advertisement
▼
Scroll to page 2
of
62
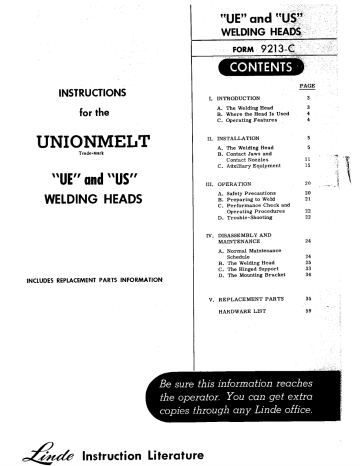
“SUE” and “US” WELDING H ee г PAGE - INSTRUCTIONS | | I. INTRODUCTION A. The Welding Head for the B. Where the Head Is Used C. Operating Features _ UNIONMELT IL. INSTALLATION A. The Weldi d Trade-Mark В e Welding Hea 5 He de ar Où. en. . Contact Jaws and Contact Nozzles 11 C. Auxiliary Equipment 15 an II. OPERATION N A. Safety Precautions 20 | WELDING HEADS B. Preparing to Weïd 21 C. Performance Check and Operating Procedures 22 D. Trouble-Shooting 22 IV. DISASSEMBLY AND MAINTENANCE 24 A. Normal Maintenance Schedule 24 The Welding Head 25 The Hinged Support 33 . The Mounting Bracket 34 vor INCLUDES REPLACEMENT PARTS INFORMATION V. REPLACEMENT PARTS 35 HARDWARE LIST 59 Be sure this information reaches the operator. You can get extra copies through any Linde office. Lindo Instruction Literature tase The purpose: of this booklet is to present the information you need to set up, operate, or a Ч 3 and: + malntain the: UNIONMELT ‘‘UE"” or ‘'US'! Welding Head in the proper manner. It ae Tn =; ag hen ie, Mths - Freie) RE = ed with. welding techniques or procedures. : ig UNIONMELT. ‘welding, the greatest degree of process flexibility and versatility can ~ be gained only through proper selection and use of the many items of available equipment, For your convenience, this booklet describes much of the accessory equipment as well as the Welding Heads. It explains in detail the steps to be. followed in assembling the various components, Some of the instructions may not be pertinent to your particular installation, but we have purvosely made this booklet all-inclusive; to cover as many types.as possible. SAFETY PRECAUTIONS As in all electric welding apparatus, there are certain exposed parts of UNIONMELT welding installations at the welding voltage potential. At times even the higher open circuit voltage may be present. Though this is never more than 115 volts, remember that it is the same as ordinary house-lighting voltage, with which the average person avoids all contact. Under conditions of low body resistance, such as when a person is perspiring and is in contact with a grounded steel plate, this voltage may force enough current through the body to be fatal. For this reason and because a shock, even though harmless in itself, may lead to other injuries due to the uncontrolled physical reaction, the operator should be aware of the live parts of the machine and follow safe operating procedures, See ‘Safety Precautions’’ on page 20. - | CONTACT JAW UNIT SUPPORT ASSEMBLY WIRE FEED M MOTOR OVABLE GEAR HOUSING FIXED GEAR HOUSING BUSBAR ASSEMBLY NOZZLE ASSEMBLY FIG. 1 -— Standard (45-degree) ''Unionmelt”? “UE” Welding Head The terms “Linde,” “Oxweld,” and “Unionmelf”” ore registered trade-marks of (inion Carbide and Carbon Corporation. |. INTRODUCTION A. The Welding Head The function of all UNIONMELT Welding Heads is to feed welding wire to the weld zone at a controlled rate. This is accomplished by an electric motor in the head which operates a feed roll through a gear reduction unit. The rate at which the wire is fed depends on the welding current and wire size used, and is regulated by means of a voltage control which supplies current to the motor. In brief, the voltage control either speeds up or slows down the wire feed motor when necessary to maintain the required con- Stant distance between the end of the welding wire and the workpiece, You will find detailed descriptions of how this is done in booklets F-6622, ‘‘Instructions for the ‘‘UE’’ Electronic Voltage Control,’’ and F-9414, ‘‘Instructions for the '*'US'* Series Voltage Control,’’ Two welding heads are described in this booklet. The only difference between the heads is in the wire feed motors and gearing. The''UE’’ Head is designed for use with the UNIONMELT Electronic Voltage Control. The ‘'US’' Headis used withthe UNIONMELT Series Voltage Control. Standard and double speed “US” Heads feed wire at approximately the same rate as standard and double speed ''UE”” Heads. Figures land 2 show the two heads. The busbar assembiy hardware, nozzle assembly, and contact jaws illustrated in Figure 1 are also used with the head shown in Figure 2, The standard UNIONMELT “UE” or ‘'US” Welding Head consists essentially of five subassem- blies. These are: (1) the wire feed motor and gear assembly, (2) the fixed gear housing assembly, (3) the movable gear housing assembly, (4) the bus- bar assembly, and (5) the unit support assembly, These five components come assembled as a complete unit ready for mounting. They function as follows: The wire feed motor drives a reduction gear train in the fixed gear housing. This drives a re- duction gear train in the movable gear housing. This second gear train connects directly to two MOVABLE GEAR HOUSING WIRE FEED MOTOR & GEAR ASSEMBLY FIXED GEAR UNIT SUPPORT HOUSING ASSEMBLY FIG. 2 ~ Standard (45-degree) ‘‘Unionmelt’’ ""US” Welding Head Shafts in the housing, on which are mounted two feed rolls, one above the other. It is these rolls which feed the welding wire to the welding zone. The force necessary for positive feed is provided by a spring-loaded pressure roll, A straightening roll removes the bend from the wire and prevents kinking or jamming of the wire in the feed mechanism. The movable gear housing assembly can be rotated in a vertical plane through an angle of 45 degrees, as indicated in Figures 1 and 2. This increases the flexibility of the welding heads by providing a greater number of possible welding positions. The copper busbar assembly receives the weld- ing current and transmits it, through apair of copper contact jaws or a nozzle assembly, to the welding wire. The support assembly provides a means for mounting the welding head. It also contains a worm and ring gear which permit the operator to rotate the head through 360 degrees about the motor axis by means of a tee wrench. An additional spiral gear assembly (Part No. 07V50) is available as an accessory. This assembly mounts on the unit support assembly and enables the operator torotate the head while standing at the front or rear of the apparatus. This is a valuable feature when welding in close quarters. A ''90-degree 'UE’ or ‘US’ Head’ is identical to the standard heads just described, with the excep- tion of the movable gear housing assembly. This housing assembly is so constructed that it can be rotated upward through 90 degrees, permitting the welding wire to emerge horizontally, when required. Special extensions can be used with this head as shown in Figure 3. Youcan use this extension singlyor in multiples of eighteen inches up to a maximum of fifteen feet. It permits you to weld in locations which cannot be reached with a standard welding head, such as inte- rior welds in small-diameter pipe. Your standard nead can easily be converted to the 90-degree head, when desired, by substitution of the movable gear housing assembly. B. Where the Head is Used Your welding head is designed for either station- ary or portable mounting. Instationary installations, the head is mounted in a fixed position and the work- piece moves beneath it. LINDE does not make or sell stationary mountings, or the jigs necessary for supporting and moving the workpiece. Your LINDE representative can suggest names of manufacturers who have specialized in providing mounting equipment for welding heads. Figure4 shows a stationary head setup for production welding of longitudinal seams in tubular sections. For portable installations, the head may be mounted on the CM-37 UNIONMELT Machine Car- riage. The assembly is designated for UE-37 or US-37 Portable Welding Machine. You will find specific instructions for assembling this machine in Section II of this booklet. The ''UE’' Head feed motor is a 1/4 hp. motor which is used in conjunction with the “UE”” Voltage Control. The ''US’ Head feed motor is a 3/8 hp. motor which is used in conjunction with the ‘'US’' Voltage Control, Both voltage controls work from a 115-volt a.c. 50 to 60-cycle line. For precision shape or contour welding, either head can be mounted on the UNIONMELT WM-6 Contour Welding Carriage {shown in Figure 22). The ‘‘UE’’ or ‘‘US’’ Head may also be mounted on the OM-48 Machine Carriage. Typical OM-48 in- stallations are shown in Figures 20 and 21. C. Operating Features The ‘‘UE” or ‘‘US’’ Welding Head has a maxi- mum welding current capacity of 2,000 amperes, a.c. ог d.c. The amount of welding current you will need for any welding operation is determined primarily by the thickness of the material being welded, but will seldom, if ever, be less than 200 amperes. Using either head (with the necessary auxiliary equipment}, you can do the welding jobs shown below in one pass. (Joints in heavy plate are welded using a multipass technique.) In addition, buildup and hard-surfacing operations can be done on fiat, cylindrical, or irregular shaped surfaces. With Proper With Jaws_ Contact Nozzle Butt Welds: 18-gage sheet to 1-1/4-in. plate Plug Welds: 1/4-in. to 1-1/2- in. plate Positioned 1/8-in. to 1-1/2- in. legs Fillet Welds: Non-Positioned Fillet Welds:t 1/8-in. to 3/8- in. legs + Contact nozzles must be used. The ‘‘UE’' Head is sold with either standard (12 rpm) or double (24 rpm) speed gearing, to provide the maximum possible efficiency within a given welding current range. Triple speed (36 rpm) gears are available for use in special applications. You can convert from one speed to another by replacing the fixed gear housing assembly, or its gears, in the welding head. Instructions for this procedure are given in Section IV, paragraph B-9. The **US*' Head is available with either standard (12 rpm) or double (24 rpm) speed gearing. Speeds of 18, 34, or 48 rpm may be obtained by replacing gears (see Figures 50 and 74) with the combinations shown in the gear interchangeability table on page 29. Instructions for changing gears are given in Section IV, paragraph B-5. The welding currents (and wire sizes) most generally used for a specific installation will deter- mine what gearing is best. Our gearing recom- mendations are shown in the following table: Welding Current* - Amperes Wire Diameter | Standard Double Triple Inches (12 rpm) | (24 rpm) | (36 rpm) 3/32 250 400 600 1/8 425 550 950 5/32 675 900 1,200 3/16 950 1,150 жж 1/4 1,400 *% x 5/16 2,000 ж* de *Minimum welding currents for each size of wire and gear train are about one-half the maximum indicated in the table. Use of welding voltage other than 32 volts will alter the ranges. ++ Not recommended. FIG. 4 — Stotionary Head, Installation ll. INSTALLATION NOTE: Installation instructions given in this section do not include special insulating procedures required with high-frequency starting. If you plan to use high-frequency starting, follow the additional instructions given in F-9081, ‘‘Installation and Operation of the High-Frequency Starting Unit for the UNIONMELT ‘UE’ Control,”’ High-Frequency starting cannot be used with the '*US'* Head. A. The Welding Head 1, MOUNTING PROCEDURE The ‘‘UE" or ‘‘US’’ Welding Head is gener- ally used in conjunction with the Hinged Support 09V41 shown in Figure 7, This allows you to adjust the position of the welding head over the work without moving or adjusting other compo- nents of the installation. The support can be attached horizontally or vertically with respect to the head. If desired, however, the head may be sup- ported alone by the bolts on the unit support assembly. Insulation must always be used to prevent electrical contact between the welding head assembly and the mounting device which should be grounded toearth, Insulating bushings and plates are supplied with the heads. Critical dimensions of the unit support assembly are shown in Figure 5, If desired, a special bracket can be designed to fit the mounting lug of the unit support assembly. (Dimensions of the '‘UE”’ and ‘‘US'’ Heads in various installations are given in Figures 78, 79, 99, and 100 at the back of this book.) The welding head and hinged support are assembled as shown in Figure 6. Make sure that the insulating plates are in the positions indicated in Figure 6, and tighten the assembly securely. INSTALLING THE MOUNTED WELDING HEAD (a) Stationary Installations (1) Welding Head and Hinged Support The assembly as shown in Figure 6 can be mounted on any vertical surface, cola 10.-5 (2) %DRILL Toloo | OS FIG. 5 — Unit Support Assembly Mounting Dimensions the Fe $ inne impone] INS, PLATE _ ee | STEEL LIMIT MOUNTING PLATE WASHER INS.PLATE SUPPORT ON HINGED SUPPORT SCREW #e T3 me ae ét SE eee age a ply RP ee a FE de ES o eh ol A ee > r BUSHING À \ FIG. 6 — Mounting ‘“UE’’ Head on Hinged Support using four 1/2-in. cap screws of appro- priate length, and four 1/2-in. steel washers {see Figure 7). The hinged support permits the welding head to be swung from side to side through an angle of 122 degrees. A clamp is pro- vided on the support to permit locking the hinge at any desired position. Anauxiliary pair of mounting holes is provided in the support adjacent to the standard holes (see Figure 7). This pair permits mounting the head on the support at right angles to the normal position shown in Figure 6. When the head is mounted in this fashion, the hinged support can be bolted to the underside of a beam or crane arm, A pair of accessory mounting holes, 6 inches on centers, is also provided. These are for use in mounting a wire reel support, or for mounting other (non-standard) apparatus. (2) Mounting Bracket Assembly 09V03 An additional support member which can be used in conjunction with the hinged support just described is the bracket assembly shown in Figure 8. The bracket contains a mounting platen with four tapped holes corre- sponding to the mounting holes in the hinged support. Four hex head cap serews and washers are supplied with the bracket for mounting the hinged support to it. Worm and spiral gears in the bracket provide adjustment of the platen position through a vertical distance of 4-3/8 inches. You can fasten the bracket to the underside of a horizontal member, as shown, or on the top side of the member (see Figure 9), as desired. When in- stalled as shown in Figure 8, the eye- bolt should be removed from the hinged support assembly so that full traverse of the platen can be used, For mounting on a vertical surface, a modified version of the bracket (Part No. 38V15) is available. This modified bracket can be seen in use in Figure 20 on the UNIONMELT OM-48 Side- Beam Carriage. A set of cable clamps is supplied with the bracket. These are for use in anchoring the welding cables. A 1/2-in. bolt three inches long, and a washer are supplied for mounting the clamps as shown in Figure 17 on the side of the CM-37 travel carriage. Tapped holes AN TA < me оо ALTERNATE POSITION | ! KL... LL Lo fe | CLAMPING SCREW LIMITS SWING | - {2}/STANDARD MOUNTING HOLES (2) AUXILIARY MOUNTING HOLES MOR | a — CLAMPING SCREW T 17 : TO 96° ON ONE SIDE. . | y Y TO OBTAIN MAX. SWING1122% 1 [5 q ON THAT SIDE TRANSFER CLAMP - : ING SCREW TO OTHER SICE OF (Ip HI o 7} Ly _ LY ES \" = ыы м , TE 100 Юте зе [EJACCESSORY MOUNTING HOLES (3) FIG. 7 — Dimensions for the Hinged Support Assembly are provided on both sides of the car- riage for this purpose. The bracket’s mounting holes are arranged in a circle 4.562 inches in diameter. The holes are 21/64 inches in diameter, and are spaced around the circle 60 degrees apart. Six 5/16-in.