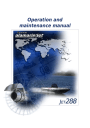
advertisement

Operation and maintenance manual
Table of contents
Operation and maintenance manual
Table of contents
3.3.1. The positions of the reversing deflector control lever ............. 7
3.3.2. Using the reversing deflector ................................................. 8
3.4. Driving under difficult conditions ..................................................... 9
4.2.1. Changing the anodes ............................................................ 11
4.2.2. Touch-up painting and antifouling ........................................ 13
4.3.1. Lubricating the front bearing ............................................... 15
4.3.2. Lubrication of the rear end bearing ..................................... 16
4.6. Hydraulic reversing deflector control system ................................. 19
4.8.1. Checking the impeller ........................................................... 24
4.8.2. Removing the impeller .......................................................... 24
4.8.3. Installing the impeller ........................................................... 26
Appendix 2. After sales questionnaire ........................................................... 38
Appendix 3. Grease recommendations ........................................................... 41
Appendix 4. Oil recommendations ................................................................. 42
KHO/288/EN/1.3.0.
iii
Introduction
Operation and maintenance manual
1. Introduction
Congratulations on puchasing a new Alamarin-Jet Jet-288 water jet propulsion unit!
This manual contains important information on the operation, use and maintenance of the unit. Read these instructions carefully before implementing the unit. This way the unit is safe to operate.
Keep this manual throughout the product's life cycle. If you lose the instructions, contact your nearest distributor for a new one. If you sell the unit, make sure to deliver this manual to the new owner.
Contact your nearest distributor if you have any queries regarding the operation or maintenance of the unit.
© Alamarin-Jet Oy
Tuomisentie 16
FI-62300 Härmä, Finland
Telephone: +358 10 7745 260
Fax: +358 10 7745 269
Internet: www.alamarinjet.com
All rights reserved.
The information in this manual may not be copied, published or reproduced in any way whatsoever or exploited for commercial purposes without explicit written permission from Alamarin-Jet Oy.
The information in this manual is subject to change without notice. Alamarin-
Jet Oy reserves the right to modify the contents without notice.
1.1. Safety precautions
Read this instruction carefully before you operate the boat equipped with the jet the engine or carry out any maintenance procedures. Also read the boat's manual. Always follow the instructions and the safety precautions below.
• Only a person with with adequate training is allowed to carry out the demanding maintenance procedures described in this manual.
• The person carrying out the procedures must always be wearing appropriate protective equipment.
• The work premises must be sufficiently large, safe and well-lit.
• The tools used must be clean and appropriate for the purpose.
1.2. Symbols
Please refer to table 1 for a description of the symbols used in this manual.
Table 1. The symbols used in the manual
Icon Description
DANGER
Negligence in the performance of a procedure can cause a threat to your life.
KHO/288/EN/1.3.0.
1
2
Introduction
Operation and maintenance manual
Icon Description
WARNING
Negligence in the performance of the procedures can lead to personal injury, breakdown of equipment, or serious malfunction of the equipment.
CAUTION
The procedure involves minor danger or a possibility of minor damage to equipment.
WARRANTY
The warranty is voided if the procedure is carried out incorrectly.
NOTE
Important notice or fact.
TIP
Additional information that facilitates the performance of work or a procedure.
MAINTENANCE ON LAND
The boat must be lifted out of the water for maintenance.
MAINTENANCE IN WATER
The maintenance procedure can be carried out in water.
CARRIED OUT BY ONE PERSON
One person can carry out the procedure.
CARRIED OUT BY TWO PERSONS
Two persons must carry out the procedure.
INDICATOR ARROW
ARROW DESCRIBING MOTION
Please note that this instruction uses the terms "jet" and "jet propulsion unit".
They mainly refer to the same thing.
KHO/288/EN/1.3.0.
The jet propulsion unit
Operation and maintenance manual
2. The jet propulsion unit
The Alamarin-Jet water jet propulsion unit (jet) is a single stage axial flow pump, which produces a high volume flow rate and thrust with high efficiency.
The operation of the unit is based on increasing the water flow rate in the nozzle. The change in the flow rate creates a reactive force in the direction of the flow, which thrusts the boat forward. By changing the direction of the jet flow, the boat can be steered in the desired direction.
The jet gets its propulsion power from a petrol or diesel engine. The most common way to transmit the power is through a gearbox, but a direct drive installation is also possible and functional. The greatest benefits of a gearbox are a real neutral gear and an intake duct backflush. In bobtail installation, it is commendable to use a flywheel adapter provided by the engine manufacturer. This will protect the engine from mechanical damage and corrosion, for example.
2.1. Structure
The jet consists of four main parts (Figure 1). These are specified in the table
Figure 1. Main parts of the jet
Table 2. Purpose of the main parts of the jet
Part
Intake duct (A)
Impeller (B)
Steering device
(C)
Purpose
Leads the water from outside the boat to the intake side of the impeller. Keeps the loss of power as small as possible and distributes velocity evenly.
Increases the water's flow rate. The impeller is rotated by the driving motor. The nozzle converts the pressure energy produced by the impeller into motion energy.
Changes the direction of the jet flow coming out of the nozzle, which creates the force needed for turning.
KHO/288/EN/1.3.0.
3
The jet propulsion unit
Operation and maintenance manual
Part
Controlling device
(D)
Purpose
Causes the boat to reverse and stop. Lowering the reversing deflector causes the boat to reverse. The direction of the jet flow changes obliquely forward under the boat, which is when the thrust is directed forward and down.
