advertisement
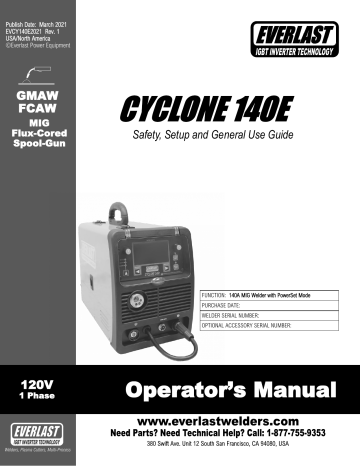
Publish Date: March 2021
EVCY140E2021 Rev. 1
USA/North America
©Everlast Power Equipment
GMAW
FCAW
MIG
Flux
-
Cored
Spool
-
Gun
Safety, Setup and General Use Guide
120V
1 Phase
Welders, Plasma Cutters, Multi Process
FUNCTION: 140A MIG Welder with PowerSet Mode
PURCHASE DATE:
WELDER SERIAL NUMBER:
OPTIONAL ACCESSORY SERIAL NUMBER:
Operator ’ s Manual
TABLE OF CONTENTS
SPECIAL NOTICE AND CALIFORNIA PROPOSITION 65 WARNING
CUSTOMER GREETING AND EXPLANATION OF PROCEDURES
WARRANTY AND CONTACT INFORMATION
SAFETY DISCLAIMER AND HF WARNING
SAFETY WARNINGS, DANGERS, CAUTIONS AND INSTRUCTIONS
GENERATOR OPERATION INFORMATION
SPECIFICATIONS, INCLUDING DUTY CYCLE AND INPUT AMPERAGE INFORMATION
DUTY CYCLE EXPLANATION
GETTING STARTED, UNPACK YOUR UNIT, CHECK FOR GAS LEAKS
CONNECTING YOUR UNIT TO THE POWER SOURCE AND WIRING INFORMATION
CONNECTING YOUR UNIT TO THE SHIELDING GAS
ADJUSTING YOUR REGULATOR 16
GUN INSTALLATION AND CONNECTING YOUR UNIT AND READYING TO WELD (POLARITY AND PANEL CONNECTIONS) 17
WIRE SPOOL INSTALLATION
DRIVE ROLL INFORMATION; HOW TO FEED THE WIRE THROUGH THE MIG GUN
18
19
TENSIONING AND TRIMMING THE WIRE
COMPONENT IDENTIFICATION AND EXPLANATION; FRONT PANEL
COMPONENT IDENTIFICATION AND EXPLANATION; REAR PANEL
COMPONENT IDENTIFICATION AND EXPLANATION; CONTROL PANEL LAYOUT AND USE
COMPONENT IDENTIFICATION AND EXPLANATION; MANUAL FUNCTION AND SCREEN LAYOUT
COMPONENT IDENTIFICATION AND EXPLANATION; POWERSET FUNCTION AND SCREEN LAYOUT
24
25
20
21
22
23
COMPONENT IDENTIFICATION AND EXPLANATION; POWERSET EXPLANATION AND PURPOSE
COMPONENT IDENTIFICATION AND EXPLANATION; POWERSET/MANUAL CHART AND SETTINGS
WELDING INFORMATION AND TIPS; EXPLANATION OF WELDER FUNCTIONS
TROUBLESHOOTING ERROR CODES
TROUBLESHOOTING COMMON ISSUES
BLANK, FOR NOTES
26
27
28
32
33
34
7
10
11
12
5
6
3
4
13
14
15
2
NOTICE:
Product specifications and features are subject to change without notice. While every attempt has been made to provide the most accurate and current information possible at the time of publication, this manual is intended to be a general guide and not intended to be exhaustive in its content regarding safety, welding, or the operation/maintenance of this unit. Due to multiple variables that exist in the welding field and the changing nature of it and of the Everlast product line,
Everlast Power Equipment INC. does not guarantee the accuracy, completeness, authority or authenticity of the information contained within this manual or of any information offered during the course of conversation or business by any Everlast employee or subsidiary. The owner of this product assumes all liability for its use and maintenance. Everlast Power Equipment INC. does not warrant this product or this document for fitness for any particular purpose, for performance/accuracy or for suitability of application. Furthermore, Everlast Power Equipment INC. does not accept liability for injury or damages, consequential or incidental, resulting from the use of this product or resulting from the content found in this document or accept claims by a third party of such liability.
WARNING!
California Proposition 65 Warning:
This product, when used for welding or cutting, produces fumes or gases which contain chemicals known to the State of California to cause birth defects and, in some cases, cancer. (California Health & Safety Code § 25249.5 et seq.)
Warning: Cancer and/or Reproductive Harm www.P65warnings.ca.gov
3
THANK YOU! We appreciate you as a valued customer and hope that you will enjoy years of use from your welder. We work to please the customer by providing a well supported, quality product. To make sure that you receive the best quality ownership experience, please see below for important information and time sensitive details.
What to do right now:
1.
Print your receipt from your confirmation email that should have been sent to you after your purchase and put it up for safe keeping. If you do not have one, contact us at 1 877 755 9353 (US customers) or 1 905 570 1818 (Canadian Customers). You will need this if anything should ever happen for original owner verification (if bought as a gift, original receipt will still be needed, or explanation sent to Everlast).
2.
Read this manual! A large number of tech and service calls are a result of not reading the manual from start to finish. Do not just scan or casually peruse this manual. There are different features and functions that you may not be familiar with, or that may operate differently than you expect.
Even if you have expertise in the field of welding, you should not assume this unit operates like other brands or models you have used.
3.
Carefully unpack and inspect all items immediately. Look for missing or damaged items. Please report any issues within 48 hours (72 hours on weekend or holidays) of receiving your product. Take pictures if you are able and contact us at 1 877 755 9353, ext. 207 if any issue is discovered between 9 am and 5 pm Eastern Time M F (US customers) or at 1 905 570 1818 (Canadian Customers) between 9am and 4 pm weekdays except on Fridays when hours are from 9 am to 12pm Eastern. If outside of the US or Canada, contact your in country/or regional distributor direct at their service number.
What to do within the next 2 3 days:
1.
Make sure your electrical system is up to date and capable of handling the inrush and rated current of the unit. Consult and use a licensed and knowledgeable electrician. If you have downloaded this manual in expectation of delivery, get started now.
2.
Make sure this machine is plugged in, turned on, and tested with every process and major feature, checking for proper function. You have a 30 day period to test and thoroughly check out the operation of this unit under our 30 day satisfaction period. If something is wrong, this policy covers shipping on the unit (30 day satisfaction policy applies to the USA only for the 48 lower states and D.C., territories and provinces are excluded) or any incidental parts that may be needed to resolve any issue. After this 30 day period, if you find something wrong with the unit, you will not receive the benefit of free shipping back and forth to resolve this issue. Your unit is still covered under the 5 year parts/labor warranty, but shipping is covered by the customer after the 30 day period is over. The first 30 days of operation with any electronic item is the most critical and if any issue will happen, it will often happen during this time. This is why it is very important that you put this unit to work as soon as possible. Any issue should be reported within 48 hours (72 if on the weekend or holiday). Everlast will not be liable for any shipping after that time.
What to do within the next 30 days:
Visit our website (US customers). Go to www.everlastwelders.com. Navigate to the resources tab and to the “ product registration ” page to register your product. While keeping your receipt/proof of purpose is still required for verification of ownership, registering will help us keep your details straight and establish a chain of ownership. Don ’ t worry, though, your warranty is still valid if you can ’ t do this. Remember: Always keep your receipt even if you register. You may want to staple a copy to your manual.
What to do if you have a warranty issue or problem with the unit:
1.
Unplug the unit. (Also do this before any maintenance or cleaning is done.)
2.
Do not attempt a self repair until authorized by an Everlast representative. This does not include performing routine maintenance such as point gap adjustments or regular internal cleaning. Any third party repairs are not covered under warranty, and can further damage your unit.
3.
Within 24 48hours, (or by the next working business day) you must contact U.S. tech support at 1 877 755 9353 ext 207(U.S. hours are 9 am to
5pm Eastern for tech support and 9 am to 5 pm Pacific for the business/sales office). If you are in Canada contact 1 905 570 1818 (Canada hours are 9am to 4pm M Th, 9am to 12pm Fri). Although phone contact is preferred to establish a warranty claim, you may send an email to [email protected] (US) or [email protected] (Canada) along with your contact information and brief explanation of the issue and ask for a follow up call. If you contact us via phone, and you do not reach a live person, please leave a brief message with the nature of your problem and your contact information. You should expect a call back within 24 hours. It is also a good idea to follow up the message with an email.
4.
Be prepared with as much information as possible when you talk with a tech advisor, including a details of the failure, settings, and application of the unit. NOTE: A Proof Of Purchase (receipt) is required before returning the unit for warranty or before warranty parts can be sent to you.
5.
Keep in mind that, you may be asked to check a few basic things. Before you call, having a screwdriver and volt/ohm meter at hand is a good idea and will save time. Many issues can be resolved over the phone. If the issue cannot be resolved over the phone/email, you may be given an option to return the unit, or have a part shipped to you, at Everlast ’ s discretion. Keep in mind, you may be asked questions that seem basic, or elementary to your knowledge base. These are not meant to question your knowledge, but rather to make sure nothing is overlooked. However the tech chooses to proceed, please cooperate with the process, even if you think you know what the cause or issue is. You may be asked to check something or open the unit during the diagnosis. This does not void the warranty! Opening the unit is a part of routine maintenance and cleaning.
This is an important step. The willingness of the customer to work with tech support can save lots of time and accelerate the warranty process. For
4
warranty to be honored, you will need to make sure that you follow these guidelines. Units that are returned without an RMA (issued by the tech support department) may not be repaired under the warranty agreement and you may be charged for the repair and can result in a delayed repair as well.
What to do if you need setup help, guidance, weld issue diagnosis or have general product compatibility questions.
Call us at 877 755 9353 ext. 204 for welding guidance and general welding issue diagnosis. Or email [email protected] with the basic issue you are having, along with your specific settings, and welding application.
Hey...wait, what is my warranty?
Warranties and service policies and procedures vary from country to country and are maintained and supported by the regional or in country distributor of Everlast welding equipment.
USA Customers Only: For full details on the 5 year parts and labor warranty, 30 day satisfaction policy, terms of sale, and how to proceed with a warranty claim, please visit: https://www.everlastgenerators.com/standard warranty. Accessories are covered by a separate warranty and detailed information can also be found at the link above.
