- Home
- Do-It-Yourself tools
- Power tools
- Paint Sprayer
- Graco
- 3A7939A, SaniSpray HP 750 Sprayer
- Owner's manual
advertisement
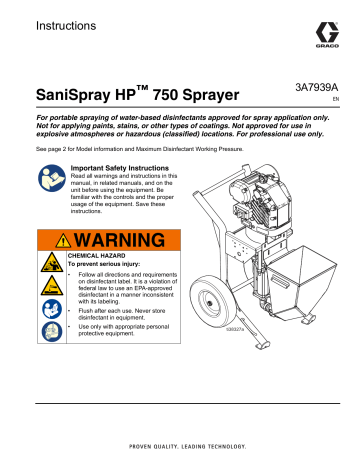
Instructions
SaniSpray HP
™
750 Sprayer
3A7939A
EN
For portable spraying of water-based disinfectants approved for spray application only.
Not for applying paints, stains, or other types of coatings. Not approved for use in explosive atmospheres or hazardous (classified) locations. For professional use only.
See page 2 for Model information and Maximum Disinfectant Working Pressure.
Important Safety Instructions
Read all warnings and instructions in this manual, in related manuals, and on the unit before using the equipment. Be familiar with the controls and the proper usage of the equipment. Save these instructions.
WARNING
CHEMICAL HAZARD
To prevent serious injury:
• Follow all directions and requirements on disinfectant label. It is a violation of federal law to use an EPA-approved disinfectant in a manner inconsistent with its labeling.
• Flush after each use. Never store disinfectant in equipment.
• Use only with appropriate personal protective equipment.
WLD
2
Contents
Important User Information . . . . . . . . . . . . . . . . . . . . . 3
Warnings . . . . . . . . . . . . . . . . . . . . . . . . . . . . . . . . . . . . 4
Component Identification . . . . . . . . . . . . . . . . . . . . . . . 7
Installation . . . . . . . . . . . . . . . . . . . . . . . . . . . . . . . . . . . 8
Grounding . . . . . . . . . . . . . . . . . . . . . . . . . . . . . . . . . 8
Connect Power . . . . . . . . . . . . . . . . . . . . . . . . . . . . . 9
Extension Cords . . . . . . . . . . . . . . . . . . . . . . . . . . . . 9
Install Vented Oil Cap Before Using Equipment . . . . 9
Setup . . . . . . . . . . . . . . . . . . . . . . . . . . . . . . . . . . . . . . . 10
Flush Before Using the Sprayer . . . . . . . . . . . . . . . 10
Disinfectant Supply Options . . . . . . . . . . . . . . . . . . 11
Remove the Hopper . . . . . . . . . . . . . . . . . . . . . . . . 11
Connect the Suction Tube. . . . . . . . . . . . . . . . . . . . 11
Connect the Hopper . . . . . . . . . . . . . . . . . . . . . . . . 11
Gun and Hose Setup Options . . . . . . . . . . . . . . . . . 12
Connect Hose(s) and Gun(s) . . . . . . . . . . . . . . . . . 12
Trigger Lock . . . . . . . . . . . . . . . . . . . . . . . . . . . . . . 15
Pressure Relief Procedure . . . . . . . . . . . . . . . . . . . 15
Prime the Sprayer . . . . . . . . . . . . . . . . . . . . . . . . . . 16
Choose Your Spray Tip . . . . . . . . . . . . . . . . . . . . . . 17
Spray . . . . . . . . . . . . . . . . . . . . . . . . . . . . . . . . . . . . . . 18
Clear Tip Clog. . . . . . . . . . . . . . . . . . . . . . . . . . . . . 19
Flushing and Cleaning . . . . . . . . . . . . . . . . . . . . . . 20
Clean the Guns . . . . . . . . . . . . . . . . . . . . . . . . . . . 21
Shutdown / Storage . . . . . . . . . . . . . . . . . . . . . . . . 22
Maintenance . . . . . . . . . . . . . . . . . . . . . . . . . . . . . . . . 23
Preventative Maintenance Schedule . . . . . . . . . . . 23
Daily Maintenance . . . . . . . . . . . . . . . . . . . . . . . . . 24
Cart Maintenance . . . . . . . . . . . . . . . . . . . . . . . . . . 24
Troubleshooting . . . . . . . . . . . . . . . . . . . . . . . . . . . . . 25
Error Code Troubleshooting . . . . . . . . . . . . . . . . . . 27
Repair . . . . . . . . . . . . . . . . . . . . . . . . . . . . . . . . . . . . . . 29
Disconnect the Pump . . . . . . . . . . . . . . . . . . . . . . . 29
Reconnect the Pump . . . . . . . . . . . . . . . . . . . . . . . 30
Replace the Rupture Disc Assembly . . . . . . . . . . . 31
Parts . . . . . . . . . . . . . . . . . . . . . . . . . . . . . . . . . . . . . . . 32
Sprayer (273215) Parts . . . . . . . . . . . . . . . . . . . . . 32
4-Gun Manifold (273226) Parts . . . . . . . . . . . . . . . 34
Dimensions . . . . . . . . . . . . . . . . . . . . . . . . . . . . . . . . . 36
Technical Specifications . . . . . . . . . . . . . . . . . . . . . . 37
Recycling and Disposal . . . . . . . . . . . . . . . . . . . . . . . 37
End of Product Life. . . . . . . . . . . . . . . . . . . . . . . . . 37
California Proposition 65 . . . . . . . . . . . . . . . . . . . . 37
Graco Warranty . . . . . . . . . . . . . . . . . . . . . . . . . . . . . . 38
Related Manuals
Manuals are available at www.graco.com.
Component manuals in English:
Part
3A7940
3A7690
3A7945
Description
SaniSpray Motor - Operation, Repair, and Parts Manual
SaniSpray HP ™ Gun - Operation Manual
Pump - Repair and Parts Manual
Models
Model
273215
273216
273217
Description
SaniSpray HP 750 Sprayer
SaniSpray HP 750 Sprayer
(includes 4-Gun Kit 273226, Qty 1)
SaniSpray HP 750 Sprayer
(includes 4-Gun Kit 273226, Qty 2)
Maximum Working Pressure
1150 psi (79 bar, 7.9 MPa)
3A7939A
Important User Information
Important User Information
Before using your disinfectant sprayer, read this manual for complete instructions on proper use and safety warnings.
The sprayer is designed to spray disinfectants that are water-based and clean up with water.
You must also read and follow the information on the disinfectant container label and ask for a Safety Data Sheet (SDS) from your supplier.
The container label and SDS will explain the contents of the disinfectant, instructions for use and the specific precautions related to the contents of the disinfectant. Those precautions include personal protective equipment (PPE).
KNOW YOUR DISINFECTANT’S
ACTIVE INGREDIENTS
For the purpose of safely using this sprayer, you need to know what kind of active ingredients are in the disinfectant.
Look on the container label for the list of active ingredients. There are two categories:
ALCOHOL: This type of disinfectant contains flammable active ingredients such as ethanol (ethyl alcohol) or isopropanol (IPA). The container label should indicate that this disinfectant is COMBUSTIBLE or
FLAMMABLE. Your sprayer is compatible with this type of disinfectant. Use flammable disinfectants in a well-ventilated area with a flow of fresh air. See the safety warnings in this manual.
NON-ALCOHOL: This type of disinfectant contains active ingredients such as aldehydes, phenols, quaternary ammonium compounds, sodium hypochlorite (bleach), peroxyacetic acid, hydrogen peroxide, and hypochlorous acid. Your sprayer is compatible with this type of disinfectant.
3A7939A 3
Warnings
Warnings
The following warnings are for the setup, use, grounding, maintenance, and repair of this equipment. The exclamation point symbol alerts you to a general warning and the hazard symbols refer to procedure-specific risks.
When these symbols appear in the body of this manual or on warning labels, refer back to these Warnings.
Product-specific hazard symbols and warnings not covered in this section may appear throughout the body of this manual where applicable.
WARNING
CHEMICAL HAZARD
Toxic disinfectant or fumes can cause serious injury or death if splashed in the eyes or on skin, inhaled, or swallowed.
• Keep away from children.
• Use only to spray surfaces. Do not spray people or animals.
• Use only with appropriate personal protective equipment. See
• Follow all directions and requirements on disinfectant label. It is a violation of Federal law to use an EPA-approved disinfectant in a manner inconsistent with its labeling.