2.2. Serial number
Every jet has a unique serial number. The serial number has been marked on
the type label, which is on the side of the bearing oil reservoir (Figure 2). The
serial number is also stamped on the body of the jet above the bearing housing
Figure 2. Serial number on the oil reservoir
4
Figure 3. Serial number on the body
KHO/288/EN/1.3.0.
Operation
Operation and maintenance manual
3. Operation
If you have never driven a jet boat before, familiarize yourself with the separate guide “Steering and controlling jet boats” before driving the boat for the first time. You can find the guide on the CD attached to the back cover of the paper version of the Operation and maintenance manual.
3.1. Starting
Before you start the engine equipped with the jet, make sure that
• the reversing deflector control lever is in centre position
• the gear is disengaged. (If the engine has no gearbox, it must be in idle position before you start it.)
The positions of the reversing deflector control lever are described in section
3.3.
Controlling
Operation for the first time
CAUTION!
Before you set the boat afloat for the first time, make sure that the jet has been installed according to the installation instructions. If you have not personally installed the jet, check with the boat's retailer that the jet has been installed correctly.
Correct installation helps to prevent the emergence of unexpected fault situations which can lead to damages.
The jet does not require separate running in. However, follow the engine manufacturer's instructions about running in during the first few drives.
Ensure the functioning of the jet carefully, at low speeds.
DANGER!
The jet can be dangerous when running.
Do not go near the rotating parts.
Do not open the jet's inspection hatch when the engine is running.
When running, the jet propulsion unit sprays water backwards at a great pressure. Make sure that there is no one in the water behind the boat!
The intake in the bottom of the boat causes suction power at the back of the boat when the jet propulsion unit is running.
Make sure that there is no one in the water affected by the intake.
When you start the engine for the first time, you may hear a jingling sound for a few minutes. This is normal and the sound will end when the impeller gap sets in place. The noise from the oil pump may be loud at first but is disappears as the system fills up with oil.
KHO/288/EN/1.3.0.
5
Operation
Operation and maintenance manual
In the first few drives the reversing deflector's hydraulic control system needs more oil than usually because the hoses and the cooler are empty. Check the oil level and add more if necessary. Follow in the instruction from section
NOTE!
An oil leak may pollute the environment.
Observe the oil level and make sure that oil does not leak out.
3.2. Steering
WARRANTY!
In this section, controlling the jet boat is described in a way that it is done through a system that has been installed as intented by the manufacturer.
Alamarin-Jet Oy is not liable for damages which derive from incorrect installation of the system.
Steering denotes exclusively moving the steering nozzle. Steering means changing the boat's bow angle.
The boat is steered by turning the steering wheel. The connection from the
wheel to the steering lever can be either mechanical or hydraulic (Figure 4).
The lever moves the nozzle through the shaft and the joint.
6
Figure 4. Steering lever
Steering is possible only when the power of the jet flow is sufficient. This is why the engine must run on sufficiently high revs when steering. A suitable number of revolutions depends on the engine. Usually it is between 1,000 and
1,500 rpm.
In sharp curves, turning the nozzle causes the boat to slow down. This is normal and increases safety.
The turning of the nozzle from one extreme position to the other takes approximately 2 turns of the wheel.
KHO/288/EN/1.3.0.
Operation
Operation and maintenance manual
3.3. Controlling
Controlling denotes exclusively moving the reversing deflector. Controlling means changing the boat's driving direction (forward - astern). The reversing deflector is moved with the lever which is usually next to the throttle lever.
The lever controls the hydraulic system mechanically (the cable operates the cylinder valve)
The reversing deflector can be lowered in front of the jet flow using hydraulics
causing the boat to reverse (Figure 5).
Figure 5. Lowering the reversing deflector
3.3.1. The positions of the reversing deflector control lever
The reversing deflector control lever can be in one of three positions: forward, rear or centre.
Forward position
When the reversing deflector control lever is in forward position, the deflector
is not blocking the jet flow and the boat moves forward (Figure 6).
Figure 6. Ahead
A Throttle lever
B Control lever
Rear position
When the reversing deflector control lever is in rear position, the deflector is
blocking the jet flow and the boat moves astern (Figure 7).
KHO/288/EN/1.3.0.
7
Operation
Operation and maintenance manual
Figure 7. Astern
A Throttle lever
B Control lever
Centre position
The centre position of the control lever corresponds to the ”idle” position of the gearbox: even though the drive is on, the boat does not move. The centre position is not absolute, it depends on the power of the jet flow. You can find the centre position by testing during the first driving hours.
3.3.2. Using the reversing deflector
When moving at low speeds, the reversing deflector is used to control the boat's speed. Because the engine is being run at 1,000–1,500 rpm to enhance steering, the boat may travel faster than desired. In this case the deflector is lowered in front of the jet flow to reduce the thrust directed towards the driving direction. This does not affect the steerability which remains good.
At high speeds, the deflector is not used to reduce speed. Instead, speed is controlled with engine revolutions.
It is possible to turn the boat in place when the deflector is in centre position.
When the nozzle is turned to the desired direction, the boat rotates about its central axis.
When reversing, steering is inversed in comparison to driving forward. If you want to reverse the boat to the left, you must turn the wheel to the right.
A good rule to remember is that the boat's bow always turns in the same direction as the wheel when reversing. When fast turns are needed, the engine revolutions are not reduced, but instead the turn is done through combined motion of the nozzle and the deflector.
Emergency stop
When the boat is run forwards at great speed, it is possible to stop the boat by only using the reversing deflector. When the reversing deflector is lowered quickly, the boat stops at a very short distance. The emergency stop is to be used in emergencies only.