Canada Customers Only: For full details on the 3 year parts and labor warranty, terms of sale, and related policies and procedures, please visit: https:// www.everlastwelders.ca/terms.php.
Who do I contact?
USA Technical Support:
Email: [email protected]
1 877 755 9353 ext. 207
9am 5pm Eastern (Closed holidays)
Monday Friday
USA Welding Support and General Product Information:
Email: [email protected]
1 877 755 9353 ext 204
9am 6:30 pm Eastern (Closed holidays)
Monday Friday
USA Sales and Main Office:
Email: [email protected]
1 877 755 9353 ext 201
9am 5pm Pacific (Closed holidays)
Monday Friday
Canada Technical Support:
Email: [email protected]
905 570 1818
9am 4pm Eastern Monday Thursday
9am 12pm Eastern Friday
Canada Sales and Main Office:
Email: [email protected]
905 570 1818
9am 4pm Eastern Monday Thursday
9am 12pm Eastern Friday
Other Countries and Regions:
Visit the U.S. Website @ www.everlastwelders.com and click on the flag of the country or region represented that is closest to you. If your country or region is not found, call the U.S. office at 1 650 588 8588 between the hours of 9am to 5pm Pacific, Monday through Friday.
5
Safe operation and proper maintenance is your responsibility.
Everlast is dedicated to keeping safety a top priority. While we have compiled this operator ’ s manual to instruct you in basic safe operation and maintenance of your Everlast product, it is no substitute for observing safe welding practices and behavior. Safe welding and related cutting operations require basic knowledge, experience and ultimately the exercise of common sense. Welding does significant hazards to your health and life! Exercise extreme caution and care in all activities related to welding or cutting. Your safety, health and even life depends upon it.
WARNING! If you do not have proper knowledge or capability to safely operate this machine, do not use this machine until proper training has been received!
While accidents are never planned, preventing an accident requires careful planning. Stay alert!
Please carefully read this manual before you operate your Everlast unit.
The warranty does not cover damage or harm created by improper use. neglect of the machine or failure to follow safe operating practices.
NOTICE:
Welding and cutting operations may generate undesirable High Frequency (HF) and EMF energy. This can interfere with surrounding electronic equipment such as computers, routers, CNC equipment, televisions, radios, fluorescent lighting etc. If disturbance in surrounding electrical and electronic equipment is noted, consult a licensed electrician to help properly ground surrounding equipment to limit the interference. This machine may cause GCFI and ground fault outlets to malfunction. This unit is designed to be operated on a dedicated, properly grounded circuit.
6
Safety Warnings, Dangers, Cautions and Instructions
NOTICE. This unit manual is intended for users with basic knowledge and skillset in welding. It is your responsibility to make certain that the use of this welder is restricted to persons who have read, understand and follow the warnings and instructions in this manual. If you or the operator needs further instruction, contact Everlast welding support at 1 877
755 9353 ext. 204 or seek qualified professional advice and training.
WARNING! High Frequency (HF) energy can interfere with the operation of pacemakers and can damage pacemakers. Consult with your physician and pacemaker manufacturer before entering an area where welding and cutting equipment is in operation and before using this welder. Some pacemakers have limited shielding. Alert any users or customers of this potential problem.
WARNING! Use approved safety glasses with wrap around shields and sides while welding and working in the weld area or serious eye damage or loss of vision may result. Use a grinding shield in addition to the safety glasses during chipping and grinding operations.
WARNING! When welding always use an approved welding helmet or shielding device equipped with at least an equivalent of a shade 9 or greater. Increase the shade number rating as amperage increase over 100 amps. Inspect helmet for cracks in lenses and in the helmet. Keep lens covers in good condition and replace as necessary.
WARNING! Welding/cutting operations carry inherent risks which include but not limited to possible cuts burns, electrical shocks, lung damage, eye damage and even death. Take all appropriate measures to use proper Personal Protective Equipment (PPE). Always use leather welding gloves, closed toe (preferably reinforced or steel toe leather shoes, and long sleeved flame resistant clothing (i.e. denim). Do not wear Poly/Nylon blend materials.
DANGER! Welding poses shock and electrocution risks. Keep this welding equipment dry.
Do not weld in the rain or where moisture accumulates. Use dry, rubber soled shoes, gloves and clothing when welding. Do not rest or contact work clamp (ground) when welding. Keep all parts of the body insulated from the part being welded when possible. Do not touch both terminals or connections at the same time. Consider all welder parts to be
“ live ” at all times even if no welding is being performed. Do not use frayed welding cables.
CAUTION! Fires are possible but also preventable while welding. Always remove flammable rags, papers, and other materials from the weld area. Keep rags stored in an approved flame proof canister. Keep a fully charged fire extinguisher at hand. Remove any fuels, oils, paint, pressurized spray cans, and chemicals from the weld area. Make sure any smoke/fire detectors function properly. Do not weld on tanks, drums or barrels, especially if pressurized or sealed. Do not weld on any container that previously held fuel or chemicals. Make sure the weld area is clear of flammable materials such as grass or wood shavings solvents and fuels. Do not wear frayed or loose clothing. Visually inspect and recheck the work area after welding looking for smoldering debris or flames.
WARNING! Welding gas cylinders are under high pressure. Keep all gas cylinders upright and chained to a cart or held safely in a safety holding pen. Never transport gas cylinders in an enclosed car, van or other vehicle. Transport gas cylinders securely. Keep all cylinders capped while not in use or during transport. Replace the cap on the cylinder when it is going to be more than 24 hours before use. Do not use or attempt to repair faulty regulators. Never weld on gas cylinders. Keep gas cylinders away from direct sparks.
7
Safety Warnings, Dangers, Cautions and Instructions
DANGER! Welding and cutting operations pose serious inhalation hazards. Some of these hazards are immediate while others are cumulative in their effect. Do not weld in enclosed spaces or in areas without adequate ventilation. Fumes and gases released in the welding and cutting operations can be toxic. Use fans or respiration equipment to ensure adequate ventilation if you are welding in a shop or garage area. Do not weld on galvanized metal under any circumstance. You may develop metal fume fever. Symptoms are similar to Flu like symptoms. Seek medical advice and treatment if you are exposed to galvanized welding fumes.
If you experience any eye burning, nose or throat irritation while welding, these are signs that you need more ventilation.
If you feel these symptoms:
• Stop work immediately and relocate work area with better ventilation.
• Wash and clean your face and hands.
• Stop work completely and seek medical help if irritation persists
DANGER! Never use brake cleaner or any chlorinated solvent to clean or degrease metal scheduled to be welded or other related equipment in the area being welded. The heating of this cleaner and its residue will create highly toxic phosgene gas. Small amounts of this vapor are harmful and can lead to organ failure and death. If degreasing of a part is necessary, use Acetone or an approved pre weld cleaner. Use the proper personal protective equipment (PPE) when handling any cleaners/solvents.
DANGER! People with pacemakers should consult a physician and pacemaker manufacturer before welding. There is a potential for damage or serious malfunction resulting in death. High Frequency energy (HF)/Electromagnetic Fields generated during welding can interfere with pacemaker signals, even permanently damaging it. Some pacemakers offer some shielding, but restrictions regarding amperage and HF starting of TIG arcs may be placed upon the individual. Warn all potential bystanders that they should exit the work area if they have a pacemaker or similar medical equipment before welding. Consult with a
Physician if a pacemaker is expected to be implanted.
DANGER! Never defeat or modify any safety guards or shields. Keep all safety covers and shields in place.
Never place your fingers in or near a fan shroud or insert any object into the fan or drive roll mechanism. Keep welder door closed while welding to prevent access to the moving parts and possible injury.
8
Safety Warnings, Dangers, Cautions and Instructions
CAUTION! Trip Hazards exist around welders. Cords, cables, welding leads and hoses pose a trip hazard. Be aware of their location and inform others of their location. Tape and secure them so they will stay out of high traffic areas.
CAUTION! Welded metal can stay hot long after welding is completed. Burns may occur.
Always wear gloves or use tongs/pliers when handling welded or cut metal. Remember the heat from the metal may catch other material on fire. Always have a fire proof area ready to place welded components until they fully cool. Use soap stone or a metal marking marker to label the metal as “ HOT ” to serve as a reminder to all present in the area.
CAUTION! Welding and cutting operations generate high levels of ultraviolet (UV) radiation which can burn and damage skin and eyes. The intensity is so high that exposed skin and eyes can burn in a few minutes of exposure. Minimize direct skin and eye exposure to this intense form of radiation by using proper PPE and sun screen where appropriate.
CAUTION! Do not allow bystanders. Do not allow others without proper Personal Protection Equipment (PPE) suitable for welding to stand in the welding area or to observe welding and welding related activities. If protection is not readily available, use a welding screen to separate the welding area from the rest of the area. If no protection or screen is available, physically exclude them from the welding area by a wall or other solid divider.
Keep all pets and young children away from the welding area.
CAUTION! Electromagnetic Fields can be generated by this welder and radiate into the work place. The effect of EMF is not fully known. Exercise caution when welding by: NOT draping welding leads (guns/cables) over your shoulders or arms, NOT coiling them around your body, NOT inserting yourself directly between the cables, and by NOT contacting the unit while welding. DO keep the work clamp connected as close as possible to the area of the weld and directly to the object being welded whenever possible.
9
Important Information: Operating this unit with a generator or other off-grid service.
This welder should only be operated on a generator certified by its manufacturer to produce clean power. Clean power is equivalent to the quality of household or shop/garage type power. This means the generator must have 5% or less total harmonic distortion (THD) of the Sine wave. If you are unsure of the power output type of the generator, contact the manufacturer of the generator for verification. Do not operate on square wave or modified square wave generators or converters/inverters or damage or malfunction may occur. Damage caused by running this welder off of “ dirty ” power or modified sine waves may not be readily apparent and can be cumulative in nature. However, damage may present itself immediately. The damage caused by running this welder on “ dirty ” power usually leaves internal tell tale signs and damages specific parts.
When operating on 120V 1 phase, you will need a minimum of 5500 surge Watts. Ideally, it is recommended for use with
6000 watt generators or larger. Operating the unit on under powered generators and/or on generators not rated with 5% or less THD can damage your unit. The generator manufacturer determines this rating, not Everlast. Do not assume that a name brand generator, or a “ new ” generator automatically provides clean power. Price paid does not guarantee a clean power output either. There are multiple brands at various price points capable of producing clean power. Investigate this before purchasing a generator. The manufacturer will usually state that a unit is clean power in the advertising information and will state actual THD. If the manufacturer does not state it, contact the manufacturer directly for actual THD.
