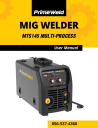
PrimeWeld MULTI-PROCESS MTS145 User Manual
Add to My manuals21 Pages
PrimeWeld MULTI-PROCESS MTS145 is a versatile welding machine designed for a wide range of applications. This machine allows you to perform MIG, TIG and stick welding. The MTS145 offers multiple welding parameter settings to help you achieve high-quality welds with various materials. Its user-friendly interface and robust design make it suitable for both professional welders and DIY enthusiasts.
advertisement
▼
Scroll to page 2
of
21
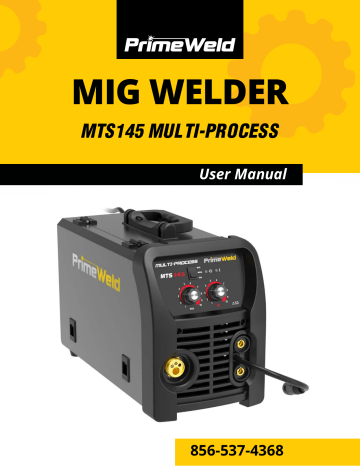
MIG WELDER MTS145 MULTI-PROCESS User Manual 856-537-4368 MTS145 MULTI-PROCESS MIG WELDER SETTING UP AND OPERATING INSTRUCTIONS Your study of this manual will be highly appreciated. Fail to follow the instructions could cause serious injury in using. Keep This Manual MIG WELDER - MTS145 MULTI-PROCESS 2 MIG WELDER Congratulations on your new product and wise decision to choose us. We are honored to have you as our customer, and will strive to provide you with the reliability all the time. This Manual’s designed to instruct you on the correct operation and use of this machine. Your satisfaction and safe operation is our ultimate care. We appreciate your time to study the entire manual, especially the Safety part. It will help to avoid potential hazards that may exist in the working, thank you. Details offered below, safety warn¬ings and precautions, assembly, operat¬ing, inspection, maintenance and cleaning procedures. You can record the product’s serial number in the tail of the manual near the assembly diagram (or month and year of purchasing if no product number). Keep the manual and receipt in a safe and dry place for future reference. Caution Be sure to read the Safety Precautions before installing or operating this equipment. Fail to follow the instructions listed below may cause electric shock, burning, or serious injury. If you are not fully understand the principles of operation and safe practices for welding machine, you are urged to read it again, or contact your supplier for further information. USER RESPONSIBILITY This equipment will operate following the instructions provided. It must be checked regularly for safety and maintenance, not well-maintained ones should not be used any more. Accessories and Parts which are broken, missing, deformed must be replaced or fixed immediately. This equipment or any of the parts should not be changed without permission. The user shall take the sole responsibility, in case of any malfunction which caused by improper use, faulty maintenance, improper fixing or repair by anyone others, if not the manufacturer or its representative. MIG WELDER - MTS145 MULTI-PROCESS 3 CONTENTS 5 Section 1 5 VITAL SAFETY INFORMATION 5 1.1 General Safety Rules 7 1.2 Specific Safety Rules 10 Section 2 10 SPECIFICATIONS 11 Section 3 11 Initial Setting Up Instructions 11 3.1 Assembly 12 Section 4 12 CONTROLS & INDICATORS 14 Section 5 14 Operating Instructions 14 5.1 Work Piece And Work Area Setting Up 15 5.2 General Operating Instructions 16 5.3 Setup for different Processes. 19 Section 6 19 Maintenance And Service 19 6.1 Cleaning, Maintenance, and Lubrication 20 Section 7 20 Troubleshooting Guide MIG WELDER - MTS145 MULTI-PROCESS 4 VITAL SAFETY INFORMATION Section 1 1.1 General Safety Rules 1. Work Area Safety a. Take a suitable work area, must be clean and well bright. Cluttered or dark areas could cause acci¬dents. b. Do not operate welders in atmospheres containing dangerously reactive or flammable liquids, gases, vapors, or dust. Provide adequate ventilation in work areas to prevent accumulation of such substances. c. Keep children and bystanders away while operating the welder. Distractions can make you lose all the control. 