- 18 x l-in. cap screws and six washers are supplied with the bracket. Use these when mounting the bracket on the CM-37 travel carriage or on the rocker hinge described below. (Tapped holes are provided in the carriage and the rocker hinge for this purpose.) Rocker Hinge 19V79 The rocker hinge (shown in Figure 10) is used in conjunction with the bracket assembly just described. The hinge provides a vertical movement of about six inches at the welding head busbar. It is used when the head is provided with anozzle guide wheel (see page 19) or other device which rides on the workpiece. The guide wheel and hinge permit the welding head to rise and fall with variations in’height of the workpiece, helping to maintain a con- stant gap between the nozzle (or jaws) and workpiece, which is essential to obtaining a good weld. Whennecessary, the rocker hinge can be locked by means of two built-in adjusting screws. The top surface of the rocker hinge has six tapped holes for 5/16-in.-18 cap screws. These holes are arranged in a circle 4.562 inches in diameter, and are spaced around the circle 60 degrees apart. Six l-in. cap screws to fit these holes are supplied. The bottom surface of the hinge has four drilled holes 11/32 inches in diameter. (These holes match the tapped holes in the top of the CM-37 travel carriage.) Their pattern is shown in Figure 11. Four 5/16-in.-18 x 7/8-in. long cap screws are supplied for use when mounting the hinge on the CM-37 carriage, (b) FIG. 8 — Bracket Assembly (Vertical Mounting) A NOTE: (4) The hopper supplied with the head is mounted in the position shown in Figure 18. A close-up of two of the mounting screws can be seen in Figure 69, A steel washer is placed under the head of the serew, and an insulating washer is placed on each side of the hopper mounting lug. The mounting lugis fitted with an insulating bushing. The hopper is insulated from the welding head to avoid the possibility of electrical shock from the hopper. Stationary installations often use a customer-built storage and distribution system for UNIONMELT Composition, providing an extra-large composition reservoir to avoid frequent refilling. Some systems are equipped with a suction tube which salvages unfused UNION MELT Composition and returns it to the reservoir through a strainer which removes fused particles. LINDE does not manufacture UNIONMELT distribution or recovery systems, but can provide suggestions for installing an appropriate distribution system. Installation on the OXWELD CM-37 Machine Carriage NOTE: Instructions for the CM-37 travel carriage are contained in the booklet which is packed with the carriage: ‘‘Instructions for OXWELD CM-37 Machine Carriage,’’ Е-9119. The bracket assembly, when desirable, ean be bolted directly to the top of the CM-37 carriage as shown in Figure 9, However, a number of portable instal- lations will also requíre the rocker hinge, to allow the welding head to follow variations in the surface of the work. Installation is as follows: (1) Position the rocker hinge on the CM-37 carriage. The hinge is normally mounted with its axis transverse to the center line of the carriage. This posi- tion is indicated by the dotted line in Figure 10. (2) Bolt the rocker hinge to the carriage with the four hex head screws you will find in the cloth bag tied on the assembly. The mounting holes normally used are indicated by arrows in Figure 11. (3) Mount the bracket assembly on the rocker hinge as shown in Figure 12. Use the six 5/16-in.-18 x 1-in. cap screws and 5/16-in. washers supplied with the bracket assembly. Install the cable clamps on the side of the carriage as shown in Figure 17, using the 1/2- in.-13 x 3-in. bolt supplied. (Tapped holes are provided on both sides of the carriage; remove the threaded plug with a screwdriver.) *FIG. 9 — Bracket Assembly Mounted on the CM-37 Travel Carriage This The “UE’ or ‘‘US’' Head assemblies are normally mounted on the CM-37 carriage with the heads facing in the opposite direction, to ensure maximum stability of the carriage through uniform distribution of the component weights. (The carriage hand le is removed to provide sufficient clearance for the busbar assembly.) Travel Carriage (4) Mount the hinged support on the platen of the bracket assembly as shown in Figure 13. Use the four 1/2-in.-13 x l-in. cap screws and four 1/2-in. washers supplied with the bracket assembly, (5) Mount the wire reel bracket on the hinged support as shown in Figure 15, using the set of bolts, nuts and washers supplied with the bracket, (6) Mount the wire reel on its bracket as shown in Figure 16. Use the four cap screws and lock washers supplied with it. (1) Remove from the welding head the two mounting bolts, their nuts and washers, and the two insulating plates. Place a steel washer on each bolt. Insert the bolts in the mounting holes on the hinged support as shown in Figure 14, FIG. 11 — Normal Mounting Holes for Rocker Hinge # NOTE: (8) (9) Mount the welding head on the hinged Support as described in Section II, paragraph Al on page 5. See Figure 17 for illustration. The "UE”’" and ‘‘US'’ Voltage Controls, “UE”" High-Frequency Starter, and “US”? Wire Retract Starter are in- Stalled in accordance with the instruc- tions supplied with these components, *FIG.-13 — Mounted Hinged Support The “UE" or “US” Head assemblies are normally mounted on the CM-37 carriage with the heads facing in the opposite direction. to ensure mazimum stability of the carriage through uniform distribution of the component weights. (The carrtage handle is removed: to provide sufficient clearance for the busbar assembly. ) 9 * NOTE: The opposite direction. This is to ensure maximum stability of the carriage through uniform distribution of the component weights. (The carriage handle is removed to provide sufficient clearance for the busbar assembly, ) FIG. 14 — Welding Head Mounting Bolts Inserted (10) Install the hopper as explained on page 8. A completed UE-37 Assembly is shown in Figure 18, the complete machine and for other applications are given in Figures 78, 79,99, and 100 at the back of this book, (c) Installation on the UNIONMELT OM-48 Side-Beam Carriage NOTE: A primary advantage of the Side- Beam Carriage is the fact that the equipment is close-coupled to the mounting carriage for rigidity. To obtain the most from this feature, the welding heads should be mounted as close to the carriage as possible and the use of long mounting arms or brackets avoided. This will prevent inaccuracies or irregularities in the track being amplified and causing the weld to run off the seam. When the track assembly has been installed, use the following procedure: (1) Attach mounting bracket (38V15) to the Dimensions for (2) (3) (4) (6) carriage frame with four 1/2-in.-13 bolts. (See Fig. 19 for location of mounting holes.) The bolis are se- cured by four 1/2-in.-13 square nuts which are weldedtothe carriage frame. Detaching the movable section of mount- ing bracket (38V15) and reassembling it in an inverted position will permit the entire welding head assembly to be lowered anadditional six inches closer to the work, if so desired. Mount the carriage by sliding it onover one end of the track. Make sure the motor unit is in a raised position so it will not interfere with the rack. Mount hinged support (09V41) on mount- ing bracket (38V15). Mount head assembly on hinged support (see Figure 6}, Mount the small wire reel and support (18N44) on hinged support (09V41). If eg ame et * FIG. 17 - ‘‘UE" Welding Head in Mounted Position 10 “UR op **US* Head assemblies are normally mounted on the CM-37 carriage with the heads facing in the . A A pm ER * FIG. 18 ~ The ““YE-37' Portable Welding Machine the large wire reel assembly (38V22) is Selected, mount itatopthe carriage. (See Figure 19.) The installation in Figure 20 shows the smail wire reel and its mounting bracket, Figure 21 gives another view of the instal- lation. (d) Installation of the UNIONMELT WM-6 Contour Welding Carriage Figure 22 shows the ‘‘UE’’ Head in- stalled on the WM-6 carriage, A standard hinged support and a modified version of the bracket assembly are used. The bracket assembly is bolted directly to the transverse arm of the carriage; then the hinged support and welding head are mounted as previously described, The large wire reel is mounted on the far end of the transverse arm by means of a special bracket. B. Contact Jaws and Contact Nozzles The welding current can be transferred from the busbar assembly to the welding wire either by a pair of contact jaws, or by acontact nozzle assembly. The majority of applications will use jaws. The curved nozzle assembly and the adaptor (see Figure 27) are used in non-positioned fillet welding and where the wire must be conducted to a joint at some distance from the busbar. The curved nozzle per- mits ‘‘trailing’’ the wire along the joint -- a more HOLES FOR CABLE CLAMP OR RETRACT STARTER oser | 7 (4)HOLES FOR LARGE ROD REEL BASE -38V22 (17/32" DRILL) A (495/16"-18 HOLES FOR REMOTE CONTROL’ & SWITCH BOX I8V68 A OR D OR US VOLTAGE CONTROL O9V73-A OR O9V73-D | oo a A À | se HOLE Are oe TOP VIEW 3/8-24 HOLE FOR CABLE CLAMP (4917/32 HOLES FOR VERTICAL SLIDE — 38VI5 OR HINGE-I9V94 (WITH (4) L2"-I3 SQ. NUTS WELDED ON TO FRAME} $ 0 (4) 5716-18 HOLES FOR “ ELECTRONIC GOVERNOR aM = 3 FRONT VIEW FIG. 19 ~ Equipment Mounting Holes in OM-48 Side Beam Carriage * NOTE: The UE" or “US” Head assemblies are normally mounted on the CM-37 carriage with the heads facing in the opposite direction, This is to ensure maximum stability of the carriage through uniform distribution of the component weights. (The carriage handle is removed to provide sufficient clearance for the busbar assembly.) WIRE REEL AND MOUNTING BRACKET PIDE-BEAR FCARRIAGH Я а es u el 2% a nn ER, E q À rh nr we ый % ых NE N ae : BUS BAR MOUNTING BRACKET CONNECTORS ASSEMBLY 38VI5 FIG. 20 - Type ''UE’' Welding Head and Smal! Wire Reel Mounted on the ‘‘Unionmelt’’ OM-48 Side-Beam Carriage favorable condition for sheet metal welding. You can build anozzle assembly of any reasonable length by using multiples of the 2-in. and 5-in. extensions. 1. INSTALLING CONTACT JAWS Contact jaws are available in six sizes to fit welding wire from 3/32 to 5/16 inches in diameter. They are not supplied with the weld- ing head, since only one or two sizes are nor- mally required by one user. Contact jaws are used in pairs consisting of a fixed jaw and a movable jaw. (The movabie jaw is distinguished by the connection lug (for the copper braid) mounted in its center — see Figure 23.) Wire grooves are machined on both sides of each jaw. When one groove is worn too deep for further redressing, the jaw can be reyersed end-for-end to use the groove on the opposite side. The following table shows the proper jaws to order for each size welding wire: Welding Wire Movable Jaw Fixed Jaw Size (in.) Part No. Part No. 3/32 07V11 12W83 7/64 and 1/8 07 v13 13W31 5/32 09V31 25W22 3/16 07V14 13W32 1/4 07V15 13W33 5/16 07V16 13W34 Accessories needed to mount the jaws on the busbar are supplied onorder under Part No, 19V92. You will use all the parts with the exception of one spring, which is a spare. 12 Select the pair of jaws appropriate to the size welding wire you plan to use, and install them as follows: (a) Remove the two nuts from the pair of threaded studs on the welding head busbar. (b) Install the movable jaw on the pair of short studs on the welding head busbar, as shown in Figure 23, (c) Install the fixed jaw on the threaded studs on the busbar, (d} Install the three plates as shown in Figure 24. Then replace the two nuts removed in step (a), and tighten. Figure 25 shows the parts installed. (e) Install the spring using the 3/8-24 x 5/8-in. cap screw. Make sure that the spring bears squarely on the side of the movable jaw, then tighten the cap screw into place. This screw can be adjusted to vary the spring tension to compensate for wear, etc. If the screw is too tight, the load on the wire may be excessive. Always loosen the spring before prying the movable jaws apart. (£) Install the two braids side-by-side as shown in Figure 26. The braids are secured to the busbar using the 5/16-in.-24 x 1-1/4-in. cap screw and nut, and to the movable jaw lug using the 5/16-in.