Reinstall coil assembly in the air handler.
6. Reattach coil support bracket to the left hand side of the air handler.
7. Replace front panels.
CAUTION
Horizontal applications in unconditioned areas, such as attics above a ceiling, require special precautionary measures. An auxiliary drain pan having at least two inches overall clearance around the unit MUST be field-fabricated and installed as shown below.
The drain outlet and drain line for the auxiliary drain pan need not be trapped but should be sloped to a suitable drain.
CAUTION
For optimum condensate drainage performance in horizontal installations, unit should be leveled along the length and width. Failure to follow this caution may result in product or property damage.
CAUTION
A P-type trap must be installed in the primary drain line as shown in figure 3 below.
Horizontal Installation
SUPPLY
AIR
RETURN AIR
SERVICE
PLATFORM
CEILING
JOISTS
AIR HANDLER SUPPORTS
(FIELD SUPPLIED)
AUXILIARY DRAIN PAN
(FIELD FABRICATED)
P-TRAP
PRIMARY
DRAIN LINE
AUXILIARY
DRAIN LINE
4
Downflow Application
Relocating Coil
CAUTION
The coil MUST be relocated for downflow application.
1. Remove coil access door.
2. Slide coil out of air handler.
3. Remove coil rack from air handler by removing screws from side of air handler.
4. Relocate rack in air handler as shown in Figure 4 using screws from side of air handler.
5. Turn air handler into downflow position.
6. Slide refrigerant coil into air handler.
7. Reverse and replace air handler door(s).
Installation Considerations
• No downflow sub-base is required with this air handler, however, local codes may require the use of a non-combustible sub-base when used with electric heater kit.
• An “L” or “T” shaped duct enclosure MUST be used as a supply plenum. No registers or outlets SHALL be located directly below the air handler supply outlet.
• Size and frame the floor opening as shown in Figure 5.
Refer to the Dimension drawing on page 10. Care
MUST be taken not to overcut the floor opening.
• Caulk around the floor opening with a nonflammable caulk such as silicone. Set the air handler in place and secure the air handler properly.
• Allow access to the low voltage connection by building the platform so that there is a minimum of
51/2" between the floor and the unit flange.
Return Air Filter Clearance
On downflow applications, certain coil models will protrude from the top of the air handler (coils greater than 15" tall on A24 through A36 air handlers and coils greater than 18" on A42 through A60 air handlers). On these models, the return air filter may be removed and a separate filter grille may be installed for closet applications.
If this method is not desirable, cabinet extension kit No.
65-1647 for A24, A30, and A36; or No.65-1649 for A42,
A48, and A60 may be ordered. The extension kit screws to the side of the air handler and extends the length of the air handler coil cabinet. In addition, the kit includes a filter compartment and door.
Emergency Drain Opening
The indoor coil emergency drain opening must be used for this application. Refer to page 8 for instructions on condensate tubing.
Relocating Coil for Downflow Position
SUPPLY
OPENING
FILTER
DOOR
DOWNFLOW
POSITION
FILTER
DOOR
UPFLOW
POSITION
2 X 6 BOTH
SIDES AND BACK
RACK
POSITION
Remove the three screws on both sides.
Flip over and replace in new position using pre-punched holes.
11
Supply Plenum Floor Opening
FLOOR
AIR HANDLER
PLENUM
UNIT
FLANGE
5 1/2”
FLOOR
SUPPLY
OPENING
5
Connect Refrigerant Piping
Use field supplied tubing of refrigerant grade. Suction tube must be insulated. Do not use damaged, dirty, or contaminated tubing because it may plug refrigerant flow control device. ALWAYS evacuate the coil and field supplied tubing before opening outdoor unit service valves.
Factory and Field-Installed Expansion Valves
1. The bulb and capillary tubing should be routed outside of the case. Make sure the capillary tube will not contact any sharp edges of the case. On factory installed expansion valves, the adjustable sensing bulb is not permanently installed onto the coils’ vapor line in order to allow easy removal during installation.
Sensing bulb attached with clamps
8 o’clock 4 o’clock
2. To assure accurate sensing and the best performance the bulb should be placed on a horizontal section of the vapor line at the four or eight o’clock position and at least 6” from the coil manifold.