2. Electrical Safety a. Avoid body contact with grounded surfaces such as pipes, radiators, ranges and refrigerators. There is an increased risk of electric shock if your body is grounded. b. Do not expose the welder to rain or wet conditions. Water entering a welder will increase the risk of electric shock. c. Do not abuse the Power Cord. Never use the Cord for pulling or unplugging the welder. Keep Cord away from heat, oil, sharp edges or moving parts. Damaged or entangled Cords increase the risk of electric shock. d. people with pacemakers should consult their physician(s) before use. Electromagnetic fields in close proximity to heart pacemaker could cause pacemaker interference or pacemaker failure. e. When operating a welder out¬doors, use an extension cord suit¬able for outdoor use. Use of a cord suitable for outdoor use reduces the risk of electric shock. f. When not welding, cut wire back to contact tip or remove electrode from electrode holder. 3. Personal Safety a. Stay alert, watch what you are doing and use common sense when oper¬ating a welder. Do not use a welder while you are tired or under the influence of drugs, alcohol or medication. A moment of inatten¬tion while operating welders may result in serious personal injury. b. Use safety equipment. Always wear eye protection. Safety equipment such as arc shaded, impact safety full face shield, dust mask or respi¬rator, heavyduty work gloves, non-skid safety shoes, or hearing protec¬tion used for appropriate conditions will reduce personal injuries. Do not wear loose fitting things, like rings, scarves, etc., which is high risk of being trapped or burnt. MIG WELDER - MTS145 MULTI-PROCESS 5 VITAL SAFETY INFORMATION Section 1 c. Avoid accidental starting. Ensure the Power Switch is in the off-position before plugging in. Plug¬ging in welders that have the Switch on invites accidents. d. Do not overreach. Keep proper foot¬ing and balance at all time. This enables better control of the welder in unexpected situations. 4. Welder Use and Care a. Use the correct welder for your application. The correct welder will do the job better and safer at the rate for which it was designed. b. Do not use the welder if the Power Switch does not turn it on and off. Any welder that can¬not be controlled with the Switch is dangerous and must be repaired. c. Disconnect the Power Cord from the power source before mak¬ing any adjustments, changing ac¬cessories, or storing the machine. Such preventive safety measures reduce the risk of starting the machine accidentally. d. Store idle machine out of the reach of children and do not allow persons unfamiliar with the welder or these instructions to oper¬ate the machine. Welders are dangerous in the hands of untrained users. e. Maintain welders. Check for misalignment or binding of moving parts, breakage of parts and any other condition that may affect the welder’s operation. If dam¬aged, have the welder re¬paired before use. Many accidents are caused by poorly maintained welders. f. Use the welder and accesso¬ries in accordance with these in¬structions and in the manner intend¬ed for the particular type of welder, taking into account the work¬ing conditions and the work to be performed. Use of the welder for operations different from those intended could result in a hazardous situation. 5. Service Have your welder serviced by a qualified repair person using only identical replacement parts. This will ensure that the safety of the welder is maintained. MIG WELDER - MTS145 MULTI-PROCESS 6 VITAL SAFETY INFORMATION Section 1 1.2 Specific Safety Rules 1. Maintain labels and nameplates on the Inverter Welder. These carry important safety information. 2. Avoid electric shock. Do not per¬mit electrically live parts, cables, or electrodes to contact skin, clothing, or gloves. Wear protec¬tive clothing. This unit draws enough current to cause serious injury or death. Do not use the welder unless you are insulated from the ground and the work piece. 3. Avoid body damage. Arc rays and infrared radiation can injure eyes and burn skin. Wear eye and body protection. Do not allow viewing by visitors without proper eye and body protection. Use a Face Shield with arc shaded filter plate. 4. Move flammable and explosive mate¬ rail at least 10 meters from the welding arc to prevent sparks or molten metal from starting a fire. Keep a type ABC fire extinguisher within easy reach. 5. Avoid unintentional starting. Prepare to begin work before turning on the Inverter Welder. 