• Flush with water after each use. Never store disinfectant in equipment.
• Read Safety Data Sheets (SDSs) to know the specific hazards of the disinfectants you are using.
• Store and dispose of disinfectants according to instructions on disinfectant container labels.
4
FIRE AND EXPLOSION HAZARD
Flammable fumes, such as disinfectants, in work area can ignite or explode. Disinfectants flowing through the equipment can cause static sparking. To help prevent fire and explosion:
• Keep sprayer area well-ventilated. Keep a good supply of fresh air moving through the area.
• Do not spray flammable disinfectants near an open flame or sources of ignition such as cigarettes, motors, and electrical equipment.
• Ground all equipment in the work area. Connect to a grounded outlet and use grounded extension cords. See
instructions.
• Never spray or flush disinfectant at high pressure.
• Keep work area free of debris, including disinfectant containers, rags and gasoline.
• Do not plug or unplug power cords, or turn power or light switches on or off when flammable fumes are present.
• Use only grounded hoses.
• Hold gun firmly to side of grounded pail when triggering into pail. Do not use pail liners unless they are anti-static or conductive.
• Stop operation immediately if static sparking occurs or you feel a shock .
Do not use equipment until you identify and correct the problem.
• Keep a working fire extinguisher in the work area.
3A7939A
3A7939A
Warnings
ELECTRIC SHOCK HAZARD
WARNING
This equipment must be grounded. Improper grounding, setup, or usage of the system can cause electric shock.
• Turn off and disconnect power cord before servicing equipment.
• Connect only to grounded electrical outlets.
• Use only 3-wire extension cords.
• Ensure ground prongs are intact on power and extension cords.
• Do not expose to rain. Store indoors.
SKIN INJECTION HAZARD
High-pressure spray from gun, hose leaks, or ruptured components will pierce skin. This may look like just a cut, but it is a serious injury that can result in amputation. Get immediate surgical treatment.
• Use only to spray surfaces. Do not spray people or animals.
• Do not point spray tip at anyone or place any part of your body in front of tip. For example, do not try to stop leaks with any part of the body.
• Do not spray without tip guard installed.
• Engage trigger lock when not spraying. Verify the trigger lock is functioning properly.
• Do not stop or deflect leaks with your hand, body, glove, or rag.
• Equipment maintains pressure after power is shut off. Do not leave equipment energized or under
pressure while unattended. Unplug the sprayer and follow the Pressure Relief Procedure on page
15 when the equipment is unattended or not in use, and before servicing, cleaning, or removing
parts.
•
Follow the Pressure Relief Procedure
when you stop spraying and before cleaning, checking, or servicing equipment.
• Verify that all connections are secure before operating the unit.
• Check hoses and parts for signs of damage. Replace any damaged hoses or parts.
5
6
Warnings
WARNING
EQUIPMENT MISUSE HAZARD
Misuse can cause death or serious injury.
• Do not operate or spray near children. Keep children away from equipment at all times.
• Do not operate the unit when fatigued or under the influence of drugs or alcohol.
• Do not exceed the maximum working pressure or temperature rating of the lowest rated system
component. See Technical Specifications
in all equipment manuals.
• Use disinfectants that are compatible with equipment wetted parts. See
in all equipment manuals. Read disinfectant manufacturer’s warnings. For complete information about your disinfectant, request Safety Data Sheets (SDSs) from distributor or retailer.
• Do not leave the work area while equipment is energized or under pressure.
•
Turn off all equipment and follow the Pressure Relief Procedure when equipment is not in use.
• Check equipment daily. Repair or replace worn or damaged parts immediately with genuine manufacturer’s replacement parts only.
• Do not alter or modify equipment. Alterations or modifications may void agency approvals and create safety hazards.
• Make sure all equipment is rated and approved for the environment in which you are using it.
• Use equipment only for its intended purpose. Call your distributor for information.
• Route hoses and cables away from traffic areas, sharp edges, moving parts, and hot surfaces.
• Do not kink or over bend hoses or use hoses to pull equipment.
• Comply with all applicable safety regulations.
MOVING PARTS HAZARD
Moving parts can pinch, cut or amputate fingers and other body parts.
• Keep clear of moving parts.
• Do not operate equipment with protective guards or covers removed.
• Equipment can start without warning. Before checking, moving, or servicing equipment, follow the
Pressure Relief Procedure and disconnect all power sources.
PERSONAL PROTECTIVE EQUIPMENT
Wear appropriate protective equipment when in the work area to help prevent serious injury, including eye injury, burns, hearing loss, and inhalation of disinfectant chemical mists and vapors.
Protective equipment includes but is not limited to:
• Protective eye-wear, and hearing protection.
• Appropriate respirators, protective clothing, and gloves.
• All protective equipment specified by the disinfectant manufacturer.
3A7939A
Component Identification
Component Identification
=
3
$
6
+
(
7
WLD
/
'
)
Ref.
Description
D
E
F
G
A
B
C
H
J
L
Electric Motor
Pump
Disinfectant Inlet
Packing Nut
Power Switch
Disinfectant Outlet
Tip and Tip Guard Assembly
Pressure Adjustment Knob
Outlet Check Valve
Status Indicator Light (LED)
3A7939A
-
&
)
;
8
9 :
Ref.
T
U
V
W
M
P
S
X
Y
Z
Description
Rupture Disc
Oil Fill Cap (vented)
Junction Box
Hopper
Hopper Bracket
Airless Hose
Gun
4-gun manifold
Gun Extension
Power Cord
< G
7
8
Installation
Installation
Grounding
The equipment must be grounded to reduce the risk of static sparking and electric shock. Electric or static sparking can cause fumes to ignite or explode.
Improper grounding can cause electric shock.
Grounding provides an escape wire for the electric current.
Sprayer: Ground the sprayer by plugging it into an outlet that is properly installed and grounded in accordance with all applicable regulations. Do not modify the power cord provided; if it does not fit the outlet, have the proper outlet installed by a qualified electrician.
Disinfectant hoses: Use only electrically conductive hoses (hoses that allow the flow of static electricity). To ensure grounding continuity, do not exceed the recommended maximum hose length of 500 ft. (152.4 m) per gun.
Spray gun: The gun is grounded through its connection to a properly grounded disinfectant hose and sprayer.
For disinfectants with alcohol active ingredients:
When you are using disinfectants with alcohol-based active ingredients, you must use conductive metal containers, which are able to be grounded.
To ground metal supply and flushing containers, use a grounding wire and clamp (GW) (Graco part 244524 - not supplied). Do not place grounded metal containers on a non-conductive surface, such as paper or cardboard, which interrupts grounding continuity.
1. Connect a ground wire (not included) to the ground stud (Y) on the back of the motor.
<
GW
WLD
2. Clamp other end of grounding wire (GW) to the metal container.
GW
WLD
3A7939A
Installation
Connect Power
NOTE: The sprayer is rated 200-240 Vac, 1 Phase, 20A,
50/60 Hz. A dedicated 20A circuit with a NEMA L6-20R receptacle is required.
1. Before use, verify that you have the required
20-Amp circuit with a NEMA L6-20R receptacle.
Extension Cords
If an extension cord is necessary, use a 12 AWG (2.5 mm 2 ) or thicker cord to carry the current that the sprayer draws. Undersized extension cords result in a drop in line voltage and loss of power and overheating.
Select the minimum cord wire gauge based on length according to the table below:
Length
50 ft (15.24 m)
100 ft (30.48 m)
200 ft (60.96 m)
300 ft (91.44 m)
Gauge
12 AWG
10 AWG
6 AWG
4 AWG mm
2
3.31
5.26
13.29
21.14
Make sure your extension cord is not damaged.
WLD
2. Plug the power cord (Z) into the receptacle.
=
Install Vented Oil Cap Before
Using Equipment
The sprayer's motor gear box is shipped from the factory pre-filled with oil. The temporary unvented cap
(PX) prevents oil leaks during shipment.
Replace the temporary unvented cap (PX) with the oil fill cap (P) before use.
P
PX
WLD ti36317a
3A7939A 9
Setup
Setup
To avoid tipping over, make sure the cart is on a flat and level surface. Failure to do so could result in injury, such as crushing.
1. Position the sprayer on a level surface. Check the oil level in the sight glass (K). If needed, fill until the oil level is near the halfway point of the sight glass.
The oil capacity is approximately 1.0–1.2 quarts
(0.9–1.1 liters). Do not overfill.
