Renishaw NC3 non-contact tool setting system Installation & User's Guide
Add to my manuals
34 Pages
Renishaw NC3 is a laser-based non-contact tool setting system that provides high-speed/high-precision measurement of cutting tools on a machining center under normal operating conditions. As a tool moves through the laser beam, the system detects when the beam is broken. Output signals sent to the controller allow the presence of a tool and the position of the tip (broken tool detection) to be established.
advertisement
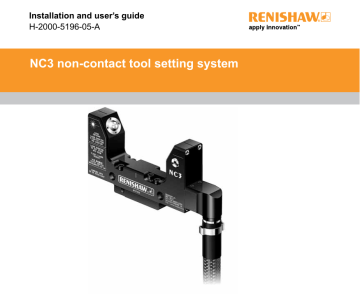
Installation and user’s guide
H-2000-5196-05-A
NC3 non-contact tool setting system
© 2002–2011 Renishaw plc. All rights reserved.
This document may not be copied or reproduced in whole or in part, or transferred to any other media or language, by any means, without the prior written permission of Renishaw.
The publication of material within this document does not imply freedom from the patent rights of
Renishaw plc.
Disclaimer
RENISHAW HAS MADE CONSIDERABLE EFFORTS
TO ENSURE THE CONTENT OF THIS DOCUMENT
IS CORRECT AT THE DATE OF PUBLICATION BUT
MAKES NO WARRANTIES OR REPRESENTATIONS
REGARDING THE CONTENT. RENISHAW
EXCLUDES LIABILITY, HOWSOEVER ARISING,
FOR ANY INACCURACIES IN THIS DOCUMENT.
Renishaw part no: H-2000-5196-05-A
First issued: 09 2002
Revised: 02 2003
08 2003
03 2004
12 2011
Trademarks
RENISHAW® and the probe emblem used in the
RENISHAW logo are registered trademarks of
Renishaw plc in the UK and other countries.
apply innovation is a trademark of Renishaw plc.
All other brand names and product names used in this document are trade names, service marks, trademarks, or registered trademarks of their respective owners.
Warranty
Equipment requiring attention under warranty must be returned to your supplier. No claims will be considered where equipment has been incorrectly installed or misused, or where repairs or adjustments have been attempted by unauthorised persons. Prior consent must be obtained in instances where Renishaw equipment is to be substituted or omitted. Failure to comply with this requirement will invalidate the warranty.
Patents
Features of the NC3 non-contact tool setting system are subject to the following patents and patent applications:
CN1187572
CN1202403
CN1660541
EP 1050368
EP 1144944
EP 1208351
EP 1506073
EP 1562020
JP 2003-521,681
JP 2003-524,154
JP 4521094
KR 0746932
KR 0810975
TW NI-153868
TW NI-178572
US 6,496,273
US 6,635,894
US 6,878,953
US 6643562
US 7,053,392
Preliminary information ..................................... 2
Warnings and cautions ..................................... 3
Warnings .................................................... 3
Caution – Laser safety ............................... 3
Laser warning labels and location of laser aperture ............................................................ 4
Introduction ....................................................... 5
Dimensions and mounting dimensions ............. 6
Installation ........................................................ 7
Base and side mounting options ................ 7
Angled mounting option ............................. 8
Mounting the unit ........................................ 9
Air supply ................................................. 10
Conduit adaptor and conduit .................... 13
General ........................................................... 15
Status LED ............................................... 15
Recommended feedrates ......................... 15
Software routines ..................................... 15
Contents
Specification ................................................... 16
Alignment ........................................................ 17
Achievable set-up tolerances ................... 17
Aligning the NC3 ...................................... 17
NCi-5 interface ................................................ 19
Installation ................................................ 19
Applying electrical power ......................... 20
NC3 to NCi-5 wiring ................................. 21
Maintenance ................................................... 22
Introduction .............................................. 22
Guidelines ................................................ 22
Cleaning ................................................... 22
Air regulator unit ....................................... 25
Parts list .......................................................... 28
1
2 Preliminary information
EC DECLARATION OF CONFORMITY c
Renishaw plc declares that the NC3 non-contact tool setting probe complies with the applicable standards and regulations.