NOTICE! Operation of this unit with generators not rated by its manufacturer as providing clean power (5% or less THD) is prohibited and will void the warranty. Operation with modified sine wave, or square wave generators and inverters/converters/
UPS that do not produce “ sine wave ” output is prohibited and doing so will also void the warranty. Use only with generators/ inverters/converters that produce an equivalent type of sine wave used in shops, homes and “ shore ” type systems.
WARNING! Do not start or stop the generator with the welder switched on. Never use the generator in ECO mode or an auto idle mode. Even with a clean power rated generator, this action can damage the unit. Turn on the welder only after full generator R.P.M. has been achieved and the engine is sufficiently warmed up.
Closely monitor generator fuel level so that the engine R.P.M doesn ’ t drop or completely shut down with the welder plugged in. For best practice: do not start or stop the generator with this welder plugged in, even if it is turned off. Unplug the welder before shutting down the generator.
If using with a welder generator, make sure the manufacturer has determined that the generator portion produces a clean sine wave. Many older models do not. Some newer models use “ divided ” power between welding and generating and cannot supply the full power to the welder unless the fine current control knob is turned to maximum. Do not use this unit with such welder/generators unless the Power/fine current control is turned to 100%. Some welder generators do have a separate alternator for generating power. If this is the case, just be sure not to weld or load the machine while this unit is in use.
WARNING! Always make sure any generator or welder generator is properly grounded, according to local code. Ground the machine per the generator manufacturers instructions to meet code. Improperly grounded generators may damage the machine and more importantly may cause severe injury or death.
Extension Cord Use:
This unit will exceed the capability of most common extension cords. You should only operate this unit on a 10 gauge extension cord that is 50 ft or less in length. Do not operate on smaller gauge extension cords. Operation on cords that are undersized or excessive in length may damage the machine and void the warranty.
10
Specifications
Construction Type
Input Voltage
Phase
I1MAX Current Rating (Inrush Amps)
I1EFF Current Rating (Rated Amps)
OCV
Processes
MIG Duty Cycle (Rated at 40 ° C @ Max Output) *
MIG Output Range
Pre Flow / Post Flow Gas Time
Burn Back Control
MIG Inductance
Wire Spool Size
Wire Diameter Stock Drive Rolls
Maximum Wire Diameter with Optional Drive Roll**
Wire Feed Speed
Recommended Spool Gun
PowerSet Metal/Gas Combinations
MIG Gun Type/Length/ Connector Type
Work Clamp with Cable Length
250A Stick Electrode Holder Length
Power Cable Length
Power Plug Type for 120V
Cooling Type
Dimensions (Approximate with handles installed)
Weight (Bare Unit)
Ingress Protection Rating
Product Specifications
Inverter (IGBT based, Digital Control)
120V(± 10%) 50/60 Hz
1 Phase 50/60Hz
120V @ 37A
120V @ 19A
60V
GMAW/FCAW (FCAW requires purchase of optional drive rolls)
25% @ 140A/21V, 60% @ 90A/18.5V
13V 21V/ 25 140A
Auto Controlled
Auto
Fixed
4” or 8” (2 12 lbs typically)
.023” .030” (.6mm – .9
mm)
.035” Solid Wire,.045
” Flux Cored/Aluminum
No Load: 50 400 IPM. Loaded: 0 385 IPM
SM100N
Steel/100% CO2, Steel/ 75/25% Ar/CO2, Flux
Core (Gasless, Self shielded)
15 Series, 9.5 ft. (3m)
5 ft (1.5m) DINSE 25 (3/8 nom. dia.)
9.5 ft (3m) DINSE 35/50 (1/2” nom. dia.)
6.5 ft (2m)
NEMA 5 15P (North American Standard)
Full Time Fan
12.5” H X 8.5” W X 17.5” L
26.5 lbs.
IP21S
**May require a liner change or different gun, or special consumables.
*Duty Cycle
Duty Cycle is simply the amount of time out of a 10 minute period in which the unit can operate. For example, if this unit has a duty cycle of 25%, that means that the unit can be operated for 2.5 minutes out of 10 minutes. This may be continuously, or intermittently during the 10 minute period of time.
This rating standard (United States) is based on a maximum ambient temperature of 40 C. Operating above this point, or at lower temperatures with high humidity may reduce the duty cycle rating. Of course, the duty cycle may increase somewhat as ambient temperature drops. Regardless, this unit ’ s duty cycle is not controlled by a timer. Rather, this unit is equipped with a heat sensor located on a heat sink near the critical power components of the welder. If the operating temperature of the unit is exceeded, welding output will stop and an over temperature warning light/error code will be displayed on the panel. If a duty cycle event is registered, do not turn the unit off! Allow the welder to continue to run at idle for at least 10 15 minutes until the temperature has fallen enough to reset the sensor and over temperature warning light . Even if the unit resets, allow the unit to cool for a full 15 minutes, or the duty cycle will be more quickly triggered since the unit resets just below the heat threshold. The fan(s) must continue to run for a full
15 minutes to cool the unit properly after the duty cycle shut down has occurred. After 15 minutes of cooling, you may switch the unit off if you are finished welding. If the unit does not automatically reset after 15 minutes, turn the unit off. Wait for 15 seconds before turning the machine back on. If the unit does not reset, contact technical support for further advice and assistance. As a best practice, when you have completed welding and have been welding continuously for extended periods of time, keep your unit on for 10 additional minutes without welding to allow it to cool.
The intentional and/or repeated triggering of the duty cycle protection feature on this unit will shorten the lifespan of the unit ’ s electronics and can weaken internal components. The effect of overheating your unit repeatedly takes a cumulative toll on the unit.
Breaker Sizing and Wiring Requirements
Before installation of this unit in any facility, always consult a licensed local electrician familiar with the requirements of properly wiring a welder into the electrical supply.
Refer to the National Electric Code (NEC) and local codes. If needed, refer the electrician to Article 630 of the NEC during consultation to determine proper application and wiring needs. Use the I1MAX and the I1EFF ratings listed above to determine the proper breaker and conductor (wire) sizing required. Everlast welders are designed around use in industrial wiring applications and are intended to be used with modern electrical systems. Household wiring may need to be upgraded before this welder may be installed. Additional HF protection and isolation may be needed if this welder interferes with the operation of electrical/electronic equipment. WARNING! Do not modify welder wiring. This unit meets the standards for conductor sizing on the power cable and takes into account power cable length, duty cycle and rated current.
11
Duty Cycle
Duty Cycle
Duty Cycle is simply the amount of time out of a 10 minute period in which the unit can operate. For example, this unit has a duty cycle of 25%. This means that the unit can be operated for 2.5 minutes out of 10 minutes at 140 Amps maximum output. This may be continuously, or intermittently during the 10 minute period of time.
This rating standard (United States) is based on a maximum ambient temperature of 40 C. Operating above this point, or at lower temperatures with high humidity may reduce the duty cycle rating. Of course, the duty cycle may increase somewhat as ambient temperature drops. Regardless, this unit ’ s duty cycle is not controlled by a timer. Rather, this unit is equipped with a heat sensor located on a heat sink near the critical power components of the welder. If the operating temperature of the unit is exceeded, welding output will stop and an over temperature warning light/error code will be displayed on the panel. If a duty cycle event is registered, do not turn the unit off! Allow the welder to continue to run at idle for at least 10 15 minutes until the temperature has fallen enough to reset the sensor and over temperature warning light . Even if the unit resets, allow the unit to cool for a full 15 minutes, or the duty cycle will be more quickly triggered since the unit resets just below the heat threshold. The fan(s) must continue to run for a full 15 minutes to cool the unit properly after the duty cycle shut down has occurred. After 15 minutes of cooling, you may switch the unit off if you are finished welding. If the unit does not automatically reset after 15 minutes, turn the unit off. Wait for 15 seconds before turning the machine back on. If the unit does not reset, contact technical support for further advice and assistance. As a best practice, when you have completed welding and have been welding continuously for extended periods of time, keep your unit on for 10 additional minutes without welding to allow it to cool.
The intentional and/or repeated triggering of the duty cycle protection feature on this unit will shorten the lifespan of the unit ’ s electronics and can weaken internal components. The effect of overheating your unit repeatedly takes a cumulative toll on the unit.
12
Setup Guide
UNPACK YOUR UNIT.
Upon arrival, you will need to completely unpack your unit, and check things over. This is a time sensitive matter. Do not delay or hold the welder unopened in the box. First, make sure the unit is opened from the top. Be careful with using knives and sharp objects so you won ’ t cut cords and cables inside the boxes. Lay all items out and inspect them.
You should have the following in your box:
1.
Welder
2.
15 Series MIG Gun 3m (9.5 ft.)
3.
Work Clamp 1.5m (5 ft)
4.
Floating Ball Type Regulator with Gas Line (4a)
1
4a
4
2 3
Inspect the welder for damage. Check for the presence and general condition of the accessories. Some slight rubbing or chaffing of some of the accessories may be present, but this is considered normal. If any item is damaged or missing, please inform Everlast within
72 hours of product receipt. See pages 4 and 5 for more details.
Assemble the front, middle and rear handles with the supplied screws. Do not overtighten the screws.
NOTICE:
This unit is shipped with a .023” and .030” drive roll intended to feed solid MIG wire. While the unit is designed for use with Flux cored, self shielded wire, the flux core drive roll is optional. The same is true if you desire to .035” solid MIG wire. The .030” diameter wire is the best choice for the widest range of use with steel. If desired, you will need to purchase additional drive rolls. Additionally, for best results a flux core nozzle may be purchased for use with your 15 series MIG gun.
These may be bought locally. Currently Everlast does not offer the Flux
Cored only nozzles for sale. (Subject to change).
POWER UP AND TEST YOUR UNIT.
You will need to fully test the unit as soon as possible. Within 72 hours after receipt of the unit, be sure to have every thing you need at hand to test the unit. Make sure the correct input power, wiring, and plug configuration is being used. Then, power up your machine without any accessories installed. Allow the unit to idle for 15 minutes. Check and observe operation of knobs, controls and buttons, cycling through each as required. Make sure the fan is running at full speed. After the test is completed, turn the unit off, connect the accessories, shielding gas (customer supplied) and conduct live testing of all the functions and features of the machine. For testing and welding make sure work clamp is connected directly to the part being welded (work). Check for arc starting and stability. If prob-
Getting Started lems are observed, contact Everlast. See page 5 for more information. NOTICE: Cosmetic damage claims after 30 days will not be accepted, unless Everlast is contacted and informed of such delay and reason for such a required delay (ie. Overseas in deployment)
CHECK FOR GAS LEAKS.