-24 x 3/4-in. cap screw and nut. (g) Make certain that all joints are tight, for good electrical contact, and that the Jaw moves freely. INSTALLING THE NOZZLE ASSEMBLY Figure 27 shows the various parts used in making up nozzle assemblies, and the order in which they are assembled. (a) Assembling the Straight Nozzle As sembly (1) Select the correct (according to welding wire size) and size welding tip FIG. 21 — Type “UE” Welding Head Mounted on the ‘‘Unionmelt”’ Side-Beam Carriage (2) (3) (4) (1) Select the correct oa a screw the nut (containing the tip) tightly onto the nozzle. If an extension is to be used, screw it into the adaptor, tighten it firmly, and slip on its insulating sleeve. (If additional extensions are needed to reach the weld zone, add them in the Same manner.) Screw the nozzle into the bottom of the extension (or into the adaptor, if no extension is used). Tighten securely, then slip on the nozzle insulating sleeve and secure it with the screw provided, Mount the assembly on the welding head busbar, and secure with the two nuts provided. (b} Assembling the Curved Nozzle Assembly size welding tip (according to the welding wire size) and FIG. 22 — “UE” Head Mounted on WM-6 Contour Welding Carriage 13 . À a “Unionmelt’' (2) (3) (4) (5) screw the nut containing the tip onto the nozzle. Screw it onto the curved neck of the nozzle for sheet metal welding, onto the straight neck of the nozzle for fillet welding. Screw a locknut on the other end of the curved nozzle, If an extension is to be used, screw it into the adaptor, tighten it firmly, and slip on its insulating sleeve. (If additional extensions are needed to reach the weld zone, add them in the same manner.) Screw the nozzle into the bottom of the extension (or into the adaptor, if no extension is used). Slip on the nozzle insulating sleeve, Mount the assembly on the welding head busbar, and secure with the two nuts provided. = АР o "reg, © FIG. 23 FIG. 24 FIG. 25 FIG. 26 Installing Contact Jaws (6) After correctly positioning the nozzle, over the extension, and the locknut and tighten the locknut firmly against the curved nozzle are screwed into the end adaptor. of the extension, The locknut holds the (c) Installing the Horizontal Extension on the nozzle in any desired position. '90-Degree’’ Welding Head The extension itself is 18 inches As shipped to you, the 90-degree mov- long. By using the necessary number of able gear housing is in the normal vertical extensions, any required length can be position, as shown in Figure 28, The stand- obtained up to a recommended ART ard busbar assembly can be installed on mum of 15 feet. The extension and the mounting lug and the head used for nozzle will fit inside a tube with an standard welding operations. The movable inside diameter of 3-1/2 inches. housing can be tilted upward to a maximum Both 45-degree and 60-degree of 45 degrees from the position shown. curved nozzlesare available in various To swing the housing up to horizontal sizes to accommodate standard sizes Les of welding wire, position (or to an angle between 45 degrees and this position), proceed as follows: Applications requiring use of the horizontal extension usually require (1) Remove the short stud (see Figure 28), special means for carrying the UNION- the long stud, and the third stud on the MELT Welding Composition to the point side of the fixed gear housing (not of welding. LINDE engineers can pro- visible in the illustration). vide suggestions for your application: (2) Tilt the housing upward to horizontal contact your LINDE district office for position. details. (3) Install the studs as shown in Figure 29, The third stud is not used in this ap- plication. S'EXTENSION oad Han os th ag The adaptor bracket and the hori- zontal extension are assembled on the welding head as indicated in the exploded view, Figure 30. Crawford Fitting Company's "Blue Goop' lubricantis ap- plied to the threads of Extension Tube No, 16N72 at the factory to eliminate a thread seizing problem, The tube is Suitable wrapped to provide protection during shipment. This wrapping must be removed when the tube is installed. The insulating sleeve is then slipped i4 2"EXTENSION INSULATING SLEEVES STRAIGHT NOZZLE NUT FiG. 27 — Nozzle Assemblies (6b) Mounting the Large Wire Reel (07V69) LONG STUD The large wire reel is equipped with a baseplate designed for bolting directly to a mounting device of your own construction. For proper wire feed, the plate must be mounted in such a manner that the coil of welding wire will lie in a vertical plane. The bolt hole dimensions of the mounting plate are given in the sketch on page 17. The assembly should be insulated from ground, using the insulating pieces supplied with the large wire reel. For mounting on the WM-6 Contour Welding Carriage, the baseplate of the wire reel is bolteddirectly to a mounting bracket supplied on order with the carriage. This mounting is illustrated in Figure 22, For mounting on the CM-37 and OM-48 Side-Beam Travel Carriage, the reel with body casting (38V22), shown in Figure 33, is used, The base is bolted to the top of the side-beam carriage, or a plate attached FIG. 28 - 90-degree ‘'UE"’ Head, as Shipped to the CM-37, as shown in Figure 33. This reel is insulated at the top of the post for high-frequency use, A clamp per- С. Auxiliary Equipment mits rotation of the reel to any position 1, THE WIRE REEL around the post. In UNIONMELT welding, the wire reel 2. WELDING COMPOSITION DISTRIBUTING DE- supports the coils of welding wire and provides VICES them with the degree of rotation required as m the wire is pulled through the feed roll. (a) Welding Composition Distributing Assembly Either a small expansion type wire reel givos (Figure 3l) or the large wire reel (Figure 32) This device is shown in Figure 34. It may be used with the ‘‘UR’’ or ‘‘US’’ Head controls the depth and confines the distri- welding installations. The large wire reel, bution of UNIONMELT Welding Composition accommodating 150-Ilb. coils of welding wire, is generally used for stationary installations, Through the use of special equipment, however, this type reel can also be mounted on the stand- ard UNIONMELT CM-37% Carriage for portable installations. The small expansion-type wire reel is de- signed to accommodate the standard small (25-lb.) coils of welding wire as well as special 50-Ib. and 65-lb. coils. It is usedon the CM-37 Carriage as part of the UE-37 Welding Machine, and may also be used on both the WM-6 Contour Welding Carriage and the OM-48 Side-Beam Travel Carriage. (a) Mounting the Expansion-Type Wire Reel (29V31) Brackets are available for mounting the wire reel on standard UNIONMELT car- riages (see Figures 16 to 20). When used in other installations, the reel must be | 4 mounted so that the coil of wire lies ina on RE в vertical plane. Four bolts are used to mount | att LONG STUD the reel. The mounting pattern is shown in | | Figure 31. FiG. 29 - 90-degree “‘UE’’ Head in Horizontal Position SHORT STUD 15 90-DEGREE ~~ D yew eevee RTE ere The width of the composition burden is HOUSING ema kt u а. controlled by lateral adjustment of the con- N _BUSBAR, ASSEMBLY ves fining plates. м ВР? + смоет ae 8 ore He 48 ny ncaa ee ae SE If the weld seam is parallel to the car- oth 1 jan er sue | riage, no swivelling action is necessary; mn ue the swivel assembly can be clamped in a RACE ae fixed position. When desirable, it can be mag removed entirely, as Figure 22 shows. When ees * , the weld seam is irregular, the swivel e ce” vs assembly, in conjunction with the guiding rs tr | kgs . device shown in Figure 40, swivels to follow paras ee > И” HÓRIEZO RE the seam and maintain uniform composition y O HESS EXTENSION . coverage, FIG. 30 - Horizontal Extension and Adaptor Bracket Mounting procedure is as follows: (1) Insulating plates, bushings, and three cap screws are supplied on the welding head busbar. Remove the rear cap over the weld. (This assembly can be used only with jaws.) The device consists essentially of a screw and loosen the two front cap funnel and a swivelassembly which supports screws as shown in Figure 35. two composition-confining plates. The UNIONMELT Welding Composition feeds (2} Fit the twoslots in the funnel mounting from its hopper, through the rubber tube pad on the shanks of the loosened cap intothe funnel, then down around the welding screws, wire to the weld zone. The two plates on the swivel assembly prevent the composition (3) Insert the third cap screw through the from spreading away from the seam, An hole in the funnel mounting pad, through adjusting knob on the swivel assembly per- the busbar and insulating plates, and mits raising or lowering the plates; this secure it with the washer and nut. controls the height of the composition layer. Tighten all three cap screws firmly. 1” (4) 11/32" DRILL lg | | | | | | | 1 F a | o. | > LA \ N i} VIEW ATA” wey nun | _ at ART Pa < - ISS S = O — > = —_ 6 El = CR = АК. NS | SAN yf SY ol] 1 К . us | | | | A |. | | 5" | 2: | 4 — 8 " | 13 a FIG. 31 — Small Exponsion Type Wire Reel Dimensions 16 EXTENDED POSITION 40° | RETRACTED POSITION 32% , | | | inh A мо h © iG e = || z/c = = . 2 E ey nt =o u|o о < |+ | a 515 a E EJE |: à © ale S|e о| 2 нЕ a fo кы, a = xo Lud o|u ih | . ta | a 4 = 2 #1: ши = E E. on me] bod be! i | Ge Fass С. SN pur = 4) INSULATING BUSHING UT Г. \ 10.750 N (ABO X "HE. HO. STEEL SUPPORT, FOR CAP SCREW & NUT 2 (4)3/4 5.4.€. STO STEEL | | ROD REEL LOCK WASHER р je o т I I I T I i т --L--Ia ‘ | 7 rm 4) HOLES 17/32" DRILL FIG. 32 - Lorge Wire Reel Dimensions (b) UNIONMELT Welding Composition Gate The UNIONMELT Manual and Automat- ic Welding Composition Gates provide a simple and convenient means for controll- ing the flow of welding composition to the welding zone. The automatic gate is shown in Figure 36. Instructions for installing both the manualand automatic gates will be found in F-9649, Instructions and Parts List for UNIONMELT Automatic and Manual Gates for UNIONMELT Welding Composi- tion. Qu . GUIDING DEVICES (a) Carriage Guide Wheel 09V48 Although the CM-37 Carriage is gener- ally guided along standard OXWELD track, the guide wheel pictured on page 19 has been made available for hand guiding. When mounted, the guide wheel raises the carriage idler wheels off the ground entirely; the resultant three-point suspension makes for easy, accurately controllable manual steer- ing. As illustrated in Figure 38, the guide wheel mounting bracket is screwed directly to the handle brackets on the carriage with the socket-head screws supplied. The steer- ing handle screws directly into the shank of the wheel fork. 17 WELDING COMPOSITION CONFINING PLATE MOUNTING FUNN PAD F EL SWIVEL FIG. 34 — Welding Composition Distributing Assembly (b) Tube and Pointer Assembly 08V77 This device, shown in Figure 36, is used in conjunction with a contact nozzle assembly. Itclamps on the nozzle insulating sleeve and acts as a support for the rubber hose and pointer. The pointer can be fabri- eated from a length of welding wire. The assembly is frequently used in conjunction with the carriage guide wheel described in (a), The pointer is mounted so that its tip almost touches the weld seam, ahead of the welding composition. It provides accurate guidance for the operator when steering the carriage. A composition gate can be installed in place of the usual welding composition hose. Setscrews are provided in the point- er assembly to hold the gate in position. FIG. 35 — Installing the Welding Composition Distributing Assembly 18 CUT AS REQUIRED TO | DISTRIBUTE COMPOSITION | (с) FIG. 36 — Automatic Composition Gate Nozzle Guide Wheel 08V94 This guide wheel is mounted ahead of the nozzle assembly, and automatically guides the welding head along the vee of the joint. When this guide wheel is used on the UE-37 or US-37 Welding Machine, the rocker hinge should be left unlocked sothat the head is free to follow the seam. The guide wheel is mounted in the posi- tion indicated in Figure 39, Slide the rear clamp on the guide up the contact nozzle until the bottom of the guide wheel is about one inch below the end of the welding tip. Then tighten the clamping screw to hold the assembly in place, and insert the rubber hose through the center hole. This guide wheel may also be used in conjunction with a welding composition gate. Remove the rubber hose from the center clamp, insert the receiving tube of the gate then tighten the setscrew in the clamp. Guiding Device Assembly 07V92 This device can be used only with the welding composition distributing device as shown in Figure 40, It attaches to the swivel assembly with a cap screw, washer, and square nut. The three guide wheels ride in the weld vee, guiding the head and swiveling the composition confining plates along the weld. A pivot joint and clamp screw are provided to allow the device to be tilted for following girth welds. (E FIG. 37 — Nozzle and Pointer Assembly . 3 y o ae fe ae wet vs E ke? ah ee fh ar BE wt sf FIG. 38 we Fa ” Corriage Guide Wheel 19 aa à Vara e „$: 7. A RA hs ee idea ae en a4 FIG. 40 — Guiding Device Assembly 4. 99-DEG. STUD (BUSBAR) CONNECTORS In some welding installations, it is not possible to bring the welding current cables to the machine from overhead and connect them in the normal manner to the busbar. If the #4/0 welding cables are carried to the head horizon- tally, the cables must be connected to the busbar by means of 90-deg. stud or busbar connectors. These can be seen in use in Figure 20. The shank of each connector is a solid copper casting which is connected to the busbar with a sleeve and jam nut. (This sleeve and jam nut, Part No. 15W35, must be ordered separately for each stud connector.) The other, short leg of the connector receives the welding cable in exactly the same manner. Four connectors, varying in length from 3-3/4 in. to 7-3/4 in., are available for use with the **UE"” or ‘'US'’ Head. The number of con- nectors which must be used for any particular welding operation depends on the amount of welding current supplied. (Each 4/0 cable is recommended for use with not more than 500 amps.) The varied lengths of the connectors permit “nesting’’ (see Figure 20), which pre- vents the cables from bunching up at the side of the head. 5. INSTALLATION OF OTHER COMPONENTS For complete instructions concerning the following equipment, refer to the booklets: "DE'' Electronic Voltage Control, Remote Con- trof and Switch Box "US" Series Voltage Control Wire Retract Starter High-Frequency Starter High-Frequency Filter Flexible Attachment CM-37 Machine Carriage OM-48 Side-Beam Carriage indicated F-6622 - Instructions for the '*'UE” Electronic Voltage Control F-9414 - Instructions for the ‘‘US'" Series Voltage Control (Series 4 and 5)+ F-9183 - Instructions for the Wire Retract starter (‘'US’’ Head only} F-9081 - Instructions for the High-Frequency Starter (‘'UE’’) F-9159 - Instructions for the Flexible Welding Attachment F-9119 - Instructions for the CM-37 Machine Carriage F-9160 - Instructions for the OM-48 Side- Beam Carriage + If series number is not shown separately, it is the first digit of the serial number, |1. OPERATION A. Safety Precautions (Also see page 2.) 