advertisement
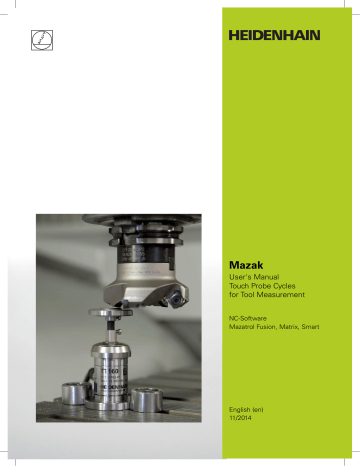
Mazak
User's Manual
Touch Probe Cycles for Tool Measurement
NC-Software
Mazatrol Fusion, Matrix, Smart
English (en)
11/2014
2
Mazak | |
Contents
1
2
3
4
Touch probe cycles: Automatic tool length and radius measurement (Format EIA/ISO).......... 37
5
6
7
8
9
Mazak | User’s Manual Touch Probe Cycles for Mazak NC Software | 11/2014
3
Contents
4
Mazak | User’s Manual Touch Probe Cycles for Mazak NC Software | 11/2014
1
1.1
1.2
1.3
Mazak | User’s Manual Touch Probe Cycles for Mazak NC Software | 11/2014
5
Contents
2
2.1
2.2
2.3
6
Mazak | User’s Manual Touch Probe Cycles for Mazak NC Software | 11/2014
3
3.1
3.2
Mazak | User’s Manual Touch Probe Cycles for Mazak NC Software | 11/2014
7
Contents
4
Touch probe cycles: Automatic tool length and radius measurement (Format EIA/ISO).......... 37
4.1
4.2
8
Mazak | User’s Manual Touch Probe Cycles for Mazak NC Software | 11/2014
5
5.1
Mazak | User’s Manual Touch Probe Cycles for Mazak NC Software | 11/2014
9
Contents
6
6.1
6.2
6.3
6.4
6.5
6.6
10
Mazak | User’s Manual Touch Probe Cycles for Mazak NC Software | 11/2014
7
7.1
7.2
Mazak | User’s Manual Touch Probe Cycles for Mazak NC Software | 11/2014
11
Contents
8
8.1
8.2
8.3
8.4
8.5
8.6
12
Mazak | User’s Manual Touch Probe Cycles for Mazak NC Software | 11/2014
9
9.1
Mazak | User’s Manual Touch Probe Cycles for Mazak NC Software | 11/2014
13
1
Fundamentals
1
Fundamentals
1.1
About this manual
1.1
About this manual
The symbols used in this manual are described below.
This symbol indicates that important information about the function described must be considered.
WARNING This symbol indicates a possibly dangerous situation that may cause light injuries if not avoided.
This symbol indicates that there is one or more of the following risks when using the described function:
Danger to workpiece
Danger to fixtures
Danger to tool
Danger to machine
Danger to operator
This symbol indicates that the described function must be adapted by the machine tool builder. The function described may therefore vary depending on the machine.
This symbol indicates that you can find detailed information about a function in another manual.
16
Mazak | User’s Manual Touch Probe Cycles for Mazak NC Software | 11/2014
Fundamental software information 1.2
1
1.2
Fundamental software information
Important notes
Please read this programming guide carefully prior to commissioning the touch probe and the cycles!
The content of the data carrier and corresponding documentation
(summarized as "data") are protected by copyright. DR. JOHANNES
HEIDENHAIN GmbH retains all rights to the data or individual parts thereof, in particular the right to copy, lease, modify, store and process in CNC controls or other electronic systems (e.g.
PCs). Distribution as well as duplication of the data, or use of the programs in more than one control is prohibited without the explicit permission of DR. JOHANNES HEIDENHAIN GMBH.
Violation obligates compensation for damages.
All data has been carefully tested. Nevertheless, no warranty can be assumed with respect to completeness and freedom from errors.
The measurement cycles should be interpreted as examples for solving measurement tasks and must be adapted by machine manufacturers or users to the specific type of machine.
Before commissioning, determine whether the parameters used by the measurement cycles are already being used. If this is the case these cycles must be adapted, as the overwriting of used parameters may cause unforeseeable damage to the machine.
When commissioning the measurement cycles the program must be tested blockwise under observance of all safety measures
(especially block testing prior to execution, single block and reduced feed rate). After completion of commissioning, parameters used and executed machine-specific program modifications must be documented.
Furthermore, DR. JOHANNES HEIDENHAIN GmbH is excluded from any liability inasmuch, for example, as it is not patently responsible according to product liability law, due to intent, gross negligence, due to bodily harm or harm to health, due to the assumption of a guarantee for specific characteristics, due to fraudulent concealment of a defect or due to the violation of essential contractual obligations. Compensation for violation of fundamental contractual obligations, however, is limited to typically foreseeable damage, inasmuch as no intent or gross negligence is involved. Specified legal disclaimers are deemed as accepted following the installing of measurement cycles at the latest.
We reserve the right to technical modifications for product improvements. Our General Sales Conditions apply.
© 2013 DR. JOHANNES HEIDENHAIN GmbH
Mazak | User’s Manual Touch Probe Cycles for Mazak NC Software | 11/2014
17
1
Fundamentals
1.2
Fundamental software information
Program overview
This software can be used to execute the most frequently required tool measurement tasks on a machine tool with a HEIDENHAIN TT touch probe.
As user you only call the measurement cycle programs. For program run, the measurement cycles need the auxiliary programs.
Example programs illustrate which parameters need to be defined when calling the measurement cycles, and how the measurement cycles can be called from within the part program.
Contents Auxiliary program
O9916 *
O9918
Machine-specific constants
User start / end programs
Error messages
*
Measurement cycle
During commissioning, machine-specific modifications must be made.
Contents
O9911
O9912
O9913
Calibration / temperature compensation
Measuring the tool length
Measuring tool length and radius
Example program
O911
Contents
O912
O913
For cycle call O9911 Calibration / temperature compensation
For cycle call O9912 Measuring the tool length
For cycle call O9913 Measuring tool length and radius
18
Mazak | User’s Manual Touch Probe Cycles for Mazak NC Software | 11/2014
Fundamental software information 1.2
1
Procedure for commissioning
The following procedure is recommended to ensure proper commissioning:
Firmly mounting the TT touch probe to the machine table (see
TT Mounting Instructions) in compliance with the following information:
"Mechanical installation", page 64
"Electrical installation", page 64
"Installing the software", page 66
"Modifying machine parameters", page 67
"Program O9916: Adapting the software to the specific machine", page 70
In "Adapting machine-specific parameters", page 72
Determining the measuring positions: "Parameter definition for two touch probes", page 78
"Calibrating the touch probe(Format EIA/ISO)", page 23
Testing the cycles using the "Programming examples (Format
Mazak | User’s Manual Touch Probe Cycles for Mazak NC Software | 11/2014
19
1
Fundamentals
1.3
Fundamentals of touch probe cycles
1.3
Fundamentals of touch probe cycles
Application possibilities for touch probe cycles
Possible measurement tasks
Calibrating the TT touch probe see page 23
(with O9911 program)
Measuring the tool length see page 31
(with O9912 program)
Measuring tool length and radius see page 37
(with O9913 program)
Compensation of thermal expansion see page 28
(with O9911 program)
Possible applications
Initial measurement of tool
Tool wear checking
(with O9912 and O9913 programs)
Tool breakage checking
(with O9912 and O9913 programs)
Notes on conducting measurements
Danger of collision
Limit the overtravel for measuring blocks to 2 mm
#100 to #149 must not collide with any other parameters you are using in your programs
(see "Adapting machine-specific parameters", page 72).
For safe, correct measurements:
Observe the maximum feed rate specified by the machine manufacturer
Use the same constant feed rate for calibration and tool measurement
Read the information about the respective touch probe in the User's Manual
Principle of function
The touch probe provides a signal (STATUS or STATUS INVERSE) connected to the measuring input of the control.
During the measuring block, the signal is detected by the control and the axis positions are saved at the time of triggering.
These axis positions are read and accounted for in the measurement cycles. During the tool measurement, the axis positions (trigger points) are offset against the calibration values to determine the tool dimensions.
20
Mazak | User’s Manual Touch Probe Cycles for Mazak NC Software | 11/2014
Fundamentals of touch probe cycles 1.3
1
Cycle call
The measurement cycles can only be run in the "AUTO" or "MDI" operating modes.
The measurement task is defined in the called measurement cycle and the call parameters. The call parameters must always be entered in the machine's unit of measurement; otherwise, the cycle will be aborted with an error message. All examples use the metric system. Some call parameters are optional, which means they do not necessarily have to be programmed.
Parameters that are not transferred are automatically set to the defaults in the cycle.
Mandatory parameters must be programmed. It is recommended to program all parameters in order to ensure a clearly defined program run.
Approach and departure strategies
Before the measurement task, a return position is approached in the tool length axis.
The radius axis and the minor axis are positioned above the touch probe.
The measurement task is executed.
The tool then moves back to the return position in the tool length axis.
Process errors
During a cycle call, the specified parameters are evaluated. If illogical values are detected or a danger of collision is identified, the cycle is aborted with an error message.
Tool data used for calculations
The cycles use the tool compensations defined for the current
D - and H numbers of the tool in the spindle. For positioning the tool, the tool length (geometry and wear) or tool radius (geometry and wear) are added.
