advertisement
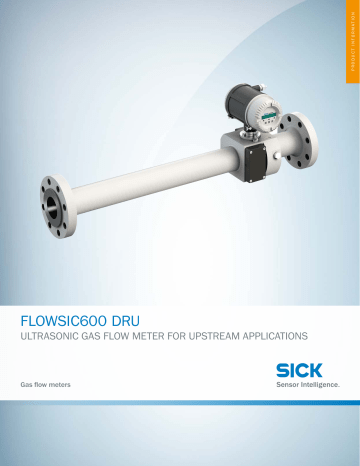
FLOWSIC600 DRU
ULTRASONIC GAS FLOW METER FOR UPSTREAM APPLICATIONS
Gas flow meters
FLOWSIC600 DRU ULTRASONIC GAS FLOW METER FOR UPSTREAM APPLICATIONS
UPSTREAM MEETS ULTRASONIC – REACHING A NEW MILESTONE
IN RANGEABILITY & REDUCED MAINTENANCE COSTS
Ultrasonic meters provide several advantages over differential pressure meters such as improved rangeability, a higher turndown, no calibration and valuable diagnostics. The FLOWSIC600 DRU, an innovative dual-path ultrasonic meter is tailor-made for upstream and gathering applications. Specially adapted sensors and path layout combines the benefits of a FLOWSIC600 with an unmatched reliability and robustness for upstream conditions. The special 10D upstream piping allows for high measurement accuracy even without high-pressure calibration, resulting in faster ROI due to the lower operational costs of a virtually maintenance-free meter.
FLOWSIC600 DRU –
improved quality in upstream gas metering.
Advanced diagnostics give you an advantage
The FLOWSIC600 DRU introduces a new diagnostic feature for the detection of liquids in the gas stream. Indication is typically provided when the gas volume fraction falls below 99.5 %. This feature can provide valuable information about the measurement quality and the performance of upstream components such as liquid separators. Additional diagnostic information can be monitored, which gives the user information about how the meter and the meter run is performing.
The additional parameters for each path are: the speed of sound, turbulence, the automatic gain control value, the signal validity parameter and analysis of the actual raw signal wave forms.
409
406
403
400
100 99,9 99,8 99,5
Gas volume fraction [%]
98,8
Path 2
97,7 95,5
Path 1
Effect of liquids in gas on the sound velocity of the two ultrasonic paths.
• The FLOWSIC600 DRU provides real-time monitoring of all diagnostic parameters, informs about the measurement conditions and generates a warning when parameters change significantly.
• Special design features ensure the FLOWSIC600 DRU is rugged even in wet gas conditions.
• Due to the decreased necessity for on-site checks and cleanings, your operating expenses stay low.
2 G A S F L O W M E T E R | S I C K 8018101/2020-07
Subject to change without notice
ULTRASONIC GAS FLOW METER FOR UPSTREAM APPLICATIONS FLOWSIC600 DRU
Rangeability and turndown
With a turndown ratio of up to 150 : 1 1 it covers flow ranges that usually require several differential pressure meters in different sizes. Diagnostics monitor the meter and process conditions, so that even large variations in flow and gas quality will not affect the measurement availability, which gives you peace of mind for natural gas production and gathering environments. By verifiable savings in CapEx and OpEx and less effort for maintenance, FLOWSIC600 DRU is an ideal alternative to differential pressure meters.
1 Below 0.9 m/s increased uncertainty
Virtually maintenance-free with self diagnostics
Ultrasonic technology is free of moving parts and has no wear and tear.
Equipped with the MEPAFLOW CBM firmware and software, FLOWSIC600 DRU monitors itself and processes changes using “real-time” monitoring of all diagnostic meter parameters. The innovative liquid loading detection feature provides indication of liquids inside the gas stream and allows you to optimize the process and plan maintenance of the
FLOWSIC600 DRU and other devices accordingly.
