advertisement
▼
Scroll to page 2
of
28
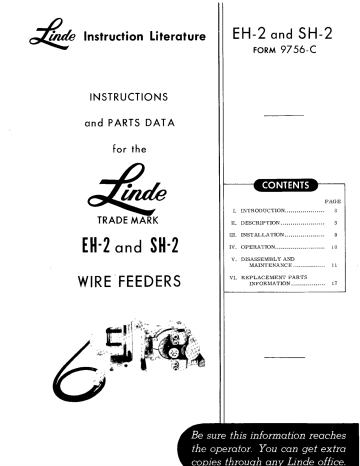
inde Instruction Literature EH-2 and SH-2 FORM 9/56-C INSTRUCTIONS and PARTS DATA for the inde PAGE I. INTRODUCTION. ..coorecaronencons 3 TRADE MARK I DESCRIPTION cree 3 Ш. INSTALLATION ,...onconoronocnonos 8 FH-? and SH-7 IV, OPERATION.....ccccccccececseeteee: 10 V. DISASSEMBLY AND MAINTENANCE ..,..,......... 11 Cr VI. REPLACEMENT PARTS INFORMATION uses 17 Be sure this information reaches the operator. You can ı get pit fe 2 The terms LINDE, UNIONARC, UNIONMELT, and SIGMA are registered trade marks of Unton Carbide Corporation. Instruction Literature INSTRUCTIONS and PARTS DATA for the inde TRADE MARK EN-2 and SH-2 WIRE FEEDERS EH-2 and SH-2 FORM 9/56-C IX, Ш. ГУ. УТ. РАСЕ INTRODUCTION. sinus. 3 DESCRIPTION... ren 3 ПЧ5ТАСГАТЮМ ....,.. зе еьанань» 8 OPERATION... 10 DISASSEMBLY AND MAINTENANCE... 11 REPLACEMENT PARTS INFORMATION... 17 Be sure this information reaches the operator. You can get extra 2 The terms LINDE, UNIONARC, UNIONMELT, and SIGMA are registered trade marks of Union Carbide Corporation. E AR n INSERT FOR FORM 930 AND FORM 9756 REVISED INSTRUCTIONS FOR LUBRICATING THE WIRE FEEDER The following information replaces previous instructions in Form 930 page 16 paragraph M and Form 9756 page 8 paragraph B. Tubes of lubricant, Part No. 29N62, are supplied with each wire feeder and should be used as follows: TO LUBRICATE WORM SECTION i. Use Linde lubricant, Part No. 29N62. Orient units so that motor and feed roll shaft are in a horizontal plane.. Remove the dip stick plug from the top of the gear reduction unit, Figure 13 in Form 930 or Figure 6 in Form 9756. Put the entire contents of one tube of Linde lubricant, Part No. 29N62 into the worm section. Replace and tighten the dip stick plug. NOTE: When the wire feeder is positioned with the axis of the output shaft vertical, it will be necessary to use two tubes of Linde lubricant, 29N62, in this section of the gear head. The breather plug should be interchanged with either of the two drain plugs located on the bottom of the gear case so that the breather will be positioned on the top side of the gear head when in use. TO LUBRICATE SPUR GEAR SECTION 1, De Use Linde lubricant, Part No. 29N62. Orient the unit so that the motor and feed roll shafts are in a horizontal plane. Remove the spur section filler plug. Put the entire contents of one tube of Linde lubricant, Part No. 29N62 into the spur gear section. Replace and tighten the filler plug. COLD WEATHER OPERATION Where the wire feeder is to be used at temperatures near or below freezing, Linde lubricant 29N63 should be used instead of Linde lubricant 29N62. Pour 3 Fluid ounces into the worm gear section and also into the spur gear section. NOTE: With the wire feeder positioned with the axis of the output shaft vertical, insert Y fluid ounces of lubricant in the worm section, and 3 fluid ounces in the spur gear section. CHECKING LUBRICANT LEVEL The head must be in the normal upright position as shown in Figure 13.in Form 930 and Figure 1 in Form 9756, in order to check the ‘‘lubricant. level. 1. When the spur section indicator plug is removed, the lubricant level should reach to approximately the middle of the plug hole and thus overflow through the plug hole. Add lubricant whenever the level falis below the plug hole. 2. ‘The level of the lubricant in the worm section is checked by means of the dip stick. Proceed as follows: (a) Remove the dip stick plug and wipe the dip stick. (b) Re-insert the dip stick plug with the bottom of the plug resting on the outside of the gear housing. Do not screw in the plug. (c) Remove the dip stick plug and note the lubricant level on the dip stick. | For normal operation, the level should reach approximately 3-3/8 inches from the bottom of the dip stick plug. Where the head is to be operated with the output shaft vertical, the tube level should reach to 2-3/16 inches from the bottom of the dip stick plug. (4) Replace or tighten the dip stick plug. NOTE: The level of Linde's lubricant 29N62 can not be determined immediately after inserting the lubricant because the lubricant does not always level out quickly. The lubricant will level out after the head has been in service for a short period and then allowed to drain to the bottom of the case. LINDE COMPANY” — AS Division of Union Carbide Corporation. _ Multilith in U.S.A. IMD- J-8562-60 F-9756 I. Introduction The purpose of this booklet is to present the information needed to set up, cperate, and maintain the LINDE EH-2 and SH-2 Wire Feeders. This booklet is not concerned with welding techniques or procedures. In any welding job, the greatest degree of flexibility and versatility can be gained only through the proper selection and use of the many items of available equipment. The EH-2 and SH-2 Wire Feeders, when used with various UNIONMELT accessory items in electric welding processes, are termed as the UEH-2 and USH-2 Welding Heads respectively. A modified EH-2 wire feeder is used with the UAM-1 UNIONARC welding machine. The feed roll shaft for this wire feeder extends through the gear reduction unit and is used to drive a magnetic drum in the flux dispenser, through a gear and clutch arrangement. Bearing and cap assembly ''C" (see Figure 7) has been changed to accommodate the lengthened feed roll shaft. In addition, different feed rolls are used for the wire sizes employed in UNIONARC welding (See F-9812). The wire feeder for the UNIONARC welding ma- chine does not use the standard EH-2 mounting clamp, but is fastened toa mounting plate on the machine by the tapped lugs onthe gear reductionunit. For your convenience, this booklet will describe only the wire feeders. Additional equipment is treated in detail in the instruction booklets listed in the table below. High speed EH-2 wire feeders for SIGMA welding canbe ordered separately or as part of a complete SEH-2 welding head assembly consisting of the wire feeder, a three roll straightener, a wire straightener exten- sion, a straightener adaptor, an argon and water hose connection block assembly, and a connection block mounting bracket. See F-930 for complete details on the Sigma wire feeders. Equipment Form No. Title Mounting Components, Wire Handling Equip- F-9758 Instructions and Parts Data for UNIONMELT Ac- ment, Composition Handling Equipment, cessories for EH-1, EH-2, and SH-2 Wire Guiding Devices Feeders Gear Adjustable Mounting Clamp F-9910 | Installation Instructions for Gear Adjustable Mounting Clamp for use with EH-2 and 5H-2 Wire Feeders, Busbar and Contact Nozzles, Busbar and Con- F-9784 Instructions and Parts Datafor Busbar and Con- tact Jaws, Deep-Groove Nozzles, Dual- tact Jaws and Nozzles for EH-1, EH-2, and Wire Nozzles SH-2 Wire Feeders "US" Series Voltage Control F-9414 | Instructions for the "US" Series Voltage Con- trol (Series 4 and 5) USC-4 Series Voltage Control F-97957 Instructions and Parts Data for the USC-4 Series Voltage Control | UCC-3 Constant Feed Control F-9673 Instructions and Parts Data for the UNIONMELT UCC-3 Constant Feed Control CM-37 Machine Carriage #-9110 | Instructions for the CM-37 Machine Carriage OM -48 Side-Beam Carriage F-9160 | Instructions and Parts Data for the LINDE OM- 48 (Series 5) Side-Beam Carriage UAM-1 UNIONARC Welding Machine F-9812 | Instructions and Parts Data for the LINDE UAM-1 UNIONARC Welding Machine SEH-2 Welding Head F-930 Instructions and Parts Data for the LINDE SEH-2 Welding Head И. Description A. The Wire Feeder mounted ona gear reduction unit which has a wire The H-2 Wire Feeder (EH-2 and SH-2) is the basic feed roll mounted on its output shaft. Knurled feed drive mechanism which when used with various ac- roll 28V53 (2-in. dia.) is used for welding wires from cessory equipment in electric welding processes, 3/32 through 3/16-in. diameter. Flat serrated feed. feeds welding wire to the weld zone at controlled roll assembly 28V 67 (1.72-in. Ча.) is