WARNING!
Alert the passengers and tell them to hold on to something if you are planning an emergency stop. Without preparation, a passenger may be thrown overboard.
8 KHO/288/EN/1.3.0.
Operation
Operation and maintenance manual
3.4. Driving under difficult conditions
Shallow water
The jet boat can be used in very shallow water. However, note that especially
on high revolutions the suction power of the intake is high (Figure 8).
Figure 8. Suction power of the intake
Loose objects may get sucked into the intake screen and small objects wash through the jet. Stones may cause damage to the jet and its parts. In sandy conditions the impeller inevitably wears. A worn impeller requires
Reed fields
At planing speeds, a jet boat usually crosses reed fields without difficulty. In difficult conditions however, clogging may be possible.
A clogged jet must be cleaned immediately (section 5.3.
3.5. Dry running
The jet may be run by the engine even out of the water, because the bearings are greased an oiled. This is a significant benefit in comparison to water lubricated bearings, that do not sustain dry running well.
During dry runs, a temporary water inlet must be arranged for the motor sea water cycle to cool the engine.
KHO/288/EN/1.3.0.
9
Operation
Operation and maintenance manual
10 KHO/288/EN/1.3.0.
Maintenance
Operation and maintenance manual
4. Maintenance
The jet is designed and manufactured to be as simple as possible. This is why the need for maintenance is low and maintenance can be carried out on shore.
However, maintenance must be performed regularly and whenever the need arises.
Alamarin-Jet can provide you with a toolkit, available through separate order, for maintenance purposes. The toolkit includes the tools needed to perform most maintenance and repair procedures on the jet. The tools included in the
toolkit are specified in Table 3.
Table 3. Toolkit
Tool
Wrench
Allen wrench
Knife
Universal pliers
3
1
Pcs Size
4 10 (0.4"), 13 (0.5"), 17 (0.7") and
19 (0.7") mm
1
-
-
5 (0.19"), 6 (0.24") and 8 (0.3") mm
4.1. Washing
Washing the jet regularly removes possible salt accruals and impurities, thus reducing the risk of corrosion.
Every time you lift the jet out of the water, it is a good idea to rinse it with fresh water.
4.2. Corrosion protection
The jet has been protected against corrosion in the manufacturing and installation phases. However, the protection requires regular maintenance.
4.2.1. Changing the anodes
The main raw materials used for manufacturing the jet parts are aluminium, acid-proof steel and plastic. Materials that have different electrochemical properties can form a galvanic couple when they are submerged in electrolytic fluid (salt water). A galvanic couple forms an electrical circuit because the materials have different inherent voltages. This in turn leads to electron movement and corrosion of the weaker material.
Cathodic protection is used to prevent the propagation of galvanic corrosion.
Cathodic protection means introducing a third material with weaker electrochemical properties into the same circuit.
The jet is protected from galvanic corrosion with passive cathodic protection, i.e. with anodes. Every critical aluminium casting has its own anode. Some acid-resistant parts are also equipped with anodes. The anodes can be either
aluminium or zinc. The locations of the anodes are shown in the Figure 9.
KHO/288/EN/1.3.0.
11
Maintenance
Operation and maintenance manual
Figure 9. Anodes
A End of the steering shaft
B Stator (2 pcs, above and below)
C Reversing deflector (2 pcs, right and left)
D Reversing deflector joint (2 pcs, right and left)
E Body (2 pcs, right and left)
F Frame (4 pcs, two inside and two outside)
G Inside of the stator (2 pcs, right and left)
H Body (2 pcs, right and left)
I Hydraulic cylinder
The functioning of the anodes is absolutely crucial to prevent corrosion. The anodes must be replaced when they have worn down to half their original size.
Replacing the anodes:
Most of the anodes are attached with simple screws. Below you will find instructions for changing the anodes that are attached differently.
A End of the steering shaft
12
Figure 10. End of the steering shaft
The end of the steering shaft has a threaded stud, to which the anode (Figure
10, point A) is attached with a nut (Figure 10, point B). Rotating the anode also
rotates and tightens the nut.
KHO/288/EN/1.3.0.
Maintenance
Operation and maintenance manual
F Frame
Figure 11. Frame anodes
The sides of the intake duct house holes for attaching anodes with the help of a mounting plate. To remove the anodes, first open the mounting plate screws
(Figure 11, point A), after which you can remove the mounting plate along
with the anode. After this, open the screw in the centre of the mounting plate
(Figure 11, point B). Now you can attach a new anode to the mounting plate.
The mounting plate should be fastened to the frame using a sealing compound
(such as Sikaflex 221).
G Inside of the stator
Figure 12. Stator anodes
The inside of the stator is protected by anodes housed under plastic plugs located on both sides of the stator. To remove the anode, first open the
arrester screw (Figure 12, point A) and unscrew the plug. Now you can
replace the anode located inside the plug. Leave the screw that holds the
anode in place (Figure 12, point B) loose and fasten the plug into place using
a sealing compound (such as Sikaflex 221). Only then attach the other end of the arrester to the stator. After this, tighten the screw that holds the anode in place.
4.2.2. Touch-up painting and antifouling
KHO/288/EN/1.3.0.
13
Maintenance
Operation and maintenance manual
The aluminium castings have been protected with paint. Painting efficiently prevents the propagation of various forms of corrosion, e.g. pit corrosion.
Bare aluminium, on the other hand, is liable to corrosion in difficult conditions.
This is why it is important to carry out touch-up painting if paint comes loose and aluminium is exposed. Touch-up painting can be done in various ways.
