- Home
- Do-It-Yourself tools
- Power tools
- Paint Sprayer
- Graco
- 3A7653D, SaniSpray HP™ 65 Portable Hopper Sprayer
- Owner's manual
advertisement
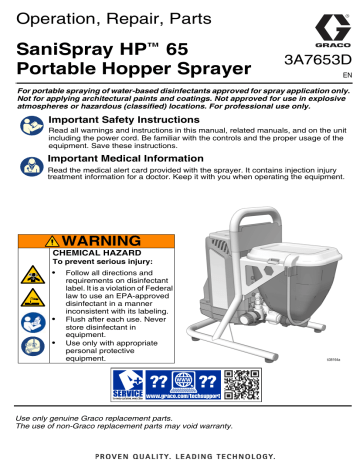
Operation, Repair, Parts
SaniSpray HP
™
65
Portable Hopper Sprayer
3A7653D
EN
For portable spraying of water-based disinfectants approved for spray application only.
Not for applying architectural paints and coatings. Not approved for use in explosive atmospheres or hazardous (classified) locations. For professional use only.
Important Safety Instructions
Read all warnings and instructions in this manual, related manuals, and on the unit including the power cord. Be familiar with the controls and the proper usage of the equipment. Save these instructions.
Important Medical Information
Read the medical alert card provided with the sprayer. It contains injection injury treatment information for a doctor. Keep it with you when operating the equipment.
WARNING
CHEMICAL HAZARD
To prevent serious injury:
• Follow all directions and requirements on disinfectant label. It is a violation of Federal law to use an EPA-approved disinfectant in a manner inconsistent with its labeling.
• Flush after each use. Never store disinfectant in equipment.
• Use only with appropriate personal protective equipment.
??
??
www.graco.com/techsupport
Use only genuine Graco replacement parts.
The use of non-Graco replacement parts may void warranty .
2
Contents
Contents
Important User Information . . . . . . . . . . . . . . . . . . . . . . . . . . . . . . . . . . 4
Power Requirements . . . . . . . . . . . . . . . . . . . . . . . . . . . . . . . . . . . . 10
Extension Cords . . . . . . . . . . . . . . . . . . . . . . . . . . . . . . . . . . . . . . . 10
Pressure Relief Procedure . . . . . . . . . . . . . . . . . . . . . . . . . . . . . . . . 12
Flushing a New Sprayer . . . . . . . . . . . . . . . . . . . . . . . . . . . . . . . . . 14
Fill Spray Gun and Airless Hose . . . . . . . . . . . . . . . . . . . . . . . . . . . 16
Choose Your Spray Tip . . . . . . . . . . . . . . . . . . . . . . . . . . . . . . . . . . 17
Spray Tip Orientation . . . . . . . . . . . . . . . . . . . . . . . . . . . . . . . . . . . . 18
Starting Your Spray and Adjusting Pressure . . . . . . . . . . . . . . . . . . 18
Clear Tip Clog . . . . . . . . . . . . . . . . . . . . . . . . . . . . . . . . . . . . . . . . . 19
Clean the Gun . . . . . . . . . . . . . . . . . . . . . . . . . . . . . . . . . . . . . . . . . 21
Quick Reference . . . . . . . . . . . . . . . . . . . . . . . . . . . . . . . . . . . . . . . 23
Airless Hoses . . . . . . . . . . . . . . . . . . . . . . . . . . . . . . . . . . . . . . . . . . 24
Pump Repair . . . . . . . . . . . . . . . . . . . . . . . . . . . . . . . . . . . . . . . . . . 24
Pump Removal . . . . . . . . . . . . . . . . . . . . . . . . . . . . . . . . . . . . . . . . 24
Pump Installation . . . . . . . . . . . . . . . . . . . . . . . . . . . . . . . . . . . . . . . 25
Inlet Valve Removal . . . . . . . . . . . . . . . . . . . . . . . . . . . . . . . . . . . . . 26
Recycling and Disposal . . . . . . . . . . . . . . . . . . . . . . . . . . . . . . . . . . . . 26
End of Product Life . . . . . . . . . . . . . . . . . . . . . . . . . . . . . . . . . . . . . 26
Parts - SaniSpray HP 65 (Quick Repair) . . . . . . . . . . . . . . . . . . . . . . . 30
Parts - SaniSpray HP 65 (Extended Repair) . . . . . . . . . . . . . . . . . . . . 32
Parts - SaniSpray HP 65 (Pump Repair) . . . . . . . . . . . . . . . . . . . . . . . 33
Technical Specifications . . . . . . . . . . . . . . . . . . . . . . . . . . . . . . . . . . . 36
California Proposition 65 . . . . . . . . . . . . . . . . . . . . . . . . . . . . . . . . . . . 37
3A7653D
Models
VAC Model
110474
Certified to
CAN/CSA
C22.2 No. 68
Conforms to
UL 1450
120
USA
230
CEE 7/7
230 Europe Multi
25R792
25R946
25R948
240 AP Multi 25R954
100 JP/TW 25R962
Maximum Working Pressure: 1000 psi (6.9 MPa, 69 bar)
Models
3A7653D 3
4
Important User Information
Important User Information
Before using your disinfectant sprayer, read this manual for complete instructions on proper use and safety warnings.
The sprayer is designed to spray disinfectants that are water-based and clean up with water.
You must also read and follow the information on the disinfectant container label and ask for a Safety
Data Sheet (SDS) from your supplier. The container label and SDS will explain the contents of the material, instructions for use and the specific precautions related to the contents of the material.
Those precautions include personal protective equipment (PPE).
KNOW YOUR DISINFECTANT’S
ACTIVE INGREDIENTS
For the purpose of safely using this sprayer, you need to know what kind of active ingredients are in the disinfectant. Look on the container label for the list of active ingredients. There are two categories:
ALCOHOL: This type of disinfectant contains flammable active ingredients such as ethanol (ethyl alcohol) or isopropanol (IPA). The container label should indicate that this material is COMBUSTIBLE or FLAMMABLE. Your sprayer is compatible with this type of material. Use flammable materials in a well-ventilated area with a flow of fresh air. See the safety warnings in this manual.