used for 1/4- rates. Each feeder is composed of four basic units: in, dia. wire. When this feed roll is used, the flat the wirefeed motor, the gear reduction unit, the pres- pressure roll 28V52 should be replaced by grooved sure roll and accessory support assembly, and the pressure roll 323009 to prevent the wire from riding mounting clamp. See Figures 1 and_2. off the roll. Wire feed speeds will be somewhat lower with the smaller diameter feed roll, The gear The only difference between the EH-2 and SH-2 is reduction unit consists of two sections of gearing, in the type of motor used to provide the initial power which reduce the output speed of the motor to that for feeding welding wire. The EH-2 is constructed required at the feed roll. The first section consists with a special d.c. shunt motor, designed especially of three stages of spur gears, the second section for constant potential applications. The SH-2 Wire consists of a worm and worm gear which drive the Feeder employs a 32-volt universal motor, designed feed roll shaft. for arc voltage control applications. The EH-2 is used with the UNIONMELT UCC-3 Constant Feed Controi orin the case of UNIONARC welding with the UACC-4 Constant Feed Control; while the SH-2 is used with either the USC-4 Arc Voltage Control or the "US" Control in UNIONMELT welding. Á spring-loaded pressure roll in the pressure roll and accessory support assembly, provides the back- up force necessary for positive, non-slip wire feed. The accessory support assembly also provides mount - ing facilities for a wire straightener, and contact noz- zles and jaws, and allows angular adjustment of these The outward appearance and construction of the two items in the plane of the feed roll. wire feed motors is exactly the same. The motor is WIRE FEED MOTOR GEAR REDUCTION UNIT FEED ROLL (ACCESSORY) PRESSURE ROLL AND ACCESSORY SUPPORT ASSEMBLY MOUNTING CLAMP FIG. 1 — LINDE EH-2 and SH-2 Wire Feeder MOUNTING CLAMP (4)"0" RING (4) LOCK WASHER FEED MOTOR ww CAPSCREW “8 “ a; O O 2) mma ‘(7 GEAR REDUCTION UNIT CAPSCREW “4” PRESSURE ROLL AND ACCESSORY SUPPORT NOTE: ASSEMBLY SPUR GEARING NOT {LLUSTRATED FIG. 2 — Basie Units of EH-2 and SH-2 Wire Feeder Assemblies The mounting clamp provides a sturdy support for the wire feeder and permits revolving the wire feeder around the axis of the motor shaft. The setup flexi- bility provided by this mounting clamp in combina- tion with the pressure roll and accessory support assembly, makes it possible to position the nozzles and jaws at almost any angle with respect to the work- piece. For positioning eltner wire feeder during weld - ing,a gear adjustable mounting clamp which permits handwheel rotation of the wire feeder is available on special order under Part No. 376777. B. Where the EH-2 and SH-2 are Used Both wire feeders can be used in either stationary or mechanized installations. Ina stationary installation, provisions are made for moving the work under the welding setup, while in mechanized installations, the wire feeder and its welding accessories are mounted on a motorized carriage which moves over the work. A wide variety of mounting components are available for installing the EH-2 and SH-2 Wire Feeders. Stand - ardization of mountings and associated hardware pro- vides awide range of possible combinations. Figures 3 and 4 illustrate typical mechanized setups. In Fig- ure 3, the EH-2 is mounted onthe LINDE OM -48 Side- Beam Carriage, while Figure 4 illustrates the SH-2 Wire Feeder mounted on the LINDE CM-37 Machine Carriage. Full details and installation instructions for mounting the wire feeders can be found in Form 9758, “Instructions and Parts Data for UNIONMELT Accessories for EH-1, EH-2, and 5H-2 Wire Feeders," | + C. Operating Features The EH-2 and 5H-2 medium duty wire feeders ac- commodate wire sizes up to 1/4-in. in diameter and welding currents up to 1200 amperes, Each contains built-in insulation which makes them ready to use in high-frequency applications. THE EH-2 WIRE FEEDER The EH-2 Wire Feeder is available in three separate speed ranges: the "low speed” 8 rpm; the “medium speed” 12 rpm; and the "standard speed” 27 rpm., Maximum output speeds of the feeder can be altered by changing the spur gears, the worm and worm gear in the last stage,or both. Detailed instructions for changing speeds are, given in Section V, Para- graph B-2. EH-2 wire feeders for use withthe UAM-1 UNIONARC welding machine are supplied in two speed ranges. A 42 rpm wire feeder (Part No. 34V10, 95:1 gear ratio) is used for feeding 3/32-in. welding wire. By simply changing the feed roll, nylon inserts for the wire guides, flexible conduit and torch guide tube, this wire feeder may be used to feed 3/64-in. wire. A high-speed, 74 rpm wire feeder (Part No. 34V09, 54:1 gear ratio) is used for feeding 3/64-in. wire only. This wire feeder may be altered to obtain the 95:1 gear ratio by changing the spur gears in the first gear reduction section. Detailed instructions for changing speeds are given in Section V, Paragraph F-9756 B-2. Welding currents to be used with these wire feeders'are given in Section II, Paragraph D of the UAM-1 Instruction Booklet, F-9812. The welding currents and wire sizes most generally used for a specific welding application, will deter - mine what speed wire feeder to use. Table I lists the recommended currents for each wire size to be used with the EH-2 Wire Feeders TABLE I RECOMMENDED CURRENTS FOR EH-2 WIRE FEEDERS Welding Current - Amperes* Low Medium standard Wire Speed Speed Speed Diameter (8 rpm) (12 rpm) (27 rpm) (inches) 28V08 28V 10 28V 12 3/32 250 350 | 600 1/8 450 600 1000 5/32 650 900 1200 3/16 850 1150 жж 1/4 1200 жж жж *Current values ore maximum values. Minimum values are approximately ane-half maximum. No load speeds shown. **Not recommended. THE SH-2 WIRE FEEDER The SH-2 Wire Feeder is available inthree separate speed ranges: the "standard speed” 12 rpm; the "medium speed''18 rpm; and the "high speed” 41 rpm. An additional "high speed" 30 rpm wire feeder is available on special order, The maximum output speeds can be altered by changing the spur gears in the first reduction stage, the worm and worm gear in the last stage, or both, Detailed instructions on the changing of gears are given in Section V, Paragraph B-2. The welding currents and wire sizes most generally used for a specific welding application, will deter - mine what speed SH-2 to use. Table I lists the rec- ommended welding currents for each size wire to be used with the SH-2 Wire Feeders, TABLE Ii RECOMMENDED CURRENTS FOR THE SH-2 WIRE FEEDERS Welding Current - Amperes Standard | Medium | High T High Wire Speed Speed Speed Speed Diameter | (12 rpm) [(19 rpm) | (30 rpm) | (41 rpm) (inches) 28V07 28V09 28V81 28V11 3/32 290 390 925 700 1/8 300 679 975 1200 5/32 700 850 1200 A 3/16 950 1200 A A 1/4 1200 A A A @ Current valves are maximum values and are based on a welding voltage of 32 valts. These values do not apply at other voltages. At 25 volts the maximum currents will be about 20% below those listed. Minimum currents are approximately one-half of maximum. No-foad speeds are shown. À Not recommended. T Available on special order only. SLIDE ADJUSTMENT ASSEMBLY(VERTICAL) LARGE EA > EH-2 WIRE FEEDER METER BOX WIRE STRAIGHTENER UCC-3 CONTROL HOPPER N COMPOSITION ELECT. GOV. FOR OM-48 MOUNTING (OPTIONAL) SLIDE ADJUSTMENT ASSEMBLY (HORIZONTAL) BUSBAR & CURVED NOZZLE ASSEMBLY FIG. 3 - EH-2 Wire Feeder in Typical OM-48 Installation F-9756 Both the EH-2 and SH-2 Wire Feeders are obtain- above, the wire feeder is designated as a right-hand able with either left- or right-hand feed. When viewed wire feeder. (Figure 2 is an exampleof a right-hand from the motor end of the assembly, with the dip stick unit; Figure 3 illustrates a left-hand wire feeder.) and vent and filler holes of the gear reduction unit on top (see Figure 6), a left-hand unit has the feed roll shaft extending out of the left