Tool length used: #102 = #134 + #136
Tool radius used: #104 = #135 + #137
To ensure the proper functioning of the tool check cycles, an initial measurement must be performed for each tool (e.g. O9912 or O9913 and measurement type B0.
). If inaccuracies of the workpiece are compensated for by means of the tool data (e.g. in the wear values), the tolerance limits for the tool check need to be increased.
Unknown tool length / tool radius
Tools of unknown length or radius can be measured using the measurement type B0.
if the value 0 is entered in the tool compensation memory.
Tools of unknown length or radius are not pre-positioned above or next to the touch probe. The measurement is started at the maximum permissible tool length or radius (procedure for locating the tool with non-rotating spindle).
Mazak | User’s Manual Touch Probe Cycles for Mazak NC Software | 11/2014
21
1
Fundamentals
1.3
Fundamentals of touch probe cycles
When using tools of unknown length or radius, there is a danger of collision with the touch probe. It is recommended to enter an approximate tool length and tool radius (+/- 2 mm).
22
Mazak | User’s Manual Touch Probe Cycles for Mazak NC Software | 11/2014
2
Calibrating the touch probe
(Format EIA/ISO)
2
Calibrating the touch probe
(Format EIA/ISO)
2.1
Fundamentals
2.1
Fundamentals
Before measuring with the touch probe, you need to calibrate the measuring device. In the process, the exact trigger position is determined.
Why calibrate?
The tool to be measured approaches the TT tool touch probe during the calibration process. As soon as the probe contact 1 is deflected by the tool, the machine stops the movement and saves the current spindle position in special calibration parameters. The saved spindle position, however, does not precisely correspond to the position of the measured tool edge.
Reasons for deviations:
Time delay between acquiring the deflection signal and saving the spindle position
1 Probe contact
2 Connecting pin
When to calibrate
Always calibrate the touch probe in the following cases:
Commissioning the touch probe
Commissioning the touch probe cycles
Breakage of the connecting pin 2 to the probe contact 1
Replacement of the probe contact
Changes to specific parameters (see page 72)
Irregularities caused, for example, when the machine heats up
If measurement uncertainties are too great
How to calibrate
To ensure that the control supplies precise measurement results, the actual trigger of a touch probe must be determined by calibration.
Use a tool that is not subject to wear, e.g. an alignment pin (Ø >
4 mm).
Clamp the reference tool in the tool holder.
Measure the length of the reference tool by using a tool presetter or by conducting a differential measurement with a dial indicator (accuracy in μ m range) within the machine.
Enter the values into the tool compensation memory.
The cycle determines the trigger positions and calculates the calibration values based on the specified length and radius of the reference tool.
24
Mazak | User’s Manual Touch Probe Cycles for Mazak NC Software | 11/2014
Please note while programming
When using the Mazatrol + EIA/ISO tool memory,
H and D need not be defined. When using the A/
B-type tool memory, H and D must be defined.
If these are not available, the measurement cycle is aborted with an error message.
If spindle orientation is active, the radius calibration is performed by rotating the spindle by 180° to probe from opposite directions and calculate the center ( #127
(see "Adapting machine-specific parameters", page 72)).
Set the override potentiometer to 100% to avoid measuring errors caused by differing measurement speeds.
The stored calibration values must not be changed manually or by other programs.
Fundamentals 2.1
2
Mazak | User’s Manual Touch Probe Cycles for Mazak NC Software | 11/2014
25
2
Calibrating the touch probe
(Format EIA/ISO)
2.2
Calibrating the touch probe
2.2
Calibrating the touch probe
In the calibration process the software finds the exact trigger points of the TT touch probe in order to attain the best possible results during actual tool measurement.
Cycle run
Calibrating the length
1 Positioning: The calibration tool moves from the current position to the return position 1 and then over the center of the touch probe 2
2 The calibration tool is positioned at the safety clearance #129 above the touch probe 3
3 Probe process: The calibration tool probes the touch probe and retracts to the safety clearance #129
4 Result: The software calculates the exact trigger point of the touch probe in the Z direction and saves the calibration value
Calibrating the radius
5 Positioning: The calibration tool moves to the starting position 4
6 The software calculates the starting position 4 from the probing direction that you defined in parameters #125 and #126.
The distance A is calculated as follows:
A = R
R
T
: Radius of the probe contact ( #114 /2 or #115 /2)
R
TOOL
T
+ #129 + R
TOOL
: Radius of the calibration tool
7 The calibration tool moves to the starting position 5 . The starting position in the Z direction is calculated as follows:
Z
Start
= #113 + #117 + Z
Z: Parameter in the cycle call for an additional offset in the Z axis
8 Probe process: The calibration tool probes the touch probe and returns to the starting position 5
9 Result: The software calculates the exact trigger point of the touch probe in the probing direction you defined, and saves the calibration value
10 With spindle orientation #127:
After the control has automatically rotated the calibration tool by 180°, the software repeats the probe process and saves the mean value of the two measurements as the radius calibration value in the probing direction you defined.
11 Final positioning: The calibration tool moves from the current position to the return position 1
You can define the location for saving the calibration values in parameter #139 in the program O9916:
Parameter number Meaning
#[#139+0]
#[#139+1]
#[#139+2]
Calibration value in X axis
Calibration value in Y axis
Calibration value in Z axis
#118 Rapid traverse
#119 Positioning feed rate
#129 Safety clearance
#113 Measuring position of touch probe head in Z
#117 Axial measuring position for radius measurement
#125 Axis for radial offset
#126 Side for radial offset
26
Mazak | User’s Manual Touch Probe Cycles for Mazak NC Software | 11/2014
Calibrating the touch probe 2.2
2
Cycle call and cycle parameters
Open a new program block and enter the cycle definition:
G65 P9911
B (optional): Define the type of measurement. If B is not defined, the software automatically uses the measurement type B0
B0 : Initial measurement
In the initial tool measurement the software determines the absolute tool length and radius, writes the determined values to the transferred tool compensation memory and sets the tool wear to zero
Z (optional): Additional offset in the Z axis by which the software is to move the calibration tool during radius calibration. If the value is not entered, the software offsets the tool by the value from #117
Example: NC blocks
T99 M6
G65 P9911 Z5.
Mazak | User’s Manual Touch Probe Cycles for Mazak NC Software | 11/2014
27
2
Calibrating the touch probe
(Format EIA/ISO)
2.3
Temperature compensation (TC) of NC axes
2.3
Temperature compensation (TC) of NC axes
If increased accuracy is required, the temperature drift of the machine can be compensated by means of the touch probe and the calibration tool.
This cycle determines the trigger positions and calculates the TC reference values B1.
and the TC shift values B2.
, based on the specified length and radius of the reference tool. They are entered in the parameters and must not be overwritten by any other program.
The TC measurement should be included in the machining procedure in the following way:
Calibrate the touch probe with the reference tool (see page 26).
Trial machining of the first workpiece until all workpiece dimensions correspond to the nominal dimensions.
TC reference measurement B1.
to define the current machine status as the reference value.
Machining of the next workpiece.
TC comparison measurement B2.
to determine the current shift of the axes compared to the reference values and to account for it, e.g. via an additive datum shift.
Depending on the machine's temperature drift and the required accuracy, the TC comparison measurement can be repeated before or after every nth workpiece machining operation.
28
Mazak | User’s Manual Touch Probe Cycles for Mazak NC Software | 11/2014
Temperature compensation (TC) of NC axes 2.3
2
Cycle call and cycle parameters
Open a new program block and enter the cycle definition:
G65 P9911
B : Define the type of measurement. If B is not defined, the software automatically uses the measurement type B0
Z (optional): Additional offset in the Z axis by which the software is to move the calibration tool during radius calibration. If the value is not entered, the software offsets the tool by the value from #117
U (optional): Maximum permissible shift in TC comparison measurement
Example of a reference measurement
T99 M6
G65 P9911 B1. Z5.
Tool call
Cycle call with B1.
and axial offset
Z5.
in Z direction.
Example of a comparison measurement
T99 M6
G65 P9911 B2. Z5. U0.1
Tool call
Cycle call with B2.
and axial offset
LOFFS Z5.
in Z direction. The definition of U0.1
is optional. If undefined, the default value from
#149 is used.
The drift values measured for the length and radius axes or the minor axis are available in the parameters #[#139+6] (X axis), #[#139+7] (Y axis) and #[#139+8] (Z axis).
If a comparison measurement is conducted and the maximum permissible tolerance is exceeded, an error message will be issued.
Please note while programming
When using the Mazatrol + EIA/ISO tool memory,
H and D need not be defined. When using the A/
B-type tool memory, H and D must be defined.
If these are not available, the measurement cycle is aborted with an error message.
Detailed descriptions of optional parameters: see
Set the override potentiometer to 100% to avoid measuring errors caused by differing measurement speeds.
The stored calibration values must not be changed manually or by other programs.
Mazak | User’s Manual Touch Probe Cycles for Mazak NC Software | 11/2014
29
3
Touch probe cycles: Automatic tool length measurement
(Format EIA/ISO)
3
Touch probe cycles: Automatic tool length measurement (Format EIA/
ISO)
3.1
Fundamentals
3.1
Fundamentals
The touch probe measures the tool length with high accuracy.