Contact Renishaw plc at www.renishaw.com/nc3 for the full EC declaration of conformity.
FCC
Information to user (FCC Section 15.19)
This device complies with Part 15 of the FCC rules.
Operation is subject to the following conditions:
1. This device may not cause harmful interference.
2. This device must accept any interference received, including interference that may cause undesired operation.
WEEE DIRECTIVE
The use of this symbol on Renishaw products and/or accompanying documentation indicates that the product should not be mixed with general household waste upon disposal. It is the responsibility of the end user to dispose of this product at a designated collection point for waste electrical and electronic equipment (WEEE) to enable reuse or recycling. Correct disposal of this product will help to save valuable resources and prevent potential negative effects on the environment. For more information, please contact your local waste disposal service or Renishaw distributor.
Information to user (FCC Section 15.105)
This equipment has been tested and found to comply with the limits for a Class A digital device, pursuant to part 15 of the FCC Rules. These limits are designed to provide reasonable protection against harmful interference when the equipment is operated in a commercial environment. This equipment generates, uses and can radiate radio frequency energy and, if not installed and used in accordance with this installation guide, may cause harmful interference to radio communications. Operation of this equipment in a residential area is likely to cause harmful interference, in which case you will be required to correct the interference at your own expense.
Information to user (FCC Section 15.21)
The user is cautioned that any changes or modifications not expressly approved by Renishaw plc or authorised representative could void the user’s authority to operate the equipment.
Warnings and cautions 3
Use of controls or adjustments or performance of procedures other than those specified within this publication may result in hazardous radiation exposure.
Switch off the power supply before carrying out maintenance on the NC3 unit.
The International standard IEC / EN 60825-1 directs to attach a laser warning label and explanatory label.
A warning label and explanatory label are permanently fixed to each side of the transmitter housing (see the next page for details). An adhesive explanatory label is provided for attachment outside the machine.
Caution – Laser safety
The laser used in the Renishaw NC3 non-contact tool setting system emits continuous visible red light at a wavelength of 670 nm and has a maximum power output of less than 1 mW.
The NC3 is classified as a Class 2 laser product as defined by the International standard
IEC / EN 60825-1:2007. The product complies with 21CFR 1040.10 and 1040.11 except for deviations pursuant to Laser Notice No. 50 dated
June 24, 2007.
Safety rules
Do not stare directly into the laser beam. The beam may be viewed safely from the side.
Avoid visual exposure to the beam with optical appliances. Ensure that the beam is not reflected into the eyes of another person via a mirror or other reflective surface.
Do not expose skin to the laser beam for longer than is absolutely essential. Instruct all operators about the hazards of direct eye contact, or long skin exposure, with the laser.
Attach the laser warning label supplied in an easily visible location on the machine.
4
Label A
Laser warning labels and location of laser aperture
Laser aperture
Label B
Label A
Label B
Warning label
Explanatory label
Except for deviations pursuant to Laser Notice
No. 50 dated June 24 2007
Introduction
Introduction
The NC3 is a laser-based non-contact tool setting system that provides high-speed/high-precision measurement of cutting tools on a machining centre under normal operating conditions.
As a tool moves through the laser beam, the system detects when the beam is broken. Output signals sent to the controller allow the presence of a tool and the position of the tip (broken tool detection) to be established.
5
6 Dimensions and mounting dimensions
26
(1.02)
13
(0.51)
29 (1.14)
135 (5.31)
80 (3.15)
38 (1.50)
Status LED for indication only
77
(3.03)
67.5
(2.66)
59.5
(2.34)
34
(1.34)
25
(0.98)
21.75
(0.86)
35.5
(1.40)
62 (2.44)
47 (1.85)
31 (1.22) centre of beam
18 (0.71)
32.5
(1.28)
±2°
4.25
(0.17)
9 (0.35)
Ø17
(0.67)
13
(0.51) 26
(1.02)
Dimensions in mm (in)
M4 screws
(supplied)
Installation – base and side mounting options
M4 side mounting arrangement
M12 (½ in) screw (not supplied)
7
M10 ( ⅜ in) screw and washer (not supplied)
M4 screws
(not supplied)
Washer
Adjuster block
M4 screws
(not supplied)
8 Installation – angled mounting option
Angled adjuster block
(see the parts lists on pages 28 to 31 for ordering details)