Be sure to check for gas leaks before attempting to weld. You can test this by first installing both back caps into the torch head (from both sides). Next install the regulator and tighten to both cylinder and unit (see section on regulator installation). After the regulator is secured, the gas flow should be set and tested. First, release all tension on the wire feeder so the wire does not feed through the gun. Next trigger the gas flow with the torch switch by holding the torch switch down, while observing the ball on the regulator. It will float while the torch switch is held. If the trigger is released, after the post flow(2 3 seconds), the ball will sink and settle to the bottom. If the ball continues to flow after 2 3 seconds, or if you hear or suspect leaks, use warm, soapy water (or a dedicated leak testing solution available from welding suppliers) and spray on all connections, including the torch connections at the head and handle. If any leaks are present, bubbles will form around the area of the leak. Tighten any clamps or fittings found to be leaking. If the problem cannot be remedied, contact Everlast.
DISTANCE YOUR WELDER FROM YOUR WORK.
As a best practice technique, be sure to locate your welder away from the immediate area you are welding. The fan found in your unit is powerful enough to create strong air turbulence in the weld area.
This will disrupt the smooth, even flow of shielding gas around your weld creating unstable arcs, and a porous look to the weld. If possible the welder should be located at least 4 5 feet away from the weld area and should be on a different level to prevent weld porosity and defects being created by the welder ’ s fan system. Keep in mind the fan draws air in from the rear and exhausts out the front and the sides of the unit. If welding outdoors, and a breeze is present, erect a wind screen around your weld area, using a tarp, plywood or similar material.
GIVE YOUR WELDER SPACE TO COOL.
The welder needs room to cool itself. Place the unit in a place that will allow 18” from all sides to allow for proper cooling. The welder pulls air in from the rear, and pushes it through the unit ’ s heat sinks to cool the electronics. The air is then exhausted through the front panel and side louvers of the unit. If the sides are blocked or restricted, the duty cycle will be reduced, and overheating will occur, leading to possible damage if the restriction is severe enough. Never attempt to restrict air flow by attaching filters to the vents. Do not modify the unit for “ on demand ” fan service, or the warranty will be voided.
13
Setup Guide
Getting Started
CONNECT YOUR UNIT TO THE OUTLET.
NOTICE:
There are special rules centered around wiring an outlet for service with a welding machine. The National Electric Code under Article
630 has developed specific regulations for wiring electrical service for welding equipment. These are different than for other types of service such as a stove or dryer in a household or even in a commercial application. You need to consult and/or employ a locally licensed electrician before installing this unit to make sure all national and local codes are followed. If you are not qualified to make these connections, don ’ t. Everlast is in no way liable for any damages caused by improper connection of your welder. Your welder should be on a dedicated branch circuit not far from an electrical disconnect box. Importantly, it should not share circuits with other shop or household items.
Your unit has been shipped with a NEMA 5 15P welder plug. This is the standard for 120V 1 Phase welders in North America. While the unit needs at least a 30A slow blow fuse, or time delayed trip breaker, the unit itself does not need a 30A plug or 30A rated conductor for safe operation. The plug and cable size are rated for the effective rating, and not the inrush rating of the unit. Also, the duty cycle of the unit is factored into the equation.. This is not a continuous duty like an air conditioner that continuously under heavy load. This unit is rated for 25% duty cycle and has a properly sized conductor and plug for this unit. However, due to long runs, a heavier gauge conductor to the receptacle from the breker box may be needed
(depending on length of the distance from the breaker box to the receptacle.) For more information, refer to Article 630 of the NEC. It is recommended to install a dedicated 120V circuit for use with this unit. No other equipment should be used or installed on this circuit during use.
NOTICE:
Do not use this unit with extension cords that are in excess of 25 ft in length. Although the 120V plug is considered 15A and the conductor is 12AWG , it is properly sized for duty cycle and I1EFF current (rated), when combined with length. However, use a 10 gauge minimum sized cord for safety due to the longer lengths. If you cannot find a 10 gauge cord, this type of cord is commonly available as an RV extension cord. 15A adapters are usually available for these cords. Alternatively, you may have one made up.
14
Setup Guide
Getting Started
CONNECT YOUR UNIT TO THE SHIELDING GAS.
What Shielding Gas Should Be Used?
With this unit, the choice of shielding gas is simple. For MIG
(GMAW) you may choose either the standard 75/25 ( which is 75%
CO2 and 25% Argon), or you may choose 100% CO2. For Stainless, use a Tri MIX type of gas with Helium. For Self Shielded Flux Cored wire welding, since it is gasless, no shielding gas is needed. Keep in mind this unit is not designed for gas shielded Flux Cored wire and should not be used with this unit.
Connect Regulator To Cylinder And Unit.
Always wear safety glasses when changing a cylinder. Before installing any cylinder, the cylinder must be chained upright to the wall or a cart. After installing the chains, uncap the cylinder. The cap may need a wrench or screw driver inserted into the cap slot to break it loose. Stand to the side of the valve, away from the discharge, and quickly open the cylinder to give it a quick blast. This will dislodge any dirt or particles stuck in the valve or the connection seat. This will help reduce the chance of dirt particles making its way into the solenoid valve, causing sticking issues later on.
Connecting your cylinder will require a cylinder wrench(1 1/16”) to connect the regulator to the cylinder (North American Cylinders with a 580 CGA valve). If you do not have a cylinder wrench, an adjustable type wrench will work, but make sure it is properly adjusted to prevent rounding of the fitting shoulders. Do not use pliers, or a serrated jaw wrench such as a pipe wrench or basin wrench to tighten the fitting. The design of the fitting means that no thread sealing tape or compound needs to be used. check for leaks. Leaks are indicated by the forming of bubbles. Retighten as needed. However, do not over tighten. If the leak does not disappear, remove the problem fitting and inspect it for dirt or metal filings, then re install and recheck.
Locate the Regulator in the packaging. The regulator may have either a hose barb connection, or a threaded connection. If the regulator supplied has a hose barb, make sure the hose barb fitting is tight on the regulator.
Connect the regulator tubing to the regulator. Tighten with a 3/4” (19mm) wrench. If it is a threaded connection, use two 3/4” (19mm) wrenches to hold both the regulator and the tubing connection at the same time. Hold counter pressure on the regulator connector while tightening the hose fitting to prevent damage to the regulator and to ensure maximum sealing.
After connecting the tubing to the regulator, connect the other end of the tubing to the one 3/4” other 3/4”(19
5/8” CGA fitting on the unit. Hold the fitting on the unit with
(19mm) wrench firmly while tightening the hose fitting with anmm) wrench.
• Inspect and verify the pressure on the cylinder. The dial reads in both PSI and Metric Equivalents.
ADJUST THE REGULATOR FLOW RATE.
• Switch the unit on. While holding the MIG gun trigger, start opening the the regulator valve by twisting the regulator adjustment knob counter clockwise As you open the valve, the floating ball will begin to rise. NOTICE: To avoid spooling out and wasting wire during this time, release the tension on the drive wheels by flipping the tensioning lever to the down position before you begin. This will release tension and allow the drive rolls to safely turn without feeding any wire.
• Important! Do not use thread tape or pipe sealant on any cylinder, regulator or unit connection. The residue and debris may get into the gas solenoid. Install the cylinder on the cart or chain it to the wall closest to the welder. Do not overtighten. If leaks persist, remove regulator from cylinder and inspect fittings for dirt or debris. Do not attempt to repair a leaking regulator. Contact Everlast for a warranty replacement if a leak is discovered in the regulator itself.
• Use a mixture of warm mildly soapy water to brush on the fittings and
• Increase the gas flow rate to a beginning point of 20 25 Cubic Feet
Per Hour (indicated on the clear gauge with the floating ball by CFH).
If MIG/Spool Gun welding Aluminum, increase flow rate to 35 CFH.
Read the middle of the ball for the best reading. Do not confuse pressure on the cylinder gauge with the flow rate on the floating ball gauge. Pressure present on the cylinder gauge does not mean gas is flowing. However, a lack of pressure on the gauge may mean there
15
Setup Guide
Getting Started is no gas flowing.
• Once adjustment is completed release the trigger. The gas will delay slightly until the post flow timer automatically shuts off the gas flow.
The ball will settle.
• When welding it may be necessary to increase or decrease gas flow rate to compensate for conditions. If you are welding outdoors or in drafty conditions, increase the flow rate until weld porosity disappears. In extreme cases, you may need to set up a tarp or plywood to serve as a wind break.
In mild conditions, if a breeze is lightly blowing you can position your body to block the wind. Alternatively, you can choose to weld with flux cored wire to eliminate this problem
• If you are concerned about wasting gas, or think gas consumption is too high, you may turn down the gas. While testing on scrap metal, turn the gas down incrementally until bubbles and porosity just begin to appear. Once they appear, adjust the regulator slightly so that they once again disappear. Once they fully disappear, add another
CFH and you will have a properly adjusted regulator
• When pressure on the cylinder drops below 300 to 500 psi, it is common to have to readjust the flow regulator to compensate for the lower pressure. Pressures under 100 psi may create unstable gas flow. Once you reach 200 psi, have a replacement cylinder ready to change out. If you completely run out of shielding gas while welding it is likely you may have some hidden porosity in your welds, creating weak welds. Always change the cylinder out when gas levels reach
75 psi.
NOTICE: If you are planning on welding during holidays or during weekends, always take notice of the cylinder pressure well before hand. This will allow you time to get another cylinder before stores close for the holidays or weekends. If possible, you may want to purchase a 20CFH cylinder in addition to the regular gas cylinder that you lease or purchase so that you have a backup cylinder in case of an emergency. A 20CFH cylinder will last an hour or two of welding. These are relatively inexpensive and can even be bought “ pre loaded ” with gas in many chain hardware stores and farm stores. These can also be refilled when empty.
Adjust the Regulator/Flow Meter.
Floating Ball
Increase flow rate by rotating the control knob counter clockwise.
WARNING!