Please note while programming
Enter the length of the tool to be measured with an accuracy of ± 2 mm into the tool compensation memory.
Detailed descriptions of call parameters (see "Call parameters", page 60)
The influence from thermal growth of the machine is compensated if a calibration was performed previously.
At the beginning of the measurement, the entered tool length and the wear length are read from the tool compensation memory and used for positioning.
At the end of the measurement, the determined length is written to the tool compensation memory and the wear length is set to 0.
Measurement types for tool length measurement:
B0.
: Initial measurement
B1.
: Wear measurement
B2.
: Verification measurement
For more information on the measurement types, see "Cycle call and cycle parameters", page 35
32
Mazak | User’s Manual Touch Probe Cycles for Mazak NC Software | 11/2014
Tool length measurement 3.2
3
3.2
Tool length measurement
Procedure
Please note while programming
If the diameter of the tool to be measured is greater than the diameter of the measuring surface on the probe contact ( #116 ), the software automatically measures the tool with rotating spindle.
When using the Mazatrol + EIA/ISO tool memory,
H and D need not be defined. When using the A/
B-type tool memory, H and D must be defined.
If these are not available, the measurement cycle is aborted with an error message.
Set the override potentiometer to 100% to avoid measuring errors caused by differing measurement speeds.
Length measurement with non-rotating spindle
The following tools are among those that you can measure with a non-rotating spindle:
Tools with diameters smaller than the diameter of the measuring surface on the probe contact ( #116 )
NC center drill, centering drill, drill
Radius cutter
Cycle run
Positioning:
1 The tool to be measured moves from the current position to the return position 1 and then over the touch probe center 2
2 From there the tool is positioned at the safety clearance #129 above the touch probe 3
Probe process:
3 The tool contacts the touch probe and retracts to the safety clearance #129
Result:
4 The software calculates the absolute tool length if the measurement type B0 is set the tool wear if the measurement type B1 is set
The values are saved in the corresponding compensation memory.
If the measurement type B2 is selected, the software does not save any values, but only checks whether the wear is within tolerance
Positioning:
5 The tool moves to the return position 2
#118 Rapid traverse
#119 Positioning feed rate
#129 Safety clearance
Mazak | User’s Manual Touch Probe Cycles for Mazak NC Software | 11/2014
33
3
Touch probe cycles: Automatic tool length measurement (Format EIA/
ISO)
3.2
Tool length measurement
Length measurement with rotating spindle
The following tools are among those that you can measure with a rotating spindle:
Tools with diameters larger than the diameter of the measuring surface on the probe contact ( #116 ), e.g. face-milling cutters
Cycle run
Positioning:
1 The tool to be measured moves from the current position to the return position 1 and then over the touch probe center 2
2 From there the tool moves over the touch probe center and switches the spindle on
3 The tool is then offset by the tool radius or by the transferred offset R . The direction of the offset depends on the measuring axis and the measuring direction that you define in the parameters
#125 and #126 (position 2 )
4 From there the tool is positioned at the safety clearance #129 above the touch probe 3
Probe process:
5 Rough measurement: The tool contacts the touch probe and then retracts by 0.2 mm
6 Accurate length measurement: The tool executes a second probing process and then returns to the safety clearance
Result:
7 The software calculates
- the absolute tool length if the measurement type B0 is set
- the tool wear if the measurement type B1 is set and saves the values in the corresponding compensation memory.
- If the measurement type B2 is selected, the software does not save any values, but only checks whether the wear is within tolerance
Final positioning:
8 The tool moves to the return position 2 and the spindle is switched off (M5)
#118 Rapid traverse
#119 Positioning feed rate
#129 Safety clearance
Z
Y
X
#125 Axis for radial offset
#126 Side for radial offset
34
Mazak | User’s Manual Touch Probe Cycles for Mazak NC Software | 11/2014
Tool length measurement 3.2
3
Cycle call and cycle parameters
Open a new program block and enter the cycle definition:
G65 P9912
Tool compensation memories A and B:
If you do not transfer the compensation number D , you must define the parameter R
Tool compensation memory C:
If you do not transfer the compensation number D , the software uses the compensation number transferred in the parameter H
B (optional): Define the type of measurement. If B is not defined, the software automatically uses the measurement type B0
B0 : Initial measurement
In the initial tool measurement the software determines the absolute tool length and radius, writes the determined values to the transferred tool compensation memory and sets the tool wear to zero
B1 : Wear measurement
Through the tool wear measurement, the software calculates the difference between the length and radius values defined in the tool compensation memory and the respective measured values. The software writes the calculated length and radius differences to the transferred tool compensation memory
If the values exceed the permissible wear tolerances
(parameter Q or parameter W or #138 ), the software issues an error message and does not write any values to the compensation memory
B2 : Verification measurement
Through the tool verification measurement, the software calculates the difference between the length and radius values defined in the tool compensation memory and the respective measured values.
If any of the differences calculated exceeds the wear tolerance, the software issues an error message. The software does not write any values to the tool compensation memory
Q (optional): Maximum permissible wear tolerance, which is used by the software for the measurement types B1 and B2.
If Q is not defined, the software uses the value defined in #138 as the maximum permissible wear tolerance
R (optional): Offset in the working plane by which the software offsets the tool from the center of the tool touch probe
If R is not defined, the software automatically moves the tool by the effective tool radius, which it calculates from the tool radius and tool radius wear defined in the tool compensation memory. The tool moves automatically only if the tool diameter is greater than the measuring surface of the probe contact
#116.
In these cases the tool length is measured with a rotating spindle
Always measure radius cutters and drills with the input R0
Example: Initial measurement of drill
T1 M6
G65 P9912 B0. R0.
Example: Wear measurement of drill
T1 M6
G65 P9912 B1. Q0.02 R0.
Example: Tool check of face-milling cutter d=32mm
T1 M6
G65 P9912 B2. Q0.02 R16.
Mazak | User’s Manual Touch Probe Cycles for Mazak NC Software | 11/2014
35
4
Touch probe cycles: Automatic tool length and radius measurement
(Format EIA/ISO)
4
Touch probe cycles: Automatic tool length and radius measurement
(Format EIA/ISO)
4.1
Fundamentals
4.1
Fundamentals
The tool touch probe enables you to measure the tool length and radius with high accuracy.
Please note while programming
Enter the length and radius of the tool to be measured with an accuracy of ± 2 mm into the tool compensation memory.
As an alternative to the radius value from the tool compensation memory, you can enter an acentric offset ROFFS in R
Detailed descriptions of call parameters (see "Call parameters", page 60)
The influence from thermal growth of the machine is compensated if a calibration was performed previously.
At the beginning of the measurement, the entered tool length and wear length as well as the tool radius and wear radius are read from the tool compensation memory and used for positioning.
At the end of the measurement, the determined length and radius are written to the tool compensation memory.
The wear length and wear radius are set to 0.
Measurement types for measuring the tool length and radius:
B0.
: Initial measurement
B1.
: Wear measurement
B2.
: Verification measurement
For more information on the measurement types, see "Cycle call and cycle parameters", page 35
38
Mazak | User’s Manual Touch Probe Cycles for Mazak NC Software | 11/2014
Measuring the tool length and radius 4.2
4
4.2
Measuring the tool length and radius
Procedure
Please note while programming
If the diameter of the tool to be measured is greater than the diameter of the measuring surface on the probe contact ( #116 ), the software automatically measures the tool with rotating spindle.
When using the Mazatrol + EIA/ISO tool memory,
H and D need not be defined. When using the A/
B-type tool memory, H and D must be defined.
If these are not available, the measurement cycle is aborted with an error message.
Set the override potentiometer to 100% to avoid measuring errors caused by differing measurement speeds.
Length measurement with non-rotating spindle
The following tools are among those that you can measure with a non-rotating spindle:
Tools with diameters smaller than the diameter of the measuring surface on the probe contact ( #116 )
NC center drill, centering drill, drill
Radius cutter
Cycle run
Positioning:
1 The tool to be measured moves from the current position to the return position 1 and then over the touch probe center 2
2 From there the tool is positioned at the safety clearance #129 above the touch probe 3
Probe process:
3 The tool contacts the touch probe and retracts to the safety clearance #129
4 The software calculates the absolute tool length if the measurement type B0 is set, and the tool wear if the measurement type B1 is set
The values are saved in the corresponding compensation memory.
If the measurement type B2 is selected, the software does not save any values, but only checks whether the wear is within tolerance
#118 Rapid traverse
#119 Positioning feed rate
#129 Safety clearance
Mazak | User’s Manual Touch Probe Cycles for Mazak NC Software | 11/2014
39
4
Touch probe cycles: Automatic tool length and radius measurement
(Format EIA/ISO)
4.2
Measuring the tool length and radius
Length measurement with rotating spindle
The following tools are among those that you can measure with a rotating spindle:
Tools with diameters larger than the diameter of the measuring surface on the probe contact ( #116 ), e.g. face-milling cutters
Cycle run
Positioning:
1 The tool to be measured moves from the current position to the return position 1
2 From there the tool moves over the touch probe center 2 and switches the spindle on
3 The tool is then offset by the tool radius or by the transferred offset R . The direction of the offset depends on the measuring axis and the measuring direction that you define in the parameters
#125 and #126 (position 2 )
4 From there the tool is positioned at the safety clearance #129 above the touch probe 3
Probe process:
5 Rough measurement: The tool contacts the touch probe and then retracts by 0.2 mm
6 Accurate length measurement: The tool executes a second probing process and then returns to the safety clearance
Result:
7 The software calculates
- the absolute tool length if the measurement type B0 is set
- the tool wear if the measurement type B1 is set and saves the values in the corresponding compensation memory.
