- Home
- Do-It-Yourself tools
- Power tools
- Paint Sprayer
- Graco
- 3A5743A, Reactor E-8p and E-15p Portable Plural Component Sprayers
- Instructions
Graco 3A5743B, Reactor E-8p and E-15p Portable Plural Component Sprayers Instructions
Add to my manuals38 Pages
Graco 3A5743A, Reactor E-8p and E-15p Portable Plural Component Sprayers are professional-grade tools designed for spraying 1:1 mix ratio formulated no-heat polyurethane foams and dispensing 1:1 mix ratio polyurea joint-fill materials. With a maximum working pressure of 2000 psi (14 MPa, 138 bar), these sprayers offer precise and efficient application of materials for various projects. The E-8p model handles up to 8 gallons per minute, while the E-15p model can manage up to 15 gallons per minute, making them suitable for both small and large-scale jobs.
advertisement
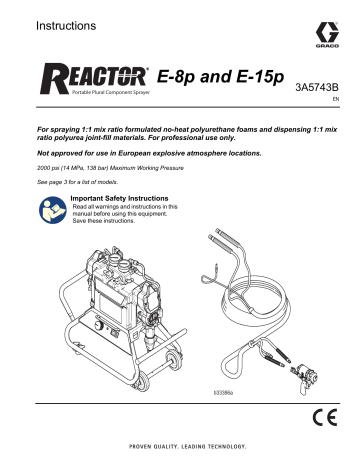
Instructions
Portable Plural Component Sprayer
E-8p and E-15p
3A5743B
EN
For spraying 1:1 mix ratio formulated no-heat polyurethane foams and dispensing 1:1 mix ratio polyurea joint-fill materials. For professional use only.
Not approved for use in European explosive atmosphere locations.
2000 psi (14 MPa, 138 bar) Maximum Working Pressure
See page 3 for a list of models.
Important Safety Instructions
Read all warnings and instructions in this manual before using this equipment.
Save these instructions.
WLD
2
Contents
Systems . . . . . . . . . . . . . . . . . . . . . . . . . . . . . . . . . . 3
Proportioners . . . . . . . . . . . . . . . . . . . . . . . . . . . . . . 3
Related Manuals . . . . . . . . . . . . . . . . . . . . . . . . . . . 3
Warnings . . . . . . . . . . . . . . . . . . . . . . . . . . . . . . . . . 4
Important Isocyanate (ISO) Information . . . . . . . . 7
Material Self-ignition . . . . . . . . . . . . . . . . . . . . . . 8
Keep Components A and B Separate . . . . . . . . . 8
Moisture Sensitivity of Isocyanates . . . . . . . . . . . 8
Foam Resins with 245 fa Blowing Agents . . . . . . 8
Changing Materials . . . . . . . . . . . . . . . . . . . . . . . 8
Overview . . . . . . . . . . . . . . . . . . . . . . . . . . . . . . . . . . 9
Component Identification . . . . . . . . . . . . . . . . . . . 10
Controls and Indicators . . . . . . . . . . . . . . . . . . . . 11
Setup . . . . . . . . . . . . . . . . . . . . . . . . . . . . . . . . . . . . 12
Location . . . . . . . . . . . . . . . . . . . . . . . . . . . . . . 12
Electrical Requirements . . . . . . . . . . . . . . . . . . 12
Grounding . . . . . . . . . . . . . . . . . . . . . . . . . . . . . 12
Connect Fluid Hoses . . . . . . . . . . . . . . . . . . . . . 13
Connect Gun to Air Hose (Air-Operated
Guns Only) . . . . . . . . . . . . . . . . . . . . . . . . . 13
Connect Main Air Supply . . . . . . . . . . . . . . . . . 13
Flush Before Using Equipment . . . . . . . . . . . . . 13
Fill Wet-cups . . . . . . . . . . . . . . . . . . . . . . . . . . . 14
Recirculate Material . . . . . . . . . . . . . . . . . . . . . 15
Flush Fluid . . . . . . . . . . . . . . . . . . . . . . . . . . . . 16
Spraying . . . . . . . . . . . . . . . . . . . . . . . . . . . . . . . . . 17
Pressure Relief Procedure . . . . . . . . . . . . . . . . . . 18
Shutdown . . . . . . . . . . . . . . . . . . . . . . . . . . . . . . . . 18
Maintenance . . . . . . . . . . . . . . . . . . . . . . . . . . . . . . 19
Troubleshooting . . . . . . . . . . . . . . . . . . . . . . . . . . . 21
Status Codes . . . . . . . . . . . . . . . . . . . . . . . . . . . 21
Repair . . . . . . . . . . . . . . . . . . . . . . . . . . . . . . . . . . . 24
Control Board . . . . . . . . . . . . . . . . . . . . . . . . . . 24
Parts . . . . . . . . . . . . . . . . . . . . . . . . . . . . . . . . . . . . 27
120 V Fusion Air Purge System Packages . . . . 27
Suggested Spare Replacement Parts . . . . . . . . . 35
Accessories . . . . . . . . . . . . . . . . . . . . . . . . . . . . . . 35
Dimensions . . . . . . . . . . . . . . . . . . . . . . . . . . . . . . . 36
Technical Data . . . . . . . . . . . . . . . . . . . . . . . . . . . . 37
Graco Standard Warranty . . . . . . . . . . . . . . . . . . . 38
3A5743B
Systems
Systems
Model
E-8p
E-15p
Part
25N014
25N015
Maximum Working
Pressure, psi (MPa, var)
2000 (14, 140)
Proportioner
(see
25A836
26C023
Gun Model
Model
Fusion
®
Air Purge
Part
247124
Proportioners
The model no., series letter, and serial no. are located on the back of the system.
Model
E-8p
E-15p
Part
25A836
26C023
Maximum Working
Pressure, psi (MPa, bar)
2000 (14, 140)
Volts
* Electrical
Connection
120 V 15 A cord
*
See page 12 for detailed electrical requirements.
Related Manuals
Manuals are available at www.graco.com.
Manual
313123
309577
309550
Description
Displacement Pump Repair-Parts
Displacement Pump Repair-Parts
Fusion AP Spray Gun Instructions-Parts
Related Proportioner
25A836
26C023
- - - - -
3A5743B 3
4
Warnings
Warnings
The following warnings are for the setup, use, grounding, maintenance, and repair of this equipment. The exclamation point symbol alerts you to a general warning and the hazard symbols refer to procedure-specific risks.
When these symbols appear in the body of this manual, refer back to these Warnings. Product-specific hazard symbols and warnings not covered in this section may appear throughout the body of this manual where applicable.
ELECTRIC SHOCK HAZARD
WARNING
This equipment must be grounded .