6. Do not leave the Welder unat¬tended when it is plugged into an electrical outlet. Turn off the machine, and unplug it from its electrical outlet before leaving. 7. Use clamps or other practical ways to secure and support the work piece to a stable platform. Holding the work by hand or against your body is unstable and may lead to loss of control. 8. This product is not a toy. Keep it out of reach of children. 9. People with pacemakers should consult their physician(s) before using. Electromagnetic fields in close prox¬imity to heart pacemaker could cause pacemaker interference or pacemak¬er failure. In addition, people with pacemakers should: Avoid operating alone. Do not use with Power Switch locked on. Properly maintain and inspect to avoid electrical shock. Any Power Cord must be prop¬erly grounded. Ground Fault Circuit Interrupter (GFCI) should also be implemented – it prevents sustained electrical shock. • • • • 10. Prevent eye injury and burns. Wearing and using personal safety clothing and safety devices reduce the risk for injury. • Wear safety impact eye goggles underneath welding eye protection featuring at MIG WELDER - MTS145 MULTI-PROCESS 7 VITAL SAFETY INFORMATION Section 1 least a Number 10 shade lens rating. • Leather leggings, fire resistant shoes or boots should be worn when using this product. Do not wear pants with cuffs, shirts with open pockets, or any clothing that can catch and hold molten metal or sparks. • Keep clothing free of grease, oil, solvents, or any flammable sub¬stances. Wear dry, insulating gloves and protective clothing. • Wear an approved head covering to protect the head and neck. Use aprons, cape, sleeves, shoulder covers, and bibs designed and approved for welding and cut¬ting procedures. • When welding/cutting overhead or in confined spaces, wear flame resistant ear plugs or ear muffs to keep sparks out of ears. 11. Prevent accidental fires. Remove any combustible material from the work area. • When possible, move the work to a location well away from combustible materials. If relocation is not pos¬sible, protect the combustibles with a cover made of fire resistant mate¬rial. • Remove or make safe all combus¬tible materials for a radius of 10 meters around the work area. Use a fire resistant material to cover or block all open doorways, win-dows, cracks, and other openings. • Enclose the work area with portable fire resistant screens. Protect combustible walls, ceilings, floors, etc., from sparks and heat with fire resistant covers. • If working on a metal wall, ceiling, etc., prevent ignition of combus¬tibles on the other side by moving the combustibles to a safe loca¬tion. If relocation of combustibles is not possible, designate someone to serve as a fire watch, equipped with a fire extinguisher, during the welding process and for at least one half hour after the welding is com¬pleted. • Do not weld or cut on materials having a combustible coating or combustible internal structure, as in walls or ceilings, without an ap¬proved method for eliminating the hazard. • Do not dispose of hot slag in containers holding combustible materi¬als. Keep a fire extinguisher nearby and know how to use it. • After welding, make a thorough examination for evidence of fire. Be aware that easily-visible smoke or flame may not be present for some time after the fire has started. Do not weld or cut in atmospheres containing dangerously reactive or flammable gases, vapors, liquids, and dust. Provide adequate ven¬tilation in work areas to prevent accumulation of flammable gases, vapors, and dust. Do not apply heat to a container that has held an unknown substance or a MIG WELDER - MTS145 MULTI-PROCESS 8 VITAL SAFETY INFORMATION Section 1 combus¬tible material whose contents, when heated, can produce flammable or explosive vapors. Clean and purge containers before applying heat. Vent closed containers, including castings, before preheating, weld¬ing, or cutting. 12. Do not touch live electrical parts. Wear dry, insulating gloves. Do not touch electrode or conductor tong with bare hand. Do not wear wet or damaged gloves. 