Never leave the gas cylinder turned open after shutting the unit down after welding is finished. Always make it a practice to close the main cylinder valve immediately after turning off the welder for more than 15 minutes. A malfunctioning regulator, valve or blown hose could fill the area with shielding gas. Argon and CO2 will build up and you can asphyxiate if the contents are not dispersed. Argon and CO2 are odorless, tasteless gases which can cause suffocation. Always fully open the cylinder valve or have it fully closed. Never leave a valve “ in between ”. Cylinder valves are only designed not to leak when they are either fully open or fully closed. Use the regulator to adjust the pressure. Do not use the tank valve to adjust the pressure.
16
Setup Guide
Getting Started
Testing Wire Feed Operation and MIG Gun Installation
After inspecting the unit for power up, it is necessary to confirm wire feed operation. This is a simple process that requires you to install the MIG gun on the unit.
To install the MIG gun:
MIG/Spool Gun (Gas) Polarity +
• Locate the MIG gun in the accessory box. Uncoil the gun and straighten it out.
• Refer to the drawing below. Line up the Euro Connector on the end of the gun with the connector on the unit, making sure the protruding pins are lining up with the corresponding hole.
• Once the pins are lined up, push the connector in until it is seated. Hand tighten the collar nut clockwise. Do not overtighten or use tools.
• Once the nut is tight, gently shake the connector to confirm that the gun is fully seated and the nut is still tight.
After you install the MIG gun, set the wire speed knob to maximum. Open the MIG door so that you can see the drive feeder mechanism. Set the wire feed control to the maximum setting. Pull the trigger to check that the drive mechanism is turning.
If it does not turn, check the MIG gun connection once again. If the drive wheel fails to rotate, contact technical support for further assistance.
MIG or Spool Gun
Work Clamp ( )
To Wire Feeder (+)
NOTICE: The Spool Gun attaches to the gun connection and the center control connector.
MIG/Spool Gun Installation
MIG Flux
-
Cored (Gasless) Polarity
-
Work Clamp (+)
MIG Gun
MIG Gun Connector
Rotate nut clockwise (hand tight).
Selecting Polarity
Choosing the correct polarity for the welding process that you are welding is, important. Without the correct polarity, weld quality and weldability of a metal will be an issue. Incorrect polarity can also cause undesirable operation of the welder such as excess spatter, birds nesting of the wire, electrode sticking, excessive consumable wear, and arc instability.
See the following images to determine which polarity should be used with your process.
To Wire Feeder ( )
NOTICE: This unit is for use with gasless, self shielded wire only. This unit is not intended for use with Gas Shielded Flux cored Wire (FCAW G).
17
Setup Guide
Getting Started
Install the Wire Spool.
The spool carrier assembly consists of several parts. Each part must be assembled correctly. See the illustration below. There are two collars that support the 8” spool. There is an inner collar and an outer collar. The roll is held in place by tension placed on the outer collar by a small spring and a small finger nut. During installation of the wire spool, pay attention to the outer collar direction when you remove it. Viewing from the rear, the narrow shoulder of the collar faces the inside. The wider side of the collar should be turned toward the outside of the welder, facing the welder door when closed. If the outer collar direction is reversed, you will have difficulty installing the spring and the tension will be too tight. Installation of the wire spool is slightly different depending upon the spool size. For 8” spools, the spool rides on the narrow shoulders of the two collars. The spool rotates on these collars. To install 4” spools, the spool is installed so that it sits between the two collars and rotates on the spindle stud.
Wire Spool Installation
Wire Spool Direction and Rotation
Which Spool Gun?
If you are wishing to extend your reach, you may be interested in using the spool gun function. If you are, you will need to purchase the
SM100N spool gun for use with this unit. It is calibrated and best synchronized for this unit. Typically spool guns are used to weld Aluminum, and occasionally small spools of flux cored wire or stainless. While this unit does not have a specific PowerSet setting for Aluminum, or Stainless, it can be used to weld in manual mode with either. Select the default C25 setting and the spool gun in this case. This will help ensure the correct gas flow programming and a moderated level of arc force
(inductance).
The wire spool must be installed so that the wire unwraps and feeds from the bottom of the spool. It should never be installed so the wire comes over the top. When installed properly, the spool will turn counter clockwise. See the following illustration for proper rotation direction. Tension the spring with the finger nut until the spool will only free wheel 1/4” turn when spun by hand. Do not let the spool free wheel completely or the wire will unwind itself and can get tangled. Don ’ t over tighten the spool, as this will cause rapid wear to the feeder components.
18
Setup Guide
Getting Started
Identifying and Changing the Drive Rolls.
Guiding the Wire Through the Feeder and Gun.
The unit comes equipped with .023” and .030” drive rolls. NOTICE: For most purposes you will likely want to use .030” wire in this unit since it covers the greatest range of metal thicknesses and amperages within the capability of this unit. However, if you change wire size or type, you will need to change the drive roll to the correct size and type.
This unit uses two drive rolls to feed the wire. The top drive roll is actually an idler roll used to hold tension and keep the wire in the groove and is not changeable. Only the bottom drive roll needs to be changed. The bottom drive roll has two small grooves that are sized for .023(.025”) and .030” wire. Additional sizes and types of drive rolls are available as options. The standard installed drive roll is meant to feed hard (solid) steel wire. The groove on this drive roll has a “ V ” shape designed for the solid wire. A Flux Cored drive roll has a serrated edge to the groove, which grips the softer, cored wire. Viewing a flux core drive roll from the top, you will see a “ zipper ” like pattern. This should never be used to feed hard steel or stainless wire or aluminum wire. This will result in damage to the wire, metal flaking and possible plugging of the MIG gun liner. To determine the exact size of wire and type you have, look at the side of the drive roll. The size of the drive roll groove is stamped on the side of the drive roll closest to the corresponding groove. The type of the drive roll will also be stamped with a V if it is for solid hard wire. If it is stamped with a “ U ”, this is a special drive roll for feeding aluminum wire. Aluminum wire is best fed with a spool gun.
Once the wire spool has been installed, flip the tensioner lever down and raise the top drive roll to the upper position. See the illustration below.
Gently guide the wire from the spool over through the wire feeder and into the front section of the gun at least 6 inches. Make sure the wire lays neatly in the groove. Hold it with your finger if necessary as you lower the top drive roll down and raise the tensioning lever with your other hand. When complete the wire should look like the illustration on the previous page.
Hint: The wire on the spool is usually bent and threaded through a small hole in the side of the spool to lock it in place and prevent de spooling of the wire. Keep one hand on the wire spool to prevent despoiling and cut the wire loose with a pair of wire cutters. Trim the wire to make sure the end of the wire is straight and able to be threaded through the wire feeder mechanism and gun.
Installing the MIG Wire
The drive roll is held in place by a black thumbscrew. Remove the screw to expose and change the drive roll. The drive roll is mounted on a bushing. The bushing should be held in place with one finger of one hand while the other hand removes the drive roll. This will prevent both bushing and drive roll from being removed from the wire feeder drive shaft. When removing make sure that the square locating key is not dismounted. If the key falls out, replace it before replacing the drive roll.
Drive Roll Size and Location Info
After the tensioner is raised back to the vertical position, confirm the wire is still in the groove and is not riding up on the shoulders of the drive roll.
Turn the welder on and adjust wire feed speed (IPM) to maximum. Remove the gas nozzle by twisting it clockwise and pull. Unscrew the contact tip as shown in the illustration below. Hold the gun cable and gun straight as possible. Pull the trigger on the gun. The wire should slowly begin to feed through the gun cable and eventually through the gun. As the wire exits the gun, allow 3 to 4 extra inches of wire to be fed out past the diffusor. Re install the contact tip over the wire and screw it in clockwise until it is tight, but not to the point of stripping. Install the gas nozzle.
5
.6mm =.023”/.025”
.8mm= .030”
.9mm= .035”
1.0mm= .040”
Assembling the MIG Gun
Always remove and install the gas nozzle by twisting clockwise.
Size/Type Stamping.
(The size is stamped on same side as corresponding groove.)
19
Gas Nozzle
M6 Contact Tip
Diffusor and Retaining Spring
Gun Neck
Flux Cored Cap
(not included, sourced from aftermarket)
Setup Guide
Getting Started
Trim the wire sticking out of the nozzle to 1/4” to 3/8” (6mm to 9mm) in length with wire cutters. See the illustration below. The gun is now ready for welding . Hint: Always make sure that you re trim the wire before beginning a new weld if the wire is not already trimmed to this length. This will help to improve arc restarts.
is enough.
Test Wire Tension Before Welding
Trim Wire Before Starting a Weld
4
5
Trim wire to 1/4” 3/8”
(6mm– 9mm)
Curl
Wood Block
Tensioning the Drive Roll Pressure
To feed properly, the wire needs to be tensioned before you begin welding. The tensioning lever has numbers on the dial. To increase tension, rotate the tension lever clock wise. Different types of wires require different tensions. There is no exact tension that works for all wire types. However, for steel wire, you will generally tension to at least 4 on the dial. For flux cored wire, it may be only two or three. Wire diameter also plays a small part in the amount of required tension that is needed. Regardless of the wire type or wire diameter, follow the process below and refer to the following illustration. Turn the unit on and pull the trigger so that the wire extends approximately 1” beyond the gas nozzle.
• Find a small block of wood, such as a two by four, and secure it to the welding table or other solid object. Do not test this on metal!
• Hold the gun approximately 2 inches off the wood. Aim the gun at the block of wood so that the nozzle is at a 30 degree angle to the wood.
• Pull the trigger and allow the wire to contact the block.
• Increase wire tension so that the wire contacts the block of wood and is forced to curl up. Continue holding the trigger so that two or three full spirals are made.
• If the wire stops, or stutters during this process, let go of the trigger immediately and increase tension.
• Adjust the wire until the stuttering or jerking disappears.
• Do not over tighten the tensioner or use more tension than necessary. When the wire begins to curl without any stoppage, the tension
20
Component Identification and Explanation
Front Panel View
7
1
2
3
6
5
4
5
6
7
Number
1
2
3
4
Component Identification
Protective Cover
Door and Latch
Negative Terminal ( )
(DINSE 25 Type, 3/8” approximate dia.)
Wire Feeder Lead
(DINSE 25 Type, 3/8” approximate dia.)
2 Pin Control Connector
Positive Terminal (+)
(DINSE 25 Type, 3/8” approximate dia.)
Handle
Component Note
Keep down and in place during welding activities and in storage.
Keep door closed while in use. Only open for wire replacement and starting
For MIG (GMAW): This is the location of the work clamp
For Gasless (self shielded) Flux Cored (FCAW): This is the location of the wire feeder lead.