P
K
NOTICE
Your sprayer comes with a factory-installed outlet check valve (J). Do not attach the airless hoses (V) directly to the pump, as this can cause air bubbles to form in the disinfectant. The outlet check valve prevents air bubbles from forming, which can cause damage to the sprayer.
J
WLD
5. Make sure the pressure setting is at the lowest level. Pull the pressure adjustment knob (H) out and turn counterclockwise until it stops, then push the knob in to lock.
H
WLD
NOTICE
Only use Graco oil (part number 16W645) in this sprayer. Any other oil may not lubricate properly and can cause damage to the drive train.
2. Use the included spanner wrench to make sure the packing nut (D) is just tight. Fill 1/3 full with Throat
Seal Liquid (TSL ™ ). Refill as needed.
WLD
6. Turn the power switch (E) OFF. Plug the power cord into a grounded outlet.
TSL
OFF
E
D
WLD
3. Determine your supply option. See Disinfectant
4. Attach electrically conductive airless hoses (V),
4-gun manifolds, and guns. See
Connect Hose(s) and Gun(s) on page 12.
Flush Before Using the Sprayer
Your sprayer's pump has been factory-tested with lightweight oil. A small amount of this oil is left in the pump to protect parts. To avoid contaminating your disinfectant with oil, flush the sprayer with warm soapy water before using it for the first time.
See Flushing and Cleaning , page 20.
10 3A7939A
Setup
Disinfectant Supply Options
You will need to determine which supply option will work best for your job.
• Hopper Feed
• Suction Tube Feed
Your sprayer comes from the factory installed with a disinfectant hopper. For bigger jobs, you can connect a separate suction tube to draw disinfectant directly from a larger container.
To use the suction tube, you will need to
Hopper and follow the Connect the Suction Tube
procedure.
Connect the Suction Tube
1. Install fitting (38) and elbow (39) to the pump (9).
2. Connect the suction tube (70), coupler (72), feed tube (71), and strainer (73) to hose (33).
3. Connect hose (33) to elbow (39).
4. Proceed to Connect Hose(s) and Gun(s) on page
Remove the Hopper
1. Disconnect fitting (24) from fitting (25).
2. Remove fitting (26) and fitting (24) from hopper (31).
3. Remove elbow (50) and fitting (25) from pump (9).
4. Remove nuts (6) and bolts (23) from hopper bracket
(19) to cart bracket (18).
5. Remove nuts (6) and bolts (23) from cart bracket
(18) and remove the bracket from cart (1).
WLD
WLD
Connect the Hopper
1. Use nuts (6) and bolts (23) to attach the bracket (18) to the cart (1).
2. Loosely attach hopper bracket (19) to cart bracket
(18) with nuts (6) and bolts (23).
3. Install elbow (50) and fitting (25) to the pump (9).
4. Install fitting (26) and fitting (24) to the hopper (31).
5. Connect fitting (24) to fitting (25).
6. Adjust the height on hopper bracket (19) until it fits under the lip on the back of the hopper (31). Tighten nuts (6).
7. Proceed to Connect Hose(s) and Gun(s) on page
3A7939A 11
Setup
Gun and Hose Setup Options
You will need to determine which gun setup option will work best for your job. There are two gun setup options for your sprayer:
•
4-Gun Setup (see page 13 for image)
•
8-Gun Setup (see page 14 for image).
Whichever setup you choose, be sure to have an operator for each gun to be used. A single operator should never spray more than one gun at a time. Once
you’ve determined your gun setup, proceed to Connect
Hose(s) and Gun(s) on page 12.
4. Connect a 3/8 in. airless hose (110) to the 4-gun manifold tee fitting (101).
5. Connect a 1/4 in. airless hose (111) to the outlet of each ball valve (104) on the 4-gun manifold.
NOTE: Use fitting (113) to add another 100 feet
(30.4 m) of 1/4 in. airless hose (111). Your sprayer comes with enough hose for 300 ft (91.5 m) per gun.
You can add an additional 200 ft (61 m) for a maximum of 500 (153 m) ft per gun.
6. Assemble the optional 1/8 in. airless whip hoses
(112) to the end of each 1/4 in. airless hose (111).
Use two wrenches to securely tighten hoses together.
Connect Hose(s) and Gun(s)
There are two disinfectant outlets (F) on your sprayer.
Each outlet supports one 4-gun manifold. To use your sprayer with a 4-gun setup, you will need to plug 1 of the disinfectant outlets.
1. To plug a disinfectant outlet, remove elbow (44) and replace it with plug (103). See the
4-Gun Setup illustration on page 13.
112
111
7. Insert the other end of each 1/8 in. airless whip hose
(112) through the hose guard at the base of each spray gun (106). Use two wrenches to tighten securely.
106
WLD
2.
4-gun and 8-gun setups: Follow steps 3 - 7 one time for each 4-gun manifold. If you are using an
8-gun setup, you will have to perform these steps
twice. See the 8-Gun Setup illustration on page 14.
3. Connect a 3/8 in. airless hose (110) to elbow (44).
112
12 3A7939A
4-Gun Setup
WLD
Setup
3A7939A 13
Setup
8-Gun Setup
WLD
14 3A7939A
Setup
Trigger Lock
Each gun has a trigger lock to prevent it from being triggered accidentally by hand, or if a gun is dropped or bumped. Always engage a gun’s trigger lock when it is not in use.
3. Make sure the pressure setting is at the lowest level. Pull the pressure adjustment knob (H) out and turn counterclockwise until it stops. Push the knob in to lock.
H
Pressure Relief Procedure
Follow the Pressure Relief Procedure whenever you see this symbol.
4. Turn the power switch (E) OFF.
OFF
E
This equipment stays pressurized until pressure is manually relieved. To help prevent serious injury from pressurized disinfectant, such as skin injection, splashing disinfectant and moving parts, follow the
Pressure Relief Procedure when you stop spraying and before cleaning, checking, or servicing the equipment.
1. Engage all trigger locks.
5. Disengage all trigger locks.
6. Hold each gun firmly against a grounded metal pail.
Trigger the each gun to relieve pressure. Guns can be triggered individually or all at the same time.
NOTE: Once the first gun has been triggered there will be a noticeable decrease in pressure, but the remaining guns will still need to be triggered to relieve all pressure.
2. Open any ball valves in use on the 4-gun manifold.
If using an 8-gun setup, open any ball valves in use on both 4-gun manifolds.
WLD
7. Engage all trigger locks.
8. If you suspect that a spray tip or hose is completely clogged or that pressure has not been fully relieved: a. VERY SLOWLY loosen the tip guard retaining nut or hose end coupling to relieve pressure gradually.
b. Loosen the nut or hose end coupling completely.
c. With tip removed, trigger each gun into the pail.
3A7939A 15
Setup
Prime the Sprayer
1. Follow the Pressure Relief Procedure on page 15.
2. Remove the tip and tip guard assembly (G) from each gun. If installed, also remove the gun extension.
6. Open any ball valves to be used on the 4-gun manifold. If using an 8-gun setup, open any ball valves in use on both 4-gun manifolds.
WLD inner outer
G
3. If using a hopper, fill the hopper with disinfectant.
WLD
4. If using a suction tube (70), place the tube into your disinfectant container.
70
NOTE: When spraying with fewer than four guns, always start by using the outer-most ball valve
(position 1). Then work your way back towards the sprayer (position 2, position 3, etc) with each additional gun.
7. Prime the hoses and guns, either separately or all at once: a. Disengage the trigger lock of each gun being used.
b. Trigger each gun into a grounded metal pail. c. Pull out the pressure adjustment knob (H) and turn it clockwise slowly to increase pressure, until a steady stream flows from each gun. d. Release all triggers, then push the pressure adjustment knob (H) in to lock.
H
WLD
5. Turn the power switch (E) ON.
e. Engage each trigger lock.
NOTE: Hoses and guns can be primed individually or all at the same time.
f.
Inspect connections for leaks. If you find a leak,
do not begin spraying. Follow the Pressure
Relief Procedure on page 15. Tighten or
replace the fittings and repeat the Prime the
Sprayer procedure.
If there are no leaks, continue on the
E
ON
WLD
16 3A7939A
Choose Your Spray Tip
Setup
3. Insert the spray tip into the tip guard. Verify that the spray tip is forward in the SPRAY position.
To avoid serious injury from skin injection, do not put your hand in front of the spray tip when installing or removing the tip and tip guard.