WARNING
ALWAYS HAVE A FIRE EXTINGUISHER AVAILABLE
WHEN WORKING WITH AN OPEN FLAME.
ALWAYS USE SAFETY GLASSES, PROTECTIVE
CLOTHING, AND WORK GLOVES.
Vapor line
8 o’clock 4 o’clock
Attach bulb to vapor line at four or eight o’clock position
CAUTION
THE TXV VALVE CAN BE DAMAGED BY EXTREME
HEAT. PROPER PRECAUTIONS SHOULD BE TAKEN TO
AVOID OVERHEATING THE TXV VALVE AND CAUSING
DAMAGE TO THE INTERNAL COMPONENTS.
CAUTION
THE TXV SENSING BULB CAN BE DAMAGED BY
EXTREME HEAT FROM BRAZING. THE BULB SHOULD
BE REMOVED BEFORE PERFORMING ANY BRAZING
PROCEDURE AND NOT INSTALLED UNTIL AFTER THE
VAPOR AND LIQUID LINES ARE BRAZED AND LEAK
CHECKED.
TXV valve can be accessed through the valve cover-plate on the front of the air handler.
3. Attach the bulb securely with the copper strap provided.
4. Insulate the bulb thoroughly with a suitable insulation material such as cork tape.
5. Coils with TXVs should be charged 10-12 degrees
(+ or – one degree) of sub-cooling. This supercedes any subcooling value listed with condensing unit’s literature.
For the majority of installations no adjustment to the
TXV setting is required. However, if the measured superheat is less than 4° or greater than 8° an adjustment is required. The adjustment stem is at the base of the valve under the flare nut. To increase superheat, tighten the stem clockwise and to decrease superheat, back-out the stem counter-clockwise. Use a
1/4
” refrigeration service wrench for this function.
NOTE:
When removing refrigerant, always use standard reclaim procedures.
6
Ductwork
This air handler shall not be installed without supply plenums and proper ducting. Connect supply air duct over 1/2“ flanges on supply air opening. Secure duct to flange and seal connection.
Use flexible connectors between ductwork and unit at discharge connection. Ductwork passing through unconditioned space must be insulated and covered with vapor barrier.
Return Air Ducting
The dimensions of the return air duct or platform must be at a minimum the same size as the return air opening on the air handler, regardless of the air handler position.
When framing a return air platform, the opening size should be as shown below. If the air handler is to be installed in a closet, be sure to allow room for wiring and refrigerant lines.
Top View
C
D
F
LINE VOLTAGE CONNECTIONS
WARNING
BEFORE PERFORMING ANY WORK ON THIS EQUIPMENT,
POWER SUPPLY MUST BE TURNED OFF AT THE
HOUSEHOLD SERVICE BOX TO AVOID THE POSSIBILITY
OF SHOCK, INJURY, DAMAGE TO EQUIPMENT OR DEATH.
1. The power supply can be connected through the right side or top of the air handler. Conduit knockouts are provided for
1/2
”,
3/4
”, 1”, and 1
1/4
” conduit.
2. Refer to the Control System section for recommended lowvoltage wire gauges.
3. See Power Supply Table on page 9 for power supply specifications.
4. Use only copper conductors for supply wiring.
5. The air handler must be permanently grounded.
The ground lug is located in the field wiring box.
B
Framed-in
Opening
Air
Handler
Bottom
Conduit Knockout Locations
Top of air handler
Right side of air handler
MODEL
AFPB24A1
AFPB24B1
AFPB36A1
AFPC48A1
AFPC48B1
AFPC60A1
AFPC60B1
A
E
A B
IN CM IN CM IN
14 37.3 14 1 /
4
36.2 2
C
CM IN
5 2
D E F
CM IN CM IN CM
5 4 10.1 4 10.1
14 37.3 14 1 /
4
36.2 2
14 37.3 14
1
/
4
36.2 2
5 2
5 2
5 4 10.1 4 10.1
5 4 10.1 4 10.1
16
3
/
8
41.6 22
1
/
4
56.5 3 7.6
3 7.6 1
3
/
4
4.4
2 5
16
3
/
8
41.6 22
1
/
4
56.5 3 7.6
3 7.6 1
3
/
4
4.4
2 5
16
3
/
8
41.6 22
1
/
4
56.5 3 7.6
3 7.6 1
3
/
4
4.4
2 5
16
3
/
8
41.6 22
1
/
4
56.5 3 7.6
3 7.6 1
3
/
4
4.4
2 5
Return Air Platform Height
If the air handler is to be used in the upflow position, the height of the return air platform should be no smaller than the height listed below for the specific model of air handler.