NON-ALCOHOL: This type of disinfectant contains active ingredients such as aldehydes, phenols, quaternary ammonium compounds, sodium hypochlorite
(bleach), peroxyacetic acid, hydrogen peroxide, and hypochlorous acid. Your sprayer is compatible with this type of material.
3A7653D
Warnings
Warnings
The following warnings are for the setup, use, grounding, maintenance, and repair of this equipment. The exclamation point symbol alerts you to a general warning and the hazard symbols refer to procedure-specific risks. When these symbols appear in the body of this manual or on warning labels, refer back to these Warnings. Product-specific hazard symbols and warnings not covered in this section may appear throughout the body of this manual where applicable.
WARNING
CHEMICAL HAZARD
Toxic disinfectant or fumes can cause serious injury or death if splashed in the eyes or on skin, inhaled, or swallowed.
• Keep away from children.
• Use only to spray surfaces. Do not spray humans or animals.
•
Use only with appropriate personal protective equipment. See PERSONAL PROTECTIVE
• Follow all directions and requirements on disinfectant label. It is a violation of Federal law to use an EPA-approved disinfectant in a manner inconsistent with its labeling.
• Flush with water after each use. Never store disinfectant in equipment.
• Read Safety Data Sheets (SDSs) to know the specific hazards of the disinfectants you are using.
• Store and dispose of disinfectants according to instructions on disinfectant container labels.
3A7653D
SKIN INJECTION HAZARD
High-pressure spray is able to inject toxins into the body and cause serious bodily injury that can result in amputation. In the event that injection occurs, get immediate surgical treatment.
• Use only to spray surfaces. Do not spray humans or animals.
• Do not point spray tip at anyone or place any part of your body in front of tip. For example, do not try to stop leaks with any part of the body.
• Always use the spray tip guard. Do not spray without spray tip guard in place. Use only
Graco spray tips.
• Use caution when cleaning and changing spray tips. In the case where the spray tip clogs while spraying, follow the
Pressure Relief Procedure , page 12, for relieving the pressure
before removing the spray tip to clean.
• Equipment maintains pressure after power is shut off. Do not leave the equipment energized or under pressure while unattended. Unplug the sprayer and follow the
Pressure Relief Procedure , page 12, when the equipment is unattended or not in use,
and before servicing, cleaning, or removing parts.
• Check hoses and parts for signs of damage. Replace any damaged hoses or parts.
• This system is capable of producing 1000 psi (69 bar, 6.9 MPa). Use Graco parts or accessories that are rated a minimum of 1000 psi (69 bar, 6.9MPa).
• Always engage the trigger lock when not spraying. Verify the trigger lock is functioning properly.
• Verify that all connections are secure before operating the unit.
• Know how to stop the unit and bleed pressure quickly. Be thoroughly familiar with the controls.
5
6
Warnings
WARNING
FIRE AND EXPLOSION HAZARD
Flammable fumes, such as disinfectants, in work area can ignite or explode. To help prevent fire and explosion:
• Do not spray flammable disinfectants near an open flame or sources of ignition such as cigarettes, motors, and electrical equipment.
• Disinfectants flowing through the equipment are able to result in static electricity. Static electricity creates a risk of fire or explosion in the presence of disinfectant fumes. All parts of the spray system, including the pump, hose assembly, spray gun, and objects in and around the spray area shall be properly grounded to protect against static discharge and sparks. Use Graco conductive or grounded high-pressure airless sprayer hoses.
• Verify that all containers and collection systems are grounded to prevent static discharge.
Do not use pail liners unless they are anti-static or conductive.
• Connect to a grounded outlet and use grounded extensions cords. Do not use a 3-to-2 adapter.
• Keep spray area well-ventilated. Keep a good supply of fresh air moving through the area.
• Sprayer generates sparks. Keep pump assembly in a well ventilated area a least 20 feet
(6.1 m) from the spray area when spraying, flushing, cleaning, or servicing. Do not spray pump assembly.
• Do not smoke in the spray area or spray where sparks or flame is present.
• Do not operate light switches, engines, or similar spark producing products in the spray area.
• Keep area clean and free of disinfectant containers, rags, and other flammable materials.
• Know the contents of the disinfectants being sprayed. Read all Safety Data Sheet (SDS) and container labels provided with the disinfectants. Follow the disinfectant manufacturer’s safety instructions.
• Keep a working fire extinguisher in the work area.
EQUIPMENT MISUSE HAZARD
Misuse can cause death or serious injury.
• Do not operate or spray near children. Keep children away from equipment at all times.
• Do not overreach or stand on an unstable support. Keep effective footing and balance at all times.
• Stay alert and watch what you are doing.
• Do not operate the unit when fatigued or under the influence of drugs or alcohol.
• Do not kink or over-bend the hose.
• Do not expose the hose to temperatures or to pressures in excess of those specified by
Graco.
• Do not use the hose as a strength member to pull or lift the equipment.
• Do not spray with a hose shorter than 25 feet.
• Do not alter or modify equipment. Alterations or modifications may void agency approvals and create safety hazards.
• Make sure all equipment is rated and approved for the environment in which you are using it.
3A7653D
3A7653D
Warnings
WARNING
ELECTRIC SHOCK HAZARD
This equipment must be grounded .
Improper grounding, setup, or usage of the system can cause electric shock.
• Turn off and disconnect power cord before servicing equipment.
• Connect only to grounded electrical outlets.
• Use only 3-wire extension cords.
• Ensure ground prongs are intact on power and extension cords.
• Do not get wet or expose to rain. Store indoors.
• Wait five minutes after disconnecting power cord before servicing.
MOVING PARTS HAZARD
Moving parts can pinch, cut, or amputate fingers and other body parts.
• Keep clear of moving parts.
• Do not operate equipment with protective guards or covers removed.
• Pressurized equipment can start without warning. Before checking, moving, or servicing equipment, follow the Pressure Relief Procedure and disconnect all power sources.
PERSONAL PROTECTIVE EQUIPMENT
Wear appropriate protective equipment when in the work area to help prevent serious injury, including eye injury, burns, hearing loss, and inhalation of disinfectant chemical mists and vapors. Protective equipment includes but is not limited to:
• Protective eye-wear, and hearing protection.
• Appropriate respirators, protective clothing, and gloves.
