advertisement
▼
Scroll to page 2
of
28
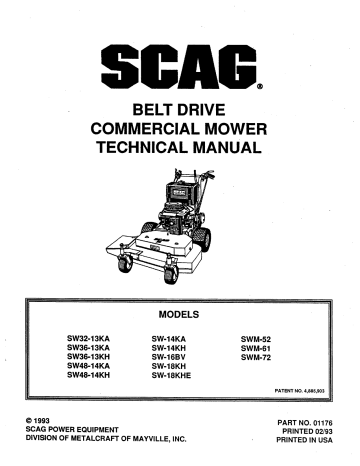
BELT DRIVE COMMERCIAL MOWER | TECHNICAL MANUAL MODELS SW32-13KA SW-14KA SW36-13KA SW-14KH SW36-13KH SW-16BV SW48-14KA SW-18KH SW48-14KH SW-18KHE PATENT NO. 4,885,903 O 1993 PART NO. 01176 SCAG POWER EQUIPMENT PRINTED 02/93 DIVISION OF METALCRAFT OF MAYVILLE, INC. : PRINTED IN USA TABLE OF CONTENTS SUBJECT Safety Instructions Before Operating — — — — — — — — — — — ——— — — — — — — — 2 While Operating - - — - — — — — - - — —- - —- —- —- — 2 While Maintaining and Storing __________._._.___ 3 Assembly Instructions — > ______ 3-5 Adjustments Cutter Deck Drive = 222 6 Drive Controls = ~~ o 6 Transmission Drive Belt — — ——————— - - - - - _ _ — — — 6 Tire Pressures — — — — — — — moon 6 Сепега! SS 7 Cutter Deck __ ________ 7 Tapered Bearing Spindle Ш 7-8 Lubrication к 8 Initial Run-n 2 9 Operating Instructions ___-—_-_-_--_--_-_----______ 9 illustrated Parts Listings 32" Cutter Deck — 2 10-11 36" Cutter Deck_____->->->-____________ 12-13 48", 52", 61" & 72" Cutter Decks _______-_-- —- __— _ 14-15 Engine Оеск к 16-18 Transmission — — —— —— — 19 Handle АззетьЬу — — 20-22 Wiring Diagram Electric Start — == = __ 23 . Wiring Diagram Manual Start Replacement Decals — — — — —§ ~~ oooo__ 25 WarrantV______---___________ 26 SAFETY INSTRUCTIONS Your mowerisonly as safe as the operator! As with any type of power equipment, carelessness or error on the part of the operator may result in serious bodily injury. in addition, improper maintenance of the machine can also result in injury. To reduce the potential for injury, please read and follow these instructions on safe operation and be certain that anyone using this mower fully understands and complies with the following instructions. BEFORE OPERATING 1. nN ad > or > N Read and understand the contents of this Technical Manual before operating the machine. Become familiar with all controls and know how to stop quickly. A free replacement manual is available by sending complete Model and Serial Number to: Scag Power Equipment, Inc. 1000 Metalcraft Drive Mayville, WI 53050 Do not aliow children to operate the machine. Do not allow adults to operate the machine without proper instruction. Before attempting to start engine, shift transmission into neutral, move biade clutch lever into STOP position and move neutral latches to NEUTRAL LOCK. Remove all debris or other objects that might be picked up andthrown by the cutter blades. Keep all bystanders away from the mowing area. Keep all shields, safety devices, and decals in place. If a shield, safety device or decal is defective or damaged, repair or replace it before operating. Also, tighten all loose nuts, bolts and screws to assure machine is in safe operating condition. Do not operate machine while wearing sandals, tennis shoes, sneakers or shorts. Also, do not wear loose fitting clothing which could get caught in moving parts. Always wear long pants and substantial shoes. Wearing safety glasses and safety shoes is advisable and required by some local ordinances and insurance regulations. Fill fuel tank with gasoline before starting the engine. Avoid spilling gasoline. Since gasoline is flammable, handle it carefully. Use an approved gasoline container. Do not fill tank while engine is hot or running. Do not smoke while handling gasoline. Fill fuel tank outdoors and up to about one inch (25 mm) below the bottom of the filler neck. Wipe up any spilled gasoline. m powx WHILE OPERATING 8. Start engine when neutral latches are in neutral lock position, cutter blades are disengaged, and transmis- sion is in neutral. Do not run the engine in a confined area without adequate ventilation. Exhaust fumes are hazardous and could possibly be deadly. . Using the machine demands attention. To prevent loss of control: A. Mow only in daylight or when there is good artificial light. Watch for holes or other hidden hazards. Do not drive close to a drop-off, ditch or creek bank or other hazard. Reduce speed when making sharp turns and when turning on hillsides. Always be sure of your footing. Keep a firm hold on the handles and walk---never run. F. Do not operate where conditions are slippery. m D OW . Thedischarge chute must always be installed andinthe down position on the side discharge cutting unit except when optional grass catcher or mulching plate are com- pletely installed. if the cutting unit discharge should plug, shut engine off and wait for all movement to stop before removing obstruction. . Disengage the blades and wait for them to stop before crossing gravel drives, walks or roads. . Shut the engine off and wait until the blades come to a complete stop before removing the grass catcher container. . Never raise the cutting unit while the blades are rotat- ing. . If the cutting blades should strike a solid object or the equipment should start to vibrate abnormally, stop the engine, disconnect the spark plug wire, and check immediately for the cause. Vibration is generally a warning of trouble. Check the cutting unit and traction unit for