Your sprayer comes with four spray tip sizes:
Fine
Medium
Coarse
LP617
LP621, LP723
LP631
Select the appropriate spray tip size to provide the acceptable spray of disinfectant. Refer to the disinfectant label for manufacturer’s recommendations.
To prevent spray tip leaks, make certain the spray tip and tip guard are installed properly.
1. Follow the
Pressure Relief Procedure on page 15.
2. Use spray tip (AA) to align the gasket and seal (BB) with the tip guard (CC).
AA
BB
CC
4. Screw the tip guard assembly (G) onto the spray gun and tighten.
G
3A7939A 17
Spray
Spray
6. Point the guns toward the surfaces to be sprayed.
7. Confirm that the pressure adjustment knob (H) is at the lowest setting.
H
Fumes from disinfectants with alcohol active ingredients, or from other flammable disinfectants can explode or ignite.
To prevent fumes from exploding or igniting:
• Keep the spray area well ventilated.
• Ground the equipment.
NOTICE
Do not allow the pump to run out of disinfectant, as it can damage the pump.
1. Follow the Prime the Sprayer procedure on page
2. Follow the Pressure Relief Procedure on page 15.
3. Select the proper spray tip for your job. See
Choose Your Spray Tip on page 17.
4. Install the tip and tip guard assembly (G) onto each gun to be used. If needed, install the optional gun extension (XT) between the tip guard assembly.
G
XT
8. Disengage all trigger locks.
WLD
9. Pull and hold the gun triggers.
10. Slowly increase pressure using the pressure adjustment knob (H). Set the knob to the minimum setting needed to produce the desired spray of disinfectant. Push the knob in to lock.
11. Adjust the spray gun distance from the surface and your hand speed to achieve the desired surface coverage. Always refer to the disinfectant manufacturer’s recommendations for an acceptable spray of disinfectant.
12. Flush the sprayer every time you are finished spraying. Follow the
Flushing and Cleaning procedure on page 20.
WLD
5. Turn the power switch (E) ON.
E
ON
WLD
18 3A7939A
Clear Tip Clog
To avoid injury, never point the gun at your hand or into a rag.
In the event debris clogs the spray tip, the gun is designed with a reversible spray tip that quickly and easily clears the particles without disassembling the gun.
1. Release the trigger. Engage the trigger lock. Rotate the spray tip to the UNCLOG position. Disengage the trigger lock. Trigger the gun into a grounded metal pail to clear the clog.
UNCLOG
Spray
2. Engage the trigger lock. Rotate the spray tip back to the SPRAY position. Disengage the trigger lock and continue spraying.
SPRAY
3A7939A 19
Spray
Flushing and Cleaning
Flushing the sprayer is required before you use your new sprayer for the first time and after each use.
Flushing after use removes any disinfectants and residues from the sprayer. It will also help ensure a trouble-free startup the next time the sprayer is used.
5. If using a suction tube, place the tube (70) into a pail of warm soapy water. To flush disinfectants with alcohol active ingredients, ground the pail according to
70
Use only water for cleaning.
Clean in a well-ventilated area.
Keep a good supply of fresh air moving through the area.
To avoid injury from splashing, always flush at the lowest possible pressure.
WLD
6. Turn the power switch (E) ON.
E
ON
NOTICE
Disinfectant left in the sprayer will damage the equipment. To avoid damage, always completely flush the sprayer with warm soapy water after every use. Do not store the sprayer with disinfectant in it.
1. Follow the Pressure Relief Procedure on page 15.
2. Remove the tip and tip guard assembly (G) from each gun. If installed, also remove the gun extension.
7. Flush the hoses and guns: a. Open all ball valves that have been used to
spray. If using an 8-gun setup, be sure to open any ball valves used on both 4-gun manifolds.
NOTE: Guns used can be flushed all at once, or they can be flushed one at a time. If flushing one gun at a time, begin with the inner-most gun
(position 4) and then work your way towards the outer-most gun (position 1) on each 4-gun manifold.
WLD
G
3. If using a hopper, dispense disinfectant until the hopper is empty (multiple guns can be used to speed up this process).
4. Fill the empty hopper with warm soapy water. inner position
4 position
3 position
2 position
1 outer b. Disengage trigger locks for the gun(s) to be flushed.
20
WLD
3A7939A
c. Trigger each gun into a grounded metal pail. d. Pull out the pressure adjustment knob (H) and turn it clockwise slowly to increase pressure until a steady stream flows from the gun. Push the knob in to lock.
Spray
NOTE: Flush all hoses and guns used at any point during spraying (even if you only opened the ball valve but did not spray the gun). i.
Engage all trigger locks. e. Trigger each gun for at least one minute, then release the trigger. f.
Close the ball valve for the gun you have just flushed, then trigger the gun again to relieve pressure.
NOTE: If using an 8-gun setup, be sure to repeat steps to flush the hoses and guns for both 4-gun manifolds.
8. Wipe the sprayer and all hoses with a soft cloth moistened with warm soapy water.
9. Dispose of unused disinfectant in the waste pail according to instructions on the disinfectant container label and follow all applicable regulations.
WLD g. Engage trigger lock.
NOTE: If flushing one gun at a time, proceed to the next gun in the line (described in the note below step 7a). Repeat steps 7b - 7e for each gun.
h. To make sure the entire 4-gun manifold is completely flushed, trigger the gun at the outer-most ball valve furthest from sprayer
(position 1) for an additional 30 seconds after flushing the other hoses. This will ensure there is no disinfectant left in the manifold.
Clean the Guns
1. Follow the Pressure Relief Procedure on page 15.
2. Remove the spray tips, tip guard assemblies, and gun extensions (if installed), then clean with warm soapy water and a brush.
WLD
3. Wipe the spray guns with a soft cloth moistened with warm soapy water. inner position
4 position
3 position
2 position
1 outer
3A7939A 21
Spray
Shutdown / Storage
Shutdown
1. Follow the Flushing and Cleaning
procedure on
2. Follow the Pressure Relief Procedure on page 15.
NOTICE
For overnight shutdown, stop the pump at the bottom of its stroke to prevent damaging the pump rod and throat packings.
Storage
NOTICE
Disinfectant left in the sprayer will damage the equipment. To avoid damage, always completely flush the sprayer with warm soapy water after every use. See
Flushing and Cleaning on page 20. Do
not store the sprayer with disinfectant in it.
• Before storing the sprayer, make sure all water is drained from the sprayer and airless hoses.
• Do not allow water to freeze in the sprayer or hoses.
• Do not store the sprayer while it is under pressure.
• Store the sprayer indoors.
• Store with all hoses and guns connected to 4-gun manifold.
22 3A7939A
Maintenance
Maintenance
Check the Oil
Position the sprayer on a level surface. Check the oil level in the sight glass (K). If needed, fill until the oil level near the halfway point of the sight glass. Do not overfill.
P
NOTICE
Do not open/remove the gear cover. The gear side is not intended to be serviced. Opening the gear cover may alter the factory set bearings and may reduce the sprayer’s life.
K
Preventative Maintenance
Schedule
The operating conditions of your sprayer affect how often maintenance is required. Establish a preventive maintenance schedule by recording when and what kind of maintenance is needed, and then determine a regular schedule for checking your sprayer.
Every 40 hours of operation, check that the packing nut
is tight. Follow the Pressure Relief Procedure
on page
15, then use a wrench to tighten the packing nut (D) until
just snug.
NOTICE
Do not over-tighten. The packing nut can become stripped and damaged.
WLD
Change the Oil
NOTE: Change the oil after a break-in period of approximately 250 hours of use. After the break-in period, change the oil once a year.
1. Follow the Pressure Relief Procedure on page 15.
2. Place a minimum 2 quart (1.9 liter) container under the oil drain port. Remove the oil drain plug and allow all oil to drain from the motor.
3. Reinstall the oil drain plug. Torque to 18–23 ft-lb
(25–30 N•m).
NOTICE
Do not over-torque. The drain plug can become stripped and damaged.
4. Position the sprayer on a level surface. Fill until the oil level is near the halfway point of the sight glass.
The oil capacity is approximately 1.0–1.2 quarts
(0.9–1.1 liters). Do not overfill.
NOTICE
Only use Graco oil (part number 16W645) in this sprayer. Any other oil may not lubricate properly and can cause damage to the drive train.