High accuracy without highpressure calibration
The special 10D inlet, superior manufacturing precision, extremely tight tolerances for each meter during the manufacturing process, and high quality components all enable the SICK
FLOWSIC600 DRU to ensure a ±1 % uncertainty without calibration. By eliminating the need for calibration, this feature alone can save start-up time and cost.
Long term stability
The FLOWSIC600 DRU keeps your costs low with long maintenance-free operating periods and high availability even in wet gas conditions. A high turndown ratio ensures reliable readings even with large variations in flow. Finally, the direct path layout is insensitive against pipeline fouling and further reduces maintenance effort, which underlines the long-term economic advantages of FLOWSIC600 DRU.
Highly durable
The FLOWSIC600 DRU is designed for use in harsh upstream environments.
High durability is made possible by hermetically sealed transducers made of titanium with special wet gas encapsulation, and a meter body that ensures that liquids and contaminants will not affect the meter performance.
Also, the integral meter design with sealed transducer cover and internal cable routing prevent harsh ambient conditions from harming the device. This gives you the certainty of meter longevity even in challenging conditions.
Profit from technology leadership in ultrasonic gas metering
SICK is the technology leader in ultrasonic gas measurement. We have more than 30 years experience in ultrasonic measurement technology and more than 10 years of field experience with
FLOWSIC600 in various applications.
This knowledge has now been transferred into FLOWSIC600 DRU in order to provide a suitable solution even for upstream measurements. Our customers rely on us when it comes to challenging applications – with FLOWSIC600 DRU they can do that in upstream, potentially wet gas applications as well.
8018101/2020-07
Subject to change without notice
G A S F L O W M E T E R | S I C K 3
FLOWSIC600 DRU ULTRASONIC GAS FLOW METER FOR UPSTREAM APPLICATIONS
1 % UNCERTAINTY
WITHOUT HIGH-PRESSURE CALIBRATION
In combination with SICK‘s leading ultrasonic transducer technology, continuous manufacturing process improvements, and our certified in-house calibration lab SICK offers a high level of production quality unmatched by anyone. Because of this, our manufacturing process for the FLOWSIC600 DRU results in a ±1 % uncertainty out-of-the-box performance without the need for high-pressure calibration.
FLOWSIC600 DRU, 3- and 4-inch version
• Integrated, high-precision 10D inlet piping
• For low to medium flow rates
FLOWSIC600 DRU, 6-inch version
• Flanged, high-precision 10D inlet piping
• For medium to high flow rates
During manufacturing of the FLOWSIC600 DRU there are five essential steps that are worth taking a closer look at:
Manufacturing precision
Superior transducer technology
Zero flow verification test
2.299
2.286
2.273
2.261
2.247
2.235
2.222
2.209
Path 1
Path 2
Tolerance limit
0,009
0,004
0
-0,004
-0,009
0,15
0,10
0,05
0
-0,05
-0,10
-0,15
Path 1
Path 2
Path 1 Path 2
Low manufacturing tolerances using the example of path length scatter
It starts with the meter body. Superior manufacturing precision and narrow tolerance limits ensure the utmost accuracy of geometric parameters of the meter body and its special 10D inlet piping. Long-term collaborations with our regional suppliers allow a thorough quality assurance level for all the high-quality components of the
FLOWSIC600 DRU.
High quality ultrasonic transducers for wet gas applications
High-quality transducers are the heart of our intelligent measurement devices. All transducers are made of titanium, are hermetically sealed without a matching layer and wet gas protected. SICK transducers are subject to precise geometrical dimensional and impedance checks before they are matched pairwise to provide the utmost accuracy on each ultrasonic path for superior performance.
Example results for zero point testing with strict acceptance criteria
After assembly of the meter, a zero flow verification test is performed to verify proper transit-time measurement. Zero flow stability dominantly affects a meter‘s low-flow performance. The acceptance criteria for FLOWSIC600 zero flow verification exceeds the requirements from AGA9, and therefore ensures good low-flow performance.