side of the gear umt, With the feed roll shaft extending out of the right side of the unit under the same conditions as A left-hand feeder can be converted to a right-hand feeder, and vice versa, by disassembling the gear re- duction unit and reversing the order of assembly. For instructions covering such conversion, refer to Section V, Paragraph B-3, VERTICAL ADJUSTMENT SLIDE . | UNIT SUPPORT WIRE REE A SN REEL ARM A PIVOT BRACKET SH-2 WIRE FEEDER WIRE STRAIGHTENER er HORIZONTAL A = ADJUSTMENT | SLIDE LIFTING HOOK BL Pf TURRET e | Fe we ut On A | HOPPER Al “we | a Eu Shah, @ SUPPORT м ПАРТОВ, FEED ROLL BUSBAR & STRAIGHT NOZZLE ASSEMBLY ROCKER HINGE de Ts Bee BeBe EOE ROT Te (tl. Installation A. Mounting the Wire Feeder The EH-2 and SH-2 Wire Feeders are mounted by means of the mounting clamp which is an integral part of each wire feeder assembly. They can be mounted on any of the stanaard mounting accessories (see F-9758), or on any flat surface. They can be mounted either horizontally (motor-gear unit axis horizontal) or vertically (motor-gear unit axis ver- tical). Vertical mounting where the gear unit is above the motor is not recommended, however. The mount- ing clampcan be rotated a full 360-degrees about the wire feeder, providing an unlimited number of pos- sible mounting positions. Once mounted, the wire feeders can be rotated within the clamp a maximum of 90° either side of vertical. See Figure 5 for further information regarding the limits to which the wire feeder can be rotated within the mounting clamp and still provide adequate gear lubrication under normal conditions, Installation instructions for gear~adjustable mounting clamp 376777 are included in F-9910 which is supplied with the mounting clamp. B. Lubricating the Wire Feeders Neither the EH-2 or SH-2 Wire Feeder is lubricated when shipped. They must be lubricated therefore, before any Operations are started. Separate con- tainers of greaseare supplied with each wire feeder. When the gear reduction unit is used inother than the normal position, in which the feed roll shaft extends horizontally to the right or left, additional grease will be required in the worm gear section to fill the cav- ities formed at the bearing caps. The lubrication procedure is as follows: + » .. 2, Wo pene PTT eq Fr ER mofo 90° ee nd . 90° q FIG. 5 — Rotation of EH-2 and SH-2 Within Mounting Clamp - To Lubricate the Worm Section i. Use the Socony Vacuum Gargoyle MC Medium Grease supplied. 2. Orient unit so that motor and feed roll shaft are in a horizontal plane. 3. Remove the dip stick from the topof the gear re- duction unit (Figure 7), and slowly pour in the grease, Fill until the grease line is approximately 3-3/4-in. from the bottom of the dip stick plug. This measurement should be made with the bottom of the dip stick pipe plug resting on the outside of the housing, not screwed in place. 4. Secure the dip stick in its receptacle. NOTE: For feeder positioned with shaft up or shaft down, follow instructions as above, but fill until the grease line is appraxi- mately 2-1/8 in. from the bottom of the dip stick plug. The breather plug should then be interchanged with either of the two drain plugs (located on the bottom of the gear case) so that it will be positioned on the top side. To Lubricate the Spur Section 1. Use the Socony Vacuum Gargoyle MC Medium Grease supplied. 2. Orient unit so that motor and feed roll shaft are in a horizontal plane. 3, Remove the spur section indicator plug in the side of the gear housing and the spur section filler plug _ on the top of the gear housing. (See Figure 6.) 4, Insert the grease from the top of the gear unit until it begins to overflow through the plug hole in the side of the housing. 5. Replace both plugs and tighten in place. C. Installation of Auxiliary Equipment 1. The Wire Feed Roll In most cases it is necessary torelieve the pressure on the pressure roll before installing the feed roll. Simply back off the pressure adjusting screw of the pressure roll and accessory support assembly, il- lustrated in Figure 10. Knurled feedroll 28V53 (3/32 through 3/16-in. wire) is installed as follows: a, Unscrew the iocknut on the end of the feed roll shaft and remove the steel washer. See Figure 6. b. Slide the feed roll onto the shaft so that the key- way in the roll engages the key in the feed roll shaft. Position the feed roll square with and flush against the feed roll positioning nut. с. Replace the washer and tighten the locknut. For feed roll assembly 28V67 (1/4-in. wire), first slide the insulating bushing on the feed roll shaft. Position the feed roll on the shaft and follow with the insulating washer, Replace steel washer and tighten the locknut. 2. The Wire Straightener The wire straightener is treated in detail in F-9758, Instructions for Welding Accessories. To install on either the EH-2 or SH-2 Wire Feeder, insert the tubular end of the straightener into the appropriate clamp of the pressure roll and accessóry support assembly. Rotate to the position desired and secure by tightening the two capscrews 'B" in the clamp as shown in Figure 10. 3. Busbar and Nozzles or Jaws The various combinations of busbar and nozzles and jaws that can be used with the EH-2 and 5H-2 Wire Feeders are treated in detail in F-9784, "Instructions for Busbar and Nozzle and Jaw Assemblies."’ To in- stall, insert the busbar adaptor of the busbar and nozzle (jaw) assembly (wire guide inthe case of dual- wire assemblies), into the appropriate clamp of the pressure roll and accessory support assembly, until the shoulder on the busbar adaptor (wire guide for dual-wire) contacts the bottom of the clamp. Rotate F-97536 to the position desired and secure by tightening two capscrews 'B" in the clamp. See Figure 10. 4. Guiding Devices Complete information, including installation instruc - tions, can be found in F-9758, 'Instructions and Parts Data for UNIONMELT Accessories for EH-1, EH-2, and SH-2 Wire Feeders." 5. Composition Handling Equipment Complete information, including installation instruc- tions, can be found in F-9758. 6. Control Equipment Complete information, including trouble shooting pro- cedures, can be found in the following: For EH-2 Wire Feeder - UCC-3 Constant Feed Control, F-9673 For SH-2 Wire Feeder - USC-4 Voltage Control, F-9757 Installation instructions can be found in F-9758 for both the UCC-3 and USC -4, WORM SECTION DIP STICK SPUR SECTION INDICATOR PLUG Г SPUR SECTION FILLER PLUG "O "RING NOTE -- FEED ROLL POSITIONING мл— TF (INCLUDES SETSCREW) SPUR GEARING NOT ILLUSTRATED WORM SECTION VENT PLUG CAP AND BEARING ASSEMBLY "4" (6) CAPSCREW ACCESSORY SUPPORT INSULATOR INSULATOR DISC (3) MACHINE SCREW 2: FEED ROLL KEY . WASHER LOCKNUT FIG. 6 — Partial Breakdown of Gear Reduction Unit IV. Operation A. Safety Precautions As in all electric welding apparatus, there are cer- tain exposed parts of the welding installation at the welding voltage potential. At times even the higher open circuit voltage may be present. Though this is never more than 115 volts, remember that it is the Same as ordinary house-lighting voltage, with which the average person avoids all contact. Under con- ditions of low body resistance, such as when a person is perspiring and is in contact with a grounded steel plate, this voltage may force enough current through the body to be fatal, For this reason and because a shock, even though harmless in itseif, may lead to other injuries due tothe uncontrolled physical reac- tion, the operator should be aware of the live parts of the machine and follow safe operating procedures. Every operator should read and observe the recom- mended operating procedures and precautionary in- formation. 