Model
AFPB24A1, AFPB24B1
AFPB36A1
AFPC48A1, AFPC48B1
AFPC60A1, AFPC60B1
Platform
Inches
Height
Cm
12
14
16
18
30.5
35.6
40.6
45.7
Conduit knockouts
Grounding Lug Location
Field wiring box
(detail)
Grounding lug
Conduit knockouts
7
24 VOLT CONTROL SYSTEM
WARNING
BEFORE PERFORMING ANY WORK ON THIS EQUIPMENT,
POWER SUPPLY MUST BE TURNED OFF AT THE
HOUSEHOLD SERVICE BOX TO AVOID THE POSSIBILITY OF
SHOCK, INJURY, DAMAGE TO EQUIPMENT, OR DEATH.
WARNING
IMPROPER INSTALLATION OF THE ELECTRICAL WIRING
OR THE HEAT ASSEMBLY MAY RESULT IN FIRE, SERIOUS
PERSONAL INJURY, OR DEATH.
Connection to unit
Wire low voltage in accordance with wiring label on the blower.
Use no. 18 AWG wire to make the low voltage connections between the thermostat, the unit, and the outdoor equipment.
If the thermostat is located more than 100 feet from the unit use 16 AWG wire. All wiring must be NEC Class 1 and must be separated from incoming power leads.
The thermostat preheat anticipator should be adjusted to match the current listed below for the EEC model heat assembly to be installed.
THERMOSTAT
TYPE
SINGLE STAGE
TWO 1ST
STAGE 2ND
EEC HEATER MODEL
5 7.5
10
.4
N/A
N/A
.4
N/A
N/A
.4
N/A
N/A
15
.8
.4
.4
20
.8
.4
.4
When used with a heat pump, the heat output must be staged for models above 10 kW. W1 should be wired as auxiliary heat to assist the heat pump. W2 must only be wired as emergency heat. Both stages of heat should never be wired so as to be energized while the heat pump is operating. See the Blower
Speed/Static Table for maximum allowable auxiliary first-stage heat. All EEC series electric heat assemblies over 10 kW have breakers factory-installed on the heat assembly.
Transformer Information
The low-voltage transformer is equipped with a 208- or 230-volt tap. The transformer is factory wired for 230-volt operation. For
208-volt operation, remove the yellow wire from the 230-volt terminal and install it onto the 208-volt terminal.
The acceptable voltage range for each tap is as follows:
Tap Voltage Range
230
208
207 – 253
187 – 229
Time Delay Relay Information
A fan relay is provided to control the operation of the indoor fan motor. All models are equipped with a time delay “OFF”type fan relay which will allow the fan motor to continue to operate for a preset time after the relay is de-energized.
CONDENSATE DRAIN PLUMBING
CAUTION
For downflow, or any installation where condensate overflow could create a hazard or water damage, the emergency drain fitting MUST be used. The emergency drain MUST be left open. If the emergency drain has to be piped away from the air handler, its outlet MUST be installed in a location that would allow any drainage to be immediately noticed.
Install condensate drain trap as close to the coil as possible.
Use drain connection size or larger. Do not operate unit without trap (see illustration below.) Unit must be level or slightly inclined toward drain.
Condensate Drain Trap
2” MINIMUM
UNIT
DRAIN
CONNECTION
FLEXIBLE
TUBING-HOSE
OR PIPE
A POSITIVE LIQUID
SEAL IS REQUIRED
3” MINIMUM
CAUTION
1. Do not connect the drain line to a closed sewer.
2. Never terminate an open sewer or drain connection within the return air duct, platform or return plenum.
3. Pitch the drain line at least
1/4
” per foot away from the drain pan.