5. Reinstall the oil fill cap (P).
3A7939A 23
Maintenance
Daily Maintenance
NOTICE
For overnight shutdown, stop the pump at the bottom of its stroke to prevent damaging the pump rod and throat packings.
Cart Maintenance
Periodically lubricate the axle between points A and B with lightweight oil (see below).
1. Follow the Flushing and Cleaning
procedure on
2. Follow the Pressure Relief Procedure on page 15.
3. Use the included spanner wrench to make sure the packing nut (D) is just tight. Refill with Throat Seal
Liquid (TSL ™ ) as needed.
TSL
$
%
Keep the cart clean by wiping up spills daily.
WLD
D
WLD
4. Check all hoses and fitting connections for leaks.
Tighten all connections before each use.
5. Check hoses for damage every time you spray. Do not attempt to repair the hose if the hose jacket or fittings are damaged. Replace all damaged parts.
24 3A7939A
Troubleshooting
Troubleshooting
Unplug the power cord and follow the Pressure Relief
Procedure on page 15 before checking or repairing
your sprayer.
NOTE: Check all possible problems and solutions listed in the table below before disassembling the pump.
NOTE: The status indicator (L) on the motor will blink if an error is detected.
Problem Cause Solution
Pump output is low on both up and down strokes
No output
Disinfectant supply is empty Refill the disinfectant supply and prime the pump.
* Clogged disinfectant outlet line, gun, etc. The hose inner diameter is too small.
Clear the hose, outlet check valve, or gun; use the hose with the larger inner diameter.
Worn piston packing
Inlet strainer is clogged (if using suction tube)
Replace the piston packing. See your pump manual.
Remove and clean inlet strainer, then reinstall.
Improperly installed intake or piston check valves
Check and repair. See your pump manual.
Intake valve is clogged Clean the intake valve.
Disinfectant supply is empty Refill the disinfectant supply and prime the pump.
Pump will not operate Disinfectant supply is empty Refill the disinfectant supply and prime the pump.
* Clogged disinfectant hose, gun, or spray tip
Follow the
the hose and gun.
procedure on page 19, or clean
Motor parts are worn or damaged
Repair or replace the motor (see your motor manual).
Disconnect the Pump (see page 29). If the motor will not
cycle and does not blink an error code, then troubleshoot the motor or replace.
No pressure or flow Disinfectant is leaking from the rupture disk
The inlet is clogged
Motor does not turn on Over voltage (over 300 V)
Output low on the down stroke
No power to the control board
Open or worn intake valve
Follow
Replace the Rupture Disc Assembly
procedure
on page 31. Do not replace with a pipe plug.
Clean the inlet. Clean the inlet strainer if using a suction tube.
See the power supply requirements in your motor manual.
Verify that the power supply is connected. Check the junction box connections.
Clear or service the intake valve.
Output low on the up stroke
Open or worn piston valve packings
Clear the piston valve. Replace the packings.
* To determine if a disinfectant hose or gun is obstructed, follow the
Pressure Relief Procedure on page 15.
Disconnect disinfectant hose and place a container at pump disinfectant outlet to catch any disinfectant. Turn pressure adjustment knob just enough to start the pump. If the pump starts, the obstruction is in the disinfectant hose or gun.
3A7939A 25
Troubleshooting
Problem
Erratic or accelerated pump speed
Cycles or fails to hold pressure at stall
Poor or irregular spray pattern
Motor does not turn over and LED is off
Motor does not turn over and LED is on
Oil is leaking
Cause Solution
Disinfectant supply is empty Refill and prime the pump.
Clogged suction Clean the suction tube.
Clear the piston valve. Replace the packings.
Open or worn piston valve packings
Open or worn intake valve Clear or service the intake valve.
Clear the gun, hose, outlet, etc.
Clogged gun, hose, outlet, etc.
Open or worn outlet check valve
Clear or service the outlet check valve.
Service the pump (see your pump manual).
Worn intake or piston valve or seals
Incorrect disinfectant pressure at gun
Dirty, worn, or damaged spray gun
Over voltage (greater than
300 V)
See your gun manual. Read the disinfectant manufacturer’s recommendations.
Service the spray gun (see your spray gun manual).
Check the power supply.
No power to the control board
Encoder fault
Oil was over filled
Drain plug is not tightened properly
Seal cartridge o-ring missing or damage
Verify that the power supply is connected. Check the junction box connections.
Cycle power. Recalibrate the encoder following the procedure listed in your motor manual. Contact your Graco distributor or Tech Service for more information.
Drain and refill oil as stated in Check the Oil , page 23.
Torque to 18-23 ft-lb (25-30 N•m).
Replace the shaft bearing assembly. See your motor manual.
26 3A7939A
Troubleshooting
Error Code Troubleshooting
To troubleshoot using an error code, you need to first determine your blink code.
1. The blink code is displayed using the status indicator (L) on the motor. The blink code given below indicates the sequence. For example, blink code 2 indicates two blinks, a pause, and then repeats.
2. Error codes can take two forms:
• Alarm: Alerts you to the cause of the alarm and shuts down the motor.
• Deviation: Alerts you to the problem, but the motor may continue to run until the absolute limits are reached.
NOTE: To clear an error code, first try turning the pressure adjustment knob (H) counterclockwise until it stops. If the status indicator (L) does not stop blinking shortly after turning the knob to zero, cycle the power by turning the power switch (E) to the OFF position for at least 30 seconds before turning back ON.
Standby Mode
When slow blinking is displayed, the motor has entered
Standby Mode. The motor will enter Standby Mode when powered on and pressurized with a knob setting greater than 7, and the pump has not moved any disinfectant for 30 minutes.
Standby Mode will be exited when:
• Disinfectant starts to dispense and causes the pump to move, OR
• The pressure control knob (H) is adjusted, OR
• The power switch (E) is cycled OFF and ON
Error Codes Table
Blink Code
1
2
3
Error Type
Alarm
Alarm
Alarm
Troubleshooting Steps
Pump Diving
Pump diving is when the pump moves through the down stroke too rapidly. A pressure imbalance between the up and down stroke of the pump cause the pump to dive with excessive speed.
• Pump diving may occur when the pump runs out of disinfectant while spraying at high pressure.
• Verify that disinfectant is being properly fed to the pump.
• Pressure from the hose could flow back into the pump on the down stroke.
• Verify that the check valve is installed and is properly working.
• Cycle power and check status indicator (L) to see if the error is still active.
Voltage Too Low
•
Verify that line voltage is within the range specified in Technical
• Cycle power and check status indicator (L) to see if the error is still active.
Voltage Too High
•
Verify that line voltage is within the range specified in Technical
• Cycle power and check status indicator (L) to see if the error is still active.
3A7939A 27
Troubleshooting
5
6
Blink Code
4
7
8
9
10
11
12
13, 14
Slow Blink
Error Type
Deviation
Deviation
Alarm
Alarm
Alarm
Alarm
Alarm
Alarm
Alarm
Alarm
Deviation
Troubleshooting Steps
High Temperature
The temperature of the system is near the maximum operation temperature. The performance has been reduced to prevent the motor from completely shutting down.
• Reduce pressure.
• Move the sprayer to a cooler location.
Low Temperature
Move the sprayer to a warmer location
Motor Temperature Fault
Motor is running too hot. Allow unit to cool.
• Reduce pressure.
• Move the sprayer to a cooler location.
Board Temperature Fault
The control board is running too hot. Allow the sprayer to cool.
• Reduce pressure.
• Move the sprayer to a cooler location.
Encoder Calibration Error
• Cycle power and check status indicator (L) to see if the error is still active.
• Follow the calibration procedure listed in your motor manual to calibrate the encoder (this code will blink if calibration is in progress).
• Contact your Graco distributor or Tech Service for more information.
Encoder Error
• Cycle power and check the status indicator (L) to see if the error is still active.
• Verify that the internal connections are intact.
• Contact your Graco distributor or Tech Service for more information.
Software Versions Do Not Match
Obtain software update token. See your motor manual for the token part number and token installation information.
Circuit Board Communication Failure
Cycle power and check status indicator (L) to see if the error is still active.
Contact your Graco distributor or Tech Service for more information.
Internal Circuit Board Hardware Failure
Cycle power and check status indicator (L) to see if the error is still active.
Contact your Graco distributor or Tech Service for more information.
Internal Software Error
Cycle power and check status indicator (L) to see if the error is still active.