1. Never touch the following parts of the installation when the welding current Contactor Switch is in the ‘‘ON”’ position: Busbar Welding Tip Wire Feed Roll and Pressure Roll Assembly Welding Wire . Wire Reel Wire Straightener . Anyuninsulated metallic portions of theinstal- lation which come in contact with the welding wire. 2, Turn off the Contactor Switch when welding opera- tions are discontinued for any length of time. In the EH-2 or 5H-2 Wire Feeder installation, weld- ing action is generally stopped by throwing the wire feed switch tothd ‘‘OFF’’ or neutral position. This does not turn off the open circuit voltage, and the operator can receive a shock from touch- ing any of the ‘“‘live’’ components listed previously. Never lift the welding machine by hand or crane with the contactor switch ‘‘ON.’’ Whenmoving the machine, detach the 8-pole plug from the voltage control to prevent accidental closing of the weld- ing contactor. 3. Besure all components of the installationare well grounded where required. Ail necessary ground connections are shownin the wiring diagrams fur- nished with the control equipment. Rough handling or movement can cause failure of a switch or other electrical part, and connect one side of a particu- lar circuit to the control or switch case. If the apparatus is well grounded, however, the control or switch will not give a shock when touched. nrono wem Fuses should be no larger than specified. 4. Care should be taken to prevent accidental strik- ing of open arcs. An open welding arc gives off a brilliant light which, on continuous exposure, may become extremely painful to the eyes. a. Never use the inching button control when weld- ing current contactor is turned on. An arc will strike if the ‘‘live’’ wire accidentally touches the work. 10 b. Cover the endof the welding wire where it con- tacts the workpiece with UNIONMELT Welding Composition before starting to weld. c. Make sure the path of travel for the machine is clear. Ifa ‘‘live’’ part of the machine touches a grounded object, suchas a steel building sup- port member, an open are will occur. B. Feed Roll and Pressure Roll Adjustment Welding wire is pulled from the wire reel and fed through the contact nozzles or jaws by the combined action of the feed roll and pressure roll. The pres- sure roll forces the wire against the driving surface of the feed roll, ensuring positive feed, The feed roll must be positioned correctly with respect tothe bus- bar adaptor of the nozzle or jaw assembly and the pressure applied tothe wire must befirm to provide even, positive feed. If after assembling the feed roll to the wire feeder, wire feeds erratically, check the following: Misalignment of Feed Rall Unless the feed roll and busbar adaptor are in the correct position with respect to each other, the wire may havea tendency toshred or become excessively scarred, Release the pressure roll adjusting screw. Loosen capscrew "A" (Figure 10), in the pressure roll and accessory support assembly and make cer- tain that the support assembly is square with and tight against the locating shoulder on the accessory support insulator, (See Figure 6.) The accessory support assembly should at all times be in this re- lation to the accessory support insulator. If the feed roll is still misaligned, loosen the lock- nut on the end of the feed roll shaft, and the setscrew in the positioning nut. (See Figure 6.) Position the feed roll centrally with respect to the bore in the busbar adaptor, and locate the positioning nut flush against the feed roll, Tighten the setscrew in the positioning nut, and tighten the locknut on the feed roll shaft. Incorrect Pressure Applied to the Wire The pressure applied on the wire by the pressure roll can be varied by adjusting the pressure adjust- ing screw of the pressure roll and accessory support assembly. (See Figure 10.) Use the insulated end wrench supplied with each wire feeder for any ad- justments. If the wire is slipping, increase the pressure on the pressure roll. If the wire is beingexcessively scar- red, let up on the pressure. Never tighten the pres- sure adjusting screw to such an extent that the two springs in the pressure roll assembly (Figure 10) are compressed solid, Detailed instructions for the operation of the weld- ing head (wire feeder plus accessories) can be found in the control booklets listed on page 2 F-9756 V. Disassembly and Maintenance A. Normal Maintenance Schedule 1. General Little maintenance is required to keep the EH-2 and SH-2 Wire Feeders in top operating condition. It is important, however, that moving parts such as feed and pressure rolls, wire feed motor, etc., be kept clean and free of dust or dirt, welding composition or UNIONARC flux when used in UNIONARC weld- ing. Cleaning is best accomplished by regularly blowing off these parts with dry compressed air. This should be done once for every eight hours of operating time; more often if necessary. In addition, whenever parts have been disassembled, extreme care should be taken to prevent accidental damage to these parts. Bearings especially, should be protected and kept free from dirt and other foreign matter. It is good practice to wrap the bearings when- ever a unit is disassembled, and to applya light film of clean oil to each bearing before reassembling. Whenever the worm and worm gear of the gear re- duction unit have been disassembled, it is recom- mended that a test run be performed before replac - ing the gear unit in operation. For a detailed check on the proper meshing of the worm and worm gear, the 'bluing' process is recommended, Daub a little prussian blue on the tooth surfaces of the worm gear, and reassemble the gears. Slowly rotate the gears a few times and disassemble. Proper meshing will be indicated by a symetrically located bright spot on each of the 'blued' teeth. A common indication of improperly meshed gears is the presence of abnor- mally high motor currents during normal operation. 2. Wire Feed Motor Maintenance Check the wire-feed motor brushes every six months, or every 200 hours of operation. Unscrew both brush plugs as indicated in Figure 9 and lift out the brush and spring assemblies. It is good practice to mark each brush with a pencil as it is withdrawn, so that it can be replaced in the original position. If the position of the brushes relative to the armature is changed, sparking is likely to occur when the motor is put back into operation due to improper brush seating. Examine the brushes. Make sure that each brush surface in contact with the motor commutator has the bright, polished finish that indicates good con- tact. The polished area should cover essentially all of the contacting surface of the brush. When replacing a brush in the motor, be sure to put it back in the same brush holder, and in its original position. Be sure also that the brush rides freely inits holder. New brushes are approximately 3/4-in. long. When they have worn downto 1/2-in. in length, they should be replaced with new ones. With the brushes removed, inspect the surface of the commutator. It should appear clean and smooth, with 11 a polished brown color where the brushes ride it. lf the surface appears rough, disassemble the motor and remove the armature. Polish the commutator surface with No. 00 sandpaper and wipe clean. For this operation, it is preferable to rotate the armature in a lathe. CAUTION: Never use emery cloth or emery stone for this operation. Emery is a conductor of electricity, and any residual loose particles may short circuit the commutator segments during operation of the motor. After two sets of brushes have been worn out, check the commutator for wear. If the surface is worn, it should be smoothed by grinding or turning down on a lathe, and undercutting the mica segments. Replacement of brushes andcommutator maintenance should be performed only by an experienced elec- trician. 3. Mechanized Installations Refer to the proper instruction booklet (See page 2) for routine maintenance of the machine carriage. 