What is important is that the paints used are suitable for aluminium and that the paint manufacturer's instructions are followed during painting.
If the boat is going to be used in waterways where the growth and sticking of organisms around the boat’s bottom and the propulsion unit is heavy, the propulsion unit can be painted with antifouling paint after installation.
Generally speaking, antifouling paints are based on various soluble substances, such as copper. Because the propulsion unit is made mainly of aluminium, copper forms a highly unfavourable galvanic couple with the propulsion unit. In other words, the aluminium starts to corrode because it functions as an anode.
WARNING!
Painting the propulsion unit with antifouling paint that contains copper will result in heavy corrosion and destruction of the propulsion unit. Do not use any other antifouling paints for painting the propulsion unit except those intended for aluminium surfaces.
A boat bottom made of reinforced plastic can be painted using antifouling paint that contains copper. In this case, leave a 50 mm (2") unpainted area around the propulsion unit in the stern and on the bottom of the boat (Figure
14
Figure 13. Antifouling
A Unpainted area
B Painted area
CAUTION!
Zinc anodes and their fastening screws must not be painted.
KHO/288/EN/1.3.0.
Maintenance
Operation and maintenance manual
4.3. Bearing
The jet's bearing is very simple. There are bearings at both ends of the direct
shaft. The structure of the front bearing (Figure 14, point A) is receptive to
axial pressure. It also carries the radial loads caused by the weight of the shaft and the parts attached to it. At the rear end, a grease lubricated needle
bearing supports the shaft (Figure 14, point B). A water-lubricated bushing
can also be used.
Figure 14. Bearing
4.3.1. Lubricating the front bearing
The front bearing is oil-lubricated and the housing is secured with a mechanical sealing. When the shaft rotates, the oil circulates through the reservoir and impurities gather to the bottom of the reservoir on the drain
plug magnet (Figure 15, point A).
Figure 15. Drain plug magnet and oil return hose
A Drain plug magnet
B Oil reservoir return hose connection
KHO/288/EN/1.3.0.
15
Maintenance
Operation and maintenance manual
Oil change
WARNING!
Use protective gloves while handling oil.
The front bearing oil must be changed after the first 20 hours of driving and then after every 500 hours or once every driving season.
Before you start changing the oil, make sure you have a container for draining the used oil.
Changing the oil:
1. Open the reservoir cap and stir the oil inside.
Impurities are easier to remove from the reservoir when they are mixed in with the oil.
2. Open the drain plug (Figure 15, point A) and drain the oil into the
container.
3. Clean the plug magnet, close the drain plug and fill the reservoir with
new oil. Oil recommendations can be found in the appendix 4.
This prevents air from drifting into the system and ensures that lubrication functions well from the start.
4. Remove the reservoir return hose (Figure 15, point B) and keep it below
the reservoir.
This way the oil drains out from the bearing housing and the hoses and the system fills up with new oil. The time it takes to drain the oil depends on how far the reservoir is from the bearing housing. The colour of the oil indicates whether all the old oil has drained out.
5. Attach the oil return hose to the reservoir once the system is filled with new oil.
6. Check the oil level from the dipstick on the reservoir cap (Figure 25, point
B) .
When the shaft starts to rotate, the system generates pressure into the return line, causing oil to start circulating in the system.
4.3.2. Lubrication of the rear end bearing
16
The rear end bearing is lubricated from the engine room with petroleum jelly.
The lubrication channel runs from the engine room to the rear end bearing housing.
An automatic lubrication unit is delivered with the propulsion unit to make sure the rear end bearing is lubricated regularly. It also prevents water from leaking into the bearing housing.
KHO/288/EN/1.3.0.
Maintenance
Operation and maintenance manual
Figure 16. Automatic lubrication unit
A
B
Oil pressure hose from the hydraulic cylinder
Adjusting the feed volume
D
E
Grease nipple for refill
C Scale F
Grease hose to the lubrication channel
Piston
Feeding
You can adjust the feed as follows:
• If the automatic lubrication unit is feeding too much grease (the reservoir gets empty too soon), decrease the pressure by loosening the adjusting
• If the automatic lubrication unit is not feeding grease to the rear bearing
(cold conditions, thick grease type), increase the pressure by tightening the
adjusting screw (Figure 17, point C).
Figure 17. Lubricating the Rear Bearing
The amount of grease fed to the rear bearing must be 0.1 l/100 h (6 cu in/100 h). The grease volume in the unit is 0.3 l (18 cu in). With these settings, the reservoir will empty in 300 hours. If you notice that the reservoir empties slower or faster than this, adjust the pressure to the desired direction.
KHO/288/EN/1.3.0.
17
Maintenance
Operation and maintenance manual
You can fill the reservoir by pushing grease into it with a grease gun through
the nipple (Figure 16, point D). This will cause the piston to protrude out of
the reservoir.
The properties of the grease to use are described in Appendix 3.
NOTE!
Any excess grease exits the bearing housing into the water.
Only use environmentally friendly grease for lubricating the bearing.
If there is no automatic lubrication unit installed into the system, there is a nipple at the end of the lubrication hose, through which grease can be pumped to the rear bearing. 0.5 dl (6 cu in) of grease should be added every 50 hrs.
4.4. Control system
The joints and shaft bushings that belong to the control systems are essentially maintenance-free, but lubrication prolongs their operating life. Locations where waterproof petroleum jelly should be added during maintenance are
marked in Figures 18–21. When the plastic bearings of the joints wear and
gaps are created, they must be replaced.