• All protective equipment specified by the disinfectant manufacturer.
7
8
Warnings
WARNING
GROUNDING
This product must be grounded. In the event of an electrical short circuit, grounding reduces the risk of electric shock by providing an escape wire for the electric current. This product is equipped with a cord having a grounding wire with an appropriate grounding plug. The plug must be plugged into an outlet that is properly installed and grounded in accordance with all local codes and regulations.
• Improper installation of the grounding plug is able to result in a risk of electric shock.
• This product is for use on a nominal 120V or 230V circuit and has a grounding plug similar to the plug illustrated below.
120V US 230V 230V ANZ ti24583b
• Only connect the product to an outlet having the same configuration as the plug.
• Do not modify the plug provided; if it does not fit the outlet, have the proper outlet installed by a qualified electrician.
• Do not use an adapter with this product.
• When repair or replacement of the cord or plug is required, do not connect the grounding wire to either power terminal.
• The wire with insulation having an outer surface that is green with or without yellow stripes is the grounding wire.
• Check with a qualified electrician or serviceman when the grounding instructions are not completely understood, or when in doubt as to whether the product is properly grounded.
Extension Cords:
• Use only a 3-wire extension cord that has a grounding plug and a grounding receptacle that accepts the plug on the product.
• When using the sprayer outdoors, use an extension cord suitable for outdoor use.
• Make sure your extension cord is not damaged.
• When using an extension cord, be sure to use a cord heavy enough to carry the current that your sprayer draws. An undersized cord results in a drop in line voltage and loss of power and overheating. When in doubt use the next heavier gauge. The smaller the gauge number the heavier the cord. See chart for appropriate sizes and lengths:
Conductor Size
AWG (American Wire Gauge)
16
12
Metric
1.5 mm 2
2.5 mm 2
Length
Maximum
25 ft. (8 m)
50 ft. (15 m)
3A7653D
Know Your Sprayer
Know Your Sprayer
A Prime/Spray Valve
B PushPrime Button
C Pressure Control Knob
D ON/OFF Switch
E Hopper
F Drain Tube (with diffuser)
G SaniSpray HP Airless Spray Gun
H Spray Tip
J Spray Tip Guard
L Hose Guard
N ProXChange™ Pump (behind Easy
Access Door)
P Fluid Outlet Fitting (Airless Hose connection)
Q Airless Hose
R Airless Whip Hose
U Power Cord
V Easy Access Door
X Pump Removal Tool
Z Inlet Valve Removal Tool
Inlet Strainer, inside hopper (not shown)
Model/Serial Tag, bottom of unit (not shown)
See
Quick Reference , page 23, for more
information.
3A7653D 9
Grounding
Grounding
Grounded surface method: Place pail on a grounded surface such as concrete. Do not place pail on a non-conductive surface such as paper or cardboard which interrupts grounding continuity.
The equipment must be grounded to reduce the risk of static sparking and electric shock. An electric or static spark can cause fumes to ignite or explode. An improper ground can cause electric shock.
A good ground provides an escape wire for the electric current.
This sprayer is equipped with a Power Cord that has a ground wire and an appropriate grounding plug.
The plug must be plugged into an outlet that is properly installed and grounded in accordance with all local codes and ordinances.
Do not modify the plug provided; if it does not fit the outlet, have the proper outlet installed by a qualified electrician.
Power Requirements
• 100-120V units require 100-120 VAC,
50/60 Hz, 8A, 1 phase.
• 230V units require 220-240 VAC, 50/60
Hz, 5A.
Extension Cords
Use an extension cord with an undamaged ground contact. If an extension cord is necessary, use a 3-wire, 12 AWG (2.5mm
2 minimum.
)
NOTE: Smaller gauge or longer extension cords may reduce sprayer performance.
Pails
For disinfectants with alcohol active ingredients: Follow local code. Use only conductive metal pails. Ground the metal pail by either placing it on a grounded surface, or by attaching a ground wire.
Ground wire method: Connect a ground wire to the pail. Clamp one end to the pail and the other end to a true earth ground such as a water pipe.
ti24584a
To maintain ground continuity when sprayer is flushed or pressure is relieved:
Hold metal part of Spray Gun firmly to the side of a grounded metal pail then trigger the
Spray Gun.
10 3A7653D
Setup
Setup
3.
Insert other end of Airless Whip Hose through Hose Guard at base of Spray
Gun. Connect to Spray Gun. Use wrenches to tighten securely.
When unpacking sprayer for the first time or after long term storage, perform Setup procedure.
1.
Connect 1/4” Graco Airless Hose to Fluid
Outlet Fitting (remove red storage plug from fitting if present). Use wrenches to tighten securely.
4.
Remove Spray Tip Guard assembly from Spray Gun.
2.
Assemble optional 1/8” Airless Whip
Hose to end of 1/4” Airless Hose. Use wrenches to tighten securely.
3A7653D 11
Start Up
Start Up
2.
Engage the Trigger Lock. Always engage the Trigger Lock when sprayer is stopped to prevent the Spray Gun from being triggered accidentally.
Pressure Relief Procedure
Follow the Pressure Relief
Procedure whenever you see this symbol.
This equipment stays pressurized until pressure is manually relieved. To help prevent serious injury from pressurized fluid, such as skin injection or splashing fluid, follow the Pressure Relief
Procedure whenever sprayer is stopped and before sprayer is cleaned or checked, and before equipment is serviced.
1.
Turn ON/OFF Switch to the OFF position.
3.
Turn Pressure Control Knob to the lowest setting.
12 3A7653D
4.
Put Drain Tube in a pail and turn
Prime/Spray Valve horizontal to PRIME position to relieve pressure.
5.
Hold a metal part of the Spray Gun firmly to a grounded metal pail. Point Spray Gun into pail. Disengage the Trigger Lock and trigger the Spray Gun to relieve pressure.
Start Up
7.
If you suspect the Spray Tip or hose is clogged or that pressure has not been fully relieved: a.
VERY SLOWLY loosen the Spray
Tip Guard retaining nut or the
Airless Hose end coupling to relieve pressure gradually.
b.
Loosen the nut or coupling completely.
c.
Clear Airless Hose or Spray Tip obstruction.