4. Adjustments for Different Diameter Wire When joint design or welding conditions require changing from one wire diameter to another, it may be necessary to change the wire feed speed of the wire feeder, and the contact nozzles and jaws used with the feeder. Refer to Tables I and Il forthe proper wire feeder to use, and to F-9784 for the proper nozzles and jaws to use. B. Disassembly of Gear Reduction Unit It is strongly recommended that a new gear unit be purchased rather than disassembling the existing unit. However, it is realized, that in some cases, field repairs or alterations must be made, and for this reason the step-by-step disassembly of the unit is presented below, There arethree possible reasons for attempting dis- assembly of the gear reduction unit. One involves a complete disassembly for repair or replacement purposes, a second calls for a partial disassembly for changing feed roll speeds, and a third involves a partial disassemblyfor changing from left- to right- hand feed or vice versa. 1. Total Disassembly a. Remove the pressure roll and accessory support assembly by unscrewing the capscrew ‘‘A’’, illus- trated in Figure 10. b. Drain the grease from the spur section by remov- ing the pipe plug in the bottom of the gear unit. see Figure 14, é. Drain the grease from the worm section of the unit by removing the pipe plug inthe side of the unit. Two plugs, one on each side, are provided. See Figure 14. d. Separate the gear reduction unit from the wire feed motor by unscrewing the four capscrews ''B’’ illustrated in Figure 2, and removing the washers and "O" rings. Note: The gear head cannot be removed "straight from" the wire feed motor. The gear unit must be separated in such a way that the pilot diameters become disengaged and then moved in the direction that will enable the cluster gear on the armature shaft to clear the cluster gear on the gear reduction unit shaft. Failure to observe this precaution may result in damage to the gearing. . Remove the spirol pin "A", Figure 8, from the gear unit shaft and slide off the washer "A" and gear pinion and bearing assembly "A'. Be sure to support the end of the worm shaft while remov- ing the pin "A" to avoid damage to the shaft or its bearings. Remove washer "'D" from the shaft, and loosen the lockscrew and setscrew beneath it in gear "B". Remove gear "B” from the shaft. . Remove the locknut, washer, feed roll, feed roll key, and feed roll positioning nut (Figure 6) from the feed roll shaft. Toremove the positioning nut, loosen the setscrew in the nut and unscrew the nut off the shaft. Be careful not to lose the as- bestos wicking inthe positioning nut. This wicking is included to prevent damage to the threads of the feed roll shaft when the positioning nut set- screw is tightened. . Remove the insulator disc by unscrewing the three machine screws, illustrated in Figure 6. Remove the accessory support insulator by unscrewing the six capscrews. k Remove bearing housing assembly "A" (Figure 7), by unscrewing the six capscrews "A", and remov- ing the washers and "O"' rings "A". The following precautions should be taken when removing a cap and bearing assembly. j. (i) The cap and bearing assemblies fit snugly into the gear unit housing, When removing, do not cock the assembly or it may bind. (ii) Correct sidewise alignment of the worm gear and worm in the gear unit depends in part on the relationship between shim pack "A", bear - ing housing assembly "A", bearing cone as- sembly "A", and the bearing locating shoulder on the feed roll shaft, The bearing housing assembly "A" consists of the mounting cap, the feed roll shaft oil seal Part No. 97W38, and a complete tapered roller bearing cup Part No. 97W31. Thecup portionof the roller bearing is pressed intothe housing. The cone assembly of the bearing is slip fitted on the feed roll shaft. If this cone assembly is re- moved, keep it matched with the bearing cup in the mounting cap "A". Do not, under any circumstances, attempt recombination of unmatched bearing compo- nents. Do not try to combine a bearing cone assembly from cap and bearing assembly "А" with a bearing cup from cap and bearing as- sembly ''B" or vice versa. To do so will in- vite misalignment of the worm and worm gear and could lead to serious and unwarranted trouble. If the shim pack '"A' has come off with the cap and bearing assembly, set itaside withthe corres- ponding cap and bearing assembly "A". . Tilt the feed roll shaft sothat the worm gear dis- engages from the worm and withdraw from the housing. (The bearing cone assembly from cap "C" (Figure 7) may come out with the shaft and gear.) BEARING & GAP ASSEMBLY tc? DIP STICK DIP STICK RECEPTACLE — OIL SEAL FEED ROLL SHAFT AND WORM GEAR GEAR LOCATING net: SHOULDER SHIM PACK “4” BEARING "2" BEARING CUP “A” Co. BEARING "A") ILL (6)"0" RING “4” PLE (6) LOCKWASHER (6) CAPSCREW Set SHIM PACK “8” BEARING LOCATING SHOULDER a Ÿ E BEARING CONE ASSEMBLY A" 9 2 BEARING HOUSING ASSEMBLY 4” À Ÿ (STAKED iN CAP AND RS (SICAPSCREW'C” (6) O'RING"C" и SHIM PACK “С” BEARING CONE ASSEMBLY’C” WORM AND BEARING ASSEMBLY "O"RING “в” BEARING CAP (4) CAPSCREW “8” “A” FiG. 7 — Exploded View of EH-2 and SH-2 Gear Reduction Unit 12 A l. Remove the bearing cap (Figure 7) by unscrewing (ii) Check the "O" rings for possible damage. the four capscrews "B". (iv) Remove any metal filings that may have col- m, Remove the "O" ring "B" and shim 'B"', and with- lected inside the gear unit housing. draw the worm from the gear housing. Press the (v) Make certain to replace the cap and bearing bearings off the worm if desired. In any case assemblies (cap, bearing, bearing cup, and where it is desired to remove a bearing which is shim} in the same relative positions of the pressed onto a shaft, make sure that the removal gear reductionunit from which they have been force is applied only tothe appropriate shoulder of removed. Care should be exercised ininsert- the inner race of the bearing so that the rollers ing the shaft through the bearing and cap will not be damaged. assembly to prevent damage to the shaft seals. NOTE: In removing the worm, be careful not to A piece of scotch tape should be laid over the damage the oil seal on the motor end of step in the shaft toease the shaft through the gear unit housing. This seal separates seal, Be sure to remove the scotch tape. the worm section of the gear reduction unit (vi) Apply a thin film of Permatex Form-A-Gasket from the spur section. No, 2 to matching faces of housing, shims, n, Remove the bearing and cap assembly "'C" by un- and bearing housing and cap assemblies "А" screwing the six capscrews ''C”, shown in Figure and € (Figure 7), 7. Be careful to keep the bearing and cap assem- (vii) With cap and bearing assemblies and shims bly "C", bearing cone assembly ‘'C", and shim bolted firmly and squarely in place, there pack "C"' interrelated in the same fashion as des- must be perceptible end play infeed roll shaft cribed in steps i, and j. above for bearing hous- and bearing assemblies. This end play must ing assembly "A" and its associated parts. not exceed 0.002-in. in final assembly. o. To reassemble (viii) When attaching the gear head to the motor Reverse the procedure outlined in steps a. thru n. assembly, the worm shaft must be directly above, exercising the following precautions: opposite the depressed counter-bored boss (i) If bearing ''D" has been removed from the in the motor end bell. worm shaft, be certain that it is replaced in 2. To Change Feed Roll Speed (ii) such a fashion that the face bearing the legend "THRUST HERE" is adjacent to the bearing cap. Make certain all bearings are clean and free of foreign material, The overall reduction in speed between the motor and the feed roll, depends on the combinationof pinion "A", gear pinion and bearing assemblies 'A" and "B", gear ''B", and the worm, and worm gear. (See Fig- KL PINION AND Tp un SLINGER INION 4 ASSEMBLY |SLINGE _—— ure 8,) GEAR AND | WASHER "8" WORM GEAR BEARING ASSEMBLY’ WASHER'£* ASA MOTOR ARMATURE BEARING KEY SPIROL PIN '4” WASHER ‘4° BEARING GEAR 8 {INCLUDES 2 SETSCREWS) GEAR AND un BEARING ASSEMBLY ‘4” WASHER D JA ) M Y SPUR SECTION WORM SECTION WORM FIG. 8 — Gear Reduction Setup for EH-2 and SH-2 Wire Feeders 13 F-9756 Tables III and IV list the various combinations of gears to use for particular wire feed speeds. TABLE Ш GEAR COMBINATIONS FOR EH-2 Feed Roll Speed (rpm) 14% 42% 27 12 8 Pinion ''A’’ 28V37 | 28V36|28V37 28V36 Gear & Bear- ing *'A”” 28V31 | 28V34 | 28V35 28V34 Gear & Bear- ‘ing ‘‘B”’ 28V32 128V31|128V33 |28V32 |28V31 Gear ''B”” 28N 12 |28N11128N13 |28N12 |28N11 Worm Gear 29N 17 28N26 Worm 28V65 28V42 * 42 rpm is obtained with the UNIONARC wire feeder 34V10 (95:1 gear ratio) 74 rpm is obtained with the UNIONARC wire feeder 34/09 (54:] gear ratio). To convert this wire feeder to the slower speed, replace the four spur gears indicated in Table Hl with those of the other ratio. TABLE iv - GEAR COMBINATIONS FOR SH-2 WIRE FEEDERS Feed Roll Speed (rpm) 12 19 30 41 | Pinion "A" 28V36 | 28V36 |28V37 | 28V37| Gear & Bearing "А" 98V 34] 28V34 | 28V31 | 28V35 Gear & Bearing "'B" | 28V31 | 28V32 |28V35]| 28V33 Gear "В" 28N11 | 28N12 |29N43 | 28N13 Worm Gear 28N26 Worm 28V 42 Separate EH-2 and SH-2 Wire Feeders are available for all speeds, and it is recommended that these units be purchased rather than changing gears. However, if the customer wishes to convert from one speed to another, he may do so by proceeding as outlined below. TOCHANGE THE SPUR GEARS AND MOTOR PINION a. b, Proceed as outlined in steps a. and b. in Para- graph B-1. To remove the spur gears - proceed thru steps e, and f. in Paragraph B-1. To remove the motor pinion and gear - Remove spirol pin "B'" from-the armature shaft. Slide off washer ''B' (Figure 8), and slide off gear pinion and bearing "B". Be sure to support the end of the motor shaft while removing pin "Bin order to avoid damage to the shaft or its bearings. . Remove washer "C", (Figure 8), and slide pinion "A" off the armature shaft. Remove the key from the shaft. . To reassemble Reverse the procedure outlined in steps a. thru d. above, exercising the following precautions: (i) Make certain to key the pinion "A" to the ar- mature shaft, A special hardened key is used at this point. It must fit tightly in the shaft. Replace the key if it fits loosely. (ii) The slinger (Figure 8) must not rub against the motor or the seal housing. (iii) Gear pinion and bearing assemblies "B' must rotate freely on the shaft. (iv) Washer "'B" must not rotate on the shaft. The groove in this washer must engage the spirol рп "В". (у) Washer "A'' must not retate on the shaft. The groove in this washer must engage the spirol pin "А". (vi) Before operating be sure to replace the lub- ricant within the spur section, Refer to Sec- tion III, Paragraph B for lubrication instruc - tions. NOTE: When the above spur gears are changed, the rpm infor- mation on the nameplate will no longer be applicable. The changed gear ratio and feed rofl speed should be indicated on the wire feeder, TO CHANGE THE WORM AND WORM GEAR a, b. Proceed as outlined in steps a, thru m, in Para- graph B-1l. Press the worm gear off the feed roll shaft and replace with the new gear. The worm gear must be keyed to the feed roll shaft and pressed in po- sition so that the gear is square and tight against the gear locating shoulder on the feed roll shaft. (See Figure 7.) Replace the worm assembly (worm and bearings) with the new worm assembly, and reassemble by reversing the procedure outlined in steps a. thru m, in Paragraph B-1. ‚ Ве sure that bearing "D" is oriented so that the face bearing the legend ''THRUST HERE" is ad- jacent to the bearing cap (Figure 7). ‚ Ве sure to apply a thin film of Permatex No, 2 to matching faces of housing, shims, and bearing housing and cap assemblies "A" and "C" (Figure 7). With bearing cap assemblies and shim packs bolted firmly in place, there must be perceptible end play in feed roll shaft and bearing assemblies. This end play must not exceed 0,002-inches. For mak- ing sure that the worm and worm gear are proper- ly meshed, the 'bluing' process (Paragraph A-1) is recommended. NOTE: When the above worm and worm gears are changed, the rpm information on the nameplate will no longer be applicable. The changed gear ratio und feedroll speed should be indicated on the wire feeder. 3. To Change Left- or Right-Hand Feed To change either wire feeder (EH-2 or SH-2) from left- to right-hand feed, or vice versa, it is not nec- essary to disassemble the whole unit. It should be noted that the H-2 gear reduction unit contains a breather tube which permits removal of the worm gear (on the feed roll shaft) from one side of the unit only. In all cases, the gear and shaft can be with- drawn from the right-hand side (Figure 7), of the unit. 14 CR ee + er 0 oT e а nn O i Gear changeover is performed as follows: а. Proceed through steps a. and c.in Paragraph B-1 excluding step b. It is necessary to drain only the worm section. . Proceed as indicated in steps g. thru n. in Para- graph B- 1. . To reassemble In reversing left- or right-hand gear units, it is particularly important to keepall units of the cap and bearing assemblies together and to take special precautions not to mix up the bearings from each assembly. (1) Reverse the feed roll shaft with worm gear and bearings attached, and insert into the unit from the right-hand side, (It will be assumed for purposes of clarity that, the Original unit was a right-hand unitas illustrated in Figure 7, and is being converted to a left-hand unit.) The long end of the feed roll shaft is now ex- tending out the left side of the unit. (ii) Attach shim pack "C" and bearing and cap assembly "С" (the "blind" cap) to the gear unit using the six capscrews ''C' shown in Figure 7. It is assumed that bearing ''C'' has been mounted on the feed roll shaft prior to inserting the shaft in the housing. Be sure to apply a thincoat of Permatex No. 2 to match- ing surfaces of housing, shims, and bearing, housing and cap assemblies "А" ап "С". (111) Reverse the procedure outlined in steps g. thru j. in Paragraph B-1. Replace the pressure roll and accessory as- sembly on the insulator disc. Make certain that the rear edge of the assembly is square with and flush against the flange of the in- sulator disc. Secure by tightening capscrew “A” illustrated in Figure 10, secure the pipe plugs (Figure 6) in the gear housing and refill with lubricant. Refer to Section III, Paragraph B for lubrication in- structions. (iv) C. Disassembly of Wire Feed Motor Under normal conditions, the only maintenance re- quired on the motor is a periodic check (and replace- ment if necessary) of the brushes. The procedure for doing so is outlined in Paragraph A of this sec- tion. If additional disassembly is required, proceed as follows: 1. Drain the grease from the spur section of the gear reduction unit by removingthe pipe plug frem the bottom of the gear unit. see Figure 13. . Separate the motor from the gear reduction unit by unscrewing the four capscrews ‘'B’’ illustrated in Figure 2. Remove the lock washers and "0" 13 rings and set aside with the capscrews for handy access when reassembling. . Remove the washer ''B", gear and bearing assem- bly "В", washer "C”, and pinion "A", (Figure 8), from the armature shaft by driving out spirol pin "В". Be sure to support the end of the motor shaft while removing pin "B” in order to prevent dam- aging the shaft or its bearings. . Unscrew the brush plugs and remove the brushes and spring assemblies, illustrated in Figure 9. Note how each brush is withdrawn so that it may be replaced in the same position. Match-mark the brushes and holders. . Unscrew the three machine screws and remove the bearing retainer and gasket. (See Figure 9.) . Unscrew the four housing screws (Figure 9}, re- move the washers and ‘‘O”’ rings. . Unscrew the frame screws and remove the fol- lowing items in the sequence indicated. Housing Armature and Bearing Assembly Fan Baffle Plate Ч. Spacers O pp . If desired withdraw the