Figure 18. Steering shaft bushing
(nipple greasing or automatic lubrication)
Figure 19. Steering nozzle joints
18
Figure 20. Steering nozzle rear end
Figure 21. Reversing deflector joints
KHO/288/EN/1.3.0.
Maintenance
Operation and maintenance manual
4.5. Seals
Figure 22. Seals
If the inspection hatch seal leaks, it causes ventilation (see chapter 5.2.
, page 33). Leaking sealings of the steering shaft bushings cause
water to leak in the bilge.
CAUTION!
If water gathers in the bilge, the cause for this must be determined immediately. Any possible leaks must be repaired immediately. Water can damage e.g. the starter motor.
4.6. Hydraulic reversing deflector control system
For controlling the reversing deflector, the jet has a hydraulic cylinder which
is operated mechanically with a cable. The cable (Figure 23, point C) operates
the valve regulator (point A). The cylinder gets its power from the pump which has been integrated in the propulsion unit.
KHO/288/EN/1.3.0.
19
Maintenance
Operation and maintenance manual
20
Figure 23. Hydraulic cylinder
In a stock delivery, the system does not include a control lever or a cable, so their type varies depending on the boat manufacturer. However, the different types of systems have the following things in common:
• The operation of the deflector is always separate from the throttle and the gearbox.
• The stroke length of the cylinder is always the same.
• The incoming direction of the cable can be chosen freely.
The oil circulating in the system must be cooled down in order to prevent excessive heating. This is done with a separate heat exchanger or a cooler in the engine.
WARRANTY!
If the oil in the system is not cooled, the manufacturer is not responsible for possible damages which derive directly or indirectly from the oil overheating.
If the valve regulator is removed, the cylinder must be readjusted. The adjustment instructions can be found in the Repair manual.
Figure 24 shows a system in which the cooling water comes from the jet
(Chapter 4.7.
Raw water cooling
, page 22). The system can consist of
different looking components depending on the boat manufacturer. What is essential is the correct order of the components. Notice especially the cooler's place after the filter. A system equipped with a separate raw water intake pump has the same main components.
KHO/288/EN/1.3.0.
Maintenance
Operation and maintenance manual
Figure 24. Cooling system
A Cylinder
B Oil pump
C Oil reservoir
D Raw water filter
E Cooler
F Line to the engine cooler
The system must have the right amount of oil. If you need to add oil to the system, add it in the oil reservoir through the cap (Figure 25, point C). There is a dipstick on the reservoir cap with markings for maximum and minimum oil levels (Figure 25).
KHO/288/EN/1.3.0.
21
Maintenance
Operation and maintenance manual
Figure 25. Checking the oil level
A
B
C
Maximum level
Minimum level
Cap
Note that you must change the oil once every driving season (section 4.3.1.
, page 15). The type of oil used is described in
You can also change the filter through the oil reservoir cap. You must change the filter every 500 hours.
4.7. Raw water cooling
The jet comes complete with the possibility to connect the engine cooling
water (Figure 26). The engine does not need a separate water pump. In case
the cooling water is taken with a separate pump, the jet's raw water line is stoppered.
At the beginning of the line, there must be a tap with which the line can be shut temporarily, such as during cleaning of the filter or other maintenance.
The raw water line requires no other separate maintenance procedures.
22 KHO/288/EN/1.3.0.
Maintenance
Operation and maintenance manual
Figure 26. Raw water cooling
A Raw water connector
B Tap
C Filter
D Input for the engine
4.8. Impeller
Depending on driving conditions, the impeller will wear down, causing a gap to develop between the duct wall and the tip of the impeller blade. The gap should be as small as possible to achieve maximum efficiency. (Factory installation gap is 0.2 mm (approx. 0.008")). When the gap expands too much, the jet's performance decreases.
The impeller usually wears on the outer edge of the blades. The impeller operates in a cone-shaped space and its position can be adjusted in the direction of the shaft in accordance with the blade wear.
The longitudinal position of the impeller in the duct reveals its power demand.
The deeper the impeller sits, the less power it takes from the engine, because the diameter of the impeller is smaller. The pitch and the length and number of blades naturally also affect the power demand.
By adjusting the impeller, its operating life can be prolonged considerably. The adjustment of the impeller should be done whenever it is necessary, but checks must be carried out at least once a year. The impeller is adjusted by removing the impeller and then reinstalling it.
KHO/288/EN/1.3.0.
23
Maintenance
Operation and maintenance manual
4.8.1. Checking the impeller
The condition of the front edge of the impeller blades is important. A damaged front edge causes cavitation.
WARNING!
The impeller blade edges can be sharp and cut your hands.
Protect your hands with protective gloves before you remove the impeller.
The front edge can be repaired by carefully hammering the marks caused by bigger stones and grinding them smooth. Sharpen the front edge to a thickness of approximately 1 mm (approx. 0.04") and round it off so that is not sharp enough to cut.
You can also return the impeller to the factory for checking and repairing.
If you suspect that there is a malfunction in the impeller, do as follows:
1. Shut down the engine and open the inspection hatch.
2. Check that there is no blockage in the intake duct.
3. Check the impeller visually. Notice especially the gap between the outer edge of the blade and the duct wall.
If there is no apparent fault, do as follows:
1. Lift the boat out of the water.
2. Remove the impeller (Chapter 4.8.2.
3. Check the impeller more closely.
Contact the importer or the manufacturer if necessary and ask for additional instructions.
4.8.2. Removing the impeller
24
Before the impeller can be removed, the reversing deflector, the steering nozzle and the stator must be removed.
Removing the impeller:
1. Open the screws indicated by arrows in Figure 27.
WARNING!