4. If condensate drain connection is on the negative side of the blower, a trap must be installed to ensure positive drainage.
5. Condensate drain lines should not be reduced in size from the connection size supplied.
6. The drain line should be insulated where necessary, to prevent sweating and damage due to condensate forming on the outside surface of the line.
7. Test condensate drain line with water before operating system.
8. If unit is located in or above a living space where damage may result from condensate overflow, a field supplied, external condensate pan should be installed under the entire unit, and a secondary condensate line
(with appropriate trap) should be run from the unit into the pan. Any condensate in this external condensate pan should be drained to a noticeable place. As an alternative to using an external condensate pan, some localities may allow the running of a separate
3/4
” condensate line (with appropriate trap) per local code to a place where the condensate will be noticeable.
8
11 Wiring Diagram
POWER SUPPLY TABLE
kW Phase No. of
230
VAC
Supply
Circuits
0
5*
10*
15*
20*
1
1
1
1
1
1
1
1
1 or 2
1 or 2
MBTUH
208/230
SINGLE CIRCUIT SUPPLY
Heat Min.
Max.
1
Wire
Size
1
Load Wire Fuse
Amps Ampacity Size AWG MM 2
Ground
1
Size
AWG MM 2
-
12.6 / 17.1
20.9
25.6 / 34.1
41.7
38.4 / 51.2
62.5
51.2 / 68.2
83.4
5.0
30
57
83
109
15
30
60
90
110
6
4
2
14
10
2.1
5.3
13.3
21.2
33.6
14
10
2.1
5.3
DUAL CIRCUIT SUPPLY
Min. Wire
1
Ampacity
Max. Fuse
1
Size
1
Ckt1
Ckt1 Ckt2 Ckt3 Ckt1 Ckt2 Ckt3 AWG MM 2
Wire Size
Ckt2
AWG MM 2
1
Ckt3
AWG MM 2
Ground Size
Ckt1
AWG MM 2
Ckt2
AWG MM 2
1
Ckt3
AWG MM 2
–
–
–
–
10
8
5.3
8.4
–
57
–
26
6 13.3
57 53
–
–
–
–
–
–
–
–
60
60
–
–
–
30
60
–
–
–
–
–
–
–
–
–
–
–
6 13.3
6 13.3
–
–
–
–
–
–
10 5.3
6 13.3
–
–
–
–
–
–
–
–
–
–
–
–
–
–
–
–
–
–
–
10 5.3 10
10 5.3 10
–
–
–
5.3
5.3
–
–
–
–
–
–
–
–
–
–
*kW does not include motor watts.
Minimum wire ampacity values are used for sizing field power conductors. Refer to the National Electrical Code (latest version), Article 310, for sizing conductors. When more than three current-carrying conductors are in the same conduit, the conductor’s ampacity MUST be derated. See Note 8 of Table 310 for ampacity adjustment factors.
1
Maximum size fuse or HACR-type circuit breaker for field wiring protection.
9
Dimensions
H
G
OUTLET OPENING
F
LOW VOLT CONNECTIONS
LINE VOLTAGE KNOCK OUTS
LOW VOLT CONNECTIONS
I
E
D
C
B
A
J
INLET WIDTH
All dimensions in inches
Models A B C D E
AFPB24A1 2 1/4 3 5/8 13 1/4 15 1/4 43 3/8
AFPB24B1 2 1/4 3 5/8 13 1/4 15 1/4 43 3/8
AFPB36A1 2 1/4 3 5/8 13 1/4 15 1/4 43 3/8
AFPC48A1 2 1/4 3 5/8 13 1/4
AFPC48B1 2 1/4 3 5/8 13 1/4
AFPC60A1 2 1/4 3 5/8 13 1/4
AFPC60B1 2 1/4 3 5/8 13 1/4
15
15
15
15
F
15
15
15
48 1/8 19 1/8
48 1/8 19 1/8
48 1/8 19 1/8
48 1/8 19 1/8
G
17
17
17
21
21
21
21
K
INLET WIDTH
H
22
22
22
26
26
26
26
I
18
18
18
22
22
22
22
J
14
14
14
K
16 1/4
16 1/4
16 1/4
16 3/8 22 1/4
16 3/8 22 1/4
16 3/8 22 1/4
16 3/8 22 1/4
10
Motor Speed
Correct heating and cooling motor speeds MUST be used for proper operation. Refer to the Blower Speed/Static Operation Table below for correct cooling speed and for minimum allowable heating speed.