4 G A S F L O W M E T E R | S I C K 8018101/2020-07
Subject to change without notice
ULTRASONIC GAS FLOW METER FOR UPSTREAM APPLICATIONS FLOWSIC600 DRU
Individual low-pressure calibration
In-process quality assurance for high-pressure performance
0
-0,5
-1,0
-1,5
-2,0
0
2,0
1,5
1,0
0,5
Acceptance criteria
3500 7000 10500
Volume flow [m³/h]
14000 17500
Quality assurance and individual low-pressure calibration
21000
Each FLOWSIC600 DRU is subject to a 7-point ambient air low pressure calibration. Calibration is done on SICK’s in-house test benches, which are certified and traceable by Germany‘s national metrology institute, PTB. Quality acceptance criteria for the resulting meter characteristics ultimately ensure proper meter performance. Based on the calibration result and thorough statistical methods, each meter is individually corrected by calibration factors (based on flow-weighted mean error calculation).
0
-0,5
-1,0
-1,5
-2,0
0
2,0
1,5
1,0
0,5
Acceptance criteria
3500 7000 10500
Volume flow [m³/h]
14000 17500
Exemplary measurement performance of a FLOWSIC600 DRU
(sample device) at different pressures
21000
Extensive testing was conducted during the development process of FLOWSIC600 DRU in order to create a good and repeatable correlation between low-pressure and high-pressure meter performance. To ensure the proper performance of each FLOWSIC600 DRU under high-pressure conditions in series production, permanent quality assurance measures have been installed. Population samples are periodically sent to certified high-pressure calibration labs to verify statistical treatment is relevant to the population. This increases the population database and ultimately decreases measurement uncertainty.
8018101/2020-07
Subject to change without notice
G A S F L O W M E T E R | S I C K 5
FLOWSIC600 DRU ULTRASONIC GAS FLOW METER FOR UPSTREAM APPLICATIONS
ULTRASONIC GAS FLOW METER FOR
UPSTREAM APPLICATIONS
6
C
®
US
Additional information
Detailed technical data . . . . . . . . . . . .7
Ordering information . . . . . . . . . . . . . .
8
Dimensional drawings . . . . . . . . . . . . .
8
Installation diagrams . . . . . . . . . . . . .10
Application range . . . . . . . . . . . . . . . 11
Maximum volume flow rate . . . . . . . 11
Product description
The FLOWSIC600 DRU is an innovative ultrasonic dual-path gas meter for upstream applications based on the
FLOWSIC600. The meter includes a 10D inlet piping (integrated for 3" and 4", flanged for 6"). With a turndown ratio of up to 150 : 1 1 it covers common flow ranges that usually require several orifice plates. Due to its special design, the FLOWSIC600 DRU provides low measurement uncertainty without need for a high-pressure flow calibration.
High quality components with superior manufacturing precision and wet gas resistant transducers ensure longterm measurement reliability even in challenging conditions. Equipped with
MEPAFLOW600 CBM firmware and software, the FLOWSIC600 DRU provides advanced diagnostic capabilities for real-time monitoring of the meter and the process. The ultrasonic measurement principle with direct path layout makes FLOWSIC600 DRU virtually maintenance-free – even with high liquid loads.
1 Below 0.9 m/s increased uncertainty
At a glance
• High turndown ratio covering flow ranges of multiple orifice meters
• High precision manufactured 10D inlet piping included
• Accurate to ±1 % without a high - pressure flow calibration
• Remote diagnostics capability
• Designed for wet gas applications
• New diagnostic feature – wet-gas detection
• Virtually maintenance-free
Your Benefit
• Low initial CapEx – accurate measurement without need for expensive flow calibration
• Low subsequent CapEx – saving costly station resizing or plate changes due to high flow turn down
• Low OpEx – long maintance-free operation and remote diagnostics indicating service demand only when needed
Fields of Application
• Upstream natural gas metering
• Multi-Well production pad meters
• Allocation and Check metering
• Metering at VRU outlets
• High measurement reliability using real-time monitoring of all diagnostic meter parameters
• Advanced process monitoring capability with unique wet-gas detection
• Better measurement accuracy than orifice meters under wet gas conditions
• Long life-span – encapsulated transducers are not affected by liquids and contaminants
• Metering at Test- and Production separator outlets
• Replacement of orifice meter installations
G A S F L O W M E T E R | S I C K
www.sick.com/FLOWSIC600_DRU
For more information, just enter the link and get direct access to technical data, CAD design models, operating instructions, software, application examples and much more.