This cable and DINSE connector is used to select the polarity of the wire feeder. This connects internally to the wire feeder to supply power to the torch. The unit will not weld without connecting this to either the Positive (+) Terminal or Negative ( ) Terminal and connecting the work clamp to the remaining opposing Terminal.
This connector is the control connector for the Spool Gun. It supplies operating voltage to the drive motor on the gun.
For MIG (GMAW): This is the location of the wire feeder lead.
For Gasless (self shielded) Flux Cored (FCAW): This is the location of the work clamp.
21
Component Identification and Explanation
Rear Panel View
1
2
3
4
5
Number
1
2
3
4
5
Component Identification
Power Switch
Shielding Gas Connection
(5/8” CGA)
Fan location
HF Ground Service Bolt**
Power Cord and NEMA 5 15 Plug
(12 Gauge, 6 ft.)
Component Note
This is used to switch the unit on and off.
5/8” CGA Fitting is used in North American Markets. Other markets may use a hose barb connection.
Periodically check for proper fan function and cleanliness.
For use in a combined effort to mitigate any electrical interference that may be caused by this unit.
This plug and cable is correctly sized for the rated amps, duty cycle and length of the cable. Consult Article 630 of the NEC for more details.
22
Component Identification and Explanation
The Control Panel Layout and Use
2
3
1
MIG C25
MIG C100
FLUX CORED
WFS/AMPS
SELECT
VOLTS
CYCLONE 140E
SELECT
POWER
SET
SPOOL
GUN
6
5
4
Number
1
2
3
4
5
6
Component Identification
Wire Feed Speed Control
Gas Type/ Mode
Parameter Input Selection Buttons
Spool Gun Mode Button
PowerSet Mode Button
Voltage Control
Component Note
This is used to set the Wire Feed Speed (WFS). This controls the top center numerical value on the screen in the “ X ”.
Select this function before selecting any other mode or function. The unit defaults to C25. This is to be used with Aluminum in manual mode when “ spool gun ” is selected or for stainless if it is to be used.
These buttons are used to select the parameters for the PowerSet mode. The left button selects Wire Diameter. The right button
Selects Metal thickness. When the unit is not in PowerSet mode, these buttons serve no function.
Select this button when you wish to use the SM100N spool gun (optional) with this unit.
This engages the PowerSet function which makes selecting the correct volt and wire feed setting much easier.
This is used to set the Voltage. This controls the bottom center numerical value on the screen in the “ X ”.
23
Component Identification and Explanation
The Control Panel Layout and Use
Manual Function and Screen
WFS/AMPS
292
WFS V
MIG C25
MIG C100
FLUX CORED
17.1
POWER
SET
SELECT SELECT
SPOOL
GUN
CYCLONE 140E
Using Manual Mode
To use the mode:
1.
Choose the Gas Type/Mode (i.e. MIG25, MIG 100, or Flux Cored). This is important. You will always need to select this whether you intend to use the PowerSet function or not to ensure that the correct gas programming and arc force (inductance) is being used.
2.
Select the spool gun function if the spool gun has been connected.
3.
Use the left control knob to set the Wire Feed Speed (WFS). This is the top, center numerical value seen in the illustration above.
4.
Use the right control knob to set the Voltage (V). The Voltage is the bottom, center numerical value seen in the illustration above.
OPERATION NOTES:
1.
The Select buttons do not function or serve a purpose in the manual mode.
2.
The segmented bars with the 4 point star serve only as a place holder in this mode. They serve no other purpose in manual mode.
3.
Manual mode may allow you to exceed the wire and/or unit ’ s capacity. Keep in mind this unit is 140A @ 25% Duty cycle.
4.
You may need to purchase additional drive rolls, liners, contact tips, nozzles and other items to take advantage of the full range of this machine.
5.
Although other wire diameters and types are offered, and can be used this unit will function in the widest range with .030” solid wire.
What mode should I use, Manual or PowerSet?
The manual mode is the basic mode that allows you to select and choose your own setting. This is designed for experienced users who have a basic understanding of MIG welding, wire types, and the technical limits of the thicknesses of the wire and volt and wire speed requirements of different thicknesses of metals. If you are new to MIG welding, the PowerSet mode may be your best choice when setting up the unit. This PowerSet mode helps to simplify setup, and reduce the amount of testing needed to derive a correct setting.
If you wish to use the Manual mode, the unit operates very similarly to any other type of MIG. This unit offers adjustment of both wire feed speed and voltage in incremental steps. The full range of adjustment of the machine is available to you at any time. The unit may also be adjusted while welding without causing harm to the machine.
Component Identification and Explanation
The Control Panel Layout and Use
PowerSet Function and Screen
WFS/AMPS
292
WFS
18GA
3/16
16GA
1/4
14GA
5/16
1/8
3/8
MATERIAL
V
5
.023
.030
.035
.045
WIRE
5
MIG C25
MIG C100
FLUX CORED
SELECT
17.1
SELECT
POWER
SET
SPOOL
GUN
2
1 3
CYCLONE 140E
4
Using Power Set
To use the PowerSet mode:
1.
Choose the Gas Type/Mode (i.e. MIG25, MIG 100, or Flux Cored). NOTE: If you select gas type after selecting PowerSet mode, you will drop out of the PowerSet mode and return to manual mode.
2.
Press the PowerSet button to turn on the PowerSet mode.
3.
Use the left select button to select wire diameter. The selected setting will flash continuously. (For .025” and wires, use .023” selection.) NOTE:
Make sure you also have selected the proper drive roll size for the wire feeder. See page 19 for more information.
4.
Use the right select button to select metal thickness. The selected setting will flash continuously. NOTE: If joining different metal thicknesses, select for the thicker metal and position the gun so that the heat is concentrated mostly on the thicker piece .
5.
The machine will automatically give you a centered setting, denoted by the flashing four pointed star for both Volts and Wire Feed Speed.
Moving up or down the range of either the Volts or Wire Feed Speed will cause other segments on the sloped guide to be highlighted and flash.
This gives you a visual reference and a targeted return point if you choose a setting too far off an optimum setting. NOTE: Test the prescribed setting before making any adjustments.
What is Power Set?
PowerSet is a feature that quickly guides you to make the best choice of settings without having to refer to a text or chart information. This feature can be used by beginners or professionals. This is accomplished by requiring you to input 3 separate pieces of information about your weld that help determine the best setting for Volts (V) and Wire Feed Speed (WFS).
Once these pieces of information are entered, the machines programming determines a setting for you. Although an optimized setting is determined, this is based on average welding conditions, since no programming can take into account every variable. In general, you should find that the settings that the unit selects are very useable in most conditions. However, even if you find that the settings the unit ’ s programming provides are not suitable (for example you are welding out of position or joining different thicknesses of metal) the PowerSet mode does not lock you into that exact setting. In fact, it allows you to fine tune both volts and wire feed speed, up or down, within a limited range. Don ’ t worry about not being able to fine tune the units setting enough. The limited range accommodates plenty of adjustment, but it is designed to help prevent you from making a completely unworkable setting. The range is typically one full volt higher or
25
Component Identification and Explanation
The Control Panel Layout and Use
PowerSet Function and Screen
lower than the recommended setting and 10 IPM higher or lower than the recommended setting. However, this may vary if the unit is reaching maximum Voltage or Wire Feed Speed Capacity. The display gives you a visual, sloped and segmented guide that helps you monitor exactly how far off the prescribed setting you have gone, and allows you to return to the programmed setting.
What metals can I weld with PowerSet?
The E (economy) series MIGs are designed for the average user in mind who will typically use the MIG to weld Mild Steels. So, the metal type is assumed to be steel. Other, more advanced MIGs in the product line allow you to choose the type of metal as well. But for this simplified version, steel is the default metal. If you need to weld other metals, use the manual mode and the default MIG C25 mode. This includes the spool gun mode for Aluminum.
What are the limitations of PowerSet?
PowerSet is designed to help you make a decision on the best setting for general purpose use. Quite simply, it is a guide based off of average expected use. It cannot take into account every possible variable or make adjustments for things like the different settings that may be required to weld vertical up, or for an outside edge weld on thin materials. It does not compensate for technical welding errors, lack of metal prep, or skill issues.
It ’ s simply to help you make the setup process quicker and easier. Having a basic knowledge of MIG welding is still required to make sound welds.
Some welders may feel “ limited ” by the narrowed adjustment range of the unit as the PowerSet mode does not allow the full range of adjustment.
But in reality, this narrowed range is considered the limits of the amount of deviation that you can have and still make a sound weld. In fact, it may even allow you to exceed the limits of what would be considered acceptable in some circumstances.
Additionally, this welder only allows you to use PowerSet mode for Steel.
This E series model is very basic and only allows you to select the wire type, size, and metal thickness and not the metal type. Always assume you are welding a mild steel. NOTICE: Always test your weld setting first, before welding anything critical, structural or of significant economic value.
Everlast in no way can be held responsible for providing settings in PowerSet mode that may cause poor weld results or unusable weld settings. If you do not find satisfactory results in PowerSet mode, use manual mode.
Why Are Some Choices Blocked in
PowerSet Mode?
You many notice that some of the setting choices are blocked or unavailable to you on this machine. This is normal. There are several reasons why this can happen.
1.
This unit shares a common LCD screen with another model. In order to simplify production and increase parts interchangeability, the screen carries programming for both units. The main control board decides which function to unlock from there. Larger diameter wires and metal thicknesses may be blocked.
2.
If a selection or combination of selections are made, it would exceed the welder ’ s capacity.
3.
If a wire diameter has been chosen, the metal thickness may exceed the capacity of the wire to be able to weld it.
4.
The technical limitations of the wire output has been reached. In other words, every wire diameter has a technical upper and lower
Amp limit. Amps are controlled by Wire speed and wire diameter.
Exceeding this limit can cause problems like burn back, excessive spatter, vaporizing of the wire etc. If the minimum wire feed threshold is not reached for a wire diameter to burn properly on a thin piece of steel, without burning through, the unit may not allow that thickness choice. However, if the machine does allow a particular adjustment in Volts or Wire Speed to be made in PowerSet mode, it does not guarantee it will be a useable or proper setting in every case. In order to err on the side of giving the user more freedom of adjustment in the PowerSet mode some combinations of
Volt and Amp settings may allow you to exceed the technical recommendations of the wire, and welding thicknesses.
5.