Trigger Lock
Always engage the Trigger Lock when sprayer is stopped to prevent the Spray from being triggered accidentally by hand or if dropped or bumped.
6.
Engage the Trigger Lock.
3A7653D 13
Start Up
Flushing a New Sprayer
This sprayer arrives from the factory with a small amount of test fluid in the system. It is important that you flush this fluid from the sprayer before using it for the first time.
1.
Perform Pressure Relief Procedure , page 12.
2.
Make certain ON/OFF Switch is OFF .
c.
Pour approximately two quarts of warm soapy water into the Hopper.
3.
Turn Prime/Spray Valve horizontal to
PRIME position.
a.
Lift Drain Tube with retainer off the
Hopper.
4.
Plug power supply cord into a properly grounded electrical outlet.
b.
While holding the Drain Tube retainer with the Drain Tube parallel to the top of a waste bucket, twist retainer over the lip of the container. Drain Tube should now be inside the waste bucket.
ti24651a
5.
Press PushPrime Button twice to loosen inlet ball.
14 ti27268a
3A7653D
6.
Turn ON/OFF Switch to ON position.
7.
Rotate Pressure Control Knob clockwise until the pump turns on.
Start Up
Fill Pump
Refer to disinfectant label for manufacturer’s directions on proper use. If dilution is required, properly dilute disinfectant prior to use.
1.
Add properly prepared disinfectant to the
Hopper.
2.
Turn ON/OFF Switch to ON position.
3.
Wait to see disinfectant coming out of the
Drain Tube.
4.
Turn ON/OFF Switch to OFF position.
NOTE: Pump may prime faster if the
ON/OFF Switch is momentarily turned off so the pump can slow and stop.
Turn ON/OFF Switch on and off several times if necessary.
8.
When sprayer starts pumping, water and air bubbles will be purged from system.
Allow fluid to flow out of Drain Tube and into waste bucket until Hopper is nearly empty.
9.
Turn ON/OFF Switch to OFF position.
3A7653D 15
Start Up
Fill Spray Gun and Airless
Hose
1.
Hold Spray Gun against grounded metal waste bucket. Point Spray Gun into waste bucket.
a.
Disengage Trigger Lock. b.
Pull and hold Spray Gun trigger.
c.
Turn Prime/Spray Valve up to
SPRAY position.
d.
Turn ON/OFF Switch to ON position.
4.
Inspect Airless Hose connections for leaks. If leaks occur, perform
Relief Procedure , page 12, then tighten
all fittings and repeat
. If there are no leaks, continue with the next step.
5.
Clip Drain Tube to Hopper.
2.
Trigger Spray Gun into waste bucket until only disinfectant comes out.
3.
Release trigger. Engage Trigger Lock.
High-pressure spray is able to inject toxins into the body and cause serious bodily injury. Do not stop leaks with hand or rag.
NOTE: When motor stops, sprayer is pressurized. If motor continues to run, sprayer is
not properly primed, repeat Fill Pump
and
Fill Spray Gun and Airless Hose , page 16.
16 3A7653D
How to Spray
How to Spray
2.
Use Spray Tip (A) to align TipSeal TM (B)
(gasket and seal) into the Spray Tip
Guard (C).
Use only disinfectants approved for spray application.
Fumes from disinfectants with alcohol active ingredients, or from other flammable disinfectants, can explode or ignite . Pump motor generates sparks. To help prevent fumes from exploding or igniting:
• Keep pump at least 20 ft from spray area.
• Do not spray pump.
• Keep spray area well-ventilated.
• Keep a good supply of fresh air moving through the area.
Choose Your Spray Tip
3.
Insert Spray Tip into Spray Tip Guard.
Verify Spray Tip is forward in the SPRAY position.
To avoid serious injury from skin injection, do not put your hand in front of the Spray
Tip when installing or removing the Spray
Tip and Spray Tip Guard.
Your sprayer comes with 3 Spray Tip sizes:
Fine
Medium
Coarse
LP515
LP617
LP619
Select the appropriate Spray Tip size to provide the acceptable spray of disinfectant. Refer to the disinfectant label for manufacturer’s recommendations.
To prevent Spray Tip leaks, make certain
Spray Tip and Spray Tip Guard are installed properly.
1.
Perform
Pressure Relief Procedure , page 12.
4.
Screw Spray Tip Guard assembly onto
Spray Gun and tighten.
3A7653D
NOTE: Spray Tip will wear with use and need periodic replacement.
17
How to Spray
Spray Tip Orientation
To avoid serious injury from skin injection, do not put your hand in front of the Spray
Tip Guard when rotating it.
Adjust the Spray Tip Guard for desired vertical or horizontal spraying direction.
Starting Your Spray and
Adjusting Pressure
Always refer to the disinfectant manufacturer’s recommendations for an acceptable spray of disinfectant.
1.
Point Spray Gun towards the surface to be sprayed.
2.
Confirm the Pressure Control Knob is at the lowest setting.
3.
Disengage Trigger Lock.
4.
Pull and hold Spray Gun trigger.
5.
Slowly increase pressure using the
Pressure Control Knob. Set to the minimum setting necessary to produce an acceptable spray of disinfect. This will help reduce overspray.
6.
Adjust the Spray Gun’s distance from the surface and your hand speed to achieve the desired surface coverage.
18 3A7653D
Clear Tip Clog
To avoid injury, never point gun at your hand or into a rag!
In the event debris clogs the Spray Tip, the
Spray Gun is designed with a reversible Spray
Tip that quickly and easily clears the particles without disassembling the Spray Gun.
1.
Release Trigger. Engage Trigger Lock.
Rotate Spray Tip to UNCLOG position.
Disengage Trigger Lock. Trigger Spray
Gun in waste bucket to clear clog.
UNCLOG
How to Spray
2.
Engage Trigger Lock. Rotate Spray Tip back to SPRAY position. Disengage
Trigger Lock and continue spraying.
SPRAY
3A7653D 19
Cleanup
Cleanup
Cleaning the sprayer is required after each use to remove any disinfectants and residues from the sprayer. It will also help ensure a trouble free start up the next time the sprayer is used.
4.
Remove Drain Tube from Hopper, wipe excess disinfectant from outside of Drain
Tube and inside of Hopper.