field assembly as far as the connected wires allow. . To reassemble Reverse the procedure outlined in steps i thru 8 above. D. Replacing the Pressure Rol] After long service, the pressure roll shown in Fig- ure 10 may develop a deep groove where it contacts the welding wire. The roll should then be replaced with a new one, to prevent the wire from binding or Slipping during welding operations. Replacement is done as follows: 1. Remove the pressure roll and accessory support assembly from the wire feeder by loosening cap- screw “‘A’’, illustrated in Figure 10. . Back off the pressure adjusting screw so that the clapper and pressure rollcan be swung awayfrom the support clamp, Using a drift punch, punch out the roll pin "A", Punch out from the top of the clapper, as the hole is enlarged on the top to accept a punch. . Slide the pressure roll shaft out of the clapper and remove the pressure roll. . Check the pressure roll bearing and the pressure roll shaft. If the roll tire is worn, or if the roll wobbles or has a sloppy fit on the shaft, replace either the roll or shaft, or both. . Reassemble the roll, shaft, and roll pin, in the reverse sequence of steps 1 thru 4 above. . Remount the assembly on the wire feeder, and adjust the pressure adjusting screw as before. MOTOR FRAME (4)"O" RING FIELD ASSEMBLY (4) HOUSING SCREW FAN BAFFLE (4) WASHER PLATE , ae Е (2)FRAME SCREW | 2 ARMATURE AND Pi _ IA A eee ASSEMBLY (3)MACHINE SCREW (2) BRUSH HOLDER BEARING RETAINER en AND SPRING ASSEMBLY (2)BRUSH PLUG FIG. 9 — Exploded View of Wire Feed Motor "O" RING SPRING BLOCK (2) CUP WASHER (2) SPRING (2) MACHINE SCREW 9, CLAPPER og и, PRESSURE ROLL ASSEMBLY CLAPPER PIN ES NE SPIROL PIN “4” PRESSURE ADJUSTING SCREW SUPPORT GLAMP (4) CAPSCREW "В" NUT CAPSGREW ‘4° FIG. 10 — Exploded View of Pressure Roll and Accessory Support Assembly 16 e ME a A he a ae VI. Replacement Parts Information HOW TO ORDER REPLACEMENT PARTS F-9756 (Diamond Grip} 17 1. All replacement parts are keyed on the drawings which follow. “Two types of numbers are used on these drawings. A. Standard Part Numbers. These are formed by two pairs of digits with a letter between (for example: 01N21, 18V69). Each standard part number is accompanied by a descriptive word or words. 8. Hardware Symbols. These are eight digit numbers (for example: 61203910). Hardware symbols are usually accompanied on drawings by a one word description, | 2, Order standard parts by part number and part name, as shown on drawings. DO NOT ORDER BY PART NUMBER ALONE. 3. Many of the standard parts on the drawings, particularly electronic parts, are "vendor items." This means that they are standard commercial parts made by and purchased from other manufacturers. It will save you time and money if you buy these parts from a local electronics outlet or directly from the manufacturer. When ordering from these outside sources,use the manufacturer's part number or desig- nation given in the "Vendor Items" list below. Of course, if you cannot obtain one of these items else- where, LINDE will furnish it on order. 4, For hardware, look up part number in hardware list on the next page. You will find there a full descrip- tion. "Hardware" items can usually be purchased locally. When ordering hardware from LINDE be sure to include the complete description given in the hardware list. Do not order hardware by the part num- ber alone, 5. When ordering, be sure to state quantity of each part needed, 6. Always state the series or serial number of the machine on which the parts are to be used. The serial number is stamped on the unit nameplate. The "series no.” is the first digit of the serial number, wherever the serial number starts with a digit followed by a letter. When the serial number starts with one or two letters, always give the complete number. 7. Indicate any special shipping instructions. 8. Order replacement parts from the LINDE district office nearest you. VENDOR ITEMS PARTS LIST Part No. Description Part No, Description 82W28 13/32 in. LD. x 5/8-in. O.D. #16 Stub 97 W289 Oil Seal-The Garlock Packing Co. No. Ga, (.065) Wrought Washer Mfg. Co. 63X89 90W39 Plug Shell - Pyle National Co. Cat. No. 97W30 Bearing-Timken Bearing Co. Single APD 2006 Row Type TS No. 05075 90W 42 Contact - Pyle National Co. 6-Pole 97W31 Bearing Cup-Timken Bearing Co. Male Cat, No. AP-610 Single Row Type TS No. 05185 90W79 Plug Shell - Pyle National Co, "PAD" 97W34 Grommet-General Cement Co, Cat, #1043 1504 97W36 Bearing - Marlin-Rockwell Corp. Lubri- 90W81 Contact - Pyle National Co, 4-Pole Seal No, 203SFF -Q7A7 Male Internal Unit Cat. No. PA-415 97W39 Oil Seal - The Garlock Packing Co. 96W 49 Terminal-Aircraft Marine Products Co, No. 51X148 No. 33726 Heavy Duty Ring Tongue 97W73 Bearing-Marlin Rockwell Corp. Cat. No. 7203-QA7 COMPOSITE HARDWARE LIST WIRE FEED ROLL (SEE TABLE) ACCESSORIES [NOT SUPPLIED) FEED ROLLS PART NO. SIZE 2B VSS (KNURLED) | 3/32" TO 3/16" f| 2BVO TISERRATEOD) 1/4" ONLY #344749 (SERRATED)) 3/32" TO 1/4" t When feed roll 28V67 is used, flat pressure roll 28V52 should be replaced by grooved pressure roll 323009, *For dual wire welding. Ног feed rolls used with UNIONARC wire feeders, see F-98172, tw Part No, Description Part No, Description 6020-1028 1/8 in. - 27 Hex. Socket, Pipe Plug, 6133-7903 #10 - 24 x 5/8 in. Lg. Socket, Cone Steel Point, Set Screw, Cad. Plated 6020-1322 3/8 in. - 18 Hex, Socket, Pipe Plug, 6134-0135 3/8 in, - 24 x 2-1/2 in. Lg. Socket, Steel Head, Cap Screw, Steel 6120-1896 #8 - 32x 2 in. Lg. Round Head, Machine 6225-0396 3/32 in. (.094) x 7/8 in. Lg. Roll Pin, Screw, Steel Steel 6120-3824 #4-40 x 1/4 in. Lg. Flat Head, Machine 6239-9346 5/64 in. (.078) x 5/8 in. Lg, Spirol Pin, screw, Steel Med, Cad Plated 6120-3910 #10-32 x 3/8 in. Lg. Flat Head, Machine 6324-0230 5/8 in, - 18 Hex Jam Nut, Steel Screw, Steel 6420-4225 5/8 in, S.A,E, Washer, Steel 6123-4890 $8 -32 x 1/8 in. Lg. Socket, Flat 6420-7075 1/4 in. Shake Proof Lockwasher, Point, Set 5crew, Steel (External Tooth), Steel 6124-0083 1/4 in. - 20 x 1/2 in. Lg. Socket Head, 6480-6918 #10 Cupwasher, Chrome Plate Cap Screw, Steel 7363-5116 Simplex Tirex Cord, Type "SO", 16 Ga. 6124-0090 1/4 in. - 20 x i in Lg. Socket Head, Cap one Conductor Screw, Steel 7363-5416 Simplex Tirex Cord, Type "SO", 16 Ga. 6124-0127 3/8 in. - 16 x 2 in. Lg. Socket Head, Cap 4 Conductor Screw, Steel 7363-5859 Simplex Tirex Cord, Type "SO", 18 Ga. 6124-0412 3/8 in, - 24x 1 in. Lg. Socket Head, 4 Conductor Cap Screw, Steel 6124-0473 1/4 in. - 20 x 3/4 in. Lg. Socket Head, 7756-0361 Cord Guard Assembly, Fastman, Cat Cap Screw, Steel #36-16 6124-1133 3/8 in, - 16x 1 in, Lg. Hex. Head, Cap 7756-0369 Body-Cord Guard, Eastman, Cat #36-9 Screw, Steel 7756-0407 Cord Guard Assembly, Eastman, Cat #40G 6124-2086 1/4 in. - 20 x 3/8 in, Lg. Socket Button- 1756-0408 Body-Cord Guard, Eastman, Cat #40-8 head, Cap Screw, Steel 9360-0020 3/32 in. Dia, Asbestos Wicking 1/4 in. 6133-4908 #10 - 32 x 1/4 in. Lg. Socket, Flat Lg. (Non-graphited) Point, Set Screw, Cad. Plated WIRE STRAIGHTENING ASSEMBLY—28V55 2 BVOT(475:1} SERIES | 2840814751) SHUNT 28V409(320:1) SERIES WIRE FEEDER_|28VY10(320:1) S4UNT ASSEMBLY £8V11 (145 :1) SERES verse js or can ge nor 28V14( 54 :1) SHUNT 2881 {200. 1) SERIES SHOWN FOR HLUSTRATION PURPOSES ONLY FIG. 11 - UEH-2 and USH-2 Welding Head Assembly se ei к. _- er mn F.9756 SposH BUIPISM Z-HSM PUD Z-H3NM © Buimba eSupine|T) — Z| *9|y = % = | 17108 ,8/£ 404 THYeGt +) = ^— 03/104 JF Neo > NOÏIVIO8 * | Es MIA DAISNOH PFD YOS SNOIS FIOH INLINGOW — A A — a DAA (b) ati 1708 FANG IFO “oO 206 9104 FH NYO 1 1G MIA 335 — © FE ta | 48 At rm с ао | > > ЕТ. | E NOLLELOG =. SH = tte = LE | AMES фо lm 1 : vie Sto | | | | аа 3 A | 5: д À и МЭМ 335— | | 0: “li _ a r = | -— 2 aed | BE, done — Ca "8 1 NA EE жуй E | HOLOW | A Y Li Lo e bo me a G — LINDE DLW 30 30/79 зим AO D E 9%. 