Improper grounding, setup, or usage of the system can cause electric shock.
• Turn off and disconnect power cord before servicing equipment.
• Connect only to grounded electrical outlets.
• Use only 3-wire extension cords.
• Ensure ground prongs are intact on power and extension cords.
• Do not expose to rain. Store indoors.
TOXIC FLUID OR FUMES HAZARD
Toxic fluids or fumes can cause serious injury or death if splashed in the eyes or on skin, inhaled or swallowed.
• Read Safety Data Sheets (SDSs) for handling instructions and to know the specific hazards of the fluids you are using, including the effects of long-term exposure.
• When spraying, servicing equipment, or when in the work area, always keep work area well-ventilated and always wear appropriate personal protective equipment. See Personal
Protective Equipment warnings in this manual.
• Store hazardous fluid in approved containers, and dispose of it according to applicable guidelines.
PERSONAL PROTECTIVE EQUIPMENT
Always wear appropriate personal protective equipment and cover all skin when spraying, servicing equipment, or when in the work area. Protective equipment helps prevent serious injury, including long-term exposure; inhalation of toxic fumes, mists or vapors; allergic reaction; burns; eye injury and hearing loss. This protective equipment includes but is not limited to:
• A properly fitting respirator, which may include a supplied-air respirator, chemically impermeable gloves, protective clothing and foot coverings as recommended by the fluid manufacturer and local regulatory authority.
• Protective eyewear and hearing protection.
3A5743B
Warnings
SKIN INJECTION HAZARD
WARNING
High-pressure fluid from gun, hose leaks, or ruptured components will pierce skin. This may look like just a cut, but it is a serious injury that can result in amputation. Get immediate surgical treatment.
• Do not spray without tip guard and trigger guard installed.
• Engage trigger lock when not spraying.
• Do not point gun at anyone or at any part of the body.
• Do not put your hand over the spray tip.
• Do not stop or deflect leaks with your hand, body, glove, or rag.
• Follow the Pressure Relief Procedure when you stop spraying and before cleaning, checking, or servicing equipment.
• Tighten all fluid connections before operating the equipment.
• Check hoses and couplings daily. Replace worn or damaged parts immediately.
3A5743B
FIRE AND EXPLOSION HAZARD
Flammable fumes, such as solvent and paint fumes, in work area can ignite or explode. Paint or solvent flowing through the equipment can cause static sparking. To help prevent fire and explosion:
• Use equipment only in well-ventilated area.
• Eliminate all ignition sources; such as pilot lights, cigarettes, portable electric lamps, and plastic drop cloths (potential static sparking).
• Ground all equipment in the work area. See Grounding instructions.
• Never spray or flush solvent at high pressure.
• Keep work area free of debris, including solvent, rags and gasoline.
• Do not plug or unplug power cords, or turn power or light switches on or off when flammable fumes are present.
• Use only grounded hoses.
• Hold gun firmly to side of grounded pail when triggering into pail. Do not use pail liners unless they are anti-static or conductive.
• Stop operation immediately if static sparking occurs or you feel a shock. Do not use equipment until you identify and correct the problem.
• Keep a working fire extinguisher in the work area.
PRESSURIZED ALUMINUM PARTS HAZARD
Use of fluids that are incompatible with aluminum in pressurized equipment can cause serious chemical reaction and equipment rupture. Failure to follow this warning can result in death, serious injury, or property damage.
• Do not use 1, 1, 1-trichloroethane, methylene chloride, other halogenated hydrocarbon solvents or fluids containing such solvents.
• Do not use chlorine bleach.
• Many other fluids may contain chemicals that can react with aluminum. Contact your material supplier for compatibility.
5
6
Warnings
WARNING
EQUIPMENT MISUSE HAZARD
Misuse can cause death or serious injury.
• Do not operate the unit when fatigued or under the influence of drugs or alcohol.
• Do not exceed the maximum working pressure or temperature rating of the lowest rated system component. See Technical Specifications in all equipment manuals.
• Use fluids and solvents that are compatible with equipment wetted parts. See Technical
Specifications in all equipment manuals. Read fluid and solvent manufacturer’s warnings. For complete information about your material, request Safety Data Sheets (SDSs) from distributor or retailer.
• Do not leave the work area while equipment is energized or under pressure.
• Turn off all equipment and follow the Pressure Relief Procedure when equipment is not in use.
• Check equipment daily. Repair or replace worn or damaged parts immediately with genuine manufacturer’s replacement parts only.
• Do not alter or modify equipment. Alterations or modifications may void agency approvals and create safety hazards.
• Make sure all equipment is rated and approved for the environment in which you are using it.
• Use equipment only for its intended purpose. Call your distributor for information.
• Route hoses and cables away from traffic areas, sharp edges, moving parts, and hot surfaces.
• Do not kink or over bend hoses or use hoses to pull equipment.
• Keep children and animals away from work area.
• Comply with all applicable safety regulations.
MOVING PARTS HAZARD
Moving parts can pinch, cut or amputate fingers and other body parts.
• Keep clear of moving parts.
• Do not operate equipment with protective guards or covers removed.
• Pressurized equipment can start without warning. Before checking, moving, or servicing equipment, follow the Pressure Relief Procedure and disconnect all power sources.
3A5743B
Important Isocyanate (ISO) Information
Important Isocyanate (ISO) Information
Isocyanates (ISO) are catalysts used in two component materials.
Isocyanate Conditions
Spraying or dispensing fluids that contain isocyanates creates potentially harmful mists, vapors, and atomized particulates.
• Read and understand the fluid manufacturer’s warnings and Safety Data Sheets (SDSs) to know specific hazards and precautions related to isocyanates.
• Use of isocyanates involves potentially hazardous procedures. Do not spray with this equipment unless you are trained, qualified, and have read and understood the information in this manual and in the fluid manufacturer’s application instructions and SDSs.
• Use of incorrectly maintained or mis-adjusted equipment may result in improperly cured material, which could cause off gassing and offensive odors. Equipment must be carefully maintained and adjusted according to instructions in the manual.
• To prevent inhalation of isocyanate mists, vapors and atomized particulates, everyone in the work area must wear appropriate respiratory protection. Always wear a properly fitting respirator, which may include a supplied-air respirator. Ventilate the work area according to instructions in the fluid manufacturer’s SDSs.
• Avoid all skin contact with isocyanates. Everyone in the work area must wear chemically impermeable gloves, protective clothing and foot coverings as recommended by the fluid manufacturer and local regulatory authority. Follow all fluid manufacturer recommendations, including those regarding handling of contaminated clothing. After spraying, wash hands and face before eating or drinking.
• Hazard from exposure to isocyanates continues after spraying. Anyone without appropriate personal protective equipment must stay out of the work area during application and after application for the time period specified by the fluid manufacturer. Generally this time period is at least 24 hours.