Use only water for cleaning.
Clean in a well-ventilated area.
Keep a good supply of fresh air moving through the area.
NOTICE
Disinfectant left in sprayer will damage the sprayer. To avoid damage, always completely flush with warm soapy water
after every use. See Cleanup , page 20. Do
not store sprayer with disinfectant in it.
1.
Perform Pressure Relief Procedure , page 12.
2.
Pour any remaining disinfectant out of the Hopper into waste bucket.
3.
Remove Spray Tip Guard and Spray Tip.
For additional information, see
5.
Place Drain Tube in waste bucket. For disinfectants with alcohol active ingredients, ground the bucket according to
ti27268a
6.
Pour warm soapy water into the Hopper.
7.
Turn ON/OFF Switch to ON position.
8.
Rotate Pressure Control Knob clockwise until the pump turns on.
20 3A7653D
9.
Allow water to flow out of drain tube and into waste bucket until approximately 1/3 of the water is emptied from the Hopper.
10. Turn ON/OFF Switch to OFF position.
NOTE:
Step 11 is for removing disinfectant
from the Airless Hose. One 50 ft Airless
Hose holds approximately 1 quart of fluid.
11. To remove disinfectant from Airless
Hose: a.
Hold Spray Gun against waste bucket.
b.
Disengage Trigger Lock.
c.
Pull and hold Spray Gun trigger.
d.
Turn Prime/Spray Valve up to
SPRAY position.
e.
Turn ON/OFF switch to ON position.
Cleanup
13. Stop triggering Spray Gun. Engage the
Trigger Lock.
14. Turn Prime/Spray Valve horizontal to
PRIME position.
*
12. Continue triggering Spray Gun into waste bucket until all water is emptied from the Hopper and Airless Hose.
15. Turn ON/OFF Switch to OFF position.
16. Dispose of the fluid in the waste bucket according to the instructions on the disinfectant container label and applicable regulations.
Clean the Gun
1.
Remove Spray Tip and Spray Tip Guard assembly. Clean with water and a brush.
3A7653D
2.
Wipe sprayer, Airless Hose, and Spray
Gun with soft cloth moistened with water.
21
Storage
Storage
With proper storage, the sprayer will be ready to use the next time it is needed.
NOTICE
Disinfectant left in sprayer will damage the sprayer. To avoid damage, always completely flush with warm soapy water after every use. See
not store sprayer with disinfectant in it.
• Before storing sprayer, make sure all water is drained out of sprayer and
Airless Hose.
• Do not allow water to freeze in sprayer or
Airless Hose.
• Do not store sprayer under pressure.
• Store sprayer indoors.
22 3A7653D
Storage
Quick Reference
B
C
D
E
F
J
K
L
N
P
Q
T
U
V
A Prime/Spray Valve
G
H
X
Z
Description
• In PRIME position directs fluid to Drain Tube.
• In SPRAY position directs pressurized fluid to
Airless Hose.
• Automatically relieves system pressure in overpressure situations.
Taps the inlet ball when pushed to loosen it.
PushPrime Button
Pressure Control Knob
ON/OFF Switch
Hopper
Drain Tube
Increases (clockwise) and decreases
(counterclockwise) fluid pressure in pump, Airless
Hose, and Spray Gun.
Turns sprayer ON and OFF.
Draws fluid into pump.
Drains fluid in system during priming and pressure relief.
SaniSpray HP Airless Spray
Gun
Spray Tip
Spray Tip Guard
Fluid Inlet Fitting
ProXChange Pump
Dispenses fluid.
• Atomizes fluid being sprayed, forms spray pattern and controls fluid flow according to hole size.
• Reverse position unclogs plugged tips without disassembly.
Reduces risk of fluid injection injury.
Prevents accidental triggering of Spray Gun.
Threaded connection for Airless Hose.
Pump Fluid Outlet Fitting
Airless Hose
Pumps and pressurizes fluid and delivers it to
Airless Hose.
Threaded connection for Airless Hose.
Transports high-pressure fluid from pump to Spray
Gun.
Inlet Strainer (inside Hopper) Prevents debris from entering pump.
Power Cord Plugs into power source.
Easy Access Door Easy Access Door permits quick access to the pump. Open pump door by pulling out on the tabs while sliding door away from the pump inlet.
Pump Removal Tool
Inlet Valve Removal Tool
Use cut out in the frame to remove/install pump packing.
Cut out in the frame provide the tools to quickly remove/install the inlet valve without additional tools.
3A7653D 23
Maintenance
Maintenance
Routine maintenance is important to ensure proper operation of your sprayer.
Activity
Inspect/clean Fluid Inlet strainer.
Inspect motor shroud openings for blockage.
NOTICE
Protect the internal drive parts of this sprayer from water. Openings in shroud allow cooling of mechanical parts and electronics inside. If water gets into these openings, the sprayer could malfunction or be permanently damaged.
Airless Hoses
Check Airless Hose for damage every time you spray. Do not attempt to repair Airless
Hose if hose jacket or fittings are damaged.
Do not use Airless Hoses shorter than 25 ft.
Wrench tighten, using two wrenches.
Spray Tips
• Always clean tips with water and brush after spraying.
• Tips may require replacement after 15 gallons or they may last through 60 gallons.
Pump Repair
When pump packings wear, material will begin to leak down outside of pump.
Purchase a Pump Cartridge Kit or replacement Pump Assembly. See Parts ,
Install pump according to
Pump Installation instructions, pages 24 and 25.
Interval
Daily or each time you spray
Daily or each time you spray
Pump Removal
The Hopper must be removed before pump can be removed.
Always perform
Pressure Relief Procedure , page 12, before starting any pump repairs.
1.
Pull tabs on sides of the Easy Access
Door pump towards you while pushing the entire door away from the inlet end of the pump.
2.
Now lift the door so that it swivels out of the way.
1
2
3 ti27463a
24 3A7653D
3.
Slide pump assembly off the mounting pins.
Maintenance
2.
Move pump displacement rod up or down until cap is level with the opening in the yoke.
Pump Installation
1.
Slide pump assembly onto the mounting pins.
ti27037a
3.
Swing Easy Access Door pump door closed while pushing the entire door towards the inlet end of the pump.