91-—-- 8 S1- 19 EE EE EE EEO E РИГА ЗАИР a is план т Е ЕНиР Á[quioss y 12p994 эим — El "DIA Aged fier dca 1 ef A 1 491 ЕЕ { 151? SALI HOONA 335 4 Г. FLE) (498) ING? Le > КАЛИ РТА СУМЫ CFIW-OW FTAO9NS 102 1 102 f À u } i 4 АРА S ero ÓN ¿bo Я 2722 я я S ANPAWOD HO HANDBA ANODOS 150 — №0075 YES Cite 8/1) FSV F749 CIN FTAODA TD GPA ' Я A SANVdWOD HO WANNA ANODOS FSO —NOMIFS WHOM FI 7 - : -:3LON NOILYFOINHNT NOVIA | 4639 | OW joe ATENISSY OTRA ON save IENGE ОМ РУ FSV FHO LN) y WISSP Я „77557 2019038 a, NOMI | OO LO ina weg 103377 Oliva 430357: зем “Vu CNE MO Nid SET ay GAR AGATE ‘at rao Woo | Lies N 19 318 Y1 Vi Ni ХУ Y Erll-P2I9—MAH95S [b) HINSHM—-OCNG6Z IFITIANE ava = (378v1 335) „В, 393) — O£NB2—33IHSVM(2) 8228 —83HSWMID) y | | (37801 335} _ LE AZSSY эму за A BEeNBETASIT, | & NOINId 'YV39 DE NOLTTS (FI “DIA 4398) | ws (FOSJBZABZ| AIINI3SSY | / ГОРА ИП Yao | | ; 0685-Е 219—М3Н2513$(2} | | S2N8Z—YIHSWM12) (Graft | , £2M146-ÓNIS 0, (b) x | “ (7 SBOE MBS | OO" „Г. PEN 4 LT A 29— Ме) = i | N | y JT [ CIA Y | \ HABT (37091 335) AIIWNISSY L4HOddNS „Я, #3559 ONIHY 34 FP OS 8 NOINId ‘4739 ve Pre (51 "DIA 44S) hore) | МПИ ЛС | MAIJW3SSY 01.8 one HOLOW peM26—ONIY ,O, SPN6e¢ —ONIHSNG (9] ‘Old AAS) ¿eNgóG-—A JA 20 F-9756 QZABZ ON HP “LOS HOABZ ON #54 "1:01 LSIT SWILI YOOUNSA 3354 ATOWASSO 7401389 9971405 FOISM OL INVISJEN] A Vadv-1 CiM46G—ONIHY38 CLML6—ONINY 38 (©) (2) SALON + / y | S30N79ONI 4 ¿or IoOdO09— IN ld Vx NOLI3S (L195 OL WIS) g1,e/1-1 I “ D NE —WIHS 2SMGB TONY ,0, | 2-8, NOLLOSS PNA WHOM fLH1S Of WHS} 8. ОИ Po EY, PND A U ne 2bN82 —1Y0d4dNns po SA GrAB? | LD | fo $ 9 DNI — 7 | WSSSY d¥O ONldVad “4 | Mt ae 0620-6269 | nu. A bie ШИМ g OEMLE-ONIAV IE Sis 6202-0209 LADE N 3227-0279 HIHSYM ADO 19) : 8227020 £étO-v219—M349S(9) Г (Ol g/t? an | oimsa— Dni 0,9) AT A | 1 ZPABZ-YOILS did- \ \ azorozosomig 3 \ 6200-09E6--INIYOIM 3055-5#:9-мМ3Н95135 \ SPNEEZ—-IAN # MONI | \ \ SA0n INE \ (SION 735 / SvbABZE—A TEN ISS SNISNOH - 6&M26 - 1945S WOy WIAD, NOLIDFS 0600 GL02° O¢ PI- 4 SGHSYMNDO —— | ГОТ. РИ e OIMSS-OINI4 ,0 (9) — CE£800--219—-M3909S(9) paper OT | | € PNG? —HOLYINSNI LeNBe-dVI A y Em26- ano KL | —TENSZ- AM s3anTanı af #2 -D2E19—- MIHOSIE) Aqwassy jun voy>npay 189 — | `9|-] (26482 EB SYABE AT GFOT TON --—— 62M26—195S 110 # [ZRAFZ BE OOABG AY G70 TOW --—. 32 "e6-—- ONIN Я + 800-9219 - -— 34/11 Н aH MaBOS ty) Y OGAG¢--—AgNL 33H 1Y3948 q) \ Sadan 13Ni | \ pOAGE—AIBW AS ZY ON 1d | \ \-TpN@2—ONISNOH \ новое опа 86702—HINIVHLS [7 ¿SNESA SA — DUNE 134 VHS os 92N8 2 ao LEN ¿162 Hvao WHOM «IG, MIA rus eragz| W3SSv 4v2o WHOM ion sane2| UNY L47ES --P219 — MIS (9) —=2 | | 21 +4145 [66 sous DAS | ^1949$5\ Big puc sorow — St "914 CEMIS E SEMIS Ni GIONTINI ¿SIT SWILT YOONTA 375 MB (S3/435) OGMGB—ONIY (8) Га ON Nid} 97 Ni 21) (5314353 9115-2982 —0409 B finnys) 18M06 O(SFIMIS) SMOG 1291405 @ (inns! 62M06 (SOS Car ÊT) c&M9S—ONTY O; EP MSS—YINIYL3H =” Е bbM925— TW3IS 3802-219 — MINIS (¢) Lans Les x IKEA 9 3LIHM | 9681-0219 с ER 3ENLVWEY {S314 35) MIOS (p) b ova DEALS Е Azua] la РМ 95— УЭН5УМ (5) PSM9S- ONIHYVIBLZ) tb азы 91314 SICOTIA TI | ¢ Mov 1g (1 NOHS) (SFIS) GEOMOAS ON Nid | ¥O109} Sav371 | SOLOW Ob M 95 —9NISNOH 3009 30709 FHP JOGWAS SiH ALIM Дыра E # (531435) 6t M96—TVNINEI1 (2) Se SPM9S—JIWVHS 32M 99— ATAN ASSVY HSNMEHS 12) (1040H5 ) ОМ 95 — АЛВИ955у нопча (2)и52/м5$) мпн$) АВА 3559 971113] 6btM 9G (5314358) AVBNAISSY 91314| 8М96 GFLVHLSATTS LON fT ONNMAIL OT NI bs) | (5.3175! 919-692 -—9Н09 (LLNAAS ) 197,82) GGBG-F9E2-AHOD (SH#3S){ 91,8) 91bG-COC4-0HO09 #551575) 20P0-961/-ATSWASSY AYUNO 9305 (INNHSI T9EO-95L2-1I9N3SSV QNYNO HO 22 {531435} OPO-95/12-A009 AYVNS 0909 (iN AHS } 69£098¿¿-A008 0Y3vn59 OOO bSM9S-ONIJVI8 x £GMIS-AISSV HIATOH HSNYE(Z) LEM9G—-ON Id НЗПУа{2) ATEN3SSY 9NIYVI9 8 AYNLYWYY F.9756 LFA8Z ‘ON HOJ — Á(QUISS 5 y jioddng A105 5932 puD [04 aunssaid — 91 “Dl 2310-7219 — M3YDS LOSNSE—dWYy 19 tSN8Z2—A090189 LS/7 SWIL/ O9N8Z—LNMN SUOINTA 338 6 eltO-t219—M149S(b) 9SNSe—-4344v719 „Ри №0295 „8-8, NOILDIFS (9 1,878) EEMLG—9INIS ,0,, BSNSZ-LAVHS ETES xa Non VEML6—-LIWNONO(S) 4 OI6£-O219—M3IYOS (2) BODECE 71084 2415539 ISN INIQIIM FHM TPA HOA x AA —Nld 96ED—SGC9NId CéNSE—M3H9S Vd CGASC— TION JISASSIHAA X EO06L-£ 219 — MIOS 23 LINDE Supplies These Quality Products to the Nation’s Industries INDUSTRIAL GASES LINDE Oxygen, Nitrogen, Argon, Neon, Helium, Krypton, Xenon, Hydrogen, and mixtures PREST-O-LITE Acetylene CALCIUM CARBIDE UNION CARBIDE Calcium Carbide OXY-ACETYLENE EQUIPMENT OXWELD Apparatus for Cutting, Joining, Treating, and Forming Metals Acetylene Generators Manifolds, Regulators and Valves Welding Rods and Supplies PUROX Welding and Cutting Apparatus PREST-O-LITE Welding and Cutting Apparatus PREST-O-LITE Air-Acetylene Apparatus and Small Tanks ELECTRIC WELDING AND CUTTING EQUIPMENT HELIARC Welding and Cutting Equipment SIGMA Welding Equipment UNIONARC Welding Apparatus and Supplies UNIONMELT Automatic Welding Apparatus and Supplies SPECIAL EQUIPMENT LINDE Jet-Piercing Equipment Plate-Edge Preparation Equipment Steel-Conditioning Machines Sub-Zero Cold Treatment Equipment Liquid Oxygen Converters Liquid Nitrogen Refrigerators Liquefied Gas Containers Storage and Transfer Equipment For Cryogenic Fluids | OXWELD Oxy-Acetylene Cutting Machines PREST-O-LITE Cylinders, Shells, and Shapes OXYGEN THERAPY SUPPLIES LINDE Oxygen U.S.P. Oxygen Regulators OXWELD Oxygen Manifolds and Valves SPECIAL PRODUCTS LINDE Synthetic Sapphire, Ruby, Spinel, ana Titania Fine Alumina Abrasive Molecular Sieves The terms “Carbie,” “Heliare,” Linde,” "Oxweld,” “Prest-O-Lite,” “Purox,” “Union Carbide,” “Unionarc,* and “Unionmelt”” are trade marks of Union Carbide Corporation, LINDE COMPANY DIVISION OF UNION CARBIDE CORPORATION (> General Office: 30 East 42nd Street, New York 17, N. Y. Sales Offices in Principal Cities—See Adjoining Column Lithographed in U.S. A. F-$756-C IMD J-8032-59 LINDE OFFICES General Office ( 30 East 42nd Street, New York 17, N. Y. Eastern States BALTIMORE 4, MD,, 200 East Joppa Road BOSTON (Needham Hgts.) 94, Mass., 300 First Avenue BUFFALO 2, N. Y,, 250 Delaware Áve. CHARLESTON 4, W. VA., P.O. Box 4078, Kanawha City Station NEW YORK, 2065 Route 22, Union, N. J. PHILADELPHIA, Pleasant Valley Rd. & Route 38, Moorestown, N. J. PITTSBURGH 22, PA., 644 The Oliver Building WASHINGTON, D. C., 777 14th Street, N.W. Central States CHICAGO 1, ILL., 230 North Michigan Avenue CINCINNATI 29, OHIO, 709 Melish Avenue CLEVELAND 14, OHIO, 1300 Lokeside Avenue DETROIT 21, MICH., 10421 West Seven Mile Road INDIANAPOLIS 4, IND., 729 North Pennsylvania Street MILWAUKEE 46, WIS., 1623 South 38th Street MINNEAPOLIS 2, MINN,, 827 Second Avenue, South ST. LOUIS, 111 So. Meramec Ave., Cleyton 5, Mo. Southern States ATLANTA 8, GA., 22 Seventh St., N. E. BIRMINGHAM ©, ALA,, 2900 Cahoba Road MEMPHIS 5, TENN., 48 West Mclemore Avenue NEW ORLEANS 19, LA., 4833 Conti Street | Southwesfern States ( DALLAS 26, TEXAS, 2626 Commerce Sireet DENVER 23, COLO., 666 So. Santa Fe Drive HOUSTON 27, TEXAS, 3839 W. Alabama KANSAS CITY 5, MO. 910 Baltimore Avenue TULSA 24, ORLA., 2901 So. Harvard Avenue Western States LOS ANGELES (Vernon) 58, CALIF., 2770 Leonis Blvd. | PORTLAND 9, ORE., 1205 Northwest Marshall Street | SALT LAKE CITY 1, UTAH, 436 W. Ninth South Street SAN DIEGO 10, CALIF,, 1004 Morena Blvd. SAN FRANCISCO 6, CALIF., 22 Battery Street SEATTLE 4, WASH., 3404 Fourth Avenue, South pul sn. In Canada | LINDE COMPANY Division of Union Carbide Caneda Limited General Office: 40 St. Clair Ave., E., Toronto 7, Canada EDMONTON, ALTA., Highway 16 and Government Road | TORONTO 4, ONTARIO, 805 Davenport Road MONTREAL 9, QUEBEC, 8311 Royden Road VANCOUVER 4, B. C., 1175 Grant Street ST. BONIFACE, MANITOBA, 733 Tache Avenue Outside United States.and Canada Linde Department UNION CARBIDE INTERNATIONAL COMPANY | Division of Union Carbide Corporation 30 East 42nd Street, New York 17, N. ¥., U.S.A. { Cable Address: UNICARBIDE, New York GENEVA, SWITZERLAND, Union Corbide Europa, $, A., 40, Rue du Rhóne MEXICO 15, D F. MEXICO, National Carbon-Eveready $. А., Calzada Mariano Escobedo No. 343
advertisement