Make sure that the reversing deflector is not accidentally lowered. This may result in serious injury!
Support the reversing deflector in the upper position.
KHO/288/EN/1.3.0.
Maintenance
Operation and maintenance manual
Figure 27. Reversing deflector screws
2. Open the six fastening screws of the stator (Figure 28).
There are six screws.
Figure 28. Stator fastening screws
3. Remove the stator and the steering nozzle as a complete unit (Figure 29).
KHO/288/EN/1.3.0.
25
Maintenance
Operation and maintenance manual
Figure 29. Removing the stator and the steering nozzle
4. Loosen the impeller fastening screws (Figure 30, point A).
Figure 30. Impeller fastening screws
5. Remove one screw completely and screw it into the threaded hole in the
plastic mounting cone (Figure 30, point B).
When you tighten the screw in the threaded hole, the fastening cone is released and the impeller can be pulled off the shaft. If the adapter is very tight, use multiple screws to release it.
4.8.3. Installing the impeller
26
New and repaired impellers are fitted in the same way.
Installing the impeller:
1. Attach the plastic fastening cone to the impeller hub and tighten the screws so that they are fingertight.
KHO/288/EN/1.3.0.
Maintenance
Operation and maintenance manual
Note that the place of the wedge groove is marked on the impeller hub
Figure 31. Position of the wedge groove
The thrust caused by the impeller is transmitted through the adjuster
sleeve to the shaft (Figure 32). The sleeve consists of rings of different
thickness. The length of the sleeve can be adjusted in 0.5 mm (approx.
0.02") increments by changing the number of the rings. This way the
impeller gap on the outer race (Figure 30, point C) becomes fit.
Figure 32. Adjuster sleeve
2. Find the right adjuster sleeve length by testing.
2.1.
2.2.
Place the impeller into the duct.
At this point the screws of the plastic mounting cone must be fingertight.
Measure the gap on the impeller outer race.
An ideal gap is between 0.4 and 0.6 mm (approx. 0.016" and
0.024").
When you measure the gap, note that the shaft is not centered when the stator is removed, but the shaft's rear end hangs low and the whole gap is visible in the upper part of the duct.
KHO/288/EN/1.3.0.
27
Maintenance
Operation and maintenance manual
CAUTION!
If the gap is too big, it will cause loss of power and reduce performance.
3. When you find the right adjuster sleeve length, place the wedge in the
shaft's groove (Figure 33) and push the impeller on the shaft against the
adjuster sleeve.
Figure 33. Wedge groove
4. Tighten the impeller fastening screws evenly in a crosswise sequence.
The tightening torque is 20 Nm (approx. 15 lb-ft.).
While tightening, the impeller moves back a bit and a small gap develops on the front. The gap will disappear when the impeller is being loaded.
5. Install the stator and the steering nozzle in place in reverse order to that
The torque to be used is the tightening torque for M10 bolts.
4.9. Intermediate shaft
28
The intermediate shaft which is connected between the jet and the engine usually depends on the boat manufacturer. Contact the shaft's manufacturer for information on the maintenance of the intermediate shaft.
Regardless of the manufacturer, the alignment of the intermediate shaft must be kept accurate. The alignment must be checked at least once every driving season (year).
KHO/288/EN/1.3.0.
Maintenance
Operation and maintenance manual
WARNING!
The intermediate shaft must absolutely be of high enough quality and properly balanced. An intermediate shaft that has been installed or balanced incorrectly can cause excessive damage to the propulsion unit.
WARRANTY!
If an intermediate shaft that has been installed or balanced incorrectly causes damage, this will not be covered by the warranty.
KHO/288/EN/1.3.0.
29
Maintenance
Operation and maintenance manual
30 KHO/288/EN/1.3.0.
Problem situations
Operation and maintenance manual
5. Problem situations
5.1. Cavitation
The most common malfunction in water jet propulsion units manifests as cavitation. Cavitation is a phenomenon in which the water pressure decreases locally in such an extent that water vaporizes on the surface of the impeller blade, creating steam bubbles. The bubbles move on the surface of the blade and when they reach a higher pressure area they collapse.
Signs of cavitation are engine overdrive and stopping of thrust, and it can often be heard as a thundering sound.
Cavitation incurs considerable reduction in capacity and damages the impeller.
Any factor that hinders the flow of water in the jet increases the chance of cavitation. Usually the cause is the reduction of pressure in the whole intake duct caused by a blockage.
If cavitation is apparent or the boat runs slowly even though the engine runs on high revolutions, find out the cause.
Checking the causes for cavitation:
1. Open the inspection hatch (Figure 34).
Figure 34. Opened inspection hatch
2. Check the grass rake (Figure 35).
Make sure that grass, reed, plastic, stone or other extraneous object is not clogging the grass rake. Remove possible blockages.
KHO/288/EN/1.3.0.
31
Problem situations
Operation and maintenance manual
Figure 35. Checking the grass rake for blockages
3. Check the stator or nozzle unit (Figure 36).
Make sure there are no extraneous objects (such as rope, reed entagled in the drive shaft, stones in the outlet port). Remove possible blockages.
32
Figure 36. Checking the stator for blockages
4. Check the impeller (Figure 37).
Make sure there are no extraneous objects and that it is not damaged. The impeller should be smooth with no sharp cuts. Remove possible extraneous
objects and fix the impeller if it is damaged (section 4.8.
KHO/288/EN/1.3.0.
Problem situations
Operation and maintenance manual
Figure 37. Smooth impeller
5. Close the inspection hatch.
6. Tighten the inspection hatch wing screw by hand.
5.2. Ventilation
Ventilation produces similar symptoms and sounds as cavitation (section 5.1.