The stated capacity of this welder is greater than what is allowed in
PowerSet mode because of issues surrounding best practices in the industry versus what can theoretically be done. With this unit, thicker metals may be welded but with multiple passes. Multi pass welds are usually done at lower Volt and Wire Feed settings. If the unit does not allow adjustment or selection of a thicker metal, or limits setting, this is by default, an indication that you should consider using multiple passes with the wire size/gas you are using, and use manual mode. The machine cannot discriminate between multiple pass weld requirements and single pass weld requirements.
It must assume single pass. Again, even though the adjustment may be allowed, it doesn ’ t mean that at the extremes of capacity of a given wire size, it will yield a desirable weld.
26
Component Identification and Explanation
The Control Panel Layout and Use
PowerSet Function and Screen
PowerSet Chart Recommended and Range Settings *
Gas Type/Mode Wire Size Metal Thickness WFS Range Optimized Setting Volt Range Optimized Setting
.035”
.030”
.030”
.030”
.030”
.035”
.035”
.035”
.035”
.045”
.045”
.045”
.045”
.030”
.030”
.030”
.030”
.035”
.035”
.035”
.023”
.023”
.030”
.030”
.030”
.030”
.035”
.035”
.035”
.035”
.035”
.023”
.023”
MIG C100
MIG C100
MIG C100
MIG C100
MIG C100
MIG C100
MIG C100
MIG C100
Flux Cored
Flux Cored
Flux Cored
Flux Cored
Flux Cored
Flux Cored
Flux Cored
Flux Cored
Flux Cored
Flux Cored
Flux Cored
Flux Cored
MIG C25
MIG C25
MIG C25
MIG C25
MIG C25
MIG C25
MIG C25
MIG C25
MIG C25
MIG C25
MIG C25
MIG C100
MIG C100
230 IPM
92 IPM
110 IPM
167 IPM
350 IPM
73 IPM
82 IPM
133 IPM
140 IPM
205 IPM
220 IPM
260 IPM
163 IPM
180 IPM
204 IPM
283 IPM
82 IPM
86 IPM
131 IPM
175 IPM
261 IPM
271 IPM
176 IPM
185 IPM
190 IPM
240 IPM
159 IPM
175 IPM
203 IPM
275 IPM
300 IPM
260 IPM
300 IPM
18 Gauge
16 Gauge
18 Gauge
16 Gauge
14 Gauge
1/8”
18 Gauge
16 Gauge
251
261
166
175
180
230
149
165
-
-
-
-
-
-
-
-
271 IPM
281 IPM
186 IPM
185 IPM
200 IPM
250 IPM
169 IPM
185 IPM
14 Gauge 193 213 IPM
1/8” 265 285 IPM
3/16”
18 Gauge
16 Gauge
290
250
290 -
-
-
310 IPM
270 IPM
310 IPM
18 Gauge
16 Gauge
14 Gauge
1/8”
18 Gauge
16 Gauge
14 Gauge
130 150 IPM
195 215 IPM
210 230 IPM
250 270 IPM
153 173 IPM
170 190 IPM
194 214 IPM
1/8”
18 Gauge
16 Gauge
14 Gauge
220 240 IPM
82 102 IPM
100 120 IPM
157 177 IPM
1/8” Gauge 340 360 IPM
18 Gauge 63 83 IPM
16 Gauge
14 Gauge
72
123
-
-
92 IPM
143 IPM
1/8”
16 Gauge
14 Gauge
1/8”
3/16”
273 293 IPM
72 92 IPM
76 96 IPM
121 141 IPM
165 185 IPM
15.4
17.4 V
16.2
18.2 V
17.0
19.0 V
18.0
20.0 V
15.8
17.8 V
17.0
19.0 V
18.0
20.0 V
19.0
21.0 V
14.5
16.5 V
15.2
17.2 V
15.7
17.7 V
19.7
21.0 V
14.5
16.5 V
14.5
16.5 V
16.0
18.0 V
19.9V
21 V
14.5
15.5 V
15.3
17.3 V
19.0
21.0 V
19.9
21.0 V
15.1
17.1 V
15.5
17.5 V
15.4
17.4 V
15.8
17.8 V
16.0
18.0 V
17.7
19.7 V
15.8
17.8 V
16.2
18.2 V
18.3
19.3 V
19.2
21.0 V
19.8
21.0 V
16.0
18.0 V
16.5
18.5 V
20.0 V
15.5 V
16.2 V
16.7 V
20.7 V
15.5 V
15.5 V
17.0 V
16.4 V
17.2 V
18.0 V
19.0 V
16.8 V
18.0 V
19.0 V
20.9 V
15.5 V
16.3 V
20.0 V
20.9 V
16.1 V
16.5 V
16.4 V
16.8 V
17.0 V
18.7 V
16.8 V
17.2 V
17.3 V
20.2 V
20.8 V
17.0 V
17.5 V
*Optional drive rolls, liners, contact tips, and nozzles may be required to weld this full range. Contact Everlast for ordering and parts interchange information.
27
Welding Information and Tips
EXPLANATION OF WELDER FUNCTIONS
Volt and Amp Settings
When welding, the two main functions that require adjustment are Voltage and Wire feed speed. The function of voltage in MIG welding is to control the overall width and to a great extent, the height of the weld bead. In other words, voltage controls the bead profile. It controls wet in at the toes of the weld, and arc length. Short arc lengths provide wider welds.
The wire feed speed directly controls the amps, and in turn amps control penetration. When setting the welder up you will notice that the wire speed is displayed in Inches Per Minute. However, while actively welding, the display will change function and display actual amp output. The relationship between wire diameter, wire speed and amps is easily figured with the following approximate industry conversions:
.023”: 3.5 x Amps = Inches per minute (IPM) class of wire. The ranges of volt and amp parameters generally varies somewhat from brand to brand, so be sure to read the packaging and/or manufacturer literature to determine what range of settings are recommended. The wire diameter also limits the practical maximum thickness of what can be reasonably welded. The issue with following charts, graphs and calculator recommendations is that most people find them either too hot or too cold. For some people, it may not be close to the setting they are used to. However, nothing can substitute for watching and listening to the arc. If the arc is correct, a steady sound, similar to the sound of bacon should be heard. The actual frying sound can vary somewhat and may have somewhat of a higher pitch whine to it. If these sounds are present, look at the arc to see if it is steady, and producing low amounts of spatter.
If large amounts of spatter are present, the puddle seems fluid (appears wet) and the wire speed is within the targeted range, decrease volts a little at a time to reduce the spatter. If this does not correct the problem, change the torch angle and torch height. Hold the torch more vertical, with less than a 15 degree deviation from vertical and reduce stick out of wire to 3/8” or less. If this still does not help, reduce the wire speed. Some spatter is normal, though it should be minimal overall.
.025”: 3.1 x Amps = Inches per minute (IPM)
.030”: 2 x Amps = Inches per minute (IPM)
.035”: 1.6 x Amps = Inches per minute (IPM)
.045”: 1 x Amps = Inches per Minute (IPM)
The wire can also pop and spatter if the voltage is too low for the wire speed and/or wire diameter. This is mostly observed as flying bits of red hot but un melted wire, along with popping as the wire inconsistently stubs into the puddle. This is followed by the wire pushing back against your hand pressure while the wire visibly turns white/red hot before burning off. Too low of voltage will also produce a high piled bead with the toes (edges) of the weld not properly wetting in resulting in poor fusion.
To convert wire speed (IPM) into approximate Amps, use the following conversion formula:
.023”: IPM ÷ 3.5 = Amps
.025”: IPM ÷ 3.1 = Amps
.030”: IPM ÷ 2 = Amps
Even though the PowerSet feature has been provided, sometimes additional adjustment may need to be made based off of welding position or joint type. With this unit, we ’ ve tried to provide plenty of adjustment range in the PowerSet function. Normally, this will still allow a functional setting.
However, when the welding wire is pushed to its maximum limits with
Volts and Wire Speed limit, welding may not be smooth and spatter, undercut, and burn back (when the wire melts back to the tip) may occur.
.035”: IPM ÷ 1.6 = Amps
Starting the Arc and Welding In the MIG Process.
.045”: IPM ÷ 1 = Amps
Keep in mind these are approximate conversions and do fall off in accuracy as amps are increased into the upper current limits for the given wire diameter.
Starting the arc is a relatively simple process. Before beginning, the wire should initially be trimmed to between 1/4 to 3/8”. Once the wire is trimmed, the gun should be firmly grasped to prevent a phenomenon often referred to as “ machine gunning ”. A light grasp, especially at start, can cause the arc to stutter as the wire pushes back on the gun, lengthening the wire stick out and creating an irregular start and a porous weld.
Even though you will find general recommendations about setting the
Amps, Volts and even shielding gas through a variety of free downloadable apps and online calculators, every filler metal manufacturer has its own specific parameters for Volt and Amp settings for each wire diameter and
The end of the wire should be positioned just barely above the metal when the trigger is pulled for the cleanest start. This will position the end of the contact tip about 1/2” above the weld. The gun should be in the vertical position, with no more than 5 degrees lean in either side to side direction.
28
Holding the wire too far off from the metal will result in rough starting and too long of wire stick out.
Once the arc has been established, the gun can then either be pushed or pulled in the direction of the weld. In either case, the gun nozzle should be positioned directly over the weld without angling the wire to one side or the other of the weld as already mentioned. The gun should have no more than 15 degrees lean pointed into (push) or pointed away from (pull) the direction of travel. In most cases a push motion is desired. However, a lot of texts offer conflicting information on whether to push or to pull the gun. In reality, both are correct if used correctly and with each having particular strength and weakness. Either one done with too much gun angle will result in undesirable results. Most open minded people who are well versed in MIG quickly develop a sense of when to push and when to pull the gun. Even for novices, a sense of when to push and pull the gun comes quickly with a little practice. Pushing can result in shallower penetration but the molten puddle is easier to see and the arc sits easily on the leading edge. It will usually leave a aesthetically pleasing bead. However, be careful to prevent the gun from leaning toward or away from the direction of travel too much as spatter will increase and shielding gas flow may become turbulent, creating porosity in the weld. Pulling will result in deeper penetration, but can result in a narrow bead without much side fusion. It also can leave an undesirable humped appearance if not done correctly or if travel is too slow. Whenever MIG welding with Aluminum, whether with the standard MIG gun or the Spool gun ALWAYS push the gun. If using Flux Cored wire, a dragging motion is almost always recommended.
gaps where fit up is a problem. A weave is also frequently used to manage heat build up. For example: when welding vertically weaves are almost always used to prevent the molten metal from sagging due to the force of gravity. The major drawback of weaving is that it introduces a greater possibility of getting inclusions and other forms of contamination in the weld. Properly done weaving is a valuable tool, but it must be practiced before employing it in any structural or critical application.