BLOWER SPEED / STATIC OPERATION TABLE
UNIT
MOTOR
SPEED
RESISTANCE HEAT
STATIC PRESSURE (IN. WC) ACROSS
HEAT ELEMENT @ MAX. CFM
RESISTANCE
HEAT ONLY
AUXILIARY HEAT STAGED
WITH HEAT PUMP
15 kW @ 0.20" 10 kW @ 0.15" HIGH
AFPA24A1
MEDIUM
LOW
15 kW @ 0.20"
10 kW @ 0.15"
5 kW @ 0.15"
N/A
AFPA24B1
HIGH
MEDIUM
LOW
AFPB36A1
HIGH
MEDIUM
LOW
HIGH
AFPC48A1
AFPC48B1
MEDIUM
LOW
AFPC60A1
AFPC60B1
HIGH
MEDIUM
LOW
15 kW @ 0.20"
15 kW @ 0.20"
10 kW @ 0.15"
20 kW @ 0.25"
20 kW @ 0.20"
20 kW @ 0.15"
*20 kW @ 0.60"
*20 kW @ 0.50"
*20 kW @ 0.40"
*20 kW @ 0.60"
*20 kW @ 0.50"
*20 kW @ 0.35"
10 kW @ 0.15"
5 kW @ 0.15"
N/A
10 kW @ 0.15"
10 kW @ 0.15"
N/A
15 kW @ 0.45"
15 kW @ 0.40"
15 kW @ 0.40"
15 kW @ 0.45"
15 kW @ 0.40"
15 kW @ 0.35"
1440
1240
2230
1950
1360
1440
1300
1160
1680
.2
925
800
655
905
785
645
1410
1220
2105
1930
1350
1350
1220
1070
1640
60 Hz OPERATION
CFM @ EXTERNAL DUCT STATIC (IN. WC)
.3
.4
.5
900
760
625
880
735
615
850
745
600
830
730
590
795
670
N/A
780
655
N/A
1380
1190
1990
1840
1340
1260
1050
950
1590
1340
1150
1895
1770
1185
1180
940
880
1520
1250
1100
1725
1590
1040
860
780
1430
.6
690
N/A
N/A
680
N/A
N/A
1080
*Specifications applicable to upflow and horizontal applications
Air flow shown at the following conditions:
• No heat elements in air handler
• Decrease CFM 1% for 5 kW, 7.5 kW, or 10 kW heat kits. Decrease CFM 2% for 15 kW or 20 kW heat kits
• 60 Hertz — 230 volts. Decrease CFM 6% for 208 volt operation
• Standard air handler filter.Dry coil airflow shown
11
ELECTRIC HEATER KIT
This unit is not equipped with an electric heater kit. A factory approved, field installed UL listed heater package is available from your equipment supplier. Heaters that are not factory approved could cause damage which would not be covered under the equipment warranty.
Installation
Only EEC series electric heat assemblies may be installed into the air handler. Consult installing contractor for the correct electric heat assembly to be installed in each model of air handler.
For ease of installation, it is recommended that the electric heat kit be installed before the furnace plenum is installed.
WARNING
BEFORE PERFORMING ANY WORK ON THIS EQUIPMENT,
POWER SUPPLY MUST BE TURNED OFF AT THE HOUSEHOLD
SERVICE BOX TO AVOID THE POSSIBILITY OF SHOCK,
INJURY, DAMAGE TO EQUIPMENT, OR DEATH .
1. Remove the upper access door from the air handler.
2. Remove and discard the field wiring compartment box by removing the screws that attach it to the right side of the air handler.