, page 31), but is caused by different reasons.
Ventilation is created when air gets to drift into the intake duct. The air causes the impeller to lose grip and the thrust weakens.
Ventilation can be caused by e.g. the following:
• The inspection hatch cover is open or the seal is damaged.
Close the inspection hatch if it is open. Change the seal if it is damaged
(section 4.5.
Seals
• The installation height of the jet is wrong and air is allowed to pass along the surface of the cavitation plate into the intake duct.
In this case the jest must be reinstalled. Consult the boat's retailer.
• During installation, places accordant with the instructions have not been sealed.
In this case, the sealing must be done again. Consult the boat's retailer.
5.3. Clogged jet
Driving among water plants or in ice sludge can clog the jet. If this happens, the blockage can stop the boat from moving.
With these simple instructions it is possible practically without exception to clean very difficult blockages from the jet. Unlike with other propulsion units,
KHO/288/EN/1.3.0.
33
Problem situations
Operation and maintenance manual in boats equipped with a jet the engine stops very rarely as a result of a water plant blockage. However, ice sludge can clog the jet so badly that it cannot be removed without lifting the boat out of the water.
Boats equipped with a gearbox
In boats equipped with a gearbox, cleaning the jet is easy because in reverse gear a back flow is created in the intake duct.
Cleaning the jet:
1. Put the gear in reverse.
2. Use some acceleration to detach the blockage.
WARNING!
The jet is designed to run in reverse only for one minute at a time and at under 2,000 rpm. This is usually enough to clear the blockage.
Too heavy a load in reverse gear can lead to jamming of the impeller or breaking down of hydraulics.
Boats without gearbox
34
If the boat has no gearbox, cleaning the jet may require several phases.
Cleaning the jet:
1. Stop the engine.
This usually helps drop any extraneous objects from the grass rake.
2. Let the engine run on high revolutions for a few times.
This often sucks the extraneous objects through the jet and cleans it.
3. If the boat is moving ahead, raise the speed of the boat as high as possible and then shut down the engine.
The speed of the boat often sweeps the grass rake clean.
4. Drive the boat on reverse as fast as possible. As the boat moves astern, shut down the engine and move the deflector control lever to forward position.
This causes water to flow backwards through the jet and usually opens all kinds of blockages.
KHO/288/EN/1.3.0.
Problem situations
Operation and maintenance manual
Difficult blockages
If the aforementioned measures do not remove the blockage, you can locate the blockage through the jet's inspection hatch and remove it manually.
Removing the blockage through the inspection hatch:
1. Open the inspection hatch (Figure 38).
Figure 38. Inspection hatch
2. Locate the blockage and remove it manually.
3. Close the inspection hatch.
4. Tighten the inspection hatch screw by hand.
WARNING!
Do not open the inspection hatch when the motor is running.
There is a rotating shaft behind the hatch.
TIP!
Keep a long tube in the boat for removing stones or other objects wedged between the grass rake.
KHO/288/EN/1.3.0.
35
Problem situations
Operation and maintenance manual
36 KHO/288/EN/1.3.0.
Declaration of incorporation for partially completed machinery
Operation and maintenance manual
Appendix 1. Declaration of incorporation for partially completed machinery
(Machinery Directive 2006/42/EC, Annex II, 1.B.)
Manufacturer: Alamarin-Jet Oy
Tuomisentie 16
FI-62300 Härmä, Finland
Compiler of the technical file:
Description of the partially completed machinery:
Water jet propulsion device
Operation of the partially completed machinery:
Hannu Rantala, Technical Manager
Alamarin-Jet Oy
Tuomisentie 16
FI-62300 Härmä, Finland
Model and type of the partially completed machinery:
The device is intended to be used as the propulsion device of a motor boat.
A propulsion device transforms the torque of the motor into propulsive force.
Jet-288
Serial number of the partially completed machinery:
_____________________________________
Alamarin-Jet Oy guarantees that the abovementioned partially completed machinery meets the requirements of the Machinery Directive (2006/42/EC) and the validating national regulations.
In addition, the company guarantees that
• the specific technical documents related to the partially completed machinery have been created according to section B of Annex VII in the
Machinery Directive (2006/42/EC), and
• the following harmonised standards are applied: SFS-EN-ISO 12100-1 and
SFS-EN-ISO 14121-1.
Alamarin-Jet Oy also undertakes to deliver the documents related to the partially completed machinery to the relevant national authority in electronic format if so requested.
The partially completed machinery must not be introduced to use before the final equipment to which it is intended to be attached has been declared to conform to the requirements of this Directive.
Place: Kauhava, Finland
_________________________________
Date and Signature
KHO/288/EN/1.3.0.
37
After sales questionnaire
Operation and maintenance manual
Appendix 2. After sales questionnaire
In order to improve our products and operations, we at Alamarin-Jet Oy are collecting feedback from the end users of water jet propulsion units. This form is intended to make it as simple as possible to give us that feedback. You either fill out the printed form or the electronic form on the CD.
Only answer questions to which you know the answer. If possible, include pictures in your feedback.
Return addresses
Returning the printed version
By mail: Alamarin-Jet Oy
Tuomisentie 16
By fax:
FI-62300 Härmä, FINLAND, Europe
+358 10 7745 269
Returning the electronic version
By e-mail to the address [email protected]
Customer’s/end user’s contact information:
(Boat owner)
Contact information of person answering the questionnaire:
Delivery information of project/device:
(For instance the serial number of the propulsion unit or other relevant document)
38 KHO/288/EN/1.3.0.
After sales questionnaire
Operation and maintenance manual
Customer service received from retailer/importer/manufacturer prior to delivery:
(Quotation, technical guidance, documentation, etc.)