1, The busbar, contact jaw or nozzle assembly, welding wire, and all parts of the wire reel and its supports are at welding voltage potential. In addition, the control cables carry various If any of these cables should fail, one side of the damaged In view of these conditions, and to prevent possible injury, DO NOT TOUCH THESE PARTS UNLESS THE MAIN CONTACTOR IS ‘OFF’? AND THE VOLT- VOLTAGE. The Unit voltages to and from the control box. circuit would still be ‘‘hot,’’ METER SHOWS ZERO Support Assembly may be adjusted while the main contactor is ‘‘ON’’ by means of the insulated socket wrench provided with the welding heads. Be careful to avoid touching anything but the insulated wrench. Be sure that there are no breaks in the insulated covering on the wrench, Turn off the contactor switch when welding operations are discontinued for any length of time. Ina “UE” or “US” Head installation, welding action is generally stopped by turning the wire feed switch to the ‘‘STOP WELD” or neutral position. This stops the wire feed, and the current relay turns off the contactor when current flow ceases. The operator must not touch any of the ‘‘live’’ components listed above until the voltmeter indicates zero, Never lift the welding machine by hand or crane with the contactor switch ‘‘ON." 20 3. Be sure all components of the installation are well grounded where required. All necessary ground connections are shown in the wiring diagrams furnished with the equipment. Rough handling or movement can cause failure of a switch or other electrical part, and connect one side of a particular circuit to the control or switch case. If the apparatus is well grounded, however, the control or switch will not give a shock when touched. Care should be taken to prevent accidental striking of open arcs, which may cause extreme eye pain. (a) Never pressthe inching button when welding current contactor is turned on. An are will be struck if the ‘‘live’’ wire accidentally touches the work. (b) Cover the end of the welding wire where it contacts the workpiece with UNIONMELT Welding Composition before starting to weld. {с} is clear. Make sure the path of travel for the machine If a ‘‘live’’ part of the machine touches a grounded object, such as a steel building support member, an open are will be struck, 9. Always wear goggles when chipping or removing solidified UNIONMELT Composition from the finished weld zone. B. Preparing to Weld MOUNTING THE WIRE COIL l, (a) (b) Expansion Reel The small expanding wire reel is de- signed to apply constant pressure to the inner diameter of a coil of welding wire. The pressure eliminates slipping between the wire coil and the reel and prevents the coil from unwinding faster than the reel is turning. HOW TO INSTALL A COIL OF WIRE (i) Loosen the thumbscrews on the retain- ing fingers of the four wire reel arms. (2) Turn the fingers so that they point toward the hub. (3) Remove the wrapping paper from the wire coil, but donot remove the binding wires. (4) Use the outer end of the coil as the starting end. (The inner end of some coils is tagged ‘‘Start This End.’ Dis- regard such instructions.) Slide the wire coil onto the reel with the starting end in the proper feed position. (3) Secure the inner end of the wire to the quick-acting wire clamp on the reel. Turn the reel fingers outward and tighten the thumbscrews. (6) (7) Secure the starting end of the coil be- tween the feed and pressure rolls of the wire feed mechanism. It maybe neces- sary to remove one or two of the coil binding wires, but do not remove all of the binding wires. (8) Tighten the hub spring retaining bolt to provide some frictiondrag for the reel. The spring pressure should be sufficient toprevent the wire coil from unwinding. However, it should not be so great as to overload the wire feed motor. Remove the remaining binding wires from the coil, BRAKE SPRING SELECTION (9) The wire reel is assembled with brake spring 28264 and a 1/2-in. plain steel washer. (See Figure 86.) This spring and washer are used for most applications. For lighter braking action, replace the spring and washer with spring 92W12 and guide washer 18N26 which are supplied in a cloth bag tied to the reel. Large ({150-lb.) Coils: Large Wire Reel (see Figure 41) (1} Remove all wrapping paper from the 21 coll and locate the starting end. This end will be designated by an attached tag which reads “Start this End.’’ Do not cut the binding wires or straps until the coil has been placed on the reel, (2) Loosen the hahdle on each of the four arms of the reel, rotate the movable fingers in toward the center of the reel, and back off the adjusting wheel (counter-ciockwise rotation), (3) Slide the coil onto the reel, making sure that the starting end is pointed toward the feed rolls. Wire is usually fed from the top side of the reel toward ihe welding head. (4) Slide the anchor end of the coil into one of the anchor holes and tighten the thumbnut. (9) Turn the movable fingers back into position; lock them into place with the handles. Expand the reel against the inner diameter of the coil by turning the adjusting wheel clockwise. (6) Adjust the drag brake to provide suf- ficient friction to prevent the wire coil from unwinding itself. Don’t use ex- cessive drag, as this will overload the wire-feed motor. (7} Hold the starting end of the coil firmly and withdraw it until the binding wires prevent further rotation. Cut each binding wire as it comes into this position. (8) When all binding wires have been cut, insert the welding wire between the pressure and feed rolls and into the nozzle assembly or contact jaws, ANCHOR HOLE FINGER LOCKING HANDLE DRAG BRAKE | ADJUSTMENT ADJUSTING WHEEL FIG. 41 ~ Large Wire Ree! 2. SPRING-LOADED PRESSURE ROLL ASSEMBLY The Spring-Loaded Pressure Roll Assembly automatically adjusts the pressure on its rolls according tothe sizeof welding wire being used. Normally the only adjustment the operator must make is to position the straightening roll cor- rectly. (See Figure 42.) If tube wire is to be used, remove the cover plate. Then remove the two small diameter inner springs and put them in a safe place. Replace the cover plate and retaining screws. C. Performance Check and Operating Procedures Detailed instructions for operating the head and controls, and for a preliminary performance check, are given in the Voltage Control instruction booklets ('US”’ and ''UE’'). When high-frequency starting is used with the ‘‘UE’' Head, also consult the instruction booklet which accompanies the high-frequency starter. When wire-retract starting is used with a ‘'US'’ Head, refer to the appropriate booklet. | D. Trouble-Shooting This section describes how to remedy faulty welding conditions that sometimes occur through mere oversight or misadjustment, You can correct a great majority of these conditions by simply checking or adjusting external controls and connec-~ tions on the installation. Detailed trouble-shooting procedures for electrical equipment are given in the various instruction booklets supplied with LINDE equipment. 1. NO WELD Probable causes: (a) Ground not connected to workpiece. (b) No welding current being supplied to the head. Remedy procedure: (1) Check input to welding transformer or motor-generator set. (2) Checkall switches for proper position. (3) Check all connections. (4) Check 115-volt circuit through contactor relay and switch. (c} Opposed polarity on paralleled generators or transformers. 2, BUTTON WELD (NO WIRE FEED) Probable causes: (a) ‘‘UE’’ control time delay switch not opera- ting. (Pilot light should goon approximately five minutes after main voltage control 22 STRAIGHTENING ROLL FIG. (с) (9) (e) (1) (g) (h) RETAINING SCREW INNER SPRING PRESSURE ROLL Ay A NE Pr N N PRESSURE ROLL 42 - Spring-Loaded Pressure Roll Assembly switch has been turned on. This indicates that the time delay switch has closed and the control is ready for operation.) “Feed-Retract' switch set at neutral (‘‘STOP-WELD’’) position. Hi-lo switch set in low instead of high position. Welding voltage setting too high. Pressure roll too loosely adjusted. Faulty connections in wire-feed motor cir- cuit. Control box welding voltage leads not con- nected. Welding voltage fuses incontrol box burned out. Remedy procedure: To check, turn contactor switch “ON.”” If there is no voltmeter reading, either the connections or fuses are faulty, or there is a break in the circuit. (1) Failure of 115-volt source. if the voltage control circuit is not defective, the carriage will run and the tubes of the ‘‘UE’’ control will light. If the tubes donot light and the carriage runs, the 115-volt fuses or tubes in the voltage control box may be burned out. (j) If motor-generator set is used, either the a.c.-d.c. switch in “UE” voltage control is out of position, or lead 1W or 2W in the voltage control may be reversed (lead 1W should be positive). (k) Voltage control not functioning because ot open circuit or burned out part. Refer to the Voltage Control instruction booklet. STICKING OF WIRE AT START OF WELD Probable causes: (a) Loose welding cable connection to workpiece. (b) Weld started with wire too close to work because steel wool ball was loosely formed; or wire was forced downtoo hard and tended to lift the welding head. (c) Hi-lo switch in high instead of low position. (d) Excessive dirt or oil in the ball of steel wool. (e) Loose head mounting. (f) Welding voltage setting too low. (g) Current too low for wire diameter being used. (h) Current relay inoperative, or its contacts dirty. (i) Control box defective; see the Voltage Con- trol instruction booklet. STICKING OF WIRE DURING WELDING OPER- ATION Probable causes: (a) Hi-lo switch in high instead of low position. (b) Welding voltage setting too low. (c) Current too low for wire diameter being used, (d) Loose welding cable connection on work- piece, (e} Defective control box; see the Voltage Con- trol instruction booklet, (+) Travelspeed erratic; see F-9119, ‘‘Instruc- tions for the OXWELD CM-37 Machine Carriage.”’ 23 5, VOLTAGE CONTROL ERRATIC AFTER WELD- ING FOR A PROLONGED PERIOD Probable cause: Thyratron tubes are firing continuously, due to high ambient temperature (“UE”” control only). Remedy procedure: around Improve ventilation in and Voltage Control. STOPPING OF WELDING ACTION WITH ALL CONTROLS PROPERLY SET Probable causes: (а) Failure of 115-volt source. (b) Broken wire or connection. (Travel car- riage may have separated a wire at a break, or may have pulled out a connection.) (c) Welding wire coil binding in reel, Remedy procedure: Loosen the coil by slipping the finishing end over or under the other strands until the binding is relieved. Should the binding be too tight to relieve by this method, re- move the coil from the reel and rewind it before using again. (d) Pressure roll too tight, (e) Fuse burned out. {f) Voltage control ceases to function; see the Voltage Control instruction booklet. FLUCTUATION OF VOLTMETER AND AM- METER, AND IRREGULAR WELD DEPOSIT Probable causes: (a) Depth of granular material too great or too small. Raiseor lower tue composition gate or tube. (b) Contact nozzle or jaws set too high above work. {c) Welding voltage setting too low, (d) Hi-lo switch set in wrong position. (e) Wire size too large for voltage desired. (f) Contact tip or jaws dirty, worn or loose, Jaws may be loose because of loose or faulty spring. (g) Wire-feed pressure roil improperly ad- justed. (Usually too loose.) (h} Wire-feed roll broken or in poor condition. (See Section IV for disassembly instructions.) A. Wire weaving from side to side in weld seam. (i) Remedy procedure: (1) Welding tip or jaws may be too large for wire being used. Replace with proper size, (2) Replace welding tip or jaws if worn, (3) (j) Wire not positioned correctly inweld seam. (k) Readjust straightening rolls, Wire or work may be rusty or oily. (If this condition exists, the weld deposits should be checked carefully for porosity.) All oil and rust should be cleaned from the wire and work prior to welding. (1) Current too high for wire size and head gearing. Carriage travel speed erratic; see F-9119, “Instructions for the OXWELD CM-37 Machine Carriage.”' (m) Welding wire coil binding; 6(c} of this Section. see paragraph (n) Weld backing not uniform. (o) Power output of welding transformer or motor-generator set may be fluctuating. (p) Thyratrons of ''UE’ control firing con- tinuously (see Item 5 of this Section). (r) (s) Magnetic influence. (D.C. welding only.) Remedy procedure: Reposition the workpiece ground to minimize magnetic influence, Poor ground connection. GRADUAL INCREASE OF VOLTMETER READ- ING Probable causes: (a) (b) (с) (а) Welding wire coil binding. Wire binding in contact nozzle or jaws. Remedy procedure: Be sure proper size nozzle or jaw is being used. Adjust position of pressure roll to provide better straightening action. Increase in welding current. Pressure or straightening roll too tight. STICKING OF THE WIRE AT THE END OF A WELD Probable cause: Improper operation of wire-feed and con- tactor switches. Remedy procedure: Always turn the wire-feed switch tothe “OFF’’ (neutral) position before turning the contactor switch '*OFF.” IV. DISASSEMBLY AND MAINTENANCE NOTE: Always shut off both the 115-volt current supply to the voltage control, and the welding trans- former or generator current supply to the welding cables, before any disassembly or maintenance operations are undertaken. Normal Maintenance Schedule for Welding Head Installations GENERAL Little maintenance is required to keep the welding head and its auxiliary equipment in top operating condition. Parts subject to wear, or to depletion of lubricant, should be inspected periodically. Important check points are listed below and identified in the illustrations which follow: | (a) Contact Jaws (or nozzles and tips) Inspect jaws every eight hours for cleanliness and wear. If necessary, clean and dress the jaws with a fine round file, The diameter of the file should never be larger than the wire size for which the jaws were designed. Worn jaws should be re- placed, 24 (b) (с) Nozzles and tips should be inspected every eight hours for cleanliness and wear. If necessary, wipe clean with steel wool, and debur with a small flat or round file, whichever is suitable. If tips are worn, loosen the jam nut and rotate the tip so that the rod bears ona new, unworn portion of the Боге, Excessively worn tips should be replaced or shortened by cutting off the ends. Wire-Feed Rolls Under normal operating conditions, check the rolls with each installation of a welding wire coil. Run out a test length of approximately 15 inches of wire and observe impressions made by the knurling. Rolls whose knurling is worn should be replaced. Pressure Rolls Inspect pressure rolls and cupped springs when movable gear housing is re- moved for the replacement of the wire-feed roll. EL + Bye м TRS ee, 4, и; eR ' Motor Brushes FIG. 43 - Removing the ‘UE’ (4d) Cover and Dust Seal Assembly Check the felt dust seal with each in- stallation of a welding wire coil, Dust seals should be replaced whenever worn. (e) Movable Gear Housing Use a good grade of grease which will not churn, channel, stiffen in the cold or liquefy with heat. Texaco Regal Starfak special grease has proved most suitable for this purpose. You can obtain it in five- pound cans through LINDE (Part No. 92W10), (f) Stationary Gear Housing Check the oil level weekly by removing the socket-head plug under the “high oil level'* mark on the side of the housing. The oil level should be maintained at this mark. For operation in warm or cold weather, use the following lubricants: Summer - SAE No, 50 Oil Winter - SAE No. 10W - 20W Oil (g) Motor Brushes Inspect motor brushes every six months. (See following pages for instructions on re- moving brushes.) Brushes less than 1/2 inch long should be replaced with new ones. (n) Refer to Form 9119, ‘‘Instructions for the OXWELD CM-37 Machine Carriage,’’ for maintenance data on the travel carriage. 