Installation – mounting the unit
Mounting the unit
1. When an adjuster block is to be used for mounting the NC3 unit, loosely secure the block to the bed of the machine.
Carefully align the block with the X or Y axis of the machine then fully tighten the securing screw(s). Recheck the alignment is parallel within 1 mm of the X or Y axis.
2. On the NC3 unit, unscrew the M4 adjusting screw so that the thread protrudes approximately 1.5 mm from the base of the
NC3 unit.
3. Position the NC3 unit on the adjuster block and evenly tighten the three M4 securing screws to 1.3 Nm (0.96 lbf.ft).
M4 securing screws
M4 adjusting screw
Adjuster block
NOTE: See page 17 for instructions on aligning the NC3.
9
10
Air supply
The air supply to the NC3 unit must conform to ISO 8573-1 air quality of class 1.7.2 and be moisture-free. If the air quality cannot be guaranteed, an air filtration unit is available from
Renishaw – see the parts lists on pages 28 to 31.
The NC3 unit requires a continual regulated air supply of between 1.5 bar (21.75 psi) minimum and 6 bar (87 psi) maximum, with a recommended pressure of 2 bar (29 psi).
Failure of the air supply may cause the NC3 unit to become contaminated. If contamination is suspected (denoted by the NC3 unit’s LED flickering or showing permanently red) carry out the cleaning procedure (see “Cleaning” on page 22).
!
CAUTION: Do not connect the NC3 unit to an oiled air supply. Purge all piping prior to connection.
Installation – air supply
Connecting and purging the air supply
!
CAUTION: Safety glasses must be worn.
1. Connect a suitable pipe to the air supply.
2. Before connecting the pipe to the inlet of the air regulator unit, briefly switch on the air supply to clear out any debris from the pipe.
When no more debris is emitted from the pipe, switch off the air supply.
3. Connect the pipe to the inlet of the air regulator unit.
4. Insert one end of the 4 mm air pipe into the air regulator.
5. Cut the 4 mm pipe to length and connect it to the M4/M3 adaptor. Make sure the length of the pipe is as short as possible to minimise the drop in air pressure.
Installation – air supply
2.0 bar
Bar
Air regulator unit
Air outlet
Air pipe
Ø4 mm air pipe
Conduit adaptor securing screws
90° conduit adaptor
Electrical cable
Adaptor
Purge air supply to dislodge debris from pipework prior to connection as small particles may block the air nozzle.
Ø3 mm air pipe
To NCi-5 interface
Electrical cable
11
12 Installation – air supply
6. Insert one end of the 3 mm air supply pipe into the M3/M4 adaptor.
7. Push the free end of the air supply pipe through the conduit and conduit adaptor.
8. Cut the 3 mm pipe to length. Make sure the length is as short as possible to minimise the drop in air pressure.
9. Before connecting the pipe to the inlet of the
NC3 unit, briefly switch on the air supply to clear out any debris from the pipe. When no more debris is emitted from the pipe, switch off the air supply.
10. Insert the air supply pipe into the air inlet of the NC3 unit.
11. Switch on the air supply.
Installation – conduit adaptor and conduit
Fitting the conduit adaptor and conduit
1. Push the NC3 unit cable through the conduit.
2. Slide the conduit adaptor over the ridged securing ring on the NC3 unit.
3. Evenly tighten the two M5 screws on the top face of the conduit adaptor and the single
M5 screw on the underside of the adaptor to
1.5 Nm (1.1 lbf.ft).
4. Push the conduit over the barb on the conduit adaptor.
5. Slide the ‘O’ clip over the conduit.
6. Use a pair of pincers to pinch the ‘O’ clip onto the conduit.
‘O’ clip
Pincers
13
14 Installation – conduit adaptor and conduit
Securing the conduit
In some instances, straining of the conduit can cause small movements of the NC3 unit. Such movements will result in poor repeatability. If the conduit is able to move relative to the NC3 unit it should be firmly secured to the machine table.