8018101/2020-07
Subject to change without notice
ULTRASONIC GAS FLOW METER FOR UPSTREAM APPLICATIONS FLOWSIC600 DRU
Detailed technical data
The exact device specifications and performance data of the product may deviate from the information provided here, and depend on the application in which the product is being used and the relevant customer specifications.
System
Measured values
Measurement principle
Number of measuring paths
Measuring medium
Measuring ranges
Volume flow rate
Repeatability
Uncertainty
Gas temperature
Operating pressure
Nominal pipe size
Flange connection
Ambient temperature
Storage temperature
Ambient humidity
Ex approvals
Flow velocity
Volume flow a.c, volume a.c, gas velocity, sound velocity
Ultrasonic transit time difference measurement
2
Natural gas
Operational:
Q min
1
14
Q t m 3 /h
47 3"
4"
6"
25
55 v min
1
81
185 v t m/s
Q max
2
700
1000
2125 v max
2
3"
4"
6"
0.9
0.9
0.9
3
3
3
1 Below 0.9 m/s increased uncertainty.
2 Q max
can be limited by the working pressure and attenuation of the gas medium.
±0.2 % of reading
(within Q t
to Q max
under consideration of installation requirements)
±1 % from Q t
to Q max
(±2 % from Q min
to Q t
)
-40 ... 85 °C
45
37
35
0 … 102 bar(g) at 38 °C
0 … 95.2 bar(g) at 85 °C
3" / 4" / 6" Schedule 80
3" / 4" / 6" ANSI B16.5, Cl.600 RF
-40 ... 60 °C
-40 ... 70 °C
≤ 95 % Relative humidity
Enclosure rating
Digital outputs
Interfaces
Bus protocol
Dimensions (W x H x D)
Weight
NEC/CEC Class I, Division 1, Group D T4
Class I, Division 2, Group D T4
Ultrasonic transducers intrinsically safe
IP66/IP67
2 DO and 1 FO:
30 V, 10 mA
Passive, galvanically isolated, open collector, f max
= 6 kHz (scalable)
RS-485 (2x, for configuration data output and diagnosis)
MODBUS ASCII, MODBUS RTU
See dimensional drawings
3": 48 kg
4": 85 kg
6": 250 kg
Electrical connection
Voltage
Power consumption
12 ... 28.8 V DC
≤ 1 W
8018101/2020-07
Subject to change without notice
G A S F L O W M E T E R | S I C K 7
FLOWSIC600 DRU ULTRASONIC GAS FLOW METER FOR UPSTREAM APPLICATIONS
Ordering information
Our regional sales organization will help you to select the optimum device configuration.