• Warn others who may enter work area of hazard from exposure to isocyanates. Follow the recommendations of the fluid manufacturer and local regulatory authority. Posting a placard such as the following outside the work area is recommended:
TOXIC FUMES
HAZARD
DO NOT ENTER DURING
SPRAY FOAM APPLICATION
OR FOR ___ HOURS AFTER
APPLICATION IS COMPLETE
DO NOT ENTER UNTIL:
DATE: ____________
TIME: ____________
3A5743B 7
Important Isocyanate (ISO) Information
8
Material Self-ignition
Some materials may become self-igniting if applied too thick. Read material manufacturer’s warnings and
Safety Data Sheets (SDSs).
Keep Components A and B
Separate
Cross-contamination can result in cured material in fluid lines which could cause serious injury or damage equipment. To prevent cross-contamination:
• Never interchange component A and component B wetted parts.
• Never use solvent on one side if it has been contaminated from the other side.
Moisture Sensitivity of
Isocyanates
Exposure to moisture (such as humidity) will cause ISO to partially cure, forming small, hard, abrasive crystal that become suspended in the fluid. Eventually a film will form on the surface and the ISO will begin to gel, increasing in viscosity.
NOTICE
Partially cured ISO will reduce performance and the life of all wetted parts.
• Always use a sealed container with a desiccant dryer in the vent, or a nitrogen atmosphere. Never store ISO in an open container.
• Keep the ISO pump wet cup or reservoir (if installed) filled with appropriate lubricant. The lubricant creates a barrier between the ISO and the atmosphere.
• Use only moisture-proof hoses compatible with
ISO.
• Never use reclaimed solvents, which may contain moisture. Always keep solvent containers closed when not in use.
• Always lubricate threaded parts with an appropriate lubricant when reassembling.
NOTE: The amount of film formation and rate of crystallization varies depending on the blend of ISO, the humidity, and the temperature.
Foam Resins with 245 fa
Blowing Agents
Some foam blowing agents will froth at temperatures above 90°F (33°C) when not under pressure, especially if agitated. To reduce frothing, minimize preheating in a circulation system.
Changing Materials
NOTICE
Changing the material types used in your equipment requires special attention to avoid equipment damage and downtime.
• When changing materials, flush the equipment multiple times to ensure it is thoroughly clean.
• Always clean the fluid inlet strainers after flushing.
• Check with your material manufacturer for chemical compatibility.
• When changing between epoxies and urethanes or polyureas, disassemble and clean all fluid components and change hoses. Epoxies often have amines on the B (hardener) side. Polyureas often have amines on the B (resin) side.
3A5743B
Overview
Overview
The system is a portable, electric-powered, 1:1 mix ratio proportioner. It is for use with formulated no-heat polyurethane foams that may be applied with impingement mix spray guns and for use with polyurea joint fill materials that may be applied with static mix guns.
Severe duty, positive displacement reciprocating piston pumps meter fluid flow to the gun for mixing and applying. When set to recirculation mode, the system will circulate fluids back to the supply pails.
An electronic processor controls the motor, monitors fluid pressures, and alerts the operator if errors occur.
See STATUS Indicator, page 11, for further information.
The system has two recirculation speeds: slow and fast, and an adjustable pressure/flow output.
Slow Recirculation
• Use for pump priming.
Fast Recirculation
• Use for flushing.
• Use for pump priming.
Output Adjust
Automatically maintains selected pressure/flow output for spraying.
3A5743B 9
Component Identification
Component Identification
/
/
$
3
0
F IG . 1: Component Identification
Key:
A Pump A
B Pump B
C Fluid Pressure Gauges
D Recirc/Spray and Overpressure Relief Valves
E Control Panel
F Electric Motor and Drive Housings
*
G Hose Bundle
H Spray Gun
J Recirculation Outlet
L Outlet Hose Connections
M Power Cord
P Fluid Inlet
+
(
WLD
%
-
)
10 3A5743B
Controls and Indicators
Controls and Indicators
Motor/Pump Control Function Knob
Status
Codes
+
-
Status Indicator
Power
Switch
-
-
TI17123b
F IG . 2: Controls and Indicators
Power Switch
Powers the system on and off.
Motor/Pump Control Function Knob
Use knob to select desired function.
Icon Setting
Stop/Park
Function
Stops motor and automatically parks pumps.
Slow Recirc Slow recirculation speed.
Fast Recirc Fast recirculation speed.
Static Mix
Spray
Use fluid flow settings 1-5 to dispense polyurea joint-fill materials through a static mixer.
Use fluid pressure settings
6-10 to spray polyurethane foam.
STATUS Indicator
Indicates system status, including power and error codes.
• Indicator steady on: power switch is turned on.
• Indicator blinking: If an error occurs, the status indicator light will blink one to seven times to indicate a specific status code, pause, and then repeat. The following table provides a brief description of each status code. For more detailed
information and corrective action, see Status
Table 1: Status Codes
(also located on the front of the Reactor)
Code Code Name
5
6
7
3
4
1
2
Pressure imbalance between A and B sides
Unable to maintain pressure setpoint
Pressure transducer A failure
Pressure transducer B failure
Excessive current draw
High motor temperature
No cycle counter switch input
NOTE: The default is to shut down if a status code indication occurs. Codes 1 and 2 may be set to disable automatic shutdown if desired; see page 22. You cannot set the other codes.
3A5743B 11
Setup
Setup
Location
• The system should always be used on a level surface.
• Do not expose the system to rain.
Grounding
Electrical Requirements
• Required power source: single dedicated circuit that is rated at a minimum of 15A.
NOTE: Cords must be 3-conductor grounded, rated for your environment.
• Power cord connector (120V):
One NEMA 5-15T
• Extension cord requirements:
Required Wire Size
Up to 50 ft (15 m)
AWG 14
Up to 100 ft (30 m)
AWG 12
The equipment must be grounded to reduce the risk of static sparking and electric shock. Electric or static sparking can cause fumes to ignite or explode.
Improper grounding can cause electric shock.
Grounding provides an escape wire for the electric current.
System: grounded through power cord.
Generator (if used): follow your local code and manufacturer’s recommendations. Start and stop the generator with power cord(s) disconnected.
Spray gun: ground through connection to a properly grounded fluid hose and system.
Fluid supply container: follow local code.
Object being sprayed: follow local code.
Solvent pails used when flushing: follow local code.
Use only conductive metal pails, placed on a grounded surface. Do not place the pail on a nonconductive surface, such as paper or cardboard, which interrupts grounding continuity.
To maintain grounding continuity when flushing or
relieving pressure: hold metal part of the spray gun firmly to the side of a grounded metal pail, then trigger the gun.