Contact your Graco distributor or Tech Service for more information.
See
28 3A7939A
Repair
Repair
Disconnect the Pump
See the Parts section starting on page 32 for all part
identification references in the steps below.
6. Unscrew the coupling nut (13) from the connecting rod adapter (11). Remove the coupling collars (12); do not lose or drop them.
1. Follow the
Flushing and Cleaning on page 20.
2. Stop the pump at the bottom of its stroke.
3. Follow the
Pressure Relief Procedure on page 15.
4. Unplug the power cord (Z).
5. Disconnect the disinfectant hose and suction tube or the hopper.
NOTE: Before disconnecting the pump (9) from the motor (4), be sure to note the relative position of the pump’s disinfectant outlet to the motor. If the motor does not require servicing, leave it attached to its mounting.
4
WLD
7. Hold the tie rod flats with a wrench to keep the rods
(8) from turning. Unscrew the nuts (10). Remove the pump (9).
9
WLD
WLD
Use at least two people when lifting, moving, or disconnecting the pump. If disconnecting the pump, be sure to securely brace the pump, or have two people hold it while another person disconnects it.
3A7939A
8. To service the pump, refer to your pump manual. To service the motor, see your motor manual. See
29
Repair
Reconnect the Pump
See the
Parts section starting on page 32 for all part
identification references in the steps below.
1. Screw the connecting rod adapter (11) to the motor shaft.
2. Screw the tie rods (8) into the motor (4). Using a wrench on the tie rod flats, torque to 50-60 ft-lb
(68-81 N•m).
NOTE: When reconnecting the pump (9) to the motor (4), be sure to match the relative position of the pump’s disinfectant outlet to the motor.
Use at least two people when lifting, moving, or connecting the pump. When connecting the pump, be sure to securely brace the pump, or have two people hold it while another person connects it.
5. Screw the nuts (10) onto the tie rods (8) and torque to 50-60 ft-lb (68-81 N•m).
6. Screw the coupling nut (13) onto the connecting rod adapter (11) loosely. Hold the connecting rod adapter flats with a wrench to keep from turning.
7. Use an adjustable wrench to tighten the coupling nut (13). Torque to 90-100 ft-lb (121-135 N•m).
8. Reconnect all hoses. Fill the packing nut (D) 1/3 full of Graco Throat Seal Liquid.
TSL
D
WLD
3. Make sure the coupling nut (13) and coupling collars
(12) are in place on the rod.
4. Use at least two people to hold the pump while another person reconnects it to the motor. Position the pump as shown below. Place the pump (9) on the tie rods (8).
WLD
9. Turn on the electric motor. Run the pump slowly to ensure that it operates properly.
8
9
WLD
30 3A7939A
Repair
Replace the Rupture Disc
Assembly
.
1. Follow the
Pressure Relief Procedure on page 15
and unplug the power cord (Z)
=
2. Remove elbow (44) from rupture disc assembly
(15).
3. Remove rupture disc assembly (15) from fitting (17).
4. Install new rupture disc assembly into fitting (17).
Use compatible liquid thread sealant or PTFE tape on connection.
5. Reinstall elbow (44) and position as shown in the image.
WLD
WLD
3A7939A 31
Parts
Parts
Model
273216
273217
Sprayer 273215
Qty.
1
1
4-Gun Manifold 273226
Qty.
1
2
Sprayer (273215) Parts
/DEHO1R
7$
&+(0,&$/+$=$5'
".HHSDZD\IURPFKLOGUHQ
"8VHRQO\WRVSUD\VXUIDFHV
'RQRWVSUD\SHRSOHRUDQLPDOV
RQGLVLQIHFWDQWODEHO
")OXVKDIWHUHDFKXVH1HYHUVWRUH
"8VHRQO\ZLWKDSSURSULDWHSHUVRQDO
SURWHFWLYHHTXLSPHQW
3(/,*5248,&2
"0DQWHQHUDOHMDGRGHORVQLV
"HORVRORSDU DURFLDUVXSHUILFLHV1RURF
SHUVRQDVRDQLPDOHV
HWLTXHWDGHOGHVLQIHFWDQWH
"(QMXDJXHGHVSXGHFDGDXVR1XQFD
DOPDFHQHGHVLQIHFWDQWHHQHOHTXLSR
6.,1,1-(&7,21+$=$5'
OLTXLGLQWRWKHERG\
".HHSFOHDURIVSUD\WLSDQGOHDNV
"'RQRWSRLQWVSUD\WLSDWDQ\RQHRU
SODFHDQ\SDUWRI\RXUERG\LQIURQWRIWLS
"1HYHUVSUD\ZLWKRXWDWLSJXDUG
"(QJDJHWULJJHUORFNZKHQQRWVSUD\LQJ
"'RQRWH[FHHGWKHPD[LPXPZRUNLQJ
SUHVVXUHRIWKHORZHVWUDWHGV\VWHP
FRPSRQHQW
")ROORZSUHVVXUHUHOLHISURFHGXUHEHIRUH
VHUYLFLQJRUFOHDQLQJ
",QFDVHRIVNLQLQMHFWLRQJHWLPPHGLDWH
3(/,*52'(,1<(&&,(1/$3,(/
DOWDSUHVLSXHGHQLQ
FXHUSR
\HFWDUIOXLGRHQHO
"0DQWJDVHDOHMDGRGHODERTXLOODGH
SXOYHUL]DFL\GHODVIXJDV
QLQJXQDSDUWHGHVXFXHUSRIUHQWHDODERTXLOOD
"1XQFDSXOYHULFHVLQODSURWHFFLGHODERTXLOOD
SXOY HUL]DQGR
"1RH[FHGDODSUHVLPLPDGHWU DEDMRGHO
FRPSRQHQWHFRQPHQRUSUHVLGHOVLVWHPD
),5($1'(;3/26,21+$=$5'
$OFRKROEDVHGRURWKHUIODPPDEOH
GLVLQIHFWDQWIXPHVFDQH[SORGHRULJQLWH
"8VHHTXLSPHQWRQO\LQZHOO
"(OLPLQDWHDOOLJQLWLRQVRXUFHV
DQWHVGHUHDOL]DUWDUHDVGHVHU
"(QFDVRGHLQ\HFFLDWU DYGHODSLHO
REWHQJD75$7$0,(17248,5*,&2GH
LQPHGLDWR
3(/,*52'(,1&(1',2<(;3/26,
/RVY DSRUHVGHVLQI HFWDQWHVDEDVHGHDOFRKRO
\RWU RVGHVLQI HFWDQWHVLQIODPDE OHVSXHGHQ
H[SORWDURHQFHQGHU VH
"8WLOLFHHOHTXLSRLFDPHQWHHQHDVELHQ
Y HQWLODGDV
"(OLPLQHWRGDIXHQWHGHLJQLFL
DWRGRHOHTXLSRGHOD]
"1RORDEUDFXDQGRHVWHQHUJL]DGR
3(/,*52'('(6&$5*$(/&75,&$
(/(&75,&6+2&.+$=$5'
"'LVFRQQHFWSRZHUVRXUFH
EHIRUHVHUYLFLQJRULQVWDOOLQJ