Use the ‘P’ clips (part no. P-CL36-0016) to secure the conduit in a fixed position on the table of the machine (see the figure below).
‘P’ clips
General
Status LED
The LED on the NC3 indicates the status of the laser beam:
Green = Laser beam is unobstructed
Red = Laser beam is obstructed.
Recommended feedrates
It is recommended that a feedrate of 2 µm-perrev. is used for a minimum of three measuring moves. A span of 5 µm over three measurements is achievable.
Software routines
Software routines for tool setting using various machine controllers are available from Renishaw.
They are described in data sheet H-2000-2289
(see www.renishaw.com).
15
16 Specification
Application
Working temperature
Storage temperature
Pneumatic supply
High-precision / high-speed non-contact tool setting and tool breakage detection
5 °C to 50 °C
-10 °C to 70 °C
IP rating IPX8 with air on
Repeatability of trigger points ±0.15 µm (±6 µin) 2s
Life Tested to > 1 million on/off cycles
Tool diameter Tool setting: 0.20 mm (0.008 in) min., 80 mm (3.15 in) max.,
101.6 mm (4.00 in) off-centre
Tool breakage: Ø0.1 mm (0.004 in) min.
Ø3 mm air pipe, 1.5 bar (21.75 psi) min., 6 bar (87 psi) max.,
2 bar (29 psi) recommended. Air supply to the NC3 must conform to
ISO 8573-1: Class 1.7.2.
120 mA @ 12 V, 70 mA @ 24 V Current consumption
(including NCi-5 interface)
Cable
Weight
Mounting
Supply protection
6-core plus screen cable. Each core 18/0.1 insulated.
Ø6.0 (0.24 in) x 10 m (33 ft)
0.75 kg (1.65 lb)
Single M10/M12 fixing.
M4 mounting holes also provided.
Resettable fuses. Reset by removing power and cause of the fault.
Alignment 17
Achievable set-up tolerances
Tool setting applications
The tolerances to which a tool can be set is dependent on the parallelism of the laser beam to the machine axes. A value of 5 µm over a span of 50 mm perpendicular to the Z axis and 1 mm to the X or Y axis is easily achievable. This setting accuracy is sufficient for the majority of tool setting applications.
Tool breakage detection
A value of less than 0.1 mm (0.0039 in) maximum over a span of 50 mm perpendicular to the
Z axis and 1 mm with X or Y axis is achievable.
This should be sufficient for the majority of tool breakage applications.
Aligning the NC3
Aligning the NC3 involves making small adjustments to the unit in the Z axis until the laser beam is parallel to the machine X or Y axis within the set-up tolerances.
You will need to run the Renishaw NC software beam alignment cycle before physically aligning the NC3 (for details of this cycle, refer to the
Renishaw non-contact tool setting system programming guide).
After running this cycle, you will be able to ascertain whether the laser beam is parallel to the machine X or Y axis or whether the receiver end of the NC3 needs to be raised or lowered with respect to the transmitter end.
18
To raise or lower the receiver end of the
NC3
1. Slacken the single securing screw at the receiver end.
2. To raise the receiver end of the NC3, tighten the adjusting screw.
To lower the receiver end of the NC3, loosen the adjusting screw.
3. Gently tighten the single securing screw.
4. Run the beam alignment cycle again to determine whether the beam is parallel to the machine X or Y axis or whether further adjustments need to be made to the NC3.
Repeat steps 1 to 3 as appropriate.
5. After alignment has been achieved, tighten the single securing screw to 1.3 Nm
(0.96 lbf.ft).
Alignment
M4 securing screws
M4 adjusting screw
Adjuster block
NCi-5 interface – installation
Introduction
The NCi-5 interface should be installed in the
CNC control cabinet. Where possible, locate the unit away from potential sources of interference such as transformers and motor controllers.