12 3A5743B
Setup
Connect Fluid Hoses
Connect fluid supply hoses to outlet hose connections
(F IG . 3). Red hoses for component A (ISO), blue for component B (RES). Fittings are sized to prevent connection errors. Connect other end of hoses to A and
B inputs of gun.
NOTICE
To prevent pressure fluctuations and equipment damage, only operate equipment with fluid supply hoses longer than 25 ft.
Connect Main Air Supply
The system requires 4 scfm (0.112 m
3
/min) compressed air for the air operated spray guns to work correctly.
Connect the main air supply to the quick disconnect fitting on the unit. The air supply hose must be at least
5/16 in. (8 mm) ID up to 50 ft (15 m) or 3/8 in. (10 mm)
ID up to 100 ft (30 m).
Connect Gun to Air Hose
(Air-Operated Guns Only)
Connect gun air hose to the gun air input and to the air filter outlet. If you are using more than one hose bundle, join the air hoses with the nipple provided with the hose bundle.
Flush Before Using Equipment
The equipment was tested with lightweight oil, which is left in the fluid passages to protect parts. To avoid contaminating your fluid with oil, flush the equipment with a compatible solvent before using the equipment.
B (RES)
A (ISO)
Compressed Air Line
WLD
A (ISO)
Air
B (RES)
F IG . 3: Hose and Air Connections
3A5743B 13
Setup
Fill Wet-cups
Keep the felt washers in the pump wet-cups saturated with Graco ISO pump oil, Part No. 217374. The lubricant creates a barrier between the ISO and the atmosphere.
Fill wet-cups through the slots in the plate, or remove a screw and swing the plate to the side.
Slots
The pump rod and connecting rod move during operation. Moving parts can cause serious injury such as pinching or amputation. Keep hands and fingers away from the wet-cup during operation. Shut off power before filling the wet-cup.
F IG . 4: Fill Wet Cup
TI17124a
14 3A5743B
Setup
Recirculate Material
The system circulates material from the fluid manifold back to the supply container.
5.
Set the Recirc/Spray valves to Recirc.
1.
Insert inlet tubes into pails.
2.
Set function knob to Stop/Park.
F IG . 5
3.
Plug in power cord.
4.
Turn on power.
+
-
TI17127b
TI17133a
F IG . 7
6.
Set function knob to Slow Recirc
.
or Fast Recirc
+
-
OR +
-
TI17128b
F IG . 8
7.
When material exits both recirculation tubes, set the function knob to Stop/Park .
8.
Set the Recirc/Spray valves to Spray.
TI17134a
F IG . 6
TI17132a
F IG . 9
3A5743B 15
Setup
Flush Fluid
1.
Insert inlet tubes into pails of solvent.
2.
Insert recirculation tubes into waste containers.
3.
Set function knob to Stop/Park
.
F IG . 10
4.
Plug in power cord.
5.
Turn on power.
+
-
TI17127b
7.
Set function knob to Slow Recirc
.
or Fast Recirc
+
-
OR +
-
TI17128b
F IG . 13
8.
When clean solvent exits both recirculation tubes, set the function knob to Stop/Park .
9.
Insert inlet tubes into the material containers.
10. Set the Recirc/Spray valves to Spray.
TI17134a
F IG . 11
6.
Set the Recirc/Spray valves to Recirc.
F IG . 14
11. Run until material exits gun manifold.
TI17132a
TI17133a
F IG . 12
16 3A5743B
Spraying
Spraying
For air operated guns, air is supplied to spray gun with gun piston safety lock engaged and gun fluid manifold valves A and B closed (if present).
F IG
1.
. 15
Set function knob to Stop/Park.
6.
Check fluid pressure gauges to ensure proper pressure balance. If imbalanced, reduce pressure of higher component by slightly turning Recirc/Spray valve for that component toward Recirc, until gauges show balanced pressures. The pressure imbalance alarm (Status Code 1) is inactive for 10 seconds after entering spray pressure mode, to allow time to balance pressures.
In this example, the B side pressure is higher, so use the B side valve to balance pressures.
Ti17137a
F IG . 19
NOTE: Watch gauges for 10 seconds to ensure pressure holds on both sides and pumps are not moving.
7.
Open gun fluid manifold valves A and B
(impingement mix guns only).
+
-
F IG . 16
2.
Engage piston safety lock.
3.
Open gun manifold.
4.
Set Recirc/Spray valves to Spray.
TI17127b
TI17132a
F IG . 17
5.
Turn the pressure control knob to the right until fluid pressure gauges show desired pressure.
NOTE: It is desirable to use lower pressure for joint filling applications.
F IG . 20
NOTICE
On impingement guns, never open the fluid manifold valves or trigger the gun while pressures are imbalanced. Opening the valves or triggering the gun during a pressure imbalance can cause material crossover in the gun, leading to equipment damage.
8.
Disengage piston safety lock.
F IG . 18
3A5743B
+
-
TI17129b
F IG . 21
9.
Test spray onto cardboard or plastic sheet. Verify that material fully cures in the required length of time, and is the correct color. Adjust pressure and temperature to get desired results. Equipment is ready to spray.
17
Pressure Relief Procedure
Pressure Relief
Procedure
Follow the Pressure Relief Procedure whenever you see this symbol.
Shutdown
For longer breaks (more than 10 minutes), use the following procedure. If you will be shut down for more
than three days, perform the Flushing procedure, page
1.
Follow Pressure Relief Procedure.
2.
Close gun fluid valves A and B. Doing this will keep the internal parts of the gun cleaner and prevent crossover.
This equipment stays pressurized until pressure is manually relieved. To help prevent serious injury from pressurized fluid, such as skin injection, splashing fluid and moving parts, follow the Pressure Relief Procedure when you stop spraying and before cleaning, checking, or servicing the equipment.
1.
Perform the gun pressure relief procedure. Refer to your separate spray gun manual.
2.
Set function knob to Stop/Park
.
F IG . 24
3.
Shut off power.
+
-
TI17127b
F IG . 22
3.
Turn Recirc/Spray valves to Recirc. Fluid will be returned to material pails. Pumps will move to the bottom of their stroke. Ensure gauges drop to 0.
TI17135a
F IG . 25
4.
Perform the gun shutdown procedure. Refer to your separate spray gun manual.
5.
Wrap hoses around sprayer.
6.
Disconnect power cord before moving.
TI17133a
F IG . 23 ti33432a
F IG . 26
18 3A5743B
Maintenance
Maintenance
•
Check pump wet-cups fluid level daily. Refer to Fill
• Do not overtighten packing nut/wet-cup. Throat u-cup is not adjustable.
• Keep component A from exposure to moisture in atmosphere, to prevent crystallization.