Metal Cleaning.
MIG and TIG welding requires a well prepped surface to obtain a sound weld. The removal of paint, rust mill scale, or other contaminate such as grease should be done before welding. Stick welding is more forgiving of rust and mill scale, but when MIG welding, contaminates will result in porosity and inclusions in the weld, weakening it. In TIG welding it can be disastrous. TIG requires the most cleaning effort. A grinder will usually prep the metal sufficiently to remove oxidation and paint. However, to remove grease a degreaser such as acetone should be used. Do not use any degreaser such a brake cleaner with chlorinated solvents or death or serious injury may occur!
Weaving in Welding. Weaving (oscillating the torch or electrode from side to side in one pattern or the other), particularly in MIG, is a topic of controversy as much as whether to push or pull the MIG gun. Stringer beads are often best for novice welders. Stringers are simply straight beads that move forward with little or no side to side travel or oscillation. These will offer the soundest welds for a beginner in MIG or Stick. Stringer welds leave little or no room for contaminates to enter the weld and are the fastest to produce without creating an opportunity for cold lap. Moving too quickly however with a stringer can create undercut which will weaken the weld. The best policy is to move a slow steady speed, making sure the sides of the weld are filled. If undercut is present, it is either from too much voltage or moving before the wire has time to fill the area the arc has melted.
Think of weaving as a method of “ sewing ” the metal together. If weaving is of interest to you, start with the basic weave pattern. Simple weaves using one variation or the other of a cursive “ e ” motion are best to begin with. Other weave patterns can be used of course. C ’ s, V ’ S, U ’ s , Triangles and many more weave patterns can be used depending upon the application. Weaves are employed for a number of reasons. Weaves are often considered to have a more pleasing appearance and can help bridge
MIG and TIG filler wires such as ER70S 6 or ER70S 2 include a sufficient level of deoxidizers such as silicone and copper that are formulated to allow it to handle minor to moderate amounts of rust and mill scale. These deoxidizers will float out most moderate amounts of contaminates out of the weld and will appear in the usual form of glassy like deposits on top of the cooled metal. They are easily brushed off before starting the next pass. They should not be welded over. Any pinholes that appear are a result of trapped gas in the weld and should be ground out before the next pass. It should be noted that some MIG wires such as ER70S levels of deoxidizers and must be thoroughly cleaned and ground before welding. MIG and TIG ER70S wire is cut to lengths and MIG wire is continuous. When welding fine gauge materials in TIG, you can substitute sections of thinner MIG wire.
Multiple Pass Welds.
-
One of the common misunderstandings that people have when beginning to weld is that if the welder has the power, then a single heavy pass should be used to weld it up. This is wrong. This technique is a good way to induce cold lap and inclusions into the weld. Single pass welds should not exceed 1/4” even with the heaviest wire the welder is capable of han-
NOTICE:
3 have low
2 and ER70S6 are the same except that TIG
This unit features a slow run in. This means the wire will feed slowly until the arc is started. It is used to improve arc initiation and reduce weld porosity which results in poor fusion during the arc starting process. Once the arc is sensed, the wire speed will ramp up and weld at the selected wire speed.
29
dling. A thick pass may also begin to cool before contaminates and gas pockets have the time to float out to the surface. It ’ s far better to make multiple smaller passes to complete a plate weld for a higher quality result.
For best results, this requires that most joints 1/4” and over be prepared with a grinder to accept multiple weld passes. The weldment edges should be ground to form a V, U or J shaped groove to create a recess where the welds can be welded one on top of another. For welding with .035” wire and under, create a bead no thicker than 3/16” in a single pass, no more than 1/8” with .030” wire, and with .025” wire and smaller no more than 3/32 for best results. This will help maintain proper fluidity of the weld and prevent gas from being trapped in the weld and give time for any minor contaminates to float out of the weld. It will also help to maintain reasonable forward travel speeds. Too slow of travel speeds will create excess build up and can tend to create cold lap at the weld toes resulting in poor tie in. One issue created with a weaving technique even if the metal deposited is the correct thickness is that it can slow the forward progress down. If weaving is too wide, one side of the puddle will cool and oxidize before the torch is brought back across to that side. This is a point where porosity can be introduced.
When Do I Use Multi Pass Welds?
When welding material 1/4” and over be careful about trying to put too much metal down in a single pass. Use multiple passes to complete the weld along with any necessary joint preparation especially with wires of smaller diameter. As metal thickness goes up so does the number of required passes. Depending upon the wire diameter and power settings used, a 1/4” joint may only require 1 or 2 passes, but a 3/8” joint in plate metal or pipe will require not only beveling but 4 to 6 overlapping
Weld Pass Examples
≥ 1/4”
Fillet
≥ 1/4”
Fillet
What Are the Different Kinds of Welds?
Besides a butt joint (Flat edge to flat edge) and lap joint (overlapping edges) which are often used for thinner metal gauges, consider using one of these groove joints for best welding results. When grinding or cutting the bevels, especially with a single V groove, it may be beneficial to leave a small land with a gap between the joint to achieve full penetration. In this case a temporary backer plate can be used to support the bottom of the weld to create the root pass. The root weld will weld the backer to the main plate. This backer can later be ground or cut off.
However, in many cases a plain open root can be used as a backer plate adds to the time and labor involved. A knife edge is also acceptable so long as the joint is fully penetrated when the weld is completed. Open root gaps without a backer can range from 1/16” to 1/8” depending upon
Joint Preparation
V GROOVE (60 80°) DOUBLE V GROOVE
≥ 1/4”
Butt
s
≥ 1/4”
V
U GROOVE DOUBLE U GROOVE
BEVEL GROOVE DOUBLE BEVEL GROOVE
J GROOVE DOUBLE J GROOVE
30
MIG Welding is fairly simple if you keep travel angle and direction in mind when welding. See below. If you are welding flux core, the gun direction is reversed. Remember: If it has gas, you use a push angle. If it is gas less you use a drag angle. The old welder ’ s saying “ If it has slag, you drag.
” applies to Flux Cored Wire welding.
VERTICAL
NO
Problem Technique: The Gun is not being held vertical from side to side. Wire is not being directed to the center of the puddle. This concentrates heat on one side of the joint and results in poor fusion on the neglected side. It also can create more buildup on one side of the joint than the other. Correction: Hold the gun so that the angle of the neck stands perpendicular from side to side.
YES
Correct Technique: The gun is held in a near vertical position. A variance of 5 degrees or less is acceptable from side to side. The purpose is to prevent the arc from being concentrated on one side of the weld joint or the other. This balances the heat on both sides of the joint and keeps the bead centered. Don ’ t confuse this with push or pull angle in the travel direction.
OK
Correct Technique: The gun is angled toward the back of the weld when traveling forward. This angle should not exceed 15 degrees. This provides a narrower but more deeply penetrating weld. Use this method when
Flux Core wire is being used. Use this method where the unit may be reaching its maximum welding capacity. Not for use with Aluminum wire.
PULL ≤15 °
YES
Correct Technique: The gun can be angled toward the front of the weld when traveling forward. This angle should not exceed 15 degrees. This provides a wider and generally more pleasing weld. However it is shallower penetrating. This method typically allows a much better view of the arc. Use for most types of welding unless deeper penetration must be achieved.
PUSH ≤15 °
31
Troubleshooting
Error Codes
TROUBLE CODE WITH WARNING LIGHT/UNIT
STOPS WELDING BUT IS TURNED ON.
01
02
04
05
DIAGNOSIS
OVER OR UNDER VOLTAGE. Check power input cable for length/size, check input voltage. Running on poor quality power supply or dirty power from generator.
OVER TEMPERATURE/ DUTY CYCLE EXCEEDED. Allow unit to rest for 15 minutes. Check for obstacles, clean welder, and heat sinks. Make sure unit is unplugged for 30 minutes before opening up for cleaning.
OVER CURRENT. Check to make sure input power cable is correct length and size. Internal unit fault or low input voltage. Possible issue running on generator with dirty power. Identify cause, plug directly into the receptacle. Cycle the switch one time. If the code does not clear, call Everlast
Tech Support.
TORCH SWITCH IS STUCK CLOSED. This simply means that the arc has been trying to start and the HF has been cycled on for too long. If this does not clear after releasing the foot pedal, turn off welder immediately and check torch switch for stuck contact. Check foot pedal for complete return or stuck micro switch. Do not hold down the switch or pedal without attempting to strike an arc.
OTHER CONTACT EVERLAST
32
Troubleshooting
Common Welding Issues
NO.
Trouble Possible Cause
1.
Unit is switched on, but the power light isn ’ t on.
Switch damaged.
Service Breaker/ Input Line Damaged
2.
After welding machine is overheating and the fan does not work.
Fan damaged.
Fan connector plus is loose
4. Intermittent, wandering arc.
5.
Porosity of the Weld. Discolored weld color.
Tungsten is discolored.
Work Clamp not connected directly to part being welded.
Work Clamp worn/damaged
Torch height too high.
Low flow rate of shielding gas. High flow rate of shielding gas. Possible gas leaks internally or externally due to loose fittings. Base metal is contaminated with dirt or grease.
6.
Weld quality is poor.
Weld is dirty/oxidized, or porous.
Drafty conditions. The welder is located on the workpiece and is blowing gas off due to fan activity. Solenoid is sticking.
7.
8.
Unstable Arc. Spatter.
Other.
Bad work clamp connection. Metal is indirectly connected through table or other item. Incorrect settings
Check.
Replace.
Replace.
Check. Reinstall.
Solution
Reconnect.
Replace.
Reduce MIG torch height to under 3/8”.
Increase flow rate on regulator. Check for kinks in tubing. Increase post flow time. Reduce stick out to less than 1/4”. Increase gas nozzle size. Clean metal thoroughly with approved metal cleaner, or use acetone and a rag to clean metal.
Eliminate drafts. Move welder. Check if there is sufficient shielding gas left in tank. Check gas flow. Adjust for higher flow of gas. Listen for audible click of gas solenoid. If no click is heard, then contact Everlast Support. Clean weld properly. Increase pre flow or post flow.
Change Work Clamp. Use a direct connection to the part being welded.
Check and adjust settings. Spatter usually increases when smaller wires are at the maximum welding capacity.
Contact Everlast
33
34
advertisement