The interface processes signals from the NC3 and converts them into a voltage-free solid state relay (SSR) output. This is transmitted to the CNC machine control, which responds to the probe inputs.
19
Installing the interface
!
WARNING: Before installing the NCi-5 interface, ensure the machine is safe to work on.
Switch off machine power when working in the control cabinet.
Install and configure the NCi-5 interface as described in the publication NCi-5 installation and user’s guide , Renishaw part no. H-5259-8500.
What to do next
After you have finished installing the NCi-5 interface, apply electrical power to the interface.
After the interface has been powered, switch on the air supply and set the air pressure.
20 NCi-5 – applying electrical power
Applying electrical power to the interface
!
WARNING: Before switching on electrical power, ensure the machine is safe to work on.
Power loss and restoration
If electrical power to the NCi-5 interface is lost and then subsequently restored when the NC3 system is in a normal operating mode, the NC3 powers down and then powers up again without loss of the original gain settings.
1. Ensure that the NCi-5 interface and air supplies have been connected correctly.
2. Switch on electrical power to the interface.
3. Check that the status LED on the NC3 unit is lit.
NC3
NC3 to NCi-5 wiring
White
Purple *
Blue
Black *
Red
Screen
Grey
21
7
8
9
10
4
5
6
1
2
3
NCi-5 connector CN1
Not used
Spare 0 V
Spare 12 V to 24 V
Analogue output 1
Analogue output 2
0 V
+12 V
Ground
* Note that some early NC3 units do not have a purple coloured wire but have one additional black wire. Both black wires should be connected to pin 7.
22 Maintenance
Introduction
The NC3 unit requires minimal maintenance, having been designed to operate as a permanent fixture on a CNC machining centre in an environment of hot metal chips and coolant.
Only the maintenance routines described in this guide should be undertaken. Further dismantling and repair of Renishaw equipment is a highly specialised operation and must only be carried out at authorised Renishaw Service centres.
Equipment requiring repair, overhaul or attention under warranty should be returned to your supplier.
Do not allow excessive waste material to build up around the unit.
Keep electrical contacts clean.
The NC3 unit is protected by a continuous stream of clean air. Approximately once a month, inspect the optics for contaminants.
The service interval may be extended or reduced dependent upon experience.
Optimum performance is achieved by running the system continuously.
Guidelines
The NC3 is a precision tool and must be handled with care.
Ensure that the unit is firmly secured to its mounting.
Cleaning
Cleaning may be required if the air to the NC3 becomes contaminated or if the system is left with the air off when coolant is present.
Excessive contamination will block the laser beam and prevent the system from functioning.
If contamination is suspected, identify the cause and rectify the problem before cleaning the system. If necessary, change the air pipe.
Maintenance
Clean the NC3 unit as follows:
1. Switch off the air supply and power supply.
2. Remove the air channel plug.
3. Remove the air caps from the transmitter and receiver units using the pin spanner provided.
23
4. Switch on the air supply and increase the pressure to purge out coolant that may be present.
5. When no further coolant is emitted from the housing for 1 minute, switch off the air supply.
(continued on next page)
Pin spanner Air cap
Air cap
Air channel plug
24
6. Wipe the optics of the NC3 unit with either a polyester swab or a cotton bud soaked in alcohol or similar (see the figure).
7. Replace the air channel plug and tighten to
1.3 Nm (0.95 lbf.ft).
Maintenance
8. Clean and replace the two air caps and tighten each one to 2 Nm (1.48 lbf.ft).
9. Switch on the air supply and set the pressure to 2 bar (29 psi).
10. Switch on the power supply.
Cleaning solvent RS Components Ltd part number 132-481 (recommended).
Alternatively, a mixture of 75% isopropyl alcohol with 25% water may be used.
Polyester swab RS Components
Ltd part number 408-1794
(recommended)
Maintenance – air regulator unit
Checking the liquid level
Regularly check the level of the accumulated liquid in each of the filter bowls. It is important that the level is kept below the filter element.