25 Each installation of welding wire coil: Fach 8 hours of The following chart is a summary of the above checks: Chart for Frequency of Maintenance Check felt dust seal - re- place when worn. Check condition of wire-feed rolls and replace if worn, Check jaws or nozzles and operation: tips for cleanliness and wear. Clean with round file. Replace worn jaws, or nozzles and tips. Weekly: Check and maintain oil at Each 6 months or 200 the high oil level mark, Check motor brushes. hours of operation: Warm season: Cold season: Wire-feed roll re- placement: Movable gear housing lubri- cant: Texaco Regal Starfak Special grease. Stationary gear housing lubricant SAE No. 50 oil, Movable gear housing lubri- cant: Texaco Regal Starfak Special grease. Stationary gear housing: As light as SAE No, 10 oil. Inspect condition of pressure rolls and cupped spring. B. The Welding Head 1. DISASSEMBLY OF THE ‘‘UE'’ DRIVE MOTOR NOTE: It is not necessary to dismount or dis- assemble the motor to inspect the commutator and brushes. Inspection is accomplished as follows: Remove the cover plate and gasket from the rear housing, as shown in Figure 43. The brushes are held against the commutator by spring-loadedfingers. Raise the finger as shown, then lift out the carbon brush. Mark each brush with a pencil as it is withdrawn, so that it can be replaced in the original position. If the posi- tion of the brushes relative to the armature is changed, sparking will likely occur when the motor is put back into operation. Examine the brushes. Make sure that each brush surface in contact with the motor com- mutator has the bright, polished finish that indicates good contact. The polished area should cover essentially all of the contacting surface of the brush, When replacing a brush in the motor, be sure to put it back in the same brush holder, and in its original position. Be sure also that the brush rides freely inits holder, New brushes are approximately 3/4 in.long, When they have worn down to 1/2 in. in length, they should be replaced with new ones, ER ey ts th ed Ч ан: RE LT ой В М мое ue FIG. 44 - Dismounting the Cover Strip with the brushes removed, inspect the surface of the commutator. Ii should appear clean and smooth, with a polished brown color where the brushes ride it. If the surface appears rough, disassemble the motor and remove the armature (see disassembly instructions below). Polish the commutator surface with No. 00 sandpaper. For this operation, it is preferable to rotate the armature in a lathe. Be sure there are no copper burs which might short-circuit the commutator segments. If necessary, de- bur the segment edges by beveling with a small, fine three-cornered file and undercut the mica segments, CAUTION: Never use emery cloth or emery stone for this operation. Emery is a conductor of electricity, and any residual loose particles may short-circuit the commutator segments during operation of the motor. Replacement of brushes, and commutator maintenance, should be performed only by an experienced electrician, The drive motor is held to the Unit Support assembly by four nuts. Two of these are di- rectly accessible, and two, as shown in Figure 44, are in recesses in the Unit Support Assembly. Withdraw the three screws which secure the cover strip over these recesses, and remove the cover strip. Then continue as follows: (a) Drain the oil from the fixed gear housing by removing the drain plug shown in Figure 44. (b) Dismount the head from its support. (c) Remove the four nuts which hold the motor and dismount it by drawing it straight back until its mounting studs are clear of the support. The oil seal gasket can then be withdrawn also; see Figure 45. (d) Loosen the socket-head setscrew in the spur gear on the motor shaft, as shown in Figure 46. Remove the gear from the shaft, being careful not to lose the key from the shaft keyway. 26 RING GEAR GASKET (e) (£) (g) (h) FIG. 45 = Dismounting the **UE”" Motor Remove the motor brushes. Unscrew the four stud caps from the rear of the motor. The rear housing and motor armature can now be withdrawn, as shown in Figure 47. To remove the armature, dismount the bearing cap from the rear of the housing and press out the armature shaft and 1ts bearing. Reassembly The motor is reassembled by reversing the procedure given above. When attaching the motor to the unit support, make sure the gasket is in placeand in good condition. If bent or otherwise damaged, replace it with a new one. Be sure the two units fit up snugly before fastening them together. This will indicate that the motor shaft is interlocked correctly with the gear in the stationary gear housing. № a TEE ot” ga A FIG. 47 — Disassembling the “UE”’ Motor Housing INSPECTION OF THE ''US” MOTOR ARMA- TURE AND BRUSHES Check the wire-feed motor brushes every six months or every 200 hours of operation. NOTE: It is not necessary to dismount or dis- assemble the motor to inspect the commutator and brushes. Inspection is done as follows: Unscrew both brush plugs as indicated in Figure 48 and lift out the brush and spring assemblies, Mark each brush with a pencil as it is withdrawn, so that it can be replaced in the original position. If the position of the brushes relative to the armature is changed, sparking is likely to occur when the motor is put back into operation. Examine the brushes. Make sure that each brush surface in contact with the motor com- mutator has the bright polished finish that indicates good contact. The polished area should cover essentially all of the contacting surface of the brush. When replacing a brush in the motor, be Sure to put it back in the same brush holder, and in its original position. Also be sure that the brush rides freely inits holder. Newbrushes are approximately 3/4 in. long. When they have worn down to 1/2 in. in length, they should be replaced with new ones. With the brushes removed, inspect the surface of the commutator. It should appear clean and smooth, with a polished brown color where the brushes ride it, If the surface appears rough, disassemble the motor and remove the armature. Polish the commutator surface with No. 00 sandpaper and wipe clean. For this operation, it is preferable to rotate the arma- ture in a lathe. CAUTION: Never use emery cloth or emery stone for this operation. Emery is a conductor of electricity, and any residuai loose particles may short-circuit the commutator segments during operation of the motor. Be sure that there are no copper burs which might short-circuit the commutator seg- ments, If necessary, debur the segment edges by beveling with a small, fine three-cornered file and undercut the mica segments. Replacement of brushes and commutator maintenance should be performed only by an experienced electrician. DISASSEMBLY OF THE ‘US’? MOTOR AND GEAR HOUSING ASSEMBLY To remove the "US" Motor and Gear Housing Assembly, loosen the four mounting screws as shown in Figure 49. When the four screws have been loosened, the Motor and Gear Housing Assembly may be separated from the Suppor! Assembly as illustrated in Figure 50. The motor is secured to the gear housing by three motor retaining nuts as shown in Figure 50. To remove the motor, take the grease out of the housing, take off the three nuts, and separate the motor from the housing as illus- trated in Figure 51. When reassembling the motor and gear housing, reverse the foregoing procedure. Be sure that the two gaskets are in good condition and replaced in their original positions as shown in Figures 50 and 51. Slide the units together until the gears mesh and replace the nuts and bolts. The gear housing must be re- packed with clean grease. The grease may be ee pe gen! POON 2 go ae FIG. 48 — Removing the '‘US’’ Motor Brushes UNIT SUPPORT SUPPORT ASSEMBLY “ ASSEMBLY “VENT ASSEMBLY ‘MOTOR AND GEAR HOUSING ASSEMBLY FIG. 49 — Removing the ‘US’? Motor and Gear Housing Assembly hand-packed before reassembly or applied wi 4, DISASSEMBLY OF THE ‘‘US’’ MOTOR th agrease gun after reassembly. To use agrease gun it is necessary toremove the vent assembly shown in Figure 49, After the motor has been removed from the gear housing as described in the preceding paragraph, the motor may be disassembled fo maintenance. r NOTE: An experienced electric motor repair- man should do this work. (a) Unscrew both brush plugs and remove the brush and spring assemblies. (See Figure 48). Note now each brush is withdrawn so that it may be replaced in the same position. Match-mark the brushes and holders. (b) Unserew the two motor housing screws as shown in Figure 52, (с) Withdraw the motor end housing. Lift out the motor armature and remove the shroud. GASKET | UNIT SUPPORT GEAR NOt ASSEMBLY 3) MOTOR ETAINING SUPPORT NUTS ASSEMBLY SETSCREW RETAINER RING GEAR NO, 2 SETSCREW FIG. 50 — ‘‘US’' Motor and Gear Housing Assembly Separated from Support Assembly 28 LOCATING PIN GASKET (3) MOUNTING STUDS FIG. 51 — '‘US"’ Motor Separated from Gear Housing (e) To remove the motor field, unscrew the two retaining screwsas shown in Figure 55. “(f) To reassemble, reverse the procedure outlined above. An exploded view of the motor is shown in Figure 54, 5. CHANGING SPEED OF '‘US’’ HEAD As indicated in the ‘‘US'' Gear Interchange- ability Table (see page 29}, different wire-feed speeds may be obtained by replacing gears #1 and #2 (shown in Figure 50) withother combina- tions, To remove either gear, simply loosen the setscrew, take off the retainer ring, and force the gear off the shaft. Be sure to insert the key when installing a replacement gear, Replace the retainer ring and tighten the set- screw. 6. REMOVAL OF ''US’ SUPPORT ASSEMBLY The Support Assembly (29V03), part of the “¿US? Motor and Gear Assembly shown in Figure 74, is held to the Unit Support Assembly (07V49), shown in Figure 76, by four nuts. Two of these ca №. № fé * gr de =. % Е д # (и É = de x y & y > e м à. ов . nee Е à : E . . ao ch : e i ob we aE . . . Lae RE BH dl # в = Еее À 3 A gr gr et et м . . .. “= i A “ 2 Hi Er ‚ м аа т * E al ze № + e | a : ER UE ae ft ee er jr . ям IS ! ere “ee ge pay ae це. Be ee „nn + | | ee eo ae pees a RES von ee u fie aa ils GR AP" ве ие 25" они“ он rr i,t ge Be Oe ney “ . кант т sag de qua dd РА eth an ag № м o | FP . ty «BR oR, css mé o aa A eat EE et fig BASE + | a À go a oi м qe e vag be gd gh a E | ~ ие АХ аи м 4% À Ex ok \ e e ив ÓN cra a M poto № . + оз в сии À нах : a ов CE NC. ! . u gen wen ong 8 о ох BLUE м. ce à . ay OH : . me Last tv + | Le A E . > % eve : ES ge Bo eut om Ge er „ен“ . . “ OS A opty : #1 À . ож CR : Bee eT ER er ба EEE a & & Rg SEE EES о о > pr a № " sigs ni E E €. os qee der mA ya o | na ane nat GE uit sut + “ RR e cda à ae Gel te a . ye © af Bt ae sé ail Hyg, ua eee Me ER wand a PR Se FIG. 52 — Removing Motor Housing Screws are directly accessible, and two, as shown in Figure 61, are in recesses in the Unit Support Assembly. Withdraw the three screws which secure the cover strip, Then continue as follows: (a) Drain the oil from the fixed gear housing by removing the drain plug shown in Figure 55. (5) Remove the four nuts which hold the support assembly and separate the Support Assembly and oil seal gasket from the Unit Support Assembly as shown in Figure 56, Reassem- ble by reversing the foregoing procedure. Note that the edge of the gasket is flattened where it fits over the worm. Be sure that the two units fit snugly before fastening them together. This will indicate that the Support Assembly shaft is correctly interlocked with the gear in the Fixed Gear Housing. Before returning the head to service, be sure to remove the oil cap shown in Figure 55 and replace the Fixed Gear Housing oil. DISASSEMBLY OF THE UNIT SUPPORT (Refer to Figure 57,) PRING SPACER 2. aoe er? a eee 3 Пт a f . * nu + .. a = м м # 2. SHROUD FIG. 54 - Exploded View of Motor SUPPORT ASSEMBLY 5 OIL CAP (4)RETAINING NUT , FIXED GEAR | HOUSING UNIT SUPPORT ASSEMBLY À A # / - y 4 ¥~DRAIN PLUG FIG. 55 ~ Removal of Support Assembly UNIT SUPPORT ASSEMBLY FIXED GEAR HOUSING (а) Dismount the ‘'UE'’ Drive Motor or ‘‘US"’ Support Assembly. Removal of the *'US” Support Assembly automatically dismounts the "US" Motor and Gear Housing Assembly. {b) Remove the ring gear which is mounted SUPPORT |! Y inside the unit support. (The gear is keyed ASSEMBLY GASKET to the rear of the fixed gear housing by two keys -- take care that they arenot lost while FIG. 56 — Support Assembly Separated from withdrawing the gear.) Unit Support Assembly “US” GEAR INTERCHANGEABILITY TABLE “US” Welding Motor and Head Assembly Gear Assembly Gear No, I Gear No, 2 Wire Feed Feed Roll Number Number Part No, Teeth Part No, Teeth ipm rpm -- -- 19N32 48 19N36 24 300 48 01Е23 29V01 19N36 24 19N32 48 75 12 01E25 29V05 19N35 36 19N35 36 150 24 -- - - 19N33 42 19N34 30 214 34 -- -- 19N34 30 19N33 42 113 18 29 INSULATING PLATE INSULATING BUSHING _ | aan WORM CLAMP SCREW FIG. 57 - Exploded View of Unit Support (c) Loosen the hex-head clamp screw at the bottom of the unit support. Then withdraw the fixed gear housing from the support, To remove the handwheel and shaft, first drive out the pin in the retaining collar on the end of the shaft. Then remove the collar and drive out the shaft. The worm will fall free as the shaft is withdrawn. The worm and shaft are keyed together. Do not lose this key during disassembly. (d) DISASSEMBLY OF THE MOVABLE GEAR HOUSING Where a single size of weiding wire is to be used continuously, it