- If the measurement type B2 is selected, the software does not save any values, but only checks whether the wear is within tolerance
#118 Rapid traverse
#119 Positioning feed rate
#129 Safety clearance
Z
Y
X
#125 Axis for radial offset
#126 Side for radial offset
40
Mazak | User’s Manual Touch Probe Cycles for Mazak NC Software | 11/2014
Measuring the tool length and radius 4.2
4
Radius measurement
Cycle run
Positioning:
1 The tool moves from the safety clearance #129 to the preposition 1 for radius measurement.
2 The software calculates the pre-position 1 from the defined probing direction (parameters #125 and #126 ). The distance A is calculated as follows:
A = R
R
T
T
+ #129 + #133
: Radius of the probe contact ( #114 /2 or #115 /2)
#129 : Safety clearance
#133 : Maximum tool radius
3 The spindle is switched on and the tool moves to the starting position 2 for radius measurement. The starting position 2 is calculated as follows:
Z
Start
= #113 + #117 + Z
Z: Parameter in the cycle call for an additional offset in the Z axis
4 The tool moves to the starting position for radius measurement 3 .
The distance B is calculated as follows:
B = R
T
R
T
+ #129 + R
TOOL
: Radius of the probe contact ( #114 /2 or #115 /2)
#129 : Safety clearance
R
TOOL
: Current tool radius
Probe process:
5 Rough measurement: The tool contacts the touch probe and then retracts by 0.2 mm
6 Accurate radius measurement: A second probing process is executed, after which the tool returns to the starting position 3
Result:
7 The software calculates
- the absolute tool radius if the measurement type B0 is set
- the tool wear if the measurement type B1 is set and saves the values in the corresponding compensation memory.
- If the measurement type B2 is selected, the software does not save any values, but only checks whether the wear is within tolerance
Repeated measurement:
8 If the determined tool radius deviates by more than 0.2 mm from the stored tool radius, the software repeats the tool length measurement with the newly determined tool radius (if R is not defined or R = tool radius)
Final positioning:
9 The tool moves to the return position 2 and switches the spindle off (M5)
#113 Measuring position of touch probe head in Z
#117 Axial measuring position for radius measurement
#125 Axis for radial offset
#126 Side for radial offset
#125 Axis for radial offset
#126 Side for radial offset
Mazak | User’s Manual Touch Probe Cycles for Mazak NC Software | 11/2014
41
4
Touch probe cycles: Automatic tool length and radius measurement
(Format EIA/ISO)
4.2
Measuring the tool length and radius
Cycle call and cycle parameters
Open a new program block and enter the cycle definition:
G65 P9913
Tool compensation memories A and B:
If you do not transfer the compensation number D , you must define the parameter R
Tool compensation memory C:
If you do not transfer the compensation number D , the software uses the compensation number transferred in the parameter H
B (optional): Define the type of measurement. If B is not defined, the software automatically uses the measurement type B0
B0 : Initial measurement
In the initial tool measurement the software determines the absolute tool length and radius, writes the determined values to the transferred tool compensation memory and sets the tool wear to zero
B1 : Wear measurement
Through the tool wear measurement, the software calculates the difference between the length and radius values defined in the tool compensation memory and the respective measured values. The software writes the calculated length and radius differences to the transferred tool compensation memory
If the values exceed the permissible wear tolerances
(parameter Q or parameter W or #138 ), the software issues an error message and does not write any values to the compensation memory
B2 : Verification measurement
Through the tool verification measurement, the software calculates the difference between the length and radius values defined in the tool compensation memory and the respective measured values.
If any of the differences calculated exceeds the wear tolerance, the software issues an error message. The software does not write any values to the tool compensation memory
Q (optional): Maximum permissible wear tolerance, which is used by the software for the measurement types B1 and B2.
If Q is not defined, the software uses the value defined in #138 as the maximum permissible wear tolerance
W (optional): Maximum permissible wear tolerance for tool radius, which is used by the software for the measurement types B1 and
B2.
If you do not define W, the software used the value defined in
#138 as the maximum permissible wear tolerance
Example: Initial measurement of drill
T2 M6
G65 P9913 B0.
42
Mazak | User’s Manual Touch Probe Cycles for Mazak NC Software | 11/2014
Measuring the tool length and radius 4.2
4
R (optional): Offset in the working plane by which the software offsets the tool from the center of the tool touch probe
If R is not defined, the software automatically moves the tool by the effective tool radius, which it calculates from the tool radius and tool radius wear defined in the tool compensation memory. The tool moves automatically only if the tool diameter is greater than the measuring surface of the probe contact
#116.
In these cases the tool length is measured with a rotating spindle
Always measure radius cutters and drills with the input R0
Mazak | User’s Manual Touch Probe Cycles for Mazak NC Software | 11/2014
43
5
Programming
(Format Mazatrol)
5
Programming (Format Mazatrol)
5.1
Programming in Mazatrol format
5.1
Programming in Mazatrol format
Mazatrol with call by M function
Danger of collision
The feed rate cannot be controlled with the override during a measuring block!
Further information: see "Definition of M functions for cycle call", page 68
46
Mazak | User’s Manual Touch Probe Cycles for Mazak NC Software | 11/2014
Programming in Mazatrol format 5.1
5
Breakage inspection without transferring variables
M function
M351
Parameter macro (J)
J77=912
J78=351
J79=1
J80=1
Comparison: EIA/ISO program
O00912
G65 P9912 B2. Q0.2
M99
Breakage inspection
Example of breakage monitoring – Mazatrol format
Mazak | User’s Manual Touch Probe Cycles for Mazak NC Software | 11/2014
47
5
Programming (Format Mazatrol)
5.1
Programming in Mazatrol format
Breakage monitoring with transfer of variables
M function
M352
Parameter macro (J)
J77=9913
J78=352
J79=1
J80=1
Example of breakage inspection – Mazatrol format
48
Mazak | User’s Manual Touch Probe Cycles for Mazak NC Software | 11/2014
Mazatrol with call through MANUAL PROGRAM
Programming in Mazatrol format 5.1
5
Example of breakage inspection – Mazatrol format
Mazak | User’s Manual Touch Probe Cycles for Mazak NC Software | 11/2014
49
5
Programming (Format Mazatrol)
5.1
Programming in Mazatrol format
Mazatrol with call through SUB PROGRAM
Comparison: EIA/ISO program
O00913
G65 P9913 B2. Q0.2 W0.02 Z5.
M99
Breakage inspection
Example of breakage inspection – Mazatrol format
50
Mazak | User’s Manual Touch Probe Cycles for Mazak NC Software | 11/2014
6
Programming examples (Format
EIA/ISO)
6
Programming examples (Format EIA/ISO)
6.1
Example: Calibration and temperature compensation
6.1
Example: Calibration and temperature compensation
B0.: Calibration
T99 M6
G65 P9911 B0. Z5.0
Tool call
Cycle call with B0.
and axial offset LOFFS Z5.0
in Z direction.
No input is required for B0.
B1.: TC reference measurement
T99 M6
G65 P9911 B1. Z5.0
Tool call
Cycle call with B1.
and axial offset LOFFS Z5.0
in Z direction.
B2.: TC comparison measurement
T99 M6
G65 P9911 B2. U0.1 Z5.0
Tool call
Cycle call with B2.
and axial offset LOFFS Z5.0
in Z direction and a maximum permissible shift of U0.1
in the TC comparison measurement.
52
Mazak | User’s Manual Touch Probe Cycles for Mazak NC Software | 11/2014
6.2
Example: Drill Ø 8 mm
B0.: Measure
T7 M6
G65 P9912 B0.
Tool call
Cycle call with measurement).
B0. (initial
No input is required for B0.
B1.: Inspect
T7 M6
G65 P9912 B1. Q0.02
Tool call
Cycle call with B1.
(wear measurement) and the tool length wear tolerance Q0.02.
B2.: Check/breakage check
T7 M6
G65 P9912 B2. Q0.05
Tool call
Cycle call with B2.
(breakage check) and the tool length wear/ breakage tolerance Q0.05.
Example: Drill Ø 8 mm 6.2
6
Mazak | User’s Manual Touch Probe Cycles for Mazak NC Software | 11/2014
53
6
Programming examples (Format EIA/ISO)
6.3
Example: Face-milling cutter Ø 60 mm
6.3
Example: Face-milling cutter Ø 60 mm
B0.: Measure
T9 M6
G65 P9913 B0. R30.0 Z2.
Tool call
Cycle call with B0.
(initial measurement), axial offset
LOFFS Z2.0
in Z direction and radial offset ROFFS
Y direction.
R30.0
in X or
No input is required for B0.
B1.: Inspect
T9 M6
G65 P9913 B1. R30.0 Z2. Q0.02
W0.02
Tool call
Cycle call with B1.
(wear measurement), axial offset
LOFFS Z2.0
in Z direction, radial offset ROFFS R30.0
in X or
Y direction, tool length wear tolerance Q0.02
and tool radius wear tolerance W0.02.