damaged or defective parts. Repair any damage before starting the engine and operating the cutter unit. Be sure blades are in good condition and blade bolts are tight. . Always park the mower and/or start the engine on a level surface. If this is not possible, block the wheels to prevent the mower from moving when you are not inthe operator’s position. . Cut grass slopes carefully. Do not start, stop or turn suddenly. Mow across the face of slopes; never up or down. Do not mow excessively steep slopes. SAFETY INSTRUCTIONS CONT'D 18. Do not touch engine or muffler while engine is running or soon after it is stopped. These areas could be hot enough to cause a burn. 19. Before leaving the operator’s position or leaving mower unattended, shift transmission into NEUTRAL, place neutral latches in NEUTRAL LOCK position, move cutter blade engagement lever to STOP and shut OFF engine. - | 20. Do not pass or stand on the grass discharge side of any mower with the engine running. Stop operation when another person approaches. MAINTENANCE AND STORAGE 21. Disconnect high tension wire from spark plug to prevent accidental starting of the engine when servicing, adjust- ing or storing the machine. | 22. If mower must be tipped to perform maintenance ог adjustment, remove battery, drain gasoline from fuel tank and oil from crankcase. . 23. To reduce potential fire hazard, keep the engine free of excessive grease, grass, leaves and accumulations of dirt. Ä 24. Be sure machine is in safe operating condition by keeping nuts, bolts, and screws tight. Check the blade mounting bolts and nuts frequently to be sure they are tightened. 25. Ifthe engine must be running to perform a maintenance adjustment, keep hands, feet, clothing and other parts ofthe body away from the cutter deck blades and other moving parts. | 26. Do not overspeed the engine by changing governor settings. To be sure of safety and accuracy, have an authorized dealer check maximum engine speedwith a tachometer. 27. Engine must be shut off before checking oil or adding oil to the crankcase. 28. Allow engine to cool before storing mower in any enclosure such as a garage or storage shed. Make sure the mower fuel tank is empty if machine is to be stored in excess of 30 days. Do not store mower near any open flame or where gasoline fumes may be ignited by a spark. 29. Always store gasoline in a safety-approved, red con- tainer. 30. Keep the mower and fuel container in locked storage to prevent children from playing and tampering with them. 31. Performonly those maintenance instructions described in this manual. If major repairs are ever needed or assistance is desired, contact an Authorized Scag Dealer. To ensure optimum performance and safety, always purchase genuine SCAG replacment parts and accessories. NEVER USE “WILL-FIT” replacement parts and accessories made by other manufacturers. Using unapproved replacement parts and accessories may void the warranty. 32. Becareful when servicingthe battery as it contains acid, which is corrosive and could cause burns to skin and clothing. 33. Batteries release explosive gases when being charged or discharged. KEEP away from any source of sparks and/or flame. | ASSEMBLY INSTRUCTIONS ELECTRIC START UNITS ONLY! Before proceeding with assembly, prep the battery. Fill each cell with electrolyte until the top of the plates are covered. Charge the battery at 3 to 4 amps for 4 hours (this insures a good initial charge), check and add electrolyte as needed to bring the fluid level to the bottom of the split ring. Then wash and dry off the battery. NOTE: Once the above fill and charge procedure has been completed only distilled water should be added to the battery cells. Set the battery into the support, connect the positive cable to the positive post, then connect the negative cable to the negative post. Put the battery cover in place (at the back of the battery), and clamp the battery into place (finger tight) using the carriage bolts and wing nuts. DO NOT OVER TIGHTEN. WARNING: Severe chemical burns can result from im- proper handling of battery electrolyte. Use proper eye, skin and clothing protection to prevent contact with eyes, skin and clothing. External contact: Flush with water. Internal contact: Drink large quantities of water, followed by milk of magnesia, beaten egg or vegetable oil. CALL A PHYSICIAN IMMEDIATELY! IMPORTANT - In case of internal contact DO NOT give fluids that would induce vomiting. Eye contact: Flush with water for at least 15 minutes and GET MEDICAL ATTENTION IMMEDIATELY! ASSEMBLY INSTRUCTIONS CONT'D A WARNING: Explosive gases are vented from a battery when being charged or discharged which could explode if exposed to a flame or spark. SET-UP ALL UNITS 1. Lay out hardware according to the “Where Used” list inthe loose parts packing list. 2. Install handle assembly to handle mounting frame using four 3/8-16 x 1" bolts, flat washers, and elastic stop nuts. Three different handie heights can be obtained using one of the three slotted holes in the handle mounting frame. l 3. Route the throttle control above the RH jackshaft and up the right side of handle. Secure to handle with 1/4-20 x 2" hex head bolt and elastic stop nut. Secure cable about half way down the handle using a cable tie. NOTE: Check that the throttle cable moves the carburetor controls through their full range. If not, adjust as re- quired. 