• Generally, flush if you will shutdown for more than three days. Flush more often if material is moisture sensitive and humidity is high in the storage area, or if material may separate or settle out over time.
• Close gun fluid valves A and B when not spraying.
Doing this will keep the internal parts of the gun cleaner and prevent crossover. See spray gun manual.
Flushing
Flush equipment only in a well-ventilated area. Do not spray flammable fluids.
• Generally, flush if you will be shut down for more than 3 days. Flush more often if material is moisture sensitive and humidity is high in the storage area, or if material may separate or settle out over time.
• Flush out old fluid with new fluid, or flush out old fluid with a compatible solvent before introducing new fluid.
• Use the lowest possible pressure when flushing.
• Always leave some type of fluid in system. Do not use water.
• For long term storage, flush out the solvent with a storage fluid such as Lanxess-brand Mesamoll
® plasticizer or, at minimum, clean motor oil.
1.
Engage piston safety lock or trigger safety lock.
Close fluid valves A and B. Leave air on.
F
IG
. 27
• Always grease the gun after use. Use Part No.
117773 Grease. See spray gun manual.
F IG . 28
2.
Set function knob to Stop/Park.
+
-
TI17127b
F IG . 29
3A5743B 19
Maintenance
3.
Remove both recirculation tubes from material containers and secure each one to a dedicated waste container.
4.
In the material containers, pull the fluid inlet tubes out of the material.
5.
Turn Recirc/Spray valves to Recirc.
NOTE: To flush the spray gun, refer to your separate spray gun instruction manual.
11. Purge gun hoses.
a.
Disconnect hoses from gun and secure to a pail of solvent.
b.
Turn Recirc/Spray valve A to Spray.
TI17133a
F IG . 30
6.
Set function knob to Fast Recirc
+
-
. Pump material from fluid inlet tubes until no more comes out.
TI17130b
TI17136a
F IG . 32 c.
Open gun into waste container A.
d.
Set function knob to Slow Recirc is flushed.
until hose e.
Set function knob to Stop/Park f.
Repeat for B side.
.
F IG . 31
7.
Set function knob to Stop/Park .
8.
Remove the fluid inlet tubes from the material containers and place the tubes in the solvent containers.
9.
Set function knob to Fast Recirc . Pump solvent through system into waste containers.
10. When nearly clear solvent exits the recirculation tubes, set function knob to Stop/Park .
12. Set function knob to Stop/Park .
13. Solvent flushing is a two step process. Go back to step 3, drain solvent, and flush again with fresh solvent.
14. Place fluid inlet tubes in a pail of plasticizer or clean motor oil and circulate fluid through the system.
Leave fluid in the unit.
NOTE: Never leave the unit dry unless it has been disassembled and cleaned. If fluid residue dries in the pumps, the ball checks may stick the next time you use the unit.
20 3A5743B
Troubleshooting
Troubleshooting
Status Codes
Determine the status code by counting the number of times the status indicator blinks.
-
-
STATUS Indicator
TI17123b1
F IG . 33
Status Code 1: Pressure Imbalance
NOTE: The unit does not check for pressure imbalance at setpoints less than 250 psi (1.75 MPa, 17.5 bar). The unit does not check for pressure imbalance for 10 seconds after entering pressure mode.
Unit senses pressure imbalance between components
A and B, and warns or shuts down, depending on settings of DIP switches 1 and 2. To turn off automatic shutdown and/or tighten pressure tolerances for status code 1, see Status Code 1 and 2 Settings.
1.
Check fluid supply of lower pressure component and refill if necessary.
2.
Reduce pressure of higher component by slightly turning Recirc/Spray valve for that component toward Recirc, until gauges show balanced pressures.
In this example, B side pressure is higher, so use the B side valve to balance pressures.
Ti17137a
F
IG
. 34
NOTE: Turn Recirc/Spray valve only enough to balance pressure. If turned completely, all pressure will bleed off.
3.
Check fluid inlet strainers and fluid filters at gun.
Status Code 2: Pressure Deviation from
Setpoint
The unit does not check for pressure deviation at setpoint less than 400 psi (2.8 MPa, 28 bar).
Unit senses pressure deviation from setpoint, and warns or shuts down, depending on settings of DIP switches 3 and 4. If equipment cannot maintain enough pressure for a good mix at the gun, try using a smaller mix chamber or nozzle.
To turn off automatic shutdown and/or tighten pressure tolerances for status code 2, see Status Code 1 and 2
Settings.
3A5743B 21
Troubleshooting
Status Code 1 and 2 Settings
1.
Locate switch SW2 on the control board.
2.
Set the four DIP switches to the desired positions.
See F IG . 35 and Table 2.
OFF
1
2
3
4 TI7023a
1
2
3
4
F
IG
. 35. DIP Switch (SW2) Settings
ON
(Default)
TI7024a
Table 2: Status Code 1 and 2 Settings
DIP Switch and Function Left
DIP Switch 1
If selected, causes shutdown or displays an advisory if the pressure imbalance exceeds selection made in DIP Switch 2
DIP Switch 2
ADVISORY
If selected, causes shutdown if A and B pressure imbalance is greater than
500 psi (3.5 MPa, 35 bar)
(60% if < 800 psi [5.6
MPa, 56 bar] running)
If selected, causes advisory if A and B pressure imbalance is greater than
300 psi (2.1 MPa, 21 bar)
(50% if < 800 psi [5.6
MPa, 56 bar] running)
DIP Switch 3
If selected, causes shutdown or displays an advisory due to deviation of pressure from setpoint exceeds selection made in
DIP Switch 4
ADVISORY
DIP Switch 4
Causes advisory if deviation of pressure from setpoint is greater than
300 psi (2.1 MPa, 21 bar)
(25% if < 800 psi [5.6
MPa, 56 bar])
Right (default setting)
SHUTDOWN
800 psi (5.6 MPa, 56 bar)
(70% if < 800 psi [5.6
MPa, 56 bar] running)
500 psi (3.5 MPa, 35 bar)
(60% if < 800 psi [5.6
MPa, 56 bar] running)
SHUTDOWN
500 psi (3.5 MPa, 35 bar)
(40% if < 800 psi [5.6
MPa, 56 bar])
Status Code 3: Transducer A Failure
1.
Check transducer A electrical connections (J3) at
2.
Reverse A and B transducer electrical connections
at board, page 25. If error moves to transducer B
(Status Code 4), replace transducer A, page 24.
Status Code 4: Transducer B Failure
1.
Check transducer B electrical connections (J8) at
2.
Reverse A and B transducer electrical connections
at board, page 25. If error moves to transducer A
(Status Code 4), replace transducer B, page 24.