1
2
3 ti27478a
NOTE: Door must be fully closed and latched before sprayer will operate.
3A7653D 25
Recycling and Disposal
Inlet Valve Removal
An integrated tool is included in the frame to remove the inlet valve assembly from the pump. If you suspect that the inlet valve is clogged or stuck, remove the valve assembly and clean.
1.
Remove Hopper and pump from sprayer. See
2.
Insert pump inlet into frame and loosen the inlet valve. Remove inlet valve.
NOTICE
Do not lose the ball and spring inside the inlet valve assembly. It may fall out when the inlet valve is removed. Pump will not prime without the ball and spring.
3.
Clean any debris from the cavity and reinstall the ball and spring. Tighten inlet valve to pump using integrated tool on the frame.
Recycling and Disposal
End of Product Life
At the end of the product’s useful life, dismantle and recycle it in a responsible manner.
• Perform the
• Drain and dispose of fluids according to applicable regulations. Refer to the material manufacturer’s Safety Data
Sheet.
• Remove motors, batteries, circuit boards, LCDs (liquid crystal displays), and other electronic components.
Recycle according to applicable regulations.
• Do not dispose of electronic components with household or commercial waste.
• Deliver remaining product to a recycling facility.
26 3A7653D
Troubleshooting
Troubleshooting
2.
Solutions at the beginning of each problem listed are the most common,
Start at the beginning and continue down the list to find a solution.
1.
Disconnect power and follow
Relief Procedure , page 12, before
checking or repairing.
Problem
Motor does not run (verify sprayer is plugged in, and power switch is on)
Cause
??
??
www.graco.com/techsupport
Solution
Easy access door not fully closed.
Pressure Control Knob is set at zero pressure.
Electric outlet is not providing power.
Extension cord is damaged.
Sprayer electric cord is damaged.
Verify the Easy Access Door is closed and latched. See page
Turn Pressure Control Knob clockwise to increase pressure setting.
Test outlet with known working device.
Reset circuit breaker or replace fuse.
Find working outlet.
Reset building circuit breaker or replace fuse.
Replace extension cord. See
Check for broken insulation or wires. Replace electric cord if damaged.
Pump is seized (water is frozen in pump.)
Turn ON/OFF Switch off and unplug sprayer from outlet.
If frozen do NOT try to start sprayer until it is completely thawed or it may damage the motor, control board and/or drive train.
Place sprayer in warm area for several hours. Check for free moving pump by removing shroud and spinning fan.
If not frozen, see
pump. See Parts , pages
Motor or control is damaged.
Replace motor or pump
3A7653D 27
Troubleshooting
Problem
Sprayer runs, but pump does not prime or loses prime while in use (pump cycles but does not pump material or build pressure).
Pump is primed, but can not achieve good spray pattern.
Cause Solution
Inlet valve check ball is stuck.
Press PushPrime Button to dislodge the ball allowing pump to prime properly.
Prime/Spray Valve is in
SPRAY position.
Turn Prime/Spray Valve down to PRIME position until material exits Drain Tube. The pump is now primed.
Inlet strainer is clogged or
Hopper is empty.
Inlet valve check ball or seat is dirty.
Outlet valve check ball is stuck.
Prime/Spray Valve is worn or obstructed with debris.
Clean debris off inlet strainer and make sure there is fluid in
Hopper.
Remove Inlet Valve. Clean ball and seat. See
Unscrew outlet valve, remove, and clean assembly.
Spray Tip is in UNCLOG position.
Pressure is set too low.
Replace Prime/Spray Valve or replace pump assembly. See
Parts
Rotate arrow-shaped handle on Spray Tip so it points forward to SPRAY position.
Increase pressure setting of
Pressure Control Knob.
Spray Tip gasket and seal worn or missing.
Inlet strainer is clogged or
Hopper is empty.
Extension cord is too long or not heavy enough gauge.
Inlet Valve or outlet pump valve is worn or clogged with debris.
Replace gasket and seal. See
Clean debris off inlet strainer and make sure there is fluid in
Hopper.
Replace extension cord. See
Check for worn or contaminated inlet valve or outlet valve.
Airless Hose is too long (if extra section was added).
• Prime sprayer.
• Trigger Spray Gun momentarily.
• When trigger is released, pump should cycle momentarily and stop.
• If pump continues to cycle, pump valves may be worn or contaminated with debris.
• Replace Inlet Valve or
Pump Assembly. See
Parts
Remove section of Airless
Hose.
28 3A7653D
Troubleshooting
Problem
Spray Gun stopped spraying while trigger is pulled.
Cause
Sprayer lost prime.
Fan pattern varies dramatically while spraying.
Cannot trigger Spray Gun.
Pressure control switch is worn and causing excessive pressure variation.
Spray Trigger Lock is engaged.
Material is coming out of pressure control.
Material leaks down outside of pump.
Motor is hot and runs intermittently. Motor automatically shuts off due to excessive heat. Damage can occur if cause is not corrected.
Pressure control is worn.
Pump packings are worn.
Vent holes in enclosure are plugged or sprayer is covered.
Extension cord is too long or not a heavy enough gauge.
Unregulated electrical generator being used has excessive voltage.
Motor needs to be replaced.
Solution
See troubleshooting section
“Sprayer runs, but pump does not prime or loses prime while in use.” on page 28.
Replace Pressure Control or
Pump Assembly. See Parts ,
Rotate Trigger Lock to disengage trigger lock. See
Replace Pressure Control or
Pump Assembly. See Parts ,
Replace Pump Cartridge or
Pump Assembly. See Parts ,
Keep vent holes clear of obstructions and keep sprayer open to air.
Replace extension cord. See
Use electrical generator with a proper voltage regulator.
Replace motor assembly. See
3A7653D 29
Parts - SaniSpray HP 65 (Quick Repair)
Parts - SaniSpray HP 65 (Quick Repair)
1
Torque to 110-120 in-lb
(12.5-13.6 N•m)
2
Torque to 30-36 in-lb
(3.4-4.0 N•m)
30 3A7653D
Parts - SaniSpray HP 65 (Quick Repair)
Parts List - SaniSpray HP 65 (Quick Repair)
Ref. Sprayer Model Part Description
25R972, 25R962 25R921 KIT, motor, drive, HP65, 120V, includes 56
Qty.