"6HUYLFHE\DTXDOLILHGHOHFWULFLDQ
"'RQRWH[SRVHWRUDLQ6WRUHLQGRRUV
":DLWPLQXWHVEHIRUHVHUYLFLQJ
%851+$=$5'
7RDYRLGVHYHUHEXUQV
"'RQRWWRXFKKRWIOXLGRUHTXLSPHQW
029,1*3$576+$=$5'
".HHSFOHDURIPRYLQJSDUWV
"'RQRWRSHUDWHZLWKFRYHUUHPRYHG
")ROORZSUHVVXUHUHOLHI
SRZHUVRXUFHVEHIRUH
VHUYLFLQJRUFOHDQLQJ
LQVWDODUROOHYDUDFDERWDUHDVGHVHU YLFLRWQLFR
"&RQHFWHDXQDIXHQWHGHDOLPHQWDFLFRQ
"8QHOHFWULFLVWDFDOLILFDGRGHEHOOHYDUDFDERODV
WDUHDVGHVHUYLFLRWQLFR
"1RH[SRQJDDODOOXYLD*XGHORHQXQUHFLQWR
FHUU DGR
"(VSHUHPLQXWRVDQWHVGHUHDOL]DUWDUHDVGH
VHUYLFLRWQLFR
3(/,*52'(48(0$'85$6
3DUDHYLWDUODVTXHPDGXUDVJUD YHV
"1RWRTXHIOXLGRVQLHTXLSRVFDOLHQWHV
3(/,*52'(3,(=$6(1029,0,(172
"0DQWJDVHDOHMDGRGHODVSLH]DVP
"1RXWLOLFHVLQODFXELHUWDFRORFDGD
YLOHV
"6LJDHOSURFHGLPLHQWRGHDOLYLRGHSUHVL\
GHUHDOL]DUWDUHDVGHVHUYLFLRWQLFRROLPSLH]D
5($',16758&7,210$18$/
)$,/85(72)2//2:7+,6:$51,1*
&$15(68/7,16(5,286,1-85<
$0387$7,2125'($7+
125(63(7$5(67$$'9(57(1&,$38('(
2&$6,21$5/(6,21(6*5$ 9(6
$0387$&,(,1&/862/$08(5 7(
'$1*(5&+,0,48(
"7HQLUKRUVGHSRUWGHVHQIDQWV
1HSXOYLVH]SDVGHSHUVRQQHVRXGDQLPDX[
"6XLYH]WRXWHVOHVLQVWUXFWLRQVHWFRQGLWLRQV
ILJXUDQWVXUOꏡWLTXHWWHGXGLQIHFWDQW
"5LQFH]DSUFKDTXHXWLOLVDWLRQ1HVWRFNH]
MDPDLVGHGLQIHFWDQWGDQVOXLSHPHQW
"3RUWH]XQXLSHPHQWGHSURWHFWLRQLQGLYLGXHOOH
DSSURSUL
5,648(6',1-(&7,21&87$1(
SHXYHQWLQMHFWHUGHVOLTXLGHVGDQVOHFRUSV
HWGHVIXLWHV
WGHODEXVHGHSXOY«ULVDWLRQ
"1HGLULJH]ODEXVHGHSXOY«ULVDWLRQYHUV
SHUVRQQHHWQHSODFH]DXFXQHSDUWLHGHYRWUH
FRUSVGHYDQWODEXVH
"1HMDPDLVSXOY«ULVHUVDQVODJDUGH
"9HUURXLOOH]ODJKHWWHFKDTXHDUUGHOD
SXOY «ULVDWLRQ
"1HMDPDLVGDVVHUODSUHVVLRQPD[LP
VHUYLFHGHOHQWOHSOXVI
"6XLYH]ODSURFXUHG YDFXDWLRQGHODSUHVVLRQ
DYDQWOHQWUHWLHQRXOHQHWWR\DJH
"(QFDVGLQMHFWLRQFXWDQ FRQVXOWH]
LPPLDWHPHQWXQPHFLQSRXUXQH
,17(59(17,21&+,585*,&$/(
5,648(6',1&(1',((7'(;3/26,21
/HVIXPVGHVROY DQWHWGHSHLQWXUHSHXYHQW
VHQIODPPHURXH [SORVHU
"8WLOLVH]OXLSHPHQWXQLTXHPHQWGDQVGHV
ORFDX[ELHQD
"OLPLQH]WRXWHVRXUFHGLQIODPPDWLRQ
"5DFFRUGH]ODWHUUHWRXVOHVXLSHPHQWV
VLWXGDQVOD] RQHGHWUDYDLO
"1HSDVRXYULUVLVRXVWHQVLRQ
5,648(6'('&+$5*(/(&75,4
"&RXSH]ODOLPHQWDWLRQHFWU LTXHDYDQW
8(
"%UDQFKH]VXUXQHVRXUFHGDOLPHQWDWLRQPLVH
ODWHUUH
"I DLUHHQWUHWHQLUSDUXQHFWU LFLHQTXDOLIL
(QWUHSRVH]OXLSHPHQWOꍀQW LHXU
"$WWHQGH]PLQXWHVDYDQWOHQWUHWLHQ
5,648(6'(%585(
3RXU YLWHUGHJUD YHVEUXUHV
"1HWRXFKH]SDVOHIOXLGHRXOXLSHPHQWFKDXG
5,648(65(/$7,)6$8;3,(6(1
0289(0(17
"7HQH]YRXVODU
"6XLYH]ODSURFXUHGHGRPSUHVVLRQHW
GU
WGHVSLHVHQPRXY
DQFKH]WRXWHVOHVVRXUFHVGDOLPHQWDWLRQ
DYDQWOHQWUHWLHQRXOHQHWWR\DJH
/,5(/(0$18(/'ꌙ16758&7,216
9(57,66(0(17
3(87(175$(5'(6%/(6685(6 *5$9(6
81($0387$7,2192,5(/$0257
HPHQW
Suction Tube Feed
32
WLD
Hopper Feed
3A7939A
Parts
Sprayer (273215) Parts List
19
20
21
22
23
24
25
8
9
10
11
6
7
4
5
12
13
14
15
Ref.
Part
1
2
3
17
18
Description
24Z852 CART, heavy duty, painted
19B547 LABEL, SaniSpray HP750
19B619 SPACER, mounting, threaded, sst
273199 MOTOR, assy, SaniSpray
103975 WASHER, lock
112913 NUT, hex
15K296 SPACER, painted
19B621 ROD, tie, sst
247599 PUMP
102216 NUT, lock
15H371 ADAPTER, m38 x 2
184130 COLLAR, coupling
19B628 NUT, coupling
113361 CAP, tube, round
273220 HOUSING, rupture disc, assembly
19B638 FITTING, elbow, 90 degree, reducing
19B627 BRACKET, hopper, upper, painted
19B624 BRACKET, hopper, painted
113362 WHEEL, semi-pneumatic
154628 WASHER
113436 RING, retaining
17V628 SCREW, cap, hex head
19B620 FITTING, cam and groove, sst
19B625 FITTING, cam/groove, 1.5m,
1-1/2 npt
Qty.
1
1
4
1
1
1
1
2
4
1
2
2
3
1
3
1
8
1
1
4
2
1
2
1
Ref.
Part Description
26
31
33
38
39
40
41
42
124445 FITTING, coupling, 1-1/2 nptf, ss
17E114 HOPPER, weldment, xtreme
214959 HOSE, coupled
121239 BUSHING, 1.5 x 1 npt reducer. sst
121245 FITTING, swivel, 1 x 1 npt
102901 TEE, pipe
206994 FLUID, TSL 8 oz bottle
235208 FITTING, union, swivel
44 127947 FITTING, elbow, male, 90 deg.
47 19B639 VALVE, check, 3/8, male x male
48 25T414 LABEL, warning
49
50
51
70
71
72
17K431 KIT, error code labels, translated
EQ1582 FITTING, elbow, street, 1-1/2 npt, ss
17U928 CORD, power, l6-30p
19B630 TUBE, suction
19B629 TUBE, intake
123996 COUPLING, 1 in. npt, ss
73 187147 STRAINER, inlet
103 110740 PLUG, pipe
Qty.
1
1
1
1
1
1
1
1
1
1
1
3
1
1
1
1
1
1
1
Replacement safety labels, tags, and cards are available at no cost.
3A7939A 33
Parts
4-Gun Manifold (273226) Parts
WLD
34 3A7939A
Parts
4-Gun Manifold (273226) Parts List
Ref.
Part Description
101 108673 TEE, street
102 235208 FITTING, union, swivel
103 110740 PLUG, pipe
104 235992 VALVE, ball
105 070408 SEALANT, pipe, sst
106 25R874 GUN, SaniSpray hp
107 26B143 EXTENSION, tip, 15 in., e-n, assy
Qty.
1
4
4
1
4
4
3
Ref.
Part Description
108 25R880 KIT, tip, seat, hp, LP (617), LP
(621)
109 LP723 TIP, spray, LP (723)
110 240797 HOSE, coupled, 3/8 in. x 50 ft
111 223771 HOSE, cpld, 1/4 in. x 100 ft
112 19Y494 HOSE, cpld, 1/8 in. x 4-1/2 ft
113 121907 FITTING, nipple, hex, 1/4 npt, sst, swv
114 LP631 TIP, spray, LP (631)
Qty.
4
12
4
4
1
8
4
3A7939A 35
Dimensions
Dimensions
A
•
Ref.