may be found desirable to install V-grooved feed rolls which are fitted to the wire size. The table which follows shows the appropriate roll part number: Welding Wire Diameter (inches) Roll Part No, 3/32 17N42 1/8 17N43 5/32 17N44 3/16 17N45 1/4 17N46 The following instructions tell how to dis- assemble the movable housing assembly for repair and replacement of rolls and other parts, It is unnecessary to order bushings sepa- rately if a replacement housing is to be ordered. Bushings are supplied as part of the housing, 30 INSULATOR FIG. 58 — Busbor Mounting Hardware and are reamed toproper dimensions. However, if only the bushings are to be replaced, they must be reamed to the dimensions indicated in Figure 81 after they are inserted into the housing. The following disassembly instructions apply equally to the standard and to the '‘90-degree’' movable gear housing assemblies, (These differ only in that the '*90-degree”” housing assembly contains an additional idler gear and shaft, as shown in Figure 61.) (a) Dismount the busbar assembly by with- drawing the three socket-head screws which hold it to the housing mounting lug. (For reassembly, see Figure 58 for correct order of parts and insulators.) FIG. 60 — Removing the Idler Gear Dismount the housing from the welding head. This is done by removing the nuts from the three studs which retain it, and drawing the housing away from the side of the fixed gear housing. Remove the cover and dust seal assembly by withdrawing the four screws which hold it. Withdraw the five cap screws and remove the roll assembly as shown in Figure 59. Remove the housing cover by withdrawing its seven cap screws. Take care not to damage the gasket during removal, (If the gasket is torn or split, obtain a new one and shellac it in place when replacing the cover.) Remove the grease from the housing. - 5 4 FIG. 61 - Interior of ‘'90’’-degree Movable Gear Housing FIG. 63 — Removing Knurled Feed Roller FIG. 62 — Removing Feed Roll Shaft Lift out the idler gear, as shown in Figure 60, Then remove the two feed roll gears and their keys. Press out the feed roll shafts from the cover side of the housing as shown in Figure 62, This will release the knurled feed roll which is keyed to each shaft, inside the housing (Figure 63). Then remove the outside bearing, _ = ; В (|) Toreassemble the parts: Place the keys in the feed roll shaft. Insert the shaft through the outside bearing hole and place the feed roll on it (Figure 63}. Align the keys with the keyways of the feed roll and press the shaft in place. Place the outside bearing over the small end of the feed roll shaft, OIL CUP FIXED GEAR HOUSING 7. WORM GEAR SHAFT SPUR GEAR SETSCREW ÿ WORM GEAR THRUST BEARING SETSCREW 8 > 0 “4 y THRUST ADJUSTMENT BUSHING THRUST BEARING KEY WORM AND SHAFT FIG. 65 — Exploded View of Fixed Gear Housing 32 LO FIG. 66 — Hinged Support Assembly and press the bearing into place in the housing. Then reverse the procedure out- lined in steps (e) and (f) on preceding page. Before replacing the housing cover, pac the housing with Texaco Regal Starfak Special grease, (This grease is obtainable from LINDE in 5-lb. cans.) DISASSEMBLY OF THE FIXED GEAR HOUSING The ‘‘UE’’ Welding Head is available with either single- or double-lead gears. To convert from single- to double-lead gears or vice versa, it is necessary to disassemble the fixed gear housing and replace its worm and worm gear. The following table indicates the parts required. Also listed are the worm and gear required for special applications which call for a triple-speed head. Worm Worm Gear Speed Part No, Part No. Single (12 rpm) 12W16 12W17 Double (24 rpm) 20W 84 29W85 Triple (36 rpm) L8N16 18N17 Disassembly of the fixed gear housing is as follows: (a) Dismount the movable gear housing assem- bly. This isdone by removing the nuts from the three studs which retain it, and drawing the assembly away from the side of the fixed gear housing. Dismount the drive motor, then the fixed gear housing assembly as directed on pages 25 and 29, rc (d) (e) (1) (8) (h) FIG. 67 ~ Gear Cover Removed Remove the gear housing cover by with- drawing the eight cap screws which secure it, Take care not to damage the gasket during removal. If the gasket is torn or split, obtain a new one and shellac it in place before replacing the cover, Loosen the setscrew in the hub of the worm gear as shown in Figure 64. Press out the worm gear shaft from the cover side of the housing. Remove the setscrew which locks the thrust adjustment bushing inplace (refer to Figure 65). Unscrew and remove the bushing. Remove the worm and shaft. To do this, it is necessary to insert a fiber drift between the threads of the worm, and drive the worm and shaft out through the front of the housing. This will also release the spur gear which is keyed to the rear end of the shaft, and the shaft thrust ball bearing. An exploded view of the assembly is shown in Figure 55. To reassemble the parts, reverse the pro- cedure outlined above, Pack the groove in the shoulder of the thrust-adjusting bushing with wicking. When the thrust-adjusting bushing is fastened inplace by its setscrew, the worm should have an end play of 0,007 in, to 0.010 in. If necessary, a new hole should 33 A PIN SGREW SPIRAL EAR e $ > e = E „в & À < woe an E FIG. 68 — Bracket Assembly be drilled and tapped for the setscrew to establish the proper tolerance. As indicated in the parts picture on page 43, it is unnecessary toorder bushings separately if a replacement housing is to be ordered. Bushings are supplied as part of the housing and are reamed to proper dimensions, However, if only the bushings are to be replaced, they must be reamed to the dimensions indicated in Figure 77 after they are inserted into the housing. When ordering areplacement housing, it is advis- able to also order a new thrust-adjustment bushing and setscrew, instead of attempting to utilize the old ones. C. Disassembly of the Hinged Support {Refer to Figure 66.) hy 2. Loosen the clamp. Loosen, but do not remove, the setscrew in the side of the bracket, Unscrew and remove the bearing cover nut in the top of the bracket. Drive out the two dowel pins. 5. 5. Remove the hex-head cap screw underneath the bracket, Using a brass drift, drive the shaft and bearing out through the top of the bracket. Do not lose the key. To reassemble the support, first place the key in the arm keyway in a bed of grease. (The grease will be sufficiently adhesive to hold the key in place during assembly.) Then reverse the procedure given on the preceding page. When reinstalling the bottom cap screw, engage all its threads in the casting before tightening the lock- nut; do not, however, screw it in far enough to lift the hinge shaft off the lower bearing. If the clamp is to be replaced, the new clamp must be marked, drilled and reamed for pinning in position. Use a 23/64-in. drill and ream to 0.374 in. plus 0.001 minus 0,000, toaccommodate the 3/8-in. dowel pins used. D. To Disassemble the Mounting Bracket Assembly 1. To inspect the gears, remove the gear cover as shown in Figure 67 by withdrawing its four screws, 34 2. To remove the platen, first loosen the four gib- locking screws inits side. (These screws are loosened by means of a hex wrench inserted through the access holes in the side of the bracket.) Then withdraw the two flat-head screws which secure the platen. Remove the platen by lifting it upward until it clears the slide. The gib will fail free as the platen is removed. To remove the adjustment shaft and its spiral gear, first remove the gear cover as directed in step 1. Then drive out the pin in the shaft collar. Drive out the shaft; the spiral gear, which is keyed to the shaft, will then fall free. To further disassemble the unit, the slide must be dismounted from the bracket, as shown in Figure 68. To do this, remove the six screws which secure it. Drive out the pin in the collar at the top of the screw. Then drive out the screw through the bottom of the slide, To reassemble the unit, reverse the procedure given above. After installing the platen and its gib, tighten the gib setscrews sufficiently to take up all sideplay; do not overtighten, since this will make adjustment of the platen height difficult. 6. 7. V. REPLACEMENT PARTS HOW TO ORDER REPLACEMENT PARTS All replacement parts are keyed on the drawings which follow. Two types of numbers are used on these drawings: A, Standard Part Numbers. These are usually formed by two pairs of digits with a letter between (for example: OIN21, 18V69). A few parts have straight digit sequence (3389) or one letter fol- lowed by several digits (A-654221). Each standard part number is accompanied by a descriptive word or words, B. Hardware Symbols. These usually have several letters preceding one or two digits. (For example: M-LO-2, M-PP-S-3.) Hardware symbols are usually accompanied on drawings by a one word description. Order standard parts by part number and part name, as shown on drawings. DO NOT ORDER BY PART NUMBER ALONE. For hardware, look up symbols in hardware list at back of book. You will find there a full description, Hardware” items can usually be purchased locally. When ordering hardware from LINDE, be sure to include the complete description given in the hardware list. Donot order hardware by the symbol alone, When ordering, be sure to state quantity of each part needed. Always state the series or serial number of the machine on which the parts are to be used, The serial number is stamped on the unit nameplate. The ''series no.** is the first digit of the serial number, wherever the serial number starts with a digit, followed by a letter, When the serial number starts with one or two letters, always give the complete number. Indicate any special shipping instructions, Order replacement parts from the LINDE district office nearest you. (See back cover.) 35 (51069 wd ÿz pre sjqnod) SrXLZ Ajquessy poop GutplomM ,.4N,, «1? (sinas uds Z| poa] 2¡6u15) L6XOZ | uuoiuf},, — 69 "914 (¿9176 8 21] HONSUM x08 94 © ,8/ct HIN3HM XO 110 06, 35 NYS LNid VIDA OS NO ВПТ HON SMM ATADOS ,L, (SONG LA TISCH L13M 143581 350H FH aS 10133 SSHONSHM MSH LHS 40 15 "NOLdHOS KT DNS me — — Weno AIBINISSY HL 03MddñAS 514 Vd PME — 31% 1d Се АС! LAN WYP 3 eee] 1GMOG. . OBMOG 43080 ND 031919345 LINDE, ELMER 93l1ddfs LON & IGNGE 9ZMBZ Ermsz Ermeı ZE “DH ¿SADO D ATEWISSV 7 71ZZ0N £9IVINODO ON uw YO SOMJB-HIHSYMIC) D SMPT LIVINOD LAN—2i-H-N{g) $8-9-5($) №3395 с8"91 3 IDASO—MBNISSY N EHMGI-ALYIG Y SEMSTEOISENNON | + D LEMSI-HOLTANNOO @ BEMSI-HOLIINNOI 1 M349S — OS1-9-Sle)- u SEMSZ | D MAY9S(& MONO > LD LOMC I-HIHS TM ых O / и. | G-M— YIHSUM(E) PME EE o A £ 621-4-5-MIUISIE) 6bl-9- O ZE Mb L-NGHSWM (9) №3855 | © o / © O (SvXI2)48A8l £L"913 Alo еже} © ХОРА SL oases ONISNOH É Oo sr: o AN Ll №3395 —801-9-5{@) 08 "9114 2bAZ0-AISNESSY SNISNOH | SPAMGI-SIY Id SIHONI - FWIS AT31VHVdIS 38 ISNA LOB AISWSSSY OVH НИМ ОЭхНУи SıLdvd “ALON MASIA, Id a LAS TO BSMZI-AFMIE) Lemz 4739 WHOM 2-MAd-0-S-MIYISIE) CEMbILIMOITVHE 6BIAAE I- LNAWOSS | о MANS о O11-9-StZ er 94 N | BtAZO-NION3SSY HOLON F —h | мес а ! PAS 1-YIHSUMLD) БУМ -319 19 6)-H-N— LNN(Z) -PS1-90-S—MIHOS(2) Nid —8-9-d .CIM6Z-ONISYO £e "914 сме Ма OlAKbI - VO ObMez-31v ld E2AGO-AIAN3ISS Y YAddOH S0M3l-1340448 |SMEI-NFFHISIE) IPMZe 19а Nid—8+-4-0-die} SSASO-FNL LGMPI-THOA SOAZO-AMIAISSY 9313399 97'914 M2I-44770ù (2) EtALO-MANBSSY LHOddMS 530nM19N | IGALO-AI9NISSV 13989 B JOINS 36 Buysipac wds yz (Z $21125} SZSLO Ajquassy poay edit „$П,, tfPusoiug,, = OZ "Old 612026) ш9а 21 (© $2142$) $2310 ‘#00 NO SSHONI - 39S QalsIOadS ATZLVYWd'S 39 LSNW LNG ATENZISSV D 6 ee Re OVSH HLIM 93Йаап$ JON D OIASVA SLYVA CJLON oto MT ONO TL A EIASOH 1T13H | I2M5Z | : | | | | 19381 350H E Crise . Was 17134 5 EME! (916 8.2/1) HONGYM XOË (GMOS (oft 8 DEI HONIHM Kor 1 CHADS. MOOS, 275 NVO LNd | 2806 zi*Dld _ JSTIUD VS, OOH NYO BTA 2 Comes © OSWISSY 31770N LOVLNOD HOME Lawgos.l, 1 IGNOB yO SIHONZHA X3H 1499 30 195 | ¿SAGO AT ry NOL d HOS a None ÓN Law DS LOVLNO ¿8-4 IHSVA (E) TANISSY HIM Olddns SI LAN LIH-N(E) 28913 vB SE) El IOAGO —ATAWASSY YYASnMAa SpMGI-SLV Te Г q | . thdO—AISMNASST LHOddns IT]. _ E Ut Wd be) GOAGZ УМРУ io a ji (WISE) лба > bMGI-3J1W 1d Е Ма АЗ (Z LN KEWISSYT 9 PSMEI-UAHSUM (2) a мн ом 3935 8 ном GEMSI №3395 —0$1-5-${2) J LON WT E 34 _ сема- 1345597 РОМС1-НАНЕММА | Г. ® S-M-HIHSTMIE) PIMZI-UIHSUM N о E + 641-4-S—M3IYOS[E) №3395 -651-9-6 f 22 Mb1-A3HS MALO) E PI СР ® 11 *914 | bbALO-NONASST ONSNOH——— o 2-0-4d-0-S—-MABOS(E) | BIM£I-LNINO3S ObPMES- JL Id IHMZE- IV Id MIYJIS—8OI- l / \ \ CHM2C- 31 1d + P # - 08*91 3 Г COMILLAS , ZpMee-3IWId 2bAZO-SIBNESSY ONISNOH CIMGZ-ONISUO ; САРУ + ObMGI-HAHSVM(b) , ISAE |-NIAHOS(E) y [61-H-N—LAN{Z) E8 *D13 8SAGO-38NL bSI-9-S-MA49S(2) GCAGO -AENISSV Hdd0H Nid—8-9-d SNAZO —AWSSSY 274479 — SHMZI-Nid BOMZI-LIHOTHE Nld —8b-4-0-dí3) ZB5MPI-IMOA IPAAZI-HS 1108 (2) SION TON! IGALO—AIENISSY 13448 8 309 37 06X0Z — Aiquessy poo} Burpjam ees60p-0% ,,3N,, ..HewuoMp,, — LZ “SIs 5ЗНОМ - 9149$ 9 G po € 2 | O | | | | | | | CT? | CI Z8N9I я EIET 22N9| 2 El GEN9I = (91/6 8 271) HONI9M XO8 | 6MOS BINS! аа! ZE (9142 8,8/2) HONZMA XO8 1 D6MOG "5 Ю 054395 №2 има ¿3MO6 м9! $29! Я 357349 VMODAOH NYI'BTT 2 ErMER ON uve ON Ltd TS JUIN HONSEM 134006 ,4, | IONOR SYNIWANND “9409 — JAMUVAANO D305b was 113 3 FP Mel Way Way S3I1770N SSHINSYM X3H 1H9I3 30 135 i £9460 6SMZI-ASH NOH LdiH95130 NYOD ON Ltd 33090 NO 03/4/9348 3199436 39 150% Ing | 06x02 AIOW1SST OY3H 3dAL 30, HL HLM IITIENS BIMeI-H749 WHOM 08x02 - AAWNFSSY HLM QO3IddNS SLavd LON S| (Sluvd OS0VHS) NOISNILX3 HYASNA WLNOZWOH: ION MIYOS y SEMZ2I-LIMSYS SEMSZ-MIHIS (2) ¿-1M--0-S(É 2°14 PrAZO-MIGW3SSY ONISNOH 61 MEl- LNANSSS Sy 5 2 2 So” ‘ O Pr ® L NOLLAYD a} COMEC -LAHO9VHE CIMGS-ONISYO CIMbI-d79 ISMEI-N3349S (€) BGA6O-3an1 S0AZ0-MBNSSSY 3714478 HAHS TM — 2-M Mau 69-0 N FEMGI-ONIHSNA (E} NY 4 €8N31-LNWHS07 SION ION г 27 Ah © 9 VE O) A N o Ih SPMSI-ALlWd 8 МСУ Ла BSA\PI-LON (2) (278% 1 338) 41Z20N (LON 335) CXYA 133361 OL do NOUWNIGWOD 9356539 ANY NI YG ATONIS 38M) FANSI-FAASA TS ONLY TSN CéNSIANI-81) 3ENk NOISNILXS CEMSI-ONIHSNE (2) bSME|-YSHSYM {2} MIOS —OS1-9-S (2) A E 98M2l-9N 1S(z) SEMZI- 1082} BGAZO-AIANISSYENS HYasng UPMSI-YIHSUM [bh 61 -Н-М— (ПМ (2) ‘ #91-9-5-M349St2) 22914 8~AZO-XTGWASSY YOLOM O © O O LO O O O осо CPMES-31Y T4 O4 MSl-SNIHSNE FSMEI-YIHSYM FLMGI-HIHSUM 6v1-9-S-—MAYOS IDA CE -310 1d 92 "5313 6bALO-AIGWASSY LYOddNS SEMGI- LON WYP 9 243376(b) EVMGE-31V ld 178 '914 6SAGO-ATAW3SSY ONISNOH ébMet-J1V 1d 38 PART NO. 19V52 PART NO. 19Y53 Il li 25° CURVED NOZZLE ASSEMBLY о FOR SHEET METAL 25° CURVED NOZZLE ASSEMBLY OR FELLET WELDING FOR 3/16" & 1/4" WIRE | О FOR 3/32" TO 5/32” WIRE — 7 Part No. | Amt Description MOVABLE FIXED Part No. | Amt Description . 