Draining the liquid
Drain the liquid that has accumulated in a filter bowl as follows:
1. Switch off the air supply. A quantity of liquid will drain from the bowl.
2. Switch on the air supply. Check that the pressure is set to 2 bar (29 psi). Adjust if necessary.
3. If the level of the liquid in the bowl is still too high, repeat steps 1 and 2 until the level reduces to a satisfactory level.
Air pressure regulator and filter unit
Oil removal filter unit
Air pressure adjusting knob
Filter bowl drain outlet
25
26 Maintenance – air regulator unit
Removing and refitting filter elements
Regularly inspect the filter elements. They should be replaced when dirty or wet and at least once each year. Do this as follows:
1. Switch off the air supply.
2. Unscrew the filter bowl by hand.
3. Remove the O-ring from the recess in the filter bowl. Discard the O-ring.
4. Unscrew and remove the filter element.
5. Fit the replacement filter and, where applicable, the O-ring. These are shown in dotted box A in the figure on the next page.
6. Fit a new O-ring into the recess in the filter bowl.
7. Refit the filter bowl and screw hand tight.
8. Switch on the air supply and set the pressure to 2 bar (29 psi).
Air pressure regulator filter bowl
Oil removal filter bowl
Maintenance – air regulator unit
Replacing other service kit components
1. Switch off the air supply.
2. Using a 38 mm A/F spanner, remove the regulator head.
3. Remove the components (shown in dotted box B in the figure) from the body of the regulator.
4. Fit the new components to the regulator body.
5. Refit the regulator head and tighten to 7.7 Nm (5.7 Ibf.ft).
6. Switch on the air supply and set the pressure to 2 bar (29 psi).
A
NOTE: Items shown within dotted boxes
A and B are included in the air filter service kit obtainable from Renishaw
(see the parts lists on pages 28 to 31).
B
27
28 Parts list
Type
NC3
NC3 kit
NCi-5 interface
Part number Description
A-4179-1500 NC3 assembly, 10 m cable, installation guide, laser warning sign
A-4179-1100 NC3 assembly, 10 m cable, NCi-5 interface, adjuster pack, tool kit, laser warning sign, installation guide, conduit, air regulator and air pipe
A-5259-2000 NCi-5 interface and box with DIN rail mounting and two terminal blocks
P-CN25-1053 10-way socket terminal for NCi-5 interface NCi-5 terminal block
(10-way)
NCi-5 terminal block
(15-way)
Tool kit
P-CN25-0009 15-way socket terminal for NCi-5 interface
Air assembly kit
A-4179-0300 Pin spanner, 2.5 mm A/F hex. wrench, 3.0 mm A/F hex. wrench
A-4179-1600 Air regulator filter Ø3 mm to Ø4 mm with air fittings,
25 m × Ø4 mm air pipe and 5 m × Ø3 mm air pipe
P-FI01-S002 Service kit for air regulator – parts for both filter bowls Air filter service kit
De luxe air filter P-FI01-0008 Air regulator with ‘blocked filter indication’ and auto drain
Angled adjuster block A-4179-1501 Block to angle the NC3 on the machine tool table
NCi-5 installation and user’s guide
H-5259-8500 NCi-5 interface installation and user’s guide
Conduit, steel braided P-HO01-0008 Ø17 mm PVC hose with steel braid – sold per metre
Tube, nylon M-4179-0161 Ø3 m nylon tube (5 m long) with a 4 mm to 3 mm reducer
Parts list 29
Type
Air nozzle kit
O-clip
Locknut
Part number Description
A-4179-0450 Air caps (2 off) for transmitter unit and receiver unit, and pin spanner
P-MA01-0045
P-NU09-0016
O-clip
M16 x 1.5 locknut
Straight conduit connector
Conduit gland
A-4179-0351 Replaces 90° conduit adaptor
Conduit gland blanking plug
P-clip
P-CA61-0063 GP11 conduit gland
P-CA61-0064 Conduit gland blanking plug
P-CL36-0016 Tubing clip Ø16 mm
NC software kit (Brother) A-4012-0904 Software for Brother 32A controllers (post June 2002), programming guide