Status Code 5: Excessive Current Draw
Shut off unit and contact distributor before resuming operation.
1.
Locked rotor: motor unable to turn. Replace motor.
2.
Short on control board. Replace board, page 24.
3.
Worn or hung up motor brush causing arching of brush at commutator. Replace brushes.
22 3A5743B
Troubleshooting
Status Code 6: High Motor Temperature
Motor is running too hot.
1.
Motor temperature too high. Reduce pressure duty cycle, gun tip size, or move system to a cooler location. Allow 1 hour for cooling.
2.
Check fan operation. Clean fan and motor housing.
Status Code 7: No Cycle Counter Switch
Input
Have not received input from cycle counter switch for 10 seconds after selecting Recirculation Mode.
1.
Check cycle counter switch connection to board
(J10, pins 5, 6), page 25 (figure control module
wiring connections).
2.
Check that magnet (224) and cycle counter switch
(223) are in place under B side motor end cover
(227). Replace if necessary.
3A5743B 23
Repair
Repair
Control Board
Power Bootup Check
There is one red LED (D11) on the board. Power must
. 37 for location. Function is:
• Startup: 1 blink for 60 Hz, 2 blinks for 50 Hz.
• Motor running: LED on.
• Motor not running: LED off.
• Status code (motor not running): LED blinks status code
Control Board Replacement
Check motor before replacing board.
1.
Follow Pressure Relief Procedure, page 18.
2.
Carefully lay the sprayer on its side on a level surface. Rotate the sprayer and rest upside-down on blocks.
NOTE: Always use two people when lifting the sprayer on to a workbench.
3.
Remove four screws (10) and control board cover
(61) to expose the control board (12).
4.
Disconnect all cables and connectors from board.
5.
Remove seven screws (13) and remove board.
6.
Install new board in reverse order.
NOTE: Apply thermal compound between the square steel piece on the back of the board and the main aluminum plate. Order Part No. 110009 Thermal
Compound.
J1
J2
J3
J4
J7
J8
J9
J10
Table 3: Control Board Connectors
(see F
. 37)
Board
Jack Pin Description
J11 n/a n/a
Main power from breaker n/a
Function knob n/a Transducer A
Motor power (230 V units)
1, 2
Motor thermal overload signal n/a
Transducer B n/a
Fan
1, 2
Status Indicator
3, 4
Not used
5, 6
Cycle switch signal
7, 8
Jumpered
9, 10
Jumpered n/a
Motor power (120 V)
10 (x4)
61
12
13 (x7)
24
F IG . 36: Control Board Removal
WLD
3A5743B
Repair
LINE
P1
P2
Motor
Fan
Black Twin Flat Cable
Red
Black
J9
Yellow
Cycle
Counter
Yellow
Red
Black
Status
Indicator
Black
Black Sheath
Jumper
White
Jumper
J1
J11
(120 V Board)
1
4
5
2
3
6
7
8
9
10
J7
J10
OFF
1
2
3
4
CONTROL
BOARD
25N033 (120 V)
ON
SW2 (see page 22 to adjust settings) not used
Black
Red
White
J2
J8 J3
Black Sheath
Function
Knob
Pressure Transducer A
Black Phone Cable and Plug
Pressure Transducer B
F IG . 37: Control Module Wiring Connections
3A5743B 25
Repair
26 3A5743B
Parts
120 V Fusion Air Purge System Packages
Parts
WLD
101
System
Package Volts Description
25N014
25N015
120 V
Fusion Air Purge Proportioner Packages for E-8p
Fusion Air Purge Proportioner Packages for E-15p
Bare Proportioner
(101)
25A836
26C023
Gun
(103)
247124
103
3A5743B 27
Parts
25A836 and 26C023, Bare Proportioner
WLD
28
1 Apply sealant to threads.
2 Apply sealant to all non-swiveling pipe threads.
3 Apply lubricant to all o-rings and bolt-wheel connection (3, 91).
4 Cover entire surface of sensor probe with lubricant before assembling onto motor plate (8).
5 Torque to 5-6 ft-lbs (6.7-8 N•m).
3A5743B
25A836 and 26C023, Bare Proportioner (continued)
A
Parts
A
WLD
WLD
29 3A5743B
Parts
25A836 and 26C023, Bare Proportioner (continued)
0$1,)2/'$&&25',1*/<
25,(1735(6685(
0$1,)2/'$&&25',1*/<
( )
25,(1735(6685(
'(7$,/&
6(('(7$,/%
'(7$,/%
D
6(('(7$,/
&
A
D
B
E 6
6(('(7$,/
$
35(6685($
327(17,20(7(5
35(6685(%
32:(5
PIN 1 - J UMPER
PIN 2 - J UMPER
PIN 3 - J UMPER
PIN 4 - J UMPER
PIN 5 - CYCLE COUNTER
PIN 6 - CYCLE COUNTER
PIN 7 - NOT USED
PIN 8 - NOT USED
PIN 9 - DISPLAY LED
PIN 10 - DISPLAY LED
B
LA
C
K W
IRE
RED
W
IRE
*5281'
027257+(50$/
<(//2:
0272532:(5287
5('$1'%/$&.
8
02725)$1
WLD
'(7$,/$
30 3A5743B
Parts
25A836 and 26C023, Bare Proportioner (continued)
17
18
19
20
21
7
8
10
11
12
13
14
22
23
27
28
29
30
31
32
33
34
Ref.
Part
3
4
1
2
5
15
16
Description Qty.
24J139 CART, painted
16H888 GROMMET, push-in, 7/8 id
16F820 WHEEL, caster
16H352 SPACER, axle
121573 BUMPER, urethane, 3/8-16, 80-90 dur
120454 WASHER, flat
16G939 PLATE, motor mount
117493 SCREW, mach, hex washer hd
102040 NUT, lock, hex
25N033 BOARD, circuit assy
107156 SCREW, mach, pan hd
24K983 SWITCH, rocker, w/breaker, 240V,
20A
119930 DIODE, light-emitting
24L002 POTENTIOMETR, adjustment, pressure
119897 FITTING, bulkhead, cable, 0.250
24K995 CORD SET, power, 125V
15G230 CABLE, harness, power
15C866 WIRE, jumper
116773 CONNECTOR, plug, 3.81 mm (10 position)
15G053 PLATE, detent, display
24L001 KNOB, control, w/ball plunger
24J147 MANIFOLD, recirculation
24J140 BRACKET, recirc mnfld, painted 1
115492 SCREW, mach, slot hex wash hd 10
1
1
1
1
1
1
1
1
108296 SCREW, mach, hex wash hd
156971 FITTING, nipple, short
155541 FITTING, swivel, 90 degree
15G292 MANIFOLD, pressure transducer
116704 ADAPTER, 9/16-18 jic x 1/4 npt
2
2
2
2
2
1
1
2
1
1
1
2
7
1
6
1
4
1
8
Ref.