19V51 1 | Curved Nozzte IV 1 _[Curved Nozzle 1009 q JAW | JAW 41W99 1 |Ins. Sleeve _ | | 105. Sleeve — => 19N43 | T [Tip Nue DNS Гм [19N47—| I [Tip for 3732" Wire | | JONSO | 1 [Tip for 3/16"Wire | | CONTACT JAWS 19N48 1 | Tip for 1/8"Rod 19N51 1 | Tip for 1/4" Wire The contact jaws, replaceable parts of the busbar 19N49 1 | Tip for 5/32" Wire N-HJ-B-21} 1 5/811 Hex. assembly, are used to introduce welding current to 578" He ll Beass Lock Nut the wire. NHJ-B-2l) 1 Brass Lock Nur WIRE GUIDE 18N11 Wire Size, In.| Movable Jaw Stationary Jaw WIRE GUIDE 18N11 (Not incl, in assembly) (Not incl. in assembly) 3/32 Part No. 07V11 Part No. 12W83 1/8 Part No. 07V13 Part No, 13W31 5/32 Pare No. 09V31 | Part No, 25W22 3/16 Pare No. 07V14 | Part No, 13W32 N-HJ-B-2I-NUT 1/4 Part No. 07V15 Part No. 13W33 —— 5/16 Part No. 07V 16 Part No. 13W34 LINSULATING SLEEVE —-41W99 | u _ O 7 о о o SS 25° CURVED NOZZLE. WIRE GUIDE 18NI | ^- = I9V50 1/16 TO 5/32 WIRE N I9v51 3/18 TO 1/4" WIRE BOLTS TO TIP NUT-19N43 BUSBAR О HERE | TIP (SEE TABLE) 65° 41W29 INS, A FOR FILLET WELDING FOR SHEET METAL WELDING 30 5" EXTENS 7 | | HIW30 5" EXTENSION CURVED NOZZLE ASSEMBLIES 4iW76 INS. SLEEVE _ HE E 4IW98 2" EXTENSION N ri HORIZONTAL BUSBAR EXTENSION ~ Used wich UNIONMELT +IW99 INS. SLEEVE qe ‘UE’? 90° Weld: , 20X90. Must be ordered ly. zul; elding Mea ust be ordered separatel y 16N39 NOZZLE or NOZZLES AVAILABLE I6N4O INS. SLEEVE DS 45 DEG. CURVATURE | 60 DEG. CURVATURE om ROD SIZE PART NO, PART NO, 19M43 NUT O 1/8" 16N 74 16N78 5/32" 16N75 16N79 7 IN ae т 1 u 77 М8 ae, 16N81 STRAIGHT NOZZLE ASSEMBLY i — i8-IN. EXTENSION ТОВЕ 16172 TIPS Wire Standard 1/4" 19N51 2902 16N73 INSULATING SLEEVE a 3/16" 19N50 EXTENSION BRACKET = 5/32" 19N49 1/8” 19N48 Threads of extension tube should be lubricated with 3/32" 19N47 Crawford Fitting Company's ‘‘Blue Goop" Lubricant. FIG. 72 — Nozzle Assemblies and Contact Jaws 39 SVALO — Ajquassy 10j0W — £Z "914 IBMES DAÑO 1SINOJIS SNÓLIVOIMIOIAS ONIONIMSY HOS SLON INN 2-PH-N(2) 99M -ONUS(E) SOMbS-Y3HSVA 2007 (2) LOVINOO JWAW 310d-¢ 6iM06-T1TI4SHS Std ayoo — (niksz)6 2 -39-9-W ISM28 -TYNINYSLZ) IBMO&-LINN PIMSI-HOLOANNOD "SCAILS “ON Asquiassy saps0 “aun 10 S]JO> pjajy a5o¡des 07 "127с9г PAOGD SIDQUINU [OJ1BS GJM SIOJ0W 5I3A02 BUIMDIP 54 1: LON SOMES LANADO 1 NV4 8 LIVH5 FENLVYNYY OOMES - HIHS VMÍE) G-71-HS-M—HIHSYMIZ) OIMPS- 0G2-1-S-—-MIH9S(2) GOMOS - SNIAY 39 INN-3-CH-N 29M2l-anLSiz) №3495 —9ЭИ-Э- Malad Yds = } pomps MIBISIE MAYS — 2dI-y-S (8) п M3 lA bLMOS - Y3A09 -LOMPS-MIYOS (Z) 92MSI-HSNYA (2) HOMES -YIHSVMA Y3070H (2) 3 19M0S-H3A09 29MCI - 13 ILMOG-dN0 22M06—3 lddiN 6905-9935 COMES— LON (+) OMEG-dAY 19 Z9MOG-ONISNOH Y. MIA 338 {1 310N 339) ESMOS — DNISNOH IMbS-ONIM 8 HIJTIOH HSNYS (310N 335) PTE (310N 338) $ 103 9133 40 ZOMES— GN1S(>) (ssDac) wdı 97) GOAGZ Aiquassy 402 UD JOIOW — . (510.9 wdı ZI) LOAGZ 19 ЭР М - УД "514 HOGYY OIYIOINOHS VIO 35367 SIOS 0 HLM NOILSOd М! 55364 -© FLON YOGHY OFEIOIMONS VIG BREE SLE9 V HLM NOLLISOd NI SSI4d ~F FLON (7 МОМ NÉ ANNE 2-H-S-M389S(Pr) SIGH TON! Weit BE-SENEI — 9 ZOAGZ—AIGSWASSV ONISNOH 9739 a 3949 SENEI- LANSVO Wdë 31 - 2CNEI = (Z TION 735/88M£6 — ONIHV 38 (2) e1-71S-M 9 SION TON! | IHSVAMIDO (E) SOAGZ—AIGWASSV LYOddNS INN-SP-H-NIE) (EOABZ N! GIONTONI) HO 8S8ME6 —INIJV 18 | 911-9-SS—M3Y0S e, Tad AT ГИ AZ I6MIb—NId y «> у ie EN Qo NN | 7 ¡ENGI— 1 4VHS As Q IR ‘cm PT | SSSR A \ E к 7 LR ZA] ZEIT = N re > G-M-A AJA E a thy “62 19Vd FH ER NO 318] SAV3D 30 | SLR E 9№11$11 313714и09 803 IIMZI-4V39 NZ 8I-H-N— LAN(Y) (22) ¿9521-00 1S(2) (2) 99MZI-0NLS (2 G8MEG-Y4ANIV 13312) E-M- AAA) 82N6|- 4V39 PBMES— UIHSVYM (ZOAGZ Ni GIGNTONI) WAY PE—GENGI uY39 COMEG— ONIJV 38 Из 2; -9Е М6 86Z202—HANIVHLS | SION TON! pOAGB?—A IEWASSY LNAA (SL 9/4 335) S2A ¿GA MBNISSV YOLOW 41 SZALS — Aquiass y 6n¡g pub 1040 HOA-ZE — SL "Dial #10 10H HSNHG—L8SMSEG (2) MAYOS HSNY9- EBMSS (2) I = renos) Wii В N (WW S)ONIUVSS-62MGS HSHSVMMD0 1—2.2 MGS (2) M3H9S—9/ MG (2) 134391399 -[3MGS 01314-S8MSS JUN LVWuV-98MSS THE ZENS A RUN] чат ит- —^ 25 и - ПИ € nn ON ONIYY 38 OBMSS (SONIA 8 SQHOD'S TUNING LINA LOYINOO'TVGHS ONTd SIGHTING OvASI-AISNASSY пла 8 0V31 3LAIdWOO 92A2LS (NI-7S) G2ALS B EGAOS(NI—ZI) QHYOD—92-39-0-W MISIS—-S¿MGS A GNLS-O6MSG(E) KIANISSY Hsnye lg IT, A vEBMSS(Z) NS ON — и HEIL III) > "Gan iddns 38V 9 -M—SUJHSVM E 6b-H-N —S LAN VHLX3 £'SHOICW SONVHOXA 403 JION ONIYdS 84MGG (SAS) SENS | [IZALS E EBAOSJSBMSI 1140748 MIYIS— 2 MSG(C) 29 MO6—LINN LOVLNOD J1VW 3104-9 GEMOG—TTHHS MIA 6 ОМ (8) ( 62-3 L6MbI-ONIY N NIZG) 62-39-I-N— Я = YA 331738 NIVHLS ЕМС — 5М96 /FWNIWHSL o 981425 UNI-02) na GEALS 8 EBAOSÜNI-PS) TT QUOD—92- 39-01 42 COLL AR-I2W54 (2) BUSHING -12W95 PIN KEY ENT P-G-26 SHAFT-12W53 SUPPORT -+2W05 $ И Зент вояки COVER -l2W90 COLLAR-13W18 L. |) (9)5-0-РК-Ц-2— CS WASHER-i2W24 5-H-244 — SCREW FIG. 76 — Unit Support Assembly — 07V49 HOUSING-12W01 (INCLUDES REAMED SPUR GEAR A SHAFT-I2W13 POINTER-13W20 — BUSHINGS,OIL SEAL SFÜR GEAR-IZWI2 ÜINGLUDED IN VEWOL OILSEAL-IIWTZ - AND SASKET, (2) BUSHING-12W28 STUD-12W64 SEE NOTE: 1) BUSHING-12W30 KEY—12W58 REAM TO .750 DIA. REAM TO O625“DIA. (INGLUDEO IN 1EWO!) {INCLUDED IN 12WOt) WORM GEAR—12W17 ~~ TT (6)SCREW-S-H-2 | a (4)SCREW-S-D-PK-U-8 \ CAUTION NAMEPLATE -23Z19 O SCREW— SS-C-114 SEE THRUST BEARING TOLERANCE ALLOWANCE BEFORE DRILLING | SS-G-114 — SCREW \ SCREW—S-H-5 i rm (2)M-PP-C-1 © PLUG O BEARING-84W 70 \ BUSHING-12W33 BEARING-89W76 / S-H-6—SCREW m (Z)KEY-I2W6O PACK SHOULDER WITH NUT, SCREW—S-H-240-2 +000 WOKING COVER—I2WO3 (GASKET ane Wet WASHER-M-WG-30 O10" OF TOLERANCE BETWEEN SHELLAC TO CASTING WASHER WORM & SHAFT- 12 WI6 WORM THRUST BEARING L_.. SPACER-I2 W62 NOTE: WHEN REPLACING HOUSING ORDER I2W33 BUSHING AND SS-C-114 GASKET —12W92 SET SCREW, (2)S-R-B-1 SCREW NOTE-WHEN USING DOUBLE THREAD GEARS AND ELECTRONIC CONTROL FOR HIGH SPEED WE Lo PAR’ NO > ERIAL, SUBSTITUTE PART NO. 29WB4 FOR I2Wi6, AND NG ON LIGHT ‚2985 FOR !2WI7 USE RESISTOR 89W8O ACROSS ARMATURE LEADS IN CONTROL BOX NOTE: FOR TRIPLE THREAD GEARS,ORDER WORM I8NI6 AND GEAR 18N17. | | 07V44 (Singl FIG. 77 — Fixed Gear Housing Assembly 18V87 т ат) 43 UOISUSAXT JDJUOZHOH WHIM POSE, | Afy,, -Fulping ouoisuewid — 6/ “Old S91|QUIISS Y AZZON YHM PO9H „„П,, ШТО |очо$чеш! а — Bf “Did ~ “TOLOW 4 NOISNIALX3 „8! 1 |, — | mn _ 4 AM 3"1ZZON.09 A t SNIGYH , 01 B06 31ZZ0N ¿09 _ y Sep JIZZON „St re mm * | NOISN31X3 8) 31ZZON SP LNN Y MIYOS avo ff OH 120905 ,8/1 2 X 12-8/£ NOILS T0 Hd SHIM aT В Boy 2 22 = нот an u . —— J1ZZON __--~ NOISNS.LX3(Z} OV2H-N yvesng J0 ONG | tl Ol 39 1M DNI G13M р este LAN 8 MISOS dVö OH LINDOS, 4 2 X bd-8/€ fy + | mE TT SON SUN à u — Fu an 4 N ie > 1 À She L BE o Ib 44 LVALO — Ajquiessy Buisnoy 4139 92/GPAON = 08 913 £0Ab2 NI CIONAIONI TOBIAS SIHL HIM SINVA Y 199, NOIL93S ¿SMEI=AJA (bd) ócoMcl— 1 4YHS (2) JNAN—-12-H-N(Z) SIM2I— 439 HNdS{) bIMZI—-ANLS() tEM<I— YSHSYM(2) M3YOS—%¢-H-S(2) о JO 4 M3YIS— SE-H-St | в о VINGI— ONIHSNE | SIONTIMI 90Ab¿— TIOY —EINSI—NiId 21-49 -d4——Nid(e) — PENDZ —M3U9S ONILSNTOY — LENOE —— 9018 - S3QN ION] D № СОЛЬ b) KIEN3SSY 7108 ONINILHOIVE LS SONIHSN8 < LSS; i, LY MBIA SAQN TONI A NT i AAA Le un M34DS— £OI-HA-SIe) OSMEZ—38N 1 ом! oe fF “AS г р HN ANOZZIO-N ONISNOH Co Yes BZN ЗУ 35 > ] 777 RE sal ce " if N RN LAN—8b-H-N— 44. DR SPMEI—ANIS-- M349S eff a У ИАА ¡Ya bbMZ]— 311V 1d — 2-M-Ad-0-S(Z) PAS MÍO ErMEI— 1738 — le > SrMEI— Y3A0I — O / IPMEI— 193$ — M3HOS SBA S3QNTONI 801-73-${2) 2м<1 E ILALO—XISNASSY 71738 8 Y3A09 = YALNIOd I een EEE „8-8. NOLLO3S MENOS AAA EE — M OBWAS SIHL HLIM SLHvd 71717 SAQNTONI ONISAS(Z) 62M2 1 — ONIHSNG Z0Abt ed —ATAWASSY 1104 SYNSSAYd AIAVON ONIS 3 A №3355 SIGN TONI - 1 ий “He N „V-V, NOILO3S nd, IMEI АЗЫ Lge ES-H-Sth) AIBW3SSY YV 39 UNAS bOMZI—YIAOD ObMZI-— 1104 0334(2) ry FF PS __ bINGI—ONIHSNE Y Ir ISMZI— LDASVO done À РИ KR A JOAP2— 1108 1 OS INSI —NId N Nid —S6-d-d-d р 4 | eR OLE GENOZ — 907 A Y II N DIR ER RER bOAvE PA . ЕР AIBN3SSV 1O0Y 38NSSIWA(Z) ZOM21 NI GAQN TONI гоме! м азаппом # GENOS— HANIVL3H 99078 92M21— ONIHSNB(2) LeM2I—9ONIHSNA() „3518 01 ИУЗЫ «586 Ol WV3U # ZENOZ — ONIUdS (2) # OfNOZ— FLW 1d YIAOO 45 65A60 — SUISNOH 1032) ajqoaow э246эр-06 — 18 “ODIs ‘uosg{sod [OIJLLDA 105 SIJOY ,,A,, 4] pub UOJHSOd [OJUOTJIOY Ul энм 10; #2104 ,,X,, Ul SPA¿S 930] y "YOJIJSOT [OIJLIDA и} рецяэр $! энм Виррэм USYM SPNES YIMAS ¿ION 310N 335 IZM6é- ON. LS téMel HAHSYM (2) LAN -12-H-N(2) 310N 335 taMEI-INLS (Ser6* WTS INIT LIMES — AIM OFCN TING ¿ZM21-9NIHSNO(3) OGMZI-ASN( +?) fecie’ WW SY INIT МЕ HM GFON TONH YIEMZI-ONIHSNALZ) ОФМС | -931108 033412) {SONIHSIG CAFE SICHT) ¿IMG - ONISNOH M3YOS —2-M-Md-0-S[b) cH S GIMGZ-LINSVO N ‘ SEN EN — NOE o e IMGZ-8IAOO CS 66-4-9-9-ма@) B2M2I-ONIHSNE {2} o CtA4O-Hw39 (2) ¡2ME€1-HILNIOd (2) @) p9-9-S— MANOS 2) PINS I-ONIHSNE ({SFGN TON £0AP2—1104 M3AYOS-LE-9-SS SINGI- Nid SENOZ-A90 718 SON TOM A POAPS L— Man3assv Mo 340155344 12) O O O | 22M21-1 4VHS(Z) 77 y ¿ESMZLAZA(Z) A ca er . ес!-ня-$ (2) == AT GIAZI-4Y3I9 HNdS (2) о NER "M349S — BOI-14-S(2) > y LINN—8b-H-N — SPMEI-ONIS — bHANCI-31Y T4 — ChMEI-7173S — £G-H-S—M349S{t) ZPMEI-HIAOI — IPMEI- IS 4 SF Tove IpAZO-WASSY 193$ 8 H3A09 MOcNO¢-HANIVLAY MOOT PING! -ONIHSNG SION TONI 9OAte- 110 CING] —Nld ¿1-9-d-Nid (2) PENOZ-MIJANS 9NILSNTOV ££NO2-49078 MI3UIS-E-9-55 (FICTION) GO AE „лай 3559 T1048 ONINALHSIVHIS MIZNO? -ONIMdS{Z} | MAHOS-¢6-9-Si bP) # 22NO02-ONINdS(Z} POSNOZ-Jlv ld YIA0D M TOMAS SIHL HIM S14V0 TI SIONTIONI EDAPE-AIBA3ISS Y 71104 IHNSSIug 030909071 Ома 46 (2) BUSHING — |5w33 BUSHING-12W70 (4)SLEEVE & JAM NUT- 5-R-B-134 - SCREW W-B-4 -WASHER (3)BUSHING-1I5W34 SILVER SOLDER _ ISW35 AC) O O = BUSBAR ASSEMBLY-07V99 (INCLUDES) ——, (2) STUD-12W86 7 T SCREW (2) BOLT -12W85 | Cr ross BUSBAR -15W32 Н 5 N-H-18- NUT $ | 7 (2)BRAID-12W88 $ all O . S—WASHER-13W54 TT S-H-48— SCREW # | ER-13W54@ Cr N-H-18—NUT $ | SCREW - —S-H-79$ O -SPRING-12W8 | (3)PLATE-12W87 8 O s (23N-H-B-18-NUT—7 JAWS AVAILABLE FOR USE WITH TYPE “U" WELDING HEAD @ MOVABLE JAW | STATIONARY JAW WIRE SIZE PART NO. PART NO. 3 > OrVI 124/83 3 07VI3 (3W3| .. y . 5” ‘Ay ONE SET 35, TWO SETS 7g AND TWO SETS y JAWS > 09v31 25W22 22 FURNISHED WITH WELOING HEAD ASSEMBLIES 20x58 & 20x59 5 O7VI4 13W32 FF W PARTS SHOWN WITH SYMFOL ARE PACKED я O7VI5 1333 IN A BAG AND MUST BE PURCHASED SEPARATELY: 5" FOR COMPLETE SET OF PARTS IN BAG, 16 СРУБ 134134 ORDER PART NO.-/1992, FIG. 82 — Complete Busbar Assembly — 09V01 SHAFT-I9W35 P-G-24 —PIN Ye + 2-DRILL (2) DISK-14W26 (3) BUSHING -14W31 WING NUT-14W87 SECTION "А-А' HOSE-29W25 (5" LONG) LHOSE-29W26 3FT LONG SUPPLIED WITH ASSEMBLIES 20X58 & 20X91 FIG. 83 — Hopper Assembly — 09V39 47 £0A60 ~ 4[quassy 1945019 Buyunow — FE ‘914 №3495 -— 20$ -13-5(2) BSMSI-L3NIVYO ZPMGI-MIAYIS IGANG 1- YY 1710012) (ем: м азалтэми (929 01 Av32)vSMS 1- ONIHSMO BPMSI-4V39 “Weaids ern EG и "WOLLY3A ЗАЛ mio E Nid —Sb-9-d{2) 6PMGI-YVAD “WeldS YIHSVA 13315 ‘39$ =! jr wat HIHSYM 13315 WS м = M3405 dvd 0OY3H XIH „EXEI- [eu №3495 dv9 OVIH X3H „IXEI- = ba №3425 ачо 131$ OvVaH X34 97 „IXBI- in| Nm Far 2 dv19 37879 | NOLLIIHOSIO NYND KAWISSy SIHL HLIM GaIlddNS на 43°-H-5 ЗЕ-Н-5 BMP cB MP | ON 1H Nld —8¿-9-d ь | Din HIHSTM—I-7-A M349S-b+-H-S dWvw 10 —2-79-W | 4 ED al =I (ESMSI NI Q3QN TONI) {295 OL Av334) SGMSI- ONIHSNEI?) 2GMGI-H77109 180 2b LAN —SI-CH-Ni +) C-M-M(2) A3 A ñ ESAS I-IJADO ROO SD pa CE LE mile | J5MSI- LIVHS pOl-G-H-S—MIHOS( +} (6SMSI NIOSONIONI) (GG OLWNV34) 9GMSG |- ONIHSNG (2) | | PJ | OSMSI—-ONIHSNAl 2) SSAMSI—ONIHSNG{ 2) b GMGI — ONIHSNA LT SL SIÓN ESMS |-3017S SL ZUNE IV Id 48 | И — Pos ZN | li — SUPPORT -25W37 à = —|r TN a rm (23PIN—P-D-P-45 + Г | 23" a ho mL 1 ! ! ga DRILL a REAM | A | 1374 9% Da) 000 SCREW-25W39 CUSHION — I3W5I BOLT — M-B-SP-] S5-6-145 — SCREW 1" I" 5 13X15 LG. NUT-12W47 IT |. ТИ ПИ - 5 à IN N ь BI h, IN (2)PIN—P-T-104 — N i WASHER -13WI7 Jf o WASHER-13W53 1 a KEY-l2We6l yo iO aa CLAMP-25W38 — ARM-I2W06 = a WASHER-I2W39 (2) N-HJ-I9—NUT SCREW —S-H- 226 FIG. 85 — Hinged Support Assembly -— 09V41 49 P-A-44-PIN SPRING - 2106 l215-A-=F2 BODY-21N08 BRACKET-ZINIG —— if = “4° 1 1 | (2) BAND -21NO6 | de | t u | S-H-1-SCREW : (4)P-R-25 — PIN ()BELL CRANK Чи ИЕИ-А 2104 WA (4)SPRING—?87Z07 (4) FINGER—21M05 ura nur CPP DPr8=PIN BUSHING l@N24 (4}5-H-13-ScREW SPRING -28264 BRAKE DISK —18N25 SH” 247— SCREW 0 : Y (4b MABE” DRILL a Pi (4) NUT—Bowse Ne e A pli „= = SEN . -. . . о Br 5 = = P <4 ; Xi E “J (6) WASHER-S WIS W-II= WASHER SS Е N м. THRUST WASHER-ISN23 pn ak BRAKE DISK-18N25 E N (4) STUD -18N28 fe espia MPR-25-PIN m =: | (INCLUDES) A | P-R-72—PHN L (ai RING—84W80 и : EHW-AN 10 -WASHER ($ STUD 21017 WIRE CLAMP ASSEMBLY cv 33 MATS SUPPLIED | (SEE WEw JJ 18426 GUIDE SPW12 | SPRING | NUT (HIN-H-40 u 4$-099 | SCREW i 415-H:34 | SCREW SECTION “3-4” (4w-L-4-1 | LOCKWASHER FIG. 86 — Expansion Wire Reel Assembly — 29V31 ml PARTS SUPPLIED QUAN, DESCRIPTION B-H-299 2 BOLT N-H-7 2 NUT W-L.-19 2 LOCKWASHER FIG. 87 — Wire Reel Bracket — 19V90 50 ZZAgE — 26014305 BP-WO YO Buiunow Joy Aqquiessy jaey 91 LLAGZ Apquiassy ay Bulsunow pup ZZABE — abou) /£-W uo Buyunoy 103 Á[quiass Y [932 31 69AL0 — Ayquossy |224 e114 26107 te 26107} i 26107} PIDPUDIS 88 ‘914 BON L-HSHS UY) # GI-M | HS YM 58 BOMPL-ONIHSNE (DIR Sa, rere с à ; | ay, | Sh 2-2-Y-d—Nid IINTZ-iNMN SEMGZ- [108 BSMPI-MOOTE GbMbI-37ONTH pompl-uzonty G2LON 335} (5300131) JLAZO-ATENSSSY WOO1S 8 939+) 03-7-M —Y4IHS YM Z-H-N- INN Z3MPI- 1089 \ polALO- 33306 (bi / ЗУМЫ-ВОМУ / fees и Yo pOMbI-DNIHIAS Y COM 1-43INIVL3IN (E) | (МУЗА! 9351 Оруро ИИ ЗЕ 50/5 YO 2E-WO NO OMILMNON 6904 ОЗЗУО $193 НИМ TH TEIMS LON Fu? JOGWAS SIR HLM Sidi $ SH ЭН СЫ ENTE GOTO ONG SON! SH УЗ Г OU POR ALLA OU Tot IS (6iz-3-S) SAFYOS ah Hi GANGS FIN ni OL LONA SECANO (el FE HOWE TE ffAL0 SETS NOOTE 8 OYFON AY FA ЗОНЫ т —icMOTIOY SF TIPISAY OAD бы РМ ie GO IRF FAM JOST ALM FOIA WO SHO TIPWS RENO 22S-H-S-MIU0S IS LON 22-1-M— SHS UM tr) 8-H-N- INNE ZINN и 7 en / / (O) / / p SBMPI-NIVHS th) 7 NN \\ ote Sy : NN (8) Nate N | EIH-S-M3UDS 6G-Y-H-L3AIH(2) KT п 7 2 ; | |- ] и | -82-4-U-L3AIH _©.2-d-N- | ee ви \ | ose as -82-8-1-14-8 AED venues 6GMbI-HV 1109 -1-99-N-4N9 | h | eres ae | i -OGMDI-AZA (2) OLMbI-ONINI] UVA | A | (ase оптом 104 5300} ZZAST NI GAGMIONI SLYVd #ObMbI-LIMOTUE / $ N \ SYMPI-MIYOS Be | _ if A ------. -----2 SLAZO-WNAO . 