4. Route the operator presence interlock wires up the left handle tube and attach the connector to the switch as shown. Be certain that the connector does not hit the safety lever stop tab, if it does, rotate the switch to the position shown (see figure 1). CONNECTOR MOUNTED FROM a THIS DIRECTION ROTATE SWITCH SO THAT CONNECTOR DOES NOT HIT STOP TAB STOP TAB Figure 1 5. Installing control rods. a) Thread rods into the swivel joints that are attached to the idler brackets on each side of the unit. b) Adjust the rods so that there is about a 1/4"-3/8" clearance to the bottom of the neutal latch slot when in the drive position. Secure with small hair pin cotter as shown (see figure 2) NEUTRAL LATCH <} а TI AE O) N 1/4” - 3/8” STEERING RAL POSITION DRIVE POSITON fez РР и = BRAKE Ни Figure 2 с) Adjust brake rods so the brakes lock when the steering levers are pulled all the way up. NOTE: Rods mustallow neutral latches to be moved to the neutral position. (see fig.ure 2) 6. Attach shift lever assembly as shown (see figure 3) on top of the short lever that is bolted to the transmission using two 5/16-18 x 1” bolts, flat washers, lock washers and hex nuts. Two heavy flat washers should be inserted above the shift lever and two inserted below. SHIFTER AS HEAVY WASHERS ON TOP SHIFT ~ A SHIFT LEVER ASSEMBLY HEAVY WASHERS ON BOTTOM Figure 3 7. The shift lever should be adjusted so that the shift lever assembly is 0 to 1/8" away from the stop when the transmission is in neutral (see figure 4). Tighten nuts securely. NOTE: Engine will not start if transmission is not in neutral. ASSEMBLY INSTRUCTIONS CONT'D NEUTRAL POSITION CoH — | 7-0 TO 1/8" HANDLE MOUNTING FRAME SHIFTER PLATE Figure 4 8. Attach fuel tank (See figure 5) as follows: a) Wrap the straps around the fuel tank to pre-form them, then set aside to be used later. b) Position the four rubber pads on the gas tank with two 1/4" thick pads in the strap grooves on top and two 3/8" pads with adhesive bottoms in the strap grooves betweenthe gastank and handle mounting frame. Attach the adhesive side of the bottom two pads to the handle mounting frame. Position the tank so the SCAG logo is forward. Place the straps around the tank going under the handle mounting frame, secure the strap together in front using (2) two 1/4-20 x 2” slotted machine screws and hex nuts. Tighten screws until the tank will not slide around. Over tightening will damage the tank or straps. Attach the fuel line to the valve on the bottom of the tank. d) [А = 7 PADS — => —STRAPS +. han, A STRAPS PASS UNDER HANDLE MOUNTING FRAME ALIGN PADS WITH GROOVES Figure 5 5 ATTACHING SWM-52, SWM-61, SWM-72 TO ENGINE DECK a) Before beginning, determine which mounting holes are to be used to best suit the cutting height requirements of your customer. (see figure 6). Low Cut (1 3/4*- 3") Mid Range (2 1/2"-3 3/4”) Engine Deck High Cut (3 1/4"-4 1/2") | Cutter Deck Figure 6 b) Remove belt cover by loosening the wing nuts securing it to the cutter deck. Position the cutter deck so that the engine deck is between the mounting brackets of the cutter deck. Install two bolts through the mounting holes selected, secure loosely with a flat washer, lock washer and hex nut. Tilt the engine deck up or down to align the remaining four holes and secure with remaining hard- ware. Torque cutter deck mounting bolts to 50 to 70 ft. Ibs.. Route belt around engine pulley and tighten bolt on engine belt guide. Connect lower blade clutch control rod to eyebolt and over center link with flat washer and hair pin. с) 9) 10. Attach discharge chute to cutter deck using two 5/16-18 x 1" bolt and elastic stop nuts. Tighten bolts on chute until chute moves freely with some resistance. 11. Attach caster wheels supports to cutter deck using four 5/16-18 x 3/4" bolts, lock washers and hex nuts. NOTE: Check all hardware to be sure it is tightened properly, also check clearance and routing of drive belts. 12. Check engine oil level and fill as is necessary. Add oilto the engine crankcase using type specified in engine operator’s manual. 13. Fill fuel tank to about 1" below the fill neck with gasoline as specified in engine operator’s manual. ADJUSTMENTS CUTTER DECK DRIVE ADJUSTMENTS 1. Engage blade clutch lever and check for proper over center clearance. There should be about 3/8" between RH Belt Tension | Г Engagement Idier rod and straight edge (see figure 7). Bend the stop tab Adjustment Idler u to adjust clearance. There aretwo holes drilled into the cam link that you can use for the bolt that secures the cam link to the mounting post welded to the deck. This will allow you to lengthen or shorten the engagement linkage to compensate for belt wear. Discharge Area ADJUST BELT TENSION Check RH Drive Check Blade Drive WITH TURN BUCKLE Belt Tension Here Belt Tension Here 3/8" Figure 8 DRIVE CONTROLS F \ 1. Steering control rods should have about 1/4" clearance between the bottom of the slot and the bottom ofthe rod JAM NUT when the steering levers are released (see figure 2). 