5. Cut the wire tie holding the heater plug and unroll the heater plug harness so that it will hang out of the electrical box.
Heater plug
Remove two screws
Remove air handler field wiring box and discard
3. The black and yellow high voltage transformer leads should be connected to the terminal block or breaker of the heat kit.
4. From the electrical compartment, remove the cover plate from the element housing.
Remove cover plate
6. Carefully slide the heat assembly into the element opening. Be sure the heater kit or elements do not rub or scrape against the metal edges or existing components in the electrical box. Guide the element support rods into the matching holes in the blower boot.
7. Make sure the assembly is bottomed out against the element housing. Install the screws provided through the assembly and into the element housing.
8. Connect the heater plugs to the heater receptacles.
9. Slide heater element in and secure with three screws. Attach wires according to wiring diagram on page 9.
Guide the element support rods into the matching holes in the blower boot
Heater receptacle
12
AIR HANDLER NOMENCLATURE
MODEL
SERIES
DESIGN
SERIES
A 24 C 1
HEATING SPECIFICATIONS
NOMINAL EVAPORATOR
BTUH DESIGNATION
ELECTRIC HEAT ASSEMBLY NOMENCLATURE
EE C 15 B 1
*A
ELECTRIC HEAT
ASSEMBLY SERIES
DESIGN
SERIES k-WAT
230 VOLTS
B=BREAKER
N= NO BREAKER
1 = 1 PHASE REVISION
HEATING TEMPERATURE RISE
Formula:
Temp. Rise °F =
3160 x kW
CFM
3160
= CONSTANT kW = kW RATING OF UNIT
CFM = AIR FLOW AT SPECIFIED CONDITIONS
Based on 230-volt operation. For voltage other than 230, multiply temperature rise by capacity correction factor. Refer to CFM tables to determine Cfm at total external static pressure in system.
TEMPERATURE RISE °F
CFM
3
19
16
1300
1400
1500
1600
1700
1800
1900
2000
2100
500
600
700
800
900
1000
1100
1200
5
32
26
TOTAL kW
10 15
40
35
32
29
26
43
40
36
34
68
59
53
47
32
30
28
26
25
49
45
42
39
70
63
57
53
37
35
33
32
30
HEATING CORRECTION FACTOR
260
250
240
230
220
210
200
.7
.8
.9
1.0 1.1
CAPACITY CORRECTION
FACTOR
For correction of unit output, multiply the correction factor times the kW rating at 230 volts.
For correction of temperature rise, multiply the correction factor times the rise calculated for the kW at 230 volts.
20
13
LIMITED WARRANTY
LIMITED FIVE YEAR WARRANTY:
Fedders will provide a replacement part or component that proves to be defective in material or workmanship.
WARRANTY LIMITATIONS:
• Limited Warranty does not include allowances for labor or travel expense connected with the installation of parts, so furnished in this Limited Warranty or for field repair, or servicing of the equipment, nor for refrigerant used
• For warranty purposes the purchase date is established by a proof of purchase. If a proof of purchase can not be verified, then warranty period will be measured from the date of manufacture plus 6 months.