13. Protect yourself from electric shock. Do not use outdoors. Insulate your¬self from the work piece and ground. Use nonflammable, dry insulating material if possible, or use dry rubber mats, dry wood or plywood, or other dry insulating material big enough to cover your full area of contact with the work or ground. 14. Ensure that the unit is placed on a stable location before use. If this unit falls while plugged in, severe injury, electric shock, or fire may result. 15. Never remove the grounding prong or modify the Power Cord Plug in any way. Do not use adapter plugs with this product. 16. Avoid overexposure to fumes and gases. Always keep your head out of the fumes. Do not breathe the fumes. Use enough ventilation or exhaust, or both, to keep fumes and gases from your breathing zone and general area. 17. Live torch when Trigger is pressed. Keep Torch away from people and flammables before touching Trigger. 18. Turn off, unplug, and discharge electrode to ground before performing any inspection, maintenance, or cleaning. 19. The warnings, precautions, and instructions discussed in this instruction manual cannot cover all possible conditions and situations that may occur. It must be understood by the operator that common sense and caution are factors which cannot be built into this product, but must be supplied by the operator. MIG WELDER - MTS145 MULTI-PROCESS 9 SPECIFICATIONS MIG WELDER - MTS145 MULTI-PROCESS Section 2 10 Initial Setting Up Instructions Section 3 Read the Entire Important Safety Information section at the beginning of this manual including all text under subheadings therein before set up or use of this product. WARNING To prevent serious injury from accidental operation: Turn the Power Switch of the Welder to its “OFF” position and unplug the Welder from its electrical outlet before assembling or making any adjustments to the machine. 3.1 Assembly 1. UNPACKING, Unpack and make sure all the items in good condition. When you receive the parcel, check it carefully to make sure no damage due to shipping. If there is any damage happened, inform the carrier immediately to claim before installing. Care the safety to avoid damaging the machine when using bars, hammers, etc. 2. Make sure the welder is transported securely. If the machine must be moved, always disconnect the power cable from the electrical outlet. Please note the HANDLE is not for mechanical lifting. And do not touch live electrical parts. 3. Check the input voltage supplied to the welder before turning it on. Verify the input connection of ground wires from the machine to the input source. Optional adapter allows for connection of the power supply input cable plug when using unique input volt¬age. 4. Since the inhalation of welding fumes can be harmful, ensure that the welding area is effectively ventilated. MIG WELDER - MTS145 MULTI-PROCESS 11 Section 4 CONTROLS & INDICATORS 1. Power indicator 2. Warning indicator 3. Weld mode selection (MIG/MMA/TIG) 5. WFS control knob (MIG) 6. Output terminal (Positive) 7. Output terminal (Negative) 4. Amp control knob (STICK/TIG) Voltage control knob (MIG) 8. Euro connector socket 9. Power switch 10. Air Inlet MIG WELDER - MTS145 MULTI-PROCESS 12. Wire Spool Spindle 11. Wire Feeder 12 Section 4 CONTROLS & INDICATORS 1. Power Indicator: Power Indicator turns on when Power switch is in ON position. 2. Warning Indicator: Warning Indicator turns on when machine working time exceeds its rated duty cycle, or input voltage exceeds the proper range. 3. Weld Mode Selection Button: Press the button can exchange the welding mode, MIG/STICK/TIG. 4. Amp/Voltage Control Knob: Turn this knob to adjust Voltage in MIG mode, and Welding Current in TIG and STICK mode. 5. WFS Control Knob: Turn this knob to adjust Wire Feeding Speed in MIG mode. 6. Output terminal (Positive) 7. Output terminal (Negative) 8. Euro Connect Socket for MIG Torch 9. Power switch 10. Air Inlet 11. Wire Feeder 12. Wire Spool Spindle MIG WELDER - MTS145 MULTI-PROCESS 13 Section 5 Operating Instructions Read the entire Important Safety Information section at the beginning of this manual including all text under subheadings therein before set up or use of this product. To prevent serious injury from accidental operation: Turn the Power Switch to “OFF” or “0” position before performing any inspection, maintenance, or cleaning procedures. 