Part Description Qty.
35
36
45
46
24K999 TRANSDUCER, pressure, control
16H530 TUBE, fluid
249629 HOSE, cpld, 1/4" x 48", moistgard 1
249630 HOSE, cpld, 1/4" x 48", resin 1
2
2
58
61
62
103473 STRAP, tie, wire 4
24J141 COVER, electronics, painted, E-8P 1
24J151 COVER, shroud, front, painted
63 24J152 COVER, shroud, back, painted
67
▲
16H569 LABEL, warning
85 16H543 HANDLE, pull
1
1
1
1
86
87
90
121114 NUT, hex, self locking
261866 WASHER, flat
112154 PIN, straight, slotted
91 15M314 SCREW, cap
92
▲
189930 LABEL, caution
93 ▲ 16H902 TAG, informational
94
96
15G458 CABLE, fan, 46" w/plug/board conn
217374 LUBRICANT, ISO pump
98
99
113505 NUT, keps, hex hd
26A503 PROPORTIONER, 120V, E-15P,
OEM
25A835 PROPORTIONER, 120 V, E-8p,
OEM
102 17L272 PLUG, rubber
103* 119992 FITTING, pipe, nipple, 3/4 x 3/4 npt
1
1
1
2
2
2
1
1
2
2
1
1
1
▲ Replacement Danger and Warning labels, tags, and cards are available at no cost.
* Only used with Reactor E-8p (25A836).
3A5743B 31
Parts
25A836 and 26C023, Bare Proportioner
LQPP
IURPLQVLGHERWWRPHGJH
LQPP
IURPLQVLGHHGJH
WLD
1 Apply lubricant to all gear teeth, motor pinion, and motor end bell on both sides of the motor.
2
Apply lubricant to rectangular cavity on connecting link.
3
Apply lubricant to threads of cylinder before assembly into housing.
4
Torque to 150+/-10 in-lbs.
5
Tighten by hand only.
6 Torque fasteners to 30-35 in-lbs. Applies only when fasteners are assembled in plastic housings (215).
7 Switch mounts to cover opposite brush end of motor only.
8
9
10
Housing must be installed on motor with crankshafts aligned with each other.
Assemble magnet to center of offset crankshaft on switch cover side of motor and adjust for park location.
Affix switch to motor cover with double-sided tape. Cut to 2 in.
(51 mm). Mount cover on side opposite the brush end of motor.
32 3A5743B
Parts
Ref.
Part Description Qty.
201 24E355 MOTOR, 120V
202 24K985 FAN, cooling, 120 VAC
203 115836 GUARD, finger
204 103646 RIVET, blind
205 120094 SCREW, pan hd, phil, zinc
207‡ 115492 SCREW, mach, slot hex wash hd
208* 116074 WASHER, thrust
209* 107434 BEARING, thrust
210* 248231 CRANK, 595
211* 180131 BEARING, thrust
212† 116073 WASHER, thrust
213† 116079 BEARING, thrust
214† 249194 GEAR, reducer (first stage) 2
215 26A505 HOUSING, drive, assembly, E-15p 2
‡ 287000 HOUSING, drive, assembly, E-8p
216 ◆ 287053 ROD, connecting
217
◆
196762 PIN, straight
218 17A257 NUT, jam, pump, E-15p
195150 NUT, jam, pump, E-8p
2
2
2
2
2
2
4
2
2
2
2
3
8
1
1
1
1
Ref.
Part Description
219 245970 PUMP, displacement, E-15p
24L006 PUMP, displacement, E-8p
220‡ 117493 SCREW, mach, hex washer hd
221 15B254 COVER, front, Graco, paint
222‡ 15B589 COVER, pump rod
223 117770 SWITCH, reed w/cable
224 24K982 MAGNET, disc, 0.38 dia, 0.100 thick
227 115711 TAPE, foam, 1/2 wide
228 119997 INSERT, thread, knock-in, 8/32 unc
229 15F849 LABEL, side, Reactor, Graco
* Included in 248231 Crankshaft Kit.
† Included in 287057 Gear Reducer Kit.
‡ Included in 287055 Drive Housing Kit.
◆ Included in 287053 Connecting Rod Kit.
Qty.
2
1
1
8
2
2
2
1
1
2
3A5743B 33
Parts
Recirculation Manifold, 24J147
507
3 506 505 3
504
3
503
1 2 3
503a
4
503b
4
501
502
Ref.
Part Description
501 24K993 MANIFOLD, recirculation
502 111763 ELBOW; 1/4 npt (mbe)
503 239914 VALVE, recirc/spray; includes items
503a, 503b
503a 15E022 SEAT, valve
503b 111699 GASKET, seat, valve
504 224807 BASE, valve
505 187625 HANDLE, valve, drain
506 111600 PIN, grooved
507 113641 GAUGE, pressure, fluid
508 116504 TEE; 1/4 npt(m) x 1/4 npt(f) run; 1/4 npt(f) branch
509 119998 ADAPTER; 5/16 JIC x 1/4 npt(m)
510 116704 ADAPTER; 3/8 JIC x 1/4 npt(m)
511 556765 ELBOW, tube; 1/4 npt(m) x 3/8 in.
(10 mm) OD tube
515 156823 UNION, swivel; 1/4-18 npt
Qty
1
4
2
2
1
1
2
2
2
2
2
1
1
2
510
508
511
515
509
TI17460a
1
2
Torque to 250 in-lb (28 N•m).
Use blue threadlocker on valve cartridge threads into manifold.
3 Apply lubricant to mating surfaces.
4 Part of item 503.
34 3A5743B
Suggested Spare Replacement Parts
Suggested Spare
Replacement Parts
Part Description
24K983 SWITCH, motor power, with circuit breaker
113641 GAUGE, pressure, fluid; sst
239914 VALVE, recirc/spray; includes seat and gasket
24L002 POTENTIOMETER, control knob
24G886 BOARD, control; 120 V units only
24G887 BOARD, control; 240 V units only
24K999 TRANSDUCER, pressure
24L006 PUMP, displacement; fits either side
249855 REPAIR KIT, displacement pump; includes seals, balls, bearings, intake valve seat)
Accessories
Fusion Air Purge Gun
Air purge gun, available in round or flat patterns. See manual 309550.