2. Thebrake rods should be adjusted so thatthe brakesdo ADJUST OVERCENTER not apply until the steering levers are pulled tight to the Li BY BENDING STOP TAB handies. When the steering levers are locked in the neutral position the unit may be pushed around. 3. The shift lever is adjustable, and can be moved right to Figure 7 left allowing proper positioning for neutral (See figure 4). 2. Adjust belt tension so that the belt moves 1/2” with 10 TRANSMISSION DRIVE BELT lbs. of pressure applied between the center and left spindle pulleys (see figure 8). Adjustment is made by loosening the jam nut and tightening/loosening the turn buckle (see figure 7). Belt driving right spindle should be checked the same way. Adjust with J-rod on RH belt tension adjustment idler. Adjust the transmission drive belt so that there is about a 3/16" deflection with 10 pounds of pressure. Adjust by loosening idler pulley mounting bolt and sliding the idler left or right to change belt tension. NOTE: Belt tension may need to be increased or TIRE PRESSURES decreased 1 to 2 Ibs. to achieve lowest bellt vibration . Drive Wheel Tires 15 psi Caster Wheels 25 psi ADJUSTMENTS GENERAL ADJUSTMENTS Check that all belts clear their guides by 1/8" to 1/4". ‚2. Adjust tension of blade drive belt by rotating turnbuckle so that about 10 pounds pull sideways deflects belt about a 1/2". DO NOT OVERTIGHTEN. Only a moder- ate force should be required on the engagement lever. 3. Check tension of transmission drive belt (under engine deck). A ten pound pull sideways should deflect belt about 3/16". Slide idler pulley if required to adjust. 4. Thetension ofthe two Twin Power Wheel Drive belts is self-adjusting. However, for adequate declutching, adjust length of steering control rods on each side of handle until about a 1/4" gap is provided between rod and bottom of neutral latch slot, when neutral latch is in drive position. 5. Adjust brake rods so that brakes will lock wheels while pulling machine rearward with steering levers fully squeezed. Check that machine rolls freely when neu- tral latches are in neutral lock position. CUTTER DECK ADJUSTMENTS Due to the many cutting conditions that exist, it is difficult to suggest a setting that will work for every lawn. There are two adjustments that can be made on these decks, pitch and height. PITCH is the angle of the blades (comparing front to rear). A positive pitchis when the front (leading) edge of the cutting plane is lowerthan the rear (trailing) edge, leve! pitchis when both front and rear are the same height, a negative pitch is when the leading edge is higher than the rear edge. We suggest that a postive pitch be used when cutting grass. The front of the deck should be 1/4" to 1/2” lower than the rear of the deck. HEIGHT is the nominal distance the blade is off of the ground. This measurement is made with the blades pointed side to side and distance is measured between cutting tip . and ground. TAPERED BEARING SPINDLE ASSEMBLY Adjusting the blade height can be done by moving any number of the four smaller 1/4" spacers on the blade mount- ing bolts to the top of the spindle shaft or below the spindle shaft. (All blades should be positioned equally). The tapered bearing spindle has a large 1/4" spacer that is installed directly below the spindle housing and is secured to the spindle with two roll pins. The blade can be adjusted all the way up to the spindle assembly if all the smaller 1/4" spacers are removed and installed above the pulley. The larger 1/4° spacer can then be removed along with the roll pins. (Do not install the larger 1/4" spacer above the pulley, store it in a convenient location away fromthe machine). When any 1/4" spacers are installed above the blades the larger 1/4" spacer must be installed directly below the spindle housing. lf a smaller 1/4" spacer is installed directly below the spindle housing and contacts the retaining ring this will cause a spindle failure and not be warrantable. For best cut and discharge, a minimum of three spacers should be installed between the blade and spindle. (see figure 10) Hex Nut-Torque lo 75 FEES mu Cutter Blade Spacer 1/4"-Small | ] L UN a | | a SN Spindle E | | be qn ПД [ | oo m \ Cutter Deck Spindle Assembly CPC RE a DCI Cutter Blade Ал Spacer 1/4"-Large [__]= Cutter Blade Spacers 1/4”-Small Washer ——— + O | Hex Head Bot 1 [ Cutter Blade Figure 10 ADJUSTMENTS CONT'D Additional range to the cutting height can be achieved by repositioning the cutter deck in relationship to the engine deck (This adjustment can also effect the pitch of the deck). There are 3 positions (see figure 6), suggested mounting is the middle holes. For cutting lower, mount the deck in the top holes. To cut higher, mountthe deck inthe bottom holes. Remember to check the cutter deck belt