B2.: Check/breakage check
T9 M6
G65 P9913 B2. R30.0 Z2. Q0.05
W0.05
Tool call
Cycle call with B2. (breakage check), axial offset LOFFS Z2.
Z direction, radial offset ROFFS in
R30.0
in X or Y direction, tool length wear/breakage tolerance
Q0.05
and tool radius wear/ breakage tolerance W0.05.
54
Mazak | User’s Manual Touch Probe Cycles for Mazak NC Software | 11/2014
Example: End mill Ø 6 mm 6.4
6
6.4
Example: End mill Ø 6 mm
B0.: Measure
T10 M6
G65 P9913 B0.
Tool call
Cycle call with measurement).
B0. (initial
No input is required for B0.
B1.: Inspect
T10 M6
G65 P9913 B1. Q0.02 W0.02
Tool call
Cycle call with B1.
(wear measurement), tool length wear tolerance Q0.02
and tool radius wear tolerance W0.02.
B2.: Check/breakage check
T10 M6
G65 P9913 B2. Q0.05 W0.05
Tool call
Cycle call with B2.
(breakage check), tool length wear/breakage tolerance Q0.05
and tool radius wear/breakage tolerance W0.05.
Z
Y
X
1
Mazak | User’s Manual Touch Probe Cycles for Mazak NC Software | 11/2014
55
6
Programming examples (Format EIA/ISO)
6.5
Example: Ball nose cutter Ø 6 mm, corner radius 3 mm
6.5
Example: Ball nose cutter Ø 6 mm, corner radius 3 mm
B0.: Measure
T15 M6
G65 P9913 B0. R0. Z3.
Tool call
Cycle call with B0.
(initial measurement) and axial offset
LOFFS Z3.0
in Z direction.
No input is required for B0.
B1.: Inspect
T15 M6
G65 P9913 B1. Q0.02 W0.02
R0. Z3.
Tool call
Cycle call with B1.
(wear measurement), axial offset
LOFFS Z3.0
in Z direction, tool length wear tolerance Q0.02
and tool radius wear tolerance W0.02.
B2.: Check/breakage check
T15 M6
G65 P9913 B2. Q0.05 W0.05
R0. Z3.
Tool call
Cycle call with B2.
(breakage check), axial offset LOFFS Z3.0
in Z direction, tool length wear/ breakage tolerance Q0.05
and tool radius wear/breakage tolerance W0.05.
56
Mazak | User’s Manual Touch Probe Cycles for Mazak NC Software | 11/2014
Example: Toroid cutter Ø 30 mm, corner radius 5 mm 6.6
6
6.6
Example: Toroid cutter Ø 30 mm, corner radius 5 mm
B0.: Measure
T2 M6
G65 P9913 B0. R10. Z5.
Tool call
Cycle call with B0.
(initial measurement), axial offset
LOFFS Z5.
in Z direction and radial offset ROFFS R10.
in X or
Y direction.
No input is required for B0.
B1.: Inspect
T2 M6
G65 P9913 B1. Q0.02 W0.02
R10. Z5.
Tool call
Cycle call with B1.
(wear measurement), axial offset
LOFFS Z5.0
in Z direction, radial offset ROFFS R10.0
in X or
Y direction, tool length wear tolerance Q0.02
and tool radius wear tolerance W0.02.
B2.: Check/breakage check
T2 M6
G65 P9913 B2. Q0.05 W0.05
R10. Z5.
Tool call
Cycle call with B2. (breakage check), axial offset LOFFS Z5.
in
Z direction, radial offset ROFFS
R10.0
in X or
Y direction, tool length wear/ breakage tolerance Q0.05
and tool radius wear/breakage tolerance W0.05.
Mazak | User’s Manual Touch Probe Cycles for Mazak NC Software | 11/2014
57
7
Parameter tables
7
Parameter tables
7.1
Call parameters
7.1
Call parameters
Parameter Input
H
D
B
Q
W
R
U
Z
Optional
Meaning
Compensation number of tool length
H code of the tool to be measured.
Note: When using the Mazatrol + EIA/ISO tool memory, H and D need not be defined. When using the A/B-type tool memory, H and D must be defined.
If these are not available, the measurement cycle is aborted with an error message.
Optional Compensation number of tool diameter
D code of the tool to be measured.
Note: When using the Mazatrol + EIA/ISO tool memory, H and D need not be defined. When using the A/B-type tool memory, H and D must be defined.
If these are not available, the measurement cycle is aborted with an error message.
Optional Type of measurement
Cycle O9911 Calibration
0 = Calibration, 1 = TC reference measurement, 2 = TC comparison measurement
Note : If B is not defined, calibration is performed with B0.
(Calibration).
Cycle O9912 Measuring the tool length, Cycle O9913 Measuring tool length and radius
0 = Measure, 1 = Inspect, 2 = Check
Note : If B is not defined, the measurement is performed with B0.
(Measure).
Optional Tool length wear tolerance
By selecting B1.
you can check whether the tool is within tolerance. The wear value is written to the tool memory.
By selecting B2.
you can check whether the tool is within tolerance. The wear value is not written to the tool memory.
Note : If Q is not defined, the software uses the wear tolerance from #138 .
Optional Tool radius wear tolerance
By selecting B1.
you can check whether the tool is within tolerance. The wear is written depending on the tool memory.
By selecting B2.
you can check whether the tool is within tolerance. The wear value is not written to the tool memory.
Note : If W is not defined, the software uses the wear tolerance #138 .
Optional Radial position for length measurement ROFFS
Offset in X or Y direction for eccentric positioning of the tool above the touch probe.
Note : If R is not defined, the software uses the radius value from the tool table.
Optional Max. permissible shift in TC comparison measurement
The thermal growth of the machine is limited. To detect whether errors have occurred in the measurement, a tolerance limit is defined for the TC comparison measurement.
Note : If U is not defined, the software uses the maximum permissible shift from #149 .
Optional Axial position for radius measurement LOFFS
#117 and Z result in the axial position for the radius measurement.
Note : If Z is not defined, only the value from #117 is used.
60
Mazak | User’s Manual Touch Probe Cycles for Mazak NC Software | 11/2014
Result parameters 7.2
7
7.2
Parameters
#[#139+0]
#[#139+1]
#[#139+2]
#[#139+3]
#[#139+4]
#[#139+5]
#[#139+6]
#[#139+7]
#[#139+8]
Result parameters
#[#139+0] - #[#139+2] are updated in every calibration ( B0 .).
#[#139+3] - #[#139+5] are updated in every TC reference measurement ( B1 .).
#[#139+6] - #[#139+8] are updated in every TC comparison measurement ( B2 .).
The parameters must not be deleted or changed when the machine is switched off.
Meaning
Calibration value trigger point in X axis
Calibration value trigger point in Y axis
Calibration value trigger point in Z axis
TC reference value in X axis
TC reference value in Y axis
TC reference value in Z axis
TC shift value in X axis
TC shift value in Y axis
TC shift value in Z axis
Mazak | User’s Manual Touch Probe Cycles for Mazak NC Software | 11/2014
61
8
Software installation
8
Software installation
8.1
Notes on touch probe installation
8.1
Notes on touch probe installation
Mechanical installation
Refer to the Mounting Instructions for the TT touch probe and remember:
Mount the TT touch probe stably in the machine's working space.
Select the mounting position to minimize the settling of chips on the TT's measuring surface.
If required, provide automatic cleaning with compressed air or similar means.
To avoid measuring error the measuring surface must be perpendicular to the tool axis. The touch probe should be mounted near the tool change position. This ensures short traverse paths and saves time.
Select the mounting position so that no collision can occur between the tool and workpiece, or between the tool and jigs or fixtures.
Electrical installation
If UTI 192 universal touch probe interface necessary:
Refer to the operating instructions of the UTI 192 and the mounting instructions of the TT touch probe.
64
Mazak | User’s Manual Touch Probe Cycles for Mazak NC Software | 11/2014
8.2
Software installation
Program overview
The following table contains a program overview of the software package.
Contents Auxiliary program
O9916 *
O9918
Machine-specific constants
User start / end programs
Error messages
*
Measurement cycle
During commissioning, machine-specific modifications must be made.
Contents
O9911
O9912
O9913
Calibration / temperature compensation
Measuring the tool length
Measuring tool length and radius
Example program
O911
Contents
O912
O913
For cycle call O9911 Calibration / temperature compensation
For cycle call O9912 Measuring the tool length
For cycle call O9913 Measuring tool length and radius
Software installation 8.2
8
Mazak | User’s Manual Touch Probe Cycles for Mazak NC Software | 11/2014
65
8
Software installation
8.2
Software installation
Installing the software
Cancel the write protection to load and test the measurement programs:
Parameter 3202 bit 4 (NE9) = 0: Write protection for programs O9xxx inactive
After installation, ensure that all files are available and check their file sizes!
66
Mazak | User’s Manual Touch Probe Cycles for Mazak NC Software | 11/2014
Modifying machine parameters 8.3
8
8.3
Modifying machine parameters
Malfunction
Erroneously set machine parameters may cause collisions and malfunctions.
System parameters should only be modified after agreement with the machine manufacturer or customer.
Read the documentation of the control manufacturer.