NC software kit (Fadal)
A-4012-1035 Software for Brother 32B controllers, programming guide
A-4016-0061 Software for Fadal 32MP and CNC88 controllers, programming guide
NC software kit (Fanuc
Macro B)
NC software kit (Haas)
A-4012-0820 Angled beam software for Fanuc 0M, 6M, 16-21M/iM,
10-15M, 15iM and 30-32iM controllers, programming guide
A-4012-0895 Software for Haas controllers, programming guide
30 Parts list
Type
NC software kit
(Heidenhain)
Part number Description
A-4014-0165 Software for Heidenhain 426 and 430 controllers, programming guide
NC software kit (Hitachi
Seiki)
A-4014-0253 Software for Heidenhain i530 controllers, programming guide
A-4012-0848 Software for Hitachi Seiki Sigma 16M and 18M controllers, programming guide
NC software kit (Hurco) A-4012-1141 Software for Hurco WinMax controllers, programming guide
NC software kit (Makino) A-4012-0900 Angled beam software for Makino Pro 3 and Pro 5 controllers, programming guide
NC software kit (Mazak) A-4013-0062 Software for Mazak M32, M Plus and Fusion 640M controllers (EIA/ISO and Mazatrol compatible), programming guide
A-4013-0088 Angled beam software for Mazak Fusion 640M controllers, programming guide
NC software kit
(Milltronics)
A-4013-0119 Angled beam software for Mazak standard machines and VTC800 Matrix M controllers (EIA/ISO and Mazatrol compatible), programming guide
A-4012-1182 Software for Milltronics controllers, programming guide
31
Type
NC software kit
(Mitsubishi Meldas)
Part number Description
A-4013-0050 Software for Mitsubishi Meldas M3, M310, M320, M335,
M500, M600 and M700 series controllers, programming guide
NC software kit (Mori
Seiki)
A-4012-0953 Software for Mori Seiki non-Hi-Tech controllers, programming guide
NC software kit (Okuma) A-4016-1021 Software for Okuma 5020M, 700M, 7000M, U10M,
U100M and OSP 200M controllers, programming guide
NC software kit (Selca) A-4014-0218 Software for Selca S3000 and S4000 controllers, programming guide
NC software kit
(Siemens)
A-4014-0344 Software for Siemens 802D controllers, programming guide
A-4014-0401 Software for Siemens 810D V5+ and 840D V5+ controllers, programming guide
A-4014-0236 Angled beam software for Siemens 810D V5+ and 840D
V5+ controllers, programming guide
NC software kit (Yasnac) A-4014-0020 Software for Yasnac MX3 and J50 controllers, programming guide
A-4014-0025 Angled beam software for Yasnac MX3, J50, I80, J100 and J300 controllers, programming guide
Renishaw plc
New Mills, Wotton-under-Edge,
Gloucestershire, GL12 8JR
United Kingdom
T +44 (0)1453 524524
F +44 (0)1453 524901
www.renishaw.com
For worldwide contact details, please visit our main web site at www.renishaw.com/contact
*H-2000-5196-05*
advertisement
* Your assessment is very important for improving the workof artificial intelligence, which forms the content of this project
Related manuals
advertisement
Table of contents
- 4 Preliminary information
- 5 Warnings and cautions
- 5 Warnings
- 5 Caution – Laser safety
- 6 Laser warning labels and location of laser aperture
- 7 Introduction
- 8 Dimensions and mounting dimensions
- 9 Installation
- 9 Base and side mounting options
- 10 Angled mounting option
- 11 Mounting the unit
- 12 Air supply
- 15 Conduit adaptor and conduit
- 17 General
- 17 Status LED
- 17 Recommended feedrates
- 17 Software routines
- 18 Specification
- 19 Alignment
- 19 Achievable set-up tolerances
- 19 Aligning the NC3
- 21 NCi-5 interface
- 21 Installation
- 22 Applying electrical power
- 23 NC3 to NCi-5 wiring
- 24 Maintenance
- 24 Introduction
- 24 Guidelines
- 24 Cleaning
- 27 Air regulator unit
- 30 Parts list