alignment. Shim- ming or attaching the idler mounting bracket from under- neath may be necessary to maintain belt life. Caster spacers also can be repositioned to change cutting heights and to change the pitch of the deck (see figure 11). Quick Pin 7797 Caster Spacers 1/2" ——— Caster Support o — In Caster Spacers 1/2" \ \ \ | Figure 11 BREAK-IN LUBRICATION & MAINTENANCE PROCEDURE COMMENTS Check all hardware for proper tightness Change engine oil and filter at 5 hours as required ine mtg. information A GT AmO e O И НИЕ A TE Grease transmission couplers Check all hardware for proper tightness Chassis grease + Grease spindle until grease comes out the relief valve 8 SCAG INITIAL RUN-IN OPERATING INSTRUCTIONS A WARNING: Use extreme caution during mower's initial run-in to assure caster wheels are adequately blocked and drive wheels do not inadvertently contact ground. Keep bystanders away from machine. Never allow mower to discharge towards bystanders. Never leave the machine unattended during the initial run-in. 1. 2. Lubricate all fittings as specified in Lubrication Section. Locate machine in a secure area, away from bystand- ers, and preferably facing a wall. Raise drive wheels off ground. Block caster wheels. Make sure area under cutter deck is clear of objects. Start engine and shift transmission into fourth gear. Engage cutter blades. Set throttle for 3/4 of full engine rpm. Run the machine for a few minutes. Declutch cutter blades. Shift transmission into NEUTRAL. Stop engine. Check tension of blade drive beit(s) and transmission drive belt. Adjust if necessary. If necessary, readjust steering control and brake rods as indicated in the Adjustments Section. Check function of all safety interlocks. Make sure that engine will not start unless transmission is in neutral and blade clutch is disengaged. Check tire pressure and adjust to: Caster Wheels Drive Wheels 25 ря. 15 psi. YOU ARE NOW READY TO MOW WITH CONFIDENCE! 1. 5. Read and understand the instructions on safety before attempting to operate. Before starting engine: * Fuel valve must be opened. * Transmission must be in NEUTRAL. ” Blade clutch lever must be in STOP position. * Neutral latches must be in NEUTRAL LOCK position. * Key switch on. * Choke as required. Start engine. Adjust throttle to achieve proper blade speed. Engage cutter blades by pushing blade clutch lever forward until it snaps into the ON position. Pull lever back to disengage cutter blades. Shift transmission into gear for desired mowing speed. NOTE: Top speed is suggested only for transport! 6. 8. While squeezing steering brake levers with both hands, release both neutral latches. When steering brake levers are released, machine will travel straight. To make a right turn, squeeze RH lever to turn left squeeze LH lever. TO STOP wheel drive, squeeze both levers, lock neu- tral latches, shift transmission into neutral. À vanne: To avoid serious bodily injury and damage to transmission, machine must be at full stop before shift- ing from forward to reverse or from reverse to forward. 9. In reverse gear, the steering brake levers must be pushed downward for maximum traction. 32" CUTTER DECK 10 32" CUTTER DECK pots Cutter Blas e 11A 43201 Spacer, Tapered Bearing 12 . Hex Hd. Bolt, 5/16-18 x 1-1/4 13 . l.ockwasher, Spring, 5/16 14 * Hex Nut, 5/16-18 m Е 19 04066-01 Quick Pin | 20 43037-01 Spacer, Caster Yoke, 1/2" long 21 48100-01 Bronze Bearing 4811 4-01 Grease Fitting Str. 1/4-28 EASE Wheel Assy. (includes 13-14a, 29-34) Tire Only Caster Wheel Inner Tube only Rim Pair, Caster Wheel Retainer, ne Caster wheel 39 46157 Belt Cover Assy. (includes decals) 40 * Washer, 25/64 x 15/16 x 12 ga.. 40А * Washer, 13/32 x 13/16 x 16 ga. 41 04029-03 Wing Nut, 3/8-16 42 48127 Pulley (includes 43-44) Ref. Part Ref. Part No. No. Description No. No. Description 1 46156 Cutter Deck 43 48141 Tapered Hub 2 46400 Cutter Spindle Assy. (Includes 3-9 & 81-85) 44 * Hex Hd. Bolt, 1/4-20 x 3/4 3 04050-04 Retaining Ring, 1” Ext.-Inverted 45 * Hex Nut, 5/8-11 4 04050-07 Retaining Ring, 2-7/16 Int.bsc 46 48278 Beit, Blade Drive 5 AT Hex Hd, Bolt, 98.16 x 5 rex ‘Hd. Bolt 7/16-14 x 1.1/4 53 . Washer, 15/32 x 59/64 x 16 ga. 54 “ Lockwasher, Spring, 7/16 55 . Hex Nut, 7/16-14 elastic stop idler Pivot 63 04070-02 Eyebolt, LH 64 04070-01 Eyeboit, RH 65 43025 Turnbuckle 66 04022-02 Wing Nut, 5/1 6-18 Washer. 39/64 » X 4 x 16 ga. 73 04062-01 Hair Pin, Large 74 . Hex Hd. Bolt, 3/8-16 x 1 75 42057 Cam Link 76 44009 Belt Guide Part Removed From Illustration 83 43218 Sleeve, Cutter Spindle 84 48677 Relief Fitting, Cutter Spindle 85 . Roll Pin, 1/8 x 1/2" 86 Y Flat Washer, 5/16 * Common hardware which should be purchased locally. All bolts are Grade 5 plated, all other fasteners are zinc plated. 11 36" CUTTER DECK 12 36" CUTTER DECK Ref. Part Ref. Part No. Number Description No. Number Description JATTENTION LINES IN BOLD LETTERS INDICATE 40А * Washer, 13/32 x 13/16 x 16 ga. EXTRA IDENTIFICATION IS NEEDED! 