The following parameters must be checked and adapted on requirement:
MAZATROL Matrix / Smart
0=no skip, 1=skip K69 G31.1 Skip conditions
K70 G31.2 Skip conditions
Bit 0: SKIP-2
Bit 1: SKIP-10
Bit 2: SKIP-3
Bit 0: SKIP-2
Bit 1: SKIP-10
Bit 2: SKIP-3
K71 G31.3 Skip conditions
F81 Program management
F92 Tool data display
EIA/ISO
F93 Tool lengh data
EIA/ISO
Bit 7:
Bit 3:
F94 Tool offset EIA/ISO Bit 2:
Bit 7:
Bit 0: SKIP-2
Bit 1: SKIP-10
Bit 2: SKIP-3
Bit 0:
Bit 1:
Bit 4:
Bit 5:
0=no skip, 1=skip
0=no skip, 1=skip
0=Released, 1=9000 Numbers locked
0=Anzeige, 1=9000 Number display locked
0=Released, 1=8000/9000 Numbers locked
0=Anzeige, 1=8000/ 9000 Number display locked
0=Tool storage Mazatrol + EIA/ISO, 1=Tool storage Type A/B
0=Tool storage Mazatrol + EIA/ISO, 1=Tool storage Type A/B
0=Tool storage Mazatrol + EIA/ISO, 1=Tool storage Type A/B
0=Tool storage Mazatrol + EIA/ISO, 1=Tool storage Type A/B
Mazak | User’s Manual Touch Probe Cycles for Mazak NC Software | 11/2014
67
8
Software installation
8.4
Definition of M functions for cycle call
8.4
Definition of M functions for cycle call
Tool measuring cycles can be called with an M function. The M function can be written directly in the Mazatrol or EIA/ISO program.
Variables can also be transferred.
Malfunction
You can define up to 4 M functions.
Ensure that the defined M function is not already being used for other functions.
The following machine parameters (macro J) need to be defined:
M function
1
J65 – J68
M function
2
J69 – J72
M function
3
J73 – J76
M function
4
J77 – J80
Examples of cycle definition
EIA/ISO format: G65 P9911 (calibration)
M function Parameter macro (J)
Meaning
M350 J69 = 9911
J70 = 350
J71 = 1
J72 = 1
Macro to be called
M function for call
Type of call (1 = G65)
Reserved
EIA/ISO format: G65 P9912 (length measurement)
M function
M351
Parameter macro (J)
J73 = 9912
J74 = 351
J75 = 1
J76 = 1
Meaning
Macro to be called
M function for call
Type of call (1 = G65)
Reserved
EIA/ISO format: G65 P9913 (length and radius measurement)
M function Meaning
M352
Parameter macro (J)
J77 = 9913
J78 = 352
J79 = 1
J80 = 1
Macro to be called
M function for call
Type of call (1 = G65)
Reserved
68
Mazak | User’s Manual Touch Probe Cycles for Mazak NC Software | 11/2014
Cycle call without call variable
Format EIA/ISO:
M351
Mazatrol format:
Cycle call with call variable
EIA/ISO format:
M351 B1. Q0.02
Mazatrol format:
Definition of M functions for cycle call 8.4
8
Tool length measurement type B0.
(initial measurement).
Cycle call with measurement type B1.
(wear measurement) and the tool length wear tolerance Q0.02.
Mazak | User’s Manual Touch Probe Cycles for Mazak NC Software | 11/2014
69
8
Software installation
8.5
Program O9916: Adapting the software to the specific machine
8.5
Program O9916: Adapting the software to the specific machine
The measurement cycles have a modular design. The subprogram
O9916 must be expanded and adapted to the machine during commissioning. Otherwise the cycles will not function properly and there is a danger of collision with the touch probe. The subprogram
O9916 is divided into seven sections:
N100 (machine-specific functions)
Machine-specific definitions, axis assignments, basic settings.
These parameters must be assigned valid values during commissioning.
N200 (user start program)
This sequence is executed before each measurement cycle.
Here, machine manufacturers and end users can program machine-specific functions.
N300 (user end program)
This sequence is executed after each cycle. Here, machine manufacturers and end users can program machine-specific functions.
N400 (switch-on of tool touch probes with infrared or radio transmission)
Tool touch probes with infrared or radio transmission must be activated by infrared or wireless signal before measurement.
The switch-on routine (e.g. M function) can be programmed in this section. When using a touch probe with cable transmission, leave this section empty.
N500 (switch-off of tool touch probes with infrared or radio transmission)
Tool touch probes with infrared or radio transmission must be deactivated by infrared or wireless signal after measurement.
The switch-off routine (e.g. M function) can be programmed in this section. When using a touch probe with cable transmission, leave this section empty.
N600 (clear temperature shift)
When temperature compensation is used, the existing shift values must be cleared before every reference measurement
(B1.). This can be programmed in this section. If no temperature compensation is used, leave this section empty.
Example when using external datum shift:
N600
#5201=0
#5202=0
#5203=0
Clear temperature shift
Clear external datum shift for X axis
Clear external datum shift for Y axis
Clear external datum shift for Z axis
GOTO9999
70
Mazak | User’s Manual Touch Probe Cycles for Mazak NC Software | 11/2014
Program O9916: Adapting the software to the specific machine 8.5
8
N700 (write temperature shift)
When temperature compensation is used, the determined shift values must be written for every comparison measurement
(B2.). This can be programmed in this section. If no temperature compensation is used, leave this section empty.
Example when using external datum shift:
N700
#5201=#[#139+6]
#5202=#[#139+7]
#5203=#[#139+8]
Write temperature shift
Write external datum shift for X axis
Write external datum shift for Y axis
Write external datum shift for Z axis
GOTO9999
Mazak | User’s Manual Touch Probe Cycles for Mazak NC Software | 11/2014
71
8
Software installation
8.6
Program O9916: Machine-specific parameters
8.6
Program O9916: Machine-specific parameters
Adapting machine-specific parameters
The basic settings for parameters are input by the user in the O9916 program.
Paths, diameters and feed rates must be entered with the unit [mm].
After changes to #xxx* parameters, the calibration cycle O9911 must be executed.
To make sure that the measurement cycles are clear and easy to use, the following constraints apply:
The tool length axis is the Z axis
The tool length is measured in the Z- direction using G43
The tool radius axis is the X or Y axis
Parameters Meaning
#110 Country identification, language output
If an error occurs, an error message is issued.
#110 contains the language code of the O9918 auxiliary program.
0 =English, 1 =German, 2 =French, 3 =Italian, 4 =Spanish, 5 =Dutch, 6 =Swedish, 7 = Portuguese,
8 =Danish, 9 =Czech
Measuring position of touch probe head #111* (X)
#112* (Y)
#113* (Z)
The measuring position of the touch probe head is specified in machine coordinates with an accuracy of approx. 0.1 mm. The measuring positions can be determined automatically by using the O9919 auxiliary subprogram (see
"Program O919: Finding the position of the tool touch probe").
#114*
#115*
Probe-contact diameter in X direction
Diameter or edge length of the probe contact in the X axis.
Value range 0 to 99.999 mm
Default value 40.000 mm
Probe-contact diameter in Y direction
Diameter or edge length of the probe contact in the Y axis.
Value range 0 to 99.999 mm
Default value 40.000 mm
72
Mazak | User’s Manual Touch Probe Cycles for Mazak NC Software | 11/2014
Program O9916: Machine-specific parameters 8.6
8
Parameters Meaning
#116* Diameter of the measuring surface on the top of the probe contact
Diameter or edge length of the probe contact in the Z axis.
Value range 0 to 99.999 mm
Default value 18.000 mm
#117*
#118
#119
#120*
#121
Axial measuring position for radius measurement
Offset in Z direction with respect to the measuring surface of the probe contact.
Value range
Default value
0 to 99.999 mm
3.5 mm
Rapid traverse
Feed rate for large positioning distances, e.g. for approaching the return position.
Default value: 10.000 mm/min
Positioning feed rate
The software uses a measuring block with positioning feed rate for pre-positioning. This prevents collision between an unknown or incorrectly inserted tool and the probe contact. Select the positioning feed rate so that the software can brake the axis within the overtravel of the touch probe head.
Default value: 5.000 mm/min
Measuring feed rate for non-rotating spindle
Select the measuring feed rate so that the software can brake the axis within the overtravel of the touch probe head. If the value is changed, recalibration must be carried out.
Default value: 150 mm/min
Calculation of measuring feed rate for rotating spindle
0 = Calculation of the measuring feed rate with constant tolerance
1 = Calculation of the measuring feed rate with variable tolerance
2 = Constant measuring feed rate
Default value: 0
#122
#123
#124
#125*
Maximum permissible measuring error for tool measurement with rotating spindle
Value range: 0.002 to 0.999 mm
Default value: 0.005 mm
Maximum permissible surface speed on the tool cutting edge
Value range: 1.000 to 129.000 m/min
Default value: 40 m/min
Maximum permissible spindle speed during tool measurement
Value range: 1 to 1000 rpm (0=1000 rpm)
Default value: 0
Number of the axis for radial offset
0 = X axis
1 = Y axis
Value range: 0 or 1
Default value: 0
Mazak | User’s Manual Touch Probe Cycles for Mazak NC Software | 11/2014
73
8
Software installation
8.6
Program O9916: Machine-specific parameters
Parameters Meaning
#126* Side for radial offset
-1 = Negative side
+1 = Positive side Value range: -1 or 1
Default value: 1
#127
#128
Return position
The tool is positioned to the return position in Z before and after measurement. The return position is entered in machine coordinates with respect to the tool-carrier reference point. It must be selected so that every tool can approach this position without a danger of collision. The input is limited to the safety clearance and the maximum tool length above the measuring position in Z.