A Height
B Depth
C Width
Dimensions
50.0 in. (1.27 m)
30.0 in. (0.76 m)
26.0 in. (0.66 m)
C
36
B
WLD
3A7939A
Technical Specifications
Technical Specifications
SaniSpray HP 750 Sprayer
Maximum Disinfectant Working Pressure
Stroke Length
Maximum Continuous Cycle Rate
Maximum Tip Size
Wetted Parts
Maximum Disinfectant Temperature
Operating Temperature Range
Input Voltage
Input Current
Minimum Recommended Generator Size
Oil Capacity
Oil Specification
Weight
273215 - SaniSpray HP 750
Sound Emissions for Normal Operation (<20 cpm)
Sound Pressure
Sound Power*
* Sound power levels were tested per ISO 3744
Inlet / Outlet Sizes
Disinfectant Inlet Sizes
Disinfectant Outlet Size
US
1150 psi
4.75 in.
33 cycles per minute
Metric
79 bar, 7.9 MPa
120 mm
0.031 in.
stainless steel, PTFE, acetal, UHMWPE, anodized aluminum, fluoroelastomer, urethane, nylon
120 °F
23 to 120 °F
50 °C
-5 to 50 °C
200-240 VAC, single phase, 50/60 Hz
20 A maximum
5 kW
1.0 to 1.2 quarts 0.9 to 1.1 liters
Graco part number 16W645 silicone-free
ISO 220 synthetic EP gear oil
308 lb
87 dBa
78 dBa
1-1/2 in. npt(f)
140 kg
1 in. npt(f) to 3/8 in. npt(m) adapter
Recycling and Disposal
End of Product Life
At the end of the product’s useful life, dismantle and recycle it in a responsible manner.
• Follow the
Pressure Relief Procedure on page 15.
• Drain and dispose of fluids according to applicable regulations. Refer to the material manufacturer’s
Safety Data Sheet.
• Remove motors, circuit boards, and other electronic components. Recycle according to applicable regulations.
• Do not dispose of electronic components with household or commercial waste.
• Deliver remaining product to a recycling facility.
California Proposition 65
CALIFORNIA RESIDENTS
WARNING: Cancer and reproductive harm – www.P65warnings.ca.gov.
3A7939A 37
Graco Warranty
Graco warrants all equipment referenced in this document which is manufactured by Graco and bearing its name to be free of defects in material and workmanship on the date of sale by an authorized Graco distributor to the original purchaser for use. Graco will, for a period of ninety (90) days from the date of sale, provide repair parts for equipment determined by Graco to be defective. This warranty applies only when the equipment is installed, operated and maintained in accordance with Graco’s written recommendations.
This warranty does not cover, and Graco shall not be liable for general wear and tear, or any malfunction, damage or wear caused by faulty installation, misapplication, abrasion, corrosion, inadequate or improper maintenance, negligence, accident, tampering, or substitution of non-Graco component parts. Nor shall Graco be liable for malfunction, damage or wear caused by the incompatibility of Graco equipment with structures, accessories, equipment or materials not supplied by Graco, or the improper design, manufacture, installation, operation or maintenance of structures, accessories, equipment or materials not supplied by Graco.
THIS WARRANTY IS EXCLUSIVE, AND IS IN LIEU OF ANY OTHER WARRANTIES, EXPRESS OR IMPLIED, INCLUDING BUT NOT LIMITED
TO WARRANTY OF MERCHANTABILITY OR WARRANTY OF FITNESS FOR A PARTICULAR PURPOSE .
Graco’s sole obligation and buyer’s sole remedy for any breach of warranty shall be as set forth herein. The buyer agrees that no other remedy
(including, but not limited to, incidental or consequential damages for lost profits, lost sales, injury to person or property, or any other incidental or consequential loss) shall be available. Any action for breach of warranty must be brought within two (2) years of the date of sale.
GRACO MAKES NO WARRANTY, AND DISCLAIMS ALL IMPLIED WARRANTIES OF MERCHANTABILITY AND FITNESS FOR A
PARTICULAR PURPOSE, IN CONNECTION WITH ACCESSORIES, EQUIPMENT, MATERIALS OR COMPONENTS SOLD BUT NOT
MANUFACTURED BY GRACO .
These items sold, but not manufactured by Graco (such as electric motors, switches, hose, etc.), are subject to the warranty, if any, of their manufacturer. Graco will provide purchaser with reasonable assistance in making any claim for breach of these warranties.
IN NO EVENT WILL GRACO BE LIABLE FOR INDIRECT, INCIDENTAL, SPECIAL OR CONSEQUENTIAL DAMAGES RESULTING FROM
GRACO SUPPLYING EQUIPMENT HEREUNDER, OR THE FURNISHING, PERFORMANCE, OR USE OF ANY PRODUCTS OR OTHER
GOODS SOLD HERETO, WHETHER DUE TO A BREACH OF CONTRACT, BREACH OF WARRANTY, THE NEGLIGENCE OF GRACO, OR
OTHERWISE.
FOR GRACO NORTH AMERICA CUSTOMERS
Please call 1-844-241-9499 or visit www.graco.com/techsupport regarding any potential defect in equipment under warranty. If the claimed defect is verified, Graco will either, at its discretion, send repair parts for owner installation or replace the product, free of charge. Warranty claims and/or service for this product are not administrated by Graco’s distributors or service centers for Graco paint equipment.
FOR GRACO EUROPE, MIDDLE EAST AND AFRICA CUSTOMERS
Please contact your regional service center or authorized distributor to administer a warranty claim.
FOR GRACO CANADA CUSTOMERS
The Parties acknowledge that they have required that the present document, as well as all documents, notices and legal proceedings entered into, given or instituted pursuant hereto or relating directly or indirectly hereto, be drawn up in English. Les parties reconnaissent avoir convenu que la rédaction du présente document sera en Anglais, ainsi que tous documents, avis et procédures judiciaires exécutés, donnés ou intentés, à la suite de ou en rapport, directement ou indirectement, avec les procédures concernées.
Graco Information
For the latest information about Graco products, visit www.graco.com
.
For patent information, see www.graco.com/patents .
TO PLACE AN ORDER, contact your Graco distributor or call to identify the nearest distributor.
Phone: 612-623-6921 or Toll Free: 1-800-328-0211, Fax: 612-378-3505
All written and visual data contained in this document reflects the latest product information available at the time of publication.
Graco reserves the right to make changes at any time without notice.
Original instructions. This manual contains English. MM 3A7939
Graco Headquarters:
Minneapolis
International Offices: Belgium, China, Japan, Korea
GRACO INC. AND SUBSIDIARIES • P.O. BOX 1441 • MINNEAPOLIS MN 55440-1441 • USA
Copyright 2020, Graco Inc. All Graco manufacturing locations are registered to ISO 9001.
www.graco.com
Revision A, July 2020
advertisement
* Your assessment is very important for improving the workof artificial intelligence, which forms the content of this project
Related manuals
advertisement
Table of contents
- 2 Related Manuals
- 2 Models
- 3 Important User Information
- 3 KNOW YOUR DISINFECTANT’S
- 3 ACTIVE INGREDIENTS
- 4 Warnings
- 7 Component Identification
- 8 Installation
- 8 Grounding
- 9 Connect Power
- 9 Extension Cords
- 9 Install Vented Oil Cap Before Using Equipment
- 10 Setup
- 10 Flush Before Using the Sprayer
- 11 Disinfectant Supply Options
- 11 Remove the Hopper
- 11 Connect the Suction Tube
- 11 Connect the Hopper
- 12 Gun and Hose Setup Options
- 12 Connect Hose(s) and Gun(s)
- 15 Trigger Lock
- 15 Pressure Relief Procedure
- 16 Prime the Sprayer
- 17 Choose Your Spray Tip
- 18 Spray
- 19 Clear Tip Clog
- 20 Flushing and Cleaning
- 21 Clean the Guns
- 22 Shutdown / Storage
- 23 Maintenance
- 23 Preventative Maintenance Schedule
- 24 Daily Maintenance
- 25 Troubleshooting
- 27 Error Code Troubleshooting
- 29 Repair
- 29 Disconnect the Pump
- 30 Reconnect the Pump
- 31 Replace the Rupture Disc Assembly
- 32 Parts
- 32 Sprayer (273215) Parts
- 34 4-Gun Manifold (273226) Parts
- 36 Dimensions
- 37 Technical Specifications
- 37 Recycling and Disposal
- 37 End of Product Life
- 37 California Proposition 65
- 38 Graco Warranty