41 04029-03 Wing Nut, 3/8-16 1 46087 Cutter Deck (Includes Decals) 42 48127 Pulley (Includes Items 43-44) 2 46400 - Cutter Spindle Assy. 43 48141 Tapered Hub * Hex Hd. Bolt, 1/4-20 x 3/4" BB: 9 04041-02 Washer. 1 -5/16 X 2-7/16 x 16 ga. 49 ° Lockwasher. Spring 3/8" 10 04063-08 Key, 1/4 x 1/4 x 2" 50 04604-02 Support, Belt Cover 11 43038 Spacer, Cutter Blade - Small 51 45098 Belt Guide 11A 43201 Spacer, Cutter Blade - Large 52 * Hex Hd. Bolt, 7/16-14 x 1-1/4" 12... Hex Hd. Bolt, 5/16-18 x 1-1/4" 53 * Washer, 15/32 x 5964 х 16 да. Flatwasher. 5/8 W 04050-05 Hex Hd. Bolt, 5/8-11 x 9-1/2” 60 04004-04 Stud Caster Assembly (Includes Items 19-28) 61 48269 Idler Pulley, Belt Clutch Quick Pin 62 * Flatwasher, 3/8” Rod End - LL Н. „Thd (Silver) Hex Locknut 1/2-13 u Wheel Assy. (Includes 13-14a, 29-34) Sleeve, Clutch Rod Tire Only Caster Wheel Cotter Pin, 3/32 x 1" Inner Tube only Washer. 33/64 x 1 x 16 ga. Rim pair caster \ Wheel Discharge ci Chute TE Spindle Bushing Hex Nut, 5/16-18 Elastic Stop 80 43218 Sleeve, Cutter Spindle Hex Hd Bolt, 5/16-18 x 1” 81 48677 Relief Fitting, Cutter Spindle 39 46085 Belt Cover Assembly (Includes Decal) 82 Ñ Flatwasher, 5/16" 40 * Washer, 25/64 x 15/16 x 12 ga. 83 ° Roll Pin, 1/8 x 1/2" “ Common hardware which should be purchased focally. All bolts are Grade 5 plated, all other fasteners are zinc plated. 13 48, 52, 61, & 72" CUTTER DECK 14 48, 52, 61, 8 72" CUTTER DECKS 15A | 15А foe 48184 a Sleeve, Caster Wheel o Ssaring ox Hd И be es Ref. Part Ref. Part No. No. Description 48 52 61 72 No. No. Description 48 52 61 72 1 46088 Cutter Deck (Includes decals) x 47 48087 Belt, RH Blade Drive X 1 46163 Cutter Deck (includes decals) x 47 48285 Belt, RH Blade Drive X 1 46119 Cutter Deck (Includes decals) x 47 48265 Belt, RH Blade Drive x 1 46194 Cutter Deck (Includes decals) x 47 48295 Belt, RH Blade Drive x 2 46400 Spindle Arme een Bearing X X X X 48 48089 Belt, Blade Drive x bos УТ ERE Panas AREA se Xx X X X Washer, 1 -5/16 x 2-7/16 x 16 ga. X X X x Hex Nut, 3/8-16, Centerlock x xX Key, 1/4 x 1/4 x 2" X X X x . Lockwasher, Spring, 3/8" хх Spacer, Cutter Blade - Small x x X X 04004-02 Support, Belt Cover хх хххх хх ee Cutter Blade - Large Belt Guide | Gutter Blade 18" * Retaining Ring, 3/4" Ext. Cutter Blade 21" x 60 46081 Idler Arm Assy. (Includes 82 & 61) Cutter Blade 24" x Bronze Bearing Cutter Blade 16-1/2"” Hi Lift x Cutter Blade 18° Hi Lift Cut A ee г J Rod, Idler Pull Spacer, 3 Pull Rod . AS x x «x X «KD X хх Bronze Bearing X xX X x 69 48544 Rod End L. H. THD. (Silver) хх Support Assy. (incl. 21-90) X X X x 70 48464 Rod End R.H. THD. (Gold) хх Caster Yoke X X X x 71 48590 Link, Turnbuckle хх хх хх хх 72 ” 3/8"- 24 Hex Nut X хх Retainer, Bearing, Caster Wheel X X X x 79 . Cotter Pin, 3/32 x 1" хх Roller Bearing, Caster Wheel X xX X X 80 . Washer, 33/64 x 1 x 16 ga. хх Grease Fitting 45 deg., 1/4-28 X X X X 81 04062-01 Hair Pin Large хх хх хх 82 . Hex Hd Bolt 3/8-16 x 1" хх Hub Assy. (inci. bolts) MEE Нонна Belt Cover (Includes decals) X 88 Flätwasher 3/4 x 1-1/4 x .035 хх Вей Cover (Includes decals) X 89 " Hex Head Bolt, 3/8-16 x 1-1/2" x x Belt Cover (Includes decals) X 90 48114-04 Grease Fitting хх Belt Cover (includes decals) X 91 48681 Seal хх хх Washer 25/64 X 15/16 x 12 ga. X X X X 92 43217 Spindle Bushing | AA SS DER Pa ee Te tet at at Hex Nut cree хх xX Хх | 98 04050-05 Retaining Ring 1- 1/8 Ext. "Е" хх Pulley, Double (Includes 43-44) Pulley, Double (Includes 43-44) X x > x © ite) 45037 ег Pivot хх x x x x XK XX M X x OK XX WK OK x XX MW “ Common hardware which should be purchased locally. All bolt Grade 5 plated, all other fasteners zinc plated. 15 ENGINE DECK ENGINE DECK REF. PART DESCRIPTION 13KH 13KA NO. NO. | 14КН14КА 16BV 18KH 18KHE 1A 48674 Engine12.5HP Kohler (PS-1256) X 1A 48357 Engine 14HP Kohler (CV12.5T PS-1413) X 1A 48190 Engine 12.5HP Kawasaki (FB460-ES05) X 1A 48528 Engine 14HP Kawasaki (FC420V) X 48863 5 5A 48122-02 Fibre Washer, thick 6 48851 Coupler, Jackshaft 7 8 хжжх x X KX X x «K X x 48114-01 Grease Fitting, straight 1/4-28 48225 Jackshaft {fits SW32, 36, & 48) x XX M OM x =< x MOM X Washer .219 x .500 x .049 X 15 * Lockwasher, #10 Ext. Tooth X 16 * Hex Nut #10-32 X Engine Deck (fits SW36, & 48) X = y ERREURS OE 21 Hex Head Bolt. 5/16-18, x qe x x X x X 21A * Carriage Head Bolt, 5/16-18 x 1” X X x X X 22 y Washer, 25/64 x 15/16 x 12 ga. X X X X X 23 48197 Pulley, Transmission Input X X X X X X X x x x 24 04063-07 3i 48137 Pulley Blade Drive, (incl. 32-33) x x X X X 32 48141 Taper Hub (for 48127) X X x X 33 * Hex Hd Boit,1/4-20 x 3/4” X x x X X 34 . Lockwasher, Spring, 3/8" X x X x X X x x x 35 | А Hex Nut, 3/8 16 X Tire, 13 x 6.50-6, 2-Ply (fits SW36,48,52,61,&72) X Rim & Bearing Assy (Incl.39) (fits SW36,48,52,61,&72) X X x х x Tire, 13x5. 00-ply (fits SW32 only) X X * Common hardware which should be purchased locally. All bolts Grade 5 plated, all other fasteners zinc plated. ENGINE DECK CONTINUED ON FOLLOWING PAGE 17 ENGINE DECK CONT'D REF. PART DESCRIPTION 13KH 13KA NO. NO. 14КН 14KA 16BV 18KH 18KHE 41 04050-08 Retaining Ring, 1" Ext.