2b-9-d—-Nidly) l9Mb1-2031d AN3(2) | mos, u a nn N Corn a A \ М-Н IZALO-MONASSY ONVE Dive | Soames: \ bLALO-SOdS (bp) == IIS INUMONTA ease one _ | : OST £ O Saat В Tea via "260, UNS ee (ISVMOBVH SION TON | A с | ИЕ „260 1HOdanS 7 HAGE-ATGNTSST > Î u a (EL ALO ME OFGN TONE Fd DLW ZEND ; ™—.3-G-Y-d —Nid SENGI "2 CINCO 39 O1 (LEALZO Mt GIE TON) и HIHSYM SNI aad A “ION | SLMGE — 1109 — ею м 030779м!) | | TINIZ—LNN PONE 3A3378 "SN [ELAZO Ni 0300724) /, [LLALO NI GFGN TON) Obv2-H-S-M3895 86M tl —»9078 SbMbI—310NVH G-H-N- INN | (ffALO0 Ni GFGNTONE SEMOS-ONIL Lid NIHPMPI-NIDN 4 “7 Es € SNE) — LUOdANS IpPM96 —ONINV IE | lo a. _. и 51 SCREW 5-0-229 SUPPLIED | WASHER (23-11 SUPPLIED / EXTENSION BAR - 15WI7? SUPPLIED (2) NUT -14W39 SUPPLIED BRACKET -l4W98 BRACKET-14W99 SCREW S-C-228 SUPPLIED (BySCREW-—S-0-53 (2) WASHER—W-8 (2)SCREW—S-C-94 (2)PIN—P-G-4 PIN IS WS D ie (2)WHEEL ASSEMBLY -07V95 FiG.91 ble ® | de (o | : | | O o q o Q o Q I Y O O O E) A (2)$-C-79 SCREW WHEEL & BLOCK ASSEMBLY-O7V9I NOTE-I5W62 SNAP RING REPLACING TOOL SUPPLIED. F1G.97 FIG. 89 — Guiding Device Assembly — 07V92 SCREW-O7V09 7 SUPPORT-O7 V¥94 г (2)55-С0-83 — $СВЕМ WING NUT-13W24 (2)NUT-I5W20 PLATE-ISWO4 SIBTIEWAA (2)PIN-P-C-4 PLATE-ISWO5 Bu | ESS BLOCK-ISWO3 : (MS-FL-I06-SCREW = PIN—P-G-24 Loa N E] \-SUPPORT-07V93 (2)P-C-4 — PIN PIN-I5WIO SPRING -ISWOG LS LINK-ISWO7 SNAP RING- I5WI6 USE TOOL 15W62 WHEN REPLACING SNAP RING * 44 DRILL PIN-|SWil WHEEL-O7 V8 BEARING-15W/2 E e FIG. 90 — Wheel and Block Assembly — 07V91 32 Е E AE nt 7 £4 = ae Eo o | № > E pd q в № | ft oe ic à SPRINGASWOS PIN-ISWII LINK-15WO? WHEEL-O? V89 BEARING-15W12 SNAP RING-15WI6 USE TOOL I5W62 WHEN REPLACING SNAP RING FIG. 91 - Wheel Assembly — 07V95 S0AZ0 — Apquessy Buingissig uolisodwoy Buippay — 76 "Dia 06X02 B 86x0< 6 "D]3 5378/3559 НИМ O3MdANS (£) 89AZO—AISN3SSY ANT ONY 31774 EDMSC-1435NI — £6 "913 JOAZO AMINISSV WHY TSAIMS ONV Y3AI39234 NOMLISOINOD SNIOTIM EEE A bEMbI-1Y3S GoóMti- LAN JJHSVM— 9 -M(2) LAN-I-H-N(2) MAYOS —12-9-S(2) 33 SWIVEL-ISW63 (2) WASHER -l4W28 ARM-ISWBS Чо о O SCREW-14W24 FUNNEL-14W17 LINK= 1420 (2)WASHER-19W54 — (2)BEARING-14W/23 (4)S-G-63—SCREW pica! PIN-P-D-P-9 PIN {2} PIN-14W37 - (49P-6-24 *42 DRILL [4)WASHER W-S-B-7 {4)$-T-2 М ri SCREW f (44 CUSHION -19W36 PL ATE-ISW88 NUT-14W30 (2)3BUSHING-19W46 (SUPPORT -14W 22 PIN—=P-6-27 (2)-5-C-68 * 42 DRILL SGRE W | | (2) 87 W66 РЕАТЕ-ОРУ96 РЕАТЕ-ОТУЭТ— WASHER Welding Composition Receiver and FIG. 93 — Swivel Arm Assembly — 07V67 FIG. 94 — Plate and Link Assembly — 07V68 HINGE-25W90 HINGE-32W99 (2) SCREW-25W93 ad, SHAFT-25W92 FARTS SUPPLIED SCREW (2) 55-C-114 QUAN, PARTNO DESCRIPTION 6 S-H-35 g-l8X 1" LG. HEX.HE AD CAP SCREW 4 S-H-34 RlBX LO HEX HEAD SAP SCREW FIG. 95 = Rocker Hinge Assembly — 19V79 54 г HANDLE- 29W39 (2)SCREW-SS-CO-93 hs: am Ct a nn A de A A ee ee En A AA | SPRING-28Z07 BRACKET-29W37 COLLAR-29W40 {4)SCREW-S-C-66 (4}WASHER —W-L-2 {(2}PIN—P-C-10 WASHER- SHER-90W94 BEARING-90W96 CASTER-O9V64 PIN-25W87 WHEEL-25W86 NOTE: K-4-3 A KA-6 HEX. ALLEN KEYS SUPPLIED FIG. 96 -- Carriage Guide Wheel Assembly — 09V48 {2) PLATE- 41W 78 HANDLE-29W39 (2) 55-CO-106 SCREW GIB-12W4 4 {2) N > 5 5 * | о ee AA oe a ann ги Fy Ba ион ee : NET RS OS к i? $ po г A JE 3 nn НИ ete! E тия SCREW-41W8O | | I 1 L (4)S-FL-104 KNOBT4IW7S SCREW | ey sorew-ss-o-90 , BRACKET-32W63 BRACKET-20W9 | sl FORK-40W95 | PiN-40W98 WHEEL 40W36 BUSHING -40W9? WHEEL- 20W96 Lil | | | | ft О | 2 3 4 5 6 SCALE INCHES FIG. 97 — Nozzle Guide Wheel Assembly — 08V94 35 UPPER CONTACT ASSEMBLY- 55W32 SPRING” 55SW34 YT SPRING-55W97 + > SPRING | © © = 55W95 LT — Г № di 10 q LOWER CONTACT ASSEMBLY — 55 \ 93 FIG. 98 — Current Relay Assembly — 18V56 56 i ee ee A eee ET = = =. . 5088 EXTENDED POSITION 464% RETRACTED POSITION Sal USING 38v22 D PLATE -2 af Lp OOO - NN, | Fan | 287/16" Mil 3213/16" MAX. —— EN - 4 i "a. 1 о Hi _ | O \ > JC = | \ АИ \ | CLAMP SCREW HERE STANDARD OXWELD TRACK A LIMITS SWING TO 96° ee AO-O- nO CARRIAGE LIMIT OF SWING WHEN STRAIGHT NOZZLE TOUCHES SIDE OF TRACK GLAMP SCREW HERE PERMITS MAX, SWING U-HEAD MOUNTED ON CM-37 SHOWING INCLUDED ANGLES FOR MAX. SWING FIG. 99 — Dimensional Outline: ‘‘UE’’ Head Mounted on CM-37 Carriage 57 ¡999 9114 9610" pub proddng pabuypy ym poa ,,f],, =SULINO jpuoısuewg — 001 "913 „8 a9 „ze SICH tee E in N Fo Q I» A — cn MANOS dvd Г Te u 81-91/5 404939945 > od ATIWNOa TYG #9712 (9) 2! a я 5’. o SII3HM 3015 ne YO 1 SNIHdS . ¡o 30 13AV8L XVA A CH = À __ Nb, I [II ES = _ : 2 2$ A yvasna | 776 | JO ana TA © 5 713345 01S IVS wein 22A8€ | | o LAN 8 М330$ 990 303 1509415— | | - Ly _ A ; ; A 713315 "0H X3H,€ X Orb/c[(b) | ] + о 5 YOLON \ ANIASNE sm (b A 7 Г. 1 i 4 : O Ne a Е: a m an O Ö i 7 mi = ==, о 4 =. " 414 = O) | | ee alg À © “ ollo | m — $2 а © © ' Io TU 2/5 28 fs 8183 à | = ” м T7 a|e a oO 2| =i ¿DE 3 8 818 > = со | 52 N 2 sn Nm ro мо юм Pb à Xe Le | UT DC mo AD | a | = 4 SE [= | и хх TT 1 Ae / Ш / — $ Ll / 22€ NOILISOd G3LOvY13Y _ / Ñ „Or NOILISO4 UJONILX3 + 58 HARDWARE LIST available, you may order these from us. öM-C-GE-26 oM-C-GE-27 £M-C-GE-29 M-C-P-2 M-CL-2 M-GC-1 1 I ı kA iol 1 L 1 23 ds e a dE hf tt J-19 J-B-21 i 1 bt => ооо U vbopnanmann 9999 Y. TUTTO ZZZZZZZAZZAARAZAZZ 1 à DESCRIPTION 5/8-in.-11 x 5 Hex Head Bolt 3/32-in. Allen Hex Key 3/16-in. Allen Hex Key #404 (1/8x1/2+in.) Woodruff Key Woodruff No. 405 Woodruff No, 606 1/2-13 x 1-1/2-in. J.H. Williams Threaded Plain Eye Bolt Simplex Tirex Cord, Type “0”, $16 Ga. 1-Conductor Simplex Tirex Cord, Type ''50””, #16 Ga. Two- Conductor Simplex Tirex, Type “SO”, F16 Ga. Four-Conductor 1/4-in. Bla6k Iron Pipe Cap 1/2-in. Gälvanized Pipe Clamp Grease Cup (Crane Cat. 4198, . 1/8-in. Pipe Thread, Size #00) 3/8-in. Pipe Octagonal Conduit Locknut 3/8 x l-in. Clevis Pin 1/8-in. Headiess Pipé Plug 33/64 x 13/16 x 1/16-in. Annéaled Copper Washer 1/4-in.-20 Hex Nut 3/8-in.-16 Hex Nut 1/2-in.-13 Hex Nut 5/8-in.-11 Hex Nut 3/4-in.-10 Hex Nut 1/4-in.-28 Hex Nut 5/16-in.-24 Hex Nut 3/8-in.-24 Hex Nut 1/2-in.-20 Hex Nut #10-32 Hex Nut No. 12-28 Hex Nut 5/16-in.-24 Hex Jam Nut 1/4-in.-20 Hex Jam Nut 1/2-in.-13 Hex Jam Nut 5/8-in.-11 Hex Brass Jam Nut 5/16-in.-18 Sq. Machine Screw Nut 7/16-in. Williams Co.’s Thumb Nut, Type ‘'A’’ 3/64 x 1/2-in. Cotter Pin 1/16 x 5/8-in. Cotter Pin 3/32 x 3/4-in. Cotter Pin 3/32 x 1-in. Cotter Pin 7/32 x 1-in. Cotter Pin 3/16 x 3/4-in. Producto Dowel Pin 3/8 x 3/4-in. Producto Dowel Pin 3/8 x 1-1/4-in. Producto Dowel Pin Мо. 50-51 5/8 x 2-3/4-in. Producto Dowel Pin 3/32 x 1/2-in. Groov-Pin 3/32 x 3/4-in. Groov-Pin 3/32 x 7/8-in. Groov-Pin 3/32 x 1-in. Groov-Pin 59 SYMBOL P-G-45 P-R-5-2 P-T-54 P-T-104 P-T-128 R-FL=T-B-28 R-R-28 R-R-59 S-B-190 S-BH-57 S-BH-103 S-C-52-1 S-C-53 S-C-63 S-C-64 5- C+ 66 S-C-68 S-C-69 S-C-71 S-C-70 S-C-84 S-C-94 S-C-95 S-C-98 $-С-108 S-C-110 S-C-125 S-C-149 S-C-150 S-C-154 S-C-21 $-С-228 S-C-229 lt will save you time and money to purchase these hardware items through local outlets, or directly from the specified manufacturer. If no other source of supply is DESCRIPTION 1/8 x 1-1/4-in. Groov-Pin #59-022-094-0625 ESNA Roll Pin No. 0 x 7/8-in. Taper Pin #4 x 2-in. Taper Pin #6 x 2-3/4-in. Taper Pin 1/8 x 1/4-in. Tubular Flat Head Brass Rivet 1/8 x 1/4-in. Rivet 3/16 x 1/2-in. Rivet #10-32 x 3/16-in. Binding Head Machine Screw #4-48 x 1/4-in. Button Head Machine Screw #6-32 x 1/4-in. Button Head Machine Screw #10-32 x 1/4-in. Socket Head Cap screw #10-32 x 3/8-in. Socket Head Cap screw 1/4-20 x 3/8-in. Socket Head Cap Screw | 1/4-20 x 1/2-in. Socket Head Cap Screw 1/4-20 x 3/4-in. Socket Head Cap screw 1/4-20 x 1-in. Socket Head Cap Screw 1/4-20 x 1-1/4-in. Socket Head Cap Screw 1/4-20 x 1-3/4-in. Socket Head Screw 1/4-28 x 5/8-in. Socket Head Cap Screw 1/4-28 x 1-1/2-in. Socket Head Cap Screw 5/16-18 x 3/4-in. Socket Head Cap Crew 5/16-in.-18 x 7/8-in. Socket Head Cap Screw 5/16-in.-18 x 1-1/2-in. Socket Head Cap Screw 5/16-24 x 1/2-in. Socket Head Cap screw 5/16-24 x 3/4-in. Socket Head Cap Screw 3/8-16 x 3/4-in. Socket Head Cap Screw 3/8-24 x 1-1/4-in. Socket Head Cap Screw 3/8-24 x 1-1/2-in. Socket Head Cap Screw 3/8-24 x 2-1/2-in. Socket Head Cap screw 1/2-13 x 5-in. Socket-Head Cap Screw 1/2-20 x 1-in. Socket Head Cap Screw 1/2-20 x 1-1/4-in. Socket Head Cap Screw HARDWARE LIST (Continued) SYMBOL S-C-232 S-D-PK-U-2 S-D-PK-U-8 S-F-179 S-F-250 S-FL-104 S-FL-106 S-FL-108 S-FL-507 S-H-2 5-H-4 5-H-5 S-H-6 S-H-34 S-H-35 S-H-48 S-H-51 S-H-53 S-H-63 S-H-79 S-H-224 S-H-226 S-H-227 S-H-235 S-H- 240 S-H-240-2 S-H-244 S-H-247 S-H-322 S-R-58 S-R-172 DESCRIPTION 1/2-20 x 2-in. Socket Head Cap Screw #00 x 3/16-in, Parker-Kalon Drive Screw #2 x 3/16-in. Parker-Kalon Drive screw #10-24 x 7/8-in. Fillister Head Machine Screw 1/4-20 x 3/4-in. Fillister Head Machine Screw No. 6-32 x 5/16-in. Flat Head Machine Screw 46-32 x 7/16-in. Flat Head Ma- chine Screw #6-32 x 5/8-in. Flat Head Machine screw 5/16-24 x 5/8-in. Flat Head Machine Screw 1/4-20 x 5/8-in. Hex Head Cap Screw 1/4-20 x 7/8-in. Hex Head Cap Screw 1/4-20 x 1-in. Hex Head Cap Screw 1/4-20 x 1-1/4-in. Hex Head Cap Screw 5/16-18 x 7/8-in. Hex Head Cap Screw 5/16-18 x 1-in. Hex Head Cap Screw 5/16-24 x 3/4-in. Hex Head Cap Screw 5/16-24 x 1-1/4-in. Hex Head Cap Screw 5/16-24 x 1-3/4-in. Hex Head Cap screw 3/8-16 x 3/4-in. Hex Head Cap Screw 3/8-24 x 5/8-in. Hex Head Cap screw 1/2-in.-20 x 1-1/4-in. Hex Head Cap Screw 1/2-13 x 7/8-in. Hex Head Cap screw 1/2-13 x 1-in. Hex Head Cap Screw 1/2-13 x 3-in. Hex Head Cap Screw 1/2-13 x 4-1/2-in. Hex Head Cap Screw 1/2-20 x 1/2-in. Hex Head Cap screw 1/2-20 x 1-1/4-in. Hex Head Cap Screw 1/2-20 x 2-in, lg. Hex-Head Cap Screw 3/4-10 x 3-in. Hex Head Cap Screw #4-48 x 5/16-in. Round Head Machine Screw No, 10-24 x 1/4-in. Round Head Machine Screw SYMBOL S-R-B-1 S-R-B-104 $5-C-90 Ss-C-91 SS-C-102 $S-C-114 55-C-116 SS-C-132 SS-C-145 88-СО- 83 SS-CO-93 35-C0-106 S-T-2 un 1 H 1 I an ı 7m Mm NS | rm q gadacede mr Poe eon ou | po W-L-4 W-L-19 W-L-20 W-L-27 W-5-B-7 W-SH-L-5 W-SL- 12 DESCRIPTION #2-56 x 1/8-in. Round Head Brass Machine Screw #6-32 x 5/16-in. Round Head Brass Machine Screw No. 10-32 x 5/16-in. Socket Head- less Cup Point Setscrew #10-32 x 3/8-in. Headless Cup Point Setscrew 1/4-in.-20 x 3/8-in. Socket Head- less Cup Point Setscrew 1/4-28 x 1/4-in. Headless Cup Point Setscrew 1/4-in.-28 x 3/8-in. Socket Head- less Cup Point Setscrew 5/16-in.-18 x 5/8-in. Socket Head- less Cup Point Setscrew 5/16-24 x 5/8-in. Headless Cup Point Setscrew #10-24 x 5/8-in. Headless Cone Point Setscrew #10-32 x 1/2-in. Headless Cone Point Setscrew 1/4-in.-20 x 3/4-in. Socket Head- less Cone Point Setscrew #10-24 x 3/4-in. Туре ‘'C”’ Williams Thumbnut 3/8-16 x 1-1/4-in. Type ‘‘C"’ Williams Thumbnut #10S.A.E. Washer #12 5.A.E, Washer 1/4-in. S.A.E. Washer 5/16-in. S.A.E. Washer 1/2-in. S.A.E. Washer 3/4-in. §.A.E. Washer #5 S.A.E. Brass Washer 1/4 x 3/32 x 1/16-in. S.A.E. Lock Washer 1/4 x 3/32 x 3/64-in. S.A.E. Lock Washer 5/16 x 1/8 x 1/16-in. S.A.E. Lock Washer 5/8 x 13/64 x 5/32-in. Steel Lock Washer 5/8 x 13/64 x 3/32-in..S.A.E. Lock Washer 3/4 x 1/4 x 1/8-in. S.A.E. Lock Washer 1/4-in. S.A.E. Small Pattern, Brass Washer 1/4 x 1/2 x .025 Shakeproof Lock Washer No, 12 x 1/16-in. x 3/64-in. Steel Lock Washer 61 LINDE Supplies These Quality Products to the Nation’s Industries INDUSTRIAL GASES LINDE Oxygen, Nitrogen, Argon, Neon, Helium, Krypton, Xenon, Hydrogen PREST-O-LITE Acetylene CALCIUM CARBIDE UNION Carbide CARBIC Processed Carbide OXY-ACETYLENE EQUIPMENT OXWELD Apparatus for Cutting, Joining, Treating, and Ferming Metals Acetylene Generators Manifolds, Regulators and Valves Welding Rods and Supplies PREST-O-WELD Welding and Cutting Apparatus PUROX Welding and Cutting Apparatus PREST-O-LITE Air-Acetylene Apparatus and Small Tanks CARBIC Acetylene Flood Lights Acetylene Generators ELECTRIC WELDING EQUIPMENT UNIONMELT Automatic Welding Apparatus and Supplies HELIARC Welding Torches LINDE Sigma Welding Equipment SPECIAL EQUIPMENT LINDE Jet-Piercing Equipment Plate-Edge Preparation Equipment Steel-Conditioning Machines Sub-Zero Cold Treatment Equipment OXWELD Oxy-Acetylene Cutting Machines Pressure-Welding Machines PREST-O-LITE Cylinders, Shells, and Shapes OXYGEN THERAPY SUPPLIES LINDE Oxygen U.S.P. Oxygen Regulators OXWELD Oxygen Manifolds and Valves SYNTHETIC CRYSTALS LINDE Synthetic Sapphire, Ruby, Spinel, and Titania Fine Alumina Abrasive The terms “Carbic,” “Heliarc,* “Linde,” "Oxweld,” "Brest-Ö-Lite,” "Prest-O-Weld,’' “Purox,” “Union,” and “Unionmelt” are registered trade-marks of Union Carbide and Carbon Corporation. LINDE AIR PRODUCTS COMPANY A DIVISION OF UNION CARBIDE AND CARBON CORPORATION Mi General Office: 30 East 42nd Street, New York 17, N. Y. Sales Offices in Principal Cities—See Adjoining Column Lithographed in U.S. A, F-9213-C IMD J-4820-56 LINDE OFFICES General Office 30 Eust 42d Street, New York 17, N. Y. Eastern States BALTIMORE 18, MD., 532 Easi 25th Street BOSTON (Needham Hgts.) 94, Mass., 300 First Avenve BUFFALO 2, N. Y., 250 Delaware Ave. CHARLESTON 1, W. VA., 2 Virginia Street NEW YORK 17, N. ¥., 205 East 42nd Street PHILADELPHIA 22, PA., 1421 North Broad Street PITTSBURGH 22, PA., 644 The Oliver Building Central States CHICAGO 1, ILL, 230 North Michigan Avenue CINCINNATI 29, OHIO, 709 Melish Avenue CLEVELAND 14, OHIO, 1300 Lakeside Avenue DETROIT 21, MICH., 10421 West Seven Mile Road INDIANAPOLIS 4, IND., 729 North Pennsylvania Street MILWAUKEE 46, WIS., 1623 South 38th Street MINNEAPOLIS 2, MINN., 827 Second Avenue, South ST, LOUIS 8, MO., 4228 Forest Park Boulevard Southern States ATLANTA 1, GA., 310 Peachtree Street, N. E, BIRMINGHAM 9, ALA., 2900 Cahaba Road JACKSONVILLE 3, FLA,, 2410 Dennis Street MEMPHIS 5, TENN., 48 West McLemore Avenue NEW ORLEANS 13, LA., 8238-32 Howard Avenue Southwestern Stafes DALLAS 1, TEXAS, 2626 Commerce Street DENVER 9, COLO., 685 South Broadway HOUSTON 11, TEXAS, 6119 Harrisburg Boulevard KANSAS CITY 5, MO., 910 Baltimore Avenue TULSA 3, OKLA., 614 National Bank of Tulsa Bidg. Western States LOS ANGELES (Vernon) 58, CALIF., 2770 ieonis Blvd, PHOENIX, ARIZ,, 401 East Buchanan Street PORTLAND 9, ORE., 1205 Northwest Marshall Street SALT LAKE CITY 1, UTAH, 436 W. Ninth, South, Street SAN FRANCISCO 6, CALIF., 22 Battery Street SEATTLE 4, WASH., 3404 Fourth Avenue, South SPOKANE 12, WASH., 2023 West Maxwell Avenye In Canada LINDE AJR PRODUCTS COMPANY Division of Union Carbide Canada Limited 40 St. Clair Ave. E., Toronto 7, Canada Outside United States and Canada Linde Department UNION CARBIDE INTERNATIONAL COMPANY A Division of Union Carbide and Carbon Corporation 30 East 42nd Street, New York 17, N. Y., U. §. A.
advertisement
Related manuals
advertisement