5.1 Work Piece And Work Area Setting Up WARNING Prevent eye injury and burns. Wearing personal protective equipment to reduce the risk of injury. An important factor in making a satisfactory weld is preparation. This includes studying the process and equipment and practicing welding before attempting to weld finished product. An organized, safe, ergonomic, comfortable, and well-lit work area should be prepared for the operator. The work area should specifically be free of all flammables with both a fire extinguisher and a bucket of sand available. To properly prepare for welding with your new welder, it is necessary to: 1. Read the safety precautions in this manual. 2. Prepare an organized, well-lit work area. 3. Provide protection for the eyes and skin of the operator and bystanders. 4. Attach the ground clamp to the bare metal to be welded, making sure of good contact. 5. Make sure that the wire-roller groove in the roller corresponds to the diameter and type of wire being used. 6. Plug the machine into a suitable outlet. Route the Power Cord along a safe route to reach the work area without creating a tripping hazard or exposing the Power Cord to pos¬sible damage. The Power Cord must reach the work area with enough extra length to allow free movement while working. 7. Completely open the gas cylinder valve. Adjust the gas pressure regulator to the correct flow rate. (Not applicable to Stick process.) 8. A barrier, such as a welding curtain or welding shroud should be put up to protect others in the work area and limit the spray of sparks. MIG WELDER - MTS145 MULTI-PROCESS 14 Section 5 Operating Instructions 5.2 General Operating Instructions 1. Gas Cylinder and Regulator Connection WARNING Cylinders are highly pressurized. Handle with care. Serious accidents can result from improper handling or misuse of compressed gas cylinders. Do not drop the cylinder, knock it over, expose it to excessive heat, flames or sparks. Do not strike it against other cylinders or strike an arc on it. The gas cylinder (not supplied) should be located near the rear of the welder, in a wellventilated area and securely fixed to the work bench or to the wall to ensure that it will not fall. For safety and economy, ensure that the regulator is fully closed (turned counterclockwise) when not welding and when fitting or removing the gas cylinder. •• Turn the regulator adjustment knob counter-clockwise to ensure the valve is fully closed. •• Screw the gas regulator down on the gas bottle valve and tighten. •• Connect the gas hose to the regulator, securing with the clip/nut provided. •• Connect the other end to the Air Inlet on the back of the machine. •• Open the cylinder valve, then set the gas flow to approximately 20 - 35 CFH (cubic ft. per hour) on the regulator. •• Depress the gun trigger to ensure that the gas is flowing through the gun. 2. Loading the Electrode Wire •• Turn the machine off. •• Open the side door of the machine. •• Unscrew the locking nut of the spool spindle. •• Load the spool with the wire on the spindle such that the spool turns anticlockwise when the wire is fed into the wire feeder. •• Make sure that the spool locating pin goes into the fitting hole on the spool. •• Screw in the fastening cap of the spindle. •• Put in the wire roll using the correct groove corresponding to the wire diameter. MIG WELDER - MTS145 MULTI-PROCESS 15 Section 5 Operating Instructions •• Free the end of the wire and cut off the bent end making sure it has no burr. •• Rotate the wire spool anticlockwise and thread the end of the wire into the wire feeder as far as the Euro Connect Socket. •• Adjust force of pressure roll of the wire feeder properly. 