Delivery of propulsion unit:
(Timeliness of delivery, contents of delivery, packaging, documentation)
After sales services:
(Include prior experiences of retailer’s/manufacturer’s services)
Spare parts services:
Other comments:
KHO/288/EN/1.3.0.
39
40
After sales questionnaire
Operation and maintenance manual
3100
3200
3300
3400
3500
3600
3700
3800
2400
2500
2600
2700
2800
2900
3000
3900
4000
4100
4200
Maximum rpm
Test information for Alamarin-Jet Oy
Date of testing:
Table 4. Testing report
Test weight of boat
Number of persons
Wind speed (m/s)
Jet serial number
Engine and gearbox
GPS/clock
Engine speed
Speed in direction 1
Speed in direction 2
Water temperature
Signature
Average speed
Observations:
KHO/288/EN/1.3.0.
Grease recommendations
Operation and maintenance manual
Appendix 3. Grease recommendations
The grease used for lubricating the propulsion unit bearing must meet the following requirements:
• lithium soap and a thickener with EP additives
• mineral oil as a base oil
• NLGI class 2
• operating temperature range -25 to 130°C (-13–266 °F)
• continuous operating temperature min. 75 °C (167 °F)
Recommended grease brands:
• Würth Multi-Purpose Grease III
• FAG Multi2
• FAG Load 220
• Mobil XHP 222
• Neste Allrex EP2
• Shell Retinax Grease EP2
A grease that has equivalent properties to those mentioned above can also be used for lubrication.
KHO/288/EN/1.3.0.
41
Oil recommendations
Operation and maintenance manual
Appendix 4. Oil recommendations
The operating hydraulic system of the reversing deflector is designed to use oil that is specifically intended for automatic transmission systems. The oil must meet the following requirements:
Kinematic viscosity 40 °C (104 °F)
Kinematic viscosity 100 °C (212 °F)
Viscosity index
Density 15 °C (59 °F)
Pour point
Flashpoint
33–36 mm
2
7.1-7.7 mm
/s (0.05-0.06 sq in/s)
2
/s (0.01-0.01 sq in/s) min. 170
0.835–0.890 g/cm in)
3
(0.030-0.032 lb/sq max. -42 °C (-43,6 °F) min. 180 °C (356 °F)
Recommended oil brands:
• Mobil ATF 320
• FormulaShell ATF DEXRON III
• Neste ATF-X
• BP Autran DX III
42 KHO/288/EN/1.3.0.
Tightening torques
Operation and maintenance manual
Appendix 5. Tightening torques
Use the tightening torques from the table 5 when tightening the propulsion
unit screws. The strength grade of an acid-proof A4-80 screw is equivalent to a class 8.8 screw.
M5
M6
M8
M10
M12
M16
Table 5. Tightening torques of the screws
Thread
Strength grade
8.8
Tightening torque
(Nm) (*)
5.5 (4)
9.6 (7)
23 (17)
46 (34)
79 (58)
145 (107)
10.9
8.1 (6)
14 (10)
34 (25)
67 (49)
115 (85)
215 (159)
12.9
9.5 (7)
16 (12)
40 (30)
79 (58)
135 (100)
250 (184)
(*) The tightening torque in pound-feet (approximate value) is marked in the table in parentheses after the corresponding value in Nm.
A suitable thread locking compound that is good for all purposes is one of medium strength, for example. Loctite 242 or similar.
KHO/288/EN/1.3.0.
43
Tightening torques
Operation and maintenance manual
44 KHO/288/EN/1.3.0.
advertisement
* Your assessment is very important for improving the workof artificial intelligence, which forms the content of this project
Related manuals
advertisement
Table of contents
- 1 Operation and maintenance manual
- 3 Table of contents
- 5 1. Introduction
- 5 1.1. Safety precautions
- 5 1.2. Symbols
- 7 2. The jet propulsion unit
- 7 2.1. Structure
- 8 2.2. Serial number
- 9 3. Operation
- 9 3.1. Starting
- 10 3.2. Steering
- 11 3.3. Controlling
- 11 3.3.1. The positions of the reversing deflector control lever
- 12 3.3.2. Using the reversing deflector
- 13 3.4. Driving under difficult conditions
- 13 3.5. Dry running
- 15 4. Maintenance
- 15 4.1. Washing
- 15 4.2. Corrosion protection
- 15 4.2.1. Changing the anodes
- 17 4.2.2. Touch-up painting and antifouling
- 19 4.3. Bearing
- 19 4.3.1. Lubricating the front bearing
- 20 4.3.2. Lubrication of the rear end bearing
- 22 4.4. Control system
- 23 4.5. Seals
- 23 4.6. Hydraulic reversing deflector control system
- 26 4.7. Raw water cooling
- 27 4.8. Impeller
- 28 4.8.1. Checking the impeller
- 28 4.8.2. Removing the impeller
- 30 4.8.3. Installing the impeller
- 32 4.9. Intermediate shaft
- 35 5. Problem situations
- 35 5.1. Cavitation
- 37 5.2. Ventilation
- 37 5.3. Clogged jet
- 41 Appendix 1. Declaration of incorporation for partially completed machinery
- 42 Appendix 2. After sales questionnaire
- 45 Appendix 3. Grease recommendations
- 46 Appendix 4. Oil recommendations
- 47 Appendix 5. Tightening torques