-"E” x X X X x 42 48200 Pulley, Wheel Drive X X x X X 43 43088 Spacer, Wheel Pulley x X X X x 44 48209 Brake Drum x x x x x 45 * Нех Hd. Bolt, S/16-18 x L Ve" X x X X X и X X X 52 04041-11 Washer, 13/32 x 1-1/2 x 7 ga. X x X 53 42361 Battery Clamp X X 54 42024 Battery Cover X x X X Plastic Wing Nut, 1/4-20 © Battery Hex Hd. Bolt, 3/8-16 x 1-1/4” Hex Nut, 5/16-18 * Common hardware which should be purchased locally. All bolts Grade 5 plated, all other fasteners zinc plated. 18 PEERLESS 700 PEERLESS TRANSMISSION MODEL 700-026 14 778145 Gear, » Spur (25 teeth) REET PE Sprocket (9 teeth) shaft, Counter Gear, Bevel (42 teeth) Gear, Souris teeth 28 786081 36 792073 37 792089A 40 792077 41 792078 Chain, Roller (No.41 chain,24 links) REF. PART REF. PART NO. NO. DESCRIPTION NO. NO. DESCRIPTION 1 770061 Case, Transmisson 20 778240 Gear, Spur (18 teeth) 2 772083 Cover, Transmission 23 780071 Bearing, Thrust 3 776217 Shaft, Output 8 Brake 27 780105A Bushing, Flanged 4 778123A Rod & Fork Assy. Shift Screw, Flanged Hex Head, thrd fmg, 1/4-20 x 1-1/4” Key Ball, Steel, 5/16" screw, Set 3/8-16 x 3/8" HANDLE ASSEMBLY 20 Beetle 20 . 21 “ 22 . 23 48309 24 48292 31 * 32 44005 33 45092 34 45093 41 45094 42 . 43 . 51 43098 52 48223 53 48224 04050-09 Control Rod, Steering 10 44004 11 04062-02 12 . 13 43032 14 04062-01 Brake Link X X x X Bell Crank Pivot Wild. X X X X Hex Hd. Bolt, 1/4-20 x 1” X X x X Lockwasher, 1/4 Spring x x X X BE eine BR x x x x EX X X X X Hair Pin, Small X x X X Cotter Pin, 3/32 x 3/4” x x x X Swivel Joint X X X X Hair Pin, Large XK x Xx x Lockwasher, 3/8 Spring Hex Head Bolt, 3/8-16 x 2-3/4" Flat Washer, 1/4" Bushing Rubber Pads, (upper) x M OX MK KM KX À XX KK OM x x OX XX XX XX x D XX À XX x X X X X Hex Hd. Bolt, 5/16-18 x 1" X X X X Brake Rod X X X X Brake Lever X X X X X X X X x X Spacer, Jackshaft Pulley X X Flange, Jackshaft Bearing X X Bearing, Jackshaft X x X X HANDLE ASSEMBLY REF. PART 13KH 13KA NO. NO. DESCRIPTION 14KH 14KA 16BV 18KH 18KHE ! ATTENTION LINES IN BOLD LETTERS INDICATE EXTRA IDENTIFICATION IS NEEDED ! 1 46084 Handle Assy. Fits SW 32, 36, 48 x x 1 46179 Handle Assy. Fits SW 52, 61, 72 x X x X x 2 + Part Removed Fom Illustration 3 * Hex Head Bolt, 3/8-16 x 1" x x X X X EX A AA x x OX x «KM OM * Common hardware which should be purchased locally. All bolts grade 5 plated, all other fasteners zinc plate. HANDLE ASSEMBLY CONTINUED ON NEXT PAGE 21 HANDLE ASSEMBLY CONT'D “8059-02 В Clamp, Fuel Hose (| (Kawasaki ‘Only) 48057-02 Fuel Filter x 48058-06 Fuel Hose, 1/4 ID x 17" x X | X x 421241 Shifter Lover Assy. x X X X + Part Removed From Illustration 04043-01 Washer, 17/64 x 7/8 x 1/8 HT x x X X 04001-55 Hex Head Bolt, 1/4-28 x 3/4 Grade 8 x x x X 46090 “Blade < Clutch Lever Assy. (Incl. 104) x x X x 48326 Grip, Lever X x x X * Hex Head Bolt, 3/8-16 x 1-3/4" x X X X | x x X X 42257 02 Neutral Latch. LH x x x + Part Removed From Illustration X x X X 04032-01 Curved Spring Washer x X X X X X ори Ргезепсе Напа Grip LH. ; & Rod (For 2 ") x X X Switch Interlock (gold colored) X X X X Hex Nut, 9/16-18 spring steel X X X X 2, Grip Return X X X Wire Harness, Briggs Vanguard adapter | REF. PART у 13KH 13KA NO. NO. DESCRIPTION _14KH14KA 16BV 18KH 18KHE ! ATTENTION LINES IN BOLD LETTERS INDICATE EXTRA IDENTIFICATION IS NEEDED ! 59 . Carriage Bolt, 1/4-20 x 1” X =: X X X X 60 48205 Rubber Pad (lower) сх X . x X x 61 48609 Key Switch x x x X X x X * Common hardware which should be purchased locally. All boits grade 5 plated, all other fasteners zinc plate. 22 ELECTRIC START ELECTRICAL SYSTEM STARTER MAGNETO ( ) | ALTERNATOR (_) ® KOHLER ENGINE 3 | E O SOLENOID AO CN FUSE 2a | \ | Ги A 7 12 a FUSE 2 Г HOLDER Sa \ 1 IGNITION 0) 10 SWITCH 9 \ Lo BATTERY N; Oo N 11 Ref. Part SW No. Number Description 18KHE 1 48017 Key Switch X 2 48297 Fuse Holder X 2A 48298 Fuse 20 Amps x 3 48016 Solenoid X 4 x Switch, 11 48231 Switch, Neutral Interlock N.O. x 12 48029-03 Battery Cable - 13.75" Red x 23 ENGINE WIRING DIAGRAM FOR MANUAL START OO 3... Ref. Part No. Number Description 1 48609 Switch, Ignition 2 48231 Switch, Neutrall Interlock, Normally Open 3 48305 Switch, Cutter Drive Interlock, Normally Closed 4 48021 Switch, Operator Presence, Normally Closed 5 48610 Wire Harness 24 REPLACEMENT DECALS À | AVOID INJURY FROM BURNS SHUT OFF ENGINE BEFORE REMOVING FUEL TANK CAP} (Located On Culver Dock Cowen - Top Surface) N AVOID ENGINE DAMAGE CLOSE FUEL VALVE WHEN ENGINE IS NOT RUNNING 48281 Decal - Operator Warning Fuel Fil (Located On Top of Fuel Tank) 48849 Decal - Instrument Panel (Located On Shifter Plate - Above Shift Lever) HEAVY DUTY COMMERCIAL 48072 . Decal-Heavy Duty Commercial (Located on Cutter Deck Cover - Front Wall) 72 48327 61 48320 52 48319 48 48318 36 48316 À WARNING INSTALL BELT COVERS BEFORE OPERATING MACHINE READ OPERATOR'S MANUAL 48712 Decal - Caution Belt Cover (Located on Cutter Deck Top Surface) A WARNING ROTATING BLADES AND BELTS + KEEP HANDS, FEET & CLOTHING CLEAR + KEEP ALL GUARDS IN PLACE « SHUT OFF ENGINE & DISENGAGE BLADE CLUTCH BEFORE SERVICING + CLEAN AREA OF DEBRIS BEFORE MOWING « USE CAUTION IN DIRECTING DISCHARGE « KEEP BYSTANDERS, CHILDREN & PETS AWAY + READ INSTRUCTION