3. Inserting Electrode Wire into MIG Gun •• Turn the welder off. •• Connect MIG gun to the Euro Connect Socket. •• Remote the nozzle from the gun and contact tip or protection cap and contact tip, then straighten the gun out flat. •• Turn the welding machine on. •• Depress the gun trigger to feed the wire through the gun linear until the wire comes out of the threaded end. Or Depress the Cold Wire Feeding Button to feed the wire instead of depressing the gun trigger, which will make the wire fed at the maximum speed. •• Turn the welding machine off. •• Install a proper contact tip, and the nozzle or protection cap. WARNING Take precaution to keep eyes and hands away from the end of the gun while the wire is being come out of the threaded end. 5.3 Setup for different Processes. WARNING Protective gear must be worn when using the Welder. Arc shaded, eye protection, a full face shield, heavy-duty work gloves, a welding apron, respirator, and heavy-duty work clothes without pockets should be worn when using this product. Do not look at the ignited arc without eye protection. Light from the arc can cause permanent damage to the eyes. Light from the arc can burn the skin. Do not breathe arc fumes. MIG WELDER - MTS145 MULTI-PROCESS 16 Section 5 Operating Instructions 1. Setup for MIG Welding •• Thread the MIG gun into the Euro Connect Socket. •• Connect the ground cable to the appropriate Dinse Socket: Ground cable to NEGATIVE (-) Dinse Socket. •• Ensure the ground clamp has a good connection to the workpiece and is connected on clean, bare metal (not rusty or painted). •• Load the spool of wire inside the door and feed it through the Wire Feeder into the gun (see “Loading the Electrode Wire” & “Inserting Electrode Wire into MIG Gun”). •• Make sure the gas shied has been connected (see ” Gas Cylinder and Regulator Connection”). Turn on the gas cylinder, pull the trigger to check for gas flow and adjust the flow rate. •• Turn the machine ON. •• Depress Weld Mode Selection Button and select MIG mode. •• Set the welding parameters through adjusting WFS Control Knob, Voltage control Knob. •• Bring the gun close to the workpiece and press the trigger to start to weld. MIG Set-up Parameter Material Thickness Gas Wire diameter 0.8mm 1.6mm 3.0mm Left Knob Right Knob Left Knob Right Knob 0.6 2.5 3 5 10 0.8 1 1 3 0.9 Flux Cord 0.8 SUS 0.8 C25 2.5 2.5 5.0mm Left Knob Right Knob Left Knob Right Knob 4 6 10 2 1 7 7.5 8.5 10 3 2 5 8.5 7 10 6 7.5 9 10 2. Setup for TIG Welding with Lift Arc •• Connect the TIG torch cable to the NEGATIVE (-) Dinse Socket and ground cable connector to the POSITIVE (+) Dinse Socket of the welder. •• Ensure the ground clamp has a good connection to the workpiece and is connected on clean, bare metal (not rusty or painted). •• Connect the TIG torch gas line to the gas regulator (argon gas only) (see ” Gas Cylinder and Regulator Connection”). Turn on the gas cylinder, pull the trigger to check for gas flow and adjust the flow rate. •• Fix a proper tungsten electrode in the TIG torch. MIG WELDER - MTS145 MULTI-PROCESS 17 Section 5 Operating Instructions •• Ensure the TIG torch is safely away from all conductive materials. •• Turn the machine ON. •• Depress Weld Mode Selection Button and select TIG mode. •• Set the output amperage with the Amp Control Knob. •• Open the gas valve on the torch handle. •• Initiate the weld arc with a lift arc technique (contact ignition and lift ignition), and start to weld. •• Close the gas valve on the torch handle after post-weld flow has been completed. TIG Set-up Parameter Material Thickness 0.8mm 1.6mm 3.0mm 5.0mm Left Knob Left Knob Left Knob Left Knob 1-2 2.5-4 4-7 7-10 Gas 100% Argon 3. Setup for STICK Welding •• Check the electrode packaging to determine the recommended polarity and connect the electrode holder and ground clamp to the POSITIVE (+) and NEGATIVE (-) Dinse Sockets accordingly. •• Ensure the ground clamp has a good connection to the workpiece and is connected on clean, bare metal (not rusty or painted). •• Turn the machine ON. •• Depress Weld Mode Selection Button and select STICK mode. •• Set the output amperage with the Amp Control Knob and arc force with Arc Force Control Knob. •• Begin Welding. STICK Set-up Parameter Material Thickness Material Type E6013 E7018 1.6mm 2mm 2.4mm 3mm 3.2mm Left Knob Left Knob Left Knob Left Knob Left Knob 4 5-6 5-7 7-10 7-10 MIG WELDER - MTS145 MULTI-PROCESS 18 Maintenance And Service Section 6 Procedures not specifically explained in this manual must be performed only by a qualified technician. WARNING To prevent serious injury from accidental operation: Turn the Power Switch of the welder to its “OFF” position and unplug the machine from its electrical outlet before performing any inspection, maintenance, or cleaning procedures. To prevent serious injury from welder failure: Do not use damaged equipment. If abnormal noise or vibration occurs, have the problem corrected before further use. 6.1 Cleaning, Maintenance, and Lubrication 1. BEFORE EACH USE, inspect the general condition of the welding machine. Check for loose screws, cracked or broken parts, damaged electrical wiring, and any other condition that may affect its safe operation. 