1
7
8
26
31†
32
36
56
25R946 25T291 KIT, motor, drive, 230V, CEE, includes 56
25R948, 25R954 25T292 KIT, motor, drive, 230V, multi, includes 56
All
All
25R920
25R922
KIT, pump
KIT, enclosure
All
25R792
25R923 KIT, hopper
25R874 GUN, SaniSpray, HP, NA
25R946, 25R948 25T289 GUN, SaniSpray, HP, EU
25R954, 25R962 25T290 GUN, SaniSpray, HP, AP
All
All
All
LP617 TIP, LP617
LP619 † TIP, LP619
LP621 TIP, LP621
112133 SCREEN, hopper
25T410 KIT, warning labels, cord
CARD, medical alert (not shown)
222385 English, Spanish, French
17F690 Dutch, German, Italian
1
1
1
1
1
1
1
1
60
98
99*
101
118
All
All
All
All
17A134 English, Chinese, Korean
17R476 English, Spanish, Portuguese (Brazil)
26A997 English, Indonesian, Hindi
26A998 English, Chinese, Japanese
25T282
25R872
25C828
25R948, 25R954 195551
EXTENSION, 15 in. (not shown)
TIPSEAL, 5-pack (not shown)
HOSE, 1/8 in. x 4-1/2 ft.
PLUG, retaining
1
144
146
25R962
25R954
244285 CORDSET, Japan (not shown)
17N232 CORDSET, India (not shown)
147 25R948, 25R954 242001 CORDSET, EU Schuko
149 25R954 242005 CORDSET, ANZ
157
158
25R948
25R948
287121 CORDSET, Italy, Denmark, Switzerland
17J242 CORDSET, UK (not shown)
1
1
Motor/Drive Kit 25R921 does not include cordset adapter for Japan. Cordset adapter must be ordered separate (see Ref. 144). Control Kit 25T292 does not include cordset adapter. Cordset adapter must be ordered separate (see Ref. 146-158).
* Two extra TipSeals (polymer spray tip seals) are included with the sprayer. For disinfectant applications, use TipSeal (polymer spray tip seal) instead of the OneSeal
(metal seal) that is included with the replacement spray tips.
† SaniSpray HP Gun includes LP619 Spray Tip.
Replacement safety labels, tags, and cards are available at no cost.
1
1
1
1
1
1
1
1
3A7653D 31
Parts - SaniSpray HP 65 (Extended Repair)
Parts - SaniSpray HP 65 (Extended Repair)
1
Torque to 110-120 in-lb
(12.5-13.6 N•m)
2
Torque to 30-36 in-lb
(3.4-4.0 N•m)
32
Ref. Sprayer Model Part Description
3
25R792, 25R962
25R946
17J173
17J175
25R948, 25R954 17L301
CORD, power, USA
CORD, power, EU Schuko
CORD, power, Multicord
BOARD, control, 100-120V, includes 15a
15
25R792, 25R962 25T416
25R946, 25R948,
25R954
25T417
25R792, 25R962 119276
BOARD, control, 220-240V, includes 15a
15a
39
25R946, 25R948,
25R954
All
129882
17K336
FUSE, 12.5A slow blow, 100-120V
FUSE, 6.3A slow blow, 220-240V
TUBE, drain, assembly
56 All 25T410 KIT, warning labels, cord
Replacement safety labels, tags, and cards are available at no cost.
Qty.
1
1
1
1
1
3A7653D
Parts - SaniSpray HP 65 (Pump Repair)
Parts - SaniSpray HP 65 (Pump Repair)
1
Torque to 140-160 in-lb
(16-18 N•m)
2
Torque to 270-330 in-lb
(30-37 N•m)
3
Torque to 30-35 ft-lb
(40-48 N•m)
4
Torque to 220-250 in-lb
(25-28 N•m)
Ref. Sprayer Model Part
6
8
25
28
All
All
All
All
Description
25T403 KIT, inlet valve assembly
25T415 KIT, prime valve
25T418 KIT, pump cartridge
25T402 KIT, control, pressure
3A7653D
Qty.
1
1
1
1
33
Wiring Diagrams
Wiring Diagrams
100-120V
M
34 ti27233a
3A7653D
220-240V
Wiring Diagrams
M ti27485a
3A7653D 35
Technical Specifications
Technical Specifications
SaniSpray HP 65 Portable Hopper Sprayer
US Metric
Sprayer
Maximum fluid working pressure 1000 psi
Maximum Delivery 0.5 gpm
Maximum Tip Size 0.023 in.
Fluid Outlet npsm
Generator Minimum
Power Requirements
Dimensions
Height
Length
Width
Weight
19.6 in.
20.2 in.
13.5 in.
28 lb.
69 bar, 6.9 MPa
1.9 lpm
0.58 mm
1/4 in.
3500 W
100–120V, 8A, 1Ø or 220-240V, 5A, 1Ø
Storage temperature range –30° to 160°F
49.8 cm
51.3 cm
34.3 cm
12.1 kg
–35° to 71°C
4° to 46°C Operating temperature range 40° to 115°F
Noise
Sound pressure
Sound power
Materials of Construction
83 dBa*
93 dBa*
Wetted materials stainless steel, PTFE, acetal, leather, UHMWPE, anodized aluminum, tungsten carbide, polyethylene, fluoroelastomer, urethane, nylon, PE-RT
Notes
* Startup pressures and displacement per cycle may vary based on suction condition, discharge head, air pressure, and fluid type.
** Sound pressure measured 3 feet (1 meter) from equipment. Sound power measured per
ISO-9614.
Never store with disinfectant or water in sprayer.
All trademarks or registered trademarks are the property of their respective owners.
36 3A7653D
California Proposition 65
California Proposition 65
CALIFORNIA RESIDENTS
WARNING: Cancer and reproductive harm – www.P65warnings.ca.gov.
3A7653D 37
Graco Warranty
Graco Warranty
Graco warrants all equipment referenced in this document which is manufactured by Graco and bearing its name to be free of defects in material and workmanship on the date of sale by an authorized Graco distributor to the original purchaser for use. Graco will, for a period of ninety (90) days from the date of sale, provide repair parts for equipment determined by Graco to be defective. This warranty applies only when the equipment is installed, operated and maintained in accordance with Graco’s written recommendations.