Retraction distance after locating unknown tools
After locating the tool and conducting a rough measurement of the tool length and/or radius, the software positions the tool by this distance above or next to the measuring surface. Locating the tool is always performed with a non-rotating spindle. For tools like face-milling cutters the specified retraction distance must be sufficiently large to prevent collision with the touch probe.
Default value: 10 mm
#129 Safety clearance above or next to the measuring surface
Before actual measurement the tool is moved to a safety clearance above or next to the measuring surface. A measuring block is executed, starting from this position.
Value range: => 1 mm
Default value: 3 mm
#130
#131
#132
Maximum overtravel
To prevent damage to the touch probe head, the maximum overtravel (measuring path) within which the software expects a trigger signal is limited. The value depends on the mechanical overtravel of the touch probe.
Value range: 1.0 to 5.0 mm
Default value: 2 mm
Maximum tool length
Value for calculation of the starting position during tool length measurement. The software checks the tool length entered in the tool compensation memory. If the entered tool length plus the wear value is greater than the maximum tool length, the cycle is aborted with an error message.
Default value: 300.000 mm
Minimum tool length
Value for calculation of the target position during tool length measurement. The software checks the tool length entered in the tool compensation memory. If the entered tool length minus the wear value is less than the minimum tool length, the cycle is aborted with an error message.
Default value: 60.000 mm
#133
#134
Maximum tool radius
Value for calculation of the starting position during tool radius measurement. The software checks the tool radius entered in the tool compensation memory. If the entered tool radius plus the wear value is greater than the maximum tool radius, the cycle is aborted with an error message.
Default value: 30.000 mm
Base address of the tool memory for the tool length
("Base address of tool compensation memoryParameters #134 to #137")
Mazatrol tool data: 60000
EIA/ISO tool data: 40000
Tool dataType A/B: 10000
Default value: 60000
74
Mazak | User’s Manual Touch Probe Cycles for Mazak NC Software | 11/2014
Program O9916: Machine-specific parameters 8.6
8
Parameters Meaning
#135
#136
#137
Base address of the tool memory for the tool diameter
("Base address of tool compensation memoryParameters #134 to #137")
Mazatrol tool data: 61000
EIA/ISO tool data: 41000
Tool dataType A/B: 10000/16000
Default value: 61000
Base address of the tool memory for the tool length wear
("Base address of tool compensation memoryParameters #134 to #137")
Mazatrol tool data: 0
EIA/ISO tool data: 40000
Tool dataType A/B: 0/11000
Default value: 0
Base address of the tool memory for the tool tool diameter
("Base address of tool compensation memoryParameters #134 to #137")
Mazatrol tool data: 0
EIA/ISO tool data: 41000
Tool dataType A/B: 0/17000
Default value: 0
#138 Tool wear tolerance
Maximum permissible length or radius wear, above which the software is to issue an error message during a tool inspection ( B1.
) or a tool check ( B2.
).
Value range: 0.0 mm to 2.0 mm
Default value: 0.02 mm
#139*
#140*
#141*
Start address of the calibration parameters
These parameters must not be deleted when the machine is switched off.
Value range: 500 to 990 mm
Default value: 500
G-Funktion für den Messsatz
Abhängig vom elektrischen Anschluss des Skip-Signals müssen unterschiedliche G-Funktionen für den Messsatz in den Zyklen programmiert werden (z.B. G31, G31.1 – G31.4).
Diese G-Funktionsnummer kann hier definiert werden. Standardwert: 31.1
Compensation value for trigger point
Default value: 0.001 sec
#142
#146*
Program stop if tolerance exceeded
If the tool status parameter #108 > 0 is set for tool measurement or tool check, the part program can be stopped with the error message "Tool out of tolerance" or "Tool is broken".
0 = Program is stopped. The program must be aborted with the RESET key
-1 = Program is not stopped
Value range: 0 or -1
Default value: 0
Length of the zero tool
The actual length of the zero tool is entered here.
0 = No zero tool
> 0 = Zero tool
Default value: 0
Mazak | User’s Manual Touch Probe Cycles for Mazak NC Software | 11/2014
75
8
Software installation
8.6
Program O9916: Machine-specific parameters
*
Parameters Meaning
#147* Oriented spindle stop with stationary spindle
-1 = No spindle orientation.
Value range: 0 to 359 degrees
Default value: -1
#148*
#149
Side for probing in the minor axis
If a temperature compensation is to be performed in 3 axes, a side for probing in the minor axis
(3rd axis) can be defined here. If 0 is entered, the temperature compensation is performed in 2 axes (length and radius axes).
-1 = Negative side, minor axis
0 = Without minor axis
+1 = Positive side, minor axis
Default value: 0
Maximum permissible shift in TC comparison measurement
The thermal growth of the machine is limited. To detect whether errors have occurred in the measurement, a tolerance limit is defined for the TC comparison measurement.
Value range: 0 mm to 0.999 mm
Default value: 0.2 mm
After changes to #xxx* parameters, the calibration cycle BZ9911 must be executed.
76
Mazak | User’s Manual Touch Probe Cycles for Mazak NC Software | 11/2014
Program O9916: Machine-specific parameters 8.6
8
Calculation of the measuring feed rate
For measurement with non-rotating spindle, the control uses the measuring feed rate from #120.
When measuring a rotating tool, the control automatically calculates the spindle speed and feed rate for measuring.
The spindle speed n is calculated as follows: n = #123 / ( r *0.0063) n: Spindle speed (rpm)
#123: Maximum permissible surface cutting speed (m/min) r: Active tool radius
Call parameter R or, if R is not defined, radius value from the tool compensation memory.
The measuring feed rate v is calculated from: v = mt * n v: Measuring feed rate mt: Measuring tolerance, depending on #121 n: Spindle speed (rpm)
With parameter #121 you can define the way the measuring feed rate is calculated:
#121 = 0
#121 = 1
The measuring tolerance remains constant, regardless of the tool radius. With very large tools, however, the measuring feed rate is reduced to zero. The smaller you set the maximum surface cutting speed #123 and the maximum permissible measuring error #122 , the sooner you will encounter this effect.
The measuring tolerance is adjusted relative to the size of the tool radius. This ensures a sufficient measuring feed rate even with large tool radii. The software adjusts the measuring tolerance according to the following table:
Measuring tolerance Tool radius
Up to 30 mm
30 to 60 mm
60 to 90 mm
90 to 120 mm
#122
2 * #122
3 * #122
4 * #122
Mazak | User’s Manual Touch Probe Cycles for Mazak NC Software | 11/2014
77
8
Software installation
8.6
Program O9916: Machine-specific parameters
#121 = 2 The measuring feed rate remains constant; the measuring error, however, rises linearly with the increase in tool radius:
Measuring tolerance = (r * #122) / 5 mm r:
#122:
Active tool radius
Call parameter R or, if R is not defined, radius value from the tool compensation memory.
Maximum permissible measuring error
N100
#111=9999.999
#112=9999.999
#113=9999.999
#139=500
GOTO130
N120
#111=9999.999
#112=9999.999
#113=9999.999
#139=
N130
#110=1
#114=30.000
#115=30.000
#116=18.000
Parameter definition for two touch probes
If a machine is equipped with two touch probes, please keep in mind that they need to be assigned different parameter settings.
In most cases, the difference is limited to the parameters of the measuring position and the base address of the calibration value.
Before the parameter routine is called, it must be clear which touch probe is to be used. The #109 variable can be used for this purpose. The variable must be preset to 1 (for touch probe 1) or 2
(for touch probe 2) before the cycle call.
Additional modifications in O9916 under N100 (example):
N100 Machine-specific functions
IF (#109EQ2) GOTO120
Parameters for touch probe 1
X axis position in MCS
Y axis position in MCS
Z axis position in MCS
Start address of calibration / TC parameters
#117=4.000
#118=10000
#119=5000
#120=500
#121=0
Parameters for touch probe 2
X axis position in MCS
Y axis position in MCS
Z axis position in MCS
Start address of calibration / TC parameters
Parameters for both touch probes
Language code 0=English, 1=German
Probe-contact diameter in X direction
Probe-contact diameter in Y direction
Diameter of the measuring surface on the top of the probe contact
Axial measuring position for radius measurement
Rapid traverse
Positioning feed rate
Measuring feed rate for non-rotating spindle
Calculation of measuring feed rate for rotating spindle
78
Mazak | User’s Manual Touch Probe Cycles for Mazak NC Software | 11/2014
#122=0.005
#123=40
#124=0
#125=0
#126=1
#127=9999.999
#128=10.000
#129=3
#130=2
#131=300
#132=60
#133=35
#134=6000010000
#135=61000
#136=0
#137=0
#138=0.02
#140=31.1
#141=0.001
#142=0
#146=0
#147=0
#148=-1
#149=0.2
GOTO9999
Program O9916: Machine-specific parameters 8.6
8
Maximum permissible measuring error for tool measurement with rotating spindle
Maximum permissible surface speed on the tool cutting edge
Maximum permissible spindle speed during tool measurement
Number of the axis for radial offset (0=X-axis/1=Y-axis)
Side for radial offset (-1=negative side/+1=positive side)
Return position (Z-axis)
Retraction distance after locating unknown tools
Safety clearance above or next to the measuring surface
Maximum overtravel
Maximum tool length
Minimum tool length
Maximum tool radius
Base address of tool memory for tool length
Base address of tool memory for tool radius
Base address of tool memory for tool length wear
Base address of tool memory for tool radius wear
Tool wear tolerance
G-Funktion für den Messsatz
Trigger point compensation
Program stop if tolerance exceeded
Length of the zero tool (0=no zero tool)
Oriented spindle stop with stationary spindle
Side for probing in the minor axis temperature compensation (-1=negative/+1=positive/0=no side)
Maximum permissible shift in temperature compensation comparison measurement
Mazak | User’s Manual Touch Probe Cycles for Mazak NC Software | 11/2014
79
9
Error messages
9
Error messages
9.1
Error messages
9.1
Error messages
Error message
In cases of error, the error marker #108 is set and an error message is displayed on the screen.