2. Remove the spatters from the welding gun nozzle. Spatters could interfere with the shielding gas flow to the arc. 3. Check the welding gun condition: replace it if necessary. 4. Check condition and operation of the fan, keep cleaning its airflow slots. 5. After Use, clean external surfaces of the welding machine with a dry cloth. 6. Periodically, using compressed air, blow out all dust and debris from the interior. 7. If the unit repeatedly shuts down from thermal overload, stop all use. Have the machine inspected and repaired by a qualified service technician. 8. Store the welding machine and accessories in a clean and dry location out of reach of children. WARNING! If any part of this welder is damaged, it must be replaced only by a qualified service technician. MIG WELDER - MTS145 MULTI-PROCESS 19 Section 7 Troubleshooting Guide WARNING To Prevent serious injury: Shut off the Welder, disconnect the power, and discharge the torch/gun to ground before adjusting, cleaning, or repairing the unit. To make sure discharge all capacitors before performing any internal procedures. MIG WELDER - MTS145 MULTI-PROCESS 20 Section 7 Troubleshooting Guide Trouble Experienced Possible reasons All LEDs OFF when turn ON the machine All LEDs OFF Yellow LED turns on Overheat Incorrect input voltage Arc does not ignite Wire feeding motor not working Improper ground connection Verify that circuit breaker hasn’t been tripped in your main power panel. Resent if needed Ambient temperature is too high, or machine reaches its limit of duty cycle. Allow the machine cool down with fan running. And check for obstructions blocking air flow and keep enough space between any obstacles and the vents on all sides of the machine. Input voltage is too high or too low. Check connection between the plug and outlet, and make sure rated input power is supplied. Make certain that the work piece is contacted properly by the Ground Clamp and that the work piece is properly cleaned near the Ground Clamp and the welding location. Work Cable broken Replace or repair work cables. Potentiometer faulty Replace potentiometer Nozzle is blocked Change nozzle Drive roll is loose Increase tension on drive roll Switch broken Cooling fan not working or Fan broken turning very slowly Wire broken or disconnected No gas flow Likely Solutions Replace switch Replace or repair the fan Check the connection and repair wire if it is damaged Torch is not connected properly Reconnect the torch Gas Pipe is crimped or block Check gas system Gas hose broken Repair or Replace the gas hose Too large contact tip makes the Change to proper contact tip and / current unsteady or drive roll Arc is not stable and spatter is large Unstable line voltage Wire feeding resistance is too large MIG WELDER - MTS145 MULTI-PROCESS Check the line voltage and, if there are problems with the wires, have a licensed electrician remedy the situation. Clean or replace the liner and keep the gun cable straight 21
advertisement
Key Features
- Multi-process welding
- MIG, TIG, STICK modes
- Amp/voltage control
- WFS control
- Euro connector socket
- Duty cycle indicator
Related manuals
Frequently Answers and Questions
How do I change the welding mode to MIG?
Press the Weld Mode Selection Button and select MIG mode.
What is the WFS control knob used for?
The WFS control knob adjusts the wire feeding speed in MIG mode.
How do I connect the TIG torch?
Connect the TIG torch cable to the NEGATIVE (-) Dinse Socket and the ground cable connector to the POSITIVE (+) Dinse Socket of the welder.
advertisement