3A5743B 35
Dimensions
Dimensions
LQ
FP
LQ
FP
WLD
LQ
FP
36 3A5743B
Technical Data
Technical Data
Reactor E-8p and E-15p
Maximum fluid working pressure
Electrical requirements
Generator Size
Minimum hose length
Maximum Ambient Temperature
Overpressure Relief
Maximum Output at 340 cycles/min
E-8p
E-15p
Output per Cycle (A and B)
E-8p
E-15p
Sound Pressure
In fast circulation mode
At 2000 psi (14 MPa, 138 bar), 0.72 gpm (2.7 lpm)
Sound Pressure per ISO 9614-2
In fast circulation mode
At 2000 psi (14 MPa, 138 bar), 0.72 gpm (2.7 lpm)
Inlet/Outlet Sizes
Fluid Outlet - Component A (ISO)
Fluid Outlet - Component B(RES)
Fluid Circulation Return - Component A (ISO)
Fluid Circulation Return - Component B(RES)
Air Inlet
Air Outlet
Hose Markings
A Side
B Side
Weight (empty), without gun and hose
Wetted Parts
Maximum Hose Length
US
2000 psi
Metric
14 MPa, 138 bar
120 Vac, 1 phase, 50/60 Hz, 1800 W; requires a single dedicated 15 A circuit
2500 W minimum
25 ft
110°F
7.6 m
43°C
Recirc/Spray valves automatically relieve excessive fluid pressure back to supply tanks
12 lb/min
15 lb/min
0.00352 gal.
0.0044 gal.
78.7 dB(A)
84.5 dB(A)
88.6 dB(A)
94.4 dB(A)
-5 JIC male
-6 JIC male
-5 JIC male
-6 JIC male
5.4 kg/min
6.8 kg/min
0.0133 liter
0.0167 liter
1/4 in. quick-disconnect industrial type pin fitting
1/4 npsm(m)
Red
Blue
95 lbs.
43.1 kg
Aluminum, stainless steel, carbon steel, brass, carbide, chrome, chemically resistant o-rings, PTFE, ultra-high molecular weight polyethylene
105 ft 32 m
3A5743B 37
Graco Standard Warranty
Graco warrants all equipment referenced in this document which is manufactured by Graco and bearing its name to be free from defects in material and workmanship on the date of sale to the original purchaser for use. With the exception of any special, extended, or limited warranty published by Graco, Graco will, for a period of twelve months from the date of sale, repair or replace any part of the equipment determined by
Graco to be defective. This warranty applies only when the equipment is installed, operated and maintained in accordance with Graco’s written recommendations.
This warranty does not cover, and Graco shall not be liable for general wear and tear, or any malfunction, damage or wear caused by faulty installation, misapplication, abrasion, corrosion, inadequate or improper maintenance, negligence, accident, tampering, or substitution of non-Graco component parts. Nor shall Graco be liable for malfunction, damage or wear caused by the incompatibility of Graco equipment with structures, accessories, equipment or materials not supplied by Graco, or the improper design, manufacture, installation, operation or maintenance of structures, accessories, equipment or materials not supplied by Graco.
This warranty is conditioned upon the prepaid return of the equipment claimed to be defective to an authorized Graco distributor for verification of the claimed defect. If the claimed defect is verified, Graco will repair or replace free of charge any defective parts. The equipment will be returned to the original purchaser transportation prepaid. If inspection of the equipment does not disclose any defect in material or workmanship, repairs will be made at a reasonable charge, which charges may include the costs of parts, labor, and transportation.
THIS WARRANTY IS EXCLUSIVE, AND IS IN LIEU OF ANY OTHER WARRANTIES, EXPRESS OR IMPLIED, INCLUDING BUT NOT LIMITED
TO WARRANTY OF MERCHANTABILITY OR WARRANTY OF FITNESS FOR A PARTICULAR PURPOSE.
Graco’s sole obligation and buyer’s sole remedy for any breach of warranty shall be as set forth above. The buyer agrees that no other remedy
(including, but not limited to, incidental or consequential damages for lost profits, lost sales, injury to person or property, or any other incidental or consequential loss) shall be available. Any action for breach of warranty must be brought within two (2) years of the date of sale.
GRACO MAKES NO WARRANTY, AND DISCLAIMS ALL IMPLIED WARRANTIES OF MERCHANTABILITY AND FITNESS FOR A
PARTICULAR PURPOSE, IN CONNECTION WITH ACCESSORIES, EQUIPMENT, MATERIALS OR COMPONENTS SOLD BUT NOT
MANUFACTURED BY GRACO. These items sold, but not manufactured by Graco (such as electric motors, switches, hose, etc.), are subject to the warranty, if any, of their manufacturer. Graco will provide purchaser with reasonable assistance in making any claim for breach of these warranties.
In no event will Graco be liable for indirect, incidental, special or consequential damages resulting from Graco supplying equipment hereunder, or the furnishing, performance, or use of any products or other goods sold hereto, whether due to a breach of contract, breach of warranty, the negligence of Graco, or otherwise.
FOR GRACO CANADA CUSTOMERS
The Parties acknowledge that they have required that the present document, as well as all documents, notices and legal proceedings entered into, given or instituted pursuant hereto or relating directly or indirectly hereto, be drawn up in English. Les parties reconnaissent avoir convenu que la rédaction du présente document sera en Anglais, ainsi que tous documents, avis et procédures judiciaires exécutés, donnés ou intentés, à la suite de ou en rapport, directement ou indirectement, avec les procédures concernées.
Graco Information
For the latest information about Graco products, visit www.graco.com.
For patent information, see www.graco.com/patents.
TO PLACE AN ORDER, contact your Graco distributor or call to identify the nearest distributor.
Phone: 612-623-6921 or Toll Free: 1-800-328-0211 Fax: 612-378-3505
All written and visual data contained in this document reflects the latest product information available at the time of publication.
Graco reserves the right to make changes at any time without notice.
Original instructions.
This manual contains English. MM 3A5743
Graco Headquarters: Minneapolis
International Offices: Belgium, China, Japan, Korea
GRACO INC. AND SUBSIDIARIES • P.O. BOX 1441 • MINNEAPOLIS MN 55440-1441 • USA
Copyright 2018, Graco Inc. All Graco manufacturing locations are registered to ISO 9001.
www.graco.com
Revision B , March 2018
advertisement
* Your assessment is very important for improving the workof artificial intelligence, which forms the content of this project
Related manuals
advertisement
Table of contents
- 3 Systems
- 3 Proportioners
- 3 Related Manuals
- 4 Warnings
- 7 Important Isocyanate (ISO) Information
- 9 Overview
- 10 Component Identification
- 11 Controls and Indicators
- 12 Setup
- 17 Spraying
- 18 Pressure Relief Procedure
- 18 Shutdown
- 19 Maintenance
- 21 Troubleshooting
- 24 Repair
- 27 Parts
- 35 Suggested Spare Replacement Parts
- 35 Accessories
- 36 Dimensions
- 37 Technical Data
- 38 Graco Standard Warranty