Abort the program with the RESET key.
Eliminate the cause of error.
Restart the program.
Number Cause of error and corrective action
E1
E2
E3
E4
E5
E6
E7
Call parameter H undefined
The tool compensation number H is 0. Tool data cannot be read or written.
Check whether you have programmed the tool compensation number H in the cycle call. Program the tool compensation number H .
Call parameter D undefined
The tool compensation number D is 0. Tool data cannot be read or written.
Check whether you have programmed the tool compensation number D in the cycle call. Program the tool compensation number D .
Kein T-Code aktiv
Es ist kein T-Code aktiv. Es können keine Werkzeugdaten gelesen oder geschrieben werden.
Überprüfen Sie, ob vor dem Zyklusaufruf ein T-Code programmiert wurde.
Programmieren Sie den T-Code.
Incorrect call parameters
One or more call parameters have been assigned critical or invalid values.
Check whether valid values have been assigned to the call parameters H , D , B , Q , W , U , R and Z .
Check all call parameter for valid values.
Incorrect tool length/radius
The tool length values given in the tool memory or measured in the cycle exceed the permissible tool limit values. There is a danger of collision.
Check whether the parameters #131 and #132 have been correctly defined in the O9916 program.
Check whether the tool data exceed the limit values.
Correctly define the limit values in the O9916 program.
The tool cannot be measured.
Error when starting a measuring block
The measuring block cannot be executed because the 'high' measuring signal is already active or the tool is in an incorrect starting position with respect to the touch probe.
Check whether the touch probe is correctly connected.
Check whether the measuring positions have been correctly defined in parameters #111 - #113 .
Check the function of the touch probe.
Check the measuring positions in the O9916 program.
Measuring block without trigger
No trigger signal was detected during the last measuring block.
Check whether the touch probe is correctly connected.
Check whether the tool is shorter than the minimum tool length in parameter #132 .
Check whether the measuring positions have been correctly defined in parameters #111 - #113 .
Check the function of the touch probe.
Correctly define the tool limit values in the O9916 program.
Correctly define the measuring positions in the O9916 program.
82
Mazak | User’s Manual Touch Probe Cycles for Mazak NC Software | 11/2014
Error messages 9.1
9
Number Cause of error and corrective action
E8 Tolerance exceeded
The permissible wear tolerance was exceeded.
Check whether the tool is worn or broken.
Check whether the tool was pulled out of the tool holder.
Check whether there are chips on the touch probe or tool cutting edge.
Check the tool and the tool data.
Replace the tool.
Remove the chips.
E9
E10
E11
E12
Tool is broken
The wear is more than twice the permissible maximum value.
Check whether the tool is broken.
Replace the tool.
Incorrect calibration or TC parameters
The calibration values deviate excessively from the measuring positions in the calibration cycle
O9911. There is a danger of collision with the touch probe.
Check whether the measuring positions have been correctly defined in parameters #111 - #113 .
Check whether the touch probe has been calibrated.
Correctly define the measuring positions in the O9916 program.
Execute calibration cycle O9911.
Temperature drift exceeds limit
The measured temperature drift exceeds the permissible tolerance.
Check whether the value defined for the tolerance U is too low.
Check whether the machine is at operating temperature.
Increase the tolerance U .
Run the warm-up program.
Incorrect table parameters
The measuring cycle cannot be executed with the table parameters set in section 1 of the O9916 program.
Check whether the parameters in section 1 of the O9916 program have been correctly defined.
Check the input values in the following parameters:
#114 = Diameter of touch probe in X axis
#115 = Diameter of touch probe in Y axis
#116 = Diameter of touch probe in Z axis
#121 = Calculation of measuring feed rate
#122 = Maximum permissible measuring error with rotating spindle
#123 = Maximum permissible surface speed on the tool cutting edge
#124 = Maximum permissible spindle speed during tool measurement
#125 = Number of radius axis
#126 = Side of radius axis
#130 = Maximum overtravel
#134 = Base address of the tool memory for the tool length
#135 = Base address of the tool memory for the tool diameter
#139 = Start address of calibration parameters
#142 = Program stop in case of error message
#147 = Oriented spindle stop with stationary spindle
#148 = Side in minor axis for temperature compensation
#149 = Maximum permissible shift in TC comparison measurement
Mazak | User’s Manual Touch Probe Cycles for Mazak NC Software | 11/2014
83
Index
Index
C
Control types
E
I
L
Length measurement
M
P
Parameters
Programming example
Programs
R
S
T
Tool touch probe cycles
Touch probe
Touch probe calibration
84
Mazak | User’s Manual Touch Probe Cycles for Mazak NC Software | 11/2014
Touch probe cycles
Mazak | User’s Manual Touch Probe Cycles for Mazak NC Software | 11/2014
85
Touch probes from HEIDENHAIN
help you reduce non-productive time and improve the dimensional accuracy of the finished workpieces.
Workpiece touch probes TS
• Workpiece alignment
• Setting datums
• Workpiece measurement
Werkzeug-Tastsysteme
TT
TT 140
TT 449
TL kabelgebundene Signalübertragung
Infrarot-Übertragung berührungslose Lasersysteme
• Werkzeuge vermessen
• Verschleiß überwachen
• Werkzeugbruch erfassen
Tool touch probes TT
• Tool measurement
• Wear monitoring
• Tool breakage detection
1124377-20 · Ver00 · 11/2014 · Printed in Germany · H
1124377-20
*I_1124377-20*
advertisement
Related manuals
advertisement
Table of contents
- 1 Mazak
- 3 Contents
- 15 1 Fundamentals
- 16 1.1 About this manual
- 17 1.2 Fundamental software information
- 17 Important notes
- 18 Program overview
- 19 Procedure for commissioning
- 20 1.3 Fundamentals of touch probe cycles
- 20 Application possibilities for touch probe cycles
- 20 Notes on conducting measurements
- 20 Principle of function
- 21 Cycle call
- 21 Approach and departure strategies
- 21 Process errors
- 21 Tool data used for calculations
- 21 Unknown tool length / tool radius
- 23 2 Calibrating the touch probe(Format EIA/ISO)
- 24 2.1 Fundamentals
- 24 Why calibrate?
- 24 When to calibrate
- 24 How to calibrate
- 26 2.2 Calibrating the touch probe
- 28 2.3 Temperature compensation (TC) of NC axes
- 31 3 Touch probe cycles: Automatic tool length measurement (Format EIA/ISO)
- 32 3.1 Fundamentals
- 33 3.2 Tool length measurement
- 33 Procedure
- 33 Length measurement with non-rotating spindle
- 34 Length measurement with rotating spindle
- 35 Cycle call and cycle parameters
- 37 4 Touch probe cycles: Automatic tool length and radius measurement (Format EIA/ISO)
- 38 4.1 Fundamentals
- 39 4.2 Measuring the tool length and radius
- 39 Procedure
- 39 Length measurement with non-rotating spindle
- 40 Length measurement with rotating spindle
- 41 Radius measurement
- 42 Cycle call and cycle parameters
- 45 5 Programming (Format Mazatrol)
- 46 5.1 Programming in Mazatrol format
- 51 6 Programming examples (Format EIA/ISO)
- 52 6.1 Example: Calibration and temperature compensation
- 53 6.2 Example: Drill Ø 8 mm
- 54 6.3 Example: Face-milling cutter Ø 60 mm
- 55 6.4 Example: End mill Ø 6 mm
- 56 6.5 Example: Ball nose cutter Ø 6 mm, corner radius 3 mm
- 57 6.6 Example: Toroid cutter Ø 30 mm, corner radius 5 mm
- 59 7 Parameter tables
- 60 7.1 Call parameters
- 61 7.2 Result parameters
- 63 8 Software installation
- 64 8.1 Notes on touch probe installation
- 64 Mechanical installation
- 64 Electrical installation
- 65 8.2 Software installation
- 65 Program overview
- 66 Installing the software
- 67 8.3 Modifying machine parameters
- 68 8.4 Definition of M functions for cycle call
- 70 8.5 Program O9916: Adapting the software to the specific machine
- 72 8.6 Program O9916: Machine-specific parameters
- 72 Adapting machine-specific parameters
- 77 Calculation of the measuring feed rate
- 78 Parameter definition for two touch probes
- 81 9 Error messages
- 82 9.1 Error messages
- 84 Index