Dimensional drawings (Dimensions in mm)
FLOWSIC600 DRU 3" and 4"
KE
EP
C
TI
T
WHIL
E CIR
CU
IT I
S A
LIV
E
A
PT: 1/2"NPT-f
Nominal pipe size
3 "
4 "
A
1040
1300
B
74
97
C
210
275
Dimensions
D
226
259
E
251
259
F
356
396
8 G A S F L O W M E T E R | S I C K 8018101/2020-07
Subject to change without notice
ULTRASONIC GAS FLOW METER FOR UPSTREAM APPLICATIONS FLOWSIC600 DRU
FLOWSIC600 DRU 6 "
KE
EP
OV
ER
TI
GH
T
WHILE
CU
IT I
S A
LIV
1977
PT: 1/2"NPT-f
8018101/2020-07
Subject to change without notice
G A S F L O W M E T E R | S I C K 9
FLOWSIC600 DRU ULTRASONIC GAS FLOW METER FOR UPSTREAM APPLICATIONS
Installation diagrams
FLOWSIC600 DRU 3" and 4"
Straight inlet
≥ 10 DN
FLOWSIC600 DRU Straight outlet
≥ 5 DN
≥ 3 DN
Flow conditioner typ CPA 55E
Pressure tap
½“ NPT female
FLOWSIC600 DRU 6"
Straight inlet
≥ 10 DN
FLOWSIC600 DRU
KE
C OV
ER
TI
GH
T
WHILE
CIR
EP
CU
IT I
S A
LIV
Straight outlet
≥ 5 DN
≥ 5 DN
Flow conditioner typ CPA 55E
Pressure tap
½“ NPT female
1 0 G A S F L O W M E T E R | S I C K 8018101/2020-07
Subject to change without notice
ULTRASONIC GAS FLOW METER FOR UPSTREAM APPLICATIONS FLOWSIC600 DRU
Application range
1250
1000
750
500
250
0
0
2500
2250
2000
1750
1500
10 20 30 70 80 90 100
3"
40 50
Line pressure [bar(g)]
4"
60
6"
Maximum volume flow rate
Maximum volume flow rate at standardized condition at different operating pressures
Pressure [bar(g)]
3 "
Volume flow rate
[m³/h s.c.]
4 "
Volume flow rate
[m 3 /h s.c.]
6 "
Volume flow rate
[m 3 /h s.c.]
3 7 10 20 30 40 50
2800 5600 7800 15 100 22 800 29 200 3200
60 70 80 90 100
40 900 46 100 50 600 54 700 58 500
4000 7900 11 000 21 300 32 100 41 500 50 200 58 600 66 500 73 600 80 000 86 200
8600 17 000 23 500 45 700 68 900 89 700 110 000 129 700 149 000 167 000 184 300 201 400
Volumetric calculations are based on a typical gas composition (see AGA 8 Amarillo), flowing at 21 °C (atmospheric pressure = 1.01 bar).
The calculations are based on the maximum volume flow rate as shown in the diagram „Application range“.
8018101/2020-07
Subject to change without notice
G A S F L O W M E T E R | S I C K 1 1
SICK AT A GLANCE
SICK is a leading manufacturer of intelligent sensors and sensor solutions for industrial applications. With more than 10,000 employees and over 50 subsidiaries and equity investments as well as numerous agencies worldwide, SICK is always close to its customers. A unique range of products and services creates the perfect basis for controlling processes securely and efficiently, protecting individuals from accidents, and preventing damage to the environment.
SICK has extensive experience in various industries and understands their processes and requirements.
With intelligent sensors, SICK delivers exactly what the customers need. In application centers in Europe,
Asia, and North America, system solutions are tested and optimized in accordance with customer specifications. All this makes SICK a reliable supplier and development partner.
Comprehensive services round out the offering: SICK LifeTime Services provide support throughout the machine life cycle and ensure safety and productivity.
That is “Sensor Intelligence.”
Worldwide presence:
Australia, Austria, Belgium, Brazil, Canada, Chile, China, Czech Republic, Denmark, Finland, France,
Germany, Great Britain, Hungary, Hong Kong, India, Israel, Italy, Japan, Malaysia, Mexico, Netherlands,
New Zealand, Norway, Poland, Romania, Russia, Singapore, Slovakia, Slovenia, South Africa, South Korea,
Spain, Sweden, Switzerland, Taiwan, Thailand, Turkey, United Arab Emirates, USA, Vietnam.
Detailed addresses and further locations
- www.sick.com
SICK AG | Waldkirch | Germany | www.sick.com
advertisement
* Your assessment is very important for improving the workof artificial intelligence, which forms the content of this project
Related manuals
advertisement