• Cost of repair or replacement of consumable parts is not covered under the terms of this warranty
• Replacement parts are warranted only for the balance of the original warranty period
• Applies only to original installation and normal use and service within the 48 contiguous United States, District of Columbia and Canada
• Applies to service performed by an authorized servicer
WARRANTY IS VOID IF:
• Serial plate is defaced
• Product has defect or damage due to product alteration, connection to an improper electrical supply, shipping and handling, fire, flood, lightning or other conditions beyond the control of Fedders
• Product is not installed according to Fedders’ instructions and specifications
• Product is operated in a corrosive environment containing concentrations of corrosive agents causing deterioration of components
• Product is operated with indoor unit or refrigerant control device that does not meet Fedders’ specifications
• Product is moved from original installation site
• Filters are not changed per manufacturer’s reccomendation
OWNER’S RESPONSIBILITIES:
• Provide proof of purchase (sales receipt)
• Provide normal care and maintenance as outlined in this manual
• Make product reasonably accessible for service
• Pay for freight, labor and travel expenses
• Pay for premium service costs for service outside servicer’s normal business hours
• Pay for service calls related to product installation and maintenance
THIS WARRANTY DOES NOT COVER DAMAGE
CAUSED BY:
• Improper installation
• Misuse of equipment
• Negligent servicing
• Improper applications
• Preventative maintenance
• Unauthorized modifications
• Improper electrical supply
• Failure to follow manufacturer’s instructions and rating plate information
• Accidents or other events beyond Fedders’ control
ENTIRE WARRANTY:
THE ABOVE CONTAINS THE SOLE AND EXCLUSIVE
STATEMENT OF THE EXPRESS WARRANTIES AND
ASSOCIATED REMEDIES AVAILABLE WITH THE
PRODUCTS DESCRIBED. NO OTHER EXPRESS
WARRANTIES ARE MADE. ALL IMPLIED
WARRANTIES, INCLUDING BUT NOT LIMITED TO
ANY IMPLIED WARRANTY OF MERCHANTABILITY
OR FITNESS FOR A PARTICULAR PURPOSE, OR
IMPLIED WARRANTIES OTHERWISE ARISING FROM
COURSE OF DEALING OR USAGE OF TRADE ARE
LIMITED IN DURATION TO ONE YEAR FROM THE
DATE OF ORIGINAL PURCHASE. IN NO EVENT SHALL
FEDDERS BE LIABLE FOR ANY INDIRECT,
INCIDENTAL OR CONSEQUENTIAL DAMAGES, EVEN
IF ADVISED IN ADVANCE OF THE POSSIBILITY OF
SUCH DAMAGES. NO WARRANTIES, EXPRESS OR
IMPLIED, ARE MADE TO ANY BUYER UPON RESALE.
SOME STATES DO NOT ALLOW LIMITATIONS ON HOW
LONG AN IMPLIED WARRANTY LASTS OR DO NOT
ALLOW THE EXCLUSION OR LIMITATION OF
INCIDENTAL OR CONSEQUENTIAL DAMAGES, SO THE
ABOVE LIMITATIONS MAY NOT APPLY TO YOU. THIS
WARRANTY GIVES YOU SPECIFIC LEGAL RIGHTS, AND
YOU MAY ALSO HAVE OTHER RIGHTS, WHICH MAY
VARY FROM STATE TO STATE. NO WARRANTIES ARE
MADE FOR UNITS SOLD OUTSIDE THE ABOVE STATED
AREAS. YOUR DISTRIBUTOR OR FINAL SELLER MAY
PROVIDE A WARRANTY ON UNITS SOLD OUTSIDE OF
THESE AREAS.
14
The information in this manual supersedes and replaces the previous instruction/operation manual with regards to air handler products. Illustrations cover the general appearance of the units at the time of publication and the manufacturer reserves the right to make changes in design and construction at any time without notice.
For replacement parts, please consult the installing dealer or contractor.
Fedders Corporation
505 Martinsville Rd.
Liberty Corner, NJ 07938 www.fedders.com
REV. 7/06 23-23-0403N-013
advertisement
Related manuals
advertisement
Table of contents
- 2 SERIES NOMENCLATURE
- 3 INTRODUCTION
- 3 INSPECTION AND UNPACKING
- 3 NOTES TO INSTALLER
- 3 INSTALLATION
- 3 Codes
- 3 Power Considerations
- 3 Electric Heat Kits
- 3 Location
- 3 Clearances
- 4 Upflow Application
- 5 Horizontal Applicaton
- 6 Downflow Application
- 7 Connect Refrigerant Piping
- 7 Factory and Field installed Expansion Valves
- 8 Ductwork
- 8 Return Air Ducting
- 8 Return Air Platform Height
- 8 LINE VOLTAGE CONNECTIONS
- 9 24 VOLT CONTROL SYSTEM
- 9 CONDENSATE PLUMBING
- 10 WIRING DIAGRAM
- 11 DIMENSIONS
- 12 BLOWER SPEED/STATIC OPERATION TABLE
- 13 ELECTRIC HEAT KIT
- 14 Heating Specifications
- 15 WARRANTY