This warranty does not cover, and Graco shall not be liable for general wear and tear, or any malfunction, damage or wear caused by faulty installation, misapplication, abrasion, corrosion, inadequate or improper maintenance, negligence, accident, tampering, or substitution of non-Graco component parts. Nor shall Graco be liable for malfunction, damage or wear caused by the incompatibility of Graco equipment with structures, accessories, equipment or materials not supplied by Graco, or the improper design, manufacture, installation, operation or maintenance of structures, accessories, equipment or materials not supplied by Graco.
THIS WARRANTY IS EXCLUSIVE, AND IS IN LIEU OF ANY OTHER WARRANTIES, EXPRESS OR
IMPLIED, INCLUDING BUT NOT LIMITED TO WARRANTY OF MERCHANTABILITY OR WARRANTY OF
FITNESS FOR A PARTICULAR PURPOSE .
Graco’s sole obligation and buyer’s sole remedy for any breach of warranty shall be as set forth herein. The buyer agrees that no other remedy (including, but not limited to, incidental or consequential damages for lost profits, lost sales, injury to person or property, or any other incidental or consequential loss) shall be available.
Any action for breach of warranty must be brought within two (2) years of the date of sale.
GRACO MAKES NO WARRANTY, AND DISCLAIMS ALL IMPLIED WARRANTIES OF MERCHANTABILITY
AND FITNESS FOR A PARTICULAR PURPOSE, IN CONNECTION WITH ACCESSORIES, EQUIPMENT,
MATERIALS OR COMPONENTS SOLD BUT NOT MANUFACTURED BY GRACO .
These items sold, but not manufactured by Graco (such as electric motors, switches, hose, etc.), are subject to the warranty, if any, of their manufacturer. Graco will provide purchaser with reasonable assistance in making any claim for breach of these warranties.
IN NO EVENT WILL GRACO BE LIABLE FOR INDIRECT, INCIDENTAL, SPECIAL OR CONSEQUENTIAL
DAMAGES RESULTING FROM GRACO SUPPLYING EQUIPMENT HEREUNDER, OR THE FURNISHING,
PERFORMANCE, OR USE OF ANY PRODUCTS OR OTHER GOODS SOLD HERETO, WHETHER DUE TO
A BREACH OF CONTRACT, BREACH OF WARRANTY, THE NEGLIGENCE OF GRACO, OR OTHERWISE.
This warranty gives you specific legal rights, and you may also have other rights which vary by country, state or province. This warranty and limitation of liability shall not exclude or limit those rights (if any) against Graco which cannot be excluded or limited under the applicable law of your country, state or province.
FOR GRACO NORTH AMERICA CUSTOMERS
Please call 1-844-241-9499 or visit www.graco.com/techsupport regarding any potential defect in equipment under warranty. If the claimed defect is verified, Graco will either, at its discretion, send repair parts for owner installation or replace the product, free of charge. Warranty claims and/or service for this product are not administrated by Graco’s distributors or service centers for Graco paint equipment.
FOR GRACO EUROPE, MIDDLE EAST, AFRICA AND ASIA PACIFIC CUSTOMERS
Please contact your regional service center or authorized distributor to administer a warranty claim.
FOR GRACO CANADA CUSTOMERS
The Parties acknowledge that they have required that the present document, as well as all documents, notices and legal proceedings entered into, given or instituted pursuant hereto or relating directly or indirectly hereto, be drawn up in English. Les parties reconnaissent avoir convenu que la rédaction du présente document sera en
Anglais, ainsi que tous documents, avis et procédures judiciaires exécutés, donnés ou intentés, à la suite de ou en rapport, directement ou indirectement, avec les procédures concernées.
38 3A7653D
Graco Information
Graco Information
For the latest information about Graco products, visit www.graco.com
.
For patent information, see www.graco.com/patents .
TO PLACE AN ORDER, contact your Graco distributor or call 1-800-690-2894 to identify the nearest distributor.
3A7653D 39
All written and visual data contained in this document reflects the latest product information available at the time of publication. Graco reserves the right to make changes at any time without notice.
Original instructions.
This manual contains English. MM 3A7653
Graco Headquarters: Minneapolis
International Offices: Belgium, China, Japan, Korea
GRACO INC. AND SUBSIDIARIES • P.O. BOX 1441 • MINNEAPOLIS MN 55440-1441 • USA
Copyright 2020, Graco Inc. All Graco manufacturing locations are registered to ISO 9001.
www.graco.com
Revision D, July 2020
advertisement
* Your assessment is very important for improving the workof artificial intelligence, which forms the content of this project
Related manuals
advertisement
Table of contents
- 3 Models
- 4 Important User Information
- 5 Warnings
- 9 Know Your Sprayer
- 10 Grounding
- 10 Power Requirements
- 10 Extension Cords
- 10 Pails
- 11 Setup
- 12 Start Up
- 12 Pressure Relief Procedure
- 14 Flushing a New Sprayer
- 15 Fill Pump
- 16 Fill Spray Gun and Airless Hose
- 17 How to Spray
- 17 Choose Your Spray Tip
- 18 Spray Tip Orientation
- 18 Starting Your Spray and Adjusting Pressure
- 19 Clear Tip Clog
- 20 Cleanup
- 21 Clean the Gun
- 22 Storage
- 23 Quick Reference
- 24 Maintenance
- 24 Airless Hoses
- 24 Spray Tips
- 24 Pump Repair
- 24 Pump Removal
- 25 Pump Installation
- 26 Inlet Valve Removal
- 26 Recycling and Disposal
- 26 End of Product Life
- 27 Troubleshooting
- 30 Parts - SaniSpray HP 65 (Quick Repair)
- 31 Parts List - SaniSpray HP 65 (Quick Repair)
- 32 Parts - SaniSpray HP 65 (Extended Repair)
- 33 Parts - SaniSpray HP 65 (Pump Repair)
- 34 Wiring Diagrams
- 34 100-120V
- 35 220-240V
- 36 Technical Specifications
- 37 California Proposition 65
- 38 Graco Warranty
- 39 Graco Information