MANUAL BEFORE OPERATING 48073 Decal - Danger, Rotating Blades (Located On Cutter Deck Cover Near Discharge Chute) A DANGER SPINNING BLADE KEEP CLEAR CONTACT CAN INJURE 48071 Decal - O.P.E.l. Safety (Located on Cutter Deck Near Discharge Chute) 25 A WARNING LIMITED WARRANTY-COMMERCIAL EQUIPMENT Any part of the Scag commercial mower manufactured by Scag and found, in:the reasonable judgment of Scag, to be defective in materials or workmanship, will be repaired or replaced by án Authorized Scag Service Dealer without charge for parts and labor.This warranty is limited to the original purchaser and is not transferable. Proof of purchase will be required by the dealer to substantiate any warranty claims. All warranty work must be performed by an Authorized Scag Service Dealer. This warranty is limited to the following specified periods from the date of the original retail purchase for defects in materials or workmanship: * Frame, deck and structural components including oil reservoirs - 1 year * Wear items including drive belts, blades, hoses and tires are warranted for 90 days * Engines and electric starters are covered by the manufacturer's warranty period. * Drive system components are covered by the manufacturer's warranty period. (Excluding fittings, hoses, cooling system, oil reservoir, drive belts.) Drive systems are warranted by Scag Power Equipment in conjunction with the component manufacturer. * Batteries are covered for 1 year. | * Any Scag product used for rental purposes is covered for 90 days. The Scag mower, including any defective part must be returned to an Authorized Scag Service Dealer within the warranty period. The expense of delivering the mower to the dealer for warranty work and the expense of returning it to the owner after repair will be paid for by the owner. Scag's responsibility is limited to making the required repairs and no claim of breach of warranty shall be cause for cancellation or rescission of the contract of sale of any Scag mower. This warranty does not cover any mower that has been subject to misuse, neglect, negligence, or accident, or that has been operated in any way contrary to the operating instructions as specified in the Technical Manual. The warranty does not apply to any damage to the mower that is the result of improper maintenance, or to any mower or parts that have not been assembled or installed as specified in the Technical Manual. The warranty does not cover any mower that has been altered or modified changing performance or durability. In addition, the warranty does not extend to repairs made necessary by normal wear, or by the use of parts or accessories which, in the reasonable judgment of Scag, are either incompatible with the Scag mower or adversely affect its operation, performance or durability. Scag Power Equipment reserves the right to change or improve the design of any mower without assuming any obliga- tion to modify any mower previously manufactured. All other implied warranties are limited in duration to the one (1) year warranty period or ninety (90) days for mowers used for rental purpose. Accordingly, any such implied warranties including merchantability, fitness for a particular purpose, or otherwise, are disclaimed in their entirety after the expiration of the appropriate one year or ninety day warranty period. Scag's obligation under this warranty is strictly and exclusively limited to the repair or replacement of defective parts and Scag does not assume or authorize anyone to assume for them any other obligation. Some states do not allow limitations on how long an implied warranty lasts, so the above limitation may not apply to you. Scag assumes no responsibility for incidental, consequential or other damages including, but not limited to, expense for gasoline, expense of delivering the mower to an Authorized Scag Service Dealer and expense of returning it to the owner, mechanic's travel time, telephone or telegram charges, rental of a like product during the time warranty repairs are being performed, travel, loss or damage to personal property, loss of revenue, loss of use of the mower, loss of time or incon- venience. Some states do not allow the exclusion or limitation of incidental or consequential damages. So the above limitation or exclusion may not apply to you. This warranty gives you specific legal rights, and you may also have other rights which vary from state to state. 26 PLEASE BE CAREFUL . Keep all shields in place, especially grass discharge. . Stop machine and remove spark plug wire to adjust or service. When mechanism becomes clogged, stop engine before cleaning. Keep hands, feet and clothing away from power-drive parts. . Keep off implement unless seat or platform is provided. . Keep others off. O O1 R U ND — ER ER OURS RARE CRE AE FAILURE TO FOLLOW CAUTIOUS OPERATING PRACTICES MAY RESULT IN SERIOUS BODILY INJURY. WE WANT YOU TO CONTINUE TO ENJOY AND PROFIT BY USING OUR PRODUCTS. (a —) OWNER REFERENCE MODEL NUMBER SERIAL NUMBER ENGINE MODEL SERIAL NUMBER | >
advertisement
Related manuals
advertisement